影响塑料薄膜干式符合强度及主要因素
塑料薄膜干式复合粘边故障的原因及处理
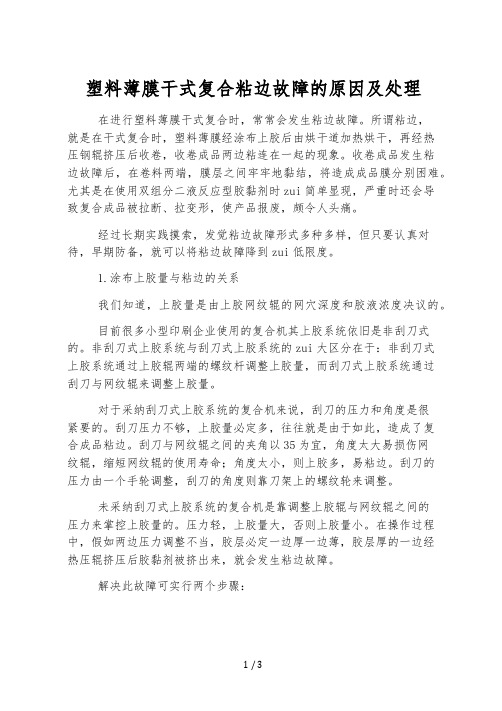
塑料薄膜干式复合粘边故障的原因及处理在进行塑料薄膜干式复合时,常常会发生粘边故障。
所谓粘边,就是在干式复合时,塑料薄膜经涂布上胶后由烘干道加热烘干,再经热压钢辊挤压后收卷,收卷成品两边粘连在一起的现象。
收卷成品发生粘边故障后,在卷料两端,膜层之间牢牢地黏结,将造成成品膜分别困难。
尤其是在使用双组分二液反应型胶黏剂时zui简单显现,严重时还会导致复合成品被拉断、拉变形,使产品报废,颇令人头痛。
经过长期实践摸索,发觉粘边故障形式多种多样,但只要认真对待,早期防备,就可以将粘边故障降到zui低限度。
1.涂布上胶量与粘边的关系我们知道,上胶量是由上胶网纹辊的网穴深度和胶液浓度决议的。
目前很多小型印刷企业使用的复合机其上胶系统依旧是非刮刀式的。
非刮刀式上胶系统与刮刀式上胶系统的zui大区分在于:非刮刀式上胶系统通过上胶辊两端的螺纹杆调整上胶量,而刮刀式上胶系统通过刮刀与网纹辊来调整上胶量。
对于采纳刮刀式上胶系统的复合机来说,刮刀的压力和角度是很紧要的。
刮刀压力不够,上胶量必定多,往往就是由于如此,造成了复合成品粘边。
刮刀与网纹辊之间的夹角以35为宜,角度太大易损伤网纹辊,缩短网纹辊的使用寿命;角度太小,则上胶多,易粘边。
刮刀的压力由一个手轮调整,刮刀的角度则靠刀架上的螺纹轮来调整。
未采纳刮刀式上胶系统的复合机是靠调整上胶辊与网纹辊之间的压力来掌控上胶量的。
压力轻,上胶量大,否则上胶量小。
在操作过程中,假如两边压力调整不当,胶层必定一边厚一边薄,胶层厚的一边经热压辊挤压后胶黏剂被挤出来,就会发生粘边故障。
解决此故障可实行两个步骤:(1)在上胶前,先将上胶辊两端的螺纹杆压紧,然后再在运行过程中渐渐调整上胶量。
上胶量不宜过大。
(2)检测胶辊的上胶量大小。
zui直接的方法是用食指挤压上胶辊,察看被挤压处胶液的厚度,肯定要保证两边一致,且必需注意安全。
由娴熟工来完成。
2.烘干温度与粘边的关系干式复合机的烘干系统分为3个区域,即:蒸发区、硬化区、排出异味区。
干式复合常见故障及处理方法
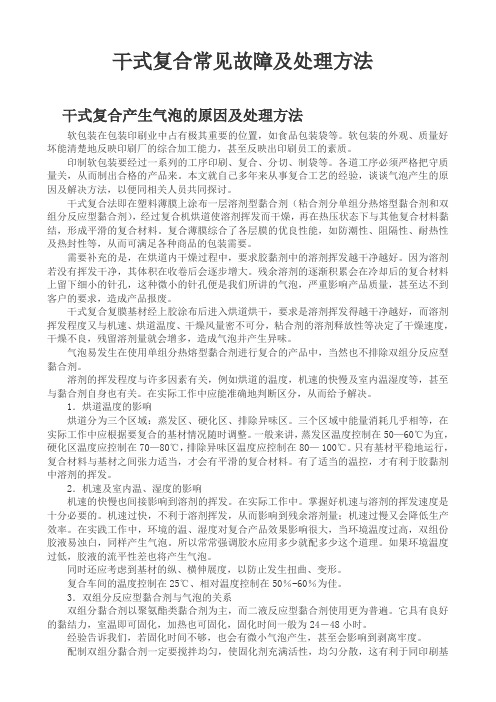
干式复合常见故障及处理方法干式复合产生气泡的原因及处理方法软包装在包装印刷业中占有极其重要的位置,如食品包装袋等。
软包装的外观、质量好坏能清楚地反映印刷厂的综合加工能力,甚至反映出印刷员工的素质。
印制软包装要经过一系列的工序印刷、复合、分切、制袋等。
各道工序必须严格把守质量关,从而制出合格的产品来。
本文就自己多年来从事复合工艺的经验,谈谈气泡产生的原因及解决方法,以便同相关人员共同探讨。
干式复合法即在塑料薄膜上涂布一层溶剂型黏合剂(粘合剂分单组分热熔型黏合剂和双组分反应型黏合剂),经过复合机烘道使溶剂挥发而干燥,再在热压状态下与其他复合材料黏结,形成平滑的复合材料。
复合薄膜综合了各层膜的优良性能,如防潮性、阻隔性、耐热性及热封性等,从而可满足各种商品的包装需要。
需要补充的是,在烘道内干燥过程中,要求胶黏剂中的溶剂挥发越干净越好。
因为溶剂若没有挥发干净,其体积在收卷后会逐步增大。
残余溶剂的逐渐积累会在冷却后的复合材料上留下细小的针孔,这种微小的针孔便是我们所讲的气泡,严重影响产品质量,甚至达不到客户的要求,造成产品报废。
干式复合复膜基材经上胶涂布后进入烘道烘干,要求是溶剂挥发得越干净越好,而溶剂挥发程度又与机速、烘道温度、干燥风量密不可分,粘合剂的溶剂释放性等决定了干燥速度,干燥不良,残留溶剂量就会增多,造成气泡并产生异味。
气泡易发生在使用单组分热熔型黏合剂进行复合的产品中,当然也不排除双组分反应型黏合剂。
溶剂的挥发程度与许多因素有关,例如烘道的温度,机速的快慢及室内温湿度等,甚至与黏合剂自身也有关。
在实际工作中应能准确地判断区分,从而给予解决。
1.烘道温度的影响烘道分为三个区域:蒸发区、硬化区、排除异味区。
三个区域中能量消耗几乎相等,在实际工作中应根据要复合的基材情况随时调整。
一般来讲,蒸发区温度控制在50—60℃为宜,硬化区温度应控制在70—80℃,排除异味区温度应控制在80—100℃。
只有基材平稳地运行,复合材料与基材之间张力适当,才会有平滑的复合材料。
干式复合工艺及故障排除
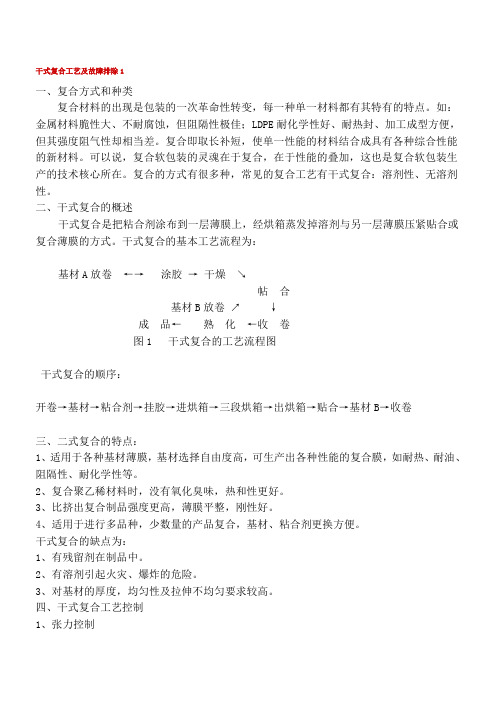
干式复合工艺及故障排除1一、复合方式和种类复合材料的出现是包装的一次革命性转变,每一种单一材料都有其特有的特点。
如:金属材料脆性大、不耐腐蚀,但阻隔性极佳;LDPE耐化学性好、耐热封、加工成型方便,但其强度阻气性却相当差。
复合即取长补短,使单一性能的材料结合成具有各种综合性能的新材料。
可以说,复合软包装的灵魂在于复合,在于性能的叠加,这也是复合软包装生产的技术核心所在。
复合的方式有很多种,常见的复合工艺有干式复合:溶剂性、无溶剂性。
二、干式复合的概述干式复合是把粘合剂涂布到一层薄膜上,经烘箱蒸发掉溶剂与另一层薄膜压紧贴合或复合薄膜的方式。
干式复合的基本工艺流程为:基材A放卷←→涂胶→干燥↘帖合基材B放卷↗↓成品←熟化←收卷图1 干式复合的工艺流程图干式复合的顺序:开卷→基材→粘合剂→挂胶→进烘箱→三段烘箱→出烘箱→贴合→基材B→收卷三、二式复合的特点:1、适用于各种基材薄膜,基材选择自由度高,可生产出各种性能的复合膜,如耐热、耐油、阻隔性、耐化学性等。
2、复合聚乙稀材料时,没有氧化臭味,热和性更好。
3、比挤出复合制品强度更高,薄膜平整,刚性好。
4、适用于进行多品种,少数量的产品复合,基材、粘合剂更换方便。
干式复合的缺点为:1、有残留剂在制品中。
2、有溶剂引起火灾、爆炸的危险。
3、对基材的厚度,均匀性及拉伸不均匀要求较高。
四、干式复合工艺控制1、张力控制张力系统可以说是复合软包装设备的生命。
复合机的张力控制包括放卷张力控制(1、2放卷张力控制)复合张力控制、收卷张力控制。
2、放卷张力系统放卷张力控制系统由磁粉制功器、电机和变频器、张力传感器、浮动辊装置、电气控制系统组成。
在放卷过程中,随着卷径逐渐减少,张力保持着恒定。
在大型高速干式复合机中,多采用电机主动放料卷和浮动辊装置相配合后,而不采用磁粉制功器放卷。
这是由于机器在高速运转时,当放卷在卷径较小时,即使磁粉制功器的输出为0,但是由于放卷轴、导辊、齿轮等的磨擦,产生较大阻尼,导致张力比设定值高;而采用电机放卷,可以将放卷轴、齿轮、导辊等的磨擦产生阻尼用电机主动放卷加以补偿。
影响粘结力和剥离强度的因素

影响塑料薄膜粘结力和剥离强度的因素塑料薄膜表面电晕处理不好,表面张力低,就会导致墨层附着牢度低,复合膜粘结强度低,在薄膜投入前应认真检测其表面张力值务必提高到3.8×10-2N/m以上,最好能达到4.0-4.2×10-2N/m,因为3.8×10-2N/m只是最低要求,表面张力值低于3.8×10-2N/m的薄膜根本就不能使油墨和胶粘剂完全铺展,复合后的成品当然达不到剥离强度的要求。
检测薄膜表面张力的方法通常有两种:1)达因笔测试,达因笔的笔液通常呈红色,规格有3.8×10-2N/m、4.0×10-2N/m、4.2×10-2N/m、4.4×10-2N/m以及4.8×10-2N/m这五种,如果用达因笔在薄膜上的笔液不收缩,均匀,无断层,则说明薄膜的表面张力已经达到使用要求,相反,笔液收缩,消失,不均匀,不连续,则说明处理不够;2)用BOPP单面胶布测试,将BOPP单面胶布贴在待测薄膜表面再撕开,电晕处理好的通常剥离声音小,粘贴牢固,相反则粘贴不牢,容易剥离,这种测试方法要依靠经验,不适合测试PET、PA等薄膜。
电晕处理不符合要求的基材决不能进行复合,因为复合后肯定达不到包装产品对剥离强度的要求。
常用基材的表面张力值为:BOPP3.8×10-2N/m、PET5.0×10-2N/m、PA5.2×10-2N/m。
溶剂残留量太高影响剥离强度,影响粘结力残留溶剂太多,复合后会形成许多微小气泡,使相邻的复合基材脱离、分层、气泡越多,剥离强度越低,要提高剥离强度,就必须减少气泡的产生。
气泡的产生与许多因素有关,诸如上胶不均匀,烘干道温度过低,热压辊温度偏低及室内温湿度不合适等,通常,室内温度宜控制在23-25℃,相对湿度应控制在50%-60%为宜,另外,避免使用高沸点溶剂,也可减少气泡的产生。
总之为提高剥离强度,提高粘接力应尽可能降低残留溶剂。
干式复合过程总会出现这些问题!超全故障指导书,提高产品质量必备!

干式复合过程总会出现这些问题!超全故障指导书,提高产品质量必备!干式复合过程总会出现这样那样的问题,本文汇总了不同问题的原因和解决方案,软包厂复合工在操作时,遇到类似问题,可直接查阅。
一、复合膜外观不良1、有气泡①薄膜润湿不良,应提高胶的浓度和涂布量,(MST、KPT)表面不易湿润,易产生气泡,特别在冬天。
油墨上的气泡,用提高胶的用量的方法去除。
②油墨表面凹凸和起泡,应把复合膜的复合温度和复合压力提高。
③油墨表面上的胶涂布量少,应增加复合辊的压贴时间及使用光滑辊筒、薄膜预热充分、降低复合速度、选择湿润性好的胶以及正确选用油墨。
④薄膜中的添加剂(润滑剂、抗静电剂)被胶渗透,应选用分子量高、固化迅速的胶,提高胶浓度,提高烘箱温度充分使胶干燥,不使用超过3个月存放期的薄膜,因为电晕处理已丧失。
⑤冬天里气温低,粘结剂对薄膜和油墨转移,润湿粘附不好,操作场所保持一定温度。
⑥干燥温度太高,发生胶的起泡或表皮结皮,内里不干,应调整胶干燥温度。
⑦复合辊薄膜间夹带入空气,应提高复合辊温度,减小复合角(薄膜厚、硬时易产生气泡)。
2、复合后无气泡,经过熟化后产生了气泡。
①由于薄膜阻隔性高,胶固化时产生的CO2气体,残留在复合膜中,未印刷处也有气泡,应提高固化剂量,使胶在干燥中固化。
②胶中的酯酸乙酯是油墨粘结料的良好溶剂,胶溶渗了油墨,只在油墨上有气泡,避免水分渗入胶中及提高胶干燥温度,减少对油墨的溶渗。
3、复合膜上有不规则皱纹、气泡①薄膜厚薄不均,避免使用厚度不均膜。
②薄膜拉伸太大,定型不够,同热收缩,以及由于吸湿,膜发生变形,应防止薄膜吸湿变形,降低印刷卷取张力以及复合时张力不宜太高。
4、复合膜上有规则的气泡和皱纹原因:网纹辊上的网眼有坏的,橡胶辊有损坏和凹点,复合辊上有脏东西,基材速度同网纹辊速度有偏差,薄膜厚度有偏差。
解决方案:应检查网纹辊,更换或修补;检查橡胶辊是否损坏,更换或修补;清洗复合辊。
5、复合膜中包有异物,有气泡原因:胶中混入灰尘、橡胶粒子,薄膜上有灰尘附着,辊筒不干净。
塑料强度的影响因素(一).
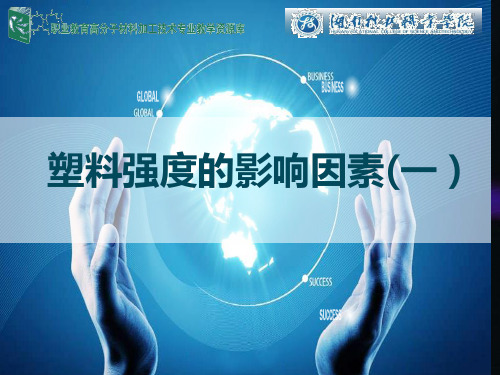
聚合物
强度Pa
25~28
50
61
83
随着极性基团或氢键,强度,但密度大,阻碍链段的运动, 不能产生强迫高弹形变——脆性断裂
② 交联
适当交联,总是提高聚合物的强度,但如果交联度太大,
会使其脆性太大而失去应用价值。
交联剂当量浓度 0.1 0.3 1.0 2.5 3.5 8.0
b
断裂强度MPa
1000
LDPE
HDPE 二次结构:
7~15
21~27
300
60
支化多
支化少
① 链的刚性
高分子链刚性增加,聚合物强度增加,韧性下降。 如:PE 24.5N/m2,PS 35.2~60N/m2, PET 80N/m2
② 分子量与分子量分布:
分子量是对高分子材料力学性能(包括强度、弹性、韧性)起决定性 作用的结构参数。 强 度
能必不可少的措施。 注意:当外力与取向方向平行,强度高,垂直,强度低。 ⑤ 应力集中 局部应力集中可以使超过聚合物的强度降低。
谢谢大家
6.47
920
16
680
21.7
440
16.4
280
6.78
90
4.6
③ 空间立构
结构规整和等规度高的
聚合物因结晶而强度提高。
无规立构含量对PP性能影响 无规立构含量% 2.0 抗张强度Pa 34.5
3.5
6.4
32.5
29
④ 支化
支化破坏了链的规整性结晶度降低,还增加了分子间的距离分子间 力减小,都使强度降低。但是韧性有所提高。 支化度对聚合物力学性能的影响 聚合物 抗张强度 b(%) 支化程度
分子量
当分子量很小时,强度随着分子量增加而增加,当分子量大到 一定值,强度与分子量无关。
干法复合的张力控制

干法复合的张力控制干法复合的张力控制干法复合的张力控制是影响复合膜质量的主要因素。
干法复合中张力控制的适当,复合机上各工段的料均平整,没有纵向或横向的褶皱,材料本身不发生塑性变形。
如果张力控制不当,不仅降低复合材料的性能还会给后期的分切、制袋、封口等工艺带来一系列的麻烦。
1、影响张力控制的因素●温度湿度的变化。
生产环境和储存环境的温湿度变化是影响材料物理性能的主要因素。
高温高湿环境中材料会变软,抗拉强度变小,伸缩率变大,相反低温低湿的环境中材料会相应变硬,变脆。
因此,夏季生产时的张力要比冬季时小。
●基材的厚薄均匀度。
不同材料的厚薄度不同,张力也不一样。
通常情况下厚的材料张力大,薄的材料张力小。
同种材料厚薄不均匀也会影响张力。
首先材料的厚薄不均匀使得材料受力不均匀,因此为保证材料能很好的复合需要适时调节张力。
其次材料厚度不均匀会造成辊间压力波动,从而影响张力。
●基材的规格质量。
根据基材的复合宽度不同,张力值也要相应的改变。
宽度越宽,张力值越大;基材质量越大,张力值也越大。
●基材的形式发生变化。
随着复合的进行,复合的卷径发生变化,由公式:M=FxR(其中:M为膜卷转动力矩,F为薄膜所受张力,R为膜卷卷径)可知当采用恒转矩控制上时,张力随卷径的减小呈反比例变化。
●接触面的摩擦变化。
基材的接触面越粗糙,张力值越大,因此干式复合机上安装的导辊均为活动的光滑钢辊以减少摩擦。
●各导辊的平行度和光滑性。
为保证复合时基材平整无皱,各导辊须互相平行;而且导辊运行的光滑性也是直接影响张力稳定的因素,因此要定期检测,发现问题及时解决。
●运行中速度的变化。
速度的变化是产生张力的一个主要原因,机器在启动、停止、增减速时都伴随张力的变化,因此,速度的缓慢变化有利于各部分张力的稳定。
另外,机器的机械性能、控制系统的特点等也会影响张力控制。
2、张力控制的分类干式复合的张力控制在干式复合中包括:放卷张力控制、干燥部位张力控制、收卷张力控制。
干式复合强度的影响因素.
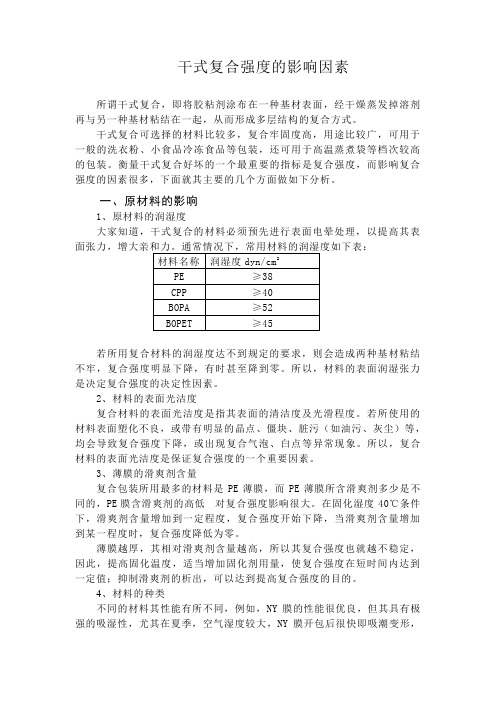
干式复合强度的影响因素所谓干式复合,即将胶粘剂涂布在一种基材表面,经干燥蒸发掉溶剂再与另一种基材粘结在一起,从而形成多层结构的复合方式。
干式复合可选择的材料比较多,复合牢固度高,用途比较广,可用于一般的洗衣粉、小食品冷冻食品等包装,还可用于高温蒸煮袋等档次较高的包装。
衡量干式复合好坏的一个最重要的指标是复合强度,而影响复合强度的因素很多,下面就其主要的几个方面做如下分析。
一、原材料的影响1、原材料的润湿度大家知道,干式复合的材料必须预先进行表面电晕处理,以提高其表若所用复合材料的润湿度达不到规定的要求,则会造成两种基材粘结不牢,复合强度明显下降,有时甚至降到零。
所以,材料的表面润湿张力是决定复合强度的决定性因素。
2、材料的表面光洁度复合材料的表面光洁度是指其表面的清洁度及光滑程度。
若所使用的材料表面塑化不良,或带有明显的晶点、僵块、脏污(如油污、灰尘)等,均会导致复合强度下降,或出现复合气泡、白点等异常现象。
所以,复合材料的表面光洁度是保证复合强度的一个重要因素。
3、薄膜的滑爽剂含量复合包装所用最多的材料是PE薄膜,而PE薄膜所含滑爽剂多少是不同的,PE膜含滑爽剂的高低对复合强度影响很大。
在固化湿度40℃条件下,滑爽剂含量增加到一定程度,复合强度开始下降,当滑爽剂含量增加到某一程度时,复合强度降低为零。
薄膜越厚,其相对滑爽剂含量越高,所以其复合强度也就越不稳定,因此,提高固化温度,适当增加固化剂用量,使复合强度在短时间内达到一定值;抑制滑爽剂的析出,可以达到提高复合强度的目的。
4、材料的种类不同的材料其性能有所不同,例如,NY膜的性能很优良,但其具有极强的吸湿性,尤其在夏季,空气湿度较大,NY膜开包后很快即吸潮变形,在复合过程中因水分过大,造成粘合剂反应不充分,复合强度下降。
所以,必须改善复合车间的环境,降低环境湿度,同时,复合NY等易吸湿的材料时,加大固化剂用量,适当提高复合强度,缩短薄膜与空气接触时间。
干法复合薄膜剥离强度影响因素分析

干法复合薄膜剥离强度影响因素分析任清杰【摘要】简单介绍了干法复合的工艺过程和保证复合膜剥离强度的重要性.从基材特性、粘合剂、油墨及印刷工艺、复合工艺和生产环境等五个方面阐述了影响复合膜剥离强度的因素,并总结了实际生产过程中应考虑的主要事项.【期刊名称】《塑料包装》【年(卷),期】2010(020)006【总页数】4页(P37-40)【关键词】干法复合;复合薄膜;剥离强度;粘合剂;影响因素【作者】任清杰【作者单位】天津科技大学,包装与印刷工程学院【正文语种】中文溶剂型干法复合就是经涂胶装置把含有溶剂(一般为乙酸乙酯)的胶粘剂均匀地涂布到一种基材薄膜上,经烘道蒸发溶剂并与另一种基材薄膜经复合钢辊热压、贴合而形成复合薄膜的方式[1]。
它适用于各种基材薄膜,基材选择自由度高,可生产出各种性能的复合膜,如耐热、耐油、高阻隔、耐化学性薄膜等[2]。
其常见生产过程如下[3]:除干法复合外,塑料薄膜的复合技术还有涂布复合法、共挤出复合法和蒸镀复合法。
由于干法复合设备投资少、工艺简单,因而应用最为广泛。
但在复合过程中由于材料选择、工艺控制等多方面的原因,易导致复合薄膜各基材剥离强度低,在使用过程中复合基材之间易出现分层现象,从而导致阻隔性下降,使包装物的保质期缩短、性能下降,或包装物因此而受外界的污染,造成不必要的损失。
干法复合薄膜各基材的剥离强度是其质量控制的关键,以下从几个方面对影响剥离强度的各因素进行简要分析。
1 基材特性对剥离强度的影响干法复合是以各种片材或膜材作基材,用凹版辊在基材表面涂覆一层粘接剂,经过干燥烘道烘干发粘后,再在复合辊上压贴复合。
它广泛适用于 PE、PP 、PET 、PA 、PVA 、PEN 膜、镀铝膜及铝箔等的复合,但由于各种复合基材的性能不同,表面特征也各不相同。
1.1 塑料薄膜表面极性的影响一般情况下,胶粘剂在塑料薄膜表面的吸附和粘合主要是靠两者分子间的作用力来实现的。
大多数塑料薄膜(如PP、PE)的分子结构中基本没有极性基团或只带有弱极性基团,属于非极性聚合物,惰性较强,而胶粘剂多为极性分子结构,两者分子间的作用力非常弱,胶粘剂在塑料薄膜表面的润湿性和附着力会比较差。
【材料】PE薄膜在干式复合中常见的四大问题及解决对策

【材料】PE薄膜在干式复合中常见的四大问题及解决对策在干式复合中经常出现一些如:复合不牢、复合白点、复合成品发涩、热封不住等问题,经过干式复合后,形成这种结果的原因是多方面的,下面仅就由于PE膜的原因造成的这种现象进行一一探讨。
1复合不牢即复合强度很低或为零,完全不能满足客户的要求,造成产品报废。
由于PE膜生产过程的特殊性,表面张力偏低、滑爽剂含量偏高、表面污染等都可能导致复合不牢。
表面张力偏低一般情况下,干式复合用PE膜的表面张力必须达到38dyn/cm以上才可以使用。
实践证明,如果PE膜的表面张力值低于38dyn/cm,就可能造成复合强度偏低的现象。
低于36dyn/cm会形成复合强度极低或为零。
同时,复合强度还与PE膜的厚度有关,如果小于30微米,在36-38dyn/cm时尚可勉强复合,厚度在30-50微米时,表面张力值37dyn/cm时,视其复合结构,如:OPP/PE,复合效果基本可以满足要求。
但厚度大于50微米时,低于38dyn/cm基本不能使用。
下面有几组数据供参考:PE膜在刚刚生产出来时的表面张力值都很大,但随着放置时间的推移,其表面张力值逐渐下降,一般情况下,PE膜可储存3-6个月,但在夏季高温潮湿的季节存放期最好不要超过2个月。
实践证明,PE 膜的表面张力值与周围环境及膜的厚度的关系极为密切,环境温湿度越高,其表面张力值下降越快,薄膜越厚,下降越快。
所以,PE膜的放置一般不宜超过3个月,尤其是梅雨季节,更应注意仓储的通风、透气。
如果由于某种原因放置时间过长,重新使用时,除要进行逐卷检验外,还要根据复合产品的用途综合考虑是否继续使用,以免造成损失。
添加剂的影响PE在聚合或PE膜在成膜时,根据其用途的不同,一般都需加入一定量的添加剂,如防静电剂、滑爽剂、开口剂等。
这些添加剂在成膜后或复合后并不是静止不动的,尤其是滑爽剂。
滑爽剂一般采用芥酸酰胺类或油酸酰胺类,由于滑爽剂造成复合强度下降的原因有两种:PE膜放置时间不久,滑爽剂迁移至PE膜的表面,形成一层很薄的致密层,这层致密层阻隔了粘合剂与PE膜表面的结合,导致粘合剂无法与PE分子接触,复合初粘力很低,随着固化时间的加长,复合强度变化不大,复合强度始终保持很低或为零。
干式复合常见问题探讨
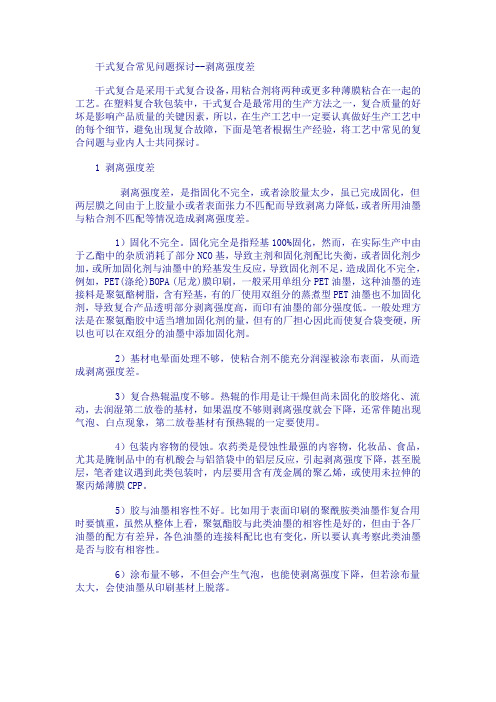
干式复合常见问题探讨--剥离强度差干式复合是采用干式复合设备,用粘合剂将两种或更多种薄膜粘合在一起的工艺。
在塑料复合软包装中,干式复合是最常用的生产方法之一,复合质量的好坏是影响产品质量的关键因素,所以,在生产工艺中一定要认真做好生产工艺中的每个细节,避免出现复合故障,下面是笔者根据生产经验,将工艺中常见的复合问题与业内人士共同探讨。
1 剥离强度差剥离强度差,是指固化不完全,或者涂胶量太少,虽已完成固化,但两层膜之间由于上胶量小或者表面张力不匹配而导致剥离力降低,或者所用油墨与粘合剂不匹配等情况造成剥离强度差。
1)固化不完全。
固化完全是指羟基100%固化,然而,在实际生产中由于乙酯中的杂质消耗了部分NCO基,导致主剂和固化剂配比失衡,或者固化剂少加,或所加固化剂与油墨中的羟基发生反应,导致固化剂不足,造成固化不完全,例如,PET(涤纶)BOPA (尼龙)膜印刷,一般采用单组分PET油墨,这种油墨的连接料是聚氨酪树脂,含有羟基,有的厂使用双组分的蒸煮型PET油墨也不加固化剂,导致复合产品透明部分剥离强度高,而印有油墨的部分强度低。
一般处理方法是在聚氨酯胶中适当增加固化剂的量,但有的厂担心因此而使复合袋变硬,所以也可以在双组分的油墨中添加固化剂。
2)基材电晕面处理不够,使粘合剂不能充分润湿被涂布表面,从而造成剥离强度差。
3)复合热辊温度不够。
热辊的作用是让干燥但尚未固化的胶熔化、流动,去润湿第二放卷的基材,如果温度不够则剥离强度就会下降,还常伴随出现气泡、白点现象,第二放卷基材有预热辊的一定要使用。
4)包装内容物的侵蚀。
农药类是侵蚀性最强的内容物,化妆品、食品,尤其是腌制品中的有机酸会与铝箔袋中的铝层反应,引起剥离强度下降,甚至脱层,笔者建议遇到此类包装时,内层要用含有茂金属的聚乙烯,或使用未拉伸的聚丙烯薄膜CPP。
5)胶与油墨相容性不好。
比如用于表面印刷的聚酰胺类油墨作复合用时要慎重,虽然从整体上看,聚氨酯胶与此类油墨的相容性是好的,但由于各厂油墨的配方有差异,各色油墨的连接料配比也有变化,所以要认真考察此类油墨是否与胶有相容性。
塑料强度的影响因素(二).

玻璃态塑料温度对强度的影响
结晶性塑料温度对强度的影响
外力作用速率
温度一定,外力作用时间越短,链段跟不上外力的变化,
为使材料屈服需要更大的外力,材料的屈服强度提高
Conclution:随温度的降低或拉伸速率的提合物的破坏方式由韧性趋向
脆性破坏
韧性聚苯乙烯的拉伸应力-应变曲线
塑料强度的影响因素(二)
PPT模板下载:/moban/
主要内容
1
添加剂
2
外力作用
向
1
添加剂
加入成核剂,得到小而多的晶体,抗张强度提高,冲击强度
提高。如PP脆,但是加入成核剂,韧性增大,还有用热处理可
以提高强度。
加入增塑剂,抗张强度降低,冲击性能提高。 共聚和共混的影响,如PS很脆,但是与丙烯腈共聚所得聚合物
的抗张强度冲击强度都提高。若进一步与丁二烯聚合,得到抗冲击
强度很高的ABS 树脂
2
外力作用
外力作用速度和温度的影响。
高分子链运动的特点,有明显的时间、温度依赖性-松
弛特性,所以外力作用速度和温度对强度有明显的影响。 温度
当时间一定时,升高温度,链段活动容易,屈服应力降低,
屈服强度低。相反降低温度会使材料的链段运动能力降低,材料 在更高的外力下发生脆性断裂 应力-应变曲线的变化
Ι → ν拉伸速率增大
当应力超过某一数值后,应力 越大,裂纹的产生、发展越快,这 个特定数值称为临界应力。 裂纹的示意图
产生裂纹还需有一个最低伸长率,称为临界伸长率。当超过临界伸长 率时,裂纹即破裂成为裂缝。 聚苯乙烯裂缝尖端部位示意图
谢谢大家
塑料制品的干燥性与干燥技术研究

塑料制品的干燥性与干燥技术研究塑料制品在我们的生活中无处不在,从日常用品到工业材料,它们都离不开干燥技术的应用干燥技术在塑料制品的制造过程中起着至关重要的作用,它直接影响到塑料制品的质量、性能和使用寿命本文将从塑料制品的干燥性入手,详细探讨干燥技术在塑料行业中的应用和研究塑料制品的干燥性塑料制品的干燥性是指塑料在制造过程中对水分的敏感程度水分对塑料制品的影响主要体现在以下几个方面:1.物理性能影响:水分会使塑料制品的物理性能下降,如强度、硬度、韧性等水分的存在会导致塑料制品在加工过程中出现气泡、裂纹等缺陷,影响其使用寿命2.化学性能影响:水分可能会改变塑料的化学稳定性,导致塑料制品的老化、降解,从而影响其性能3.加工性能影响:水分会使塑料的加工性能变差,如影响塑化的均匀性,降低制品的表面光洁度等因此,对塑料制品的干燥性进行深入研究,对于提高塑料制品的质量具有重要意义干燥技术研究干燥技术是塑料制品制造过程中不可或缺的一环干燥技术的目的是去除塑料原料和制品中的水分,以保证塑料制品的质量目前,常用的干燥技术主要有以下几种:1.热风干燥:通过热风将热量传递给塑料原料,使水分蒸发这是一种应用最广泛、效果最好的干燥方法2.红外干燥:利用红外线的热能,使塑料原料中的水分直接蒸发红外干燥具有干燥速度快、能耗低等优点3.真空干燥:在真空环境下,通过降低塑料原料表面的气压,使水分蒸发这种方法适用于那些易受热氧化的塑料4.微波干燥:利用微波的能量,使塑料原料中的水分分子振动,从而产生热量,使水分蒸发微波干燥具有干燥速度快、均匀性好等优点每种干燥技术都有其特点和适用范围,选择合适的干燥技术对于提高塑料制品的质量具有重要意义在未来的研究中,我们需要进一步深入研究塑料制品的干燥性,以及各种干燥技术的原理和应用,以期能够更好地服务于塑料行业,提高塑料制品的质量,减少资源浪费,保护环境这是文章的相关的内容,下一部分将详细探讨各种干燥技术的具体应用和研究干燥技术的具体应用和研究在塑料制品的制造过程中,干燥技术的应用至关重要下面我们将详细探讨几种常用干燥技术的具体应用和研究热风干燥热风干燥是最常用的干燥方法,其原理是通过热风将热量传递给塑料原料,使水分蒸发热风干燥的特点是干燥速度快、效果好,适用于大部分塑料制品的干燥在热风干燥的研究中,主要关注以下几个方面:1.干燥温度:干燥温度的选择对干燥效果有重要影响研究发现,适当的干燥温度可以提高干燥速度,同时保证塑料制品的质量2.干燥时间:干燥时间的长短也会影响塑料制品的质量研究干燥时间对于优化生产效率和保证产品质量具有重要意义3.热风湿度:热风湿度对干燥效果也有很大影响适当降低热风湿度可以提高干燥速度,减少塑料制品中的水分含量红外干燥红外干燥是利用红外线的热能,使塑料原料中的水分直接蒸发红外干燥具有干燥速度快、能耗低等优点,适用于一些特殊要求的塑料制品的干燥红外干燥的研究主要集中在以下几个方面:1.红外波长:不同的红外波长对干燥效果有不同的影响研究红外波长对于优化红外干燥工艺具有重要意义2.红外功率:红外功率的大小直接影响到干燥速度和效果研究红外功率对于确定合适的干燥条件具有重要意义3.塑料原料的种类:不同种类的塑料对红外干燥的响应不同研究不同塑料原料的干燥特性,可以更好地优化红外干燥工艺真空干燥真空干燥是在真空环境下,通过降低塑料原料表面的气压,使水分蒸发这种方法适用于那些易受热氧化的塑料在真空干燥的研究中,主要关注以下几个方面:1.真空度:真空度的大小对干燥效果有重要影响研究发现,适当的真空度可以提高干燥速度,同时保证塑料制品的质量2.干燥时间:在真空环境下,干燥时间的长短也会影响塑料制品的质量研究干燥时间对于优化生产效率和保证产品质量具有重要意义3.温度控制:在真空干燥过程中,温度的控制也很重要适当控制温度可以防止塑料原料的热氧化,保证塑料制品的质量微波干燥微波干燥是利用微波的能量,使塑料原料中的水分分子振动,从而产生热量,使水分蒸发微波干燥具有干燥速度快、均匀性好等优点微波干燥的研究主要集中在以下几个方面:1.微波频率:不同的微波频率对干燥效果有不同的影响研究微波频率对于优化微波干燥工艺具有重要意义2.微波功率:微波功率的大小直接影响到干燥速度和效果研究微波功率对于确定合适的干燥条件具有重要意义3.塑料原料的种类:不同种类的塑料对微波干燥的响应不同研究不同塑料原料的干燥特性,可以更好地优化微波干燥工艺以上对几种常用干燥技术的具体应用和研究进行了详细探讨,希望对塑料行业的生产和发展有所帮助在未来的研究中,我们将继续深入探讨干燥技术的原理和应用,以期能够更好地服务于塑料行业干燥技术的优化与应用为了提高塑料制品的质量,减少生产成本,优化干燥技术具有重要意义以下是一些干燥技术的优化与应用干燥技术的组合应用在实际生产中,为了达到更好的干燥效果,常常将多种干燥技术组合使用例如,可以将热风干燥与红外干燥相结合,先用热风干燥去除塑料原料中的大部分水分,再用红外干燥进行深度干燥,以提高干燥效果干燥技术的自动化控制为了提高干燥效率和保证干燥质量,干燥技术的自动化控制是一个重要的研究方向通过传感器实时监测干燥过程中的温度、湿度等参数,并自动调节干燥条件,可以达到更好的干燥效果干燥技术在特定塑料制品中的应用不同种类的塑料制品对干燥技术的要求不同,因此需要针对特定的塑料制品开发相应的干燥技术例如,对于一些易受热氧化的塑料制品,可以采用真空干燥或微波干燥等低温干燥技术,以防止塑料制品的热氧化干燥技术在塑料制品的制造过程中起着至关重要的作用通过深入研究塑料制品的干燥性和各种干燥技术的原理和应用,我们可以更好地优化干燥工艺,提高塑料制品的质量,减少资源浪费,保护环境在未来的研究中,我们将继续深入探讨干燥技术的优化与应用,以期能够更好地服务于塑料行业,推动塑料行业的发展。
干式复合上胶量的控制与测算

02
改进阶段
随着工业技术的发展,出现了涂胶机等专用设备,实现了涂胶量的精确
控制和自动化生产。
03
创新阶段
近年来,随着环保意识的提高和新型粘合剂的研发,上胶技术不断创新,
出现了水基粘合剂和无溶剂粘合剂等环保型产品,为包装行业的发展提
供了新的动力。
02 干式复合上胶量的影响因 素
基材特性
基材厚度
01
05 干式复合上胶量控制与测 算的挑战与解决方案Βιβλιοθήκη 上胶不均匀问题总结词
上胶不均匀是干式复合工艺中常见的问题,会导致产品质 量下降。
详细描述
上胶不均匀通常是由于涂胶系统设计不合理、涂胶装置调 整不当或涂胶材料性质不均一所致。它会导致薄膜表面涂 胶量差异较大,影响产品的外观和性能。
解决方案
为了解决上胶不均匀问题,可以优化涂胶系统设计,调整 涂胶装置,确保涂胶材料性质均一。同时,定期检查和维 护涂胶系统,确保其正常工作。
降低了不良品率,并提高了生产效率。
案例二:某品牌产品上胶量稳定性提升
要点一
总结词
要点二
详细描述
通过严格控制原材料质量和工艺参数,提高上胶量稳定性
某品牌产品在干式复合过程中,对上胶量的稳定性要求极 高。为了达到这一要求,他们对原材料质量和工艺参数进 行了严格的控制,包括对上胶液的粘度、固含量、PH值等 参数进行精确测量和控制,同时对涂布轮转速、涂布压力 、烘干温度等工艺参数进行优化调整。通过这些措施,他 们成功地提高了上胶量的稳定性,保证了产品质量和客户 满意度。
06 实际应用案例分析
案例一:某公司上胶量控制优化
总结词
通过改进上胶工艺和设备,提高上胶量精度 和稳定性
详细描述
干式复合张力的影响因素与控制措施
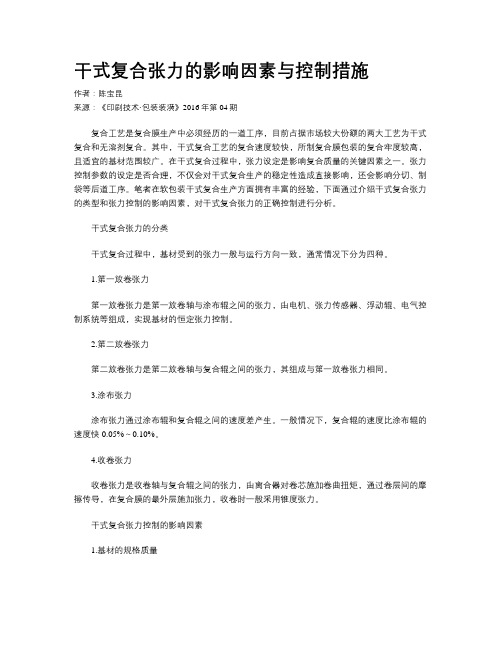
干式复合张力的影响因素与控制措施作者:陈宝昆来源:《印刷技术·包装装潢》2016年第04期复合工艺是复合膜生产中必须经历的一道工序,目前占据市场较大份额的两大工艺为干式复合和无溶剂复合。
其中,干式复合工艺的复合速度较快,所制复合膜包装的复合牢度较高,且适宜的基材范围较广。
在干式复合过程中,张力设定是影响复合质量的关键因素之一。
张力控制参数的设定是否合理,不仅会对干式复合生产的稳定性造成直接影响,还会影响分切、制袋等后道工序。
笔者在软包装干式复合生产方面拥有丰富的经验,下面通过介绍干式复合张力的类型和张力控制的影响因素,对干式复合张力的正确控制进行分析。
干式复合张力的分类干式复合过程中,基材受到的张力一般与运行方向一致,通常情况下分为四种。
1.第一放卷张力第一放卷张力是第一放卷轴与涂布辊之间的张力,由电机、张力传感器、浮动辊、电气控制系统等组成,实现基材的恒定张力控制。
2.第二放卷张力第二放卷张力是第二放卷轴与复合辊之间的张力,其组成与第一放卷张力相同。
3.涂布张力涂布张力通过涂布辊和复合辊之间的速度差产生。
一般情况下,复合辊的速度比涂布辊的速度快0.05%~0.10%。
4.收卷张力收卷张力是收卷轴与复合辊之间的张力,由离合器对卷芯施加卷曲扭矩,通过卷层间的摩擦传导,在复合膜的最外层施加张力,收卷时一般采用锥度张力。
干式复合张力控制的影响因素1.基材的规格质量不同类型的基材,厚度和表面均匀度不同,在干式复合过程中需要的张力自然也不同,通常情况下,较厚基材所需张力较大。
而对于同种基材,当表面均匀度不同时,所需张力也不同,因为基材表面不均匀就会导致厚度不一致,从而使辊间压力出现波动,影响张力控制。
此外,当料卷的复合宽度和重量发生变化时,所需张力也会随之发生变化。
一般情况下,料卷的复合宽度越宽、重量越重,所需张力越大。
一些常用基材的单位张力(单位张力即材料单位宽度所受的张力)如表1所示。
2.料卷卷径的变化随着干式复合生产的进行,料卷卷径会逐渐变小,根据公式M=F×R(其中,M为料卷转动力矩,F为基材所受张力,R为料卷卷径)可知,张力与料卷卷径为反比例关系,即随着干式复合生产的进行,基材所需压力逐渐变大。
CPP,CPE流延膜干式复合过程中容易出现的五大问题及解决办法

CPP,CPE流延膜干式复合过程中容易出现的五大问题及解决办法一、流延膜的基本介绍1.什么是流延膜流延膜,是通过熔体流涎骤冷生产的一种无拉伸、非定向的平挤薄膜。
与一般的吹胀法相比,其特点是生产速度快,产量高,薄膜厚度均匀性以及透明度、光泽性等都非常好。
可分为单层流涎和多层共挤流涎两种方式。
2.流延膜的工艺流程生产工艺过程为原料经挤出机塑化熔融后,熔体经过一个T形狭缝模头挤出,流延铸片经急冷辊冷却, 成型为薄膜。
此法生产速度快,急冷辊一般为表面镀铬、光洁度高的钢辊,而且薄膜透明度高、厚度均匀,薄膜的纵向和横向性能一致。
图 1流延膜工艺流程采用横向定位装置来控制薄膜的平均厚度,通过γ射线测厚区域的监视器反馈信息到模头,调节模唇开合度。
共挤流延膜由2个以上挤出机分别控制物料的挤出量,经分流梭按比例分配后,由T形模头按设定比例流延。
3.流延膜的生产方式CPP/CPE的生产有单层流延与多层共挤流延两种方式。
单层薄膜主要要求材料低温热封性能和柔韧性好。
多层共挤流延膜一般可分为热封层、支撑层、电晕层三层。
•热封层:要进行热封合加工,所以要求滑爽性和抗黏连性好的同时,析出物的量要非常少,单层用量占总膜量的15%左右,要求材料的熔点低,热封温度要宽。
;•支撑层:对薄膜起到支撑作用,增加薄膜的挺性,同时降低成本,首先要有好的刚性,其次要有良好光学性能,薄膜的整体性能基本上靠支撑层来体现,用量占总膜量的70%左右;•电晕层:要进行印刷或金属化处理,要求有适度的表面张力,一般要达到38 dyn/cm 以上( PE 35.6dyn/cm , PP 29.8dyn/cm )。
所以PE,PP薄膜在印刷之前都要进行表面处理来提高其表面张力,对电晕层原料的要求是,既要有一定的抗黏连性,又要严格控制低分子物的含量,因此,树脂中应不含有任何析出的添加剂,用量占总膜量的15%左右。
二、流延膜的干式复合方法的优点由于单种塑料薄膜总是存在着树脂带来的固有优点同时也有它存在的一定的缺点,远不能满足越来越多种商品对包装广泛而严苛的性能要求。
浅谈影响cpp塑料薄膜性能的主要因素

清洁辊压力:辊压力压力大,容易吧清洁辊的形状印在膜上,即薄膜上会面出现清洁辊的斜纹,压力太小,在短时间内就会出现白斑,出现白色粉末剥离,粘在薄膜上,形成硬币般大小的白斑。压力辊在收卷过程中还能起到去除薄膜表面皱褶的作用。
5。原料选择的影响
做复合材料用的CPP薄膜多采用三层共挤流延法的加工工艺,原料以挤出(薄膜)级的聚丙烯树脂为主,要求流动性要好,一般选用溶值为6-13的树脂。
3。速度的影响
挤出速度和挤出机的螺杆转速加工材料的性能,加工温度,以及模头内的阻流器有关,同时也和牵引速度有关。 在其他条件不变的情况下,增加螺杆转速,熔体的挤出速度增加,在同样的加工条件下,加工温度升高,熔体的挤出速度增加。加工材料的熔融指数越大,挤出速度越大,改变分流道的阻流器的位置也可以控制挤出速度的大小,挤出速度调节不当也易引起薄膜厚度的不均匀。挤出速度太快,薄膜透明度降低,爽滑性差,表明横向强度小,在实际生产过程中必须使挤出速度和牵引速度相匹配。
7。流延定型影响
流延薄膜的定பைடு நூலகம்部分由正压风刀和负压风吸气罩,锁边机,流延辊组成,其中负压吸风罩是定型最大的影响装置,
2。冷却温度的影响
冷却温度也是影响薄膜物理机械性能和外观的重要因素,冷却辊的表面温度升高,薄膜定型速度慢,不利于薄膜的晶点的形成,结晶度高,晶体形态会发生变化,造成薄膜雾度上升,光泽度下降,透明度下降,膜的挺度变好,但抗冲击的强度明显下降,冷却温度过高还会导致薄膜(尤其是厚膜)定型失效时有较多的添加剂淅出,产生不规则的白色条纹,影响外观和使用性能。冷却温度过低,薄膜定型速度加快,材料的结晶度下降,透明度和光泽度变好,薄膜变的柔软,表面摩擦系数增大,对牵引和收卷(尤其是2微米的薄膜)的张力较为敏感,牵引和收卷张力过大会导致薄膜变形和严重发粘而无法分切和使用。
聚乙烯膜落标不合格
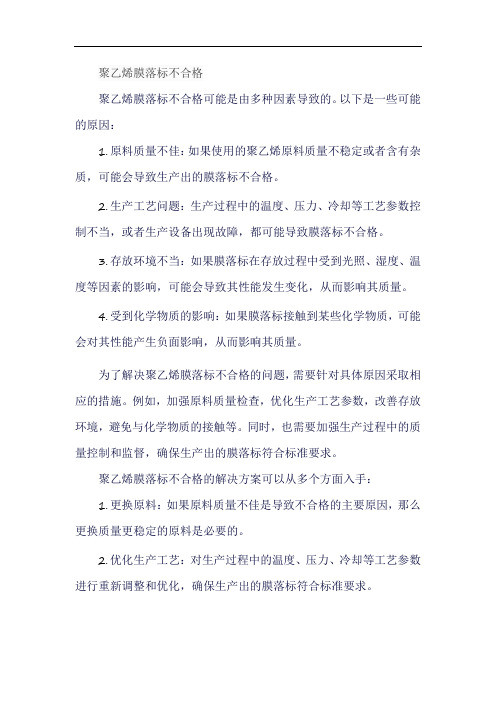
聚乙烯膜落标不合格聚乙烯膜落标不合格可能是由多种因素导致的。
以下是一些可能的原因:1.原料质量不佳:如果使用的聚乙烯原料质量不稳定或者含有杂质,可能会导致生产出的膜落标不合格。
2.生产工艺问题:生产过程中的温度、压力、冷却等工艺参数控制不当,或者生产设备出现故障,都可能导致膜落标不合格。
3.存放环境不当:如果膜落标在存放过程中受到光照、湿度、温度等因素的影响,可能会导致其性能发生变化,从而影响其质量。
4.受到化学物质的影响:如果膜落标接触到某些化学物质,可能会对其性能产生负面影响,从而影响其质量。
为了解决聚乙烯膜落标不合格的问题,需要针对具体原因采取相应的措施。
例如,加强原料质量检查,优化生产工艺参数,改善存放环境,避免与化学物质的接触等。
同时,也需要加强生产过程中的质量控制和监督,确保生产出的膜落标符合标准要求。
聚乙烯膜落标不合格的解决方案可以从多个方面入手:1.更换原料:如果原料质量不佳是导致不合格的主要原因,那么更换质量更稳定的原料是必要的。
2.优化生产工艺:对生产过程中的温度、压力、冷却等工艺参数进行重新调整和优化,确保生产出的膜落标符合标准要求。
3.维护和检修设备:检查生产设备是否存在故障,并进行必要的维修和保养,以确保设备的正常运行。
4.改善存放环境:控制好膜落标的存放环境,避免光照、湿度、温度等因素对其性能产生负面影响。
5.避免化学物质接触:确保膜落标在存放和使用过程中不与任何有害化学物质接触。
6.加强质量控制:在生产过程中加强质量控制和监督,及时发现和纠正问题,确保生产出的膜落标符合标准要求。
7.培训员工:对员工进行必要的培训,提高他们的技能和意识,确保他们能够按照标准要求进行操作和管理。
这些解决方案需要根据具体情况进行选择和实施,同时需要持续监测和改进,以确保聚乙烯膜落标的生产质量得到不断提高。
干式复合出现气泡、起皱、黏结不牢、异味问题及相应的
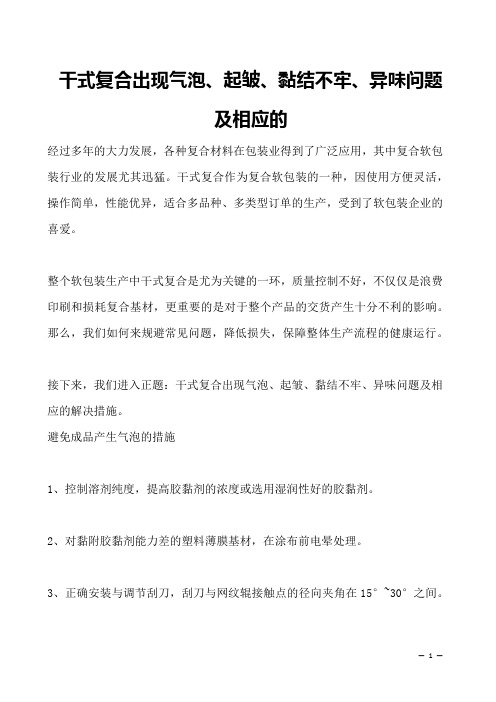
干式复合出现气泡、起皱、黏结不牢、异味问题及相应的经过多年的大力发展,各种复合材料在包装业得到了广泛应用,其中复合软包装行业的发展尤其迅猛。
干式复合作为复合软包装的一种,因使用方便灵活,操作简单,性能优异,适合多品种、多类型订单的生产,受到了软包装企业的喜爱。
整个软包装生产中干式复合是尤为关键的一环,质量控制不好,不仅仅是浪费印刷和损耗复合基材,更重要的是对于整个产品的交货产生十分不利的影响。
那么,我们如何来规避常见问题,降低损失,保障整体生产流程的健康运行。
接下来,我们进入正题:干式复合出现气泡、起皱、黏结不牢、异味问题及相应的解决措施。
避免成品产生气泡的措施1、控制溶剂纯度,提高胶黏剂的浓度或选用湿润性好的胶黏剂。
2、对黏附胶黏剂能力差的塑料薄膜基材,在涂布前电晕处理。
3、正确安装与调节刮刀,刮刀与网纹辊接触点的径向夹角在15°~30°之间。
4、选择合适的烘干温度(80℃~100℃为宜)。
5、提高复合膜的压合温度和复合压力。
6、提高复合加热辊的温度、减小复合角度。
另外,为防灰尘黏附在薄膜的复合表面上,需要清洁网纹辊和薄膜,清洗复合辊,注意环境卫生。
避免成品起皱的措施1、调整基材的平整度。
2、适当降低基材的运行张力,避免其拉伸过大,定型不够。
3、调节复合辊压力,确保复合辊两端压力均匀。
其次,清洗复合辊,更换已损坏的橡胶压辊,也能避免复合成品起皱。
设计时,如果在复合前增加一根预热辊对第二放卷基材表面进行预热,使第二放卷基材与涂布基材复合前的温度基本保持一致,也可防止复合膜冷却后出现卷曲变形。
避免成品黏结不牢的措施1、合理选择黏合剂及其涂布量,准确配制。
2、提高涂胶量,可选用网穴较深的网纹辊,或通过增大橡胶辊压力及减少刮刀与网纹辊的接触压力来增加基材表面的涂胶量。
对于黏附胶黏剂能力差的塑料薄膜基材,在涂布前电晕处理。
3、选用合适的烘干温度或选择耐高温和耐蒸煮性良好的胶黏剂。
4、在确保复合辊两端压力均匀的情况下,适当增加复合压力。
干式复合加工常见故障及解决办法
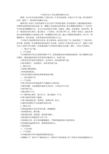
干式复合加工常见故障及解决办法摘要:本文针对包装印刷的干式复合加工中常见的故障,如复合产品气泡、复合强度不良等,提供了一系列相应的解决办法。
随着食品、医药工业的发展和人民生活水平的逐步提高,对包装提出了越来越高的要求,对塑料包装的要求更是如此,单一薄膜已无法满足这些要求,复合薄膜包装得到了广泛应用。
不同性质的薄膜复合后,显示出良好的综合性能,如透水、透氧、抗张强度、热封性等。
复合一般采取共挤出复合、湿式复合、干式复合、挤出复合等工艺。
所谓干式复合,就是在要复合的两种薄膜当中选择适当的一种薄膜涂布粘合剂,通过干燥箱使溶剂挥发,再与另一种薄膜复合,然后收卷,从而形成多层结构的复合方式。
干式复合可选择的材料比较多,复合强度高,适应性比较广泛,因此得到了广泛的应用。
真空袋、蒸煮袋、冷冻袋等要求较高的产品包装,多采用干式复合的方法生产。
现就干式复合加工过程中常出现的一些质量故障产生的原因及解决办法做一浅析,与同行共同探讨。
一、复合产品气泡1.产生原因⑴压辊使用时间过长或使用维护不当,会使胶辊表面局部腐蚀或损伤,复合薄膜经过复合辊时,腐蚀或损伤部位没有受到压辊的压力,形成气泡;⑵溶剂含活性氢的含量较高,反应放出二氧化碳形成气泡;⑶涂布量低于一定限度时,也容易形成气泡。
2.解决办法⑴更换压辊或修复;⑵控制溶剂纯度;⑶对涂布辊进行清洗处理或更换涂布辊。
二、复合强度不良1.产生原因⑴粘合剂及其涂布量选择不当或配比计量有误;⑵溶剂含醇、水或吸湿性基材含水较多,主剂反应不完全;⑶涂布量不足;⑷熟化条件不当;⑸干燥和复合条件(复合压力、复合温度)不当;⑹复合基材表面张力偏低;⑺复合基材添加剂(爽滑剂、抗静电剂)析出;⑻基材表面塑化不良或基材表面污染。
2.解决方法⑴重新选择粘合剂及其涂布量,准确配制;⑵控制溶剂水、醇含量;⑶提高涂布量(或更换、清洗涂布辊);⑷检查涂布压胶辊是否正常工作;⑸更换粘合剂。
粘合剂应随配随用,严格控制剩余粘合剂的使用;⑹控制熟化温度和时间,抑制爽滑剂析出;⑺更换基材。
- 1、下载文档前请自行甄别文档内容的完整性,平台不提供额外的编辑、内容补充、找答案等附加服务。
- 2、"仅部分预览"的文档,不可在线预览部分如存在完整性等问题,可反馈申请退款(可完整预览的文档不适用该条件!)。
- 3、如文档侵犯您的权益,请联系客服反馈,我们会尽快为您处理(人工客服工作时间:9:00-18:30)。
影响塑料薄膜干式符合强度的主要因素一、塑料薄膜表面特性对复合强度的影响1.塑料薄膜表面极性的影响一般情况下, 胶粘剂在塑料薄膜表面的吸附和粘合主要是靠两者分子间的作用力来实现的。
大多数塑料薄膜(如PP、PE)的分子结构中基本没有极性基团或只带有弱极性基团, 属于非极性聚合物, 惰性较强, 而胶粘剂多为极性分子结构, 两者分子间的作用力非常弱, 胶粘剂在塑料薄膜表面的润湿性和附着力会比较差。
一般来说, 塑料薄膜在复端合前都要进行表面处理, 在非极性的薄膜表面引入极性基团,来增强薄膜表面的极性, 提高薄膜和胶粘剂两者分子间的作用力, 从而提高胶粘剂在薄膜表面的吸附力并保证复合膜的粘接强度。
2.塑料薄膜表面自由能的影响塑料薄膜的表面自由能通常是很低的, 胶粘剂在其表面的润湿性和粘合性比较差, 因此, 必须使塑料薄膜的临界表面张力大于或等于胶粘剂的表面张力, 才能够保证胶粘剂在其表面上得到充分的润湿并保证足够的复合强度。
一般来说, 通过对塑料薄膜进行表面处理可以提高其表面能, 大大提高和改进胶粘剂在其表面的润湿性和附着性, 因此, 生产前一定要对薄膜的表面张力进行检测, 一旦发现表面张力太低, 应立即更换薄膜或对薄膜重新进行处理。
而且, 经表面处理过的薄膜的表面张力应当是均匀一致的, 否则也会对复合强度产生一定的影响。
3.塑料薄膜中助剂的影响聚烯烴等薄膜在加工造粒或者制膜的过程中,为了是薄膜具有较好的开口性、抗静电、耐老化、防紫外线照射等性能, 往往要加入一定量的助剂, 如开口剂、抗静电剂、增塑剂、稳定剂等, 而这些助剂又都是低分子物质, 极易析出,随着时间的推移会从薄膜的内部向内外两表面迁移渗出, 形成油污。
时间越长, 迁移出来的助剂的量也就越多, 把胶膜跟薄膜隔离开来, 破坏了原有的粘接状态, 从而使复合强度降低。
因此, 要特别注意薄膜中助剂(特别是爽滑剂)对复合强度的影响。
二、油墨及印刷工艺对复合强度的影响1.油里类型的影响对于塑料凹版里印工艺而言, 由于印刷后还要进行复合, 因此, 必须要采用复合里印油墨, 而决不能用普通的表印油墨。
复合里印油墨跟普通表印油墨的区别主要在于前者跟复合用胶粘剂有着良好的粘接性和亲和性,且残留溶剂少, 利于复合并保证复合强度。
此外, 如果是生产蒸煮包装膜(袋), 则必须采用耐蒸煮的复合里印油墨, 否则可能会使复合强度大幅度降低, 使有油墨处的两层薄膜发生剥离、脱开。
因此, 在实际生产中应当根据承印物材料的类型、内容物的性质、后加工的条件等具体的情况和要求来选择适当类型的复合里印油墨, 这也是保证复合膜粘接强度的一个方面。
2.油墨质最的影响如果油墨本身质量比较差, 或者油墨已经发生了变质, 这当然会影响到它跟薄膜及复合用胶粘剂的亲和性。
比如油墨的附着性比较差, 或者油墨配方中过多地加入了一些有可能会对复合强度产生不利影响的辅料, 致使油墨多的地方粘接牢度低, 而油墨少或无油墨处的粘合牢度反而较好。
因此, 在生产中一定要注意对复合油墨各项性能指标的检测, 并保证其在薄膜表面有较强的附着牢度。
3.油墨干燥性能的影响油墨的干燥性能是油墨的一大主要印刷性能, 在印刷过程中必须保证油墨能够充分干燥。
如果油墨干燥不良, 特别是当油墨中大量地使用了甲苯、丁醇等沸点比较高的溶剂, 而且干燥箱温度设置不当的话, 就会有少量或较大量的溶剂残留在油墨层中, 在经过复合工艺之后, 这些残留溶剂就可能产生许多小气泡, 造成复合膜分层剥离, 影响复合强度。
因此, 在印刷过程中一定要对油墨的干燥性能进行严格的控制, 保证油墨能够充分干燥,选择油墨干燥速度的一般原则是: 在印刷机现有的条件下, 油墨在进行下一印刷色组之前及进行复卷或堆叠之前应该能够充分千燥, 但是在印版上却不能干燥。
4. 印刷工艺的影响在印刷过程中还要注意对印刷速度和干燥温度等工艺条件的控制, 这些也会对油墨中溶剂的挥发干燥产生一定的影响。
一般来说, 在设定干燥箱的温度时, 必须综合考虑印刷速度、油墨的干燥速度、承印物材料的种类以及印刷图案的大小等因素的影响。
如果印刷速度较快, 且印刷机的干燥箱的温度又比较低的话, 油墨中的溶剂可能无法完全挥发掉, 这些残留的溶齐lJ就会形成一些小泡, 从而造成复合好的基材分层, 复合膜的粘接牢度下降。
此时, 应当降低印刷速度, 并适当提高干燥温度。
三、胶粘剂对复合强度的影响1.胶粘剂极性的影响干式复合用胶粘剂一般都含有极性基团, 也就是说分子结构为极性结构。
胶粘剂主体材料的极性基团对复合强度的影响很大, 胶粘剂的粘合强度与胶粘剂主体材料基团的极性大小和数量多少成正比。
对于表面能比较高的复合基材来说, 胶粘剂的极性越强, 则其粘接强度就越大; 相反, 对于低表面能的复合基材而言, 胶粘剂极性的增大往往会因其基团互相约束使链段的扩散能力减弱, 导致胶粘剂的润湿性能变差, 从而使粘接强度降低。
复合所用的塑料薄膜的类型、品牌以及表面处理工艺的不同, 其表面能也不相同, 应当选用不同的胶粘剂。
2.胶粘剂相对分子质量的影响胶粘剂的相对分子质量(主要指聚合度)是很重要的参数, 它对胶粘剂的一系列性能起着决定性的作用。
一般情况下, 粘合强度随着相对分子质量的增大而升高, 升高到一定范围后会逐渐趋于一个定值。
如果相对分子质量继续增大, 由于胶粘剂的润湿性能下降, 反而会使复合强度严重下降。
为了适应高速干式复合工艺, 现在大都采用高固含量、低粘度的胶粘剂, 但低粘度的胶粘剂往往分子质量较小, 内聚力不大, 刚复合时的初粘力很小, 粘接强度差。
因此, 选择高含固量、低粘度、初粘力高的胶粘剂, 是解决这一问题的首选办法。
3.胶粘剂粘度的影响胶粘剂的粘度对胶粘剂的流动性、润湿性、涂胶均匀度等都有着十分重要的影响。
干式复合中应当将胶粘剂的粘度控制在适当的范围之内, 并应当考虑到其粘度在涂布、干燥、复合等过程中的变化, 使之在各个阶段都具有适当的粘度, 保证胶粘剂对复合基材的良好润湿, 降低涂胶过程中气泡和漏涂等故障的发生率, 从而提高复合强度。
4.胶粘剂表面张力的影响胶粘剂的表面张力也是影响胶粘齐U润湿及渗透的一个重要因素, 如果胶粘剂的表面张力比复合用塑料薄膜的表面张力小, 则胶粘剂在复合薄膜表面就能够得到很好的润湿, 也就容易粘合。
也就是说, 表面张力较低的胶粘剂的润湿性能好, 易于涂布、渗透、扩散, 适用范围也比较广。
因此, 在实际生产中, 常常向胶粘剂中加入少量的表面活性剂, 适当降低胶粘剂的表面张力值, 保证胶粘剂的粘接强度。
5.胶粘荆类型、质最的影响必须综合考虑复合基材的种类、性能、后加工条件以及复合材料的最终用途等实际情况, 选择适宜的胶粘剂。
比如蒸煮包装复合膜不能用普通的胶粘剂, 而应当选用耐蒸煮胶粘剂,否则包装袋不耐蒸煮, 经高温蒸煮后剥离强度降低粘接牢度变差, 引起复合膜的分层次脱胶。
另外, 如果胶粘剂的质量比较差, 达不到所要求的标准,或者在使用前已经吸收空气中的水分发生交联固化反应, 生成立体网状结构的不溶物, 也会对复合强度产生不利影响。
干式复合工艺对复合强度的影响四、对复合强度产生直接影响的主要复合工艺参数包括以下几项:1.涂胶量的影响影响涂胶量的因素主要包括以下3 个方面: 一是涂胶用的网纹辊, 其网线数、网穴深浅都直接影响着涂胶量的大小; 二是胶液的浓度; 三是涂布胶辊的软硬程度、压力大小、刮刀的角度及压力大小也会对涂胶量产生一定的影响。
在实际生产中应当根据包装内容物的不同要求来确定合适的涂胶量,涂胶量不足或者过大, 都会对复合膜的粘接强度产生不利的影响。
比如在生产中我厂对于普通包装一般选用165线/英寸,50μm的涂布辊; 对于水煮袋一般选用120线/英寸,8μm涂布辊; 对于蒸煮袋一般选用80线/英寸,120μm涂布辊。
2.胶液的浓度和状态的影响胶液的浓度影响着涂胶量的大小,因此,应当控制好胶液的工作浓度, 一般在30%-40%之间,视具体工艺情况而定。
在配双组分胶粘剂时一定要搅拌均匀, 使其均匀分散, 有利于在复合薄膜上的润湿和粘合。
配制好的胶液还要充分静置脱气, 然后再倒入胶盘中使用, 否则胶液中的气泡也会影响复合膜的粘接强度。
倒胶时要沿胶盘边缘缓慢地倒下, 不要用棒在胶盘内剧烈搅动, 以免胶中混入空气, 影响复合强度。
3.稀释剂的影响目前, 干式复合聚氨醋胶粘剂所使用的稀释剂一般为乙酸乙醋, 而且要求乙酸乙醋中水分和醇的含量不能超过。
2 %。
如果稀释剂的纯度不高, 含有水、醇等活性物质, 那么聚氨醋所含的一NCO基团就会踉水或醇中的活泼氢原子发生反应, 消耗掉一部分固化剂, 造成胶粘剂中主剂与固化剂的实际比例不适当, 使粘接力下降。
同时还会放出C02气体, 使胶液中含有气泡,严重影响复合膜的粘接强度。
因此, 一定要做好稀释剂检测, 保证其纯度。
4.烘道干燥温度、排风量的影响烘道干燥温度的设置应当根据基材的耐热性、复合时基膜的线速度、胶液中溶剂的含量等因素综合进行考虑。
干燥温度太低, 胶粘剂干燥不够充分, 溶剂挥发不彻底, 出现小气泡, 会影响复合强度, 使复合膜分层、脱离。
但如果干燥温度太高的话, 会使涂胶层表皮结膜影响涂层内部溶剂的挥发, 也会造成溶剂的残留和微小气泡的形成, 同样也会造成复合膜粘接强度的下降。
一般来说, 烘道三段的干燥温度分别控制在50-60℃、60-70℃、70-80℃3个梯度之间, 而且还要根据基材的耐热性、复合线速度、所使用的溶剂种类和用量等具体情况来定。
总的来说, 应当使溶剂能够充分干燥, 严格控制溶剂的残留量, 以免影响复合强度, 如果残留溶剂太多的话, 则应适当提高烘道的干燥温度, 降低复合线速度, 并加大排风量。
5. 复合线速度的影响复合线速度的快慢间接影响着胶粘剂中溶剂的挥发。
复合线速度过快,基材通过烘道时间短, 不利于溶剂的挥发, 溶剂干燥不充分还会造成残余溶剂量过多, 从而影响复合膜的复合强度。
如果单靠升高烘道的干燥温度来解决, 则可能会导致基材变形, 因此, 在设置复合线速度时还应考虑到烘道的干燥温度、基材的伸缩性、复合膜的厚度等因素。
欢迎您的下载,资料仅供参考!。