3数控车床编程
数控车床编程指令大全
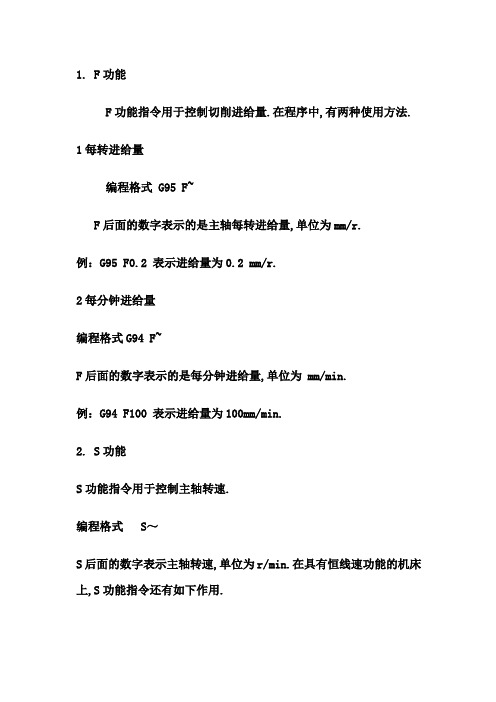
1. F功能F功能指令用于控制切削进给量.在程序中,有两种使用方法. 1每转进给量编程格式 G95 F~F后面的数字表示的是主轴每转进给量,单位为mm/r.例:G95 F0.2 表示进给量为0.2 mm/r.2每分钟进给量编程格式G94 F~F后面的数字表示的是每分钟进给量,单位为 mm/min.例:G94 F100 表示进给量为100mm/min.2. S功能S功能指令用于控制主轴转速.编程格式 S~S后面的数字表示主轴转速,单位为r/min.在具有恒线速功能的机床上,S功能指令还有如下作用.1最高转速限制编程格式 G50 S~S后面的数字表示的是最高转速:r/min.例:G50 S3000 表示最高转速限制为3000r/min.2恒线速控制编程格式 G96 S~S后面的数字表示的是恒定的线速度:m/min.例:G96 S150 表示切削点线速度控制在150 m/min.3恒线速取消编程格式 G97 S~S后面的数字表示恒线速度控制取消后的主轴转速,如S未指定,将保留G96的最终值.例:G97 S3000 表示恒线速控制取消后主轴转速3000 r/min.3. T功能T功能指令用于选择加工所用刀具.编程格式 T~T后面通常有两位数表示所选择的刀具号码.但也有T后面用四位数字,前两位是刀具号,后两位是刀具长度补偿号,又是刀尖圆弧半径补偿号.例:T0303 表示选用3号刀及3号刀具长度补偿值和刀尖圆弧半径补偿值.T0300 表示取消刀具补偿.4. M功能M00:程序暂停,可用NC启动命令CYCLE START使程序继续运行;M01:计划暂停,与M00作用相似,但M01可以用机床“任选停止按钮”选择是否有效;M03:主轴顺时针旋转;M04:主轴逆时针旋转;M05:主轴旋转停止;M08:冷却液开;M09:冷却液关;M30:程序停止,程序复位到起始位置.5. 加工坐标系设置G50编程格式 G50 X~ Z~式中X、Z的值是起刀点相对于加工原点的位置.G50使用方法与G92类似.在数控车床编程时,所有X坐标值均使用直径值,如图所示.例:按图设置加工坐标的程序段如下:G50 X128.7 Z375.1设定加工坐标系6. 快速定位指令G00G00指令命令机床以最快速度运动到下一个目标位置,运动过程中有加速和减速,该指令对运动轨迹没有要求.其指令格式:G00 XU____ ZW____;当用绝对值编程时,X、Z后面的数值是目标位置在工件坐标系的坐标.当用相对值编程时,U、W后面的数值则是现在点与目标点之间的距离与方向.如图所示的定位指令如下:G50 X200.0 Z263.0; 设定工件坐标系G00 X40.0 Z212.0;绝对值指令编程A→C或G00 U-160.0 W-51.0;相对值指令编程A→C因为X轴和Z轴的进给速率不同,因此机床执行快速运动指令时两轴的合成运动轨迹不一定是直线,因此在使用G00指令时,一定要注意避免刀具和工件及夹具发生碰撞.如果忽略这一点,就容易发生碰撞,而快速运动状态下的碰撞就更加危险7. 直线插补指令G01G01指令命令机床刀具以一定的进给速度从当前所在位置沿直线移动到指令给出的目标位置.指令格式:G01 XU____ZW____F ;其中F是切削进给率或进给速度,单位为mm/r或mm/min,取决于该指令前面程序段的设置.使用G01指令时可以采用绝对坐标编程,也可采用相对坐标编程.当采用绝对坐编程时,数控系统在接受G01指令后,刀具将移至坐标值为X、Z的点上;当采用相对坐编程时,刀具移至距当前点的距离为U、W值的点上.如图所示的直线运动指令如下:G01 X40.0 Z20. F0.2; 绝对值指令编程G01 U20.0 W-25.9 F0.2; 相对值指令编程8. 圆弧插补指令G02、G03圆弧插补指令命令刀具在指定平面内按给定的F进给速度作圆弧插补运动,用于加工圆弧轮廓.圆弧插补命令分为顺时针圆弧插补指令G02和逆时针圆弧插补指令G03两种.其指令格式如下:顺时针圆弧插补的指令格式:G02XU____ZW____I____K____F____;G02 XU____ZW___R___ F____;逆时针圆弧插补的指令格式:G03 XU____ZW____ I____K____F____;; G03 XU____ZW___R___ F____;使用圆弧插补指令,可以用绝对坐标编程,也可以用相对坐标编程.绝对坐标编程时,X、Z是圆弧终点坐标值;增量编程时,U、W是终点相对始点的距离.圆心位置的指定可以用R,也可以用I、K,R 为圆弧半径值;I、K为圆心在X轴和Z轴上相对于圆弧起点的坐标增量; F为沿圆弧切线方向的进给率或进给速度.当用半径R来指定圆心位置时,由于在同一半径R的情况下,从圆弧的起点到终点有两种圆弧的可能性,大于180°和小于180°两个圆弧.为区分起见,特规定圆心角α≤180°时,用“+R”表示;α>180°时,用“-R”.注意:R编程只适于非整圆的圆弧插补的情况,不适于整圆加工.例如,图3-13中所示的圆弧从起点到终点为顺时针方向,其走刀指令可编写如下:G02 X50.0 Z30.0 I25.0 F0.3;绝对坐标,直径编程,切削进给率0.3mm/rG02 U20.0 W-20.0 I25.0 F0.3;相对坐标,直径编程,切削进给率0.3mm/rG02 X 50. 0 Z30.0 R25.0 F0.3;绝对坐标,直径编程,切削进给率0.3mm/rG02 U20.0 W-20.0 R25.0 F0.3;相对坐标,直径编程,切削进给率0.3mm/r9. 暂停指令G04G04指令用于暂停进给,其指令格式是:G04 P____或G04 XU____暂停时间的长短可以通过地址XU或P来指定.其中P后面的数字为整数,单位是ms;XU后面的数字为带小数点的数,单位为s.有些机床,XU后面的数字表示刀具或工件空转的圈数.该指令可以使刀具作短时间的无进给光整加工,在车槽、钻镗孔时使用,也可用于拐角轨迹控制.例如,在车削环槽时,若进给结束立即退刀,其环槽外形为螺旋面,用暂停指令G04可以使工件空转几秒钟,即能将环形槽外形光整圆,例如欲空转2.5s时其程序段为: G04 X2.5或G04 U2.5或G04 P2500;G04为非模态指令,只在本程序段中才有效.10. 英制和米制输入指令G20、G21G20表示英制输入,G21表示米制输入.G20和G21是两个可以互相取代的代码.机床出厂前一般设定为G21状态,机床的各项参数均以米制单位设定,所以数控车床一般适用于米制尺寸工件加工,如果一个程序开始用G20指令,则表示程序中相关的一些数据均为英制单位为英寸;如果程序用G21指令,则表示程序中相关的一些数据均为米制单位为mm.在一个程序内,不能同时使用G20或G21指令,且必须在坐标系确定前指定.G20或G21指令断电前后一致,即停电前使用G20或G21指令,在下次后仍有效,除非重新设定.11. 进给速度量纲控制指令G98、G99在数控车削中有两种切削进给模式设置方法,即进给率每转进给模式和进给速度每分钟进给模式.1进给率,单位为mm/r,其指令为:G99;进给率转换指令G01X____Z____F____; F的单位为mm/r2进给速度,单位为mm/min,其指令为:.G98;进给速度转换指令G01X____Z____F____; F的单位为mm/minG98和G99都是模态指令,一旦指定就一直有效,直到指定另一方式为止.车削CNC系统缺省的进给模式是进给率,即每转进给模式,只有在用动力刀具铣削时才采用每分钟进给模式.12. 参考点返回指令G27、G28、G30参考点是CNC机床上的固定点,可以利用参考点返回指令将刀架移动到该点.可以设置最多四个参考点,各参考点的位置利用参数事先设置.接通电源后必须先进行第一参考点返回,否则不能进行其它操作.参考点返回有两种方法:1手动参考点返回.2自动参考点返回.该功能是用于接通电源已进行手动参考点返回后,在程序中需要返回参考点进行换刀时使用的自动参考点返回功能.自动参考点返回时需要用到如下指令:1返回参考点检查G27G27用于检验X轴与Z轴是否正确返回参考点.指令格式为:G27 XU____ ZW____XU、ZW为参考点的坐标.执行G27指令的前提是机床通电后必须手动返回一次参考点.执行该指令时,各轴按指令中给定的坐标值快速定位,且系统内部检查检验参考点的行程开关信号.如果定位结束后检测到开关信号发令正确,则参考点的指示灯亮,说明滑板正确回到了参考点位置;如果检测到的信号不正确,系统报警,说明程序中指令的参考点坐标值不对或机床定位误差过大.2参考点返回指令G28、G30G28 XU ____ ZW ____;第一参考点返回,其中XU、ZW为参考点返回时的中间点,X、Z为绝对坐标,U、W为相对坐标.参考点返回过程如图3-14所示.G30 P2 XU____ ZW____;第二参考点返回,P2可省略G30 P3 XU____ Z W____;第三参考点返回G30 P4 XU____ ZW____;第四参考点返回第二、第三和第四参考点返回中的XU、Z W的含义与G28中的相同.如图3-14所示为刀具返回参考点的过程,刀具从当前位置经过中间点190,50返回参考点,其指令为:G30 X190 Z50;G30 U100 W30;如图3-14中的虚线路径所示,如果参考点返回时不经过中间点,则刀具会与工件发碰撞,引起事故.G功能0快速1直线插补2顺圆3逆圆33螺纹32攻牙循环90外内圆柱面循环92螺纹循环94外内圆锥面循环74端面钻孔循环75外内元切槽循环71外圆初车循环72端面初车循环22局部循环开始80局部循环结束50设工件绝对坐标26XZ回参考点27x回参考点29z回参考点4延时93系统偏置98每分进给99每转进给M功能0暂停2程序结束20循环加工30程序结束关主轴和冷却3正转4反转5停主轴8.9开关冷却10.11工件松紧41.42.43主轴123档78.79尾座进退97程序转移98子程序调用99子程序返回M是主轴的指令开头,S是转速的开头,T是刀具的开头,G就是车削形式的开头.举几个例子,M03是主轴正转,M04主轴反转,M05主轴停止.G00就是快速移动,G01直线插补,G02顺时针圆弧插补,G03逆时针圆弧插补.还有很多不一一列举了太多了,买本书自己看看我感觉比FANUC简单.数控编程指令全套指令常用的2008年03月05日星期三 16:19下面是简单的代码和指令.很实用的哦M 指令和 G 代码M03 主轴正转M03 S1000 主轴以每分钟1000的速度正转M04主轴逆转M05主轴停止M10 M14 .M08 主轴切削液开M11 M15主轴切削液停M25 托盘上升M85工件计数器加一个M19主轴定位M99 循环所以程式G 代码G00快速定位G01主轴直线切削G02主轴顺时针圆壶切削G03主轴逆时针圆壶切削G04 暂停G04 X4 主轴暂停4秒G10 资料预设G28原点复归G28 U0W0 ;U轴和W轴复归G41 刀尖左侧半径补偿G42 刀尖右侧半径补偿G40 取消G97 以转速进给G98 以时间进给G73 循环G80取消循环 G10 00 数据设置模态G11 00 数据设置取消模态G17 16 XY平面选择模态G18 16 ZX平面选择模态G19 16 YZ平面选择模态G20 06 英制模态G21 06 米制模态G22 09 行程检查开关打开模态G23 09 行程检查开关关闭模态G25 08 主轴速度波动检查打开模态G26 08 主轴速度波动检查关闭模态G27 00 参考点返回检查非模态G28 00 参考点返回非模态G31 00 跳步功能非模态G40 07 刀具半径补偿取消模态G41 07 刀具半径左补偿模态G42 07 刀具半径右补偿模态G43 17 刀具半径正补偿模态G44 17 刀具半径负补偿模态G49 17 刀具长度补偿取消模态G52 00 局部坐标系设置非模态G53 00 机床坐标系设置非模态G54 14 第一工件坐标系设置模态G55 14 第二工件坐标系设置模态G59 14 第六工件坐标系设置模态G65 00 宏程序调用模态G66 12 宏程序调用模态模态G67 12 宏程序调用取消模态G73 01 高速深孔钻孔循环非模态G74 01 左旋攻螺纹循环非模态G76 01 精镗循环非模态G80 10 固定循环注销模态G81 10 钻孔循环模态G82 10 钻孔循环模态G83 10 深孔钻孔循环模态G84 10 攻螺纹循环模态G85 10 粗镗循环模态G86 10 镗孔循环模态G87 10 背镗循环模态G89 10 镗孔循环模态G90 01 绝对尺寸模态G91 01 增量尺寸模态G92 01 工件坐标原点设置模态三大数控系统G代码快速通读一、数控车床系统G代码×为本软件中不能用现象表达的指令G功能字含义 FANUC数控系统 SIEMENS数控系统华中数控系统快速进给、定位 G00 G0 G00直线插补 G01 G1 G01圆弧插补CW顺时针 G02 G2 G02圆弧插补CCW逆时针 G03 G3 G03暂停 G04 G04英制输入 G20 G70 G20 ×公制输入 G21 G71 G21回归参考点 G28 G74 G28由参考点回归 G29 G29返回固定点 G75直径编程 -- G23 G36半径编程 -- G22 G37刀具补偿取消 G40 G40 G40左半径补偿 G41 G41 G41右半径补偿 G42 G42 G42设定工件坐标系 G50 G92设置主轴最大的转速 G50 G26上限 G25下限 -- ×选择机床坐标系 G53 G53 G53选择工作坐标系1 G54 G54 G54选择工作坐标系2 G55 G55 G55选择工作坐标系3 G56 G56 G56选择工作坐标系4 G57 G57 G57选择工作坐标系5 G58 G58选择工作坐标系6 G59 G59精加工复合循环 G70 G70内外径粗切复合循环 G71 G71 端面粗切削复合循环 G72 G72 闭环车削复合循环 G73 LCYC95 G73 螺纹切削复合循环 G76 G76外园车削固定循环 G90 G80端面车削固定循环 G94 G81螺纹车削固定循环 G92 LCYC97 G82绝对编程 --- G90 G90相对编程 --- G91 G91每分钟进给速度 G98 G94 G94 ×每转进给速度 G99 G95 G95 ×恒线速度切削 G96 G96 G96 ×恒线速度控制取消 G97 G97 G97 ×二、数控铣床系统G代码×为本软件中不能用现象表达的指令G功能字含义 FANUC数控系统 SIEMENS数控系统华中数控系统快速进给、定位 G00 G0 G00直线插补 G01 G1 G01圆弧插补CW顺时针 G02 G2 G02圆弧插补CCW逆时针 G03 G3 G03暂停 G04 G04选择XY平面 G17 G17 G17选择XZ平面 G18 G18 G18 ×选择YZ平面 G19 G19 G19 ×英制输入 G20 G70 G20 ×公制输入 G21 G71 G21回归参考点 G28 G74 G28由参考点回归 G29 G29返回固定点 G75刀具补偿取消 G40 G40 G40左半径补偿 G41 G41 G41右半径补偿 G42 G42 G42刀具长度补偿+ G43 G43刀具长度补偿- G44 G44刀具长度补偿取消 G49 G49 取消缩放 G50 G50 ×比例缩放 G51 G51 ×机床坐标系选择 G53 G53 G53选择工作坐标系1 G54 G54 G54 选择工作坐标系2 G55 G55 G55 选择工作坐标系3 G56 G56 G56 选择工作坐标系4 G57 G57 G57 选择工作坐标系5 G58 G58 选择工作坐标系6 G59 G59 坐标系旋转 G68 G68 ×取消坐标系旋转 G69 G69 ×高速深孔钻削循环 G73 G73 左螺旋切削循环 G74 G74精镗孔循环 G76 G76取消固定循环 G80 G80中心钻循环 G81 G81反镗孔循环 G82 G82深孔钻削循环 G83 G83右螺旋切削循环 G84 G84镗孔循环 G85 G85镗孔循环 G86 G86反向镗孔循环 G87 G87镗孔循环 G88 G88镗孔循环 G89 G89绝对编程 G90 G90 G90相对编程 G91 G91 G91设定工件坐标系 G92 G92固定循环返回起始点 G98 G98 返回固定循环R点 G99。
04丰展数控车床数控3犀牛编程说明

犀牛编制数控车床程序说明在利用犀牛编写数控车床3程序前应了解车床,特别是三个轴的正负方向,以及分清哪一把刀为粗车刀,哪一把为精车刀。
犀牛程序的安装见视频。
编程步骤准备工作:如图,将栏杆翻转并将顶部移至坐标原点(车形时从顶端开始,以减少栏杆的震动),花形与方料连接圆角处需延伸至最大回转直径(如下图绿色线所示),然后只保留下面右图所示部分,保证所保留部分为一条连贯的曲线。
将图纸保存为dwg或dxf格式。
1、将作好的图导入到犀牛中,然后将所有曲线组合(如下图)。
2、用单轴缩放命令,在X轴方向放缩曲线,注意需点击复制为防止车形时,车刀破坏上图中直线部分的柱料棱角,可以打开控制点后将直线部分向左拖移一定距离。
下图中左侧曲线到绿线的距离为粗车刀的车削量,两条曲线的间距为精车刀的车削量,因此,要注意两车刀车削量的合理分配。
3、右键点击旋转命令,将Z车刀路径绕Y轴旋转90°,然后将旋转后的曲线沿+Y方向移动10mm(此值为两把车刀在Y轴上的距离,为固定值)。
4、为使两把车刀的车削运动起始点与结束点一致,需用线段将两曲线的起终点对齐,并分别组合(如下图)。
5、分别将两条曲线用曲面-直线挤出命令拉伸出曲面。
拉伸后的曲面宽度至少要超出另一条曲线。
6、从两个曲面的交集建立一条曲线(如下图所示),这条曲线在XOY 和YOZ 平面的投影就是两把车刀的车削轨迹。
用下图所示命令检查交集曲线的起点,使其在靠近原点的一端。
检查完毕后把多余的点删去。
若曲线起点不在靠近原点一端,则需要重新计算交集曲线(可通过改变点击拉伸曲面顺序来改变此曲线起始点)7、用修剪命令把交集线右边和上边两部分剪去,完成后如下图:8、选中交集线,点击下图所示命令:RhinoCAM—Toolbars—BrowserRhinoCAM的各种设置如下图:<1>、设置车床及旋转轴:<2>、设置刀具参数:<3>、计算刀具路径<4>、输出路径程序后处理文件选择AxyzGCode ;输出文件格式为NC ,即**.nc此处文件格式改为nc。
数控车床基本编程指令

数控车床基本编程指令
数控车床(Computer Numerical Control Lathe)的基本编程指令通常是用来描述加工轴向、径向、切削速度、进给速度等方面的操作。
下面是一些常见的数控车床基本编程指令:
G代码:用于指定不同的功能和动作。
例如:
G00:快速定位
G01:直线插补
G02:圆弧顺时针插补
G03:圆弧逆时针插补
G04:暂停(延时)
G28:回零点
G71:开启公制单位
G72:开启英制单位
M代码:用于控制机床的辅助功能和动作。
例如:
M03:主轴正转
M04:主轴反转
M05:主轴停止
M08:冷却液开启
M09:冷却液关闭
M30:程序结束
X、Y、Z轴坐标控制:用于控制工件在不同轴向上的移动。
例如:
X10.0:将X轴移动到坐标10.0处
Y5.0:将Y轴移动到坐标5.0处
Z-2.0:将Z轴移动到坐标-2.0处
F代码:用于设定进给速度(切削速度)。
例如:
F100:设定进给速度为每分钟100毫米(或英寸)
S代码:用于设定主轴转速。
例如:
S1000:设定主轴转速为每分钟1000转
T代码:用于选择工具。
例如:
T0101:选择编号为0101的刀具
这些是最基本的数控车床编程指令,实际上还有更多用于高级功能和特定应用的指令。
正确理解和使用这些指令对于确保数控车床操作的准确性和效率至关重要。
数控车床编程实例详解(30个例子)

数控车床编程实例详解(30个例子)1. 基础G00轨迹移动G00指令可以用于快速移动机床上的工具,不做切削。
例如,要将铣刀从(0,0,0)点移动到(100,100,0)可以使用下面的编程:G00 X100 Y100 Z02. 简单的G01直线插补3. 向X正方向设定工件原点在某些情况下,需要在工件上设计的特定原点作为整个程序的起点。
在下面的例子中,我们将工件原点移到X轴上的10毫米位置:G92 X104. G02 G03 模拟圆弧G02和G03指令可以用于沿着一条圆弧轨迹移动工具。
例如,以下代码将插入一个逆时针圆弧:G03 X50 Y50 I25 J05. 床上对刀长度测量刀具长度对刀是数控车床操作的重要步骤。
在这个例子中,我们使用手动设定对刀。
首先,我们将铣刀移动到Z轴处的一个位置,然后将刀具轻轻放置在工件上以测量其长度。
最后,我们将刀具测量值输入机床,以便于适当地调整刀具长度。
6. 坐标旋转在某些情况下,需要在XY平面上绕特定角度旋转工件,以便于确保最佳切削角度。
在这个例子中,我们将工件绕着Z轴旋转45度:G68 X0 Y0 R457. 使用M code 启动或停止旋转工件M03用于启动旋转工作台的主轴,M05用于关闭它。
例如,以下代码段启动了工作台的主轴,并等待它旋转到合适速度,以便于切削。
8. 镜像轨迹在制造工具或零件时,可能需要将一个轮廓沿着特定轴镜像。
例如,以下代码镜像X 轴上的轮廓:G01 X50 Y0G01 X0 Y50G01 X-50 Y0G01 X0 Y-50MHE29. 使用G04指令延迟程序G04指令用于程序内部的延迟。
例如,以下代码让机床停顿1秒钟:G04 P100010. 利用G10指令改变工作坐标系G10指令可以用于更改工作坐标系。
例如,下面的代码段将当前坐标系设定为{X50 Y50 Z0}:11. 使用G17, G18和G19指令绘制园形、X-Y平面和Z-X平面G17G02 X50 Y50 I25 J0G02 X0 Y0 I-25 J0G02 X-50 Y50 I0 J25G02 X0 Y100 I25 J0G02 X50 Y50 I0 J-25G02 X0 Y0 I-25 J0MHE2M30指令可以用于彻底结束程序。
数控车床编程操作【全】

#§1-1 数控入门知识随着科学技术和社会生产和迅速发展,机械产品日趋复杂,对机械产品和质量和生产率的要求越来越高.在航天、造船、军工和计算机等工业中,零件精度高、形状复杂、批量小、经常改动、加工困难,生产效率低、劳动强度大,质量难以保证。
机械加工工艺过程自动化是适应上述发展特点的最重要手段.为了解决上述问题,一种灵活、通用、高精度、高效率的“柔性”自动化生产设备-—-——-数控机床在这种情况下应运而生。
目前数控技术已做逐步普及,数控机床在工业生产中得到了广泛应用,已成为机床自动化的一个重要发展方向.1—1—1数控定义数控即数字控制(Numerical Control),是数字程序控制的简称。
数控车床由数字程序控制车床简称;CNC表示计算机数控车床。
数控机床加工原理是把刀具与工件的运动坐标分成最小的单位量即最小位移量,由数控系统根据工件的要求,向各坐标轴发出指令脉冲,使各坐标移动若干个最小位移量,从而实现刀具与工件的相对运动,以完成零件的加工.数控的实质是通过特定处理方式下的数字信息(不连续变化的数字量)去自动控制机械装置进行动作,它与通过连续变化的模拟量进行的程序控制(即顺序控制),有着截然不同性质.由于数控中的控制信息是数字化信息,而处理这些信息离不开计算机,因此将通过计算机进行控制的技术通称为数控技术,简称数控。
这里所讲的数控,特指用于机床加工的数控(即机床数控)。
1—1-2 机床数控与数控机床机床数控是指通过加工程序编制工作,将其控制指令以数字信号的方式记录在信息介质上,经输入计算机处理后,对机床各种动作的顺序、位移量和速度实现自动控制的一门技术。
数控机床则是一种通过数字信息控制按给定的运动规律,进行自动加工的机电一体化新型加工装备。
§1—2 数控机床的用途分类1—2—1 数控车床的用途数控车床与卧式车床一样,也是用来加工轴类或盘类的回转体零件。
但是由于数控车床是自动完成内外圆柱面、圆锥面、圆弧面、端面、螺纹等工序的切削加工,所以数控车床特别适合加工形状复杂的轴类或盘类零件。
数控车床技能鉴定培训单元3FANUC0i系统数控车床的常用编程代码

图3-2螺纹切削
例3-1:如图3-4所示,切削螺纹编程,螺纹导程为2mm,单线 螺纹。
O0031; T0303; M03 S200; G00 X32 Z5;定义A点 G00 X29.1;下刀到第一次切深 G32 Z-53 F2;切削螺纹 G00 X32;退刀 Z5;退刀 X28.4;下刀到第二次切深 ……;切削螺纹、退刀同第一刀 G00 X150 Z150; M05; M30;
图3-11 圆柱面切削循环应用
例3-4:如图3-12所示,运用锥面切削循环指令编程。
O0034; T0101; G98 G90 X40 Z20 R-5.5 F30; 快进至循环起点
X30; X20; G00 X100 Z160 M05; M30;
图3-12 圆锥面切削循环应用
3.4.1单一固定循环指令 2、端面切削循环指令G94
O0036; T0202; M03 S600; G98 G00 X70 Z40; G94 X20 Z34 R-5 F30;AB-C-D-A
Z30;A-E-F-D-A G00 X100 Z160 M05; M30;
图3-16 斜端面切削循环应用
3.4.1单一固定循环指令 3、螺纹切削循环指令G92
(1)指令格式:G92 X(U)— Z(W)— R— F— ; (2)指令功能:切削圆柱螺纹和锥螺纹。 (3)指令说明:R表示锥螺纹始点与终点在长轴方向的坐标增 量(X轴用半径量),圆柱螺纹切削循环时R为零,可省略; 其它参数同G32。
G73 Pns Qnf UΔu WΔw Ff Ss Tt ;
图3-25 固定形状切削复合循环
O0311;
N010 T0101 M03 S600 G99;
例3-11:如图3-26所示,
数控车床编程与操作案例3

编制如图所示零件的加工程序,材料为45钢,棒料直径为40 mm。
1.刀具设置1号刀:90°正偏刀;2号刀:切槽刀(刀宽4 mm);3号刀:60°外螺纹车刀。
2.工艺路线(1)工件伸出卡盘外85 mm,找正后夹紧。
(2)用90°外圆刀车工件右端面,粗车外圆至Φ38.5×80 mm。
(3)先车出Φ30.5×40 mm圆柱,再车出Φ22.5×20 mm圆柱。
(4)用车圆法车右端圆弧,车圆锥,分别留0.5 mm精车余量。
(5)精车外形轮廓至尺寸。
(6)切退刀槽,并用切槽刀右刀尖倒出M38×3 mm螺纹左端C2倒角。
(7)换螺纹刀车双头螺纹。
(8)切断工件。
3.相关计算(1)计算双头螺纹M38×3(P1.5)的底径:d=D-2×0.65p=(38-2×0.65×1.5)mm=36.05 mm(2)确定背吃刀量分布:1 mm、0.5 mm、0.45 mm。
4.加工程序程序一:N10 G90 G94分进给,绝对值编程N20 S600 M03主轴正转,转速600 r/minN30 T1D1 M08换1号外圆刀,切削液开N40 G00 X45 Z0快速进刀N50 G01 X0 F80车端面N60 G00 X38.5 Z2快速退刀N70 G01 Z-80 F80粗车外圆N80 G00 X40 Z2快速退刀N90 G00 X36快速进刀N100 G01 Z-40粗车外圆N110 G00 X40 Z2快速退刀N111 G00 X33快速进刀N100 G01 Z-40粗车外圆N110 G00 X40 Z2快速退刀N120 G00 X30.5快速进刀N130 G01 Z-40粗车外圆N140 G00 X40 Z2快速退刀N150 G00 X26快速进刀N160 G01 Z-20粗车外圆N170 G00 X30 Z2快速退刀N180 G00 X22.5快速进刀N190 G01 Z-20粗车外圆N200 G00 X30 Z2快速退刀N210 G00 X0快速进刀N220 G03 X26 Z-11 R=13 F100车R13圆弧N230 G00 Z0.5快速退刀N240 G00 X0快速进刀N250 G03 X23 Z-11 CR=11.5车R11.5圆弧(留0.5加工余量)N260 G00 X25.5 Z-18快速进刀N270 G01 X25.5 Z-20N280 X30.5 Z-40车圆锥N290 G00 X100 Z100快退至换刀点N295 S1200 M03主轴变速,转速1 200 r/minN300 G00 X2 Z2快速进刀N310 G01 X0 Z0 F100进刀至(0,0)点N320 G03 X22 Z-11 CR=11精车R11圆弧N330 G01 Z-20精车22外圆N190 X25精车台阶N200 X30 Z-40精车圆锥N210 X34精车台阶N220 X37.8 Z-42倒角N230 Z-60精车M38螺纹外圆至37.8N240 X37.9975N250 Z-80以公差中间值精车38外圆N260 G00 X100 Z100快退至换刀点N270 T2D1 换2号切槽刀N280 S300 M03主轴变速,转速300 r/minN290 G00 X40 Z-68快速进刀至(X40,Z-68)N300 G01 X30.2 F30切槽至30.2N310 G00 X40快速退刀N320 G00 Z-64向右移动4 mmN330 G01 X30 F30切槽至30N340 Z-68向左横拖4 mm,消除切刀接缝线N350 G00 X40快速退刀N360 G00 Z-61快速进刀N370 G01 X34 Z-64 F30用槽刀右刀尖倒螺纹左端C2倒角N380 G00 X100快退至换刀点N390 Z100N400 T3D1换3号螺纹刀N410 S400 M03主轴变速,转速400 r/minN420 G00 X37 Z-34快速进刀N430 L10调子程序车第一条螺纹N440 G00 X36.5快速进刀N450 L10调子程序车第一条螺纹N460 G00 X36.05快速进刀N470 L10调子程序车第一条螺纹N500 G00 X37 Z-35.5 与第一条螺纹的起刀点错开一个螺距N510 L10调子程序车第二条螺纹N520 G00 X36.5 快速进刀N530 L10调子程序车第二条螺纹N540 G00 X36.05快速进刀N550 L10调子程序车第二条螺纹N580 G00 X100 Z100 M09快退至换刀点,切削液关N650 M05主轴停转N660 M02主程序结束L10 车螺纹子程序N800 G91 G33 Z-28 K3车削螺纹,导入量导出量均为4 mmN810 G00 X10快速退刀N820 G00 Z28返回N830 G90换回绝对坐标编程N840 M17子程序结束程序二(用LCYC93切槽循环、LCYC95毛坯轮廓循环、LCYC97螺纹切削循环指令编程):N10 G90 G95采用绝对值编程,转进给N20 S600 M03主轴正转,转速600 r/minN40 T1D1 M08换1号外圆刀,切削液开N50 G00 X45 Z0快速进刀N60 G01 X0 F0.2车端面N70 G00 X38.5 Z2快速退刀N80 G01 Z-80 F0.2车外圆至38.5N90 G00 X45 Z5快速退刀_CNAME=“L11”轮廓循环子程序定义R105=1加工方式:纵向、外部、粗加工R106=0.25精加工余量0.25 mm(半径值)R108=1.5粗加工背吃刀量1.5 mm(半径值)R109=0粗加工切入角0°R110=2粗加工横向退刀量2 mm(半径值)R111=0.2粗加工进给率0.2 mm/rR112=0.1 精加工进给率0.1 mm/rN100 LCYC95调用轮廓循环N110 S1200 M03 F0.1主轴变速精加工,进给率0.1 mm/r N120 L11调用L11子程序进行轮廓精加工N130 G00 X100 Z100退回换刀点N140 T2D1换2号切刀N150 S300 M03 F0.1主轴变速切槽N160 G00 Z-64快速进刀N165 X40快速进刀R100=38切槽起始点直径38 mm(X向)R101=-64 切槽起始点Z坐标-64(Z向)R105=5切槽方式:纵向、外部、从右往左切R106=0.1精加工余量0.1 mm(半径值)R107=4切槽刀宽4 mmR108=1.5每次切入深度1.5 mm(半径值)R114=8 槽宽8 mmR115=4槽深4 mm(半径值)R116=0切槽斜角0°R117=0槽沿倒角为0°R118=0槽底倒角0°R119=0槽底停留时间0°LCYC93调用切槽循环N170 G00 X40快速退刀N180 G00 Z-61快速进刀N190 G01 X34 Z-64 F0.1用槽刀右刀尖倒螺纹左端C2倒角N200 G00 X100N210 Z100快退至换刀点N220 T3D1 换3号螺纹刀N230 S500 M03主轴转速500 r/minR100=38螺纹起点直径38 mmR101=-40螺纹轴向起点Z坐标-40R102=38螺纹终点直径38 mmR103=-60螺纹轴向终点Z坐标-60R104=3螺纹导程3 mmR105=1螺纹加工类型,外螺纹R106=0.1螺纹精加工余量0.1 mm(半径值)R109=4空刀导入量4 mmR110=3空刀导出量3 mmR111=0.975螺纹牙深度0.975 mm(半径值)R112=0螺纹起始点偏移R113=8螺纹粗切削次数8次R114=2螺纹线数N240 LCYC97调用螺纹切削循环N250 G00 X100 Z100 M09退回换刀点,切削液关N310 M05主轴停转N320 M02主程序结束L11子程序N10 G01 X0 Z0N20 G03 X22 Z-11CR=11N30 G01 Z-20N40 X25N50 X30 Z-40N60 X37.8 Z-40 CHF=2 N70 Z-68N80 X37.9975N90 Z-80N100 RET。
机床数控技术第3章数控加工程序的编制
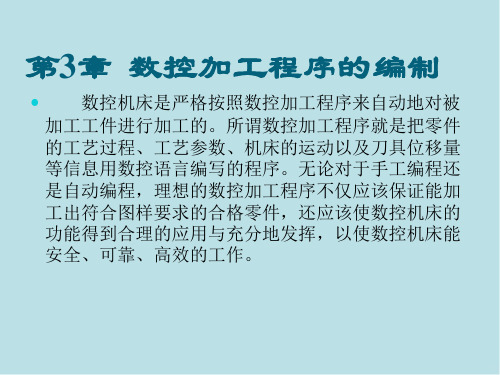
6. 程序校验和首件试切
程序送入数控系统后,通常需要经过试运行和首 件试切两步检查后,才能进行正式加工。通过试运行, 校对检查程序,也可利用数控机床的空运行功能进行 程序检验,检查机床的动作和运动轨迹的正确性。对 带有刀具轨迹动态模拟显示功能的数控机床可进行数 控模拟加工,以检查刀具轨迹是否正确;通过首件试 切可以检查其加工工艺及有关切削参数设定得是否合 理,加工精度能否满足零件图要求,加工工效如何, 以便进一步改进,直到加工出满意的零件为止。
1—脚踏开关 2—主轴卡盘 3—主轴箱 4—机床防护门 5—数控装置 6—对刀仪 7—刀具8—编程与操作面板 9—回转刀架 10—尾座 11—床身
3.2 数控车削加工程序编制
数控车床主要用来加工轴类零件的内外圆柱面、 圆锥面、螺纹表面、成形回转体表面等。对于盘类零 件可进行钻、扩、铰、镗孔等加工。数控车床还可以 完成车端面、切槽等加工。
3. 程序名
FANUC数控系统要求每个程序有一个程序名,
程序名由字母O开头和4位数字组成。如O0001、 O1000、O9999等
3.2.3 基本编程指令
1. 快速定位指令G00
格式:G00 X(U)_ Z(W)_;
说明:
(1) G00指令使刀具在点位控制方式下从当前点以快移速度 向目标点移动,G00可以简写成G0。绝对坐标X、Z和其增 量坐标U、W可以混编。不运动的坐标可以省略。
3.2.1 数控车床的编程特点
(1)在一个程序段中,可以用绝对坐标编程,也可用 增量坐标编程或二者混合编程。
(2)由于被加工零件的径向尺寸在图样上和在测量时 都以直径值表示,所以直径方向用绝对坐标(X)编程时 以直径值表示,用增量坐标(U)编程时以径向实际位移 量的2倍值表示,并附上方向符号。
数控车床编程教案
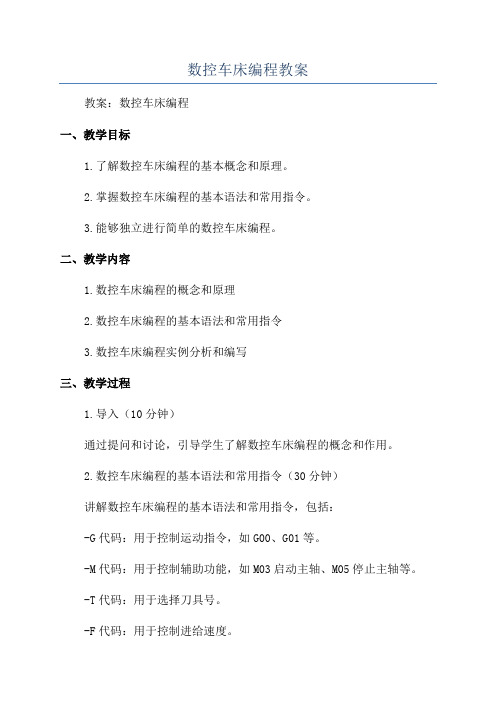
数控车床编程教案教案:数控车床编程一、教学目标1.了解数控车床编程的基本概念和原理。
2.掌握数控车床编程的基本语法和常用指令。
3.能够独立进行简单的数控车床编程。
二、教学内容1.数控车床编程的概念和原理2.数控车床编程的基本语法和常用指令3.数控车床编程实例分析和编写三、教学过程1.导入(10分钟)通过提问和讨论,引导学生了解数控车床编程的概念和作用。
2.数控车床编程的基本语法和常用指令(30分钟)讲解数控车床编程的基本语法和常用指令,包括:-G代码:用于控制运动指令,如G00、G01等。
-M代码:用于控制辅助功能,如M03启动主轴、M05停止主轴等。
-T代码:用于选择刀具号。
-F代码:用于控制进给速度。
-S代码:用于控制主轴转速。
3.数控车床编程实例分析和编写(40分钟)通过实际案例分析和讲解,引导学生学会分析和编写数控车床程序。
实例包括:-面铣:通过分析面铣过程,学习如何编写相应的数控车床程序。
-镗孔:通过分析镗孔过程,学习如何编写相应的数控车床程序。
-外圆车削:通过分析外圆车削过程,学习如何编写相应的数控车床程序。
四、教学总结(10分钟)总结数控车床编程的要点和关键步骤,强调学生应掌握的基本知识和技能。
五、教学反馈通过课堂练习和作业,检查学生对数控车床编程的理解和掌握程度。
六、教学资源1.教学课件和案例分析材料。
2.计算机和数控车床编程软件。
七、教学评价通过对学生的课堂表现、练习和作业的评价,对教学效果进行评估和反思,并做出相应改进。
八、教学延伸1.组织学生进行实际操作,编写和调试数控车床程序。
2.进一步拓展学生对数控车床编程的理论知识和实际应用的学习。
3.组织学生参观数控车床加工现场,了解实际生产中数控车床编程的应用。
以上是关于数控车床编程的教案,希望能够帮助学生掌握数控车床编程的基本知识和技能,为日后的实际应用打下坚实的基础。
数控车床编程基础教案

图17圆弧插补b
A.绝对坐标编程
半径法:G02 R23. F30;
圆心法:G02 I23. K0 F30;
B.相对坐标编程
半径法:G02 R23. F30;
圆心法:G02 I23. K0 F30;
图18圆弧插补C
A.绝对坐标编程
半径法:G03 R30 F30;
圆心法:G03 I0 K-30 F30;
为了确定机床的运动方向和移动的距离,要在机床上建立一个坐标系,这个坐标系就是标准坐标系,也叫机床坐标系,机床坐标系采用右手笛卡尔坐标系;
图2右手笛卡尔坐标系
图3机床坐标系的建立
2.机床坐标轴方向和方位的确定
1Z轴的规定
平行于机床主轴轴线的坐标轴为Z轴,如数控铣床主轴带动刀具旋转,与主轴平行的坐标即为Z坐标,如图4所示;
相对坐标编程为:G01-25.9 F;
作业
课后习题
教学后记
绝对编程与增量编程的方法和区别、单位设置、进给量设置、主轴转速设置、是编程的前题条件,基本指令G00、G01是最常用的两条指令,要注意各自的适用场合;
第二章 数控车床编程基础教案
课题
第三节圆弧插补指令
课时
2
教学目标
1.圆弧顺逆的判断前置刀架与后置刀架
图6卧式数控铣床的机床坐标系
3Y轴的确定
Y轴方向可根据已确定的Z轴、X轴方向,用右手直角笛卡儿坐标系来确定;
4回转轴
绕X轴回转的坐标轴为A,绕Y轴回转的坐标轴为B,绕Z轴回转的坐标轴为C,方向采用右手螺旋定则;
5附加坐标轴
如果机床除有X、Y、Z主要的直线运动坐标外,还有平行于它们的坐标运动,则应分别命名为U、V、W;
适用范围:适用于加工形状复杂的如具有非圆曲线、列表曲线和曲面组成的零件编程,以及各类柔性制造系统FMS和集成制造系统CIMS,应用广泛;
数控车床编程步骤和用法【技巧】

数控机床编程课,是数控专业的一门综合性较强的专业课,它要求学生不仅会读懂程序,还要会手工编写简单零件的加工程序。
编程的入门较难,入门以后就显得简单一点。
下面就先给大家介绍一下数控车床编程步骤和用法。
数控车床编程方法与步骤:数控机床编程课,是数控专业的一门综合性较强的专业课,它要求学生不仅会读懂程序,还要会手工编写简单零件的加工程序。
编程的入门较难,入门以后就显得简单一点。
现把编程方法总结如下:一、分析零件图样、确定加工工艺过程分析零件的材料、形状、尺寸、精度及毛坯形状和热处理要求等,确定正确的加工方法、定位夹紧以及加工顺序、所用刀具和切削用量等,即制定加工工艺。
这一个环节是数控编程的一个重要环节。
其主要目的是确定数控加工的工艺路线、切削用量以及工件的定位、夹紧等。
首先是数控加工工艺的划分,如加工端面、车外圆、切槽、切断等等;其次是刀具的选择,应该合理选择加工刀具;然后是工序顺序的安排,要求在确定工艺过程中,要做到加工路线短,进给、换刀次数少,充分发挥数控机床的功能,使加工安全、可靠,效率高。
走刀路线是指在加工过程中,刀具刀位点相对于工件的运动轨迹和方向,它不仅包括了工步内容,还反映了工步顺序。
在安排可以一刀或多刀进行的精加工工序时,其零件的最终轮廓应由最后一刀连续加工而成。
这时,加工刀具的进退刀位置要考虑妥当,尽量不要在连续的轮廓中安排切人和切出或换刀及停顿,以免因切削力突然变化而造成弹性变形,致使光滑连接轮廓上产生表面划伤、形状突变或滞留刀痕等疵病。
二、数值计算根据零件的尺寸要求、加工路线及设定的坐标系,进行运动轨迹坐标值的计算。
对于由圆弧和直线组成的简单零件,只要求计算零件轮廓上各几何元素的交点或切点的坐标,得出各几何元素的起点、终点、圆弧圆心的坐标值。
如果数控系统无刀具补偿功能,还应该计算刀具刀位点的运动轨迹。
对于由非圆曲线组成的复杂零件,由于数控机床通常只具有直线和平面圆弧插补功能,因而只能采用支线段或圆弧段逼近的方法进行加工,这时就要计算逼近线段和被加工曲线的交点(即节点)的坐标值。
数控车床编程与操作教学课件三德国SIEMENS-802SC系统数控车床基础编程

第一章 基础编程
《数控车床编程与操作》
第一节 基本指令
知识链接 一、准备功能
准备功能主要用来指令机床或数控系统的工作方式。与 FANUC 系统一样SIEMENS-802S/C系统的准备功能也用地址 符G和后面数字表示。具体G指令代码如图:
第一章 基础编程
《数控车床编程与操作》
第一节 基本指令
知识链接 一、准备功能
《数控车床编程与操作》
第二节 圆弧、倒角、倒圆编程指令
知识链接 二、 SIEMENS-802S/C系统的的倒角、倒圆编程
2、倒圆角指令RND=: 表示直线轮廓之间、圆弧轮廓之间以及直线轮廓和圆弧
轮廓之间切入一圆弧,圆弧与轮廓进行切线过渡,如: N10 G01 X~Z~RND=~
第一章 基础编程
《数控车床编程与操作》
第一章 基础编程
《数控车床编程与操作》
第一章 基础编程
目录
第一节 基本指令 第二节 圆弧、倒角、倒圆编程指令 第三节 循环编程指令 第四节 刀具补偿功能 第五节 螺纹编程指令及应用 第六节 R参数变量编程及应用 第七节 编程实例
第一章 基础编程
《数控车床编程与操作》
第一节 基本指令
任务描述
1、能够解释G94、G95的含义。 2、能够阐述G96、G97的含义、格式、注意事项并进行应用举例。 3、能够说出SIEMENS系统刀具号加刀补号的刀具调用编程指令格式。 4、能够说出SIEMENS系统加工程序由哪三部分组成。 5、能够列举坐标系偏移指令并以G158指令进行应用举例。
第一章 基础编程
《数控车床编程与操作》
第五节 螺纹编程指令及应用
知识链接
二、螺纹切削循环指令LCYC97
2、纵向螺纹和横向螺纹的判别 系统根据R100~R103螺纹起终点参数自动判别纵向螺纹或 横向螺纹。如果圆锥角小于或等于45°,则按纵向螺纹加工,否 则按横向螺纹加工。调用循环之前必须保证刀具无碰撞地到 达编程确定的位置(螺纹起始点+空刀导入量)。
数控车床如何自动编程

数控车床的自动编程实现数控车床是一种高度自动化的加工设备,广泛应用于各种机械加工行业。
其自动编程功能不仅能提高生产效率,还可以减少人为因素对加工精度的影响,实现精准加工。
下面将介绍数控车床如何实现自动编程的原理和方法。
1. 数控车床自动编程的基本原理数控车床的自动编程是通过输入加工零件的几何图形和加工参数,由数控系统自动生成加工程序,并控制车床自动运行完成加工过程。
其基本原理包括以下几个步骤:(1) 几何图形输入操作人员通过数控系统的编程界面,输入加工零件的几何图形数据,通常以CAD软件生成的DXF或DWG文件格式进行输入。
(2) 加工参数设置根据加工要求,设置加工工艺参数,如刀具直径、切削速度、进给速度等参数,以确保加工质量。
(3) 自动编程数控系统根据输入的几何图形数据和加工参数,自动生成加工程序,包括刀具路径、进给速度、切削速度等信息。
(4) 车床控制数控系统通过控制车床的各轴运动,实现自动生成的加工程序的执行,完成加工过程。
2. 数控车床自动编程的方法数控车床的自动编程可以通过以下几种方法实现:(1) 手动编程操作人员根据加工要求,手动编写加工程序,包括刀具路径、运动速度等信息,再通过数控系统进行验证和执行。
(2) 图形对话框式编程操作人员通过数控系统提供的图形对话框界面,直观地设置加工参数和刀具路径,由系统自动生成加工程序。
(3) CAM软件辅助编程利用CAM软件,将CAD设计的零件图形自动转换为数控车床可执行的加工程序,提高编程效率和准确性。
(4) 刀具路径优化通过优化刀具路径和运动轨迹,减少加工时间和刀具磨损,提高加工效率和加工质量。
3. 数控车床自动编程的应用数控车床的自动编程不仅广泛应用于零部件加工,还可用于复杂曲面加工、多轴联动加工等领域。
其应用优势包括:•自动编程准确度高,能够实现复杂零件的精确加工;•编程效率高,节约人力和时间成本;•可实现加工过程的数字化监控和控制,确保加工质量。
第3章数控车床编程
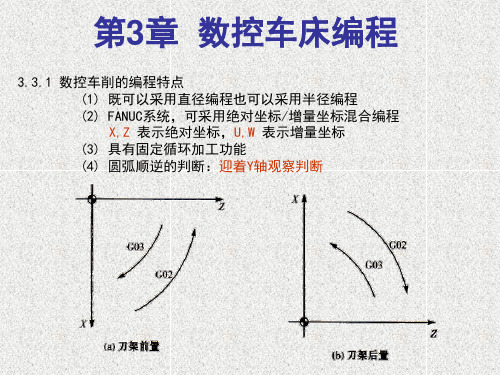
把一系列连续加工动作,用一个循环指令完成
如: 切入 — 切削 — 退刀 — 返回
1. 圆柱面(圆锥面)切削固定循环(G90) (用于轴类零件)
(1) 圆柱面切削
G90 X(U)_ Z(W)_ F_
(2)圆锥面切削循环:G90 X(U)_Z(W)_ R_ F_;
【例3-5】加工图示零件。主轴转速1000 r/m,进给速度200 mm/min,试 利用圆柱面切削单一循环指令编写其粗、精加工程序
图3-24平端面切削循环的轨迹 图3-25 斜端面切削循环的轨迹
例3-7 试用平端面切削循环G94指令编写图3-24所示工件的加工程序,毛 坯为φ50mm的棒料,只加工φ20mm外圆至要求尺寸。
• O0007; •
N10 T0101; • N20 M03 S600; • N30 G00 X52.0 Z2.0; • N40 G94 X20.0 Z-2.0 F100 • N50 Z-4.0; • N60 Z-6.0; • N70 Z-7.5; • N80 Z-8.0 F50; • N90 G00 X100.0 Z100.0; • N100 M30;
例3-8 试用斜端面切削循环G94指令编写图3-25所示工件的加工程序,毛 坯为φ50mm的棒料,只加工锥面至要求尺寸。
• O0006; • N10 T0101; • N20 M03 S600; • N30 G00 X53.0 22.0; • N40 G94 X20 .0 Z5.0 R-5 .5 F100; • N50 Z3.0; • N60 Z1.0; • N70 Z-1.0; • N80 Z-3.0; • N90 Z-4.5; • N100 Z-5.0 F50; • N110 G00 X100.0 Z100.0; • N120 M30;
第三章 数控车床编程
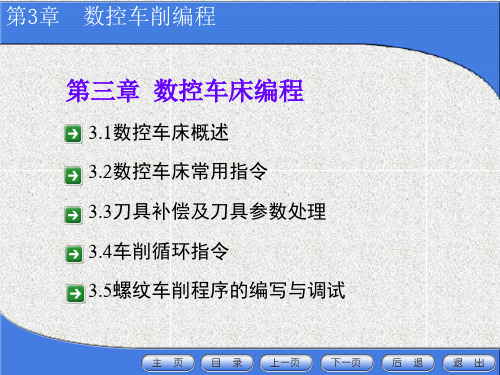
第3章 数控车削编程
2.任意角度倒角(略)
直线进给程序段尾部加上C__
C的数值是虚拟拐角
点距倒角始点或终点
间的距离,如图:
L1 o L2
a
例:G01 X50 C10
X100 Z-100
b
第3章 数控车削编程
3.倒圆角 编程格式: G01 Z(W) b R±r 圆弧倒角情况如图所示 编程格式: G01 X(U) b R±r 圆弧倒角情况如图所示
例:G99 F0.2 表示
进给量为0.2 mm/r
第3章 数控车削编程
(2)每分进给量(单位:mm/min) 编程格式:G98 F ; 该指令组合是用来设定主轴每分钟刀具的进给量,如图所示。F指令 范围为1~15000.0000(mm/min)。
例:G98 F100 表示
进给量为100mm/min
G02/G03 参数说明
第3章 数控车削编程
4) 当已知圆弧终点坐标和半径时,可以选取半径编程的方式插补圆弧,R为 圆弧半径,当圆心角小于等于180度时R为正;大于180度时R为负。 5)当I、K和R在同一程序段出现时,R优先,I、K无效。 6)当程序段中省略X、Z时,表示起点与终点重合,若在程序段中指定了I、 K,即可进行整圆编程。
2) 相对编程 N10 G00 X40 Z110; N20 G03 U80 W-40 I0 K-40 F0.1;(R40) N30 G02 U-32 W-32 I0 K-20;(R20)
第3章 数控车削编程
作业1: 如图所示,编写下图零件精加工程序(分别采用前置刀架坐 标系和后置刀架坐标系)
第3章 数控车削编程
例如:欲停留1.5s时,则程序段为: G04 X1.5 或 G04 U1.5 或 G04 P1500
数控车床编程基础

FANUC公司目前生产的CNC装置有:F0、F10、F11、F12、
F15、F16、F18。F00、F100、110、120、150系列是在F0、
10、11、12、15的基础上加了MMC功能,即CNC、PMC、MMC三
位一体的CNC。
2. SIEMENS数控系统
SIEMENS数控系统是德国西门子公司开发研制的,
一个零件的轮廓可能由许多不同的几何要素所组成,各
几何要素之间的连接点称为基点。基点坐标是编程中重要数
据,可以直接作为其运动轨迹的起点和终点。
上一页 下一页 返回
第6章 数组
6.1 一维数组 6.2 二维数组 6.3 字符数组 6.4 数组程序举例
6.1 一维数组
6.1.1一维数组的定义方式
3.1 数控车床程序编制概述
3.1.3 数控系统主要功能
数控系统可以通过硬件和软件的结合,实现许多功能,
其中包括以下功能:
⑴ 准备功能。准备功能也称G功能,用来指挥机床动作
方式。包括基本移动、程序暂停、平面选择、坐标设定、刀
具补偿、基准点返回、固定循环、公英制转换等。
⑵ 插补功能。CNC装置通过软件插补,其中数据采样插
言编程。
上一页 下一页 返回
3.1 数控车床程序编制概述
② CAD/CAM计算机辅助编程
利用CAD/CAM计算机辅助编程是以零件CAD模型为基础的
一种加工工艺规划及数控编程为一体的自动编程方法。
CAD/CAM软件采用人机交互方式,进行零件几何建模,对车床
刀具进行定义和选择,确定刀具相对于零件的运动方式、切
6.1.3一维数组的初始化
给数组赋值的方法除了用赋值语句对数组元素逐个赋值外, 还可采用初始化赋值和动态赋值的方法。数组初始化赋值是 指在数组定义时给数组元素赋予初值。数组初始化是在编译 阶段进行的。这样可以减少运行时间,提高效率。
数控车床编程实例详解(30个例子)
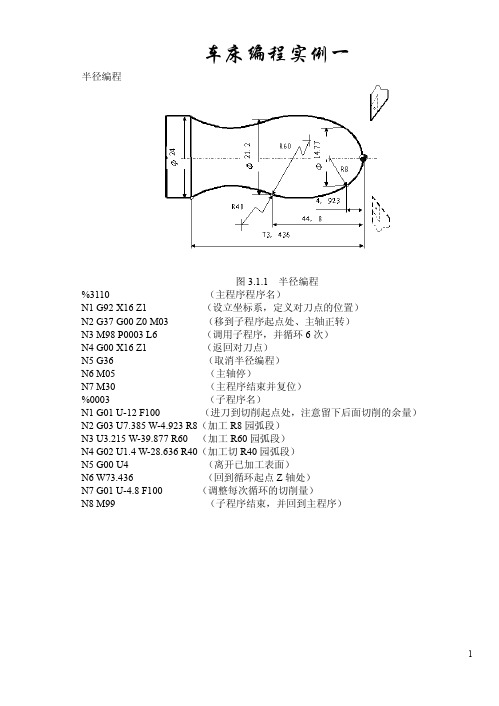
半径编程图3.1.1 半径编程%3110 (主程序程序名)N1 G92 X16 Z1 (设立坐标系,定义对刀点的位置)N2 G37 G00 Z0 M03 (移到子程序起点处、主轴正转)N3 M98 P0003 L6 (调用子程序,并循环6次)N4 G00 X16 Z1 (返回对刀点)N5 G36 (取消半径编程)N6 M05 (主轴停)N7 M30 (主程序结束并复位)%0003 (子程序名)N1 G01 U-12 F100 (进刀到切削起点处,注意留下后面切削的余量)N2 G03 U7.385 W-4.923 R8(加工R8园弧段)N3 U3.215 W-39.877 R60 (加工R60园弧段)N4 G02 U1.4 W-28.636 R40(加工切R40园弧段)N5 G00 U4 (离开已加工表面)N6 W73.436 (回到循环起点Z轴处)N7 G01 U-4.8 F100 (调整每次循环的切削量)N8 M99 (子程序结束,并回到主程序)直线插补指令编程图3.3.5 G01编程实例%3305N1 G92 X100 Z10 (设立坐标系,定义对刀点的位置)N2 G00 X16 Z2 M03 (移到倒角延长线,Z轴2mm处)N3 G01 U10 W-5 F300 (倒3×45°角)N4 Z-48 (加工Φ26外圆)N5 U34 W-10 (切第一段锥)N6 U20 Z-73 (切第二段锥)N7 X90 (退刀)N8 G00 X100 Z10 (回对刀点)N9 M05 (主轴停)N10 M30 (主程序结束并复位)车床编程实例三圆弧插补指令编程%3308N1 G92 X40 Z5 (设立坐标系,定义对刀点的位置)N2 M03 S400 (主轴以400r/min旋转)N3 G00 X0 (到达工件中心)N4 G01 Z0 F60 (工进接触工件毛坯)N5 G03 U24 W-24 R15 (加工R15圆弧段)N6 G02 X26 Z-31 R5 (加工R5圆弧段)N7 G01 Z-40 (加工Φ26外圆)N8 X40 Z5 (回对刀点)N9 M30 (主轴停、主程序结束并复位图3.3.8 G02/G03编程实例倒角指令编程图3.3.10.1 倒角编程实例%3310N10 G92 X70 Z10 (设立坐标系,定义对刀点的位置)N20 G00 U-70 W-10 (从编程规划起点,移到工件前端面中心处)N30 G01 U26 C3 F100 (倒3×45°直角)N40 W-22 R3 (倒R3圆角)N50 U39 W-14 C3 (倒边长为3等腰直角)N60 W-34 (加工Φ65外圆)N70 G00 U5 W80 (回到编程规划起点)N80 M30 (主轴停、主程序结束并复位)车床编程实例五倒角指令编程%3310N10 G92 X70 Z10 (设立坐标系,定义对刀点的位置)N20 G00 X0 Z4 (到工件中心)N30 G01 W-4 F100 (工进接触工件)N40 X26 C3 (倒3×45°的直角)N50 Z-21 (加工Φ26外圆)N60 G02 U30 W-15 R15 RL=3(加工R15圆弧,并倒边长为4的直角)N70 G01 Z-70 (加工Φ56外圆)N80 G00 U10 (退刀,离开工件)N90 X70 Z10 (返回程序起点位置)M30 (主轴停、主程序结束并复位)图3.3.10.2 倒角编程实例圆柱螺纹编程螺纹导程为1.5mm,δ=1.5mm,δ '=1mm ,每次吃刀量(直径值)分别为0.8mm、0.6 mm 、0.4mm、0.16mm图3.3.12 螺纹编程实例%3312N1 G92 X50 Z120 (设立坐标系,定义对刀点的位置)N2 M03 S300 (主轴以300r/min旋转)N3 G00 X29.2 Z101.5 (到螺纹起点,升速段1.5mm,吃刀深0.8mm)N4 G32 Z19 F1.5 (切削螺纹到螺纹切削终点,降速段1mm)N5 G00 X40 (X轴方向快退)N6 Z101.5 (Z轴方向快退到螺纹起点处)N7 X28.6 (X轴方向快进到螺纹起点处,吃刀深0.6mm)N8 G32 Z19 F1.5 (切削螺纹到螺纹切削终点)N9 G00 X40 (X轴方向快退)N10 Z101.5 (Z轴方向快退到螺纹起点处)N11 X28.2 (X轴方向快进到螺纹起点处,吃刀深0.4mm)N12 G32 Z19 F1.5 (切削螺纹到螺纹切削终点)N13 G00 X40 (X轴方向快退)N14 Z101.5 (Z轴方向快退到螺纹起点处)N15 U-11.96 (X轴方向快进到螺纹起点处,吃刀深0.16mm)N16 G32 W-82.5 F1.5 (切削螺纹到螺纹切削终点)N17 G00 X40 (X轴方向快退)N18 X50 Z120 (回对刀点)N19 M05 (主轴停)N20 M30 (主程序结束并复位)恒线速度功能编程图3.3.14 恒线速度编程实例%3314N1 G92 X40 Z5 (设立坐标系,定义对刀点的位置)N2 M03 S400 (主轴以400r/min旋转)N3 G96 S80 (恒线速度有效,线速度为80m/min)N4 G00 X0 (刀到中心,转速升高,直到主轴到最大限速)N5 G01 Z0 F60 (工进接触工件)N6 G03 U24 W-24 R15 (加工R15圆弧段)N7 G02 X26 Z-31 R5 (加工R5圆弧段)N8 G01 Z-40 (加工Φ26外圆)N9 X40 Z5 (回对刀点)N10 G97 S300 (取消恒线速度功能,设定主轴按300r/min旋转)N11 M30 (主轴停、主程序结束并复位)车床编程实例八%3317M03 S400 (主轴以400r/min旋转)G91 G80 X-10 Z-33 I-5.5 F100(加工第一次循环,吃刀深3mm)X-13 Z-33 I-5.5(加工第二次循环,吃刀深3mm)X-16 Z-33 I-5.5(加工第三次循环,吃刀深3mm)M30 (主轴停、主程序结束并复位)图3.3.17 G80切削循环编程实例G81指令编程(点画线代表毛坯)图3.3.20 G81切削循环编程实例%3320N1 G54 G90 G00 X60 Z45 M03 (选定坐标系,主轴正转,到循环起点)N2 G81 X25 Z31.5 K-3.5 F100 (加工第一次循环,吃刀深2mm)N3 X25 Z29.5 K-3.5 (每次吃刀均为2mm,)N4 X25 Z27.5 K-3.5 (每次切削起点位,距工件外圆面5mm,故K值为-3.5)N5 X25 Z25.5 K-3.5 (加工第四次循环,吃刀深2mm)N6 M05 (主轴停)N7 M30 (主程序结束并复位车床编程实例十G82指令编程(毛坯外形已加工完成)%3323N1 G55 G00 X35 Z104(选定坐标系G55,到循环起点)N2 M03 S300 (主轴以300r/min正转)N3 G82 X29.2 Z18.5 C2 P180 F3(第一次循环切螺纹,切深0.8mm)N4 X28.6 Z18.5 C2 P180 F3(第二次循环切螺纹,切深0.4mm)N5 X28.2 Z18.5 C2 P180 F3(第三次循环切螺纹,切深0.4mm)N6 X28.04 Z18.5 C2 P180 F3(第四次循环切螺纹,切深0.16mm)N7 M30 (主轴停、主程序结束并复位)图3.3.23 G82切削循环编程实例车床编程实例十一外径粗加工复合循环编制图3.3.27所示零件的加工程序:要求循环起始点在A(46,3),切削深度为1.5mm(半径量)。
- 1、下载文档前请自行甄别文档内容的完整性,平台不提供额外的编辑、内容补充、找答案等附加服务。
- 2、"仅部分预览"的文档,不可在线预览部分如存在完整性等问题,可反馈申请退款(可完整预览的文档不适用该条件!)。
- 3、如文档侵犯您的权益,请联系客服反馈,我们会尽快为您处理(人工客服工作时间:9:00-18:30)。
2.直线插补指令(G01)
直线插补指令用于直线或斜线运动。 可使数控车床沿x轴、z轴方向执行单轴运 动,也可以沿x、z平面内任意斜率的直线 运动。
输入格式:
G01 X(U) Z(W) F ;
3.圆弧插补指令(G02 G03)
输入格式: G02 X Z I K F ; 或 G02 X Z R F ; G03 X Z I K F ; 或 G03 X Z R F ; (1)用增量坐标U、W也可以; (2)C轴不能执行圆弧插补指令。
3-4是数控车床及车铣中心的M指令说明。
下面介绍几个特殊M代码的使用方 法。 M03:主轴或旋转刀具顺时针旋转 (CW); M04:主轴或旋转刀具逆时针旋转 (CCW); M05:主轴或旋转刀具停止旋转;
3.2.4 进给功能指令
1.每转进给量指令(G99)、每分钟 进给量指令(G98) 指定进给功能的指令方法有如下两种。 (1)每转进给量(G99)(如图3-23 所示)。 输入格式:G99 (F ); F :主轴每转进给量(进给速度 mm/r)。
(2)主轴箱 (3)主轴伺服电机 (4)夹紧装置 (5)往复拖板 (6)刀架 (7)控制面板
3.数控车床的加工特点
数控车床加工具有如下特点。 (1)加工生产效率高 (2)减轻劳动强度、改善劳动条件 (3)对零件加工的适应性强、灵活性好 (4)加工精度高、质量稳定 (5)有利于生产管理
3.1.2 数控车床坐标系统 1.机床坐标系
输入格式:G50 X Z ,其中X Z 为 刀具出发点的坐标(如图3-19所示)。
3.2.2.4 自动回原点指令(G28) 自动回原点指令使刀具自动返回机械 原点或经某一中间点回机械原点(如图320和图3-21所示)。 输入格式: G28 X(U) Z(W) T00; (1)X(U) 和Z(W) 为中间点的坐标。 (2)T00(刀具复位)指令必须写在 G28指令的同一程序段或该程序段之前。
(3)数控车削中心:在数控车床的
基础上增加其他的附加坐标轴。
按结构和用途数控车床主要可分为数 控卧式车床、数控立式车床和数控专用车 床(如数控凸轮车床、数控曲轴车床、数 控丝杠车床等)。
2.数控车床的基本构成
(1)数控系统:数控车床的数控系 统是由CNC装置、输入输出设备、可编程 控制器(PLC)、主轴驱动装置和进给驱 动装置以及位置测量系统等几部分组成。
3.2 FANUC系统数控车床程序的编制
3.2.1 程序结构
1.程序段的构成
N_G_X(U)_Z(W)_F_M_S_T_;
其中,N_:程序段顺序号; G_:准备; X(U)_:x轴移动指令; Z(W)_:z轴移动; F_:进给功能; M_:辅助功能; S_:主轴功能; T_:工具功能。
2.程序段的要求
⑦ 在G74~G76、G90~G92固定循环 指令中不用刀尖半径补偿。 ⑧ 在手动输入中不用刀尖半径补偿。 ⑨ 在加工比刀尖半径小的圆弧内侧时, 产生报警。 ⑩ 在阶梯锥面连接处退刀时指定G40, 在指定G40的程序段里使用反映斜面方向 的I、K地址来防止工件被过切。
3.2.6 固定循环切削功能指令 3.2.6.1 单一形状的固定循环 1.外圆车削循环G90
第3章 数控车床编程
3.1 数控车床编程基础
3.2 FANUC系统数控车床程序的编制
3.1 数控车床编程基础
3.1.1 数控车床概述 1.数控车床的分类
数控车床品种繁多,按数控系统的功 能和机械构成可分为简易数控车床(经济 型数控车床)、多功能数控车床和数控车 削中心。
(1)简易数控车床(经济型数控车 床):是低档次数控车床,一般是用单板 机或单片机进行控制,机械部分是在普通 车床的基础上改进设计的。 (2)多功能数控车床:也称全功能 型数控车床,由专门的数控系统控制,具 备数控车床的各种结构特点。
3.端面切削循环G94
G94是用于一些短、面大的工件加工 的固定循环指令。
(1)车大端面循环切削指令格式: G94 X(U) Z(W) F ; (2)车大锥面切削循环指令格式: G94 X(U) Z(W) K F ;
3.2.6.2 多重固定循环
1.圆粗车循环G71
G71指令将工件切削至精加工之前的
度没有指定界限;
② 接入电源时,系统默认G99模式 (每转进给量)。
3.2.5 刀具功能指令
1.T功能
T功能也称为刀具功能,表示选择刀 具和刀补号。
输入格式: T□□□□
2.刀具半径补偿功能(G40、
G41、G42)
(1)刀尖半径和假想刀尖的概念
① 刀尖半径
② 假想刀尖
(2)刀尖半径补偿模式的设
(1)G96(控制线速度恒定指令): 当工件直径变化时主轴每分钟转数也随之 变化,这样就可保证切削速度不变,从而 提高了切削质量。 (2)主轴转速连续变化,M38设定主 轴在低速范围变化(粗加工),M39设定 主轴在高速范围变化(精加工)。
2.辅助功能指令(M指令)
M指令设定各种辅助动作及其状态,表
2.端面粗车循环G72
G72指令与G71指令类似,不同 之处就是刀具路径是按径向方向循环 的,输入格式同G71指令,刀具循环 路径如图3-44所示。
G72 Pns Qnf Uu Ww Dd (F S T ); 其中:d——粗加工每次切深(半径 值)。其他参数与G71相同。
3.固定形状粗车循环G73
3.2.2.1 插补功能
1.定位G00
定位指令命令刀具以点位控制方式从 刀具所在点快速移动到目标位置,无运动
轨迹要求,不需特别规定进给速度。
输入格式:
G00 X(U) Z(W) ;
(1)“X(U) Z(W) ”目标点的坐标
(下文同);
(2)X(U)坐标按直径值输入;
(3)“;”表示一个程序段的结束。
3.2.3 主轴及辅助功能指令
1.主轴功能指令(S指令)和主轴转 速控制指令(G96、G97、G50) 主轴功能指令(S指令)是设定主轴 转速的指令。 (1)主轴最高转速的设定(G50)。 (G50) S ;中S 为主轴最高转速。
(2)直接设定主轴转速指令(G97), 主轴速度用转速设定,单位为r/min。 (G97) (G97) 定功能。 S (M38或M39); :取消主轴线速度,恒
(2)每分钟进给量(mm/min),如
图3-27所示。
(G98) F ; 其中F 为每分钟刀具
进给量,指令范围为1~15000(mm/min)。
(3)螺纹切削进给速度(mm/r), 如图3-28所示。
F 指定螺纹的螺距,指令范围为
0.0001~500.0000(mm)。
① 每转进给量切螺纹时,快速进给速
定(G40、G41、G42指令)
① G40(解除刀具半径补偿)
② G41(左偏刀具半径补偿)
③ G42(右偏刀具半径补偿)
(3)刀尖半径补偿注意事项
① G41、G42指令不能与圆弧切削指
令写在同一个程序段,可以与G00和G01 指令写在同一个程序段内,在这个程序段 的下一程序段始点位置,与程序中刀具路 径垂直的方向线过刀尖圆心。
3.2.2.2 螺纹切削指令(G32)
G32指令能够切削圆柱螺纹、圆锥螺
纹、端面螺纹(涡形螺纹)
输入格式:
G32 X(U) Z(W) F ;“F ”为螺纹的
螺距。
3.2.2.3 工件坐标系设定指令(G50)
工件坐标系设定指令以程序原点为工 件坐标系的中心(原点),指定刀具出发 点的坐标值(如图3-19所示)。图3-19 G50设定工作坐标系
(2)每分钟进给量(G98) 。
输入格式:G98 (F );
F :(G04)
(G99)G04 U(P) ;指令暂停进刀 的主轴回转数。 (G98)G04 U(P) ;指令暂停进刀 的时间。
3.进给功能指令(F指令)
进给功能指令指定刀具的进给速度, 有3种形式。 (1)每转进给量(mm/r),如图326所示。 (G99) F ; F :主轴每转刀具进给量小数点输入 指令范围为0.0001~500.0000(mm/r)。
G73指令与G71、G72指令功能相同,
只是刀具路径是按工件精加工轮廓进行循
环的,如图3-45所示。
输入格式: G73 Pns Qnf II KK UU WW Dd (F S T ); 其中:I——x轴方向的退出距离 (半径值)和方向; k—z轴方向的退出距离和方向; d—粗切次数。其他参数与G71相同。
几种等效的表示方法:
N0012 G00 M08 X0012.340 X5000 X5.0
↓ ↓ ↓ ↓ ↓ ↓
N12
G0
M8 X12.34
X5.
X5.
3.2.2 准备功能指令
准备功能也称为G功能(或称G代 码),它是用来指令机床动作方式的功能。 准备功能是用地址G及其后面的数字来指 令机床动作的。如用G00来指令运动坐标 快速定位。表3-2为FANUC-0TD系统的准 备功能G代码表。
S (M38或M39):设定主轴转速 (r/min),指令范围为0~9999。
(3)设定主轴线速度恒定指令
(G96),主轴速度用线速度(m/min)
值输入,并且主轴线速度恒定。
(G96)
(G96)
S
(M38或M39);
:主轴转速恒定。
S (M38或M39):设定主轴线速度,
即切削速度(m/min)。
尺寸,精加工前的形状及粗加工的刀具路 径由系统根据精加工尺寸自动设定。
输入格式: G71 Pns Qnf Uu Ww Dd (F S T ); 其中:ns—精加工程序第一个程序段的序 号; nf—精加工程序最后一个程序段的序号; U—x轴方向精加工留量(直径值); W—z轴方向精加工留量; d—精加工每次切深。