FMEA介绍失效模式与影响分析
FMEA(失效模式与影响分析)简介

没有影响;事件发生的频率要记录特定的失效原因和机理多长时间发生一次以及发生的几率。
如果为10,则表示几乎肯定要发生,工艺能力为0.33或者ppm大于10000。
5.2检测等级是评估所提出的工艺控制检测失效模式的几率,列为10表示不能检测,1表示已经通过目前工艺控制的缺陷检测。
5.3计算风险优先数RPN(riskprioritynumber)。
RPN是事件发生的频率、严重程度和检测等级三者乘积,用来衡量可能的工艺缺陷,以便采取可能的预防措施减少关键的工艺变化,使工艺更加可靠。
对于工艺的矫正首先应集中在那些最受关注和风险程度最高的环节。
RPN最坏的情况是1000,最好的情况是1,确定从何处着手的最好方式是利用RPN的pareto图,筛选那些累积等级远低于80%的项目。
推荐出负责的方案以及完成日期,这些推荐方案的最终目的是降低一个或多个等级。
对一些严重问题要时常考虑拯救方案,如:一个产品的失效模式影响具有风险等级9或10;一个产品失效模式/原因事件发生以及严重程度很高;一个产品具有很高的RPN值等等。
在所有的拯救措施确和实施后,允许有一个稳定时期,然后还应该对修订的事件发生的频率、严重程度和检测等级进行重新考虑和排序。
在设计和制造产品时,通常有三道控制缺陷的防线:避免或消除故障起因、预先确定或检测故障、减少故障的影响和后果。
FMEA正是帮助我们从第一道防线就将缺陷消灭在摇篮之中的有效工具。
FMEA是一种可靠性设计的重要方法。
它实际上是FMA(故障模式分析)和FEA(故障影响分析)的组合。
它对各种可能的风险进行评价、分析,以便在现有技术的基础上消除这些风险或将这些风险减小到可接受的水平。
及时性是成功实施FMEA的最重要因素之一,它是一个"事前的行为',而不是"事后的行为'。
为达到最佳效益,FMEA必须在故障模式被纳入产品之前进行。
FMEA实际是一组系列化的活动,其过程包括:找出产品/过程中潜在的故障模式;根据相应的评价体系对找出的潜在故障模式进行风险量化评估;列出故障起因/机理,寻找预防或改进措施。
潜在失效模式和后果分析FMEA
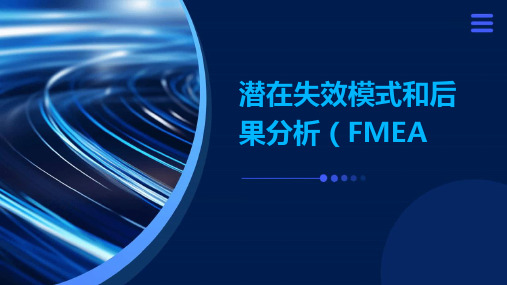
制定优先改进措施
01
根据RPN值评估结果,确定需要优先改进的潜在失效模式。
02
制定针对性的改进措施,包括设计优化、工艺改进、检验加强
等。
制定改进措施的实施计划和时间表,确保改进措施的有效执行
03 。
跟踪改进措施的实施情况
要点二
详细描述
在汽车行业中,FMEA被广泛应用于产品设计、生产和质 量控制过程中。例如,在发动机设计阶段,FMEA分析可 能识别出发动机气缸密封圈的潜在失效模式,如密封圈材 料疲劳或安装不当。这种失效可能导致发动机性能下降或 漏油,影响车辆的安全性和可靠性。通过FMEA分析,设 计团队可以采取措施优化密封圈材料和安装工艺,降低失 效风险。
服务流程改进
在服务流程中应用FMEA,有助于发 现和改进可能导致服务失败的潜在问
题。
生产过程控制
在生产过程中应用FMEA,有助于识 别和解决可能导致生产不合格品的潜 在问题。
维修和维护
在产品维修和维护过程中应用FMEA ,有助于预防和解决可能导致产品失 效的潜在问题。
02
CATALOGUE
FMEA分析过程
详细描述
潜在失效模式是指产品或过程中可能发生的故障或性能下降。通过分析历史数据、类似产品的失效模式以及专家 意见等途径,可以识别出潜在的失效模式。
确定失效影响
总结词
评估潜在失效模式对系统、产品或过程 的影响,有助于了解失效的严重程度。
VS
详细描述
失效影响是指潜在失效模式发生时,对系 统、产品或过程性能的影响程度。通过评 估失效影响,可以了解失效的严重程度, 为后续的风险评估提供依据。
FMEA失效模式与影响分析培训课程大纲

常用FMEA工具概述
FMEA表格
用于记录失效模式、影响、原因、控制措施等信息,是FMEA分 析的基础工具。
故障树分析(FTA)
通过图形化方式展示系统失效的逻辑关系,帮助识别潜在失效模式 。
因果图(鱼骨图)
用于分析失效原因,从人、机、料、法来自环等方面进行深入挖掘。软件辅助进行FMEA分析优势
高效性
通过减少产品失效,可以降低维修和 保修成本,提高客户满意度。
培训课程目标与内容
• 课程目标:使学员掌握FMEA的基本原理和方法,能够独立完 成FMEA分析,并具备在团队中推广和应用FMEA的能力。
培训课程目标与内容
课程内容 FMEA基本概念和原理
失效模式识别与评估
培训课程目标与内容
影响分析与风险控制
案例二
某石油化工企业对炼油装置进行FMEA分析,识别潜在的设备故障和操作风险,制定相应 的预防措施和应急预案,确保了生产过程的安全稳定运行。
案例三
某电力公司对变电站设备进行FMEA分析,通过识别潜在的电气故障和机械故障模式,优 化设备维护和检修计划,提高了电网运行的稳定性和可靠性。
04
FMEA工具与软件介绍
软件可快速处理大量数 据,提高分析效率。
准确性
软件内置算法可准确计 算风险优先数(RPN)
,避免人为误差。
可视化
软件提供图形化界面, 方便用户直观理解分析
结果。
可追溯性
软件可记录分析过程和 数据,方便后续审查和
改进。
工具软件操作演示
FMEA软件界面介绍
展示软件界面,介绍各功能模块。
数据输入与编辑
演示如何在软件中输入和编辑FMEA 相关数据。
案例分析
FMEA失效模式及后果分析PPT课件
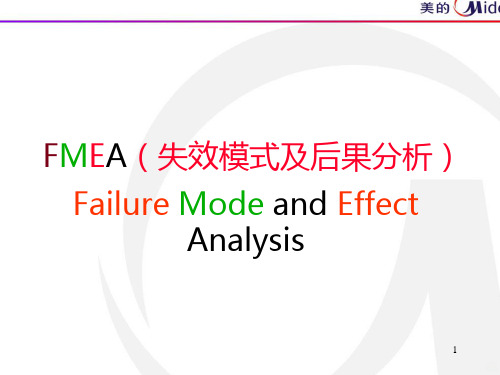
弯曲 断裂 脏污 短路 表面粗糙
毛刺 转运损坏 变形 开路 开孔太深
孔错位 漏开孔 表面太光滑
失效模式应以规范化技术术语描述, 不同于顾客察觉的现象
32
潜在失效的后果
对最终 使用者
噪音 粗糙 费力 工作不正常 异味
渗漏 不能工作 报废 外观不良
对下道 工序
无法紧固 不能配合 不能连接 无法安装 损坏设备 危害操作者
•1960’s-70’s第一次被注意和使用在工程可 靠性 •多方小组准备对产品/过程潜在失效模式和产 品性能影响的文件化体系 •评定产品或过程潜在失效模式的文件,采取 相应措施来消除或降低潜在失效的影响
7
典型的FMEAs
系统
设计
过程
部件 子系统 主系统
部件 子系统 主系统
注意:将系统的 失效模式降为最小
-后果到底有多糟? •O=Likelihood of Occurrence 频 度
-经常发生吗? •D=Likelihood of Detection 探测 度
18
RPN 流程
来自经验和数据
来自预测
DFMEA
项目/功能
潜在 失效模式
潜在 失效后果
严 重级 度别
潜在失效 的起因/机理
频 度
现行 设计控制
10
FMEA 小组
小组 • 为完成同一任务或目标的两个或更多的共同
行动的个体 集体讨论 • 发现许多可能存在和可能发生情况需要小组
的集体讨论
11
成功的FMEA 小组
•控制方向和焦点 •建立自身的统一性 •负责并使用测量方 法 •有全体的支持 •是横向多功能小组
12
FMEA 小组的守则
• 决定前召开小组会议 • 决定谁将参加 • 预先准备议题 • 主张进行会议笔记或记录 • 建立基本准则 • 遵守事先的议程 • 评价会议 • 不允许中断
过程失效模式及影响分析(过程FMEA)
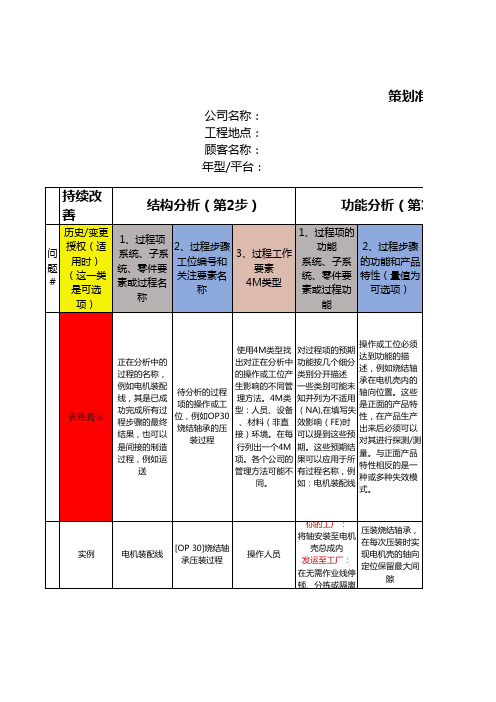
探测度 (D)
AP
特 殊 特 性
筛选器 代码 (选 填)
预防 控制
负
探测 措施
责 人 姓
目标 完成 时间
名
初始状态-过去经过验证 的控制和/或将要采用的
控制
1-10
H、M、L 、NA
CC
LL
为降低频 度所需的 附加措施
为改善 探测所 需的附 加措施
姓名
根据规范MRKL5039对
电机性能曲线进行100%
更多。量值/规格为 、过程项、最终用户)
可选,请查看过程文 建议在三个考虑方面旁
档。例如:压力、机 列出严重度评级,并使
器温度、冲洗液浓度 用最高的严重度评级。
、速度等。在过程进 例如,最终用的某个方面
行中可对过程特性进 可能并不总是获得最高
行测量。
的严重度评级。
1-10
失效模式 在“过程工作要
在产品 素的功能和过程
公司名称: 工程地点: 顾客名称: 年型/平台:
策划准备(第一步)
持续改 善
结构分析(第2步)
功能分析(第3步)
历史/变更
问 题 #
授权(适 用时) (这一类 是可选
项)
1、过程项 系统、子系 统、零件要 素或过程名
称
2、过程步骤 工位编号和 关注要素名
称
3、过程工作 要素
4M类型
1、过程项的 功能
跨职能团队:
分析(第3步)
失效分析(第4步)
失效影响的严重度 (S)
3、过程工作要 1、对于上一高层级
素的功能和过程 要素或最终用户的
特性
失效影响(FE)
2、关注 要素的 失效模
式 (FM)
FMEA失效分析与失效模式分析全

擦伤或损坏)。 由于横向性能差而在锻件中出现分离线的失效现象。
11
在服役条件下由于质量恶化而产生失效的原因包括
过载或未预见的加载条件。 磨损(磨蚀、因过度磨损而咬住、粘住、擦伤、气蚀)。 腐蚀(包括化学接触、应力腐蚀、腐蚀疲劳、脱锌、铸铁石
找出被分析对象的“单点故障”。所谓单点故障是指这种故障单独发 生时,就会导致不可接受的或严重的影响后果。一般说来,如果单点 故障出现概率不是极低的话,则应在设计、工艺、管理等方面采取切 实有效的措施。产品发生单点故障的方式就是产品的单点故障模式。
为制定关键项目清单或关键项目可靠性控制计划提供依据。 为可靠性建模、设计、评定提供信息。 揭示安全性薄弱环节,为安全性设计(特别是载人飞船的应急措施、
16
什么是失效分析?
失效分析:考察失效的构件及失效的情景(模式), 以确定失效的原因。
失效分析的目的:在于明确失效的机理与原因。改 进设计、改进工艺过程、正确地使用维护。
失效分析的主要内容:包括明确分析对象,确定失 效模式,研究失效机理,判定失效原因,提出预防 措施(包括设计改进)。
17
失效分析的要点?
失效模式的判断分为定性和定量分析两个方面。在一般 情况下,对一级失效模式的判断采用定性分析即可。而 对二级甚至三级失效模式的判断,就要采用定性和定量、 宏观和微观相结合的方法。
19
一级失效模式的分类
20 主要失效模式的分类与分级
21
如某型涡轮叶片在第一榫齿处发生断裂,通过断口 的宏观特征可确定一级失效模式为疲劳失效。然后 通过对断口源区和扩展区特征分析和对比,并结合 有限元应力分析等,可作出该叶片的断裂模式为起 始应力较大的高周疲劳断裂的判断,即相当于作出 了三级失效模式的判断。
失效模式与影响分析

失效模式与影响分析失效模式与影响分析(英文:Failure mode and effects analysis,FMEA),又称为失效模式与后果分析、失效模式与效应分析、故障模式与后果分析或故障模式与效应分析等,是一种操作规程,旨在对系统范围内潜在的失效模式加以分析,以便按照严重程度加以分类,或者确定失效对于该系统的影响。
FMEA广泛应用于制造行业产品生命周期的各个阶段;而且,FMEA在服务行业的应用也在日益增多。
失效原因是指加工处理、设计过程中或项目/物品(英文:item)本身存在的任何错误或缺陷,尤其是那些将会对消费者造成影响的错误或缺陷;失效原因可分为潜在的和实际的。
影响分析指的是对于这些失效之处的调查研究。
基本术语失效模式(又称为故障模式)观察失效时所采取的方式;一般指的是失效的发生方式。
失效影响(又称为失效后果、故障后果)失效对于某物品/项目(英文:item)之操作、功能或功能性,或者状态所造成的直接后果。
约定级别(又称为约定级)代表物品/项目复杂性的一种标识符。
复杂性随级数接近于1而增加。
局部影响仅仅累及所分析物品/项目的失效影响。
上阶影响累及上一约定级别的失效影响。
终末影响累及最高约定级别或整个系统的失效影响。
失效原因(又称为故障原因)作为失效之根本原因的,或者启动导致失效的某一过程的,设计、加工处理、质量或零部件应用方面所存在的缺陷严重程度(又称为严重度)失效的后果。
严重程度考虑的是最终可能出现的损伤程度、财产损失或系统损坏所决定的,失效最为糟糕的潜在后果[1]。
历史从每次的失效/故障之中习得经验和教训,是一件代价高昂而又耗费时间的事情,而FMEA 则是一种用来研究失效/故障的,更为系统的方法。
同样,最好首先进行一些思维实验。
二十世纪40年代后期,美国空军正式采用了FMEA[2]。
后来,航天技术/火箭制造领域将FMEA用于在小样本情况下避免代价高昂的火箭技术发生差错。
其中的一个例子就是阿波罗空间计划。
失效模式与影响分析(FMEA)

可能给错药 药物名称或外表 厂商制造原 造成病人伤 相似 因 害
1
1
10
10
三、举例
4.分析失效模型和影响因素 表4.3 护士到病人单位给药 失效模式 原因 结果 S 1.护士太 可能给错 护士没有核对 匆忙。2. 药造成病 10 病人身份 病人没有 人伤害 识别手圈 1.无法识 给药途径 药物给药途径 别医嘱。 错误造成 10 错误 2.缺乏相 影响结果 关知识。
护士对药 卡 到备药间 备药 到病人病 房给药
三、举例
4.分析失效模型和影响因素
4.1 护士给药 表4.1护士核对给药纪录单
失效模式 结果 S 没有依照处 1.医嘱遗失。 给药记录单没有 方给药可能 10 2.书写医嘱 更新 影响病人结 时分心 果 1.书写医嘱 时不注意。 没有依照处 2.写后的医 方给药可能 给药时间不正确 嘱没有双重 10 影响病人结 核对。3.没 果 有计算机处 方系统 原因 O 5 D 5 RPN 改善措施 250
O
D RPN 改善措施
1.加强培 训。2.病 10 人佩戴手 圈
1
1
5
5
250
三、举例
5. 评判结果 失效模式 给药记录单没有更新 RPN 250
给药时间不正确 药物不正确 药物名称或外表相似
护士没有核对病人身份
250 250 10
10
药物给药途径错误
250
三、举例
6.根本原因分析 6.1列出最需要改善的失效模式: 给药记录单没有更新、给药时间不正确、药物不 正确、药物给错途径 6.2 对相应失效模式分析原因。
三、举例
3. 分析流程 主题1:病人辨识和输血流程:
制作及佩 戴手圈 采血和 备血 检验科 流程 送血到 病房 核对 病人
失效模式及影响分析

失效模式及影响分析失效模式及影响分析(Failure mode and effects analysis,简称FMEA)是一种用于系统故障预防和可靠性改进的方法。
通过对系统的各个组成部分及其可能的失效模式和影响进行分析,能够帮助识别和消除潜在的故障点,提高系统的可靠性和安全性。
失效模式(Failure mode)是指系统、产品或组件在正常条件下未能按预期执行其功能或要求的方式,即失效的特定表现形式。
常见的失效模式包括:停止工作、性能下降、产生误差、漏水/泄露、短路、断裂等。
影响(Effects)是指失效模式对系统、用户、环境或企业造成的潜在危害或负面影响。
影响的级别可以从事故、严重故障、中度故障、轻微故障、降低可靠性等方面来评估。
FMEA通过对失效模式和其影响进行分析,可以进行以下几个方面的评估:1. 严重性评估(Severity Evaluation):根据失效模式对系统、用户或环境的影响程度,评估其严重性级别。
将影响分为高、中、低等级,并确定具体的损失程度。
2. 发生频率评估(Occurrence Evaluation):根据失效模式发生的概率或频率,评估其出现的可能性。
通过对设备或系统历史数据的统计分析,可确定每年失效次数或概率。
3. 检测能力评估(Detection Evaluation):根据可用的检测手段和方法,评估对失效模式的检测能力。
检测能力可以通过验证和验证手段的准确性和可靠性来评估。
通过对这三个因素进行综合评价,可以计算出风险优先数(Risk Priority Number, RPN)。
RPN是一个综合评估指标,用于确定优先改进的失效模式。
FMEA的主要目的是帮助预防失效,减少系统故障,并且在设计或改进产品或过程时识别并降低风险。
通过FMEA分析,可以及早发现和解决潜在问题,提高系统可靠性,减少维修和停机时间,降低成本和提高用户满意度。
FMEA可以应用于各个领域,如制造业、软件开发、航空航天等。
FMEA失效分析与失效模式分析
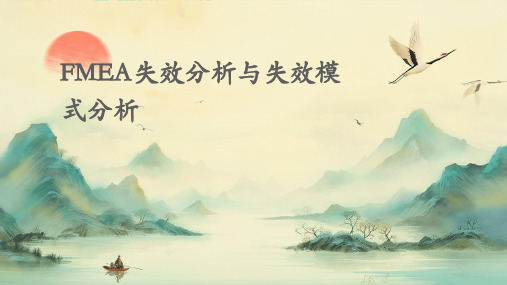
FMEA失效分析通常包括失效模式分析作为其一部分,两者都是质量 保证和可靠性工程的重要工具。
02
FMEA失效模式分析
失效模式的定义与分类
失效模式定义
在产品或过程中,可能导致产品或系 统不能达到预期功能的现象或问题。
失效模式分类
按失效的性质可分为功能失效、潜在 失效、外观失效等;按失效的原因可 分为设计缺陷、制造缺陷、使用不当 等。
06
案例研究
案例一:汽车刹车系统的FMEA失效分析
总结词
全面分析,预防为主
详细描述
通过对汽车刹车系统进行FMEA失效分析, 识别出潜在的失效模式和原因,并采取相应 的预防措施,确保刹车系统的可靠性和安全
性。
案例二
要点一
总结词
细致入微,失效定位
要点二
详细描述
对电子产品电路板进行FMEA失效模式分析,准确定位失 效模式和原因,提出改进措施,提高电路板的可靠性和稳 定性。
失效风险
指产品或系统在实现其功能过程中可能出现的故障、异常或性能下降的风险。
分类
按照失效模式和影响分析(FMEA)的方法,失效风险可分为功能失效风险和潜在失效 风险。
失效风险的分析方法
01
故障树分析(FTA)
通过建立故障树,分析系统各部件的故障对系统整体性能的影响。
02
事件树分析(ETA)
通过建立事件树,分析系统各事件的发生对系统性能的影响。
失效模式的分析方法
故障树分析法
01
通过建立故障树,分析导致故障的各种因素,确定故障发生的
概率和影响程度。
故障模式与影响分析法
02
分析产品或系统的各种故障模式,评估其对系统功能的影响程
失效模式和影响分析FMEA

c. 使新產品新製程順利開發, 並第一次就 把事情做好
d. 让顧客使用者產生安心感, 滿足感而對 產品或製程產生信賴, 並嚴深對公司所 有產品製程的信任與喜愛
(2). 實施FMEA功能
a. 預測機能達成度與安全性 b. 作為品質保證的一環而做好產品責任預防 c. 提供應注意重點以作為檢查與試驗計劃 d. 當使用時發生不良故障時提供解析情報 e. 次期產品設計參考 f. 作為產品點檢整備的要點 g. 作為設計審查依據 h. 作為估計保全費的依據
d.故障發生原因所指系統的某項目可能為
構成品
聯繫不同構成品或系統的連結處
(4) 一般故障都呈現一定模式如變形, 破 裂,短路等, 設計人員可進行物理性分 析,診斷與改善
(5)設計研發人員常致力於機能與性能而 忽視於故障防止
5. 實施可靠性解析
(1). 為實施FMEA與FTA所需開發上文件 a.可靠性目標文件有四個重點項目 環境與操作之使用條件 規定時間 要求任務機能 可靠性水準 b. 設計文件 c. 可靠性方塊圖或邏輯圖
2. 實施FMEA手法的概念
設計 產生製程
圖面
潛在 故障
副系統的故 障影响
全系統的故 障影响
問題對策案
指出 可靠性問題
故障 等級
故障 經驗
固有 技術
3. 實施FMEA目的與效果
(1). 實施目的與效果
a. 產品開發設計階段或製程設計階段, 籍 由FMEA手法事前發現可靠性欠陷, 可靠度
(1). 高性能化而產品構造,製造流程複雜化
產品 單純 → 複雜 製造 單純 → 複雜 故障 即發性→遲發性
FMEA潜在失效模式及后果分析

FMEA (F ailure M ode and E ffects A nalyses )——潜在失效模式及后果分析------预防问题发生的有效工具初次接触FMEA ,感到比较陌生,以前仅仅在质量专业资格考试的教材中看到过简短的介绍,对它并没有过多的了解。
接到FMEA 培训的任务,让我有了深入了解它的机会,接下来,让我们共同揭开它神秘的面纱。
首先,我们来了解一下,什么是FMEA ?FMEA 是在产品设计阶段和过程设计阶段,对构成产品的子系统、零件,对构成过程的各个工序逐一进行分析,找出所有潜在的失效模式,并分析其可能的后果,从而预先采取必要的措施,以提高产品的质量和可靠性的一种系统化的活动,并将全部过程形成文件。
FMEA 是一种工具,是对确定设计或过程必须做哪些事情才能使顾客满意这一过程的补充;它是一种事前行为,可以帮助我们一次就把事情做对,通过运用FMEA ,就可以实现将内部的产品制造装配过程的问题纠正及外部客户投诉产生的纠正成本降到最低。
FMEA 具备以下几方面的特点:1. 失效还未产生,可能发生、但不是一定要发生;2.在设计或过程开发阶段前开始;3.需要由各种有经验和专业知识的人组成小组合作;4.FMEA 分析的文件记录为专用表格,作为动态文件使用,按照过程/产品/服务寿命周期期间要求随时更改;4.其核心以预防为主,对潜在失效模式的风险和后果进行评定;5.指导贯穿整个过程、产品和服务周期;FMEA 有哪些类型?1.SFMEA ——系统FMEA ;2.DFMEA ——产品FMEA (设计FMEA );3.PFMEA ——过程FMEA (制造/装配FMEA );4.AFMEA ——应用FMEA ;5.SFMEA ——服务FMEA ;6.PFMEA ——采购FMEA 。
从这些分类我们可以看出FMEA 应用于产品的设计初期、采购、生产过程、服务等过程,其应用范围之广,堪称强大。
介绍一下FMEA 的发展历史,世界上首次采用FMEA 这种概念与方法的是在20世纪60年代中期美国的航天工业。
FMEA(失效模式与影响分析)

失效模式与影响分析即“潜在失效模式及后果分析”。
FMEA是在产品设计阶段和过程设计阶段,对构成产品的子系统、零件,对构成过程的各个工序逐一进行分析,找出所有潜在的失效模式,并分析其可能的后果,从而预先采取必要的措施,以提高产品的质量和可靠性的一种系统化的活动。
FMEA又根据产品故障可能产生的环节:设计、制造过程、使用、承包商(供应商)以及服务可细分为:1. DFMEA:设计FMEA2. PFMEA:过程FMEA3. EFMEA:设备FMEA4. SFMEA:体系FMEA一、概念潜在的失效模式及后果分析(Failure Mode and Effects Analysis,简记为FMEA),是“事前的预防措施”,并“由下至上。
关键词:潜在的—失效还没有发生,它可能会发生,但不一定会发生。
“核心”集中于:预防—处理预计的失效,其原因及后果/影响。
主要工作:风险评估—潜在失效模式的后果影响。
FMEA 开始于产品设计和制造过程开发活动之前,并指导贯穿实施于整个产品周期。
进行分析系统中每一产品所有可能产生的故障模式及其对系统造成的所有可能影响,并按每一个故障模式的严重程度,检测难易程度以及发生频度予以分类的一种归纳分析方法。
二、目的·能够容易、低成本地对产品或过程进行修改,从而减轻事后危机的修改。
·找到能够避免或减少这些潜在失效发生的措施;三、RPN的评价准则1.1 设计FMEA严重性(Severity :S)1)评分原则a)衡量是小的影响程度b)失效影响:产品或制程的某一失效对产品外观,结构,功能,性能稳定性,可靠性影响c)或对下一制程,使用者或设备的影响d)或对最终客户、政府法规、安全、环保的违及e)划分标准——主观判定2)设计:FMEA风险评估标准说明严重性(Severity :S):严重性是对下一个制程、系统或客户所发生的潜在失效模式效果的严重性进行评估,严重性仅适用于效果,严重性等级指数的减低只能透过设计变更才能够生效,严重性应该在1~10的等级上评估。
FMEA失效模式及分析手段

通过X光谱进行照射来分析不良,一般用在肉眼所看 不到的位置
三、声学扫描
通过超声波对内部进行扫描分析。 适用于晶元内部封装,各种孔洞,X光无法穿透物料
四、SEM&EDX
扫描电子显微镜&能谱仪
五、XPS
XPS: X光线电子能谱,也被称作化学分析用电子能谱。
原理:XPS的原理是用X射线去辐射样品,使原子或分子的内层电子或价电子 受激发射出来。被光子激发出来的电子称为光电子。可以测量光电子的能 量,以光电子的动能/束缚能为横坐标,相对强度(脉冲/s)为纵坐标可做 出光电子能谱图。从而获得试样有关信息。 适用于:元素的定性分析 ,鉴定元素的成分;元素的定量分析,原子的 含量或相对尝试;固体表面分析;化合物的结构;
FMEA是Failure Mode and Effects Analysis的 首字母简写即“失效模式与影响分析”,是在 产品的设计阶段和过程设计阶段,对构成 产品的子系统、零件、以及对构成的各个 程序逐一进行分析,找出所有潜在的失效 模式,分析其可能的影响,评估其风险, 降低其可能发生的概率,以提高产品质量 的可造性,确保顾客满意的系统化活动。
狭义:产品外观、功能的不良
FMEA
失效模式与影响分析
广义:引起不良的定位及分析
基于失效现象,能过信息收集、功能测试、电性能测试 以及简单的外观检查,确定失效部位与失效模式
使用各种物理、化学手段分析导致焊点失效或缺陷产生的机理,如 虚焊、污染、静电损伤、潮湿应力、介质腐蚀、疲劳损伤、离子迁 移、应力过载......
六、TOP-SIMS飞行时间二次离子质谱
TOF-SIMS是通过用一次离子激发样品表面,打出极其 微量的二次离子,根据二次离子因不同的质量而飞行到探 测器的时间不同来测定离子质量的极高分辨率的测量技术 。
- 1、下载文档前请自行甄别文档内容的完整性,平台不提供额外的编辑、内容补充、找答案等附加服务。
- 2、"仅部分预览"的文档,不可在线预览部分如存在完整性等问题,可反馈申请退款(可完整预览的文档不适用该条件!)。
- 3、如文档侵犯您的权益,请联系客服反馈,我们会尽快为您处理(人工客服工作时间:9:00-18:30)。
PPT文档演模板
FMEA介绍失效模式与影响分析
•誰負責FMEA
•------FMEA總負責人為PDT/PMT Leader或QIT Leader, • 因為Leader要對開發案或改善案成敗負責; •------系統組裝工程師及TEAM負責系統組裝FMEA, • 並將此給PDT/PMT/QIT; •------設計工程師及TEAM負責設計FMEA,並將此給PDT/PMT/QIT; •------制程工程師及TEAM負責制程FMEA,並將此給PDT/PMT/QIT; •------設備工程師及TEAM負責設備FMEA,並將此給PDT/PMT/QIT; •------各段制作FMEA工程師必定是PDT/PMT/QIT成員.
•分析嚴重度
•計算風險優先數 •決定優先改善之失效模式
•建議改善措施 •改善實施
•結果確認有效
PPT文档演模板
FMEA介绍失效模式与影响分析
•FMEA 結果應用
•實際------
▪ 避免採用不良率高的設計和制程; ▪ 集中資源,循序改善產品設計和制程; ▪ 循環改善,不斷提升設計和制程可靠度改進設計之參考; ▪ 制程檢驗、測試標準、檢驗程序、檢驗規範等之參考; ▪ 下次FMEA分析之參考; ▪ 產品可靠性、制程安全性、環保之評估參考; ▪ 工程師訓練之參考;
•三. 主要的特性(Major)
•4.業界標准 •1.信賴性測試
•2.產品制程不良率及分析
PPT文档演模板
FMEA介绍失效模式与影响分析
•嚴重度(S)劃分標准
•等級/評分(Rank)
•劃分標準(Criteria)
•1 (Minor)
•幾乎不會對產品有任何影響,即使有影響,客 戶亦不會注意.
•2~3(Low)
PPT文档演模板
FMEA介绍失效模式与影响分析
•FMEA種類
•系統組裝 •針對產品內子系統互相組合搭配后,可能產生之失效
FMEA:
進行FMEA
•設計FMEA: •針對產品本身因設計不當后可能產生之失效進行 FMEA
•制程FMEA •針對產品因制造流程不當后可能產生之失效進行 FMEA;或制造工藝不當后可能產生之失效進行FMEA
•在設計FMEA中, 預估產品在設計上可能發生的缺點; 衡量該 項缺點可能造成的影響, 並擬定為防止或檢測該項目缺點應 改善的設計控制, 並推動其標準化作業.
PPT文档演模板
FMEA介绍失效模式与影响分析
•設計FMEA表單
PPT文档演模板
FMEA介绍失效模式与影响分析
•潛在失效模式及后果分析表單格式
FMEA介绍失效模式与影响分析
•FMEA的益處
•PFMEA:
• ------有助於確保產品相關過程失效模式及其后果的說明;
• -----識別相關的原因和機理;
Байду номын сангаас
• -----識別減少或消除失效發生的措施;
• -----識別潛在生產或裝配過程的失效原因;
• -----識別過程參數,若該參數受控,則可減少失效情況的發生或
PPT文档演模板
FMEA介绍失效模式与影响分析
•FMEA的益處
•DFMEA: • ------有助於設計測試和開發程序; • -----從顧客角度評價失效; • -----允許跟蹤和文件化降低風險的措施; • -----將來分析和設計的極好參考; • -----設計FMEA過程的文件化.
PPT文档演模板
• 或對下一個制程,使用者和設備的影響
• 或對最終客戶,政府法規,安全,環保的違及.
▪ 劃分標準-----主觀判定
•
1-----幾乎不會有甚麼影響
•
10-----會違及安全,法規
PPT文档演模板
FMEA介绍失效模式与影响分析
•嚴重度分類
•一. 危險特性(Catestrophie)
• (無法滿足則不能銷售)
•≧1.00
•≧0.83 •≧0.67 •≧0.51 •≧0.33 •<0.33
PPT文档演模板
FMEA介绍失效模式与影响分析
•難檢度(Detection)
▪ 在現行的控制措施下,偵測失效發生的能力 ▪ 劃分標準: • 主觀判定 統計資料
•
1----有有效手段完全可以檢測出來
• 10----無任何手段可以檢測出來
▪ 及早謀求解決措施
▪根據以往經驗與教訓對一些環節的分析
•簡而言之:就是用工程方法預防失效或錯誤的發生,防患於未然.
PPT文档演模板
FMEA介绍失效模式与影响分析
•FMEA及時性
•它是一個“事前的行為”而不是“事后 行為” • • -------減輕事后修改的危機
PPT文档演模板
FMEA介绍失效模式与影响分析
意圖.主要由負責設計的工程師應用.
•PFMEA •在開發或可行性階段,在生產制程及工裝的設計 之前,主要由負責生產的工程師應用;
•FMEA •FMEA 是一種隨著新問題和信息的出現而不 斷更新的方法,是動態的永無止境的方法.
PPT文档演模板
FMEA介绍失效模式与影响分析
•FMEA 主流程
•組成FMEA團隊 • 注:開發案為PDT,改善案為QIT,團隊一定要有負責人
PPT文档演模板
FMEA介绍失效模式与影响分析
•設計FMEA
定義: 設計失效模式、效應與關鍵性分析是屬于在概念定義到設
計定型整個研究發展過程中的一項實質的設計機能, 為求達到 其效益, 設計FMEA必須配合設計發展之程序反復執行.
設計FMEA涵蓋內容包括: 產品設計FMEA、制造設計 即開 • 模或SOP等設計FMEA. •
PPT文档演模板
FMEA介绍失效模式与影响分析
•FMEA作用
•FMEA是一種工程技術及方法,用以定義、確認及消除產 品在系統、設計、制程及服務還沒有達到顧客以前已知的 或潛在的失效、問題、錯誤等等.,它是:
▪ 可靠性分析技術
▪ 系統化工程設計輔助工具
▪ 利用表格進行工程分析
▪ 在設計階段早期發現問題
PPT文档演模板
FMEA介绍失效模式与影响分析
•難檢度(D)劃分標準
•等級/評分
•劃分標準
•描述
•可偵度
•1~2
•幾 乎 可 以 肯 定 地 檢 測出來
•≧99.99%
•3~5
•有 良 好 的 手 段 可 以 檢測
•≧99.80%
•6~8
•可能檢測出來
•≧98.00%
•9
•很有可能檢測不出 •≧90.00%
PPT文档演模板
FMEA介绍失效模式与影响分析
•嚴重度、發生率、難檢度、風險優先數
▪ 嚴重度------S ▪ 發生率------O ▪ 難檢度------D ▪ 風險優先數------RPN=S*O*D
PPT文档演模板
FMEA介绍失效模式与影响分析
•嚴重度定義
▪ 恒量失效的影響程度
▪ 失效影響: 產品或制程的某一失效對產品外觀,結構,功 能,性能穩定性,可靠性影響.
•4(Moderate) •5(Moderate)
•偶爾發生,但不佔 有大的比例
•6(Moderate)
•7(High) •8(High)
•經常發生
•9(Very High) •10(Very High)
•幾乎不可避免
•1/2K
•1/400
•1/80 •1/20 •1/8 •1/3 •1/2
•≧1.17
•FMEA之本質
•工程分析
專業工程師
•(設計、制造、裝配、售后服務、質量及可靠性等)
PPT文档演模板
FMEA介绍失效模式与影响分析
•完善之FMEA必需具備
•1.確認已知及潛在失效模式 •2.確認每一失效模式的效應和原因 •3.風險優先評估(嚴重性、發生頻率及難檢度) •4.提供問題跟催及改正行動
•4.類似產品之客訴及原因
•5.類似產品之依賴性失效及原因 •表格格式
•6.類似產品之管理性問題 •7.使用維修
•分析層次
•8.環境
•失效定義
•成果整合
•時 機
•分析制程特性 •分析失效原因
•定義製造流程
•分析預估失效模 式 •分析現行控制方法
•分析產品特性 •分析失效效應
•分析發生率
•分析難檢度
•導致客戶停線或對產品有致命性的功能性 影響,或可能導致安全事故,或違及政府法規.
PPT文档演模板
FMEA介绍失效模式与影响分析
•發生率(Occurrence)
▪ 某一原因而導致失效發生的幾率
▪ 劃分標準:
•
•
CPK 主觀判定 統計資料
•
1----幾乎不會發生
•
10---幾乎肯定會發生
PPT文档演模板
•1.耐火性、自然性、UL 、CAS •2.工業標准 •3.顧客要求 •4.內部工程需要由Critical量測項目
•1.客戶及供應商共同制定特性
•二. 重大特性(Significant)
•2.或客戶指定特性,例如:規格/尺 寸
•(無法滿足則不能銷售給指定客戶 • /速度/力/溫度等.
)
•3.設計工程師指定的特性
•
增加探測性;
• -----有助於糾正措施的優先順序安排;
• ----過程中的極好參考;
• ----過程FMEA文件化;
PPT文档演模板
FMEA介绍失效模式与影响分析
•DFMEA與PFMEA實施之區別
•DFME •在開發或設計概念形成時,DFMEA在體現設計
A
意圖的同時,還應保證制造或裝配能夠實現設計
•客戶可能會注意,可能會對客戶造成裝配和 使用上的輕微不便.可能會使下道工站輕微的 重工.