枪钻系列刀具的特点及应用
枪钻机床的特点和设计
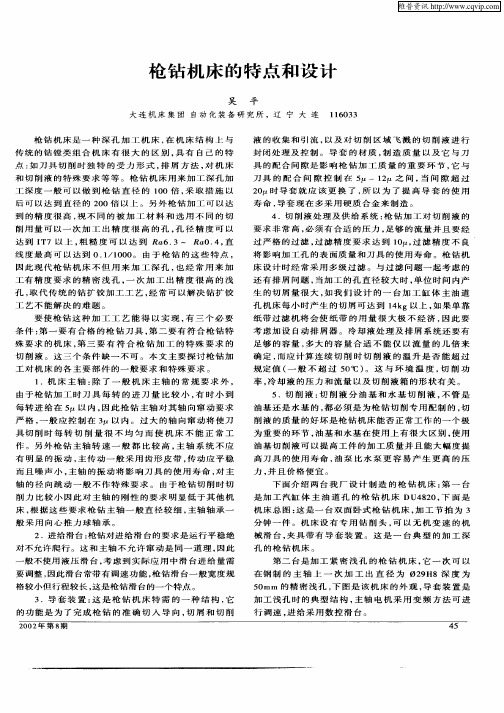
由 于 枪 钻 加 工 时 刀 具 每 转 的 进 刀 量 比较 小 , 时 小 到 有 每 转 进 给 在 5 以 内 , 此 抢 钻 主轴 对 其 轴 向窜 动要 求 因
严 格 , 般 应 控 制 在 3 以 内 。 过 大 的 轴 向 窜 动 将 使 刀 一 具 切 削 时 每 转 切 削 量 很 不 均 匀 而 使 机 床 不 能 正 常 工 作 。另 外 枪 钻 主 轴 转 速 一 般 都 比 较 高 , 轴 系 统 不 应 主
维普资讯
枪 钻 机 床 的 特 点 和 设 计
吴 平 大 连 机 床 集 团 自动 化 装 备 研 究 所 ,辽 宁 大 连 1 6 3 10 3 枪 钻 机 床 是 一 种 深 孔 加 工 机 床 , 机 床 结 构 上 与 在 液 的收 集 和 引 流 , 及 对 切 削 区 域 飞 溅 的 切 削 液 进 行 以 封 闭 处 理 及 控 制 。 导 套 的 材 质 , 造 质 量 以 及 它 与 刀 制 具 的 配 合 间 隙 是 影 响 枪 钻 加 工 质 量 的 重 要 环 节 , 与 它
工 对 机 床 的 各 主 要 部件 的一 般 要 求 和 特 殊 要 求 。 1 .机 床 主 轴 : 了 一 般 机 床 主 轴 的 常 规 要 求 外 , 除
率 , 却 液 的 压 力 和 流 量 以及 切 削 液 箱 的形 状 有 关 。 冷
5.切 削 液 : 削 液 分 油 基 和 水 基 切 削 液 , 管 是 切 不
到 的 精 度 很 高 , 不 同 的 被 加 工 材 料 和 选 用 不 同 的 切 视 削 用 量 可 以 一 次 加 工 出 精 度 很 高 的 孔 , 径 精 度 可 以 孔 达 到 I 7 以 上 , 糙 度 可 以 达 到 R 6 3~ Ra 4, T 粗 a . O. 直 线 度 最 高 可 以 达 到 0. / 0 0 由 于 枪 钻 的 这 些 特 点 , 1 10 。 因此 现 代 枪 钻 机 床 不 但 用 来 加 工 深 孔 , 经 常 用 来 加 也 工 有 精 度 要 求 的 精 密 浅 孔 , 次 加 工 出 精 度 很 高 的 浅 一 孔 , 代 传 统 的 钻 扩 铰 加 工 工 艺 , 常 可 以 解 决 钻 扩 铰 取 经
深孔加工的王者,枪钻!
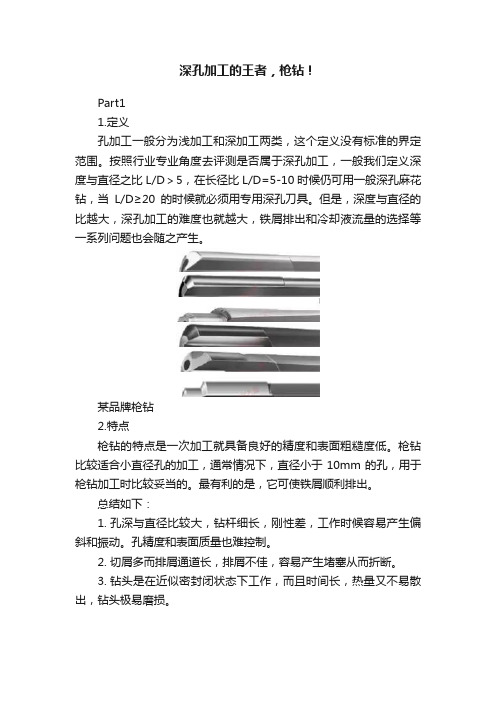
深孔加工的王者,枪钻!Part11.定义孔加工一般分为浅加工和深加工两类,这个定义没有标准的界定范围。
按照行业专业角度去评测是否属于深孔加工,一般我们定义深度与直径之比L/D>5,在长径比L/D=5-10时候仍可用一般深孔麻花钻,当L/D≥20的时候就必须用专用深孔刀具。
但是,深度与直径的比越大,深孔加工的难度也就越大,铁屑排出和冷却液流量的选择等一系列问题也会随之产生。
某品牌枪钻2.特点枪钻的特点是一次加工就具备良好的精度和表面粗糙度低。
枪钻比较适合小直径孔的加工,通常情况下,直径小于10mm的孔,用于枪钻加工时比较妥当的。
最有利的是,它可使铁屑顺利排出。
总结如下:1.孔深与直径比较大,钻杆细长,刚性差,工作时候容易产生偏斜和振动。
孔精度和表面质量也难控制。
2.切屑多而排屑通道长,排屑不佳,容易产生堵塞从而折断。
3.钻头是在近似密封闭状态下工作,而且时间长,热量又不易散出,钻头极易磨损。
专机实际应用Part23.结构枪钻是由枪头,枪杆和钻柄构成。
枪头常用的是硬质合金材料,枪杆是有高强度的合金管压制而成,枪柄是将钻头和机床连接起来的部分。
枪钻有两条主切削刃和一跳副切削刃,靠近钻心的叫内刃,另一条称之为外刃,其交点称之为钻尖。
专业名称4.角度钻尖几何参数的选择。
枪钻钻削主要取决于外刃角φ外,内刃角φ内及钻尖的偏心距。
钻尖角2φ[2φ=180°-(φ外+φ内)],一般来说较硬的材料需要用较小的钻尖角,较软的材料则需要交大的钻尖角,无论钻尖角度如何,外刃角和内刃角的选用必须保证钻头在切削时的径向分离和主切削力能合理的作用在钻头的支撑区上,以便起到挤光孔表面的作用。
切削刃的交点位置距离钻头中心一般为1/4直径。
根据硬质合金枪钻受力平衡分析,要求外刃径向切削力等于内刃径向切削力,但实际加工过程中很难保证。
为了避免钻孔偏心,只有外刃径向切削力大于内刃径向切削力,才能使径向合力始终作用于待加工表面。
超大长径比深孔加工的先进工艺技术——枪钻加工技术
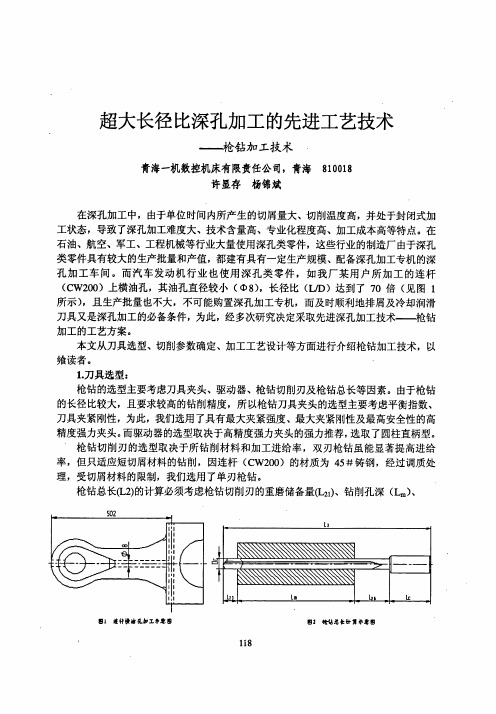
(Cw200)上横油孔,其油孔直径较小(①8),长径比(∽)达到了70倍(见图l
所示),且生产批量也不大,不可能购置深孔加工专机,而及时顺利地排屑及冷却润滑
刀具又是深孔加工的必备条件,为此,经多次研究决定采取先进深孔加工技术——枪钻
加工的工艺方案。 本文从刀具选型、切削参数确定、加工工艺设计等方面进行介绍枪钻加工技术,以 飨读者。 1.刀具选型: 枪钻的选型主要考虑刀具夹头、驱动器、枪钻切削刃及枪钻总长等因素。由于枪钻 的长径比较大,且要求较高的钻削精度,所以枪钻刀具夹头的选型主要考虑平衡指数、 刀具夹紧刚性,为此,我们选用了具有最大夹紧强度、最大夹紧刚性及最高安全性的高 精度强力夹头。而驱动器的选型取决于高精度强力夹头的强力推荐,选取了圆柱直柄型。 枪钻切削刃的选型取决于所钻削材料和加工进给率,双刃枪钻虽能显著提高进给 率,但只适应短切屑材料的钻削,因连杆(Cw200)的材质为45#铸钢,经过调质处 理,受切屑材料的限制,我们选用了单刃枪钻。 枪钻总长(L2)的计算必须考虑枪钻切削刃的重磨储备量(L21)、钻削孔深(Lm)、
120
超大长径比深孔加工的先进工艺技术——枪钻加工技术
作者: 作者单位: 许显存, 杨锦斌 青海一机数控机床有限责任公司,青海 810018
本文链接:/Conference_6524710.aspx
n=2600r/min。
3.钻削加工过程: 枪钻的钻削过程包括钻削导向孑L、钻削油孔两方面内容。因导向孔在枪钻钻削过程 中具有导向套的功效,所以导向孑L的直径和钻深要求较严,导向孔直径比枪钻直径大 0.0l~0.02,导向孔深至少有枪钻直径的2.5倍,由此看来,导向孔加工最好使用SANDVIK
CoroDrilI钻或U钻。
即完成枪钻钻削过程。
枪钻和深孔合金钻在深孔加工的对比应用

【 btat o pr d f et ahn g a r ephl p cs d cs addsr et A s c】C m a ie n m ci n yf e o r es i us n eci e r e fr i w od e o , s b h
a v na eo u r l n e ph l l yd i ,o a e eee c . d a tg f ndi dd e oeal rl fr e d r or frn e g la o l r t
【 摘要 】 介绍 了模具加工 中深孔加工的不 同方式, 并结合其各 自的特点, 进行 了详 细说 明,
供读者参考。
关键 词 : 钻 ; 枪 深孔 钻 ; 孔加 工 深
中图分 类 号 :P 1 T 35
文 献标 识 码 : B
Co p r n p ia i n o n Drl a d De p m a e a d Ap l to fGu i n e c l Ho e Al y Drl i h e l o e s l l i n t e De p Ho ePr c s o l
工在 当前机 械加工 中的应用 日益广泛 , 特别是 在汽 车、 建机 、 机床 、 矿机 、 模具 、 冶金设备乃至航空航天和 核 电站等零部件加工 中, 都离不开深孑 加工 。 L 在模具加工深孔钻削 时 , 散热和排屑 困难 , 一直 是深孔加工 中的难题 , 因钻杆细长而 刚性差 , 且 易产 生弯 曲和振 动。一 般都要 借助压力冷却系统解决冷 却和排 屑问题 。深孔 钻按排 屑方 式分为外排屑和 内 排屑两类。外排屑的有枪钻 、 深孔扁钻 和深孑螺旋形 L 钻钻 头等 , 内排屑深孔钻根据所用 的加工 系统不 同 , 分 B A深孔 钻 、 T 喷射钻和 D 深孔 钻 3 。因 内排 屑 F 种 的加 工系统 比较复杂 , 在实 际应用 中很少 , 现就外排 屑中的枪钻及深孑合金钻头的应用做对 比介绍。 L
枪钻的设计与应用讲解

图4
二、枪钻刀头的组成、设计及几何参数
刀头是枪钻的主要部分,它直接影响加工质量,刀具寿 命。 枪钻刀头的组成:有二个切削刃,其这二个切削刃相交 处为钻尖,这二个切削刃称为内刃和外刃,分别具有内外 角。
1.内外刃的内外角与钻尖的关系
图5:枪钻刀头切削部分要素
在设计上必须保证钻削是径向力接近平 衡(图b),并使切削刃的合理分布在 钻头的两导向块之间,因此,作用在外, 内刃上的径向力分别为:
(3)刀杆外形与刀头的外形对称问题: 理论上要求对称度误差越小越好,对使用效果也越理想, 但实际上做不到其原因是: a.刀杆长度太长甚至2~3米,甚至个别还长。 b.即便刀杆不十分过长,焊后精加工刀头但圆磨加工 中也有一定误差。 c.个别由于多种原因刀头精加工后才进行焊接,这时 对称度更有困难。(见下图)
经过上面分析得出:通常刀具偏移中心距离—e=D/(35),现常取e=D/4,对于加工结构钢和铸铁取Kr2=20°, Kr1=30°~40°。
图a
图b
图c
由图a不难看出:外刃径向力过大,使作用于导向 块得挤压力加大,摩擦增大会使加工表面恶化,热量 增多。
图b内刃径向力增大,会引起孔的直线外刃径向力相等或者外刃径向力稍许大 于内刃径向力,而取e=D/4时工作状态良好,同 时又防止了钻头中心处切削速度为零,挤压被切削材 料,诸多因素钻尖e要取一个适当的距离。
刀头与刀杆对称度最好控制在0.1-0.2视直径大小 有关,因刀杆与刀头最大尺寸有一定差值,况且直径 越大其两差值也大,否则无法使用。 总之,当刀头直径在可能条件力争焊后再进行精加 工,外刃及其刃形和各部后角。 为了保证孔加工精度,其刀头上有分布合理的导向 块,形成二个导向块和外切削刃的刃带三点固定圆, 起自行导向作用,见图4:
各大类型钻头的特点及用途
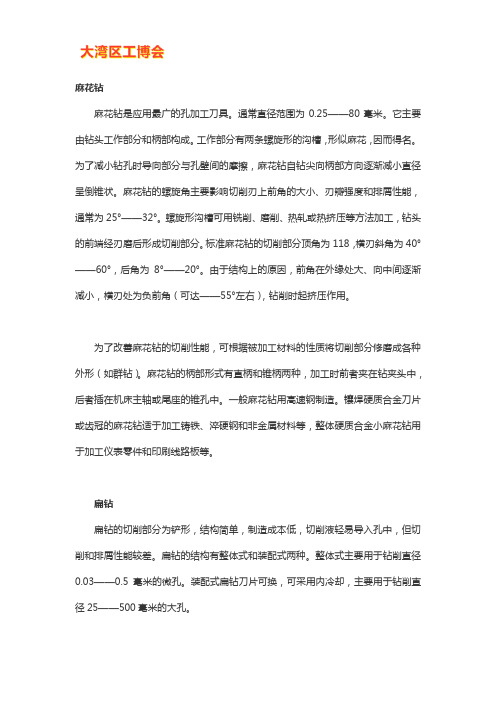
麻花钻麻花钻是应用最广的孔加工刀具。
通常直径范围为0.25——80毫米。
它主要由钻头工作部分和柄部构成。
工作部分有两条螺旋形的沟槽,形似麻花,因而得名。
为了减小钻孔时导向部分与孔壁间的摩擦,麻花钻自钻尖向柄部方向逐渐减小直径呈倒锥状。
麻花钻的螺旋角主要影响切削刃上前角的大小、刃瓣强度和排屑性能,通常为25°——32°。
螺旋形沟槽可用铣削、磨削、热轧或热挤压等方法加工,钻头的前端经刃磨后形成切削部分。
标准麻花钻的切削部分顶角为118,横刃斜角为40°——60°,后角为8°——20°。
由于结构上的原因,前角在外缘处大、向中间逐渐减小,横刃处为负前角(可达——55°左右),钻削时起挤压作用。
为了改善麻花钻的切削性能,可根据被加工材料的性质将切削部分修磨成各种外形(如群钻)。
麻花钻的柄部形式有直柄和锥柄两种,加工时前者夹在钻夹头中,后者插在机床主轴或尾座的锥孔中。
一般麻花钻用高速钢制造。
镶焊硬质合金刀片或齿冠的麻花钻适于加工铸铁、淬硬钢和非金属材料等,整体硬质合金小麻花钻用于加工仪表零件和印刷线路板等。
扁钻扁钻的切削部分为铲形,结构简单,制造成本低,切削液轻易导入孔中,但切削和排屑性能较差。
扁钻的结构有整体式和装配式两种。
整体式主要用于钻削直径0.03——0.5毫米的微孔。
装配式扁钻刀片可换,可采用内冷却,主要用于钻削直径25——500毫米的大孔。
深孔钻深孔钻通常是指加工孔深与孔径之比大于6的孔的刀具。
常用的有枪钻、BTA 深孔钻、喷射钻、DF深孔钻等。
套料钻也常用于深孔加工。
扩孔钻扩孔钻有3——4个刀齿,其刚性比麻花钻好,用于扩大已有的孔并提高加工精度和光洁度。
锪钻锪钻有较多的刀齿,以成形法将孔端加工成所需的外形,用于加工各种沉头螺钉的沉头孔,或削平孔的外端面。
中心钻中心钻供钻削轴类工件的中心孔用,它实质上是由螺旋角很小的麻花钻和锪钻复合而成,故又称复合中心钻。
枪钻技术在数控车床上加工深孔零件的探讨

文献标识码 :A
文章编号 :2095—980X(2016)03~0025—02
Discussion about Processing Deep hole Parts with Gun
Drill Technology in CNC Lathe
u H uai-lin (Gaochun Secondary Professional School,Nanjing,Jiangsu 211300,China)
2 枪钻技术的概述及工作原理
枪钻是一种有效 的深孔加工刀具 ,其加 工范围很 广 ,从模 具钢材 ,玻璃纤 维 、特氟龙 等塑料 到高强度 合金 (如 铬镍铁合 金 )的深孔加工 。在公差和表面粗糙度要求较严 的深孔加工 中 ,枪钻 可保证孔 的尺寸精 度 、位置精度和直线度 。
专业的枪钻系统 由深孔钻机 、单刃或双刃的枪钻及高压 冷却系统组成。枪钻柄部被夹持在 机床主轴上 ,钻头通过导 引 孔或导套进入工件表面 ,进入后钻刃的独特结构起到 自导 向 的作用 ,保证 了切削精度 。这时冷却液通过钻头 中间的通道 到 达切削部位 ,并将切 屑从 排屑槽带 出工 件表 面 ,同时对钻刃进
(2)枪钻技术在数控 车床上加 工深孔零 件的现状 。有些企 业仍然采用传统技术生产深孔零件 ,不 仅生 产效 率低 下 ,而且 零件质量不高 ,造成人力 、物力 、财力 大量耗 费 ,企业效益不乐 观 。所 以说先进 的设备 、领先 的技 术 、良好 的团队技术人员对 于企业 的发展前途是非常重要 的。如果企业都引进枪钻技术 在数控车床上加工深孔零件 ,这样 就节 约了加工 成本 ,提高 了 生产效率 ,企业 的效 益也会 Et益提 高。
摘 要 :在科技快速发展的时代 ,枪钻技术在数控 车床上 的广泛应 用使 零件的质量逐步提 高 ,加 工效率也有 了很大 提 高。枪钻技术的应用,不仅 节约 了资金 ,也降低 了企业生产成本 ,有利于企业的发展 。
德国TBT枪钻

在相同的加工条件下,通关更改钻头的刃磨角度可以影响被加工表面,切屑形状,孔径公差,孔的中心线偏移,排屑情况,被加工表面质量以及刀具寿命等。
TBT拥有多种标准刃磨角度,这些标准角度可以完成绝大部分情况下的加工要求:当遇到产生长铁屑或难切削的材料时使用特殊刃磨角度。在某些情况下,也可以采用错齿分屑或增加断屑阶的办法来加强断屑,提高加工质量。我们已经根据不同客户情况,为客户设计,改进,订制了许多特殊角度。标准型TBT单刃磨角度是按枪钻直径和被加工材质来调整,因此,我们推荐您使用TBT通用刃磨或TBT双轴刃磨机对您的刀具进行刃磨。
枪钻,曦信双刃枪钻是深孔钻的一种,其直径范围为4-25mm,长径比可以达30-40.这种刀具具有两个对称切削刃。双刃钻可以采用整体硬质合金式,也可以采用焊接式。双刃钻与单刃枪钻也有着相同的切削液循环系统,切削液经由两个进油孔供入切削刃部,切削液和切削和混合物由刀杆外部的排屑槽排出。由于双刃钻的容屑空间有限,因此它适用于加工易断易屑材料。
tbt枪钻钻柄分类:
目前标准件的钻柄规格为默认一下规格:
总长为500mm的默认为:12.7*38.1
总长为700mm的默认为:19.05*69.8
总长800mm以上的默认为:25*70
(详情了解:) 作Байду номын сангаас:姚树芳
tbt扩孔枪钻
tbt扩孔枪钻是种特殊刀具,用于在已经加工好的通孔上进行扩孔。加工时,切屑沿着进给方向排出。
tbt阶梯钻
tbt单刃阶梯钻,这种刀具在一次加工中可以加工出几种不同的孔径,这样可以满足阶梯加工的同轴度要 求。
Tbt枪钻整体硬质合金单刃阶梯钻,这种刀具的钻头和钻杆为一个整体,同普通单刃阶梯钻一样,这种刀具可 以在一次加工中可以加工出几种不同的孔径,从而满足阶梯孔之间的最高同轴要求,整体硬质合金阶梯钻 的刀具总长可达350mm。
深孔钻加工的一个详细说明(枪钻功能)
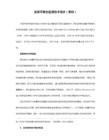
在深孔加工环节中孔的偏斜度,是深孔加工质量一个重要的技术指标。特别是在实际过程中,对零件的加工要求越来越高,对偏斜度相应的提出了更高的要求。尤其是深度较深的孔,如何控制孔偏斜量就显得尤为重要了。切削参数的选择是否合理对偏斜度也有一定程度的影响。在不影响生产进度的情况下,不宜采用大的走刀量。走刀量的加大会对孔的偏斜带来负面影响。
直线度:1/1000
同心度:1/1000或更好
孔直径公差:±0.0127mm
光洁度:4Ra
适用于交叉孔、平底盲孔
重复性好
可实现一次贯穿的加工方式
(详情了解:) 文章作者:姚树芳
为避免刀具过热发生变形影响加工精度和延长其使用寿命,通常使用切削液。要解决减少或免除切削液带来的问题,刀具镀层不仅应使刀具具有长寿命,且应有自润滑的功能。类金刚石涂层的出现在对某些材料的机械加工方面显示出优势,但经过多年的研究表明类金刚石涂层的内应力高、热稳定性差和与黑色金属间的触媒效应使SP3结构向SP2转变等三种缺点,决定了它目前只能应用于加工有色金属,因而限制了它在机加工方面的进一步应用。
专业的枪钻系统由深孔钻机、单刃或双刃的枪钻及高压冷却系统组成,使用时,枪钻钻头通过导引孔或导套进入工件表面,进入后,钻刃的独特结构起到自导向的作用,保证了切削精度。
冷却液通过钻头中间的通道到达切削部位,并将切屑从排屑槽带出工件表面,同时对钻刃进行冷却和对背部的支撑凸台进行润滑,从而获良好的加工表面和加工质量。
目前刀具产品除了提高使用寿命外还要求减少切削时的污染,尽可能使用干切削。在不能完全取消切削液的时候,尽量做到其中只含防锈剂而无有机物,这样可以使循环回收的成本大为降低。
枪钻钻头磨刀角度表【免费下载】
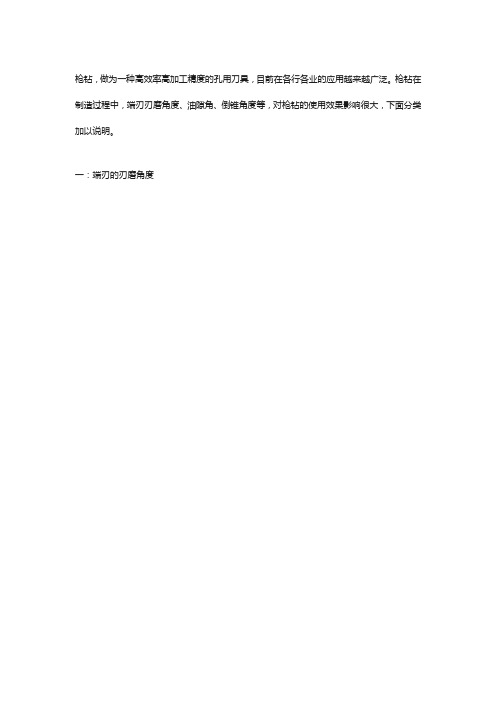
枪钻,做为一种高效率高加工精度的孔用刀具,目前在各行各业的应用越来越广泛。
枪钻在制造过程中,端刃刃磨角度、油隙角、倒锥角度等,对枪钻的使用效果影响很大,下面分类加以说明。
一:端刃的刃磨角度1.标准值:(摘自陕西金石机械制造有限公司2012年枪钻样册)2.特殊需要下的角度(摘自陕西金石机械制造有限公司2012年枪钻样册)2.1提高偏斜度和尺寸精度:外刃长于内刃,对加工孔的偏斜的控制有益处;另外,对于孔径尺寸有微量缩小的功用。
所以,当深孔偏斜度要求较高,或者加工孔径尺寸偏大的情况下,可以采用下图的方法刃磨枪钻。
当内刃长于外刃时,枪钻的加工孔径会略有增大。
所以,当加工的孔径尺寸偏小的情况下,可以采用外刃短于内刃的方式来尝试减小孔径尺寸。
2.2 不易断屑材料的加工:减小枪钻内、外刃角度,即枪钻内外刃磨的更平一些,对加工断屑有很大的帮助。
另外,切削线速度的提高,对断屑效果也很明显。
加工不易断屑材料时,枪钻端刃可以参考如下角度:2.3 枪钻内外刃的后角大小对加工偏斜度的影响。
当孔径<φ10mm时,适当的加大刀具后角,会减小枪钻加工过程中的阻力,对加工孔的偏斜度会有明显改善。
参见下图。
补充说明:刀具后角加大,会对刀具的强度造成负面影响。
所以应当逐步增加角度,以免造成刀具崩刃,降低刀具使用寿命。
对于硬度较高的材料(HRC30以上),不宜采用加大刀具后角的方法。
二:枪钻油隙类型与实际应用枪钻的油隙是指枪钻切削平面后部的圆柱支撑的形状。
不同的油隙形状,在枪钻加工过程中,对枪钻的润滑效果,支撑效果不同。
依据大量实验得知,不同的油隙,因为润滑效果和支撑效果不同,会对枪钻的使用寿命,钻孔尺寸精度,内孔粗糙度等,均有明显的影响。
现将常用的油隙形式整理如下:G形油隙:应用最广泛的油隙结构。
如无特殊要求,油隙通常都会采用该种结构;称之为低油隙。
此种油隙的刀具,最大直径已经无法测量。
实测量刀头尺寸通常会小于名义尺寸0.015mm左右。
深孔钻削应用指南

深孔钻削应用指南深孔钻削可采用多种机床安装方式:工件旋转,刀具做进给运动;工件不动,刀具旋转又做进给运动;工件旋转,刀具做反向旋转又做进给运动。
具体采用何种方式则依据工件特征及所加工孔的情况而定。
目前常用的深孔钻削加工系统有枪钻系统、BTA单管钻系统、喷吸钻系统。
它们代表着先进、高效的孔加工技术,通过一次走刀就可以获得精密的加工效果,加工出来的孔位置准确,尺寸精度好;直线度、同轴度高,并且有很高的表面光洁度和重复性。
能够方便的加工各种形式的深孔,对于特殊形式的深孔,比如交叉孔、斜孔、盲孔及平底盲孔等也能很好的解决。
上述深孔加工系统可达到加工精度孔径尺寸:lT6~lT11表面粗糙度: Ra0.2~ Ra6.3um直线度: <0.3mm/1000mm偏斜度:≤1mm/1000mm下图为最常用的两种深孔钻削加工刀具:枪钻和BTA单管钻深孔钻削的最主要特征1.极高的材料去除率;在正常加工条件下钻削深孔均一次贯穿,无需中途退刀;能获得极佳的孔径尺寸精度、直线度、表面粗糙度,并能加工各种形式的深孔,如交叉孔,盲孔,斜孔等;加工质量的高度一致性。
当钻削深孔时,整个切削过程对刀具、机床及其相关设备有着极高的要求。
2.深孔加工是处于封闭或半封闭的状态下,故不能直接观察到刀具的切削情况。
目前只能凭经验,通过同声音、看切屑、观察机床负荷及压力表、触摸震动等外在现象来判断切削过程是否正常。
3.切削热不易传散。
一半切削过程中有80%的切削热被切屑带走,而深孔钻削只有40%,刀具占切屑热得比例较大,扩散迟、易过热,刀口温度可达600℃,必须采取强制有效地冷却方式。
4.切屑不易排出。
由于孔深,切屑经过的路线长,容易发生堵塞,造成钻头崩刃。
因此,切屑的长短和形状要加以控制,并要进行强制性排屑。
5.工艺系统刚性差。
因受孔径尺寸限制,孔的长径比较大,钻杆细而长,刚性差,易产生震动,钻孔易走偏,因而支撑导向极为重要。
这点在枪钻机床中更为突出。
枪钻和深孔钻的区别【一文搞懂】

首先简述一下深孔钻。
深孔钻是一款专门用于加工深孔的钻头,其可分为外排屑和内排屑两类。
在机械加工中通常把孔深与孔径之比大于6的孔称为深孔。
深孔钻削时,散热和排屑困难,且因钻杆细长而刚性差,易产生弯曲和振动。
一般都要借助压力冷却系统解决冷却和排屑问题。
深孔钻按排屑方式分为外排屑和内排屑两类。
外排屑的有枪钻、深孔扁钻和深孔麻花钻等;内排屑的因所用的加工系统不同,分BTA深孔钻、喷射钻和DF深孔钻3种。
深孔钻分为枪钻、单管钻、喷吸钻,所以,枪钻属于深孔钻的一员。
深孔钻:1、属于外排屑专用深孔加工刀具。
v型角为160°。
2、深孔钻系统专用。
3、冷却及排屑方式为脉冲式高压雾装冷却。
4、有普通硬质合金及涂层刀头两类。
而枪钻属于外排屑专用深孔加工刀具。
v型角为120°。
枪钻是一种有效的深孔加工刀具,其加工范围很广,从模具钢材,玻璃纤维、特氟龙(Teflon)等塑料到高强度合金(如P20和铬镍铁合金)的深孔加工。
在公差和表面粗糙度要求较严的深孔加工中,枪钻可保证孔的尺寸精度、位置精度和直线度。
要想使枪钻加工深孔时能够达到满意的效果,必须熟练掌握枪钻系统的性能(包括刀具、机床、夹具、附件、工件、控制单元、冷却液和操作程序)。
操作者的技术水平也很重要。
根据工件的结构及工件材料的硬度以及深孔加工机床的工作情况和质量要求,选择适当的切削速度、进给量、刀具几何参数、硬质合金牌号和冷却液参数,才能获得优异的加工性能。
枪钻:1、属于外排屑专用深孔加工刀具。
v型角为120°。
2、枪钻专用机床使用。
直径深孔数控枪钻机床设计

小直径深孔数控枪钻机床设计摘要::枪钻机床主要采用的是外排屑深孔钻削技术。
枪钻系统主要由中心架、导向排屑器、钻杆联结器和冷却润滑油路系统组成。
枪钻系统的工作原理是:切削液通过钻杆箱上受油孔进入钻杆内部,到达钻头头部进行冷却润滑,并将切屑从钻头外部的V型槽排出。
该系统主要用于小直径的深孔加工。
数控枪钻机床的主电机通常是交流电机,进给电机选用直流伺服电机,主轴箱的电机选用变频电机。
系统运动方式为直线控制系统,以便进行平行与机床主轴轴线的钻削加工。
主运动系统是钻头的旋转运动,为了合理选择钻削速度,使其换速平稳,实现不停车自动换速,选无极变速系统。
进给运动系统是主轴的直线运动,为保证一定的传动精度和平稳性,尽量减小摩擦力,选用滚珠丝杠直线导轨传动。
通过枪钻机床设计,阐述了枪钻在数控车床上的深孔应用,包括枪钻的加工原理和枪钻的结构以及机床各部件。
这里包括进给系统设计,主轴箱的设计,授油器的设计,工作台的设计。
这说明:枪钻具有加工精度高,加工时间短,钻头寿命高,排屑好的特点,尤其应用在数控车床上,相对应用专用的枪钻设备来说,所需的工装夹具少,备件少,成本低。
本课题还介绍了D F系统的工作原理及授油器原理,并将DF系统机理应用于外排屑深孔钻削中,设计出了外排屑小直径深孔钻削系统。
本文从经济性、实用性出发,针对小直径深孔钻削系统进行了较为详细的介绍,对外排屑DF系统的主要装置授油器作了详细的设计说明。
关键词:小直径深孔枪钻;数控车床;主轴箱;授油器;钻削系统The Design of Small Diameter Deep Hole Drilling MachineCNC gunAbstract: Gun drill machine is mainly outside the BTA deep hole drilling technique. Gun drill system consists of center frame ,oriented chip conveyor ,drill pipe couplings and cooling lubricating oil system components. Gun drill system works by:cuting fluid through the drill pipe into the drill hole by the boxes within,cooling and lubicationg to reach the head drill,and drill cutings from the discharge outside the V-groove.The syetem is mainly used for small diameter deep hole C gun drill machine are usually AC motor of main motor,feed motor DC servo motoe selction,headstock frequecy electrical motor selection .Mode of motion is linear control syetem for parallel with the axis of the drilling spindle.Main movetment is a bie of rotation syetem for drilling speed to a reasonable choice and to smooth exchange rate,without stopping the automatic change-speeg,infinitely variable speed selection systen.Feed motion is the main axis of linear motion systems,in oder to guarantee the transmission accuracy and smoothness to minimize friction,use ball screw linear guide drive.Thruogh the gun drill machine tool design,demonstrates the application for hole machining of gun drill, contains machining theory,structure and various parts of machine tools.The design has feeding system ,headstock,oil coolet grant and table.It shows that gun drill has characteristic on high precision ,quic machine ,long life ,good chip break,especially application on NC laths,it takes on less tools and spare parts ,low cost.The main topics on the DF system and the principle of Oil granted,and DF system mechanism for debris from outside escape of chips deep hole drilling,designed the small diameter deep hole drilling system. This article from the economic,practical starting, for small diameter deep hole drilling system a more detailed introduction and outside escape of chips DF system's main oil installations award for a detailed description of the design.Key words:small-diameter deep-holes gun drill;NC laths; headstock; oil coolet grant; drilling system目录1 绪论 (1)1.1本课题的背景及研究目的 (1)1.2国内外研究现状 (2)1.3枪钻机床的特点和设计 (2)1.4枪钻的结构 (4)1.5课题的研究方法 (4)1.6深孔加工的类型及特点 (5)1.6.1 深孔加工的特点 (5)1.6.2 深孔加工中要解决的主要问题 (5)2 深孔加工系统的类型及选择 (7)2.1常用深孔加工系统的简介 (7)2.1.1 枪钻系统 (7)2.1.2 BTA系统 (7)2.1.3 DF系统 (8)2.1.4 喷吸钻系统 (8)2.2DF系统的设计理论 (9)2.2.1 外排屑DF系统 (9)2.2.2 DF系统的抽屑机理 (10)3 数控枪钻机床总体方案设计 (12)3.1总体方案的设计 (12)3.2小直径数控枪钻机床钻削系统的设计 (13)3.2.1 授油器的分类及原理 (13)3.2.2 授油器的结构设计 (15)3.2.3 主轴箱的设计 (16)3.2.4 带传动的设计 (20)4 枪钻机床进给系统设计 (24)4.1进给系统的组成及特点 (24)4.2进给系统的电机选择 (25)4.3滚珠丝杠幅的安装 (25)4.4滚珠丝杠幅的计算 (27)4.5滚珠丝杠幅的防护和润滑 (32)4.6滚珠丝杠在高速数控机床上的应用 (32)4.7联轴器的选择 (33)4.8导轨的选择 (34)结论 (38)参考文献 (39)1绪论1.1本课题的背景及研究目的在机械加工过程中,经常会碰到深孔加工的难题,而深孔钻削在核能,航空航天,石油和天然气等行业有着广泛的应用。
深孔钻枪钻钻孔具有的优点

深孔钻枪钻钻孔具有的优点
1.在小深孔加工范畴,它几乎是唯一的最有效的刀具,长径比越大,优越性越显著。
2.生产效率高,由于转速高,所以进给量在30~180mm/min以上,而且连续进给,不需要中途退刀排屑。
3.较稳定的孔径尺寸,及孔径变化范围较小,一般可稳定地获得H9级精度的孔,在条件较好时,也可达到H8级精度
4.被加工孔表面粗糙度较高,标准钢材可达Ra1.6~0.8以下,有色金属可达Ra0.4~0.05,铸铁Ra0.8以下。
5.高的形位公差,孔圆度<0.005mm,轴线平行度<0.2mm/1000mm (要根据孔径和材料的硬度确定)
6.适应范围广,被加工材料硬度大HRC45,仍可加工。
7.刀具耐用度高,加工钢材为4~15m/刃磨一次,铸铁约为100m/刃磨一次,铝约为380m/刃磨一次。
刀头一般允许重磨10-20次,其寿命是相当可观的。
8.孔钻通后,孔口无飞边、毛刺。
枪钻使用

2. 深孔(枪)钻系统基本组成:
深孔(枪)钻系统由 WHP 脉冲式冷却液与压缩空气混合雾化装置;混合 油气管及喷嘴;深孔(枪)钻专用夹持套筒和深孔(枪)钻钻头组成。当使用 小直径钻头,机床转数不能满足深孔(枪)钻切削速度要求时,需在夹持套筒 与机床主轴间安装固定速比为 1:3.81 的增速器。
3. 深孔(枪)钻系统(雾化装置)工作原理:
到可满足需要的长度(钻科公司可提供枪钻钻头的最大长度为 3000mm)。
4.4. 主轴增速装置的选用:
由于钻头直径小,而机床主轴转数不能满足枪钻的切削速度(参见表 6)
时,应选用主轴增速器,钻科公司提供固定速比为 1:3.81 的主轴增速器。
4.5. 挡水环的选择:
为保护机床主轴应选用与枪钻直径相匹配的挡水环。
按逆序先停止进给,再停止主轴转动和喷雾,主轴停止转动后再将钻头退出。
6. 刃(修)磨
6.1. 深孔(枪)钻钻头切削刃和后刀面出现明显磨损;刀口切削边缘起毛,至 使无法顺利排屑;或发生粘刀、切屑卷曲、切削时刀杆颤抖等现象,无法通过
调整切削参数制止时,钻头需要重新刃(修)磨。
6.2. 加工不同材质的标准钻刃研磨及支撑肩部轮廓搭配示意
表1
编号 D1 L2 D2
L1
L3 莫氏
Part mm mm mm
mm
mm 锥柄号
TH-31 16 40 31.75 88.90 24.13 1
TH-32 25 50 45.97 113.03 30.99 2
TH-33 25 50 45.97 113.03 30.99 3
切削主轴旋转式:摩式锥柄夹持套筒
4.1.4. 将乳化切削油按 1:10 比例混合好后装满油箱。 4.1.5. 将喷嘴连接到安装于机床主轴的钻头夹持套筒上。 4.2. 深孔(枪)钻尾端驱动柄夹持套筒的选择。
枪钻的简要介绍可达精度

枪钻的简要介绍可达精度在机加行业,钻头钻孔孔深达到或超过15×D时我们就称为深孔加工了,枪钻能加工甚至更深的孔.枪钻加工的孔有更高的表面光洁度,同轴度和直线度.近年来,带内冷的钻孔刀具越来越普及.冷却液也能及时有效地被输送到被加工部位.这大大提高了钻头,丝锥等刀具的寿命,降低了崩刃和断刀的概率.目前市场上的内冷刀具都能使用较高压力故也能加工较深的孔.枪钻可在加工中心,车床等设备上使用. 该工艺在机加行业也已越来越普及.注所有的枪钻在加工过程中必须要有支引导孔或钻套支撑。
枪钻在没有支撑的情况下不能全速旋转。
在普通机床上使用枪钻在普通设备上使用枪钻的步骤为:·引导孔的加工(公差H8).低转速快进给地进入到引导孔内,一般n=200rev./min, F=500mm/min. 钻深超过40XD时,要求枪钻反转进入引导孔。
·打开冷却液同时提升转速.·按照正常的切削参数一次性加工到要求深度.·加工到预定深度后关闭冷却液.·停转并快速退刀.建议:· 在加工深度超过40×D时我们推荐用两支或更多枪钻由浅到深来加工·枪钻长度超过40×D时,要求枪钻反转进入引导孔.·在加工长屑材料时我们建议选用排屑槽抛光的枪钻.·单刃枪钻加工长屑铝时我们建议选用平头(180°)带冷却倒角的头部形式.· 加工Si含量<1%的铝合金,如,分段提速,最终速度Vc>160m/min.另外,要求约3XD的预钻孔。
在专机上使用枪钻单刃枪钻的精度基本公差单刃枪钻加工的孔能达到一个较紧的基本公差,因其切削刃不对称,加工时的径向切削力只能通过侧面支撑条的反作用力而抵消,而不象麻花钻径向切削力几乎为零故而易导致孔径偏大直线度因为焊硬质合金枪钻是把高精度的硬质合金头部焊在韧性极好的钢管上,故孔能达到一很高的直线度.然而,工件材料及其它不利因素都会影响到孔的精度.表面质量加工时的径向切削力通过支撑导条而作用在孔壁,可使孔表面因挤压作用而更加光亮.故支撑导条和孔壁之间的润滑就非常重要.润滑越好,孔表面光洁度就越高.同轴度例如当用麻花钻加工孔时,钻尖的修磨质量(对称性)直接影响着孔的同轴度.而单刃枪钻其不对称的径向切削力,使侧面支撑导条始终紧贴在孔表面,从而确保能达到很高的孔的同轴度.孔直线度偏差。
枪钻使用技巧

( 2 )在车床上 ,按上序的顶尖孔中心找正 ,直 径还有 1 m余量 , .m 5 外圆车两段找正带; ( 3 )在枪钻上 ,按找正带找正,按修正的引导
封面图片 :由中国一重制造的四台 出口印度 BN IA反应器在一 重加氢反 应器制造基地码头待海运 用麻 花 钻加 工 细长 孔 时 ,
由于加工件内部夹渣 、气孔等缺陷导致钻头走偏的 现象。由于麻花钻是双刃切削刀具,加工中自动寻 求两刃切深均匀 ,使所受径向力相等 ,以达到平
01 . m通 孔 ; 55 m
()在 车床上 ,重新 检测后 ,内孔 与外 圆孔 同 4
() 在镗 床上 ,在孔 偏 的一端 ,按 01 m孔 1 2m 按 低 点 扩 至 01. m 55 m,5 m 深 的引 导 孔 ,精 铰 0m 引导孔 ,重 修顶尖 孔 ;
4 结 语
随着不锈钢 、耐热合金等管类产品的不 断增 加 ,枪钻的应用范围将越来越广,其使用技术也将 会不 断发展 和提 高 。
2 刃磨角度和切 削参数
()垂直角度+ 2 ; 1 3 。
21 刃磨角 度 .
( 2 )水平角度 0 。 , 。
用枪钻加工不锈钢和耐热合金材质产品时 ,对 刃磨角度应有特殊要求 ( 见图 1 图 5 。 一 )
图 3 钻 尖后面刃磨角度
( 1 )垂直角度+ 4 ; 1。 ()垂直角度+ 8 ; 1 1。
如 某 产 品加 工 一根 管 的 01 l中心通 孔 后 , 2mi l
发现其同轴度加工误差达到 0 m的问题 。而内 4 m 孔 最终尺 寸为 01.mm,现外 圆为 0 0m 55 5 m,外 圆 最终尺寸为 0 4 m 4 .m 。如果按常规工艺方案按内 5 孑 找正 ,则外圆必须加工到 0 2 m方可修正。 L 4 m 现采用枪钻进行修正,其工艺方法如下 :
枪钻加工原理及参数分析

枪钻加工原理及参数分析摘要:在金属深孔加工中,排屑及刀具寿命一直是难题,枪钻作为深孔加工的刀具之一,其切削刃参数及断屑排屑能力是影响枪钻使用寿命的主要因素。
本文通过对硬质合金枪钻钻头部分受力、断屑机理以及切削液供给的分析,提出合理的参数,改善枪钻切削条件。
关键词:枪钻断屑切削液枪钻加工系统由深孔钻机、硬质合金枪钻和高压冷却系统组成。
加工时,硬质合金枪钻通过工件自身导孔或导套进入工件,由于枪钻的独特结构,在钻削时能自导向,减少震动。
由于具有高压内冷却系统,枪钻能够连续进给且具有较高的切削速度,无需中途退刀排屑。
冷却液通过内通道到达切削部位,并将切屑带出v形排屑槽,同时能对刀具冷却并在工件切削表面形成润滑膜,降低刀具磨损。
本文主要分析外排屑枪钻的加工参数选择,其适用于加工φ2~φ20mm、长径比大于100、表面粗糙度ra12.5~3.2μm、精度it10~it8级的深孔。
1、硬质合金枪钻的结构硬质合金枪钻由钻头、钻杆、钻杆三部分组成(图1),钻头通常分为整体硬质合金、硬质合金镶片式、切削刃部分焊接cbn刀片整体硬质合金三种系列;钻头有单圆孔、双圆孔和肾形孔三种形式的冷却孔;钻头部分有小倒角,使钻杆外径小于钻头外径0.05~1mm,防止切削时摩擦已加工孔壁。
钻杆一般采用低碳或者低合金无缝钢管轧制成110~120°的v形槽,要求钻杆有足够的强度在小变形下提供钻削所需的扭矩;同时钻杆的有足够的韧性,以便吸收高速旋转所产生的震动。
2、硬质合金枪钻切削原理2.1.1钻头参数枪钻钻头的几何参数如图2所示。
其中α1为外角、α2为内角、α3α4分别为外刃第一、二后角、α5为钻尖后角、α6为内刃后角、α7与α2差值为油隙角、l为外刃宽度、d为钻头外径。
2.1.2受力分析枪钻钻头受力分析图如图3所示。
图3中f1为外刃法相力、f2为内刃法相力、fy1为外刃径向力、fy2为内刃径向力、fx1为外刃轴向力、fx2为内刃轴向力。
枪钻概述
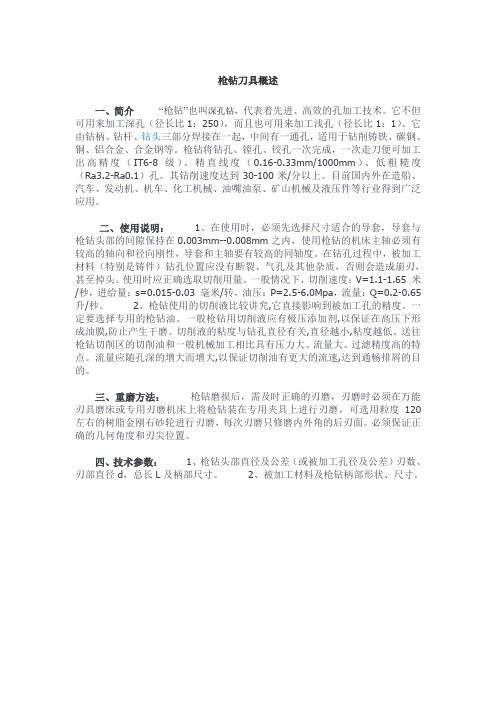
枪钻刀具概述一、简介“枪钻”也叫深孔钻,代表着先进、高效的孔加工技术。
它不但可用来加工深孔(径长比1:250),而且也可用来加工浅孔(径长比1:1)。
它由钻柄、钻杆、钻头三部分焊接在一起,中间有一通孔,适用于钻削铸铁、碳钢、铜、铝合金、合金钢等。
枪钻将钻孔、镗孔、铰孔一次完成,一次走刀便可加工出高精度(IT6-8级)、精直线度(0.16-0.33mm/1000mm)、低粗糙度(Ra3.2-Ra0.1)孔。
其钻削速度达到30-100米/分以上。
目前国内外在造船、汽车、发动机、机车、化工机械、油嘴油泵、矿山机械及液压件等行业得到广泛应用。
二、使用说明:1、在使用时,必须先选择尺寸适合的导套,导套与枪钻头部的间隙保持在0.003mm--0.008mm之内,使用枪钻的机床主轴必须有较高的轴向和径向刚性,导套和主轴要有较高的同轴度。
在钻孔过程中,被加工材料(特别是铸件)钻孔位置应没有断裂、气孔及其他杂质,否则会造成崩刃,甚至掉头。
使用时应正确选取切削用量。
一般情况下,切削速度:V=1.1-1.65 米/秒,进给量:s=0.015-0.03 毫米/转,油压:P=2.5-6.0Mpa,流量:Q=0.2-0.65 升/秒。
2、枪钻使用的切削液比较讲究,它直接影响到被加工孔的精度。
一定要选择专用的枪钻油。
一般枪钻用切削液应有极压添加剂,以保证在高压下形成油膜,防止产生干磨。
切削液的粘度与钻孔直径有关,直径越小,粘度越低。
送往枪钻切削区的切削油和一般机械加工相比具有压力大、流量大、过滤精度高的特点。
流量应随孔深的增大而增大,以保证切削油有更大的流速,达到通畅排屑的目的。
三、重磨方法:枪钻磨损后,需及时正确的刃磨,刃磨时必须在万能刃具磨床或专用刃磨机床上将枪钻装在专用夹具上进行刃磨,可选用粒度120左右的树脂金刚石砂轮进行刃磨,每次刃磨只修磨内外角的后刃面。
必须保证正确的几何角度和刃尖位置。
四、技术参数:1、枪钻头部直径及公差(或被加工孔径及公差)刃数、刃部直径d,总长L及柄部尺寸。
深孔钻头之枪钻的概述及其分类
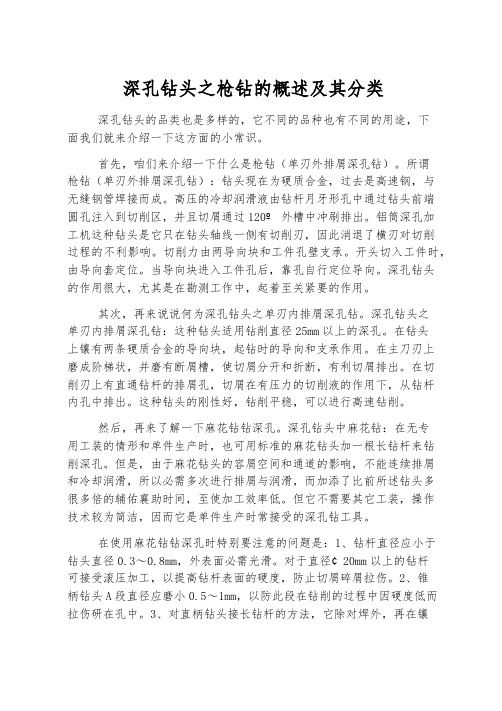
深孔钻头之枪钻的概述及其分类深孔钻头的品类也是多样的,它不同的品种也有不同的用途,下面我们就来介绍一下这方面的小常识。
首先,咱们来介绍一下什么是枪钻(单刃外排屑深孔钻)。
所谓枪钻(单刃外排屑深孔钻):钻头现在为硬质合金,过去是高速钢,与无缝钢管焊接而成。
高压的冷却润滑液由钻杆月牙形孔中通过钻头前端圆孔注入到切削区,并且切屑通过120º外槽中冲刷排出。
铝筒深孔加工机这种钻头是它只在钻头轴线一侧有切削刃,因此消退了横刃对切削过程的不利影响。
切削力由两导向块和工件孔壁支承。
开头切入工件时,由导向套定位。
当导向块进入工件孔后,靠孔自行定位导向。
深孔钻头的作用很大,尤其是在勘测工作中,起着至关紧要的作用。
其次,再来说说何为深孔钻头之单刃内排屑深孔钻。
深孔钻头之单刃内排屑深孔钻:这种钻头适用钻削直径25mm以上的深孔。
在钻头上镶有两条硬质合金的导向块,起钻时的导向和支承作用。
在主刀刃上磨成阶梯状,并磨有断屑槽,使切屑分开和折断,有利切屑排出。
在切削刃上有直通钻杆的排屑孔,切屑在有压力的切削液的作用下,从钻杆内孔中排出。
这种钻头的刚性好,钻削平稳,可以进行高速钻削。
然后,再来了解一下麻花钻钻深孔。
深孔钻头中麻花钻:在无专用工装的情形和单件生产时,也可用标准的麻花钻头加一根长钻杆来钻削深孔。
但是,由于麻花钻头的容屑空间和通道的影响,不能连续排屑和冷却润滑,所以必需多次进行排屑与润滑,而加添了比前所述钻头多很多倍的辅佑襄助时间,至使加工效率低。
但它不需要其它工装,操作技术较为简洁,因而它是单件生产时常接受的深孔钻工具。
在使用麻花钻钻深孔时特别要注意的问题是:1、钻杆直径应小于钻头直径0.3~0.8mm,外表面必需光滑。
对于直径¢20mm以上的钻杆可接受滚压加工,以提高钻杆表面的硬度,防止切屑碎屑拉伤。
2、锥柄钻头A段直径应磨小0.5~1mm,以防此段在钻削的过程中因硬度低而拉伤研在孔中。
3、对直柄钻头接长钻杆的方法,它除对焊外,再在镶装部磨两个坑后焊好,磨圆即成。
- 1、下载文档前请自行甄别文档内容的完整性,平台不提供额外的编辑、内容补充、找答案等附加服务。
- 2、"仅部分预览"的文档,不可在线预览部分如存在完整性等问题,可反馈申请退款(可完整预览的文档不适用该条件!)。
- 3、如文档侵犯您的权益,请联系客服反馈,我们会尽快为您处理(人工客服工作时间:9:00-18:30)。
枪钻系列刀具的特点及应用
一般钻削孔深与孔径之比大于10的孔,被称为深孔钻削。
由于长径比较大,采用一般的麻花钻来钻削时,排屑、冷却、润滑和导向就成了难以解决的题目,孔的质量要求也很难达到。
德国钴领刀具有限公司集百年专业生产孔加工刀具的丰富经验及二十多年深孔加工领域的专业枪钻制造为基础,开发出以下具有深孔加工领域领先技术的枪钻系列刀具:
EB100单刃整体硬质合金枪钻:
加工范围:Ф1.2-5.0mm,最大槽长300mm,几乎适用于所有材料加工。
EB80单刃焊硬质合金刀头枪钻:
加工范围:Ф2-40mm,总长最大达3000mm,几乎适用于所有材料加工。
ZB80双刃焊硬质合金刀头枪钻:
加工范围:Ф6-27mm,总长最大达1000mm,适用于铸铁、铝和短铁屑非金属材料的加工。
一、枪钻的工作原理
枪钻工作时,冷却液被高压泵通过循环冷却系统经钻杆内部送进切削部分,以冷却和润滑刀具,并依靠冷却液的压力再将切屑从孔的内壁与钻杆上的“V”型槽排出。
工作时,枪钻可由机床主轴带动旋转加工,也可枪钻固定而工件旋转,工件旋转时加工出的孔的形位公差更好。
二、枪钻的结构
枪钻由钻尖、钻杆和刀柄三部分组成。
钻尖
钻尖部分是枪钻的最重要部分,它担负着重要的钻削工作,为了保证被加工孔的精度,在它的圆周部分设计有导向块,其在导向孔的引导下一次进刀就可以加工出高精度的孔。
钻尖结构形式根据不同的加工条件有多种类型可供选取。
钻尖材料则采用钴领公司自身研究开发的高品质DK460UF超细晶粒硬质合金,并涂以TiN、FIRE或MolyGlide涂层,具有非常高的硬度和韧性,极大地进步了枪钻的钻削性能和使用寿命。
钻杆
钻杆通常呈“V”型结构设计,外径略小于钻尖,在保证钻杆足够的强度和刚度的条件下,钻杆的冷却液孔和排屑空间尽可能做到最大,以利于钻尖部分的冷却、润滑和排屑。
EB100系列钻杆采用与钻尖一体化硬质合金磨制而成。
EB80 、ZB80系列钻杆则采用高等级无缝钢管轧制而成。
刀柄
刀柄部分主要用来传递动力。
钴领公司可提供十三大类,总共42种规格的标准刀柄供客户选择,并可承接非标刀柄的定制。
三、钻尖部分的结构形式
钻尖部分的几何外形,直接影响到枪钻的切削加工性能及被加工孔的精度,钴领公司结合自身二十多年制造枪钻的成功经验,优化了以下5种类型的钻尖外圆型式,并结合多种钻尖的不同角度磨削型式供用户选择,确保针对不同的工件材料及要求,总有一款适合您。
G型:通用型,适合加工各种材料,尤其适合加工孔公差范围较小的孔。
C型:标准型,适合加工难加工材料,如高合金钢等。
E型:专用型,适合加工各种材料,尤其适合加工孔公差范围较大的孔。
A型:专用型,适合在难以正确定位的状况下加工各种材料。
D型:专用型,特别适合加工灰铸铁。
四、枪钻的用途
枪钻往往做成单刃刀头形式,它一般适用于加工Φ2-Φ20mm直径的小径深孔,长径比可达80倍,枪钻最长可达3000mm,被加工工件的表面粗糙度为Ra0.4-1.6,孔径精度为IT7-9级,孔的直线性高,并且孔口无毛刺,精度的重复性好。
广泛适用于汽车制造业、飞机船舶制造业和机床制造等行业,主要加工对象为:缸体、缸盖、曲轴和各种引擎零件等。
钴领系列枪钻可应用于深孔加工专机、加工中心、车削中心等满足枪钻冷却及导向等要求的设备上对碳钢、不锈钢、铸铁、有色金属及木材、塑料等材料进行加工,钴领公司可针对客户的机床状况,提供最优化的切削工艺参数,确保发挥枪钻最高的切削性能。
为了使枪钻能长期稳定可靠地工作,钴领公司还为本公司系列枪钻匹配有小巧可靠的台式修磨枪钻系列装置:TBM116、TBV116;这两套修磨夹具结构紧凑,占地面积小,简便易用,通过短暂的培训,用户就可以用该夹具修磨出接近原刀的几何参数尺寸,确保修磨后的枪钻
达到接近新刀的加工性能及质量。
配套提供的粗、精磨一体化金钢石砂轮:
DSS125,可以保证枪钻在一次装夹中完成粗、精修磨,极大地进步了修磨的效率及质量。
配套的刀具附件:钻套、密封套和支撑座等,则为枪钻的顺利钻削保驾护航。