工序单位能耗的计算方法、及企业吨钢可比能耗计算方法
粗钢生产工序能耗计算

粗钢生产工序能耗计算引言能耗计算是工业生产过程中的一个重要环节,通过对不同工序的能耗进行准确计算,可以帮助企业找出能耗较高的环节,进而采取相应的节能措施,提高生产效率,降低成本。
本文将针对粗钢生产过程中的不同工序进行能耗计算,以帮助企业更好地控制和优化能源消耗。
粗钢生产工序简介粗钢是指通过冶炼过程制得的未经初步加工的钢材,具有较高的含碳量和较低的纯度。
粗钢生产工序一般包括:原料准备、熔炼冶炼、钢水处理、连铸、初轧和粗轧等环节。
原料准备能耗计算原料准备环节主要包括铁矿石的破碎、磨矿、混合和配料等过程。
根据实际产量和生产数据,可以计算出原料准备环节的能耗。
原料准备能耗 = 原料准备消耗能量 / 产量熔炼冶炼能耗计算熔炼冶炼环节是将铁矿石和其他辅助材料经高温熔炼,得到钢水的过程。
熔炼冶炼能耗可以通过以下公式计算:熔炼冶炼能耗 = 燃料消耗能量 + 电能消耗能量 + 冷却水消耗能量 / 产量钢水处理能耗计算钢水处理环节是将熔炼冶炼出来的钢水经过脱硫、脱氧等处理,提高钢水的纯度和质量。
钢水处理能耗可以通过以下公式计算:钢水处理能耗 = 电能消耗能量 + 冷却水消耗能量 / 产量连铸能耗计算连铸是将钢水浇铸成连续铸坯的过程,连铸能耗可以通过以下公式计算:连铸能耗 = 电能消耗能量 + 冷却水消耗能量 + 氧气消耗能量 / 产量初轧能耗计算初轧环节是将连铸坯经过初轧机轧制成规定尺寸的厚板,并进行质量控制。
初轧能耗可以通过以下公式计算:初轧能耗 = 电能消耗能量 + 冷却水消耗能量 / 产量粗轧能耗计算粗轧环节是将初轧后的厚板不断轧制,降低其厚度,最终得到要求尺寸的薄板。
粗轧能耗可以通过以下公式计算:粗轧能耗 = 电能消耗能量 + 冷却水消耗能量 / 产量结论通过对粗钢生产工序的能耗计算,可以帮助企业找出能源消耗较高的环节,并针对性地采取节能措施,提高能源利用效率,降低生产成本。
在实际应用中,还应考虑到设备能效、操作参数等因素对能耗的影响,以实现更精确和全面的能耗计算和优化。
工业企业单位产品能耗指标计算方法
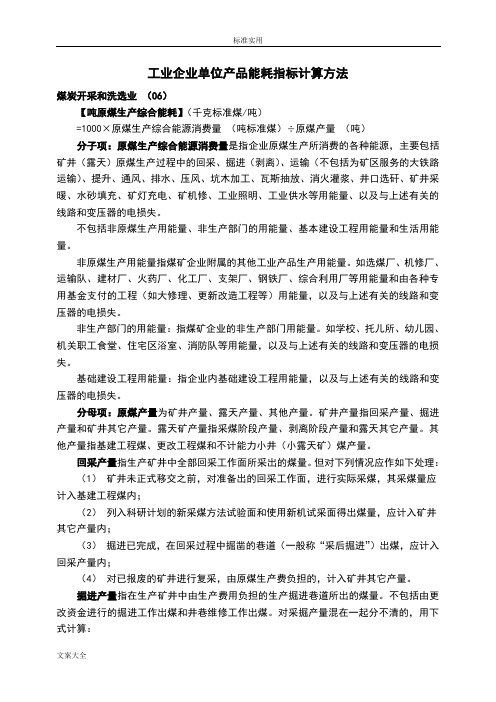
工业企业单位产品能耗指标计算方法煤炭开采和洗选业(06)【吨原煤生产综合能耗】(千克标准煤/吨)=1000×原煤生产综合能源消费量(吨标准煤)÷原煤产量(吨)分子项:原煤生产综合能源消费量是指企业原煤生产所消费的各种能源,主要包括矿井(露天)原煤生产过程中的回采、掘进(剥离)、运输(不包括为矿区服务的大铁路运输)、提升、通风、排水、压风、坑木加工、瓦斯抽放、消火灌浆、井口选矸、矿井采暖、水砂填充、矿灯充电、矿机修、工业照明、工业供水等用能量、以及与上述有关的线路和变压器的电损失。
不包括非原煤生产用能量、非生产部门的用能量、基本建设工程用能量和生活用能量。
非原煤生产用能量指煤矿企业附属的其他工业产品生产用能量。
如选煤厂、机修厂、运输队、建材厂、火药厂、化工厂、支架厂、钢铁厂、综合利用厂等用能量和由各种专用基金支付的工程(如大修理、更新改造工程等)用能量,以及与上述有关的线路和变压器的电损失。
非生产部门的用能量:指煤矿企业的非生产部门用能量。
如学校、托儿所、幼儿园、机关职工食堂、住宅区浴室、消防队等用能量,以及与上述有关的线路和变压器的电损失。
基础建设工程用能量:指企业内基础建设工程用能量,以及与上述有关的线路和变压器的电损失。
分母项:原煤产量为矿井产量、露天产量、其他产量。
矿井产量指回采产量、掘进产量和矿井其它产量。
露天矿产量指采煤阶段产量、剥离阶段产量和露天其它产量。
其他产量指基建工程煤、更改工程煤和不计能力小井(小露天矿)煤产量。
回采产量指生产矿井中全部回采工作面所采出的煤量。
但对下列情况应作如下处理:(1)矿井未正式移交之前,对准备出的回采工作面,进行实际采煤,其采煤量应计入基建工程煤内;(2)列入科研计划的新采煤方法试验面和使用新机试采面得出煤量,应计入矿井其它产量内;(3)掘进已完成,在回采过程中掘凿的巷道(一般称“采后掘进”)出煤,应计入回采产量内;(4)对已报废的矿井进行复采,由原煤生产费负担的,计入矿井其它产量。
3能耗指标体系的分类计算

能耗指标体系的分类钢铁企业能耗指标主要有吨钢综合能耗、吨钢可比能耗、主要产品的工序能耗、主要产品的实物单耗(如炼铁焦比、炼焦煤耗等)以及产值能耗、增加值能耗等等。
能源分析评价指标中,包括企业内部能源加工转换指标和企业损失指标。
按钢铁企业能耗经济技术指标体系可分为:(1)企业级能源技术经济指标:如吨钢综合能耗、万元产值能耗、吨钢耗新水、吨钢电耗、损失率等。
(2)工序级能源技术经济指标:如炼钢工序能耗、炼铁工序能耗等。
(3)耗能设备级能源技术经济指标:加热炉燃耗、高炉焦比、制氧机电耗等。
按钢铁企业能效对标指南中能耗指标体系可分为:(1)综合性指标:如企业级能源消耗总量、工序级能源消耗总量、各类能源介质消耗总量、企业能源亏损量等指标。
(2)单耗性指标:如吨钢综合能耗、企业吨钢可比能耗、工序单位产品能耗。
(3)经济性指标:万元产值能耗、万元增加值能耗等。
2.能耗指标的范围及计算钢铁制造流程是由多个不同的生产工序组成的,前一道工序的产品为下一道工序的原料,这是钢铁工业的特点,由于其复杂性,因此,统计范围和指标定义必须规范,以便于对标,找出节能潜力,提升企业效益。
(1)吨钢综合能耗范围及计算综合能耗是规定的耗能体系在一段时间内实际消耗的各种能源实物量按规定的计算方法和单位分别折算为标准煤后的总和。
吨钢综合能耗(comprehensive energy consumption ):吨钢综合能耗是企业生产每吨粗钢所综合消耗的各种能源自耗总量;也就是每生产一吨钢,企业消耗的净能源量。
其计算公式为:吨钢综合能耗=企业钢产量企业自耗能源量(吨标准煤/吨钢,千克标准煤/吨;tce/t ,kgce/t )式中,企业自耗能源量即报告期内企业自耗的全部能源量。
统计上报按企业全部耗能量。
企业自耗能源量= 企业购入能源量 ± 库存能源增减量 - 外销能源量= 企业各部位耗能量之和 + 企业能源亏损量作为行业对标,吨钢综合能耗的统计范围可按照企业生产流程的主体生产工序(包括原料储存、焦化、烧结、球团、炼铁、炼钢、连铸、轧钢、自备电厂、制氧等动力厂)、厂内运输、燃料加工及输送、企业亏损等消耗能源总量,不包括矿石的采、选工序,也不包含炭素、耐火材料、机修、石灰、精制及铁合金等非钢生产工序的能源消耗量。
6钢铁企业吨钢可比能耗计算方法

规模以上工业统计报表制度 —1—6.钢铁企业吨钢可比能耗计算方法工序 部位工序单位能耗 吨标准煤/吨产品(1)钢比或铁比 吨产品/吨钢(铁)(2)可比能耗的组成 吨标准煤/吨钢 (1)×(2)备 注焦化Aa =(烧结、球团、炼铁)耗焦量/全铁折合产量A ·aa b c 为折算铁比系数,只适用于能耗指标计算烧结 Bb =烧结矿消耗量/全铁折合产量B ·b球团 Cc =球团矿消耗量/全铁折合产量C ·c炼铁D =炼铁工序能耗/全铁折合产量D 1=炼铁工序能耗/全铁产量E = A ·a+ B ·b+ C ·c+ De :吨钢耗生铁量 E ·eD :炼铁工序折合全铁单位能耗;D 1:炼铁工序全铁单位能耗;E :企业吨铁单位能耗;转炉 电炉 其他炉 连铸F 1 F 2 F 3 F 4f 1转炉钢率 f 2电炉钢率 f 3其他炉钢率 f 4连铸钢率 (f 1+ f 2+ f 3=1)F= F 1·f 1+ F 2·f 2 + F 3·f 3+ F 4·f 4连铸能耗属炼钢工序开坯G :初轧单位能耗g ·[1— (连铸坯量+直接成材耗锭量)/ (初轧耗锭量+连铸坯量+直接成材耗锭量)]M=初轧开坯累计耗能量/(初轧耗锭量+连铸坯量+直接成材耗锭量)1.式中连铸坯量系企业直接成材消耗的连铸坯量;2.在特钢企业用钢锭成材时,生产的锻钢件(材)可按直接成材处理;3.M=G ·g ·[1— (连铸坯量+直接成材耗锭量)/ (初轧耗锭量+连铸坯量+直接成材耗锭量)]g.初轧钢坯成坯率轧材H=轧材耗能量/企业最终钢材产量h: 企业由钢到材的综合成材率 H ·h机车I=运输能耗量/企业钢产量燃气加工与输送J=燃气加工与输送耗量/企业钢产量 企业能源亏损K=企业能源亏损量/企业钢产量 企业吨钢可比能耗L=E ·e+F+M+ H ·h +I+J+K。
工序能耗计算方法

工序能耗计算方法
工序能耗计算方法:
①明确计算边界包括直接消耗能量如燃料电力以及间接消耗如蒸汽压缩空气等并确定计算周期通常以生产批次或固定时间段为准;
②收集所有相关设备运行参数比如电机功率加热炉温度冷却水流量等记录开始结束时间计算实际工作时长;
③计算单台设备能耗使用公式耗能量等于功率乘以时间单位转换成标准形式如千瓦时或兆焦耳;
④对于非直接测量项目如蒸汽消耗量通过热量平衡法估算根据蒸汽压力温度查表得出焓值再乘以流量换算成能量形式;
⑤将所有单个设备耗能量汇总得出整个工序总耗能量如果存在多个工序则分别计算各自能耗再相加得到系统总能耗;
⑥考虑到能源转换效率不同能源形式之间需要按照等价值原则进行折算例如电力转换系数通常取值为3.6MJ/kWh以便比较分析;
⑦分析工序中各环节能源利用效率识别能源浪费环节比如无效散热不必要空转等提出改进措施降低能耗;
⑧建立能源基准即在当前技术水平和操作条件下达到最佳能效状态时所消耗的能量用于评估未来改进效果;
⑨利用生命周期评估LCA方法考虑原材料获取加工运输安装使用废弃处置等全生命周期阶段能量消耗情况综合评价工序整体能效;
⑩应用能源管理系统如ISO50001标准持续监测关键能源使用区域定期审核能源绩效确保长期维持高效状态;
⑪结合历史数据分析季节性变化规律预测未来能耗趋势为节能减排提供决策支持;
⑫最后通过持续改进措施不断优化能源使用结构提高能源利用效率实现绿色低碳生产目标。
吨钢可比能耗限额与计算方法
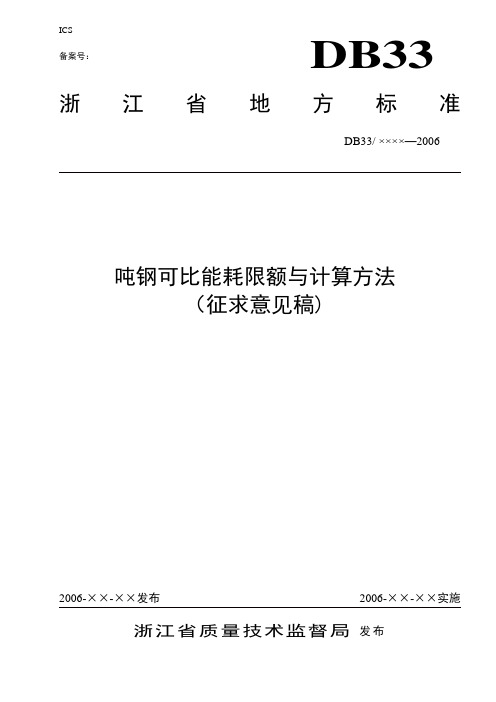
ICS备案号:DB33吨钢可比能耗限额与计算方法(征求意见稿)浙江省质量技术监督局 发布前言本标准由浙江省经济贸易委员会提出并归口。
本标准起草单位:浙江省节能协会。
本标准主要起草人:吨钢可比能耗限额与计算方法(征求意见稿)1 范围本标准规定了钢铁联合企业吨钢可比能耗限额及计算方法。
本标准适用于钢铁联合企业。
2 规范性引用文件下列文件中的条款通过本标准的引用而成为本标准的条款。
凡是注日期的引用文件,其随后所有的修改单(不包括勘误的内容)或修订版均不适用于本标准,然而,鼓励根据本标准达成协议的各方研究是否可使用这些文件的最新版本。
凡是不注日期的引用文件,其最新版本适用于本标准。
GB 17167-2006《用能单位计量器具配备与管理通则》;GB/T 6422《企业能耗计量与测试通则》;GB33/××××-××××《用能单位能源消耗量化管理要求》;《关于颁发〈钢铁企业能源平衡及能耗指标计算办法的暂行规定〉的通知》冶金工业部(82)冶能字第551号;《关于统一钢铁企业能源统计报表中各类能源折算系数的通知》冶金工业部(84)冶能办字第005号;《主要行业产品能源消耗指标培训材料》主编单位:国家统计局工交司、中国钢铁工业协会等,2006年8月。
3 定义吨钢可比能耗是指钢铁企业在报告期内,每生产一吨粗钢,从炼焦、烧结、炼铁、炼钢直到企业最终钢材配套生产所必须的耗能量及企业燃料加工与运输、机车运输能耗及企业能源亏损所分摊在每吨粗钢上的耗能量之和。
不包括钢铁工业企业的采矿、选矿、铁合金、耐火材料制品、炭素制品、煤化工产品及其它产品生产、辅助生产及非生产的能耗。
4 吨钢可比能耗的限额本限额适用期限为2006年~2010年。
指标名称计量单位指标限额吨钢可比能耗千克标准煤/吨 6305 吨钢可比能耗的计算方法钢铁企业可参照本标准引用文件中相关文件的规定,定期编制《钢铁企业能源平衡表》,并依照以下计算方法计算吨钢可比能耗,见表1。
工业企业单位产品能源消耗指标计算方法

工业企业单位产品能源消耗指标计算方法(按统计局的统计口径计算)【选煤电力单耗】(千瓦时/吨)=100×选煤生产过程耗电量(万千瓦时)/入选原煤量(吨)分子项:选煤生产过程耗电量按电业部门结算的电量计算,不包括选煤厂向外转供电量,以及与选煤生产无直接关系的各种用电量(如居民生活用电、基建工程用电、文化福利设施用电等)。
分母项:入选原煤量指从入厂毛煤中拣出的不计原煤产量的大块(一般指50毫米以上)矸石后进入选煤过程,进行加工处理的原煤量。
无机碱制造(2612)【单位烧碱生产综合能耗】(千克标准煤/吨)=1000×液体烧碱综合能源消耗量(吨标准煤)/液体烧碱产量(折100%)(吨)分子项:烧碱综合能源消耗量是指用于烧碱生产的各种能源折标准煤后的总和。
包括烧碱生产工艺系统耗能量和为烧碱生产服务的辅助系统和附属生产系统耗能量。
烧碱生产系统耗能量的统计范围,从原料投入开始,包括盐水制备、整流、电解、蒸发、蒸煮至成品烧碱包装入库为止的所有工艺用的电解用交流电、动力用电、蒸汽、油、煤等实际消耗量。
烧碱生产的辅助和附属系统耗能量的统计范围包括:电槽修理、阳极组装、石棉绒回收、炭极加工、以及车间检修、车间分析、车间办公室、休息室、更衣室等各种耗能量。
分母项:烧碱产量折成100%计算。
氢氧化钠(烧碱)(折100%)包括由盐水电解法或由纯碱(或天然碱)苛化法生产的液体氢氧化钠。
也包括氢气干燥和本企业其他产品自用的合格烧碱。
不同方法生产的各种烧碱,经检验符合国家标准(GB209-93),方可统计产量。
产量中不包括在使用烧碱过程中回收的烧碱和生产烧碱过程中自用的电解碱液、浓缩碱液、回收盐液中的含碱量。
企业填报烧碱产量,应将不同的生产方法(水银法、隔膜法、离子膜法、苛化法)生产的液碱折成100%计算产量。
【单位烧碱生产耗交流电】(千瓦小时/吨)=100×交流电消耗量(万千瓦时)/液体烧碱(100%)产量(吨)分子项:交流电消耗量以电业局安装的直流耗交流电度表为准。
粗钢生产工序能耗计算

②高炉煤气的折标量:当月高气消耗量115.09万立方米×1.30038 (当月煤热值
÷7000)=149.67吨标煤
③焦炉煤气的折标量:当月焦气消耗量180.02 万立方米×6.20457(当月煤热值
÷7000)=1116.95吨标煤
技术要求(限额准入值) v 当电力折标准煤系数采用等价值0.404kgce/(kw·h)
时,新建或改扩建烧结机生产设备烧结工序单位产 品综合能耗限额准入值应不大于60kgce/t。 v 当电力折标准煤系数从等价值0.404kgce/(kw·h)改 为当量值0.1229 kgce/(kw·h) 时,新建或改扩建烧 结机生产设备烧结工序单位产品综合能耗限额准入 参考值应不大于51kgce/t。
v 本标准适用于钢铁企业进行烧结工序(不含球 团)、高炉工序、转炉工序和电炉工序单位产品 能耗的计算、考核,以及新建设备的能耗控制 。
粗钢生产工序能耗计算
二、标准规范性引用文件
v 下列文件中的条款通过本标准的引用而成为 本标准的条款。凡是注日期的引用文件,其 随后所有的修改单(不包括勘误的内容)或修订 版均不适用于本标准,然而,鼓励根据本标 准达成协议的各方研究是否可使用这些文件 的最新版本。凡是不注日期的引用文件,其 最新版本适用于本标准。
v 企业应定期对粗钢生产的几个主要工序能耗情况进行考核, 并把考核指标分解落实到各基层单位,建立用能责任制度。
v 企业应按要求建立健全能耗统计体系,建立能耗计算和考核 结果的文件档案,并对文件进行受控管理。
v 企业应根据GB 17167的要求配备能源计量器具,并建立能 源计量管理制度。
v 树立系统节能、管理节能的大局意识,从完善工艺操作流程 、提高系统的综合生产能力、产品合格率、设备作业率、利 用系数等方面开展综合节能工作;结合生产工艺改造、扩建 、新建,实现生产设备大型化,提高产能规模。
工业企业单位产品能耗指标计算方法

工业企业单位产品能耗指标计算方法首先,计算单位产品能耗需要知道以下几个基本参数:
1.产品产量:表示工业企业在其中一时期内生产的产品数量,通常以单位统计,如吨、立方米等。
2.能源消耗:表示工业企业在其中一时期内消耗的能源数量,能源种类通常包括煤炭、原油、天然气、电力等。
3.产品能值:表示单位产品所含有的能量,不同产品的能值由产品的组成和工艺决定,通常以能量单位表示,如焦耳、千卡等。
根据以上参数,单位产品能耗的计算公式如下:
单位产品能耗=能源消耗/(产品产量×产品能值)
在实际计算过程中,为了更加准确和综合地反映单位产品能耗,还可以引入其他因素,如工艺损耗、能源损失等。
具体计算方法如下:
1.在考虑工艺损耗和能源损失的情况下,单位产品能耗=(能源消耗+工艺损耗+能源损失)/(产品产量×产品能值)
其中,工艺损耗可以通过对工艺流程进行能量平衡分析来确定,能源损失可以通过能源系统的能量平衡和能源消耗统计来确定。
2.如果需要进行综合评价和比较,可以引入能耗指标。
常见的能耗指标包括单位产品能耗、能源综合利用率、综合能耗等。
能源综合利用率表示单位产品所消耗的能源中,能够转化为产品能源的比例。
综合能耗表示单位产品所消耗的各种能源总量。
以上是一种常用的工业企业单位产品能耗的计算方法,根据实际情况,还可以根据需要进行适当调整和改进。
通过对单位产品能耗的计算和评估,工业企业可以了解自己的能源利用情况,找到节能减排和提高能源利用效
率的途径,从而推动可持续发展和绿色制造。
吨钢可比能耗计算

吨钢可比能耗计算
先计算出吨钢在各工序的耗能量,再∑
吨钢可比能耗=∑(各工序上方数*下方数)+吨钢辅助工序及亏损耗能
1、工序上方红色数据:表示吨钢所耗钢前各工序的产品量或所产出钢后工序的产品量,即相当于以吨钢计算的物流;工序下方绿色数据:表示吨钢在该工序所耗能量,即各工序的吨钢能耗。
即1.45*54.9+0.99*415.30+1*(-7.68)+0.97*42.94=524.73kgce/t
2、吨钢辅助工序及亏损耗能:
亏损耗能:燃料加工与运输、机车运输、企业能源亏损。
⑴2012年高炉煤气放散率11.66%,氧气放散率
22.32%,氮气放散率21.5%,柴油914.36吨。
(11.66%*12412万m3*0.11+22.32%*15978万m3*0.062+21.5%*19854万m3*0.033+914.36*1.4571)/钢产量=24.53+1.77+1.13+1.07=28.5kgce/t
⑵辅助工序(石灰工序+矿渣粉工序+动力工序)即:
(石灰工序总能耗+矿渣粉工序总能耗+动力工序总能
耗)/钢产量
=(21991.57+8873.03+11201.96+296.03)/1245391*1000
34.01kgce/t
3、综合上述:2012年企业吨钢可比能耗524.73+28.5+34.01=587.24kgce/t。
2009年有限公司吨钢可比能耗541 kgce/t、2008年559 kgce/t、2007年544 kgce/t。
粗钢生产工序能耗计算

设备性能
总结词
设备性能的优劣直接关系到能耗的高低。
详细描述
设备的效率、维护状况以及设备老化程度等都会影响能耗。高效的设备可以降 低能耗,而设备维护不当或老化严重则可能导致能耗增加。
直接能耗计算方法是根据实际消耗的能源量和相应的能耗系数,计算出直 接能耗量。
直接能耗计算需要考虑不同生产工艺和设备对能源消耗的影响,以及能源 利用效率和能源品质等因素。
间接能耗计算
01
间接能耗是指在粗钢生产过程中,为保证生产正常运
行而消耗的能源,如供热、通风、照明等。
02
间接能耗计算方法是根据实际消耗的能源量和相应的
。
推广节能操作方法
03
总结和推广各生产工序中的节能操作方法,规范员工的操作行
为。
提高员工节能意识
开展节能宣传教育
通过宣传栏、内部刊物、培训等方式,普及节 能知识,提高员工的节能意识。
组织节能培训
定期组织节能培训和交流活动,让员工学习节 能技术和经验,提高节能技能。
鼓励员工提出节能建议
建立员工建议征集制度,鼓励员工提出节能意见和建议,激发全员参与节能的 积极性。
能耗系数,计算出间接能耗量。
03
间接能耗计算需要考虑生产工艺和设备对能源消耗的
需求,以及能源利用效率和能源品质等因素。
总能耗计算
01
总能耗是指粗钢生产过程中直 接和间接消耗的能源总量。
02
总能耗计算方法是将直接能耗 和间接能耗相加,得出总能耗 量。
03
总能耗计算需要考虑不同生产 工艺和设备对能源消耗的影响 ,以及能源利用效率和能源品 质等因素。
工序单位能耗的计算方法、及企业吨钢可比能耗计算方法

一、各工序单位能耗计算方法:二、其它能耗计算方法的资料中国8个钢铁企业产量达千万吨近几年中国钢铁工业生产规模明显扩大,年产钢1000万吨以上的企业已有8家,年产钢500万吨以上的共有1 7家,年产钢300万吨以上的有30多家。
2005年产钢1000万吨以上企业由2000年的1家(宝钢)上升到8家(宝钢、鞍钢、唐钢、武钢、首钢、沙钢、济钢、莱钢),合计产钢11191.9万吨,占全国钢产量的31.76%。
产钢大于500万吨小于1000万吨企业由2000年的3家(鞍钢、首钢、武钢)上升到2005年的9家 (马钢、华菱钢铁、包钢、邯钢、攀钢、安阳钢铁、太钢、酒钢、建龙钢铁),合计产钢6051.21万吨,占全国钢产量的17. 17%。
产钢300万吨以上企业共30家,合计产钢22079.65万吨,占全国钢产量的62.65%。
据介绍,中国钢产量已由2000年的1.28亿吨上升到2005年的3.52亿吨,钢产量占世界钢产量的比例由2000年的15.2%上升至2005年的31.1%。
标准煤系数就是把某一能源品种的实物量折合成标准量时所采用的系数,换句话说,就是单位能源的实际发热值与7000千卡的比率:即:单位能源的实际发热值7000千卡=该能源品种折标准煤系数例如:1公斤焦炭的平均低位发热量为6800千卡,其折标准煤系数为:6800千卡÷7000千卡=0.9714。
也就是说,1公斤焦炭相当于0.9714公斤标准煤,1000吨焦炭相当于971.4吨标准煤。
在企业内部同一能源品种,由于到货时间、供货单位的不同,其实际发热值也不一样。
在此情况下,确定企业标准煤系数,一般采用“加权算术平均数”的计算方法,加权算术平均数是反映次数结构影响的算术平均数,它的计算方法是总体各标志值(变量值)乘以相应的次数(权数)之和与总次数(总权数)的比。
例如:某企业2002年5月份先后从枣庄、肥城、山西、兖州等地购入原煤的实际数量分别为150吨、175吨、250吨、250吨,每次到货后实测发热值分别为4910千卡/公斤、4509千卡/公斤、5101千卡/公斤、5250千卡/公斤,这些原煤在本月全部消耗,那么该企业5月份消耗煤炭折标准煤587.62吨,折标准煤系数为0.7123。
工序能耗计算公式

工序能耗计算公式以工序能耗计算公式为标题,本文将介绍工序能耗计算的基本原理和方法。
一、工序能耗计算的重要性工序能耗计算是企业能源管理的关键环节之一,通过对工序能耗的准确计算,可以帮助企业找出能源浪费的环节,制定合理的节能措施,提高能源利用效率,降低生产成本,实现可持续发展。
工序能耗计算公式是根据能量守恒定律和质量守恒定律建立的,通常可以表示为以下形式:工序能耗 = 能耗系数× 生产量其中,能耗系数是指单位产量所消耗的能源量,可以根据实际情况进行测算或参考相关标准;生产量是指工序的产出数量。
三、工序能耗计算方法1. 确定能耗系数:根据工序的特点和能源使用情况,可以通过实际测算或参考相关标准确定能耗系数。
不同工序的能耗系数可能会有所不同,因此需要根据具体情况进行调整。
2. 收集生产量数据:通过生产记录或生产统计系统等方式,收集工序的产量数据。
要保证数据的准确性和完整性,可以进行抽样检查或全面统计。
3. 进行计算:根据工序能耗计算公式,将能耗系数和生产量代入计算公式,进行计算,得出工序的能耗数据。
4. 分析结果:根据计算结果,对工序的能耗情况进行分析,找出能源浪费的环节,制定相应的节能措施。
可以比较不同工序的能耗数据,找出能效较低的工序,重点改善。
四、工序能耗计算的实例以某家纺织企业的染色工序为例,假设染料消耗量为100千克,染色机每千克染料耗电0.5度,染色机的能耗系数为0.5度/千克。
染色工序的产量为1000千克。
根据工序能耗计算公式,可以计算出染色工序的能耗:工序能耗 = 0.5度/千克× 1000千克 = 500度通过对染色工序能耗的计算,企业可以了解到染色工序的能源消耗情况,进而制定相应的节能措施,如优化染色机的使用方式,减少染料的消耗量,提高能源利用效率,降低能源成本。
五、工序能耗计算的应用工序能耗计算不仅可以用于企业内部的能源管理,还可以用于能耗评估和能源标识等方面。
国内外吨钢综合能耗、可比能耗和工序能耗比较

内外吨钢综合能耗、可比能耗和工序能耗比较钢铁工业是国民经济重要的基础原材料工业,也是高耗能、高污染工业。
钢铁工业节约潜力巨大,为此,国外大型钢铁企业纷纷采取先进技术,开展节能降耗和综合利用,发展循环经济,不断优化工业的能耗指标和环保指标,以期达到能耗最少,环保最优。
与国外发达水平相比,我国钢铁工业差距明显。
2004年,我国大中型钢铁企业吨钢综合能耗为761千克标煤,比国际先进水平高81千克标煤;吨钢耗新水11. 15m3,比国际先进水平高 7. 3m:,;固体废物综合利用率乩比国际先进水平低个百分点。
在此,以我国大中型钢铁企业的相关指标与国外发达水平作对比,目的是寻找差距,迎头赶上。
下表列出了2003年我国重点企业主要工序能耗与国际先进水平(1999年)的比较,数据表明,我国转炉工序能耗与国外先进水平差值最大,炼铁工序差值最小。
2003年我国钢铁工业吨钢综合能耗为770kgce,吨钢可比能耗698kgce;2003年日本钢铁工业吨钢综合能耗为656kgce, 2000年国外主要产钢国家(英、日、法、徳)平均吨钢可比能耗为642kgce。
这两项指标分别比国外先进水平高出%和觥在国外,先进企业的高炉焦比已达到300kg/t以下,燃料比小于500kg/to我国重点钢铁企业的入炉焦比为426kg/t,部分其它企业为488kg/t,燃料比为560kg/t左右。
高炉工艺的能耗(标媒)比世界先进水平高出50〜 100kg/to同时,我国重点企业之间主要工序能耗的差距很大,指标先进的(如宝钢集团)已达到或超过国际先进水平, 而落后的能耗要高出先进值的1倍或数倍。
这说明,我国钢铁工业节能的潜力还是很大的。
新制订的《钢铁产业发展政策》明确提出,要建立循环型钢铁工厂,500万吨以上规模钢铁联合企业,要努力做到电力自供有余,实现外供。
2005年,全行业吨钢综合能耗降到吨标煤、吨钢可比能耗吨标煤、吨钢耗新水12吨以下;2010年分别降到吨标煤、吨标煤、8吨以下;2020年分别降到吨标煤、吨标煤、6吨以下。
吨钢可比能耗限额和电炉钢冶炼电耗 限额及计算方法

5 统计范围和计算方法
5.1 能耗统计范围及能源折标准煤系数取值原则
5.1.1 统计范围
5.1.1.1 吨钢可比能耗:包括焦化、烧结、球团、炼铁、炼钢、开坯、轧材等工序耗能量及企业燃料 加工与输送、机车运输能耗及企业能源亏损所消耗的能源量之和。扣除回收利用和外供的能源量。不包 括钢铁工业企业的采矿、选矿、铁合金、耐火材料制品、炭素制品、煤化工产品及其它产品生产、辅助 生产及非生产的能耗。 5.1.1.2 电炉钢冶炼电耗:炼钢电炉变压器一次侧表,即炉前电度表指示的耗电量。不包括为提高电 炉钢质量服务的 LF 等炉外精炼所耗电量,不包括电炉炼钢工序(车间)的其它用电量。
5
DB33/ XXXXX—2011
注:工序单位能耗,指的是报告期内各自工序所消耗的燃料、动力量,扣去本工序回收的燃料、动力以及余压、余 热后的耗能量,与本工序合格产品的比值。
6
DB33/ 666—2011 BB
附录B (资料性附录) 各种能源折标准煤参考系数
工业企业单位产品能耗指标计算方法报告
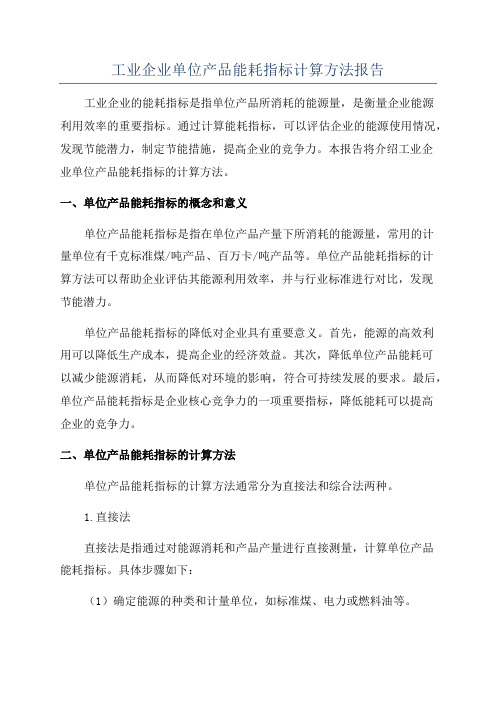
工业企业单位产品能耗指标计算方法报告工业企业的能耗指标是指单位产品所消耗的能源量,是衡量企业能源利用效率的重要指标。
通过计算能耗指标,可以评估企业的能源使用情况,发现节能潜力,制定节能措施,提高企业的竞争力。
本报告将介绍工业企业单位产品能耗指标的计算方法。
一、单位产品能耗指标的概念和意义单位产品能耗指标是指在单位产品产量下所消耗的能源量,常用的计量单位有千克标准煤/吨产品、百万卡/吨产品等。
单位产品能耗指标的计算方法可以帮助企业评估其能源利用效率,并与行业标准进行对比,发现节能潜力。
单位产品能耗指标的降低对企业具有重要意义。
首先,能源的高效利用可以降低生产成本,提高企业的经济效益。
其次,降低单位产品能耗可以减少能源消耗,从而降低对环境的影响,符合可持续发展的要求。
最后,单位产品能耗指标是企业核心竞争力的一项重要指标,降低能耗可以提高企业的竞争力。
二、单位产品能耗指标的计算方法单位产品能耗指标的计算方法通常分为直接法和综合法两种。
1.直接法直接法是指通过对能源消耗和产品产量进行直接测量,计算单位产品能耗指标。
具体步骤如下:(1)确定能源的种类和计量单位,如标准煤、电力或燃料油等。
(2)记录能源消耗量和产品产量,可通过仪表记录和生产数据进行获取。
(3)计算单位产品能耗指标,单位为能源消耗量/产品产量。
2.综合法综合法是指通过统计能源消耗和产品产量的数据,计算单位产品能耗指标。
具体步骤如下:(1)收集企业的生产数据,包括能源消耗量和产品产量。
(2)制定能源消耗和产品产量的统计表格,对数据进行分类汇总。
(3)计算能源消耗的综合指标,即能源消耗量/产品产量。
三、单位产品能耗指标的应用单位产品能耗指标的应用可以帮助企业发现节能潜力,制定节能措施,提高能源利用效率。
除了与行业标准进行对比外,还可以与历史数据进行对比,评估节能效果。
在应用过程中,还需注意以下几个问题:首先,要确保数据的准确性和完整性,避免因为数据错误而导致判断错误;其次,要考虑不同产品的能耗差异,避免简单地将能耗指标平均分配给不同产品;最后,要充分考虑生产工艺和设备变化,以及人员素质等因素的影响。
单位能耗计算公式
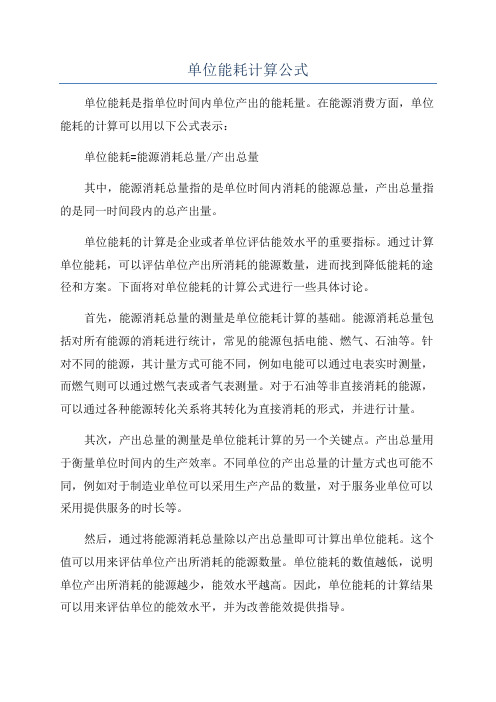
单位能耗计算公式单位能耗是指单位时间内单位产出的能耗量。
在能源消费方面,单位能耗的计算可以用以下公式表示:单位能耗=能源消耗总量/产出总量其中,能源消耗总量指的是单位时间内消耗的能源总量,产出总量指的是同一时间段内的总产出量。
单位能耗的计算是企业或者单位评估能效水平的重要指标。
通过计算单位能耗,可以评估单位产出所消耗的能源数量,进而找到降低能耗的途径和方案。
下面将对单位能耗的计算公式进行一些具体讨论。
首先,能源消耗总量的测量是单位能耗计算的基础。
能源消耗总量包括对所有能源的消耗进行统计,常见的能源包括电能、燃气、石油等。
针对不同的能源,其计量方式可能不同,例如电能可以通过电表实时测量,而燃气则可以通过燃气表或者气表测量。
对于石油等非直接消耗的能源,可以通过各种能源转化关系将其转化为直接消耗的形式,并进行计量。
其次,产出总量的测量是单位能耗计算的另一个关键点。
产出总量用于衡量单位时间内的生产效率。
不同单位的产出总量的计量方式也可能不同,例如对于制造业单位可以采用生产产品的数量,对于服务业单位可以采用提供服务的时长等。
然后,通过将能源消耗总量除以产出总量即可计算出单位能耗。
这个值可以用来评估单位产出所消耗的能源数量。
单位能耗的数值越低,说明单位产出所消耗的能源越少,能效水平越高。
因此,单位能耗的计算结果可以用来评估单位的能效水平,并为改善能效提供指导。
同样重要的是,在计算单位能耗时,还需要考虑单位时间的选择。
通常,单位能耗以年度或季度为单位进行计算。
这是因为单位能耗的计算结果需要一定的时间间隔来进行比较和分析,以便发现能源消耗的趋势和规律。
除了以上的基本公式,对于一些特殊情况,如多能源消耗的单位或者多产出类型的单位,可以采用不同的计算方法来计算单位能耗,如加权平均法、成本法等。
这些方法可以更精确地反映单位能耗情况,提供更有效的能源管理措施。
在实际应用中,单位能耗的计算可以应用于各个行业和领域。
比如在制造业中,可以计算不同产品的单位能耗,找出能源消耗较高的产品,并通过优化生产工艺、设备更新等措施降低能耗。
工业企业单位产品能源消耗指标计算方法
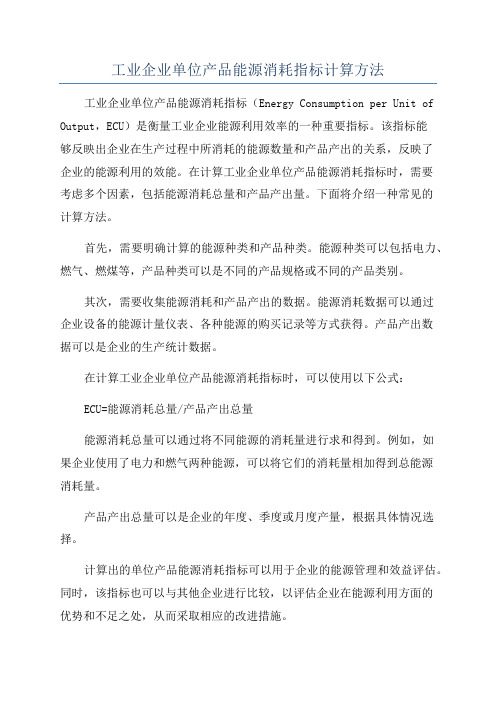
工业企业单位产品能源消耗指标计算方法工业企业单位产品能源消耗指标(Energy Consumption per Unit of Output,ECU)是衡量工业企业能源利用效率的一种重要指标。
该指标能够反映出企业在生产过程中所消耗的能源数量和产品产出的关系,反映了企业的能源利用的效能。
在计算工业企业单位产品能源消耗指标时,需要考虑多个因素,包括能源消耗总量和产品产出量。
下面将介绍一种常见的计算方法。
首先,需要明确计算的能源种类和产品种类。
能源种类可以包括电力、燃气、燃煤等,产品种类可以是不同的产品规格或不同的产品类别。
其次,需要收集能源消耗和产品产出的数据。
能源消耗数据可以通过企业设备的能源计量仪表、各种能源的购买记录等方式获得。
产品产出数据可以是企业的生产统计数据。
在计算工业企业单位产品能源消耗指标时,可以使用以下公式:ECU=能源消耗总量/产品产出总量能源消耗总量可以通过将不同能源的消耗量进行求和得到。
例如,如果企业使用了电力和燃气两种能源,可以将它们的消耗量相加得到总能源消耗量。
产品产出总量可以是企业的年度、季度或月度产量,根据具体情况选择。
计算出的单位产品能源消耗指标可以用于企业的能源管理和效益评估。
同时,该指标也可以与其他企业进行比较,以评估企业在能源利用方面的优势和不足之处,从而采取相应的改进措施。
需要注意的是,由于能源消耗和产品产出可能受到多个因素的影响,企业在计算单位产品能源消耗指标时应当尽可能保证数据的准确性和可比性。
此外,不同行业和不同企业之间的单位产品能源消耗指标也会存在差异,因此,在比较企业的能源利用效率时应当考虑到行业特点和企业规模等因素。
总之,单位产品能源消耗指标是衡量工业企业能源利用效率的重要指标。
通过合理的计算方法和数据收集,可以得出准确的指标值,从而帮助企业进行能源管理和效益评估,提高能源利用效率。
单位产品能源消耗情况指标的计算方法

单位产品能源消耗情况指标的计算方法单位产品能源消耗情况指标的计算方法黑色金属冶炼及压延加工业(32)吨钢综合能耗:钢铁企业在报告期内,按每吨粗钢合格产出量核算的钢铁工业生产中能源净消耗量。
计算公式:吨钢综合能耗(千克标准煤/吨)=企业净耗能源量(吨标准煤)/粗钢合格产出量(吨)×1000粗钢合格产出量是指报告期内,企业完成了粗钢生产过程,并符合产品质量要求的模铸钢锭、连铸钢坯、铸造用液态钢(铸钢水)产出量之和,包括订货者来料加工生产的产品,不包括委外加工生产的产品。
吨钢综合电耗:钢铁企业在报告期内,按每吨粗钢合格产出量核算的钢铁工业生产中净耗电总量。
计算公式:吨钢综合电耗(千瓦时/吨)=钢铁工业生产中净耗电总量(万千瓦时)/粗钢合格产出量(吨)×10000计算说明:钢铁工业生产中净耗电总量包括报告期内生产直接消耗的各种电力及其辅助生产系统实际消耗的各种电力,即企业净耗的全部电量。
吨钢耗新水:钢铁企业在报告期内,按每吨粗钢合格产出量核算的钢铁工业生产中耗用新水量。
计算公式:吨钢耗新水(吨/吨)=企业耗用新水量(万吨)/粗钢合格产出量(吨)×10000计算说明:1.“新水用量”为企业报告期内用新鲜水量,即直接取自“自来水”、“地下水”、“地表水”及其他外购水及水产品的数量。
2.钢铁联合企业的普通钢厂或特殊钢厂的新水取水量(新水量)供给范围,包括主要生产(含烧结、球团、焦化、炼铁、炼钢、轧钢、金属制品等)辅助生产(含鼓风机站、氧气站、石灰窑、空压站、锅炉房、机修、电修、检化验、运输等)和附属生产(含厂部、科室、绿化、厂内食堂、厂区和车间浴室、保健站、厕所等);不包括企业电厂用于发电的取水量(含电厂自用的化学水)、矿山选矿用水和外供水量。
3.不产粗钢的企业可以选定自己的主产品,参照本指标计算“吨产品耗新水”。
吨钢可比能耗:钢铁企业在报告期内,每生产一吨粗钢,从炼焦、烧结、炼铁、炼钢直到企业最终钢材配套生产所必须的耗能量及企业燃料加工与运输、机车运输能耗及企业能源亏损所分摊在每吨粗钢上的耗能量之和。
工序能耗计算方法及等级指标

⼯序能耗计算⽅法及等级指标主扇通风机⼯序能耗计算⽅法及等级指标本⽅法适⽤于煤矿主扇通风机⼯序能耗的计算及等级划分。
1.⼯序能耗定义主通风机⼯序能耗是指在统计期内主扇通风机排出(或压⼊)1兆⽴⽅⽶风量,压⼒升⾼1帕时,所消耗的电能。
2.主扇通风机⼯序边界以拖动主扇通风机的电动机开关柜输⼊端为起点,风机出(⼊)风⼝为能量终端。
3.统计期主扇通风机⼯序能耗以测试和统计数据为基础,统计期为⼀年。
4.主扇通风机⼯序能耗统计计算公式 4.1单台主扇通风机⼯序能耗计算公式:'410f W E Q P=?式中:'f E=—统计期内单台主风扇通风机⼯序能耗,kw ·h/Mm 3·pa ;W ——统计期内单台主风扇通风机⼯序耗电量,kw ·h ;Q ——统计期内单台主风扇通风机⼯序抽出(压⼊)的风量,m 3; P ——统计期内单台主风扇通风机⼯序平均全压,pa; 为了便于实际应⽤,上式可以⽤如下形式表⽰,即:'1t mj jj m W E t Q P ==∑'t E ——统计期内单台风机⼯序能耗,kw ·h/Mm 3·pa ;W ——统计期内单台主风扇通风机⼯序耗电量,kw ·h ;t ——统计期内单台风机的运⾏时间,s ; m ——统计期内单台风机测试次数;Q j ——统计期内第j 次测量流量,m 3/s; P j ——统计期内第j 次测量全压,Pa ;4.2 测点:在通风机进、出风⼝两侧选择测试截⾯和测点。
4.3 ⽅法:通风机全压和风量测试计算⽅法按照煤炭⼯业出版社《矿⼭固定设备技术测定》中规定的有关风机风量、全压测算⽅法进⾏。
4.4 测试⼯况:只测算风机正常运⾏⼯况下的全压、风量,勿需折算到标准状态。
4.5 测试时间:在统计期内每季度⾄少测试⼀次,且每季度测试次数必须相同,测试稳定⼯况下的风量、全压。
4.6 耗电量的统计计算:统计期内主通风机所消耗的电能,以拖动风机的电动机实际消耗的电能为准(同步电机包括励磁电能消耗)。
- 1、下载文档前请自行甄别文档内容的完整性,平台不提供额外的编辑、内容补充、找答案等附加服务。
- 2、"仅部分预览"的文档,不可在线预览部分如存在完整性等问题,可反馈申请退款(可完整预览的文档不适用该条件!)。
- 3、如文档侵犯您的权益,请联系客服反馈,我们会尽快为您处理(人工客服工作时间:9:00-18:30)。
一、各工序单位能耗计算方法:
二、其它能耗计算方法的资料
中国8个钢铁企业产量达千万吨
近几年中国钢铁工业生产规模明显扩大,年产钢1000万吨以上的企业已有8家,年产钢500万吨以上的共有1 7家,年产钢300万吨以上的有30多家。
2005年产钢1000万吨以上企业由2000年的1家(宝钢)上升到8家(宝钢、鞍钢、唐钢、武钢、首钢、沙钢、济钢、莱钢),合计产钢万吨,占全国钢产量的%。
产钢大于500万吨小于1000万吨企业由2000年的3家(鞍钢、首钢、武钢)上升到2005年的9家 (马钢、华菱钢铁、包钢、邯钢、攀钢、安阳钢铁、太钢、酒钢、建龙钢铁),合计产钢万吨,占全国钢产量的17. 17%。
产钢300万吨以上企业共30家,合计产钢万吨,占全国钢产量的%。
据介绍,中国钢产量已由2000年的亿吨上升到2005年的亿吨,钢产量占世界钢产量的比例由2000年的%上升至2005年的%。
标准煤系数就是把某一能源品种的实物量折合成标准量时所采用的系数,换句话说,就是单位能源的实际发热值与7000千卡的比率:即:
单位能源的实际发热值
=该能源品种折标准煤系数
7000千卡
例如:1公斤焦炭的平均低位发热量为6800千卡,其折标准煤系数为:6800千卡÷7000千卡=。
也就是说,1公斤焦炭相当于0.9714公斤
标准煤,1000吨焦炭相当于吨标准煤。
在企业内部同一能源品种,由于到货时间、供货单位的不同,其实际发热值也不一样。
在此情况下,确定企业标准煤系数,一般采用“加权算术平均数”的计算方法,加权算术平均数是反映次数结构影响的算术平均数,它的计算方法是总体各标志值(变量值)乘以相应的次数(权数)之和与总次数(总权数)的比。
例如:某企业2002年5月份先后从枣庄、肥城、山西、兖州等地购入原煤的实际数量分别为150吨、175吨、250吨、250吨,每次到货后实测发热值分别为4910千卡/公斤、4509千卡/公斤、5101千卡/公斤、5250千卡/公斤,这些原煤在本月全部消耗,那么该企业5月份消耗煤炭折标准煤吨,折标准煤系数为。
即 :折标准煤=150×4910+175×4509+250×5101+250×5250
7000 =(吨)
折标准煤系数=错误!=
计算折标准煤系数时可将上两步合为一步求得:即
折标准煤系数=150×4910+175×4509+250×5101+250×5250
7000
÷825=
错误!=
由此可以得出计算任一能源品种在某一时期内折标准煤系数的一般计算公式为:
某一时期任一能源品种 折标准煤系数 =∑〔某一批能源 品种购入量 ×该品种能源平均低位发热量
〕
7000千卡 ÷
该能源某一时期内购入量之和
能源品种折标准煤系数的确定
(一)煤炭折标准煤系数的确定
可按下列顺序依次确定:l、由实测计算确定。
2、如不具备实测条件,可用煤矿发货单上的发热量计算出。
3、按照当年能源统计制度规定的参考系数。
(二)焦炭折标准煤系数的确定
有条件的单位应实测计算,否则用当年统计制度规定的参考系数计算。
(三)天然气折标准煤系数的确定
有条件的单位应按气田天然气、油田伴生气、煤田天然气(即煤矿瓦斯气)分别实测计算,否则以当年统计制度规定的折算系数折标(即每立方米天然气折1.3300公斤标准煤,每万立方米天然气折吨标准煤)。
(四)热力折标准煤系数的确定及其换算
热力主要指蒸汽和热水量。
蒸汽分为饱和蒸汽和过热蒸汽。
热力的计算单位现行统计报表制度要求统一换算为“百万千焦”或“万百万千焦”。
其换算关系为:
以“卡”作单位转换为以“焦耳”作单位及其折标准煤系数。
1千卡=千焦,
1百万千卡=百万千焦=吨标煤
1万百万千卡=万百万千焦=万吨标煤。
以“焦耳”作单位转换为以“卡”为单位及折标准煤系数。
l千焦=千卡
1百万千焦=百万千卡=吨标煤
1万百万千焦=万百万千卡=万吨标煤各种能源折标准煤参考系数
注:此表平均低位发热量用千卡表示,如需换算成焦耳,只需乘上即可。
吨钢综合能耗
包括从铁水(原料)进厂到钢锭(坯)出厂全部工艺过程中所消耗的一次和二次能源。
铁水预处理、连铸工艺、炉外精炼、电除尘设备等的燃料(含煤气、燃油)消耗及服务于炼钢的各种蒸汽、压缩空气、电力等动力消耗,都要计入炼钢工序能耗中,按其平均低位发热量折算标准煤。
计算公式为:
吨钢综合能耗(千克标准煤/吨)
=炼钢燃料消 耗 量 +动 力消耗量 - 转炉煤气余热
回收外供量 (千克标准煤)
钢产量(吨)
注:为方便计算,规定子项单位为吨标准煤,母项单位为吨。
计算结果乘以1000。
吨钢可比能耗(联合企业)
指企业每生产一吨钢,从炼铁、炼钢直到成材配套生产所必需的耗能量及企业燃料加工与输送、机车运输能耗及企业能源亏损量之和,折算成标准煤。
计算列于下表:
钢铁企业吨钢可比能耗计算方法
L=E·e+F+M+ H·h+I+J+K
.钢铁企业吨钢可比能耗计算方法
工序
部位
工序单位能耗
吨标准煤/吨产品
(1)钢比或铁比
吨产品/吨钢(铁)
(2)可比能耗的组成
吨标准煤/吨钢
(1)×(2)
备注
焦化
A
a=(烧结,球团,炼铁)耗焦量/全铁折合产量
A・a
a b c为折算铁比系数,只适用于能耗指标计算烧结
B
b=烧结矿消耗量/全铁折合产量B・b
球团
C
c=球团矿消耗量/全铁折合产量C・c
炼铁
D=炼铁工序能耗/全铁折合产量1=炼铁工序能耗/全铁产量
E= A・a+ B・b+ C・c+ D
e:吨钢耗生铁量
E・e
D:炼铁工序折合全铁单位能耗; D1:炼铁工序全铁单位能耗; E:企业吨铁单位能耗;
转炉
电炉
其他炉
连铸
F1
F2
F3
F4
f 1转炉钢率
f2电炉钢率
f3其他炉钢率
f4连铸钢率
(f 1+ f2+ f3=1)
F= F1・f 1+ F2・f2
+ F3・f3+ F4・f4
连铸能耗属炼钢工序
开坯
G:初轧单位能耗
g・[1― (连铸坯量+直接成材耗锭量)/ (初轧耗锭量+连铸坯量+直接成材耗锭量)]
M=初轧开坯累计耗能量/(初轧耗锭量+连铸坯量+直接成材耗锭量)
1.式中连铸坯量系企业直接成材消耗的连铸坯量;
2.在特钢企业用钢锭成材时,生产的锻钢件(材)可按直接成材处理;
=G・g・[1― (连铸坯量+直接成材耗锭量)/ (初轧耗锭量+连铸坯量+直接成材耗锭量)]
g.初轧钢坯成坯率
轧材
H=轧材耗能量/企业最终钢材产量
h: 企业由钢到材的综合成材率
H・h
机车
I=运输能耗量/企业钢产量
燃气加工与输送
J=燃气加工与输送耗量/企业钢产量
企业能源亏损
K=企业能源亏损量/企业钢产量
企业吨钢可比能耗
L=E・e+F+M+ H・h0+I+J+K
―― 规模以上工业统计报表制度
规模以上工业统计报表制度――。