苏州智能工厂建设指南
智能工厂整体建设方案

智能工厂整体建设方案随着科技的发展和智能化的推进,智能工厂作为一种新型的生产制造模式,正逐渐成为现代工业发展的趋势。
智能工厂的建设不仅是对传统生产模式的转变,更是对生产效率和质量的提升,以及资源利用的最大化。
本文将就智能工厂的整体建设提出一套方案,帮助企业实现高效、智能、可持续发展。
一、智能化设备引进智能工厂的核心是智能化设备的应用。
因此,在整体建设方案中,首先需要对目标产线的设备进行评估和升级,引进先进的智能化设备。
这些设备可以通过自动化、机器人技术、机器视觉等手段实现智能化生产,从而提高生产效率,并降低人为因素对质量的影响。
二、数据集成和互联网应用智能工厂的核心是数据。
对生产过程中的数据进行采集、分析和应用,是提高生产效率、优化生产布局的关键。
在整体建设方案中,需要引入先进的数据采集和处理系统,将设备、工序、物料等方面的数据进行集成,并通过互联网技术实现数据的共享和调度。
这样可以实现生产过程的全程监控,及时发现问题,减少浪费,提高效率。
三、人机协同和智能决策支持智能工厂的建设不仅仅局限在设备和技术的引进方面,还需要注重人与机器的协同作业。
在整体建设方案中,应该充分考虑如何通过人机协同的模式,提高人员的工作效率和生产能力。
同时,引入人工智能技术,通过对数据的分析和模型的建立,为生产决策提供智能支持,增强企业的决策能力和竞争力。
四、安全管理和技术培训智能工厂的建设还需要关注安全管理和技术培训。
在整体建设方案中,应该设立科学的安全管理制度,确保工作环境的安全和员工的健康;同时,组织员工参与相关的技术培训,提高员工对智能化设备操作和维护的能力,确保智能工厂的稳定运行。
五、可持续发展和资源循环利用智能工厂的建设也需要考虑可持续发展和资源循环利用的问题。
在整体建设方案中,应该注重节能减排和资源利用的最大化。
通过应用清洁能源、优化生产工艺和产品设计,降低能源消耗和环境污染。
同时,通过回收再利用和废物处理等手段,实现资源的循环利用,提高资源利用效率,降低生产成本。
苏州市智能工厂项目申报书

苏州市智能工厂项目申报书申报书项目名称:苏州市智能工厂项目一、项目背景和意义智能制造是当前国际制造业发展的主流趋势,也是中国制造业转型升级的重要方向。
苏州市作为中国制造业的重要基地,积极推进智能制造领域的发展,加快传统工业转型。
智能工厂项目的实施将为苏州市制造业转型升级提供重要支持,培育高端制造业集群,增强市场竞争力。
二、项目内容和规模三、项目技术和创新1.智能化生产线:引进国内外先进的自动化设备和机器人技术,实现生产过程的自动化、智能化,提高生产效率和产品质量。
2.物联网平台:建立物联网平台,实现设备之间的互联互通,实时监控设备状态,提供精准的生产数据分析和预警功能。
3.智能仓储系统:引进智能化仓储设备和管理系统,实现仓储工作的自动化、智能化,提高物流配送效率。
四、项目带动效应1.人才培养:项目实施过程中将培养一批掌握智能制造技术和管理的高级人才,为苏州市智能制造产业的发展提供人力资源支持。
2.制造业转型:智能工厂项目的实施将推动苏州市传统制造业向智能制造的转型,提高产品质量和市场竞争力。
3.产业集聚效应:智能工厂项目的建设将吸引相关产业链上的企业入驻,形成智能制造产业集群,促进区域经济的发展。
五、项目实施计划1.前期准备阶段(2024年1月-2024年6月):完成项目立项、筹资、选址等工作。
2.建设阶段(2024年7月-2024年12月):完成工厂主体建设、设备采购、系统调试等工作。
3.运营阶段(2024年1月-):正式投入生产,并实施运营管理,逐步达到设计产能。
六、项目投资和资金筹措项目总投资5000万元,计划通过银行贷款3000万元,企业自筹2000万元。
七、项目风险分析和对策1.技术风险:需引进先进的智能制造技术,如遇技术难题,将与技术合作单位合作解决。
2.市场风险:根据市场需求进行产品规划,建立健全的市场推广策略,降低市场风险。
3.资金风险:合理控制项目投资,加强资金管理,确保项目顺利进行。
智能工厂建设方案

智能工厂建设方案智能工厂建设方案:一、前期准备1. 需要进行市场调研,确定智能工厂的建设目标和需求。
2. 完成人员招聘,组建专业团队,包括研发、技术、生产和管理等方面的人才。
3. 与相关政府部门和企业合作,获得政策支持和资金支持。
二、基础设施建设1. 建立高速、稳定、安全的网络系统,实现机器之间的数据共享和通信。
2. 配备高性能的服务器和数据存储设备,提供大数据分析和运算能力。
3. 优化车间布局和设备配置,确保生产过程的高效和安全。
三、装备采购和升级1. 购买先进的生产设备和机器人,实现智能化生产和自动化操作。
2. 通过物联网技术,实现设备和系统的互联互通,提高生产效率和质量。
3. 配备智能传感器和监控设备,实现对设备和生产过程的实时监测和管理。
四、数据管理和分析1. 建立完善的工厂信息管理系统,实现对生产数据、质量数据和设备数据的实时收集和分析。
2. 运用大数据分析技术,提取和挖掘有价值的信息,优化生产调度和决策。
3. 建立数据安全和隐私保护机制,确保数据的安全和合规使用。
五、人员培训和管理1. 组织员工进行智能化技术培训,提升员工的技能和知识水平。
2. 建立绩效评估体系,激励员工的积极性和创造力。
3. 加强内部沟通和合作,营造良好的工作氛围和团队精神。
六、可持续发展1. 引入清洁能源和节能技术,降低能耗和环境污染。
2. 探索循环经济模式,实现废材料的再利用和资源的最大化利用。
3. 鼓励研发和应用新型材料和工艺,提高产品的品质和附加值。
通过以上的方案,可以实现智能工厂的高效、智能、绿色和可持续发展。
同时,智能工厂的建设还可以推动传统制造业向智能制造业转型升级,提高企业的竞争力和市场地位。
苏州智慧工厂软件系统设计方案
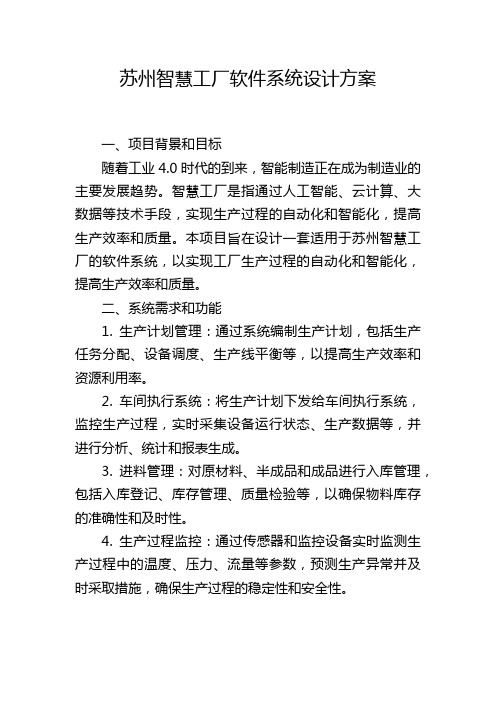
苏州智慧工厂软件系统设计方案一、项目背景和目标随着工业4.0时代的到来,智能制造正在成为制造业的主要发展趋势。
智慧工厂是指通过人工智能、云计算、大数据等技术手段,实现生产过程的自动化和智能化,提高生产效率和质量。
本项目旨在设计一套适用于苏州智慧工厂的软件系统,以实现工厂生产过程的自动化和智能化,提高生产效率和质量。
二、系统需求和功能1. 生产计划管理:通过系统编制生产计划,包括生产任务分配、设备调度、生产线平衡等,以提高生产效率和资源利用率。
2. 车间执行系统:将生产计划下发给车间执行系统,监控生产过程,实时采集设备运行状态、生产数据等,并进行分析、统计和报表生成。
3. 进料管理:对原材料、半成品和成品进行入库管理,包括入库登记、库存管理、质量检验等,以确保物料库存的准确性和及时性。
4. 生产过程监控:通过传感器和监控设备实时监测生产过程中的温度、压力、流量等参数,预测生产异常并及时采取措施,确保生产过程的稳定性和安全性。
5. 质量管理:对生产过程中的质量数据进行采集、分析和控制,包括生产过程中的质量检测、产品追溯等,以确保产品质量符合标准要求。
6. 设备维护管理:对工厂设备进行定期维护和保养,通过系统提供的设备维护计划、维修记录等功能,提高设备的可靠性和使用寿命。
7. 能源管理:对工厂的能源消耗进行监控和管理,通过系统提供的能源消耗统计、能耗预测等功能,实现能源的节约和环保。
8. 数据分析和决策支持:通过系统对生产过程中的数据进行分析和挖掘,提供生产效率、质量管理等方面的指标和报表,为决策层提供数据支持。
三、系统架构和技术选型1. 系统架构:采用分布式架构,将各个功能模块分散到不同的服务器上,通过消息队列、微服务等技术实现各模块之间的通信和协作。
2. 前端技术:采用Web前端开发技术,如HTML、CSS、JavaScript等,实现系统的用户界面和交互功能。
3. 后端技术:采用Java语言作为主要开发语言,使用Spring框架、Spring Boot微服务框架等,搭建系统的后端服务。
智能工厂整体建设方案详细
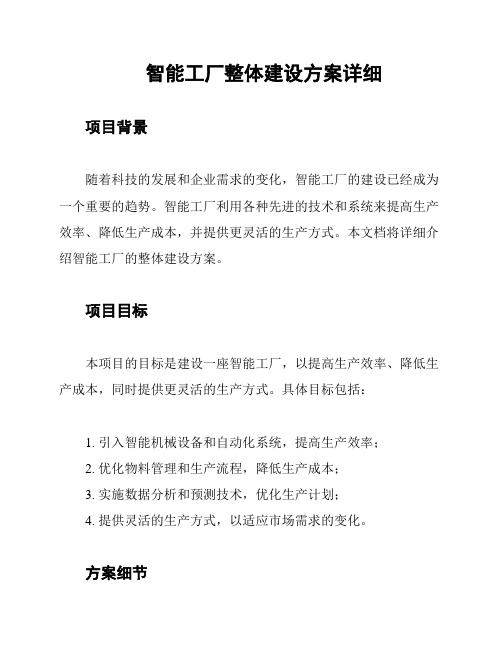
智能工厂整体建设方案详细项目背景随着科技的发展和企业需求的变化,智能工厂的建设已经成为一个重要的趋势。
智能工厂利用各种先进的技术和系统来提高生产效率、降低生产成本,并提供更灵活的生产方式。
本文档将详细介绍智能工厂的整体建设方案。
项目目标本项目的目标是建设一座智能工厂,以提高生产效率、降低生产成本,同时提供更灵活的生产方式。
具体目标包括:1. 引入智能机械设备和自动化系统,提高生产效率;2. 优化物料管理和生产流程,降低生产成本;3. 实施数据分析和预测技术,优化生产计划;4. 提供灵活的生产方式,以适应市场需求的变化。
方案细节1. 引入智能机械设备和自动化系统通过引入智能机械设备和自动化系统,可以实现生产过程的自动化和智能化。
具体措施包括:- 选择先进的机械设备,具备自动控制和监测功能;- 配置传感器和监测设备,实时获取生产数据;- 实施自动化控制系统,实现生产过程的自动化和优化。
2. 优化物料管理和生产流程优化物料管理和生产流程可以提高生产效率和降低生产成本。
具体措施包括:- 实施物料需求计划系统,准确预测物料需求;- 优化供应链管理,确保物料供应的及时性和稳定性;- 优化生产流程,减少生产环节和时间浪费。
3. 数据分析和预测技术通过数据分析和预测技术,可以优化生产计划,提高生产效率。
具体措施包括:- 收集生产数据并建立数据仓库;- 运用数据分析技术,挖掘生产过程中的潜在问题;- 运用预测技术,准确预测市场需求和物料需求。
4. 灵活的生产方式为了适应市场需求的变化,智能工厂需要提供灵活的生产方式。
具体措施包括:- 实施柔性生产线,能够快速实现生产线的切换;- 引入智能仓储和物流系统,提高物料管理的灵活性;- 优化生产调度系统,实现生产计划的快速调整。
总结本文档详细介绍了智能工厂的整体建设方案,包括引入智能机械设备和自动化系统,优化物料管理和生产流程,实施数据分析和预测技术,以及提供灵活的生产方式。
江苏省智能制造示范工厂培育和建设指南

江苏省智能制造示范工厂培育和建设指南下载温馨提示:该文档是我店铺精心编制而成,希望大家下载以后,能够帮助大家解决实际的问题。
文档下载后可定制随意修改,请根据实际需要进行相应的调整和使用,谢谢!并且,本店铺为大家提供各种各样类型的实用资料,如教育随笔、日记赏析、句子摘抄、古诗大全、经典美文、话题作文、工作总结、词语解析、文案摘录、其他资料等等,如想了解不同资料格式和写法,敬请关注!Download tips: This document is carefully compiled by theeditor.I hope that after you download them,they can help yousolve practical problems. The document can be customized andmodified after downloading,please adjust and use it according toactual needs, thank you!In addition, our shop provides you with various types ofpractical materials,such as educational essays, diaryappreciation,sentence excerpts,ancient poems,classic articles,topic composition,work summary,word parsing,copy excerpts,other materials and so on,want to know different data formats andwriting methods,please pay attention!江苏省智能制造示范工厂的培育与建设指南一、引言江苏省,作为中国制造业的重要基地,近年来积极推动智能制造的发展,以提升产业核心竞争力。
苏州智能化工厂建设指南
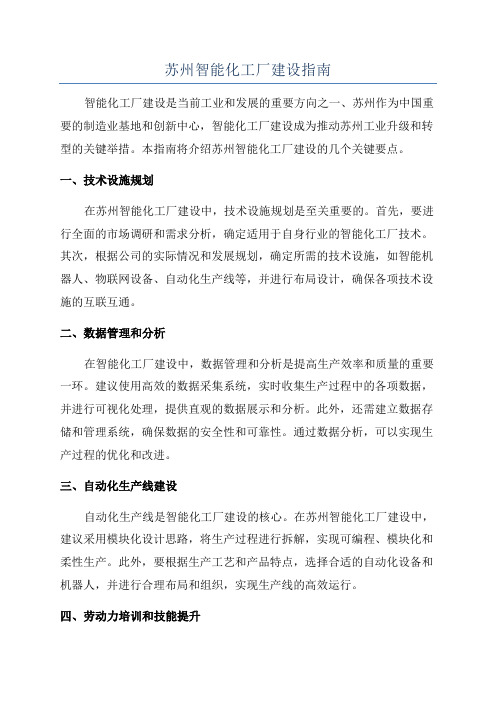
苏州智能化工厂建设指南智能化工厂建设是当前工业和发展的重要方向之一、苏州作为中国重要的制造业基地和创新中心,智能化工厂建设成为推动苏州工业升级和转型的关键举措。
本指南将介绍苏州智能化工厂建设的几个关键要点。
一、技术设施规划在苏州智能化工厂建设中,技术设施规划是至关重要的。
首先,要进行全面的市场调研和需求分析,确定适用于自身行业的智能化工厂技术。
其次,根据公司的实际情况和发展规划,确定所需的技术设施,如智能机器人、物联网设备、自动化生产线等,并进行布局设计,确保各项技术设施的互联互通。
二、数据管理和分析在智能化工厂建设中,数据管理和分析是提高生产效率和质量的重要一环。
建议使用高效的数据采集系统,实时收集生产过程中的各项数据,并进行可视化处理,提供直观的数据展示和分析。
此外,还需建立数据存储和管理系统,确保数据的安全性和可靠性。
通过数据分析,可以实现生产过程的优化和改进。
三、自动化生产线建设自动化生产线是智能化工厂建设的核心。
在苏州智能化工厂建设中,建议采用模块化设计思路,将生产过程进行拆解,实现可编程、模块化和柔性生产。
此外,要根据生产工艺和产品特点,选择合适的自动化设备和机器人,并进行合理布局和组织,实现生产线的高效运行。
四、劳动力培训和技能提升苏州智能化工厂建设不仅需要先进的技术设施,还需要具备相应的人才。
因此,建议在建设初期就进行劳动力培训和技能提升。
培训内容可以包括智能化工厂操作技能、数据分析和管理能力等方面。
通过培训,提高员工的智能化工厂应用能力,增强企业的核心竞争力。
五、安全管理和风险控制智能化工厂建设需要充分考虑安全管理和风险控制。
建议制定完善的安全管理和应急预案,确保员工的安全和生产的持续性。
此外,还需要引入智能监控和预警系统,对生产过程进行实时监测和预测,避免出现安全事故和生产故障。
六、绿色环保和可持续发展苏州智能化工厂建设要注重绿色环保和可持续发展。
建议采用节能设备和清洁生产技术,降低生产过程中的能耗和排放。
智能工厂的自动化生产线设计与建设指南

智能工厂的自动化生产线设计与建设指南智能工厂是利用先进的信息技术和自动化控制系统实现生产过程智能化、自动化的现代化工厂。
在当前数字化时代,智能工厂已成为企业提高生产效率和降低成本的关键手段。
为了帮助企业设计和建设智能工厂的自动化生产线,本文将提供一份详细的指南。
1. 规划与布局在设计智能工厂的自动化生产线之前,首先需要进行全面的规划和布局。
这包括确定工厂的整体目标、产品流程和生产能力等。
在规划阶段,需要考虑到生产线的布局和流程的优化,以最大程度地提高生产效率和降低生产成本。
2. 选购设备与技术选购设备与技术是智能工厂自动化生产线设计中的重要一环。
在此阶段,需要根据生产需求和目标确定所需的设备和技术。
选择合适的设备和技术可以增加生产效率、降低运营成本,并提高产品质量。
3. 自动化控制系统设计自动化控制系统是智能工厂自动化生产线的核心。
它负责对生产线进行整体控制和管理,并确保设备之间的协调运作。
在设计自动化控制系统时,需要考虑到生产线的复杂性和灵活性,并选择合适的控制方式和技术,如PLC(可编程逻辑控制器)、SCADA(监控与数据采集系统)等。
4. 机器人应用与集成机器人技术是智能工厂自动化生产线的重要组成部分。
机器人的应用可以大大提高生产效率和产品质量。
在设计自动化生产线时,需要确定机器人的类型和数量,并考虑到与其他设备的集成,以实现整体协同作业。
5. 数据采集与分析智能工厂的关键特点之一是数据的实时采集和分析。
通过对生产过程和设备数据的监控与分析,可以及时发现问题并采取相应的措施,以提高生产效率和产品质量。
在设计自动化生产线时,应充分考虑数据采集与分析的需求,并配置相应的传感器、仪表和软件系统等。
6. 培训与管理智能工厂的自动化生产线需要有专业的操作和维护人员。
在建设阶段,需要对相关员工进行培训,使其熟悉设备和工艺流程,并具备解决常见故障的能力。
此外,还需要建立相应的管理机制,确保生产线的稳定运行和持续改进。
智能工厂的建设与优化
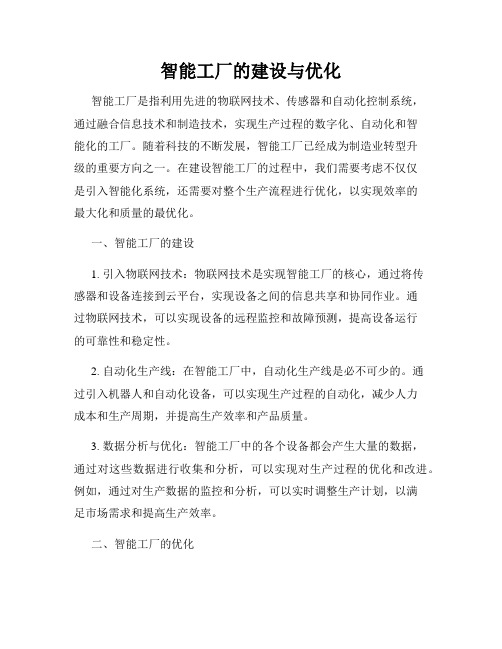
智能工厂的建设与优化智能工厂是指利用先进的物联网技术、传感器和自动化控制系统,通过融合信息技术和制造技术,实现生产过程的数字化、自动化和智能化的工厂。
随着科技的不断发展,智能工厂已经成为制造业转型升级的重要方向之一。
在建设智能工厂的过程中,我们需要考虑不仅仅是引入智能化系统,还需要对整个生产流程进行优化,以实现效率的最大化和质量的最优化。
一、智能工厂的建设1. 引入物联网技术:物联网技术是实现智能工厂的核心,通过将传感器和设备连接到云平台,实现设备之间的信息共享和协同作业。
通过物联网技术,可以实现设备的远程监控和故障预测,提高设备运行的可靠性和稳定性。
2. 自动化生产线:在智能工厂中,自动化生产线是必不可少的。
通过引入机器人和自动化设备,可以实现生产过程的自动化,减少人力成本和生产周期,并提高生产效率和产品质量。
3. 数据分析与优化:智能工厂中的各个设备都会产生大量的数据,通过对这些数据进行收集和分析,可以实现对生产过程的优化和改进。
例如,通过对生产数据的监控和分析,可以实时调整生产计划,以满足市场需求和提高生产效率。
二、智能工厂的优化1. 环境监测与管理:智能工厂应该实现对生产环境的实时监测和管理。
通过安装传感器,可以实时监测生产车间的温度、湿度和气体浓度等环境参数,及时发现并解决潜在的环境问题。
2. 设备维护与管理:智能工厂中的设备需要定期进行维护和管理,以确保其正常运行。
通过物联网技术,可以实现对设备的远程监控和故障预测,及时发现设备故障并进行维修,提高设备的可靠性和稳定性。
3. 生产过程优化:通过对生产数据和运营数据进行分析,可以实现生产过程的优化。
例如,通过对生产数据的监控和分析,可以发现生产中存在的问题,并及时调整生产计划和工艺参数,以提高生产效率和产品质量。
三、智能工厂的挑战与展望1. 数据安全与隐私保护:智能工厂中产生的大量数据需要保证其安全性和隐私性。
在建设智能工厂的过程中,需要采取相应的安全措施,确保数据不被泄露或篡改。
智能工厂总体规划及实施指南方案

智能工厂总体规划及实施指南方案一、引言随着科技的不断发展和智能技术的应用,智能工厂正逐渐成为制造行业的未来发展方向。
本文将详细介绍智能工厂总体规划的重要性以及实施指南方案,以帮助企业顺利实现智能化转型。
二、智能工厂总体规划1. 目标和愿景在制定智能工厂的总体规划时,首先需要确定明确的目标和愿景。
这些目标和愿景应与企业的战略目标相一致,并能够满足市场的需求和趋势。
2. 技术基础设施智能工厂的建设离不开先进的技术基础设施,包括先进的传感器、物联网技术、大数据分析、云计算等。
企业需要根据自身需求和资源情况,选择合适的技术基础设施来支持智能工厂的运营。
3. 生产流程优化智能工厂的总体规划应包括对生产流程的优化和改进。
通过引入自动化设备和智能化系统,可以提高生产效率、降低成本、减少人为错误,并提供更高质量的产品。
4. 数据安全和网络互联智能工厂涉及大量的数据收集、传输和分析,因此数据安全和网络互联是非常重要的考虑因素。
企业应制定相应的数据安全措施,确保数据的保密性和完整性。
5. 人力资源管理智能工厂的建设需要具备相关技能和知识的人才支持。
因此,企业在总体规划中需要考虑培训和招聘计划,以确保有足够的人力资源来支持智能工厂的运营。
三、实施指南方案1. 阶段性规划智能工厂的建设是一个复杂且长期的过程,企业可以将其分为不同的阶段进行规划和实施。
每个阶段应明确具体的目标和时间表,并根据实际情况进行调整和优化。
2. 资源投入和风险控制在实施智能工厂的过程中,企业需要合理安排资源投入,并进行风险评估和控制。
这包括资金、技术、人力资源等方面的投入,以及对可能出现的问题进行预判和解决方案的准备。
3. 跨部门合作智能工厂的建设需要涉及多个部门和团队的合作。
企业应设立跨部门的工作组,加强沟通和协调,确保各方的利益得到充分考虑,并共同推动智能工厂的建设。
4. 数据管理和分析智能工厂的运营依赖于大量的数据收集和分析,因此,企业需要建立有效的数据管理和分析系统。
加快建设智能工厂方案
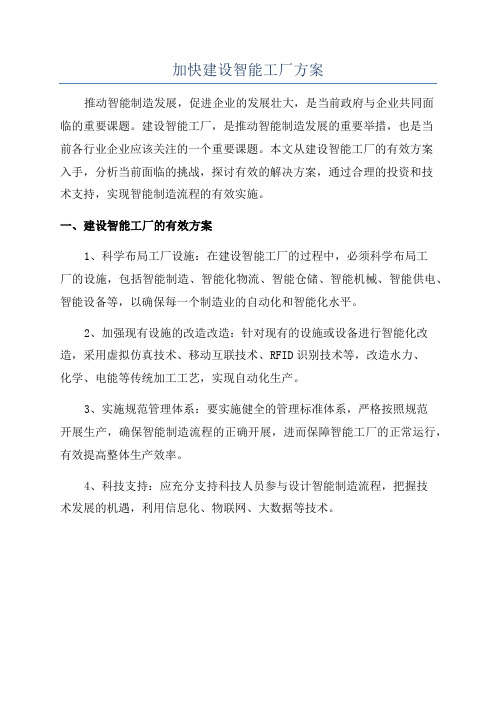
加快建设智能工厂方案
推动智能制造发展,促进企业的发展壮大,是当前政府与企业共同面
临的重要课题。
建设智能工厂,是推动智能制造发展的重要举措,也是当
前各行业企业应该关注的一个重要课题。
本文从建设智能工厂的有效方案
入手,分析当前面临的挑战,探讨有效的解决方案,通过合理的投资和技
术支持,实现智能制造流程的有效实施。
一、建设智能工厂的有效方案
1、科学布局工厂设施:在建设智能工厂的过程中,必须科学布局工
厂的设施,包括智能制造、智能化物流、智能仓储、智能机械、智能供电、智能设备等,以确保每一个制造业的自动化和智能化水平。
2、加强现有设施的改造改造:针对现有的设施或设备进行智能化改造,采用虚拟仿真技术、移动互联技术、RFID识别技术等,改造水力、
化学、电能等传统加工工艺,实现自动化生产。
3、实施规范管理体系:要实施健全的管理标准体系,严格按照规范
开展生产,确保智能制造流程的正确开展,进而保障智能工厂的正常运行,有效提高整体生产效率。
4、科技支持:应充分支持科技人员参与设计智能制造流程,把握技
术发展的机遇,利用信息化、物联网、大数据等技术。
苏州市智能车间奖励标准
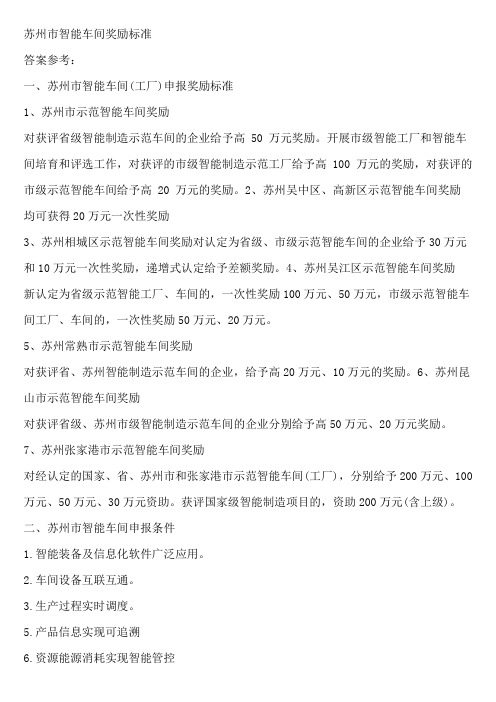
苏州市智能车间奖励标准答案参考:一、苏州市智能车间(工厂)申报奖励标准1、苏州市示范智能车间奖励对获评省级智能制造示范车间的企业给予高 50 万元奖励。
开展市级智能工厂和智能车间培育和评选工作,对获评的市级智能制造示范工厂给予高 100 万元的奖励,对获评的市级示范智能车间给予高 20 万元的奖励。
2、苏州吴中区、高新区示范智能车间奖励均可获得20万元一次性奖励3、苏州相城区示范智能车间奖励对认定为省级、市级示范智能车间的企业给予30万元和10万元一次性奖励,递增式认定给予差额奖励。
4、苏州吴江区示范智能车间奖励新认定为省级示范智能工厂、车间的,一次性奖励100万元、50万元,市级示范智能车间工厂、车间的,一次性奖励50万元、20万元。
5、苏州常熟市示范智能车间奖励对获评省、苏州智能制造示范车间的企业,给予高20万元、10万元的奖励。
6、苏州昆山市示范智能车间奖励对获评省级、苏州市级智能制造示范车间的企业分别给予高50万元、20万元奖励。
7、苏州张家港市示范智能车间奖励对经认定的国家、省、苏州市和张家港市示范智能车间(工厂),分别给予200万元、100万元、50万元、30万元资助。
获评国家级智能制造项目的,资助200万元(含上级)。
二、苏州市智能车间申报条件1.智能装备及信息化软件广泛应用。
2.车间设备互联互通。
3.生产过程实时调度。
5.产品信息实现可追溯6.资源能源消耗实现智能管控7.车间安全水平提升。
8.经济效益明显提升。
9.积极应用国产核心软件和核心装备。
三、苏州市智能工厂申报条件1、企业在本市注册,具有独立法人资格,具有健全的财务管理机构和制度,信用良好且无违法记录2项目须具有知识产权归属明确的核心技术;3、项目总投资不低于1亿元,其中智能制造装备、系统与软件投入不低于7000万元;4、项目单位应牵头组织系统集成商、软件开发商、核心智能制造装备供应商等单位按照市场化原则建立项目联合体,联合体须突出需求牵引和问题导向,通过签署合作协议书,明确组织方式和责权利,形成推进智能制造发展的长效机制:5、每个项目单位限报1个项目;智能工厂项目建设具体要求参考《苏州市智能工厂建设指南》。
苏州智慧工地实施方案

苏州智慧工地实施方案一、背景。
随着城市建设的不断发展,工地施工管理面临着越来越多的挑战。
传统的施工管理方式已经不能满足现代化城市建设的需求,因此,引入智慧工地管理成为了当前城市建设的必然选择。
作为中国具有代表性的历史文化名城之一,苏州市在城市建设中也积极探索智慧工地实施方案,以提高工地管理效率,保障施工安全,促进城市建设的可持续发展。
二、目标。
苏州智慧工地实施方案的目标是通过引入先进的信息技术和智能设备,实现工地管理的数字化、智能化和网络化,提高工地管理的效率和水平,减少施工安全事故,改善施工环境,为城市建设提供更好的支持。
三、实施方案。
1.信息化管理。
引入建筑信息模型(BIM)技术,实现对工地施工全过程的数字化管理。
通过BIM技术,可以对建筑结构、设备、材料等进行全方位的模拟和管理,提前发现施工中的问题,并进行优化,提高施工效率,减少资源浪费。
2.智能监控。
在工地内部和周边设置智能监控设备,实现对施工现场的实时监控。
通过视频监控、传感器等设备,可以及时发现施工中的安全隐患,预防事故的发生。
同时,还可以对施工现场的环境进行监测,保障施工环境的安全和卫生。
3.移动化管理。
引入移动化管理系统,实现对工地管理的实时监控和调度。
工地管理人员可以通过移动设备随时随地对工地施工情况进行监控和管理,及时处理施工中的问题,提高管理效率。
4.智能设备。
在工地施工中引入智能设备,如智能机械臂、无人机等,实现对施工过程的自动化和智能化。
这些智能设备可以减少人力投入,提高施工效率,同时减少人员的安全风险。
四、效果。
通过苏州智慧工地实施方案的实施,可以实现工地管理的数字化、智能化和网络化,提高工地管理的效率和水平,减少施工安全事故,改善施工环境,为城市建设提供更好的支持。
同时,还可以为其他城市的智慧工地建设提供借鉴和参考。
苏州智能化工厂建设指南规范
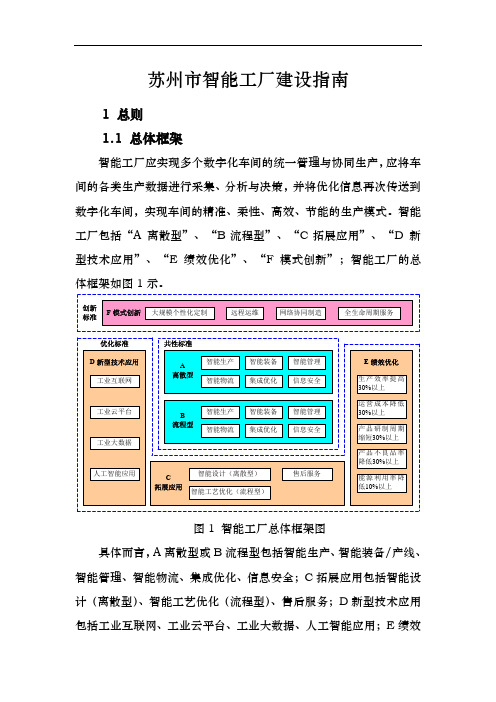
苏州市智能工厂建设指南1 总则1.1 总体框架智能工厂应实现多个数字化车间的统一管理与协同生产,应将车间的各类生产数据进行采集、分析与决策,并将优化信息再次传送到数字化车间,实现车间的精准、柔性、高效、节能的生产模式。
智能工厂包括“A 离散型”、“B流程型”、“C拓展应用”、“D 新型技术应用”、“E 绩效优化”、“F 模式创新”;智能工厂的总体框架如图1示。
图1 智能工厂总体框架图具体而言,A离散型或B流程型包括智能生产、智能装备/产线、智能管理、智能物流、集成优化、信息安全;C拓展应用包括智能设计(离散型)、智能工艺优化(流程型)、售后服务;D新型技术应用包括工业互联网、工业云平台、工业大数据、人工智能应用;E绩效优化包括生产效率提高30%以上、运营成本降低30%以上、产品研制周期缩短30%以上、产品不良品率降低30%以上、能源利用率降低10%以上。
F模式创新包括大规模个性化定制、远程运维、网络协同制造、全生命周期服务。
1.2 基本要求智能工厂的基本要求如下:(1) 设施全面互联建立各级标识解析节点和公共递归解析节点,促进信息资源集成共享;建立工业互联网工厂内网,工业以太网、工业现场总线、IPv6等技术,实现生产装备、传感器、控制系统与管理系统的互联;利用IPv6、工业物联网等技术实现工厂内、外网以及设计、生产、管理、服务各环节的互联,支持内、外网业务协同。
(2) 系统全面互通工厂的总体设计、工艺流程及布局均已建立数字化模型可进行模拟仿真,应用数字化三维设计与工艺技术进行设计仿真;建立制造执行系统(MES),实现计划、调度、质量、设备、生产、能效等管理功能;建立企业资源计划系统(ERP),实现供应链、物流、成本等企业经营管理功能;建立产品数据管理系统(PDM),实现产品设计、工艺数据的管理;在此基础上,制造执行系统(MES)、企业资源计划(ERP)与数字化三维设计仿真软件、产品数据管理(PDM)、供应链管理(SCM)、客户关系管理(CRM)等系统实现互通集成。
智能制造工厂布局与规划作业指导书
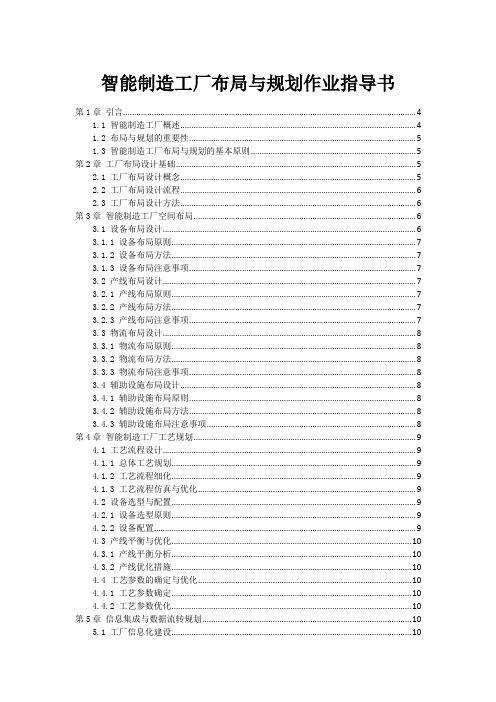
智能制造工厂布局与规划作业指导书第1章引言 (4)1.1 智能制造工厂概述 (4)1.2 布局与规划的重要性 (5)1.3 智能制造工厂布局与规划的基本原则 (5)第2章工厂布局设计基础 (5)2.1 工厂布局设计概念 (5)2.2 工厂布局设计流程 (6)2.3 工厂布局设计方法 (6)第3章智能制造工厂空间布局 (6)3.1 设备布局设计 (6)3.1.1 设备布局原则 (7)3.1.2 设备布局方法 (7)3.1.3 设备布局注意事项 (7)3.2 产线布局设计 (7)3.2.1 产线布局原则 (7)3.2.2 产线布局方法 (7)3.2.3 产线布局注意事项 (7)3.3 物流布局设计 (8)3.3.1 物流布局原则 (8)3.3.2 物流布局方法 (8)3.3.3 物流布局注意事项 (8)3.4 辅助设施布局设计 (8)3.4.1 辅助设施布局原则 (8)3.4.2 辅助设施布局方法 (8)3.4.3 辅助设施布局注意事项 (8)第4章智能制造工厂工艺规划 (9)4.1 工艺流程设计 (9)4.1.1 总体工艺规划 (9)4.1.2 工艺流程细化 (9)4.1.3 工艺流程仿真与优化 (9)4.2 设备选型与配置 (9)4.2.1 设备选型原则 (9)4.2.2 设备配置 (9)4.3 产线平衡与优化 (10)4.3.1 产线平衡分析 (10)4.3.2 产线优化措施 (10)4.4 工艺参数的确定与优化 (10)4.4.1 工艺参数确定 (10)4.4.2 工艺参数优化 (10)第5章信息集成与数据流转规划 (10)5.1 工厂信息化建设 (10)5.1.2 信息系统规划 (11)5.1.3 信息安全策略 (11)5.2 设备互联互通 (11)5.2.1 设备联网 (11)5.2.2 设备数据接口 (11)5.2.3 设备远程监控与维护 (11)5.3 数据采集与处理 (11)5.3.1 数据采集 (11)5.3.2 数据预处理 (11)5.3.3 数据存储与管理 (11)5.4 数据流转与共享 (12)5.4.1 数据流转机制 (12)5.4.2 数据共享平台 (12)5.4.3 数据分析与挖掘 (12)第6章智能制造工厂物流规划 (12)6.1 物流系统设计 (12)6.1.1 设计原则 (12)6.1.2 设计目标 (12)6.1.3 设计内容 (12)6.2 仓储规划与管理 (12)6.2.1 仓储规划 (12)6.2.2 仓储管理 (13)6.3 输送设备选型与布局 (13)6.3.1 输送设备选型 (13)6.3.2 输送设备布局 (13)6.4 智能物流系统集成 (13)6.4.1 系统集成目标 (13)6.4.2 系统集成内容 (13)6.4.3 系统集成技术 (13)第7章智能制造工厂安全与环保规划 (14)7.1 安全生产规划 (14)7.1.1 安全生产目标 (14)7.1.2 安全生产组织架构 (14)7.1.3 安全生产制度 (14)7.1.4 安全生产措施 (14)7.2 环境保护规划 (14)7.2.1 环保目标 (14)7.2.2 环保设施 (14)7.2.3 环保制度 (14)7.2.4 环保措施 (14)7.3 职业健康与安全 (14)7.3.1 职业健康目标 (15)7.3.2 职业健康管理 (15)7.3.4 职业安全防护 (15)7.4 应急预案与风险管理 (15)7.4.1 应急预案 (15)7.4.2 应急演练 (15)7.4.3 风险识别与评估 (15)7.4.4 风险监测与预警 (15)第8章智能制造工厂质量管理 (15)8.1 质量管理体系构建 (15)8.1.1 建立质量管理框架:根据智能制造工厂的特点,构建全面、系统的质量管理体系,保证生产过程中产品质量的稳定与可靠。
智能工厂和数字车间建设实施指南

智能工厂和数字车间建设实施指南智能工厂和数字车间建设实施指南的主要目的是为企业提供一个系统化的指导,帮助其实施智能工厂和数字车间的建设。
下面是一些关键步骤和注意事项:1. 评估现状:首先要对企业现有的生产流程、设备和技术进行评估,确定目前的数字化程度和需要改进的地方。
2. 制定计划:根据评估结果,制定一个详细的建设计划,包括目标、时间表、资源需求和预算等。
3. 设计架构:确定智能工厂和数字车间的架构,包括网络通信、数据采集和分析平台、传感器和物联网设备等。
4. 设备采购和安装:根据设计架构,选择合适的设备和技术供应商,并进行采购和安装。
5. 数据集成和分析:配置设备,使其能够进行数据采集并与其他系统进行集成。
同时,建立数据分析平台,对采集到的数据进行处理和分析,以实现实时监控和优化生产。
6. 培训和转型:培训员工,使其掌握智能工厂和数字车间的操作和管理技能。
同时,推动组织文化和流程的转型,以适应数字化生产环境。
7. 持续改进:建立一个持续改进的机制,定期评估和优化智能工厂和数字车间的性能,引入新技术和解决方案,以提高生产效率和质量。
在实施智能工厂和数字车间建设时,也需要注意以下几点:1. 统一标准:确保设备、通信和数据分析等方面有统一的标准,以便实现不同系统之间的互操作性和数据共享。
2. 安全保护: 在数字化生产环境下,要做好信息安全和设备安全的保护工作,以防止数据泄露、设备故障和网络攻击等风险。
3. 合作伙伴选择:选择有经验和专业能力的合作伙伴,能够提供技术支持和解决方案,并在建设过程中进行有效的沟通和协作。
4. 技术选型:选择合适的技术和解决方案,要考虑其适应性、可扩展性和成本效益等因素。
5. 绩效评估:建立一个完善的绩效评估体系,通过指标和数据来评估智能工厂和数字车间的效果,从而为持续改进提供依据。
总之,智能工厂和数字车间的建设需要一个系统化的规划和实施过程,同时还需要注重标准化、安全保护和持续改进等方面的工作。
智能工厂建设步骤以及注意事项

智能工厂建设步骤以及注意事项智能工厂是一个高度自动化和数字化的制造环境,它利用先进的技术和系统来提高生产效率、降低成本和提升产品质量。
本文将介绍智能工厂建设的基本步骤和需要注意的事项。
1. 规划阶段在智能工厂建设之前,需要进行详细的规划。
这包括确定工厂的目标、制定实施计划、评估技术和人力需求,以及确定预算和时间表。
2. 技术选型在选择智能工厂的技术时,需要考虑以下因素:- 自动化设备:选择适合生产需求的自动化设备,例如机器人、传感器和控制系统。
- 数据管理系统:建立先进的数据管理系统,包括工厂自动化系统、物联网设备和云计算平台。
- 联网能力:确保智能工厂中的各种设备可以相互通信和协同工作。
3. 设备安装和配置安装和配置智能工厂的设备是建设过程中的关键步骤。
这包括:- 设备安装:确保设备按照制造商的指导进行正确安装,以确保其正常运行。
- 系统配置:根据工厂的需求和规格,对自动化系统和数据管理系统进行配置。
4. 人员培训在智能工厂建设完成后,培训工作人员以确保他们能够熟练使用新的技术和系统。
这包括:- 操作培训:培训工人和操作员使用自动化设备和相关系统。
- 维护培训:培训维修人员进行设备维护和故障排除。
5. 监控和优化一旦智能工厂开始运行,需要进行持续的监控和优化。
这包括:- 数据分析:使用工厂的数据管理系统分析生产数据,发现潜在的问题和优化机会。
- 进行改进:根据数据分析的结果,采取措施改进生产效率和品质。
注意事项在智能工厂建设中,还需要注意以下事项:- 安全性:确保设备和系统的安全性,防止数据泄露和设备故障引发的安全风险。
- 数据隐私:保护工厂和客户的数据隐私,遵守相关法规和规定。
- 人力资源:培养和吸引具备智能制造技术知识的员工,以确保工厂的可持续发展。
以上是智能工厂建设的基本步骤以及需要注意的事项。
根据工厂的具体情况和需求,可能会有一些额外的步骤和问题需要考虑。
因此,在实际建设过程中,建议寻求专业的咨询和指导。
江苏省工业互联网标杆工厂建设指南【模板】

附件1:江苏省工业互联网标杆工厂建设指南根据国家《国务院关于深化“互联网+先进制造业”发展工业互联网的指导意见》,以及江苏省工业互联网协同发展工作要求,鼓励和支持企业开展工业互联网技术集成应用,推进江苏省工业互联网标杆工厂建设,特制订本指南。
工业互联网标杆工厂主要依托工业互联网平台,综合运用数据采集与集成应用、建模分析与优化等技术,实现制造系统各层级优化,以及产品、工厂资产和商业的全流程优化,完成企业生产模式创新。
本指南主要包括企业基础能力、企业标杆能力和业态模式创新等方面建设内容。
一、企业基础能力1、基础技术能力一是网络技术方面。
在工厂内建有相对完善的通信网络架构,建立标识管理系统,运用实时工业以太网、4G/5G通讯、NB-IoT、工业PON、IPv6等技术,实现设计、工艺、制造、检测、物流等各环节之间的全面互联互通,并形成对产品局部或全部生产流程的信息追溯能力。
二是平台技术方面。
在工厂内应用工业互联网平台,实现数据的集成、分析和挖掘。
综合运用协议转换、边缘计算、分布式存储、并行计算、负载与资源调度、多租户管理、容器与虚拟化、面向服务的架构(SOA)/微服务架构(MSA)、图形化编程、低代码开发、深度学习、知识图谱等技术,拓展数据的汇聚与- 1 -管理能力,提升企业管理与决策能力,实现面向单独及综合场景的统一建模与集成分析优化。
三是安全技术方面。
在工厂内部署运用工业防火墙、安全检测审计、入侵检测等安全技术措施,形成网络防护、应急响应等信息安全保障能力,采用全生命周期方法有效避免系统失效。
2、制造系统能力一是生产现场优化方面。
运用智能感知与控制、机器视觉、边缘计算、数据可视化管理、数据挖掘、模式识别、统一模型管理等技术,构建建模分析环境和优化模型组件,实现工艺流程的优化调整和产品质量数据的在线检测,完成生产现场的工艺优化与质量检测。
二是生产管理优化方面。
运用数据集成、统一模型管理、模式识别、事件驱动架构、大数据、数据仓库、非关系型数据库、联机分析处理(OLAP)、数据挖掘、系统冗余、路径规划算法等技术,实现排产计划调整、产品质量追溯、能耗平衡分析、物流路径控制、安全风险预警等功能,完成生产管理层的进度智能管控、全流程质量优化、能源效率优化、厂内物流优化、智能安全管控。
- 1、下载文档前请自行甄别文档内容的完整性,平台不提供额外的编辑、内容补充、找答案等附加服务。
- 2、"仅部分预览"的文档,不可在线预览部分如存在完整性等问题,可反馈申请退款(可完整预览的文档不适用该条件!)。
- 3、如文档侵犯您的权益,请联系客服反馈,我们会尽快为您处理(人工客服工作时间:9:00-18:30)。
苏州市智能工厂建设指南1 总则1.1 总体框架智能工厂应实现多个数字化车间的统一管理与协同生产,应将车间的各类生产数据进行采集、分析与决策,并将优化信息再次传送到数字化车间,实现车间的精准、柔性、高效、节能的生产模式。
智能工厂包括“A 离散型”、“B流程型”、“C拓展应用”、“D 新型技术应用”、“E 绩效优化”、“F 模式创新”;智能工厂的总体框架如图1示。
图1 智能工厂总体框架图具体而言,A离散型或B流程型包括智能生产、智能装备/产线、智能管理、智能物流、集成优化、信息安全;C拓展应用包括智能设计(离散型)、智能工艺优化(流程型)、售后服务;D新型技术应用包括工业互联网、工业云平台、工业大数据、人工智能应用;E绩效优化包括生产效率提高30%以上、运营成本降低30%以上、产品研制周期缩短30%以上、产品不良品率降低30%以上、能源利用率降低10%以上。
F模式创新包括大规模个性化定制、远程运维、网络协同制造、全生命周期服务。
1.2 基本要求智能工厂的基本要求如下:(1) 设施全面互联建立各级标识解析节点和公共递归解析节点,促进信息资源集成共享;建立工业互联网工厂内网,工业以太网、工业现场总线、IPv6等技术,实现生产装备、传感器、控制系统与管理系统的互联;利用IPv6、工业物联网等技术实现工厂内、外网以及设计、生产、管理、服务各环节的互联,支持内、外网业务协同。
(2) 系统全面互通工厂的总体设计、工艺流程及布局均已建立数字化模型可进行模拟仿真,应用数字化三维设计与工艺技术进行设计仿真;建立制造执行系统(MES),实现计划、调度、质量、设备、生产、能效等管理功能;建立企业资源计划系统(ERP),实现供应链、物流、成本等企业经营管理功能;建立产品数据管理系统(PDM),实现产品设计、工艺数据的管理;在此基础上,制造执行系统(MES)、企业资源计划(ERP)与数字化三维设计仿真软件、产品数据管理(PDM)、供应链管理(SCM)、客户关系管理(CRM)等系统实现互通集成。
(3) 数据全面互换建立生产过程数据采集和分析系统(SCADA),实现生产进度、现场操作、质量检验、设备状态、物料传送等生产现场数据自动上传,并实现可视化管理。
制造执行系统(MES)、企业资源计划(ERP)与数字化三维设计仿真软件、产品数据管理(PDM)、供应链管理(SCM)、客户关系管理(CRM)等系统之间的多元异构数据实现互换。
建有工业信息安全管理制度和技术防护体系,具备网络防护、应急响应等信息安全保障能力。
建有功能安全保护系统,采用全生命周期方法有效避免系统失效。
(4) 产业高度互融构建基于云计算的集成共享服务平台,实现从单纯提供产品向同时提供产品和服务转变,从大规模生产向个性化定制生产转变,促进制造业与服务业相融合。
2 共性标准智能车间是智能工厂的基础,智能车间标准参见《江苏省智能车间认定方法》。
共性标准是智能工厂的必备条件,解决智能工厂共性关键问题,包括智能生产、智能装备/产线、智能管理、智能物流、集成优化、信息安全。
2.1 智能生产(离散型)建立制造执行系统(MES),实现生产计划管理、生产过程控制、产品质量管理、车间库存管理、项目看板管理智能化,提高企业制造执行能力。
建立企业资源计划系统(ERP),实现供应链、物流、成本等企业经营管理功能。
建立工厂内部通信网络架构,实现设计、工艺、制造、检验、物流等制造过程各环节之间,以及制造过程与制造执行系统(MES)和企业资源计划系统(ERP)的信息互联互通。
2.1.1 生产排程柔性化建立高级计划与排产系统(APS),通过集中排程、可视化调度及时准确掌握生产、设备、人员、模具等生产信息,应用多种算法提高生产排程效率,实现柔性生产,全面适应多品种、小批量的订单需求。
2.1.2 生产作业数字化生产作业基于生产计划自动生产,工单可传送到机台,系统自动接收生产工单,并可查询工艺图纸等工艺文件。
2.1.3 质量控制可追溯建立数据采集与监视控制系统(SCADA),通过条形码、二维码或无线射频识别(RFID)卡等识别技术,可查看每个产品生产过程的订单信息、报工信息、批次号、工作中心、设备信息、人员信息,实现生产工序数据跟踪,产品档案可按批次进行生产过程和使用物料的追溯;自动采集质量检测设备参数,产品质量实现在线自动检测、报警和诊断分析,提升质量检验效率与准确率;生产过程的质量数据实时更新,统计过程控制(SPC)自动生成,实现质量全程追溯。
2.1.4 生产设备自管理设备台账、点检、保养、维修等管理实现数字化;通过传感器采集设备的相关工艺参数,自动在线监测设备工作状态,实现在线数据处理和分析判断,及时进行设备故障自动报警和预诊断,部分设备可自动调试修复;设备综合效率(OEE)自动生成。
2.1.5 生产管理透明化可视化系统实时呈现包含生产状况(生产数、生产效率、订单总数、完成率)、品质状况(生产数中的不良数、不良率)、设备状况等生产数据;生产加工进度通过各种报表、图表形式展示,直观有效地反映生产状况及品质状况。
2.1.6 物流配送智能化基于条形码、二维码、无线射频识别(RFID)等识别技术实现自动出入库管理,实现仓储配送与生产计划、制造执行以及企业资源管理等业务的集成;能够基于生产线实际生产情况拉动物料配送,根据客户和产品需求调整目标库存水平。
2.1.7 能源资源利用集约化建立能源综合管理监测系统,主要耗能设备实现实时监测与控制;建立产耗预测模型,水、电、气(汽)、煤、油以及物料等消耗实现实时监控、自动分析,实现能源资源的优化调度、平衡预测和有效管理。
2.2 智能生产(流程型)建立生产执行系统(MES),生产计划、调度均建立模型,实现生产模型化分析决策、过程量化管理、成本和质量动态跟踪以及从原材料到产成品的一体化协同优化。
建立企业资源计划系统(ERP),实现企业经营、管理和决策的智能优化。
建立工厂通信网络架构,实现工艺、生产、检验、物流等制造过程各环节之间,以及制造过程与数据采集和监控系统、生产执行系统(MES)、企业资源计划系统(ERP)之间的信息互联互通。
2.2.1 生产排程柔性化建立高级计划与排产系统(APS),通过集中排程、可视化调度、工业大数据等及时准确掌握生产、设备、人员等生产信息,应用多种算法提高生产排程效率,实现柔性生产,全面适应多品种、小批量的订单需求。
2.2.2 生产作业数字化生产管理系统和分布式控制系统(DCS)全面集成,自动生成企业所需要的日报表、盘点表、月质量报表等相关报表。
生产流水线上重要工艺参数、设备状态、料位、喂料量等实行实时监控;图形站上的生产流程图所有显示值均为动态数据,可定时刷新。
2.2.3 质量控制可追溯生产线安装大量传感器探测温度、压力、热能、振动和噪声等,用大数据分析整个生产流程,一旦某个流程偏离标准工艺,及时报警预判。
质量管理系统和化验设备无缝集成,实现在线检测。
企业基于同一个平台系统进行操作,与检测设备集成,自动形成使用数据,系统自动汇总质量数据信息。
统计过程控制(SPC)自动生产,实现质量全程追溯。
2.2.4 生产设备自管理设备台账、点检、保养、维修等管理实现数字化;通过传感器采集设备的相关工艺参数,自动在线监测设备工作状态,实现在线数据处理和分析判断,及时进行设备故障自动报警和预诊断,部分设备可自动调试修复;设备综合效率(OEE)自动生成。
2.2.5 生产管理透明化可视化系统实时呈现包含生产状况(生产数、生产效率、订单总数、完成率)、品质状况(生产数中的不良数、不良率)、设备状况等生产数据;生产加工进度通过各种报表、图表形式展示,直观有效地反映生产状况及品质状况。
2.2.6 能源系统和水电仪表无缝整合准确掌握各类能源介质分系统运行状况;完善能源计量体系,提供数据支撑、统一数据来源。
2.2.7 物流配送智能化基于条形码、二维码、无线射频识别(RFID)等识别技术实现自动出入库管理;实现仓储配送与生产计划、制造执行以及企业资源管理等业务的集成。
能够基于生产线实际生产情况拉动物料配送,基于客户和产品需求调整目标库存水平。
2.3 智能装备(离散型)智能装备主要包括高档数控机床与工业机器人、增材制造装备、智能传感与控制装备、智能检测与装配装备、智能物流与仓储装备等。
制造装备数控化率超过70%,并实现高档数控机床与工业机器人、智能传感与控制装备、智能检测与装配装备、智能物流与仓储装备等关键技术装备之间的信息互联互通与集成。
2.4 智能产线(流程型)采用自动化生产线、机器人、高端数控机床等,建立先进控制系统,配置数据采集系统,建立实时数据平台。
采用先进控制系统,生产工艺数据自动采集率90%以上,工厂自控投用率达到90%以上,关键生产环节实现基于模型的先进控制和在线优化。
2.5 智能管理建立企业资源计划(ERP),以系统化思维和供应链管理为核心,科学配置资源,优化运行模式,改善业务流程,提高决策效率。
利用跨供应链的产品全生命周期管理系统(PLM),改善产品研发速度和敏捷性,增强交付客户化、为客户量身定做的能力。
高级计划与排产系统(APS)应用拓展到企业上下游供应链,围绕核心企业的网链关系,在正向需求流及逆向供应流之间增加供需平衡管控机制,实现供应链各环节共同规划需求、订单和预测分析评估调整、产能和关键物料规划与控制、多工厂多车间协同、短中长期物料供需平衡管控等。
2.5.1 客户管理企业信息中心应用先进的信息(CRM、APP等)以及互联网技术,全方位管理企业内部销售体系及面向市场的商业机会,需涉及人员、订单、服务,以及客户跟踪、维护与反馈等信息,从而实现信息化的管理模式,并需建立创新的与客户互动的信息平台,所采集的交期达成、产品质量、售前(后)服务等数据需及时反馈给工厂资源管理信息中心。
2.5.2 供应商管理以数字化车间集成信息及采购运营数据为支撑,分析不同时期影响各个产品采购的主要因素,动态指导供应商管理,提升供应商水平。
结合客户订单及生产制造基础信息,自动计算采购清单和采购订单分配方案,降低采购风险,提高供应商对采购决策的信服度,增强供应商战略合作的稳定性。
2.5.3 供应链管理在对工厂运营和车间集成信息等进行关联细分的基础上,实现工厂与车间、车间与车间之间供应链各环节成员能力与特征的标签化,结合客户管理和供应商管理,以实现工厂柔性生产为目标,根据成员标签动态调整供应链各环资源配置和信息流向,增强供应链稳定性和抗风险能力,实现供应链整体能力的提升。
2.5.4 终端客户质量管理根据工厂信息系统(CRM、SCM)结合物联网CPS技术搜集客户质量反馈和产品使用状况反馈数据,并用实时的、满足大数据体量的数据汇集到大数据平台,运用分析引擎智能分析质量问题模式及产生原因,排查影响质量的因素,智能化地提供改善建议。