机床与刀具65
机床加工中的刀具性能测试与评估
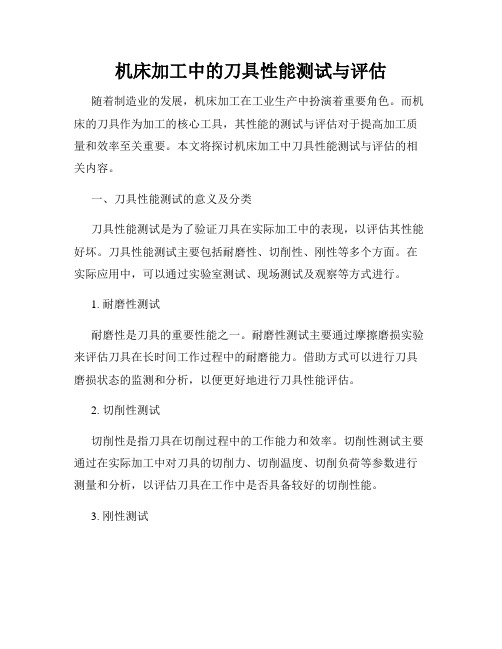
机床加工中的刀具性能测试与评估随着制造业的发展,机床加工在工业生产中扮演着重要角色。
而机床的刀具作为加工的核心工具,其性能的测试与评估对于提高加工质量和效率至关重要。
本文将探讨机床加工中刀具性能测试与评估的相关内容。
一、刀具性能测试的意义及分类刀具性能测试是为了验证刀具在实际加工中的表现,以评估其性能好坏。
刀具性能测试主要包括耐磨性、切削性、刚性等多个方面。
在实际应用中,可以通过实验室测试、现场测试及观察等方式进行。
1. 耐磨性测试耐磨性是刀具的重要性能之一。
耐磨性测试主要通过摩擦磨损实验来评估刀具在长时间工作过程中的耐磨能力。
借助方式可以进行刀具磨损状态的监测和分析,以便更好地进行刀具性能评估。
2. 切削性测试切削性是指刀具在切削过程中的工作能力和效率。
切削性测试主要通过在实际加工中对刀具的切削力、切削温度、切削负荷等参数进行测量和分析,以评估刀具在工作中是否具备较好的切削性能。
3. 刚性测试刀具的刚性对加工精度和表面质量有着重要影响。
刚性测试主要通过对刀具的振动、刚度等参数进行测量和分析,以评估刀具在加工过程中的刚性表现。
二、刀具性能评估的方法刀具性能评估是通过对刀具在实际工作中的表现进行定量分析,以便得出相应的评估结果。
目前常用的刀具性能评估方法主要包括实验测量、数据分析和模拟仿真等。
1. 实验测量方法实验测量方法是最常用的刀具性能评估方法之一。
通过在实际加工中对刀具的切削力、磨损情况、工件表面质量等参数进行测量和分析,以评估刀具的性能。
2. 数据分析方法数据分析方法是一种基于大量数据统计和分析的评估方法。
通过采集和分析刀具的使用数据,如刀具寿命、加工效率等,从而评估刀具的性能。
3. 模拟仿真方法模拟仿真方法是一种通过计算机模拟和仿真技术来评估刀具性能的方法。
通过建立刀具加工过程的仿真模型,模拟刀具的磨损、切削力等情况,以评估刀具的性能。
三、刀具性能测试与评估的意义和挑战刀具性能测试与评估对于提高加工质量和效率具有重要意义。
31数控加工对刀具的要求

3.1数控加工对刀具的要求3.1.1 数控刀具在数控加工中的地位和作用刀具技术和机床技术相结合,工件材料技术与刀具材料技术交替进展,成为切削技术不断向前发展的历史规律,对推动切削技术的发展起着决定性作用。
机床与刀具的发展是相辅相成、相互促进的。
在由机床、刀具和工件组成的切削加工工艺系统中,刀具是最活跃的因素。
刀具切削性能的好坏取决于构成刀具的材料和刀具结构。
切削加工生产率和刀具寿命的高低、加工成本的多少、加工精度和加工表面质量的优劣等,在很大程度上取决于刀具材料、刀具结构及其的合理选择。
随着作为切削加工最基本要素的刀具材料迅速发展。
各种新型刀具材料,其物理力学性能和切削加工性能都有了很大的提高,应用范围也不断扩大。
开发出了许多新型刀具材料的刀具,如聚晶金刚石刀具(PCD)、聚晶立方氮化硼刀具(PCBN)、CVD金刚石刀具、纳米复合刀具、纳米涂层刀具、晶须增韧陶瓷刀具、超细晶粒硬质合金刀具、TiC(N)基硬质合金刀具、粉末冶金高速钢刀具等。
先进的数控机床加工设备只有与高性能的数控刀具相配合,才能发挥其应有的效能,取得良好的经济效益。
数控刀具是指与这些先进高效的数控机床相配套使用的各种刀具的总称,是数控机床不可缺少的关键配套产品,数控刀具以其高效、精密、高速、耐磨、长寿命和良好的综合切削性能取代了传统的刀具。
表3-1-1为传统刀具与现代数控刀具的比较。
表3-1-1 传统刀具与现代数控刀具的比较数控刀具的重要性主要表现在以下几方面:(1) 数控刀具的性能和质量直接影响到数控机床生产效率的高低、加工质量的好坏和经济效益。
数控加工机床生产效率的高低、被加工工件质量的好坏以及生产成本,在很大程度上取决于数控刀具材料及其刀具结构的合理选择。
(2) 数控刀具不仅为先进制造业提供了高效、高性能的切削刀具,而且还由此开发出了许多新的加工工艺,成为当前先进制造技术发展的重要组成部分和显著特征之一。
(3) 数控刀具具有“三高一专”(即高效率、高精度、高可靠性和专用化)的特点,广泛应用于高速切削、精密和超精密加工、干切削、硬切削和难加工材料的加工等先进制造技术领域,可提高加工效率、加工精度和加工表面质量。
机床加工过程中的刀具管理与维护

机床加工过程中的刀具管理与维护在机床加工过程中,刀具是至关重要的工具之一。
良好的刀具管理与维护可以有效地提高机床的加工质量和效率,延长刀具的使用寿命。
本文将介绍一些刀具管理与维护的方法和技巧。
一、刀具管理刀具管理包括采购、入库、领用、使用、保养和报废等环节。
合理的刀具管理可以确保刀具的准时供应和高效利用。
1. 采购:在采购刀具时,应根据加工需求选择合适的刀具类型和规格。
同时,要选择信誉好、质量可靠的供应商,以确保刀具的品质。
2. 入库与领用:刀具入库时,应对其进行严格的检验,确保刀具符合要求。
在领用刀具时,要做好详细的记录,包括刀具型号、数量和领用人员等信息,以便于刀具的使用和追溯。
3. 使用:在使用刀具时,操作人员应该熟悉刀具的使用规范和安全操作要求。
刀具应根据加工要求选择合适的切削参数,避免过度切削或切削不足,从而降低刀具的磨损和损坏。
4. 保养:定期对刀具进行保养是提高其使用寿命的关键。
刀具保养包括清洁、润滑和修复等方面。
清洁时要使用适当的清洁剂,彻底清除刀具表面的切屑和油污。
润滑时要使用专用的润滑剂,以减少刀具与工件之间的摩擦和磨损。
修复方面,可以选择刀具磨削或更换磨损部件等方法进行。
5. 报废:当刀具严重磨损或者无法修复时,应及时进行报废处理。
报废前要对刀具进行检测和评估,以确定是否可以进行再利用或回收。
二、刀具维护刀具维护是刀具管理工作的重要组成部分。
通过合理的维护措施,可以延长刀具的使用寿命,提高加工质量和效率。
1. 定期检查:对刀具进行定期的检查,及时发现和排除潜在故障和问题。
检查内容包括刀具的磨损程度、刃口状态、夹持方式、刀柄紧固情况等。
2. 高效切削润滑:在切削过程中,刀具与工件之间的摩擦和热量会导致刀具磨损和工件表面质量下降。
因此,要选择适当的切削润滑剂,保持切削面的润滑和冷却,减少热量的积聚和刀具的磨损。
3. 及时更换磨损部件:刀具在使用过程中,由于切削力的作用,容易出现磨损或损坏。
金工实习车削加工车床介绍、刀具介绍

二 、车刀的组成
车刀的组成:车刀是由刀体和刀头两部分组 成。刀头担任切削工作,刀体用来安装夹持车刀。
车刀的刀头由三个面,两个切削刃和一个刀 尖组成:前刀面、主后刀面、副后刀面;主切削 刃、副切削刃;刀尖。
2、硬质合金:是用碳化钨、碳化钛和钴等材 料,用粉末冶金方法制成一定形状的刀片,焊接或 机械夹固在中碳钢的刀杆上使用。它具有很高的热 硬性在800℃—1000℃高温下能保持高硬度 HRC74—82。
常用硬质合金有:钨钴和钨钴钛两大类
1)、钨钴类:YG3、YG6、YG8用于半精加 工和精加工,适应于铸铁青铜等脆性材料的加工。
规 格、性 能
2、规格: 以C616—1为例: 加工最大直径为320mm。 最大加工长度750mm。 主轴转速19—1400转/分。 3、性能: 加工精度IT7—IT12 高→低 表面粗糙度Ra12.5—1.6 µm 低→高
二、C616车床的组成部分及其作用
C616车床主要由四箱、两架、一床身及光 杠、丝杠几部分组成。
车削加工是最基本、用途最广的一种刀具 切削加工方法,主要用来加工各种回转表面。
车床的种类很多,有卧式车床、立式车床、 转塔车床、仿形车床及数控车床等,其中以卧 式车床通用性最好,广泛使用。
一、车床的型号、规格、性能
1、型号:以 C6132为例 C —机床类别代号(车床类) 6 —机床组别代号(卧式车床组) 1—机床系别代号(卧式车床系) 32—机床主参数代号(表示床身上工件最大加工回转 直径 320mm 的1/10) 旧:以C616—1 为例 C—车床汉语拼音的第一个字母 6—普通车床 16—最大加工回转半径的1/10 1—第一次改进
数控机床刀具装夹与刀具位置校正方法

数控机床刀具装夹与刀具位置校正方法数控机床是一种利用计算机控制系统进行运动控制的高精度机床。
在数控机床的工作中,刀具的装夹与刀具位置校正是非常重要的环节,它们直接影响着加工工件的精度和质量。
本文将为您介绍数控机床刀具装夹与刀具位置校正的方法,以帮助您更好地理解和应用。
首先,我们来了解一下数控机床刀具的装夹方法。
常见的数控机床刀具装夹方法有机械装夹和液压装夹两种。
机械装夹是利用夹持力将刀具固定在工作台上。
它通常包括夹头、螺栓和刀具座等部件。
夹头是夹持刀具的主要部件,它具有一定的夹持力和刚性,能够保证刀具的固定和稳定。
螺栓用于调整夹头的夹持力,刀具座则用于连接夹头和刀具。
在使用机械装夹时,需要根据刀具的类型和规格选择合适的夹头和刀具座,并通过螺栓调整夹持力,保证刀具的牢固性和稳定性。
液压装夹是利用液压力将刀具固定在工作台上。
它通常包括液压缸、活塞和刀具座等部件。
液压装夹具有夹持力大、夹持刚性好的特点,能够更好地保证刀具的稳定性和精度。
在使用液压装夹时,需要保证液压系统的良好工作状态,及时检查并调整液压缸和活塞的压力,以确保刀具的正确装夹和工作状态。
除了选择合适的刀具装夹方法外,刀具的位置校正也是数控机床加工过程中不可忽视的环节。
刀具位置校正的目的是保证刀具在加工过程中的准确位置,以提高加工精度和质量。
数控机床刀具位置校正的方法主要有以下几种:1. 刀具长度补偿:利用数控系统中的刀具长度补偿功能,通过设定刀具的长度补偿值,使刀具的实际位置与程序中设定的位置相符。
刀具长度补偿的值可以根据实际加工情况进行调整,以确保加工精度的要求。
2. 刀具半径补偿:利用数控系统中的刀具半径补偿功能,通过设定刀具的半径补偿值,使刀具的实际位置与程序中设定的位置相符。
刀具半径补偿的值可以根据实际加工情况进行调整,以保证加工轮廓的精度和形状。
3. 刀具位置校正:利用数控机床的手动或自动操作功能,通过对刀具位置的调整和修正,使其达到加工要求。
数控机床的刀具补偿与补偿方法
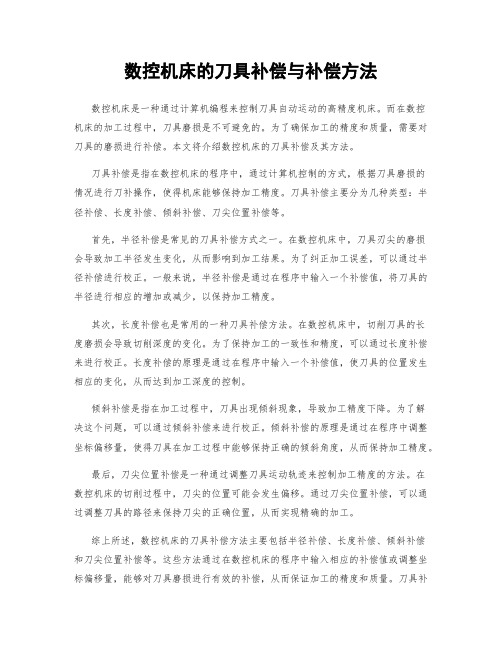
数控机床的刀具补偿与补偿方法数控机床是一种通过计算机编程来控制刀具自动运动的高精度机床。
而在数控机床的加工过程中,刀具磨损是不可避免的。
为了确保加工的精度和质量,需要对刀具的磨损进行补偿。
本文将介绍数控机床的刀具补偿及其方法。
刀具补偿是指在数控机床的程序中,通过计算机控制的方式,根据刀具磨损的情况进行刀补操作,使得机床能够保持加工精度。
刀具补偿主要分为几种类型:半径补偿、长度补偿、倾斜补偿、刀尖位置补偿等。
首先,半径补偿是常见的刀具补偿方式之一。
在数控机床中,刀具刃尖的磨损会导致加工半径发生变化,从而影响到加工结果。
为了纠正加工误差,可以通过半径补偿进行校正。
一般来说,半径补偿是通过在程序中输入一个补偿值,将刀具的半径进行相应的增加或减少,以保持加工精度。
其次,长度补偿也是常用的一种刀具补偿方法。
在数控机床中,切削刀具的长度磨损会导致切削深度的变化。
为了保持加工的一致性和精度,可以通过长度补偿来进行校正。
长度补偿的原理是通过在程序中输入一个补偿值,使刀具的位置发生相应的变化,从而达到加工深度的控制。
倾斜补偿是指在加工过程中,刀具出现倾斜现象,导致加工精度下降。
为了解决这个问题,可以通过倾斜补偿来进行校正。
倾斜补偿的原理是通过在程序中调整坐标偏移量,使得刀具在加工过程中能够保持正确的倾斜角度,从而保持加工精度。
最后,刀尖位置补偿是一种通过调整刀具运动轨迹来控制加工精度的方法。
在数控机床的切削过程中,刀尖的位置可能会发生偏移。
通过刀尖位置补偿,可以通过调整刀具的路径来保持刀尖的正确位置,从而实现精确的加工。
综上所述,数控机床的刀具补偿方法主要包括半径补偿、长度补偿、倾斜补偿和刀尖位置补偿等。
这些方法通过在数控机床的程序中输入相应的补偿值或调整坐标偏移量,能够对刀具磨损进行有效的补偿,从而保证加工的精度和质量。
刀具补偿是数控机床加工过程中不可或缺的一部分,它使得机床能够适应刀具磨损的变化,同时提高了加工的效率与精度。
数控机床刀具的安装与调整方法

数控机床刀具的安装与调整方法在数控机床的加工过程中,刀具的安装与调整是非常重要的环节。
正确的安装和调整可以保证数控机床的正常运行,提高加工效率和产品质量。
本文将介绍数控机床刀具的安装与调整方法,以帮助您正确地操作数控机床。
首先,我们需要了解数控机床刀具的组成。
刀具系统通常由刀柄、刀片、刀夹和刀头组成。
刀柄负责刀具的刚性连接,刀片是刀具的主要工作部分,刀夹用于夹持刀片,刀头则是用于切割材料的工具。
在安装之前,务必保证刀具的质量和完整性。
当安装数控机床刀具时,首先要选择合适的刀具,刀具的选用应根据加工材料和加工方式来确定。
根据所需加工的工件,选择合适的切削速度、进给速度和刀具刃尺寸等参数。
在安装刀柄时,应先清洁刀柄孔和刀片座,确保没有任何异物。
然后将刀柄插入刀柄孔中,利用适当的工具将其固定在机床上。
刀柄的安装位置应严格按照机床的要求进行调整,以确保其与工件之间的距离和角度。
安装刀片时,应先检查刀片的完整性和质量。
将刀片放在刀片座上,确保刀片与刀柄安装牢固。
然后,根据加工要求调整刀片的位置和方向。
调整刀片的位置可以通过移动刀柄或调整夹具来完成。
通过调整刀片的方向,可以选择不同的切削方式,如顺铣、逆铣或高速切削等。
安装刀夹时,应注意刀夹的选择和安装方式。
刀夹的选择应根据刀具的尺寸和形状来确定,确保刀片能够在刀夹中保持良好的稳定性。
安装刀夹时,应将刀具放入夹具中,并利用适当的夹紧力固定刀具。
夹具的安装位置应根据机床的要求进行调整,以确保刀具的刚性连接。
在刀具安装完成后,还需要进行调整和校正。
首先,检查刀具的水平度和垂直度,并进行必要的校正。
然后,调整刀具的位置和方向,以确保其与工件之间的夹紧力和角度均匀。
最后,进行切削试验,检查刀具的切削效果和加工质量。
总之,数控机床刀具的安装和调整是确保数控机床正常运行和提高加工效率的关键环节。
正确的安装和调整可以提高切削效率和产品质量,减少刀具的损耗和机床的停机时间。
机械制造工程学 习题答案 作者 李伟 谭豫之 第3章 机床与刀具(2)
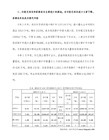
第3章 机床与刀具
特点:
① 粗切齿制成轮切式结构,分块拉削,精切齿采用 成形式结构,分层拉削。② 缩短了拉刀长度。③ 提 高了拉削生产率。④ 拉削后的表面质量较好。
36
机械制造工程学
3、拉削的工艺特点及应用
第3章 机床与刀具
① 生产率高。
② 加工精度高,表面质量好。IT8~IT7,Ra0.8~0.4 μ m。
陶瓷结合剂:(V)
性适能用:范围:
强适用度于高通,用耐砂热轮、、耐成腐形蚀磨性 好削砂,轮气。孔一率般大V,<3但5m较/s脆。, 弹性差。
56
机械制造工程学
三、砂轮的特性与选择
第3章 机床与刀具
4. 结合剂:用来粘结磨料的物质,其性能决定着砂轮 的强度、抗冲击性、耐热性以及抗腐蚀能力
陶瓷结合剂:(V) 树脂结合剂:(B)
第3章 机床与刀具
2_05 镗孔
17
机械制造工程学
2、镗孔的特点
① 镗刀的结构简单,调整方便。 单刃镗刀 多刃镗刀
第3章 机床与刀具
18
机械制造工程学
2、镗孔的特点
第3章 机床与刀具
① 镗刀的结构简单,调整方便。
单刃镗刀
多刃镗刀 ② 通用性大。
经济精度:IT8~IT7
Ra1.6~0.8 2_10 双刃浮动镗刀
陶瓷结合剂:(V) 树脂结合剂:(B) 橡胶结合剂:(R)
性适能用:范围:
强主度要最用高于金,刚导石热砂性轮好及,电但 自解锐磨性削差用砂。轮常见 。的 磨是 削青 硬铜 质 结合合金剂、。玻璃、陶瓷等。
29
机械制造工程学
1、拉刀的特点
第3章 机床与刀具
① 切削刃与被加工表面的横截面形状相同。
数控车床常用刀具及选择
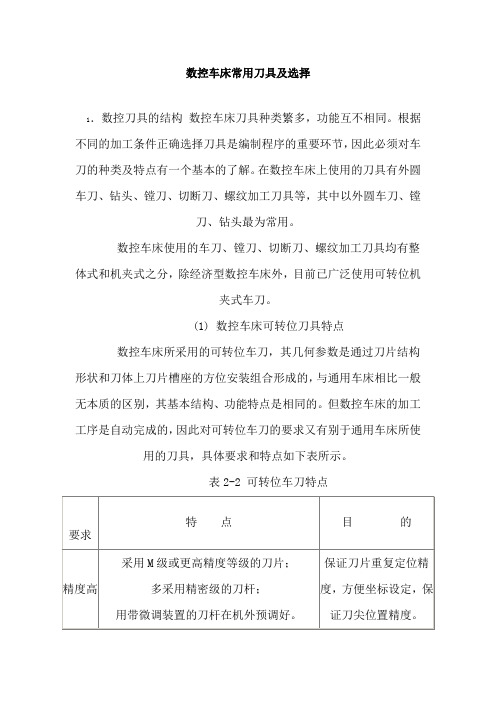
数控车床常用刀具及选择1.数控刀具的结构数控车床刀具种类繁多,功能互不相同。
根据不同的加工条件正确选择刀具是编制程序的重要环节,因此必须对车刀的种类及特点有一个基本的了解。
在数控车床上使用的刀具有外圆车刀、钻头、镗刀、切断刀、螺纹加工刀具等,其中以外圆车刀、镗刀、钻头最为常用。
数控车床使用的车刀、镗刀、切断刀、螺纹加工刀具均有整体式和机夹式之分,除经济型数控车床外,目前已广泛使用可转位机夹式车刀。
(1) 数控车床可转位刀具特点数控车床所采用的可转位车刀,其几何参数是通过刀片结构形状和刀体上刀片槽座的方位安装组合形成的,与通用车床相比一般无本质的区别,其基本结构、功能特点是相同的。
但数控车床的加工工序是自动完成的,因此对可转位车刀的要求又有别于通用车床所使用的刀具,具体要求和特点如下表所示。
表2-2 可转位车刀特点(2) 可转位车刀的种类可转位车刀按其用途可分为外圆车刀、仿形车刀、端面车刀、内圆车刀、切槽车刀、切断车刀和螺纹车刀等,见表2-3。
表2-3 可转位车刀的种类(3) 可转位车刀的结构形式①杠杆式:结构见图2-16,由杠杆、螺钉、刀垫、刀垫销、刀片所组成。
这种方式依靠螺钉旋紧压靠杠杆,由杠杆的力压紧刀片达到夹固的目的。
其特点适合各种正、负前角的刀片,有效的前角范围为-60°~+180°;切屑可无阻碍地流过,切削热不影响螺孔和杠杆;两面槽壁给刀片有力的支撑,并确保转位精度。
②楔块式:其结构见图2-17,由紧定螺钉、刀垫、销、楔块、刀片所组成。
这种方式依靠销与楔块的挤压力将刀片紧固。
其特点适合各种负前角刀片,有效前角的变化范围为-60~+180。
两面无槽壁,便于仿形切削或倒转操作时留有间隙。
③楔块夹紧式:其结构见图2-18,由紧定螺钉、刀垫、销、压紧楔块、刀片所组成。
这种方式依靠销与楔块的压下力将刀片夹紧。
其特点同楔块式,但切屑流畅不如楔块式。
此外还有螺栓上压式、压孔式、上压式等形式。
数控机床刀具寿命的延长与再利用方法

数控机床刀具寿命的延长与再利用方法数控机床刀具是数控加工中不可或缺的重要工具,其寿命的延长和再利用方法对提高生产效率和降低成本具有重要意义。
本文将介绍实现数控机床刀具寿命延长和再利用的几种方法。
首先,在数控机床刀具寿命延长方面,我们可以采取以下措施:1.正确选择和使用刀具材料:不同的加工材料需要选择适合的刀具材料。
例如,钢材通常使用硬质合金刀具,而铝合金则使用高速钢刀具。
2.采用合适的刀具涂层:刀具表面涂层可以有效减少刀具磨损和摩擦,延长刀具寿命。
常见的刀具涂层有涂碳化钛涂层、氮化钛涂层等。
3.合理选择和调整切削参数:根据不同的加工需求和材料特性,合理选择切削速度、进给速度和切削深度等参数,避免刀具过度磨损。
其次,在数控机床刀具再利用方面,我们可以采取以下方法:1.刀具刃口修复:一些磨损较轻的刀具可以通过刃口修复技术进行修复。
刃口修复可以去除刀具损坏部分,恢复其正常使用状态,延长其寿命。
2.刀具重新涂层:对于表面涂层磨损较为严重的刀具,可以进行重新涂层处理。
重新涂层可以修复刀具表面涂层,恢复其使用性能。
3.刀具再磨削:有些刀具可以通过再磨削处理进行修复和再利用。
再磨削可以恢复刀具的新刃,并通过刃磨来达到延长使用寿命的效果。
除了上述方法,还有一些其他值得注意的事项:1.切勿超负荷使用:避免在工作过程中超负荷使用刀具,以免造成刀具磨损过快或损坏。
2.及时检查和更换:定期检查刀具的磨损情况,并根据实际情况及时更换刀具,避免刀具磨损过度导致生产效率下降。
3.合理存放和保养:在刀具使用结束后,应该将其进行合理的存放和保养。
注意刀具的防锈和防腐,避免刀具在存放过程中受到损害。
总的来说,数控机床刀具的寿命延长和再利用是提高生产效率和降低成本的重要手段。
通过正确选择和使用刀具材料、采用合适的刀具涂层、合理调整切削参数等方法可以延长刀具的使用寿命;而刀具刃口修复、重新涂层处理和再磨削等技术可以使刀具得以再利用。
同时,及时检查和更换刀具,合理存放和保养也是刀具寿命延长和再利用的关键。
机床刀具的选择与使用技巧
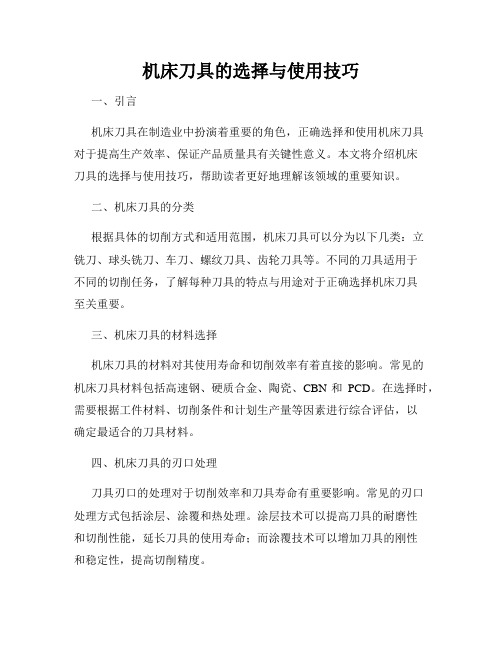
机床刀具的选择与使用技巧一、引言机床刀具在制造业中扮演着重要的角色,正确选择和使用机床刀具对于提高生产效率、保证产品质量具有关键性意义。
本文将介绍机床刀具的选择与使用技巧,帮助读者更好地理解该领域的重要知识。
二、机床刀具的分类根据具体的切削方式和适用范围,机床刀具可以分为以下几类:立铣刀、球头铣刀、车刀、螺纹刀具、齿轮刀具等。
不同的刀具适用于不同的切削任务,了解每种刀具的特点与用途对于正确选择机床刀具至关重要。
三、机床刀具的材料选择机床刀具的材料对其使用寿命和切削效率有着直接的影响。
常见的机床刀具材料包括高速钢、硬质合金、陶瓷、CBN和PCD。
在选择时,需要根据工件材料、切削条件和计划生产量等因素进行综合评估,以确定最适合的刀具材料。
四、机床刀具的刃口处理刀具刃口的处理对于切削效率和刀具寿命有重要影响。
常见的刃口处理方式包括涂层、涂覆和热处理。
涂层技术可以提高刀具的耐磨性和切削性能,延长刀具的使用寿命;而涂覆技术可以增加刀具的刚性和稳定性,提高切削精度。
五、机床刀具的几何参数机床刀具的几何参数对于切削过程中的稳定性和精度具有重要影响。
主要几何参数包括刀尖半径、刃倾角、前角、主偏角和后角等。
正确选择几何参数可以减小切削力、改善切削效果,并降低机床的振动和噪音。
六、机床刀具的切削液选择切削液在机床切削过程中起着冷却、润滑和清洁的作用,对于机床刀具的寿命和切削效果有显著影响。
在选择切削液时,需要考虑工件材料、切削条件和环境要求等因素,确保使用合适的切削液以提供良好的切削条件。
七、机床刀具的日常维护机床刀具的正确维护可以延长其使用寿命,提高生产效率。
日常维护包括定期清洗、涂油和磨损检查等。
另外,还需要注意刀具的正确存放和保养,避免受到外界环境的损害。
八、机床刀具的故障及处理方法在使用机床刀具过程中,可能会出现一些故障,比如断刀、磨损过快和加工精度下降等。
对于不同的故障情况,需要采取相应的处理措施,比如更换刀具、调整切削参数和检修机床等。
数控机床技术中的刀具测量与校准方法
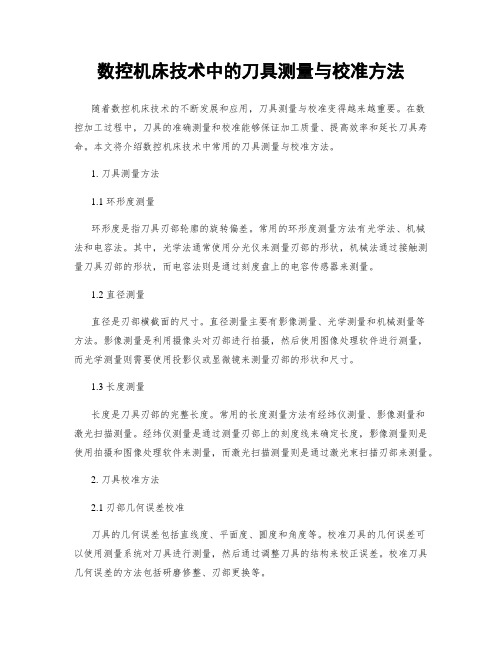
数控机床技术中的刀具测量与校准方法随着数控机床技术的不断发展和应用,刀具测量与校准变得越来越重要。
在数控加工过程中,刀具的准确测量和校准能够保证加工质量、提高效率和延长刀具寿命。
本文将介绍数控机床技术中常用的刀具测量与校准方法。
1. 刀具测量方法1.1 环形度测量环形度是指刀具刃部轮廓的旋转偏差。
常用的环形度测量方法有光学法、机械法和电容法。
其中,光学法通常使用分光仪来测量刃部的形状,机械法通过接触测量刀具刃部的形状,而电容法则是通过刻度盘上的电容传感器来测量。
1.2 直径测量直径是刃部横截面的尺寸。
直径测量主要有影像测量、光学测量和机械测量等方法。
影像测量是利用摄像头对刃部进行拍摄,然后使用图像处理软件进行测量,而光学测量则需要使用投影仪或显微镜来测量刃部的形状和尺寸。
1.3 长度测量长度是刀具刃部的完整长度。
常用的长度测量方法有经纬仪测量、影像测量和激光扫描测量。
经纬仪测量是通过测量刃部上的刻度线来确定长度,影像测量则是使用拍摄和图像处理软件来测量,而激光扫描测量则是通过激光束扫描刃部来测量。
2. 刀具校准方法2.1 刃部几何误差校准刀具的几何误差包括直线度、平面度、圆度和角度等。
校准刀具的几何误差可以使用测量系统对刀具进行测量,然后通过调整刀具的结构来校正误差。
校准刀具几何误差的方法包括研磨修整、刃部更换等。
2.2 刀具动平衡校准刀具在高速旋转时,由于材料不均匀或磨损等原因,会出现不平衡现象,称为刀具动平衡误差。
刀具动平衡校准可以通过旋转平衡机进行,根据测量数据调整刀具的结构或在刀具上增加配重来实现校准。
2.3 刀具刀尖磨合校准刀具刀尖磨合校准是为了消除刀具在加工过程中产生的振动和噪声。
校准方法可以采用研磨修整、镜面涂层和刃部更换等。
研磨修整是通过磨削刀尖来消除磨合不良的表面,镜面涂层则可以提高刀尖的硬度和润滑性。
总结数控机床技术中的刀具测量与校准方法对于保证加工质量、提高效率和延长刀具寿命起着至关重要的作用。
机床刀具的正确选择与使用方法
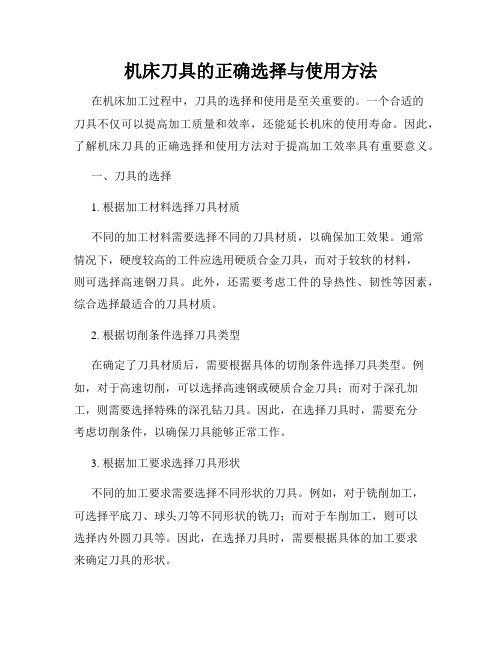
机床刀具的正确选择与使用方法在机床加工过程中,刀具的选择和使用是至关重要的。
一个合适的刀具不仅可以提高加工质量和效率,还能延长机床的使用寿命。
因此,了解机床刀具的正确选择和使用方法对于提高加工效率具有重要意义。
一、刀具的选择1. 根据加工材料选择刀具材质不同的加工材料需要选择不同的刀具材质,以确保加工效果。
通常情况下,硬度较高的工件应选用硬质合金刀具,而对于较软的材料,则可选择高速钢刀具。
此外,还需要考虑工件的导热性、韧性等因素,综合选择最适合的刀具材质。
2. 根据切削条件选择刀具类型在确定了刀具材质后,需要根据具体的切削条件选择刀具类型。
例如,对于高速切削,可以选择高速钢或硬质合金刀具;而对于深孔加工,则需要选择特殊的深孔钻刀具。
因此,在选择刀具时,需要充分考虑切削条件,以确保刀具能够正常工作。
3. 根据加工要求选择刀具形状不同的加工要求需要选择不同形状的刀具。
例如,对于铣削加工,可选择平底刀、球头刀等不同形状的铣刀;而对于车削加工,则可以选择内外圆刀具等。
因此,在选择刀具时,需要根据具体的加工要求来确定刀具的形状。
二、刀具的使用方法1. 切勿超负荷使用刀具刀具在工作时会受到一定的负荷,如果超负荷使用,容易导致刀具磨损过快甚至断裂。
因此,在使用刀具时,需要根据切削条件合理设置切削参数,避免超负荷使用刀具。
2. 定期检查刀具状态刀具在使用过程中会出现磨损,因此需要定期检查刀具状态。
一旦发现刀具磨损严重或者出现其他异常情况,应及时更换或修磨刀具,以确保刀具的正常使用。
3. 注意刀具的保养刀具在使用过程中需要定期进行清洁和保养,以延长刀具的使用寿命。
在清洁时,应使用专用清洁剂擦拭刀具表面,防止刀具受到腐蚀。
同时,在使用完毕后,应将刀具储存在干燥通风的环境中,避免受潮生锈。
总结:正确选择和使用机床刀具对于提高加工效率和质量具有重要意义。
通过根据加工材料选择刀具材质、根据切削条件选择刀具类型、根据加工要求选择刀具形状等方法,能够有效提高刀具的使用效率和寿命。
数控机床刀具夹持与工件装夹技术要点

数控机床刀具夹持与工件装夹技术要点数控机床是现代制造业中不可或缺的重要设备,而刀具夹持和工件装夹技术则是数控机床加工过程中至关重要的环节。
本文将从数控机床刀具夹持和工件装夹两个方面,探讨其技术要点。
一、数控机床刀具夹持技术要点1. 刀具夹持方式的选择刀具夹持方式的选择直接影响到加工质量和效率。
常见的刀具夹持方式有机械夹持、液压夹持和电磁夹持等。
机械夹持适用于加工精度要求不高的工件,液压夹持适用于精密加工,而电磁夹持则适用于高速加工。
2. 刀具夹持力的控制刀具夹持力的控制是保证加工质量的重要因素。
夹持力过大会导致刀具磨损加剧,夹持力过小则会引起刀具与工件之间的相对滑动,影响加工精度。
因此,合理控制刀具夹持力,保证刀具与工件之间的稳定接触是关键。
3. 刀具夹持装置的精度和刚性刀具夹持装置的精度和刚性直接影响到加工精度和稳定性。
刀具夹持装置应具备足够的刚性,以抵抗切削力的作用,避免刀具的振动和变形。
同时,刀具夹持装置的精度也要高,以确保刀具与工件的精确定位和夹持。
二、数控机床工件装夹技术要点1. 工件夹持方式的选择工件夹持方式的选择取决于工件的形状、材料和加工要求。
常见的工件夹持方式有机械夹持、液压夹持和真空吸附等。
机械夹持适用于形状规则的工件,液压夹持适用于大型工件,而真空吸附则适用于薄板材料等。
2. 工件夹持力的控制工件夹持力的控制是保证加工质量和安全的重要因素。
夹持力过大会导致工件变形,夹持力过小则会引起工件的相对移动,影响加工精度。
因此,合理控制工件夹持力,保证工件的稳定夹持是关键。
3. 工件夹持装置的精度和刚性工件夹持装置的精度和刚性对加工精度和稳定性有重要影响。
工件夹持装置应具备足够的刚性,以抵抗切削力的作用,避免工件的振动和变形。
同时,工件夹持装置的精度也要高,以确保工件的精确定位和夹持。
总结:刀具夹持和工件装夹是数控机床加工过程中不可或缺的环节。
合理选择刀具夹持方式和工件夹持方式,控制夹持力,以及保证夹持装置的精度和刚性,是确保加工质量和效率的关键要点。
CNC机床加工过程中的刀具选择与使用

CNC机床加工过程中的刀具选择与使用CNC机床是一种通过计算机程序控制的机床,能够实现高精度的自动加工。
在CNC机床加工过程中,刀具的选择与使用是至关重要的,它们直接影响到加工效率和加工质量。
本文将探讨在CNC机床加工过程中如何选择和使用刀具。
一、刀具选择的原则与技巧在选择刀具时,需要考虑以下几个原则与技巧:1. 材料选择:根据被加工材料的种类,选择适合的刀具材料。
常见的刀具材料有高速钢、硬质合金、陶瓷等。
不同材料的刀具具有不同的硬度和耐磨性,选择合适的刀具材料可以提高切削效率和刀具的使用寿命。
2. 切削速度选择:根据被加工材料的硬度和切削面积,选择合适的切削速度。
切削速度过高会造成刀具磨损严重,切削速度过低则会影响加工效率。
通过试切和经验可以确定合适的切削速度。
3. 刀具形状选择:根据被加工零件的形状和要求,选择合适的刀具形状。
常见的刀具形状有平头刀、球头刀、圆头刀等。
选择合适的刀具形状可以保证加工出符合要求的零件轮廓。
4. 切削液选择:根据被加工材料和切削状态选择合适的切削液。
切削液可以起到冷却、润滑和清洁的作用,提高切削效率和刀具的使用寿命。
二、刀具使用的注意事项在使用刀具时,需要注意以下几个事项:1. 定期检查刀具:定期检查刀具的磨损情况,合理安排刀具的更换周期。
磨损严重的刀具会影响加工质量和加工效率,及时更换刀具可以保证加工的稳定性和准确性。
2. 正确安装刀具:刀具的安装要保证精度和稳定性。
刀具的杆部要清洁,刀具的夹持要牢固。
松动的刀具会导致加工误差和切削不稳定。
3. 合理调整切削参数:根据加工要求和切削情况,合理调整切削参数。
包括切削速度、进给量、切削深度等。
合理调整切削参数可以提高加工效率和加工质量。
4. 切忌过度负荷刀具:在加工过程中,不要过度负荷刀具。
如果刀具超过负荷工作,会导致刀具破损和加工质量下降。
合理安排刀具的负荷,可以延长刀具的使用寿命。
结语CNC机床加工过程中的刀具选择与使用对于保证加工质量和提高加工效率至关重要。
CNC机床加工中的刀具材料选择与刀具性能

CNC机床加工中的刀具材料选择与刀具性能在CNC机床加工中,刀具材料的选择和刀具性能发挥着至关重要的作用。
正确选择刀具材料可以提高切削效率、延长刀具寿命,而刀具性能的优劣也直接影响加工质量和成本。
因此,针对不同的加工需求和工件材料,正确选择刀具材料,并了解刀具性能指标十分必要。
下面将从刀具材料的分类和特点、刀具性能指标以及刀具材料选择的注意事项等方面进行论述。
一、刀具材料的分类和特点1. 高速钢刀具高速钢是常见的刀具材料之一,具有良好的硬度和耐磨性,适用于加工较低硬度的材料。
高速钢刀具还具有较好的韧性和可加工性,广泛应用于常规车削、铣削和钻孔等加工操作中。
然而,高速钢刀具的耐热性和刚性相对较低,不适用于高速、高温的加工环境。
2. 硬质合金刀具硬质合金刀具由高硬度的金属碳化物和粘结相组成,具有较高的硬度、耐磨性和耐热性。
因此,硬质合金刀具适用于加工硬度较高的金属材料,如钢、铸铁和合金钢等。
硬质合金刀具的耐热性较好,可以在高速、高温的加工环境下工作。
然而,硬质合金刀具的脆性较大,容易断裂,因此在加工时需要注意避免过量切削和碰撞。
3. 陶瓷刀具陶瓷刀具由氧化物和非氧化物陶瓷材料制成,具有极高的硬度和耐磨性,适用于加工硬度极高的材料,如铸造铁、铸钢和钛合金等。
陶瓷刀具还具有良好的耐热性和耐腐蚀性,可以在高速、高温和腐蚀性环境下工作。
然而,陶瓷刀具的韧性和抗冲击性较差,容易破碎,因此在使用时需要注意避免碰撞和过量切削。
二、刀具性能指标1. 切削力切削力是指刀具在切削过程中受到的力的大小,也是评价刀具性能的重要指标之一。
切削力的大小直接影响加工过程中的功耗和加工质量,因此选择具有较小切削力的刀具能够降低能耗、提高加工效率。
2. 耐磨性刀具在加工过程中会与工件表面接触,产生摩擦和磨损。
耐磨性是指刀具能够承受摩擦和磨损的能力,直接影响刀具的使用寿命。
具有良好耐磨性的刀具能够延长刀具的寿命、降低工具更换频率。
3. 耐热性耐热性是指刀具在高温环境下不易软化和变形的能力。
木工机床与刀具行业标准目录(一)

标 灌与检测 S na d et t dra s a dnT
木 工机 床 与 刀具 行 业 标 准 目录 ( ) 一
C ne t o d sr l tn adfr o d okn c i r n u i os 1 o tns fn uta a d r o w rigma hn ya dc tn t l( ) i i s ow e tg o
5 .B T 58—19 二 、 、 2 J/ 64 93 三 四面木 工刨 床 技术 条件
5 .B T 54— 93 二 、 、 3J/ 65 19 三 四面木工刨床 参数 5 . B T 37 19 二 、 、 4 G / 152— 92 三 四面木工刨床 精度 5 .B 12 19 二 、 四面木工刨床和铣床 5 J6 1 — 9 2 三、 结构安全 5 .B T 74 9 1 四面木工刨床 静刚度 6 J/ 53 —19 5 . B T 99 — 05 木工机床安全 四面铣床和四面刨床 7 G / 199 20 5 .B T5 0 19 木工平刨床 8J/ 65 — 9 3
3 .B T 18 19 木工带锯机和跑车 4 J/ 37 — 93
3 .B T 55 93 木工带锯机和跑车 5 J/ 35 —19
参数
技术条件
3 . /3 5 . — 99 木工带锯机和跑车 精度 6J ,5 5 1 19 BI
3 2 W OODW ORKI MACHI RY NG NE
3 .B T4 0—19 木 工带锯 机 1J/ 73 94
术语和精度
锯片往复木工锯板机 术语和精度 安装 圆锯 片处 的主轴 直径 锯轴部件端部尺寸
锯轮
3 . 60 — 92 普通木工带锯机 结构安全 2J 18 19 B 3 . 60 — 92 自动进给木工带锯机 结构安全 3J 16 19 B
木工机床与刀具行业标准目录(二)

8 . /2 0 — 0 5 木工机 床安全 镂 铣机 4 GBT 0 6 2 0
8 .Br62 19 普 通木 工车床 参数 5 J厂2 7— 99 8 . BT 7— 4 普通木 工 车床 精度 6 G /136 19 5 9 8 .B 1 19 普通 木工 车床 结构 安全 7 J 6 1 9 2 1— 8 . BT 9 8— 05 木工机 床 盘式 磨光 机 术语 8 G /196 20
19 J/79 — 94 木 工刨 刀刃磨 机 技术 条件 0.BT 4 7 19 10 J/7 9.— 99 木工 刨 刀刃磨 机 精度 .BT 4 71 19 1 1 J/79 .—9 9 木工 刨刀 刃磨 机 参数 1 BT 4 7 19 1. 2
12 J52 — 9 1 木工磨刀机 结构安全 .B 7 5 19 1 13 J/73 —9 4 木 工 自动 万能磨 锯机 技术条 件 .BT 4 3 19 1
8 . BT 2 — 0 0 木工机 床 宽带 砂光 机 术语 9 G /122 20 8
9 .BT 5 6 19 木 工 多用 机床 技 术条件 0 J/64 — 93 9 .BT 561 19 木工 多用 机床 参 数 1J/64 .— 93 9 .BT 562 19 木工 多用 机床 精 度 2 J/64 .— 3 9 9 .BT 17 19 木 工 多用 机床 结 构安 全 3 J/60 — 92 9 .BT 5 1 19 木 工平 压两用 刨床 技 术条件 4 J/6 5— 93 9 .B1 5 1 — 93 木工 平压 两用刨 床 参 数 5 J,6 5. 19 r 1 9 .BT 5 2 19 木工 平压两 用刨 床 精度 6 J/65 .— 3 1 9 9 . B 5— 0 3 木工 机床 安全 平压 两用 刨床 7 G 96 20 1 8 9 .BT 5 7 19 台式 多用 木工 机床 技 术条 件 8 J/65 — 93 9 .B15 5 19 台式 多用 木工 机床 参数 9 J,65 — 93 r 10 J/6 5— 93 台式 多用 木工 机床 精 度 0 .BT 5 6 19
- 1、下载文档前请自行甄别文档内容的完整性,平台不提供额外的编辑、内容补充、找答案等附加服务。
- 2、"仅部分预览"的文档,不可在线预览部分如存在完整性等问题,可反馈申请退款(可完整预览的文档不适用该条件!)。
- 3、如文档侵犯您的权益,请联系客服反馈,我们会尽快为您处理(人工客服工作时间:9:00-18:30)。
拉床、刨床、插床加工分析
拉床、刨床、插床加工分析
? 拉刀的类型及其应用 按受力不同分为:拉刀和推刀
按加工工件表面不同分为:内拉刀和外拉刀
? 内拉刀是加工工件内表面的,常见的有圆孔拉刀、键 槽拉刀及花键孔拉刀; ? 外拉刀是加工工件外表面的,常见的有平面拉刀、 成形表面拉刀及外齿轮拉刀等。 按拉刀结构不同可分为:整体式与组合式拉刀。
拉床、刨床、插床加工分析
? 拉削方式
圆孔拉刀的结构及拉削过程
拉床、刨床、插床加工分析
? 拉刀类型
小径定心渐开线花键拉刀
拉床、刨床、插床加工分析
? 拉刀类型
键槽拉刀
拉床、刨床、插床加工分析
? 拉刀类型
花键拉刀
拉床、刨床、插床加工分析
? 拉刀类型
圆拉刀
拉床、刨床、插床加工分析
? 拉刀类型
异形拉刀
拉床、刨床、插床加工分析
?拉刀切削部分设计参数
1)齿升量af:前、后两刀 齿半径或高度之差。 影响拉削力、拉刀长度、 生产率和加工表面质量。
粗切齿: af=0.02~
0.20mm
精切齿: af=0.005 ~
0.015mm
拉床、刨床、插床加工分析
?拉刀切削部分设计参数
2)齿距p:相邻两刀齿之间的轴向距离。
Hale Waihona Puke 、刨削、插削加工? 插床: 用插刀
加工工件表面的机 床。实质是立式刨 床 主要用于加工:工 件的内表面,如内 孔中键槽、多边形 孔、成形内表面
插床
二、刨削、插削加工
? 插床:
插床的运动(成形运动): 主运动—滑枕带动插刀沿垂直方向(立柱的导轨3)所作的往复 直线运动。向下运动是工作行程,向上是空行程。 进给运动—工作台可作纵、横两个方向的进给运动,圆形工作 台可绕垂直轴旋转,完成圆周进给或进行分度。 床鞍6完成横向进给运动,溜板7完成纵向进给运动。
影响容屑空间、同时工作齿数及工作平稳性。 3)前角γo:根据工件材料选择。 4)后角αo:为使刀齿前刀面重磨之后,直径变小较慢,以及 延长拉刀的使用寿命,拉刀的后角应取较小值。
5)刃带宽度ba1 其作用是制造时便于控制刀齿直径、保持切削过程的稳定
性和重磨后保持直径不变。
拉床、刨床、插床加工分析
? 拉削方式
第四章 金属切削机床基本知识 拉床、刨床、插床加工分析
拉床、刨床、插床加工分析
一、拉削加工 在拉床上用拉刀加工工件的工艺过程,称为拉削加工。 ? 拉削工艺范围广:不但可以加工各种形状的通孔,还可以拉 削平面及各种组合成形面。
由于受拉刀制造工艺以及拉床动力的限制,过小或过大尺寸 的孔不适宜拉削加工(拉削孔径一般为10~100mm,孔的深径比 一般不超过5),盲孔、台阶孔和薄壁孔也不适宜拉削加工。 ? 拉削加工特点: 拉削加工质量好,生产率高。拉刀寿命长,并且拉床结构简单。 但拉刀结构复杂,制造比较麻烦,价格较高,因而多用于大量和 批量生产的精加工。
分块式拉削
分块式拉削与分层式拉削的区别在于:工件上的每层金属 是由一组尺寸基本相同的刀齿切去,每个刀齿仅切去一层金属 的一部分。
拉床、刨床、插床加工分析
? 综合式拉削:综合了上述两种拉削方式的优点,拉刀短,生 产率高,加工表面也较光洁。
综合式拉削
集中了以上两种拉削的优点,即粗切齿制成分块式结构,精切 齿则采用分层式结构,这样即缩短了拉刀长度,保持较高生产率 ,又获得较好的工件表面质量。我国生产的圆孔拉刀较多的采用 该结构。
拉床、刨床、插床加工分析
二、刨削、插削加工
刨床和插床的主运动→直线运动,属于直线运动机床 ? 刨床:用刨刀加工工件的机床
主要用于加工各种平面(水平面、垂直面、斜面)和沟槽 (T形槽、燕尾槽、V形槽)。 ? 刨床的运动(成形运动):主运动和进给运动都是直线运动。 ? 主要类型:
1.牛头刨床
2.龙门刨床
? 分层式拉削:可获得较高的表面质量,但拉刀长度较长,
生产率较低
分层式拉削图形
切削部的刀齿高度向后递增,工件上的拉削余量被一层一 层地切去,最终由最后一个切削齿切出所要求的尺寸,经校准 齿修光达到预定的尺寸精度及表面粗糙度。
拉床、刨床、插床加工分析
? 分块式拉削:拉刀长度短,生产率高,但拉刀结构复杂,制造 困难,拉削后的工件表面比较粗糙。
2.龙门刨床
适用加工:大型 或重型零件上 的各种平面、 沟槽和各种导 轨面(长而窄 的平面和沟槽) 或多件加工
二、刨削、插削加工
龙门刨床
二、刨削、插削加工
2.龙门刨床 工作台带动工件沿床身导轨作纵向往复直线运动—主运动; 横梁上两个垂直刀架,可在横梁导轨上作水平方向进给运动 —横向进给运动; 左右侧刀架,可分别沿垂直方向作进给运动,以加工侧平面 —垂直进给运动; 横梁可沿左右立柱的导轨作垂直升降,以调整刀架位置,适 应不同高度工件的加工需要—辅助运动(调整运动)。
2. 拉刀的结构
头部——与机床连接,传递运动和拉力。 颈部——头部和过渡锥连接部分。 过渡锥部——使拉刀容易进入工件孔中,起对准中心的作用。 前导部——起导向和定心作用,防止拉刀歪斜,并可检查拉削前孔径是否太小, 以免拉刀第一刀齿负荷太大而损坏。 切削部——切除全部的加工余量,由粗切齿、过渡齿和精切齿组成。 校准部——起校准和修光作用,并作为精切齿的后备齿。 后导部——保持拉刀最后几个刀齿的正确位置,防止拉刀即将离开工件时, 工件下垂而损坏已加工表面。 尾部——防止长而重的拉刀自重下垂,影响加工质量和损坏 刀齿。
整体式主要用于中、小型尺寸的高速钢拉刀;组合式主 要用于大尺寸拉刀和硬质合金拉刀。
拉床、刨床、插床加工分析
拉刀的类型
拉床、刨床、插床加工分析
YL-6120A 型拉床
拉床、刨床、插床加工分析
? 拉刀的结构
圆孔拉刀的结构 1-头部;2-颈部;3-过渡圆锥;4-前导部 5-切削部;6-校准部;7-后导部;8-尾部
二、刨削、插削加工 1.牛头刨床:用于加工小型(尺寸和重量较小)零件
二、刨削、插削加工
1. 牛头刨床: 滑枕可带动刀具沿床身的水平导轨作往复运动—主运动 工作台带动工件沿滑板导轨作间歇的横向进给运动—进给运动
刀座可绕水平轴线转动,刀架可沿刀座导轨移动,以适应不同 的加工角度和调整切削深度—辅助运动(切入运动和调整运动) 滑板可床身的垂直导轨上下移动,以工件的不同高度—辅助运 动(调整运动); 主运动的传动方式: 机械传动:常用曲柄摇杆机构; 液压传动:用于规格较大的牛头刨床。 进给运动的传动方式: 机械传动:一般采用棘轮机构; 液压传动。