齿轮润滑油泵的润滑状态分析
电动润滑油泵工作原理

电动润滑油泵工作原理
电动润滑油泵是一种通过电动机驱动的润滑装置,常用于各类机械设备的润滑系统中。
其工作原理是通过电动机的旋转运动,驱动一根传动轴,传动轴上附着有一片或多片齿轮。
当电动机运行时,传动轴旋转,齿轮也随之旋转。
在油泵壳体内,有一个润滑油箱,里面存放着润滑油。
当齿轮转动时,齿轮之间的间隙会不断变大和变小,从而改变了液体容积。
当间隙变大时,润滑油会被吸入到齿轮之间的间隙中;当间隙变小时,润滑油会被压入到出口管道中。
这样,润滑油就会不断地从润滑油箱中吸入和压出,形成了一定的流动。
为了确保润滑油能够顺利地吸入和压出,电动润滑油泵通常还配备了一些辅助装置,如吸入管、排气阀和过滤器。
吸入管负责将润滑油从润滑油箱吸入到油泵中;排气阀用于排除油泵内部产生的空气;过滤器则用于过滤润滑油中的杂质,保证油品的清洁。
通过这种方式,电动润滑油泵可以将润滑油输送到需要润滑的设备部位,提供良好的润滑效果。
同时,电动润滑油泵还具有自动化控制的功能,可以根据设备的工作状态和需求进行智能调节,确保润滑系统的稳定性和运行安全性。
1.齿轮油泵的用途

1.齿轮油泵的用途
齿轮油泵是一种用于输送润滑油的设备,主要用途如下:
1. 提供润滑油:齿轮油泵能够将润滑油从储油器或油箱中抽取并输送到需要润滑的机械设备中,确保设备运行过程中不发生过热、磨损等问题,保障设备的正常运转。
2. 冷却:齿轮油泵可以通过循环润滑油的方式对机械设备进行冷却,帮助降低设备的温度,避免设备过热导致损坏。
3. 清洁:齿轮油泵可以通过高压泵送方式将润滑油喷射到机械设备的摩擦表面,起到清洁作用,将机械设备表面的污垢、异物等清除掉,保持设备的运行环境清洁。
4. 维护润滑膜:齿轮油泵可以为机械设备提供稳定的润滑膜,降低设备运行时的摩擦系数,减少磨损和能耗,延长设备的使用寿命。
总之,齿轮油泵的用途主要是为机械设备提供润滑油,确保设备的正常运转和延长设备寿命。
齿轮箱润滑系统解析
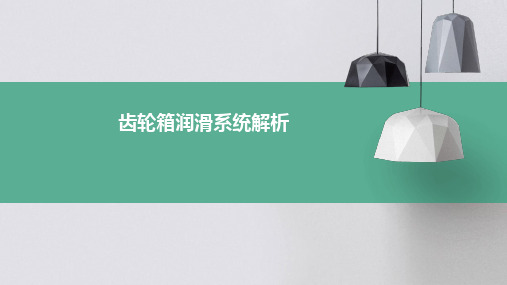
油箱是储存润滑油的容器,通常设计 有过滤网和加热器等装置,以确保润 滑油的清洁和适宜的温损耗性润滑系统和循环润滑系统。全损耗性润滑系统 是指润滑油在循环过程中不经过冷却和过滤,直接用于润滑 齿轮和轴承;循环润滑系统则是指润滑油在循环过程中经过 冷却和过滤,再输送到各个润滑点。
保养滤清器
定期更换或清洗滤清器,防止杂质进入润滑系统,影响润滑效果。
润滑系统的检查与维修
检查油泵
定期检查油泵的运行状况,确保油泵能 够正常工作,保证润滑油的循环和供给 。
VS
维修润滑系统
对于润滑系统中出现的故障或损坏,应及 时进行维修或更换相关部件,以保证系统 的正常运行。
04
齿轮箱润滑系统常见问题及 解决方案
THANKS
作用
齿轮箱润滑系统的主要作用是确保齿轮和轴承等运动部件的正常运转,提高设 备的使用寿命和稳定性,同时降低能耗和维护成本。
齿轮箱润滑系统的组成
油泵
油泵是润滑系统的核心部件,用于将 润滑油从油箱中抽出,并输送到各个 润滑点。
油箱
过滤器用于清除润滑油中的杂质和微 粒,保持润滑油的清洁度。
油管
油管用于连接油泵、过滤器和润滑点 ,将润滑油输送至各个需要润滑的部 位。
齿轮箱润滑系统解析
$number {01}
目 录
• 齿轮箱润滑系统概述 • 齿轮箱润滑系统的原理 • 齿轮箱润滑系统的维护与保养 • 齿轮箱润滑系统常见问题及解决
方案 • 齿轮箱润滑系统的发展趋势与展
望
01
齿轮箱润滑系统概述
齿轮箱润滑系统的定义与作用
定义
齿轮箱润滑系统是用于向齿轮箱内的齿轮、轴承等运动部件提供润滑油的装置, 以减少摩擦和磨损,降低工作温度,防止腐蚀,并起到缓冲和减震的作用。
润滑系统机油泵的工作原理(一)

润滑系统机油泵的工作原理(一)润滑系统机油泵的工作润滑系统机油泵是发动机的重要组成部分,负责为发动机提供足够的润滑油,以确保各个摩擦面之间的摩擦不会产生过多的热量和磨损,从而延长发动机寿命。
下面我们来一步一步了解润滑系统机油泵的工作原理。
机油泵的主要部件润滑系统机油泵一般由以下几个部件组成:•泵体•齿轮•泵轴•安装基座•进出油口•滤清器机油泵的工作原理润滑系统机油泵的工作原理主要分为两个部分,下面我们来分别介绍。
吸油过程1.润滑油从进油口流入机油泵的泵体内;2.随着泵轴的转动,齿轮开始运转;3.齿轮转动时,齿轮的凹槽内会产生一个低压区域,使润滑油被吸入齿轮的一个齿槽中;4.随着泵轴和齿轮的不断转动,润滑油被推移到泵体出油口处。
推油过程1.润滑泵将润滑油推出泵体的强制性过程;2.润滑油进入进油口,并填充齿轮的凹槽;3.同时随着齿轮的转动,润滑油被推入出口;4.润滑油通过出口到达相应的润滑点,起到润滑作用。
机油泵的故障与维护机油泵在使用过程中可能会出现以下故障:•泵体失灵•齿轮轴承损坏•润滑油流量不足为了保证机油泵的正常工作,我们需要经常进行以下维护:•定期更换机油和机油滤清器•检查机油泵的进出口连通情况•检查机油泵的齿轮磨损情况•定期清洗泵体和齿轮,消除泥沙等杂质对机油泵的影响润滑系统机油泵的工作原理比较简单,但其工作对发动机的性能和寿命影响极大。
因此,我们需要对机油泵进行定期的检修和维护,以确保其正常工作。
机油泵的类型和选用机油泵有多种类型,主要有齿轮泵、螺杆泵、液压泵等。
不同类型的机油泵适用于不同的场合和性能要求。
在选用机油泵时,需要考虑以下因素:•发动机的转速和功率•润滑油的粘度和流量要求•润滑系统的压力和温度•设备的可靠性和寿命综合考虑以上因素,选用适合的机油泵,才能保证润滑系统的正常工作和设备的长久使用。
结语机油泵是润滑系统的核心部件之一,其工作原理和性能直接影响发动机的性能和寿命。
因此,了解机油泵的工作原理和故障维护方法,对于保障设备性能和寿命具有重要意义。
齿轮油泵毕业设计

齿轮油泵毕业设计齿轮油泵毕业设计毕业设计是大学生在校期间的重要任务之一,它既是对所学知识的综合运用,也是对学生综合素质的考验。
在机械工程专业中,齿轮油泵是一个常见的研究课题。
本文将从齿轮油泵的原理、设计要点以及实际应用等方面进行探讨。
一、齿轮油泵的原理齿轮油泵是一种常用的润滑系统,其工作原理基于齿轮的旋转和齿间的间隙。
当齿轮旋转时,齿间的间隙会形成一片低压区域,使液体从低压区域被吸入,然后通过齿轮的旋转将液体挤出。
这样循环往复,实现了油液的输送和润滑。
二、齿轮油泵的设计要点1. 齿轮的选择:齿轮的材质和齿数是设计中需要考虑的重要因素。
材质的选择应根据工作环境的要求,例如耐磨性、耐腐蚀性等。
齿数的选择则需要根据所需的输送流量和工作压力来确定。
2. 齿轮的配对:齿轮的配对是保证油泵正常工作的关键。
配对时需要考虑齿轮的模数、齿轮的啮合角、齿轮的啮合系数等因素。
合理的配对可以减小齿轮的磨损和噪音,提高油泵的效率。
3. 泵体的设计:泵体的设计需要考虑流体的流动性和泵的结构强度。
流体的流动性可以通过优化泵体的内部结构来实现,例如增加流道的流线型设计。
泵的结构强度则需要根据工作压力和载荷来确定,以确保泵体不会发生变形或破裂。
4. 密封系统的设计:密封系统是齿轮油泵中的关键部件之一。
合理的密封系统设计可以减小泄漏和污染,提高油泵的工作效率。
常见的密封系统包括轴封、密封垫圈等。
三、齿轮油泵的实际应用齿轮油泵广泛应用于各种机械设备中,例如汽车发动机、工业机械等。
在汽车发动机中,齿轮油泵负责将润滑油送到各个润滑点,保证发动机的正常运转。
在工业机械中,齿轮油泵常用于润滑系统,确保机械设备的正常工作。
齿轮油泵的设计和应用涉及到机械工程、流体力学等多个学科领域,对于提高学生的综合能力和解决实际问题具有重要意义。
在毕业设计中选择齿轮油泵作为课题,可以让学生深入了解润滑系统的原理和设计要点,并通过实际应用来验证设计的有效性。
总之,齿轮油泵是机械工程专业中一个重要的研究课题。
齿轮油泵性能及参数

齿轮油泵性能及参数一、齿轮油泵产品概述:1、本泵适用于输送各种有润滑性的液体,温度不高于70℃,如需高温200℃,同本单位联系可配用耐高温材料即可,粘度为5×10-5~1.5×10-3m2/s。
2、齿轮油泵不适用于输送腐蚀性的、含硬质颗粒或纤维的、高度挥发或闪点低的液体,如汽油、笨等。
泵体中装有一对回转齿轮,依靠两齿轮的相互啮合,把泵内的整个工作腔分两个独立的部分。
泵运转时主动齿轮带动被动齿轮旋转,当齿轮脱开啮合时在吸入侧就形成局部真空,液体被吸入。
被吸入的液体充满齿轮的各个齿谷而带到排出侧,单级单吸油泵齿轮进入啮合时液体被挤出而排出泵外。
二、齿轮油泵结构说明:本产品由泵体、齿轮、前后泵盖、安全阀、轴承及密封装置等零、部件组成。
1、泵体、前后盖等零件为灰铸铁件,齿轮用优质碳素钢制作;亦可根据用户需要用铜材或不锈钢制作。
2、安全阀。
齿轮油泵自身不带安全阀,用户在使用时需自行在管路系统中安装安全阀。
KCB,系列齿轮油泵在后泵盖或泵体上方装有安全阀,当泵或排出管道发生故障或将排出阀门完全关闭而产生高压和高压击时安全阀就会自动打开,卸除部分或全部的高压液体回到吸入腔,从而对泵及管道起到安全保护作用。
3、轴承。
齿轮油泵全部采用DU轴承;可根据用户要求采用锡青铜轴承。
&0818.3-83.3、1.1齿轮油泵采用DU轴承;可根据用户要求采用锡青铜轴承。
KCB133-960、8-60齿轮油泵有采用DU轴承,锡青铜轴承和滚动轴承三种结构,需在订货时注明。
订货时未注明者均按DU轴承结构供货。
轴承为内置型式,依靠被输送介质进行润滑;011轴承和锡青铜轴承能在非润滑性介质中工作。
4、轴封。
本系列产品的轴端密封有骨架油封、机械密封及填料密封三种结构。
a.骨架油封:骨架油封的特点是维护、更换方便,成本低,但寿命较短。
丁晴胶骨架油封适用于1001:以下工作环境;氟橡胶骨架油封适用于200℃以下工作环境。
齿轮式机油泵的工作原理

齿轮式机油泵的工作原理齿轮式机油泵是一种常见的润滑系统元件,其主要作用是将机油从油底壳中吸取并压送到发动机内部各个润滑点,以保证发动机的正常运转。
下面将详细介绍齿轮式机油泵的工作原理。
一、齿轮式机油泵的结构齿轮式机油泵由驱动齿轮、从动齿轮、泵体和配流器等组成。
其中,驱动齿轮由发动机曲轴带动旋转,从而带动从动齿轮旋转,使得泵体内的机油被吸入,并通过配流器被压送至发动机润滑系统。
二、齿轮式机油泵的工作原理1. 吸入阶段当发动机启动时,曲轴带动驱动齿轮旋转,从而带动从动齿轮旋转。
在此过程中,因为两个相互啮合的齿轮之间存在空隙,所以在其啮合点附近形成了一定大小的容积。
当从动齿轮与驱动齿轮之间形成容积时,泵体内的机油就会被吸入到齿轮之间的空隙中。
2. 压送阶段当从动齿轮继续旋转时,其啮合点逐渐向泵体的出口方向移动,从而使得齿轮之间的容积逐渐减小。
因为机油是不可压缩的,所以在容积减小的过程中,机油会受到一定的压力作用,并通过配流器被压送至发动机润滑系统。
3. 排出阶段当从动齿轮完全旋转一周后,其啮合点回到了起始位置。
此时,在驱动齿轮和从动齿轮之间仍然存在一定大小的容积,但是其中已经没有机油了。
因此,在下一个工作周期开始前,需要将这部分空气排出泵体,以便下一次工作时能够正常吸入机油。
三、齿轮式机油泵的优缺点1. 优点(1)结构简单:由于齿轮式机油泵只由少量部件组成,因此其结构相对简单。
(2)工作稳定:由于其工作原理比较简单,在使用过程中很少出现故障。
(3)压力稳定:齿轮式机油泵在压送机油时,由于齿轮之间的容积是固定的,因此其压力相对稳定。
2. 缺点(1)噪音大:由于齿轮之间存在空隙,因此在工作过程中会产生一定的噪音。
(2)易磨损:由于齿轮之间需要相互啮合,因此在长期使用过程中容易磨损。
(3)润滑不足:由于齿轮式机油泵本身就是用来压送机油的,因此其自身润滑不足。
如果长时间使用不加润滑油,则会导致泵体内部的齿轮磨损加剧。
齿轮泵

齿轮油泵适用于输送各种有润滑性的液体,温度不高于70℃,如需高温200℃,可配用耐高温材料即可,粘度为5×10-5~1.5×10-3m2/s。
本泵不适用于输送腐蚀性的、含硬质颗粒或纤维的、高度挥发或闪点低的液体,如汽油、苯等。
润滑系统中机油泵的作用:机油泵作用是将机油提高到一定压力后,强制地压送到发动机各零件的运动表面上。
其结构多采用齿轮式机油泵。
发动机工作时,曲轴带动主动齿轮传动,被动齿轮作反方向旋转。
吸油腔内的机油便沿着齿隙和泵壁压入出油腔。
因吸油腔内的机油被不断带走,故吸油腔内产生吸力,不断地将油底壳内的机油吸入吸油腔,并同时将一定压力的机油泵入润滑油路。
一工作原理齿轮泵是用两个齿轮互啮转动来工作,对介质要求不高。
一般的压齿轮油泵力在6MPa以下,流量较大。
齿轮油泵在泵体中装有一对回转齿轮,一个主动,一个被动,依靠两齿轮的相互啮合,把泵内的整个工作腔分两个独立的部分。
A为吸入腔,B为排出腔。
齿轮油泵在运转时主动齿轮带动被动齿轮旋转,当齿轮从啮合到脱开时在吸入侧(A)就形成局部真空,液体被吸入。
被吸入的液体充满齿轮的各个齿谷而带到排出侧(B),齿轮进入啮合时液体被挤出,形成高压液体并经泵排出口排出泵外。
齿轮油泵结构原理图注:1、齿轮油泵不宜作空运转,使用时,抽吸完毕,即停泵,否则会加速磨损。
也可能磨损泵管,因本泵电机空载转速可达10000转/分。
2、齿轮油泵及时调换电刷,电刷磨损到将不能使用时,须及时调换(2只电刷同时调换)否则会使电刷与换向器接触不良引起坏损,损坏换向器,严重时会烧坏电枢。
3、齿轮油泵在下列情况下不得使用,在使用过程中如发现绝缘损坏,电源线工电缆护套破裂,插头插座开裂或接触不良,以及断续运转,出现严惩火花等故障时,电机外壳操作时,应立即进行修理。
在未修复前不得使用。
4、齿轮油泵防止过载,使用时,凡遇转速异常或降低时,应即停机检查是否有杂物卡住叶轮或电机是否发生故障,抽液泵因故刹车时必须立即切断电源5、齿轮油泵使用工具要爱惜,所有抽涂泵要小心轻放避免受到冲击。
9FA燃气轮机交流润滑油泵工作异常分析

9FA燃气轮机交流润滑油泵工作异常分析燃气轮机交流润滑油泵的工作异常可能会导致润滑油供应不足或者完全停止,对轴承的润滑效果产生影响,进而引发轴承损坏等严重故障。
因此,对燃气轮机交流润滑油泵的工作异常进行分析和处理显得尤为重要。
1.泵的振动异常:如果交流润滑油泵工作时出现明显的振动,说明泵运行不稳定,可能是由于轴与轴套不匹配、轴承损坏、叶片破损或不平衡等问题引起的。
解决方法包括更换不合格的轴套和轴承,或进行动平衡处理,使泵轴运行平稳。
2.泵的噪音异常:如果交流润滑油泵工作时出现异常的噪音,可能是由于泵叶片磨损严重、叶轮与静态环的间隙过大或发生变形等问题所致。
解决方法包括更换磨损严重的叶片,调整叶轮与静态环之间的间隙,或更换变形的叶轮。
3.泵的密封故障:如果交流润滑油泵出现泄漏现象,可能是由于密封件老化、密封面破损或密封环安装不当等原因导致。
应该及时更换老化的密封件,修复或更换破损的密封面,并确保密封环正确安装。
4.泵的排气异常:如果交流润滑油泵工作时无法正常排气,可能是由于进气阀门堵塞、排气阀门密封不良或阀门弹簧损坏等问题引起的。
解决方法包括清洗或更换堵塞的进气阀门,修复或更换密封不良的排气阀门,以及更换损坏的阀门弹簧。
5.泵的流量异常:如果交流润滑油泵供给润滑系统的流量异常,可能是由于进口管道堵塞、出口阀门未完全打开、泵叶片磨损或泵齿轮故障等问题所致。
应当清洗堵塞的进口管道,确保完全打开出口阀门,更换磨损的泵叶片,或修复泵齿轮故障。
6.泵的电机异常:如果交流润滑油泵的电机无法正常启动或持续运行,可能是由于电源故障、电机绕组断路或电机过载等问题引起的。
应仔细检查和排除电源故障,修复电机绕组的断路问题,或调整电机的负荷以确保正常运行。
总之,燃气轮机交流润滑油泵的工作异常可能涉及泵的振动、噪音、密封、排气、流量以及电机等方面的问题。
通过仔细分析异常现象的原因,并采取相应的解决方法,可以保证燃气轮机的润滑油供应正常,提高设备的可靠性和工作效率。
慢速齿轮传动的润滑方法
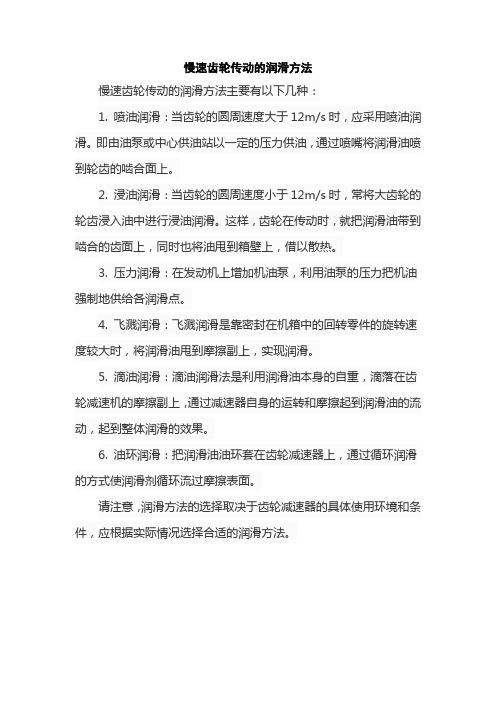
慢速齿轮传动的润滑方法
慢速齿轮传动的润滑方法主要有以下几种:
1. 喷油润滑:当齿轮的圆周速度大于12m/s时,应采用喷油润滑。
即由油泵或中心供油站以一定的压力供油,通过喷嘴将润滑油喷到轮齿的啮合面上。
2. 浸油润滑:当齿轮的圆周速度小于12m/s时,常将大齿轮的轮齿浸入油中进行浸油润滑。
这样,齿轮在传动时,就把润滑油带到啮合的齿面上,同时也将油甩到箱壁上,借以散热。
3. 压力润滑:在发动机上增加机油泵,利用油泵的压力把机油强制地供给各润滑点。
4. 飞溅润滑:飞溅润滑是靠密封在机箱中的回转零件的旋转速度较大时,将润滑油甩到摩擦副上,实现润滑。
5. 滴油润滑:滴油润滑法是利用润滑油本身的自重,滴落在齿轮减速机的摩擦副上,通过减速器自身的运转和摩擦起到润滑油的流动,起到整体润滑的效果。
6. 油环润滑:把润滑油油环套在齿轮减速器上,通过循环润滑的方式使润滑剂循环流过摩擦表面。
请注意,润滑方法的选择取决于齿轮减速器的具体使用环境和条件,应根据实际情况选择合适的润滑方法。
goldka润滑油泵说明书

goldka润滑油泵说明书1主要用于各种机械设备中的润滑系统中输送润滑油,适用于输送粘度在10。
E(75C.S.t)以下,温度在300℃以下的具有润滑性的油料。
2结构润滑油泵主要由泵体、齿轮、轴、轴承、前盖后盖、密封部件、联轴器等部件组成。
轴端密封有二种形式:填料密封、机械密封。
3工作原理啮合的齿轮在泵体内旋转时,轮齿不断进入和退出跟啮合。
在吸入室,轮齿逐渐退出啮合状态,这样吸入室的容积逐渐增大,压力降低,液体在液面压力的作用下进入吸入室,随齿轮齿间进入排出室。
在排出室,轮齿又逐渐进入啮合状态,齿轮的齿间逐渐被一齿轮的轮齿占据,排出室的容积减少,排出室内液体压力升高,于是液体从泵的排出口被排出泵外,齿轮边续旋转,上述过程不断进行,形成连续的输油过程。
4故障与排除不排油或排油少原因:1.吸入高度太高超过额定值2.吸入管道漏气3.旋转方向不对4.吸入管道堵塞或阀门关闭5.液体温度低而使粘度增大6.齿轮与泵体麿损严重方法:1.提高吸油面或减少管阻力2.检查各接合处是否漏气或漏液并加石棉等密封村料加以密封3.按泵的指示方向纠正转向4.清除堵塞物,开启阀门5.预热液体,如不可能则降低排出压力减少排油量6.拆卸检查有关另件并更换之密封漏油原因:1.轴封处未调整好2.密封圈磨损,间隙增大3.机械密封静环和动环的磨擦面损坏或有毛刺划痕等缺陷4.弹簧松弛方法:1.重新调整2.造量拧紧螺母,或更换密封圈3.更换动静环或重新研磨4.更换弹簧噪音或振动大原因:1.吸入网或滤网堵塞2.吸管伸入油池较浅3.管道进入空气4.排出管道阻力太大5.齿轮、轴承或侧板磨损严重6.吸入液体的粘度太大方法:1.清除滤网上的污物2.吸入管应伸入油池0.5米左右3.检查各连接之处使之密封4.对管道和阀门进行检查,并排出堵塞之物,或调整管路减少弯头、阀门等5.更换新齿轮、轴承或侧板6.按第一段第六条处理。
齿轮油泵不上油的原因

齿轮油泵不上油的原因
齿轮油泵不上油的原因
齿轮油泵是一种常见的润滑油泵设备,但在实际使用中,有时会出现齿轮油泵不上油的情况,这将导致机器损坏,生产效率下降等问题。
下面是齿轮油泵不上油的原因分析。
一、油泵本身故障
1.轴承故障:如果轴承已经磨损或者损坏,轴就会堆积,减少了油泵的效率,导致油泵不能正常输送油液。
2.内部涂层磨损:这种问题可能出现在长期使用的机器上,如果齿轮油泵内部涂层已经磨损,就会导致泵的工作不正常,无法推动油。
3.密封不良:如果油泵的密封性不好,部分液体将会被泄漏,导致泵总体效率降低。
二、油泵系统故障
1.油泵进口过滤器阻塞:如果油泵进口的过滤器被阻塞,液体将无法进入油泵,从而导致油泵失效。
2.油泵口管路堵塞:管路堵塞可能使齿轮油泵缺乏足够的油液,并且无法将油液输送到正确的目的地。
三、过错误的操作
1.使用错误的油液:齿轮油泵需要粘稠度高、流动性好的油液才能正
常工作。
如果使用了不合适的油液,那么油泵就会出现故障。
2.机器长时间停运:长期不使用设备会使部件生锈、沉淀和堵塞,这将导致油泵出现故障。
结论
以上是齿轮油泵不上油的几个可能原因,我们可以采取相应措施来避免这些问题的出现。
例如,我们可以定期检查油泵运转状态、检查管路是否通畅,以及正确选择合适的油液。
这样,在实际使用中,我们才能避免油泵故障,提高生产效率。
齿轮油泵设计及工艺分析

齿轮油泵设计及工艺分析毕业设计(论文)题目齿轮油泵设计及工艺分析专业精密机械班级学号 2姓名指导教师年月日I学生姓名专业班级联系方式指导老师指导老师职称联系方式课题名称齿轮油泵设计和工艺分析一、设计的技术要求(或论文的主要内容):(1)完成齿轮油泵相关技术资料的查阅,收集与课题相关的信息;(2)分析齿轮油泵的工作原理与结构;(3)完成齿轮油泵的装配图和重要零件的零件图;(4)设计齿轮油泵的三维立体图形。
(5)按学校要求独立撰写毕业设计论文。
二、实施操作的技能要求:1、技能要求:(1)学会查阅技术文献和资料; 课 (2)掌握齿轮油泵的工作原理与结构; 题 (3)熟练运用AUTOCAD进行绘图;任 (4)熟练运用UG软件进行三维实体建模;务 (5)掌握撰写论文的方法和能力。
要 2、内容要求求 (1)完成设计图纸一套(包括装配图一套;零件图2-3张);(2)三维效果图一份;(3)开题报告及论文各一份三、时间安排与要求:2014年9月23日---10月6日准备阶段2014年10月7日---11月10日开题阶段2014年11月11日---12月8日课题阶段设计2014年12月9日---12月29日论文撰写阶段2014年12月30日---1月5日答辩阶段专业组审批意见专业负责人(签字)年月日二级学院审批意见分管院长(签字)年月日指导教师(签字)年月日,此表一式3份~1份上交机电工程学院教学科~1份下达至学生~1份存指导老师处。
,II齿轮油泵设计[摘要] 齿轮泵是液压系统中最重要的动力源,在液压传动系统中应用广泛, 因此, 吸引了大量学者对其进行研究,其主要部件是内部相互啮合的一对齿轮。
齿轮油泵主要用于各种机械设备中的润滑系统中输送润滑油,适用于输送粘度为5×10-6,1.5×10-3m2/s (5-1500cSt),温度在300?以下的具有润滑性的油料。
不锈钢齿轮泵,可输送无润滑性的油料、饮料、低腐蚀性的液体。
简述齿轮泵的困油现象及解决措施

简述齿轮泵的困油现象及解决措施
齿轮泵是驱动机械油进行分配和流动的一种设备,广泛用于内燃机、柴油机、汽车等设备。
齿轮泵运行时,难免会出现困油现象,这就给机械设备的安全性能带来一定的影响。
下面,我们就来讨论一下齿轮泵的困油现象及解决措施。
一、齿轮泵的困油现象
1、空气污染:齿轮泵在运行过程中,油泵内的空气会被油泵的空气过滤器清除,但是由于油泵本身的漏油现象,会干扰油泵内部的空气流动,更容易产生空气污染。
2、油量不足:油泵长期运行,风扇吸入的空气会吸收空气中的水分,从而减少油泵内部的润滑油量。
3、油泵压力不足:齿轮泵内部吸入的空气越多,其压力会相对较低,导致油泵的压力失灵,无法驱动机械设备的正常运行。
二、解决困油现象的措施
1、更换油泵:油泵在运行过程中,如果发现润滑油量不足,则应及时更换油泵,以更新油泵内部的机械部件,减少漏油现象,延长油泵寿命。
2、清洁过滤器:油泵内部的空气过滤器要及时清洗,以减少空气中的杂质、水分等,提高齿轮泵的运行效率。
3、定期检查:齿轮泵的定期检查非常重要,可以及时发现油泵的问题,并及时采取纠正措施。
4、安装润滑系统:安装润滑系统,可以在运行过程中,对油泵
的润滑状态进行实时监控,以及调节润滑油的流量,确保油泵正常运行。
以上就是齿轮泵的困油现象及解决措施,要想有效提高齿轮泵的正常运行,需要正确使用油泵,科学进行维护、检查,有效降低设备的缺陷率,提高设备的故障率。
此外,还建议大家定期进行清洗和保养,以防止油泵出现漏油、漏气等现象,减少其他故障的发生,保证机械设备的安全性能。
齿轮泵的振动分析及解决办法
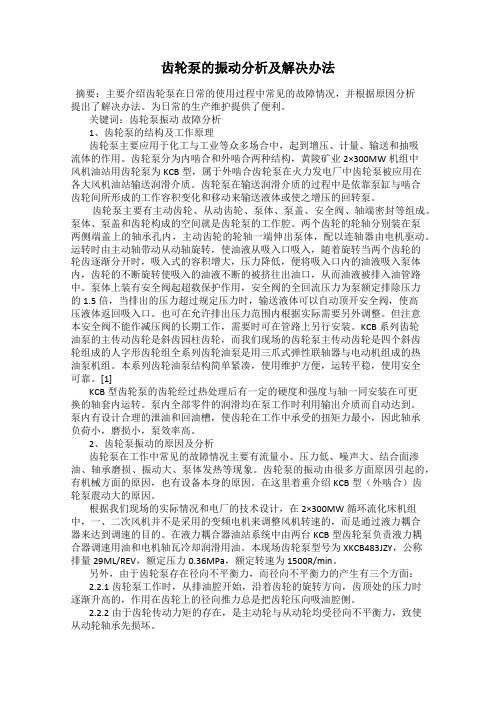
齿轮泵的振动分析及解决办法摘要:主要介绍齿轮泵在日常的使用过程中常见的故障情况,并根据原因分析提出了解决办法。
为日常的生产维护提供了便利。
关键词:齿轮泵振动故障分析1、齿轮泵的结构及工作原理齿轮泵主要应用于化工与工业等众多场合中,起到增压、计量、输送和抽吸流体的作用。
齿轮泵分为内啮合和外啮合两种结构,黄陵矿业2×300MW机组中风机油站用齿轮泵为KCB型,属于外啮合齿轮泵在火力发电厂中齿轮泵被应用在各大风机油站输送润滑介质。
齿轮泵在输送润滑介质的过程中是依靠泵缸与啮合齿轮间所形成的工作容积变化和移动来输送液体或使之增压的回转泵。
齿轮泵主要有主动齿轮、从动齿轮、泵体、泵盖、安全阀、轴端密封等组成。
泵体、泵盖和齿轮构成的空间就是齿轮泵的工作腔。
两个齿轮的轮轴分别装在泵两侧端盖上的轴承孔内,主动齿轮的轮轴一端伸出泵体,配以连轴器由电机驱动。
运转时由主动轴带动从动轴旋转,使油液从吸入口吸入,随着旋转当两个齿轮的轮齿逐渐分开时,吸入式的容积增大,压力降低,便将吸入口内的油液吸入泵体内,齿轮的不断旋转使吸入的油液不断的被挤往出油口,从而油液被排入油管路中。
泵体上装有安全阀起超载保护作用,安全阀的全回流压力为泵额定排除压力的1.5倍,当排出的压力超过规定压力时,输送液体可以自动顶开安全阀,使高压液体返回吸入口。
也可在允许排出压力范围内根据实际需要另外调整。
但注意本安全阀不能作减压阀的长期工作,需要时可在管路上另行安装。
KCB系列齿轮油泵的主传动齿轮是斜齿园柱齿轮,而我们现场的齿轮泵主传动齿轮是四个斜齿轮组成的人字形齿轮组全系列齿轮油泵是用三爪式弹性联轴器与电动机组成的热油泵机组。
本系列齿轮油泵结构简单紧凑,使用维护方便,运转平稳,使用安全可靠。
[1]KCB型齿轮泵的齿轮经过热处理后有一定的硬度和强度与轴一同安装在可更换的轴套内运转。
泵内全部零件的润滑均在泵工作时利用输出介质而自动达到。
泵内有设计合理的泄油和回油槽,使齿轮在工作中承受的扭矩力最小,因此轴承负荷小,磨损小,泵效率高。
齿轮油泵的故障分析及排除方法
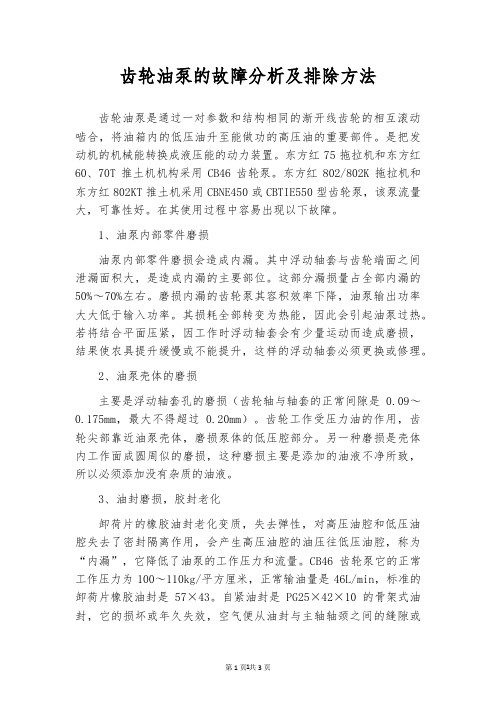
齿轮油泵的故障分析及排除方法齿轮油泵是通过一对参数和结构相同的渐开线齿轮的相互滚动啮合,将油箱内的低压油升至能做功的高压油的重要部件。
是把发动机的机械能转换成液压能的动力装置。
东方红75拖拉机和东方红60、70T推土机机构采用CB46齿轮泵。
东方红802/802K拖拉机和东方红802KT推土机采用CBNE450或CBTIE550型齿轮泵,该泵流量大,可靠性好。
在其使用过程中容易出现以下故障。
1、油泵内部零件磨损油泵内部零件磨损会造成内漏。
其中浮动轴套与齿轮端面之间泄漏面积大,是造成内漏的主要部位。
这部分漏损量占全部内漏的50%~70%左右。
磨损内漏的齿轮泵其容积效率下降,油泵输出功率大大低于输入功率。
其损耗全部转变为热能,因此会引起油泵过热。
若将结合平面压紧,因工作时浮动轴套会有少量运动而造成磨损,结果使农具提升缓慢或不能提升,这样的浮动轴套必须更换或修理。
2、油泵壳体的磨损主要是浮动轴套孔的磨损(齿轮轴与轴套的正常间隙是0.09~0.175mm,最大不得超过0.20mm)。
齿轮工作受压力油的作用,齿轮尖部靠近油泵壳体,磨损泵体的低压腔部分。
另一种磨损是壳体内工作面成圆周似的磨损,这种磨损主要是添加的油液不净所致,所以必须添加没有杂质的油液。
3、油封磨损,胶封老化卸荷片的橡胶油封老化变质,失去弹性,对高压油腔和低压油腔失去了密封隔离作用,会产生高压油腔的油压往低压油腔,称为“内漏”,它降低了油泵的工作压力和流量。
CB46齿轮泵它的正常工作压力为100~110kg/平方厘米,正常输油量是46L/min,标准的卸荷片橡胶油封是57×43。
自紧油封是PG25×42×10的骨架式油封,它的损坏或年久失效,空气便从油封与主轴轴颈之间的缝隙或从进油口接盘与油泵壳体结合处被吸入油泵,经回油管进入油箱,在油箱中产生大量气泡。
会造成油箱中的油液减少,发动机油底槽中油液增多现象,使农具提升缓慢或不能提升。
齿轮油泵的工作原理

齿轮油泵的工作原理
齿轮油泵是一种常见的润滑系统设备,用于将润滑油输送到机械设备的齿轮系统中,以提供必要的润滑和冷却。
其工作原理如下:
1. 泵的内部结构:齿轮油泵主要由泵体、驱动轴和齿轮组成。
泵体内设有两个齿轮,分别为驱动齿轮和从动齿轮。
驱动齿轮由驱动轴带动旋转,而从动齿轮则通过咬合与驱动齿轮一起转动。
2. 工作原理:当泵体与润滑系统连通后,润滑油从润滑系统进入泵体中。
当驱动轴转动时,驱动齿轮也开始旋转。
由于从动齿轮与驱动齿轮咬合,当驱动齿轮转动时,从动齿轮也被带动一同旋转。
3. 润滑油吸入:当齿轮组转动时,从动齿轮的齿槽会逐渐与泵体内的吸油腔相连。
吸油腔与进油通道相连,从而使润滑油从进油通道被吸入吸油腔。
4. 润滑油排出:同时,从动齿轮的齿槽也会逐渐与与出油通道相连,使润滑油从泵体的出油通道被排出。
5. 循环输送:润滑油被泵送出去后,会进入润滑系统,通过管路输送到需要润滑和冷却的齿轮系统。
在齿轮系统中,润滑油起到了润滑、冷却、减少磨损和摩擦等作用。
总结:齿轮油泵的工作原理是通过齿轮组的咬合和转动,使润
滑油被吸入泵体并排出,从而实现对齿轮系统的润滑和冷却。
这种工作原理确保了齿轮系统的正常运行和延长了机械设备的使用寿命。
齿轮油常见指标分析

齿轮油常见指标分析
1、合适的粘度和黏温性能:齿轮油要求的粘度偏高于大多其他工业润滑油。
润滑油的粘度小,能承受的负荷能力差,尤其在极压条件下,会起不到润滑作用,磨损设备。
2、热氧化稳定性:夏天重载车辆的齿轮箱中,油温可达到150-160℃,油品氧化速度很快,会产生腐蚀性的酸性物质,对齿轮产生腐蚀磨损、烧结。
3、抗磨损及耐载荷性能:抗磨损及耐载荷性能是齿轮油要求较为突出的性能。
如果抗磨、耐载荷性能不好,会直接导致齿尖磨损,齿轮咬合不住,引发设备事故。
4、抗泡性:齿轮油在使用过程中被不断剧烈搅动,生成大量气泡,这些气泡使油泵抽空、供油不连续,生成的泡沫不能很快消失,将影响齿轮咬合处油膜形成,夹带泡沫使实际工作油量减少,影响散热,使设备产生故障。
5、抗乳化性:齿轮传动是机械行业中应用最广泛的动力传动及转向的方式之一,因此与水接触的机会不可避免,齿轮油遇水乳化,不但会破坏金属表面的油膜而产生磨损,而且会使添加剂失效,产生沉积物。
6、抗剪切安定性:齿轮油在润滑齿轮中,受到很大的剪切应力,因此不能使用基础油中有高相对分子质量组分,否则会造成设备运行不稳定、缩短使用寿命。
- 1、下载文档前请自行甄别文档内容的完整性,平台不提供额外的编辑、内容补充、找答案等附加服务。
- 2、"仅部分预览"的文档,不可在线预览部分如存在完整性等问题,可反馈申请退款(可完整预览的文档不适用该条件!)。
- 3、如文档侵犯您的权益,请联系客服反馈,我们会尽快为您处理(人工客服工作时间:9:00-18:30)。
齿轮润滑油泵的润滑状态分析解生泽沈阳职业技术学院汽车分院 ,辽宁 沈阳 110015摘要:由斯特莱贝克曲线可知,在油润滑下,两个相对运动物体表面分为三种润滑状态。
通过计算,齿轮润滑油泵工作时齿面处于混合润滑状态,齿面有磨损产生。
而实际观察可知,齿轮润滑油泵齿面没有磨损,齿面可能处于流体润滑状态。
关键词:摩擦 磨损 润滑 油膜两个物体表面相互接触并相对运动就会产生摩擦,有摩擦就会产生磨损。
磨损会破坏表面质量,降低机械的运动精度,消耗能源,缩短零件的使用寿命。
而润滑则是减少摩擦和磨损最有效的手段。
于是,人们对摩擦现象进行了深入的研究和分析,并取得了丰硕的成果。
1 润滑状态分析在本世纪初,德国科学家斯特莱贝克(Stribeck )根据对滚动轴承和滑动轴承的试验结果,提出了著名的斯特莱贝克曲线[]1,后经人们的补充和完善,如图1所示。
Nv 载荷速度粘度η 承载特性数 ⨯= 图1 斯特莱贝克(Stribeck )曲线图中纵坐标是摩擦系数μ,横坐标是反映承载特性的参量N Vη;η是润滑油的动力粘度,V 是两个摩擦表面对润滑油的综合速度,N 是载荷。
可以看出,根据R h min =λ,可将润滑类型分为流体润滑、混合润滑和边界润滑。
其中(=R R 212221)R +,1R 和2R 是两摩擦表面的相应的粗糙度值。
(1)流体润滑区:R h 3.>,两摩擦表面完全为连续的油膜分开,不直接接触,载荷由油膜承担。
(2)混合润滑区:R h 3≤,摩擦表面的一部分被油膜分开,另有部分微凸体接触,其余被边界膜分开。
载荷由油膜、微凸体和边界膜共同承担。
(3)边界润滑区:0→h ,摩擦表面微凸体接触较多,油膜的润滑作用减少,甚至完全不起作用,载荷几乎完全由微凸体和边界膜共同承担。
(4)干摩擦区:属于边界润滑区左边一小部分,摩擦表面无油膜存在,载荷完全由金属基体或氧化膜承担。
图2 齿轮润滑油泵的工作原理图2 齿轮润滑油泵齿面的润滑状态分析齿轮润滑油泵用于泵送润滑油。
它的公称压力低(一般小于MPa 1),流量大。
为提高齿面的硬度、耐磨性和接触疲劳强度,往往对齿面进行淬火等热处理和磨齿等精加工,最终导致成本增加。
齿面磨损程度取决于其齿面的润滑状态。
如果处于混合或边界润滑区域,两个齿面直接接触,磨损量大,齿面必须热处理以提高硬度和耐磨性;如果处于流体润滑区域,两个齿面被油膜分隔开,不会产生磨损,齿面不必热处理。
其主要工作件由两个互相啮合的齿轮组成,一个主动,一个被动。
当齿轮按图2所示方向旋转时,右侧油腔两轮齿逐渐分离,左侧的轮齿逐渐啮合;油在大气作用下进入右腔,随齿轮旋转带到左腔,经左腔压出。
齿轮属于线接触的高副接触,其力学模型是两个圆柱体的线接触,按弹性流体动压润滑的基本方程计算最小油膜厚度min h 。
下面,以国产RCB —315型润滑油泵(由日本润滑油泵转化)为例进行齿面润滑状态计算,其参数如下:齿数:1221==Z Z , 法面模数:n m =6mm ,螺旋角:β=35°,o b 6.32=β,法面压力角:n α=20°,中心距;a =87.896×10-3m ,齿宽:B =120mm ,精度:8FJ ,齿面粗糙度:==21R R 1.6m μ,材料:45钢,公称压力:p =0.63MPa ,转数:n =970min /r ,油品:N 100工业齿轮油,粘压系数:N m /102.228-⨯=α,粘度:22/109m S N ∙⨯=-η。
计算如下:(1) 传动比 11221===Z Z nn i (2) 综合粗糙度 (=R R212221)R +m μ2624.2=(3) 当量弹性模量 []1'E =)11(211222121E E νν-+-=211211/102651.21m N E ⨯=-ν其中27.021==νν1E =2E =210GPa[]2 (4) 齿轮泵的排量 []3 V =2πZ m B m Z B n t 22)cos (2βπ=r m /108517.434-⨯=(5) 转矩 M =m N pV ∙=67.482π(6) 圆周力 F t =N Z m M Z m M d M n t 48.1107cos 222===β(7) 节点处当量曲率半径[]4 R =m i ia n 32210174.9cos )1(sin -⨯=+βα (8) 对润滑油的卷吸速度[]4 U =s m i na n /1087.1862cos )1(sin 303-⨯=+∙βαπ (9) 单位齿宽上的载荷[]5 βαβcos cos cos n b t B F L W ==10.1m N 310⨯ (10) 无量纲参量[]1 *U =R E U 'η=11100682.8-⨯= ,6'*1086.4/-⨯==RE L W W3*10983.4'⨯==E G α(11) 粘性参量[]1 919.521*23**==-UW G g v (12) 弹性参量[]1 e g =541.021**=-UW (13) (),e v g g []1点落在-R Ⅰ区域内,用Martin 方程计算。
油膜厚度参数 9.4=f h(14) 最小油膜厚m L W URh h f μη7462.0/ min ===(15) 膜厚比 Rh min =λ33298.0<= 由以上结果可以看出,齿面出于混合润滑状态。
一般齿轮传动齿面也都是处于混合润滑状态,这与计算结果是相符合的。
所以,为防止磨损,点蚀,胶合等破坏形式,齿面要热处理以提高硬度和耐磨性。
但实际观察润滑油泵齿面情况并非如此。
92年鞍钢厚板厂引进日本二手轧机,对其润滑油泵进行解剖可知,齿面上刀痕依稀可见,并无磨损痕迹,且齿面为软齿面,硬度为HB200,该泵已运行十年之久。
观察国内生产的润滑油泵齿面情况也是如此。
可见,润滑油泵工作时齿面为连续油膜分开,应为流体润滑,这与计算结果不相符合。
3 对润滑油泵齿面润滑状态探讨出现以上情况是因为工作条件不同。
一般齿轮工作时,润滑油没有压力,只是被齿面间的相对滑动速度产生的卷吸作用带入摩擦表面间。
滑动速度很小,加上齿面载荷作用的阻碍,以及油的粘度等因素,齿面间难以形成连续的油膜,有齿面的直接接触,属于混合润滑状态。
而润滑油泵工作时是浸入油中,润滑条件好。
当油泵工作时,吸油腔的齿轮逐渐退出啮合,使吸油腔的空间加大,压力降低,形成负压,油随齿轮转动进入压油腔。
压油腔的齿轮逐渐进入啮合,空间变小,油的压力升高。
压油腔和吸油腔存在压力差,其值略大于泵的工作压力。
齿轮是高副的线接触,接触区实际是一个狭长的面接触。
在压力差的作用下,少量的压力油经接触区泄回吸油腔,在接触区形成连续的油膜,成为流体润滑状态。
正如静压轴承,在轴转动之前,压力油经轴下面的油孔流出,将轴浮起,使轴与滑动轴承之间形成一个连续的油膜。
轴与轴承之间没有直接接触,不会产生磨损。
4 结论由于工作条件不同,用计算普通齿轮齿面油膜厚度的方法已不能满足计算齿轮润滑油泵齿面的油膜厚度,需要对原有的计算方法加以改进和修订。
参考文献:[1] 汪德涛 。
《润滑技术手册》 机械工业出版社。
1999[2] 张秉荣 章剑青。
《工程力学》 机械工业出版社。
2000[3] 左健民。
《液压与气动传动》 机械工业出版社。
2001[4] 姚玉泉,马先贵,丁津原。
《摩擦磨损润滑密封》东北大学出版社。
1989[5] 温诗铸。
《摩擦学原理》。
清华大学出版社,1990The Analysis of Lubrication Condition on Gear Lubrication Oil PumpXIE Sheng-ze1,ZHOU Chao-mei1, MA Xian-guei2,DING Jin-yuan 2(1.Shenyang College of Auto Industry,Shenyang 110015; 2.Northeast University, Shenyang 110006)Abstract:Stribeck curve divides the lubrication condition of the surface of two opposite movement bodys under oil lubrication into three sections.Through calculating two footh faces Of gear whool lubrication oil pump that are working are in the section of mixed Lubrication and wear can occur.By observing practicing ,wear is not on the tooth Faces of gear whool lubrication oil pump ,and two footh faces may be in section of fluid lubrication .Key words: friction;wear;lubrication;oil films。