金属表面热处理渗碳工艺对比
金属材料热处理方法有几种
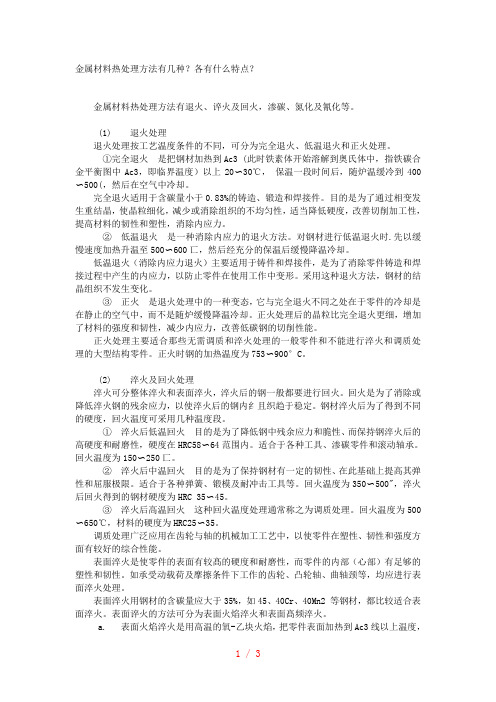
金属材料热处理方法有几种?各有什么特点?金属材料热处理方法有退火、谇火及回火,渗碳、氮化及氰化等。
(1) 退火处理退火处理按工艺温度条件的不同,可分为完全退火、低温退火和正火处理。
①完全退火是把钢材加热到Ac3 (此时铁素体开始溶解到奥氏体中,指铁碳合金平衡图中Ac3,即临界温度)以上20〜30℃,保温一段时间后,随炉温缓冷到400〜500(,然后在空气中冷却。
完全退火适用于含碳量小于0.83%的铸造、锻造和焊接件。
目的是为了通过相变发生重结晶,使晶粒细化,减少或消除组织的不均匀性,适当降低硬度,改善切削加工性,提高材料的韧性和塑性,消除内应力。
② 低温退火是一种消除内应力的退火方法。
对钢材进行低温退火时.先以缓慢速度加热升温至500〜600匸,然后经充分的保温后缓慢降温冷却。
低温退火(消除内应力退火)主要适用于铸件和焊接件,是为了消除零件铸造和焊接过程中产生的内应力,以防止零件在使用工作中变形。
采用这种退火方法,钢材的结晶组织不发生变化。
③ 正火是退火处理中的一种变态,它与完全退火不同之处在于零件的冷却是在静止的空气中,而不是随炉缓慢降温冷却。
正火处理后的晶粒比完全退火更细,增加了材料的强度和韧性,减少内应力,改善低碳钢的切削性能。
正火处理主要适合那些无需调质和淬火处理的一般零件和不能进行淬火和调质处理的大型结构零件。
正火时钢的加热温度为753〜900°C。
(2) 淬火及回火处理淬火可分整体淬火和表面淬火,淬火后的钢一般都要进行回火。
回火是为了消除或降低淬火钢的残余应力,以使淬火后的钢内纟且织趋于稳定。
钢材淬火后为了得到不同的硬度,回火温度可采用几种温度段。
① 淬火后低温回火目的是为了降低钢中残余应力和脆性、而保持钢淬火后的高硬度和耐磨性,硬度在HRC58〜64范围内。
适合于各种工具、渗碳零件和滚动轴承。
回火温度为150〜250匸。
② 淬火后中温回火目的是为了保持钢材有一定的韧性、在此基础上提高其弹性和屈服极限。
各种渗碳方法比较

A:主要反应式:2 NaCN + O2= 2 NaCNO(1)
NaCN + CO2= NaCNO + CO(2)
高温:4 NaCNO = 2 NaCNO + Na2CO3+ CO +2 N(3)
Na2CO3+ C→2CO + Na2O(5)
C、处理温度越高,处理时间越长,渗碳层厚度越大。
液体渗碳法(liquid carburizing)
1、将钢料浸入以氰化钠(NaCN)为主成分的溶融盐浴中,NaCN分解出C和N渗入钢料表层。因为同时渗碳及氰化,亦称为渗碳氮化(Carbonitriding)。
A:主要反应式:C + CO2= 2CO(CO2少许)(1)木炭表面:C + O2= CO2(2)零件表面:yFe+2CO→yFe〔C〕+CO2(3)〔C〕稱為初生碳或活性碳(nascent Carbon)
B:固態反應甚慢。加入促進劑:BaCO3,Na2CO3,LiCO3,SrCO3可促進反應。
BaCO3+ C→2CO + BaO(4)
2、处理温度约以700℃为界,此温度以下以氮化为主,渗碳为辅,700℃以上则渗碳为主,氮化为辅。
3、滲碳劑主成分:NaCN,添加NaCl、NaCO3、BaCl2(减轻NaCN氧化、挥发、劣化,BaCl2促进渗碳)
4、处理的零件200-500℃预热处理:A:减少温度降低和热应变B:蒸发附着水分,防止爆炸。
C、真空渗碳是通过渗碳时间与扩散时间配合来控制表面碳量和渗碳深度。
D、真空渗碳优点:(1)渗碳层表面碳量和渗碳深度控制简单、准确(2)渗碳效果均匀(3)可缩短作业时间(4)渗碳后零件扔保持辉面状态
金属热处理

四、渗金属 指以金属原子渗入钢的表面层的过程。它是使 钢的表面层合金化,以使工件表面具有某些合金钢、 特殊钢的特性,如耐热、耐磨、抗氧化、耐腐蚀等。 生产中常用的有渗铝、渗铬、渗硼、渗硅等。
表面淬火
将钢件的表面通过快速加热到临界温度以上, 但热量还未来得及传到心部之前迅速冷却,这样就 可以把表面层被淬在马氏体组织,而心部没有发生 相变,这就实现了表面淬硬而心部不变的目的。适 用于中碳钢。
热处理工艺曲线示意图
热处理可以提高零件的强度、硬度、 韧性、弹性。热处理是改善原材料或毛 坯的工艺性能、保证产品质量、延长使 用寿命、挖掘材料潜力不可缺少的工艺 方法。铁碳合金状态图是确定热处理工 艺的重要依据。
铁碳合金状态图铁碳合金状态图.doc
金属热处理是机械制造中的重要工艺之 一,与其它加工工艺相比,热处理一般不 改变工件的形状和整体的化学成分,而是 通过改变工件内部的显微组织,或改变工 件表面的化学成分,赋予或改善工件的使 用性能。其特点是改善工件的内在质量, 而这一般不是肉眼所能看到的。 金属热处理工艺大体可分为整体热处理、 表面热处理、局部热处理和化学热处理等。
七:固溶处理: 指将合金加热到高温单相区恒温保持, 使过剩相充分溶解到固溶体中后快速冷却, 以得到过饱和固溶体的热处理工艺。 固溶处理的目的 主要是改善钢和合金的塑性和韧性,为 沉淀硬化处理作好准备等。
八、沉淀硬化(析出强化) 指金属在过饱和固溶体中溶质原子偏聚区 和(或)由之脱溶出微粒弥散分布于基体中 而导致硬化的一种热处理工艺。如奥氏体沉 淀不锈钢在固溶处理后或经冷加工后,在 400~500℃或700~800℃进行沉淀硬化处理, 可获得很高的强度。
二、正火 指将钢材或钢件加热到Ac3 或Acm(钢的上临界 点温度)以上30~50℃,保持适当时间后,在静止 的空气中冷却的热处理的工艺。 正火的目的 主要是提高低碳钢的力学性能,改善切削加工性, 细化晶粒,消除组织缺陷,为后道热处理作好组织 准备等。 正火主要用于 1、取代完全退火 2、用于普通结构件的最终热处理 3、用于过共析钢,以减少或消除网状二次渗碳 体,为球化退火做好准备
表面化学热处理技术

化学热处理渗碳:为了获得高硬度、高耐磨的表面及强韧的心部,渗碳后必须进行淬火加低温回火处理。
按渗碳介质可分为:气体渗碳、液体渗碳、固体渗碳。
渗氮:①渗氮层具有高硬度、高耐磨性;②渗氮层比热容打,在钢件表面形成压应力层可显著提高耐疲劳性能,渗氮层的耐疲劳性优于渗碳层;③渗氮层表面有化学稳定性高的ε相,能显著提高耐腐蚀性。
渗氮能形成性能优越的渗氮层,但由于工艺时间太长,使得生产率太低,成本高,应尽量少采用。
渗氮一般用在强烈磨损、耐疲劳性要求非常高的零件,有的场合是除要求机械性能外还要求耐腐蚀的零件。
碳氮共渗(俗称“氰化”):按工艺温度分:低温碳氮共渗(520-580℃),工艺温度低,共渗过程是以氮原子为主、碳原子为辅的渗入过程,俗称“软氮化”;中温碳氮共渗(780-880℃);高温碳氮共渗(880-930℃)。
优点:①与渗碳相比处理温度低,渗后可直接淬火,工艺简单,晶粒不易长大,变形裂倾向小,能源消耗少,共渗层的疲劳性和抗回火稳定性好;②与渗氮相比,生产周期大大缩短,对材料适用广。
氮碳共渗:氮碳共渗起源于西德,是在液体渗氮基础上发展起来的。
早期氮碳共渗是在含氰化物的盐浴中进行的。
由于处理温度低,一般在500-600℃,过程以渗氮为主,渗碳为辅,所以又称为“软氮化”。
氮碳共渗工艺的优点如下:①氮碳共渗有优良的性能:渗层硬度高,碳钢氮碳共渗处理后渗层硬度可达HV570-680;渗氮钢、高速钢、模具钢共渗后硬度可达HV850-1200;脆性低,有优良的耐磨性、耐疲劳性、抗咬合性和耐腐蚀性。
②工艺温度低,且不淬火,工件变形小。
③处理时间短,经济性好。
④设备简单,工艺易掌握。
存在问题是:渗层浅,承受重载荷零件不宜采用。
渗硼:渗硼是一种有效地表面硬化工艺。
将工件置于能产生活性硼的介质中,经过加热、保温,使硼原子渗入工件表面形成硼化物层的过程称为渗硼。
金属零件渗硼后,表面形成的硼化物(FeB、Fe2B、TiB2、ZrB2、VB2、CrB2)及碳化硼等化合物的硬度极高,热稳定性。
钢的渗碳和碳氮共渗、淬火、回火工艺
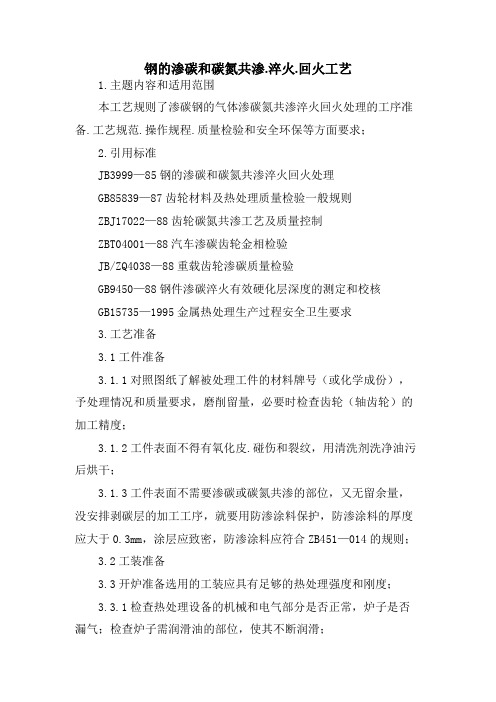
钢的渗碳和碳氮共渗.淬火.回火工艺1.主题内容和适用范围本工艺规则了渗碳钢的气体渗碳氮共渗淬火回火处理的工序准备.工艺规范.操作规程.质量检验和安全环保等方面要求;2.引用标准JB3999—85钢的渗碳和碳氮共渗淬火回火处理GB85839—87齿轮材料及热处理质量检验一般规则ZBJ17022—88齿轮碳氮共渗工艺及质量控制ZBT04001—88汽车渗碳齿轮金相检验JB/ZQ4038—88重载齿轮渗碳质量检验GB9450—88钢件渗碳淬火有效硬化层深度的测定和校核GB15735—1995金属热处理生产过程安全卫生要求3.工艺准备3.1工件准备3.1.1对照图纸了解被处理工件的材料牌号(或化学成份),予处理情况和质量要求,磨削留量,必要时检查齿轮(轴齿轮)的加工精度;3.1.2工件表面不得有氧化皮.碰伤和裂纹,用清洗剂洗净油污后烘干;3.1.3工件表面不需要渗碳或碳氮共渗的部位,又无留余量,没安排剥碳层的加工工序,就要用防渗涂料保护,防渗涂料的厚度应大于0.3mm,涂层应致密,防渗涂料应符合ZB451—014的规则;3.2工装准备3.3开炉准备选用的工装应具有足够的热处理强度和刚度;3.3.1检查热处理设备的机械和电气部分是否正常,炉子是否漏气;检查炉子需润滑油的部位,使其不断润滑;3.3.2检查测温仪表,热电隅是否正常,要定期进行校验;3.3.3定期清理气体渗碳炉炉罐中的碳黑和灰烬;3.4工件的表卡和试样3.4.1根据工件的形状和要求,选用适当的吊具和夹具;3.4.2工件间要有5~10mm的间隙;3.4.3应随炉放臵与装炉工件材质和予处理相同和符合GB8539—87“齿轮材料及热处理质量检验的一般规则”规则的样式,并放臵在有代表性的位臵,以备炉前操作抽样检查;4.渗碳和碳氮共渗淬火回火处理的工艺规范和操作规程4.1渗碳.碳氮共渗处理4.1.1装炉4.1.1.1工件装炉前应把炉温升到渗碳或共渗温度,连续生产时可干上一炉出炉后立即装炉;4.1.1.2工件应装在炉子的有效加热区内,加热区的炉温不得超过±15℃;4.1.1.3每炉装载量不大于设备的装载量;4.1.2气体渗碳工艺规范和操作规程4.1.2.1气体渗碳工艺规范参照图1,低碳合金渗碳钢的渗碳温度取上限;4.1.2.2排气期排气期的渗剂滴入量,参照表1,炉子到温后的排气时间的长短取决于排气程度,应取气进行分析,当CO2和O2的含量低于0.5%时,即可关闭试样孔,转入强渗期;无气体分析仪时,可观察废气火苗的颜色和状态,当火苗呈杏黄色,上升无力时,排气基本结束;一般地排气时间为1~1.5小时;4.1.2.3强渗期,关闭试样孔,点燃排出的废气;检查炉盖及通风机轴处是否漏气;调整煤油.异丙醇的滴入量,滴量多少取决于设备大小,装炉工件表面积的大小及炉子密封的情况,表1的滴量供选择时参考;强渗期炉气成份应控制在表2规则的范围内;有条件应采用红外线CO2碳位自控仪或露点仪控制炉气或用奥氏体分析仪对炉气进行分析,作为调正滴量的依据;强渗期的炉压控制在100~300pa;废气燃烧的火苗高度控制在200~250㎜的长度;根据工件有效硬化层要求和渗速经验,约达到1/2~2/3渗层深度时,抽验第一根试样,根据第一个试样的渗层确定第二个试样的时间,当有效硬化层深度达到或接近工件的有效硬化深度时,即可进入扩散期;4.1.2.4扩散期:扩散期的煤油.异丙醇滴量约为强渗期的0.5倍,为了保证炉压,并同时加滴甲醇,扩散期的时间与工件要求的有效硬化层深度有关,有效硬化层深度愈深,扩散时间要求愈长一些,与工件的碳势(试样的碳势)有关,碳势高要求扩散时间长一些,还与试样渗层深度有关,为了保证工件表面0.85~1.0%的碳浓度和合理的过滤层,扩散时间约为1~3小时;4.1.2.5降温期:抽验的第三个试样,如果网状碳化物≥5级为作正火处理,920℃出炉空冷,对20CrMnMo17Cr2Ni20CrNi2Mo当工件室冷到300-400℃时要放到回火炉中炉冷,防止在表面和次层在空冷时产生马氏体,形成表面裂纹;对于17CrNi2Mo.20Cr2NiMo等Cr.Ni渗碳钢即使碳化物不超级也要出炉空冷,空冷的炉温度为860~880℃;对于碳化物不超级的20CrMnTi.20CrMnMo~840℃,保渗碳齿轮,随炉冷到830温0.5~1H后直接淬火;4.1.3气体碳氮共渗工艺规范和操作规程;4.1.3.1气体碳氮共渗操作规程;4.1.3.2采用煤油加氨氧的气体碳氮共渗工艺曲线4.1.3.3共渗过程其炉气成分应符合下表规则4.2.1工件渗碳后直接淬火;对本质细晶粒钢工件渗碳后可采用直接淬火的方法,以获得所需要的表层和心部硬度以及有效硬化层深度,如20CrMo.20CrMnMo,以及含硼和稀土的合金钢渗碳件;直接淬火一般在炉中降温到830~850℃,均温0.5~1H出炉后淬火工件渗碳后直接淬火另一个条件是渗层金相组织网状碳化物≤4级;工件要求渗层深,炉中碳势又高的情况,容易造成碳化物超级,而对于模数≤5的20CrMnTi.20CrMnMo齿轮,渗碳深度1.2~1.3㎜(含磨量)碳化物不易超级,可以直接淬火,模数大于5的齿轮视渗层的金相组织中网状碳化物的级别而定,如果网状碳化物小于4级可以直接淬火;5级以上则要高温正火,消除网状碳化物或降低网状碳化物级别;4.2.2工件渗碳后空冷后再淬火,按方法有以下几种原因:a.工件渗碳后需要进行机械加工,如制碳层;b.容易发生过热的碳钢和非细晶粒合金钢件,以及某些不宜直接淬火的工件(如需要在压床上淬的齿轮);c.渗层组织如出现网状碳化物超级对于a.b两种情况,炉冷到850~860℃空冷,但对20CrMnMo渗件要求在400℃以下缓冷,否则易再次表层出现马氏体组织形成裂纹,对于C种情况,要求在900~930℃出炉直接空冷;4.2.312CrNi3.12Cr2Ni4.17CrNi2Mo.20CrNi4.20Cr2Ni4.20Cr2Ni4MoA.20Cr2Ni4WA等高强合金渗碳件,渗碳炉冷到920℃出炉空冷(用于制作大模数齿轮),400以下缓冷,并增加一次至二次650~680℃,5~6H的高温回火;这种高温回火称为催化或促变处理,它不仅能改善机械加工性能,更主要它是获得良好淬火组织的条件和保证;必须严格执行;4.2.4碳氮共渗的工件一般都从共渗温度或低于共渗温度出炉直接淬火;4.2.5经过渗碳淬火或碳氮共渗淬的工件,通常采用180℃±10℃的低温回火;4.2.5.1碳氮共渗齿轮回火的温度为180℃±10℃,回火时间3H;4.2.5.2模数1~3的齿轴渗碳淬火后温度200~210℃,时间3H,模数1~3的齿轮渗碳淬火后的回温度220℃±10℃,时间3H4.2.5.3模数3~5的齿轴.齿轮渗碳淬火后进行二次回火;第一次回火温度230℃,时间4H;第二次齿轴的回火温度230℃,回火时间3H;4.2.5.4模数≥6的齿轮.齿轴,渗碳后直接淬火的工件,需要进行三次回火;第一次回火温度230℃,回火时间3H;第二次回火,齿轴的回火温度230℃,时间3H,齿轮的回火温度240℃,时间3H;第三次回火,齿轴的回火温度220℃,时间3H,齿轮的回火温度240℃,时间3H;4.2.5.5模数≥6的齿轮齿轴渗碳后空冷,后加热淬火;进行二次回火;第一次回火温度230℃,时间4H;第二次回火,齿轴的回火温度220℃,时间4H,齿轮的回火温度240℃,时间4H;4.2.5.6前一次回火后,工件空冷到室温或≤50℃,才能进行下一次回火;4.2.5.7工件回火必须放在回火炉的有效加热区内(渗碳淬火的齿轮部分需量出回火炉底部300㎜);4.3渗碳和碳氮共渗淬火回火件的最后处理;4.3.1清理:进行喷砂,以清除赤面的油污和氧化模;4.3.2校直和矫正:用偏摆仪检查齿轴的变形,当超过允许变形时,应对其校直和矫正;随后进行去应力回火;条件允许(淬火工件量少时)应在淬火后马上进行校直,然后再回火;5.质量检验5.1外观:不得有裂纹和碰伤5.2表面硬度5.2.1硬度检验方法,按GB23083《金属洛氏硬试验法》或其他硬度试验法进行;5.2.2表面硬度的偏差范围,表面硬度不得超过下表规则:5.3.1有效硬化层检验方法,按GB《钢的渗碳硬化层有效硬化层深度的测定和校验》中的规则执行;5.3.2有效硬化层深度偏差不得超过下表规则;根据零件的要求,按有关标准进行检定;5.5变形:零件的变形应符合技术要求;6.安全与环保6.1操作者要穿戴好必须的劳动保护用品;6.2执行所用设备的安全操作规程;6.3气体渗碳或碳氮共渗出炉淬火时,同时淬火的工件量大时,应先检查油温,当油温>100℃时,应先降油温后淬火,以防止油槽着火;着火时需用灭火器,石棉被灭火,严禁用水灭火;6.4要防止渗碳炉滴注器渗漏,以免引起炉盖着火,烧毁电机或造成渗剂失火;6.5其它方面按GB15735—1995,金属热处理生产过程安全卫生要求;。
渗碳
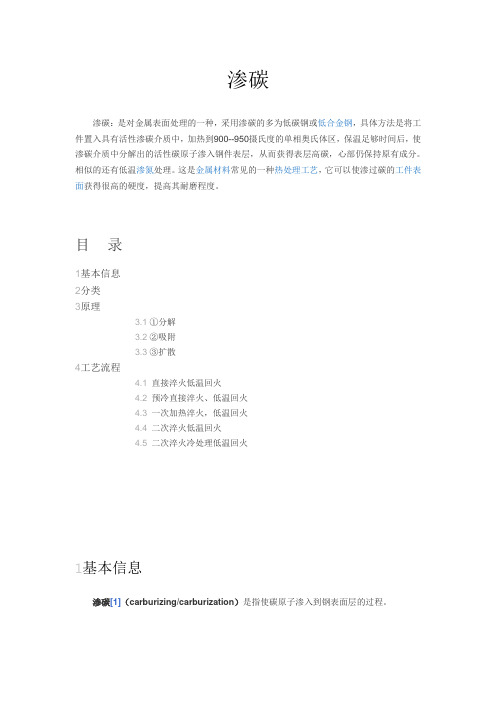
渗碳渗碳:是对金属表面处理的一种,采用渗碳的多为低碳钢或低合金钢,具体方法是将工件置入具有活性渗碳介质中,加热到900--950摄氏度的单相奥氏体区,保温足够时间后,使渗碳介质中分解出的活性碳原子渗入钢件表层,从而获得表层高碳,心部仍保持原有成分。
相似的还有低温渗氮处理。
这是金属材料常见的一种热处理工艺,它可以使渗过碳的工件表面获得很高的硬度,提高其耐磨程度。
目录1基本信息2分类3原理3.1 ①分解3.2 ②吸附3.3 ③扩散4工艺流程4.1 直接淬火低温回火4.2 预冷直接淬火、低温回火4.3 一次加热淬火,低温回火4.4 二次淬火低温回火4.5 二次淬火冷处理低温回火1基本信息渗碳[1](carburizing/carburization)是指使碳原子渗入到钢表面层的过程。
也是使低碳钢的工件具有高碳钢的表面层,再经过淬火和低温回火,使工件的表面层具有高硬度和耐磨性,而工件的中心部分仍然保持着低碳钢的韧性和塑性。
渗碳工件的材料一般为低碳钢或低碳合金钢(含碳量小于0.25%)。
渗碳后﹐钢件表面的化学成分可接近高碳钢。
工件渗碳后还要经过淬火﹐以得到高的表面硬度﹑高的耐磨性和疲劳强度﹐并保持心部有低碳钢淬火后的强韧性﹐使工件能承受冲击载荷。
渗碳工艺广泛用于飞机﹑汽车和拖拉机等的机械零件﹐如齿轮﹑轴﹑凸轮轴等。
渗碳工艺在中国可以上溯到2000年以前。
最早是用固体渗碳介质渗碳。
液体和气体渗碳是在20世纪出现并得到广泛应用的。
美国在20年代开始采用转筒炉进行气体渗碳。
30年代﹐连续式气体渗碳炉开始在工业上应用。
60年代高温(960~1100℃)气体渗碳得到发展。
至70年代﹐出现了真空渗碳和离子渗碳。
2分类按含碳介质的不同﹐渗碳可分为气体渗碳、固体渗碳﹑液体渗碳﹑和碳氮共渗(氰化)。
气体渗碳是将工件装入密闭的渗碳炉内,通入气体渗剂(甲烷、乙烷等)或液体渗剂(煤油或苯、酒精、丙酮等),在高温下分解出活性碳原子,渗入工件表面,以获得高碳表面层的一种渗碳操作工艺。
金属表面处理工艺及技术
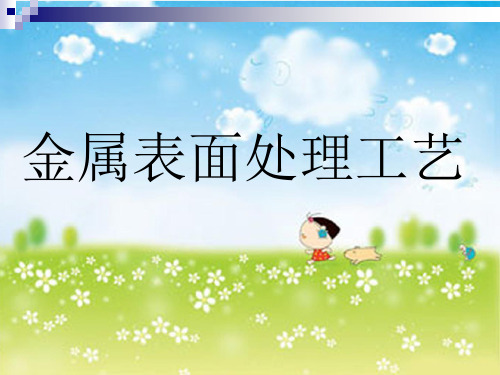
四 喷涂的涂层厚度为几十微米至数毫米.
二.热喷涂的特点
一 工艺灵活,适用范围广.热喷涂施工对象可大可小,小的可 到一0mm内孔[线爆喷涂],大的可到桥梁、铁塔[火焰线材喷 涂或电孤喷涂],可在室内喷涂,也可在野外现场作业;可 整体喷涂,也可以局部喷涂.
低碳钢渗碳缓冷后的组织
五渗碳后的热处理 淬火+低温回火, 回火温度为一六0-一八0℃.淬火方法有: ⑴ 预冷淬火法 渗碳后预冷到略高于Ar一温度直接淬火.
渗碳后的热处理示意图
⑵一次淬火法:即渗碳缓冷后重新加热淬火. ⑶ 二次淬火法: 即渗碳缓冷后第一次加热为心部Ac三+三0-五0℃,细化心部;
金属表面处理工艺
一、表面热处理
一、表面淬火 表面淬火是指在不改变钢的化学成分及心部组织情
况下,利用快速加热将表层奥氏体化后进行淬火以强 化零件表面的热处理方法.
火焰加热 感
应 加 热
表面淬火目的: 一 使表面具有高的硬度、耐磨性和疲劳极限; 二 心部在保持一定的强度、硬度的条件下,具有足够的塑
碳钢. 常用钢号为三八CrMoAl. ⑵氮化温度为五00-五七0℃ 氮化层厚度不超过0.六-0.七
mm.
井式气体氮化炉
⑶常用氮化方法 气体氮化法与离子氮化法. 气体氮化法与气体渗碳法类似,
渗剂为氨. 离子氮化法是在电场作用下,
使电离的氮离子高速冲击作为 阴极的工件.与气体氮化相比, 氮化时间短,氮化层脆性小.
第二次加热为Ac一+三0-五0℃,细化表层.
渗碳后的热处理示意图
常用方法是渗碳缓冷后,重新加热到Ac一+三0-五0℃淬火+低 温回火.此时组织为:
很全面,渗碳+渗氮+碳氮共渗表面处理工艺

很全面,渗碳+渗氮+碳氮共渗表面处理工艺渗碳与渗氮一般是指钢的表面化学热处理渗碳必须用低碳钢或低碳合金钢。
可分为固体、液体、气体渗碳三种。
应用较广泛的气体渗碳,加热温度900-950摄氏度。
渗碳深度主要取决于保温时间,一般按每小时0.2-0.25毫米估算。
表面含碳量可达0.85%-1.05%。
渗碳后必须热处理,常用淬火后低温回火。
得到表面高硬度心部高韧性的耐磨抗冲击零件。
渗氮应用最广泛的气体渗氮,加热温度500-600摄氏度。
氮原子与钢的表面中的铝、铬、钼形成氮化物,一般深度为0.1-0.6毫米,氮化层不用淬火即可得到很高的硬度,这种性能可维持到600-650摄氏度。
工件变形小,可防止水、蒸气、碱性溶液的腐蚀。
但生产周期长,成本高,氮化层薄而脆,不宜承受集中的重载荷。
主要用来处理重要和复杂的精密零件。
涂层、镀膜、是物理的方法。
“渗”是化学变化,本质不同。
钢的渗碳——就是将低碳钢在富碳的介质中加热到高温(一般为900-950C),使活性碳原子渗入钢的表面,以获得高碳的渗层组织。
随后经淬火和低温回火,使表面具有高的硬度、耐磨性及疲劳抗力,而心部仍保持足够的强度和韧性。
渗碳钢的化学成分特点(1)渗碳钢的含碳量一般都在0.15%-0.25%范围内,对于重载的渗碳体,可以提高到0.25%-0.30%,以使心部在淬火及低温回火后仍具有足够的塑性和韧性。
但含碳量不能太低,,否则就不能保证一定的强度。
(2)合金元素在渗碳钢中的作用是提高淬透性,细化晶粒,强化固溶体,影响渗层中的含碳量、渗层厚度及组织。
在渗碳钢中通常加入的合金元素有锰、铬、镍、钼、钨、钒、硼等。
常用渗碳钢可以分碳素渗碳钢和合金渗碳钢两大类(1)碳素渗碳钢中,用得最多的是15和20钢,它们经渗碳和热处理后表面硬度可达56-62HRC。
但由于淬透性较低,只适用于心部强度要求不高、受力小、承受磨损的小型零件,如轴套、链条等。
(2)低合金渗碳钢如20Cr、20Cr2MnVB、20Mn2TiB等,其渗透性和心部强度均较碳素渗碳钢高,可用于制造一般机械中的较为重要的渗碳件,如汽车、拖拉机中的齿轮、活塞销等。
渗碳热处理
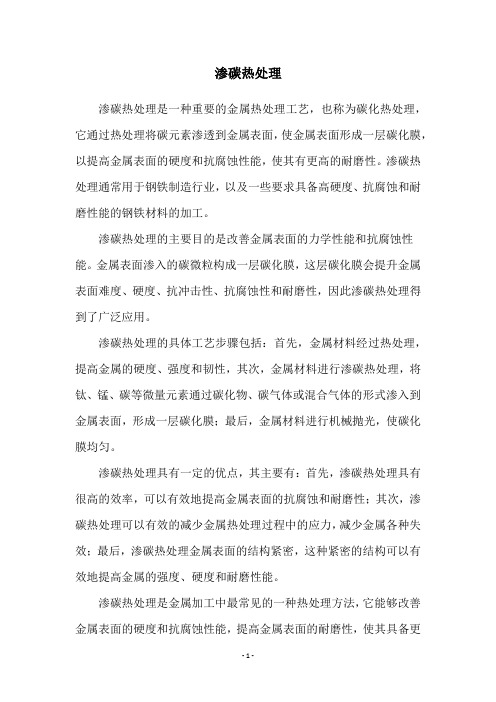
渗碳热处理渗碳热处理是一种重要的金属热处理工艺,也称为碳化热处理,它通过热处理将碳元素渗透到金属表面,使金属表面形成一层碳化膜,以提高金属表面的硬度和抗腐蚀性能,使其有更高的耐磨性。
渗碳热处理通常用于钢铁制造行业,以及一些要求具备高硬度、抗腐蚀和耐磨性能的钢铁材料的加工。
渗碳热处理的主要目的是改善金属表面的力学性能和抗腐蚀性能。
金属表面渗入的碳微粒构成一层碳化膜,这层碳化膜会提升金属表面难度、硬度、抗冲击性、抗腐蚀性和耐磨性,因此渗碳热处理得到了广泛应用。
渗碳热处理的具体工艺步骤包括:首先,金属材料经过热处理,提高金属的硬度、强度和韧性,其次,金属材料进行渗碳热处理,将钛、锰、碳等微量元素通过碳化物、碳气体或混合气体的形式渗入到金属表面,形成一层碳化膜;最后,金属材料进行机械抛光,使碳化膜均匀。
渗碳热处理具有一定的优点,其主要有:首先,渗碳热处理具有很高的效率,可以有效地提高金属表面的抗腐蚀和耐磨性;其次,渗碳热处理可以有效的减少金属热处理过程中的应力,减少金属各种失效;最后,渗碳热处理金属表面的结构紧密,这种紧密的结构可以有效地提高金属的强度、硬度和耐磨性能。
渗碳热处理是金属加工中最常见的一种热处理方法,它能够改善金属表面的硬度和抗腐蚀性能,提高金属表面的耐磨性,使其具备更高的质量。
但是,渗碳热处理也有一定的缺点,由于渗入的碳微粒侵蚀金属材料的组织,有时会导致金属材料发生裂纹,因此,在进行渗碳热处理时必须非常小心,以免破坏金属材料的性能。
总之,渗碳热处理是一种重要的金属热处理工艺,它可以改善金属表面的力学性能和抗腐蚀性能,提高金属表面的硬度、强度和耐磨性,使金属表面有更好的防腐蚀性能,但在进行渗碳热处理时,还必须注意渗入的碳微粒不能导致金属材料发生裂纹。
渗碳淬火热处理工艺【详解】

渗碳淬火热处理工艺详解内容来源网络,由深圳机械展收集整理!1、钢的淬火钢的淬火与回火是热处理工艺中最重要,也是用途最广泛的工序。
淬火可以显著提高钢的强度和硬度。
为了消除淬火钢的残余应力,得到不同强度,硬度和韧性配合的性能,需要配以不同温度的回火。
所以淬火和回火又是不可分割的、紧密衔接在一起的两种热处理工艺。
淬火、回火作为各种机器零件及工、模具的最终热处理是赋予钢件最终性能的关键工序,也是钢件热处理强化的重要手段之一。
1.1 淬火的定义和目的把钢加热到奥氏体化温度,保温一定时间,然后以大于临界冷却速度进行冷却,这种热处理操作称为淬火。
钢件淬火后获得马氏体或下贝氏体组织。
图4为渗碳齿轮20CrNi2Mo材料淬火、回火工艺。
淬火的目的一般有:1.1.1 提高工具、渗碳工件和其他高强度耐磨机器零件等的强度、硬度和耐磨性。
例如高速工具钢通过淬火回火后,硬度可达63HRC,且具有良好的红硬性。
渗碳工件通过淬火回火后,硬度可达58~63HRC。
1.1.2 结构钢通过淬火和高温回火(又称调质)之后获得良好综合力学性能。
例如汽车半轴经淬火和高温回火(280~320HB)及外圆中频淬火后,不仅提高了花键耐磨性,而且使汽车半轴承受扭转、弯曲和冲击载荷能力(尤其是疲劳强度和韧性)大为提高。
淬火时,最常用的冷却介质是水、盐水、碱水和油等。
通常碳素钢用水冷却,水价廉易得,合金钢用油来冷却,但对要求高硬度的轧辊采用盐水或碱水冷却,辊面经淬火后硬度高而均匀,但对操作要求非常严格,否则容易产生开裂。
1.2 钢的淬透性2.2.1 淬透性的基本概念所谓钢材的淬透性是指钢在淬火时获得淬硬层深度大小的能力(即钢材淬透能力),其大小用钢在一定条件下(顶端淬火法)淬火获得的有效淬硬层深度来表示,淬透性是每种钢材所固有的属性,淬硬层愈深,就表明钢的淬透性愈好,例如45、40Cr 、42CrMo钢三种试样,按相同条件淬火后(油冷却),经检测45钢能被淬透的最大直径(称临界直径)φ10mm;40Cr钢能被淬透的最大直径φ22mm; 42CrMo钢能被淬透的最大直径φ40mm。
氮化处理与渗碳处理技术的对比研究

氮化处理与渗碳处理技术的对比研究氮化处理与渗碳处理技术是常用的表面处理技术,用于提高材料的硬度、耐磨性和抗腐蚀性能。
本文将对这两种技术进行对比研究。
首先,氮化处理是一种在材料表面形成氮化物层的技术。
它可以通过离子氮化、气体氮化或盐浴氮化等方法实现。
氮化层具有高硬度、低摩擦系数和良好的抗腐蚀性能。
氮化处理可以应用于不锈钢、铜合金、钢铁等材料,广泛用于机械制造、航空航天、汽车工业等领域。
渗碳处理是一种将碳元素渗入材料表面形成碳化层的技术。
常用的方法包括气体渗碳、盐浴渗碳或液体渗碳等。
渗碳层具有高硬度、耐磨性和抗腐蚀性能。
渗碳处理常用于低碳钢、合金钢等材料,并广泛应用于轴承、齿轮和工具等领域。
在硬度方面,氮化处理的硬度通常比渗碳处理更高。
这是因为在氮化处理中,氮原子与基体原子形成固溶体,使材料表面硬度显著提高。
而渗碳处理中,碳原子主要作用于金属晶界和缺陷,使得硬度的提高程度有限。
在耐磨性方面,渗碳处理表现出更优越的性能。
渗碳层中的碳化物具有良好的耐磨性,可以增加材料的使用寿命。
而氮化处理中的氮化物层因为脆性较高,容易开裂剥离,降低了耐磨性能。
在抗腐蚀性能方面,氮化处理相对于渗碳处理更具优势。
氮化层具有良好的耐腐蚀性,可以防止金属表面氧化和金属离子的溶解。
而渗碳处理在一些腐蚀介质中容易发生腐蚀。
此外,渗碳处理的工艺更为复杂,一般需要数小时甚至几十小时才能完成。
而氮化处理的工艺时间相对较短,可以在几分钟到几小时内完成。
这使得氮化处理更适用于批量生产和自动化生产。
综上所述,在硬度、耐磨性和抗腐蚀性能方面,氮化处理和渗碳处理各有千秋。
选择使用哪种处理技术需要根据具体材料和使用环境来决定。
不过,随着技术的进步,氮化处理和渗碳处理的组合也被广泛应用于一些特殊材料的表面处理,以获得更好的综合性能。
在氮化处理和渗碳处理技术的应用方面,两者都有各自的适用领域。
氮化处理常被应用于不锈钢、铜合金、钢铁等材料的表面处理。
对于不锈钢来说,氮化处理可以提高其硬度和耐磨性,同时改善其抗腐蚀性能。
金属热处理,渗碳,渗氮,发黑发蓝等处理

金属热处理,渗碳,渗氮,发黑发蓝等处理金属热处理,渗碳,渗氮,发黑发蓝等处理金属热处理:1.金属热处理是将金属工件放在一定的介质中加热到适宜的温度,并在此温度中保持一定时间后,又以不同速度冷却,通过改变金属材料表面或内部的组织结构来控制其性能的一种工艺。
2.金属热处理是机械制造中的重要工艺之一,与其他加工工艺相比,热处理一般不改变工件的形状和整体的化学成分,而是通过改变工件内部的显微组织,或改变工件表面的化学成分,赋予或改善工件的使用性能。
其特点是改善工件的内在质量,而这一般不是肉眼所能看到的。
3.钢铁的热处理是金属热处理的主要内容。
另外,铝、铜、镁、钛等及其合金也都可以通过热处理改变其力学、物理和化学性能,以获得不同的使用性能。
4.热处理工艺一般包括加热、保温、冷却三个过程,有时只有加热和冷却两个过程。
这些过程互相衔接,不可间断。
5.加热是热处理的重要工序之一。
金属热处理的加热方法很多,最早是采用木炭和煤作为热源,进而应用液体和气体燃料。
电的应用使加热易于控制,且无环境污染。
利用这些热源可以直接加热,也可以通过熔融的盐或金属,以至浮动粒子进行间接加热。
6.金属加热时,工件暴露在空气中,常常发生氧化、脱碳(即钢铁零件表面碳含量降低),这对于热处理后零件的表面性能有很不利的影响。
金属通常应在可控气氛或保护气氛中、熔融盐中和真空中加热,也可用涂料或包装方法进行保护加热。
7.加热温度是热处理工艺的重要工艺参数之一,选择和控制加热温度,是保证热处理质量的主要问题。
加热温度随被处理的金属材料和热处理的目的不同而异,但一般都是加热到相变温度以上,以获得高温组织。
另外转变需要一定的时间,因此当金属工件表面达到要求的加热温度时,还须在此温度保持一定时间,使内外温度一致,使显微组织转变完全,这段时间称为保温时间。
采用高能密度加热和表面热处理时,加热速度极快,一般就没有保温时间,而化学热处理的保温时间往往较长。
8.冷却也是热处理工艺过程中不可缺少的步骤,冷却方法因工艺不同而不同,主要是控制冷却速度。
20CrMnTi齿轮渗碳和碳氮共渗工艺对比[1]
![20CrMnTi齿轮渗碳和碳氮共渗工艺对比[1]](https://img.taocdn.com/s3/m/9ad47bc95fbfc77da269b14c.png)
2 试验结果及分析
在两炉经不同工艺处理的齿轮中 ,随机各拿出 5 个来进行硬度 ,变形量等技术参数检测结果见表 1 。
可见 ,齿轮经碳氮共渗后 ,性能及技术参数均优 于原渗碳工艺 。在碳氮共渗过程中 ,齿轮入炉温度 860 ℃,入炉后降为 550 ℃左右 ,升温 750 ℃约需 45~ 50min,750 ℃升至 860 ℃约需 40min。在升温中只通甲
61~63 40~43 018~1 8 级 合格 合格 合格 不合格
60~63 39~42 018~1 8 级 合格 合格 合格 合格
渗碳 59~62 38~40 018~1 6 级 合格 合格 合格 合格
60~62 40~42 018~1 6 级 合格 合格 合格 合格
60~62 37~40 018~1 6 级 合格 合格不合格 合格
1 试验设备 、条件及工艺
试验设备 RJJ-90-9T 井式渗碳炉 。试验材料 , 为工厂同一批实际生产的齿轮零件 。工艺流程 :下料 —锻造 —正火 —渗碳 (碳氮共渗) —淬火 —回火 —清 洗 。钢坯齿轮经正火后 ,带状组织 3 级 ,晶粒度 9 级 。 试验工艺分别见图 1 和图 2 。
图 1 20CrMnTi渗碳工艺
摘 要 :通过 20CrMnTi齿轮渗碳和碳氮共渗工艺对比试验 ,寻求减少齿轮变形 ,提高生产效率的方法 。 关键词 :齿轮 ,渗碳 ,碳氮共渗 中图分类号 :TG15618 + 2 文献标识码 :A 文章编号 :1007-4414 (2000) 04-0060-01
农用车齿轮要求高硬度 ,高耐磨性 ,高冲击韧度 和疲劳强度 ,一直采用 20CrMnTi材料 ,其常规热处理 为渗碳工艺 ,但热处理过程中 ,变形控制是技术难题 , 废品率极高 。我们采用碳氮共渗工艺与原工艺进行 对比试验 ,以寻找减少变形 ,提高生产效率的途径 。
很全面,渗碳+渗氮+碳氮共渗表面处理工艺

很全面,渗碳+渗氮+碳氮共渗表面处理工艺很全面,渗碳+渗氮+碳氮共渗表面处理工艺渗碳与渗氮一般是指钢的表面化学热处理渗碳必须用低碳钢或低碳合金钢。
可分为固体、液体、气体渗碳三种。
应用较广泛的气体渗碳,加热温度900-950摄氏度。
渗碳深度主要取决于保温时间,一般按每小时0.2-0.25毫米估算。
表面含碳量可达0.85%-1.05%。
渗碳后必须热处理,常用淬火后低温回火。
得到表面高硬度心部高韧性的耐磨抗冲击零件。
渗氮应用最广泛的气体渗氮,加热温度500-600摄氏度。
氮原子与钢的表面中的铝、铬、钼形成氮化物,一般深度为0.1-0.6毫米,氮化层不用淬火即可得到很高的硬度,这种性能可维持到600-650摄氏度。
工件变形小,可防止水、蒸气、碱性溶液的腐蚀。
但生产周期长,成本高,氮化层薄而脆,不宜承受集中的重载荷。
主要用来处理重要和复杂的精密零件。
涂层、镀膜、是物理的方法。
“渗”是化学变化,本质不同。
钢的渗碳——就是将低碳钢在富碳的介质中加热到高温(一般为900-950C),使活性碳原子渗入钢的表面,以获得高碳的渗层组织。
随后经淬火和低温回火,使表面具有高的硬度、耐磨性及疲劳抗力,而心部仍保持足够的强度和韧性。
渗碳钢的化学成分特点1)渗碳钢的含碳量一般都在0.15%-0.25%范围内,对于重载的渗碳体,可以提高到0.25%-0.30%,以使心部在淬火及低温回火后仍具有足够的塑性和韧性。
但含碳量不能太低。
否则就不能保证一定的强度。
2)合金元素在渗碳钢中的感化是进步淬透性,细化晶粒,强化固溶体,影响渗层中的含碳量、渗层厚度及构造。
在渗碳钢中通常加入的合金元素有锰、铬、镍、钼、钨、钒、硼等。
常用渗碳钢可以分碳素渗碳钢和合金渗碳钢两大类1)碳素渗碳钢中,用得最多的是15和20钢,它们经渗碳和热处置惩罚后外表硬度可达56-62HRC。
但因为淬透性较低,只适用于心部强度要求不高、受力小、蒙受磨损的小型零件,如轴套、链条等。
渗碳热处理
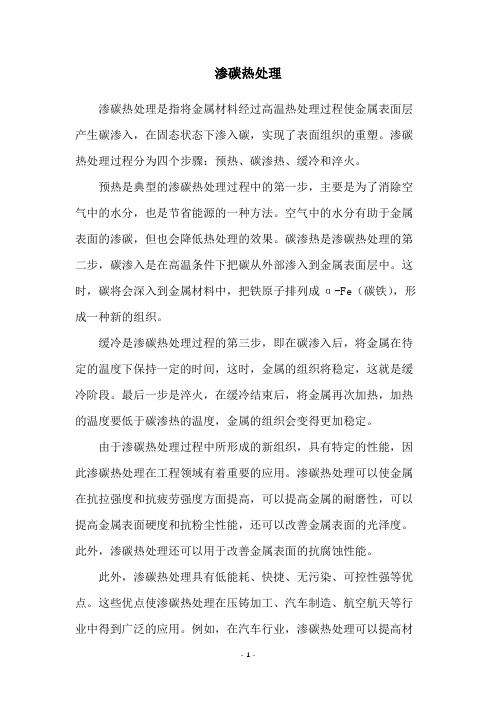
渗碳热处理渗碳热处理是指将金属材料经过高温热处理过程使金属表面层产生碳渗入,在固态状态下渗入碳,实现了表面组织的重塑。
渗碳热处理过程分为四个步骤:预热、碳渗热、缓冷和淬火。
预热是典型的渗碳热处理过程中的第一步,主要是为了消除空气中的水分,也是节省能源的一种方法。
空气中的水分有助于金属表面的渗碳,但也会降低热处理的效果。
碳渗热是渗碳热处理的第二步,碳渗入是在高温条件下把碳从外部渗入到金属表面层中。
这时,碳将会深入到金属材料中,把铁原子排列成α-Fe(碳铁),形成一种新的组织。
缓冷是渗碳热处理过程的第三步,即在碳渗入后,将金属在待定的温度下保持一定的时间,这时,金属的组织将稳定,这就是缓冷阶段。
最后一步是淬火,在缓冷结束后,将金属再次加热,加热的温度要低于碳渗热的温度,金属的组织会变得更加稳定。
由于渗碳热处理过程中所形成的新组织,具有特定的性能,因此渗碳热处理在工程领域有着重要的应用。
渗碳热处理可以使金属在抗拉强度和抗疲劳强度方面提高,可以提高金属的耐磨性,可以提高金属表面硬度和抗粉尘性能,还可以改善金属表面的光泽度。
此外,渗碳热处理还可以用于改善金属表面的抗腐蚀性能。
此外,渗碳热处理具有低能耗、快捷、无污染、可控性强等优点。
这些优点使渗碳热处理在压铸加工、汽车制造、航空航天等行业中得到广泛的应用。
例如,在汽车行业,渗碳热处理可以提高材料的物理性能,提高结构件的抗弯强度,提高车身的结构强度和耐腐蚀性,提高汽车发动机的耐热性与耐磨性,延长发动机的使用寿命。
渗碳热处理具有很大的发展潜力,可以在金属加工、航空航天、汽车制造等领域得到广泛应用。
但在进行渗碳热处理时,应注意金属材料的热稳定性和恒温性,以确保质量达标。
此外,在渗碳热处理过程中应以安全和环保为原则,避免环境污染及不必要的安全隐患。
总之,渗碳热处理是一种常用的表面处理方法,主要用于调整金属表面的组织结构,改善金属表面的物理性能和耐腐蚀性,提高工件的抗疲劳强度和使用寿命。
热处理工艺中的表面渗碳处理及其应用

热处理工艺中的表面渗碳处理及其应用热处理是指通过改变材料的组织结构、性能和形状来满足特定的使用要求的一种工艺。
在热处理中,表面渗碳处理是一种常用的方法,通过在金属表面形成一层富碳的薄膜,改善材料的硬度和耐磨性,提高其使用寿命。
本文将对表面渗碳处理的原理、方法以及应用进行探讨。
一、表面渗碳处理的原理表面渗碳处理,顾名思义,就是在材料的表面形成一层富碳的薄膜。
其主要原理是通过在高温下将含有碳源的气体与金属表面接触,使其碳原子浓度在金属表面达到饱和,并在一定时间内进行扩散,从而形成富碳薄膜。
二、表面渗碳处理的方法表面渗碳处理有多种方法,常用的有固体碳源法、气体碳源法和液体碳源法。
1. 固体碳源法:这种方法最常见,通常使用含有高碳量的固体材料,如碳化硼粉末或含碳化合物的固体混合物,在高温下与金属表面接触,通过热分解或扩散反应释放出碳原子,形成富碳薄膜。
2. 气体碳源法:在这种方法中,通常使用含有碳原子的气体,如一氧化碳(CO)或甲烷(CH4),在高温下与金属表面反应,使碳原子扩散到金属表面形成富碳薄膜。
3. 液体碳源法:这种方法更多用于渗碳钢件的处理,通过将含有碳原子的液体,如酚酸盐溶液或含有碳氰化物的液体,与金属表面接触,在高温下使碳原子扩散到金属表面,形成富碳薄膜。
三、表面渗碳处理的应用表面渗碳处理可以显著改变材料的性能,提高其硬度和耐磨性,因此在很多领域都有广泛的应用。
1. 汽车工业:表面渗碳处理可以用于汽车发动机零部件的制造,如曲轴、凸轮轴等。
这些零部件经过表面渗碳处理后,硬度得到提高,耐磨性和耐腐蚀性也得到了改善,从而延长了汽车发动机的使用寿命。
2. 机械制造业:在机械制造过程中,很多工件需要具备较高的硬度和耐磨性,以满足使用要求。
通过表面渗碳处理,可以将软钢表面变成硬质合金,提高零件的使用寿命。
3. 刀具制造业:在刀具制造过程中,表面渗碳处理是很常见的一种工艺。
通过在刀具表面形成富碳薄膜,刀具的硬度得到了提高,从而提高了切削性能和使用寿命。
金属表面热处理渗碳工艺对比
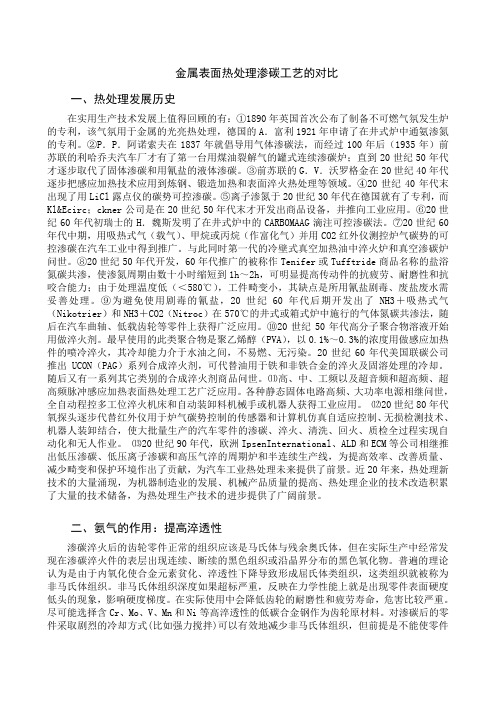
金属表面热处理渗碳工艺的对比一、热处理发展历史在实用生产技术发展上值得回顾的有:①1890年英国首次公布了制备不可燃气氛发生炉的专利,该气氛用于金属的光亮热处理,德国的A.富利1921年申请了在井式炉中通氨渗氮的专利。
②P.P.阿诺索夫在1837年就倡导用气体渗碳法,而经过100年后(1935年)前苏联的利哈乔夫汽车厂才有了第一台用煤油裂解气的罐式连续渗碳炉;直到20世纪50年代才逐步取代了固体渗碳和用氰盐的液体渗碳。
③前苏联的G.V.沃罗格金在20世纪40年代逐步把感应加热技术应用到炼钢、锻造加热和表面淬火热处理等领域。
④20世纪40年代末出现了用LiCl露点仪的碳势可控渗碳。
⑤离子渗氮于20世纪30年代在德国就有了专利,而KlÊ;ckner公司是在20世纪50年代末才开发出商品设备,并推向工业应用。
⑥20世纪60年代初瑞士的H.魏斯发明了在井式炉中的CARBOMAAG滴注可控渗碳法。
⑦20世纪60年代中期,用吸热式气(载气)、甲烷或丙烷(作富化气)并用CO2红外仪测控炉气碳势的可控渗碳在汽车工业中得到推广。
与此同时第一代的冷壁式真空加热油中淬火炉和真空渗碳炉问世。
⑧20世纪50年代开发,60年代推广的被称作Tenifer或Tufftride商品名称的盐浴氮碳共渗,使渗氮周期由数十小时缩短到1h~2h,可明显提高传动件的抗疲劳、耐磨性和抗咬合能力;由于处理温度低(<580℃),工件畸变小,其缺点是所用氰盐剧毒、废盐废水需妥善处理。
⑨为避免使用剧毒的氰盐,20世纪60年代后期开发出了NH3+吸热式气(Nikotrier)和NH3+CO2(Nitroc)在570℃的井式或箱式炉中施行的气体氮碳共渗法,随后在汽车曲轴、低载齿轮等零件上获得广泛应用。
⑩20世纪50年代高分子聚合物溶液开始用做淬火剂。
最早使用的此类聚合物是聚乙烯醇(PVA),以0.1%~0.3%的浓度用做感应加热件的喷冷淬火,其冷却能力介于水油之间,不易燃、无污染。
不同钢种的热处理工艺比较

Ac3以上
碳钢、低合金结构零件、锻件轧件等
提高钢强韧性。
良好拉伸、冲击、疲劳性及断裂韧性
低温形变热处
加热至奥氏体状体
结构/弹簧/轴承/工具
良好的塑性和韧性
表面淬火
(感应加热)
将工件快速加热到淬火温度,然后迅速冷却,仅使表面层获得淬火组织的热处理工艺。
高频感应加热
80~1000kHz
中小模数齿轮和小轴
工艺
定义
分类
加热温度
适用钢种
目的
最终组织
性能
退火
将钢加热到临界点Ac1以上或以下温度,保温以后随炉缓慢冷却以获得近乎平衡态组织的热处理工艺。
完全退火
Ac3以上20~30℃
亚共析钢
均匀钢的化学成分组织,细化晶粒,调整硬度,消除内应力和加工硬化,改善钢的成形及切削加工性能,并为淬火做好组织准备。
先共析铁素体+珠光体
不完全退火
Ac1~Ac3
亚共析钢
珠光体
Ac1~Acm
过共析钢
球化退火
共析/过共析/合金工具
粒状珠光体
扩散退火
Ac3或Acm以上150℃
钢锭/铸件/缎坯
去应力退火
约500~600℃
热轧或缎后钢材
在结晶退火
约650~700℃
冷变形合金结构钢
均匀等轴晶粒
正火
将钢加热到Ac3(或Acm)以上适当温度,保温后在空气中冷却得到珠光体类组织的热处理工艺。
表面高强度和硬度和耐磨性,心部具有一定的强度、足够的塑性和韧性。
马氏体
表硬心韧
中频感应加热
2500~8000Hz
曲轴/大模数齿轮/大轴
ห้องสมุดไป่ตู้低频感应加热
- 1、下载文档前请自行甄别文档内容的完整性,平台不提供额外的编辑、内容补充、找答案等附加服务。
- 2、"仅部分预览"的文档,不可在线预览部分如存在完整性等问题,可反馈申请退款(可完整预览的文档不适用该条件!)。
- 3、如文档侵犯您的权益,请联系客服反馈,我们会尽快为您处理(人工客服工作时间:9:00-18:30)。
金属表面热处理渗碳工艺的对比一、热处理发展历史在实用生产技术发展上值得回顾的有:①1890年英国首次公布了制备不可燃气氛发生炉的专利,该气氛用于金属的光亮热处理,德国的 A.富利1921年申请了在井式炉中通氨渗氮的专利。
②P. P•阿诺索夫在1837年就倡导用气体渗碳法,而经过100年后(1935年)前苏联的利哈乔夫汽车厂才有了第一台用煤油裂解气的罐式连续渗碳炉;直到20世纪50年代才逐步取代了固体渗碳和用氰盐的液体渗碳。
③前苏联的G V沃罗格金在20世纪40年代逐步把感应加热技术应用到炼钢、锻造加热和表面淬火热处理等领域。
④20世纪40年代末出现了用LiCl 露点仪的碳势可控渗碳。
⑤离子渗氮于20世纪30年代在德国就有了专利,而KIÊ ; ckner公司是在20世纪50年代末才开发出商品设备,并推向工业应用。
⑥20世纪60年代初瑞士的H.魏斯发明了在井式炉中的CARBOMAA滴注可控渗碳法。
⑦20世纪60 年代中期,用吸热式气(载气)、甲烷或丙烷(作富化气)并用CO2红外仪测控炉气碳势的可控渗碳在汽车工业中得到推广。
与此同时第一代的冷壁式真空加热油中淬火炉和真空渗碳炉问世。
⑧20世纪50年代开发,60年代推广的被称作Tenifer或Tufftride 商品名称的盐浴氮碳共渗,使渗氮周期由数十小时缩短到1h〜2h,可明显提高传动件的抗疲劳、耐磨性和抗咬合能力;由于处理温度低(v 580C),工件畸变小,其缺点是所用氰盐剧毒、废盐废水需妥善处理。
⑨为避免使用剧毒的氰盐,20世纪60年代后期开发出了NH3+吸热式气(Nikotrier )和NH阱CO2( Nitroc )在570E的井式或箱式炉中施行的气体氮碳共渗法,随后在汽车曲轴、低载齿轮等零件上获得广泛应用。
⑩20世纪50年代高分子聚合物溶液开始用做淬火剂。
最早使用的此类聚合物是聚乙烯醇(PVA,以0.1%〜0.3%的浓度用做感应加热件的喷冷淬火,其冷却能力介于水油之间,不易燃、无污染。
20 世纪60 年代美国联碳公司推出UCO(PAG系列合成淬火剂,可代替油用于铁和非铁合金的淬火及固溶处理的冷却。
随后又有一系列其它类别的合成淬火剂商品问世。
(11)高、中、工频以及超音频和超高频、超高频脉冲感应加热表面热处理工艺广泛应用。
各种静态固体电路高频、大功率电源相继问世,全自动程控多工位淬火机床和自动装卸料机械手或机器人获得工业应用。
?(12)20世纪80年代氧探头逐步代替红外仪用于炉气碳势控制的传感器和计算机仿真自适应控制、无损检测技术、机器人装卸结合,使大批量生产的汽车零件的渗碳、淬火、清洗、回火、质检全过程实现自动化和无人作业。
?(13)20世纪90年代,欧洲Ipsenlnternational 、ALD和ECM等公司相继推出低压渗碳、低压离子渗碳和高压气淬的周期炉和半连续生产线,为提高效率、改善质量、减少畸变和保护环境作出了贡献,为汽车工业热处理未来提供了前景。
近20年来,热处理新技术的大量涌现,为机器制造业的发展、机械产品质量的提高、热处理企业的技术改造积累了大量的技术储备,为热处理生产技术的进步提供了广阔前景。
二、氨气的作用:提高淬透性渗碳淬火后的齿轮零件正常的组织应该是马氏体与残余奥氏体,但在实际生产中经常发现在渗碳淬火件的表层出现连续、断续的黑色组织或沿晶界分布的黑色氧化物。
普遍的理论认为是由于内氧化使合金元素贫化、淬透性下降导致形成屈氏体类组织,这类组织就被称为非马氏体组织。
非马氏体组织深度如果超标严重,反映在力学性能上就是出现零件表面硬度低头的现象,影响硬度梯度。
在实际使用中会降低齿轮的耐磨性和疲劳寿命,危害比较严重。
尽可能选择含Cr、Mo V Mn和Ni等高淬透性的低碳合金钢作为齿轮原材料。
对渗碳后的零件采取剧烈的冷却方式(比如强力搅拌)可以有效地减少非马氏体组织,但前提是不能使零件产生开裂或严重的变形。
因此在零件变形允许的条件下,尽可能采用激烈的冷却介质和采取剧烈的冷却方式。
例如对大的轴齿类零件采用强力搅拌的冷却方式,可以有效地提高齿轮心部硬度及减少非马氏体组织。
在渗碳工艺的扩散段,当炉温降至860C左右时,开始通入氨气(流量为0.3m3/h), —直到零件淬火关闭。
该方法的原理是,通入氨气给零件渗氮,由于氮原子的渗入,可以补充由于内氧化减少的合金元素,在一定程度上提高了零件表层的淬透性,因此减少了非马氏体组织。
(参考文献:李新斌,齿轮渗碳淬火表层非马氏体组织产生的原因及对策[J].热加工工艺,2010,39(04):161-172.)三、各种渗碳方法的比较四、铝合金淬火介质的分类及特性实际使用的淬火介质种类繁多,一般可分为液体(水、无机物水溶液、有机聚合物水溶液、淬火油、熔融金属、熔盐、熔碱等)、气体(空气、压缩空气、液化气等)、固体(流态床、金属板等)三大类。
其中,水、无机物水溶液、有机聚合物水溶液、各种淬火油等,在淬火时要发生物态转变,而气体、熔盐金属、熔碱、熔盐等,在淬火时则不发生物态变化.工件淬火希望的理想效果是获得高而均匀的表面硬度和足够的淬硬深度,消除淬火裂纹和减小淬火变形。
即实现“高温阶段快冷,低温阶段慢冷”的理想冷却。
通常对淬火介质特性的要求是应满足冷却转变曲线对冷却速度的要求,避免工件变形和开裂;淬火后工件表面应保持清洁;在使用过程中性能稳定,不分解、不变质、不老化、易于控制;工件浸入时不产生大量烟雾和有害气体,以保持良好的劳动条件;便于配置、运输和存储,使用安全:原材料易得,成本廉价。
淬火介质的冷却能力,主要取决于该介质的组成及其物理化学性能。
在实际运用中,要注意淬火介质冷却特性对淬火工件的质量影响,并根据工件的合金成分多少、淬透性高低、有效厚度和形状复杂程度等因素,来选择合适的淬火介质。
采用同一种淬火介质,如果能够改进冷却方法和适当调整工艺参数,则可以获得最佳淬火效果。
例如,对淬火介质进行循环、搅拌或施以一定的压力通过工件表面时,可提高淬火介质的冷却能力和工件冷却的均匀性,这对于避免形成淬火软点、减少变形和开裂具有良好的作用。
(1)水水是应用最早、最广泛、最经济的淬火介质[55,561 ,它价廉易得、无毒、不燃烧、物理化学性能稳定、冷却能力很强。
通过控制水的温度、提高压力、增大流速、采用循环水、利用磁场等作用,均可改善水的冷却特性,减少变形和开裂,获得比较理想的淬火效果。
由于这些方法需增加专门设备,且工件淬火后的性能不太稳定,故未能推广应用。
所以说,纯水只适合于少数淬透性低且形状简单的工件淬火。
(2)淬火油用于淬火的矿物油通常以精制程度高的中性石蜡基油为基础油,它具有闪点高、粘度低、油烟少、油垢少,抗氧化性与热稳定性好,使用寿命长等优点,适合淬火使用。
淬火油只适合于淬透性好、工件壁厚不大、形状复杂、要求淬火变形小的工件。
淬火油对周围环境污染大,淬火时易引起火灾,需配备必要的清洗、通风和防火安全设施。
影响淬火油冷却能力的主要因素是其粘度值,在常温下低粘度油比高粘度油冷却能力大,温度升高,油的流动性增加,冷却能力有所提高。
适当提高淬火油使用温度,也能使油的冷却能力提高。
普通机油的使用温度一般都控制在60 摄氏度-80 摄氏度, 最高不超过120摄氏度,以保证使用安全。
另外,淬火油在使用过程中,因形成的炭黑及残渣等会使粘度增加,闪点升高,降低其冷却能力,使得淬火油老化和失效。
淬火油的闪点、粘度、酸值、皂化值的变化是其临近老化的重要数据,因此,必须进行定期的检测和维护,定期沉降过滤,适时补充新油,这对于延长淬火油的使用寿命是很重要的。
由于各种淬火油的组成不同,其密度、粘度和闪点也不相同,因而具有不同的种类和使用范围。
在油中加入各种不同的添加剂(如催化剂、光亮剂、抗氧化剂等),再配合搅拌、喷淋、超声强化和改进淬火设备等,能大幅度提高淬火油的冷却速度,改善冷却的均匀性,或使工件表面光亮洁净,或延长淬火油的使用寿命。
随着热处理技术的发展,各种淬火油也得到发展和广泛应用。
(3)NaC1水溶液氯化钠加入水中,能显著提高水的冷却能力。
氯化钠溶于水中,降低了蒸气膜的稳定性,提高了特性温度。
当水中含有5%的氯化钠时,工件进入溶液以后,蒸气膜几乎立即破坏。
这是因为氯化钠水溶液与灼热的工件接触,水被蒸发,氯化钠微粒附着在工件表面上,这些氯化钠微粒即刻激烈爆炸成云雾状,使蒸气膜遭到破坏。
工件表面上的氧化铁皮也被炸掉,使工件表面与水能直接接触,工件的冷却速度急剧增加,而且冷却进行得也比较均匀。
氯化钠水溶液冷却能力强,价格便宜,应用广泛。
浓度为5-15%的氯化钠溶液冷却能力大。
应用5-15%氯化钠溶液,工件不但得到高的硬度,而且硬度均匀,它多被用于淬透性比较低的钢种。
高浓度的氯化钠水溶液,冷却速度变得比较低,可应用于要求变形和开裂倾向的小的工件。
氯化钠水溶液淬火介质的缺点是催火后易生锈。
淬火后要进行仔细清洗。
(4)熔盐、熔碱这类淬火介质的特点是在冷却过程中不发生物态变化,工件淬火主要靠对流冷却,通常在高温区域冷却速度快,在低温区域冷却速度慢,淬火性能优良,淬透性强,淬火变形小,基本无裂纹产生,但是对环境污染大,劳动条件差,耗能多、成本高,常用于形状复杂、截面尺寸变化大的工件和工模具的淬火。
熔盐有氯化盐、硝酸盐、亚硝酸盐等,工件在盐浴中淬火可以获得较高的硬度,变形极小,不易开裂,通常用作等温淬火或分级淬火。
其缺点是熔盐易老化,对工件有氧化腐蚀作用。
熔碱有氢氧化钠、氢氧化钾等,具有较大的冷却能力,工件加热时若未氧化,淬火后可获得银灰色的洁净表面,有一定的应用。
但熔碱蒸汽具有腐蚀性,对皮肤有刺激作用,使用时应注意通风和采取防护措施。
五、常用炉型的选择炉型应依据不同的工艺要求及工件的类型来决定:1.对于不能成批定型生产的,工件大小不相等的,种类较多的,要求工艺上具有通用性、多用性的,可选用箱式炉。
2.加热长轴类及长的丝杆,管子等工件时,可选用深井式电炉。
3.小批量的渗碳零件,可选用井式气体渗碳炉。
4.对于大批量的汽车、拖拉机齿轮等零件的生产可选连续式渗碳生产线或箱式多用炉。
5.对冲压件板材坯料的加热大批量生产时,最好选用滚动炉,辊底炉。
6.对成批的定型零件,生产上可选用推杆式或传送带式电阻炉(推杆炉或铸带炉)。
7.小型机械零件如:螺钉,螺母等可选用振底式炉或网带式炉。
8.钢球及滚柱热处理可选用内螺旋的回转管炉。
9.有色金属锭坯在大批量生产时可用推杆式炉,而对有色金属小零件及材料可用空气循环加热炉。