氧气转炉“留渣+双渣”炼钢工艺技术131210王新华
转炉双渣法炼钢少渣冶炼.

基本反映了该炼钢方法的技术操作特点。从已发 表的报道来看,值得注意的有以下2点。
(1)转炉容量:80t~300t,表明少渣冶炼生产
的规模大
(2)讨论内容:操作技术;经济效益;前期渣
特点,形成了完整的工艺方法
1、转炉双渣法少渣冶炼现状
已经发表文章的单位(不完全统计)及生产转炉 的容量:
双渣法之所以能够在吹炼前期造渣倒掉,吹炼中
期再造渣,减少了总渣量也能够达到单渣法吹炼 大渣量的那种脱磷效果,原因就在于利用了脱磷 与温度的关系和基本原理。
2、双渣法少渣冶炼原理
由(2)式可知,温度对脱磷反应的影响非常显著, 当温度由1680℃降低至1350℃时,脱磷反应平衡
常数可大幅度增加6个数量级。少渣冶炼的基本
③传统工艺出钢后会有钢水留在炉内,一部分会
替部分石灰和镁球。 钢研总院研究对300t转炉的前期渣打水后返回使 用,每炉次加入3~6t返回渣,每炉可节约0.7~1t 石灰。
鞍钢鲅鱼圈研究含磷钢冶炼,不加石灰而只加轻
烧白云石。
2、双渣法少渣冶炼原理
双渣法过去主要用来冶炼高硅、高磷铁水,或者
在铁水硅、磷不高时要冶炼低磷钢或超低磷钢。
用的相关情况,在大分、八幡、室兰、君
津等钢厂采用,产钢量占新日铁总产钢量
55%左右,转炉炼钢石灰消 耗 减少了40%
以上。
1、转炉双渣法少渣冶炼现状
MUCR工艺将转炉冶炼分为2个阶段,在
第1阶段主要进行脱硅、脱磷,结束后倒 出部分炉渣,然后进行第2阶段吹炼,吹 炼结束后出钢但将炉渣保持在炉内,下一 炉在炉内留渣情况下装入废钢、铁水,然 后进行第1和第2阶段吹炼,并以此循环 往复。
转炉炼钢中留渣技术的原理及应用

2.3留渣安锂 近年来,随着我国转炉炼钢技术不断发展和完
善,由于顶底复合吹炼、溅渣护炉等一系列的工艺出 现之后,能有效地解决喷溅问题。对于渣循环来说, 它能够带来良好的经济效益,从单扎法中衍生出各 种各样的操作工艺,自从留渣技术应用之初,要考虑 到它自身的安全,采取留渣操作之后进入废钢以后,
间,这对前期脱离有着积极的推动作用,经过反复的 实践研究,其中影响脱离效率撮主要的因素就在于 物质的酸碱度和炉渣的含量,避免炉渣中氧化铁过 多,产生的喷溅,必须要确保它的游离氧含量大于 900x10电科学的调整留渣含量叫 32稳定留渣量
对于绝大部分的炼钢厂来说,冶炼效果和留渣 量的稳定性,两者密切相关。如果炉渣发泡过稀,此 时可以使用氮气进行溅渣 ,能有效的控制问题的发 生,进而实现渣量稳定控制。我国首先使用的是
钢工艺实践[J].新疆钢铁,2018(2):26-30.
(编辑:苗运平)
(下转第116页)
・116・
.山酉肖金 E—mail:sxyjbjb@
第44卷
问题根源,实施改进措施。
3结论 1) 棒材劈头堆钢主要由钢坯质量问题引起(偏
析、夹杂)。
2) 钢坯内裂属于铸造缺陷,但与冶炼时成分相关。 3) 冶炼时应避开包晶点,可以有效避免偏析、 内裂。
4) 提高钢中镒硫比例可防治方坯内裂。 5) 轧制过程中,粗轧岗位密切盯钢,尽量及时处 理钢质问题。
6 )年修时,对轧机的轧制线对正,跟换更耐磨的
3、5架导卫衬板。 7)适当调大2、4机架导卫扭转角。
参考文献
[1 ]王凯.降低高线粗轧机轧辐轴承消耗的措施[J] •轧钢,2006,23
氧气转炉“留渣+双渣”炼钢工艺技术分析

渣进 行 固化 处理 ,在 完成 固化 工作 之后 , 即 可将 铁水 与废 钢装 入其 中 ,开展 脱磷 吹 炼 ,这 一步 骤完 成后 即可 开展 倒渣 工作 , 并 步入 到脱 碳环 节 中 ,结 束 出钢与 留渣 工 作 ,循 环往 复 。该种 工艺 利用 了热 力学 原 理 ,在 炼终 点 ,温度 非 常高 ,此 时钢水 中 基 本上 没有 磷 ,不会 进行 脱磷 反应 ,在炉 中 留出一 定量 的终 渣 。在 进行 下一 吹炼 工 作 时 ,温度 也是 较低 的 ,但是 钢水 中 已经 有 大量 的磷 ,此 时炉 渣有 开始 能够 脱磷 , 在 吹炼 工作 的进 行下 ,在 温度 升高 之后 , 即 可在脱 磷 不利 的状 态下 将炉 渣倒 出 ,再 进行 脱碳 吹炼 ,这一 工艺 将上 炉 留渣原 理 充分 利 用起来 ,能够 减少 白云石和 石灰 的
中 ,一般 不会 由于倒 渣损 失钢 铁料 量 ,该 之 后 ,必 须要及 时将 炉 渣倒 出 ,而采 用快
种工 艺 的优势是 非常 显著 的。 速 足量倒 渣工 艺 即可完成 这一 目的。 2 “ 留渣 + 双渣 ”炼 钢 工艺 开 发 与 使 2 - 3 S G R S 3 2 艺磷 控制 方式 。与一 般 的
转炉留渣双渣操作生产实践

转炉留渣双渣操作生产实践吕凯辉(福建三安钢铁有限公司炼钢厂,福建泉州362411)摘要:介绍了福建三安炼钢厂的转炉留渣双渣操作,以及留渣操作中安全问题的解决措施,分析了应用留渣双渣操作工艺的石灰消耗、钢铁料耗、转炉炉龄、氧耗、冶炼周期、脱磷等效果。
通过优化顶底复吹转炉留渣双渣工艺制度,提高转炉前期脱磷效果,在无铁水预处理的设备条件下可以冶炼高铬铁水,满足了对钢的洁净度要求。
关键词:转炉;留渣;双渣;操作;实践0引言留渣双渣操作是将转炉上炉部分或全部的高碱度、高氧化亚铁的渣留在炉中,然后在吹炼第一期结束时倒出来,重新造渣的操作模式[1]。
该工艺具有高的碱度和比较高的∑(FeO)含量,对铁水具有一定的去磷和去硫能力,且本身还含有大量的物理热,将该种炉渣部分地甚至全部留在炉内可以显著加速下一炉初期渣的成渣过程,提高吹炼前期去磷率、节省石灰用量和提高炉子的热效率。
但在留渣双渣操作中,必须特别注意防止兑铁水时产生严重喷溅[2]。
福建三安炼钢厂研究了留渣操作喷溅和预防的机理,摸索出了1套留渣操作方法,取得了显著的经济效益。
1福建三钢的留渣双渣操作三安炼钢厂结合本厂的实际情况(高炉使用“印尼高铬矿”时,铁水铬含量高,由于铬能显著降低磷的活度,铁水中的铬氧化生成大量Cr2O3,使脱磷渣“硬化”,不利于脱磷反应的进行,转炉渣脱磷能力下降),实行的生产工艺为:“留渣双渣法”加“高拉后吹”的生产冶炼工艺,留渣双渣法工艺对于高磷高硅高铬等铁水的冶炼比较具有实用性,其工艺流程为:溅渣留渣→进废钢铁水→下枪冶炼→起泡沫渣时提枪倒渣下枪→脱碳升温出钢。
该工艺和一般工艺的差异在于倒渣操作在吹炼中途进行,其原理是:在温度为1320~1420℃时,转炉冶炼脱磷脱硅效果较明显;而温度>1550℃时,转炉渣对于脱磷是反效果的,也即会回磷。
所以在脱硅、脱磷操作基本完成后进行倒渣操作,能有效脱磷,不影响冶炼周期,可以降低转炉石灰消耗和钢铁料消耗。
首秦100t氧气转炉“留渣双渣”炼钢工艺实践
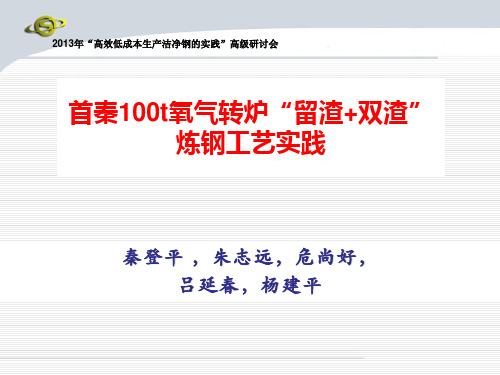
SGRS工艺应用效果
➢渣量的确定— 理论计算渣量
使用普通活性石灰,铁水Si含量在0.50%左右, SGRS工艺渣量70-80kg/t,普通工艺渣量100-120kg/t。 SGRS工艺比普通工艺降低35kg/t,降低比例31.8%。
➢渣量的确定—铁水称量实测渣量
使用普通石灰,铁水Si含量在0.50%左右,SGRS工 艺渣量75kg/t,普通工艺渣量108kg/t。SGRS工艺比普通 工艺降低33kg/t,降低比例31.4%。 渣量的降低和Tfe含量的变化合计钢铁料消耗降低8.25 kg/t钢。
脱磷期回收工艺:
CO浓度>30%,O2<1.5%; 下枪吹炼≥2分钟; 达标时间≤3.5分钟; 氧枪下枪吹炼(氧枪在开氧点以下) 罩裙低位;
SGRS转炉煤气的回收技术应用
脱碳期回收工艺技术优化 脱碳期吹炼前期转炉煤气发生特点: •前期CO浓度上升很快,且波动小 •O2浓度下降速率较快,稳定 前期达标即回收,CO>30%,O2<1.5%,无时间和延时限制; 回收末期控制条件与常规冶炼工艺相同;
脱磷期结束倒渣控制研究
脱磷期结束倒渣量,t
6
5
4
3
2
1
0
0
5
10
15
脱磷期结束倒渣时间,min
倒渣时间增加到一定程度后,倒渣量增加不再显著。
脱磷期结束倒渣控制研究
25.0
出钢后倒渣
20.0
脱磷倒渣
15.0
12.7
倒渣量,t
10.0
5.0 4.3 6.5 7.1 7.0 7.3 6.8 7.2
0.0 第一炉 第二炉 第三炉 第四炉 第五炉 第六炉 第七炉 SGRS循环周期
氧气转炉“留渣+ 双渣” 炼钢工艺技术研究
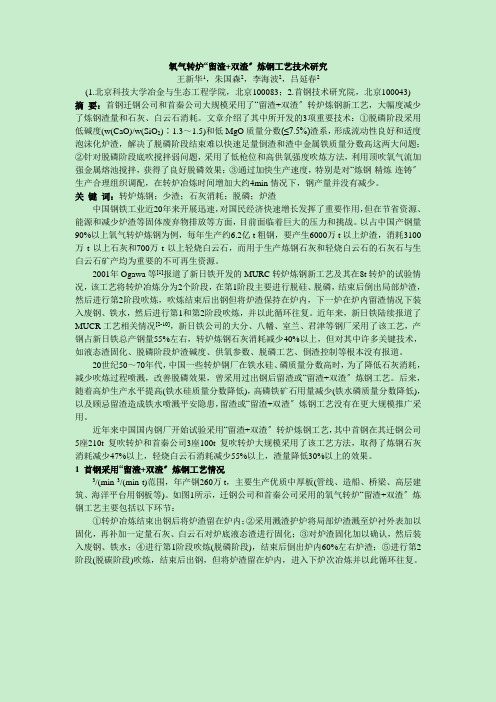
氧气转炉“留渣+双渣〞炼钢工艺技术研究王新华1,朱国森2,李海波2,吕延春2(1.北京科技大学冶金与生态工程学院,北京100083;2.首钢技术研究院,北京100043)摘要:首钢迁钢公司和首秦公司大规模采用了“留渣+双渣〞转炉炼钢新工艺,大幅度减少了炼钢渣量和石灰、白云石消耗。
文章介绍了其中所开发的3项重要技术:①脱磷阶段采用低碱度(w(CaO)/w(SiO2)∶1.3~1.5)和低MgO质量分数(≤7.5%)渣系,形成流动性良好和适度泡沫化炉渣,解决了脱磷阶段结束难以快速足量倒渣和渣中金属铁质量分数高这两大问题;②针对脱磷阶段底吹搅拌弱问题,采用了低枪位和高供氧强度吹炼方法,利用顶吹氧气流加强金属熔池搅拌,获得了良好脱磷效果;③通过加快生产速度,特别是对“炼钢-精炼-连铸〞生产合理组织调配,在转炉冶炼时间增加大约4min情况下,钢产量并没有减少。
关键词:转炉炼钢;少渣;石灰消耗;脱磷;炉渣中国钢铁工业近20年来开展迅速,对国民经济快速增长发挥了重要作用,但在节省资源、能源和减少炉渣等固体废弃物排放等方面,目前面临着巨大的压力和挑战。
以占中国产钢量90%以上氧气转炉炼钢为例,每年生产约6.2亿t粗钢,要产生6000万t以上炉渣,消耗3100万t以上石灰和700万t以上轻烧白云石,而用于生产炼钢石灰和轻烧白云石的石灰石与生白云石矿产均为重要的不可再生资源。
2001年Ogawa等[1]报道了新日铁开发的MURC转炉炼钢新工艺及其在8t转炉的试验情况,该工艺将转炉冶炼分为2个阶段,在第1阶段主要进行脱硅、脱磷,结束后倒出局部炉渣,然后进行第2阶段吹炼,吹炼结束后出钢但将炉渣保持在炉内,下一炉在炉内留渣情况下装入废钢、铁水,然后进行第1和第2阶段吹炼,并以此循环往复。
近年来,新日铁陆续报道了MUCR工艺相关情况[2-10],新日铁公司的大分、八幡、室兰、君津等钢厂采用了该工艺,产钢占新日铁总产钢量55%左右,转炉炼钢石灰消耗减少40%以上,但对其中许多关键技术,如液态渣固化、脱磷阶段炉渣碱度、供氧参数、脱磷工艺、倒渣控制等根本没有报道。
转炉双渣法炼钢少渣冶炼

1、转炉双渣法少渣冶炼现状
对于转炉吹炼前期渣的操作控制也进行了研究,
北京科技大学的王新华等在首钢迁安210t转炉上 试验,脱磷阶段采用低碱度(R=1.3~1.5)和低
MgO质量分数(≤7.5%)的渣系,能够形成流动
性良好和适度泡沫化的炉渣,解决了脱磷阶段结
束难以快速足量倒渣和渣中金属铁含量高这两大
3、少渣冶炼的关键技术
图7和图8分别为氧枪枪位和炉渣FeO含量
对脱磷阶段结束[P]含量的影响,可以看到, 采用较低枪位和高强度供氧,由于熔池搅 拌显著加强,尽管炉渣FeO含量降低至 9.5%附近,脱磷效率非但没有降低,反而 有较大幅度的提高。
3、少渣冶炼的关键技术
采用上述高效脱磷工艺,在铁水磷含量为
溅,引发重大安全事故。迁钢公司曾采用加入多
量石灰、白云石或废钢直接冷却对液态炉渣进行 固化的方法,但发现存在以下问题: ①如石灰、白云石加入量多,造成脱磷阶段炉渣 碱度和MgO含量过高,导致倒渣困难;
3、少渣冶炼的关键技术
②如采用废钢对液态渣进行冷却固化,由于废钢
尺寸不均衡,常发生炉内废钢“搭棚”情况,炉 底液态渣不能被充分固化,存在安全隐患。通过
稳定运行。
3、少渣冶炼的关键技术
为了使炉渣具有良好的流动性,还须对MgO含量
进行严格控制。后面的图为210t转炉脱磷阶段结
束时倒渣量与渣中MgO含量的关系,当将MgO含
量控制在7.5%以下时,倒渣量可在8t以上,能够
满足少渣冶炼工艺稳定运行的要求,为此规定对 脱磷阶段炉渣MgO含量按低于7.5%控制。这一 MgO含量控制目标低于常规工艺初期渣的MgO含 量控制目标值,采用后并未发现对炉龄有不利影
③传统工艺出钢后会有钢水留在炉内,一部分会
8-转炉“留渣-双渣”少渣炼钢工艺实践
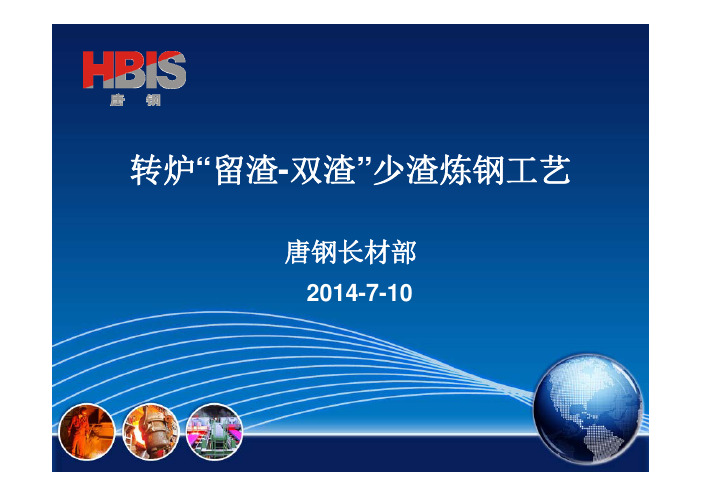
“留渣-双渣”工艺示意图
3.转炉脱磷影响因素
3.脱磷的基本原理
2[P]+5(FeO)+4(CaO)=4CaO·P2O5+5[Fe]
a 4CaO P2 O 5 a a
2 p 5 F eO
Kp
a
4 C aO
% 4CaO P2 O 5 4CaO P O 4 5 4 % P 2 f P2 % F e O 5 F e O % CaO C aO
演变:首钢公司从2011年开始,在首钢首秦和迁钢分别连续试验单
转炉“留渣-双渣”操作,取得较好的效果,目前首钢集团首钢长治, 首钢水钢均推广应用“留渣-双渣”少渣炼钢操作工艺,工艺相对成熟 。
1. 大幅度减少炼钢石灰、白云石等渣料消耗和炼钢渣量; 2. 可以利用出钢后炉渣的物理热,预热废钢; 3. 炼钢终渣含Tfe:15~25%,渣量减少可以降低钢铁料消耗; 4. 双渣倒渣的炉渣主要为脱磷阶段低碱度渣,自由CaO含量低, 可以简化炉渣处理; 5. 常规转炉出钢后留在炉内钢水随炉渣倒出,采用“留渣-少渣”工 艺终点少倒渣、出钢后不倒渣,可以提高钢水收得率。
FeO%
H11Mn2SiA
3A14306-1 3A14306-2 3B14615-1 3B14615-2 3C14935-1 3C14935-2 3A14301-1 3A14301-2 3B14603-1 3B14603-2 3B14612-1 3B14612-1
1 冶炼周期影响
类别 加料 脱磷期 双渣 脱碳期 终点 加废钢 兑铁时间 前期吹炼时间 氮气刹渣 倒渣时间 中后期吹炼 拉碳、补吹时间 等待终点成分 出钢时间 溅渣时间 总冶炼周期 留渣-双渣 1.7 2.4 4.5 2.1 3 8.8 2 1 2.5 2 30 单渣法 1.7 2.2 4.5 / / 8.7 2 1 2.5 2.5 25.1
转炉“留渣+双渣”少渣炼钢工艺实践

转炉“留渣+双渣”少渣炼钢工艺实践李伟东;杨明;何海龙;刘鹏飞;乔冠男【摘要】The key technologies on steelmaking based on the slag reserving and duplex slag process in converter in General Steelmaking Plant of Angang Steel Co., Ltd. are introduced, in-cluding slag reserving and slag solidifying technology, slag fluidity controlling and high efficient dephosphorization technology, fast slagging sufficiently and deslagging technology from molten iron, control technology for slag getting dry and content of FeO in final slag and fast operation technolo-gy based on slag reserving and duplex slag process. After these technologies are used the cost is reduced by 12.19 yuan RMB per ton steel.%介绍了鞍钢股份有限公司炼钢总厂转炉“留渣+双渣”工艺的关键技术,包括留渣及炉渣固化技术、炉渣流动性控制及高效脱磷技术、快速足量放渣及渣铁分离技术、炉渣返干控制及终渣FeO控制技术以及“留渣+双渣”快速生产技术,采用这些技术后,吨钢成本降低12.19元。
【期刊名称】《鞍钢技术》【年(卷),期】2015(000)005【总页数】5页(P41-45)【关键词】转炉;少渣;留渣;双渣;脱磷【作者】李伟东;杨明;何海龙;刘鹏飞;乔冠男【作者单位】鞍钢股份有限公司炼钢总厂,辽宁鞍山114021;鞍钢股份有限公司科技质量部,辽宁鞍山114021;鞍钢股份有限公司炼钢总厂,辽宁鞍山114021;鞍钢股份有限公司炼钢总厂,辽宁鞍山114021;鞍钢股份有限公司炼钢总厂,辽宁鞍山114021【正文语种】中文【中图分类】TF777少渣炼钢是指转炉冶炼总渣量极少化的一种炼钢工艺。
转炉留渣双渣工艺前期脱磷热力学及实践
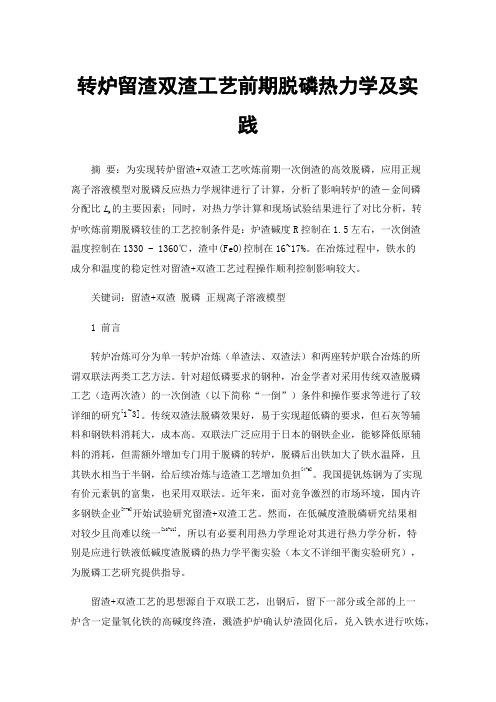
转炉留渣双渣工艺前期脱磷热力学及实践摘要:为实现转炉留渣+双渣工艺吹炼前期一次倒渣的高效脱磷,应用正规离子溶液模型对脱磷反应热力学规律进行了计算,分析了影响转炉的渣-金间磷的主要因素;同时,对热力学计算和现场试验结果进行了对比分析,转分配比LP炉吹炼前期脱磷较佳的工艺控制条件是:炉渣碱度R控制在1.5左右,一次倒渣温度控制在1330 - 1360℃,渣中(FeO)控制在16~17%。
在冶炼过程中,铁水的成分和温度的稳定性对留渣+双渣工艺过程操作顺利控制影响较大。
关键词:留渣+双渣脱磷正规离子溶液模型1 前言转炉冶炼可分为单一转炉冶炼(单渣法、双渣法)和两座转炉联合冶炼的所谓双联法两类工艺方法。
针对超低磷要求的钢种,冶金学者对采用传统双渣脱磷工艺(造两次渣)的一次倒渣(以下简称“一倒”)条件和操作要求等进行了较详细的研究[1~3]。
传统双渣法脱磷效果好,易于实现超低磷的要求,但石灰等辅料和钢铁料消耗大,成本高。
双联法广泛应用于日本的钢铁企业,能够降低原辅料的消耗,但需额外增加专门用于脱磷的转炉,脱磷后出铁加大了铁水温降,且其铁水相当于半钢,给后续冶炼与造渣工艺增加负担[4~6]。
我国提钒炼钢为了实现有价元素钒的富集,也采用双联法。
近年来,面对竞争激烈的市场环境,国内许多钢铁企业[7-9]开始试验研究留渣+双渣工艺。
然而,在低碱度渣脱磷研究结果相对较少且尚难以统一[10~11],所以有必要利用热力学理论对其进行热力学分析,特别是应进行铁液低碱度渣脱磷的热力学平衡实验(本文不详细平衡实验研究),为脱磷工艺研究提供指导。
留渣+双渣工艺的思想源自于双联工艺,出钢后,留下一部分或全部的上一炉含一定量氧化铁的高碱度终渣,溅渣护炉确认炉渣固化后,兑入铁水进行吹炼,在吹炼到一定程度后将首批渣尽可能倒尽;然后,重新造渣吹炼进入脱碳期。
留渣+双渣工艺的优点是加速吹炼前期初渣形成,利用低温阶段快速脱磷,同时通过高碱度终渣热态循环以利用,实现降低石灰和钢铁料消耗的效果。
氧气转炉“留渣+双渣”炼钢工艺技术深究
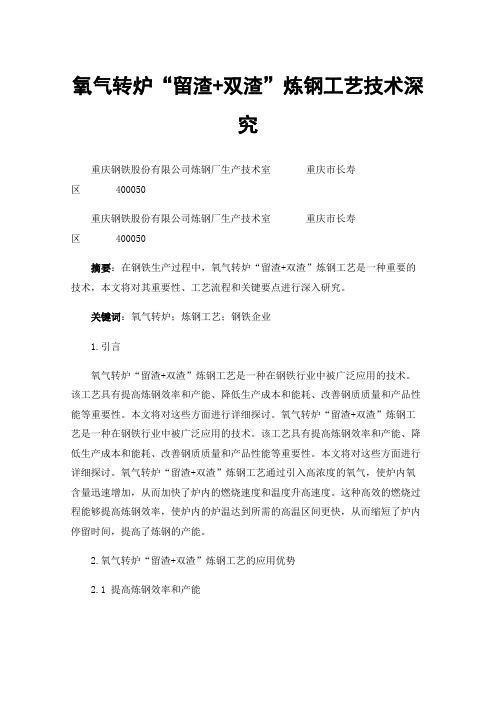
氧气转炉“留渣+双渣”炼钢工艺技术深究重庆钢铁股份有限公司炼钢厂生产技术室重庆市长寿区 400050重庆钢铁股份有限公司炼钢厂生产技术室重庆市长寿区 400050摘要:在钢铁生产过程中,氧气转炉“留渣+双渣”炼钢工艺是一种重要的技术,本文将对其重要性、工艺流程和关键要点进行深入研究。
关键词:氧气转炉;炼钢工艺;钢铁企业1.引言氧气转炉“留渣+双渣”炼钢工艺是一种在钢铁行业中被广泛应用的技术。
该工艺具有提高炼钢效率和产能、降低生产成本和能耗、改善钢质质量和产品性能等重要性。
本文将对这些方面进行详细探讨。
氧气转炉“留渣+双渣”炼钢工艺是一种在钢铁行业中被广泛应用的技术。
该工艺具有提高炼钢效率和产能、降低生产成本和能耗、改善钢质质量和产品性能等重要性。
本文将对这些方面进行详细探讨。
氧气转炉“留渣+双渣”炼钢工艺通过引入高浓度的氧气,使炉内氧含量迅速增加,从而加快了炉内的燃烧速度和温度升高速度。
这种高效的燃烧过程能够提高炼钢效率,使炉内的炉温达到所需的高温区间更快,从而缩短了炉内停留时间,提高了炼钢的产能。
2.氧气转炉“留渣+双渣”炼钢工艺的应用优势2.1 提高炼钢效率和产能氧气转炉“留渣+双渣”炼钢工艺通过引入高浓度的氧气,使炉内氧含量迅速增加,从而加快了炉内的燃烧速度和温度升高速度。
这种高效的燃烧过程能够提高炼钢效率,使炉内的炉温达到所需的高温区间更快,从而缩短了炉内停留时间,提高了炼钢的产能。
氧气转炉“留渣+双渣”炼钢工艺还可以通过增加氧气流量和调整炉内操作参数,实现更高的钢水流量和更短的炉次时间。
这种高效的生产方式可以提高钢铁企业的生产效率,满足市场需求,提升市场竞争力。
2.2 降低生产成本和能耗氧气转炉“留渣+双渣”炼钢工艺在炼钢过程中可以实现较高的能量利用率。
通过增加氧气流量和优化燃烧过程,可以提高炉内温度,减少燃料消耗。
与传统的炼钢工艺相比,该工艺能够降低煤气消耗,减少燃料成本。
由于氧气转炉“留渣+双渣”炼钢工艺能够加快炉内的燃烧速度和钢水温度升高速度,使得炼钢过程更加高效,减少了炉内的停留时间。
转炉双渣留渣工艺研究

转炉双渣留渣工艺研究
李帅
【期刊名称】《莱钢科技》
【年(卷),期】2015(000)005
【摘要】介绍了转炉留渣双渣工艺操作过程,以及在生产过程中遇到的操作难点和解决方法。
实践表明,实施该工艺可降低石灰消耗,提高脱磷效率,实现少渣炼钢等显著效果。
【总页数】2页(P30-31)
【作者】李帅
【作者单位】特钢事业部
【正文语种】中文
【中图分类】TF713
【相关文献】
1.转炉“留渣+双渣”少渣炼钢工艺实践 [J], 李伟东;杨明;何海龙;刘鹏飞;乔冠男
2.转炉“留渣-双渣”少渣炼钢工艺实践 [J], 项有兵;刘善喜;李双武
3.70 t顶底复吹转炉\"留渣+双渣\"前期脱磷工艺研究与实践 [J], 张旭;潘军;薛顺;赵斌;宋磊
4.70t转炉"留渣+双渣"脱磷工艺研究与实践 [J], 潘军; 邓南阳; 赵滨; 薛顺; 赵斌; 杨勇
5.邯钢120t转炉"留渣+双渣"脱磷工艺研究 [J], 高福彬;李建文;王玉刚
因版权原因,仅展示原文概要,查看原文内容请购买。
对留渣和双渣转炉炼钢工艺高效脱磷技术的思考

对留渣和双渣转炉炼钢工艺高效脱磷技术的思考
徐震;胡帅;崔应秦
【期刊名称】《冶金与材料》
【年(卷),期】2024(44)1
【摘要】在钢铁生产过程中,经常会出现一些磷元素,影响钢铁生产质量。
传统的去磷工艺存在效率低、污染环境、成本高,以及操作复杂等缺点,无法满足现代钢铁生产的需求。
留渣和双渣转炉炼钢工艺是一种高效的脱磷技术,其通过充分利用转炉熔化期后期的热量和渣子中的氧化钙含量,有效地提高脱磷效率。
并且,通过控制温度和渣子的成分,进而有效控制钢水的成分和温度,提高钢水的质量和产量。
因此,文章基于此,对留渣和双渣转炉炼钢工艺高效脱磷技术进行研究。
通过分析传统去磷工艺的不足,以及留渣和双渣转炉炼钢工艺高效脱磷技术的优势,以此来对留渣和双渣转炉炼钢工艺的应用提供参考。
【总页数】3页(P142-144)
【作者】徐震;胡帅;崔应秦
【作者单位】江苏永钢集团炼钢厂
【正文语种】中文
【中图分类】TF7
【相关文献】
1.留渣+双渣转炉炼钢工艺高效脱磷技术研究
2.“留渣+双渣”转炉炼钢工艺高效脱磷技术
3.转炉双渣留渣法脱磷渣物相对渣中磷富集的影响
4.转炉留渣双渣工艺脱磷阶段成渣路线研究
5.复吹转炉“留渣-双渣”脱磷工艺试验
因版权原因,仅展示原文概要,查看原文内容请购买。
氧气转炉“留渣+双渣”炼钢工艺技术131210王新华
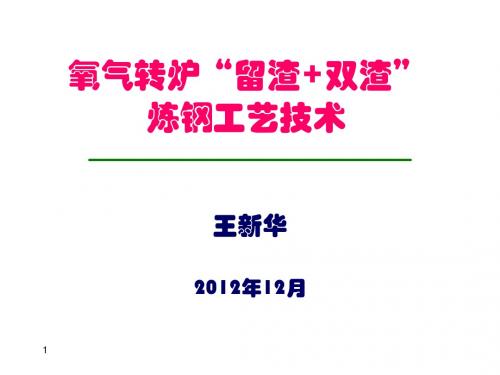
新工艺基本原理
在温度升至对脱磷不利前尽量将炉渣倒出, 加入渣料进行第二阶段吹炼。 冶炼结束炉渣在高温下 已基本不具备去磷能力。
下炉吹炼前期,由于温度低, 所留炉渣重新具备去磷能力。
11
MURC工艺能够显著降低石灰耗量
T. Matsumiya, et al, 10th Japan-China Symposium on Science and Technology of Iron and Steel, 2004, Chiba
6
渣量比较
工艺A:传统炼钢工艺; 工艺B:铁水罐脱磷预处理; 工艺C:转炉铁水脱磷预处理; 工艺D:转炉铁水预处理,80% 脱碳转炉渣返回脱磷转 炉利用。
S. Kitamura, et al., 9th China-Japan Symposium on Science and Technology of Iron and Steel, 2001, Xian 7
SGRS工艺:
SGRS工艺应用情况
• • • 迁钢和首秦公司采用SGRS工艺产钢比率分别达到了79.1% 和81.1% ; 吨钢石灰消耗分别降低了47.3%和41.1% (迁钢降低至 22.0kg/t,首秦降低至37.2kg/t); 轻烧白云石消耗分别降低了55.2%和56.6% (迁钢降低至 8.0kg/t,首秦降低至8.2kg/t);
新日铁开发“MURC”炼钢工艺
岩崎正樹,松尾充高,製鋼技術開発の歩みと今後の展望,新日鉄技報, 2011 ,第 391 号,p88-93 8 小川雄司,転炉を用いた脱りん脱炭連続処理プロセスの開発,鉄と鋼, 87(2001) , p21-28
新日铁炼钢工厂
1. 君津製鉄所(950万吨):
一炼钢厂: 220t转炉×3 二炼钢厂: 300t转炉×2 炼钢厂: 380t转炉×3
氧气转炉出钢脱硫-LF精炼生产超低硫钢的工艺

氧气转炉出钢脱硫-LF精炼生产超低硫钢的工艺郝宁;王新华;王海涛;李宏;崔爱民;王国连;龚坚;李林【期刊名称】《特殊钢》【年(卷),期】2006(027)006【摘要】因210 t BOF冶炼终点NVA32(%:0.12~0.18C、1.30~1.60Mn)钢中硫含量由0.005%升高至0.020%,通过BOF出钢过程加入1000 kg二元合成渣CaO-CaF2、200 kg铝粒,并加入硅锰和硅铝钡合金,可使钢中硫含量降低0.007%~0.008%,脱硫率达30%.在LF精炼时,通过进一步加入合成渣800 kg,600~900 L/min吹氩,加热后喂600 m硅钙线,30~45L/min吹氩10 min,终渣碱度R=4.5~5.5,钢中硫含量进一步降低至0.001%~0.002%.【总页数】3页(P44-46)【作者】郝宁;王新华;王海涛;李宏;崔爱民;王国连;龚坚;李林【作者单位】北京科技大学冶金与生态工程学院,北京100083;北京科技大学冶金与生态工程学院,北京100083;北京科技大学冶金与生态工程学院,北京100083;北京科技大学冶金与生态工程学院,北京100083;首钢集团总公司,北京100041;首钢集团总公司,北京100041;首钢集团总公司,北京100041;首钢集团总公司,北京100041【正文语种】中文【中图分类】TG1【相关文献】1.LF精炼工艺对36MnVNS4含硫非调质钢硫含量和夹杂物形貌的影响 [J], 熊玉彰;张贤忠2.150t EAF-LF-VD-CC流程生产超低硫钢的工艺实践 [J], 马全峰;武守防3.精炼渣的配比对超低硫钢脱硫的影响 [J], 王雅娜;朱荣;李士琦;王新华;李素芹;孙纪青4.超低硫钢LF炉精炼生产实践 [J], 单庆林;王朝斌;陈玉鑫;5.LF-RH工艺生产超低硫钢钢水温度预报模型 [J], 樊智勇;熊玮;胡汉涛;黄翼飞因版权原因,仅展示原文概要,查看原文内容请购买。
转炉炼钢中留渣技术的原理及应用杨正府

转炉炼钢中留渣技术的原理及应用杨正府发布时间:2021-09-26T07:45:34.951Z 来源:《防护工程》2021年15期作者:杨正府[导读] 转炉留渣法炼钢技术的普及和推广应用,为冶炼技术发展做出了极大的贡献。
在明确技术应用方法和工艺的基础上,做好对技术的创新与完善,将会进一步提升留渣冶炼技术应用价值。
柳钢转炉炼钢厂广西壮族自治区柳州市 545002摘要:转炉留渣法炼钢技术的普及和推广应用,为冶炼技术发展做出了极大的贡献。
在明确技术应用方法和工艺的基础上,做好对技术的创新与完善,将会进一步提升留渣冶炼技术应用价值。
关键词:转炉炼钢;留渣技术;脱磷引言在钢铁行业降本增效大背景下,转炉炼钢留渣法作为一种能够显著降低辅料消耗、降低钢铁料消耗的技术,使得炼钢生产成本得到了切实的控制和降低,并且提升了生产效率。
随着钢铁工业技术日益向精细化发展,转炉留渣法炼钢技术应用效果也越来越明显,更多的炼钢企业和技术人员愿意挖掘这一技术的潜在应用价值,对转炉留渣法炼钢技术进行不断创新和完善,进一步拓展该技术的使用范围。
1 转炉炼钢留渣技术原理转炉留渣法技术原理:将上一炉部分终渣留在炉内,溅渣护炉后,作为下一炉初渣,利用其高温,高碱度,高T.Fe以及含有MgO的碱性渣特点,促进石灰轻烧快速熔化成渣和前期脱磷,从而降低熔剂消耗,降低生产成本。
通过大规模工业试验和对转炉脱磷过程热力学、动力学分析,得到转炉铁水“三脱”预处理各工艺参数和如下主要结论:(1)转炉铁水脱磷效果决定于采用的脱磷工艺,经过工业实践:低碱度高FeO渣脱磷率为55.4%,中高碱度高FeO渣脱磷率为83.4%,中高碱度低FeO渣脱磷率为86.4%。
三种方案相比,中高碱度低FeO渣脱磷效果好、铁损低,应是脱磷工艺的首选方案。
(2)炉渣碱度是提高脱磷率的关键,炉渣碱度增大,脱磷率增加。
(3)在相同炉渣碱度条件下,随脱碳量增加,脱磷率增大;说明炉渣的脱磷能力决定了熔池中C.P平衡关系,在相同熔池C条件下,炉渣碱度越高,与C平衡的P越低。
- 1、下载文档前请自行甄别文档内容的完整性,平台不提供额外的编辑、内容补充、找答案等附加服务。
- 2、"仅部分预览"的文档,不可在线预览部分如存在完整性等问题,可反馈申请退款(可完整预览的文档不适用该条件!)。
- 3、如文档侵犯您的权益,请联系客服反馈,我们会尽快为您处理(人工客服工作时间:9:00-18:30)。
迁钢在铁水[Si]含量0.22-0.40%范围,脱磷结束倒渣量应达到 6.0-12.5吨; 首秦公司在铁水[Si]在0.40-0.60%条件下,倒渣量应达到4.0 -8.0吨。
29
炉渣流动性控制
能否快速倒出足量脱磷炉渣,主要取决于对炉渣流动性的控制, 为此必须做到:
1. 炉渣充分熔化,不含未溶石灰颗粒以及方镁石(MgO)、 2CaOSiO2等高熔点析出相; 2. 控制炉渣组成使其具有较低粘度值; 3. 采用较低枪位,加强搅拌促进化渣;
10
新工艺基本原理
在温度升至对脱磷不利前尽量将炉渣倒出, 加入渣料进行第二阶段吹炼。 冶炼结束炉渣在高温下 已基本不具备去磷能力。
下炉吹炼前期,由于温度低, 所留炉渣重新具备去磷能力。
11
MURC工艺能够显著降低石灰耗量
T. Matsumiya, et al, 10th Japan-China Symposium on Science and Technology of Iron and Steel, 2004, Chiba
(3)倒渣增加冶炼时间,渣量波动对吹炼过程控制稳定性造成很大影 响。
•
迁钢和首秦公司采用SGRS工艺后相当长时间里,遇到了脱磷阶段 倒渣量不足和渣中裹入铁珠量大(15~20%)造成的严重困难。
28
倒渣量影响计算
210t转炉 铁水[Si]:0.35% 脱磷阶段碱度:1.5 脱碳阶段碱度:3.5
• •
19
首钢转炉“留渣+双渣”工艺试验研究
• • 2010年开始,在迁钢五座210t复吹转炉和首秦公司三座 100t复吹转炉,对“留渣+双渣”炼钢工艺开展试验研究; 开发了终渣快速固化、炉渣物性控制、高效脱磷、快速足量 倒渣、吹炼稳定控制、干法除尘与煤气回收、“转炉 -精炼连铸”生产组织与周期匹配等关键技术; 根据该工艺能够大幅度减少炼钢渣量的特点,命名为 SGRS 工艺(Slag Generation Reduced Steelmaking)。
2. 大分製鉄所(900万吨): 3. 名古屋製鉄所(550万吨):
一炼钢厂: 160t转炉×2 (脱P、脱S); 二炼钢厂: 270t转炉×3 一炼钢厂: 170t转炉×2 三炼钢厂: 350t转炉×3
4. 八幡製鉄所(350万吨):
5. 室蘭製鉄所(特殊钢棒线材)。
9
基本原理:温度对脱磷反应影响
•
•
转炉炼钢渣量减少30%以上;
钢铁料消耗分别降低了6.07kg/t和6.31kg/t。
23
二、关键工艺技术
技术难度:
1. 冶炼周期延长 (影响“转炉-精炼-连铸”工序间匹配;降 低钢产量); 2. 难以快速、足量倒渣(炉内渣量蓄积导致循环中断;倒出炉 渣含大量金属铁珠); 3. 脱磷难度增大 (初始渣P2O5含量高;国内转炉底吹弱); 4. 过程控制精度降低 (改为两阶段吹炼;炉内渣量变化); 5. 留渣装铁水存在安全隐患 (所留炉渣-铁水剧烈反应)。
16
新日铁对两种炼钢工艺方法评价
17
新日铁对两种炼钢工艺方法评价
18
国内“留渣+双渣”工艺应用情况
上世纪60~70年代:
小转炉、侧吹转炉; 高磷含量铁水; 目的:提高脱磷效率(早成渣,增加渣量)。
近年来三明钢厂试验采用MURC工艺:
目的:促进脱磷(厚板磷含量控制要求严); 未能解决倒渣量不足、倒渣含铁珠量多的难题; 报道很少。
13
新日铁8t转炉试验
14 小川雄司,転炉を用いた脱りん脱炭連続処理プロセスの開発,鉄と鋼,2001,Vol.87,No.1,p21-28
石灰消耗随连续炉次变化(计算)
15 小川雄司,転炉を用いた脱りん脱炭連続処理プロセスの開発,鉄と鋼,2001,Vol.87,No.1,p21-28
新日铁对LD-ORP和MURC工艺方法评价云石均为重要的不可再 生资源,我国石灰石资源并不富裕; • 据北京市规划设计院2007年资料, 已探明石灰石矿储量(750亿吨), 按目前石灰石耗量仅可用45年;
• 此外,大量开采石灰石、白云石还 会加剧植被破坏、水土流失,对生 态环境造成不利影响。
首钢石灰石矿山
冶炼前期温度较后期低300℃左右,脱磷反应 平衡常数较后期高出4个数量级以上。
2[P]+5[O]=P2O5(l)
△G0= -832384+632.65T
log K log
a P2O5 a a
2 5 [P] [O]
前期温度(~4min): 1320~1380℃。
43443 33.02 T
冶炼终点温度: 1630~1680℃。
3
转炉脱磷预处理 + 转炉脱碳炼钢
• 日本钢铁企业开发了“转炉脱磷预处理 + 转炉脱碳炼钢” 工艺(LD-ORP,SRP,H炉): • • • • 高效经济生产洁净钢(包括低磷、超低磷钢); 缩短炼钢生产周期; 降低40%以上石灰消耗和30%以上渣量(早期称为 Less Slag炼钢法)。
需要专门脱磷转炉(新建钢厂或炼钢能力有较大富余钢厂)。
SGRS工艺:
SGRS工艺应用情况
• • • 迁钢和首秦公司采用SGRS工艺产钢比率分别达到了79.1% 和81.1% ; 吨钢石灰消耗分别降低了47.3%和41.1% (迁钢降低至 22.0kg/t,首秦降低至37.2kg/t); 轻烧白云石消耗分别降低了55.2%和56.6% (迁钢降低至 8.0kg/t,首秦降低至8.2kg/t);
3. T. Matsumiya and M. Ichida, Recent Progress and Topics in Iron- and Steelmaking Technology in Japan, The 10th Japan-China Symposium on Science and Technology of Iron and Steel, Nov.18-19, 2004, Chiba, p1-11
• “双渣”工艺:
• • 主要目的:生产低磷钢; 石灰消耗和渣量多于常规单渣工艺。 主要目的:降低石灰、钢铁料等消耗,减少渣量; 石灰消耗和渣量少于常规单渣工艺。
•
SGRS工艺:
• •
2. 与传统“留渣兑铁”工艺不同:
• • 传统留渣兑铁:
• • 液态渣条件下兑铁,安全隐患大。 液态渣固化后兑铁,无安全隐患。
氧气转炉“留渣+双渣” 炼钢工艺技术
王新华
2012年12月
1
一、背景和意义
钢铁工业是重要基础产业,近十多年来 发展迅速,其中尤以中国钢铁工业的崛 起令人瞩目; 钢铁生产在资源、能源消耗和炉渣等废 弃物排放方面存在很大问题; 氧气转炉炼钢(产钢比>91%):
为去除磷、硫杂质等需要,炼钢过程 必须加入石灰、白云石等造渣; 全国氧气转炉年产钢6.45亿吨以上, 每年消耗4400万吨以上石灰石和 1000万吨以上白云石,产生6200万 吨以上炉渣。
6
渣量比较
工艺A:传统炼钢工艺; 工艺B:铁水罐脱磷预处理; 工艺C:转炉铁水脱磷预处理; 工艺D:转炉铁水预处理,80% 脱碳转炉渣返回脱磷转 炉利用。
S. Kitamura, et al., 9th China-Japan Symposium on Science and Technology of Iron and Steel, 2001, Xian 7
12
新日铁MURC工艺相关报道
1. 小川雄司,矢野正孝,北村信也,平田浩,転炉を用いた脱りん脱炭連続処理プ ロセスの開発,鉄と鋼,2001,Vol.87,No.1,p21-28 2. K. Kume, K. Yonezawa, M. Yoshimi, H. Hondo and M. Kumakura, CAMP-ISIJ, 2003, Vol.16, p116
新日铁开发“MURC”炼钢工艺
岩崎正樹,松尾充高,製鋼技術開発の歩みと今後の展望,新日鉄技報, 2011 ,第 391 号,p88-93 8 小川雄司,転炉を用いた脱りん脱炭連続処理プロセスの開発,鉄と鋼, 87(2001) , p21-28
新日铁炼钢工厂
1. 君津製鉄所(950万吨):
一炼钢厂: 220t转炉×3 二炼钢厂: 300t转炉×2 炼钢厂: 380t转炉×3
4. K. Morita, M. Kumakura, T. Washizu and K. Kume, Efficiency Promotion of Refining Process in Nippon Steel Corporation, The 4th International Congress on the Science and Technology of Steelmaking, Oct.6-8, 2008, Gifu, p253-256 5. Y. Ueshima and K. Saito, Recent Advances and Topics of Iron- and Steel-making Technology in Japan, The 12th Japan-China Symposium on Science and Technology of Iron and Steel, Oct.17-19, 2010, Nagoya, p11-18 6. 岩崎正樹,松尾充高,製鋼技術開発の歩みと今後の展望,新日鉄技報,2011, 第391号,p88-93
27
1、脱磷阶段低碱度渣系开发与炉渣物性控制
• • 采用SGRS炼钢工艺,脱磷阶段结束后能否快速倒出足够量炉渣具 有非常重要的意义; 如倒渣量不足:
(1)炉内渣量逐炉蓄积,碱度不断增加,倒渣愈加困难,最后导致 SGRS工艺无法接续,循环被迫停止;
(2)炉渣流动性逐炉变差,渣中裹入金属铁珠量大,钢铁料消耗增加 ;