机械制造知识点总结第二章
机械制造工艺学知识点总结(含名词解释)
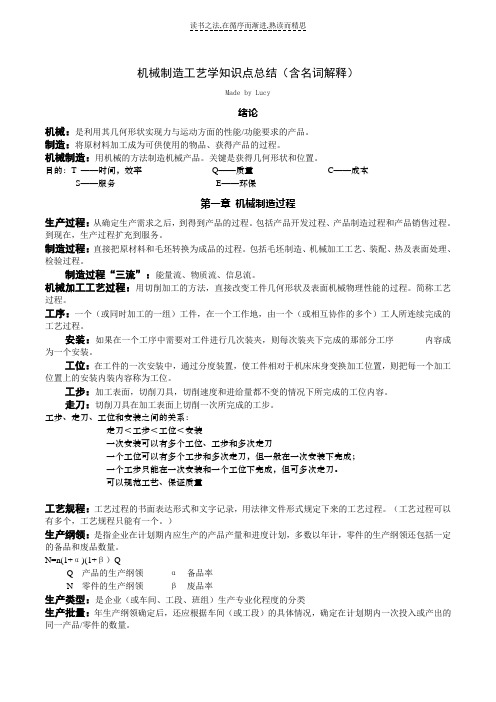
机械制造工艺学知识点总结(含名词解释)Made by Lucy绪论机械:是利用其几何形状实现力与运动方面的性能/功能要求的产品。
制造:将原材料加工成为可供使用的物品、获得产品的过程。
机械制造:用机械的方法制造机械产品。
关键是获得几何形状和位置。
目的:T ——时间,效率Q——质量C——成本S——服务E——环保第一章机械制造过程生产过程:从确定生产需求之后,到得到产品的过程。
包括产品开发过程、产品制造过程和产品销售过程。
到现在,生产过程扩充到服务。
制造过程:直接把原材料和毛坯转换为成品的过程。
包括毛坯制造、机械加工工艺、装配、热及表面处理、检验过程。
制造过程“三流”:能量流、物质流、信息流。
机械加工工艺过程:用切削加工的方法,直接改变工件几何形状及表面机械物理性能的过程。
简称工艺过程。
工序:一个(或同时加工的一组)工件,在一个工作地,由一个(或相互协作的多个)工人所连续完成的工艺过程。
安装:如果在一个工序中需要对工件进行几次装夹,则每次装夹下完成的那部分工序内容成为一个安装。
工位:在工件的一次安装中,通过分度装置,使工件相对于机床床身变换加工位置,则把每一个加工位置上的安装内装内容称为工位。
工步:加工表面,切削刀具,切削速度和进给量都不变的情况下所完成的工位内容。
走刀:切削刀具在加工表面上切削一次所完成的工步。
工步、走刀、工位和安装之间的关系:走刀<工步<工位<安装一次安装可以有多个工位、工步和多次走刀一个工位可以有多个工步和多次走刀,但一般在一次安装下完成;一个工步只能在一次安装和一个工位下完成,但可多次走刀。
可以规范工艺、保证质量工艺规程:工艺过程的书面表达形式和文字记录,用法律文件形式规定下来的工艺过程。
(工艺过程可以有多个,工艺规程只能有一个。
)生产纲领:是指企业在计划期内应生产的产品产量和进度计划,多数以年计,零件的生产纲领还包括一定的备品和废品数量。
N=n(1+α)(1+β)QQ---产品的生产纲领α---备品率N---零件的生产纲领β---废品率生产类型:是企业(或车间、工段、班组)生产专业化程度的分类生产批量:年生产纲领确定后,还应根据车间(或工段)的具体情况,确定在计划期内一次投入或产出的同一产品/零件的数量。
机械制造基础 知识点汇总
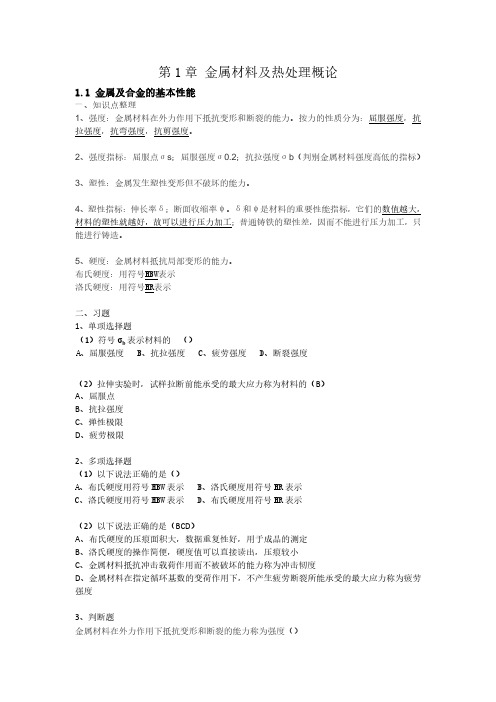
第1章 金属材料及热处理概论1.1 金属及合金的基本性能2、强度指标:屈服点σs ;屈服强度σ0.2;抗拉强度σb (判别金属材料强度高低的指标)3、塑性:金属发生塑性变形但不破坏的能力。
5、硬度:金属材料抵抗局部变形的能力。
布氏硬度:用符号HBW 洛氏硬度:用符号表示 HR表示二、习题1、单项选择题(1)符号σb 表示材料的 ()A 、屈服强度B 、抗拉强度C 、疲劳强度D 、断裂强度(2)拉伸实验时,试样拉断前能承受的最大应力称为材料的(B ) A 、屈服点 B 、抗拉强度 C 、弹性极限 D 、疲劳极限2、多项选择题(1)以下说法正确的是()A 、布氏硬度用符号HBW 表示B 、洛氏硬度用符号HR 表示C 、洛氏硬度用符号HBW 表示D 、布氏硬度用符号HR 表示(2)以下说法正确的是(BCD )A 、布氏硬度的压痕面积大,数据重复性好,用于成品的测定B 、洛氏硬度的操作简便,硬度值可以直接读出,压痕较小C 、金属材料抵抗冲击载荷作用而不被破坏的能力称为冲击韧度D 、金属材料在指定循环基数的变荷作用下,不产生疲劳断裂所能承受的最大应力称为疲劳强度3、判断题金属材料在外力作用下抵抗变形和断裂的能力称为强度()4、填空题强度按力的性质有___、___、___。
5、简答题简述拉伸低碳钢过程,拉伸曲线的变化以及金属变形答案:1、B B 2、AB BCD 3、√4、屈服强度 抗拉强度 抗弯强度 抗剪强度5、在力到达Fe 之前处于弹性变形阶段△L 线性增加,超过Fe 以后不仅有弹性变形还有塑性变形,形成永久变形,到Fs 以后出现塑性变形,出现屈服现象,进入强化阶段。
1.2 金属和合金的晶体结构及结晶过程一、知识点整理1、内部原子在空间按一定次序有规律的排列的物质称为晶体,反之为则为非晶体晶体具有。
固定的熔点和各向异性等特征,非晶体则反之。
2、晶体中源于排列规律具有明显的周期性征的最小几何单元,称为晶胞。
机械制造工艺基础知识点总结

机械制造工艺基础知识点第一章金属切削加工基础知识一、切削加工基本概念1、成形运动(切削运动)是为了形成工件表面所必需的、刀具与工件之间的相对运动。
成形运动(切削运动)包括主运动和进给运动。
2、主运动是指直接切除工件上的切削层,形成已加工表面所需的最基本运动。
一般来讲,主运动是成形运动中速度最高、消耗功率最大的运动,机床的主运动只有一个。
3、进给运动是指不断地把切削层投入切削的运动,以加工出完整表面所需的运动。
进给运动可能有一个或几个,通常运动速度较低,消耗功率较小。
4、切削过程中,工件上形成三个表面1)待加工表面——将被切除的表面;2)过渡表面——正在切削的表面;3)已加工表面——切除多余金属后形成的表面。
5、切削用量三要素1)切削速度v c切削刃上选定点在主运动方向上相对于工件的瞬时速度。
2)进给量f在进给运动方向上,刀具相对于工件的位移量,称为进给量。
3)背吃刀量a p背吃刀量是在通过切削刃基点并垂直于工作平面方向上测量的切削深度。
6、成形运动简图7、切削层尺寸要素(1)切削层:刀具切过工件的一个单程,或只产生一圈过渡表面的过程中所切除的工件材料层。
(2)切削层尺寸平面:通过切削刃基点并垂直于该点主运动方向的平面,称为切削层尺寸平面。
(3)切削层尺寸要素①切削厚度:指在切削层尺寸平面内,沿垂直于切削刃方向度量的切削层尺寸。
②切削宽度:指在切削层尺寸平面内,沿切削刃方向度量的切削层尺寸。
③切削面积:是指在给定瞬间,切削层在切削层尺寸平面里的实际横截面面积。
二、刀具角度1、车刀的组成三个刀面:前面、主后面、副后面两个切削刃:主切削刃、副切削刃一个刀尖2、辅助平面1)基面:过切削刃选定点,垂直于主运动方向的平面。
2)主切削平面:过切削刃选定点,与切削刃相切,并垂直于基面的平面。
3)正交平面:通过主切削刃上的某一点,并同时垂直于基面和切削平面的平面。
3、车刀的标注角度γ(1)前角在正交平面中测量,是刀具前面与基面之间的夹角。
机械制造技术考点汇总
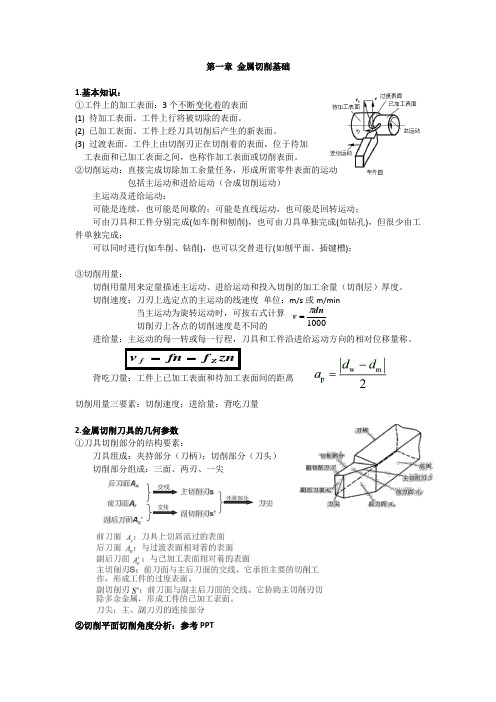
第一章 金属切削基础1.基本知识:①工件上的加工表面:3个不断变化着的表面 (1) 待加工表面。
工件上行将被切除的表面。
(2) 已加工表面。
工件上经刀具切削后产生的新表面。
(3) 过渡表面。
工件上由切削刃正在切削着的表面,位于待加 工表面和已加工表面之间,也称作加工表面或切削表面。
②切削运动:直接完成切除加工余量任务,形成所需零件表面的运动包括主运动和进给运动(合成切削运动)主运动及进给运动:可能是连续,也可能是间歇的;可能是直线运动,也可能是回转运动;可由刀具和工件分别完成(如车削和刨削),也可由刀具单独完成(如钻孔),但很少由工件单独完成;可以同时进行(如车削、钻削),也可以交替进行(如刨平面、插键槽);③切削用量:切削用量用来定量描述主运动、进给运动和投入切削的加工余量(切削层)厚度。
切削速度:刀刃上选定点的主运动的线速度 单位:m/s 或m/min当主运动为旋转运动时,可按右式计算 切削刃上各点的切削速度是不同的进给量:主运动的每一转或每一行程,刀具和工件沿进给运动方向的相对位移量称。
znf fn v Z f ==背吃刀量:工件上已加工表面和待加工表面间的距离切削用量三要素:切削速度;进给量;背吃刀量2.金属切削刀具的几何参数①刀具切削部分的结构要素:刀具组成:夹持部分(刀柄);切削部分(刀头) 切削部分组成:三面、两刃、一尖②切削平面切削角度分析:参考PPT1000dnv π=第二章金属切削的基本规律及其应用1.切屑的种类及其变化①分类:带状切屑;底面光滑,背面呈毛茸状挤裂切屑;底面光滑有裂纹,背面呈锯齿状节状切屑;底面已不光滑,呈粒状金属块的堆砌崩碎切屑:不规则块状颗粒②影响切屑形状的因素:工件材料、切削速度、进给量、刀具角度③切屑形状对加工过程的影响:切削过程平稳性、表面质量④切屑控制:卷曲和折断2.切削层金属的变形①三个变形区②变形程度的表示:变形系数;剪切角;剪应变变形系数PS:能表示变形程度的参数:切屑形态(方便、定性);剪切角(定量);变形系数(纯挤压,易测);剪应变(纯剪切,较合理,忽略挤压)③刀—屑接触区的变形与摩擦第二变形区特征:切屑底层晶粒纤维化,流速减慢,甚至滞留。
机械制造技术基础第二章课后答案

机械制造技术基础第二章课后答案#1.金属切削过程的实质是什么答:金属切削过程就是刀具从工件上切除多余的金属,使工件得到符合技术要求的几何精度和表面质量的过程。
2.切削运动可分哪两类,各有什么特点答:切削运动可分为主运动和进给运动。
主运动在切削过程中速度最高,消耗的功率最大,并且在切削过程中切削运动只有一个。
进给运动的速度较低、消耗的功率较小,进给运动可以有一个或多个。
3.切削用量的主要参数有哪些答.:切削用量的参数有切削速度、进给量和背吃刀量。
4.试述车刀前角、后角、主偏角、负偏角和刃倾角的作用,并指出如何使用答:前角对切削的难易程度有很大的影响,前角大小的选择与工件材料、刀具材料、加工要求有关。
后角的作用是为了减小后刀面与工件之间的摩擦和减少后刀面的磨损。
主偏角的大小影响切削条件、刀具寿命和切削分力的大小。
!5.车外圆时,车刀装得过高或过低、偏左或偏右,刀具角度会发生哪些变化什么情况下可以利用这些变化答:当刀尖高于工作中心时,刀具工作前角将增大,工作后角将减小。
如果刀尖低于工作中心,则刀具工作前角减小,后角增大。
若刀杆右偏,则车刀的工作主偏角将增大,负偏角将减小。
若刀杆左偏,则车刀的工作主偏角将减小,负偏角将增大。
6.试标出图刀具的五个基本角度及主切削刃和副切削刃。
7.列举外圆车刀在不同参考系中的主要标准角度及其定义。
答:1)前角:在正交平面内测量的前刀面与基面之间的夹角;后角:在正交平面内测量的主后刀面与切削平面之间的夹角;主偏角:在基面内测量的主切削刃在基面上的投影与进给方向的夹角;副偏角:在基面内测量的副切削刃在基面上的投影与进给运动反方向的夹角;刃倾角:在切削平面内测量的主切削刃与基面之间的夹角;副后角:在副切削刃上选定点的副正交平面内,副后刀面与副切削平面之间的夹角。
8.偏角的大小对刀具耐用度和三个切削分力有何影响当车削细长轴时,主偏角应选得较大还是较小为什么答:当切削面积不变时,主偏角增大,切削厚度也随之增大,切屑变厚,因而主切削力随着主偏角的增大而减小,但当主偏角增大到60~70之间时,主切削力又逐渐增大主偏角;背向力随着主偏角的增大而减小,进给力随着主偏角的增大而增大。
机械制造工艺学知识点总结(含名词解释)
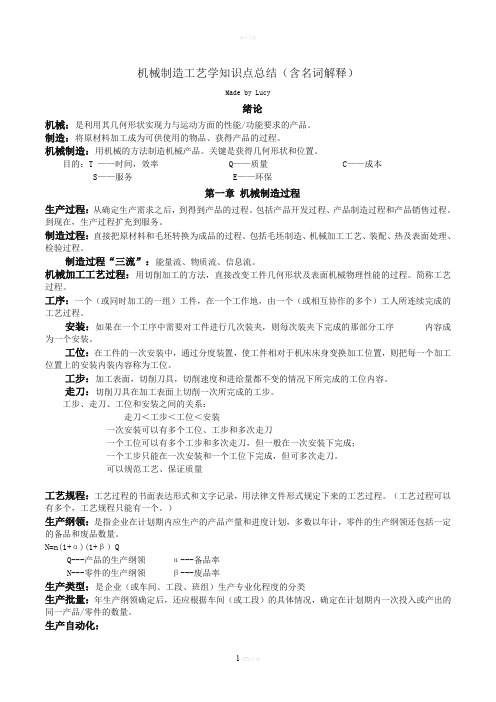
机械制造工艺学知识点总结(含名词解释)Made by Lucy绪论机械:是利用其几何形状实现力与运动方面的性能/功能要求的产品。
制造:将原材料加工成为可供使用的物品、获得产品的过程。
机械制造:用机械的方法制造机械产品。
关键是获得几何形状和位置。
目的:T ——时间,效率 Q——质量 C——成本S——服务 E——环保第一章机械制造过程生产过程:从确定生产需求之后,到得到产品的过程。
包括产品开发过程、产品制造过程和产品销售过程。
到现在,生产过程扩充到服务。
制造过程:直接把原材料和毛坯转换为成品的过程。
包括毛坯制造、机械加工工艺、装配、热及表面处理、检验过程。
制造过程“三流”:能量流、物质流、信息流。
机械加工工艺过程:用切削加工的方法,直接改变工件几何形状及表面机械物理性能的过程。
简称工艺过程。
工序:一个(或同时加工的一组)工件,在一个工作地,由一个(或相互协作的多个)工人所连续完成的工艺过程。
安装:如果在一个工序中需要对工件进行几次装夹,则每次装夹下完成的那部分工序内容成为一个安装。
工位:在工件的一次安装中,通过分度装置,使工件相对于机床床身变换加工位置,则把每一个加工位置上的安装内装内容称为工位。
工步:加工表面,切削刀具,切削速度和进给量都不变的情况下所完成的工位内容。
走刀:切削刀具在加工表面上切削一次所完成的工步。
工步、走刀、工位和安装之间的关系:走刀<工步<工位<安装一次安装可以有多个工位、工步和多次走刀一个工位可以有多个工步和多次走刀,但一般在一次安装下完成;一个工步只能在一次安装和一个工位下完成,但可多次走刀。
可以规范工艺、保证质量工艺规程:工艺过程的书面表达形式和文字记录,用法律文件形式规定下来的工艺过程。
(工艺过程可以有多个,工艺规程只能有一个。
)生产纲领:是指企业在计划期内应生产的产品产量和进度计划,多数以年计,零件的生产纲领还包括一定的备品和废品数量。
N=n(1+α)(1+β)QQ---产品的生产纲领α---备品率N---零件的生产纲领β---废品率生产类型:是企业(或车间、工段、班组)生产专业化程度的分类生产批量:年生产纲领确定后,还应根据车间(或工段)的具体情况,确定在计划期内一次投入或产出的同一产品/零件的数量。
机械设计期末知识点总结

第一章绪论1.通用零件、专用零件有哪些?P4通用零件:传动零件——带、链、齿轮、蜗轮蜗杆等;连接零件——平键、花键、销、螺母、螺栓、螺钉等;轴系零件——滚动轴承、联轴器、离合器等。
专用零件:汽轮机的叶片、内燃机的活塞、纺织机械中的纺锭、织梭等。
第二章机械设计总论1.机器的组成。
P5机器的组成:原动机部分、传动机部分、执行部分、测控系统、辅助系统。
2.机械零件的主要失效形式有哪些?P13①整体断裂;②过大的残余变形;③零件的表面破坏;④破坏正常工作条件引起的失效。
3.机械零件的设计准则有哪些?P16①强度准则;②刚度准则;③寿命准则;④振动稳定性准则;⑤可靠性准则。
第三章机械零件的强度1.交变应力参数有哪些?应力比r的定义是什么?r = -1、r =0、r=1分别叫什么?P27最大应力σmax、最小应力σmin、平均应力σm=σmax+σmin2、应力幅度σa=σmax−σmin2、应力比(循环特性系数)r=σminσmax。
最小应力与最大应力之比称为应力比(循环特性系数)。
r = -1:对称循环应力、r =0:脉动循环应力、r =1:静应力。
第五章螺纹连接和螺旋传动1.连接螺纹有哪些?各有哪些特点?P71①普通螺纹。
牙型为等边三角形,牙型角α=60°,内、外螺纹旋合后留有径向间隙。
同一公称直径螺纹按螺距大小可分为粗牙螺纹和细牙螺纹。
②55°非密封管螺纹。
牙型为等腰三角形,牙型角α=55°。
管螺纹为英制细牙螺纹。
可在密封面间添加密封物来保证密封性。
③55°密封管螺纹。
牙型为等腰三角形,牙型角α=55°。
螺纹旋合后,利用本身的变形就可以保证连接的紧密型。
④米制锥螺纹。
牙型角α=60°,螺纹牙顶为平顶。
2.传动螺纹有哪些?各有哪些特点?P72①矩形螺纹。
牙型为正方形,牙型角α=0°。
传动效率比其他螺纹高。
②梯形螺纹。
牙型为等腰梯形,牙型角α=30°。
机械制造技术基础-2基础知识

0.8
40 5 150 50 2×1 35
2×1 30
0 φ35 -0.017
φ32
φ40
flash
flash
图2-3 阶梯轴
11
2.2.1 机械加工工艺过程及其组成
工位——工件在机床上占据每一个位置所完成的那部分 工序称为工位。
24
2.3.4 切削用量与切削层截面参数
切削层截面参数
切削厚度
切削宽度
h D f sin r
(2-4) (2-5)
f bD sin
ap
Dm
f
a)
b) 图2-7 切削层截面
c)
25
bD = ap hD = f
dw
Κr
机械制造技术基础
第2章 机械制造过程基础知识 Fundamental of Mechanical Manufacturing Process
材料成形法 —— 进入工艺过程物料初始重量近似等于 加工后最终重量。如铸造、压力加工、粉末冶金、注塑成 形等,这些方法多用于毛坯制造,但也可直接成形零件。
材料去除法 —— 零件的最终几何形状局限在毛坯的初 始几何形状范围内,零件形状的改变是通过去除一部分材 料,减少一部分重量来实现的。如切削与磨削,电火花加 工、电解加工等特种加工等。
第2章 机械制造过程基础知识
本章要点
机械制造工艺 机械加工方法 定位原理与定位误差 机床与夹具 刀具材料与刀具几何角度 工件材料切削加工性
1
机械制造技术基础
第2章 机械制造过程基础知识 Fundamental of Mechanical Manufacturing Process 2.1 机械制造工艺总论
小说制造机械知识点总结
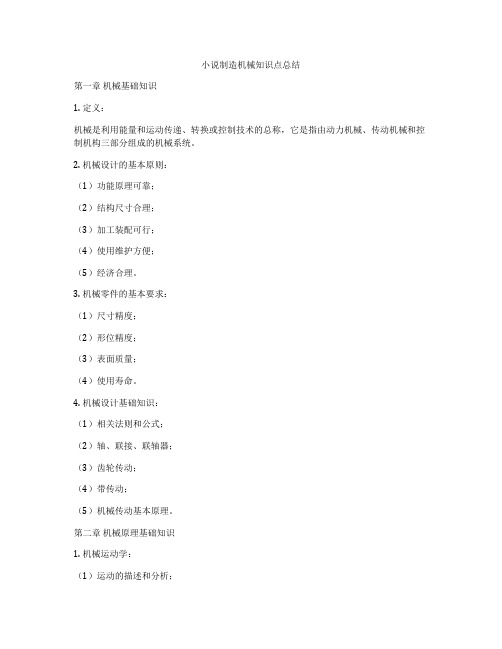
小说制造机械知识点总结第一章机械基础知识1. 定义:机械是利用能量和运动传递、转换或控制技术的总称,它是指由动力机械、传动机械和控制机构三部分组成的机械系统。
2. 机械设计的基本原则:(1)功能原理可靠;(2)结构尺寸合理;(3)加工装配可行;(4)使用维护方便;(5)经济合理。
3. 机械零件的基本要求:(1)尺寸精度;(2)形位精度;(3)表面质量;(4)使用寿命。
4. 机械设计基础知识:(1)相关法则和公式;(2)轴、联接、联轴器;(3)齿轮传动;(4)带传动;(5)机械传动基本原理。
第二章机械原理基础知识1. 机械运动学:(1)运动的描述和分析;(2)刚体平动和转动;(3)力对刚体的作用;(4)力矩和力矩平衡。
2. 静力学和动力学:(1)平衡条件;(2)动量和动量守恒;(3)力和加速度。
3. 力的分析和合成:(1)力的分解;(2)力的合成。
4. 转矩和机械力建设计:(1)转矩的概念;(2)机械力建设的原则。
第三章机械设计知识1. 机械设计基本步骤:(1)明确设计任务;(2)分析设计条件;(3)选择设计方案;(4)计算和校核;(5)绘图和制造。
2. 机械设计基本原则:(1)合理性、可靠性、安全性;(2)实用性、经济性;(3)可制造性、维修性、环保性。
3. 符号和规范:(1)机械设计图纸符号;(2)机械设计规范。
4. 机械传动设计:(1)连杆机构设计;(2)齿轮传动设计;(3)带传动设计;(4)液力传动设计。
第四章机械制造技术知识1. 机械加工基本工艺:(1)铣削、车削、钻削和研磨;(2)锻造、压铸、热处理和焊接。
2. 机械加工设备:(1)数控机床;(2)车床、铣床、钻床等;(3)磨床、磨料加工设备。
3. 机械加工工艺:(1)工艺分析;(2)切削原理;(3)刀具选择;(4)加工工艺流程。
4. 机械制造材料:(1)金属材料;(2)非金属材料;(3)特种材料。
第五章机械维修与保养知识1. 机械设备维修:(1)维修工具和设备;(2)设备故障诊断;(3)维修方法和技巧。
机械制造技术基础(第二章)

(第二章 机械制造中的加工方法)
主讲: 肖新华
天津工业大学机械电子学院
2.1 概述
机械零件的结构形状千变万化。零件结构形式的 不同,使之有很多的加工方法,根据加工过程中零 件质量的变化情况,零件的制造过程可分为Δm<0,
Δm=0和Δm>0三种形式,不同的类型有不同的工艺
方法。
一. Δm<0的制造过程
外圆表面的磨削
1.中心磨削
(1)纵磨
(2)横磨
(3)复合磨
2.无心磨削
纵磨特点:工件或砂轮需作轴向进给。磨削深度小、磨削接触面积 小,散热较好,容易得到较高的精度和表面质量,因而应用广泛。 但由于走刀次数多,生产效率低,适用于单件小批生产中磨削较长 的外圆表面。
横磨
横磨特点:砂轮宽度大于磨削宽度。工件不需作轴
弹性式 :由300~320HBS的弹簧丝制成,可研孔 径d为1~4mm的小孔 。用于研一般精度的小孔或母
线为曲线的小孔 。
研磨孔视频
2.4.6 珩磨孔
珩磨孔是利用安装于珩磨头圆周上的油石,采用特定结构 推动油石径向扩张,直至与工件接触,并保持一定的压力,以 较低的切削速度对孔进行精加工。加工过程中,油石不断作径 向进给运动,珩磨头作旋转和沿孔轴心方向的直线运动,从而 实现对孔的低速切削,显著提高孔的尺寸精度和形状精度,降 低表面粗糙度值。 采用珩磨加工孔时,加工精度可达IT7~IT6,孔的圆度和 圆柱度误差可控制在5~3m,表面粗糙度Ra为0.025~0.2m, 加工质量好,切削效率高。 珩磨视频
2.3外圆表面加工
1.车削
2.磨削
3.光整加工
2.3外圆表面加工
车削加工
钳工和机械加工
机械制造技术基础 第2章

积屑瘤对切削加工的影响:
(1)实际γo ↗ (2) ap ↗ (3)Ra ↗ (4)影响刀具耐用度
防止产生积屑瘤的措施:
(1)低速或高速切削 (2)加强润滑 (3) ↗γo以减小刀屑接触区压力 (4) ↗材料硬度(如热处理), ↘加工硬化倾向
2.1.2切屑的类型
⑴带状切屑经过塑性变形过程形成的切屑,外形呈带状.切削塑
方便又直观。 上述是根据纯剪切观点提出的,但切削过 程是复杂的,既有剪切、又有前刀面Aγ 对切屑 的挤压和摩擦作用,不能反映全部的变形实质。
(例如 Λh =1时,而实际情况是有变形的)
(3)剪切面与剪切角
合力最小原理
最小能量原理
图2.7 切屑上受力分析
2.1.1.4 前刀面上的挤压摩擦与积屑瘤
(1)刀-屑接触区的摩擦特性
①自然热电偶法 ②人工热电偶法 P43图2.30 P44图2.31
2.3.3影响切削温度的因素 ⑴切削用量的影响 *
• 切削用量ap、f和vc对切削温度的影响关系:
• 切削用量ap 、 f和vc对切削温度的影响规律: 切削用量ap 、 f和vc增大,切削温度增加。其中切削速度 vc对切削温度影响最大,进给量f次之,切削深度ap影响 最小,即对切削温度的影响: • 由此可见,在金属切除率相同的条件下,为了减少切削 温度影响,防止刀具迅速磨损,保持刀具耐用度,增大 切削深度ap或进给量f比增大切削速度vc更有利。
vc >f >ap ( 与Fr相反)。
⑵刀具几何参 数影响 ①前角γo γo ↗ ,切 削变形和摩 擦↘ ,因此 产生的热量 少,切削温 度↘ 。 但 γo ↗ 至 18o 左右,由 于楔角减少 使刀具散热 变差,切削 温度略有↗ 。
机械制造技术基础课件最新版第二章第2节
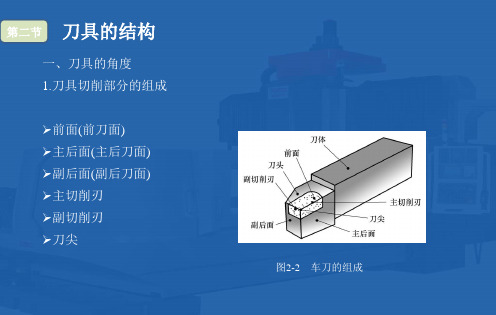
(5)螺纹刀具
螺纹可用切削法和滚压 法进行加工。螺纹加工可在车床 上车削完成(外螺纹),也可用手动 或在钻床上用丝锥进行加工(内 螺纹)。
图2-23 常用切削法加工螺纹的螺纹刀具 a)平体螺纹梳刀 b)棱体螺纹梳刀 c)圆体螺纹梳刀 d)板牙 e)丝锥
第二节 刀具的结构
(6)齿轮刀具 齿轮刀具是用于加工齿轮齿形的刀具,按刀具的工作原理,齿轮刀具分为 成形齿轮刀具和展成齿轮刀具。常用的成形齿轮刀具有盘形齿轮铣刀 和指形齿 轮铣刀等。常用的展成齿轮刀具有插齿刀、滚刀和剃齿刀等。
第二节 刀具的结构
5)铰刀 铰刀是精加工刀具,加工精度可达IT7~IT6,加工表面粗糙度Ra值可达 1.6~0.4μm。下图所示是几种常用铰刀,其中图a、b所示为手用铰刀,图c、d所示 为机用铰刀,图所示为两把一套的锥度铰刀。
图2-18 几种常用的铰刀
第二节 刀具的结大类。
第二节 刀具的结构
图2-13 麻花钻的结构
图2-14 中型标准群钻
第二节 刀具的结构
2)中心钻 中心钻 用于加工轴类工件的中心孔。钻孔时,先打中心孔,也有利于钻头 的导向,可防止钻偏。 3)深孔钻 深孔钻是专门用于钻削深孔(长径比≥5)的钻头。为解决深孔加工中的断 屑、排屑、冷却润滑和导向等问题,人们先后开发了外排屑深孔钻、内排屑深孔 钻、喷吸钻和套料钻等多种深孔钻。
机械制造技术基础(第二版)第二章-8-9

32
实践证明,机械磨损、热磨损以及综合磨损的磨 损速度随温度变化的特性如图所示:
33
不同刀具材料的磨损特性
34
不同刀具材料的磨损特性各不相同。 耐热性较低的高速钢刀具,其磨损的主要原
因是硬质点磨损和粘结磨损。 硬质合金刀具主要是伴有粘结磨损的扩散磨
损等。 加工钢铁件时,氧化铝陶瓷刀具主要是伴随
23
3)扩散磨损
由于切削时的高温,刀具表面又始终与被切出 的材料新鲜表面相接触,很大的化学活性会使 两摩擦面的化学元素互相扩散到对方,削弱刀 具材料性能,加速磨损过程。
扩散速度随切削温度升高而增加,它是按照指 数函数增加的。
不同元素的扩散速度是不同的,扩散磨损剧烈 程度与刀具材料的化学成分关系很大。例如,Ti 的扩散速度比C、Co、W等元素低很多,故YT 类硬质合金抗扩散能力比YG类高。
后刀面与工件实际上是小面积接触,磨损就发 生在这个接触面上。
切削铸铁和以较小的切削厚度切削塑性材料时 多产生。
12
后刀面磨损带往往不均匀。刀尖部分(C区)强 度较低,散热条件又差,磨损比较严重,其最大 值为VC。
主切削刃靠近工件外皮处的后刀面(N区)上,磨 成较严重的深沟,以VN表示。
在后刀面磨损带中间部位(B区)上,磨损比较 均匀,平均磨损带宽度以VB表示,而最大磨损 宽度以VBmax表示。
- 1、下载文档前请自行甄别文档内容的完整性,平台不提供额外的编辑、内容补充、找答案等附加服务。
- 2、"仅部分预览"的文档,不可在线预览部分如存在完整性等问题,可反馈申请退款(可完整预览的文档不适用该条件!)。
- 3、如文档侵犯您的权益,请联系客服反馈,我们会尽快为您处理(人工客服工作时间:9:00-18:30)。
第二章金属切削原理与刀具基本概念:1. 金属切削加工:利用刀具切去工件毛坯上多余的金属层,以获得具有一定的几何精度和表面质量的机械零件的加工方法。
2. 切削运动:刀具与工件间的相对运动称为切削运动。
包括主运动和进给运动两种。
主运动:切除多余金属层所必需的最基本的运动,速度最高、功率最大,只能有一个。
进给运动:是多余材料不断投入切削,从而加工出完整表面所需要的运动。
速度较低,功率较小,是形成已加工表面的辅助运动。
3.4. 切削速度:切削加工时,刀具切削刃上选定点相对工件的主运动的速度。
5. 进给量:在工件或刀具主运动每转一转或每一行程时,刀具和工件之间在进给运动方向上的相对位移量。
6. 背吃刀量:在垂直于主运动方向和进给运动方向确定的工作平面内测量的刀具切削刃与工件切削表面的接触长度。
7. 削切宽度:在主切削刃上选定点的基面内,沿过渡表面度量的切削层厚度。
8. 切削厚度:在主切削刃选定点的基面内,垂直于过渡表面度量的切削层厚度。
9. 切削层面积:在主切削刃选定点的基面内的切削层横截面积。
10. 自由切削:刀具在切削过程中,如果只有一条直线切削刃参加切削工作,称为自由切削。
11. 非自由切削:刀具在切削过程中,切削刃是曲线或者有几条切削刃都参加切削,并且同时完成整个切削过程,称为非自由切削。
切削要素切削用量切削速度进给量背吃刀量切削层几何参数切削宽度切削厚度切削面积12.直角切削(正交切削):刀具主切削刃的刃倾角等于零时的切削,此时,主切削刃与切削速度方向成直角。
13.斜角切削:刀具主切削刃的刃倾角不等于零时的切削,此时主切削刃与切削速度方向不成直角。
直角切削和非直角切削都属于自由切削。
14.切削平面:通过切削刃上选定点,切于工件过渡表面的平面。
包含有刀刃在该点的切线以及合成切削运动向量。
15.基面:通过切削刃上选定点,垂直于该点合成切削运动向量的平面。
16.刀具的工作角度:以切削过程中实际的切削平面、基面和正交平面为参考面所确定的刀具角度称为刀具的切削角度。
17.剪切角:剪切滑移面与切削速度之间的夹角,它剪切滑移面的位置。
18.切削力:金属切削时,刀具切入工件,使被加工材料发生变形并称为切屑所需的力。
19.切削时的三个发热区域:剪切面、切屑与前刀面接触区、后刀面与过渡表面接触区。
20.切削温度:前刀面与切屑接触区域的平均温度。
21.刀具寿命:一把新刀(或刚刃磨过的刀具)从开始使用直到达到磨钝标准所经历的实际切削时间。
对于可重磨刀具,刀具寿命是指刀具两次刃磨之间所经历的实际切削时间。
而对其从第一次投入使用直至完全报废时,所经历的实际切削时间。
22.工件材料切削加工性:在一定的切削条件下,对工件材料进行切削加工的难易程度。
23.良好的切削加工性:1)刀具寿命较长或者在一定寿命下的切削速度较高;2)相同的切削条件下切削力较小,切削温度低;3)容易获得较好的表面质量;4)切屑形状容易控制或者断屑。
重要原理1.车刀的切削部分:三面、两刃、一尖前刀面:切下的切屑沿其流出的表面;后刀面:与工件上过渡表面相对的表面;副后刀面:与工件上已加工表面相对的表面;主切削刃:前刀面和主后刀面相交而得到的边锋,完成主要的切除工作;副切削刃:前刀面与副后刀面相交而得到的边锋,配合主切削刃完成切削工作,并最终完成工件的已加工表面。
刀尖:主切削刃和副切削刃连接处的一段刀刃。
为增加刀尖强度,往往把它磨成圆弧形或者一段小直线。
2.刀具的标注角度:1)前角:在正交平面内测量的前刀面与基面之间的夹角。
2)后角:在正交平面内测量的主后角面与切削平面之间的夹角;作用是为了减小后刀面与工件之间的摩擦和减小后刀面的磨损。
3)主偏角:在基面内测量的主切削刃在基面上的投影与进给运动方向的夹角。
4)副切削刃:在基面内测量的福切削刃在基面上的投影与进给运动反方向的夹角。
5)刃倾角:在切削平面内测量的主切削刃与基面之间的夹角。
6)副后角:在副切削刃上选定点的副正交平面内,副后刀面与副切削刃之间的夹角。
3.刀具材料应具备的性能:1)高的硬度和耐磨性,即比工件硬和抗磨损的能力;2)足够的强度和韧性,以承受切削中的冲击和振动,避免崩刃和折断;3)高的耐热性,即高温下保持硬度、耐磨性、强度和韧性;4)良好的物理性能和耐冲击性能;5)良好的工艺性,如锻造性、热处理性等;6)良好的经济性。
4.金属切削时的变形区及其基本特征:1)第变形区:切削层的塑性变形区。
特征:沿滑移线的塑性变形以及随之产生的加工硬化;2)第变形区:切屑与前刀面相互摩擦的区域。
特征:是切屑底层靠近前刀面处纤维化,流动速度减慢,甚至滞留在前刀面上;切屑弯曲;由摩擦产生的热量是切屑与刀具接触面温度升高。
3)第变形区:以加工表面与后刀面相互接触的区域。
特征:已加工表面受到切削刃钝圆部分与后刀面的挤压与摩擦,产生变形和回弹,造成纤维化和加工硬化。
5.切屑的类型及其控制:1)带状切屑:产生条件:切削塑性材料,切削速度较高,切削厚度较小,刀具前角较大时产生带状切屑。
特征:切削过程平稳,切削力波动较小,已加工表面粗糙度小。
2)挤裂切屑:产生条件:切削塑性材料时,切削速度较低,切削厚度较大,刀具前角较小时产生挤裂切屑。
3)单元切屑:产生条件:切削塑性材料时,切削速度进一步减小,切削厚度继续加大,刀具前角进一步减小时产生的单元切屑。
4)崩碎切屑:产生条件:切削脆性材料时,特别是切削厚度较大时容易产生崩碎切屑。
是由于材料所受应力超过了它的抗拉极限。
特征:切削过程很不平稳,切削力波动很大,已加工表面粗糙度值大。
避免措施:减小切削厚度,使切削成针状或片状;提高切削速度,以增加工件的塑性。
切屑控制(断屑):在切削加工中采取适当的措施来控制切屑的卷曲、流出与折断,使之形成可接受的良好屑形。
常用的方法是:在前刀面磨出断屑槽或使用压块式断屑器。
6.积屑瘤:1)定义:在切削速度不高而又能形成连续切屑的情况下,加工一般钢料或者其他塑性材料时,常常在前刀面处黏着一块剖面有时呈三角形状的硬块,其硬度很高,当处于比较稳定的状态下时能代替切削刃进行切削,这块金属叫做积屑瘤或者刀瘤。
2) 对切削过程的影响:a)实际前角增大; b)实际切削厚度增大; c)使表面粗糙度增大;积屑瘤的突出部分不光滑使加工表面变得粗糙; d) 影响刀具寿命。
3) 积屑瘤产生原因:切屑与前刀面在一定温度和压力下产生黏结(冷焊),切屑从黏在刀面的底层上流过,形成内摩擦;如果温度和压力适当,底层上面的金属因内摩擦而变形,也会发生加工硬化,从而被阻滞在底层,黏成一体;黏结层逐渐长大,直到该处的温度和压力不至于继续黏结,积屑瘤就产生了。
影响因素:金属材料的硬化程度、刃前区的温度与压力。
4) 防止积屑瘤产生的主要方法:a) 降低切削速度,使切削温度降低,黏结现象不易产生;b) 提高切削速度,是切削温度升高,黏结现象不易产生;c) 采用润滑性能好的润滑液,减小摩擦;d) 增加刀具前角,以减小切屑与前刀面接触区的压力;e) 适当改变工件材料的加工特性,减小加工硬化倾向。
7.正常磨损:在切削过程中刀具前刀面和后刀面在高温高压作用下产生的正常磨钝的现象。
塑性破损:由于高温高压室前后刀面发生塑性流动而丧失切削能力。
脆性破损:刀具在机械及热冲击作用下产生崩刃、碎断、裂纹等现象。
8. 刀具磨损的原因:1) 硬质点磨损;低速刀具磨损的主要原因2) 黏结磨损;刀具与工件材料接触到原子距离时所产生的结合现象,黏结点由于相对运动,刀具中晶粒或晶粒群受拉或受剪而被带走,造成黏结磨损。
切削温度是主要影响因素,温度越高,黏结磨损越严重。
刀具磨损正常刀具磨损前刀面磨损后刀面磨损边界磨损非正常刀具磨损塑性破损脆性破损3)扩散磨损;两摩擦表面的化学元素扩散到对方去,使刀具表层的化学成分发生变化,削弱刀具材料的性能,使刀具磨损加快。
主要与切削温度和刀具材料的化学成分等有关。
4)化学磨损(氧化磨损):在一定条件下,刀具材料与周围介质发生化学作用,在刀具表面形成一层硬度较低的化合物而被切屑带走,加剧刀具腐蚀或者磨损。
5)热电磨损。
在切削区高温作用下,刀具与工件之间形成热电偶,产生热电势,使刀具与切屑及刀具与工件之间有电流通过,加快扩散磨损。
总结:对于一定工具材料和工件材料,其主导作用的是切削温度,在低温区以硬质点磨损为主;在高温区,以热化学磨损,即黏结磨损、扩散磨损、化学磨损和热点磨损为主。
9.刀具磨损过程:1)初期磨损阶段:磨损较快。
原因:刃磨后的新刀具,后刀面与加工表面的接触面积较小,压应力较大;新刃磨刀面上的微观粗糙度也加速了磨损。
2)正常磨损阶段:磨损缓慢均匀,后刀面磨损量随切削时间的增长而近似成比例增加。
原因:经初期磨损之后,后刀面上被磨出一条狭窄的棱面,压强减小,磨损速度缓慢,并且比较稳定。
3)急剧磨损阶段:在这个阶段之前要更换刀具。
原因:经过正常磨损阶段之后,切削刃显著变钝,切削力增大;磨削带宽度达到一定限度之后,切削力与切削温度均急剧升高,磨削速度增加很快,使刀具损坏而丧失切削能力。
10.切削用量的选择:1)切削速度是影响刀具寿命最主要的因素,其次是进给量、背吃刀量;2)选择切削用量的顺序为:首先选择尽可能大的背吃刀量,其次选尽可能大的进给量,最后选尽可能大的切削速度。
3)粗加工时,应以提高生产率为主,同时保证规定的刀具寿命。
一般选取较大的背吃刀量和进给量,切削速度不能太大;4)精加工时,应以保证零件的加工精度和表面质量为主,同时考虑刀具寿命和较高的生产率。
用逐渐减小背吃刀量的方法逐步提高加工精度;进给量大小依据表面粗糙度要求选取;切削速度要避开积屑瘤产生的速度范围。
一般选较小的背吃刀量和进给速度,较高的切削速度。
11.改善材料切削性能要求的措施:1)调整材料的化学成分;2)热处理。
另:12.影响切削力的因素13.影响切削温度的主要因素。