Mastercam数控编程实例介绍
mastercamX3车床自动编程
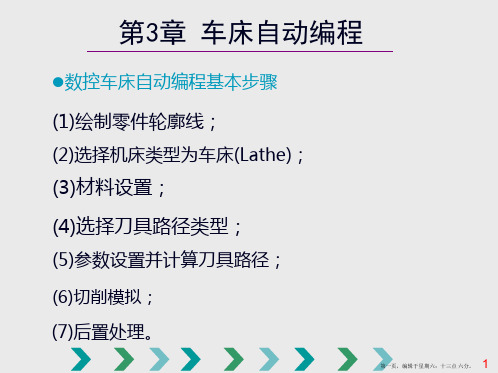
15 第十五页,编辑于星期六:十三点 六分。
16 第十六页,编辑于星期六:十三点 六分。
刀具的引入和退出
17 第十七页,编辑于星期六:十三点 六分。
刀具的切入参数
18 第十八页,编辑于星期六:十三点 六分。
19 第十九页,编辑于星期六:十三点 六分。
六、粗车圆弧面
20 第二十页,编辑于星期六:十三点 六分。
21 第二十一页,编辑于星期六:十三点 六分。
22 第二十二页,编辑于星期六:十三点 六分。
23 第二十三页,编辑于星期六:十三点 六分。
24 第二十四页,编辑于星期六:十三点 六分。
25 第二十五页,编辑于星期六:十三点 六分。
二、绘制零件轮廓线
工件原点 46 第四十六页,编辑于星期六:十三点 六分。
三、选择机床类型
点击菜单【机床类型】→【车床】→【默认】。
四、定义毛坯形状与尺寸
47 第四十七页,编辑于星期六:十三点 六分。
五、生成刀具路径 (1)粗镗内孔
48 第四十八页,编辑于星期六:十三点 六分。
(2)精镗内孔
六、切削模拟
55 第五十五页,编辑于星期六:十三点 六分。
七、后置处理,生成数控程序
56 第五十六页,编辑于星期六:十三点 六分。
练习题目
毛坯φ60×150
练习1
57 第五十七页,编辑于星期六:十三点 六分。
螺纹的编程大径为Ф48,编程小 径为Ф46。
毛坯φ85×102
练习2
58 第五十八页,编辑于星期六:十三点 六分。
四、车端面
9 第九页,编辑于星期六:十三点 六分。
设置刀具和参数
基于MasterCAM9.1的曲面加工编程实例
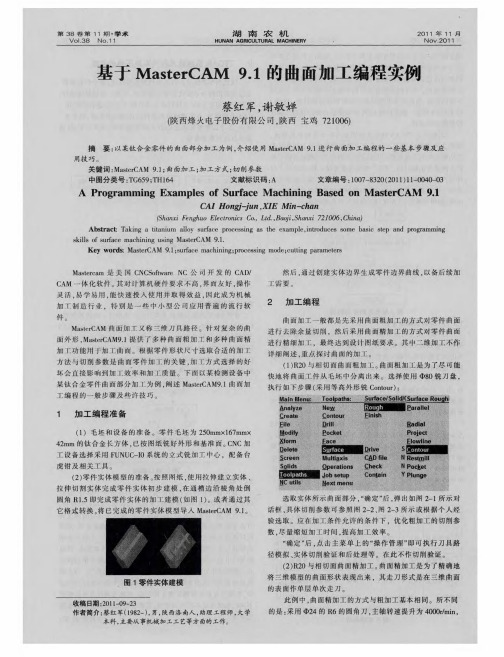
[ 李云龙 , 3 】 曹岩. a e a . 数控加工实例精解【 ] b : 工业 M s r m 91 tc M 京 机械
出版社 . 0 4 2o.
( 上接 第 3 9页)
『1 M. 北京: 北京航 空航天大学 出版社 ,0 7 20.
3 结语
T C N 系统 的 应 用 前 景 很 大 ,中 国 正 处 在 高 速 发 展 阶 YA 段 。 民 拥 有 的 汽 车 数 据 逐 年 上 升 , 通 事 故 率 也 相 对 增 加 居 交
7 9.
给交通造成 了很大影 响 , 系统 对于构建智能交通 系统是个 此
很 好 的 设想 , 有 重 要 的 科 研 意 义 和使 用 应 用价 值 。 具
参 考 文 献
【饶运涛 , 1 】 邹继军 , 宏, 勇芸. 王进 郑 现场总线 C N原理与应用技术 A
几 乎 一 以完 成 常 规 的所 有 简 单 和 复 杂 形 状 零 l I 件 的力l , lI 同 内外 市场 得 到 广 泛 学 和 膻 J 以 上所 H。 _
介 绍 的 Mat C M 91的应 用 技 术 , 对 实 际 加 工生 产 , 』 srA . e 针 埘
【饶运 涛. 间触发的 C N网络设计【. 2 】 带时 A J计算机 工程 ,083(1 】 20 , 2) 4
2 6 21 . 1 — 8
f 周震, 3 】 杨正林. 时间触发 c N T C N J 气 电器,0 5 A —_ A [0 车 r 】 20. 【 卞卡明, 4 】 黎光显 , 秦利升.F A T C N的硬件 实现及在智能压路机上 的 应.[ . e J 中国工程机械学报, 0 . 1 2 7 0
4 2
mastercam车床圆球编程实例-概述说明以及解释
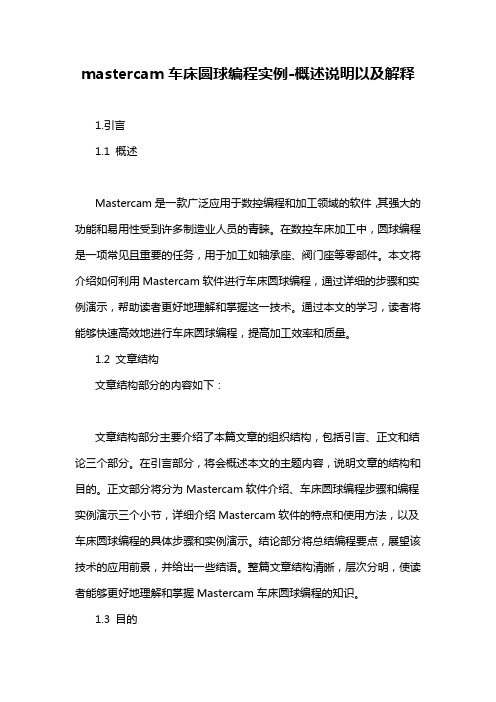
mastercam车床圆球编程实例-概述说明以及解释1.引言1.1 概述Mastercam是一款广泛应用于数控编程和加工领域的软件,其强大的功能和易用性受到许多制造业人员的青睐。
在数控车床加工中,圆球编程是一项常见且重要的任务,用于加工如轴承座、阀门座等零部件。
本文将介绍如何利用Mastercam软件进行车床圆球编程,通过详细的步骤和实例演示,帮助读者更好地理解和掌握这一技术。
通过本文的学习,读者将能够快速高效地进行车床圆球编程,提高加工效率和质量。
1.2 文章结构文章结构部分的内容如下:文章结构部分主要介绍了本篇文章的组织结构,包括引言、正文和结论三个部分。
在引言部分,将会概述本文的主题内容,说明文章的结构和目的。
正文部分将分为Mastercam软件介绍、车床圆球编程步骤和编程实例演示三个小节,详细介绍Mastercam软件的特点和使用方法,以及车床圆球编程的具体步骤和实例演示。
结论部分将总结编程要点,展望该技术的应用前景,并给出一些结语。
整篇文章结构清晰,层次分明,使读者能够更好地理解和掌握Mastercam车床圆球编程的知识。
1.3 目的本文的主要目的是通过对Mastercam车床圆球编程实例的介绍和演示,帮助读者了解和掌握Mastercam软件的使用技巧,特别是在车床圆球编程方面的操作步骤和注意事项。
通过具体的编程实例,读者可以深入了解Mastercam软件的功能和运用,从而提升自己在数控编程领域的技能水平。
同时,本文也旨在激发读者对数控编程的兴趣,帮助他们在实际工作中更加灵活和高效地应用Mastercam软件,提升生产效率和质量水平。
希望通过本文的介绍和演示,读者能够更加深入地了解Mastercam 软件在车床圆球编程方面的应用,为其日后的工作和学习提供有益的参考和支持。
2.正文2.1 Mastercam软件介绍Mastercam是一款专业的CAD/CAM软件,是美国CNC Software Inc.公司研发的数控编程软件。
Mastercam数控编程案例教程(2021版)教学课件6任务六 烟灰缸编程加工

生成外形铣削刀路
6.5 刀路编制
6.5.10 实体模拟加工
模拟结果
6.6 小结
本章结合零件图形特点灵活地生成了较多的刀路辅助曲 线与曲面,从而生成更加流畅、优美的刀路,在编制刀 路的应用上具有较高的技巧性。相信读者通过本例学习 后,在处理如何根据图形特点生成辅助曲线与曲面的能力 有一个大的提高。
《MasterCAM数控编程案例教程(2021版)》“十二五”职业教育国家规划教材
任务六
烟灰缸编程加工
6.1 任务目标
➢ 提高区域划分与刀具路径的控制能力, 特别是干涉曲面的应用。
➢ 掌握如何根据零件形状特点创建辅助曲 线与曲面,从而生成更加流畅、优美的 刀路。
6.2 任务导入
打开随书光盘“源文件/cha06/烟灰缸.mcx-5”,图形如下图所示。
6.5 刀路编制
6.5.4 等高外形精加工
技术指导:等高外形精加工的最大 切削深度是Z方向的间距,在加工平 缓曲面时,Z方向间距不变的情况下 ,刀路的水平步距会随着平缓度的 增加而变大。如果被加工的曲面比 较平缓时,刀路就会变得疏一些, 为避免这种现象的发生,可选用等 高外形精加工刀路所提供的浅平面 加工刀路,将【分层铣深的最小切 削深度】设置得更小,对该平缓区 域增加刀路,能有效地保证较平缓 曲面部位的加工效果,这里 R2.5mm曲面圆弧过渡属于较平缓 的区域。
6.7 提高练习
打开随书光盘“练习文件/cha06/6-2.mcam”,如下图所示。
提高练习零件
6.3.2 工艺分析 该零件曲面造型变化大且不连续,对刀路的连续生成造成了一定的困难。
如果根据零件图形具有对称性的特点,将其划分为四个区域进行镜像加工,生成 的刀路将不连续,刀路也变得复杂,实践证明这种方法生成的NC程序很大,加 工时间长,表面质量差。因此这里将根据图形特点创建一些辅助曲线与曲面从而 更好地控制刀路的生成,以达到良好的加工效果。
数控自动编程Mastercam实例
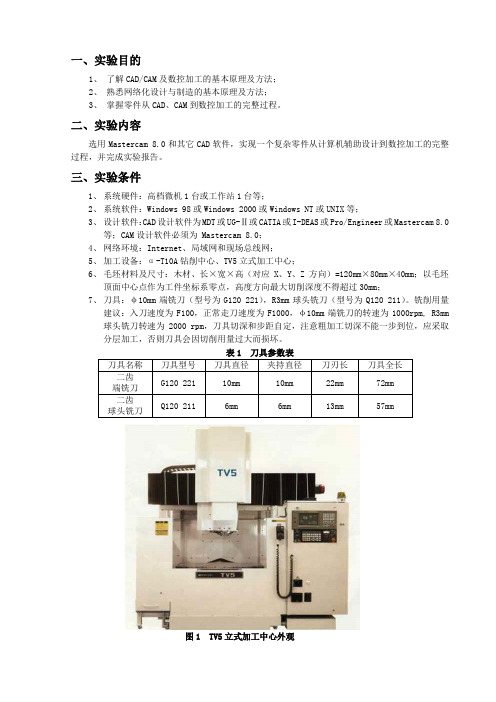
一、实验目的1、了解CAD/CAM及数控加工的基本原理及方法;2、熟悉网络化设计与制造的基本原理及方法;3、掌握零件从CAD、CAM到数控加工的完整过程。
二、实验内容选用Mastercam 8.0和其它CAD软件,实现一个复杂零件从计算机辅助设计到数控加工的完整过程,并完成实验报告。
三、实验条件1、系统硬件:高档微机1台或工作站1台等;2、系统软件:Windows 98或Windows 2000或Windows NT或UNIX等;3、设计软件:CAD设计软件为MDT或UG-Ⅱ或CATIA或I-DEAS或Pro/Engineer或Mastercam 8.0等;CAM设计软件必须为 Mastercam 8.0;4、网络环境:Internet、局域网和现场总线网;5、加工设备:α-T10A钻削中心、TV5立式加工中心;6、毛坯材料及尺寸:木材、长×宽×高(对应X、Y、Z方向)=120mm×80mm×40mm;以毛坯顶面中心点作为工件坐标系零点,高度方向最大切削深度不得超过30mm;7、刀具:φ10mm端铣刀(型号为G120 221),R3mm球头铣刀(型号为Q120 211)。
铣削用量建议:入刀速度为F100,正常走刀速度为F1000,φ10mm端铣刀的转速为1000rpm, R3mm 球头铣刀转速为2000 rpm,刀具切深和步距自定,注意粗加工切深不能一步到位,应采取分层加工,否则刀具会因切削用量过大而损坏。
表1 刀具参数表图1 TV5立式加工中心外观图2 α-T10A钻削加工中心外观四、实验过程1、用Mastercam 8.0或其它CAD软件完成型面或型腔零件的建模,通常要用到实体造型和曲面造型功能。
若用其它CAD软件建模,则应将零件模型转化成Mastercam 8.0能读取的文件格式存盘(建议用IGES格式);2、要求统一选用Mastercam 8.0的MILL模块刀具生成路径和NC程序;1)加工工艺规划:粗加工、半精加工、精加工,中间还需穿插清根工序;2)选取加工刀具并设置刀具参数;3)设定毛坯尺寸、材料以及工件坐标系;4)设置刀具加工形式和切削用量;5)编制刀具路径;6)加工过程仿真和修改参数。
基于MasterCAM—X的典型零件数控加工编程
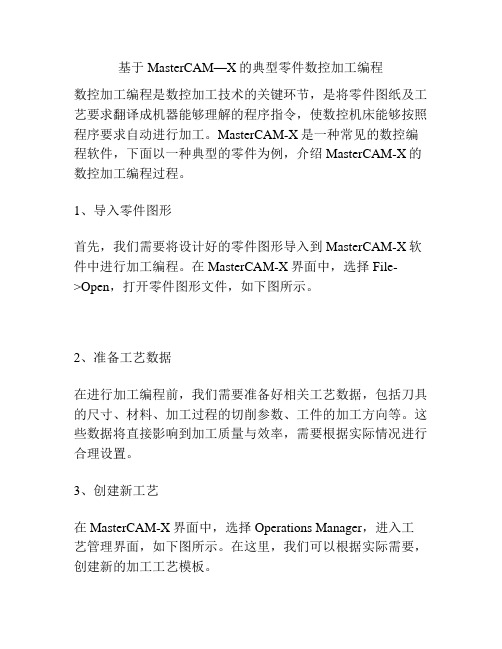
基于MasterCAM—X的典型零件数控加工编程数控加工编程是数控加工技术的关键环节,是将零件图纸及工艺要求翻译成机器能够理解的程序指令,使数控机床能够按照程序要求自动进行加工。
MasterCAM-X是一种常见的数控编程软件,下面以一种典型的零件为例,介绍MasterCAM-X的数控加工编程过程。
1、导入零件图形首先,我们需要将设计好的零件图形导入到MasterCAM-X软件中进行加工编程。
在MasterCAM-X界面中,选择File->Open,打开零件图形文件,如下图所示。
2、准备工艺数据在进行加工编程前,我们需要准备好相关工艺数据,包括刀具的尺寸、材料、加工过程的切削参数、工件的加工方向等。
这些数据将直接影响到加工质量与效率,需要根据实际情况进行合理设置。
3、创建新工艺在MasterCAM-X界面中,选择Operations Manager,进入工艺管理界面,如下图所示。
在这里,我们可以根据实际需要,创建新的加工工艺模板。
4、建立刀具库刀具是数控加工中重要的工具,可以直接影响到加工质量和效率。
在MasterCAM-X中,我们可以使用刀具库,快速方便地选择需要的刀具。
选择Tool Manager,进入刀具管理界面,如下图所示。
在刀具管理界面中,可以设置切削刀具的相关参数,包括刀具直径、长度、刀尖半径、速度、进给量等。
接着,在工艺管理界面中新增工艺步骤,将刀具库中的刀具与工艺进行绑定,实现自动化的刀具选择。
5、生成切削路径将刀具库中的刀具与零件图形进行绑定后,我们需要生成合理的切削路径。
在MasterCAM-X界面中,我们可以使用散集命令、多边形命令等方式,快速生成切削路径。
需要注意的是,在切削路径生成的过程中,需要充分考虑切削参数、加工方向、刀具的尺寸等因素,以实现高效、准确的加工质量。
6、生成NC代码生成NC代码是数控加工编程的最后一步,也是最重要的一步。
在MasterCAM-X界面中,选择操作模块Operations Manager,点击Generate Code,即可生成NC代码。
mastercam编程实例图文讲解
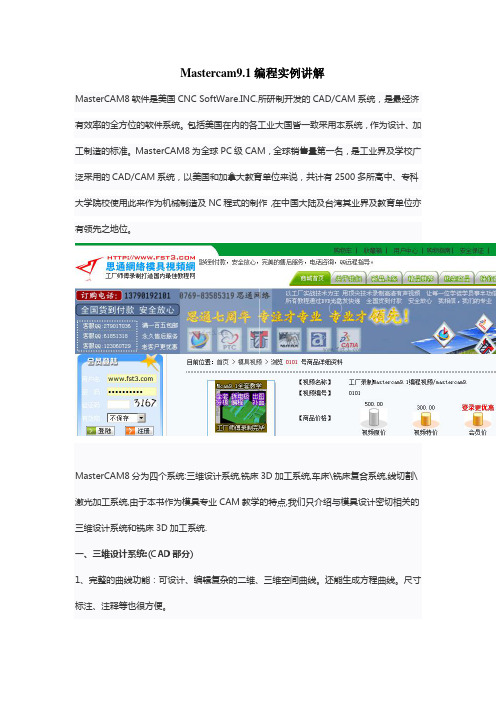
Mastercam9.1编程实例讲解MasterCAM8软件是美国CNC SoftWare.INC.所研制开发的CAD/CAM系统,是最经济有效率的全方位的软件系统。
包括美国在内的各工业大国皆一致采用本系统,作为设计、加工制造的标准。
MasterCAM8为全球PC级CAM,全球销售量第一名,是工业界及学校广泛采用的CAD/CAM系统,以美国和加拿大教育单位来说,共计有2500多所高中、专科大学院校使用此来作为机械制造及NC程式的制作,在中国大陆及台湾其业界及教育单位亦有领先之地位。
MasterCAM8分为四个系统:三维设计系统,铣床3D加工系统,车床\铣床复合系统,线切割\激光加工系统,由于本书作为模具专业CAM教学的特点,我们只介绍与模具设计密切相关的三维设计系统和铣床3D加工系统.一、三维设计系统:(CAD部分)1、完整的曲线功能:可设计、编辑复杂的二维、三维空间曲线。
还能生成方程曲线。
尺寸标注、注释等也很方便。
2、强大的曲面功能:采用NURBS、PARAMETRICS等数学模型,有十多种生成曲面方法。
还具有曲面修剪、曲面间等(变)半径倒圆角、倒角、曲面偏置、延伸等编辑功能。
3、崭新的实体功能:以PARASOLID为核心,倒圆角、抽壳、布尔运算、延伸、修剪等功能都很强。
4、可靠的数据交换功能,可转换的格式包括:IGES、SAT(ACIS SOLIDS)、DXF、CADL、VDA、STL、DWG、ASCII。
并可读取Parasolid、HPGL、CATIA、PRO/E、STEP等格式的数据文件。
二、铣床3D加工系统.(CAM部分)1、完整三维设计系统。
2、完整的铣床2D、2.5D加工系统。
3、多重曲面的粗加工及精加工。
4、等高线加工。
5、环绕等距加工。
6、平行式加工。
7、放射状加工。
8、插拉刀方式加工。
9、投影加工。
10、沿面加工。
11、浅平面及陡斜面加工。
12、G01可过滤为G02、G03并可程式过滤更平稳。
数控加工自动编程技术Mastercam 9.0详解

Allowable Tools Material(刀具材料选项组):选择用于 加工该材料的刀具材料。
Output feed Rates In(进给量长度单位选项组):设置 进给量所使用的长度单位。
Retract rate:主轴退刀速率。
Spindle speed:主轴转速。 Number of flutes:刀具切削槽数。 % of Matl cutting:切削速度的百分比。 %of Matl Feed per:进刀量(每齿)的百分比。 Spindle rotation:主轴旋转方向。
Coolant:加工时的冷却方式。
2.Create new(设置材料参数) 通过设置材料各参数来定义材料。选择该选项后,打开 图8-7所示的“Material definition”对话框。
图8-7 “Material definition”对话框
Material(材料名称输入框):输入材料的名称。 Base cutting speed(基本切削线速度输入框):设置材料 的基本切削线速度。
Comment注释框:可为该工件材料输入相关的注释文字。
四、其他参数设置
1.Toolpath Configuration 刀具路径设置 Output operation comments to NCI:生成的NCI文件 中包括操作注解。 Generate Tools path immediately:在编辑刀具路径后 ,立即更新NCI文件。 Save Tools path in MC9 fi1e:在MC9文件中存储刀具 路径信息。 Assign Tools number sequentially:在设置当前刀具列 表时,系统自动依序制定刀具号。 Use Tools’s step,peck,coolant:加工中使用刀具的步 距、步进、冷却设置等参数。 Search Tools library when entering Tools:当在 “Too1s parameter”选项卡中输入刀具号时,系统自动使 用刀具库中对应刀具号的刀具。
MasterCAM X7 车床编程范例

Instruction of MasterCAM X7 programming for LatheMasterCAM X7 车床编程范例(英文版)I.Import SLDPRT file and modify the coordinate system1.1Import the SLDPRT file(1)Click “Main Menu→File→Open”, choose the target file and cli ck “Open”. Then the file is imported into MasterCAM, shown in the drawing area.(2)Click “No hidden wireframe” on the tool bar. Then the whole wireframe of the entity is shown.(3)Press “F9” and “Alt+F9”. The coordinate system is then visible.(4)One can modify the viewing angle by pressing and dragging mouse wheel or by choosing viewing plane in “Gview” option at the bottom.1.2Modify the coordinate system(1)Click “Planes→Lathe diameter→+D +Z (WCS)”.(2)Click “Gview→Top(WCS)” and “WCS→Top WCS”.1.3Rotate and translate the entity as required(1)Select the whole entity, click “Xform Move to Origin” and then select the outside circle of the top of the candle holder. Then the center of the top circle of the holder is set to be the origin.(2)Set back to a Top Gview. Select the entity. Use the “Xform Rotate” tool to fix the center line of the entity on the x axis of the World Coordinate System which is indicated in the drawing area.In our case, the rotate angle is -90 degree.Then a standard view of the entity and coordinate system should be gotten.II.Turn the wireframe into profile2.1Set up another geometry level(1)Click “Level” in the bottom of the software.(2)Type “2” in the yellow input bar under “Number” in the “Main Level” section. Then click the green OK button. A new level 2 is created.2.2Turn wireframe to profile on level 2Click “Main Menu→Create→Turn Profile”, select the entity and press “ENTER” on the key board. Click the green OK button on the new window. The profile of the entity is created. A better vision can be achieved by hiding level1.2.3Hide level 1Click the “level” button in the bottom of the software. Click the two areas shown in the below with the indicated sequence. Then the “Visible” sign of level 1 is unchecked. Level 1 is hidden.III.Plan the toolpaths3.1Set up a machine group.Click “Main Menu→Lathe→Default”. A machine group is then set up in the Operation Manager.3.2Set the parameters of stock and chunk jaws(1)Click “Tool settings” in the Operations Manager to open the “Machine Group Properties”setting window. Then set the parameters as shown in the figures.(2)Click “Properties” button of Stock and Chunk Jaws. Set the parameter as shown below.3.3Plan the toolpath for facing(1)Click “Main Mune→Toolpaths→Face”. Click the green OK button. A setting window is shown. Set the parameters in the window as shown. Turn on the flood cooling in “Coolant” option.Left click the tool “R0.8 OD ROUGH RIGHT –80 DEG.”, right click it, choose “Edit tool”. Select “triangle” in the Shape section. Click green OK button.(2) Click “Face parameters” tab, set the parameters shown below. Then click “Lead in/Out”. Setthe parameters as shown. Click green OK button. The facing toolpath is then finished.3.4Plan the roughing toolpaths(1)Add two short lines on the profile as shown to avoid roughing process going into the grooving part and to leave some place for cutting off at the bottom.(2)Click “Main Menu→Toolpaths→Rough”. A chain selecting window is shown. Select the lines along the roughing surface line by line to select the chain.(3)Set the parameters as shown in the figure. Turn on the flood cooling in “coolant” option. Click the green OK button after setting. Then the roughing toolpath is generated.3.5Plan the grooving toolpaths(1)Click “Main Menu→Toolpaths→Groove”. Select “Chain” in the following “Grooving Options” window. Then a chain selecting window is shown. Select the lines along the surface of the design till the deep groove which will be made later for safety concerns. Click the green OK button when finishing the selection.(2)Select an “OD CUTOFF RIGHT” tool and set the parameters in Toolpath parameters” tab of “Lathe Groove (Chain) Properties” windows as shown below. Then right click on the tool icon, click “Edit tool” and set the parameters as shown.(3)Click the “Groove rough parameters” tab on the “Lathe Groove (Chain) Properties” window and set the parameters there as shown. Check the choosing boxed of “Peck Groove” and “Depth Cuts…” and set the parameters inside as shown.(4)Click the “Groove finish parameters” tab on the “Lathe Groove (Chain) Properties” window and uncheck “Finish” on the left top corner.3.6Plan the finishing toolpaths(1)Click “Main Menu→Toolpaths→Finish” to set up a right-hand finishing toolpath. Choose thesame chain as that in 3.4 (2). Set the parameters as shown below. Turn on the flood cooling in “coolant” option. Click all the green OK button after setting. A right-hand finishing toolpath is set.(2)Click “Main Menu→Toolpaths→Finish” to set up a left-hand finishing toolpath. The chosen chain is only the part which cannot be finished by the right-hand finishing as shown below.(3)Set the parameters as shown below. T urn on the flood cooling in “coolant” option. Click all the green OK button after setting. A right-hand finishing toolpath is set.3.7Plan the Grooving path(1)Click “Main Menu→Toolpaths→Groove” to start a grooving toolpath setting. Choose “3 lines”option to set the path in our case. The path is then chose as shown below. Press “ENTER” on the keyboard. Then the parameter setting window shows up.(2)Choose the same grooving tool as in 3.5 and set the toolpath parameters as shown. Set the flood coolant. Then right click the tool, click “Edit Tool”. Set the parameters of “Inserts”, then the “Holders”. Click green OK button. Choose the “Groove rough parameters” and “Groove finish parameters” tap separately in the Lathe Groove parameters window and set the para meters there.In the “Groove rough parameters”tab, remember to select “Peck Groove” and “Depth cuts…” and set the parameters inside. Click all the green OK button. The grooving path is then set.3.8Plan the drilling pathClick “Main Menu→Toolpaths→Drill” to start a drilling toolpath setting. Set the parameters in “Toolpath parameters” tab as below. Set up the flood coolant. Select a tool similar to “END MILL 15. DIA”. Left click the tool. Click “Edit Tool”, set the tool parameter as shown below. Click the OK button. Then set parameters in “Simple drill –no peck” tab.3.9Plan the boring path(1)Draw a line connecting the origin to the center point of the internal circle of the holder. Then translate it with D=15.(2)Then break the line of the inner circle’s radius into two parts using the new drawn line with the “Break Two pieces” button.(3)Click “Main Menu→Toolpaths→Rough” to start a roughing toolpath setting. Select the toolpath as shown below. Then a parameter setting window shows up.(4)Select a tool similar to “ROUGH MIN 16. DIA. –80 DEG.”. Set the parameters in “Toolpath parameter” as shown below. Turn on the flood cooling. Then left click the tool, select “Edit tool”and change the “Corner Radius” to 08 in the “Inserts” tab. Then click OK button, back to the “Lathe Rough Properties” window.(5)Set parameters in “Rough Parameters” tab, including those in “Lead In/Out” and “Plunge Parameters” as shown below. Click all the OK button. A boring roughing path is then created.(6)Click “Main Menu→Toolpaths→Finish” to start a finishing toolpath setting. Select path as shown below. Select the same tool in the parameter setting window. Set the parameters in “Toolpath parameter” as shown below and turn on the flood cooling. Click OK button to get back to “Lathe Finish Properties” window.(7)Set parameters in “Finish Parameters” tab, including those in “Lead In/Out” and “Plunge Parameters” as shown below. Then the finishing path is set.IV.Generate operationsAfter finishing all the toolpaths design, one can use functional buttons in Operation Manager to generate, backplot, verify and post operations.Click “Select all operations”. One choose all the operations. Click “Generate all selected operations”. One can generate all the operations and check if there is any error. The final view of the programming should be like:V.Generate operationsBackplot is often used after generating the toolpaths to check whether the fabricating process details are exactly same as the expectation including chains, pecking, cutting depth, etc.VI.V erify operationsClick “Verify selected operations”. One can verify the operations by simulating the whole process. The simulator can show the whole process in detail with controllable speed and precision, such as:VII.Post operationsBy posting operations, MasterCAM can change the visible programming into G code which can be understood and ran by the CNC machine. The posted code is like:Make sure that your program number is relatively unique.。
Mastercam数控加工-1.4认识数控程序代码指令与编程格式

任务四认识数控程序代码指令与编程格式任务书1-4-1 编程零件图任务描述教师通过背景知识的讲解,帮助学生认识数控加工程序代码、格式;通过完成任务所设定的编程内容,使学生掌握FANUC Oi 数控系统的编程格式及编程代码。
任务目标1、了解数控铣床程序编制的一般步骤,加工程序的构成及格式2、掌握G00 、G01 、G02 、G03 运动指令的编程方法3、掌握编程的基本功能指令的用法4、掌握编程的常用功能指令的用法5、掌握常用程序指令代码格式及编程要点任务实施1、编写如图1-4-1 所示零件图的加工程序2、编写如图1-4-19 所示零件图的加工程序【任务相关知识点】一、程序的结构与格式加工程序是数控加工中的核心组成部分,不同的数控系统,其加工程序的结构及程序段格式也可能有某些差异,以FANUC Oi数控系统为例来说明。
1、程序的结构一个完整的程序由程序号、程序内容和程序结束三部分组成,程序的开始部分通常取文件名以“O”+ 四位数字组成、中间是程序段、结束部分用“M30”表示,如图1-4-2所示图1-4-2 程序结构格式(1)程序号程序号是程序的开始部分,为了区别存储器的程序,每个程序都要进行编号,FANUC 系统一般采用英文字母“O”+ 四位数字组成。
(2)程序内容程序内容部分是整个程序的核心,它由许多程序段组成,每个程序由一个或多个指令构成,它表示数控机床要完成的操作。
程序的构成-----由若干个“程序段”组成程序段构成-----每个程序段由按照一定顺序和规定排列的“指令字”组成指令字构成------由表示地址的英文字母、特殊文字和数字集合而成(3)程序结束用程序结束指令M02或M03来结束整个程序2、程序格式:程序的开始部分、程序内容部分和程序结束图1-4-3 程序格式3、程序段组成:由指令字组成图1-4-4 程序结构格式4、指令字由地址符(指令字符)和带符号(由定义尺寸的字)或不带符号(如准备功能字G 代码)的数字数据组成。
MasterCAM数控编程培训课件ppt

THANKS FOR WATCHING
感谢您的观看
Mastercam界面与工具栏
01
详细介绍Mastercam软件的界面布局、工具栏及常用功能。
绘制几何图形
02
演示如何使用Mastercam软件绘制各种几何图形,如直线、圆
弧、曲面等。
刀路模拟与后处理
03
讲解如何进行刀路模拟,检查加工过程是否正确,以及如何生
成后处理文件,将刀路数据传输到数控机床上。
详细描述
介绍如何使用Mastercam进行简 单的二维轮廓加工、钻孔加工等 操作,包括毛坯设置、刀具路径 生成、切削参数设置等步骤。
复杂零件编程实例
总结词
通过复杂的零件编程实例,深入学习 Mastercam的高级功能和技巧。
详细描述
介绍如何处理复杂的曲面、模具等零 件的加工,学习使用Mastercam的曲 面粗加工、精加工等高级功能,以及 如何优化刀路和切削参数。
刀路模拟与后处理
总结词
学习如何进行刀路模拟和后处理,确保程序正确性和加工安 全性。
详细描述
介绍如何使用Mastercam的刀路模拟功能检查刀具路径的正 确性,以及如何进行后处理,将刀具路径转换为数控机床可 执行的代码格式。同时,强调后处理文件的管理和优化。
04 刀具路径优化
刀具选择与参数设置
总结词
实际加工案例操作
案例一
加工铝制零件:通过实际操作演 示,讲解如何使用Mastercam软 件进行铝制零件的数控编程与加
工。
案例二
加工钢制零件:以钢制零件为例, 演示如何根据材料特性调整加工参 数,确保加工质量。
案例三
多轴加工应用:介绍多轴加工的特 点、适用范围及在Mastercam中的 实现方法,通过实际操作演示多轴 加工过程。
MasterCAM9.1四轴编程实例

MasterCAM四轴编程实例一、任务描述:
二、图纸解读:
该零件右端已在车床加工完成,在加工中心主要加工面、内腔、凸台。
难点是怎样在一次装夹完成加工的程序编写。
三、刀具选择:
刀具一览表
四、工艺路线:
五、编程与加工:
MasterCAM9.1编程:
(1)打开MasterCAM软件,导入装配体XT文件,按F9显示坐标系,平移装配体把编程坐标
原点设置在零件左端面中心。
(2)点击作别图层,设置如下图层:
(3)开毛坯图层,其余关闭,另存STL格式毛坯文件。
(4)将构图面与刀具面设一致。
(5) 开零件图层和使用铣面图层绘制直线,铣平面。
参数设好单击确定出现刀具路径:
实体切削验证:
(6)旋转路径:
右键单机操作管理刀具路径1,选择路径转换弹出菜单:
参数设好后,单击确定,在操作管理菜单生成了新操作:
对不同深度的铣削面参数修改,修改完成后单击操作管理菜单中的重新计算:
实体验证:
(7)铣内腔,开零件图层,使用挖槽图层,选择挖槽加工:
生成的刀具路径:
对刀具路径进行旋转:
实体切削验证:
(8)铣凸台,开零件图层,使用铣凸台图层,选择外轮廓铣削:
对刀具路径进行旋转(同上):
实体切削验证:
(9)后处理
单击操作管理菜单中的执行后处理,储存NC程序:
11。
Mastercam X数控编程实例
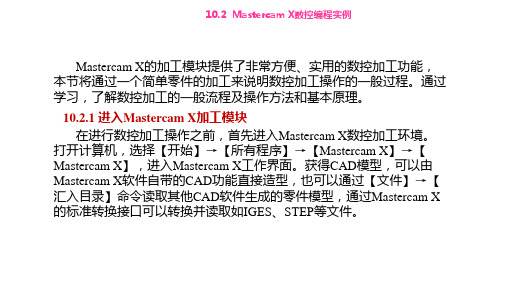
10.2 Mastercam X数控编程实例
2. 实体切削验证 (1)在“操作管理”中确认“1-曲面粗加工挖槽-[WCS:俯视图]- [刀具 平面:俯视图]”被选中,然后单击“验证己选择的操作” 按钮,如图 10-22所示,系统弹出图10-23所示的“验证”对话框,零件模型也随之 变化为毛坯形状。
图10-14 选择刀具对话框
2. 选择刀具
10.2 Mastercam X数控编程实例
图10-15 曲面粗加工挖槽及定义 刀具-机床群组-1对话框
10.2 Mastercam X数控编程实例
3. 设置刀具参数 (1)定义刀具。 在图1015的“曲面粗加工挖槽”对 话框中,选中“刀具路径参 数”选项卡,列表框中显示 出上步选取的刀具。双击该 刀具,系统弹出图10-16所示 的“定义刀具-机床群组-1” 对话框。 (2)设置刀具号。在“定 义刀具-机床群组-1”对话 框中,把“刀具号码”文本 框中原有的数值123改为1。
10.2 Mastercam X数控编程实例
图10-5 机器群组属性
图10-6 边界盒选项
图10-7 机器群组属性
10.2 Mastercam X数控编程实例
1. 选择刀具路径 选择下拉菜单【T 刀具路径】→【R 曲面粗加工】→【K 粗加工挖 槽加工】命令,如图10-8所示,系统弹出图10-9所示的"输入新NC名 称"对话框,采用系统默认的NC名称或输入新命名的NC名称,单击 “√”按钮,弹出图10-10,提示选择加工面。
图10-16定义刀具-机床群组-1对话框
10.2 Mastercam X数控编程实例
(3) 设置刀具的加工参数。单击 “定义刀具一机床群组-1”对话 框的“参数”选项卡,设置如图 10-17所示的参数。 (4) 设置冷却方式。在“参数”选 项卡中单击“Coolant”按钮,系 统弹出“Coolant. . . ”对话框, 在“Flood”(切削液)下拉列表中 选择“on”, 单击“√”按钮, 关闭“Coolant. . . ”对话框。 4. 完成刀具设置
mastercamx5高级数控车编程
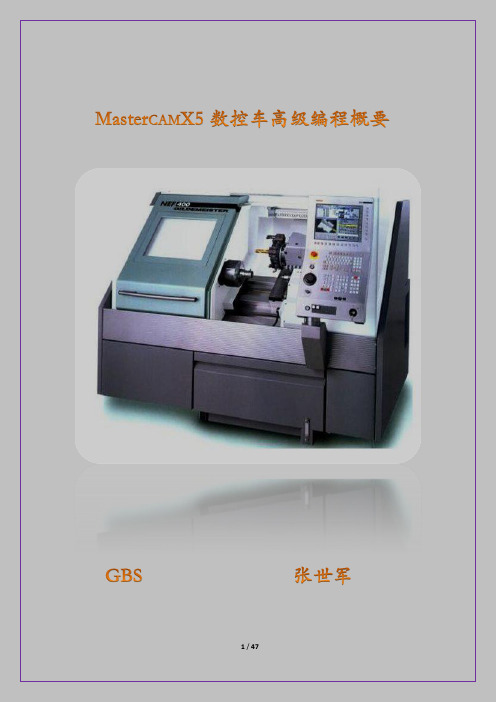
图 15
至此。此工件所有的编程工作结束,可以到现场跟踪进行一些参数的 修正,使之程序达到最佳的效率与优化。对以后的经验积累打下坚实
的基础。
20 / 47
3.1 毛坯设臵参数
图 16
21 / 47
毛坯设臵界面如下 下拉菜单有几种设臵方法
常用的有选择旋转轮廓的方法
图 17
22 / 47
设臵好的毛坯如图 18 所示 芯轴工装
另外,系统还提供有 CATIA、PRO-E、STEP 和 DXF、DWG 等数据交换器。
车削编程更加方便 刀具路径与几何模型完全相关(Full Associative)。当修改几何模型、刀具参数或加 工参数后,刀具路径自动更新。 在 Mastercam 的任务管理器中,可生成、修改和分析走刀路径。 可把经常使用的加工工步存于数据库中,以提高编程的自动化程度。如,粗、 精车零件时,可从库中调用储存的加工工步,作用于待加工零件。 自动选刀功能在选择刀具时,优先显示本加工工步所需的刀具类型。如无合适 的,也可访问刀具库中其它的刀具。
第三部,转换移动工件原点到 WCS(原点),通常是靠近刀具的那端设为 Z 向原点。
转换
平移
全部-图素
√ 应用
选移动-从一点到 2 点
(选取你要移动到的原点-原点。)如图 4 所示。
12 / 47
继续进行修剪,将不要的图素删掉,留下需要加工的部分。 测量毛坯后将毛坯图汇出,如图 5 所示。
23 / 47
3.2 卡爪与夹具设臵
此处串联可以预先绘制工装截面
此处是设臵卡爪
图19 设臵夹具有参数和串联2种方法 参数是卡爪设臵,将各种卡爪的状态予以设臵 串联是将提前绘制的夹具串联,(绘制方法和毛坯绘制方法一致) 卡具是可选项,主要是用来验证干涉和模拟仿真使用。 将卡具设臵好,可以是很好很直观的进行后期处理。
mastercam 加工中心编程实例

Mastercam加工中心编程实例介绍Mastercam是一款广泛应用于数控机床编程的软件,通过使用Mastercam可以进行各种复杂的零件加工编程。
本文将通过一个具体的实例来演示如何使用Mastercam 进行加工中心编程。
实例背景假设我们需要对一个铝合金材料进行加工,制作一个带有孔和凹槽的零件。
该零件尺寸为100mm x 100mm x 20mm,图纸如下:加工准备在开始编程之前,我们需要完成以下准备工作:1.确定刀具和夹具的选择:根据零件的形状和要求,选择合适的刀具和夹具。
2.确定机床坐标系:确定机床坐标系原点和方向。
3.导入CAD图纸:将零件图纸导入Mastercam中。
创建新项目1.打开Mastercam软件,并选择“新建项目”。
2.在项目设置中,设置机床类型为“加工中心”。
3.设置刀具库、夹具库等相关参数。
创建加工操作1.在Mastercam中打开导入的CAD图纸。
2.使用绘图工具创建孔和凹槽的几何形状。
3.使用刀具工具栏中的工具选择合适的刀具。
4.根据刀具和加工要求,设置切削参数,如进给速度、切削深度等。
加工路径生成1.在Mastercam中选择“加工路径生成”功能。
2.选择合适的加工策略,如钻孔、铣削等。
3.根据零件形状和加工要求,设置加工路径生成参数,如过渡方式、切割方式等。
仿真和后处理1.在Mastercam中进行仿真操作,检查加工路径是否正确。
2.如果需要输出数控机床程序文件,则选择“后处理”功能,并设置相应的后处理参数。
3.保存并导出数控机床程序文件。
加工操作1.将导出的数控机床程序文件拷贝到数控机床控制系统中。
2.在数控机床控制系统中加载并运行该程序文件。
3.监视加工过程,确保零件按照预期进行加工。
结束语通过本实例,我们演示了如何使用Mastercam进行加工中心编程。
从准备材料到最终完成零件的加工过程都需要仔细规划和操作。
希望本文能为您提供一些参考和帮助,使您能够更好地使用Mastercam进行加工中心编程。
MasterCAM的车削编程实例
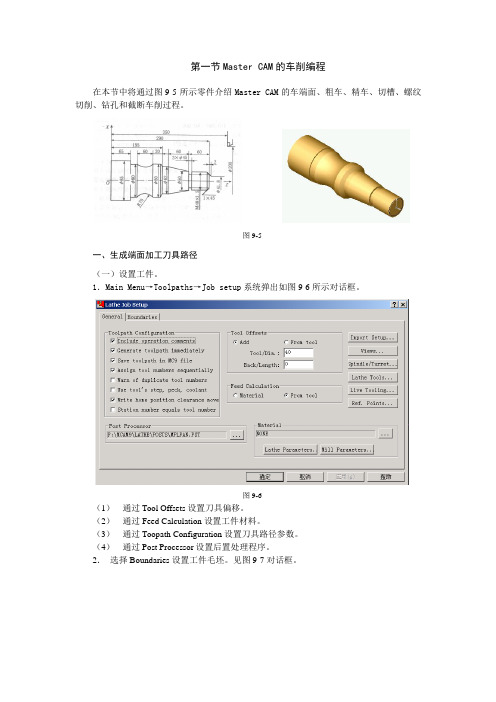
第一节Master CAM的车削编程在本节中将通过图9-5所示零件介绍Master CAM的车端面、粗车、精车、切槽、螺纹切削、钻孔和截断车削过程。
图9-5一、生成端面加工刀具路径(一)设置工件。
1.Main Menu→Toolpaths→Job setup系统弹出如图9-6所示对话框。
图9-6(1)通过Tool Offsets设置刀具偏移。
(2)通过Feed Calculation设置工件材料。
(3)通过Toopath Configuration设置刀具路径参数。
(4)通过Post Processor设置后置处理程序。
2.选择Boundaries设置工件毛坯。
见图9-7对话框。
图9-7(1)通过Stock项目设置工件毛坯大小。
选择Parameters→Take from 2 point设置毛坯的左下角点为(-100,-310),右上角点为(100,10),生成虚线如图9-8所示的毛坯。
(2)通过Tailstock尾座顶尖的参数。
(3)通过Chuck设置卡盘的参数。
(4)通过Steady rest设置辅助支撑的参数。
图9-8(5)选择Ok,工件设置完成。
(二)生成车端面刀具路径1.Main Menu→Toolpaths→Face系统弹出如图9-9所示的对话框。
2.在Tool parameters参数对话框中选择刀具,并设置其他参数。
3.选择对话框中的Face parameters标签,并设置参数。
见图9-10所示。
Face parameters 选项中各参数的含义如下:(1)Entry amountEntry amount输入框用于输入刀具开始进刀时距工件表面的距离(2)Roughstepover当选中Roughstepover输入框前面的复选框时,按该输入框设置的进刀量生成端面车削粗车刀具路径。
(3)Finish stepover当选中Fini9hstepover输入框前面的复选框时,按该输入框设置的进刀量生成端面车削精车刀具路径。
MasterCAM数控加工体验实例
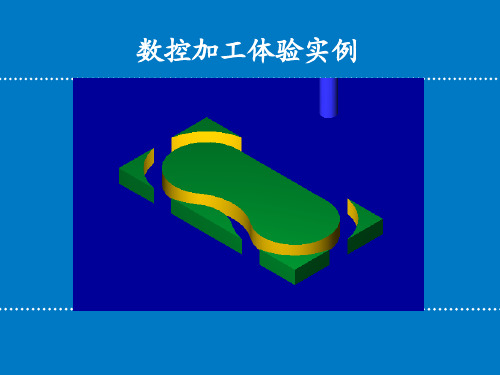
数控加工体验实例
操作步骤:1.绘制零件图
1.新建一个Mastercam文件
效果图如下:
2.绘制一个圆,选择“圆心点”工具
操作步骤:1.绘制零件图
3. 设置圆心ቤተ መጻሕፍቲ ባይዱ标为X0,Y0,Z0,按Enter 5.用同样的方法绘制第二个圆,圆心坐标 为X100,Y0,Z0,半径36。 6.两个圆绘制完毕后按“确认”按钮,效 果如图
1.设置机床:在菜单中选择“机床类型— 铣床—默认” 3.在弹出的“串连选项”对话框中选取 一种选择方法
2.设置刀具:在菜单中选择“刀具路径— 外形铣削”
操作步骤:2.设置机床及刀具
4.选择需要加工的图形
5.完成后在选项框中点选“确定”按钮
操作步骤:2.设置机床及刀具
6.紧接着弹出“外形”选项对话框,打开 刀库,从中选择号码为224的刀具 7.修改刀具的相应参数
1.点选“模拟加工”按 钮
2.在弹出的“实体验证”对 话框中选择“刀头”及模拟 速度,按“开始”按钮即可 开始模拟
操作步骤:3. 加工及编程
3.自动编程:在操作管理器中单击 “后处理”按钮
4.在弹出的“另存为”对话框中选取保 存位置,更改文件名,然后进行保存。
操作步骤:3. 加工及编程
5.软件自动生成零件的加工程序
4.设置圆的半径值为36,按Enter键, 点选“应用”图标
操作步骤:1.绘制零件图
7.绘制切弧:打开圆的工具下拉菜单, 点选“E点边界圆” 9.分别点选两个相切的圆
10.在出现的所有切弧中点选正确的那条 保留下来 8.在工作条中选中“相切”图标, 并设置切弧的半径为50,按Enter
MasterCAM数控编程培训课件

04
加工参数与后处理
刀路参数设置
切削方式
详细解释了切削方式的选择,如顺铣和逆铣,以及它们对切削效果的 影响。
切削深度
阐述了切削深度对加工效率和表面质量的影响,并给出了如何根据材 料和加工需求设置切削深度的建议。
进给速率
介绍了进给速率的选择原则,以及如何根据刀具、材料和切削条件来 调整进给速率。
主轴转速
详细描述
用户可以根据不同的材料和加工要求,设置合理的切削参 数,如刀具类型、切削速度、进给速度等,以确保加工质 量和效率。
总结词
Mastercam的2D加工编程具有高度灵活的刀路编辑功能 ,方便用户进行路径优化和调整。
详细描述
Mastercam提供了多种刀路编辑工具,如剪切、延长、 缩短等,使用户能够快速调整加工路径,提高加工精度和 减少加工时间。
系统设置
对软件界面、绘图单位、图层设置等参数进行设置。
基础绘图工具
线段绘制
使用线段工具绘制直线、圆弧等基本图形元 素。
圆与圆弧绘制
使用圆弧工具绘制圆形或圆弧。
修剪与延伸
对已绘制的图形进行修剪、延伸等编辑操作 。
几何变换
对图形进行平移、旋转、镜像等几何变换操 作。
02
数控编程基本概念
数控编程简介
码等。
04
后处理文件修改与调试
讲解了如何修改和调试后处理文 件以满足特定加工需求。
05
案例分析与练习
案例一:2D加工编程实例
总结词
掌握2D加工编程的基本流程和技巧
详细描述
通过一个简单的2D零件加工编程案例,介绍Mastercam的界面、工具栏、菜单 等基本操作,以及如何创建毛坯、选择刀具、设置加工参数、生成刀路轨迹等 步骤。
mastercam数控编程实例
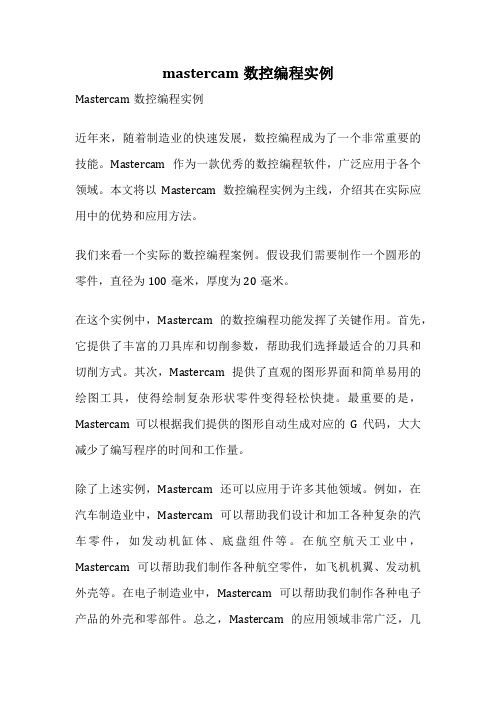
mastercam数控编程实例Mastercam数控编程实例近年来,随着制造业的快速发展,数控编程成为了一个非常重要的技能。
Mastercam作为一款优秀的数控编程软件,广泛应用于各个领域。
本文将以Mastercam数控编程实例为主线,介绍其在实际应用中的优势和应用方法。
我们来看一个实际的数控编程案例。
假设我们需要制作一个圆形的零件,直径为100毫米,厚度为20毫米。
在这个实例中,Mastercam的数控编程功能发挥了关键作用。
首先,它提供了丰富的刀具库和切削参数,帮助我们选择最适合的刀具和切削方式。
其次,Mastercam提供了直观的图形界面和简单易用的绘图工具,使得绘制复杂形状零件变得轻松快捷。
最重要的是,Mastercam可以根据我们提供的图形自动生成对应的G代码,大大减少了编写程序的时间和工作量。
除了上述实例,Mastercam还可以应用于许多其他领域。
例如,在汽车制造业中,Mastercam可以帮助我们设计和加工各种复杂的汽车零件,如发动机缸体、底盘组件等。
在航空航天工业中,Mastercam可以帮助我们制作各种航空零件,如飞机机翼、发动机外壳等。
在电子制造业中,Mastercam可以帮助我们制作各种电子产品的外壳和零部件。
总之,Mastercam的应用领域非常广泛,几乎涵盖了制造业的各个方面。
在实际应用中,掌握Mastercam的数控编程技能非常重要。
对于制造业从业人员来说,掌握Mastercam可以大大提高工作效率和质量。
同时,Mastercam也为制造业的发展提供了强有力的支持。
总结起来,Mastercam数控编程是一项非常重要的技能,广泛应用于制造业的各个领域。
通过Mastercam软件,我们可以快速、准确地设计和加工各种复杂的零件。
掌握Mastercam数控编程技能,对于提高工作效率和质量,推动制造业的发展具有重要意义。
因此,我们应该积极学习和应用Mastercam数控编程技术,为制造业的发展贡献自己的力量。
- 1、下载文档前请自行甄别文档内容的完整性,平台不提供额外的编辑、内容补充、找答案等附加服务。
- 2、"仅部分预览"的文档,不可在线预览部分如存在完整性等问题,可反馈申请退款(可完整预览的文档不适用该条件!)。
- 3、如文档侵犯您的权益,请联系客服反馈,我们会尽快为您处理(人工客服工作时间:9:00-18:30)。
构图平面之后,所绘制的图形就出现在该平面上。可以通过工具栏中的按钮
来改变构
图面也可以通过状态栏
(T/Cplane)改变。
3. 设置工作深度
构图平面实际上只是确定绘图平面,在同一方向上,可以根据设计需要设置多个构图平
面,而构图平面的位置由工作深度 Z 来确定。例如,设置了构图平面是“T 俯视图”,这时绘
图 1-116 二维模型图
图 1-117 刀具路径操作窗口 20
(3)加工工艺分析 不管是手工编程还是计算机辅助编程,加工工艺都是必须关注的。Mastercam 软件的 CAM 工能主要是自动产生刀具路径,加工工艺还需要编程人员事先制定。图 1-101 所示的 零件图,毛坯是经过预先铣削加工过的规则合金铝材,尺寸为 96mm×96mm×50mm。 1)装夹方法 此零件毛坯规则,采用平口钳装夹。 2)设定毛坯尺寸 单击图 1-117 中“材料设置”,出现如图 1-118 所示对话框。设置参数如图所示,其余为 默认设置,单击确定按钮,设定好毛坯尺寸。单击工具栏中 按钮,将视角设为等角视图, 结果如图 1-119 所示,双点划线部分为毛坯外形。 3)刀具设定 点击图 1-117 或 1-118 中的“刀具设置”,进入刀具设置界面,选中“刀具路径设置”中的“按 顺序指定刀具号码”。
零件尺寸如图 1-109。在 Mastercam 软件中,
为了编制零件的应用 NC 加工程序,需要先建立
该零件的模型。分析上述零件,只要建立如图
1-109 所示的俯视图的二维外形模型,根据二维
外形模型,结合 Z 轴的深度(从主视图中获得),
产生零件的二维加工刀具路径轨迹,经过后处
理,产生 NC 加工程序,就可以在数控铣床或加
工中心上加工出该零件。加工过程中,XY 方向
两轴做进给运动,Z 轴不做进给运动。
(1)二维模型的绘制
分析图 1-109 俯视图,绘图思路为:中心线
→底面正方形→台阶正方形→倒圆角→正五边
形→Φ40 孔→Φ10 孔
1)绘制中心线。
①设置图层属性。单击状态栏
,出现
图 1-109 二维铣削零件
17
图层属性设置对话框,设置图层 1 颜色为红色,线型为中心线,其它采用默认设置。 ②按 F9 键,出现十字交叉线,显示坐标轴及坐标原点。将零件对称中心点设在坐标原
图 1-112 多边形选项对话框
5)绘制 Φ40 孔和 4-Φ10 孔
单击菜单栏
→
→
图 1-113 绘制正五边形
或单击工具栏按钮
,执行画圆命令,
按交互提示信息,首先捕捉图形中心作为圆心或在
输入
中心点坐标,然后单击
输入直径 40,回车,得到 Φ40 的孔。再以同样的步
骤,依次以(-35,35),(35,35),(35,-35),(-35,-35)为圆心,以 10 为直径,画圆,得到如
(2)加工前的设置 1)图层设置
图 1-114 绘制Ф40 孔和 4-Φ10 孔
将当前图层设为 2,将中心线所在的图层 1 关闭。方法如下:单击状态栏 ,或按 快捷键“Alt+Z”,出现如图 1-115 所示的图层管理对话框,在编号下单击第二行,则第二行 变为黄色,当前图层为图层 2。
图 1-115 图层管理对话框
19
图 1-114 所示图形。 至此,我们建立了此零件的 2D 模型,根据已
完成的二维外形图,就可以编制此零件的加工刀 具路径。一般为检验分析所画图形的正确性,需 要进行分析验证和标注尺寸,此处不再叙述。
6)保存
单击菜单栏
→
或工具栏按
钮 ,在“保存”文件对话框中输入文件名“二维铣 削零件”,回车,完成文件保存。
位置
输入左上角点坐标(-48,48),回
车,然后在 面正方形绘制完毕。
③绘制台阶正方形
处输入宽度 96,在
处输入高度-96,回车,底
下面通过串连补正绘制台阶正方形。单击菜单栏
→
或直接单击工
具栏按钮 ,进入串连对话框,单击绘图区中已绘制的正方形的一条边,串连正方形,
其它按默认设置,然后单击
按钮确定,进入串连补正对话框,将水平补正(即 XY
制的图形将出现在 XY 平面(Z=0)上,如果希望绘制的图形出现 Z=10 的平面上,则点选
状态栏中
,从键盘输入 10,回车确认,则设置工作深度为
ቤተ መጻሕፍቲ ባይዱ
。
2.2 Mastercam X3 自动编程实例
本节通过几个典型零件说明 Mastercam X3 的零件造型、刀具路径的生成、模拟加工及
后处理方法。
1. 二维铣削零件
平面内)距离
设为 3,
为补正深度,即 Z 方向补正距
离,设为 0,其它按默认设置,然后单击
按钮确定,在绘图区右击鼠标右键,再单
击
,得到台阶正方形,结果如图 1-110。
3)倒圆角
单击菜单栏
→
→
或直接按工具栏按钮 ,执行倒圆
角命令。首先在
位置输入半径 10,回车,然后按交互提示信息,选取台阶
18
正方形的相邻两条边,倒完所有圆角后,按确定 应处于选中状态。得到如图 1-111 所示图形。
。在倒圆角时,要注意修剪延伸按钮
R10
底面 正方形
台阶 正方形
图 1-110 串连补正得到台阶正方形
图 1-111 倒圆角
4)绘制正五边形
单击菜单栏
→
或单击工具栏按钮
中的小三角形,在下拉按
钮中选中
,进入多边形选项对话框,如图 1-112 所示,选择图形中心作为基准
点,然后设置参数如图所示,单击确认,得到如图 1-113 所示图形。
点。
③单击菜单栏中
→
→
或工具栏按钮 ,然后单击自
动捕捉栏“快速点”按钮 (或按键盘空格键),输入起始点坐标“-50,0”,然后回车,再用同
样的步骤输入终点坐标“50,0”,点击 ,绘制出水平中心线。下面用另一种方法绘制垂直
中心线,用与绘制水平中心线相同的方法输入起点坐标“0,-50”,系统提示
,
此时在任意位置单击鼠标左键,系统弹出
在图 1-115 中,在“突显”这一列下单击第一行的“×”,则“×”消失。回车确认,则图层 1 关闭,中心线被隐藏,如图 1-116 所示,这样图面较简洁,方便选取加工图素。
2)选择机床类型 根据此零件特点选择立式数控铣床。方法如下:单击菜单栏
→ 所示信息。
→ 。此时操作管理窗口“刀具路径管理器”下,会出现如图 1-117
过工具栏中的按钮
(分别是俯视图 Top Gview、前视图 Front Gview、右视图
Right Gview、等角视图 Isometric Gview)改变视角,也可以通过快捷键或状态栏
改
变。
2. 设置构图平面 构图平面就是当前要使用的绘图平面,系统默认构图平面为俯视图(Top Gview)。设置
(不用理会),再单击指定长度按钮
,并输入长度 100,绘制出垂直中心线,点击 2)绘制正方形 ①改变主要层
,退出绘制任意直线命令。
在状态栏
的层别“1”改为层别“2”,并设置图层 2 的属性,
设置图层 2 颜色为黑色,线型为实线,线宽选用第二个宽度,其它采用默认设置。
②绘制底面正方形
单击菜单栏
→
或工具栏按钮 ,然后在坐标输入及捕捉栏的坐标