压盖级进模设计及模具设计
级进模模具毕业设计论文

目录摘要 (I)1 绪论 (2)2冲压的现状及趋势 (4)3冲压件工艺分析 (7)3.1冲压工艺方案的设计 (7)3.1主要设计步骤计算 (7)4工作零件刃口尺寸计算 (11)4.1模具总体设计 (12)4.2主要零部件设计 (12)5模具主要零件加工工艺规程的编制 (16)5.1 冲压模具制造技术要求 (16)5.2 总装工艺 (16)6 压力机的校核 (18)6.1 公称压力 (18)6.2 滑块行程 (18)6.3 行程次数 (18)6.4 工作台面的尺寸 (18)6.5 滑块模柄孔尺寸 (18)6.6 闭合高度 (18)总结 (19)致谢 (19)参考文献 (20)1 绪论材料成型是先进加工技术的重要组成部分,属于少、无切削加工,制造方法简单、生产效率高,特别是经过成型加工后的金属零件具有优越的力学性能,可满足工程需要。
因此,成型加工在未来制造业技术发展中,将占有举足轻重的地位。
而目前的成型加工,都需要采用相应的模具才能实现,模具工业的发展和提高是材料成型加工的必要保证。
在现代化基本建设中,模具工业已经逐渐形成为制造工业的基础核心产业。
越来越多的工业生产制造与模具有关,根据国际生产协会的专家预测,在21世纪末,50%~75%的机械模具生产制件产品都将利用模具进行加工制造。
模具是工业的基础工艺装备,用模具生产制件所表现出的高精度、高复杂度、高一致性、高生产力和低消耗,是其他加工方法所不能比拟的,工业发达国家的模具生产总值已超过机床生产总值。
因此,模具工业已经成为现代化制造业的重要支柱性产业。
特别是近些年来,模具设计制造的需求量以及高速度化、高效率化已经成为汽车制造业有待提高的一项重要技术。
模具生产技术水平的高低不仅是衡量一个国家产品制造水平高低的重要标志,而且在很大程度上决定着这个国家产品质量、笑意及新产品的开发能力。
随着社会经济的发展,对于工业产品的品种、数量、质量及款式等都提出了越来越高的要求,因此,也促进了模具工业的快速发展。
级进模具设计说明书
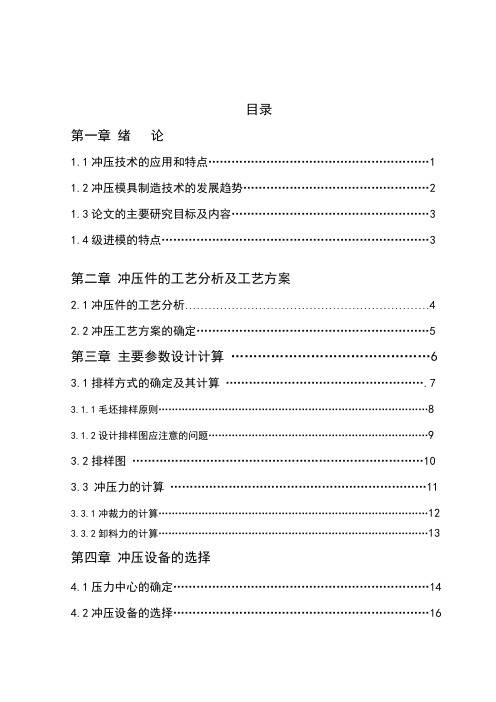
目录第一章绪论1.1冲压技术的应用和特点 (1)1.2冲压模具制造技术的发展趋势 (2)1.3论文的主要研究目标及内容 (3)1.4级进模的特点 (3)第二章冲压件的工艺分析及工艺方案2.1冲压件的工艺分析 (4)2.2冲压工艺方案的确定 (5)第三章主要参数设计计算 (6)3.1排样方式的确定及其计算 (7)3.1.1毛坯排样原则 (8)3.1.2设计排样图应注意的问题 (9)3.2排样图 (10)3.3 冲压力的计算 (11)3.3.1冲裁力的计算 (12)3.3.2卸料力的计算 (13)第四章冲压设备的选择4.1压力中心的确定 (14)4.2冲压设备的选择 (16)4.2.1冲压设备类型的选择 (17)4.2.2冲压设备规格的确定 (19)第五章模具主要零件的结构与设计5.1工作零件 (20)5.1.1凸模的设计 (21)5.1.1.1冲孔凸模的结构设计 (22)5.1.1.2冲孔凸模的结构设计 (23)5.1.1.5凸模强度校核 (24)5.1.2凹模的设计 (25)5.3卸料与顶件装置 (26)5.3.1卸料板 (29)5.3.2卸料螺钉的结构 (30)5.4.2 导正销 (31)5.4.3导柱导套 (32)5.5固定与联接零件 (33)5.5.1固定板与垫板 (34)5.5.2螺钉与销钉 (35)6.1模具设计总装图 (36)设计总结参考文献致谢摘要本次设计题目是带宽凸缘的覆盖件模具设计,制件来源于生产。
其带宽凸缘的覆盖件零件上需冲制三个孔、两个折弯位置。
通过对该零件的级进模具设计,掌握一般级进冲压模具的设计方法、特点和成型过程。
级进模的特点是冲压生产效率高、操作安全简单、生产成本较低、带宽凸缘的覆盖件质量高。
本设计详细介绍了级进模的排样方式、总体设计、零部件的设计以及工艺参数的选择计算。
注意设计当中的某些细节问题,了解冲压模具结构及工作原理;通过对AutoCAD的应用,从而有效的提高工作效率。
护盖级进模设计

方 案一 的评价 :
郝彦琴(9 4 ) 女, 17 一 , 工程师, 从事模具设计与制造 工作
该 方 案 先 冲孔 再 拉 深 , 始 冲 的 结 构 孔 , 作 为 开 可
导 正 孔 , 保 证 其 位 置 精 度 , 其 不 足 在 于 该 孔 在 后 能 但
续工 序 中会 发生 变形 , 难 保 证孔 的大小 。 且 结构 很 而 过 于 紧 凑 , 保 证 凸模 的精 度 。 难
10以 下 0
~
量 、 产效 率 、 具 结构 与 寿命 。 生 模
31 材 料 利 用 率 . 材 料 利 用 率 指 所 有 制 件 所 占 的 实 际 面 积 与 所 用
的 板 料 面 积 的 百 分 比 ( 4) 图 。
其 拉深性 能 和 冲压性 能好 , 仅 能满 足产 不
性 能 的技 术 要 求 , 满 足 冲 裁 和 拉 还 对 材料 的基 本要求 。 ) 深 件 结 构 工 艺 性 拉
盖 零 件 形 状 较 简 单 ,形 状 轴 对 称 ,
审 审 01 - — 6
D— — 工 件 垂 直 于 送 料 方 向 的 最 大 尺 寸 ,n Ym;
0 1 — — —
冲 模 设 计 中有 3种 排 样 : 即制 件 在 条 料 上 的 布
置 方 式 ; 进 模 的 制 件 和 工 序 排 列 方 式 ; 切 割 加 工 级 线 凸 模 或 凹模 时 工 件 在 毛 坯 上 的排 样 方 式 。排 样 的合
( ) 深件 的精度 3拉
护 盖 零 件 见 图 1所 示 ,使 用 材 料 0 8钢 , 料 厚 2 m, 寸 公 差 等 级 :T1 大 批 量 生 产 。 a r 尺 I 2,
上下罩盖级进模设计
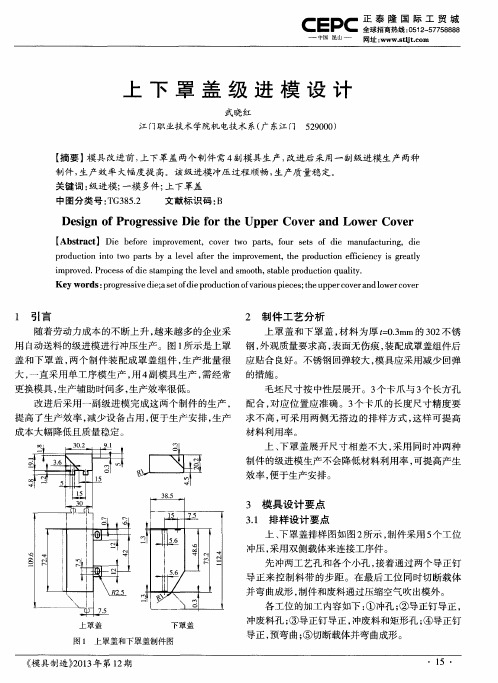
冲废料孑 L ; ③导正钉导正 , 冲废料和矩形孑 L ; ④导正钉
图 1 上罩盖和下罩盖制件 图
导正 , 预弯曲; ⑤切断载体并弯 曲成形 。
・l 5・
《 模 具制 造 b 2 o 1 3 年第 1 2 期
h t  ̄ : / / w w w . 5 z m o l c J 5 . E D M模 具 制 造 立 体 传 媒 电 子 商 务 平 台
-
剑I j
I
 ̄ - q
l寸
_ =
r — — \ l
I R 2 5
、
\
并弯曲成形 , 制件和废料通过压缩空气 吹出模外 。 各工位的加工内容如下 : ① 冲孑 L ; ②导正钉导正 ,
冲压模具级进模毕业设计

冲压模具级进模毕业设计冲压模具级进模是一种用于压力成形加工的模具,它能够在一次循环中完成多个工序,提高生产效率和产品质量。
本次毕业设计旨在设计一套适用于冲压模具级进模的工艺和设备,以满足工业生产的需求。
以下是本次毕业设计的具体内容和步骤。
1.需求分析首先,需要对冲压模具级进模的应用场景和要求进行需求分析。
了解冲压模具级进模的工作原理、具体应用领域以及对模具设计和设备要求等方面的信息,从而为后续设计工作提供方向和参考。
2.工艺设计根据需求分析的结果,进行工艺设计。
包括将原始材料加工成所需产品的具体步骤、工序和操作流程等。
在设计过程中,需要考虑模具的装夹方式、进模方式和工装设计等相关问题,确保工艺设计的合理性和可行性。
3.模具设计在完成工艺设计后,进行模具的设计工作。
模具设计主要包括模具结构设计和零件设计两个方面。
模具结构设计需要考虑模具的切削和定位原理,选用适当的材料和成型工艺,确保模具具备足够的强度和刚度。
零件设计需要根据产品尺寸和形状要求进行模具零件的设计,包括上模、下模、导向装置和顶杆等。
4.设备选型和设计在模具设计的基础上,进行设备选型和设计。
设备选型需要考虑工艺要求、生产能力和设备性能等方面的因素,选择适合的设备类型和规格。
设备设计包括设备整体结构设计和相关零部件设计,确保设备功能完善、操作方便和安全可靠。
5.制造和组装将模具和设备的设计图纸转化为实际产品。
制造过程包括原材料的采购、加工和热处理等工序,确保模具和设备的质量和性能。
组装过程则将各个零部件进行装配,确保模具和设备的完整性和一体性。
6.调试和测试对制造完成的模具和设备进行调试和测试。
通过调整参数、检查设备运行情况和模具质量等方面的测试,确保模具和设备的正常工作和满足产品质量要求。
7.结果分析和总结根据调试和测试的结果,对设计和制造过程进行分析和总结。
评估设计和制造的准确性和合理性,发现问题并提出改进措施,为实际生产提供参考。
通过以上步骤的设计和实施,能够完成一套适用于冲压模具级进模的工艺和设备。
水泵密封圈压盖的级进模具设计
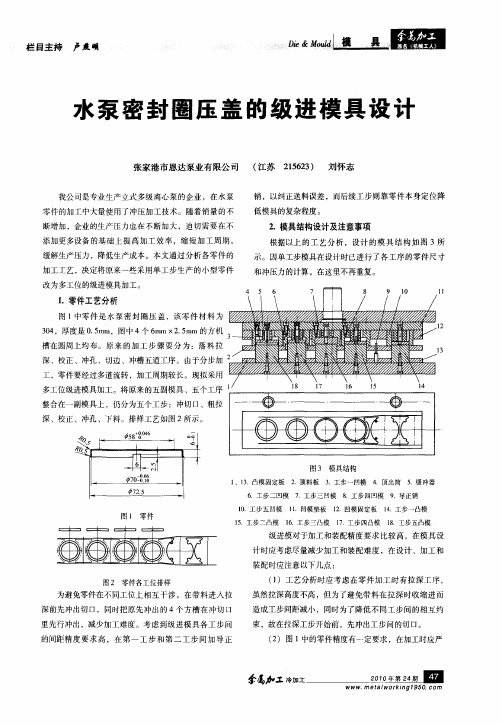
1.工步二凸模 5
1. 6 工步三凸模
1.工步四凸模 7
1. 8 工步五凸模
级进模对于加工 和装配精度要求 比较高 ,在模具设
1
.
、
、
计时应考虑尽量减少加工和装配难 度 ,在设计 、加工和 装配时应注意以下几点 :
图 2 零件各工位排样
( )工艺分析时应考 虑在零 件加工时 有拉深工序 , 1
l 2
槽在 圆周上均布 。原来 的加工 步 骤要 分为 :落 料拉 深 、校正 、冲孔 、切边 、冲槽五道工序 。由于分步加
工 ,零件要经过多道流转 ,加工周期较长 。现拟采用
1 3
多工位级进模 具加工 。将原来的五副模具 、五个 工序 整合在一副模具上 ,仍分为五个工步 :冲切 1 、粗拉 2 1 深、校正 、冲孔、下料。排样工 艺如图 2所示。
折 弯下 模
现零件的一边 与折弯机的面板干涉 ,经过分析 ,我们认
为该零件的长宽 比太大 ,分别达到 了 15 .4和 15 ,都 .2
线 。用该模 具能折 成的 u形 零
格按图样 施工 ,保证在 冲压 时零 件达到设计要求 。凸模
和凹模分别使用 固定板 定位 ,凸 、凹模 固定板 的定 位孑 L 在加工时 ,应用定位精 度高 的慢 走丝线切割或加工 中心
造成工步间距减小 ,同时为了降低 不同工步 问的相互 约
束 ,故在拉深工步开始前 , 冲出工步问的切口。 先
( ) 图 1中的零 件精度有一定要求 ,在加工时应严 2
磊 工冷 工 加
WWW. met wor n T 50 com a1 ki g 9 .
兰!堡 塑 _ 笙!
栏主 燕 目 持卢明
电机端盖冲压工艺与模具结构设计

电机端盖冲压工艺与模具结构设计摘要:文章通过对电机端盖冲压成型工艺的分析,确定该端盖的冲压工艺的方案。
并进行压力工位的设计,选择合适的拍样方案,画出了相应的拍样图,最后设计出模具的结构图。
通过端盖设计的整体思路,为模具设计者提供了一个设计的思路及方向。
关键词:端盖;排样;拉深;工艺引言:为了提高端盖加工的效率,减少劳动力,降低加工费用等问题,提出了一张电机端盖冲压工艺及其模具结构设计,对电机端盖进行了工艺的分析。
通过排样分析、拉深次数计算、翻边力计算及压力中心位置的确认来设计出整体模具的结构,并利用CAD对模具进行结构绘制。
一、电机端盖冲压工艺分析(一)毛坯直径的确定此零件的凸缘直径为44mm,相对凸缘直径为144/120=1.2,可取修边余量≤3.5mm。
即实际凸缘直径dF=df+2≤151mm。
按等面积法求得毛坯下料直径D为248mm。
(二)冲压工艺分析此零件属于复杂冲压件,主要包括拉伸和冲裁两类工艺,首先完成拉伸类工艺,待成型后再进行冲裁类工艺,从而完成整个零件的冲压加工。
根据工艺分解原则,此零件拉伸类工艺包括拉伸、反拉伸、整形等工序;冲裁类工艺包括下料、切边、冲孔、冲侧孔、冲侧舌等工序。
(三)冲裁工艺设计由冲压工艺分析可知,此零件冲裁类工艺主要包括凸缘轮廓切边,冲凸缘上孔为4.5mm、中心孔为16mm和顶部6处腰形孔及冲侧面出线孔、侧面腰形孔及4处均布的侧面止口。
凸缘上孔为4.5mm的孔口到凸缘边缘为144mm的距离a=1.75mm工位来完成,同时应位于整个模具的后4个工位。
因此可确定7工位到10工位的加工内容为:第7工位:切边。
切凸缘外形轮廓。
第8工位:冲孔。
冲凸缘平面上的为4.5mm、中心为16mm和顶部平面6个腰形孔。
第9工位:冲侧孔。
冲出线孔为14mm和5处侧向腰形孔。
第10工位:冲侧。
冲侧面4处均布的止口。
(四)拉伸工艺设计此零件拉伸类工艺比较复杂,包括拉伸、反拉伸、整形等工序。
轴盖件冲压工艺优化及其模具设计
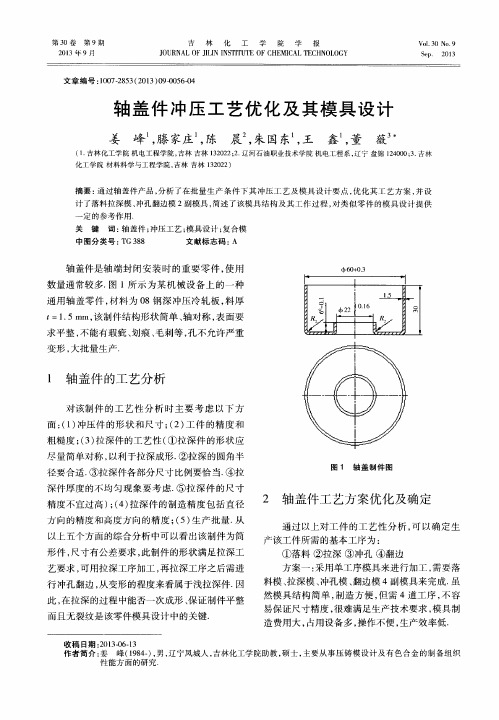
方案 二 : 采 用 先落料 , 再 拉深 、 冲孔 , 最 后 翻边
需 计 算 修 边 余 量.由《冲压 工 艺 学 》 表4 _ 4可 知, 修边 余 量 8取 2 m m. 则 D=d 十 2= 9 9 . 9 3+2
× 2=1 0 3 . 9 3 m m. 故 毛坯 直径 取 1 0 4 m m.
收 稿 日期 : 2 0 1 3 06 - — 1 3
①落 料 ②拉深 ③ 冲孔 ④ 翻边 方 案一 : 采 用单拉 深模 、 冲孔模 、 翻边 模 4副模具来 完成 . 虽 然模 具 结 构简 单 , 制 造方 便 , 但 需 4道 工 序 , 不 容 易保 证 尺寸精 度 , 很 难满 足生产技 术要 求 , 模 具制
复合模 , 由于该 轴 盖件 的结 构不 复杂 而且 轴对 称 ,
毛 坯 相 对 厚 度 : 古 × 1 0 0 = × 1 o 0 = 1 . 4 4 2 ,
该 圆筒 件 的拉 深 系数 : m= = =0 . 5 6 3 , 判
复合模 的成本 不高 , 制造 的难 度不 大 , 易保 证尺 寸 的精度 , 操 作方 便 , 需 用 2副 复合 模 , 与单 工 序 模 相 比, 减少 单工 序模 具数 量 , 提高 生产 效率 . 通过 上述 三个 工艺 方 案 在 产 品 质 量 、 生 产 效 率、 设 备 条件 、 模具 的制 造 和经 济效益 等方 面进 行
第3 0卷
第 9期
吉 林 化 工 学 院 学 报
J O U R NA L O F J I L I N I N S T I T U T E 0 F C H EM I C AL T E C HN O I OG Y
Vo 1 . 3 0 No . 9
级进模工艺和结构设计注意事项

600T级进模上台面能承受的重量不超过7吨
旧
新
改进措施:不影响模具强度及产品质量的情况下, 尽量减轻上模座及压料器的重量
级进模工艺和结构设计注意事项
四、级进模结构设计注意事项
1、上模重量超过上台面能承受的重量
B515-N617K65-66-BA工装厂开始设计上模的重量为7.8吨,而我司
600T级进模上台面能承受的重量不超过7吨
3-2、噪音处理-由于级进模生产节拍快,切边冲头较多,导致噪音较大 案例2:对于切边线在250mm左右,刀口做成波浪剪,减小冲裁力 的同时减小噪音的分贝
级进模工艺和结构设计注意事项
四、级进模结构设计注意事项
3-3、噪音处理3-由于级进模生产节拍快,切边冲头较多,导致噪音较大 案例3:当冲切刀块过多时,刀块需要做成高低差,以达到减小噪音的分贝
求废料排出是否顺畅
送料的稳定性
噪音的处理
零件成型性工艺是否可 行材料利用率
冲头结构的设计 产品滑出是否顺畅
5、对于异性冲头,我司目前一般采取做挂台结构实现防掉(因为当 螺纹与冲头连接松动后冲头掉在模具上,易出现安全事故)
更改后
级进模工艺和结构设计注意事项
四、级进模结构设计注意事项
6、产品划出不顺
CD391-F020C47冲压完成后,零件会卡在下模翻边凸模与切边刀块之间(如右图), 导致无法靠料带将产品推出
级进模工艺和结构设计注意事项
一、级进模的定义
2、级进冲压设备的构成
送料机:按照一定的 步距完成送料
模具与机床:完成各工序 冲压
级进模工艺和结构设计注意事项
二、级进模排样设计基本原则
1、展开制件
通常使用AutoForm/Dynaform/Formingsuite®进行产品展开
级进模结构设计
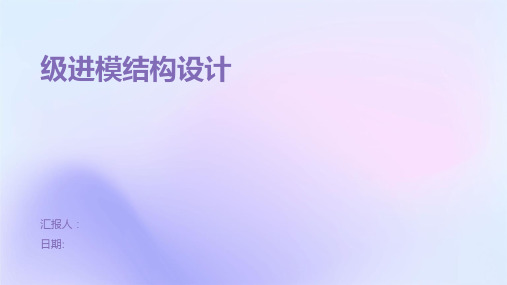
汽车零件的级进模设计要求高强度,能够保证零件的耐用 性。
精密零件的级进模设计
01
精确度高
精密零件的级进模设计要求精确度高,能够保证零件的精度和性能。
02
耐磨性好
精密零件的级进模设计要求耐磨性好,能够保证零件的使用寿命。
03
易于维修
精密零件的级进模设计要求易于维修,能够在出现故障时方便地进行维
修。
THANKS。
05
级进模的调试与优化
调试流程
初步调试
01
完成模具装配后,进行初步的调试,检查各机构动作是否正常
,确认没有明显的结构问题。
试片调试
02
根据试片调试结果,对模具进行微调,找出并修正可能存在的
机构问题,保证试片质量和稳定性。
批量生产调试
03
在正式批量生产前,进行大量的试片和生产调试,评估模具的
稳定性和生产效率,确认是否达到生产要求。
04
级进模的制造工艺
材料选择与处理
模具材料选择
根据模具的复杂程度、使用要求和寿 命等因素,选择合适的模具材料,如 高速钢、硬质合金、不锈钢等。
材料处理
对模具材料进行预处理,如锻造、退 火等,以消除材料内部的应力、提高 韧性等。
数控加工
数控编程
根据模具设计图纸,进行数控编程,确定加工路径、切削速 度、进给速度等参数。
02
级进模的组成结构
定位装置
01
02
03
定位原理
定位装置主要负责确保材 料在模具中的位置准确, 避免材料在冲压过程中移 动或滑动。
常见类型
包括固定定位销、活动定 位销、导正销、定位孔等 。
设计要点
根据产品要求和材料特性 选择合适的定位方式,同 时要考虑操作方便和更换 材料的灵活性。
级进模的要求和种类
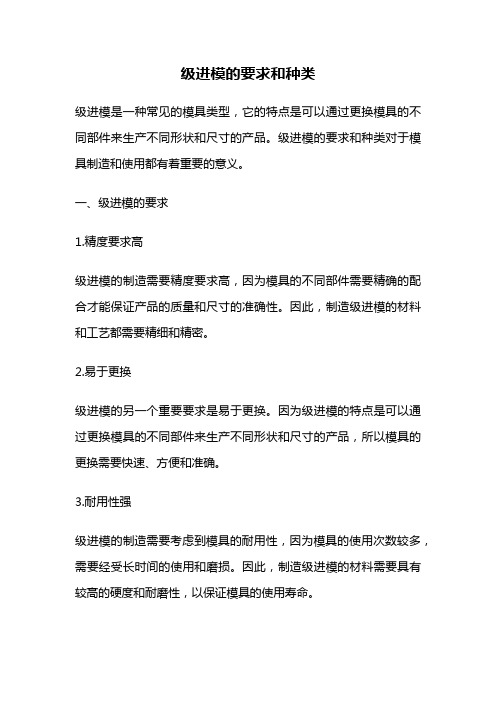
级进模的要求和种类级进模是一种常见的模具类型,它的特点是可以通过更换模具的不同部件来生产不同形状和尺寸的产品。
级进模的要求和种类对于模具制造和使用都有着重要的意义。
一、级进模的要求1.精度要求高级进模的制造需要精度要求高,因为模具的不同部件需要精确的配合才能保证产品的质量和尺寸的准确性。
因此,制造级进模的材料和工艺都需要精细和精密。
2.易于更换级进模的另一个重要要求是易于更换。
因为级进模的特点是可以通过更换模具的不同部件来生产不同形状和尺寸的产品,所以模具的更换需要快速、方便和准确。
3.耐用性强级进模的制造需要考虑到模具的耐用性,因为模具的使用次数较多,需要经受长时间的使用和磨损。
因此,制造级进模的材料需要具有较高的硬度和耐磨性,以保证模具的使用寿命。
4.安全性高级进模的制造需要考虑到模具的安全性,因为模具的使用需要遵守一定的安全规范,以保证操作人员的安全。
因此,制造级进模的设计需要考虑到模具的安全性,以避免意外事故的发生。
二、级进模的种类1.单向级进模单向级进模是一种常见的级进模类型,它的特点是只能在一个方向上进行级进。
单向级进模通常用于生产较小的产品,如电子元器件、塑料制品等。
2.双向级进模双向级进模是一种可以在两个方向上进行级进的模具类型。
双向级进模通常用于生产较大的产品,如汽车零部件、家电产品等。
3.多向级进模多向级进模是一种可以在多个方向上进行级进的模具类型。
多向级进模通常用于生产复杂的产品,如机械零部件、航空航天产品等。
4.旋转级进模旋转级进模是一种可以通过旋转模具来进行级进的模具类型。
旋转级进模通常用于生产圆形或弧形的产品,如轮胎、管道等。
5.滑动级进模滑动级进模是一种可以通过滑动模具来进行级进的模具类型。
滑动级进模通常用于生产长条形或异形的产品,如门窗、管道等。
级进模的要求和种类对于模具制造和使用都有着重要的意义。
制造级进模需要考虑到精度、易于更换、耐用性和安全性等因素,而级进模的种类则根据不同的产品形状和尺寸来选择。
级进模模具课程设计

级进模模具课程设计一、课程目标知识目标:1. 学生能理解级进模模具的基本概念,掌握其分类和特点;2. 学生能够掌握级进模模具在设计过程中的关键参数和计算方法;3. 学生能够了解级进模模具在工业生产中的应用及其对产品质量的影响。
技能目标:1. 学生能够运用所学知识,分析并解决级进模模具设计中的实际问题;2. 学生能够运用绘图软件完成级进模模具的初步设计;3. 学生能够通过实验或模拟操作,验证级进模模具设计的合理性。
情感态度价值观目标:1. 学生能够培养对模具设计与制造的热爱,增强对我国制造业的自豪感;2. 学生能够培养团队协作意识,提高沟通与交流能力;3. 学生能够树立正确的工程观念,认识到级进模模具在现代工业中的重要作用。
课程性质分析:本课程为专业技术课程,旨在让学生掌握级进模模具的基本知识、设计方法和应用技巧。
课程内容紧密结合实际生产,注重培养学生的动手能力和解决实际问题的能力。
学生特点分析:本年级学生具备一定的模具基础知识,具有较强的学习能力和实践操作能力。
学生对新技术和新方法充满兴趣,但可能对复杂计算和理论分析存在一定程度的抵触情绪。
教学要求:1. 注重理论与实践相结合,提高学生的实际操作能力;2. 采用案例教学,引导学生运用所学知识解决实际问题;3. 强化团队合作,培养学生的沟通与协作能力;4. 注重过程评价,关注学生的个性发展和能力提升。
二、教学内容1. 级进模模具概述- 模具分类与级进模模具特点- 级进模模具的应用领域2. 级进模模具设计原理- 设计流程与方法- 关键参数的计算与选择- 模具结构及其对产品质量的影响3. 级进模模具设计实践- 绘图软件操作与模具设计- 模具设计案例分析- 设计方案的优化与评价4. 级进模模具应用案例分析- 案例介绍与分析- 模具设计在产品生产中的作用- 案例启示与总结5. 级进模模具发展趋势与新技术- 国内外级进模模具发展现状- 新技术应用与发展趋势- 创新设计与绿色制造理念教学内容安排与进度:第1周:级进模模具概述第2-3周:级进模模具设计原理第4-5周:级进模模具设计实践第6周:级进模模具应用案例分析第7周:级进模模具发展趋势与新技术教材章节关联:《模具设计与制造》第3章:级进模模具设计《模具设计与制造》第4章:模具设计实践与应用《模具设计与制造》第5章:模具新技术与发展趋势教学内容确保科学性和系统性,结合课程目标,注重理论与实践相结合,提高学生的实际操作能力和创新意识。
级进模模具设计标准

级进模模具设计标准一、什么是级进模模具设计标准?级进模具是一种高效的生产方法,可以大大提高生产效率和产品质量。
在这种生产方式下,模具必须要有很强的可靠性和稳定性,以确保生产的连续性。
为此,制定了一系列关于级进模模具设计的标准,以保障模具的性能和质量。
级进模模具设计标准是以国际上先进的模具设计和加工技术为基础的标准,旨在规范模具的设计、加工、质量监控、使用和维护等方面的内容。
它主要包括以下几个方面:1.设计和制造要求2.加工精度要求3.使用和维护要求4.质量监控和检测要求二、为什么要制定级进模模具设计标准?1.提高产品质量通过采用科学的设计和制造标准,可以确保模具的精度和稳定性,从而提高产品的质量和可靠性。
2.提高生产效率采用高效的生产方法可以大大提高生产效率。
级进模具的制作需要非常精密的工艺和设备,而级进模模具设计标准可以统一设计和加工要求,使生产过程更加流畅。
3.节约成本通过标准化的设计和制造过程,可以减少误差和浪费,从而降低成本,增加利润。
4.提高工人安全性标准化的设计和制造过程可以确保模具的安全性和可靠性,从而减少事故的发生,保障工人的安全。
5.提高品牌声誉通过采用科学的设计和制造标准,可以提高产品质量和可靠性,从而提高品牌声誉和市场竞争力。
三、级进模模具设计标准的关键要素1.设计和制造要求设计和制造要求是保证模具性能和质量的基础。
设计要求包括模具的设计原则、结构要求、材料要求、尺寸公差要求和表面要求等;制造要求包括加工要求、装配要求和试验要求等。
2.加工精度要求加工精度是判断模具质量的重要标准。
加工精度要求包括尺寸精度要求、表面精度要求和几何精度要求等。
3.使用和维护要求使用和维护要求是保障模具性能和寿命的重要保障。
使用和维护要求包括贮存要求、使用要求、保养要求和检修要求等。
4.质量监控和检测要求质量监控和检测要求是保障模具质量的重要手段。
质量监控和检测要求包括生产过程中的监控和检测、产品出厂前的检测和使用过程中的检测等。
冲压模具课程设计---级进模设计说明

项目
公式
结果
卸料板工作行程外
h 1 = hx+ t + h2
4 mm
橡胶工作椭
Hi.= h i:+ h#
9 mm
橡胶自由局度用""
"顿=4乩
36 mm
橡胶的预压缩量七
H预=15%H自由
5.4 mm
每个橡胶承受的载荷4
F\ =弓/4
192.5N
橡胶的外径D
D=』(『+1.27( FJp)
FT=nktF=8x0. 06x19252
9241N
〃取8
Fz=F+F, + 5=19252+770+9241
29263N
弹性卸料
下出件
在确定工作零件刃口尺寸计算方法之前,
首先要考虑工作零件的加工方法及模具装配方
法。结合该模具的特点,工作零件的形状相对较
简单,适宜采用线切割机床分别加工落料凸模, 凹模,凸模固定板,卸料板,这种加工方法可以
Rf=9.885
0 -0.012
冲孔
4> 8
寺8严
山=(《心-XA)l
+41
dA=(Jr-Zmin/2) °
dT=8.18
0 -0.008
dA=8.205
+0.012 0
孔心距
40
40±0.62
Lx= L± A/8
L =40±0.15
5
(5)卸料橡胶的设计
卸料橡胶的设计计算见表三。选用的4快 橡胶板的厚度无比一致,不然会造成受力不均 匀,运动产生歪斜,影响模具的正常工作。
方案二:落料一冲孔复合冲压。采用复合模生产。
固定盖板级进模设计
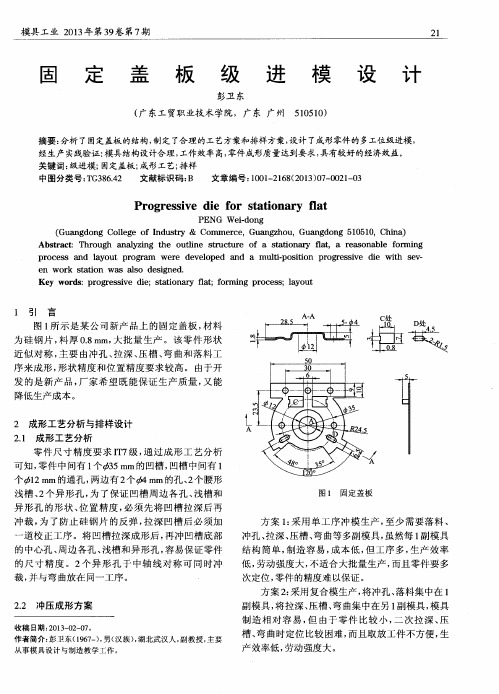
异 形 孔 的形 状 、 位置精度 , 必 须 先将 凹槽 拉 深 后 再 冲裁 , 为 了防 止 硅 钢 片 的反 弹 , 拉 深 凹槽 后 必 须加
一
方案 1 : 采用单工序冲模生产, 至 少 需 要 落料 、
冲孔、 拉深 、 压槽 、 弯 曲等 多副模 具 , 虽然 每 1 副 模具
Pr o g r e s s i v e di e f o r s t a t i o na r y la f t
PEN G We i — d on g
( G u a n g d o n g C o l l e g e o f I n d u s t r y& C o mme r c e , G u a n g z h o u , G u a n g d o n g 5 1 0 5 1 0 , C h i n a )
由于零件 为大 批量 生 产 , 决 定采 用整 卷 硅钢 片
作者 简 介 : 彭卫东( 1 9 6 7 一 ) , 男( 汉族) , 湖 北武 汉人 , 副 教授 , 主要 从 事模 具设 计 与制造 教 学工 作 。
槽、 弯 曲时定位 比较 困难, 而且取放工件不方便 , 生 产 效率 低 , 劳动 强度大 。
模具工业 2 0 1 3 年第 3 9 卷第7 期 方案 3 : 采用级进模生产, 只需 l 幅模具, 无需多 次 取放 工件 , 能 确保 冲制 出合 格 零 件 , 并达 到 高 效 率生 产 的 目的 , 但 模具 制造 复杂 , 成本 高 。
道校 正工 序 。将 凹槽 拉深 成 形 后 , 再 冲 凹槽 底 部
的 中, 5 , T L 、 周边 各 孔 、 浅 槽和 异 形 孔 , 容 易保 证 零件 的尺 寸 精 度 。2个 异 形 孔 于 中轴 线 对 称 可 同 时 冲
级进模结构设计
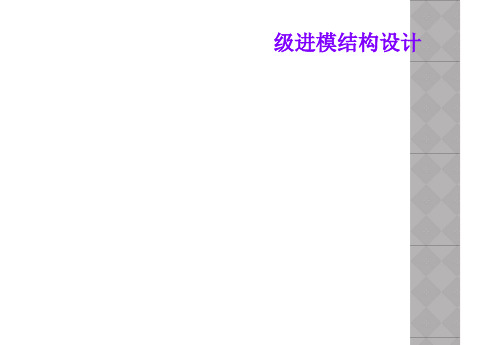
•
⑥定位针装在弹压板上,定位针露出弹压板下平面的有效长度为lmm左右。
(2)整体弹压板多工位级进模应用场合
•
①A型整体弹压板模具适应所有原料厚度,B型整体弹压板模具适应原材料厚度大于0.15mm;
原材料硬度超过100HV的情形。
•
②适应大批量生产。
•
③适应各类产品生产。
•
④产品精度高,毛刺小于0.03mm。
• ②模板内镶嵌零件与安装孔采用过渡或小过盈配合,过盈配合的双边负间隙为0.005mm。
• ③弯曲起伏尽量采取向下弯曲方式。
• ④下模板内的抬料弹顶装置要用装在上模板上的打杆打下,注意:
•
弹顶杆长度≥定位针有效长度≥冲裁凸模及成形凸模的长度;它们之间的长度级推荐采用上下模板各工位有合模要求的型孔及定位销孔同线切割。
,定位针直径略大,防止条料刚度不足、粘料而引起条料变形。 • ④为简化模具的设计与制造,允许部分成形凸模零件直接装于弹压板内。 • ⑤上模板型孔与凸模采用大间隙配合,双边间隙0.05~0.10mm。 • ⑥推荐采用弹压板与下模板中各工位有合模要求的型孔及导向导柱之导套孔同线切割。
4.5.4 分段弹压板多工位级进模
• 分段式独立弹压板级进模具结构适应更高冲压速度、提高模具的通用性、提高更换及维护模具的效 率、提高模具的可靠性及寿命、提高模具制造及产品制造精度,可以有效地降低高精度模具制造的 工艺难度。
(1)分段式弹压板级进模具结构特点
•
①使用高级精度标准模架,
•
②各个独立单元体相当于一副小型整体弹压板模具。
•
③各个独立单元体内主模板之间有四个高精度滚珠导向导柱。
•
④弹压板弹性元件直接压在四个导柱上,通过导柱传递弹力给弹压板
水管联接压盖模具毕业设计
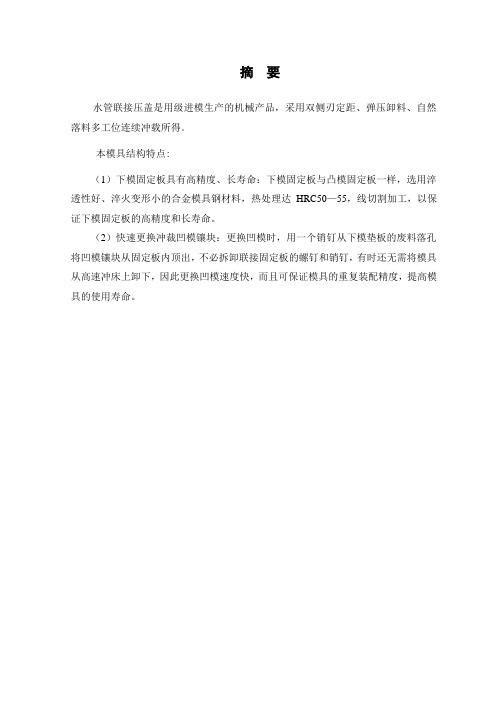
摘要水管联接压盖是用级进模生产的机械产品,采用双侧刃定距、弹压卸料、自然落料多工位连续冲载所得。
本模具结构特点:(1)下模固定板具有高精度、长寿命:下模固定板与凸模固定板一样,选用淬透性好、淬火变形小的合金模具钢材料,热处理达HRC50—55,线切割加工,以保证下模固定板的高精度和长寿命。
(2)快速更换冲裁凹模镶块:更换凹模时,用一个销钉从下模垫板的废料落孔将凹模镶块从固定板内顶出,不必拆卸联接固定板的螺钉和销钉,有时还无需将模具从高速冲床上卸下,因此更换凹模速度快,而且可保证模具的重复装配精度,提高模具的使用寿命。
AbstractWater pipe link is a mould production uses grade stock engineering ,adopt pairs of side edge make distance, suppress, unload material, natural blanking large Engine .This mould unique feature:(1) the mould retainer plate has a high precision:A long macrobiotic life: the lower mould retainer plate like as protruding model's retainer plate。
It's better to select quench sex kind quenching and out of shape light Mould steel products material of alloy to use。
Heat treatment reaches to HRC50-55, cut and processed the line, so as to ensure the high precision of the mould retainer plate and macrobiotic life.(2) Change the concave model of blanking and inlay one quickly: while changing the concave mould, fall with one pin from die mould waste material of backing board hole inlay carry out, produce from the retainer plate concave mould, needn't dismantle screw and pin。
级进模模具设计标准
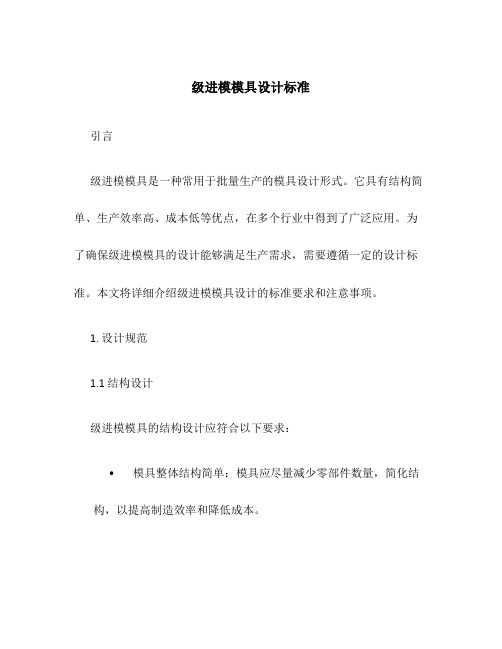
级进模模具设计标准引言级进模模具是一种常用于批量生产的模具设计形式。
它具有结构简单、生产效率高、成本低等优点,在多个行业中得到了广泛应用。
为了确保级进模模具的设计能够满足生产需求,需要遵循一定的设计标准。
本文将详细介绍级进模模具设计的标准要求和注意事项。
1. 设计规范1.1 结构设计级进模模具的结构设计应符合以下要求:•模具整体结构简单:模具应尽量减少零部件数量,简化结构,以提高制造效率和降低成本。
•模腔划分合理:根据产品的形状和尺寸要求,合理划分模腔,使之满足产品的加工需求。
•模腔间距适当:模腔之间应保持适当的间距,以便于模具的制造和使用。
•导向方式合理:模具的导向方式应选择合适的形式,以确保模腔的定位准确性和稳定性。
1.2 材料选择级进模模具的材料选择应满足以下要求:•耐磨性:模具材料应具有较高的耐磨性,以保证模具的使用寿命。
•硬度:模具材料应具有足够的硬度,以防止在使用过程中产生变形或磨损。
•导热性:模具材料应具有良好的导热性能,以便于热量的传导和分散。
•韧性:模具材料应具有一定的韧性,以防止在使用过程中出现断裂等问题。
1.3 管理要求级进模模具的设计还需要满足一定的管理要求:•标准化设计:级进模模具的设计应尽量遵循标准化设计,以便于制造流程的统一和生产效率的提高。
•文档管理:对级进模模具的设计文件应进行有效的管理,确保设计变更的及时更新和追踪。
•维护保养:对模具的维护保养工作应进行规范化管理,定期检查和维护模具,延长模具的使用寿命。
2. 设计流程级进模模具的设计流程可以分为以下几个步骤:2.1 产品分析在设计级进模模具之前,需要进行产品的详细分析。
分析产品的形状、尺寸、材料等特点,确定模具的基本要求和设计方案。
2.2 模腔划分根据产品的特点和生产需求,设计师需要合理划分模腔。
在划分过程中,需要考虑产品的形状、尺寸、生产效率等因素,确保模腔的布局合理。
2.3 结构设计在模腔划分完成后,设计师需要进行模具的结构设计。
- 1、下载文档前请自行甄别文档内容的完整性,平台不提供额外的编辑、内容补充、找答案等附加服务。
- 2、"仅部分预览"的文档,不可在线预览部分如存在完整性等问题,可反馈申请退款(可完整预览的文档不适用该条件!)。
- 3、如文档侵犯您的权益,请联系客服反馈,我们会尽快为您处理(人工客服工作时间:9:00-18:30)。
摘要本次设计的主要内容是压盖的排样方案及模具设计,原排样方案为多工位级进模的纵向单排,因为纵向单排排样时材料会造成大量的浪费,为了增大材料的利用率,本文主要设计了倾斜双排排样方案和倾斜三排排样方案并及纵向单排排样方案的比较,比较得出,纵向单排排列模具最简单,材料轻易加工,但其材料利用率为51%,快要一半的材料华侈掉了,很是的不合理,材料容易加工,但其材料利用率为51%,将近一半的材料浪费掉了,非常的不合理。
纵向双排排样模具结构虽然复杂,但其材料利用率达到了76%,材料得到了比较充分的利用,而且制件速度提高了纵向单排排列的二倍,非常适用该厂的现有条件。
倾斜三排排列的材料利用率约为78%,其模具结构复杂,模具体积庞大,虽然其利用率是三种排样方案中最大的,但该厂其对冲制设备的要求不能达到标准要求。
通过以上三种排样方案的比较,从模具的复杂程度,材料的利用率及原企业的设备条件状况等多方面考虑,选用倾斜双排排列的方案最为合理,不仅符合该厂现有的设备要求,而且材料利用率大大提高,生产成本降低了。
关键字:材料利用率;多工位级进模;倾斜排列AbstractThe main content of this design is the layout plan of the gland, the original layout scheme for multiple work position progressive die of vertical single row, due to the vertical single volleys of sample material will cause a lot of waste, in order to improve the utilization rate of materials, this paper designed the tilt double lining sample solutions and three volleys of sample tilt and compared with the vertical single volleys of sample solution, is concluded, the simplest, vertical in-line arrangement mould materials to processing, but the material utilization rate is 51%, nearly half of the waste material, very unreasonable. Vertical double lining sample mould structure complex, but its material utilization rate reached 76%, materials got more fully utilized, and raised longitudinal stamping speed single permutation twice, very applicable to the plant's existing conditions. Tilting three arrange the material utilization of about 78%, its mold structure is complex, the mould bulky, although its utilization is the biggest of the three kinds of layout scheme, but the plant its claim to hedge system equipment can not meet the standard requirements. Through the above three kinds of layout scheme comparison, from the complexity of the mould, the utilization rate of material and the conditions of equipment and other aspects to consider, select tilt double row arrangement scheme is the most reasonable, not only can meet the demands of the plant of the existing equipment, and greatly improve the material utilization ratio, reduce the production cost.Key words: material utilization; Multi-station progressive die. Tilting arrangement目录摘要1Abstract2目录31 绪论02 工艺性分析23工艺设计43.1纵排单排排列设计43.1.1工位的确定43.1.2搭边43.1.3步距及条料宽度53.1.4材料利用率的计算53.2 倾斜双排排样设计53.2.1倾斜排样角度的确定53.2.2导正孔83.2.3 工位的确定93.2.4 材料利用率的计算93.3倾斜三排排样设计103.3.1 排样角度的确定103.3.2 搭边的确定103.3.3 条料宽度和步距的确定103.3.4 导正孔103.3.5 工位的确定103.3.6材料利用率的计算113.4 最优方案的选择113.5 冲压力及压力中心的计算及压力机的选择123.5.1 冲压件受力计算123.5.2压力中心的计算133.6压力机的选择144模具设计144.1 冲裁凹凸模刃口尺寸154.2 凹凸模刃口尺寸的计算方法154.3 拉深模174.3.1坯料尺寸的确定174.3.2 凸凹模结构的确定184.4 压印凸模尺寸194.5 切口模的设计194.6 凹模尺寸的计算204.7其他模具零部件规格204.8凸模设计214.8.1凸模强度的校核214.8.2 凸模的总长度计算214.9 模架模座模柄的确定234.10 其他零件的规格244.10.1浮升销244.10.2导正销244.10.3 卸料螺钉和卸料弹簧254.10.4压边装置的配置254.10.5 凹模固定及定位零件264.11压力机的校核27总结29致谢30参考文献311 绪论多工位级进模是在同一套模具里可以连续完成冲孔,拉深,落料等冲压工序的一套模具,也就是说,被加工材料通过自动送料进入级进模,然后一个工序冲压一次,可以制成一个复杂的制件,只要在一个模具里就可以冲压制成。
这就是级进模的最大优点。
级进模加工速度快,加工过程容易,质量好,提高了工厂的经济效益,一般适于大批量生产的零件,是一副效率高,精密度高,寿命高的高效模具随着科技的发展,模具已经成为各个国家必不可少的工具,我国的大量精密模具都是从国外进口的,可以看出模具的重要性。
本次设计是完成压盖的排样设计,及制作压盖的级进模具设计,设计的重点有有级进模的排样方法,排样方法有多种,如单排排列,双排排列,三排排列,直排排列,斜排排列等方法,一个工件排列方法的不同,可以影响一套模具的生产效益,毕竟生产总成本中,材料的费用占相当一部分。
所以,本次设计中主要针对材料利用率进行排样,主要方案有多排,斜排等,多排主要通过材料利用率及工厂现有的设备进行分析,选出最合适的排数;斜排主要研究制件排列的角度,角度的不同,可以影响材料利用率的大小,所以,设计出最合理的角度至关重要,本文中主要通过比较得出最适合的角度。
最后进行模具设计,一套完整的级进模具不仅要考虑它的制件精度,还要考虑它的使用年限。
设计中的关键技术问题是,各个构件之间的相互配合,各个构件之间的最适合的配合尺寸,配合方式,使各个构件不发生碰撞,方便灵活,操作平稳。
2 工艺性分析该压盖零件为一冲压件,如图1冲压件工程图所示,其结构比较简单,料厚0.7mm ,外形为菱形的椭圆。
中间经浅拉深成型,压印,及冲圆形孔,圆孔直径为6.4mm,同心度为ϕ0.5mm,两端各有一个冲腰圆孔,孔心距52.4±0.5mm。
实物图如图2-2,材料为10号碳素结构钢,使用于一般结构和工程金属构件,塑性好,有一定的强度,冲裁性较好,适用于普通冲裁加工。
生产批量为大批量生产。
由上可知,主要的冲压工艺有:冲导正孔,冲裁废料,压印,浅拉深成形,冲孔及落料。
一般落料公差等级最后低于IT10级,冲压件公差等级最后低于IT9级图2-1 冲压件工程图制造一个工件,其工序包括拉深,冲压,落料,压印,切边等工序,首先要确定的是其排样图,排样图有很多种,根据材料的利用率,模具寿命等多方面的的因素,选出最合理的排样图,一般排样图根据以下条件确定:a 合理确定工位数b材料利用率。
c 保证送料步距精度。
d 使模具简单,寿命高。
e 保证冲裁件质量。
图2-2冲压件实物图根据材料的利用,排样可分为有废料排样法,少废料排样法,无废料排样法。
其中,无废料排样法可以提供材料的利用率,但用这种方法制成的零件精度不好,零件大多不合格,本次设计的零件为小型零件,为了保证其精度,可以选用有废料排样法。
3工艺设计3.1纵排单排排列设计3.1.1工位的确定确定工位的方法有好多,冲压件,拉深件等其第一工位一般是冲导正孔,然后是冲孔,之后拉深如图3-1所示,共分五个工位完成。
图3-1 纵排单排排列第一工位:冲导正孔。
第二工位:冲裁废料。
第三工位:压印。
第四工位:浅拉深成形。
第五工位:冲孔及落料。
3.1.2搭边工件及工件之间及工件及条料侧边之间的余料叫做搭边。
搭边的目的是为了冲出精度更高的制件,保证冲出合格件。
根据送料步距及条料宽度比a=S/W确定搭边值。
a=38.6+(3-2)/60.5+(2-4) <1.5考虑到冲头的强度,每个工件之间的搭边值b=4.2mm;a=2.22mm。
3.1.3步距及条料宽度(1)步距指条料在模具上每次送进的距离。
步距S=A+M即S=A+bS=38.6+4.2=42.8mm(2)条料宽度由于保证导料板的顺利送料,使条料宽度的公差带下偏差为(-e)。
条料宽度B=(D+2a+e)-0eB=(60.5+2*2.22+0.5)=(65.44)-00.53.1.4材料利用率的计算材料的成本大概占总成本的百分之六十几,所以,材料的合理利用起关键性作用。