《精益生产改善案例》PPT课件
合集下载
改善提案(精益)课件
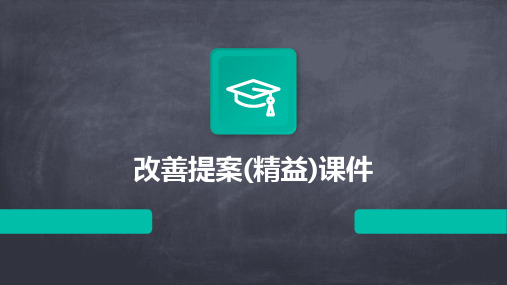
精益生产的优势与局限
适用范围有限
精益生产主要适用于制造业,对 于其他行业可能不太适用。
对员工素质要求高
实施精益生产需要员工具备一定的 技能和素质,否则难以取得预期效 果。
变革阻力
企业内部的变革往往会遇到来自员 工和管理层的阻力,需要有效的沟 通和激励。
企业如何选择合适的精益方法
为了实施精益生产,企业需要对 员工进行相关培训,提高其技能 和意识。
技术更新换代
02
随着技术的不断发展,企业需要不断更新设备和系统以适应新
的发展趋势。
人才短缺
03
具备精益生产和数字化转型能力的人才短缺,企业需要加强人
才培养和引进。
THANKS
感谢观看
实施精益生产不是一蹴而就的过 程,需要持续改进和优化。
评估需求 培训员工
选择合适的方法 持续改进
企业需要明确自身需求,了解精 益生产所能解决的问题和预期目 标。
根据企业实际情况选择适合的精 益方法,如5S、TPM、JIT等。
未来精益发展趋势与挑战
数字化转型
随着信息技术的发展,数字化转型将 成为精益生产的重要趋势。
改善提案(精益)课件
目录
• 精益生产概述 • 精益工具与技术 • 精益实施步骤 • 精益案例分享 • 总结与展望
01
精益生产概述
Chapter
精益生产定义
精益生产是一种以客户需求为导向的生产方式,通过消 除浪费、持续改进和不断创新,实现低成本、高效率和 高质量的生产。 它强调以客户需求来确定生产计划和流程,以减少不必 要的库存和等待时间,提高生产效率和产品质量。
通过持续改进,企业可以不断识别和解决存在的问题,提高工作效率和产品质量。
工厂精益生产改善案PPT(共 33张)
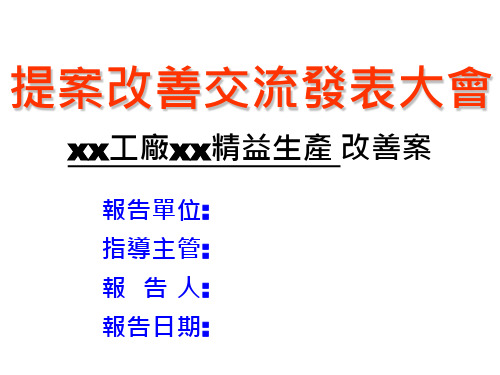
10 5 0
品質不穩定
00:00~ 02:00~ 04:00~ 06:00~ 08:00~ 10:00~ 12:00~ 14:00~ 16:00~ 18:00~ 20:00~ 22:00~
01:00 03:00 05:00 07:00 09:00 11:00 13:00 15:00 17:00 19:00 21:00 23:00
案
傳送帶
安裝節
實施單
層
上標示
拍控制
元生產
節拍線
器
(C1)
(C2)
(C3)
三. 改善歷程(2) --節奏式生產-矩陣分析
構造四個兩兩比較矩陣
A
A/B C1 C2
C3
C1 1 C1/C2 C1/C3 B1 B2
B3
C2 C2/C1 1 C2/C3
…… C3 C3/C1 C3/C2 1
C1 C2 C3
檢嚴重 段
生
工站排 配不合
理
物料搬 運頻繁
前後工站存 在重複動作
產
不
物料設計不 精
合理
益
Machine
Material
三. 改善歷程--改善思路
主要 問題
平衡性浪費
工時浪費
改善 1.消除動作浪費 3.縮短瓶頸時間
內容
2.推行節奏式生產 4.優化排班管理
改善
目的
消除工廠浪費,實現精益生產
三. 改善歷程(1) --改善HI-POT工站-動作分析
三. 改善歷程(1) --改善HI-POT工站-改善實施
合併Hi-Pot & Ast工站
Hi-pot工站 Combine
Ast工站
V=
F C
品質不穩定
00:00~ 02:00~ 04:00~ 06:00~ 08:00~ 10:00~ 12:00~ 14:00~ 16:00~ 18:00~ 20:00~ 22:00~
01:00 03:00 05:00 07:00 09:00 11:00 13:00 15:00 17:00 19:00 21:00 23:00
案
傳送帶
安裝節
實施單
層
上標示
拍控制
元生產
節拍線
器
(C1)
(C2)
(C3)
三. 改善歷程(2) --節奏式生產-矩陣分析
構造四個兩兩比較矩陣
A
A/B C1 C2
C3
C1 1 C1/C2 C1/C3 B1 B2
B3
C2 C2/C1 1 C2/C3
…… C3 C3/C1 C3/C2 1
C1 C2 C3
檢嚴重 段
生
工站排 配不合
理
物料搬 運頻繁
前後工站存 在重複動作
產
不
物料設計不 精
合理
益
Machine
Material
三. 改善歷程--改善思路
主要 問題
平衡性浪費
工時浪費
改善 1.消除動作浪費 3.縮短瓶頸時間
內容
2.推行節奏式生產 4.優化排班管理
改善
目的
消除工廠浪費,實現精益生產
三. 改善歷程(1) --改善HI-POT工站-動作分析
三. 改善歷程(1) --改善HI-POT工站-改善實施
合併Hi-Pot & Ast工站
Hi-pot工站 Combine
Ast工站
V=
F C
精益生产现场管理和改善ppt课件
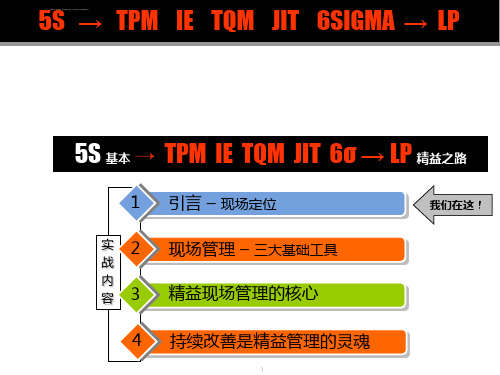
目视工作现场的建立
讨论 目视化工作现场的建立
现在有哪些目视管理
识别哪些地方需要建立目视管理
讨论确定如何和怎样去建立目视管理
实施和跟踪
5S 基本 → TPM IE TQM JIT 6σ → LP 精益之路
实 战 内 容
看板是如何提升管理的精度?
1
看板有哪些,如何确定?
2
围绕看板,构建目标管理运作平台
3
管理看板是发现问题、解决问题的非常有效且直观的手段
确定谁将要做什么 使之目视控制 在适当的位置进行目视控制
目视化工作现场的建立
制订目视化控制计划
协调和标准化目视控制
创建和实施目视控制
检验和修正目视控制
建立目视化控制持续改进计划
在流程中自己进行检查控制 邀请另外一个团队审计目视控制 邀请参与各方审计控制设备 按要求休整目视控制设备
目视化工作现场的建立
人
机
料
法
环
目视管理常用工具及制作要领 (二)、目视管理工具的基本要素
1、提高工作环境的改善 2、提高安全管理的措施 3、提高品质管理的水准 4、提高设备TPM的水准 5、提高现物管理精度
通过彻底5S的实施 安全、舒适的工作环境,人人都按标准办 大家都来做改善
目视管理5项直接效果及其常见措施
制订目视化控制计划
协调和标准化目视控制
创建和实施目视控制
检验和修正目视控制
建立目视化控制持续改进计划
确定后续活动 确定谁在什么时候将要做什么 决定谁将得到信息及如何的到 实施改进计划
目视工作现场的建立
必须取得高层领导的支持
要从流程和人/机/料/法/环方面综合考虑
要坚持用同一个标准
讨论 目视化工作现场的建立
现在有哪些目视管理
识别哪些地方需要建立目视管理
讨论确定如何和怎样去建立目视管理
实施和跟踪
5S 基本 → TPM IE TQM JIT 6σ → LP 精益之路
实 战 内 容
看板是如何提升管理的精度?
1
看板有哪些,如何确定?
2
围绕看板,构建目标管理运作平台
3
管理看板是发现问题、解决问题的非常有效且直观的手段
确定谁将要做什么 使之目视控制 在适当的位置进行目视控制
目视化工作现场的建立
制订目视化控制计划
协调和标准化目视控制
创建和实施目视控制
检验和修正目视控制
建立目视化控制持续改进计划
在流程中自己进行检查控制 邀请另外一个团队审计目视控制 邀请参与各方审计控制设备 按要求休整目视控制设备
目视化工作现场的建立
人
机
料
法
环
目视管理常用工具及制作要领 (二)、目视管理工具的基本要素
1、提高工作环境的改善 2、提高安全管理的措施 3、提高品质管理的水准 4、提高设备TPM的水准 5、提高现物管理精度
通过彻底5S的实施 安全、舒适的工作环境,人人都按标准办 大家都来做改善
目视管理5项直接效果及其常见措施
制订目视化控制计划
协调和标准化目视控制
创建和实施目视控制
检验和修正目视控制
建立目视化控制持续改进计划
确定后续活动 确定谁在什么时候将要做什么 决定谁将得到信息及如何的到 实施改进计划
目视工作现场的建立
必须取得高层领导的支持
要从流程和人/机/料/法/环方面综合考虑
要坚持用同一个标准
精益生产.改善方案活动的开展ppt课件

改善KAIZEN
New Challenge
5
在做改善中不应该讲的话
1. “我都不行,你能行?真是笑话!”__耻笑的话 2. “我不知道”(是自己的工作职责)__没有责任心的话 3. “那肯定是不行的”(当众讲)__否定性的话 4. “他懂什么”__蔑视的话 5. “我忙,没有时间”__推托/找借口的话 6. “好好的换什么”__无赖安逸主义的话 7. “这程序就可以”__推迟的话 8. ……
体系人员:1.品质体系的维护 2.优化公司的工作流程与程序文件 3.所有品质活动参与和支持 4.所有改善活动的监控与督促 5.依体系要求为改善团队提供建议与方向
改善KAIZEN
New Challenge
11
三、改善前的准备 成立改善小组(改善前2周)
改善KAIZEN
品管
1.组织团队成员制 订内部检查计划 2.推动和监控所有 成员的活动是否按 计划进行 3.定期召开品质会 议或改善会议汇报 前阶段的成绩与总 结不足,以及下阶 段的重点与方向 4.组织确认和验证 改善的实效性 5.反馈问题给高层 获取资源与支持
组长
SMG 徐(S敏upor党)
凯 史向阳
王二 品管
张三 生产
李四 赵五
生产 工程
体系
品管
工程
生产
物控
马六 体系
New Challenge
10
三、改善前的准备
成立改善小组(改善前2周)
职责与权限:
总经理:为改善团队提供所需的资源; 执行副总:为改善团队提供支持,帮助与协调; 客户:为改善团队提供建议与要求
• 我用第六感觉也知道工厂内什么地方有什么 • 不良是与我无关的事,只要认真做我自己的事就行 • 我们一直都这样做,既简便又快捷,没什么可改的 • 因物料不足,设备或生产工具坏掉,交期赶不上也是没办法的事 • 做事的人受伤是常事,上一次药就好了 • 工厂虽不干净整洁,但我们的产品很畅销呀 • 搞什么5S呀,改善呀,净整些华面不实,没用的东西 • 公司虽然问题比较多,但我们客户几乎都没投诉,品质好才是关键 • ……
精益改善项目案例生产效率提升PPT课件(42页)(2024版)

项目范围: 项目通过推进精益生产,减少生产制造全流程内的浪费,有效减少作业人员、提升产量,缩短交付周期,在降低制造成本的同时,快速满足客户的需求。以工厂为试点,三地工厂同步实施,在制冷集团各事业部推广。
变量
名称
CTQ
单位
Y
生产效率提升
月人均产出
套/人
Y1
生产组织模式变革
订单交付周期
天
Y2
制造技术提升
大线组长 柔性线组长 柔性线巡检
减少1人 两两合并 两两合并
15
Y2改善(节选)—管理优化减员
改善效果:计划减员101人,实际减员101人,计划达成率100%。
部门(分厂)
总一
总二
总三
部装
注塑
财务
品质
职能部
目标(人)
7
2
6
3
31
14
18
20
推进 方向
Y1的改善 摘录1
改善项目名称:订单下达规范性
改善类别
技术
管理
设备
材料
费用
其它
√
改善前
改善后
问题点
改善方案
1、针对计划下达准确率、计划完成及时性的责任划分不明晰,产销责权关系不清,存在管理真空; 2、相关流程时间节点不规范、不合理,且操作随意性较强; 3、产销信息传递不畅。经常出现生产计划与销售计划间的信息不对称;
1、以文件形式彻底固化尾数清理流程、明确激励考核要求; 2、计划管理建立专人监控机制,按周、月通报 3、物资管理监督车间生产过程物料损耗,并每日统计滚动输出; 4、供应商建立安全库存,保证欠产物料补缺的及时性,减少超期作业任务产生; 5、车间物料管护规范每周稽查不少于2次。
精益生产成本改善实例 ppt课件

烫金 喷胶
抛光 喷漆
价值流
传统思维中,我们总是从工厂内部来考虑,从原 材料开始一直追踪到产品的完成来检查价值流。
过程
冲压
价值 流
过程
焊接
过程
总装单元
原材料
成品
也可以用价值流的方法来绘制业务过程。
价值流
价值流绘制 (VSM) 是一个手工方法通过用特定的图标绘画 来表现整个价值流的过程,包括物流,信息流和过程流。
▶不是说必须要反复五次以上 ,而是说 ▶反复到找出问题的根本原因为止
浪费的发现
七大浪费之改善流程
计划(P)
实施(D) 确认(C) 处理(A)
1:主题选定 2:目标设定 3:活动计划拟定 4:现状把握 5:要因分析 6:对策拟定 7:对策实施及检讨
8:效果确认 9:标准化
10:检讨及今后计划
解决问题的步骤
Inv.Time ? days
Pro.cTime
? days
3 Shifts TAKT Time CT = C/O Time = DT = Scrap / Rework= Small Lot WIP =
3 Shifts TAKT Time CT = C/O Time = DT = Scrap / Rework = # Operators WIP =
波峰焊
检验
灌胶 QA 包装 运输
重工
什么是价值
插装 搬运 波峰焊
检验
灌胶 QA 包装
重工
增值 流动
工作过程
必要的 减少
非增值 非必要的 消除
动动脑~搭乘云霄飞车
排隊
爬升
俯衝
对客户而言,哪些是具有附加价值!
要让客戶满意,如何转换上述活动?
精益生产现场改善PPT课件

物料
工具
第10页/共15页
物流距离
物流布局应以总物流负载 最小为最佳方案(总物 流负载=距离*对应的物 流量的总和)。
十二 设备优化与摆放
1>按工序布置 2>“U”形、逆时针布置 3>设备布置“三不”原则(不落地生根,不寄人篱下, 不离群索居) 4>设备间距小 5>设备功能够用就好(不追求大而全)
第11页/共15页
十三 产线布局优化
第12页/共15页
传统流水线
适合大订单,大 批量生产。
单元生产线
适合大小订单, 小批量生产。
精简CELL线 适合少量多样,
柔性生产。
十四 现场员工关系管理的秘诀
和谐的员工关系
• 员工工作责任心强 • 工作积极性高 • 企业生产效率高 • 员工稳定,流失率低 • 管理层和员工有效沟通
提高流程的效率,改善平面布置图 去掉时间浪费,缩短生产周期
第9页/共15页
加工 搬运 检查
停滞
十一 物流距离的优化原则
传统物流
供货商
大仓库
IQC
线边仓
生产线
物料员
成品仓
客户
精益物流 供货商
供货商端驻点IQC
生产线
成品仓
客户
三角形原理
物料或工具的放置点、产 品组装点、操作者的 位置形成的三角形的 边长越小越好。
简化(Simplify):经过取消、合并、重组之后,再对该项工作作进一步更深
入的分析研究,使现行方法尽量地简化,以最大限度地缩短作业时间,提高工作效率。
第6页/共15页
八 动作经济的16原则
1
关于人体动作方面: 1 双手并用原则 2 对称反向原则 3 排除合并原则 4 降低动作等级原则 5 减少动作限制原则 6 避免动作突变原则 7 保持轻松节奏原则 8 利用惯性原则 9 手脚并用原则
精益生产现场管理和改善ppt课件
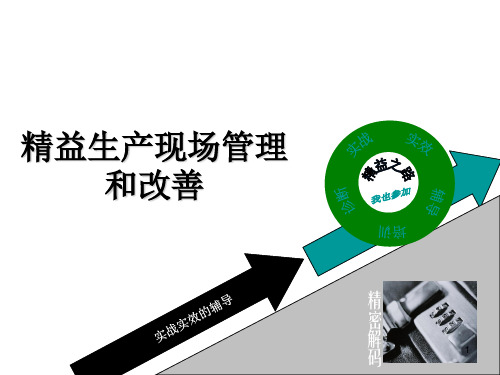
34
目视工作现场的建立
在实施前得到相关方面的认同 要坚持用同一个标准 要从流程和人/机/料/法/环方面综合考虑 必须取得高层领导的支持
35
目视工作现场的建立
讨论 目视化工作现场的建立
实施和跟踪 讨论确定如何和怎样去建立目视管理 识别哪些地方需要建立目视管理 现在有哪些目视管理
36
5S 基本 → TPM IE TQM JIT 6σ → LP 精益之路
透明化、显现化、立即化
作业标准化
基准化 管理基础
透明化 降低难度
管理看板
看板化 增加精度
13
什么叫目视管理
工作区域不解自明 自动调节/自我改进 使问题无处可藏
3
标准化
原 视觉化 则 透明化
14
目视管理的理念
• 哲学——促进[走动管理]的效果 • 目的——塑造[一目了然]的工作场所
企业信息中心
Business Objectives
1. 在流程中自己进行检查控制 2. 邀请另外一个团队审计目视控制 3. 邀请参与各方审计控制设备 4. 按要求休整目视控制设备
33
目视化工作现场的建立
建立目视化控制持续改进计划 检验和修正目视控制 创建和实施目视控制 协调和标准化目视控制 制订目视化控制计划
1. 确定后续活动 2. 确定谁在什么时候将要做什么 3. 决定谁将得到信息及如何的到 4. 实施改进计划
•对企业的影响
– 减少(时间和精力上的)浪费,提高劳动生产率 – 营造“以人为本”的工作环境,提高可靠性和稳定性 – 突出工作场所危险,提高安全性和减少停机时间 – 为业绩改善政策和做法提供支持(如:标准作业、6S、
快速换线、预防性维护)
•对员工的影响
精益生产案例分享ppt课件
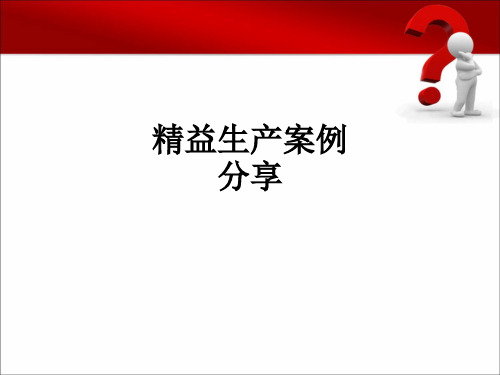
Effort which adds no
value
to a product or service 对最终产品或服务 不增加价值的 过程
Waste of Inventory 库存浪费
Any supply
in excess of process requirements necessary to produce goods 任何超过加工必须的 物料供应
Inventory Covers All Problem 库存掩盖所有问题
库存水平
维修问题
效率问题
质量问题
交货问题
Low Down Inventory To Expose Problem 通过降库存暴露问题
库存水平
维修问题
效率问题
质量问题
交货问题
Waste of Waiting 等待
Idle Time That Is Produced When Two Dependent Variables Are Not Fully Synchronized
改进后
1.改进后2人,充分发挥个人效益 2.改进后实现单件流 3.交付周期缩短50% 4.采取防错,当场发现 5.员工收入5800-6200
生产效率的提升大家自己算
12
JIT与TPS
Just In Time
适品 · 适量 · 适时
JIT的基本思想是:只在需要的时候、按需要 的量、 生产所需的产品,故又被称为准时制生产、适时生产方式、 看板生产方式。 JIT的核心是:零库存和快速应对市场变化。 JIT的概念最早由日本丰田汽车提出,在大野耐一带领 下创造出一套具竞争优势的运作方式,人们习惯称之为JIT 模式,又称丰田生产方式(TPS)。
等待浪费
value
to a product or service 对最终产品或服务 不增加价值的 过程
Waste of Inventory 库存浪费
Any supply
in excess of process requirements necessary to produce goods 任何超过加工必须的 物料供应
Inventory Covers All Problem 库存掩盖所有问题
库存水平
维修问题
效率问题
质量问题
交货问题
Low Down Inventory To Expose Problem 通过降库存暴露问题
库存水平
维修问题
效率问题
质量问题
交货问题
Waste of Waiting 等待
Idle Time That Is Produced When Two Dependent Variables Are Not Fully Synchronized
改进后
1.改进后2人,充分发挥个人效益 2.改进后实现单件流 3.交付周期缩短50% 4.采取防错,当场发现 5.员工收入5800-6200
生产效率的提升大家自己算
12
JIT与TPS
Just In Time
适品 · 适量 · 适时
JIT的基本思想是:只在需要的时候、按需要 的量、 生产所需的产品,故又被称为准时制生产、适时生产方式、 看板生产方式。 JIT的核心是:零库存和快速应对市场变化。 JIT的概念最早由日本丰田汽车提出,在大野耐一带领 下创造出一套具竞争优势的运作方式,人们习惯称之为JIT 模式,又称丰田生产方式(TPS)。
等待浪费
《精益生产完整》课件

日本电气公司
日本电气公司通过采用精益生产方法,成功减少了生产中的浪费和成本。
总结
精益生产是一种通过持续改进和消除浪费来提高效率和质量的生产管理方法。
通过建立精益文化、具体实践和借鉴成功案例,可以推动精益生产实施并提 升管理能力。
通过保持工作区域整洁、建立标准化工作流程和培养良好的工作习惯,可以 提高生产效能。
TPM维护 (Total Productive Maintenance)
TPM维护是一种通过持续和预防性的设备维护来保持设备正常运行的方法。 通过优化设备维护计划和提供员工培训,可以减少停机时间和提高设备的可靠性。
SMED单点换模
精益生产的优势
1 提高效率
通过优化流程和消除不必要的步骤,可以大幅提高生产ቤተ መጻሕፍቲ ባይዱ率。
2 降低成本
通过消除浪费,精益生产可以降低成本并提高利润。
3 提高品质
通过持续改进和关注细节,精益生产可以提高产品和服务的质量。
精益生产的历史
1
起源
精益生产起源于日本的丰田生产方式,旨在提高生产效率。
2
应用
随着时间的推移,精益生产的理念得到了广泛应用,跨越了不同行业和国家。
每个单元都专注于特定的任务,并与其他单元协同工作,以确保整个过程的 流畅性。
一次性流程设计
一次性流程设计旨在减少或消除生产过程中的非价值创造步骤,从而提高效 率和质量。
通过优化和简化流程,可以减少时间浪费、材料浪费和人力浪费,从而提高 生产效能。
产出平衡
产出平衡是指在不同工序之间达到良好的平衡,以确保不会出现过剩或短缺的情况。 通过平衡产出,可以最大限度地提高生产效率,并减少资源的浪费。
3
发展
精益生产不断演进和改进,适应了现代企业的需求和挑战。
日本电气公司通过采用精益生产方法,成功减少了生产中的浪费和成本。
总结
精益生产是一种通过持续改进和消除浪费来提高效率和质量的生产管理方法。
通过建立精益文化、具体实践和借鉴成功案例,可以推动精益生产实施并提 升管理能力。
通过保持工作区域整洁、建立标准化工作流程和培养良好的工作习惯,可以 提高生产效能。
TPM维护 (Total Productive Maintenance)
TPM维护是一种通过持续和预防性的设备维护来保持设备正常运行的方法。 通过优化设备维护计划和提供员工培训,可以减少停机时间和提高设备的可靠性。
SMED单点换模
精益生产的优势
1 提高效率
通过优化流程和消除不必要的步骤,可以大幅提高生产ቤተ መጻሕፍቲ ባይዱ率。
2 降低成本
通过消除浪费,精益生产可以降低成本并提高利润。
3 提高品质
通过持续改进和关注细节,精益生产可以提高产品和服务的质量。
精益生产的历史
1
起源
精益生产起源于日本的丰田生产方式,旨在提高生产效率。
2
应用
随着时间的推移,精益生产的理念得到了广泛应用,跨越了不同行业和国家。
每个单元都专注于特定的任务,并与其他单元协同工作,以确保整个过程的 流畅性。
一次性流程设计
一次性流程设计旨在减少或消除生产过程中的非价值创造步骤,从而提高效 率和质量。
通过优化和简化流程,可以减少时间浪费、材料浪费和人力浪费,从而提高 生产效能。
产出平衡
产出平衡是指在不同工序之间达到良好的平衡,以确保不会出现过剩或短缺的情况。 通过平衡产出,可以最大限度地提高生产效率,并减少资源的浪费。
3
发展
精益生产不断演进和改进,适应了现代企业的需求和挑战。
精益生产系列现场管理和改善PPT
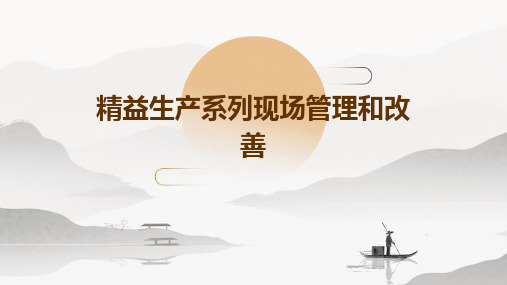
制定物品定置管理的标准操作流程,确保员 工能够按照标准执行。
目视化管理
01
视觉识别
利用颜色、图形、文字等视觉元素, 使信息传递更加直观。
异常预警
通过红、黄、绿等颜色标识,及时 发现异常情况并进行处理。
03
02
标准化操作流程
通过可视化的方式展示操作步骤和 要点,提高工作效率。
目视化沟通
促进员工之间的信息交流和协作, 提高整体工作效率。
生产布局优化
• 总结词:通过合理规划生产布局,降低物料搬运成本和时间。
• 详细描述:生产布局是指生产设备和人员在工作场所的布局方式。合理的生产布局可以降低物料搬运成本和时间,提高 生产效率。在传统生产模式下,设备和人员布局可能存在不合理之处,导致物料搬运距离过长、时间浪费等问题。通过 优化生产布局,企业可以将设备和人员集中在一起,减少物料搬运距离和时间。这不仅可以降低生产成本,还可以提高 产品质量和客户满意度。为了实现生产布局优化,企业需要对工作场所进行重新规划和设计,并加强员工培训和标准化 操作。
跨部门协作与沟通
加强部门间的沟通和协作, 共同推进持续改进工作。
培训与知识分享
开展相关培训和知识分享 活动,提高员工的质量意 识和持续改进能力。
05
员工参与与多技能培养
员工建议系统
鼓励员工提出改进意见
建立一个平台或渠道,让员工可以随时提出对生产流程、设备、 工作环境等方面的改进意见。
定期评审与实施
持续学习与发展
鼓励员工持续学习和提升,提供进一步培训和认证的机会,促进 个人职业发展。
员工激励措施
薪酬激励
提供具有竞争力的薪酬待遇,激励员工努力工作。
晋升机会
为员工提供明确的晋升通道和机会,激发员工的 积极性和工作动力。
目视化管理
01
视觉识别
利用颜色、图形、文字等视觉元素, 使信息传递更加直观。
异常预警
通过红、黄、绿等颜色标识,及时 发现异常情况并进行处理。
03
02
标准化操作流程
通过可视化的方式展示操作步骤和 要点,提高工作效率。
目视化沟通
促进员工之间的信息交流和协作, 提高整体工作效率。
生产布局优化
• 总结词:通过合理规划生产布局,降低物料搬运成本和时间。
• 详细描述:生产布局是指生产设备和人员在工作场所的布局方式。合理的生产布局可以降低物料搬运成本和时间,提高 生产效率。在传统生产模式下,设备和人员布局可能存在不合理之处,导致物料搬运距离过长、时间浪费等问题。通过 优化生产布局,企业可以将设备和人员集中在一起,减少物料搬运距离和时间。这不仅可以降低生产成本,还可以提高 产品质量和客户满意度。为了实现生产布局优化,企业需要对工作场所进行重新规划和设计,并加强员工培训和标准化 操作。
跨部门协作与沟通
加强部门间的沟通和协作, 共同推进持续改进工作。
培训与知识分享
开展相关培训和知识分享 活动,提高员工的质量意 识和持续改进能力。
05
员工参与与多技能培养
员工建议系统
鼓励员工提出改进意见
建立一个平台或渠道,让员工可以随时提出对生产流程、设备、 工作环境等方面的改进意见。
定期评审与实施
持续学习与发展
鼓励员工持续学习和提升,提供进一步培训和认证的机会,促进 个人职业发展。
员工激励措施
薪酬激励
提供具有竞争力的薪酬待遇,激励员工努力工作。
晋升机会
为员工提供明确的晋升通道和机会,激发员工的 积极性和工作动力。
《精益生产完整》课件

人工智能可以通过机器学习和深度学习等技术,对大量数据进行处理和 分析,预测未来的市场需求和生产趋势,为生产计划和决策提供依据。
人工智能还可以通过智能控制和优化算法等技术,对生产过程进行实时 监控和调整,提高生产过程的稳定性和效率。
绿色精益生产
绿色精益生产是指将环保理念融入生产 过程中,通过改进和优化生产过程,减 少对环境的负面影响。
精益生产的重要性
01
提高生产效率和产 品质量
通过消除浪费和优化流程,精益 生产能够显著提高生产效率和产 品质量。
降低成本
02
03
增强企业竞争力
通过减少浪费和优化库存,精益 生产能够降低生产成本和运营成 本。
精益生产能够帮助企业提高效率 和效益,从而在激烈的市场竞争 中获得竞争优势。
精益生产的历史与发展
总结词:精细管理
详细描述:某物流企业通过精益化运营实践,实现了对运输、仓储和配送等环节的精细化管理。通过 消除浪费、提高运输效率、优化仓储布局和配送路线,该企业成功降低了运营成本,提高了客户满意 度。同时,精益化运营还促进了企业内部的沟通与协作,增强了团队凝聚力。
THANK YOU
01
人才缺乏
中国在精益生产方面的专业人才相对较 少,这可能会影响精益生产的推广和应 用。
02
03
制度环境
中国的制度环境可能对精益生产的推 广和应用产生影响,例如法律法规、 政策等。
05
精益生产的未来发展
数字化精益生产
01
数字化精益生产是指利用数字化技术对生产过程进行优化和改进,以提高生产 效率和产品质量。
素养
培养员工遵守规章制度、注重 细节、积极主动的良好习惯, 提高整体素质。
快速换模
人工智能还可以通过智能控制和优化算法等技术,对生产过程进行实时 监控和调整,提高生产过程的稳定性和效率。
绿色精益生产
绿色精益生产是指将环保理念融入生产 过程中,通过改进和优化生产过程,减 少对环境的负面影响。
精益生产的重要性
01
提高生产效率和产 品质量
通过消除浪费和优化流程,精益 生产能够显著提高生产效率和产 品质量。
降低成本
02
03
增强企业竞争力
通过减少浪费和优化库存,精益 生产能够降低生产成本和运营成 本。
精益生产能够帮助企业提高效率 和效益,从而在激烈的市场竞争 中获得竞争优势。
精益生产的历史与发展
总结词:精细管理
详细描述:某物流企业通过精益化运营实践,实现了对运输、仓储和配送等环节的精细化管理。通过 消除浪费、提高运输效率、优化仓储布局和配送路线,该企业成功降低了运营成本,提高了客户满意 度。同时,精益化运营还促进了企业内部的沟通与协作,增强了团队凝聚力。
THANK YOU
01
人才缺乏
中国在精益生产方面的专业人才相对较 少,这可能会影响精益生产的推广和应 用。
02
03
制度环境
中国的制度环境可能对精益生产的推 广和应用产生影响,例如法律法规、 政策等。
05
精益生产的未来发展
数字化精益生产
01
数字化精益生产是指利用数字化技术对生产过程进行优化和改进,以提高生产 效率和产品质量。
素养
培养员工遵守规章制度、注重 细节、积极主动的良好习惯, 提高整体素质。
快速换模