塑料挤出机开题报告
塑料挤出机械项目可行性研究报告申请报告

塑料挤出机械项目可行性研究报告申请报告并用行文流畅、逻辑清晰的叙述方式表达出报告的内容。
报告摘要
本研究是给科技公司的塑料挤出机械项目的可行性研究报告,目的在
于提供一份详细的报告,以帮助公司决定是否参与这个项目。
本报告从投
资成本分析、市场调研、技术分析、竞争环境分析、营销分析等几个方面
进行分析,充分考虑了这个项目的可行性。
该报告得出的结论是,在正确
定位项目的情况下,这项塑料挤出机械项目具有较高的可行性。
1绪论
科技公司正在考虑开发新的塑料挤出机械项目。
为此,本报告通过投
资成本分析、市场调研、技术分析、竞争环境分析、营销分析等几个方面,以审核该项目的可行性并提出相应的建议。
2投资成本分析
科技公司的塑料挤出机械项目总投资估计为760万美元,其中包括公
司财务投入585万美元、中外投资共计175万美元。
由于公司已经详细考
虑了该项目的全部投资成本,因此投资成本估计准确可靠。
3市场调研。
挤出模具设计开题报告
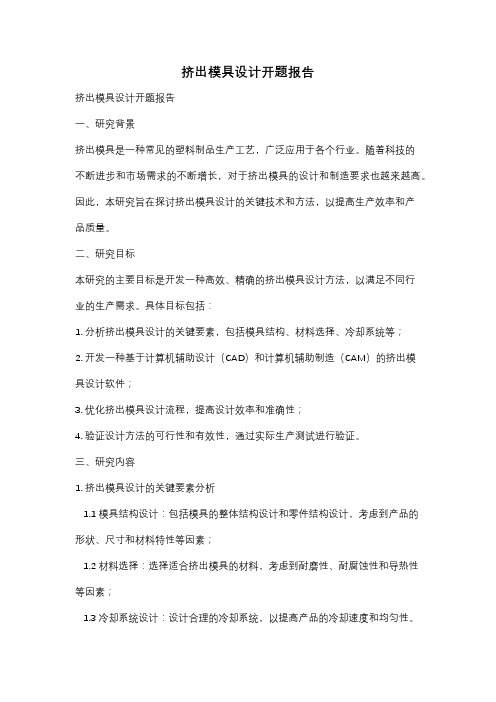
挤出模具设计开题报告挤出模具设计开题报告一、研究背景挤出模具是一种常见的塑料制品生产工艺,广泛应用于各个行业。
随着科技的不断进步和市场需求的不断增长,对于挤出模具的设计和制造要求也越来越高。
因此,本研究旨在探讨挤出模具设计的关键技术和方法,以提高生产效率和产品质量。
二、研究目标本研究的主要目标是开发一种高效、精确的挤出模具设计方法,以满足不同行业的生产需求。
具体目标包括:1. 分析挤出模具设计的关键要素,包括模具结构、材料选择、冷却系统等;2. 开发一种基于计算机辅助设计(CAD)和计算机辅助制造(CAM)的挤出模具设计软件;3. 优化挤出模具设计流程,提高设计效率和准确性;4. 验证设计方法的可行性和有效性,通过实际生产测试进行验证。
三、研究内容1. 挤出模具设计的关键要素分析1.1 模具结构设计:包括模具的整体结构设计和零件结构设计,考虑到产品的形状、尺寸和材料特性等因素;1.2 材料选择:选择适合挤出模具的材料,考虑到耐磨性、耐腐蚀性和导热性等因素;1.3 冷却系统设计:设计合理的冷却系统,以提高产品的冷却速度和均匀性。
2. 挤出模具设计软件的开发基于CAD和CAM技术,开发一种用户友好的挤出模具设计软件。
该软件应具备以下功能:2.1 模具结构设计:提供多种模具结构设计方案,根据用户需求进行自定义设计;2.2 材料选择:提供常用挤出模具材料的数据库,根据产品要求进行材料选择;2.3 冷却系统设计:自动计算最佳冷却系统布局和参数,以提高产品质量。
3. 挤出模具设计流程的优化3.1 流程分析:对传统的挤出模具设计流程进行分析,找出存在的问题和瓶颈;3.2 流程改进:通过引入新的设计方法和工具,优化设计流程,提高设计效率和准确性;3.3 流程管理:建立完善的设计流程管理体系,确保设计过程的顺利进行。
四、研究方法本研究将采用以下方法进行:1. 文献综述:对挤出模具设计的相关文献进行综述,了解当前研究状况和存在的问题;2. 实验研究:通过实际生产测试,验证设计方法的可行性和有效性;3. 数值模拟:利用计算机仿真软件对挤出模具设计进行数值模拟,分析设计方案的优劣。
双螺杆挤出机传动系统的方案比较和强度分析的开题报告

双螺杆挤出机传动系统的方案比较和强度分析的开题报告
一、研究背景和意义
随着塑料行业的不断发展,双螺杆挤出机已成为制造塑料制品的重要工业设备。
传统的双螺杆挤出机采用传统的侧向齿轮传动系统,齿轮系统的传动效率低、噪声大、过载能力弱等问题已经越来越受到关注。
因此,本文旨在设计一种新型的传动系统并进行比较和强度分析,以提高双螺杆挤出机的性能和使用寿命。
二、研究内容
1. 传统侧向齿轮传动系统的缺陷及双螺杆挤出机传动系统代替方案的研究和设计。
2. 选择传动系统的材料,并分析该材料的机械性能和耐久性。
3. 建立传动系统模型,并进行有限元分析。
4. 对传统侧向齿轮传动系统和新型传动系统进行比较和强度分析,并分析两种系统的优缺点。
三、研究方法
1. 通过实验和文献资料查阅,了解双螺杆挤出机的相关知识。
2. 设计新型传动系统方案,并选择合适的材料。
3. 建立传动系统模型,并通过有限元分析软件模拟传动系统应力状态和变形情况。
4. 对传统侧向齿轮传动系统和新型传动系统进行比较和强度分析。
四、预期结果
在完成研究后,预计可以得出以下结论:
1. 新型传动系统相比传统侧向齿轮传动系统在传动效率、噪声和过载能力方面具有明显优势。
2. 新型传动系统的设计可以提高双螺杆挤出机的性能和使用寿命。
五、结论
本研究将为双螺杆挤出机传动系统的改进提供新思路和参考,为塑料制品制造企业提高生产效率和降低生产成本做出贡献。
毕业设计双螺杆挤出机开题报告含全套CAD图纸
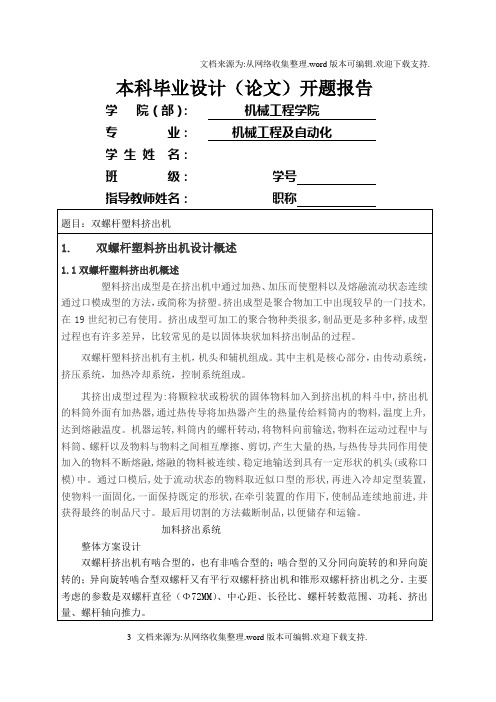
双螺杆的结构设计包括芯轴、螺杆轴、螺杆元件的设计以及各种螺杆元件的类型、数量及如何装配在一起等总体规划设计。
(4)螺杆的材质及热处理
螺杆材质的选自要考虑强度、耐磨度、耐腐蚀等问题,国内双螺杆挤出机厂家一般用合金结构钢,制成螺杆后氮化处理,氮化层厚度一般0.3-0.5mm。
1.2.2机筒设计
挤出成型有如此发展趋势主要原因为:螺杆挤出机能将一系列化工基本单元过程,如固体输送、增压、熔融、排气、脱湿、熔体输送和泵出等物理过程集中在挤出机内的螺杆上来进行。近年来,挤出工程的创新表现,更多的过程,如发泡、胶联、接枝、嵌段、调节相对分子质量甚至聚合反应等化学加工过程都愈来愈多地在螺杆挤出机上进行。螺杆挤出工艺装备逐步取代了一些由多台经典化工装备组成的生产线。连续生产代替间歇生产,必然有较高的生产率和较低的能耗,减少生产面积和操作人员数量,降低生产成本,也易于实现生产自动化,创造好的劳动条件和减少少的环境污染。与此同时,螺杆的搅拌作用也提高了混合质量。正因如此,螺杆挤出这种工艺不仅广泛地用于聚合物加工,而且在建材、食品、纺织、军工、和造纸等工业部门中都得到了愈来愈多的应用。
本科毕业设计(论文)开题报告
学院(部):
机械工程学院
专业:
机械工程及自动化
学生姓名:
班级:
学号
指导教师姓名:
职称
题目:双螺杆塑料挤出机
1.双螺杆塑料挤出机设计概述
1.1双螺杆塑料挤出机概述
塑料挤出成型是在挤出机中通过加热、加压而使塑料以及熔融流动状态连续通过口模成型的方法,或简称为挤塑。挤出成型是聚合物加工中出现较早的一门技术,在19世纪初已有使用。挤出成型可加工的聚合物种类很多,制品更是多种多样,成型过程也有许多差异,比较常见的是以固体块状加料挤出制品的过程。
矿泉水瓶挤出吹塑成型工艺开题报告

华侨大学厦门工学院毕业设计(论文)开题报告系(部):机械工程及自动化专业班级:******姓名*** 学号******* 指导教师****职称学历副教授课题名称矿泉水瓶挤出吹塑成型工艺及模具设计毕业设计(论文)类型(划√)工程设计应用研究开发研究基础研究其他√一、本课题的研究目的和意义:本课题来源于工程实践,是结合学生的专业特点和就业方向而设计的一个课题。
通过本次设计,掌握塑料件挤出吹塑成型模具设计的过程和基本技能;利用计算机辅助模具设计;掌握模具制造、装配的工艺要求。
模具设计全程应用CAD/CAM/CAE技术以及UG三维制图软件,从设计到最后出现成品都用现代先进的模具设计软件完成,已达到提高生产效率和成品精度的要求,减少重复设计的繁琐操作。
并且在设计过程中尽量采用标准件来完成整个模具的设计,以便于以后的维修及零部件的更换。
通过对矿泉水的性质和流通环境的分析,设计能在流通过程中起保护作用的包装,设计合理的包装不仅仅能保护产品、方便储运,而且还能在很大程度上起到介绍产品和促进销售的作用。
本设在矿泉水在流通过程得到保护,同时激起人们的购买欲望,从而促进其销售。
为了设计一款兼有良好的容装性,保护性,方便性,有美观经济的优点,满足消费者购买和使用习惯的矿泉水水瓶包装也是很有经济价值和市场前景的。
二、文献综述(国内外研究情况及其发展):模具生产技术水平的高低,已成为衡量一个国家产品制造水平高低的重要标志,因为模具在很大程度上决定着产品的质量、效益和新产品的开发能力。
经国务院批准,从1997 年到2000 年,对80 多家国有专业模具厂实行增值税返还70%的优惠政策,以扶植模具工业的发展。
所有这些,都充分体现了国务院和国家有关部门对发展模具工业的重视和支持。
年来我国的模具工业也有了很大的提高,有的模具已达到国际水平,年出口额达7.38亿美元。
由于近年来市场需求的强劲拉动,中国模具工业高速发展,市场广阔,以2003年为例,年增长就达25%之多,广东、江苏、浙江、山东等地的增长甚至在25%以上,其中广东模具生产企业近7000余家,年产值早巳超过200亿元,占全国模具年产值的40%多,几成就了我国模具工业的半壁江山。
聚乙烯挤出成型开题报告
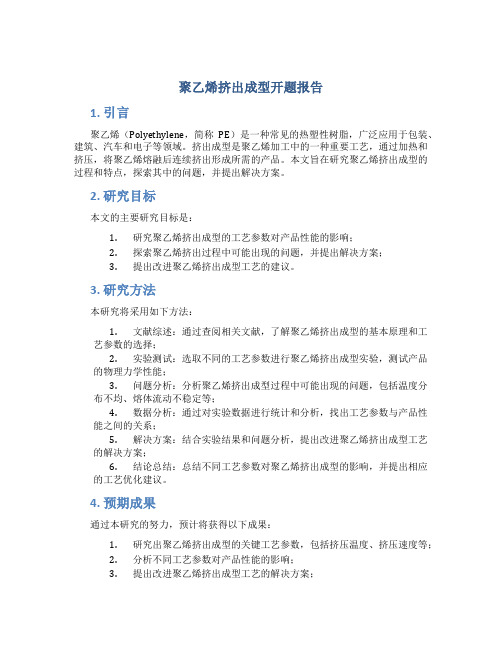
聚乙烯挤出成型开题报告1. 引言聚乙烯(Polyethylene,简称PE)是一种常见的热塑性树脂,广泛应用于包装、建筑、汽车和电子等领域。
挤出成型是聚乙烯加工中的一种重要工艺,通过加热和挤压,将聚乙烯熔融后连续挤出形成所需的产品。
本文旨在研究聚乙烯挤出成型的过程和特点,探索其中的问题,并提出解决方案。
2. 研究目标本文的主要研究目标是:1.研究聚乙烯挤出成型的工艺参数对产品性能的影响;2.探索聚乙烯挤出过程中可能出现的问题,并提出解决方案;3.提出改进聚乙烯挤出成型工艺的建议。
3. 研究方法本研究将采用如下方法:1.文献综述:通过查阅相关文献,了解聚乙烯挤出成型的基本原理和工艺参数的选择;2.实验测试:选取不同的工艺参数进行聚乙烯挤出成型实验,测试产品的物理力学性能;3.问题分析:分析聚乙烯挤出成型过程中可能出现的问题,包括温度分布不均、熔体流动不稳定等;4.数据分析:通过对实验数据进行统计和分析,找出工艺参数与产品性能之间的关系;5.解决方案:结合实验结果和问题分析,提出改进聚乙烯挤出成型工艺的解决方案;6.结论总结:总结不同工艺参数对聚乙烯挤出成型的影响,并提出相应的工艺优化建议。
4. 预期成果通过本研究的努力,预计将获得以下成果:1.研究出聚乙烯挤出成型的关键工艺参数,包括挤压温度、挤压速度等;2.分析不同工艺参数对产品性能的影响;3.提出改进聚乙烯挤出成型工艺的解决方案;4.提供聚乙烯挤出成型工艺优化的参考建议。
5. 研究计划本研究将按照如下计划进行:任务时间安排文献综述第1周实验测试第2-4周问题分析第5周数据分析第6周解决方案第7周结论总结第8周论文撰写第9-10周论文修改第11-12周论文最终定稿第13周答辩准备第14周6. 论文结构本论文将包括以下几个部分:1.引言:介绍聚乙烯挤出成型的背景和研究目标;2.相关理论:对聚乙烯挤出成型的基本原理和工艺参数进行介绍;3.实验设计:详细介绍实验的组织和方法,包括材料准备、设备选择和实验步骤;4.实验结果与分析:对实验数据进行统计和分析,总结工艺参数对产品性能的影响;5.问题分析与解决方案:分析聚乙烯挤出成型过程中可能出现的问题,并提出解决方案;6.结论与展望:总结本研究的主要成果和不足之处,并展望未来的研究方向;7.参考文献:列出本文所引用的相关文献。
双螺杆挤出机的传动系统研究的开题报告
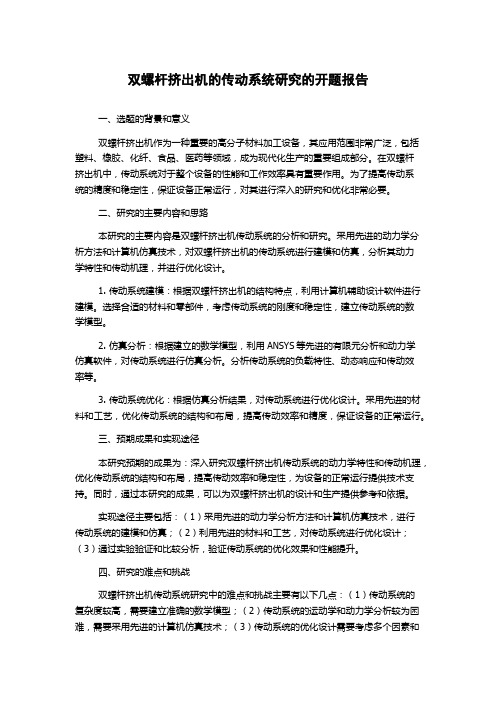
双螺杆挤出机的传动系统研究的开题报告一、选题的背景和意义双螺杆挤出机作为一种重要的高分子材料加工设备,其应用范围非常广泛,包括塑料、橡胶、化纤、食品、医药等领域,成为现代化生产的重要组成部分。
在双螺杆挤出机中,传动系统对于整个设备的性能和工作效率具有重要作用。
为了提高传动系统的精度和稳定性,保证设备正常运行,对其进行深入的研究和优化非常必要。
二、研究的主要内容和思路本研究的主要内容是双螺杆挤出机传动系统的分析和研究。
采用先进的动力学分析方法和计算机仿真技术,对双螺杆挤出机的传动系统进行建模和仿真,分析其动力学特性和传动机理,并进行优化设计。
1. 传动系统建模:根据双螺杆挤出机的结构特点,利用计算机辅助设计软件进行建模。
选择合适的材料和零部件,考虑传动系统的刚度和稳定性,建立传动系统的数学模型。
2. 仿真分析:根据建立的数学模型,利用ANSYS等先进的有限元分析和动力学仿真软件,对传动系统进行仿真分析。
分析传动系统的负载特性、动态响应和传动效率等。
3. 传动系统优化:根据仿真分析结果,对传动系统进行优化设计。
采用先进的材料和工艺,优化传动系统的结构和布局,提高传动效率和精度,保证设备的正常运行。
三、预期成果和实现途径本研究预期的成果为:深入研究双螺杆挤出机传动系统的动力学特性和传动机理,优化传动系统的结构和布局,提高传动效率和稳定性,为设备的正常运行提供技术支持。
同时,通过本研究的成果,可以为双螺杆挤出机的设计和生产提供参考和依据。
实现途径主要包括:(1)采用先进的动力学分析方法和计算机仿真技术,进行传动系统的建模和仿真;(2)利用先进的材料和工艺,对传动系统进行优化设计;(3)通过实验验证和比较分析,验证传动系统的优化效果和性能提升。
四、研究的难点和挑战双螺杆挤出机传动系统研究中的难点和挑战主要有以下几点:(1)传动系统的复杂度较高,需要建立准确的数学模型;(2)传动系统的运动学和动力学分析较为困难,需要采用先进的计算机仿真技术;(3)传动系统的优化设计需要考虑多个因素和约束,需要综合考虑各种因素和进行平衡;(4)传动系统的实验验证和效果分析需要具备较强的实验技能和数据分析能力。
毕业设计-双螺杆挤出机开题报告(含全套CAD图纸)

毕业设计-双螺杆挤出机开题报告(含全套CAD图纸)本科毕业设计(论文)开题报告学院,部,: 机械工程学院专业: 机械工程及自动化学生姓名: 班级: 学号指导教师姓名: 职称- 3 -题目:双螺杆塑料挤出机1. 双螺杆塑料挤出机设计概述1.1双螺杆塑料挤出机概述塑料挤出成型是在挤出机中通过加热、加压而使塑料以及熔融流动状态连续通过口模成型的方法,或简称为挤塑。
挤出成型是聚合物加工中出现较早的一门技术,在19世纪初已有使用。
挤出成型可加工的聚合物种类很多,制品更是多种多样,成型过程也有许多差异,比较常见的是以固体块状加料挤出制品的过程。
双螺杆塑料挤出机有主机,机头和辅机组成。
其中主机是核心部分,由传动系统,挤压系统,加热冷却系统,控制系统组成。
其挤出成型过程为:将颗粒状或粉状的固体物料加入到挤出机的料斗中,挤出机的料筒外面有加热器,通过热传导将加热器产生的热量传给料筒内的物料,温度上升,达到熔融温度。
机器运转,料筒内的螺杆转动,将物料向前输送,物料在运动过程中与料筒、螺杆以及物料与物料之间相互摩擦、剪切,产生大量的热,与热传导共同作用使加入的物料不断熔融,熔融的物料被连续、稳定地输送到具有一定形状的机头(或称口模)中。
通过口模后,处于流动状态的物料取近似口型的形状,再进入冷却定型装置,使物料一面固化,一面保持既定的形状,在牵引装置的作用下,使制品连续地前进,并获得最终的制品尺寸。
最后用切割的方法截断制品,以便储存和运输。
加料挤出系统整体方案设计- 4 -双螺杆挤出机有啮合型的,也有非啮合型的;啮合型的又分同向旋转的和异向旋转的;异向旋转啮合型双螺杆又有平行双螺杆挤出机和锥形双螺杆挤出机之分。
主要考虑的参数是双螺杆直径(Φ72MM)、中心距、长径比、螺杆转数范围、功耗、挤出量、螺杆轴向推力。
1.2 挤出系统设计1.2.1 螺杆设计(1)螺杆元件的设计根据实现功能的不同,可将螺杆元件分为输送元件(它由螺纹元件组成,可有不同的螺纹头数和导程),剪切元件(主要是捏合盘及其组成),混合元件(主要是齿形元件等)。
塑料管挤压机开题报告

湖南工业大学本科毕业设计(论文)开题报告(2012届)学院(部):机械工程学院专业:机械设计制造及其自动化学生姓名:林木学号 08406 班级:机设085指导教师姓名:刘华职称教授2011年12 月29 日题目:塑料管挤压机机头及加料装置的设计1.文献综述(1)塑料挤出机现状和发展趋势塑料挤出机高速、高产,可使投资者以较低的投入获得较大的产出和高额的回报。
但是,挤出机螺杆转速高速化也带来了一系列需要克服的难点:如物料在螺杆内停留时间减少会导致物料混炼塑化不均,物料经受过度剪切可能造成物料急骤升温和热分解,挤出稳定性控制困难会造成挤出物几何尺寸波动,相关的辅助装置和控制系统的精度必须提高,螺杆与机筒的磨损加剧需要采用高耐磨及超高耐磨材质,减速器与轴承在高速运转的情况下如何提高其寿命等问题都需要解决。
塑料挤出机的高效主要体现在高产出、低能耗、低制造成本方面。
在功能方面,螺杆挤出机已不仅仅用于高分子材料的挤出成型和混炼加工,它的用途已拓宽到食品、饲料、电极、炸药、建材、包装、纸浆、陶瓷等领域。
此外,将混炼造粒与挤出成型工序合二为一的“一步法挤出工艺”也值得重视。
实现挤出成型设备的大型化可以降低生产成本,这在大型双螺杆造粒机组、吹膜机组、管材挤出机组等方面优势更为明显。
国家重点建设服务所需的重大技术装备,大型乙烯工程配套的三大关键设备之一的大型挤压造粒机组长期依靠进口,因此必须加快国产化进程,满足石化工业发展需要。
而精密化可以提高产品的含金量,如多层共挤复合薄膜等均需要精密挤出,而作为实现精密挤出的重要手段——熔体齿轮泵必须加大力度进行开发研究。
模块化生产可以适应不同用户的特殊要求,缩短新产品的研发周期,争取更大的市场份额;而专业化生产可以将挤出成型装备的各个系统模块部件安排定点生产甚至进行全球采购,这对保证整期质量、降低成本、加速资金周转都非常有利。
发达国家的挤出机已普遍采用现代电子和计算机控制技术,对整个挤出过程的工艺参数如熔体压力及温度、各段机身温度、主螺杆和喂料螺杆转速、喂料量,各种原料的配比、电机的电流电压等参数进行在线检测,并采用微机闭环控制。
塑料挤出成型实验报告(3篇)
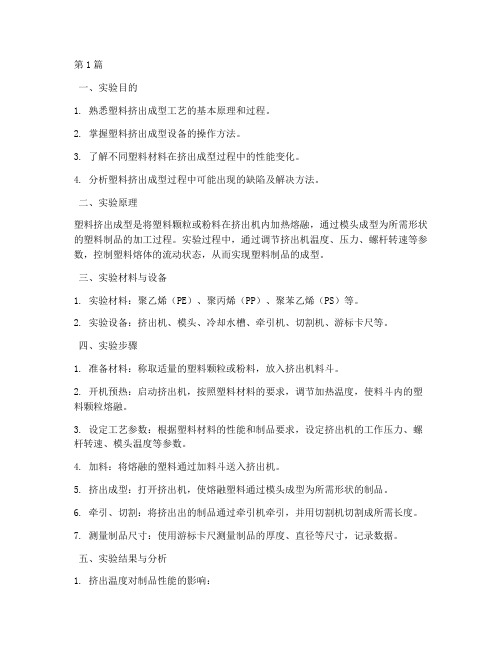
第1篇一、实验目的1. 熟悉塑料挤出成型工艺的基本原理和过程。
2. 掌握塑料挤出成型设备的操作方法。
3. 了解不同塑料材料在挤出成型过程中的性能变化。
4. 分析塑料挤出成型过程中可能出现的缺陷及解决方法。
二、实验原理塑料挤出成型是将塑料颗粒或粉料在挤出机内加热熔融,通过模头成型为所需形状的塑料制品的加工过程。
实验过程中,通过调节挤出机温度、压力、螺杆转速等参数,控制塑料熔体的流动状态,从而实现塑料制品的成型。
三、实验材料与设备1. 实验材料:聚乙烯(PE)、聚丙烯(PP)、聚苯乙烯(PS)等。
2. 实验设备:挤出机、模头、冷却水槽、牵引机、切割机、游标卡尺等。
四、实验步骤1. 准备材料:称取适量的塑料颗粒或粉料,放入挤出机料斗。
2. 开机预热:启动挤出机,按照塑料材料的要求,调节加热温度,使料斗内的塑料颗粒熔融。
3. 设定工艺参数:根据塑料材料的性能和制品要求,设定挤出机的工作压力、螺杆转速、模头温度等参数。
4. 加料:将熔融的塑料通过加料斗送入挤出机。
5. 挤出成型:打开挤出机,使熔融塑料通过模头成型为所需形状的制品。
6. 牵引、切割:将挤出出的制品通过牵引机牵引,并用切割机切割成所需长度。
7. 测量制品尺寸:使用游标卡尺测量制品的厚度、直径等尺寸,记录数据。
五、实验结果与分析1. 挤出温度对制品性能的影响:- 当挤出温度过低时,塑料熔体流动性差,制品表面易出现气泡、裂纹等缺陷。
- 当挤出温度过高时,塑料熔体流动性好,但易出现制品收缩、翘曲等缺陷。
2. 挤出压力对制品性能的影响:- 当挤出压力过低时,制品易出现熔体破裂、厚薄不均等缺陷。
- 当挤出压力过高时,制品易出现内应力、变形等缺陷。
3. 螺杆转速对制品性能的影响:- 当螺杆转速过低时,塑料熔体在挤出机内的停留时间过长,易出现制品色泽不均、表面粗糙等缺陷。
- 当螺杆转速过高时,制品易出现熔体破裂、厚薄不均等缺陷。
4. 制品尺寸测量:根据实验要求,测量制品的厚度、直径等尺寸,并与理论计算值进行比较,分析实验误差。
塑料挤出机开题报告

图5流线式挤管机头
1、螺杆2、机筒3、流线型过度套4、法兰
5、机头体6、流线型分流器7、分流支架8、芯棒9、口模
另一种是流线式挤管机头,如图5所示,与第一种直通式挤管机头的不同之处在于:1、过滤板设计成流线型过渡套;2、分流器设计成流线型分流器。能够很好得解决直通式挤管机头存在的问题。并且我选择的是聚乙烯管的挤出机,流线式挤管机头更适合。
5.设计挤管机头;
6.绘制挤出机及其机头装配图;
7.撰写毕业论文。
四、研究工作进度:
序号
时间
内容
1
第3~4周
搜集与塑料挤管机相关的文献与资料
2
第5~6周
学习塑料成型理论及塑料成型机械的相关知识
3
第7~10周
设计塑料挤出机主机
4
第11~12周
学习塑料模具成形理论
5
第13~16周
设计挤管机头
6
第17~18周
在机头方面,普通挤管机头的基本形式有两种:一种是常用的直通式挤管机头,另一种是流线式挤管机头。直通式机头的结构特点:主要是机头的结构设计比较简单加工容易,制造成本低。但是也存在一定的缺陷,主要有以下三个方面:1、内部结构有死角;2、机头与挤出机连接处空间过大时,加工PVC管材极不利;3、机头与挤出机的型号大小选配上互换性差。
塑料挤出机装置自动换网机构的研究和改进的开题报告
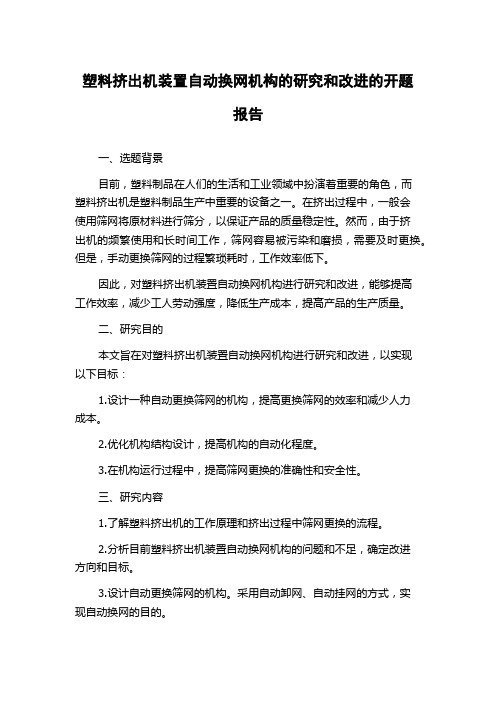
塑料挤出机装置自动换网机构的研究和改进的开题报告一、选题背景目前,塑料制品在人们的生活和工业领域中扮演着重要的角色,而塑料挤出机是塑料制品生产中重要的设备之一。
在挤出过程中,一般会使用筛网将原材料进行筛分,以保证产品的质量稳定性。
然而,由于挤出机的频繁使用和长时间工作,筛网容易被污染和磨损,需要及时更换。
但是,手动更换筛网的过程繁琐耗时,工作效率低下。
因此,对塑料挤出机装置自动换网机构进行研究和改进,能够提高工作效率,减少工人劳动强度,降低生产成本,提高产品的生产质量。
二、研究目的本文旨在对塑料挤出机装置自动换网机构进行研究和改进,以实现以下目标:1.设计一种自动更换筛网的机构,提高更换筛网的效率和减少人力成本。
2.优化机构结构设计,提高机构的自动化程度。
3.在机构运行过程中,提高筛网更换的准确性和安全性。
三、研究内容1.了解塑料挤出机的工作原理和挤出过程中筛网更换的流程。
2.分析目前塑料挤出机装置自动换网机构的问题和不足,确定改进方向和目标。
3.设计自动更换筛网的机构。
采用自动卸网、自动挂网的方式,实现自动换网的目的。
4.优化自动换网机构的结构设计。
结合实际需要,调整机构的构造,提高机构的自动化程度和可靠性。
5.制造和试验自动换网机构。
对设计的自动更换筛网的机构进行制造和装配,并进行实验检测,检验机构的性能和效果。
四、研究意义本研究通过对塑料挤出机装置自动换网机构的研究和改进,能够有效提高塑料挤出机生产过程的效率和质量。
另外,通过对自动换网机构的优化设计和实验测试,可以探索应用自动化技术提高工业生产效率,推动工业制造的现代化转型。
五、研究方法1. 文献分析法。
通过阅读相关的文献和资料,了解塑料挤出机的工作原理和挤出过程中筛网更换的流程,并学习和借鉴国内外自动换网机构的设计经验和成功案例。
2. 实验方法。
通过对设计的自动更换筛网的机构进行制造和装配,并进行实验检测,检验机构的性能和效果。
3. 经济分析法。
微孔塑料挤出成型熔体输送流动的数值模拟的开题报告

微孔塑料挤出成型熔体输送流动的数值模拟的开题报告一、选题背景微孔塑料挤出成型技术是目前广泛应用于医疗、电子、光学等领域的一种新兴成型技术。
当塑料熔体通过微孔板时,熔体中的高分子长链分子在微孔板上留下了微小的残留物,形成了所谓的微孔结构,使塑料具有特殊的性能,如透气、过滤等。
然而,微孔板的制造和微孔塑料挤出成型的过程比较复杂,需要对熔体的输送和流动进行深入的研究,才能提高微孔板的质量和产品的成型精度。
数值模拟方法是一种有效的手段,可以探究微孔塑料挤出成型熔体的输送流动行为,为优化成型工艺的设计提供参考。
二、研究目的本文旨在研究微孔塑料挤出成型熔体输送流动的数值模拟方法,揭示微孔板结构和成型工艺对熔体流动行为的影响,为优化微孔塑料挤出成型工艺提供理论基础和实验指导。
三、研究内容和方法本文主要研究内容包括:(1) 建立微孔塑料挤出成型熔体输送流动的数学模型;(2) 利用有限体积法,对微孔塑料挤出成型熔体的输送流动进行数值模拟;(3) 分析微孔板孔径、孔距、孔形等结构因素对熔体流动的影响;(4) 研究熔体温度、流量、粘度等工艺参数对熔体流动的影响。
四、研究意义本文研究成果对于提高微孔塑料挤出成型熔体输送流动的精度和效率,提高微孔板的加工质量,推广微孔塑料挤出成型技术和产品的广泛应用,具有重要的理论和实际意义,具有较好的应用前景。
五、预期成果本文预期完成的研究成果包括:(1) 建立微孔塑料挤出成型熔体输送流动的数学模型;(2) 利用有限体积法,对微孔塑料挤出成型熔体的输送流动进行数值模拟;(3) 分析微孔板孔径、孔距、孔形等结构因素对熔体流动的影响;(4) 研究熔体温度、流量、粘度等工艺参数对熔体流动的影响;(5) 提出优化微孔塑料挤出成型熔体输送流动的建议和措施。
(完整版)注塑机毕业设计开题报告
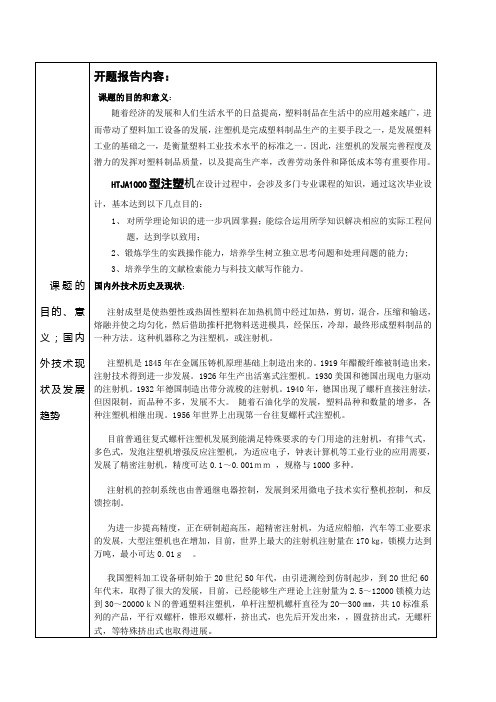
为进一步提高精度,正在研制超高压,超精密注射机,为适应船舶,汽车等工业要求 的发展,大型注塑机也在增加,目前,世界上最大的注射机注射量在 170 ㎏,锁模力达到 万吨,最小可达 0.01g 。
我国塑料加工设备研制始于 20 世纪 50 年代,由引进测绘到仿制起步,到 20 世纪 60 年代末,取得了很大的发展,目前,已经能够生产理论上注射量为 2.5~12000 锁模力达 到 30~20000kN的普通塑料注塑机,单杆注塑机螺杆直径为 20—300 ㎜,共 10 标准系 列的产品,平行双螺杆,锥形双螺杆,挤出式,也先后开发出来,,圆盘挤出式,无螺杆
课 题 的 国内外技术历史及现状:
目的、意 义;国内
注射成型是使热塑性或热固性塑料在加热机筒中经过加热,剪切,混合,压缩和输送, 熔融并使之均匀化,然后借助推杆把物料送进模具,经保压,冷却,最终形成塑料制品的 一种方法。这种机器称之为注塑机,或注射机。
外技术现 状及发展 趋势
注塑机是 1845 年在金属压铸机原理基础上制造出来的。1919 年醋酸纤维被制造出来, 注射技术得到进一步发展。1926 年生产出活塞式注塑机。1930 美国和德国出现电力驱动 的注射机。1932 年德国制造出带分流梭的注射机。1940 年,德国出现了螺杆直接注射法, 但因限制,而品种不多,发展不大。 随着石油化学的发展,塑料品种和数量的增多,各 种注塑机相继出现。1956 年世界上出现第一台往复螺杆式注塑机。
目前普通往复式螺杆注塑机发展到能满足特殊要求的专门用途的注射机,有排气式, 多色式,发泡注塑机增强反应注塑机,为适应电子,钟表计算机等工业行业的应用需要, 发展了精密注射机,精度可达 0.1~0.001mm ,规格与 1000 多种。
注射机的控制系统也由普通继电器控制,发展到采用微电子技术实行整机控制,和反 馈控制。
聚碳酸酯反应挤出过程模拟研究的开题报告

聚碳酸酯反应挤出过程模拟研究的开题报告一、研究背景聚碳酸酯是一种重要的高分子材料,具有高温耐性、高刚度、高强度、透明度好、耐化学腐蚀等优良性能。
聚碳酸酯的反应挤出过程是制备高性能聚碳酸酯制品的重要工艺,其成功与否直接影响到制品的品质和成本。
目前,针对聚碳酸酯的反应挤出过程进行模拟研究的国内外文献较为有限,特别是在考虑各种外部因素(如压力、温度、流速等)对挤出过程的影响下,模拟挤出过程的精度和可靠性仍有待提高。
因此,本文拟开展聚碳酸酯反应挤出过程模拟研究,为制备高性能聚碳酸酯制品提供理论依据和参考。
二、研究目的本研究旨在开展聚碳酸酯反应挤出过程的数值模拟,深入了解挤出过程中各种外部因素对产品成型质量的影响规律和机理,从而优化整个挤出生产工艺及相关参数设置。
具体目标如下:1. 建立数学模型,通过计算流体力学方法,对挤出过程进行模拟;2. 分析挤出过程中关键的物理参数及其相互作用,包括温度、压力、速度等;3. 模拟挤出过程中料液的流动规律,探究其对产品成型的影响;4. 通过模拟,优化生产工艺和生产参数设置,制备出性能更佳的聚碳酸酯制品。
三、研究内容本研究将聚焦于聚碳酸酯反应挤出过程模拟研究,具体可分为以下内容:1. 聚碳酸酯挤出生产工艺及现状的调研和分析;2. 挤出过程数值模拟的基本理论及流体力学的基本原理;3. 利用计算流体力学方法,建立聚碳酸酯反应挤出过程的数学模型,包括材料的物理性质、温度流场等;4. 计算分析挤出过程中各种外部因素对产品成型质量的影响,如温度、压力、速度等;5. 优化生产工艺和生产参数设置,制备出性能更佳的聚碳酸酯制品。
四、研究方法与技术路线本研究将采用计算流体力学方法对聚碳酸酯反应挤出过程进行数值模拟,并通过实验对模拟结果进行验证和优化。
具体技术路线如下:1. 文献调研和工艺分析,确定研究对象和研究目标;2. 确定数学模型,包括材料的物理性质、温度流场等;3. 使用ANSYS Fluent等计算流体力学软件模拟挤出过程,分析各种外部因素对产品成型质量的影响;4. 在实验室进行挤出实验,对模拟结果进行验证和优化;5. 按照优化后的工艺和参数制备聚碳酸酯制品,并对其物理性能和机械性能进行测试和分析。
塑料挤出综合实训报告

塑料挤出综合训练报告一、实训目的1、熟悉掌握塑料挤出的相关操作2、了解塑料包装袋及管材成型的基本原理3、了解单螺杆挤出机、吹膜机等结构和工作原理4、掌握塑料挤出的工艺参数调整及分析挤出产品的质量问题5、了解塑料管材及包装袋的生产流程6、了解双螺杆混炼造粒机的操作二、实训原理1、PE包装袋生产原理包装袋的生产原理实质就是在挤出的型胚内通过空气吹胀后成型的,它包括吹塑薄膜和中空吹塑成型。
在吹塑薄膜成型中,根据牵引的方向不同,通常分为平挤上吹、平挤下吹、平挤平吹三种工艺方法,其基本原理都是相同的,其中平挤上吹法应用最广。
塑料包装袋的吹塑成型是基于高聚物的分子量高、分子间力大而具有可塑性及成膜性能。
在挤出机的前端安装吹塑口模,粘流态的塑料从挤出机口模挤出成管胚后用机头底部通入的空气使之均匀而自由地吹胀成直径较大的管膜,膨胀的管膜在向上被牵引的过程中,被纵向拉伸并逐步被冷却,并由人字板夹平和牵引辊牵引,最后经卷绕辊卷绕成双折膜卷。
2、PPR管材生产原理塑料管材成型是基于高聚物的分子量高、分子间力大而具有可塑性。
粘流态的塑料从挤出机口模挤出成管胚,经过真空冷却定型装置通过冷却水冷却成型,然后经过冷却水冷却,接着经过牵引机牵引,最后经过切割部分切割规定长度的塑料管材。
3、双螺杆混炼挤出造粒机工作原理高聚物经过螺杆挤出机的塑化、熔融,通过机头挤出成条形或带形后,由造粒设备切成颗粒,在经过震动筛的筛选,获得所需粒径的塑料颗粒。
挤出形式可分为热切和冷切,本实验采用的是冷切,即物料从机头模孔中挤出后牵引拉成条状,进入水槽中冷却后进行切粒的方法。
三、实训装置1、PE包装袋生产装置(1)单螺杆挤出机(2)直通式吹膜机头口模(3)冷却风环(4)牵引、卷取装置(5)空气压缩机(6)千分尺、卷尺、手套、剪刀、卷轴(7)导向展平管2、PPR管材生产装置(1)游标卡尺(2)卷尺(3)堆料装置(4)牵引装置(5)冷却装置四、实训步骤1、PE包装袋生产步骤(1)按照挤出机的操作规程,接通电源,开机运转和加热。
螺杆挤出机胶料挤出性能研究的开题报告
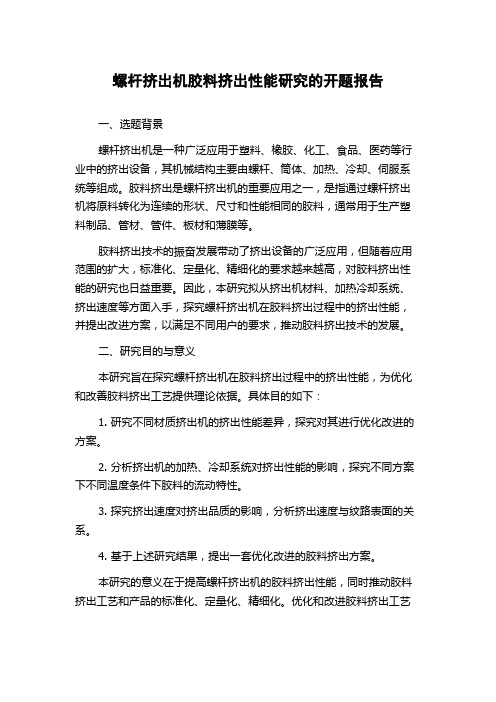
螺杆挤出机胶料挤出性能研究的开题报告一、选题背景螺杆挤出机是一种广泛应用于塑料、橡胶、化工、食品、医药等行业中的挤出设备,其机械结构主要由螺杆、筒体、加热、冷却、伺服系统等组成。
胶料挤出是螺杆挤出机的重要应用之一,是指通过螺杆挤出机将原料转化为连续的形状、尺寸和性能相同的胶料,通常用于生产塑料制品、管材、管件、板材和薄膜等。
胶料挤出技术的振奋发展带动了挤出设备的广泛应用,但随着应用范围的扩大,标准化、定量化、精细化的要求越来越高,对胶料挤出性能的研究也日益重要。
因此,本研究拟从挤出机材料、加热冷却系统、挤出速度等方面入手,探究螺杆挤出机在胶料挤出过程中的挤出性能,并提出改进方案,以满足不同用户的要求,推动胶料挤出技术的发展。
二、研究目的与意义本研究旨在探究螺杆挤出机在胶料挤出过程中的挤出性能,为优化和改善胶料挤出工艺提供理论依据。
具体目的如下:1. 研究不同材质挤出机的挤出性能差异,探究对其进行优化改进的方案。
2. 分析挤出机的加热、冷却系统对挤出性能的影响,探究不同方案下不同温度条件下胶料的流动特性。
3. 探究挤出速度对挤出品质的影响,分析挤出速度与纹路表面的关系。
4. 基于上述研究结果,提出一套优化改进的胶料挤出方案。
本研究的意义在于提高螺杆挤出机的胶料挤出性能,同时推动胶料挤出工艺和产品的标准化、定量化、精细化。
优化和改进胶料挤出工艺将有助于提高生产效率、减少成本,进一步促进塑料、橡胶等行业的发展。
三、研究内容及方法本研究包括以下三个方面:1. 螺杆挤出机材料的研究:研究螺杆挤出机的材料种类、密度、强度等性质,探究不同材料挤出性能差异。
2. 挤出加热冷却系统的研究:研究加热、冷却系统的原理和结构,探究不同方案下温度对挤出品质的影响。
3. 挤出速度对挤出品质的影响研究:探究不同挤出速度对挤出品质的影响,比较不同产品表面纹路的差异。
本研究将采用多种研究方法:1. 文献资料法:查阅国内外相关文献资料,了解螺杆挤出机的胶料挤出性能研究现状及发展趋势。
- 1、下载文档前请自行甄别文档内容的完整性,平台不提供额外的编辑、内容补充、找答案等附加服务。
- 2、"仅部分预览"的文档,不可在线预览部分如存在完整性等问题,可反馈申请退款(可完整预览的文档不适用该条件!)。
- 3、如文档侵犯您的权益,请联系客服反馈,我们会尽快为您处理(人工客服工作时间:9:00-18:30)。
一、综述本课题国内外研究动态,说明选题的依据和意义
1、国内外研究动态
塑料成型加工是一门工程技术,所涉及的内容是将塑料转变为塑料制品的各种工艺。其成型方法有:压缩模塑、层压成型、冷压模塑、传递模塑、低压成型、挤出成型、挤拉成型、注射成型、吹塑成型、浇铸、手糊成型、纤维缠绕成型、压延、涂覆、发泡成型、二次成型、二次加工等。
在传动系统方面,传动系统是挤管机的主要组成部分之一。其作用是驱动螺杆并使螺杆能在选定的工艺操作条件下(如温度、压力和速度等)获得所需的扭矩并能均匀地旋转,以完成对塑料的塑化和连续地输送、挤出成型。
挤管机的传动系统通常由原动机(如电动机等)、减速装置、调速装置等所组成。但目前在生产实践中,挤管机大多采用齿轮减速器,小型挤管机也采用蜗轮蜗杆减速器。而目前随着电工技术和数控技术的发展,调速方法有:(1)用整流子电机调速;(2)用直流电机调速;(3)用滑差电机调速;(4)用三相交流电机与变频器相结合调速。当前用三相交流电机与变频器相结合调速的技术已比较成熟,且容易掌握,所以我打算在原有的传动系统上做点改进,将原来的普通电动机改作三相交流电机,配合变频器来实现电机的调速,以取代原来的减速装置,这样既提高了管子的生产效率,同时也减低了制造成本。
[23]北京化工学院、天津轻工业学院塑料成型机械[M]轻工业出版社1982
[24]梁基照挤出机螺杆加料段的优化设计[M]橡胶工业2001 48(8):489~491
[25]Taylor P. Rotomoulding[J].British Plastics and rubber, 1986(2):22~27
塑料挤管机是挤出成型机的一种,它由挤出机、挤管机头、定径装置、冷却装置、切割装置及堆放装置等组成。如图1所示
图1管材挤出机组
1—塑料管2—牵引机3—真空定型及冷却装置4—机头5—挤出机
其中单螺杆挤出机的基本结构主要包括挤出装置、传动机构和加热、冷却系统传动装置、加料装置、料筒、螺杆、机头和口模等部分,如图2所示
2、选题的依据和意义:
普通的螺杆根据各功能的不同,可分为三段(加料段、熔融段和计量段)。如图3所示:
图3常规全螺纹螺杆的三个职能区
其中加料段是由加料区(又称冷却料斗区)、固体输送区以及一个过滤的迟滞区所组成,其功能是对塑料进行压实和输送。此段的工作过程如下:
塑料自料斗进入螺杆以后,在旋转着的螺杆的作用下,通过机筒内壁和螺杆表面的摩擦作用向前输送和压实。一般来说,塑料在加料段是呈固态向前输送的。根据观察,通常在接近加料段的末端,由于强烈的摩擦而产生的热的作用,与机筒内壁相接触的塑料已达到黏流态温度,开始熔融,而出现一个过渡区。严格地说,一般所谓的迟滞区是指从固体输送区结束到熔池最初出现的这一区域。为了提高管料的输送效率,提高产量,打算在原来的螺杆的加料段的中段处加一冷却装置,目的是为了不让塑料在螺杆中过早的熔融而粘在螺杆上,而降低螺杆原料的输送速度。
与其他成型方法相比,挤出机及其成型有下述主要特点:生产过程是连续的,因而其产品也是连续的;生产效率高;应用范围广,不仅能连续生产各种制品,而且还可以进行混合、塑化、造粒、脱水喂料和着色等的准备工序;投资少,收效快。
根据螺杆的数量,塑料挤出机可以分为:无螺杆挤出机(其中又分柱塞式挤出机和黏弹熔体挤出机)、单螺杆挤出机、双螺杆挤出机(其中又分平行双螺杆挤出机和锥形双螺杆挤出机以及反向和同向旋转的双螺杆挤出机)、多螺杆挤出机或行星螺杆挤出机;根据螺杆的转速,塑料挤出机可以分为:普通挤出机、高速挤出机和超高速挤出机;根据装配结构,塑料挤出机可以分为:整体式挤出机和分体式挤出机;根据安装位置的不同,塑料挤出机可以分为:卧式挤出机(螺杆在空间呈水平安装)、立式挤出机(螺杆直立于地面安装);根据其功能的不同,塑料挤出机还可以分为:排气式挤出机、混炼挤出机、两段式挤出机和超高分子量聚合物挤出机、往复式单螺杆挤出机等。目前国内应用最多的是务实单螺杆整体装配式挤出机和双螺杆挤出机。
其中挤出成型也称挤压模塑或挤塑,它是在挤出机中通过加热、加压而使物料以流动状态连续通过口模成型的方法,是塑料成型加工的重要成型方法之一。大部分热塑性塑料都能用此方法成型。挤出成型是在挤出机上进行的,挤出机是塑料成型加工机械的主要装备之一。挤出法主要用于热塑性塑料的成型,也可用于某些热固性塑料。挤出的制品都是连续的型材,如管、棒、丝、板、薄膜、电线电缆包覆层等。此外,还可用于塑料的混合、塑化造粒、着色、掺合等。
5.设计挤管机头;
6.绘制挤出机及其机头装配图;
7.撰写毕业论文。
四、研究工作进度:
序号
时间
内容
1
第3~4周
搜集与塑料挤管机相关的文献与资料
2
第5~6周
学习塑料成型理论及塑料成型机械的相关知识
3
第7~10周
设计塑料挤出机主机
4
第11~12周
学习塑料模具成形理论
5
第13~16周
设计挤管机头
6
第17~18周
1.搜集与塑料挤管机相关的文献与资料;
2.学习塑料成型理论及塑料成型机械的相关知识;
3.根据了解的资料与所学的知识,设计塑料挤出机主机(包括挤出机的工作特性、单螺杆挤出机挤压系统的主要零部件、加料装置、传动系统、加热冷却装置等);
4.学习塑料模具成形理论(包括注塑成型模具、压塑成型模具、热固性塑料的传递和注塑成型模具、挤塑成型模具、吹塑制品成型模具、热成型模具等);
[10]吴清文,王世杰,黄群塑料挤出模头口模定型段长度的确定[J]塑料科技,1994,99(1): 26~29
[11]王晓枫,朱元吉,谢挺,尹延国塑料挤出成型模具流道优化设计[J]塑料科技,1996,2:42~44
[12]北京化工大学,华南理工大学塑料机械设计,第二版[M]北京:中国轻工业出版社,1995
二、研究的基本内容,拟解决的主要问题:
1.挤出壁厚1~2 mm聚乙烯管的挤出机参数确定;
2.分析塑料挤出原理,阐述挤出理论;
3.设计塑料挤出机(螺杆直径65mm,塑料管直径30mm);
4.掌握变频调速在传动系统中的应用技术;
5.分析塑料模具成形理论;
6.设计挤管机头;
7.绘制挤出机及其机头装配图。
三、研究步骤、方法及措施:
[5]张燕宾SPWM变频调速应用技术[M]北京:机械工业出版社1997.12
[6]朱复华挤出理论及应用[M]北京:中国轻工业出版社,2001
[7]马金骏塑料挤出成型模具设计[M]北京:中国轻工业出版社
[8]W米歇利挤塑模头设计及工程计算[J]烃加工出版社1989,135~147
[9]夏振国环形共挤出模头新近展[J]塑料机械与设备34~37
图2挤出机结构图
图中:1为机头连接法兰;2为滤板;3为冷却水管;4为加热器;5为螺杆;6为料筒;7为油泵;8为测速电机;9为止推轴承;10为料斗;11为减速箱;12为螺杆冷却装置。
总的来说,由于我国的塑料工业与发达国家相比起步还是晚一些,因此在经济规模上,尤其是在管料性能、效率和传动系统等方面与发达国家相比还存在一定的差距。
[13]北京化工学院,天京轻工业学院塑料成型机械[M]北京:轻工业出版社,1985
[14]黄锐塑料工程手册[M]北京:机械工业出版社,2000
[15]朱复华螺杆设计及其理论挤出[M]北京:中国轻工业出版社,1984
[16]宗远智塑料机械电气装置[M]北京:轻工业出版社,1987
[17]李庆春,懂磊单螺杆挤出机——熔体泵串联挤出系统的性能与应用[J]中国塑料2003(6)
[18]马金骏塑料基础模具设计图册[M]北京轻工业出版社1984
[19]成都科技大学塑料成型模具[M]北京轻工业出版社1990
[20]张小文塑料管道及管件加工与应用[M]北京中国石化出版社2002
[21]申长雨等塑料模具计算机辅助工程[M]郑州:河南科学技术出版社1998
[22]林德宽、冯少如塑料制件成型工艺及设备[M]国防工业出版社1980
在常规单螺杆挤出机组的性能方面,我国已能生产螺杆直径为Φ12~250mm的多种规格、门类齐全的挤出机组,长径比大多为25~30。一些新型的混炼元件如分离型、屏障型、分流型、变流道型以及流速位置变换型等混炼元件得到了较为广泛的应用。以直径为Φ90mm的单螺杆挤出机为例,从1961年其产量为90整提高了6.7倍;又如WP公司生产的同向平行双螺杆挤出机从1995~2001年的6年间,其螺杆转速从600r/min提高到1800r/min,产量则相应提高了2.5倍。2000年我国挤出机的产量已达7784台,其中同向平双844台,异向平双及锥双1255台,在进口1817台挤出成型机中绝大部分是大型的、精密的机器。
熔融段是使塑料进一步压实和塑化,使包围在塑料内的空气压回到加料口处排出,并改善塑料的热传导性能。这一段的螺槽应该是压缩型的,而且螺杆的几何压缩比应当大于物料的物理压缩比。因此该段的温度显得非常重要,合适的温度才能使塑料完全熔融,从而使包围在塑料内的空气通过挤压顺利排出,从而提升成品的质量,管料质地结实无空洞,同时也能提高整体塑料的流量,增加参量,提高效率。故打算在该段安装温度检测装置,使物料快速提升到较适宜的温度,如果包围在塑料内的空气压还是不能顺利排出,可采用双螺杆来输送。
图5流线式挤管机头
1、螺杆2、机筒3、流线型过度套4、法兰
5、机头体6、流线型分流器7、分流支架8、芯棒9、口模
另一种是流线式挤管机头,如图5所示,与第一种直通式挤管机头的不同之处在于:1、过滤板设计成流线型过渡套;2、分流器设计成流线型分流器。能够很好得解决直通式挤管机头存在的问题。并且我选择的是聚乙烯管的挤出机,流线式挤管机头更适合。
在机头方面,普通挤管机头的基本形式有两种:一种是常用的直通式挤管机头,另一种是流线式挤管机头。直通式机头的结构特点:主要是机头的结构设计比较简单加工容易,制造成本低。但是也存在一定的缺陷,主要有以下三个方面:1、内部结构有死角;2、机头与挤出机连接处空间过大时,加工PVC管材极不利;3、机头与挤出机的型号大小选配上互换性差。