江鑫钢铁10流方圆坯连铸机设计特点
一套R10m十机十流方圆坯连铸机技术平台(可编辑)

1 以高起点高效率为原则确保将项目建设成为具有先进水平科技
含量高经济效益好资源消耗少人力资源优势得到充分发挥的现代化
2 合理选择生产工艺和技术对各生产环节的生产工艺附件进行严
格科学的论证采用先进可靠的技术现代化高效化的设备配置紧凑合
理的总图布置实现企业的最低成本和最佳的经济效益
连铸机工艺技术在连铸生产中起着至关重要的作用本章就临沂
手动夹持装置
液压控制单元
技术参数
表 3-8 技术参数
数量 10×2 套快换结构四支缸
形式 带 有推 进液 压缸 的
快速更换装置
推进液压缸行程 300mm 液压介质供应 单
独液压站 塞棒自动执行机构
功能和结构
塞棒自动执行机构安装在中间罐体上用于在浇注过程中控制中
间罐至结晶器的钢水流量流量由结晶器液面控制系统控制
技术参数
表 3-3 技术参数
数量 2 套
形式 半自动
长水口压紧方式 液压
旋转方式 减速器
摆动方式 手动 前后移动 手动
水口密封气体 氩气 参数以最终设计为准
中间罐
功能与结构
中间罐采用钢板焊接结构内部砌耐火砖
罐体上设有吊耳方便中间罐的吊动和检修更换中间罐上设有挡
块方便中间罐盖在中间罐上的定位同时中间罐上设有加工好的安装
辅助设备包括液压管线阀块控制阀台等
技术参数
表 3-12 技术参数
型式 高低轨式 承载能力 ~80t 行走机构 行 走 驱 动 装
置 变频电机减速器驱动
行走驱动电机功率 75KW×2
行走速度 2~20mmin 变频可调 升降机构 升 降 驱 动 型 式
液压缸 一组 4 个
升降行程 ~400mm
方板坯兼用连铸机的设计特点

方板坯兼用连铸机的设计特点许剑豪【摘要】主要结合湘潭引进的2号方板坯连铸机,介绍了其在线主要设备的设计特点;该铸机也是为数不多的能生产高合金钢的方板坯连铸机;目前该铸机设备运行稳定、可操作性高、易于维护,且生产的方、板坯内部和外部质量均满足要求.同时还介绍了国内其他几种型号的方、板坯兼用的连铸机,并对这几种型号机的优缺点进行了讨论和比较.【期刊名称】《山西冶金》【年(卷),期】2018(041)005【总页数】3页(P56-58)【关键词】方板坯;连铸机;设计【作者】许剑豪【作者单位】中冶京诚工程技术有限公司,北京 100176【正文语种】中文【中图分类】TF777.1目前国内钢材市场波动较大,方坯和板坯产品价格也交替波动,因此有越来越多的钢厂寻求一机多能,以适应市场的变化。
目前大部分的方、板坯连铸机的设计均以板坯连铸机为基础,在板坯连铸机的基础上进行变化,本文主要介绍湘潭从S-VAI引进的方板坯连铸机的设计特点。
该铸机也是为数不多的能生产高合金钢的方、板坯连铸机。
该铸机只需要更换结晶器和弯曲段,就可以实现板坯和方坯之间的生产互换。
1 方、板坯连铸机的主要技术参数(见表1)表1 方、板坯连铸机的主要技术参数2 方、板坯连铸机的设计特点通常板坯连铸机的设备比方(矩)型坯连铸机复杂,因此在设计方、板坯兼容的连铸机时,一般都是在板坯连铸机为基础上进行变化,在保证板坯连铸机正常生产的情况下,兼顾满足方坯生产的需求;本文介绍的方、板坯兼容的连铸机就是这样的形式,因此以下内容主要介绍不同于普通板坯连铸机部分。
2.1 回转台及中间罐车设计回转台及中间罐车在浇注方板和板坯时通用,与普通板坯连铸机的设计类似,在此不再描述。
2.2 中间罐设计中间罐采用T型结构,中间罐上设计有3个彼此独立的开孔,用于安装式水口(如下页图1)。
浇注板坯时,堵住边上2个水口,采用浸入式水口快换装置[1-3];而浇注方坯则采用整体式水口并配事故闸板(如下页图 2)。
347-其他资源-连铸机型及特点

1.3 连铸机的机型及其特点按结晶器是否移动可以分为两类:☆固定式结晶器(包括固定振动结晶器)的各种连铸机如立式连铸机、立弯式连铸机、弧形连铸机、椭圆形连铸机、水平式连铸机等;☆同步运动式结晶器的各种连铸机这种机型的结晶器与铸坯同步移动,铸坯与结晶器壁间无相对运动,适合于生产接近成品钢材尺寸的小断面或薄断面的铸坯,如双辊式连铸机、双带式连铸机、单辊式连铸机、单带式连铸机,轮带式连铸机等。
按铸坯断面形状分为:方坯连铸机圆坯连铸机板坯连铸机异型连铸机方/板坯兼用型连铸机按钢水的静压头分为:高头型低头型超低头型连铸机连铸机机型示意图1—立式连铸机;2—立弯式连铸机;3—直结晶器多点弯曲连铸机 4—直结晶器弧形连铸机;5—弧形连铸机;6—多半径弧形(椭圆形)连铸机;7—水平式连铸机同步运动结晶器连铸机机型1—双辊式连铸机;2—单辊式连铸机3—双带式连铸机;4—单带式连铸机;5—轮带式连铸机立式连铸机20世纪50年代至60年代的主要机型。
立式连铸机从中间包到切割装置等主要设备均布置在垂直中心线上,整个机身矗立在车间地平面以上。
1—钢包;2—中间包;3—导辊;4—结晶器;5—拉辊;6—切割装置;7—移坯装置采用立式连铸机浇注时,由于钢液在垂直结晶器和二次冷却段冷却凝固:钢液中非金属夹杂物易于上浮铸坯四面冷却均匀不受弯曲矫直应力作用产生裂纹的可能性较小铸坯质量好,适于优质钢、合金钢和对裂纹敏感钢种的浇铸。
立弯式连铸机立弯式连铸机是连铸技术发展过程的过渡机型。
立弯式连铸机是在立式连铸机基础上发展起来的,其上部与立式连铸机完全相同,不同的是待铸坯全部凝固后,用顶弯装置将铸坯顶弯90o C,在不同方向切割出坯,它主要适用于小断面铸坯的浇铸。
弧形连铸机弧形连铸机的结晶器、二次冷却段夹辊、拉坯矫直机等设备均布置在同一半径的1/4圆周弧线上;铸坯在1/4圆周弧线内完全凝固,经水平切线处被一点矫直,而后切成定尺,从水平方向出坯。
我国合金钢方坯连铸机现状及设计要点

我国合金钢方坯连铸现状及设计特点周干水中冶连铸技术工程股份有限公司1. 前言在国外,特殊钢的生产比例不断提高,20世纪80年代初期工业发达国家的生产比例达到了总产量的15~30%(其中优质碳素结构钢占特殊钢的17~24%),已基本实现连铸生产。
而我国优质钢生产技术起步较晚且以优质碳结钢为主(占优质钢的76%),特殊钢产量较低、质量较差,90年代以前基本以模铸生产主。
2. 我国合金钢连铸机的现状2.1 我国合金钢连铸技术的发展过程在国际上合金钢连铸已经是完全成熟的技术,几乎能浇注所有钢种,如碳结钢、合结钢、弹簧钢、工具钢、不锈钢、轴承钢等。
由于我国特殊钢的生产主要集中在一些平炉、电炉厂,且以小型电炉厂居多,主要采用模铸-开坯-轧制成材生产工艺。
因此,我国的合金钢连铸技术起步较晚,直到80年代中期才开始引入连铸技术,受生产规模、厂房条件、资金条件、生产设备状况、生产经验等多种因素的影响,连铸机机型小、产量低、配置不完善,很多采用水平连铸机或小半径的连铸机,技术装备及设计特性与普通连铸机无多大区别,如一些生产厂采用R5.25m或R6m铸机生产弹簧钢、高碳钢及40Cr 等合结钢。
大部分水平连铸机为国内自主开发,技术装备低、生产能力低下。
为适应世界市场及国内市场的需要,90年代以后,我国合金钢连铸技术得到了迅猛的发展,早期主要以引进为主,部分钢厂通过技术改造或配套,在已有普通连铸机上生产中低碳优质碳结钢及一般合结钢等,并取得了一定效果,现阶段合金钢方坯连铸已基本达到国产化,板坯及超大方坯尚无成功国产化设计的先例。
2.2 我国合金钢连铸机的基本特点我国合金钢连铸机的建设主要表现为如下四种形式:(1). 原有特殊厂在进行炼钢系统的技术改造的同时,纷纷建造合金钢连铸机,如:长城特钢、大冶特钢、陕西特钢、重庆特钢、西宁特钢、无锡钢厂等。
其中一些小型钢厂由于资金等原因,早期采用引进二手设备或国产化设备技术装备水平普遍较低,产量规模较小,设备配置不完善,从而造成生产陷入困境、生产率低下;一些规模较大的钢厂采用引进全新设备与技术,生产效率高,合金钢生产比例较高,质量稳定。
连铸机的特点
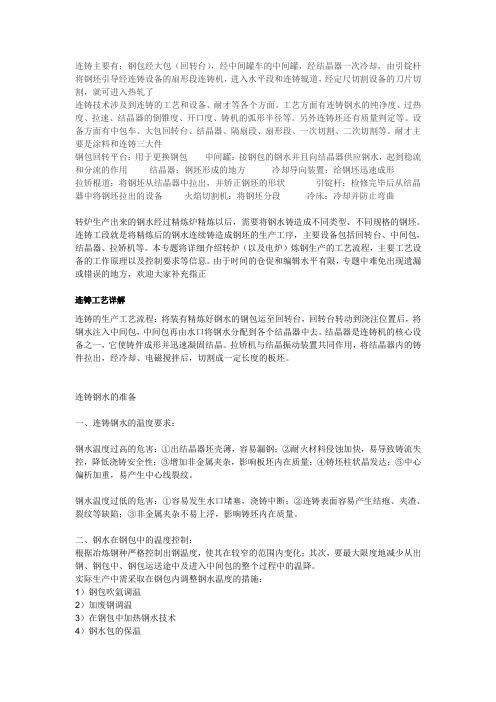
连铸主要有:钢包经大包(回转台),经中间罐车的中间罐,经结晶器一次冷却,由引锭杆将钢坯引导经连铸设备的扇形段连铸机,进入水平段和连铸辊道,经定尺切割设备的刀片切割,就可进入热轧了连铸技术涉及到连铸的工艺和设备、耐才等各个方面。
工艺方面有连铸钢水的纯净度、过热度、拉速、结晶器的倒锥度、开口度、铸机的弧形半径等。
另外连铸坯还有质量判定等。
设备方面有中包车、大包回转台、结晶器、隔扇段、扇形段、一次切割、二次切割等。
耐才主要是涂料和连铸三大件钢包回转平台:用于更换钢包中间罐:接钢包的钢水并且向结晶器供应钢水,起到稳流和分流的作用结晶器:钢坯形成的地方冷却导向装置:给钢坯迅速成形拉矫棍道:将钢坯从结晶器中拉出,并矫正钢坯的形状引锭杆:检修完毕后从结晶器中将钢坯拉出的设备火焰切割机:将钢坯分段冷床:冷却并防止弯曲转炉生产出来的钢水经过精炼炉精炼以后,需要将钢水铸造成不同类型、不同规格的钢坯。
连铸工段就是将精炼后的钢水连续铸造成钢坯的生产工序,主要设备包括回转台、中间包,结晶器、拉矫机等。
本专题将详细介绍转炉(以及电炉)炼钢生产的工艺流程,主要工艺设备的工作原理以及控制要求等信息。
由于时间的仓促和编辑水平有限,专题中难免出现遗漏或错误的地方,欢迎大家补充指正连铸工艺详解连铸的生产工艺流程:将装有精炼好钢水的钢包运至回转台,回转台转动到浇注位置后,将钢水注入中间包,中间包再由水口将钢水分配到各个结晶器中去。
结晶器是连铸机的核心设备之一,它使铸件成形并迅速凝固结晶。
拉矫机与结晶振动装置共同作用,将结晶器内的铸件拉出,经冷却、电磁搅拌后,切割成一定长度的板坯。
连铸钢水的准备一、连铸钢水的温度要求:钢水温度过高的危害:①出结晶器坯壳薄,容易漏钢;②耐火材料侵蚀加快,易导致铸流失控,降低浇铸安全性;③增加非金属夹杂,影响板坯内在质量;④铸坯柱状晶发达;⑤中心偏析加重,易产生中心线裂纹。
钢水温度过低的危害:①容易发生水口堵塞,浇铸中断;②连铸表面容易产生结疱、夹渣、裂纹等缺陷;③非金属夹杂不易上浮,影响铸坯内在质量。
连铸机的分类及特点

(5)水平式连铸机
结晶器、二次冷却区、拉矫机、切割装置等设备布置在水平 位置上。中间包与结晶器是紧密相连的,相连处装有分离环。 拉坯时,结晶器不振动,而是通过拉坯机带动铸坯做拉—反 推—停不同组合的周期性运动来实现拉坯的。
(5)水平式连铸机
优点是高度低,投资省。设备维修、处理事故方便。钢水静 压力小,避免了鼓肚变形;不受弯曲矫直作用,有利于特殊钢 和高合金钢的浇注。
1.按铸坯断面形状分类 (1)方坯连铸机 :(50×50)~(450×450)mm; (2)圆坯连铸机:Φ40~Φ600mm; (3)板坯连铸机:最大为450×3100mm; (4)矩形坯连铸机:(50×108)~(400×630)mm; (5)异型连铸机:120×240mm(椭圆形);Φ450×Φ100mm (中空形);460×400×120mm、356×775×100mm(H形)。
连续铸钢生产
1.1 钢的浇注概述
1.1.4连铸机的分类
1按结晶器是否移动分类
(1)固定式结晶器(包括固定振动结晶器):所谓固定式结
晶器,是指结晶器“固定”不动,连铸坯与结晶器之间存在相对
运动。
1—立式 2—立弯式
3—直结晶器多点弯曲
4—直结晶器弧形
5—弧形
6—多半径弧形(椭圆形)
7—水平式
1.1 钢的浇注概述
缺点是受拉坯时惯性力限制,适合浇注200mm以下中小断面 方、圆坯。另外,结晶器的石墨板和分离环价格贵。
感谢聆听
4 按连铸机机构外形(机型)分类 (1)立式连铸机 (2)立弯式连铸机 (3)弧形连铸机 (4)椭圆形连铸机 (5)水平式连铸机
(1)立式连铸机
20世纪50年代至60年代的主要机型 主要特点是从中间包到切割装置等 主要设备均布置在垂直中心线上。
方坯连铸机-资料
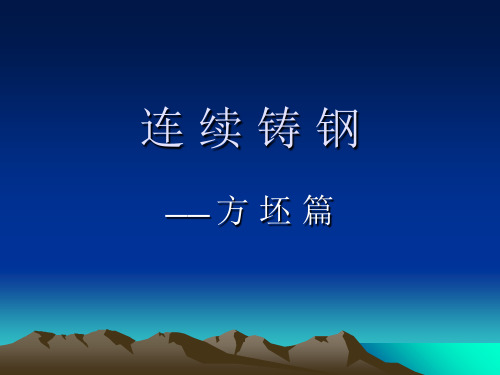
铸机最小圆弧半径:
R≥cD 式中 R—连铸机圆弧半径;
D—铸坯厚度; c—系数,一般中小型铸坯取30~40; 大型板坯及合金钢,取40以上。国外,普 通钢种取33~35,优质钢取42~45。
3、液相深度
液相深度L液是指铸坯从结晶器液面开 始到铸坯中心液相凝固终了的长度,也称 为液心长度。
液相深度是确定连铸机二次冷却区长度 的重要参数;对于弧形连铸机来说,液相 深度也是确定圆弧半径的主要参数,它直 接影响铸机的总长度和总高度。
结晶器的要求:凝固过程是在坯壳与结晶器壁 连续、相对运动下进行的。为此,结晶器应具有良 好的导热性和刚性,不易变形;重量要轻,以减少 振动时的惯性力;内表面耐磨性要好,以提高寿命; 结晶器结构要简单,便于制造和维护。
结晶器的结构有管式结晶器和组合式结 晶器两种。
结晶器的重要参数:倒锥度。钢液在结 晶器内冷却凝固生成坯壳,进而收缩脱离 结晶器壁,产生气隙。因而导热性能大大 降低,由此造成铸坯的冷却不均匀;为了 减小气隙,加速坯壳生长,结晶器的下口 要比上口断面略小,称结晶器倒锥度。倒 锥,引起横裂甚至坯壳断裂。
拉钢机、铸坯存放台架
Vc=f/D 式中 D—铸坯厚度,mm;
f —系数,m·mm/m2
t
1.3 最大拉坯速度
限制拉坯速度的因素主要是铸坯出结晶
器下口坯壳的安全厚度(最小坯壳厚度)。 对于小断面铸坯壳安全厚度为8~10mm;大 断面铸坯坯壳安全厚度不小于15mm。
方圆坯弧形连铸机工艺设备特点简介
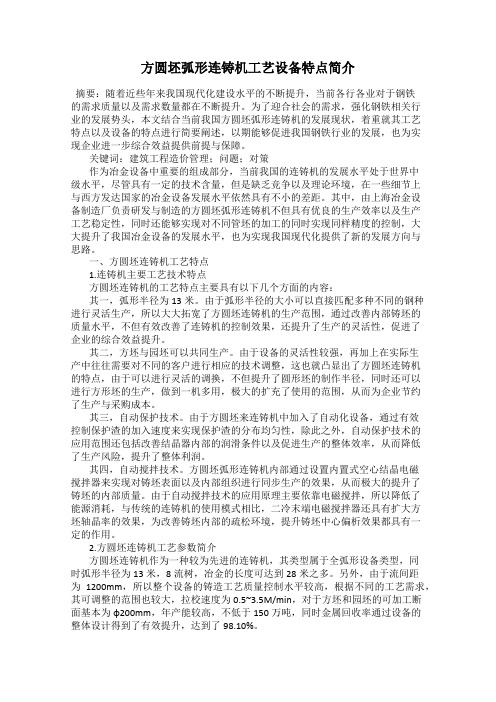
方圆坯弧形连铸机工艺设备特点简介摘要:随着近些年来我国现代化建设水平的不断提升,当前各行各业对于钢铁的需求质量以及需求数量都在不断提升。
为了迎合社会的需求,强化钢铁相关行业的发展势头,本文结合当前我国方圆坯弧形连铸机的发展现状,着重就其工艺特点以及设备的特点进行简要阐述,以期能够促进我国钢铁行业的发展,也为实现企业进一步综合效益提供前提与保障。
关键词:建筑工程造价管理;问题;对策作为冶金设备中重要的组成部分,当前我国的连铸机的发展水平处于世界中级水平,尽管具有一定的技术含量,但是缺乏竞争以及理论环境,在一些细节上与西方发达国家的冶金设备发展水平依然具有不小的差距。
其中,由上海冶金设备制造厂负责研发与制造的方圆坯弧形连铸机不但具有优良的生产效率以及生产工艺稳定性,同时还能够实现对不同管坯的加工的同时实现同样精度的控制,大大提升了我国冶金设备的发展水平,也为实现我国现代化提供了新的发展方向与思路。
一、方圆坯连铸机工艺特点1.连铸机主要工艺技术特点方圆坯连铸机的工艺特点主要具有以下几个方面的内容:其一,弧形半径为13米。
由于弧形半径的大小可以直接匹配多种不同的钢种进行灵活生产,所以大大拓宽了方圆坯连铸机的生产范围,通过改善内部铸坯的质量水平,不但有效改善了连铸机的控制效果,还提升了生产的灵活性,促进了企业的综合效益提升。
其二,方坯与园坯可以共同生产。
由于设备的灵活性较强,再加上在实际生产中往往需要对不同的客户进行相应的技术调整,这也就凸显出了方圆坯连铸机的特点,由于可以进行灵活的调换,不但提升了圆形坯的制作半径,同时还可以进行方形坯的生产,做到一机多用,极大的扩充了使用的范围,从而为企业节约了生产与采购成本。
其三,自动保护技术。
由于方圆坯来连铸机中加入了自动化设备,通过有效控制保护渣的加入速度来实现保护渣的分布均匀性,除此之外,自动保护技术的应用范围还包括改善结晶器内部的润滑条件以及促进生产的整体效率,从而降低了生产风险,提升了整体利润。
连铸机型及特点

连铸机型及特点(1)连铸机型分类从上世纪50年代连铸工业化开始,30多年来,连铸机的机型发展经历了一个由立式、立弯式到弧形演变过程。
图7-1表示了现有几种用于工业生产的连铸机型简图。
图7-1 各种型式连铸机结构特征a-立式;b-立弯式;c-直结晶器弧形;d-弧形;e-多半径弧形(椭圆形);f-水平式连铸机可以按多种形式来分类。
若按结构外形可把连铸机分为立式连铸机,立弯式连铸机,带直线段弧形连铸机,弧形连铸机,多半径椭圆形连铸机和水平连铸机。
近年来随着连铸技术的发展,又开展了轮式连铸机,特别是薄板坯连铸机的研究。
如果按照连铸机所浇铸的断面的大小和外形来区分,连铸机又可分为板坯连铸机、小方坯连铸机,大方坯连铸机、圆坯连铸机、异形断面连铸机和薄板坯连铸机。
在方坯连铸机中也包括矩形坯连铸机,通常把浇铸断面或当量断面积大于200×200mm的铸坯叫大方坯,断面或当量断面积小于160×160mm的铸坯叫小方坯,宽厚比大于3矩形坯称为板坯。
若按连铸机在共用一个钢水包下所能浇铸的铸坯流数来区分,则可分为单流、双流或多流连铸机。
在一台连铸机上,根据生产要求,既可浇铸板坯又能同时浇铸几流方坯的连铸机叫做方、板坯复合连铸机或简称为复合式连铸机。
有的厂家为了区分连铸机所能浇铸的钢种,在铸机前冠以特殊方坯连铸机或不锈钢板坯连铸机,以示与浇普通钢连铸机的区别。
中国冶金行业网(2)各类连铸机的特点1)立式连铸机立式连铸机的主要特点是:①铸机的主要设备布置在垂直中心线上,从钢水浇注到铸坯切成定尺,整个工序是在垂直位置完成的。
铸坯在切成定尺后由升降机或运输机送到地面。
②从工艺上看,钢水是在直立结晶器和二冷段逐渐结晶,有利于钢水中非金属夹杂物上浮,坯壳冷却也比较均匀,这对浇铸优质钢和合金钢是有利的。
另外,铸坯在整个凝固过程中不受任何弯曲、矫直作用,更适合于裂纹敏感性高的钢种的浇铸。
③立式连铸机设备高,建设费用大,设备的维护和铸坯的运送都比较困难。
课程设计--小方坯连铸机设计 二

课程设计--小方坯连铸机的设计一引言连铸技术是现代炼钢生产中最具有革命性的技术之一,其特点是节约能源、提高成材率和便于机械化、自动化操作,在过去的三十年中连铸技术得到了快速的发展与推广,特别是在两次世界石油危机的推动下,连铸生产规模空前扩大,涌现了许多实现全连铸的钢铁联合企业,连铸比的高低已经成为一个国家钢铁工业发展水平的标志。
随着现代工业对特殊钢、高质量钢的需求不断扩大,以及连续铸钢技术的迅速发展,对连铸工艺过程也有了更高的要求。
连续铸钢工艺从原料到成品的过程中起着关键性作用。
连铸工艺的优与劣直接影响钢产品的质量、性能和企业的经济效益。
且随着炼钢和轧钢技术的进展,钢铁工业结构的变化和对产品的规格、质量的新要求,这使得采用常规和铸锭—开坯工艺难以满足一些大型钢铁企业的生产和发展,为此,研究连铸的新工艺和新技术是必要的。
本文在阅读大量文献基础上,着重介绍了小方坯连续铸钢的发展概况、连铸机的选型,以及连铸机的工艺参数确定、设备的选型和相关参数进行了设计,并对连铸车间进行布置,使其保证连铸稳定、持续的进行。
最后本文还介绍了一些方坯连铸的新技术。
第一章绪论1.1我国方坯连铸发展的状况我国是在炼钢生产中研究、应用连铸技术较早的国家之一。
20世纪50年代中期,当连铸技术在前苏联、英国、意大利、加拿大等国进入工业性试验阶段时,我国即着手进行试验研究工作。
1956年我国在当时的重工业部钢铁综合研究所建成了直径80mm的圆坯半连铸试验装置。
1957年在上海钢铁公司中心试验室建成一台高架立式方坯连铸机;1958年在唐山钢铁厂建成了第一台工业生产的立式连铸机,同年在重庆第三钢铁厂建成投产一台两机两流,配合30t转炉,浇铸175mm×250mm矩形坯的立式连铸机。
1960年在唐山钢铁厂建成一机一流,配合5t转炉浇铸150mm×150mm小方坯的立式连铸机。
我国发展的连铸机型大多为立式连铸机,生产效率低。
150t炼钢连铸的钢包回转台设计

毕业设计说明书150t 炼钢连铸的钢包回转台设计源设计图纸请联系本人,参见豆丁备注。
毕业生姓名:专业:机械设计制造及其自动化学号:指导教师:所属系(部):机械电子工程系二〇一四年六月摘要钢包回转台是现代炼钢连铸生产中的主要设备之一,其作用是支撑和运载钢包进行浇铸,为实现多炉连浇创造了条件。
钢包回转台是连续铸钢设备中负荷最大、体积最大的焊接件。
它的主要组成部分是回转臂、推力轴承及塔座三部分。
为了安全运转,要求他的各个零部件有足够的强度和刚度。
本设计说明书是以江苏省镔鑫特钢材料有限公司炼钢厂的连铸车间方坯连铸机的钢包回转台为借鉴,以蝶式钢包回转台为形式进行的设计。
主要内容包括:钢包回转台传动方案的设计,回转台的结构尺寸的确定,主要零件的选择、计算与校核;电动机、减速器的选择与计算,以及钢包升降装置、称量装置、加盖装置的设计,此外,还介绍了部分主要零件具体的安装、维修、润滑、操作方法。
关键词:连铸;蝶式钢包回转台;传动方案;回转台结构尺寸。
AbstractThe ladle turret is one of the main casting equipments.Principal affect is supporting ladle and carrying to operation. For continue us casting invent a condition that working with many ladles.The ladle turret is the most load and volume jointing part in the casting equipments. It's making up of revolving arm,thrust-axletree,foundation. For the safety, needing every parts have enough intensity and rigidity.To take a basis of the dishing ladle helicoid dado for the square-circle castings BinXin Steel Iron Works. This direction is involved in many respects including drive scheme device ,Construvtion and size of helicoid dado, main pare parts calibration, motor, reduction gear, aircylinder, and ladle lifting device, locking device, weighing device, cove lifting device, elicit introduced about the concert install, lubrication and operation.Key words: casting equipment,dishing ladle helicoid dado, drive scheme, helicoid dado configurable.目录摘要 (II)Abstract (III)1 绪论 (1)1.1 国内外连铸机术的发展及我国与世界连铸技术的差距 (1)1.2 连铸机的主要设备及分类 (3)1.3 连铸机钢包旋转 (7)1.3.1 钢包旋转台的形式 (7)1.3.2 钢包旋转台的主要结构特点 (8)1.3.3 各类连铸机钢包回转台的特点 (9)1.4 钢包回转台的组成 (11)1.5 钢包回转台的工作特点 (12)2 初步确定方案 (13)2.1 已知条件 (13)2.1.1 设计题目 (13)2.1.2 技术参数及性能 (13)2.2 方案的总体布置形式 (13)2.3 回转台具体部件设计方案的确定 (13)2.3.1 钢包旋转驱动方式 (13)2.3.2 锁紧方式 (14)2.3.3 钢包盖的升降装置 (15)2.3.4 长水口机械手动作方式 (15)2.3.5 钢包升降驱动方案 (15)3 电机的计算与选择 (17)3.1钢包回转功率的计算 (17)3.1.1 基本数据的计算 (17)3.1.2 情况Ⅰ的回转功率计算 (19)3.1.3 情况Ⅱ的回转功率计算 (19)3.1.4 情况Ⅲ的回转功率计算 (20)3.2 电动机和电气马达的选择 (21)3.2.1 电动机的选择: (21)3.2.2马达的选择 (22)3.3 减速器的设计 (22)3.3.1 确定减速器的结构 (22)3.3.2 传动比的计算和分配,计算传动装置的运动和动力参数 (23)3.3.3 齿轮的设计 (24)3.3.4 轴的设计 (30)3.3.5 减速器箱体的结构尺寸 (39)4 回转台主要构件分析 (40)4.1 对回转臂进行分析 (40)4.2 滚柱回转支承 (40)4.2.1 径向滚柱的分析 (41)4.2.2 轴向滚柱的分析 (42)4.3 地脚螺栓设计与计算 (43)4.3.1 选择材料 (43)4.3.2 确定螺栓的基本数据 (43)5 销齿传动的设计与计算 (45)T (45)5.1 销轮轴转矩35.2 选材及许用应力的确定 (45)5.2.1 材料的选择 (45)5.3 销齿直径确定 (46)5.4 校核齿轮弯曲强度 (47)5.5 确定尺寸 (47)6 钢包旋转台的加盖装置的设计 (48)7 称量传感器的形式选择与容量计算 (49)8 地脚螺栓的设计与计算 (50)8.1 选材及尺寸确定 (50)8.2 螺栓工作负荷的确定 (50)9 钢包回转台设备安装、使用和维护 (52)9.1 一些设备的安装 (52)9.1.1 滚柱旋转轴承的使用方法以及安装 (52)9.1.2 提升缸的安装与拆卸 (52)9.2 钢包回转台的使用和维护 (52)总结 (54)参考文献 (55)外文资料 (56)中文翻译 (61)致谢 (65)1 绪论1.1 国内外连铸机术的发展及我国与世界连铸技术的差距把高温钢水连续不断地浇铸成具有一定断面形状和一定尺寸规格铸坯的生产工艺过程叫做连续铸钢。
大圆坯连铸机的设计特点及装备水平
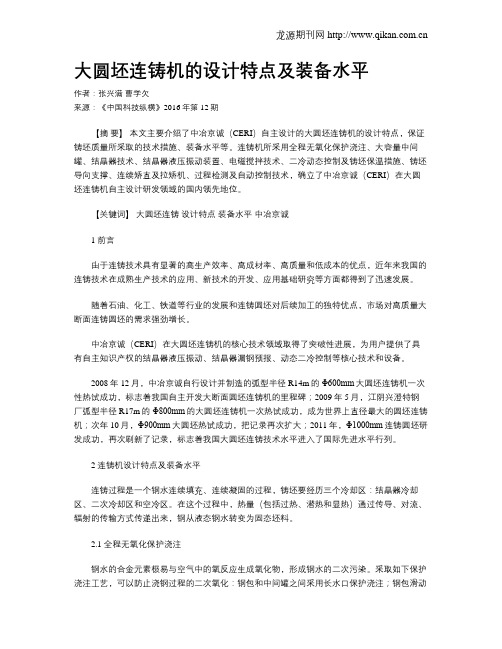
大圆坯连铸机的设计特点及装备水平作者:张兴满曹学欠来源:《中国科技纵横》2016年第12期【摘要】本文主要介绍了中冶京诚(CERI)自主设计的大圆坯连铸机的设计特点,保证铸坯质量所采取的技术措施、装备水平等。
连铸机所采用全程无氧化保护浇注、大容量中间罐、结晶器技术、结晶器液压振动装置、电磁搅拌技术、二冷动态控制及铸坯保温措施、铸坯导向支撑、连续矫直及拉矫机、过程检测及自动控制技术,确立了中冶京诚(CERI)在大圆坯连铸机自主设计研发领域的国内领先地位。
【关键词】大圆坯连铸设计特点装备水平中冶京诚1 前言由于连铸技术具有显著的高生产效率、高成材率、高质量和低成本的优点,近年来我国的连铸技术在成熟生产技术的应用、新技术的开发、应用基础研究等方面都得到了迅速发展。
随着石油、化工、铁道等行业的发展和连铸圆坯对后续加工的独特优点,市场对高质量大断面连铸圆坯的需求强劲增长。
中冶京诚(CERI)在大圆坯连铸机的核心技术领域取得了突破性进展,为用户提供了具有自主知识产权的结晶器液压振动、结晶器漏钢预报、动态二冷控制等核心技术和设备。
2008年12月,中冶京诚自行设计并制造的弧型半径R14m的Φ600mm大圆坯连铸机一次性热试成功,标志着我国自主开发大断面圆坯连铸机的里程碑;2009年5月,江阴兴澄特钢厂弧型半径 R17m的Φ800mm的大圆坯连铸机一次热试成功,成为世界上直径最大的圆坯连铸机;次年10月,Φ900mm大圆坯热试成功,把记录再次扩大;2011年,Φ1000mm连铸圆坯研发成功,再次刷新了记录,标志着我国大圆坯连铸技术水平进入了国际先进水平行列。
2 连铸机设计特点及装备水平连铸过程是一个钢水连续填充、连续凝固的过程,铸坯要经历三个冷却区:结晶器冷却区、二次冷却区和空冷区。
在这个过程中,热量(包括过热、潜热和显热)通过传导、对流、辐射的传输方式传递出来,钢从液态钢水转变为固态坯料。
2.1 全程无氧化保护浇注钢水的合金元素极易与空气中的氧反应生成氧化物,形成钢水的二次污染。
R10m十机十流方圆坯连铸机技术平台

文档来源为:从网络收集整理.word版本可编辑.欢迎下载支持.临沂华盛江泉管业有限公司一套R10m十机十流方圆坯连铸机技术平台2013年01月第一章项目概述1.项目概况项目名称:临沂华盛江泉管业有限公司一套R10m十机十流方圆坯连铸机建设地点:山东省临沂市根据临沂华盛江泉管业有限公司的生产规模和产品方案,转炉炼钢厂配置1座120t转炉,及一套R10m十机十流方圆坯连铸机。
2.总体设计原则本次一套R10m十机十流方圆坯连铸机项目总体设计所遵循的主要原则是:(1)以高起点、高标准、高效率为原则,确保将此项目建设成为具有国内先进水平,科技含量高、经济效益好、资源消耗少、人力资源优势得到充分发挥的现代化连铸生产线。
(2)合理选择生产工艺和技术。
对各生产环节的生产工艺附件进行严格、科学的论证,采用先进可靠的技术,现代化、高效化、实用型的设备配置,紧凑合理的总图布置,实现企业的最低成本和最佳的经济效益。
第二章连铸工艺连铸机工艺技术在连铸生产中起着至关重要的作用,本章就临沂华盛江泉管业有限公司一套R10m十机十流方圆坯连铸机的冶炼条件、产品大纲、金属平衡、主要工艺参数选择、厂房布置条件等工艺技术问题做了具体说明。
1.连铸机冶炼条件表2—1炼钢系统主要工艺参数如下表2.连铸产品大纲断面:方坯150mm×150mm、圆坯Ф150 mm2、Ф160 mm2,Ф180 mm2预留Ф350 mm2。
定尺长度: 6~12m;表2—2参考产品大纲如下表3.连铸机主要工艺参数的确定3.1机型本台连铸机选用全弧形连铸机,多点矫直技术。
由于在连铸机的设计中采用了多点矫直技术,使铸坯的变形率得到了有效的控制,从而获得了较高的铸坯质量。
3.2基本弧形半径连铸机的弧形半径是连铸机的重要参数之一,它的大小影响着铸坯的质量。
连铸机弧形半径的确定主要取决于浇注钢种与断面尺寸,同时与拉速及其生产能力也是相关的。
此方圆坯连铸机的弧形半径取R10m,按最大断面通过详细理论计算得出,固液两相区变形率和表面变形率满足工艺要求,则其他断面铸坯固液两相区变形率和表面变形率也满足工艺要求。
合金钢大方圆坯连铸机的工艺参数及设计特点
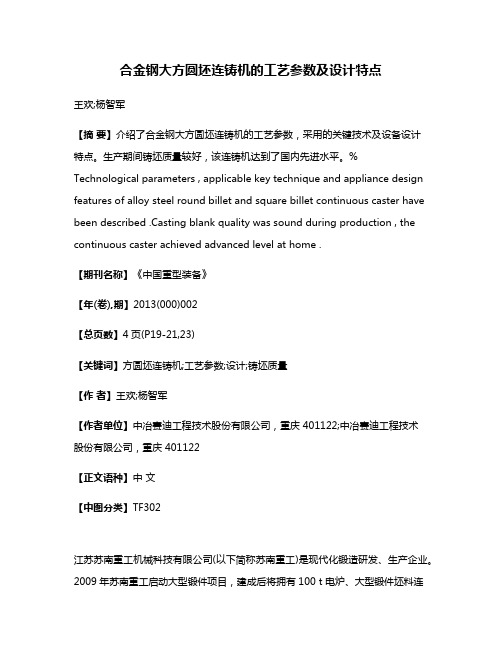
合金钢大方圆坯连铸机的工艺参数及设计特点王欢;杨智军【摘要】介绍了合金钢大方圆坯连铸机的工艺参数,采用的关键技术及设备设计特点。
生产期间铸坯质量较好,该连铸机达到了国内先进水平。
% Technological parameters , applicable key technique and appliance design features of alloy steel round billet and square billet continuous caster have been described .Casting blank quality was sound during production , the continuous caster achieved advanced level at home .【期刊名称】《中国重型装备》【年(卷),期】2013(000)002【总页数】4页(P19-21,23)【关键词】方圆坯连铸机;工艺参数;设计;铸坯质量【作者】王欢;杨智军【作者单位】中冶赛迪工程技术股份有限公司,重庆 401122;中冶赛迪工程技术股份有限公司,重庆 401122【正文语种】中文【中图分类】TF302江苏苏南重工机械科技有限公司(以下简称苏南重工)是现代化锻造研发、生产企业。
2009年苏南重工启动大型锻件项目,建成后将拥有100 t 电炉、大型锻件坯料连铸设备等,形成年产各类大型锻件25 万吨的能力。
为满足项目建设要求,需新建一台4 机4 流浇注合金钢的方圆坯兼容的连铸机,钢水由炼钢厂的一座100 t 电炉供给。
由于浇注合金钢的连铸机装备水平要求较高,所以连铸机的工艺参数及主要设备结构的选择显得尤为重要。
1 产品大纲及工艺流程新建的连铸机为方圆坯兼容,产量为52.5 万吨/年,其中圆坯29.5 万吨/年,方坯23 万吨/年,其产品及代表钢种见表1,连铸机的工艺流程见图1。
连铸圆坯缺陷类型

连铸圆坯缺陷类型(原创版)目录1.连铸圆坯的概述2.连铸圆坯的主要缺陷类型3.缺陷类型对连铸圆坯表面和内部质量的影响4.我国大规格连铸圆坯生产技术领先世界5.承德建龙新建 4 号大圆坯连铸项目的成功案例6.项目的技术创新和应用领域正文一、连铸圆坯的概述连铸圆坯是一种通过连铸工艺生产的圆形钢坯,具有尺寸精度高、表面质量好、内部缺陷少等优点,广泛应用于石油、化工、船舶、电力、冶金等重工业领域。
二、连铸圆坯的主要缺陷类型连铸圆坯的主要缺陷类型包括表面缺陷和内部缺陷。
表面缺陷有裂纹、气孔、夹渣、震痕和凹陷、成分偏析等;内部缺陷有裂纹、气孔、夹渣、缩孔和缩松、成分偏析等。
三、缺陷类型对连铸圆坯表面和内部质量的影响表面缺陷会影响连铸圆坯的力学性能、耐磨性和耐腐蚀性;内部缺陷则会影响其力学性能、加工性能和使用寿命。
四、我国大规格连铸圆坯生产技术领先世界我国在连铸圆坯生产技术方面取得了显著成果。
承德建龙新建 4 号大圆坯连铸项目成功生产出 800mm 规格连铸坯,填补了我国在大规格连铸圆坯生产技术上的空白,并领先世界。
五、承德建龙新建 4 号大圆坯连铸项目的成功案例承德建龙新建 4 号大圆坯连铸项目采用全智能化、数字化连铸生产线,可生产 700mm-1300mm 的大直径连铸圆坯。
该项目是世界第一条集节能环保、先进工艺、智能化等于一体的世界一流连铸生产线。
六、项目的技术创新和应用领域项目采用了达涅利冶金设备有限公司设计制作建设的三机三流大圆坯连铸机生产线核心设备技术,应用了全流程保护浇注、下渣检测、自动开浇、涡流型自动液面控制、铸坯加热、激光定尺、自动喷号机器人等国际领先技术。
十流连铸中间包内型优化研究

7. / /
式 () 7中 v _ 夹 杂 物 上 浮 速 度
中间包 内钢液 的流动属湍流流动 , 根据相似定理 可知 , 当流体流动 的R 数大于第二临界值时 , e 流体 的湍动程度及流速 的分布不再受 R 数 e 的影 响。此时 流体 的流动状态 不再变化 , 且彼此相似 。所 以采用水 模 型对结 晶器 内的流动进行物理模拟可 以只考虑 n相等 。 本实验 中间包 的几何 相似 比 = ., 05 实验装 置如 图 1 所示 。根据相
v ——模 型液体 流速/ ) ( m Vn — 实 型 液 体 流 速 / — ( m ) Q_一 模 型液体 流量/ ) ( m Q ——实型液体流 量/ s ( m_ ) 用刺激一 响应试 验法测定液 体停 留时间分布 。在 中间包 的模 型 中, 随着钢包 注流注入 一定剂 量的 电解 质溶液, 电导 电极 测定浓 度 C 用 和时 间t R D曲线上, 的 T 从而得 出从 示踪剂 的加入到 中间包 出 口处示踪 剂 刚刚响应的时 间t ̄ m, i浓度达到最 大的时间 t 及计算 得 出流体平 均停 留时 间 t, 死区体积 v, 活塞区体积 V 和混合区体积 v , 数学关系如下:
科技信息
专题 论述
十 流 连 铸 巾间 包 内 型 优 化研 穷
马鞍 山钢 铁股 份有 限& s仓 储 配送 中心 还 海峰 - J
[ 摘 要] 本研究通过水 力学模 型试验 , 优化 了板坯连铸机 中间包 内型。试验结果表 明, 优化后 的中间包开孔位置使 流场趋于合理 , 水模 异型 流场
图3 方案一 的R D曲线 T
1 . 钢包 2加 N C . a L液漏斗 3阀 门 4中间包 5塞棒 6电导电极 . . . . 7 . 流量计 8 . 电导仪 9 数据采集板 1 . 算机数据处理终端 O 计 图1 水模 实验装 置示 意图 夹 杂物 的最小 直径 由斯托克斯 阻力 公式 中的过 渡 区公 式计算 所
连铸工艺特点

连铸工艺特点
连铸工艺特点
一、热机特点:
1.连铸设备机械结构简洁、工艺流程洁净、工艺量一致、热处理效果好;
2、连铸机的高温煅烧温度可以达到15~1700℃,熔炼工艺温度可达1850~2200℃,可以满足高精度钢铁产品的熔炼;
3、连铸机煅烧和熔炼工艺的动力要求比较小,宜于能源利用,可以减少能源消耗;
4、连铸的熔炼工艺和机械工艺可以改变,能够满足多种特殊材料的要求;
5、连铸机械设备具有良好的刚性和可靠性。
二、冷机性能特点:
1.连铸设备冷却时间短,冷却速率大,冷却效果好;
2、连铸设备冷却时间比传统的铸造工艺更短,可以有效提高铸件生产效率;
3、由于连铸设备具有较大的冷却面积和多种冷却方式,可以满足多种要求;
4、连铸设备还可以通过改变冷却工艺,改善钢铁易碳化、易结晶和较大残余应力的特性;
5、连铸设备在铸造工艺中,还可以考虑热处理的问题,从而提高钢铁的性能。
八钢十机十流连铸机工艺特点

八钢十机十流连铸机工艺特点本文介绍了八钢十机十流小方坯连铸机的工艺及装备特点,为同类型连铸机的设计、建设提供了参考。
标签:十机十流;方坯;连铸机;工艺;装备八钢十机十流方坯连铸机设计、建设于2011年2月,2012年8月投产,是八钢150t转炉炼钢连铸项目的配套项目,与一座150t转炉及150t双工位LF精炼炉匹配,可生产碳素结构钢、优质碳素结构钢、合金结构钢、弹簧钢、硬线钢、焊丝钢、抽油杆钢、预应力钢绞线钢等钢种,设计年产钢坯150万吨,最大产能180万吨。
1 连铸机机型及主要工艺参数2 连铸机机型该连铸机为R=10m的全弧型刚性引锭杆方坯连铸机。
铸坯矫直采用连续矫直方式,在连续矫直区内,铸坯在矫直区内半径由10m 到无穷大的弧是一条连续的光滑曲线,其曲率半径是连续变化的,可以使铸坯逐渐变形,使每一点的变形率都保持在形成裂纹的临界值之下。
3 连铸机主要工艺设备特点和技术装备水平3.1 主要工艺特点(1)钢包下渣检测(电磁涡流式)(2)全程保护浇注。
根据产品大纲中浇注钢种的要求,从钢包—中间罐采用长水口+氩气密封;中间罐—结晶器之间采用浸入式水口+保护渣浇注方式,避免钢流的二次氧化;生产优质钢种时采用整体式浸入式水口。
(3)大容量、深液面的中间罐冶金技术。
采用优化设计的L型中间罐,双中包浇注,中间罐内钢液有足够深度保证钢水内夹杂物有充分的上浮时间,工作液位为850mm(浇注吨位36t),溢流液位达到950mm(浇注吨位42t)。
(4)二冷水采用气水雾化,配水工艺采用二冷动态自动控制模型。
为适应生产高级钢种弱冷的需要,二冷段采用气雾冷却。
二冷动态控制模型是在建立在铸坯凝固数学模型的基础上的,根据工艺条件的变化,具有实时计算和调整二冷水及压缩空气压力的功能,使铸坯的表面温度控制在理想的目标温度内。
(5)连续矫直技术。
采用连续矫直技术,保证在较高拉速条件下降低铸坯在矫直区内表面/两相区矫直变形应力,改善铸坯表面和内部质量。
江鑫钢铁10流方圆坯连铸机设计特点

江鑫钢铁10流方圆坯连铸机设计特点作者:段世钰陈永军来源:《建筑建材装饰》2014年第01期摘要:介绍江鑫钢铁10流连铸机设计特点,该连铸机具有流数多、浇铸断面丰富、自动化控制程度高的特点。
关键词:连铸机;设计特点;10流前言为了贯彻我国钢铁发展产业政策,淘汰落后产能,优化生产结构,山东临沂江鑫钢铁有限公司扩建120t转炉炼钢车间。
钢厂采用铁水预脱硫→顶底复吹转炉炼钢→(吹氩处理)→LF 钢包精炼炉→连铸→(铸坯热送热装轧机生产线加热炉)的先进的工艺流程,车间内新建一座120t顶底复吹转炉、一座LF钢包精炼炉和一台10机10流方圆坯连铸机。
此连铸机是临沂江鑫钢铁有限公司长期战略发展的一部分,同时也有利于带动周边相关企业的发展。
1 生产规模及产品2 连铸机性能参数表1 连铸机性能参数3 连铸机工艺流程钢包在回转台上座定之后,旋转180°到浇注位。
钢包具有两个水口,分别向两个中间包内同时浇注钢水。
打开钢包滑动水口,使钢水经长水口进入中间包,当钢水液面达到一定深度后,开启中间包水口,使钢水进入结晶器。
在结晶器内冷却水的强制冷却下,钢水开始凝固,形成具有一定厚度的坯壳。
在拉矫装置的作用下,铸坯从结晶器内被拉出,进入二次冷却区,在此铸坯受到气水雾化二次冷却,钢水继续凝固,进入拉矫装置后达到完全凝固或带有较少量的液心,铸坯经矫直,由弧形变为水平。
铸坯进入切割机时,已完全凝固,火焰切割机将铸坯切割为所要求定尺长度的成品,经运输辊道送至冷床系统,通过热送辊道或汽车运送到轧钢车间加热炉区域。
4 连铸机工艺布置连铸机车间厂房由连铸跨、过渡跨、出坯跨组成,三跨平行布置。
连铸机回转台布置在连铸跨与钢水接收跨之间,浇铸设施、操作平台、结晶器及振动装置、导向段设备、拉矫设备等布置在连铸跨,切割设备、运输辊道、引锭杆及其存放设施布置在过渡跨,冷床设施布置在出坯跨。
中间包修砌、中间包干燥、中间包存放、结晶器维修、结晶器存放等设备布置在连铸跨厂房内,备件存放等设备布置在过渡跨,铸坯堆存区域设在出坯跨。
- 1、下载文档前请自行甄别文档内容的完整性,平台不提供额外的编辑、内容补充、找答案等附加服务。
- 2、"仅部分预览"的文档,不可在线预览部分如存在完整性等问题,可反馈申请退款(可完整预览的文档不适用该条件!)。
- 3、如文档侵犯您的权益,请联系客服反馈,我们会尽快为您处理(人工客服工作时间:9:00-18:30)。
江鑫钢铁10流方圆坯连铸机设计特点
作者:段世钰陈永军
来源:《建筑建材装饰》2014年第01期
摘要:介绍江鑫钢铁10流连铸机设计特点,该连铸机具有流数多、浇铸断面丰富、自动化控制程度高的特点。
关键词:连铸机;设计特点;10流
前言
为了贯彻我国钢铁发展产业政策,淘汰落后产能,优化生产结构,山东临沂江鑫钢铁有限公司扩建120t转炉炼钢车间。
钢厂采用铁水预脱硫→顶底复吹转炉炼钢→(吹氩处理)→LF 钢包精炼炉→连铸→(铸坯热送热装轧机生产线加热炉)的先进的工艺流程,车间内新建一座120t顶底复吹转炉、一座LF钢包精炼炉和一台10机10流方圆坯连铸机。
此连铸机是临沂江鑫钢铁有限公司长期战略发展的一部分,同时也有利于带动周边相关企业的发展。
1 生产规模及产品
2 连铸机性能参数
表1 连铸机性能参数
3 连铸机工艺流程
钢包在回转台上座定之后,旋转180°到浇注位。
钢包具有两个水口,分别向两个中间包内同时浇注钢水。
打开钢包滑动水口,使钢水经长水口进入中间包,当钢水液面达到一定深度后,开启中间包水口,使钢水进入结晶器。
在结晶器内冷却水的强制冷却下,钢水开始凝固,形成具有一定厚度的坯壳。
在拉矫装置的作用下,铸坯从结晶器内被拉出,进入二次冷却区,在此铸坯受到气水雾化二次冷却,钢水继续凝固,进入拉矫装置后达到完全凝固或带有较少量的液心,铸坯经矫直,由弧形变为水平。
铸坯进入切割机时,已完全凝固,火焰切割机将铸坯切割为所要求定尺长度的成品,经运输辊道送至冷床系统,通过热送辊道或汽车运送到轧钢车间加热炉区域。
4 连铸机工艺布置
连铸机车间厂房由连铸跨、过渡跨、出坯跨组成,三跨平行布置。
连铸机回转台布置在连铸跨与钢水接收跨之间,浇铸设施、操作平台、结晶器及振动装置、导向段设备、拉矫设备等布置在连铸跨,切割设备、运输辊道、引锭杆及其存放设施布置在过渡跨,冷床设施布置在出
坯跨。
中间包修砌、中间包干燥、中间包存放、结晶器维修、结晶器存放等设备布置在连铸跨厂房内,备件存放等设备布置在过渡跨,铸坯堆存区域设在出坯跨。
5 连铸机设计特点
(1)连铸机机型选择大半径弧形连铸机,采用多点矫直技术,使铸坯的变形率得到了有效控制,从而获得了较高的铸坯质量。
(2)带钢包称量和钢包加盖的直臂式大包回转台。
采用钢包加盖装置可减少钢包内钢水在浇注过程中的温降,同时也可防止空气中夹杂物进入钢包,保持钢水清洁度。
(3)带液压升降、液压横移的高低腿式中间包车。
(4)采用大容量、深液面中间包冶金技术,钢水在中间包内停留时间大于10min,保证钢水中大颗粒非金属夹杂物有充分的时间上浮。
(5)中间包内腔为“L”形结构,有利于设置冲击杯、挡渣墙等设施,确保钢水合理流动。
利用数学模型,结合水力学试验来设计的中间包,拥有最佳几何尺寸、最佳流场。
(6)采用双中间包浇注,相应减少了中间包尺寸,保证中间包刚性,包底变形小,确保水口对中。
(7)浇注过程中使用双中间包,另有双中间包在烘烤位备用,可实现中间包的热更换,提高铸机作业率。
(8)采用塞棒自动执行机构控制中间包钢流,以保证结晶器内钢水液面的稳定,从而实现恒拉速、恒液位生产,提高铸坯质量和炼钢工艺水平。
(9)采用中间包定径水口快速更换装置,可以提高连铸机连浇炉数及钢水收得率,减少耐火材料消耗,降低生产成本,提高经济指标[1]。
(10)浇注高品质钢种时,钢包到中间包采用长水口及氩气保护浇注,中间包到结晶器采用浸入式水口保护浇注,防止钢水二次氧化及气体的吸入,同时减少钢水温度降,减少钢水在浇注过程中形成的夹杂物,提高连铸坯洁净度,保证轧材质量[2]。
(11)采用国际先进的均匀窄水缝、高水速冷却的管式结晶器。
这种结构将会有效避免冷却水的局部沸腾,从而使通过结晶器的铸坯在凝固的同时,不仅增加了坯壳厚度,而且可减少裂纹。
(12)结晶器液面自动控制采用铯源型液位检测,减小钢水液面波动量。
(13)采用结晶器外置式电磁搅拌技术,在钢水最初的凝固过程中,对钢水进行搅拌,将树枝晶打碎作为结晶核心扩大等轴晶区,有利于气泡和夹杂物的去除,同时减轻铸坯中心成分偏析,从而改善铸坯的表面和内部质量。
此外,它还能消除部分钢水温度波动造成的对铸坯质量的不利影响,加快钢水热量传递、散发,提高浇铸速度[3]。
(14)采用四连杆电动缸非正弦振动技术,可以实现振动参数、振幅、振动频率、偏斜率等的在线调节;刚度大,能满足大断面拉矫阻力的要求,适用于高负载、高频率、高拉速的生产条件;工作平稳、可靠,振幅精确,便于维修、磨损小,利于长期使用。
(15)二冷区采用气水雾化冷却。
其水量根据不同钢种、坯型、拉速、钢水温度等参数,运用二次配水方程进行配置,形成多条水量曲线,并可通过PLC进行多种选择、调整和修正,有效保证了铸坯质量。
(16)采用四机架多点矫直拉矫机,拉速可调,可满足不同钢种和不同铸坯断面对拉速提出的不同要求,满足上引锭时较快的速度要求;通过液压缸调整上下辊的开口度,能够满足多种铸坯断面和引锭杆通过的工艺要求;采用全水冷型拉矫机,对拉矫辊、机架、轴承座、减速机实施有效水冷措施,彻底解决了拉矫机因高温工作环境而造成的故障率高、维护工作量大,影响铸机作业率,甚至造成因机架和辊子等经常变形而严重影响铸坯质量等问题。
(17)采用非接触式红外自动定尺系统,可大大提高定尺精度,定尺控制精度达到5~
8mm。
(18)采用液压步进翻转冷床来实现对长定尺铸坯的移送及翻转,使铸坯冷却快而均匀,平直度好。
6 结束语
临沂江鑫10流方圆坯连铸机在总体工艺流程的选择上,以实现本项目所选定的生产品种为核心目标,合理选择设备配置,形成所选定产品的最佳生产模式,为企业创造一个良好的生产管理平台,获得最佳的综合技术经济指标;在总图布置上,充分利用车间工艺条件,紧密联系各工序之间的技术衔接,使各工序都能充分发挥其生产能力,尽量减少生产过程中各类物质的输送路线,运输工具的相互矛盾与干扰,实现连续化和紧凑化生产,实现连铸生产的工艺现代化、生产集约化;在设备配置上,力求配置一流的新型设备,侧重设备的先进性、可靠性、实用性,使各工序设备做到物尽其用,实现连铸生产的高效率。
总之,临沂江鑫10流方圆坯连铸机是科技含量高、经济效益好、资源消耗少的具有国内先进水平的生态环保型现代化连铸生产线。
参考文献:
[1]张胜生,孟宪俭,杨君胜,陈向阳,陈绍明.连铸中间罐不断流快速更换定径水口技术.连铸,2001,2:13—15
[2]杨君胜.小方坯保护浇注及对铸坯质量的影响.连铸,2001,4:35—36
[3]杨君胜,韩永刚,焉永刚,李伟,张兆柱.莱钢合金钢大方坯连铸机的设计与生产实践.连铸,2003,5:6—8。