65瓷的低温烧成
低温坯釉一次烧成日用细瓷的研制
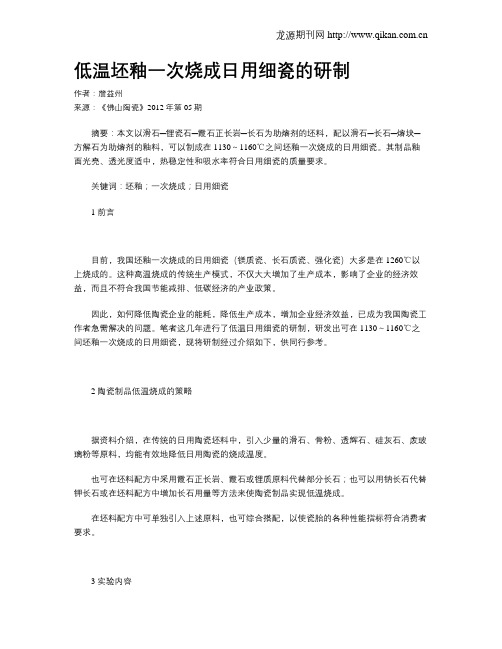
低温坯釉一次烧成日用细瓷的研制作者:詹益州来源:《佛山陶瓷》2012年第05期摘要:本文以滑石─锂瓷石─霞石正长岩─长石为助熔剂的坯料,配以滑石─长石─熔块─方解石为助熔剂的釉料,可以制成在1130~1160℃之间坯釉一次烧成的日用细瓷。
其制品釉面光亮、透光度适中,热稳定性和吸水率符合日用细瓷的质量要求。
关键词:坯釉;一次烧成;日用细瓷1 前言目前,我国坯釉一次烧成的日用细瓷(镁质瓷、长石质瓷、强化瓷)大多是在1260℃以上烧成的。
这种高温烧成的传统生产模式,不仅大大增加了生产成本,影响了企业的经济效益,而且不符合我国节能减排、低碳经济的产业政策。
因此,如何降低陶瓷企业的能耗,降低生产成本,增加企业经济效益,已成为我国陶瓷工作者急需解决的问题。
笔者这几年进行了低温日用细瓷的研制,研发出可在1130~1160℃之间坯釉一次烧成的日用细瓷,现将研制经过介绍如下,供同行参考。
2 陶瓷制品低温烧成的策略据资料介绍,在传统的日用陶瓷坯料中,引入少量的滑石、骨粉、透辉石、硅灰石、废玻璃粉等原料,均能有效地降低日用陶瓷的烧成温度。
也可在坯料配方中采用霞石正长岩、霞石或锂质原料代替部分长石;也可以用钠长石代替钾长石或在坯料配方中增加长石用量等方法来使陶瓷制品实现低温烧成。
在坯料配方中可单独引入上述原料,也可综合搭配,以使瓷胎的各种性能指标符合消费者要求。
3 实验内容3.1实验原料本实验所用原料的化学组成如表1所示。
为了降低生产成本,本实验在满足坯泥工艺性能的同时,选用潮州本地及附近县市的原料,如:黄村粘土、揭阳钾长石、揭西石英、普宁黑粘土等。
所用原料除了表1之外,还采用了部分工业纯的化工原料。
3.2坯釉配方及工艺参数3.2.1坯料配方及工艺参数本文坯泥配方共设计了10个,按助熔剂组成来分可分为五个系列。
即:滑石─霞石正长岩─长石,滑石─锂瓷石─霞石正长岩─长石,锂瓷石─滑石─长石,长石─滑石─骨粉,长石─滑石─硅灰石。
陶瓷烧成

烧成:陶瓷坯体通过高温热处理,发生一系列物理化学变化,矿物组成、显微结构发生变化,最终得到具有某种特定要求的陶瓷制品的工艺过程。
一次烧成:成形、干燥或施釉后的生坯,在陶瓷窑内一次烧成陶瓷产品的工艺路线。
二次烧成:即先素烧后施釉,再釉烧的工艺路线。
分为低温素烧高温釉烧和高温素烧低温釉烧。
坯体加热过程中的物理化学变化:(1)低温阶段——常温~300℃排除干燥残余水分和吸附水,少量收缩或不收缩,气孔率、强度略有增加;基本无化学变化。
(2)氧化分解阶段——300~950℃1化学变化(1)氧化反应:碳素和有机物氧化,黄铁矿(FeS2)等有害物质氧化(2)分解反应:结构水排除;碳酸盐、硫酸盐分解(3)石英晶型转变2 物理变化:(1)重量减轻,气孔率提高,有一定的收缩;(2)有少量液相产生,后期强度有一定提高。
(3)高温阶段——950℃~烧成温度一化学反应1在1050℃以前,继续上述的氧化分解反应并排除结构水;2硫酸盐的分解和高价铁的还原与分解(在还原气氛下);3形成大量液相和莫来石;→大量液相+一次莫来石生成+二次莫来石4新相的重结晶和坯体的烧结;晶粒长大,晶界移动,致密烧结。
二物理变化:气孔率降低,坯体收缩较大,强度提高,颜色变化。
(4)冷却阶段——烧成温度~室温烧成制度包括:温度制度(包括各阶段的升温速率、降温速率、最高烧成温度和保温时间)气氛制度(升温的高温阶段的气氛要求)(氧化、中性、还原)压力制度(对窑内压力的调节)注意:1坯体出现剧烈膨胀/收缩、化学反应、相变的温度区域——应缓慢升降温或适当保温2坯体形状复杂,厚度大,规格尺寸大,入窑水分高——应缓慢升降温或适当保温3低铁高钛坯料(北方)常用氧化气氛烧成;4高铁低钛坯料(南方)常用还原气氛烧成5对于普通陶瓷产品冷却制度一般为:高温阶段应当快速冷却,低温阶段相对缓慢,晶型转变温度附近最慢。
陶瓷胎体的显微结构:晶相、玻璃相、气相。
长石质瓷显微结构中各相:1 莫来石(10-30%)2 玻璃相(40-65%)3 石英(10-25%)4.气孔工艺因素对显微结构的影响:(一)陶瓷原料及配比;(二)原料粉末的特征1、颗粒大小影响成瓷后晶粒尺寸:一般规律:细颗粒粉料制成的陶瓷晶粒小,且均匀。
低温快烧环保日用细瓷
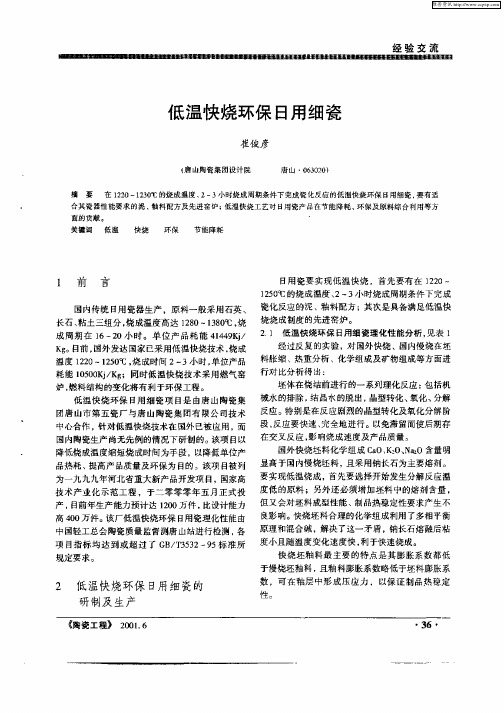
经 验 交 流
低 温快烧 环保 日用 细 瓷
崔俊彦
《 山陶瓷集 团设计院 唐 唐山 - 60 0 0 32
摘
要 在 12 2 0~13  ̄ 20C的烧成温度、 2—3 小时烧成周期条件下完成瓷化反应的低温快烧环保 日用 细瓷 . 要有适 。 快烧 环 保 节能降耗
3 3 拆卸过程 .
拆 卸 主螺母时 的油压 略高于上 紧时 的油压 , 其
高压油 泵将液 压 油打人 油缸 中,使活 塞升 高 , 压力 等级 由高到低 分为 3 MP 、1MP 、1 ̄ a和 2 a 7 a 2/ I P 并使 承压螺母 将 主螺栓 拉长 ,扳 动 主螺母上 紧 扣 , 7Ia拆 卸方法 与上 紧时类 同 ]P ,  ̄ 然后卸去 油压就 完成 了预 紧工作 。同理 , 上油压 , 打 板动主螺母 松扣 , 卸去油 压就完成 拆卸 工作 。
{ 稿 日期 : 0 1一O 收 20 3—0 ) 5
综上所 述 , 温快烧技 术是 陶瓷 节能 和原料 综 低
远 的 意 义
变 质长石岩 、变 质伊 利石 、蒙 脱石类 原料不 能 应用 合 利用及环 境保护 的综合技 术 ,利国利 民 ,具有 深
( 接第 3 上 5页 1 23 . 工 作 原 理
对 比分析 , 陶瓷烧 结过程 中发生 的理化 反 应来 认 从
新 型燃 气 低 温快 烧辊 道 窑 选用 了意 大利 意 比
识快 烧坯釉 料特点 的本质 , 据 国内原 料特点合 理 窑 炉 , 窑炉热工 制度合 理 、 度均匀 、 依 该 温 自动化程 度 保 } 生 热损失小 、 采用 明焰裸烧 , 单位 产 设 计 坯釉 配 方 ,该 厂 摸索 掌握 了低 温快 烧 工 艺 技 高 、 温・ 能好 、
【精品文章】氧化铝陶瓷的低温烧结技术简介

氧化铝陶瓷的低温烧结技术简介
一、氧化铝陶瓷简介
氧化铝陶瓷材料。
具有机械强度高、硬度大、高频介电损耗小、高温绝缘电阻高、耐化学腐蚀性和导热性良好等优良综合技术性能。
同时其生产原料来源广、价格相对便宜、加工制造技术较为成熟等优势,故已被广泛应用于电子、电器、机械、化工、纺织、汽车、冶金和航空航天等行业,成为目前世界上用量最大的氧化物陶瓷材料。
氧化铝陶瓷是一种以α氧化铝为主晶相的陶瓷材料,氧化铝含量一般在75~99.9%之间,通常习惯以氧化铝的含量来分类。
氧化铝的含量在75%左右称为“75瓷”,含量在85%左右称作“85瓷”,含量在99%左右称作“99瓷”。
含量在99%以上的称作刚玉瓷或纯刚玉瓷。
99瓷氧化铝瓷材料主要用于制作高温坩埚、耐火炉管及特殊耐磨材料,如陶瓷轴承、陶瓷密封件及水阀片等;95氧化铝瓷主要用作耐腐蚀、耐磨部件;85瓷中由于常掺入部分滑石,提高了电性能与机械强度,可与钼、铌、钽等金属封接,有的用作电真空装置器件。
氧化铝有α(刚玉型)、β、γ、δ等11种变体,其中主要是α、γ两种晶型,而且只有一种热力学稳定相,即α氧化铝。
而β氧化铝是含碱的铝酸盐(R2O·11Al2O3或RO·6Al2O3)。
它们的结构各不相同。
氧化铝陶瓷
二、氧化铝陶瓷低温烧结技术
由于氧化铝熔点高达2050℃,导致氧化铝陶瓷的烧结温度普遍较高(参见表一中标准烧结温度),从而使得氧化铝陶瓷的制造需要使用高温发热体。
陶瓷材料的低温烧结工艺

陶瓷材料的低温烧结工艺陶瓷材料是一种重要的非金属材料,具有高硬度、高强度、耐高温等特点,被广泛应用于建筑、电子、冶金等领域。
而低温烧结工艺作为陶瓷材料加工的一种重要方法,能够有效提高陶瓷材料的致密度和力学性能。
低温烧结是指在800℃以下进行的陶瓷材料烧结工艺。
相对于高温烧结工艺,低温烧结具有温度低、烧结时间短、能耗低的显著优势。
然而,由于陶瓷材料本身的特性,低温烧结工艺也面临着一些挑战。
本文将从烧结机理、添加剂和工艺参数等方面探讨陶瓷材料的低温烧结工艺。
低温烧结工艺的成功与否,首先要了解烧结机理。
在低温下,陶瓷材料的表面存在着一层氧化皮,这对烧结过程形成一种阻碍。
因此,要采取一定的措施来减小氧化皮对烧结的影响。
常见的方法包括添加剂和控制烧结温度。
添加剂是低温烧结工艺不可或缺的一部分。
添加剂可以分为表面活性剂和粘结剂两大类。
表面活性剂的作用是改变陶瓷颗粒表面的性质,促进颗粒间的结合。
常用的表面活性剂有钛酸酯、磷酸三丙酯等。
粘结剂则是增加陶瓷材料的粘合力,使颗粒聚集更加紧密。
常见的粘结剂有聚乙烯醇、聚氨酯、聚乙烯醇等。
除了添加剂,低温烧结工艺中的温度控制也至关重要。
烧结温度过高会导致颗粒粘结剂熔化,陶瓷颗粒之间无法紧密结合;而烧结温度过低则不能达到预期的烧结效果。
因此,选择适当的烧结温度是保证低温烧结工艺成功的关键。
此外,烧结时间也是影响陶瓷材料烧结效果的重要参数。
一般情况下,烧结时间越长,陶瓷材料的致密度越高,力学性能越好。
然而,过长的烧结时间不仅会增加生产周期,还会造成能源的浪费。
因此,在实际的生产过程中,需要在确保陶瓷材料烧结质量的前提下,尽量缩短烧结时间。
另外,低温烧结工艺还需要考虑颗粒尺寸、烧结气氛和压力等因素对烧结效果的影响。
颗粒尺寸的大小会直接影响到陶瓷材料的烧结致密度,通常情况下,颗粒尺寸越均匀,烧结效果越好。
烧结气氛则会影响到陶瓷材料中氧化物的还原反应,从而影响烧结过程。
而增加压力可以提高陶瓷材料的致密度,但过高的压力也会导致颗粒破碎,影响材料的力学性能。
烧瓷器的窑炉温度

烧瓷器的窑炉温度
烧瓷器的窑炉温度通常参考以下几个阶段:
1. 低温加热:起始温度大约在800摄氏度左右,用于除去陶器中的水分和有机物质。
2. 预烧阶段:将温度逐渐提高到900-1000摄氏度,使白陶器的颜色逐渐变红,并消除一些结构缺陷。
3. 石英变化阶段:温度达到约1200摄氏度时,石英发生相变,从α相变为β相,这个过程被称为石英变化点。
4. 最终烧成阶段:在接近1300-1400摄氏度的高温下,使瓷器充分烧结,并形成坚固的晶体结构。
在这个阶段,还可以添加釉料,使瓷器表面光滑并具有艳丽的色彩。
总的来说,烧瓷器的窑炉温度在800摄氏度至1300摄氏度左右,不同的瓷器类型和工艺会有所差异。
陶瓷爱好者:烧成过程各阶段的主要反应及最大升温速度

陶瓷爱好者:烧成过程各阶段的主要反应及最大升温速度20-150:非化学结构水排出,失重小于2%,窑内必须通风,坯体发生的主要反应及操作重点,建议最大升降速度130度/小时150-500:坯体可以快速升温,比较安全,失去结合水,碳酸盐、黑云母的分解,气体很容易溢出。
500-700:较松散,窑内必须通风,石英在573度有突变,膨胀系数大,但坯体其余组成膨胀率与之相比要小的多。
700-900:可快速加热坯体,比较安全,碳化物燃烧成气体,并排出,坯体气孔增多,可不限制加热速度,因为坯体很薄,而且坯体可渗透性强。
900-1100:在烧成收缩很严重之前要减小制品间的温差,在900度时升温较慢,碳酸盐分解许多气泡在釉面玻化之前必须排出,快速升温会导致石膏粉混入坯体或已经干燥的可溶性盐类集中到一起,坯体炸裂。
1100:上釉产品釉面玻化,釉面玻化温度必须控制在1090-1130度1100-1200:分解出气体必须从未上釉区域顺利排出,坯体内部玻化,釉面接近成熟,坯体继续收缩。
1200-1205:在30分钟内极缓慢升温,使坯体内部玻化,并完全收缩,釉面反应完全。
1205-1200:在30分钟内极缓慢冷却制品,使釉面气泡澄清并且不再产生新气泡,坯体进上步玻化并下垂。
1200-700:快速冷却比较完全,开始时制品高温塑性变性,直到变硬,没有大的体积变形。
700-600:应缓冷,避免在石英晶型转变点573度前后,坯体内外温差不能过大,在大约650度时釉层固化并覆盖在冷却的坯体上。
600-540:应缓冷,避免在石英晶型转变点573度发生惊裂,物化反应应加速,坯体变硬,体积不再变化。
540-490:坯体继续降温,但由于窑内各部分温度下降不够,十分均匀,应小心进行快速冷却。
490-290:可快速冷却制品,已没有惊裂的危险,根据传热条件最大的冷却速率一般在200度。
290-20:可以在空气中自然冷却,没有惊裂的危险。
陶瓷的烧成详细分析

在不过烧的情况下,随着烧成温度的的升高,瓷坯的体积密度增大, 吸水率和显气孔率逐渐减小,釉面的光泽度不断提高,釉面的显微硬 度也随着温度的升高而不断增大。 在烧成温度范围内,适当提高烧成温度,有利于电瓷的机电性能 和细瓷的透光度的提高。 保温是指烧成过程中,达到最高烧成温度范围后,保持一段时间, 或在较低温度下保持一段时间,这段时间称为保温时间,随后进入冷 却阶段。在生产实践中,适当降低烧成温度,延长保温时间,有利于 提高产品品质,降低烧成损失率。保温时间及保温温度对希望釉面析 晶的产品(如结晶釉等艺术釉产品)更为重要。为了控制釉层中析出 晶核的速度、尺寸和数量,这类产品的保温温度往往比烧成温度低得 多,百问世间直接关系到晶体的形成率。 烧成过程中的升降温速度是否恰当,较直观地是看其对制品在烧 成过程中体积热胀冷缩带来的影响(有无变形、开裂)。
陶瓷的烧成过程及烧成制度
陶瓷的烧成过程
烧成过程实质上是若干过程的综合,一般来说,它包括下列五个过程: 1 物料的物理化学变化过程 2 物料的运动过程
3 气体流动过程 4 燃料燃烧的过程 5 传热过程 后四个过程是窑炉为了实现坯体的物理化学变化而建立外在条件(温 度、气氛)的需要。广义来说,烧成有熔制(液态)、煅烧(散料) 以及烧制(成型制品)。狭义来说,烧成就是指成型制品的烧制。
坯体处于弹性状态时,如果加热或冷却过快,则造成坯体内外温 差过大,膨胀不一致,由此引起的热力效应达到了极限值,或因坯体 内外晶型转化不一致而产生的应力达到了极限值,(最常见的是石英 在573的晶型转化),就会使坯体开裂而变成废品。在残余物化结合 水排除阶段,因坯体水分一般都在临界水分以下,不会产生干燥收缩。 但如水分较多,升温过快,水分蒸发过急,则会使坯体炸裂。 坯体在塑性状态时,上述应力受到液相缓冲可能减小或消失。但 当存在较大重力负荷,或因坯体烧成收缩不一致时,坯体就会变形而 成废品,坯体温度愈高,其中液相粘度愈低,就越容易变形。由于烧 成温度不够高或过高,保温时间不足或过长,会导致产品生烧或过烧。 生烧表现为坯体烧结不够,坯体内物理化学变化不充分;过烧则表现 为坯体烧结过分,或发生不希望出现的变化,并常伴随有变形。
低温陶器的烧成温度测定及其初步应用

以往的研究曾错误地认为,陶瓷样品原始烧成温度的 测定依据是,当测试温度低于陶瓷器的原始烧成温度时,样 品的膨胀是可逆的。而测试温度一旦超过其原始烧成温度, 样品内部的气孔将进一步收缩,这样,样品在线性膨胀的同 时,将附加一个不可逆的收缩效应,其热膨胀曲线上便相应 出现一个明显的拐点。人们通常将这一拐点所对应的温度 视为古陶瓷器的原始烧成温度。然而,早在 1969 年,英国牛 津大学 Tite 教授即根据实验指出①,若陶器的原始烧成温度 低于玻璃相形成温度时,利用热膨胀仪测得的热膨胀曲线, 其拐点温度通常近似于出现玻璃相的温度,而不是原始烧 成温度。换句话说,对于原始烧成温度低于玻璃相形成温度 的陶器,采用常规的热膨胀方法,是测不出其原始烧成温度 的;热膨胀曲线上拐点的出现,实际上缘自坯体玻璃相的形
Key words:Low-temperature pottery;Determination of temperature;Thermal expansion method;Original firing
temperature
前言
精确测定古陶瓷的原始烧成温度,是古陶瓷烧成工艺 研究的重要内容。尽管测定陶瓷原始烧成温度的方法有多 种,但相比之下,热膨胀法仍最为精确,因而其应用也最为 广泛。热膨胀法测温的判定依赖于热膨胀曲线。所谓热膨胀 曲线,即由温度变化与受其影响导致的样品长度相对变化 率组成的曲线。这里的样品长度相对变化率用 ΔL/L0 表示, 符号 L0 为样品原长,而 ΔL 为其长度的增量。陶瓷坯体烧 成过程的相关研究指出,当烧成温度一俟达到玻璃化温度 (一般在 700~950℃间,主要取决于坯体原料中熔剂的含 量,如 Na2O、K2O、Fe2O3 和 CaO 等),其坯体内部出现玻璃 相,并伴随着体积收缩,这一收缩效应与温度的升高和时间 的延长成正比①。
氧化铝陶瓷的低温烧结技术

氧化铝陶瓷的低温烧结技术氧化铝陶瓷是一种以Al2O3为主要原料,以刚玉(α—Al2O3)为主晶相的陶瓷材料。
因其具有机械强度高、硬度大、高频介电损耗小、高温绝缘电阻高、耐化学腐蚀性和导热性良好等优良综合技术性能,以及原料来源广、价格相对便宜、加工制造技术较为成熟等优势,氧化铝陶瓷已被广泛应用于电子、电器、机械、化工、纺织、汽车、冶金和航空航天等行业,成为目前世界上用量最大的氧化物陶瓷材料。
然而,由于氧化铝熔点高达2050℃,导致氧化铝陶瓷的烧结温度普遍较高(参见表一中标准烧结温度),从而使得氧化铝陶瓷的制造需要使用高温发热体或高质量的燃料以及高级耐火材料作窑炉和窑具,这在一定程度上限制了它的生产和更广泛的应用。
因此,降低氧化铝陶瓷的烧结温度,降低能耗,缩短烧成周期,减少窑炉和窑具损耗,从而降低生产成本,一直是企业所关心和急需解决的重要课题。
目前,对氧化铝陶瓷低温烧结技术的研究工作已很广泛和深入,从75瓷到99瓷都有系统的研究,业已取得显著成效。
表一是已实现的各类氧化铝陶瓷低温烧结情况。
表中低温烧结氧化铝陶瓷的各项机电性能均达到了相应瓷种的国家标准,甚至中铝瓷在某些技术标准上超过高铝瓷的国标,如中科院上海硅酸盐研究所研制的1360℃烧成的85瓷,其抗弯强度超过99%Al2O3陶瓷的国标,各项电性能都优于95%Al2O3瓷的国标;Al2O3含量分别为90%和95%的低温烧结陶瓷,其机电性能都优于95瓷及99瓷的国标。
纵观当前各种氧化铝瓷的低温烧结技术,归纳起来,主要是从原料加工、配方设计和烧成工艺等三方面来采取措施,下面分别加以概述。
一、通过提高Al2O3粉体的细度与活性降低瓷体烧结温度。
与块状物相比,粉体具有很大的比表面积,这是外界对粉体做功的结果。
利用机械作用或化学作用来制备粉体时所消耗的机械能或化学能,部分将作为表面能而贮存在粉体中,此外,在粉体的制备过程中,又会引起粉粒表面及其内部出现各种晶格缺陷,使晶格活化。
日用陶瓷的低温快速烧成
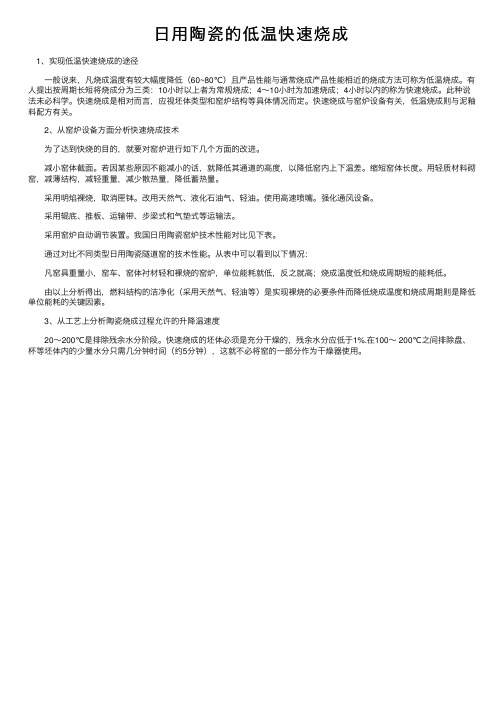
⽇⽤陶瓷的低温快速烧成 1、实现低温快速烧成的途径 ⼀般说来,凡烧成温度有较⼤幅度降低(60~80℃)且产品性能与通常烧成产品性能相近的烧成⽅法可称为低温烧成。
有⼈提出按周期长短将烧成分为三类:10⼩时以上者为常规烧成;4~10⼩时为加速烧成;4⼩时以内的称为快速烧成。
此种说法未必科学。
快速烧成是相对⽽⾔,应视坯体类型和窑炉结构等具体情况⽽定。
快速烧成与窑炉设备有关,低温烧成则与泥釉料配⽅有关。
2、从窑炉设备⽅⾯分析快速烧成技术 为了达到快烧的⽬的,就要对窑炉进⾏如下⼏个⽅⾯的改进。
减⼩窑体截⾯。
若因某些原因不能减⼩的话,就降低其通道的⾼度,以降低窑内上下温差。
缩短窑体长度。
⽤轻质材料砌窑,减薄结构,减轻重量,减少散热量,降低蓄热量。
采⽤明焰裸烧,取消匣钵。
改⽤天然⽓、液化⽯油⽓、轻油。
使⽤⾼速喷嘴。
强化通风设备。
采⽤辊底、推板、运输带、步梁式和⽓垫式等运输法。
采⽤窑炉⾃动调节装置。
我国⽇⽤陶瓷窑炉技术性能对⽐见下表。
通过对⽐不同类型⽇⽤陶瓷隧道窑的技术性能。
从表中可以看到以下情况: 凡窑具重量⼩,窑车、窑体衬材轻和裸烧的窑炉,单位能耗就低,反之就⾼;烧成温度低和烧成周期短的能耗低。
由以上分析得出,燃料结构的洁净化(采⽤天然⽓、轻油等)是实现裸烧的必要条件⽽降低烧成温度和烧成周期则是降低单位能耗的关键因素。
3、从⼯艺上分析陶瓷烧成过程允许的升降温速度 20~200℃是排除残余⽔分阶段。
快速烧成的坯体必须是充分⼲燥的,残余⽔分应低于1%.在100~ 200℃之间排除盘、杯等坯体内的少量⽔分只需⼏分钟时间(约5分钟),这就不必将窑的⼀部分作为⼲燥器使⽤。
- 1、下载文档前请自行甄别文档内容的完整性,平台不提供额外的编辑、内容补充、找答案等附加服务。
- 2、"仅部分预览"的文档,不可在线预览部分如存在完整性等问题,可反馈申请退款(可完整预览的文档不适用该条件!)。
- 3、如文档侵犯您的权益,请联系客服反馈,我们会尽快为您处理(人工客服工作时间:9:00-18:30)。
65高铝瓷的低温烧成
姓名:
班级:
学校:
专业:
65高铝瓷的低温烧成
摘要:本文从原料细度、化学组成以及烧成工艺三方面对氧化铝陶瓷烧结温度的影响进行了概述,简要介绍了几种降低氧化铝陶瓷烧结温度的实用工艺与方法。
关键词:氧化铝陶瓷,低温烧成
1引言:
氧化铝陶瓷是一种以Al2O3为主要原料,以刚玉为主晶相的陶瓷材料。
随着科学技术的发展.特别是能源、空问技术的发展,对材料的性能要求也越来越高,氧化铝陶瓷由于强度高、耐高温、绝缘性好、耐腐蚀.且具有良好的机电性能.广泛应用于电子、机械、化工工业等,如利用其机械强度较高,绝缘电阻较大的性能.可以用作真空器件、电路基板等;利用其耐高温性.可以用做:坩埚、钠光灯管等;利用其稳定的化学性能.可以用作生物陶瓷、催化载体等。
然而,由于氧化铝熔点高达2050℃,导致氧化铝陶瓷的烧结温度普遍较高,从而使得氧化铝陶瓷的制造需要使用高温发热体或高质量的燃料以及高级耐火材料作窑炉和窑具,这在一定程度上限制了它的生产和更广泛的应用。
因此,降低氧化铝陶瓷的烧结温度,降低能耗,缩短烧成周期,从而降低生产成本,一直是企业所关心和急需解决的重要课题。
目前,对氧化铝陶瓷低温烧结技术的研究工作已很广泛和深入,从75瓷到99瓷都有系统的研究,业已取得显著成效。
表一是各类氧化铝陶瓷的烧成情况。
表中低温烧结氧化铝陶瓷的各项机电性能均达到了相应瓷种的国家标准,当前各种氧化铝瓷的低温烧结技术,归纳起来,主要是从原料加工、配方设计和烧成工艺等三方面来采取措施。
2实验
实验研究以氧化铝含量为65%的高铝瓷为对象。
烧成温度控制在1260 ~1300℃,强度大于240Mpa。
2.1实验原料
本实验原料采用工业氧化铝(纯度99.8%,平均粒径5um)和CaO-MgO-SiO2玻璃相(CMS)分别按30∶9∶21的质量比称量混合的添加剂作为烧结助剂,以及TiO2(纯度99%,平均粒径2.7μm) 。
将氧化铝粉料和各个含量的烧结助剂一起用高纯的氧化铝小球湿磨48h,使用激光粒度测试仪检测粒径,粒径达到5um后烘干,加入PVA造粒,然后在50MPa条件下压力成型,然后在电炉中烧结,保温3h。
2.4实验结果及分析
1.利用Archimedes法测量试样的体积密度,计算样品相对密度;
2.测定试样的吸水率
3.测定试样的抗压强度
通过各项数据分析可得65氧化铝烧结情况较为理想,抗压强度达到预期指标,低温烧结氧化铝陶瓷的各项机电性能均达到了相应瓷种的国家标准。
3讨论
高温氧化物较难烧结,重要原因之一,就在于:它们有较大的晶格能和较稳定的结构状态,质点迁移需要较高的活化能.采用晶粒小、比表面积大、表面活性高的超细单分散氧化铝粉料,初期烧结基本在一次颗粒问进行.由于颗粒间扩散距离短.所以仅需较低的烧结温度和烧结活化能。
可以采用两次球磨工艺制粉。
在烧结氧化铝陶瓷时加入少量TiO2添加剂,形成低熔点的玻璃相,粘接分散的晶相,添加剂与烧结物形成固溶体时.将使晶格畸变而得到活化,故可降低烧结温度.生成的玻璃相沿各颗粒的接触界面分布,原子通过液体扩散传输。
扩散系数大.使烧结速度加。
4结论
对65高铝瓷烧结原料超细化,加入适量的烧结助剂使65瓷的烧结温度显著降低,在1260℃下烧结良好,各项机电性能均达到了相应瓷种的国家标准,样品强度大于240Mpa,达到预期标准。
5参考文献
[1]曹南萍,王仲军,南小英等.降低高铝瓷烧成温度的研究[J].硅酸盐通报,2006,25(4):150-155.DOI:10.3969/j.issn.1001-1625.2006.04.033.
[2]蔡晓峰.氧化铝陶瓷的低温烧结技术[J].佛山陶瓷,2003,(11):1-3.DOI:10.3969/j.issn.1006-8236.2003.11.001.
[3]史国普,王志,侯宪钦等.低温烧结氧化铝陶瓷[J].济南大学学报(自然科学版),2007,21(1):17-19.DOI:10.3969/j.issn.1671-3559.2007.01.005.
[4]孟德安,马慧侠,刘高兴等.降低95氧化铝瓷烧成温度的研究[J].现代技术陶瓷,2002,23(3):11-13.DOI:10.3969/j.issn.1005-1198.2002.03.003.
[5]曹南萍,南小英,黎荣奎等.降低高铝瓷烧成温度势在必行[C].//2005年景德镇高技术陶瓷国际论坛论文集.2005:4-12.
[6]刘君昌,吴伯麟.烧结助剂对高铝陶瓷烧成温度及磨损性能的影响[J].陶瓷,2014,(2):16-19.DOI:10.3969/j.issn.1002-2872.2014.02.002.
[7]漆虹,范益群,徐南平等.保温时间对低温烧成多孔氧化铝支撑体性能影响的研究[J].膜科学与技术,2001,21(3):5-10.DOI:10.3969/j.issn.1007-8924.2001.03.002.
[8] 黄晓巍1液相烧结氧化铝陶瓷的致密化机理[J]1材料导报,2005(19):393-3951
[9] 陆佩文1无机材料科学基础[M]1武汉:武汉工业大学出版社,1996。