城市轨道交通钢轨探伤技术检测系统
城市轨道交通钢轨的智能化监测与诊断系统

城市轨道交通钢轨的智能化监测与诊断系统随着城市轨道交通的快速发展和规模的不断扩大,轨道交通的安全和运行效率成为了社会关注的焦点。
而钢轨作为轨道交通的基础设施之一,其状态的监测和诊断对于保障轨道交通的安全和稳定运行具有重要意义。
为了实现城市轨道交通钢轨的智能化监测与诊断,提升城市轨道交通的安全性和运行效率,钢轨监测与诊断系统应运而生。
一、智能化监测技术1. 引言智能化监测技术是指利用先进的传感器、无线通信、大数据和人工智能技术等手段,对城市轨道交通的钢轨进行全方位的状态监测和数据采集,并通过数据分析和处理,为钢轨的维护、保养和诊断提供有力的支持。
2. 传感器技术传感器技术是智能化监测系统的核心,可实现对钢轨的位移、应力、温度等关键参数的实时监测。
通过精准的传感器数据,可以快速捕获钢轨的异常情况,并及时采取相应的维修措施,保障轨道交通的运行安全。
3. 无线通信技术无线通信技术是实现智能化监测的重要手段之一,通过建立无线通信网络,可以将传感器采集到的数据迅速传输至监测中心。
同时,无线通信技术也可以实现远程维护和诊断,提高钢轨监测的效率和准确度。
4. 大数据和人工智能技术大数据和人工智能技术可以对传感器采集到的海量数据进行深度学习和分析,从而实现对钢轨状态的智能诊断。
通过建立智能化的模型和算法,系统可以自动判断钢轨是否存在异常,并提供相应的维护建议。
二、智能化诊断系统1. 数据采集与管理智能化诊断系统通过传感器对钢轨进行全方位的数据采集,并将采集到的数据经过处理、存储和管理。
通过建立合理的数据管理机制,可以实现对钢轨状态的长期监测和分析。
2. 数据分析与诊断智能化诊断系统通过对采集到的数据进行分析和处理,提取出关键信息,如钢轨的应力分布、变形情况和磨损程度等。
通过与预设的模型和算法进行对比,系统可以判断钢轨是否处于正常状态,并对异常情况进行诊断。
3. 维护建议与预测智能化诊断系统可以根据对钢轨状态的诊断结果,提供相应的维护建议。
钢轨表面缺陷非接触检测系统-精选文档
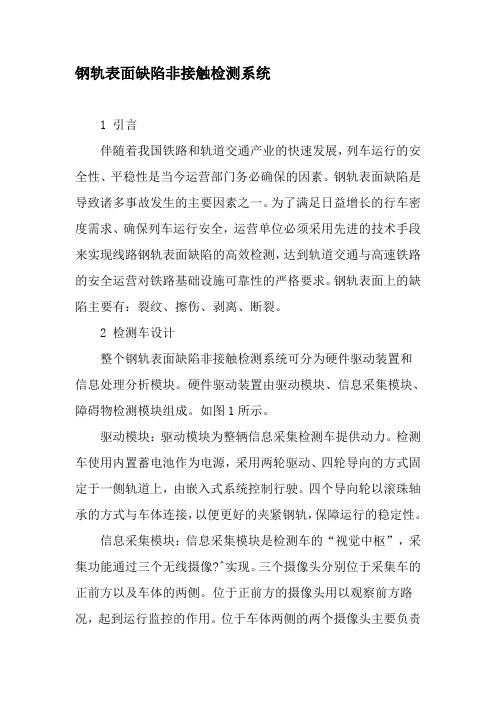
钢轨表面缺陷非接触检测系统1 引言伴随着我国铁路和轨道交通产业的快速发展,列车运行的安全性、平稳性是当今运营部门务必确保的因素。
钢轨表面缺陷是导致诸多事故发生的主要因素之一。
为了满足日益增长的行车密度需求、确保列车运行安全,运营单位必须采用先进的技术手段来实现线路钢轨表面缺陷的高效检测,达到轨道交通与高速铁路的安全运营对铁路基础设施可靠性的严格要求。
钢轨表面上的缺陷主要有:裂纹、擦伤、剥离、断裂。
2 检测车设计整个钢轨表面缺陷非接触检测系统可分为硬件驱动装置和信息处理分析模块。
硬件驱动装置由驱动模块、信息采集模块、障碍物检测模块组成。
如图1所示。
驱动模块:驱动模块为整辆信息采集检测车提供动力。
检测车使用内置蓄电池作为电源,采用两轮驱动、四轮导向的方式固定于一侧轨道上,由嵌入式系统控制行驶。
四个导向轮以滚珠轴承的方式与车体连接,以便更好的夹紧钢轨,保障运行的稳定性。
信息采集模块:信息采集模块是检测车的“视觉中枢”,采集功能通过三个无线摄像?^实现。
三个摄像头分别位于采集车的正前方以及车体的两侧。
位于正前方的摄像头用以观察前方路况,起到运行监控的作用。
位于车体两侧的两个摄像头主要负责采集钢轨表面图像,检查钢轨病害。
采集到的图像通过无线技术传回计算机,达到检测目的。
障碍物检测模块:障碍物检测模块是检测车的自我保护模块,用以实现检测车遇到前方钢轨上有异物无法通过时的制动功能。
该功能不需要人工操控。
传感器发出一个红外信号,如果有障碍物,则接收头就会收到反馈信号,进而采取制动,避免发生碰撞。
3 钢轨表面缺陷算法研究本系统使用halcon软件作为工具完成检测功能,由于摄像头采集图像的不确定性,必须对图像进行滤波、图像增强等处理。
本算法分为图像预处理及图像特征提取两部分。
3.1 图像预处理图像预处理部分包括图像输入、图像增强、图像降噪、钢轨表面定位及分割钢轨背景五个流程。
通过无线信号将采集到的图像传输回计算机并转换为灰度,就完成了图像输入的流程。
无损检测 轨道交通双轨探伤 超声检测系统 征求意见稿编制说明

中国材料与试验团体标准无损检测超声检测轨道交通双轨探伤超声检测系统编制说明一、标准编制说明内容1、工作简要过程,来源、主要参加单位和工作组成员等依据中国铁路总公司印发的《双轨式钢轨超声波探伤仪暂行技术条件》(TJ/GW157-2017)和参与的铁路总公司重大课题项目《高铁钢轨浅表层缺陷快速检测关键技术研究及装备研制》,国家科技部重大科学仪器开发专项《在役钢轨缺陷综合检测监测设备开发与应用》,每年需对轨道交通双轨探伤设备进行技术状态鉴定,轨道交通双轨探伤采用动态标定方式,铺设低速、高速试验线,建立由静态到动态、低速到高速的探伤标定体系,保证检测数据的精准,对轨道交通双轨探伤设备的技术发展及应用提供重要的指导作用。
该项目的实施,不仅可以促进我国探伤装备产业的发展,同时对我国机械设备制造业及冶金、材料生产的发展也具有十分重要的推动作用,对促进相关技术和产业进步,扩大社会就业,产生积极的影响。
国内主要采用的是超声波检测方法,检测形式主要有大型高速探伤车、中速双轨电动探伤车以及手推式单轨探伤车。
其中超声波检测基本采用水轮探头,与钢轨滚动式接触,可搭载在大型高速探伤车和中速双轨电动车上。
由于超声波检测技术在近表面有反射杂波,所以只能检测钢轨内部的较大缺陷。
国内外工业对超声检测技术的发展十分重视,IlW以及各工业发达国家的相关学术机构均设置了专门委员会,以协调和促进超声检测技术的发展。
世界最早的钢轨检测技术由美国SPeITy公司于1928年研发,由于技术发展早,工业生产水平高,至今美国已拥有世界领先的无损检测技术。
英、德、日等传统工业强国在无损检测及钢轨检测领域也开展了许多研究并取得了突出的成果,其相应的设备和产品在国际上占据了主要的市场,有举足轻重的作用。
随着科技的不断发展,多种无损检测手段被用于钢轨检测行业。
SPeiTy公司研制的大型高速探伤车,其最高检测速度可达80km∕h,搭载超声波水轮探头,可实现实时在线检测,可对缺陷进行标定和类型判断,检测钢轨内部和轨底的缺陷。
城市轨道交通钢轨探伤技术检测系统
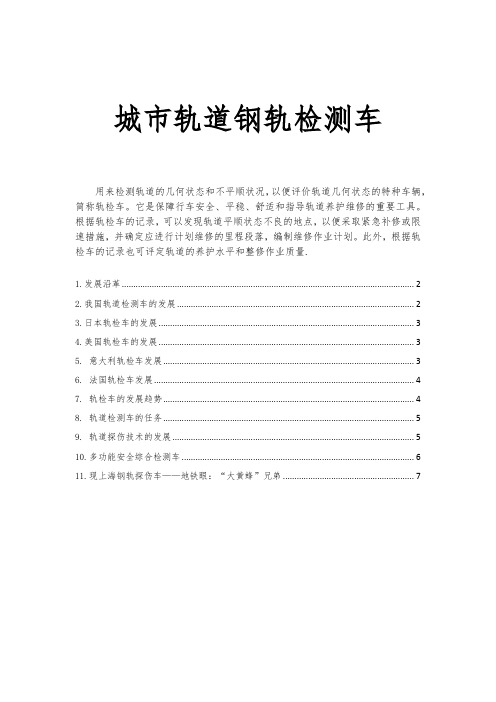
城市轨道钢轨检测车用来检测轨道的几何状态和不平顺状况,以便评价轨道几何状态的特种车辆,简称轨检车。
它是保障行车安全、平稳、舒适和指导轨道养护维修的重要工具。
根据轨检车的记录,可以发现轨道平顺状态不良的地点,以便采取紧急补修或限速措施,并确定应进行计划维修的里程段落,编制维修作业计划。
此外,根据轨检车的记录也可评定轨道的养护水平和整修作业质量.1.发展沿革 (2)2.我国轨道检测车的发展 (4)3.日本轨检车的发展 (4)4.美国轨检车的发展 (5)5. 意大利轨检车发展 (5)6. 法国轨检车发展 (6)7. 轨检车的发展趋势 (7)8. 轨道检测车的任务 (7)9. 轨道探伤技术的发展 (8)10.多功能安全综合检测车 (10)11.现上海钢轨探伤车——地铁眼:“大黄蜂”兄弟 (11)1.发展沿革早期轨道状态采用人工检测,19世纪70年代出现了轨道检查小车。
用人力推行小车和机动的检测小车进行检测。
用这些方法检查不能反映轨道在列车车轮荷载作用下的几何状态。
因此在19世纪70~80年代,欧洲有些国家开始研究在普通客车上装备检测设备,并出现了一些雏型的轨道检查车。
20世纪初,俄国、德国和美国铁路正式使用轴重较大的客重式机械轨检车,检测在轮载作用下的轨道几何状态,开创了轨道动态检测新阶段。
机械轨检车是借助检测车轮、重铊、杠杆、滑轮、弹簧等机件,由钢丝绳直接牵动绘图笔在纸带上记录检测的结果。
这种轨检车的检测速度低,误差大。
20世纪50年代末,苏、日等国制成电气轨道检查车。
此后各种电测装置逐渐取代了机械检测系统。
70年代以前的轨检车,都用弦测法和接触检测小轮来测量轨道的不平顺状况。
弦测法的测量值随测量弦的长度与轨道不平顺波长的比值变化,测得的高低等波形,往往与实际轨道不平顺情况有较大的差异。
接触检测小轮在高速时,因惰性等影响,误差较大。
近十多年来,由于行车速度提高,运量增大,需进一步提高轨道的不平顺性,要求更准确地测出轨道不平顺波形,因而促进了轨道检测新技术的发展。
基于人工智能的钢轨探伤车智能诊断系统研究

基于人工智能的钢轨探伤车智能诊断系统研究摘要:随着铁路行业的快速发展,钢轨的安全性备受关注。
钢轨探伤车被广泛应用于实地巡检和诊断,以保障铁路运输的安全性。
然而,传统的钢轨探伤车在诊断过程中存在着工作效率低下和诊断准确率不高的问题。
本研究旨在基于人工智能技术,设计一种智能诊断系统,以提高钢轨探伤车的工作效率和诊断准确率。
通过深度学习算法,结合图像处理技术和物体检测算法,实现对钢轨图像的智能分析和诊断。
本文将详细介绍该系统的设计与实现,并对其性能进行评估和分析。
1. 引言随着中国铁路行业的迅速发展,高速铁路和城市轨道交通网络的扩张,钢轨的安全性成为重要的议题。
由于钢轨的连续使用和受力状态,往往会产生各种缺陷,如裂纹、疲劳、腐蚀等。
这些缺陷如果得不到及时发现和处理,将对铁路运输的安全性造成严重威胁。
因此,加强钢轨的巡检和及早诊断成为必要的措施。
2. 相关工作钢轨探伤车已被广泛应用于铁路巡检和钢轨诊断,以取代传统的人工巡检方法。
然而,目前的钢轨探伤车在诊断过程中存在一些问题,如工作效率低下,诊断准确率不高,无法及时发现细小缺陷等。
为了解决这些问题,一些研究者提出了多种改进方案,如图像处理、机器学习等技术的应用。
3. 方法与实现本研究提出了一种基于人工智能的钢轨探伤车智能诊断系统,该系统由图像采集设备、图像处理模块和诊断算法三个主要部分组成。
首先,通过图像采集设备获取钢轨的图像数据。
然后,利用图像处理技术对图像进行预处理,包括图像去噪、图像增强等。
接着,采用深度学习算法进行物体检测和分类,识别出钢轨上的各类缺陷。
最后,根据缺陷的位置和程度,对钢轨进行诊断和评估,并生成诊断报告。
4. 系统性能评估为了评估该智能诊断系统的性能,我们进行了一系列实验。
首先,采集了不同类型缺陷的钢轨图像,建立了钢轨图像数据集。
然后,利用数据集对系统进行训练和测试,并评估其诊断准确率和工作效率。
实验结果表明,该系统具备较高的诊断准确率和较快的工作效率,能够有效帮助铁路运输部门提高钢轨的安全性。
城市轨道交通钢轨无损检测技术分析
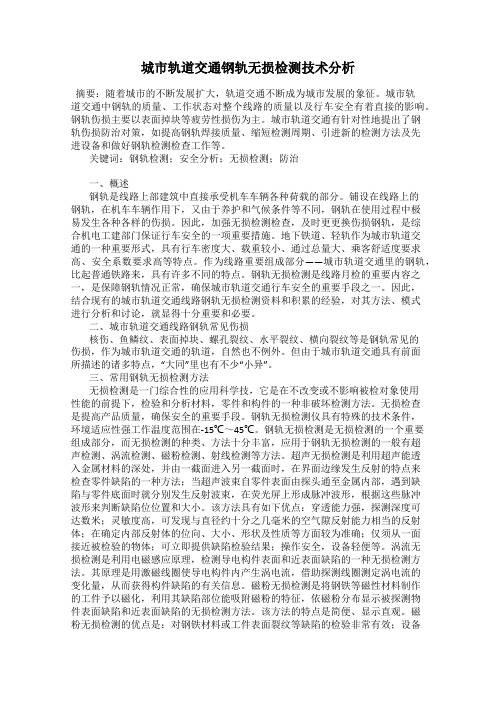
城市轨道交通钢轨无损检测技术分析摘要:随着城市的不断发展扩大,轨道交通不断成为城市发展的象征。
城市轨道交通中钢轨的质量、工作状态对整个线路的质量以及行车安全有着直接的影响。
钢轨伤损主要以表面掉块等疲劳性损伤为主。
城市轨道交通有针对性地提出了钢轨伤损防治对策,如提高钢轨焊接质量、缩短检测周期、引进新的检测方法及先进设备和做好钢轨检测检查工作等。
关键词:钢轨检测;安全分析;无损检测;防治一、概述钢轨是线路上部建筑中直接承受机车车辆各种荷载的部分。
铺设在线路上的钢轨,在机车车辆作用下,又由于养护和气候条件等不同,钢轨在使用过程中极易发生各种各样的伤损。
因此,加强无损检测检查,及时更更换伤损钢轨,是综合机电工建部门保证行车安全的一项重要措施。
地下铁道、轻轨作为城市轨道交通的一种重要形式,具有行车密度大、载重较小、通过总量大、乘客舒适度要求高、安全系数要求高等特点。
作为线路重要组成部分——城市轨道交通里的钢轨,比起普通铁路来,具有许多不同的特点。
钢轨无损检测是线路月检的重要内容之一,是保障钢轨情况正常,确保城市轨道交通行车安全的重要手段之一。
因此,结合现有的城市轨道交通线路钢轨无损检测资料和积累的经验,对其方法、模式进行分析和讨论,就显得十分重要和必要。
二、城市轨道交通线路钢轨常见伤损核伤、鱼鳞纹、表面掉块、螺孔裂纹、水平裂纹、横向裂纹等是钢轨常见的伤损,作为城市轨道交通的轨道,自然也不例外。
但由于城市轨道交通具有前面所描述的诸多特点,“大同”里也有不少“小异”。
三、常用钢轨无损检测方法无损检测是一门综合性的应用科学技,它是在不改变或不影响被检对象使用性能的前提下,检验和分析材料,零件和构件的一种非破坏检测方法。
无损检查是提高产品质量,确保安全的重要手段。
钢轨无损检测仪具有特殊的技术条件,环境适应性强工作温度范围在-15℃~45℃。
钢轨无损检测是无损检测的一个重要组成部分,而无损检测的种类、方法十分丰富,应用于钢轨无损检测的一般有超声检测、涡流检测、磁粉检测、射线检测等方法。
城市轨道交通轨检系统

城市轨道交通轨检系统1. 简介城市轨道交通轨检系统是指运用先进的技术和设备,对城市地铁、轻轨等轨道交通系统中的轨道进行检测和维护的系统。
该系统可以通过对轨道进行定期巡查和实时监测,帮助运营公司提前发现轨道的异常状况,并及时采取措施进行修复和维护,确保轨道交通系统的安全和正常运营。
2. 轨道检测技术城市轨道交通轨检系统采用了多种轨道检测技术,包括以下几种:2.1. 超声波检测超声波检测技术通过将超声波发射到轨道表面,然后接收回波进行分析,来判断轨道的状态。
该技术可以检测轨道的厚度、裂缝、腐蚀等问题,对于轨道的损伤程度和位置定位有较高的精度。
2.2. 磁粉探伤磁粉探伤技术通过在轨道表面涂覆磁粉,然后通过磁场的作用,对轨道表面的缺陷进行检测。
该技术可以检测到轨道表面的裂纹、疲劳、焊缝等问题,对轨道的损伤程度和位置定位有很高的准确性。
2.3. 红外热像技术红外热像技术通过检测轨道表面的温度分布,来判断轨道是否存在异常情况。
该技术可以检测到轨道表面的热点、温度差异等问题,对轨道的潜在故障有较高的敏感度。
2.4. 激光测量技术激光测量技术通过激光器发射激光束,然后通过接收激光束的反射信号,来测量轨道的几何参数。
该技术可以检测到轨道的水平、垂直度、几何偏差等问题,对轨道的形状和位置有很高的精度。
3. 轨道监测设备城市轨道交通轨检系统使用了多种轨道监测设备,包括以下几种:3.1. 轨道检测车轨道检测车是一种专门设计用于轨道检测的车辆,配备了各种轨道检测仪器和设备。
该车辆可以沿着轨道行驶,将检测数据实时传输到指挥中心,为轨道维护和修复提供关键的信息。
3.2. 轨道监测传感器轨道监测传感器可以安装在轨道上,用于检测轨道的各种参数。
传感器可以实时监测轨道的温度、震动、变形等情况,并将数据传输到指挥中心进行分析和处理。
3.3. 轨道监测系统轨道监测系统是城市轨道交通轨检系统的核心部分,包括数据采集、数据处理、数据分析和报警等功能。
钢轨轮廓检测系统及检测方法

钢轨轮廓检测系统及检测方法钢轨轮廓检测系统及检测方法本发明提供了一种钢轨轮廓检测系统及检测方法中,手持式三维扫描仪扫描设置有所述检测定位点的被测钢轨,以生成所述被测钢轨的三维模型,数据处理装置根据所述被测钢轨的三维模型获得所述被测钢轨的轮廓及测量分析报告。
本发明的钢轨轮廓检测系统运用过程中,携带更轻巧方便,测量更科学精准,可同时检测钢轨的横断面轮廓及纵断面轮廓,分析更直观可靠,降低了人力物力的耗费,提高了工作效率,满足本领域的实际需求。
【专利说明】钢轨轮廓检测系统及检测方法【技术领域】[0001] 本发明涉及测量【技术领域】,特别涉及一种钢轨轮廓检测系统及检测方法。
【背景技术】[0002] 铁路运输是我国运输事业的主要力量,它的发展直接制约着中国经济的发展。
随着铁路事业的飞快发展,高速、重载列车运行量的增加,钢轨的磨损也越来越严重。
钢轨磨损是钢轨质量参数中重要的一项。
钢轨磨损造成钢轨轮廓尺寸变化,恶化了轮轨动力,加大列车运行过程中事故发生的可能性,减少钢轨和机车的使用寿命。
铁路网的不断扩大和养护维修需求的增加对钢轨检测提出新的要求。
[0003] 钢轨轮廓尺寸变化是影响钢轨寿命的主要原因。
由于轮轨与钢轨长期接触,导致钢轨发生磨损,造成钢轨轮廓尺寸变化,减少了钢轨金属量,从而减少了钢轨使用寿命。
钢轨轮廓尺寸变化,也严重影响机车运行中的平稳性、安全性,也增加了轮轨动力,所W需要及时的对钢轨轮廓尺寸进行检测,保证列车的正常运行。
钢轨轮廓尺寸检测可W检测出的钢轨的磨损W及钢轨服边等问题,其检测结果决定着钢轨打磨的必要性W及打磨是否合格,对钢轨打磨有着重要的指导意义。
[0004] 目前,国内外的钢轨轮廓的检测方法主要是接触式和非接触式,其中,接触式测量的测量精度较高,但操作繁琐,测量效率低,测量精度低,且接触式测量所采用的装置只能完成横断面或纵断面的一种测量。
非接触式测量采用激光传感器和线性电机驱动同时测量钢轨横断面及纵断面,但非接触式测量的装置测量前需要固定在钢轨上或者固定在车辆上,便携性较差。
地铁轨道检测系统介绍

地铁轨道综合检测系统目录目录 01、系统简介 (2)2、功能与指标 (3)2.1 轨道几何参数测量 (3)2.2 钢轨伤损检测 (6)2.3 限界入侵(隧道断面)检测 (6)2.4 第三轨(导电轨)检测 (7)1、系统简介科技地铁轨道综合检测系统是移动测量技术在城市轨道综合检测中的具体应用。
其以轨道系统为平台,集成GNSS/惯性导航单元(IMU)/DMI组合定位定姿系统、3D激光扫描仪、线结构激光传感器、多传感器同步控制单元、嵌入式计算机以及电源供电系统等设备,组建轨道检测与测量平台,在同步控制单元的协调下使各个传感器之间实现时空同步,快速采集地铁轨道的全断面时空数据。
自主开发处理软件和算法对原始多元时空数据进行融合、处理,实现轨道几何尺寸(轨距、水平、高低、轨向、扭曲)、钢轨伤损(轨廓、剥离掉块、擦伤)、限界(隧道断面)以及接触网(导电轨)等参数的快速、智能检测与测量,并将检测结果以可视化图形、数字报表等方式输出给用户,为地铁轨道交通的日常运营和检修提供数据支撑和决策辅助。
图1a)检测系统构成图;b)检测系统工作状态;c)数据采集软件;d)数据后处理及可视化2、功能与指标地铁轨道综合检测系统检测运行速度为3-25km/h,系统的主要检测功能包括轨道几何参数测量、轨道伤损检测、限界入侵(隧道断面)检测、第三轨(导电轨)检测等四个方面。
下面依次对四个方面的功能进行介绍。
2.1 轨道几何参数测量轨道几何参数包括轨距、水平、轨向、高低、扭曲五个检测项目。
利用系统两端的线结构激光采集轨道上两边钢轨的内侧廓形,提取左右钢轨轨顶面并以轨顶面以下16mm处的距离作为轨距测量值。
利用系统的高精度定位定姿数据,辅以传感器间的标定参数,推算钢轨曲线,根据相应规范定义计算水平、轨向、高低、扭曲。
图2 轨道几何参数测量项目测量精度测量范围轨距0.1mm 1435±25mm水平0.2mm ±100mm轨向0.5mm/10m,2mm/30m高低1mm/10m,2mm/30m扭曲0.2mm/3m➢检测系统地铁内定位精度:当每60米一个控制点时,可实现0.05m的绝对定位精度。
钢轨损伤的无线传感网络监测系统
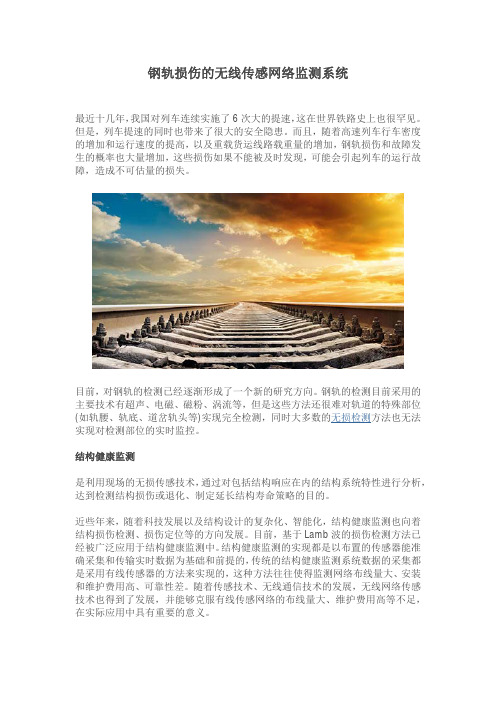
处的幅值都随着添加损伤长度的增加而不断减小,说明长度越长的损伤对信号的 散射越强,这使得接收到的信号越弱。通过对不同频谱的分析可以用来判断损伤 程度的大小。 为了直观显示不同长度损伤的接收幅值大小,通过 MATLAB 软件对得到的损伤 信号在 40kHz 处的峰值幅值进行拟合,从拟合的曲线可以更直观地观察出接收 信号的幅值与损伤长度变化的关系。
不同长度损伤接收信号
在图中的椭圆虚线标注的地方可以明显发现:无损以及其他不同长度损伤的接收 信号在此处有明显的差异,无损伤情况下的接收信号的幅值小于有损伤情况下的 幅值;而在有损伤情况下的接收信号中,其信号的幅值随着损伤长度的增大而增 大,这为损伤的判别提供了依据。
城市轨道交通轨检系统

唐源公司轨道检测系统检测原理—曲率
定义: 曲率测量定义为一定弦长的曲线轨道(如30M)对应之园心角θ (度/30 米)。度数大、曲率大、半径小;反之,度数小、曲率小、半径大。
轨检梁惯性包测得检测梁在轨道面上的转动角 积分并对30m基长作差,得到曲率
预留接口(波磨和扣件识别检测设备)
客户端
输出
中央数据处 理系统
线路数据库
惯性包
速度 里程
轨距 磨耗
轨向
高低
水平
三角 坑
车体加 速度
唐源公司轨道检测系统组成—设备布局
唐源公司轨道检测系统组成—检测梁布局
全断面轨检梁
由4台2D激光传感器及惯性包组成 惯性包含加速度传感器、陀螺、倾角仪等 采用最新设计轨检方案
唐源公司轨道检测系统简介
基于惯性基准的轨道不平顺测量装置、二维激光轨距测量装置和多 功能振动测量装置及强大的数据处理系统 检测快捷,准确,可靠,智能
适用于铁路及城市轨道交通(地铁、轻轨、有轨电车)等轨道几何 状态检测,是轨道科学维护管理的基础,同时也为轨道结构设计、
病害原因分析及维护标准制定等提供科学依据。
第四代轨道检测系统 由2台2D激光传感器、陀螺仪、倾角仪等组成
唐源公司轨道检测系统—应用展示
典型应用四
杭州地铁2号线轨道检测车
第五代轨道检测系统 由4台2D激光传感器、陀螺仪、倾角仪等组成
唐源公司轨道检测系统—应用展示
典型应用五
杭州地铁4号线轨道检测车
第五代轨道检测系统 由4台2D激光传感器、陀螺仪、倾角仪等组成
国内外轨检车简介
- 1、下载文档前请自行甄别文档内容的完整性,平台不提供额外的编辑、内容补充、找答案等附加服务。
- 2、"仅部分预览"的文档,不可在线预览部分如存在完整性等问题,可反馈申请退款(可完整预览的文档不适用该条件!)。
- 3、如文档侵犯您的权益,请联系客服反馈,我们会尽快为您处理(人工客服工作时间:9:00-18:30)。
城市轨道钢轨检测车用来检测轨道的几何状态和不平顺状况,以便评价轨道几何状态的特种车辆,简称轨检车。
它是保障行车安全、平稳、舒适和指导轨道养护维修的重要工具。
根据轨检车的记录,可以发现轨道平顺状态不良的地点,以便采取紧急补修或限速措施,并确定应进行计划维修的里程段落,编制维修作业计划。
此外,根据轨检车的记录也可评定轨道的养护水平和整修作业质量.1.发展沿革 (2)2.我国轨道检测车的发展 (4)3.日本轨检车的发展 (4)4.美国轨检车的发展 (5)5. 意大利轨检车发展 (5)6. 法国轨检车发展 (6)7. 轨检车的发展趋势 (7)8. 轨道检测车的任务 (7)9. 轨道探伤技术的发展 (8)10.多功能安全综合检测车 (10)11.现上海钢轨探伤车——地铁眼:“大黄蜂”兄弟 (11)1.发展沿革早期轨道状态采用人工检测,19世纪70年代出现了轨道检查小车。
用人力推行小车和机动的检测小车进行检测。
用这些方法检查不能反映轨道在列车车轮荷载作用下的几何状态。
因此在19世纪70~80年代,欧洲有些国家开始研究在普通客车上装备检测设备,并出现了一些雏型的轨道检查车。
20世纪初,俄国、德国和美国铁路正式使用轴重较大的客重式机械轨检车,检测在轮载作用下的轨道几何状态,开创了轨道动态检测新阶段。
机械轨检车是借助检测车轮、重铊、杠杆、滑轮、弹簧等机件,由钢丝绳直接牵动绘图笔在纸带上记录检测的结果。
这种轨检车的检测速度低,误差大。
20世纪50年代末,苏、日等国制成电气轨道检查车。
此后各种电测装置逐渐取代了机械检测系统。
70年代以前的轨检车,都用弦测法和接触检测小轮来测量轨道的不平顺状况。
弦测法的测量值随测量弦的长度与轨道不平顺波长的比值变化,测得的高低等波形,往往与实际轨道不平顺情况有较大的差异。
接触检测小轮在高速时,因惰性等影响,误差较大。
近十多年来,由于行车速度提高,运量增大,需进一步提高轨道的不平顺性,要求更准确地测出轨道不平顺波形,因而促进了轨道检测新技术的发展。
70年代前期,美、英、日等国相继采用惯性基准、无接触检测等先进技术,研制成功用电子计算机自动处理检测数据、能如实地反映轨道状态、检测速度达每小时200公里的现代化高速电子轨道检查车。
近年来,各国使用的现代轨道检查车由检测和数据处理系统(图1)、发电供电系统、空气调节系统、仪表工作室、了望台以及走行转向架等几部分组成。
其检测项目有轨道的高低、水平、三角坑、方向、轨距,以及里程和行车速度等。
有的还能测量曲线超高、曲率,以及高低方向等轨道不平顺的变化率、曲线通过的均衡速度等。
还有些现代轨检车通过测量车体和轴箱的振动加速度、轮轨作用噪声,以及轮轨间的垂直力、水平力、脱轨系数等,为更全面地评价轨道的状态提供依据。
现代轨检车能及时提供直观反映轨道状态的波形图,并能提供经车载计算机处理打印成的轨道状态报告表,以及记录在磁带上的轨道状态资料等。
有的还可在轨道状态严重不良和需紧急补修的地方,直接在轨道上喷上颜色标记。
将磁带记录送地面计算机进一步处理,便可编制出各种轨道状态管理图和轨道整修作业计划表。
2.我国轨道检测车的发展中国于1953年试制成功第一辆自己设计的客车式机械轨检车。
1971年又制成客车式电气轨检车。
图2为1971年中国制成的“TSK22”型电气轨道检查车。
这种电气轨检车长约26米,自重约62吨,能同中国的特快列车联挂进行检测。
这种电气轨检车采用旋转变压器作位移传感器,借助三个轮对所构成的18.5米不对称弦测量轨道高低,用三轴转向架的三个轮对构成的3.4米对称弦测量钢轨接头低陷;轨道水平状态由陀螺装置测量,三角坑由相距15.1米的两个轮对测得。
测量结果用电磁笔记录仪记录在纸带上。
70年代中期,中国开始进行轨检新技术的研究,现已先后研制出能测量轨道高低、水平、轨面不平顺的“惯性基准轨道不平顺检测装置”和“轨道超高检测装置”、“充电式轨距检测装置”、“多功能振动检测装置”等新装置。
目前正在进一步研制用这些新装置和其他先进设备(如电子计算机等)装备的新型轨道检查车。
3.日本轨检车的发展East-i综合检测列车可在一次运行过程中实现对线路的综合检测功能,但各检测项目之间的检测数据并不综合到一个统一的中心,各检测单元有各自独立的数据显示、记录、转储和地面分析、处理、维护管理决策等系统,全系统仅有位置、时间和速度是统一的。
一般认为,弦测法传递函数收敛性差,East-i采用了相应的修正方法。
由于弦测法不能全部真实反映轨道状况,在复原及逆滤波处理时仅能换算到40m 波长的测值,因此该方法存在一定的缺陷。
惯性基准法受速度影响较大,不适宜低速检测,在高速时更具优势。
另外,East-i整套设备及软件均为日本的品牌和自主开发的产品,与我国设备和软件的兼容性差,不利于系统的后续使用和二次开发。
4.美国轨检车的发展美国各铁路公司均拥有自主研发的轨检车,美国联邦铁路署还委托ENSCO 公司研制了技术先进的T10型轨检车,用于抽查各铁路公司的线路质量。
T10型轨检车采用惯性基准测量原理和非接触式测量方法,应用光电、伺服、数字滤波、局域网技术,最近还增加了钢轨断面测量系统,使轨检车的功能更加齐全,检测速度可达192km/h。
ImageMap公司研制的Laserail轨道测量系统采用激光摄像、高速图像处理技术取代了光电伺服技术,体现了轨道检测技术的发展方向。
它采用惯性基准原理、非接触式测量方法,系统包括两个光纤陀螺和两个加速度计及其模拟处理板,4个激光器、10台摄像机等,可测量轨距、左右轨向、左右高低、超高、水平、三角坑、曲率、钢轨顶磨和侧磨等。
检测速度可达300km/h。
5. 意大利轨检车发展“阿基米德号”综合检测列车又称Roger2000,是MER MEC公司和TECNOGAMMA公司为意大利铁路设计制造的,检测速度可达220km/h。
检测项目包括轨道几何参数、钢轨断面、钢轨波浪磨耗、接触网及受流状态、通信和信号、车体和轴箱加速度、轮轨作用力等。
车上有57台计算机,每秒钟可处理30G数据,有24个激光器、43个光学摄像传感器、47个加速度计以及大量的强度速度、定位以及温度传感器,以及用于航空电子领域的惯性平台。
意大利高速铁路使用“阿基米德号”综合检测列车已经形成了一整套检测和维修养护体制。
综合检测列车各子系统有独立的存储数据库,在速度、时间、空间上保持同步,所有子系统的检测数据集成到车载中央数据库,由中央数据库将数据通过无线网络传输到地面的RFI数据处理中心进行综合分析、比较,从而制定科学的维修保养计划,指导养护维修。
其轨道检测在较低速度时采用弦测法,在较高速度时采用惯性基准法,较好地发挥了两种测量原理的优势。
6. 法国轨检车发展MGV是专为法国高速铁路研制的综合检测列车,该车检测速度设计为320km/h,检测周期预计为两周一次,设计目标是在列车正常运行条件下检测各项基础设施参数,于2006年6月投入运用。
MGV综合检测列车车辆由法国铁路公司(SNCF)指定,拟采用法国既有成熟的动力集中式TGV动车组。
SNCF作为该车检测系统的集成商,各子系统通过国际公开招标方式采购。
该车检测项目比较齐全,几乎包括了从接触网及受流状态、通信信号、轨道几何、钢轨断面、钢轨表面、线路环境数字图像、扣件、轨枕、道碴等各项基础设施和运行状态。
7. 轨检车的发展趋势现代化轨检车有两种代表性检测系统。
英国、加拿大采用了由传感器、模拟计算机、数字、计算机组成的捷联式系统。
美国ENSCO公司的轨检车采用了由传感器、模拟与数字混合处理组成的捷联式系统,由于模拟及数字处理特征相匹配,各误差信号进行完善修正与补偿,轨检结果不受速度和运行方向的影响,具有很高的一致性。
因此,传感器、模拟及数字混合处理捷联式系统是将来高速轨检车发展的主要方向。
高速线路上,轨道的短波不平顺,如波浪磨耗、扁疤、焊接部分的凹凸不平等,引起轮对对轨道的巨大动力作用,并产生强噪声,长波不平顺将降低旅客乘车舒适度指标。
因此,扩大不平顺检测波长范围,是高速轨检车发展中必须解决的一个重要课题。
现代化轨检车中,计算机不单单是轨检数据处理的工具,在模拟数字混合处理轨检系统中,计算机还是轨道几何参数检测的重要组成部分。
微机轨检数据检测处理将在轨检车上广泛发展8. 轨道检测车的任务检查——依据确定的评价指标,在一定程度范围内检测,评价轨道状态和养护水平计划——根据不同等级线路提出的安全度和舒适度要求,提出恢复到设计状态所需要进行的维修保养计划分析——提供轮轨关系在行车、科研、养路等方面的原始数据并进行整理分析,用以加强科学管理,提高养路水平9.轨道探伤技术的发展铁路是较早开展无损检测工作的部门之一,钢轨探伤是无损检测技术应用的一个重要领域,由于钢轨在使用过程中会因应力作用产生各种疲劳裂纹,如检测不及时,会造成钢轨断裂,以至于引起列车颠覆,中断交通等恶性事故,因而各国对钢轨探伤都十分重视,不惜投入大量人力物力对现役钢轨进行定期检测,以便及早发现疲劳伤损,防止断轨,确保安全。
在探伤设备和手段方面,国内外有较大差别。
目前国外钢轨探伤主要使用大型探伤车,小型设备一般只用来复查大型探伤车的检测结果。
目前探伤车探伤速度大多在20~50km/h。
德国拟把电磁声技术运用到钢轨探伤车上,准备研制探伤速度在70km/h以上的探伤车,但此项目目前还没有正式投入使用,探伤车的工作方式多采用停顿式,即探伤线路是封闭的,发现伤损马上停下来手工复核,一旦确认立即换轨,目前这点在我国也很难做到。
美国、德国、法国、澳大利亚、俄罗斯等国都可以设计和生产钢轨探伤车,有些国家还少量出口。
美国PJT公司生产的SYS—1000型探伤车是较有代表性的具有90年代先进水平的探伤车,我国成都铁路局等使用的是该型进口探伤车,国内生产的GT3型大型探伤车,其检测系统就是SYS—1000,探伤速度可达40km/h。
国外钢轨探伤部门一般与铁路运输部门是分离的,也就是说探伤部门和铁路部门分属不同的公司,铁路部门将探伤工作以合同形式委托给探伤公司,铁路部门只负责提供必要的探伤条件,探伤公司则要根据铁路部门要求定期对钢轨进行检验。
这种做法的优点在于责任明确,工作上避免人为的干扰,铁路部门可以不必配备大量的探伤人员和设备,而探伤公司则可按照探伤工作固有规律开展工作,履行职责。
这样打破了探伤技术和设备的行业所有,有利于发挥探伤人员的积极性,真正做到人尽其才,物尽其用。
在激烈的市场竞争中,迫使探伤部门不断完善更新自己的探伤技术、设备和提高探伤人员素质,有利于探伤技术水平的提高。
另外,国外在探伤方面的投资也很大,许多国家都建有钢轨探伤的研究中心或探伤设备的生产基地。
如美国的SPERY公司、PJT公司,康州大学;德国的明登机械研究所、弗琅霍费研究所;法国的MATIX公司等,都有很强的钢轨探伤研究能力和探伤设备的生产能力。