去毛刺的方法以及优缺点汇总
11种去毛刺除毛刺方法选择
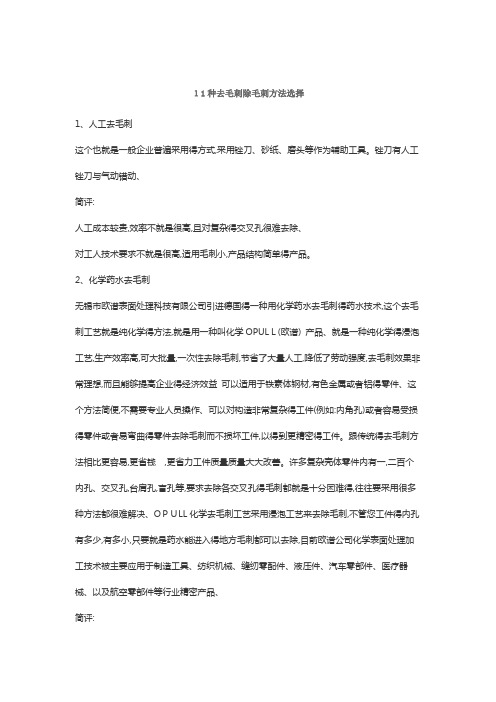
11种去毛刺除毛刺方法选择1、人工去毛刺这个也就是一般企业普遍采用得方式,采用锉刀、砂纸、磨头等作为辅助工具。
锉刀有人工锉刀与气动错动、简评:人工成本较贵,效率不就是很高,且对复杂得交叉孔很难去除、对工人技术要求不就是很高,适用毛刺小,产品结构简单得产品。
2、化学药水去毛刺无锡市欧谱表面处理科技有限公司引进德国得一种用化学药水去毛刺得药水技术,这个去毛刺工艺就是纯化学得方法,就是用一种叫化学OPULL(欧谱) 产品、就是一种纯化学得浸泡工艺,生产效率高,可大批量,一次性去除毛刺,节省了大量人工,降低了劳动强度,去毛刺效果非常理想,而且能够提高企业得经济效益可以适用于铁素体钢材,有色金属或者铝得零件、这个方法简便,不需要专业人员操作、可以对构造非常复杂得工件(例如:内角孔)或者容易受损得零件或者易弯曲得零件去除毛刺而不损坏工件,以得到更精密得工件。
跟传统得去毛刺方法相比更容易,更省钱,更省力工件质量质量大大改善。
许多复杂壳体零件内有一,二百个内孔、交叉孔,台肩孔,盲孔等,要求去除各交叉孔得毛刺都就是十分困难得,往往要采用很多种方法都很难解决、OPULL化学去毛刺工艺采用浸泡工艺来去除毛刺,不管您工件得内孔有多少,有多小,只要就是药水能进入得地方毛刺都可以去除,目前欧谱公司化学表面处理加工技术被主要应用于制造工具、纺织机械、缝纫零配件、液压件、汽车零部件、医疗器械、以及航空零部件等行业精密产品、简评:生产效率高,可大批量,一次性去除毛刺,节省了大量人工,降低了劳动强度,去毛刺效果非常理想,而且能够提高企业得经济效益?、3、冲模去毛刺采用制作冲模配合冲床进行去毛刺。
简评:需要一定得冲模(粗模+精冲模)制作费,可能还需要制作整形模、适合分型面较简单得产品,效率及去毛刺效果比人工佳。
4、研磨去毛刺此类去毛刺包含振动、喷砂、滚筒等方式,目前企业采用较多、简评:存在去除不就是很干净得问题,可能需要后续人工处理残余毛刺或者配合其她方式去毛刺。
打磨去毛刺方案
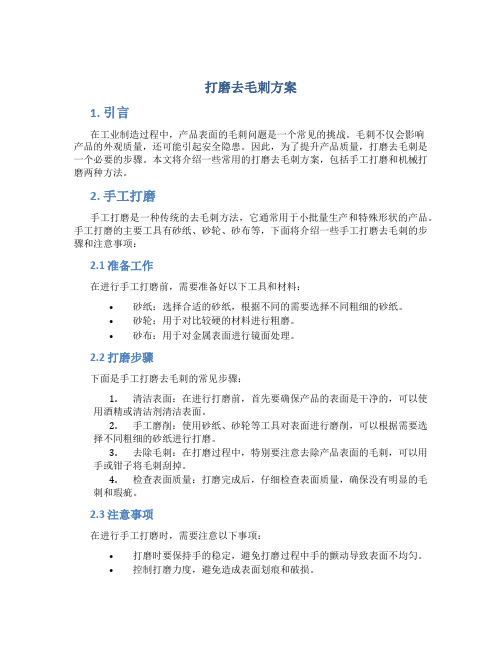
打磨去毛刺方案1. 引言在工业制造过程中,产品表面的毛刺问题是一个常见的挑战。
毛刺不仅会影响产品的外观质量,还可能引起安全隐患。
因此,为了提升产品质量,打磨去毛刺是一个必要的步骤。
本文将介绍一些常用的打磨去毛刺方案,包括手工打磨和机械打磨两种方法。
2. 手工打磨手工打磨是一种传统的去毛刺方法,它通常用于小批量生产和特殊形状的产品。
手工打磨的主要工具有砂纸、砂轮、砂布等,下面将介绍一些手工打磨去毛刺的步骤和注意事项:2.1 准备工作在进行手工打磨前,需要准备好以下工具和材料:•砂纸:选择合适的砂纸,根据不同的需要选择不同粗细的砂纸。
•砂轮:用于对比较硬的材料进行粗磨。
•砂布:用于对金属表面进行镜面处理。
2.2 打磨步骤下面是手工打磨去毛刺的常见步骤:1.清洁表面:在进行打磨前,首先要确保产品的表面是干净的,可以使用酒精或清洁剂清洁表面。
2.手工磨削:使用砂纸、砂轮等工具对表面进行磨削,可以根据需要选择不同粗细的砂纸进行打磨。
3.去除毛刺:在打磨过程中,特别要注意去除产品表面的毛刺,可以用手或钳子将毛刺刮掉。
4.检查表面质量:打磨完成后,仔细检查表面质量,确保没有明显的毛刺和瑕疵。
2.3 注意事项在进行手工打磨时,需要注意以下事项:•打磨时要保持手的稳定,避免打磨过程中手的颤动导致表面不均匀。
•控制打磨力度,避免造成表面划痕和破损。
•定期更换砂纸、砂轮等工具,保持其良好的工作状态。
3. 机械打磨机械打磨是一种自动化的去毛刺方法,它适用于大批量生产和产品形状相对规则的情况。
常见的机械打磨设备有研磨机、抛光机等,下面将介绍一些机械打磨去毛刺的步骤和注意事项:3.1 设备选择根据产品的形状和材料特性,选择合适的机械打磨设备,例如研磨机适用于对较硬材料进行粗磨,抛光机适用于对金属表面进行光洁处理。
3.2 打磨步骤下面是机械打磨去毛刺的常见步骤:1.准备工作:清洁产品表面,确保没有灰尘和污染物。
2.调整机械设备:根据产品的尺寸和要求,调整机器的转速、进给速度等参数。
产品涂装挂位孔毛刺改善对策

产品涂装挂位孔毛刺改善对策工件生产、加工后,外形轮廓部位容易出现毛刺(部分塑胶称“披锋”)。
一旦出现毛刺将会对产品尺寸精度、外观造成影响。
为了保证批量生产质量,工件在完成所有加工后增加去毛刺工艺就成为了必须。
不同的加工类型,产品毛刺的形状不一样。
如果只是单纯的采用某种去毛刺方法很难满足所有需求。
因此,不同的去毛刺工艺、方法应运而生。
打毛刺方法一、人工去除法在中小型企业这种方法非常常见。
利用人工打毛刺无需特殊设备、工具只要一把锉刀或砂纸,人员也无需专业培训即可上岗。
因为不适合大批量生产、结构复杂无法去除,再加上现在国内人力成本的不断增加,这种方法将会慢慢消失。
二、特定模具根据零件特性,设计专用模具对毛刺进行去除。
但是,考虑到模具成本及对产品的影响,一般只适合简单且尺寸要求不高的零件使用。
但是,效率相对人工更高。
三、研磨、震动法通过专业去毛刺设备去除毛刺。
此方法对小零件、大批量有奇效。
专用设备原理可分:振动、喷砂、滚筒等。
四、急速冷冻法主要原理是通过冷却使毛刺变脆,然后通过喷砂、震动等方法去除(与上种方法配合更加)。
不过,需要通过专用设备将零件进行急速冷冻。
因为其设备价格较贵,一般不低于30万。
很多公司望而却步五、热爆法主要原理是通过高温将毛刺进行融化,以达到去除毛刺的目的。
由于需要将易燃气体通过处理后实现瞬间爆燃升温。
因为实现的方式特殊,设备本身的价格也并不便宜。
一般只用于高精密零件中,如:航空、航天器零件等。
六、放电法类似电火花设备加工,通过瞬间高温熔化或气化毛刺。
不过,因为点解会存在不定性,因此工件本身也容易被腐蚀。
因为工艺特殊,可以去除复杂工件外部毛刺而被使用。
七、高压水流法通过高压水枪对工件进行冲刷,通过水枪瞬间强力去除毛刺。
不过只适合实心不变形产品。
八、超声波法超声波去除法类似清洗来达到去毛刺。
不过,这方法只适合产品精度要求非常高,毛刺属于细微级别,可能需要通过放大镜或显微镜来观察。
机加工铜铝件内孔去毛刺工艺
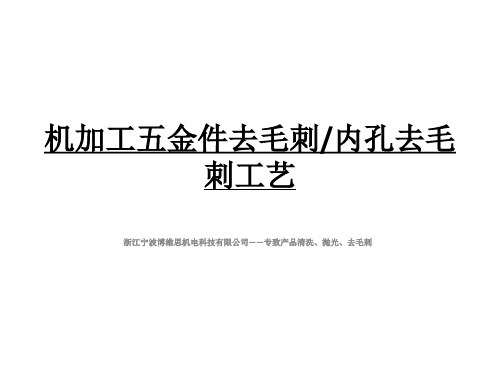
磁针研磨去毛刺的特点
• 特点: • >轻铁类金属、非铁类金属、硬质塑料等精密零件 成品,去除毛边、倒角、抛光、洗净等精密研磨 • 工作一次完成。 • >不规则状零件、孔内、管内、死角、夹缝等皆可 研磨加工。 • >加工速度快,操作简易安全,成本低,无须任何 耗材。 • >成品加工后绝不变形,绝不损伤表面,绝不影响 精度。 • >机种齐全,可设计专用机种。
国内磁针去毛刺机现状目前国内磁针去毛刺机主要分为高端中端低端三个层次国内亦有代理商代理销售台湾日本品牌磁针去毛刺机使用磁针去毛刺机关注点4设备合理使用保养磁针去毛刺机图片
机加工五金件去毛刺/内孔去毛 刺工艺
浙江宁波博维思机电科技有限公司——专致产品清洗、抛光、去毛刺法及弊端
磁针去毛刺机的用途
• • • • • • • 用途: >去除毛边精密研磨。 >金饰业打磨洗净工作。 >成品表面抛光处理。 >去除氧化薄膜工作。 >锈蚀去除处理。 >烧结痕迹处理。
磁针去毛刺机使用行业
• 适合行业产品: • >走心、走刀、CNC自动车床零件。 • >精密弹簧、弹片零件。 • >锌、铝压铸零件。 • >航天、医疗零件。 • >精密冲压零件。 • >电子、计算机、通信零件。 以及其他各类五金电子行业
磁针去毛刺机的优势
• 四合一功能设备:产品清洗、抛光、去毛刺、内孔抛光 去毛刺一次性大批量完成设备 • 说明: • 1.研磨速度快,平均一次研磨时间约3分至20分左右, 替换工件快,可在机器运转中替换研磨零件。 • 2.操作简单,绝对安全,完全免技术,一人可操作数台 机器。 • 3.成本低,不锈钢针为半永久性磨材,消耗极低,唯一 的耗材为研磨液。 • 4.无污染,研磨液是含90%水分,故无毒性及发生火灾 之虑,完全符合环保排放标准。 • 5.研磨完成后,工件好处理,可用筛网、筛筒或分离机 轻易将工件及不锈钢针分离。
修边,去毛刺的常用方法
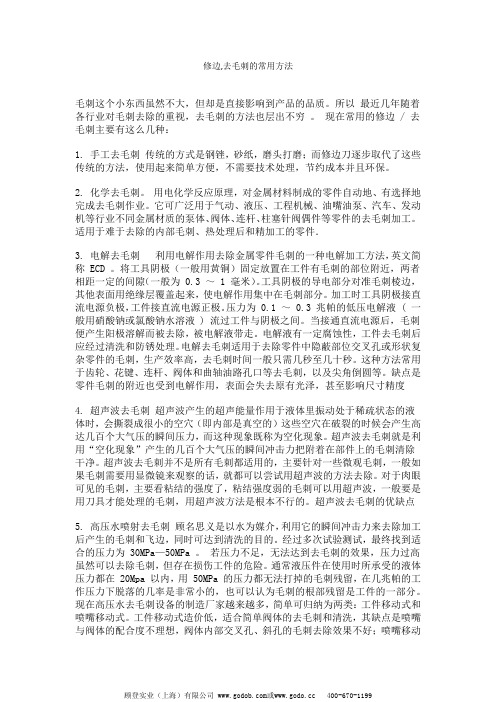
修边,去毛刺的常用方法毛刺这个小东西虽然不大,但却是直接影响到产品的品质。
所以最近几年随着各行业对毛刺去除的重视,去毛刺的方法也层出不穷。
现在常用的修边 / 去毛刺主要有这么几种:1. 手工去毛刺传统的方式是钢锉,砂纸,磨头打磨;而修边刀逐步取代了这些传统的方法,使用起来简单方便,不需要技术处理,节约成本并且环保。
2. 化学去毛刺。
用电化学反应原理,对金属材料制成的零件自动地、有选择地完成去毛刺作业。
它可广泛用于气动、液压、工程机械、油嘴油泵、汽车、发动机等行业不同金属材质的泵体、阀体、连杆、柱塞针阀偶件等零件的去毛刺加工。
适用于难于去除的内部毛刺、热处理后和精加工的零件.3. 电解去毛刺利用电解作用去除金属零件毛刺的一种电解加工方法,英文简称 ECD 。
将工具阴极(一般用黄铜)固定放置在工件有毛刺的部位附近,两者相距一定的间隙(一般为 0.3 ~ 1 毫米)。
工具阴极的导电部分对准毛刺棱边,其他表面用绝缘层覆盖起来,使电解作用集中在毛刺部分。
加工时工具阴极接直流电源负极,工件接直流电源正极。
压力为 0.1 ~ 0.3 兆帕的低压电解液 ( 一般用硝酸钠或氯酸钠水溶液 ) 流过工件与阴极之间。
当接通直流电源后,毛刺便产生阳极溶解而被去除,被电解液带走。
电解液有一定腐蚀性,工件去毛刺后应经过清洗和防锈处理。
电解去毛刺适用于去除零件中隐蔽部位交叉孔或形状复杂零件的毛刺,生产效率高,去毛刺时间一般只需几秒至几十秒。
这种方法常用于齿轮、花键、连杆、阀体和曲轴油路孔口等去毛刺,以及尖角倒圆等。
缺点是零件毛刺的附近也受到电解作用,表面会失去原有光泽,甚至影响尺寸精度4. 超声波去毛刺超声波产生的超声能量作用于液体里振动处于稀疏状态的液体时,会撕裂成很小的空穴(即内部是真空的)这些空穴在破裂的时候会产生高达几百个大气压的瞬间压力,而这种现象既称为空化现象。
超声波去毛刺就是利用“空化现象”产生的几百个大气压的瞬间冲击力把附着在部件上的毛刺清除干净。
去毛刺新工艺4

去毛刺新工艺一、现今对复杂形体毛刺处理中遇到的问题1.复杂形体易变形,一般对工件表面要求比较高,而在加工过程中对毛刺处理比较难。
2.复杂形体毛刺处理速度慢,现如今依然停留在使用人工应用刮刀等手工刀具处理。
3.由于使用人工处理,质量稳定性很差,很容易出现问题。
4.由于形体复杂,有的地方用手工很难去毛刺。
二、去毛刺新工艺1、应用电化学方法对复杂形体进行一次性成型的去毛刺处理。
2、电化学去毛刺是利用金属在电解液中发生阳极溶解反应而去除工件上多余的材料、将零件毛刺去除的一种方法。
3、电化学去毛刺的决定因素:3.1决定毛刺去除量的主要参数:去毛刺电流:根据去毛刺工件的所去毛刺的范围而决定。
一般5到10A。
去毛刺时间:根据去的毛刺大小有关。
一般为十几到几时秒。
工件材料导电率:根据去毛刺的材质有关。
3.2决定去毛刺的参数:电流密度:电流密度决定切削量和表面质量。
导电率:电解液的浓度决定导电率,单位S/cm根据区毛刺的需要,浓度应该控制在8%到25% ,温度对其也有影响。
间隙:夹具(阴极)工件(阳极)之间的间隙决定电流大小和电解液的冷却能力。
电化学液压力:间隙中的液体压力影响着电流和材料的去除。
实施温度:一般控制在20到35度之间。
PH值:一般在6.5到8.0之间。
电解液纯度:纯净的电解液能确保恒定量的产生。
三、项目适用范围:本项目适用于扭簧也可以加工我厂的733-106、736-14、736A-13整流子组件等各类复杂形体的毛刺处理;可以去除不锈钢、中低碳钢等硬度比较大的导电材质。
四、电化学去毛刺的优点:1.表面质量好,因去毛刺过程中不产生切削热,可达到较低的表面粗糙度。
2.操作简单,它可以通过简单地操作来处理复杂形体的毛刺且不影响工件自身强度。
3.可长期使用,理论上电极可长期使用,无损耗。
4.去毛刺生产率高,一般一个工件可在十几秒内全部去除干净,可进行平行加工,一般适用于批量处理。
5.该工艺属于绿色加工方法,电化学液很环保,一般使用中性无机盐类就可以处理,例如NaCl溶液,NaSO4溶液等。
圆周铸件去毛刺的方法有
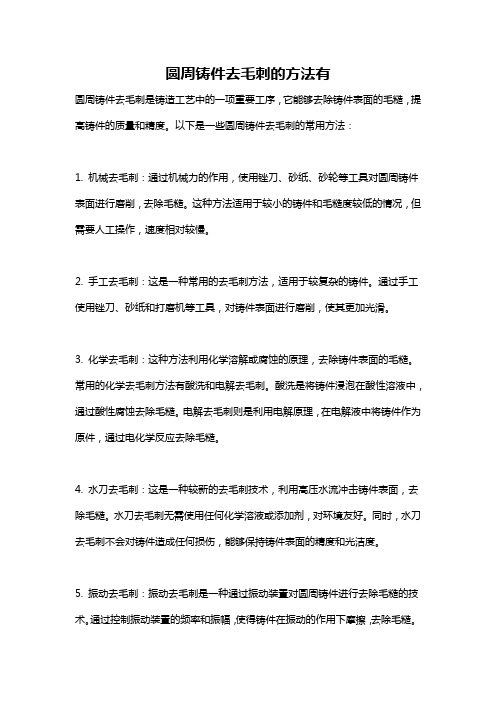
圆周铸件去毛刺的方法有圆周铸件去毛刺是铸造工艺中的一项重要工序,它能够去除铸件表面的毛糙,提高铸件的质量和精度。
以下是一些圆周铸件去毛刺的常用方法:1. 机械去毛刺:通过机械力的作用,使用锉刀、砂纸、砂轮等工具对圆周铸件表面进行磨削,去除毛糙。
这种方法适用于较小的铸件和毛糙度较低的情况,但需要人工操作,速度相对较慢。
2. 手工去毛刺:这是一种常用的去毛刺方法,适用于较复杂的铸件。
通过手工使用锉刀、砂纸和打磨机等工具,对铸件表面进行磨削,使其更加光滑。
3. 化学去毛刺:这种方法利用化学溶解或腐蚀的原理,去除铸件表面的毛糙。
常用的化学去毛刺方法有酸洗和电解去毛刺。
酸洗是将铸件浸泡在酸性溶液中,通过酸性腐蚀去除毛糙。
电解去毛刺则是利用电解原理,在电解液中将铸件作为原件,通过电化学反应去除毛糙。
4. 水刀去毛刺:这是一种较新的去毛刺技术,利用高压水流冲击铸件表面,去除毛糙。
水刀去毛刺无需使用任何化学溶液或添加剂,对环境友好。
同时,水刀去毛刺不会对铸件造成任何损伤,能够保持铸件表面的精度和光洁度。
5. 振动去毛刺:振动去毛刺是一种通过振动装置对圆周铸件进行去除毛糙的技术。
通过控制振动装置的频率和振幅,使得铸件在振动的作用下摩擦,去除毛糙。
这种方法适用于形状复杂的铸件。
6. 磁力去毛刺:磁力去毛刺是一种靠磁力作用去除铸件表面毛糙的方法。
通过在铸件表面施加磁场,将铸件表面的金属颗粒吸附在磁力上,去除毛糙。
这种方法适用于一些较小的圆周铸件。
7. 研磨去毛刺:研磨是通过在铸件表面搭载研磨剂,进行研磨操作,去除毛糙。
这种方法既可以手工进行,也可以采用机械研磨设备进行处理。
这种方法适用于各种不同材质的铸件。
总结:以上是一些常用的圆周铸件去毛刺的方法。
根据铸件形状、材质和毛糙度的不同,可以选择合适的去毛刺方法。
通过去除铸件表面的毛糙,可以提高铸件的质量和精度,增加铸件的使用寿命。
常见的去毛刺工具有哪些

常见的去毛刺的工具有哪几种?价格便宜的去毛刺设备又有哪些?日常处理机械零件的时候有哪些去毛刺的方法?接下来跟着小编一起去看看吧。
先说去毛刺工具中最简单的那些吧:
第一:一般企业普遍采用的去毛刺工具,有锉刀、砂纸、磨头等
优点:对工人技术要求不是很高,普通人即可操作,适用毛刺小,产品结构简单的产品。
缺点:人工成本较贵,效率不是很高,有些内孔的毛刺无法去除。
第二:去毛刺工具,冲模
采用制作冲模配合冲床进行去毛刺。
总结:
需要一定的冲模(粗模+精冲模)制作费,可能还需要制作整形模。
适合分型面较简单的产品,效率及去毛刺效果比人工佳。
第三:去毛刺工具,研磨
总结:
此类去毛刺包含振动、喷砂、滚筒等方式,目前企业采用较多。
存在去除不是很干净的问题,可能需要后续人工处理残余毛刺或者配合其他方式去毛刺,适合批量较大的小产品。
第四:去毛刺工具,雕刻机
总结:
设备价格在几万区间,适用于空间结构简单的机械零部件,所需去毛刺位置需要简单有规律。
第五:去毛刺工具,冷冻机
总结:设备价格在二三十万区间,适合毛刺壁厚较小且产品也较小的产品,利用降温使毛刺迅速脆化,然后喷射弹丸去除毛刺。
第六:去毛刺工具,热爆机
总结:设备价格在上百万,操作技术要求高,效率低,副作用(生锈、变形);主要运用在一些高精密的零部件领域,如汽车航天等精密零部件。
去毛刺工艺

毛刺去除作业规范
1、目的
规范作业动作,提高工作效率,确保产品品质和人员安全2、适用范围:
各车间生产部门
3、作业内容
毛刺的判定:手摸无扎手刺手感。
去毛刺工具:锉刀,刮刀,倒角刀,倒角机等
去毛刺作业方法; 1、当产品毛边超规需去毛边,首先考虑用倒角机,若毛边少只需适用锉刀捎带一下时,小工件用锉刀45°锉除,较长工件则用刮刀从起点至终点一次完成,不可断断续续导致出现锯齿,毛边不顺滑等不良
2、使用锉刀去边时,锉刀与产品毛边成45°来回一次降毛边去好,不能中途停顿,断断续续,这样会将产品边缘锉成锯齿不光滑而影响产品品质,确保无刮手感觉。
4、主要职责与权限
上道工序交于下道工序时,必须确保本工序加工部分无毛刺毛边
即日起施行,请各位认真贯彻执行。
三山海口
2014-07-05。
浅谈机械零件去毛刺工艺
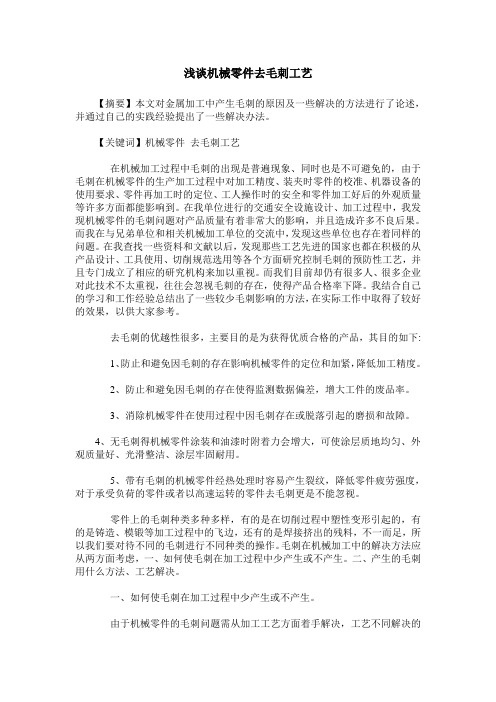
浅谈机械零件去毛刺工艺【摘要】本文对金属加工中产生毛刺的原因及一些解决的方法进行了论述,并通过自己的实践经验提出了一些解决办法。
【关键词】机械零件去毛刺工艺在机械加工过程中毛刺的出现是普遍现象、同时也是不可避免的,由于毛刺在机械零件的生产加工过程中对加工精度、装夹时零件的校准、机器设备的使用要求、零件再加工时的定位、工人操作时的安全和零件加工好后的外观质量等许多方面都能影响到。
在我单位进行的交通安全设施设计、加工过程中,我发现机械零件的毛刺问题对产品质量有着非常大的影响,并且造成许多不良后果。
而我在与兄弟单位和相关机械加工单位的交流中,发现这些单位也存在着同样的问题。
在我查找一些资料和文献以后,发现那些工艺先进的国家也都在积极的从产品设计、工具使用、切削规范选用等各个方面研究控制毛刺的预防性工艺,并且专门成立了相应的研究机构来加以重视。
而我们目前却仍有很多人、很多企业对此技术不太重视,往往会忽视毛刺的存在,使得产品合格率下降。
我结合自己的学习和工作经验总结出了一些较少毛刺影响的方法,在实际工作中取得了较好的效果,以供大家参考。
去毛刺的优越性很多,主要目的是为获得优质合格的产品,其目的如下:1、防止和避免因毛刺的存在影响机械零件的定位和加紧,降低加工精度。
2、防止和避免因毛刺的存在使得监测数据偏差,增大工件的废品率。
3、消除机械零件在使用过程中因毛刺存在或脱落引起的磨损和故障。
4、无毛刺得机械零件涂装和油漆时附着力会增大,可使涂层质地均匀、外观质量好、光滑整洁、涂层牢固耐用。
5、带有毛刺的机械零件经热处理时容易产生裂纹,降低零件疲劳强度,对于承受负荷的零件或者以高速运转的零件去毛刺更是不能忽视。
零件上的毛刺种类多种多样,有的是在切削过程中塑性变形引起的,有的是铸造、模锻等加工过程中的飞边,还有的是焊接挤出的残料,不一而足,所以我们要对待不同的毛刺进行不同种类的操作。
毛刺在机械加工中的解决方法应从两方面考虑,一、如何使毛刺在加工过程中少产生或不产生。
去毛刺常用方法分析(全文)
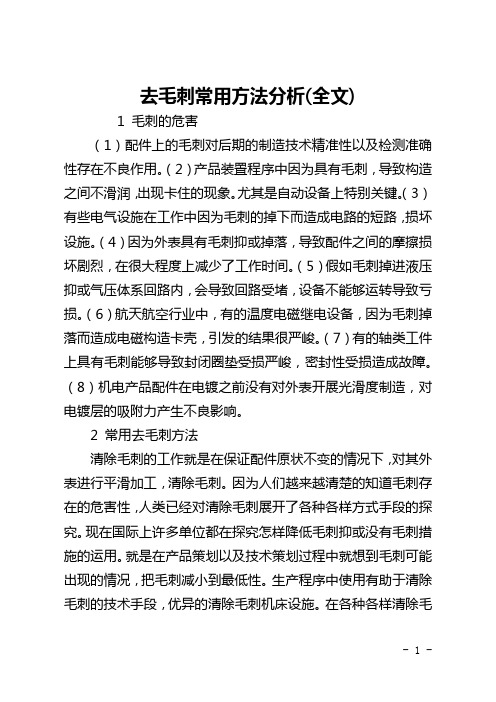
去毛刺常用方法分析(全文)1 毛刺的危害(1)配件上的毛刺对后期的制造技术精准性以及检测准确性存在不良作用。
(2)产品装置程序中因为具有毛刺,导致构造之间不滑润,出现卡住的现象。
尤其是自动设备上特别关键。
(3)有些电气设施在工作中因为毛刺的掉下而造成电路的短路,损坏设施。
(4)因为外表具有毛刺抑或掉落,导致配件之间的摩擦损坏剧烈,在很大程度上减少了工作时间。
(5)假如毛刺掉进液压抑或气压体系回路内,会导致回路受堵,设备不能够运转导致亏损。
(6)航天航空行业中,有的温度电磁继电设备,因为毛刺掉落而造成电磁构造卡壳,引发的结果很严峻。
(7)有的轴类工件上具有毛刺能够导致封闭圈垫受损严峻,密封性受损造成故障。
(8)机电产品配件在电镀之前没有对外表开展光滑度制造,对电镀层的吸附力产生不良影响。
2 常用去毛刺方法清除毛刺的工作就是在保证配件原状不变的情况下,对其外表进行平滑加工,清除毛刺。
因为人们越来越清楚的知道毛刺存在的危害性,人类已经对清除毛刺展开了各种各样方式手段的探究。
现在国际上许多单位都在探究怎样降低毛刺抑或没有毛刺措施的运用。
就是在产品策划以及技术策划过程中就想到毛刺可能出现的情况,把毛刺减小到最低性。
生产程序中使用有助于清除毛刺的技术手段,优异的清除毛刺机床设施。
在各种各样清除毛刺手段中,手工清除毛刺方式对毛刺尺寸、毛刺匀称性以及严峻性要求都不高。
但是使用机器抑或电化学方式清除毛刺就对其尺寸、匀称以及严峻性有一定程度的需求。
我们要想到工件的材料,工件制造时的手段,工件的大小、形状,出现毛刺的位置以及毛刺自身的尺寸。
在不影响零件大小精准度、外貌和方位精准度的根本上,符合最佳规范,并且还要想到不能出现二次毛刺。
在众多去毛刺方法中,机械去毛刺是最早、最广泛采纳的方法,其特点是使用简单,成本低。
使用锉刀、固结砂轮、铲刀、钢丝刷、针刷、研磨砂带及油石等带磨料的材料都属于此类方法。
但随着ZG制造业竞争日益激烈,对产品质量要求也日益提高,此类加工的零件质量精度已不能满足更为严格的标准要求。
机械零件去毛刺的四大方法

3.高温去毛刺
先将需要去毛刺的零件放在紧固的密封室内,然后送入一定压力的氢氧混合气体,经火花塞点火后,混合气体瞬时爆炸,放出大量的热,瞬时温度高达3300℃以上。由于爆炸时间极短,使零件的毛刺被烧掉,而零件的其他部分来不及变化。
此法适用于有色、黑色金属零件,特别适用于形状复杂的零件及用机械、手工方法难以去除的内孔、交叉孔及内表面的毛刺,能去除特硬零件如钼、镍、钛、淬火零件的毛刺。
2.化学去毛刺
将清洗干净的金属零件放到化学溶液(50℃)中,零件表面金属将以离子形式转到溶液中。这些离子聚集在工件表面,经化学反应形成一层电阻大、电导率小的黏液膜,保护工件表面不被腐蚀,而毛刺突出于表面,化学作用会将毛刺去掉。
机械零件去毛刺的四大方法
1.电解去毛刺
这是利用电能、化学能溶解阳极去掉毛刺。零件与直流电源的正极相边为阳极,成形工具与直流电源的负极相连为阴极,两极之间保持一定的间隙,让电解液循环流动。
当阳极和阴级浸入溶液并通入直流电后,阳极表面发生电化学反应,零件表面被溶解的金属与电解液形成黏性液体集中在零件表面的低凹处,具有较高的电阻和较小的腐蚀;
用此方法,零件变形小,设备简单,易操作,磨料来源广,经济性好,但大毛刺难去除。
零件在去毛刺前,必须清洗干净并烘干;去毛刺后,放入磷酸混合溶液中进行中和处理,去除氧化膜。
4.滚磨去毛刺
把一定比例的工件和磨料放入封闭的滚筒,在滚筒转动过程中,零件与磨料、零件与零件间产生磨削,去除毛刺。滚磨去毛刺设备有专用去毛刺机和离心滚抛机。磨料可用石英砂、木屑、氧化铝、陶瓷、白云石、碳化硅、金属环等。根据零件的材料、形状和尺寸以及毛刺部位和大小等进行选择。
高压水射流去毛刺技术的优缺点介绍

高压水射流去毛刺技术的优缺点介绍高压水射流去毛刺技术是一种接受高压水流来去除金属材料表面毛刺的方法。
它是一种绿色环保技术,与传统机械去毛刺相比有很多优势。
在这篇文档中,我们将介绍高压水射流去毛刺技术的优缺点。
优点1.高效率高压水射流去毛刺技术具有高效率的特点,一般来说仅需几秒钟即可完成一次去毛刺工作。
因此,相比传统的去毛刺方法节省了大量的时间和人力成本,能够极大提高生产效率。
2.高工艺性高压水射流去毛刺技术对金属材料的损伤很小,甚至可以达到零损伤。
在去毛刺的同时可进行喷砂和磨料操作,从而能够实现一次性完成多重工艺,大大提高了工作效率。
3.工作环境安全高压水射流去毛刺技术是一种特别安全的方法,由于在工作过程中不会产生任何化学气味和尘埃。
相比传统方法,工人的安全性得到了极大的保障。
4.可控性强高压水射流去毛刺技术的操作比较简单,只需要设置好操作参数就能够轻易地完成毛刺去除工作。
可以依据所处理的金属材料的不同,进行参数调整,以保证效果的一致性。
5.环保节能高压水射流去毛刺技术是一种特别环保的技术,它不需要任何化学药品和磨削材料,并且可以对水进行循环利用,大大地节省了能源和资源。
此外,与传统去毛刺方法相比,它能够削减二次污染的风险。
缺点1.较高的成本高压水射流去毛刺技术设备的选购和维护成本较高,对于小型企业来说可能会产生确定的负担。
2.水质要求高对于高压水射流去毛刺技术而言,水质的要求比较高。
假如水质没有达到要求,会影响到其效果和使用寿命。
3.噪音问题高压水射流去毛刺技术在工作过程中会产生较大的噪音,影响到周边环境。
4.处理面积受限高压水射流去毛刺技术处理面积比较受限,不能针对较大的面积进行去毛刺。
结论虽然高压水射流去毛刺技术存在确定的缺点,但其优点也是不可忽视的。
它具有高效率、高工艺性、工作环境安全、可控性强、环保节能等特点。
因此,它将会成为将来去毛刺技术的一个紧要趋势。
毛刺虽小,危害俱全!如何解决毛刺问题

毛刺虽小,危害俱全!如何解决毛刺问题金属加工中出现毛刺是大家都会遇到的问题,比如钻孔,车削,铣削,板材切割毛刺的危害之一就是容易割伤!为了去除毛刺,通常需要进行称为去毛刺的二次操作。
精密部件的3次去毛刺和边缘精加工可能占成品部件成本的30%。
此外,二次精加工操作难以自动化,所以毛刺真的变成了很棘手的问题。
大家头痛的易出现毛刺的地方都在这里了加工过程中进给方向毛刺(入口和出口毛刺)侧向和切割方向毛刺如何解决毛刺化学去毛刺是利用化学能进行加工,化学离子会附着在零件表面,形成电阻大、电导率小的膜层,保护工件不受到腐蚀,而毛刺由于高出表面,可以通过化学作用去除掉毛刺。
这种去毛刺的方法被广泛应用于气动、液压、工程机械等领域。
高温去毛刺先将需要去毛刺的零件放入紧固的密封室内,然后将其整体送入有一定压力的氢氧混合气体中,点火使混合气体爆炸,放出热量,将零件的毛刺烧掉,不会伤及零件。
滚磨去毛刺将零件与磨料一同放入封闭的滚筒中,在滚筒转动的过程中,动态扭矩传感器、零件与磨料一起产生磨削,去除毛刺。
磨料可以用石英砂、木屑、氧化铝、陶瓷以及金属环等等。
手工去毛刺这种方法比较传统也是最费时、费力的。
主要是通过人工用钢锉、砂纸、磨头等工具进行打磨。
现在生产中最常用的是修边刀。
工艺去毛刺边缘倒圆可以指所有去除金属部件边缘的动作。
但是,它通常与创建零件边缘的半径相关联。
边角倒圆边缘倒圆不是简单地去除锋利度或去毛刺,而是打破金属部件的边缘,以改善其表面覆盖涂层并保护其免受腐蚀。
边缘圆角机包括:旋转挫:适用于激光切割,冲压或机加工零件的边缘。
手动研磨机:适用于需要磨削和边缘倒圆或去毛刺的金属加工项目。
特殊难题铣削零件中的毛刺在铣削零件中,去毛刺更复杂,成本更高,因为铣削不同尺寸的不同位置会形成多个毛刺。
这时候选择正确的工艺参数以最小化毛刺尺寸就显得尤为重要。
影响端铣毛刺形成的主要因素①铣削参数、铣削温度、切削环境等对毛刺的形成会产生一定的影响,部分主要因素如进给速度、铣削深度等的影响通过平面切出角理论和刀尖退出顺序EOS理论体现出来。
13种各类去毛刺方法的优缺点点评

13种各类去毛刺方法的优缺点点评金属加工中出现毛刺是大家都会遇到的问题,比如钻孔,车削,铣削,板材切割。
毛刺的危害之一就是容易割伤!为了去除毛刺,通常需要进行称为去毛刺的二次操作。
精密部件的3次去毛刺和边缘精加工可能占成品部件成本的30%。
此外,二次精加工操作难以自动化,所以毛刺真的变成了很棘手的问题。
大家头痛的易出现毛刺的地方都在这里了加工过程中进给方向毛刺(入口和出口毛刺)侧向和切割方向毛刺如何解决毛刺 :01.人工去毛刺这个是较传统的普遍采用的方式,采用锉刀(锉刀有人工锉刀和气动锉刀)、砂纸、砂带机、磨头等作为辅助工具。
缺点:人工成本较贵,效率不是很高,且对复杂的交叉孔很难去除。
适用对象:对工人技术要求不是很高,适用毛刺小,产品结构简单的铝合金压铸件。
02.冲模去毛刺采用制作冲模配合冲床进行去毛刺。
缺点:需要一定的冲模(粗模精冲模)制作费,可能还需要制作整形模。
适用对象:适合分型面较简单的铝合金压铸件,效率及去毛刺效果比人工佳。
03.研磨去毛刺此类去毛刺包含振动、喷砂、滚筒等方式,目前压铸厂采用较多。
缺点:存在去除不是很干净的问题,可能需要后续人工处理残余毛刺或者配合其他方式去毛刺。
适用对象:适合批量较大的小铝合金压铸件。
04.冷冻去毛刺利用降温使毛刺迅速脆化,然后喷射弹丸去除毛刺。
设备价格大概在二三十万;适用对象:适合毛刺壁厚较小且体积也较小的铝合金压铸件。
05.热爆去毛刺也叫热能去毛刺、爆炸去毛刺。
通过将一些易然气体,通入到一个设备炉中,然后通过一些介质及条件的作用,让气体瞬间爆炸,利用爆炸产生的能量来溶解去除毛刺。
缺点:设备昂贵(上百万价格),操作技术要求高,效率低,副作用(生锈、变形);适用对象:主要运用在一些高精密的零部件领域,如汽车航天等精密零部件。
06.雕刻机去毛刺设备价格不是很贵(几万)。
适用对象:适用于空间结构简单,所需去毛刺位置简单有规律。
07.化学去毛刺用电化学反应原理,对金属材料制成的零件自动地、有选择地完成去毛刺作业。
去毛刺

In挤压掉而是被刀具切削掉的,这样就会使产
生的毛刺变小甚至消除,同时毛刺是沿着刀
具的平行方向形成,有利于后续毛刺的去除
(见图 3-9/10)。
发动机一厂技术科
12
PDF created with pdfFactory Pro trial version
去毛刺工艺指南
2、毛刺大小的标准等级
毛刺的大小按其高度大致可分为以下 10 个等级(见图 2-1)。
Internal Use Only
当毛刺能用手或指甲
感觉到时,其毛刺高度约 在 0.1mm 以上,也就是 在 4 级以上
图 2-1
发动机一厂技术科
5
PDF created with pdfFactory Pro trial version
去毛刺工艺指南
3、影响毛刺大小的主要因 素
3.1 工件材料
3.1.1 硬度低、塑性好的材料,加工后越
容易产生毛刺且毛刺较大(如:铝 合金、尼龙、塑料)。
ly 3.1.2 硬度高、塑性较差的材料,加工后 n 不会产生较大的毛刺且毛刺很容易 O 被去除(如:铸铁缸体、粉末冶金、 e 硬质合金以及经过热处理的材料)。
图 3-3
图 3-4
◆工件末端以>90°倒角形式的过渡(见 图 3-5)。
发动机一厂技术科
9
PDF created with pdfFactory Pro trial version
去毛刺工艺指南
se Only 图3-5 U 工件末端以 >90°倒角形式过渡的 al 结构,在刀具加工至工件末端时,由于工件 n 末端的支承强度有所增加,工件末端的加工 r 余量不是被挤压掉而是被刀具切削掉的,这 te 样就会使产生的毛刺变小,同时毛刺是沿着 In刀具的平行方向形成,也有利于后续毛刺的
工业零件毛刺、毛边、披锋去掉的方法
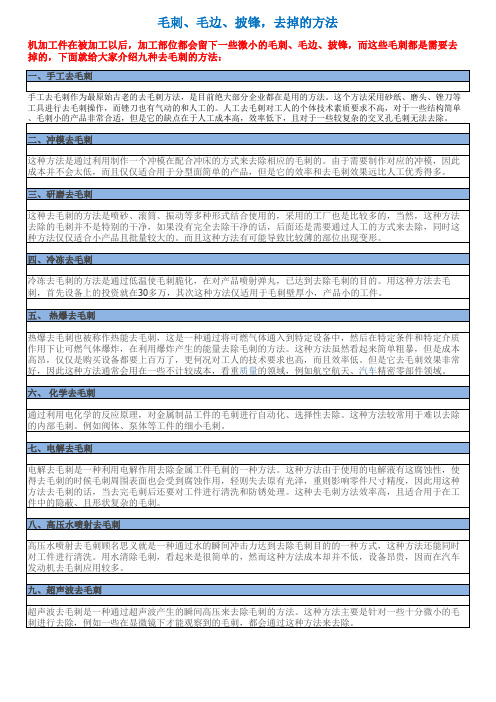
通过利用电化学的反应原理,对金属制品工件的毛刺进行自动化、选择性去除。这种方法较常用于难以去除 的内部毛刺。例如阀体、泵体等工件的细小毛刺。
七、电解去毛刺
电解去毛刺是一种利用电解作用去除金属工件毛刺的一种方法。这种方法由于使用的电解液有这腐蚀性,使 得去毛刺的时候毛刺周围表面也会受到腐蚀作用,轻则失去原有光泽,重则影响零件尺寸精度,因此用这种 方法去毛刺的话,当去完毛刺后还要对工件进行清洗和防锈处理。这种去毛刺方法效率高,且适合用于在工 件中的隐蔽、且形状复杂的毛刺。
四、冷冻去毛刺
冷冻去毛刺的方法是通过低温使毛刺脆化,在对产品喷射弹丸,已达到去除毛刺的目的。用这种方法去毛 刺,首先设备上的投资就在30多万,其次这种方法仅适用于毛刺壁厚小,产品小的工件。
五、 热爆去毛刺
热爆去毛刺也被称作热能去毛刺,这是一种通过将可燃气体通入到特定设备中,然后在特定条件和特定介质 作用下让可燃气体爆炸,在利用爆炸产生的能量去除毛刺的方法。这种方法虽然看起来简单粗暴,但是成本 高昂,仅仅是购买设备都要上百万了,更何况对工人的技术要求也高,而且效率低。但是它去毛刺效果非常 好,因此这种方法通常会用在一些不计较成本,看重质量的领域,例如航空航天、汽车精密零部件领域。
毛刺、毛边、披锋,去掉的方法
机加工件在被加工以后,加工部位都会留下一些微小的毛刺、毛边、披锋,而这些毛刺都是需要去 掉的,下面就给大家介绍九种去毛刺的方法:
一、手工去刺
手工去毛刺作为最原始古老的去毛刺方法,是目前绝大部分企业都在是用的方法。这个方法采用砂纸、磨头、锉刀等 工具进行去毛刺操作,而锉刀也有气动的和人工的。人工去毛刺对工人的个体技术素质要求不高,对于一些结构简单 、毛刺小的产品非常合适,但是它的缺点在于人工成本高,效率低下,且对于一些较复杂的交叉孔毛刺无法去除。
几种去毛刺的方法
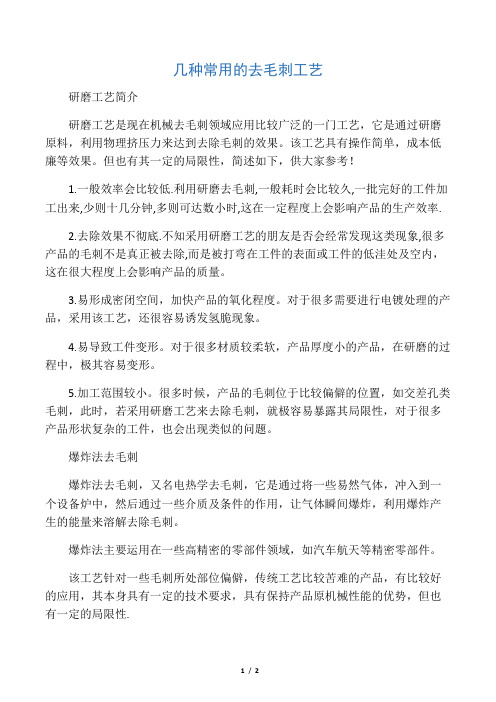
几种常用的去毛刺工艺研磨工艺简介研磨工艺是现在机械去毛刺领域应用比较广泛的一门工艺,它是通过研磨原料,利用物理挤压力来达到去除毛刺的效果。
该工艺具有操作简单,成本低廉等效果。
但也有其一定的局限性,简述如下,供大家参考!1.一般效率会比较低.利用研磨去毛刺,一般耗时会比较久,一批完好的工件加工出来,少则十几分钟,多则可达数小时,这在一定程度上会影响产品的生产效率.2.去除效果不彻底.不知采用研磨工艺的朋友是否会经常发现这类现象,很多产品的毛刺不是真正被去除,而是被打弯在工件的表面或工件的低洼处及空内,这在很大程度上会影响产品的质量。
3.易形成密闭空间,加快产品的氧化程度。
对于很多需要进行电镀处理的产品,采用该工艺,还很容易诱发氢脆现象。
4.易导致工件变形。
对于很多材质较柔软,产品厚度小的产品,在研磨的过程中,极其容易变形。
5.加工范围较小。
很多时候,产品的毛刺位于比较偏僻的位置,如交差孔类毛刺,此时,若采用研磨工艺来去除毛刺,就极容易暴露其局限性,对于很多产品形状复杂的工件,也会出现类似的问题。
爆炸法去毛刺爆炸法去毛刺,又名电热学去毛刺,它是通过将一些易然气体,冲入到一个设备炉中,然后通过一些介质及条件的作用,让气体瞬间爆炸,利用爆炸产生的能量来溶解去除毛刺。
爆炸法主要运用在一些高精密的零部件领域,如汽车航天等精密零部件。
该工艺针对一些毛刺所处部位偏僻,传统工艺比较苦难的产品,有比较好的应用,其本身具有一定的技术要求,具有保持产品原机械性能的优势,但也有一定的局限性.1/ 2其一,生产效率一般比较低。
由于该工艺要求在比较严格的环境底下进行,在这种爆炸设备中,能大批量处理的数量比较有限。
其二,处理成本偏高。
购买一台爆炸的去毛刺设备,一般需要上百万。
很多中小型企业根本没有能力承担这种费用。
其三,易导致产品生锈。
产品在高温的爆炸炉中,极容易导致生锈。
其四,工件易变形。
其五,操作有一定的技术要求,不是普通人容易操作的。
去除产品毛刺方法

去除产品毛刺方法1、人工去除毛刺这个是小厂最常用的方法,用锉刀、砂纸、磨头作为基本工具。
其中,锉刀有人工锉和气动锉。
备注:人工成本高,效率低,且对异形的穿插孔很难去除。
适用范围:工人技术要求不高,适用毛刺小,且零件结构复杂。
2、冲模去毛刺适用模具,利用模具在冲床中去除毛刺。
备注:要一个冲模(粗模+精冲模)成本,也许还加多一套整形模。
适用范围:适宜分型面较复杂的工件,效率及去毛刺效果比人工要好。
3、研磨去毛刺关于研磨去毛刺的方法就有很多了,其中最常见的包括:振荡、喷砂、滚动等方法。
备注:存在除不净的弊端,有的还需要后续人工处理剩余毛刺或其他方法去毛刺。
适用范围:适宜批量较大的小件4、冷冻去毛刺运用降温是毛刺表面变脆,后利用喷发弹丸去除毛刺。
备注:设备大约在二三十万左右,不是什么公司都能用的。
适用范围:适合毛刺壁厚较小,且工件也较小的产品。
5、热爆去毛刺或者叫热能去毛刺、爆破去毛刺。
将一些易燃气体,通入到设备炉中,然后经过一些介质和条件,让气体瞬间爆破,运用爆破发出的能量来溶解去除毛刺。
备注:设备非常贵(上百万),操作人员技术要求高,效率低,有副作用(生锈、变形等)。
适用范围:运用在一些高精密的零部件上,如轿车航天器等精密零部件。
6、雕刻机去毛刺。
备注:设备不是很贵(几万),适用范围:适用于空间结构复杂,所需去除毛刺复杂有规律。
7、化学去毛刺用电化学原理,对金属材料制成的零件自动地、有选择地去除毛刺作业。
备注:适用于很难去除的内部毛刺,适用范围:适宜泵体、阀体等工件毛刺很大的情况(厚度小于7个丝)。
8、电解去毛刺运用点解效果去除金属零件毛刺的一种电解加工方法。
备注:电解液有一定腐蚀性,零件毛刺的周围也遭到电解,表面会失掉原有的光泽,影响尺寸精度,工件去毛刺后应经过清洗和防锈处理。
适用范围:适用于去除零件中隐蔽部位交叉孔或外形杂乱零件的毛刺,效率高,去毛刺只需几秒到几十秒。
适用于齿轮、连杆、阀体和曲轴油路孔口等去毛刺,以及尖角倒圆等。
毛刺缺陷及解决措施

毛刺缺陷及解决措施毛刺缺陷简介毛刺是指在产品制造过程中,表面出现的凸起或凹陷的小颗粒,这些颗粒常常会对产品的质量和外观造成影响。
毛刺缺陷通常是由于材料的不均匀性、工艺参数设置不当、模具磨损等原因引起的。
在很多行业中,特别是在电子、汽车、玩具等领域中,毛刺缺陷被视为一种重要的质量问题。
毛刺缺陷的影响毛刺缺陷对产品的影响是多方面的。
首先,毛刺会给产品的表面质量带来负面影响,降低产品的外观美观度,甚至可能降低产品的销售价值。
其次,毛刺也可能对产品的功能产生影响,例如在电子产品中,毛刺导致的电气联系问题可能会影响产品的性能稳定性。
此外,毛刺还可能造成产品在运输、装配等过程中的损坏,增加了后续的维修和保养成本。
毛刺缺陷解决措施针对毛刺缺陷,以下是一些常见的解决措施:1. 优化工艺参数毛刺缺陷通常是由于工艺参数设置不当导致的,因此,优化工艺参数是解决毛刺问题的首要步骤。
通过合理地调整注塑温度、注射速度、冷却时间等参数,可以减少毛刺的产生。
此外,还可以考虑采用其他加工工艺,如喷涂、热压等,来避免毛刺的产生。
2. 使用高质量的模具模具的质量对毛刺的产生有很大影响。
使用高质量的模具,可以加强产品表面的光滑度,并减少毛刺的产生。
此外,在模具的设计和制造过程中,还应考虑合理的表面处理,如钝化、抛光等,以减少毛刺的形成。
3. 使用合适的材料毛刺的产生与材料的性质密切相关。
使用合适的材料,特别是具有较低粘度和较高流动性的材料,可以减少毛刺的形成。
此外,对于某些特殊要求的产品,也可以考虑使用特殊的防毛刺材料,来解决毛刺问题。
4. 加强质量检查与控制加强质量检查与控制是解决毛刺缺陷的重要环节。
在生产过程中,应建立严格的质量控制标准,并配备相应的质量检测设备,及时发现和排除可能引起毛刺的问题。
此外,还应加强对原材料的检验,确保使用的材料符合质量要求。
5. 定期维护和保养设备设备的磨损和老化是毛刺形成的常见原因之一。
定期维护和保养设备,及时更换损坏和磨损的零件,可以减少毛刺的产生。
- 1、下载文档前请自行甄别文档内容的完整性,平台不提供额外的编辑、内容补充、找答案等附加服务。
- 2、"仅部分预览"的文档,不可在线预览部分如存在完整性等问题,可反馈申请退款(可完整预览的文档不适用该条件!)。
- 3、如文档侵犯您的权益,请联系客服反馈,我们会尽快为您处理(人工客服工作时间:9:00-18:30)。
10种简单的去毛刺方式,适合你的才是最好的
1、人工去毛刺
这个也是一般企业普遍采用的方式,采用锉刀、砂纸、磨头等作为辅助工具。
锉刀有人工锉刀和气动错动。
简评:人工成本较贵,效率不是很高,且对复杂的交叉孔很难去除。
对工人技术要求不是很高,适用毛刺小,产品结构简单的产品。
2、冲模去毛刺
采用制作冲模配合冲床进行去毛刺。
简评:需要一定的冲模(粗模+精冲模)制作费,可能还需要制作整形模。
适合分型面较简单的产品,效率及去毛刺效果比人工佳。
3、研磨去毛刺
此类去毛刺包含振动、喷砂、滚筒等方式,目前企业采用较多。
简评:存在去除不是很干净的问题,可能需要后续人工处理残余毛刺或者配合其他方式去毛刺。
适合批量较大的小产品。
4、冷冻去毛刺
利用降温使毛刺迅速脆化,然后喷射弹丸去除毛刺。
简评:设备价格大概在二三十万;
适合毛刺壁厚较小且产品也较小的产品。
5、热爆去毛刺
也叫热能去毛刺、爆炸去毛刺。
通过将一些易然气体,通入到一个设备炉中,然后通过一些介质及条件的作用,让气体瞬间爆炸,利用爆炸产生的能量来溶解去除毛刺。
简评:设备昂贵(上百万价格),操作技术要求高,效率低,副作用(生锈、变形);主要运用在一些高精密的零部件领域,如汽车航天等精密零部件。
6、雕刻机去毛刺
简评:设备价格不是很贵(几万),适用于空间结构简单,所需去毛刺位置简单有规律。
7、化学去毛刺
用电化学反应原理,对金属材料制成的零件自动地、有选择地完成去毛刺作业。
简评:适用于难于去除的内部毛刺,适合泵体、阀体等产品细小毛刺(厚度小于7丝)。
8、电解去毛刺
利用电解作用去除金属零件毛刺的一种电解加工方法。
简评:电解液有一定腐蚀性,零件毛刺的附近也受到电解作用,表面会失去原有光泽,甚至影响尺寸精度,工件去毛刺后应经过清洗和防锈处理。
电解去毛刺适用于去除零件中隐蔽部位交叉孔或形状复杂零件的毛刺,生产效率高,去毛刺时间一般只需几秒至几十秒。
适用于齿轮、连杆、阀体和曲轴油路孔口等去毛刺,以及尖角倒圆等。
9、高压水喷射去毛刺
以水为媒介,利用它的瞬间冲击力来去除加工后产生的毛刺和飞边,同时可达到清洗的目的。
简评:设备昂贵,主要用于汽车的心脏部位和工程机械的液压控制系统。
10、超声波去毛刺
超声波产生瞬间高压去除毛刺。
简评:主要针对一些微观毛刺,一般如果毛刺需要用显微镜来观察的话,就都可以尝试用超声波的方法去除。
(本文转自沐风机械)。