管壳式换热器折流板的设计
管壳式换热器的设计及计算
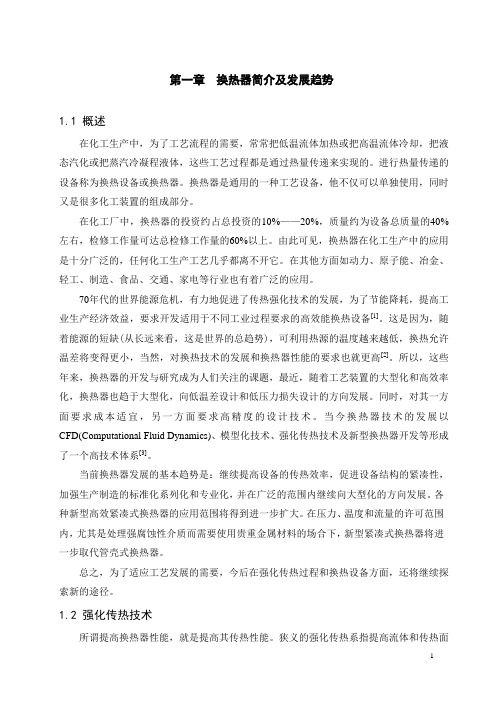
第一章换热器简介及发展趋势1.1 概述在化工生产中,为了工艺流程的需要,常常把低温流体加热或把高温流体冷却,把液态汽化或把蒸汽冷凝程液体,这些工艺过程都是通过热量传递来实现的。
进行热量传递的设备称为换热设备或换热器。
换热器是通用的一种工艺设备,他不仅可以单独使用,同时又是很多化工装置的组成部分。
在化工厂中,换热器的投资约占总投资的10%——20%,质量约为设备总质量的40%左右,检修工作量可达总检修工作量的60%以上。
由此可见,换热器在化工生产中的应用是十分广泛的,任何化工生产工艺几乎都离不开它。
在其他方面如动力、原子能、冶金、轻工、制造、食品、交通、家电等行业也有着广泛的应用。
70年代的世界能源危机,有力地促进了传热强化技术的发展,为了节能降耗,提高工业生产经济效益,要求开发适用于不同工业过程要求的高效能换热设备[1]。
这是因为,随着能源的短缺(从长远来看,这是世界的总趋势),可利用热源的温度越来越低,换热允许温差将变得更小,当然,对换热技术的发展和换热器性能的要求也就更高[2]。
所以,这些年来,换热器的开发与研究成为人们关注的课题,最近,随着工艺装置的大型化和高效率化,换热器也趋于大型化,向低温差设计和低压力损失设计的方向发展。
同时,对其一方面要求成本适宜,另一方面要求高精度的设计技术。
当今换热器技术的发展以CFD(Computational Fluid Dynamics)、模型化技术、强化传热技术及新型换热器开发等形成了一个高技术体系[3]。
当前换热器发展的基本趋势是:继续提高设备的传热效率,促进设备结构的紧凑性,加强生产制造的标准化系列化和专业化,并在广泛的范围内继续向大型化的方向发展。
各种新型高效紧凑式换热器的应用范围将得到进一步扩大。
在压力、温度和流量的许可范围内,尤其是处理强腐蚀性介质而需要使用贵重金属材料的场合下,新型紧凑式换热器将进一步取代管壳式换热器。
总之,为了适应工艺发展的需要,今后在强化传热过程和换热设备方面,还将继续探索新的途径。
化工原理课程设计管壳式换热器的设计
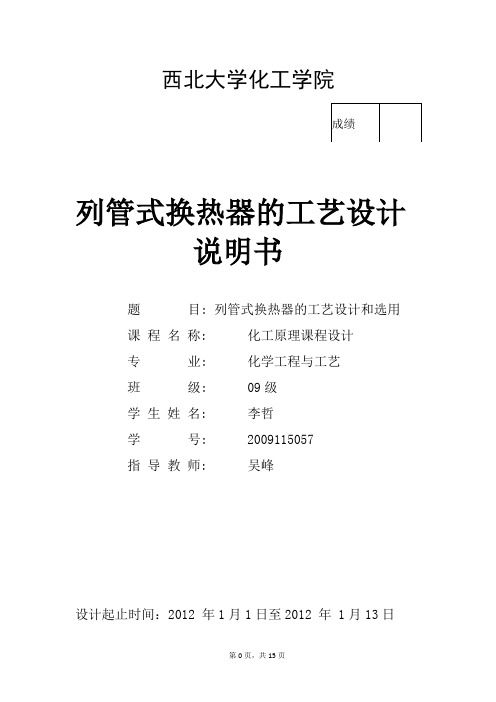
西北大学化工学院列管式换热器的工艺设计说明书题目: 列管式换热器的工艺设计和选用课程名称: 化工原理课程设计专业: 化学工程与工艺班级: 09级学生姓名: 李哲学号: 2009115057指导教师: 吴峰设计起止时间:2012 年1月1日至2012 年 1月13日设计题目:列管式换热器的工艺设计和选用一、设计条件炼油厂用循环水将煤油油从230℃冷却到120℃。
柴油流量位28700kg/h;循环水初温为22℃,经换热后升温到46℃。
换热器的热损失可忽略。
管、壳程阻力压降不大于100kPa。
试设计能完成上述任务的列管式换换热器。
二、设计说明书的内容1、设计题目及原始数据;2、目录;3、设计方案的确定;4、工艺计算及主体设备设计;5、辅助设备的计算及选型;(主要设备尺寸、衡算结果等);6、设计结果概要或设计结果汇总表;7、参考资料、参考文献;目录一.设计任务及设计条件 (3)二.设计方案 (3)1.换热器类型选择 (3)2.流程选择 (3)3.流向选择 (3)三.确定物性数据 (3)四.估算传热面积 (3)五.工艺结构尺寸计算 (3)1.管径及管内流速选择 (3)2.传热管数和传热管程数 (4)3.平均传热温差校正及壳程数 (5)4.传热管排列和分程方法 (5)5.壳体内径 (5)6.折流板 (5)7.其他主要附件 (6)8.接管 (6)9.壁厚的确定、封头 (7)六.换热器核算 (7)(一).热流量核算 (7)1.壳程表面传热系数核算 (8)2.管程表面传热系数核算 (8)3.污垢热阻 (9)4.传热面裕度 (9)(二)传热管壁温及壳体壁温计算 (9)(三)阻力计算 (10)1.管程流体阻力计算 (10)2.壳程流体阻力计算 (10)七.换热器主要计算结果汇表 (11)八.主要符号说明 (11)九.换热器主要结构尺寸图和管子布置图 (12)十.参考文献 (15)一.设计任务及设计条件:用循环冷却水将流量为28700Kg/h 的煤油从230℃降至120℃,冷却水为清净河水,进口温度22℃,选定冷却水出口温度46℃,设计一台列管换热器完成冷却任务。
换热器折流板各种型式的讨论

换热器折流板各种型式的讨论兰州四方容器设备有限责任公司李建仓摘要:本文介绍了换热器所用折流板的几种型式,对其结构及工作形式作了阐述,并将其优点及缺点进行了说明和总结,从而为折流板换热器的设计选型及制造提供了依据和指导。
折流板顾名思义是用来改变流体流向的板,常用于管壳式换热器设计壳程介质流道,根据介质性质和流量以及换热器大小确定折流板的多少。
折流板是列管式换热器中的一个零件可用以起到提高传热系数和支承管束的作用;但由于它结构简单所以往往被设计者所忽视。
现实的情况可以证实到目前为止无论是我国自行设计还是国外引进的设备折流板的结构常是五花八门,其中有些结构既制造复杂又不利于提高传热系数。
其原因在于设计者没有根据具体的传热性质来认真地对它进行分析后再确定具体的结构和尺寸。
本文拟对各种型式折流板的优缺点一一列出并进行对比,提出换热器在什么情况下所适用哪种折流板的一些个人意见和有关同志进行商榷。
折流板有常用折流板和异形折流板之分。
常用折流板主要有弓形和圆盘-圆环折流板,其中弓形又分为单弓形、双弓形和三弓形,如图一:图一异形折流板有:矩形折流板、折流杆型折流板和格栅折流板等,如图二~四:矩形折流板(图二)折流杆换热器示意图(图三)格栅折流板(图四)这些折流板都有各自的优缺点,逐一说明如下;一、弓形折流板。
大部分换热器都采用弓形折流板。
弓形折流板在壳程内的放置形式上下方向排列的形式,用以造成液体剧烈扰动以增大传热系数;左右方向排列的,多数用于卧式换热器,设备中都伴随着有气相的吸收冷凝,以利于冷凝液和气体的流动,当列管是正方形排列时,为了使介质形成湍流以提高换热效果,则采用转角切口。
单弓形折流板主要是为了提高整体的壳程的错流程度,切口的百分数一般为20%~49%;通常为20%~25%,最佳大小为20%,此时单位压降下传热膜系数最高,小于20%(缺口处不布管除外)压降较大;切口超过20%,导致形成流体流速的滞留区,切口过大或过小,都会降低管束的传热性能;为了减小振动,亦可采用缺口处不布管,缺口可减小到15%或者25%左右,其压降只有单弓形的1/3左右。
换热器设计

换热器设计:一:确定设计方案:1、选择换热器的类型两流体温度变化情况,热流体进口温度130°C,出口温度80°C;冷流体进口温度40°C,出口温度65°C。
该换热器用自来水冷却柴油,油品压力0.9MP,考虑到流体温差较大以及壳程压强0.9MP,初步确定为浮头式的列管式换热器。
2、流动空间及流速的确定由于冷却水容易结垢,为便于清洗,应使水走管程,柴油走壳程。
从热交换角度,柴油走壳程可以与空气进行热交换,增大传热强度。
选用Φ25×2.5 mm的10号碳钢管。
二、确定物性数据定性温度:可取流体进口温度的平均值。
壳程柴油的定性温度为T1=130°C,T2=80°C,t1=40°C,t2=65°CT=(130+80)/2=105(°C)管程水的定性温度为t=(40+65)/2=52.5(°C)已知壳程和管程流体的有关物性数据柴油105°C下的有关物性数据如下:ρ=840 kg/m3密度定压比热容C o=2.15 kJ/(kg·k)导热系数λo=0.122 W/(m·k)粘度µo=6.7×10-4N·s/m2水52.5°C的有关物性数据如下:ρ=988 kg/m3密度iC=4.175 kJ/(kg·k)定压比热容iλ=0.65 W/(m·k)导热系数i粘度 µi =4.9×10-4 N·s/m 2三、计算总传热系数1.热流量m 0=95000(kg/h)Q 0= m 0C o Δt o =95000×2.15×(130-80)=10212500kJ/h=2836.8(kw) 2.平均传热温差m t '∆=(Δt 1-Δt 2 )/ln (Δt 1/Δt 2)=[(130-65)-(80-40)]/ln[(130-65)/(80-40)]=51.5(°C) 其中Δt 1=T 1-t 2,Δt 2=T 2-t 1。
管壳式换热器传热计算示例终 用于合并
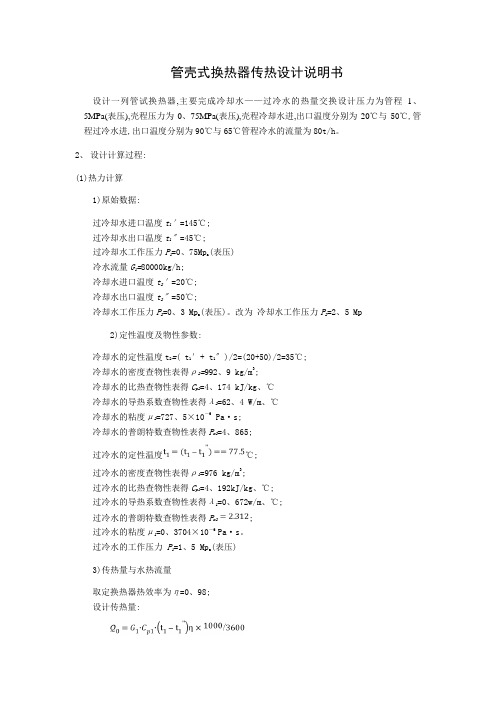
Pa;
取导流板阻力系数:
;
导流板压降:
壳程结垢修正系数: 壳程压降:
Pa ;(表 3-12)
管程允许压降:[△P2]=35000 Pa;(见表 3-10) 壳程允许压降:[△P1]=35000 Pa;
△P2<[△P2] △P1<[△P1] 即压降符合要求。
Pa;
(2)结构设计(以下数据根据 BG150-2011)
m2; 选用φ25×2、5 无缝钢管作换热管; 管子外径 d0=0、025 m; 管子内径 di=0、025-2×0、0025=0、02 m; 管子长度取为 l=3 m; 管子总数:
管程流通截面积:
取 720 根 m2
管程流速: 管程雷诺数: 管程传热系数:(式 3-33c)
m/s 湍流
6)结构初步设计: 布管方式见图所示: 管间距 s=0、032m(按 GB151,取 1、25d0); 管束中心排管的管数按 4、3、1、1 所给的公式确定:
结构设计的任务就是根据热力计算所决定的初步结构数据,进一步设计全部结构尺寸, 选定材料并进行强度校核。最后绘成图纸,现简要综述如下:
1) 换热器流程设计 采用壳方单程,管方两程的 1-4 型换热器。由于换热器尺寸不太大,可以用一台,未考虑 采用多台组合使用,管程分程隔板采取上图中的丁字型结构,其主要优点就是布管紧密。 2)管子与传热面积 采用 25×2、5 的无缝钢管,材质 20 号钢,长 3m,管长与管径都就是换热器的标准管子 尺寸。 管子总数为 352 根,其传热面积为:
3)传热量与水热流量
取定换热器热效率为η=0、98; 设计传热量:
过冷却水流量:
; 4)有效平均温差 逆流平均温差:
根据式(3-20)计算参数 p、R: 参数 P:
管壳式换热器设计参数的选择

管壳式换热器设计参数的选择摘要:文章探讨了管壳式换热器设计过程中管箱、壳体、管束、折流板和防冲板等参数的选择,提出了对设计过程中常见问题的解决方案,可以为此类换热器的设计提供参考。
关键词:管壳式换热器,管箱,壳体,管束,折流板,防冲板,设计Parameters Determine in Shell-Tube Heat Exchanger DesigningZhou Hai-ge*, SUN Ai-jun(China Textile Industry Engineering Institute, Beijing 100037)Abstract: Parameters determine of tube box, shell, bundle, baffle and impingement in shell-tube heat exchanger designing is discussed in this article. Propose the solution to ordinary question in designing. It is can be the reference for this type exchanger designing.Keywords: shell-tube heat exchanger, tube box, shell, bundle, baffle, impingement, design引言管壳式换热器是石化行业中应用最广泛的间壁式传热型换热器,适用范围从真空到超高压(超过100MPa),从低温到高温(超过1100℃),约占市场多于65%的份额[1],因此对于工程设计人员来说,管壳式换热器的设计十分重要。
管壳式换热器的主要组合部件包括壳体、前端管箱和后端结构(含管束)三部分。
管箱、壳体、管束、折流板、防冲板等设计参数决定了换热器的类型、规格及性能特点。
1. 管箱1.1 前端管箱的选择原则GB151中分别列出了A、B、C、N、D五种前端管箱型式[2]。
管壳式换热器设计介绍
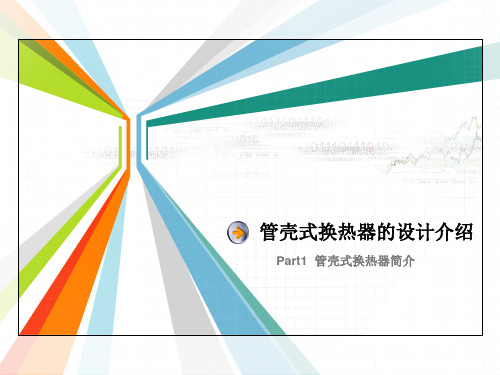
TEMA type
Shell Type
TEMA type Shell Type (1/2)
– E-shell is most commonly used. – F-shell gives pure counter-current flow with two tube passes. – However, longitudinal baffle is difficult to seal with the shell especially when reinserting the shell after maintenance. Therefore, some clients don’t allow to use F-shell. – K-shell is used for pure component boiling service.(kettle reboiler) Longitudinal baffle
Fixed Tubesheet Type Heat Exchanger
U-Tube Type Heat Exchanger
Type of STHE
Floating Head Type Heat Exchanger
Q: Which type is cheapest either H-BEM or HAES?
Type of STHE
固定管板式换热器 Fixed Tubesheet Type
Tubesheets are welded to shell. Simple construction and low cost Shell side mechanical cleaning is impossible. Shell side fluid should be clean and less corrosive (<0.00026m2K/W). Expansion bellows are sometimes required due to metal temp. difference (>60 degC).
管壳式换热器的设计及计算
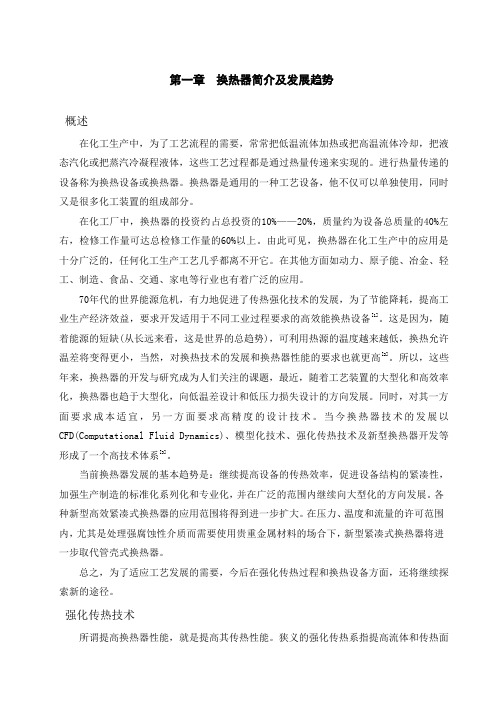
所谓提高换热器性能,就是提高其传热性能。狭义的强化传热系指提高流体和传热面之间的传热系数。其主要方法归结为下述两个原理,即使温度边界层减薄和调换传热面附近的流体,前者采用各种间断翅片结构,后者采用泡核沸腾传热[2]。最近还兴起一种EHD技术,即电气流体力学技术,又称为电场强化冷凝传热技术,进一步强化了对流、冷凝和沸腾传热,特别适用于强化冷凝传热,并适用于低传热性介质的冷凝,因而引起人们的普遍关注[3]。其原理是,对某些不导电液体的表面施以相垂直的电场,使液体表面变得很不稳定,借冷凝液表面的张力作用和在静电场下液膜的不稳定现象使液膜厚度减薄,从而强化冷凝传热。其所需电场耗用的电力很小。人们想尽各种办法实施强化传热,归结起来不外乎两条途径,即改变传热面的形状和在传热面上或传热流路径内设置各种形状的湍流增进器或插入物。
当前换热器发展的基本趋势是:继续提高设备的传热效率,促进设备结构的紧凑性,加强生产制造的标准化系列化和专业化,并在广泛的范围内继续向大型化的方向发展。各种新型高效紧凑式换热器的应用范围将得到进一步扩大。在压力、温度和流量的许可范围内,尤其是处理强腐蚀性介质而需要使用贵重金属材料的场合下,新型紧凑式换热器将进一步取代管壳式换热器。
第一章
在化工生产中,为了工艺流程的需要,常常把低温流体加热或把高温流体冷却,把液态汽化或把蒸汽冷凝程液体,这些工艺过程都是通过热量传递来实现的。进行热量传递的设备称为换热设备或换热器。换热器是通用的一种工艺设备,他不仅可以单独使用,同时又是很多化工装置的组成部分。
在化工厂中,换热器的投资约占总投资的10%——20%,质量约为设备总质量的40%左右,检修工作量可达总检修工作量的60%以上。由此可见,换热器在化工生产中的应用是十分广泛的,任何化工生产工艺几乎都离不开它。在其他方面如动力、原子能、冶金、轻工、制造、食品、交通、家电等行业也有着广泛的应用。
管壳式换热器传热计算示例(终)
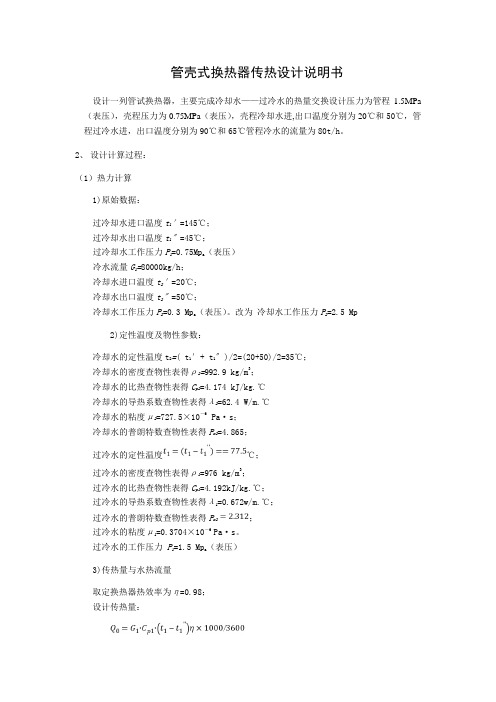
管壳式换热器传热设计说明书设计一列管试换热器,主要完成冷却水——过冷水的热量交换设计压力为管程1.5MPa (表压),壳程压力为0.75MPa(表压),壳程冷却水进,出口温度分别为20℃和50℃,管程过冷水进,出口温度分别为90℃和65℃管程冷水的流量为80t/h。
2、设计计算过程:(1)热力计算1)原始数据:过冷却水进口温度t1′=145℃;过冷却水出口温度t1〞=45℃;过冷却水工作压力P1=0.75Mp a(表压)冷水流量G1=80000kg/h;冷却水进口温度t2′=20℃;冷却水出口温度t2〞=50℃;冷却水工作压力P2=0.3 Mp a(表压)。
改为冷却水工作压力P2=2.5 Mp2)定性温度及物性参数:冷却水的定性温度t2=( t1′+ t1〞)/2=(20+50)/2=35℃;冷却水的密度查物性表得ρ2=992.9 kg/m3;冷却水的比热查物性表得C p2=4.174 kJ/kg.℃冷却水的导热系数查物性表得λ2=62.4 W/m.℃冷却水的粘度μ2=727.5×10-6 Pa·s;冷却水的普朗特数查物性表得P r2=4.865;过冷水的定性温度℃;过冷水的密度查物性表得ρ1=976 kg/m3;过冷水的比热查物性表得C p1=4.192kJ/kg.℃;过冷水的导热系数查物性表得λ1=0.672w/m.℃;过冷水的普朗特数查物性表得P r2;过冷水的粘度μ1=0.3704×10-6 Pa·s。
过冷水的工作压力P1=1.5 Mp a(表压)3)传热量与水热流量取定换热器热效率为η=0.98;设计传热量:过冷却水流量:;4)有效平均温差逆流平均温差:根据式(3-20)计算参数p、R:参数P:参数R:换热器按单壳程2管程设计,查图3—8得温差校正系数Ψ=0.83;有效平均温差:5)管程换热系数计算:附录10,初定传热系数K0=400 W/m.℃;初选传热面积:m2;选用φ25×2.5无缝钢管作换热管;管子外径d0=0.025 m;管子径d i=0.025-2×0.0025=0.02 m;管子长度取为l=3 m;管子总数:取720根管程流通截面积:m2管程流速:m/s管程雷诺数:湍流管程传热系数:(式3-33c)6)结构初步设计:布管方式见图所示:管间距s=0.032m(按GB151,取1.25d0);管束中心排管的管数按4.3.1.1所给的公式确定:取20根;壳体径:m 取Di=0.7m;长径比:布管示意图l/D i=3/0.9=3.3 ,合理选定弓形折流板弓形折流板弓高:折流板间距:m折流板数量:折流板上管孔直径由GB151-2014可确定为 0.0254mm折流板直径由GB151-2014可确定为 0.6955m 7)壳程换热系数计算壳程流通面积:根据式(3-61)中流体横过管束时流道截面积046.0032.0025.016.0233.01o i c1=⎪⎪⎭⎫⎝⎛-⨯=⎪⎪⎭⎫ ⎝⎛-=s d BD A m 2壳程流速:m/s ;壳程质量流速:kg m 2/s ;壳程当量直径:m ;壳程雷诺数:; 切去弓形面积所占比例按 h/D i =0.2查图4-32得为0.145壳程传热因子查 图3-24得为j s =20 管外壁温度假定值 t w1′=45℃ 壁温过冷水粘度 Pa.s粘度修正系数:根据式(3-62)计算壳程换热系数:8)传热系数计算:水侧污垢热阻:r 2=0.000344m 2.℃/w 管壁热阻r 忽略 总传热系数:传热系数比值,合理9)管壁温度计算:管外壁热流密度:W/m2.℃根据式(3-94a)计算管外壁温度:℃误差较核:℃,误差不大;10)管程压降计算:根据式(3-94b)计算管壁温度:℃;壁温下水的粘度:Pa·s;粘度修正系数:;查图3-30得管程摩擦系数:管程数:;管沿程压降计算依据式(3-112):Pa (W=w.ρ)回弯压降:Pa;取进出口管处质量流速:W N2=1750 ㎏/㎡·s; (依据ρw2<3300取 w=1.822m/s) 进出口管处压降(依据 3-113):;管程结垢校正系数:;管程压降:11)壳程压降计算:壳程当量直径:m;雷诺数:;查得壳程摩擦系数:λ1=0.08;(图 3-34)管束压降(公式3-129):Pa;取进出口质量流速: kg/m2·s;( ρw2<2200 取W N2=1000 ㎏/㎡·s) 进出口管压降:Pa;取导流板阻力系数:;导流板压降:Pa壳程结垢修正系数:;(表3-12)壳程压降:Pa;管程允许压降:[△P2]=35000 Pa;(见表3-10)壳程允许压降:[△P1]=35000 Pa;△P2<[△P2]△P1<[△P1]即压降符合要求。
管壳式换热器的设计计算

管壳式换热器的设计计算1.流体流径的选择哪一种流体流经换热器的管程,哪一种流体流经壳程,下列各点可供选择时参考(以固定管板式换热器为例)(1) 不洁净和易结垢的流体宜走管内,以便于清洗管子。
(2) 腐蚀性的流体宜走管内,以免壳体和管子同时受腐蚀,而且管子也便于清洗和检修。
(3) 压强高的流体宜走管内,以免壳体受压。
(4) 饱和蒸气宜走管间,以便于及时排除冷凝液,且蒸气较洁净,冷凝传热系数与流速关系不大。
(5) 被冷却的流体宜走管间,可利用外壳向外的散热作用,以增强冷却效果。
(6) 需要提高流速以增大其对流传热系数的流体宜走管内,因管程流通面积常小于壳程,且可采用多管程以增大流速。
(7) 粘度大的液体或流量较小的流体,宜走管间,因流体在有折流挡板的壳程流动时,由于流速和流向的不断改变,在低Re(Re>100)下即可达到湍流,以提高对流传热系数。
在选择流体流径时,上述各点常不能同时兼顾,应视具体情况抓住主要矛盾,例如首先考虑流体的压强、防腐蚀及清洗等要求,然后再校核对流传热系数和压强降,以便作出较恰当的选择。
2. 流体流速的选择增加流体在换热器中的流速,将加大对流传热系数,减少污垢在管子表面上沉积的可能性,即降低了污垢热阻,使总传热系数增大,从而可减小换热器的传热面积。
但是流速增加,又使流体阻力增大,动力消耗就增多。
所以适宜的流速要通过经济衡算才能定出。
此外,在选择流速时,还需考虑结构上的要求。
例如,选择高的流速,使管子的数目减少,对一定的传热面积,不得不采用较长的管子或增加程数。
管子太长不易清洗,且一般管长都有一定的标准;单程变为多程使平均温度差下降。
这些也是选择流速时应予考虑的问题。
3. 流体两端温度的确定若换热器中冷、热流体的温度都由工艺条件所规定,就不存在确定流体两端温度的问题。
若其中一个流体仅已知进口温度,则出口温度应由设计者来确定。
例如用冷水冷却某热流体,冷水的进口温度可以根据当地的气温条件作出估计,而换热器出口的冷水温度,便需要根据经济衡算来决定。
管壳式换热器原理与设计

管壳式换热器原理与设计管壳式换热器是一种常见的换热设备,广泛应用于化工、炼油、石油化工、动力、核能等多个工业领域。
其工作原理和设计要点如下:工作原理:基本构造:管壳式换热器主要由壳体、管束、管板、折流板、管箱等部件组成。
壳体通常为圆筒形,内部装有平行排列的管束,管束两端固定在管板上。
流体通过管内(管程)和管外(壳程)进行热交换。
热量传递:冷热两种流体分别在管程和壳程中流动,热量通过管壁从高温流体传递给低温流体。
一种流体在管内流动(管程流体),另一种流体在管外,即壳体内流动(壳程流体)。
热量传递遵循热力学第二定律,从高温区自发流向低温区。
强化传热:为了提高传热效率,壳程内常设置折流板,迫使壳程流体多次改变方向,增加流体湍流程度,从而提高传热系数。
管束的排列(如等边三角形或正方形)也会影响传热效率和清洁维护的便利性。
设计要点:流体选择:根据工艺要求决定哪种流体走管程,哪种走壳程。
一般而言,易结垢或腐蚀性的流体走管程便于清洗和更换管束。
材料选择:根据流体的性质(如温度、压力、腐蚀性)选择合适的材料,如不锈钢、碳钢、铜合金等,以确保换热器的耐用性和安全性。
热负荷计算:根据工艺条件计算所需的热负荷,确定换热面积,进而决定管束的数量、长度和直径。
压降考虑:设计时需考虑流体在管程和壳程中的压降,确保泵送能耗合理,避免因压降过大导致系统运行不稳定。
结构设计:包括管板的设计(固定管束的方式)、壳体厚度设计、支撑和悬挂结构设计等,以保证换热器的机械强度和稳定性。
清洗与维护:设计时应考虑换热器的可维护性,如管束的可拆卸性,以及便于清洗壳程内部的结构设计。
综上所述,管壳式换热器的设计是一个综合考虑热工性能、机械强度、材料选择、经济性和可维护性的复杂过程,需要精确的计算和细致的工程设计。
管壳式换热器设计毕业设计

管壳式换热器设计毕业设计目录1 引言 (1)1.1 管壳式换热器的研究 (1)1.2 管壳式换热器的研究趋势 (1)1.3 螺旋板式换热器的研究 (2)1.3.1 螺旋板式换热器国内研究进展 (2)1.3.2 螺旋板式换热器国外研究进展 (2)1.4 本课题的目的和意义 (2)2管壳式换热器的工艺计算 (3)2.2 确定管程软水的物性参数 (3)2.2.1 定性温度 (3)2.2.2 热容 (4)2.2.3 黏度 (4)2.2.4 导热系数 (4)2.2.5 密度 (4)2.3 确定壳程气氨的物性参数 (4)2.3.1 定性温度 (4)2.3.2 热容 (4)2.3.3 黏度 (4)2.3.4 导热系数 (4)2.3.5 密度 (4)2.4 估算传热面积 (4)2.4.1 热负荷Q按大的传热量 (4): (5)2.4.2 平均有效温差tm2.4.3 传热面积 (5)2.5 工艺结构尺寸 (5)2.5.1 决定通入空间,确定管径 (5)2.5.3 确定管程(数)、传热管数n、管长L及壳体内径 (5)2.5.4 拉杆 (5)2.5.5 折流板 (5)2.5.6 画布管图 (6)2.5.7 接管 (6)2.6 换热器核算 (7)2.6.1 传热能力的核算 (7)2.6.2 换热器内流体阻力计算 (9)3 管壳式换热器的结构设计及强度计算 (12)3.1 换热器筒体及封头的设计 (12)3.1.1 筒体设计 (12)3.1.2 封头与管箱设计 (12)3.2 换热器水压试验及其壳体应力校核 (13)3.2.1 压力试验的目的 (13)3.2.2 试验压力及应力校核 (13)3.3 开孔补强 (13)φ管程接管的补强计算 (13)3.3.1 对mm9219⨯φ壳程接管的补强计算 (15)3.3.2对mm480⨯103.4 法兰的选用 (17)3.4.1 筒体法兰的选用 (17)3.4.2 管法兰的选用 (17)3.5 折流板设计 (17)3.6 管板设计 (17)3.6.1换热气的设计条件 (17)3.6.2结构尺寸参数 (17)3.6.3各元件材料及其设计数据 (19)3.6.4设计计算 (19)3.7 支座形式的确定 (30)3.7.1 已知条件 (30)3.7.2 校核 (31)3.7.3 计算支座承受的实际载荷Q (31)M (31)3.7.4 计算支座处圆筒所受的支座弯矩L4 螺旋板式换热器的设计 (31)4.1 传热工艺计算 (31)4.1.1 传热量计算 (32)4.1 .2 冷却水的出口温度 (32)4.1.3 螺旋通道截面积与当量直径de的计算 (32)4.1.4 雷诺数Re和普朗特数P (32)r4.1.5 给热系数α的计算 (33)4.1.6 总传热系数K (33)4.1.7 对数平均温差t∆ (34)m4.1.8 换热器传热面积F (34)4.1.9 螺旋通道长度L (34)4.1.10 螺旋圈数n与螺旋体外径D (34)4.2 流体压力降ΔP计算 (35)4.2.1 按直管压力降的计算公式 (35)4.2.2 按大连工学院等单位推荐的公式计算 (36)4.3 螺旋板的强度、挠度与校核 (36)4.3.1 强度计算 (36)4.3.2 螺旋板的挠度 (37)4.3.3 螺旋板式换热器的稳定性 (38)4.4 螺旋板式换热器的结构尺寸 (38)4.4.1 密封结构 (38)4.4.2 定距柱尺寸 (38)4.4.3 换热器外壳 (38)4.4.4 进出口接管直径 (39)4.4.5 中心隔板的尺寸 (39)4.4.6 水压试验时应力校核 (40)结束语 (41)致谢 (42)参考文献 (43)1 引言换热设备是化工、炼油、动力、能源、冶金、食品、机械、建筑工业中普遍应用的典型设备。
换热器折流板最大间距的 探讨

换热器折流板最大间距的探讨王兰生摘要本文以DN400水-水换热器设计计算为例,说明GB151-89《钢制管壳式换热器》中关于折流板的最大间距应不大于圆筒内直径的规定是不尽合理的,不利于壳程流体压力降的降低,并提出了相应的建议。
关健词折流板最大间距压力降1 问题的提出我们知道,由于管壳换热器的壳程流通截面积通常较管程流通截面积为大,因而除壳程为蒸气冷凝的工况外(冷凝传热系数与流动状态无关),均在壳程设置折流板以提高壳程流体的流速,改变流体的流动方向,使流体沿垂直于换热管中心线的方向流过管束,增加湍流程度,从而提高壳程的传热效果。
同时,折流板对管束又起着支撑作用。
从传热方面考虑,合理的折流板间距不仅应使换热器获得较好的传热效果,以满足给定的传热要求,而且应使壳程的流体压力降不超过允许的最大压力降,以免动力消耗过大。
管壳式换热器工艺设计计算中控制的折流板最小间距为,且不小于50mm。
换热管无支撑的最大折流板间距为171d0.74(d为换1/3~1/2Ds热管外径,mm)。
允许的最大压力降为0.4atm(40.53kPa)[1]。
GB151-89《钢制管壳式换热器》(以下简称GB151)中的3.9.3.2条规定:“折流板的最小间距应不小于圆筒内直径的五分之一,且不小于50mm。
最大间距应不大于圆筒内直径,且满足表3-22的要求”。
表3-22 mm显而易见,GB151规定的折流板最小间距及最大无支撑跨距(防止换热管变形过大和便于安装)与工艺设计基本是一致的,但是却增加了折流板最大间距应不大于圆筒内直径的限制。
这样一来,在管壳式换热器的设计中,就可能会出现工艺专业提出的满足传热要求和压力降限制的折流板间距超出壳体内径,而设备专业由于GB151的规定难以在设计中予以认可的情况。
实际上,笔者在水-水换热器系列的设计中就遇到了这一问题。
下面以DN400水-水换热器的设计计算为例加以说明。
2 设计计算实例2.1 工艺及结构参数文[2]中的水-水换热器系列为国家建筑标准设计,用于一般工业及民用建筑采暖通风系统。
《热交换器原理与设计》管壳式热交换器设计21-23
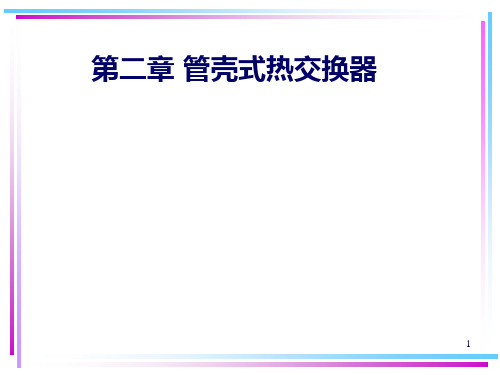
内容 :
管程流通截面积 确定壳体直径 壳程流通截面积
进出口连接管尺寸
一、管程流通截面积的计算 单管程热交换器的管程流通截面积为:
36
At Mt /twt
式中: At——为管程流通截面积,m2;
Mt——为管程流体的质量流量,Kg/s; ρt——为管程流体的密度,Kg/m3; Wt——为管程流体的流速,m/s;
水平 竖直
竖直 转角
(a) (a单 )单弓形 ( 弓a) 形单弓形
转角
过程设备设计
(c()三C)弓三弓形形 (C)三弓形
(b)双(弓 b形 )双(b弓)双形弓形
(d)( 圆d) 盘四弓 -圆形环形(d)四弓形
弓形缺口高度h 应使流体流过缺口时与横向流过管束时的流速相近
缺口大小用弓形弦高占壳体内直径的百分比来表示, 如单弓形折流板,h=(0.20~0.45)Di,最常用0.25Di。 13
作用: a. 减小跨距→防振 b.支承管子→增加管子刚度,防止管子产生过大挠度
形状尺寸: 同折流板
最大无支撑跨距:
换热管外径
10 12 14 16 19 25 32 38 45 57
最大无
钢管
- - 1100 1300 1500 1850 2200 2500 2750 3200
支撑跨距
有色金属 管
750
a1 a2 a3
a2
Dmh1
d0 sn
As a2a3
a3——盘周至圆筒内壁截面减去该处管子所占面积
Dm——环内径D1和盘径D2的算术平均值
sn ——与流向垂直的管间距
50
第三节 管壳式热交换器的传热计算
一、传热系数的确定
经验选用数据
管壳式换热器设计
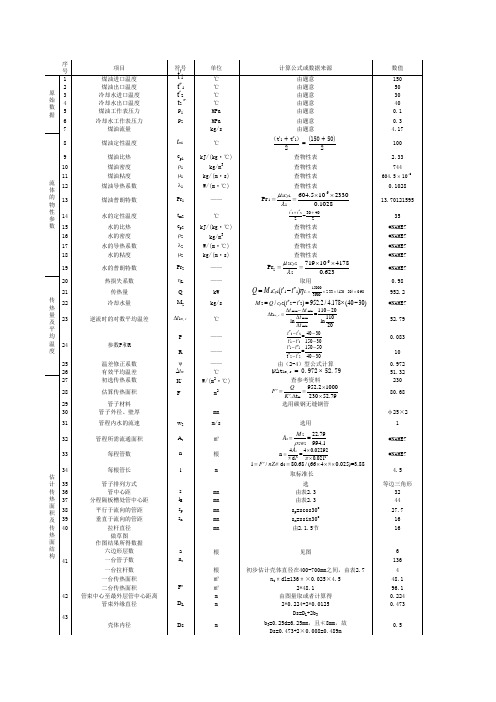
弓形 0.125
120 0.25
17 116 0.0254 112 24
57
折流板直径
Db
58
折流板缺口面积
Awg
59 错流区内管数占总管数的百分比
Fc
60
缺口处管子所占面积
Awt
61
流体在缺口处流通面积
Ab
62 流体在两折流板间错流流通截面积 Ac
63
壳程流通截面积
As
课
程 64
壳程接管直径
72.1/61.85
1 tw1 tm1 K 0( rs,1)tm
0 查图2.35
假定
查物性表
Pi
4 fi
L
wt 2
(
/
)0.14 w2
di 2
4
0.0065
4 4.5 0.021
996 2
(
719 654
106 106
)-0.14
Pr 4 wt2 Zt 4 996 4
2
2
PN 1.5 wt2 1.5 996.951
s
㎡
0.25[0.5 0.473 0.473 0.025 (0.032 0.025)]
0.031
0.032
㎡
As Ab Ac = 0.0260.031
0.028515335
π
mm
按
D2 1
0.0285
计算,并由钢管标准选接近规格
φ203×6
4
排
由图
8
排
Ncw 0.8 h
3.6
sp
1
对
100
2.33 744 60.40.5006100456 0.1028
- 1、下载文档前请自行甄别文档内容的完整性,平台不提供额外的编辑、内容补充、找答案等附加服务。
- 2、"仅部分预览"的文档,不可在线预览部分如存在完整性等问题,可反馈申请退款(可完整预览的文档不适用该条件!)。
- 3、如文档侵犯您的权益,请联系客服反馈,我们会尽快为您处理(人工客服工作时间:9:00-18:30)。
设计
折流板的设计壳式换热器折流板的
管壳式换热器
HTRI2012 上海CC China Meeting
1106
2012-11-06
管壳式换热器折流板的设计
管壳式换热器中折流板的常用形式
----单弓
----NTIW(单弓窗口不布管)
----双弓
----螺旋折流板
----双螺旋折流板
----折流杆(Rod Baffle)
管壳式换热器折流板的设计
•单弓
折流板的阻挡和扰流作用使得流体冲击折流板时改变流向,同时由于流通截面的突变而在弓形折流板缺口处形成流体速度突变和压力突变,且在折流板背面形成回流区,造成压力损失。
管壳式换热器折流板的设计
•单弓
折流板间距与切割率增大,将降低壳程压降, 但同时壳程传热系数减小;折流板间距与切割率减小,将增大壳程传热系数, 但同时壳程压降也急剧增大。
即壳程压降与壳程传热系数同增或同减, 但壳程压降增大或减小的幅度大于壳程传热系数。
为此, 在压降允许范围内, 减小折流板间距与圆缺率, 加强传热效果。
管壳式换热器折流板的设计
•单弓-窗口不布管
减小管子的无支撑间距,牺牲部分换热空间,降低诱导及弹性振动的可能性,同时增加壳程流体的流通量。
管壳式换热器折流板的设计
•双弓
双弓弓形折流板换热器保留了弓形折流板的结构形式, 但增加了切割面积, 使壳程流动形式从单弓时的错流改变成顺错流态, 并克服了流体急剧回弯流动造成的管束震动,在相同压降下即可把流速提高至二倍以上, 从而提高传热速率。
尤其适合用于壳侧流体流量大, 粘度大的场合。
管壳式换热器折流板的设计
•螺旋折流板
螺旋折流板换热器突破了壳程介质流横向垂直和管子相切的传统观念, 流体在壳侧呈连续柱塞状螺旋流动,不会出现传统折流板换热器内的流动死区,并且由于旋流产生的涡与管束传热界面边界层相互作用, 使湍流度大幅度增强, 有利于提高壳侧膜传热系数。
管壳式换热器折流板的设计
•螺旋折流板
连续螺旋折流板换热器的折流板形状是自壳体进口向出口推进的完全螺旋面,介质在壳体内做到相对连续平稳旋转流动。
非连续型螺旋折流板换热器的结构由块椭圆(以椭圆长、短轴为边)或扇
2~4
形(以椭圆短边为对称线截取)自壳程进口处向出口处呈螺旋状首尾相接组装形成。
管壳式换热器折流板的设计
•螺旋折流板的设计
四分之一扇形螺旋折流板组成的一个完整螺旋有四块折流板,单块折流板在换热器壳程横截面上投影为90°。
而三分之一扇形螺旋折流板夹角在螺旋角相同的条件下应大于四分之一扇形螺旋折流板的夹角且在壳体横截面上投影为120°,一个完整螺旋由三块折流板组成。
管壳式换热器折流板的设计
•螺旋折流板的设计
单螺旋结构螺距的1/2 处,平行布置一组同样的螺旋折流板,将原有的单螺旋通道分为平行的两股螺旋通道,就形成了双螺旋结构。
单螺旋双螺旋
管壳式换热器折流板的设计
•螺旋折流与弓形折流板阻力系数和传热系数的对比
管壳式换热器折流板的设计
•不同螺旋角的传热系数和压降的对比
不同螺旋角的壳程传热系数对比不同螺旋角的压降对比
管壳式换热器折流板的设计
•单螺旋与双螺旋的传热系数对比
管壳式换热器折流板的设计
•单螺旋与双螺旋的传热系数对比
管壳式换热器折流板的设计
•单螺旋与双螺旋的压降对比
管壳式换热器折流板的设计
•单螺旋与双螺旋的压降对比
管壳式换热器折流板的设计
•折流杆(ROD型)
若干个折流杆组成折流圈来代替折流板的设计,改善了壳程介质的诱导振动,既起到了对壳程介质的扰动作用,又起到了对换热管的支撑作用,使介质在壳程
中的流动的阻力降低,相同流速下,折流杆换热器比双弓形折流板换热器传热效率高(15%-40%)。
管壳式换热器折流板的设计
谢谢!
上海CC China Meeting
h。