焦化企业能耗与节能潜力分析
彭楠焦化工业能耗及节能工作
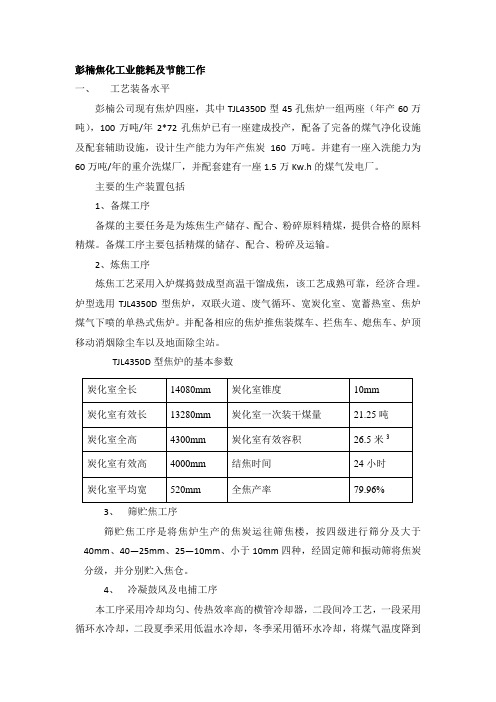
彭楠焦化工业能耗及节能工作一、工艺装备水平彭楠公司现有焦炉四座,其中TJL4350D型45孔焦炉一组两座(年产60万吨),100万吨/年2*72孔焦炉已有一座建成投产,配备了完备的煤气净化设施及配套辅助设施,设计生产能力为年产焦炭160万吨。
并建有一座入洗能力为60万吨/年的重介洗煤厂,并配套建有一座1.5万Kw.h的煤气发电厂。
主要的生产装置包括1、备煤工序备煤的主要任务是为炼焦生产储存、配合、粉碎原料精煤,提供合格的原料精煤。
备煤工序主要包括精煤的储存、配合、粉碎及运输。
2、炼焦工序炼焦工艺采用入炉煤捣鼓成型高温干馏成焦,该工艺成熟可靠,经济合理。
炉型选用TJL4350D型焦炉,双联火道、废气循环、宽炭化室、宽蓄热室、焦炉煤气下喷的单热式焦炉。
并配备相应的焦炉推焦装煤车、拦焦车、熄焦车、炉顶移动消烟除尘车以及地面除尘站。
TJL4350D型焦炉的基本参数3、筛贮焦工序筛贮焦工序是将焦炉生产的焦炭运往筛焦楼,按四级进行筛分及大于40mm、40—25mm、25—10mm、小于10mm四种,经固定筛和振动筛将焦炭分级,并分别贮入焦仓。
4、冷凝鼓风及电捕工序本工序采用冷却均匀、传热效率高的横管冷却器,二段间冷工艺,一段采用循环水冷却,二段夏季采用低温水冷却,冬季采用循环水冷却,将煤气温度降到23度以下,煤气中的焦油和萘尽量脱除,确保后续工序的正常运行。
煤气加压采用离心风机,并配套液力偶合器调速。
焦油氨水的分离采用机械化焦油氨水澄清槽。
煤气中的焦油雾及萘的清除,采用高效率的蜂窝式电捕焦油器,并布置在鼓风机前,最大限度的脱除煤气中的焦油雾滴及萘,保护风机,提高后续工序的开工率。
5、脱硫及蒸氨工序本工序采用焦炉煤气中的氨作为碱源,以PDS脱硫剂作催化剂的湿法脱硫工艺,该法脱硫效率较高。
6、硫铵及蒸氨工序采用先进的喷淋式饱和器吸收煤气中的氨,生成硫酸铵,经离心分离、干燥获得硫铵产品。
将剩余氨水和粗苯分离水进行混合蒸氨,浓氨气进进入饱和器,蒸氨废水再经生化处理后熄焦。
焦化行业节能降耗空间巨大
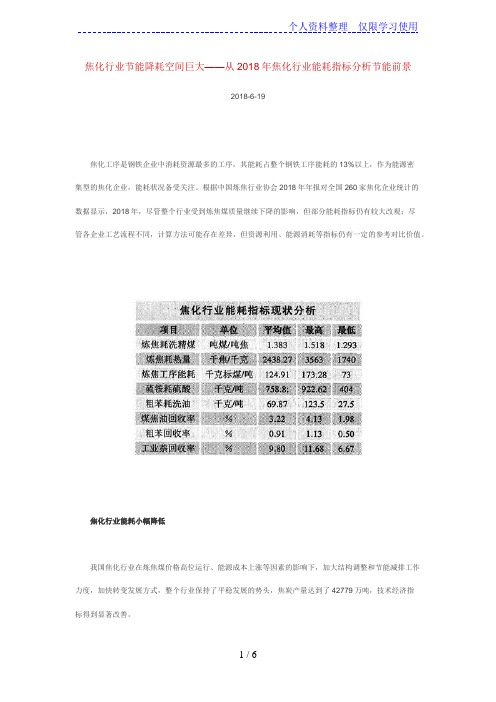
焦化行业节能降耗空间巨大——从2018年焦化行业能耗指标分析节能前景2018-6-19焦化工序是钢铁企业中消耗资源最多的工序,其能耗占整个钢铁工序能耗的13%以上,作为能源密集型的焦化企业,能耗状况备受关注。
根据中国炼焦行业协会2018年年报对全国260家焦化企业统计的数据显示,2018年,尽管整个行业受到炼焦煤质量继续下降的影响,但部分能耗指标仍有较大改观;尽管各企业工艺流程不同,计算方法可能存在差异,但资源利用、能源消耗等指标仍有一定的参考对比价值。
焦化行业能耗小幅降低我国焦化行业在炼焦煤价格高位运行、能源成本上涨等因素的影响下,加大结构调整和节能减排工作力度,加快转变发展方式,整个行业保持了平稳发展的势头,焦炭产量达到了42779万吨,技术经济指标得到显著改善。
炼焦耗洗精煤、炼焦耗热量和炼焦工序能耗是焦化行业的三大能耗指标,代表着焦化企业的整体管理水平。
2018年焦化行业炼焦耗热量、炼焦工序能耗指标比2070年略有下降,但幅度不大,如炼焦工序能耗只比2018年降低了0.64千克标煤/吨焦,改善幅度为0.5%;重点统计焦化企业吨焦耗洗精煤达1.383吨煤/吨焦,增加43千克吨煤/吨焦,比2018年增长了3.2%。
受炼焦煤质量影响,2018年炼焦配合煤灰分比2018年增长1%,导致焦炭灰分增长12.95%,同比提高3%;焦炭硫分也比2018年增长0.02%。
2018年大中型钢铁企业焦炭平均干熄焦率达到84.7%,焦化企业煤气放散率降至2%以下,水二次循环利用率提高0.3%,但我国30%以上焦化企业的吨焦耗电量,远远高于炼焦行业清洁生产每吨焦小于40千瓦时的标准,新水消耗量距2.5立方M/吨焦的标准尚有不小差距,部分焦化企业的耗水量超过了3立方M/吨焦。
化工产品回收率有所提高近年来在煤、焦价格严重倒挂趋势延续的状况下,焦化企业面临多种生产成本压力,2018年重点焦化企业炼焦煤平均采购成本上涨12.94%,冶金焦制造成本上涨10.5%。
延迟焦化装置的能耗分析和节能措施
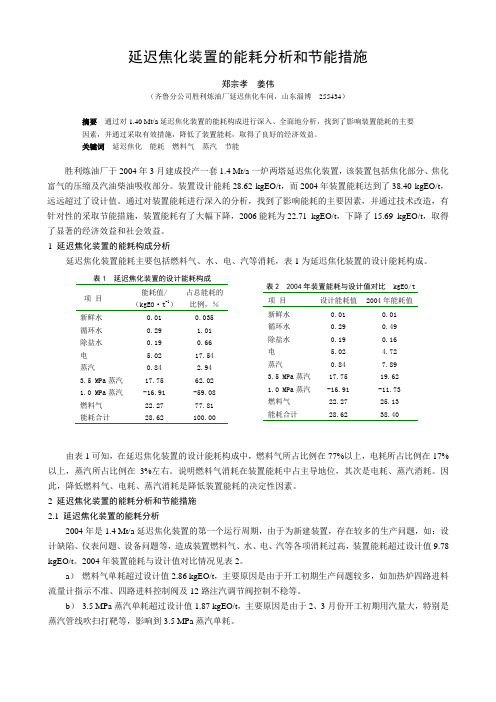
延迟焦化装置的能耗分析和节能措施郑宗孝 姜伟(齐鲁分公司胜利炼油厂延迟焦化车间,山东淄博 255434)摘要 通过对1.40 Mt/a 延迟焦化装置的能耗构成进行深入、全面地分析,找到了影响装置能耗的主要因素,并通过采取有效措施,降低了装置能耗,取得了良好的经济效益。
关键词 延迟焦化 能耗 燃料气 蒸汽 节能胜利炼油厂于2004年3月建成投产一套1.4 Mt/a 一炉两塔延迟焦化装置,该装置包括焦化部分、焦化富气的压缩及汽油柴油吸收部分。
装置设计能耗28.62 kgEO/t ,而2004年装置能耗达到了38.40 kgEO/t ,远远超过了设计值。
通过对装置能耗进行深入的分析,找到了影响能耗的主要因素,并通过技术改造,有针对性的采取节能措施,装置能耗有了大幅下降,2006能耗为22.71 kgEO/t ,下降了15.69 kgEO/t ,取得了显著的经济效益和社会效益。
1 延迟焦化装置的能耗构成分析延迟焦化装置能耗主要包括燃料气、水、电、汽等消耗,表1为延迟焦化装置的设计能耗构成。
由表1可知,在延迟焦化装置的设计能耗构成中,燃料气所占比例在77%以上,电耗所占比例在17%以上,蒸汽所占比例在3%左右。
说明燃料气消耗在装置能耗中占主导地位,其次是电耗、蒸汽消耗。
因此,降低燃料气、电耗、蒸汽消耗是降低装置能耗的决定性因素。
2 延迟焦化装置的能耗分析和节能措施 2.1 延迟焦化装置的能耗分析2004年是1.4 Mt/a 延迟焦化装置的第一个运行周期,由于为新建装置,存在较多的生产问题,如:设计缺陷、仪表问题、设备问题等,造成装置燃料气、水、电、汽等各项消耗过高,装置能耗超过设计值9.78 kgEO/t 。
2004年装置能耗与设计值对比情况见表2。
a ) 燃料气单耗超过设计值2.86 kgEO/t ,主要原因是由于开工初期生产问题较多,如加热炉四路进料流量计指示不准、四路进料控制阀及12路注汽调节阀控制不稳等。
焦化厂节能减排的现状分析和未来展望
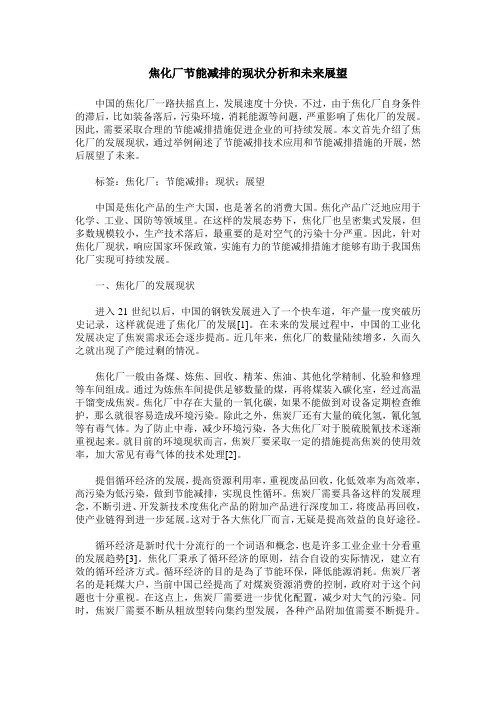
焦化厂节能减排的现状分析和未来展望中国的焦化厂一路扶摇直上,发展速度十分快。
不过,由于焦化厂自身条件的滞后,比如装备落后,污染环境,消耗能源等问题,严重影响了焦化厂的发展。
因此,需要采取合理的节能减排措施促进企业的可持续发展。
本文首先介绍了焦化厂的发展现状,通过举例阐述了节能减排技术应用和节能减排措施的开展,然后展望了未来。
标签:焦化厂;节能减排;现状;展望中国是焦化产品的生产大国,也是著名的消费大国。
焦化产品广泛地应用于化学、工业、国防等领域里。
在这样的发展态势下,焦化厂也呈密集式发展,但多数规模较小,生产技术落后,最重要的是对空气的污染十分严重。
因此,针对焦化厂现状,响应国家环保政策,实施有力的节能减排措施才能够有助于我国焦化厂实现可持续发展。
一、焦化厂的发展现状进入21世纪以后,中国的钢铁发展进入了一个快车道,年产量一度突破历史记录,这样就促进了焦化厂的发展[1]。
在未来的发展过程中,中国的工业化发展决定了焦炭需求还会逐步提高。
近几年来,焦化厂的数量陆续增多,久而久之就出现了产能过剩的情况。
焦化厂一般由备煤、炼焦、回收、精苯、焦油、其他化学精制、化验和修理等车间组成。
通过为炼焦车间提供足够数量的煤,再将煤装入碳化室,经过高温干馏变成焦炭。
焦化厂中存在大量的一氧化碳,如果不能做到对设备定期检查维护,那么就很容易造成环境污染。
除此之外,焦炭厂还有大量的硫化氢,氰化氢等有毒气体。
为了防止中毒,减少环境污染,各大焦化厂对于脱硫脱氰技术逐渐重视起来。
就目前的环境现状而言,焦炭厂要采取一定的措施提高焦炭的使用效率,加大常见有毒气体的技术处理[2]。
提倡循环经济的发展,提高资源利用率,重视废品回收,化低效率为高效率,高污染为低污染,做到节能减排,实现良性循环。
焦炭厂需要具备这样的发展理念,不断引进、开发新技术度焦化产品的附加产品进行深度加工,将废品再回收,使产业链得到进一步延展。
这对于各大焦化厂而言,无疑是提高效益的良好途径。
焦化装置能耗分析及节能措施的应用2100字
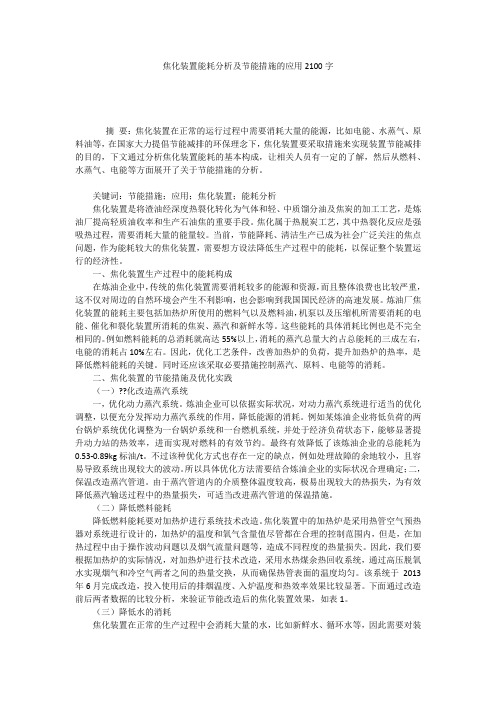
焦化装置能耗分析及节能措施的应用2100字摘要:焦化装置在正常的运行过程中需要消耗大量的能源,比如电能、水蒸气、原料油等,在国家大力提倡节能减排的环保理念下,焦化装置要采取措施来实现装置节能减排的目的,下文通过分析焦化装置能耗的基本构成,让相关人员有一定的了解,然后从燃料、水蒸气、电能等方面展开了关于节能措施的分析。
关键词:节能措施;应用;焦化装置;能耗分析焦化装置是将渣油经深度热裂化转化为气体和轻、中质馏分油及焦炭的加工工艺,是炼油厂提高轻质油收率和生产石油焦的重要手段。
焦化属于热脱炭工艺,其中热裂化反应是强吸热过程,需要消耗大量的能量较。
当前,节能降耗、清洁生产已成为社会广泛关注的焦点问题,作为能耗较大的焦化装置,需要想方设法降低生产过程中的能耗,以保证整个装置运行的经济性。
一、焦化装置生产过程中的能耗构成在炼油企业中,传统的焦化装置需要消耗较多的能源和资源,而且整体浪费也比较严重,这不仅对周边的自然环境会产生不利影响,也会影响到我国国民经济的高速发展。
炼油厂焦化装置的能耗主要包括加热炉所使用的燃料气以及燃料油,机泵以及压缩机所需要消耗的电能、催化和裂化装置所消耗的焦炭、蒸汽和新鲜水等。
这些能耗的具体消耗比例也是不完全相同的。
例如燃料能耗的总消耗就高达55%以上,消耗的蒸汽总量大约占总能耗的三成左右,电能的消耗占10%左右。
因此,优化工艺条件,改善加热炉的负荷,提升加热炉的热率,是降低燃料能耗的关键。
同时还应该采取必要措施控制蒸汽、原料、电能等的消耗。
二、焦化装置的节能措施及优化实践(一)??化改造蒸汽系统一,优化动力蒸汽系统。
炼油企业可以依据实际状况,对动力蒸汽系统进行适当的优化调整,以便充分发挥动力蒸汽系统的作用,降低能源的消耗。
例如某炼油企业将低负荷的两台锅炉系统优化调整为一台锅炉系统和一台燃机系统,并处于经济负荷状态下,能够显著提升动力站的热效率,进而实现对燃料的有效节约。
最终有效降低了该炼油企业的总能耗为0.53-0.89kg标油/t。
焦化厂节能降耗方案

焦化厂节能降耗方案焦化厂作为重工业行业,能源消耗较大,排放污染物也较为严重,所以要想实现节能降耗是非常重要的。
下面是我对焦化厂节能降耗方案的一些建议。
1.优化生产工艺在焦化生产过程中,可以采用先进的焦炉技术,如热风炉、热顶炉等,使其燃烧效率更高。
此外,合理安排焦炉炉型结构,使煤气产生更加充分利用,减少能源的浪费。
另外,在配煤时合理选用合适的煤种,以降低焦化过程中的能源消耗。
2.推广余热回收利用技术焦化过程会产生大量的余热,如果能够将这些余热有效地回收利用,将能够显著地降低焦化厂的能源消耗。
可以利用余热发电、余热利用等技术,将余热转化为电力或热能供应给生产设备或周边区域。
此外,还可以将余热用于再生焦炉燃烧,提高焦化炉燃烧效率。
3.环保设施改造焦化过程中会产生大量的污水和废气,所以要想降低能源消耗,还需要对环保设施进行改造。
可以采用先进的污水处理技术,如生物法、反渗透等,将污水处理后再利用或排放。
同时,对废气进行高效治理,如安装炉顶封罩、布袋除尘器等,减少废气的排放。
4.强化能源管理建立完善的能源管理体系,制定相应的能源管理制度和标准,加强对能源的监测和分析。
通过对能源的监测和分析,找出能源消耗的主要问题和瓶颈,然后制定相应的改善措施。
此外,培养员工的节能意识,通过培训和教育等方式提高员工对能源节约的认识和重视程度。
5.加强能源技术研发焦化厂要想实现节能降耗,还需要加大对能源技术的研发和引进力度。
可以与科研院所、高校等合作,开展能源技术研发工作,推动能源技术的创新和应用。
可以开发制造更加节能高效的设备,引进先进的能源管理系统,提高能源利用效率。
综上所述,焦化厂节能降耗方案包括优化生产工艺、推广余热回收利用技术、环保设施改造、强化能源管理和加强能源技术研发等。
只有综合多种手段,全面提高能源利用效率,才能够实现焦化厂的节能降耗目标,减少能源消耗和环境污染。
延迟焦化装置能耗分析及降耗探讨

延迟焦化装置能耗分析及降耗探讨延迟焦化装置是煤化工产业中常用的一种装置,它主要用于焦化煤的加热处理,促使煤中的挥发分析分解出来,从而得到焦炭、焦油和煤气等产品。
在延迟焦化过程中,能耗是一个非常重要的问题。
本文将对延迟焦化装置的能耗进行分析,并就如何降低能耗进行探讨。
一、延迟焦化装置能耗分析1. 燃料消耗延迟焦化装置在加热煤炭的过程中需要消耗大量的燃料。
燃料的类型包括煤炭、天然气、柴油等。
燃烧燃料产生的热量用于加热煤炭,使得煤中的挥发分解出来。
燃料消耗是延迟焦化装置主要的能耗来源之一。
2. 电力消耗延迟焦化装置中的一些设备,如电动机、风机、泵等都需要消耗电力。
这些设备的运行对于延迟焦化装置的正常运行至关重要,但同时也占据了一定的能耗。
3. 蒸汽消耗在延迟焦化过程中,有些装置需要使用蒸汽进行加热处理。
蒸汽是一种重要的能源源,其消耗也对整个延迟焦化装置的能耗有一定的影响。
二、降耗探讨1. 提高设备效率对于延迟焦化装置中的设备,可以通过技术手段进行改造和提升效率。
可以采用高效的电动机、风机等设备,以减少电力消耗;可以对加热炉进行技术改造,提高燃料利用率,减少燃料消耗;可以对蒸汽系统进行优化,减少蒸汽的消耗等。
2. 优化工艺流程通过对延迟焦化装置的工艺流程进行优化,可以降低能耗。
可以对热交换设备进行合理配置,提高热能利用率;可以采用先进的控制系统,对设备进行精细调控,降低能耗。
3. 节约能源在延迟焦化装置的生产过程中,可以采取一些节能措施,如加强能源管理,优化设备运行参数,增加热能回收等,来降低能耗。
4. 加强能耗监测通过加强对延迟焦化装置能耗的监测和分析,及时发现能耗异常,采取相应的措施进行调整,以降低能耗。
结语延迟焦化装置的能耗分析及降耗探讨是一个复杂的课题,需要综合考虑设备、工艺、能源等多方面因素。
通过优化设备、改进工艺、节约能源等措施,可以有效降低延迟焦化装置的能耗,提高其生产效率和经济效益。
希望随着技术的进步和管理水平的提高,延迟焦化装置能耗能够得到进一步的降低,在保证生产的前提下实现能源的节约和减排。
浅 谈 焦 化 厂 节 能
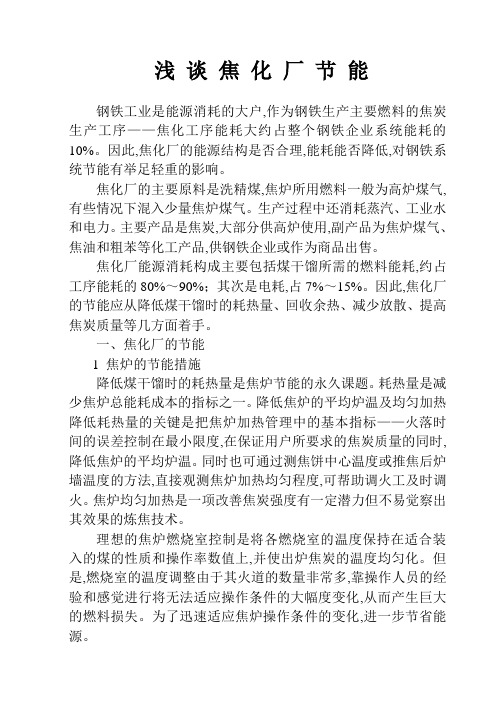
浅谈焦化厂节能钢铁工业是能源消耗的大户,作为钢铁生产主要燃料的焦炭生产工序——焦化工序能耗大约占整个钢铁企业系统能耗的10%。
因此,焦化厂的能源结构是否合理,能耗能否降低,对钢铁系统节能有举足轻重的影响。
焦化厂的主要原料是洗精煤,焦炉所用燃料一般为高炉煤气,有些情况下混入少量焦炉煤气。
生产过程中还消耗蒸汽、工业水和电力。
主要产品是焦炭,大部分供高炉使用,副产品为焦炉煤气、焦油和粗苯等化工产品,供钢铁企业或作为商品出售。
焦化厂能源消耗构成主要包括煤干馏所需的燃料能耗,约占工序能耗的80%~90%;其次是电耗,占7%~15%。
因此,焦化厂的节能应从降低煤干馏时的耗热量、回收余热、减少放散、提高焦炭质量等几方面着手。
一、焦化厂的节能1 焦炉的节能措施降低煤干馏时的耗热量是焦炉节能的永久课题。
耗热量是减少焦炉总能耗成本的指标之一。
降低焦炉的平均炉温及均匀加热降低耗热量的关键是把焦炉加热管理中的基本指标——火落时间的误差控制在最小限度,在保证用户所要求的焦炭质量的同时,降低焦炉的平均炉温。
同时也可通过测焦饼中心温度或推焦后炉墙温度的方法,直接观测焦炉加热均匀程度,可帮助调火工及时调火。
焦炉均匀加热是一项改善焦炭强度有一定潜力但不易觉察出其效果的炼焦技术。
理想的焦炉燃烧室控制是将各燃烧室的温度保持在适合装入的煤的性质和操作率数值上,并使出炉焦炭的温度均匀化。
但是,燃烧室的温度调整由于其火道的数量非常多,靠操作人员的经验和感觉进行将无法适应操作条件的大幅度变化,从而产生巨大的燃料损失。
为了迅速适应焦炉操作条件的变化,进一步节省能源。
2 焦炉配煤的调湿技术为了满足规定的焦炭质量,炼铁用焦通常是在配合十几种原料煤后用焦炉干馏生产的。
焦化工序能耗中,原料煤和干馏耗热量所占比例较大。
煤的调湿技术以减少上述能耗为目的。
焦炉的调湿煤设备是将通常8%~12%的焦炉装入煤水分预先干燥至5%~6%,炼焦耗热量大幅度下降。
因此,焦化厂可以因地制宜,充分利用焦炉燃烧废气的显热进行煤调湿。
浅 谈 焦 化 厂 节 能
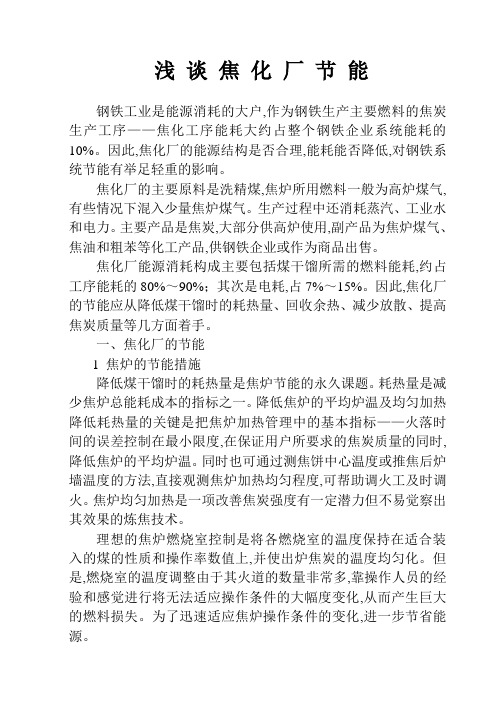
浅谈焦化厂节能钢铁工业是能源消耗的大户,作为钢铁生产主要燃料的焦炭生产工序——焦化工序能耗大约占整个钢铁企业系统能耗的10%。
因此,焦化厂的能源结构是否合理,能耗能否降低,对钢铁系统节能有举足轻重的影响。
焦化厂的主要原料是洗精煤,焦炉所用燃料一般为高炉煤气,有些情况下混入少量焦炉煤气。
生产过程中还消耗蒸汽、工业水和电力。
主要产品是焦炭,大部分供高炉使用,副产品为焦炉煤气、焦油和粗苯等化工产品,供钢铁企业或作为商品出售。
焦化厂能源消耗构成主要包括煤干馏所需的燃料能耗,约占工序能耗的80%~90%;其次是电耗,占7%~15%。
因此,焦化厂的节能应从降低煤干馏时的耗热量、回收余热、减少放散、提高焦炭质量等几方面着手。
一、焦化厂的节能1 焦炉的节能措施降低煤干馏时的耗热量是焦炉节能的永久课题。
耗热量是减少焦炉总能耗成本的指标之一。
降低焦炉的平均炉温及均匀加热降低耗热量的关键是把焦炉加热管理中的基本指标——火落时间的误差控制在最小限度,在保证用户所要求的焦炭质量的同时,降低焦炉的平均炉温。
同时也可通过测焦饼中心温度或推焦后炉墙温度的方法,直接观测焦炉加热均匀程度,可帮助调火工及时调火。
焦炉均匀加热是一项改善焦炭强度有一定潜力但不易觉察出其效果的炼焦技术。
理想的焦炉燃烧室控制是将各燃烧室的温度保持在适合装入的煤的性质和操作率数值上,并使出炉焦炭的温度均匀化。
但是,燃烧室的温度调整由于其火道的数量非常多,靠操作人员的经验和感觉进行将无法适应操作条件的大幅度变化,从而产生巨大的燃料损失。
为了迅速适应焦炉操作条件的变化,进一步节省能源。
2 焦炉配煤的调湿技术为了满足规定的焦炭质量,炼铁用焦通常是在配合十几种原料煤后用焦炉干馏生产的。
焦化工序能耗中,原料煤和干馏耗热量所占比例较大。
煤的调湿技术以减少上述能耗为目的。
焦炉的调湿煤设备是将通常8%~12%的焦炉装入煤水分预先干燥至5%~6%,炼焦耗热量大幅度下降。
因此,焦化厂可以因地制宜,充分利用焦炉燃烧废气的显热进行煤调湿。
延迟焦化装置能耗分析及降耗探讨

延迟焦化装置能耗分析及降耗探讨引言随着工业化进程的不断推进,能源消耗问题日益突出。
在石化行业中,延迟焦化装置是能耗较大的设备之一,因此对其能耗进行分析并探讨降耗措施对于提高能源利用效率和降低生产成本至关重要。
一、延迟焦化装置能耗分析1. 焦化装置的能耗来源延迟焦化装置是炼油厂的重要设备,主要用于将重质馏分通过热裂解反应转化成轻质馏分和延迟焦炭。
焦化装置的能耗主要包括原料预热、热裂解反应、冷却凝析等环节。
热裂解反应是焦化装置的主要能耗环节,占据了总能耗的大部分。
2. 能耗分析在热裂解反应过程中,主要能耗包括加热炉燃料能耗、试验裂解炉燃料能耗、原料预热能耗、冷却凝析能耗等。
根据实际测算数据,加热炉燃料能耗占总能耗的30%,试验裂解炉燃料能耗占总能耗的25%,原料预热能耗占总能耗的20%,冷却凝析能耗占总能耗的15%。
由此可见,热裂解反应是延迟焦化装置的主要能耗来源。
二、延迟焦化装置能耗降耗探讨1. 提高热效率为了减少焦化装置的能耗,首先要提高热效率。
通过改善热裂解反应过程中的热量传递和利用方式,可以降低加热炉和试验裂解炉的燃料能耗。
采用先进的热交换设备和节能技术,可以有效提高热效率,降低能耗。
2. 优化操作控制优化操作控制是降低延迟焦化装置能耗的重要手段。
通过提高原料预热和冷却凝析过程的操作控制水平,合理调整操作参数,可以降低能耗。
加强设备检修和维护,保持设备正常运行状态,也能有效降低能耗。
3. 推广新技术推广新技术是减少能耗的重要途径。
随着科技的不断进步,石化行业不断涌现出新的节能技术和设备。
通过引进新技术,改造现有设备,更新老旧设备,可以显著降低延迟焦化装置的能耗。
4. 加强管理和培训加强管理和培训是降低能耗的基础。
通过建立完善的管理体系,加强设备运行监控和检测,实施能耗考核和激励机制,提高员工节能意识和技能水平,可以有效降低延迟焦化装置的能耗。
三、结语延迟焦化装置是炼油厂的关键设备之一,对其能耗进行分析并开展降耗探讨对于提高炼油厂的能源利用效率和降低生产成本具有重要意义。
焦化节能
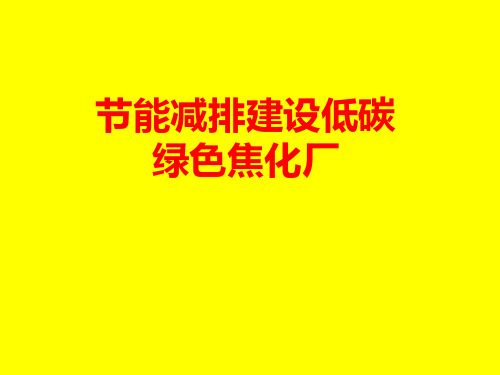
4
研发荒煤气带出热的回收和利用
从炭化室经上升管逸出的650℃~700℃荒煤气 带出热占焦炉总热量36%。为了冷却高温的荒煤气必
须喷洒大量70℃~75℃循环氨水,高温荒煤气因循环
氨水的大量蒸发而被冷却至82℃~85℃,再经初冷器
冷却至22℃~35℃,荒煤气带出热被白白浪费。
冷却水 22~35℃
喷洒氨水
节能减排建设低碳 绿色焦化厂
1.炼焦行业节能减排潜力大
焦化厂是能源转换工厂,在巨大 的能源转换过程中节能潜力巨大。只要 降低单位产品的能耗,就能节省巨大的 能量。最近徐匡迪院士指出:目前钢铁 企业尚有30%的余热、余能未被回收利 用。其中,焦化过程约有50千克/吨焦。
100kwh/t焦
电 电站
2000m3/t焦 废气
祝2010年全国冶金焦化信息网 大会圆满成功
谢 谢
来自脱硫再生塔底的部分脱硫贫液
三 段 22℃焦炉煤气去电扑焦油器
荒煤气带出热用于再生脱硫液
最近,我国江苏双良集团开发出一种热水制冷机, 可利用初冷器第一段65℃高温冷却水制取16℃的低温 水,就近用于焦化厂初冷器第三段的低温冷却。以年 产120万吨焦炭焦化厂为例,如果取初冷器第一段高 温冷却水温度为68℃/58℃,则可取出750t/h热水,可 以实现320万kcal/h的制冷量。虽然热水制冷的成本 大约是常规蒸汽制冷的一倍,但其投资回收期基本上 在2.5年以内。
器上段与荒煤气间接换热。换热后脱硫贫液通过再
生塔底部闪蒸装置,产生蒸汽,作为脱硫液再生热 源,节能效果显著。对于一个年产200万吨焦炭焦化
厂,年节约低压蒸汽26万吨,相当于回收利用了25%
荒煤气带出热。此技术已在焦化工程中推广。
来自焦炉荒煤气
焦化企业能耗与节能潜力分析
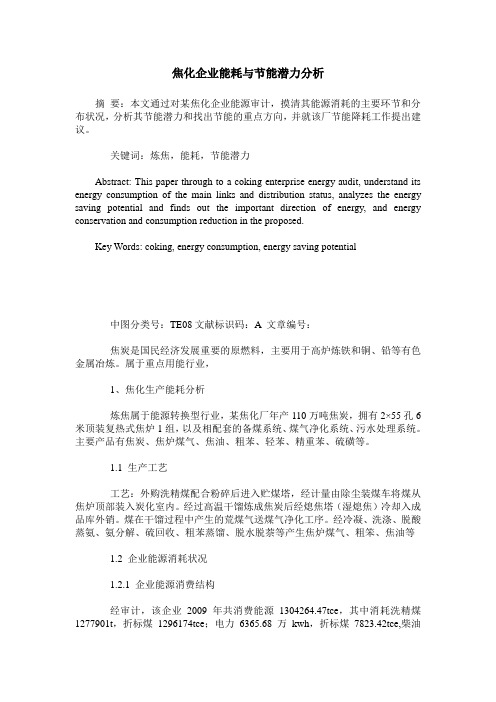
焦化企业能耗与节能潜力分析摘要:本文通过对某焦化企业能源审计,摸清其能源消耗的主要环节和分布状况,分析其节能潜力和找出节能的重点方向,并就该厂节能降耗工作提出建议。
关键词:炼焦,能耗,节能潜力Abstract: This paper through to a coking enterprise energy audit, understand its energy consumption of the main links and distribution status, analyzes the energy saving potential and finds out the important direction of energy, and energy conservation and consumption reduction in the proposed.Key Words: coking, energy consumption, energy saving potential中图分类号:TE08文献标识码:A 文章编号:焦炭是国民经济发展重要的原燃料,主要用于高炉炼铁和铜、铅等有色金属冶炼。
属于重点用能行业,1、焦化生产能耗分析炼焦属于能源转换型行业,某焦化厂年产110万吨焦炭,拥有2×55孔6米顶装复热式焦炉1组,以及相配套的备煤系统、煤气净化系统、污水处理系统。
主要产品有焦炭、焦炉煤气、焦油、粗苯、轻苯、精重苯、硫磺等。
1.1 生产工艺工艺:外购洗精煤配合粉碎后进入贮煤塔,经计量由除尘装煤车将煤从焦炉顶部装入炭化室内。
经过高温干馏炼成焦炭后经熄焦塔(湿熄焦)冷却入成品库外销。
煤在干馏过程中产生的荒煤气送煤气净化工序。
经冷凝、洗涤、脱酸蒸氨、氨分解、硫回收、粗苯蒸馏、脱水脱萘等产生焦炉煤气、粗笨、焦油等1.2 企业能源消耗状况1.2.1 企业能源消费结构经审计,该企业2009年共消费能源1304264.47tce,其中消耗洗精煤1277901t,折标煤1296174tce;电力6365.68万kwh,折标煤7823.42tce,柴油100.46t,折标煤146.38 tce,消耗自来水139.65万t,折标煤119.68tce产出焦炭1001091t,折标准煤972459.80tce;焦油42995t, 折标准煤49138.99tce;粗笨12570t,折标准煤17957.50tce;外销焦炉煤气24171.67万m³,折标准煤122689.12tce. 2009年综合能耗为141971.31tce,能源转换率为89.11%。
延迟焦化装置能耗分析与节能措施
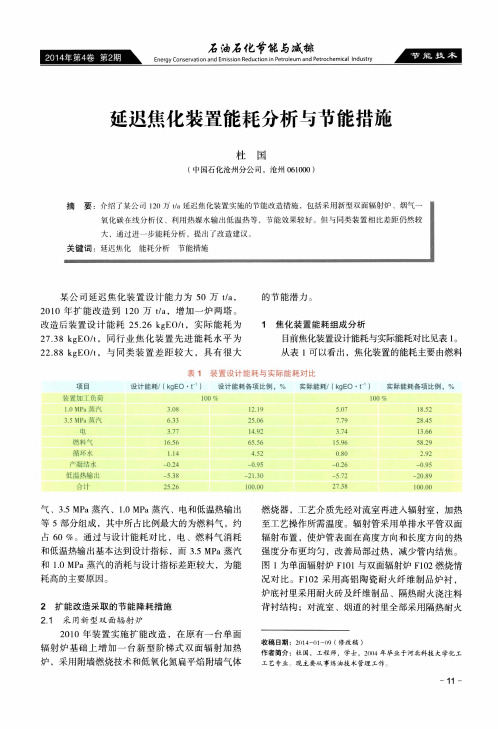
蒸汽;分馏塔和吸收稳定 系统低温热没有有效利 用,而采用循环水空冷冷却。
装置改造后:1) 分馏塔中段系统与原料换热 后引入解析塔重沸器,蜡油系统与原料换热后引入 稳定塔重沸器;2) 回收分馏塔顶、顶循系统等80℃ 以上低温热,通过热媒水 输出装置。以“温度对
口,梯 级利用”为原 则,串并联 交叉使用低温 热, 热媒水换热网络见图3 。
12 一
表2( :¨分析
序号
名称
…一”川’
:
、,1、…蠢_I_l h
4
㈨1I ,孜,}√÷
5
m&/( 时一I J 。l
实施 前
实施 后
0
1 00
2.2
0.8
74
39
92
92. 7
O.2
竺竺:兰兰!!兰兰三!!!二竺三!!!!竺)lI嗣盈I蚕商盈譬蟹盐
2.3优化换热网络 装置改造前:吸收稳定重沸器热源为3.5 MPa
行定点测量,由于烟气偏流和混合不均等原因,使 得这 种测量不 能充分反 映整个 加热炉的 燃烧情况 , 另外氧化锆对氧含量变化的反应很慢,无法满足控 制系统对燃烧波动的及时响应。为此装置增上了
c 0在线分析仪,通过对C0的控制来直接控制燃烧 的效果,实现燃料和空气的最佳配比,降低燃烧过 程中和烟气中的氧含量,减少过剩空气,提高加热 炉的热效率,节约炉的操作更 加安全和平稳。图2为CO/O,/N0,燃烧关系。
焦化厂节能降耗
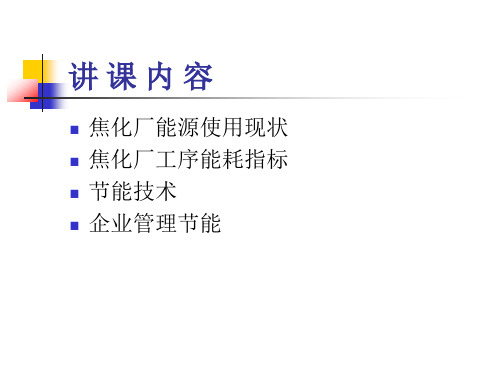
焦化厂能源使用现状 焦化厂工序能耗指标 节能技术 企业管理节能
1、我厂能源消耗现状
我厂能源消耗的主要途径: 焦炉:焦炉煤气、高炉煤气、转炉煤气、仪
表空气、工业新水、电
化产:焦炉煤气、工业新水、蒸汽、氮 气、空气、电 煤备:电、蒸汽(冬季) 运焦:电、蒸汽(冬季)、空气
2008年6月份能源消耗分配表
熵分析法、火用分析法
(一)最小外部损失原则
(1)减少跑、冒、滴、漏。跑、冒、滴、漏造成的 损失,不容忽视。
例如,每小时泄漏423K的饱和蒸汽15㎏,相当于每 年损失标准煤1.64×104㎏=16.4 t
(2)减少废弃物和污染物的排放量,减少可燃气体和 有用气体的放空。
(3)减少散热和散冷损失等。设备、管道保温和保冷 不良,由于系统和环境的热交换而造成散热和散冷损失。
(4)余热的回收利用。首先要调查余热的数量、质量 及稳定性,看余热回收是否必要和用途,在此基础上确定 余热回收的方法。
(二)最佳推动力原则
从能量利用的观点看,一切过程都是能量的 传递和转化过程,都是在一定的热力学势差(如 温度差、压力差、电位差、化学位差等)推动下 进行。过程进行的速率与推动力成正比,没有热 力学势差,就没有推动力的过程,实际上是无法 实现的。由于任何热力学势差都是不可逆因素, 都会导致过程的火用损失。
主要是指生产过程中回收的产品、热能 等,如我厂回收作业区回收的轻苯、重 苯、焦油;焦炉回收的煤气;干熄焦回 收的余热等。
能源消耗=投入能量-回收能量
企业能耗技术指标
企业能耗的技术指标是用来衡量和评价企业设备的耗 能大小,用能水平,节能能力、能源科学管理完善程度 及同行业对比的指标。
由于行业不同设备繁多,为了全面反映上述情况,指 标必须合理,还必须具有综合性和可比性。评价企业能 耗的技术指标可以分为两类:
焦炭项目节能评估报告
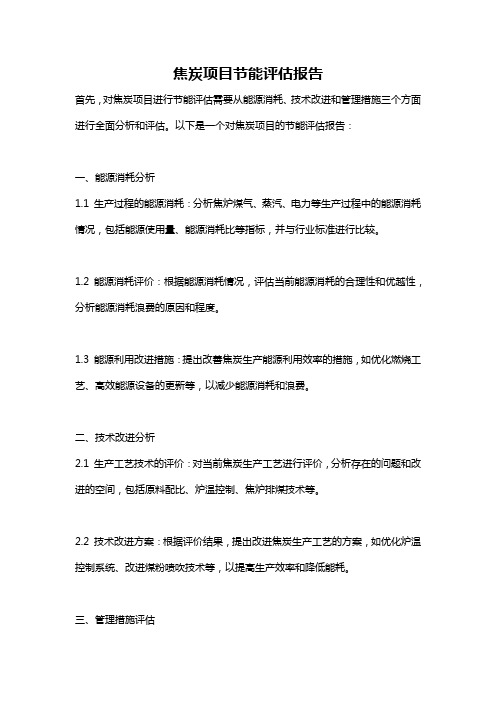
焦炭项目节能评估报告首先,对焦炭项目进行节能评估需要从能源消耗、技术改进和管理措施三个方面进行全面分析和评估。
以下是一个对焦炭项目的节能评估报告:一、能源消耗分析1.1 生产过程的能源消耗:分析焦炉煤气、蒸汽、电力等生产过程中的能源消耗情况,包括能源使用量、能源消耗比等指标,并与行业标准进行比较。
1.2 能源消耗评价:根据能源消耗情况,评估当前能源消耗的合理性和优越性,分析能源消耗浪费的原因和程度。
1.3 能源利用改进措施:提出改善焦炭生产能源利用效率的措施,如优化燃烧工艺、高效能源设备的更新等,以减少能源消耗和浪费。
二、技术改进分析2.1 生产工艺技术的评价:对当前焦炭生产工艺进行评价,分析存在的问题和改进的空间,包括原料配比、炉温控制、焦炉排煤技术等。
2.2 技术改进方案:根据评价结果,提出改进焦炭生产工艺的方案,如优化炉温控制系统、改进煤粉喷吹技术等,以提高生产效率和降低能耗。
三、管理措施评估3.1 管理制度分析:评估焦炭生产过程中的管理制度,包括能源管理制度、设备维护管理制度等,分析存在的问题和改进的空间。
3.2 管理措施改进方案:提出改进焦炭生产管理制度的方案,如加强能源管理考核、建立设备维护纪录等,以提升能源利用效率和减少系统能耗。
总结:通过综合分析能源消耗、技术改进和管理措施三个方面的评估,可以得出一个综合评价结果。
该结果可以给出建议和措施,如优化能源消耗结构、提高能源利用效率、改进生产工艺技术等,以降低焦炭项目的能耗和环境影响,促进项目的可持续发展。
在报告中,需要详细说明每一方面的评估方法和分析结果,提出具体的改进建议和措施,并给出实施这些改进建议和措施所带来的效益预估,以便项目管理方能更好地判断是否值得采纳和推广。
新型煤化工企业能耗现状与节能潜力分析

新型煤化工企业能耗现状与节能潜力分析摘要:近几年来,我国煤化工企业发展迅猛,但煤化工企业在生产过程中,不仅会排放大量污染物(如氮氧化物等),而且也会消耗大量能源。
由此可见,煤化工企业的迅猛发展,会出现严重的高能耗问题;这必将影响国家拟定的低碳节能增长目标。
因此,需要认真研究煤化工企业的能耗问题,并且要认真寻找节能措施。
关键词:新型煤化工;能耗现状;节能潜力1煤化工企业能耗现状分析(1)能源利用率较低。
作为煤化工大国,我国对化工产品的需求较大。
从目前发展情况来看,煤化工在制造、生产过程中都取得了优异的“成绩”;而且煤化工生产能力领先于其他国家,甚至远超世界。
但煤化工产品的单位耗电量也高于国外同类产品。
例如,日本的煤化工工业企业单位用电量仅为我国同类产品的1/8;这意味着国内煤化工企业能源利用率过低。
以过低的能源利用率生产大量煤化工产品,必然造成高能耗问题。
此外,煤炭是不可再生资源,现在一些产煤大省为了谋求本地的经济社会发展,争相发展煤化工项目,使用、消耗了大量煤炭;这会在宏观层面上造成高能耗的问题。
(2)新技术研发力度较小。
从现阶段发展情况来看,国家还没有为节能技术的应用搭建相匹配的应用机制,而且也没有建立降低成本和增加利润的应用机制。
根据2015-2019年统计数据显示,目前仍有30%的煤化工企业处于设备和技术还未更新的情况,这也导致用电量较大的情况,无法满足煤化工企业的发展需要。
同时,新技术开发和研究,也存在缺乏技术、缺乏研发投入、缺乏人员情况,从而阻碍了煤化工行业淘汰高耗能生产方式。
因此,在当前和今后很长一段时期,国内煤化工企业将只能生产成本较高、能耗较高的产品。
2企业节能潜力分析和建议随着我国经济和科技水平的不断发展,新型煤化工技术逐渐在煤化工行业广泛应用。
我国经济发展需要消耗大量的煤炭资源,煤化工行业技术创新带来大量煤炭资源应用的同时,也带来了很多环境问题。
要想满足经济效益和生态效益的共同发展,需要将节能减排技术应用到新型煤化工领域中,促进产业结构升级。
新型煤化工企业能耗现状与节能潜力分析

新型煤化工企业能耗现状与节能潜力分析摘要:随着我国人民生活水平的提高,人们越来越重视节能环保。
在这一过程中,合理的节能减排举措在控制能源消耗上具有重要的价值,增加环保工作效率,帮助化工企业健康发展。
所以化工企业必须不断优化传统化学工艺,以实现节能减排的目标,为行业的可持续发展做出贡献。
基于此,本篇文章对新型煤化工企业能耗现状与节能潜力分析进行研究,以供参考。
关键词:新型煤化工;能耗现状;节能引言社会的高速发展给人们的生活生产提供了极大的便利,但是也衍生出了能源危机问题。
现阶段,如电力、石油化工行业等大多数行业的经营和发展都夹杂着能源消耗问题。
社会产业结构的优化和技术的变革离不开能源的支持,在能源危机日益加重的当下,节能降耗也成为当下社会发展过程中重要面对的课题方向。
而作为高能耗、高污染的化工行业,落实节能降耗技术也是社会发展的必要要求。
1生产工艺流程概述化工企业生产甲醇主要消耗的能源是焦炉煤气、中压蒸汽、电和水。
来自化产公司的焦炉煤气,首先进入湿法脱硫工段,在此阶段,煤气中的硫化氢含量脱除至小于20mg/m3后送往焦炉气压缩机,经多级压缩后提高焦炉煤气压力,送入精脱硫工段。
此后,依次经过过滤器、预脱硫槽、焦炉气初预热器、一级加氢、氧化铁脱硫槽、二级加氢、氧化锌脱硫槽后,进入转化工段,焦炉气进行自热转化。
在转化炉中催化剂作用下,焦炉煤气中的甲烷发生转化反应,控制出口气体CH4≤0.9%,经过废锅和进一步脱氯、脱硫后,气体中总硫达到0.1ppm以下去合成压缩机。
转化气经过九级压缩,得到的原料气送往甲醇合成系统。
合成塔催化剂床层,在220~260℃下CO、CO2与H2反应生成甲醇和水,同时还有微量的有机杂质生成,热反应气体经过气气换热器、水冷器和甲醇分离器后,得到不溶气体和粗甲醇。
不溶气体部分回到合成气压缩循环利用,部分作为燃料或原料进行综合利用,粗甲醇去精馏工段,经过三塔精馏系统(预精馏塔、加压精馏塔和常压精馏塔),得到精甲醇和杂醇油。
- 1、下载文档前请自行甄别文档内容的完整性,平台不提供额外的编辑、内容补充、找答案等附加服务。
- 2、"仅部分预览"的文档,不可在线预览部分如存在完整性等问题,可反馈申请退款(可完整预览的文档不适用该条件!)。
- 3、如文档侵犯您的权益,请联系客服反馈,我们会尽快为您处理(人工客服工作时间:9:00-18:30)。
焦化企业能耗与节能潜力分析
摘要:本文通过对某焦化企业能源审计,摸清其能源消耗的主要环节和分布状况,分析其节能潜力和找出节能的重点方向,并就该厂节能降耗工作提出建议。
关键词:炼焦,能耗,节能潜力
Abstract: This paper through to a coking enterprise energy audit, understand its energy consumption of the main links and distribution status, analyzes the energy saving potential and finds out the important direction of energy, and energy conservation and consumption reduction in the proposed.
Key Words: coking, energy consumption, energy saving potential
中图分类号:TE08文献标识码:A 文章编号:
焦炭是国民经济发展重要的原燃料,主要用于高炉炼铁和铜、铅等有色金属冶炼。
属于重点用能行业,
1、焦化生产能耗分析
炼焦属于能源转换型行业,某焦化厂年产110万吨焦炭,拥有2×55孔6米顶装复热式焦炉1组,以及相配套的备煤系统、煤气净化系统、污水处理系统。
主要产品有焦炭、焦炉煤气、焦油、粗苯、轻苯、精重苯、硫磺等。
1.1 生产工艺
工艺:外购洗精煤配合粉碎后进入贮煤塔,经计量由除尘装煤车将煤从焦炉顶部装入炭化室内。
经过高温干馏炼成焦炭后经熄焦塔(湿熄焦)冷却入成品库外销。
煤在干馏过程中产生的荒煤气送煤气净化工序。
经冷凝、洗涤、脱酸蒸氨、氨分解、硫回收、粗苯蒸馏、脱水脱萘等产生焦炉煤气、粗笨、焦油等
1.2 企业能源消耗状况
1.2.1 企业能源消费结构
经审计,该企业2009年共消费能源1304264.47tce,其中消耗洗精煤1277901t,折标煤1296174tce;电力6365.68万kwh,折标煤7823.42tce,柴油
100.46t,折标煤146.38 tce,消耗自来水139.65万t,折标煤119.68tce
产出焦炭1001091t,折标准煤972459.80tce;焦油42995t, 折标准煤49138.99tce;粗笨12570t,折标准煤17957.50tce;外销焦炉煤气24171.67万m³,折标准煤122689.12tce. 2009年综合能耗为141971.31tce,能源转换率为89.11%。
1.2.2该企业各主要生产工序能源消耗流向如下:
能源品种单位备煤工序炼焦工序化产工序动力辅助部门损失合计
电力万kWh 442 647 4127 1133 17 6366
tce 543 795 5072 1393 20 7823
焦炉
煤气万m3 94 20169 958 5587 26808
tce 536 115246 5475 31924 153181
水m3 2641 67006 876010 450767 1396424
tce 0.23 5.74 75 38.63 119.6
柴油t 100 0 100
tce 146 0 146
蒸汽t 7884 9102 189231 52626 55925 314768
tce 1014 1170 24335 6768 7192 40479
合计tce 2239 117217 34957 40123 7212 201748
比例% 1.11 58.1 17.33 19.89 3.58 100
从表中可以看出炼焦工序、化产和动力辅助部门为主要耗能功能工序,应作为节能工作的重点。
2、产品能耗指标
根据该厂能源消耗总量和各工序能量消耗统计,以及静态和动态统计方
法统计的产品产量,得出该厂的主要产品能耗如下
焦炭单位产品能耗=能源转换差/干基全焦产量=141971.31/1001091=141.82kece/t
公司单耗国家限额河北省限额国家先进值工信部标杆值
焦炭单位铲平综合能耗kgce/t 141.82 155 152 115 105
公司单位产品综合能耗141.82kgce/t,低于国家限定值和河北省限额值,但与国家先进值以及工信部标杆值相比仍存在着较大的差距。
主要原因是公司余热资源利用不充分,红焦余热,烟气余热未能有效利用,吨焦电耗较高等,公司仍存在着较大的节能潜力。
3、焦炉系统效率分析
公司2×55孔JN60型顶装复热式焦炉,主要运行参数及测试数据如下:
燃料参数成分分析表
种类H2 CH4 CO N2 CO2 CmHn O2 Qnet,ar(MJ/m3)
焦炉煤气57.6 24.8 7.6 4.4 2.5 2.5 0.7 17.84
Mt Mad Vad Aad F cad Sd
入炉煤 9.2 0.93 20.51 9.27 69.29 0.71
出炉焦炭 3.4 0.43 1.57 12.49 85.51 0.62
焦炉系统测试数据
设备名称设备型号主要能源热效率(%)湿煤耗热量(kJ/kg)
焦炉JN-60型煤炭、焦炉煤气74.42 2423
锅炉测试数据
给水温度
℃蒸发量
t /h 蒸汽温度
℃蒸汽压力
MPa 排烟温度
℃排烟O2含量% 热效率
%
102 40 420 3.10 134.7 9.02 89.77
由测试分析结果可以看出,入炉煤水分较大,湿煤耗热量偏高,建议企业在生产工艺允许条件下降低配合煤水分,减少能源消耗。
对焦炉不同部位科学合理地选用隔热保温材料,提高焦炉热效率。
锅炉实际热效率为89.77%,未达到设计效率91%的水平,企业应调整负荷,使锅炉达到经济运行状态。
4、机电设备测试分析
配电变压器测试结果
设备名称设备型号负载率/% 功率因数负载系数效率/%
1#煤塔变S9-1000/10 38 0.70 0.24 98.28
动力分厂1#变S9-1000/10 76 0.86 0.05 96.38
炼焦分厂2#变S9-1000/10 68 0.98 0.11 98.12
泵类设备测试结果
设备名称型号电机额定功率电机输入功率电机功率
因数电机负载率泵输出功率泵类效率
2#锅炉给水泵DG85-80×9 315 286.54 0.89 82 145.74 50.86
回收循环水泵500S59A 330 366.78 0.85 101 225.10 61.37
风机电机测试结果
拖动设备风机型号额定功率功率因数电机负载率电机型号效
率
冷却塔1#风机LF77-6 75kW 0.87 90 Y280S-4 93
冷却塔3#风机LF77-6 75kW 0.87 90 Y280S-4 91
由上表可以看出,配电变压器负载率和配电系统功率因数均低于《评价企业合理用电技术导则》(GB/ T 3485-1998)的规定值85%(三班制生产)和0.90,说明企业用电存在较大的不均衡性。
负载系数不符合《变压器运行监测(试行)》、《电力变压器经济运行》(GB/T 13462-2008)标准的要求。
5、企业节能建议
以上节能潜力分析不难看出,该企业的主要节能潜力在提窑炉系统效率和用电管理方面,具体建议如下。
1、企业应提高配电系统的日负荷率以减少电力损耗,根据“集中和分散补偿相结合,以分散补偿为主”的原则,加强对配电系统负荷侧的无功补偿,降低无功损耗。
对负载系数不合格的两台配电变压器的容量匹配进行核定,如无增加负荷的需求建议更换小容量变压器。
2、干熄焦工艺技术改造,采用干熄焦技术可回收80%左右的炙热焦炭热量。
年可实现节能量40044tce,实现经济效益4755万元。
3、焦炉烟气回收工艺改造,改进生产工艺利用焦炉烟气作为热源进行煤调湿。
年可实现节能量14015tce,实现经济效益1500万元。
4、采用捣固炼焦工艺对焦炉系统改造,可以降低炼焦成本,显著改善焦炭质量、降低焦比。
由以上分析可知,该公司按以上节能措施年可实现理论节能54059tce,年节约资金4325万元,节能效益明显。
参考文献:①《焦化企业的主要节能减排措施》郑文华史正岩《山东冶金》2008 第6期-;
②《降低炼焦工序能耗的实践》全喜红《节能与环保》2010 第10期
③《控制炼焦工序能耗降低生产运行成本》谢东《冶金能源》2007 第5期
④《企业能源审计》安阳国资委李保才2006年10月
注:文章内所有公式及图表请用PDF形式查看。