CVD工艺简介
CVD工艺介绍

-----CVD入门介绍
CISEMI 周华强 2012/07/25
目录
1: CVD概念和特点 2:几种CVD类型、原理及特性 3:薄膜CVD膜和扩散CVD膜的区别 4: 薄膜区其它工艺介绍 5:薄膜各种膜及各膜在IC的作用 6:薄膜常见异常
1: CVD的概念、特点
1.1 CVD的概念:
一般而言,淀积的二氧化硅同热生长二氧化硅相比,密度较低,硅与氧数量之比与热生 长SiO2也存在轻微的差别,因而薄膜的力学和电学特性也就有所不同.高温淀积或者在淀积 之后进行高温退火,都可以使CVD二氧化硅薄膜的特性接近于热生长SiO2的特性.
3.2 LPCVD和PECVD SiO2膜的区别
(1)APCVD(400℃,P=760Torr):SiH4+O2 a. dep rate<2000A/min b. coverage:50-60%
段。
2.4 低压化学气相淀积系统
晶圆装载 门
压力计
晶圆
加热线圈
制程气体入口 温度
晶舟 中心区
均温区
至真空pump 石英管 距离
2.5 等离子增强型化学气相淀积(PECVD)
PECVD的特性:
• 相对低温,有高的淀积速率. • 较低的压力下离子有较长的平均自由路径,会提高淀积速
率
• Plasma的离子轰击能够去除表面杂质,增强黏附性 • 射频RF可以控制淀积薄膜的应力 • 反应室可用Plasma清洗.
上面讲了 PECVD和LPCVD的区别;
Any Questions
下面我进入薄膜区,来介绍 薄膜区其它工艺介绍
1:SACVD 2: SOG 3: CMP 4: WCVD
Any Questions
cvd化学气相沉积工艺

CVD(化学气相沉积)是一种重要的薄膜生长工艺,广泛应用于半导体、光电子、纳米材料和涂层工业中。
以下是CVD工艺的基本概述:1. 概念:CVD是一种通过将气体前体化合物沉积在固体表面上来生长薄膜或涂层的工艺。
这些前体气体通过加热可升华或分解,然后在基底表面反应并形成所需的材料。
2. 基本步骤:CVD工艺包括以下基本步骤:a. 前体气体引入:气体前体化合物以气体或液体形式引入反应室。
b. 基底准备:基底通常是硅片、玻璃、金属等,必须事先准备,例如清洗和加热,以确保薄膜附着良好。
c. 气体分解或反应:前体气体在高温下分解或反应,生成反应产物。
d. 反应产物沉积:反应产物沉积在基底表面,形成所需的薄膜或涂层。
e. 废气排放:废气将未反应的气体和副产物排出反应室。
3. 温度和压力控制:控制CVD工艺的温度和压力非常重要。
温度通常高于反应气体的沸点,以确保气体前体可以蒸发或分解。
压力可以调整以控制气体的浓度和反应速率。
4. 类型:CVD工艺有多种类型,包括:a. 热CVD:在高温下进行,常用于硅片生产等。
b. 低压CVD(LPCVD):在较低的压力下进行,适用于高质量薄膜的生长。
c. PECVD(等离子体增强化学气相沉积):使用等离子体激活气体前体,通常用于生长氢化非晶硅薄膜等。
d. MOCVD(金属有机化学气相沉积):用于生长半导体材料,如GaAs、InP等。
5. 应用:CVD工艺在半导体制造、光电子器件、太阳能电池、涂层技术、纳米材料制备等领域具有广泛应用。
它用于生长晶体薄膜、导电涂层、光学涂层、硅片的外延生长等。
6. 控制和监测:CVD工艺需要精确的温度、压力和气体流量控制,以及监测反应产物和废气的化学成分。
总之,CVD是一种重要的化学气相沉积工艺,可用于生长各种薄膜和涂层,广泛应用于多个工业领域,是现代微电子和纳米技术的基础之一。
CVD工艺原理及设备介绍
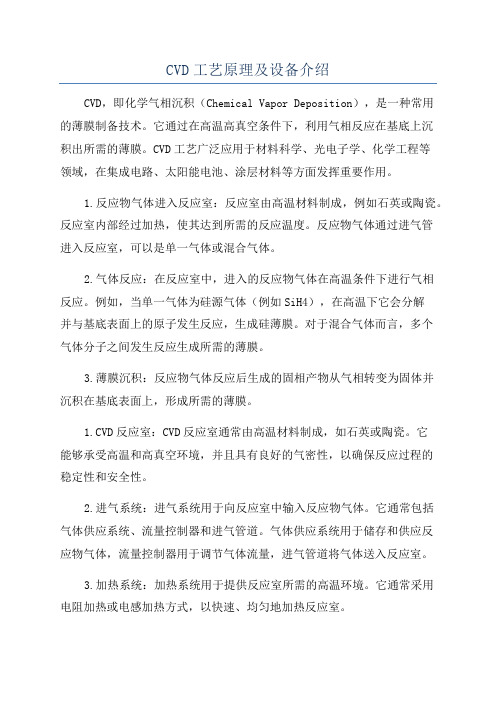
CVD工艺原理及设备介绍CVD,即化学气相沉积(Chemical Vapor Deposition),是一种常用的薄膜制备技术。
它通过在高温高真空条件下,利用气相反应在基底上沉积出所需的薄膜。
CVD工艺广泛应用于材料科学、光电子学、化学工程等领域,在集成电路、太阳能电池、涂层材料等方面发挥重要作用。
1.反应物气体进入反应室:反应室由高温材料制成,例如石英或陶瓷。
反应室内部经过加热,使其达到所需的反应温度。
反应物气体通过进气管进入反应室,可以是单一气体或混合气体。
2.气体反应:在反应室中,进入的反应物气体在高温条件下进行气相反应。
例如,当单一气体为硅源气体(例如SiH4),在高温下它会分解并与基底表面上的原子发生反应,生成硅薄膜。
对于混合气体而言,多个气体分子之间发生反应生成所需的薄膜。
3.薄膜沉积:反应物气体反应后生成的固相产物从气相转变为固体并沉积在基底表面上,形成所需的薄膜。
1.CVD反应室:CVD反应室通常由高温材料制成,如石英或陶瓷。
它能够承受高温和高真空环境,并且具有良好的气密性,以确保反应过程的稳定性和安全性。
2.进气系统:进气系统用于向反应室中输入反应物气体。
它通常包括气体供应系统、流量控制器和进气管道。
气体供应系统用于储存和供应反应物气体,流量控制器用于调节气体流量,进气管道将气体送入反应室。
3.加热系统:加热系统用于提供反应室所需的高温环境。
它通常采用电阻加热或电感加热方式,以快速、均匀地加热反应室。
4.泵系统:泵系统用于建立和维持反应室内的高真空环境。
它可以采用机械泵、分子泵或离子泵等不同类型的泵,以实现有效的气体抽取和排放。
5.控制系统:控制系统用于监控和调节CVD过程中的各个参数,如温度、气体流量、制备时间等。
它通常由传感器、控制器和数据记录设备组成,以确保制备过程的可重复性和稳定性。
总之,CVD工艺是一种重要的薄膜制备技术,通过在高温高真空条件下将气相物质沉积到基底表面上,实现薄膜的制备。
第四章CVD工艺

早期CVD 技术以开管系统为主, 即Atmosphere Pressure
CVD (APCVD)。
近年来,CVD技术令人注目的新发展是低压CVD技术,
即Low Pressure CVD(LPCVD)。
LPCVD原理与APCVD基本相同,主要差别是:
低压下气体扩散系数增大,使气态反应物和副产物的
三、CVD方法简介
☞封闭式(闭管沉积系统)CVD
闭管法的优点:污染的机会少,不必连续抽气保持
反应器内的真空,可以沉积蒸气压高的物质。
闭管法的缺点:材料生长速率慢,不适合大批量生长,
一次性反应器,生长成本高;管内压力检测困难等。
闭管法的关键环节:反应器材料选择、装料压力计算、
温度选择和控制等。
四、低压化学气相沉积(LPCVD)
学气相沉积。用来制备化合物薄膜、非晶薄膜、外
延薄膜、超导薄膜等,特别是IC技术中的表面钝化
和多层布线。
五、等离子增强化学气相沉积(PECVD)
☞等离子化学气相沉积
Plasma CVD
Plasma Associated CVD
Plasma Enhanced CVD
这里称PECVD
PECVD是指利用辉光放电的物理作用来激活化学
一、化学气相沉积的基本原理
☞化学气相沉积的基本原理
➢ CVD的(化学反应)动力学
热分解反应(吸热反应)
(2)金属有机化合物
M-C键能小于C-C键,广泛用于沉积金属和氧化物薄膜。
金属有机化合物的分解温度非常低,扩大了基片选
择范围以及避免了基片变形问题。
(3)氢化物和金属有机化合物系统
广泛用于制备化合
气相沉积反应的CVD技术。广泛应用于微电子学、
碳化硅外延cvd法-概述说明以及解释
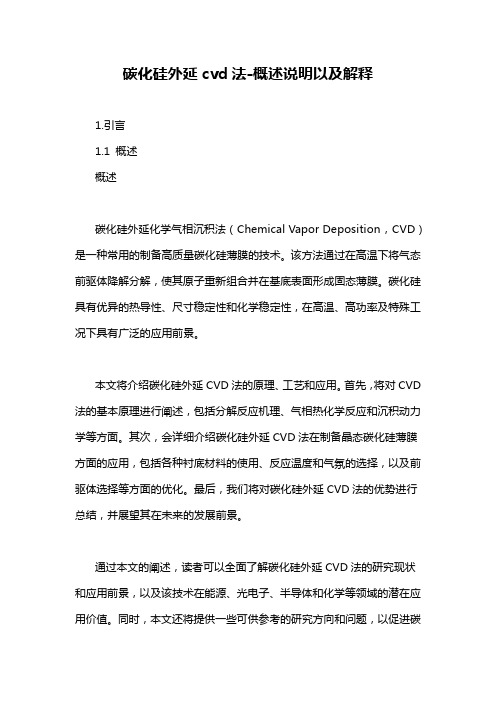
碳化硅外延cvd法-概述说明以及解释1.引言1.1 概述概述碳化硅外延化学气相沉积法(Chemical Vapor Deposition,CVD)是一种常用的制备高质量碳化硅薄膜的技术。
该方法通过在高温下将气态前驱体降解分解,使其原子重新组合并在基底表面形成固态薄膜。
碳化硅具有优异的热导性、尺寸稳定性和化学稳定性,在高温、高功率及特殊工况下具有广泛的应用前景。
本文将介绍碳化硅外延CVD法的原理、工艺和应用。
首先,将对CVD 法的基本原理进行阐述,包括分解反应机理、气相热化学反应和沉积动力学等方面。
其次,会详细介绍碳化硅外延CVD法在制备晶态碳化硅薄膜方面的应用,包括各种衬底材料的使用、反应温度和气氛的选择,以及前驱体选择等方面的优化。
最后,我们将对碳化硅外延CVD法的优势进行总结,并展望其在未来的发展前景。
通过本文的阐述,读者可以全面了解碳化硅外延CVD法的研究现状和应用前景,以及该技术在能源、光电子、半导体和化学等领域的潜在应用价值。
同时,本文还将提供一些可供参考的研究方向和问题,以促进碳化硅外延CVD法的进一步发展和应用。
1.2文章结构1.2 文章结构本文主要介绍了碳化硅外延CVD法的技术和应用。
具体内容包括以下几个方面:第二部分将详细介绍碳化硅外延技术。
首先会对碳化硅外延的基本概念进行解释,并介绍其在半导体工业中的重要性。
然后会介绍CVD法在碳化硅外延中的应用,包括其原理、工艺流程和实验设备等。
第三部分将对碳化硅外延CVD法的优势进行总结。
这一部分将重点探讨CVD法在碳化硅外延制备中的优点,如高晶体质量、可控性和制备效率等。
最后,第四部分将展望碳化硅外延CVD法在未来的发展前景。
这一部分将分析当前碳化硅外延CVD法存在的挑战和问题,并提出改进和发展思路,以期实现碳化硅外延技术的进一步发展和应用。
通过对碳化硅外延CVD法的全面介绍和分析,本文旨在为读者提供全面了解碳化硅外延CVD法的基础知识,以及认识和认识碳化硅外延技术在半导体工业中的应用前景。
cvd的工艺流程

cvd的工艺流程那咱就开始唠唠CVD的工艺流程哈。
CVD呢,它全称叫化学气相沉积。
这可是个很有趣的技术哦。
一、反应气体的准备。
CVD的第一步呀,就是要准备那些反应气体。
就像是做菜要先准备食材一样。
这些气体可都是有讲究的呢。
比如说,可能会用到硅烷(SiH₄)之类的气体。
这些气体得保证纯度比较高,要是不纯呀,就像做饭的时候食材坏了一样,后面做出来的东西肯定不行。
这些气体要通过特殊的管道系统输送到反应室,管道得密封得严严实实的,可不能让气体偷偷跑掉啦。
二、反应室里的事儿。
接下来就是反应室这个大舞台啦。
反应室的环境很关键哦。
它里面的温度、压力都得控制得恰到好处。
温度就像是反应的指挥棒,不同的反应可能需要不同的温度。
比如说有的可能要几百度,有的可能要上千度呢。
压力也很重要,就像给反应营造一个舒适的氛围一样。
在这个反应室里,那些反应气体在高温或者其他条件的作用下,就开始发生奇妙的化学反应啦。
原子呀,分子呀,就像一群调皮的小精灵,开始重新组合排列。
三、沉积过程。
在反应室里发生反应的时候呢,就会有物质沉积下来。
这就好比是盖房子的时候,一块一块的砖头慢慢垒起来。
这些沉积下来的物质可能会在基底上形成一层薄膜,这薄膜的质量就取决于前面那些步骤做得好不好啦。
如果前面气体不纯,或者反应室的条件没控制好,那这薄膜可能就会有很多缺陷,就像一件漂亮衣服上有很多破洞一样,肯定不好看也不实用呀。
而且沉积的速度也很关键呢,太快了可能会导致薄膜不均匀,太慢了又会影响效率。
四、反应后的处理。
等反应结束了,可还没算完事儿呢。
还得对沉积好的东西进行处理。
就像是做完菜得装盘,还要稍微装饰一下一样。
要把它从反应室里取出来,然后可能要进行一些清洗呀,检测呀之类的操作。
清洗是为了把一些杂质去掉,检测就是看看这东西到底做得合不合格。
要是不合格,可能就得重新调整工艺,再做一次。
这就像是考试没考好,得重新复习再考一次一样。
CVD的工艺流程其实很复杂的,每一个小步骤都像是一颗小珠子,串起来才能成为一个漂亮的项链。
cvd碳化硅工艺流程

cvd碳化硅工艺流程CVD碳化硅工艺流程引言:CVD(化学气相沉积)碳化硅工艺是一种广泛应用于半导体行业的工艺,用于制备高纯度、高质量的碳化硅薄膜。
本文将介绍CVD碳化硅工艺的流程及其关键步骤。
一、前期准备在开始CVD碳化硅工艺之前,需要进行一系列的前期准备工作。
首先,选取合适的硅衬底,并进行表面清洁处理,以保证薄膜的质量。
其次,准备碳源和气体源,如甲烷(CH4)、硅源气体(SiH4)和稀释气体(如氢气)等。
此外,还需准备反应室、加热装置、气体供给系统等设备。
二、加载硅衬底在CVD碳化硅工艺中,首先将清洁处理过的硅衬底放置于反应室中,固定好位置。
硅衬底表面应尽量避免有杂质和氧化物,以免影响薄膜质量。
同时,反应室需要真空抽气,以确保后续反应的稳定性。
三、预热在加载硅衬底后,需要进行预热步骤。
预热的目的是提高反应室温度,使其达到适宜的反应温度。
通常,预热温度为600-900摄氏度,预热时间一般为10-30分钟。
预热过程中,还需将气体源和碳源预热至适宜的温度,以确保反应的均匀性。
四、反应预热完成后,开始注入碳源和气体源。
通常情况下,甲烷作为碳源,硅源气体作为主要的硅衬底源。
此外,还可以添加适量的稀释气体,如氢气,以调节反应的活性和薄膜的成分。
在反应过程中,需要控制气体流量和反应时间,确保反应的充分进行。
五、冷却反应完成后,需要将反应室冷却至室温。
冷却的过程中,需要保持反应室的真空状态,以避免薄膜受到空气中的污染。
冷却时间一般为10-30分钟。
在冷却过程中,也可以通过气体的流动来加速冷却。
冷却完成后,可以取出硅衬底,并进行后续的处理和测试。
六、后期处理CVD碳化硅工艺完成后,可以对薄膜进行后期处理和测试。
常见的后期处理包括退火、刻蚀、沉积其他材料等。
退火可以改善薄膜的结晶度和电学性能;刻蚀可用于制作器件结构;沉积其他材料可用于制备复合薄膜等。
此外,还可以通过各种测试手段对薄膜进行表征,如SEM(扫描电子显微镜)、XRD(X射线衍射)等。
半导体cvd工艺
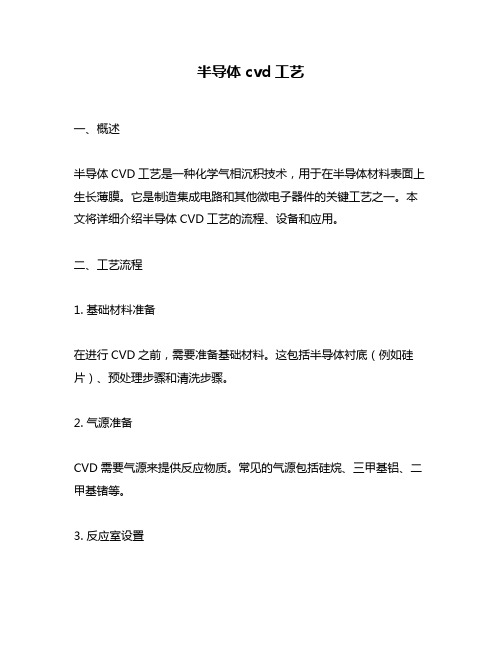
半导体cvd工艺一、概述半导体CVD工艺是一种化学气相沉积技术,用于在半导体材料表面上生长薄膜。
它是制造集成电路和其他微电子器件的关键工艺之一。
本文将详细介绍半导体CVD工艺的流程、设备和应用。
二、工艺流程1. 基础材料准备在进行CVD之前,需要准备基础材料。
这包括半导体衬底(例如硅片)、预处理步骤和清洗步骤。
2. 气源准备CVD需要气源来提供反应物质。
常见的气源包括硅烷、三甲基铝、二甲基锗等。
3. 反应室设置反应室是进行CVD反应的地方。
它通常由高温炉子和反应器组成。
在进行CVD反应之前,需要将反应器清洗干净,并将所需的气源送入反应室中。
4. 气态淀积层生长一旦所有材料和设备都准备就绪,就可以开始进行气态淀积层生长了。
在此过程中,所需的气源会被引入到高温反应室中,然后在半导体衬底表面上沉积一层薄膜。
5. 氧化在CVD过程结束后,需要进行氧化处理。
这通常包括将样品放入氧化炉中,在高温和高压下进行氧化反应。
这个步骤可以增强薄膜的质量和稳定性。
6. 后处理最后,需要进行后处理步骤,以确保薄膜的完整性和可靠性。
这可能包括清洗、退火或其他处理方法。
三、设备1. 反应器反应器是CVD工艺的核心部件。
它是一个密封的容器,用于将气源送入其中,并在高温下使其反应并沉积到半导体衬底上。
2. 气源系统气源系统用于将所需的气源输送到反应器中。
它通常由几个瓶子、阀门、流量计和管道组成。
3. 炉子炉子是用于加热反应器的设备。
它可以通过控制温度来控制CVD过程中的反应速率和沉积速率。
4. 气相分析仪气相分析仪用于监测CVD过程中产生的气体。
它可以帮助确定反应条件是否正确,并且可以检测到任何意外的气体泄漏。
5. 氧化炉氧化炉用于进行氧化处理,以增强薄膜的质量和稳定性。
它通常由一个密封的炉子和一个高温和高压的环境组成。
四、应用1. 集成电路制造CVD工艺是制造集成电路中各种元件所需的关键步骤之一。
它可以用于生长多种材料,包括二氧化硅、多晶硅、金属等。
cvd碳化钽工艺路线

cvd碳化钽工艺路线CVD碳化钽工艺路线引言:CVD碳化钽是一种高性能的材料,具有优异的耐热、耐腐蚀和高硬度特性。
其制备工艺路线是通过化学气相沉积(Chemical Vapor Deposition,简称CVD)的方法,在高温下使钽前驱体分解并沉积在基底上。
本文将介绍CVD碳化钽的工艺路线以及其制备过程中的关键步骤和注意事项。
一、前驱体选择在CVD碳化钽的制备过程中,选择合适的前驱体是非常重要的。
常用的前驱体有氯化钽和钽酸等,其中氯化钽是最常用的一种。
氯化钽易于蒸发,能够在高温下快速分解,生成碳化钽。
同时,选择适当的载气也是必要的,常用的载气有氢气和氩气等。
二、反应器和反应条件CVD碳化钽的制备需要一个稳定的反应器,并且需要控制好反应条件。
常见的反应器有石英管炉和石墨炉等。
在反应过程中,温度是一个关键参数。
通常,反应温度在1200℃至1500℃之间,不同的反应温度将会影响沉积速率和膜的结晶性能。
此外,反应压力、反应时间等参数也需要仔细控制。
三、基底处理在进行CVD碳化钽的制备前,需要对基底进行一系列的处理步骤。
首先,基底需要进行表面清洗,以去除表面的污染物和氧化层。
常用的清洗方法包括酸洗、超声波清洗等。
其次,为了增加碳化钽与基底的结合力,可以进行钨化或钽化等处理。
四、前驱体输送和分解在制备过程中,前驱体需要通过气体输送到反应器中,并在高温下分解。
通常采用氢气作为载气,通过气体流动将前驱体输送到反应器中。
在反应器中,前驱体分解产生的氮化物会与基底表面反应生成碳化钽。
五、膜的沉积和后处理在前驱体分解后,碳化钽会沉积在基底上形成薄膜。
薄膜的沉积速率和均匀性与反应条件有关。
通常,较高的温度和较长的反应时间可以获得较高的沉积速率。
在沉积完成后,还需要进行后处理步骤,例如退火处理,以提高膜的结晶性能和降低残余应力。
六、膜的性能测试为了评估CVD碳化钽薄膜的性能,需要进行一系列的测试。
常见的测试方法包括X射线衍射、扫描电镜等。
CVD的原理与工艺

CVD的原理与工艺CVD(化学气相沉积)是一种常用的薄膜制备技术,通过在高温条件下将气体衍生物在固体表面沉积形成薄膜。
它在半导体、光电子、材料科学等领域有着广泛的应用。
本文将介绍CVD的基本原理和常见的工艺流程。
CVD的基本原理是利用气体在固体表面发生化学反应产生固体沉积。
其过程可以简单概括为三个步骤:传输扩散、化学反应和沉积。
首先,在高温下,气体分子从气相传输到固相表面,这个过程称为传输扩散。
然后,在固体表面发生化学反应,气体分子与表面原子或分子发生物理或化学相互作用。
最后,与固体表面反应的产物发生聚集并沉积到固相表面上,形成薄膜。
CVD工艺可以分为四个主要组成部分:反应室、基底、前驱物和载气。
反应室是进行反应的容器,通常由高温和高真空环境下的材料制成。
基底是待沉积薄膜的衬底,可以是玻璃、硅等多种材料。
前驱物是产生沉积薄膜的化学物质,通常是气态或液态的。
载气是用来稀释前驱物的气体,使其在反应室中更均匀地传输。
CVD的工艺流程是在反应室中将前驱物供应和载气送入,通过传输扩散和化学反应后,形成薄膜并覆盖在基底上。
根据前驱物供应的方式和反应室的特点,CVD可以分为几个常见的工艺类型。
最常见的是热CVD,也称为低压CVD(LPCVD)。
在低压下,前驱物和气体通过加热传输到反应室中,沉积在基底上。
这种方法适用于高温下的材料制备,例如多晶硅、氮化硅等。
另一种常见的是PECVD(等离子体增晶体化学气相沉积)。
在PECVD 中,通过产生等离子体来激活前驱物的化学反应。
在等离子体的作用下,前驱物转化为离子和活性物种,进一步在基底上反应形成薄膜。
这种方法适用于制备非晶硅、氮化硅等。
还有一种CVD工艺称为MOCVD(金属有机化学气相沉积)。
在MOCVD 中,金属有机化合物作为前驱物供应,经氢气或氨气稀释。
通过热解和化学反应,金属有机前驱物转化为金属原子和活性物种,在基底上形成薄膜。
这种方法适用于制备复杂的金属氧化物、尖晶石等。
cvd真空镀膜工艺流程
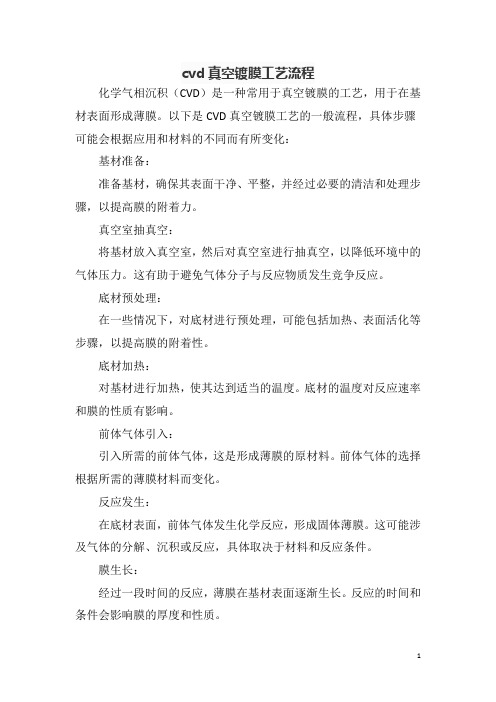
cvd真空镀膜工艺流程
化学气相沉积(CVD)是一种常用于真空镀膜的工艺,用于在基材表面形成薄膜。
以下是CVD真空镀膜工艺的一般流程,具体步骤可能会根据应用和材料的不同而有所变化:
基材准备:
准备基材,确保其表面干净、平整,并经过必要的清洁和处理步骤,以提高膜的附着力。
真空室抽真空:
将基材放入真空室,然后对真空室进行抽真空,以降低环境中的气体压力。
这有助于避免气体分子与反应物质发生竞争反应。
底材预处理:
在一些情况下,对底材进行预处理,可能包括加热、表面活化等步骤,以提高膜的附着性。
底材加热:
对基材进行加热,使其达到适当的温度。
底材的温度对反应速率和膜的性质有影响。
前体气体引入:
引入所需的前体气体,这是形成薄膜的原材料。
前体气体的选择根据所需的薄膜材料而变化。
反应发生:
在底材表面,前体气体发生化学反应,形成固体薄膜。
这可能涉及气体的分解、沉积或反应,具体取决于材料和反应条件。
膜生长:
经过一段时间的反应,薄膜在基材表面逐渐生长。
反应的时间和条件会影响膜的厚度和性质。
冷却和清洗:
完成反应后,停止前体气体的供应,冷却基材。
有时可能需要进行清洗步骤,以去除表面残留的杂质。
真空室回气:
允许气体重新进入真空室,准备取出镀膜好的基材。
膜质量检测:
对形成的膜进行质量检测,可能包括厚度测量、表面形貌分析等。
这只是CVD真空镀膜的一般流程,。
CVD的原理与工艺

CVD的原理与工艺CVD是化学气相沉积的缩写,是一种重要的薄膜制备工艺。
其原理是通过化学反应在基板表面沉积出所需的薄膜。
CVD工艺具有高温、通用性、高产率等优点,被广泛应用于半导体、光电子、材料科学等领域。
CVD工艺的原理主要涉及三个基本过程:传输过程、反应过程和沉积过程。
传输过程是指气相中物质在反应室中的输送和混合过程。
反应过程是指气相中物质发生化学反应的过程。
沉积过程是指反应生成物在基板表面的吸附和成膜过程。
CVD工艺的实施基础是高温条件下反应气体中的化学反应。
通常,CVD工艺需要在几百摄氏度到几千摄氏度的高温下进行。
高温条件下,反应气体中的分子活性增加,促使反应发生。
此外,高温条件下也有利于沉积物的生长和晶格匹配。
CVD工艺中常用的气体有两种类型:反应物气体和载体气体。
反应物气体是指与基板表面发生化学反应的气体,可以是纯净气体或有机金属(如金属有机化合物)。
载体气体是指将反应物气体输送到反应室中,并稀释以便控制反应速率和成膜均匀性的气体。
常用的载体气体有氢气、氮气、氩气等。
具体而言,CVD工艺的实施过程可以分为以下几个步骤:1.反应物气体输送:反应物气体通常通过质量流控制器控制流量,并由气体输送系统输送到反应室中。
2.传输与混合:反应物气体进入反应室后,通过传输与混合过程,与载体气体充分混合,形成气相反应体系。
3.化学反应:在高温条件下,混合的反应气体在反应器中发生化学反应。
这些化学反应通常是复杂的多步骤反应,生成物在气相中。
4.吸附与扩散:生成物与基板表面发生吸附和扩散,使得沉积物开始形成。
5.成膜和生长:沉积物在基板表面不断生长,并形成所需的薄膜。
CVD工艺的成功实施需要考虑许多因素。
其中,关键的因素包括:反应温度、反应气体浓度、反应压力、基板表面状态等。
这些因素直接影响了沉积物的结构、性能和均匀性。
为了实现理想的薄膜沉积,CVD工艺还需要进行流程优化和参数调控。
通过控制反应条件、改变反应气体浓度和流量,以及调整基板表面状态,可以实现不同结构和性能的沉积物。
CVD工艺原理及设备介绍
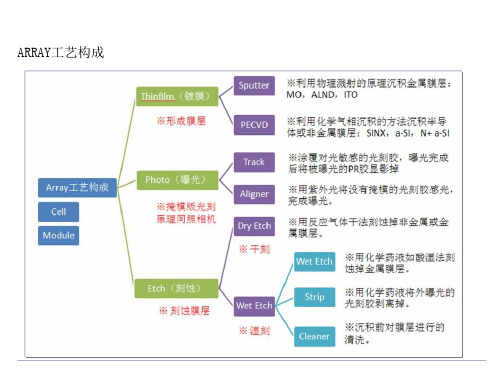
1.CVD的介 绍
一种利用化学反应方式,将反应物(气体)生成固态的产物,并 沉积在基片表面的薄膜沉积技术. 如可生成: 导体: W(钨)等; 半导体:Poly-Si(多晶硅), 非晶硅等; 绝缘体(介电材质): SiO2, Si3N4等.
2.PECVD的介绍
为了使化学反应能在较低的温度下进行, 利用了等离子体的活 性来促进反应, 因而这种CVD称为等离子体增强化学气相沉积 (PECVD).
6. 绝缘膜、有源膜成膜机 理
(1) SiNX绝缘膜: 通过SiH4与NH3混合气体作为反应气体, (2) 辉光放电生成等离子体在衬底上成膜。
(3) a-Si:H有源层膜: SiH4气体在反应室中通过辉光放电,经 过一系列初级、次级反应,生成包括离子、子活性团等较 复杂的反应产物,最终生成a-Si:H薄膜沉积在衬底上,其 中直接参与薄膜 生长的主要是一些中性产物SiHn(n为0~ 3)
➢ 4个Cassette Stage:A,B,C,D(向外从左向右) ➢ 层流净化罩(Laminar Flow Hood):Class 10 ➢ 最大能力:24(目前20 Slot/Cassette) ➢ Light Curtain(红外线):防止设备自动进行时有人接近 Stage ➢ 设备状态指示器
Lid Cart
Process Chamber要在必须的真空和温度环境下 打开Slit阀门
真空机械手end-effector把在Lift Pins上的 玻璃放进 process chamber以及缩回后放进transfer chamber slit阀关闭及密封 susceptor举起玻璃偏离lift pins而放之于 diffuser下方 工艺气体和射频能量打开, 产生等离子体通过 diffuser到达process chamber. 想要的材料沉积在玻璃上 susceptor按需要上升或下降到达必要的电极距
cvd连续硅渗碳工艺技术

cvd连续硅渗碳工艺技术
连续硅渗碳工艺技术(Continuous Silicon Infiltration Carbon,CVD-SiC)是一种通过化学气相沉积(Chemical Vapor Deposition,CVD)方法制备的连续硅渗碳材料的工艺技术。
CVD-SiC工艺技术的基本步骤如下:
1. 基材准备:选择适当的基材,通常使用聚合物泡沫或陶瓷纤维作为基材。
2. 气相反应:将基材放置在反应室中,通过控制温度和流量,使硅源气体与基材表面反应生成硅烷等气体。
3. 渗透和沉积:由于反应室中温度较高,硅烷等气体在基材表面分解,释放出纯硅,并渗透到基材内部,同时生成碳化硅。
4. 冷却和固化:将基材从反应室中取出后,通过冷却使硅渗碳材料固化。
5. 后处理:可进行各种后处理工艺,如研磨、打磨、烧结等,以获得所需的硅渗碳材料的性能。
CVD-SiC工艺技术具有以下特点:
1. 连续性:由于是在连续的反应室中进行沉积和渗透过程,因此可以制备大尺寸和复杂形状的硅渗碳材料。
2. 高纯度:通过精确控制反应条件和纯度高的硅源气体,可以得到高纯度的硅渗碳材料。
3. 均匀性:由于反应室中温度、压力和气体流动都能够得到良好控制,因此可以制备均匀的硅渗碳材料。
4. 可调性:通过调整反应条件,如温度和气体流量,可以调控硅渗碳材料的性能,如密度、硬度等。
CVD-SiC工艺技术广泛应用于高温、耐腐蚀、高强度、高刚度等领域,如航空航天、能源、化工、电子等。
它可以制备出具有优异性能的硅渗碳材料,满足不同领域的需求。
cvd纳米金刚石涂层工艺流程

CVD纳米金刚石涂层工艺流程一、概述CVD (化学气相沉积)纳米金刚石涂层工艺是一种先进的表面涂层技术,通过在基材表面沉积纳米级厚度的金刚石薄膜,可以显著提高材料的硬度、耐磨性和耐腐蚀性。
本文将详细介绍CVD纳米金刚石涂层的工艺流程,包括材料选择、表面处理、沉积工艺、质量控制等环节。
二、材料选择1. 基材材料:金属、陶瓷、塑料等材料均可用于CVD纳米金刚石涂层。
常用的基材包括硬质合金、不锈钢、钛合金等。
2. 基材形状:CVD纳米金刚石涂层工艺适用于各种形状的基材,包括平板、管材、复杂形状零件等。
3. 表面粗糙度:基材表面粗糙度对涂层的质量有重要影响,一般要求基材表面粗糙度在Ra<0.4um。
三、表面处理1. 清洗:将基材进行去油、除尘、去氧化处理,以保证涂层与基材之间的良好结合。
2. 粗糙化处理:对于一些表面平整的基材,可以采用砂喷或喷丸处理,增加表面粗糙度,有利于涂层附着。
3. 防粘接处理:在表面处理之后,可以在基材表面进行一些特殊的处理,以增强涂层与基材之间的黏附力。
四、CVD纳米金刚石涂层工艺1. 基材预热:将基材置于CVD反应室中进行预热,通常温度在800-1000摄氏度之间。
2. 气氛控制:在反应室中控制好气氛,通常使用氢气和甲烷混合气体,通过精确控制气氛比例和流量来控制沉积速率和涂层质量。
3. 沉积过程:在预热后的基材表面开始沉积金刚石薄膜,通过化学气相反应在基材表面沉积碳原子,形成金刚石晶粒,不断沉积形成厚度可控的金刚石薄膜。
4. 控制工艺参数:沉积过程中需要严格控制温度、压力、气氛比例、沉积时间等工艺参数,以确保获得高质量的纳米金刚石涂层。
五、质量控制1. 涂层厚度检测:使用X射线衍射仪、激光剥蚀仪等设备对涂层厚度进行检测。
2. 显微结构分析:通过光学显微镜、扫描电子显微镜等设备对涂层显微结构进行分析。
3. 涂层性能测试:对涂层的硬度、耐磨性、耐腐蚀性等性能进行测试,确保涂层符合要求。
CVD工艺介绍

高温SiO2(掺杂或不 掺杂)、Si3N4、多 晶硅、W、WSi2
等离子体辅助CVD
等离子体增强 CVD(PECVD) 高密度等离子体 CVD(HDPCVD)
低温,快速淀积, 好的台阶覆盖能力, 好的间隙填充能力
要求RF系统,高成 本,压力远大于张 力,化学物质(如 H2)和颗粒沾污
高的深度比间隙的填 充,金属上的低温 SiO2,ILD-1,ILD,为 了双镶嵌结构的铜籽 晶层,钝化(Si3N4)
4.6 CMP 的作用效果
Pre-CMP
During CMP
Post-CMP
The pressure of high step area is much bigger , so the remove rate is much higher , that makes surface global planarity when CMP a long time .
4.3 SOG 工艺过程
SOG工艺过程,分为旋涂,热板烘焙,退火三个步骤。
SOG平坦化工艺流程一般采用三明治结构,即由两层CVD法淀积的SiO2膜包夹着SOG膜。
其一般分为有回刻和无回刻两种方法。
PECVD SiO2 阻挡层
旋转涂布211液(SOG) SOG 固化 SOG 回蚀 PECVD SiO2 覆盖层
Step Height: IMD1 CMP Pre - Center SEM Bar
10000 9000 8000 7000 6000 5000 4000 3000 2000 1000 0 1
196 391 586 781 976 1171 1366 1561 1756 1951 2146
Step Height: IMD1 CMP Post - Center SEM Bar
光伏cvd工艺
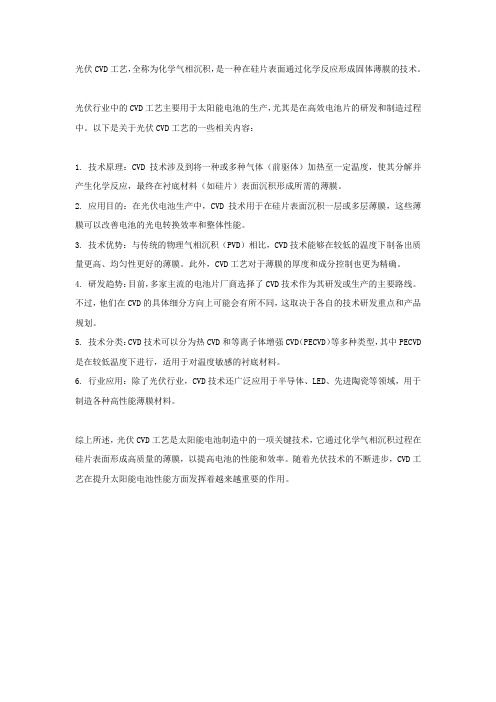
光伏CVD工艺,全称为化学气相沉积,是一种在硅片表面通过化学反应形成固体薄膜的技术。
光伏行业中的CVD工艺主要用于太阳能电池的生产,尤其是在高效电池片的研发和制造过程中。
以下是关于光伏CVD工艺的一些相关内容:
1. 技术原理:CVD技术涉及到将一种或多种气体(前驱体)加热至一定温度,使其分解并产生化学反应,最终在衬底材料(如硅片)表面沉积形成所需的薄膜。
2. 应用目的:在光伏电池生产中,CVD技术用于在硅片表面沉积一层或多层薄膜,这些薄膜可以改善电池的光电转换效率和整体性能。
3. 技术优势:与传统的物理气相沉积(PVD)相比,CVD技术能够在较低的温度下制备出质量更高、均匀性更好的薄膜。
此外,CVD工艺对于薄膜的厚度和成分控制也更为精确。
4. 研发趋势:目前,多家主流的电池片厂商选择了CVD技术作为其研发或生产的主要路线。
不过,他们在CVD的具体细分方向上可能会有所不同,这取决于各自的技术研发重点和产品规划。
5. 技术分类:CVD技术可以分为热CVD和等离子体增强CVD(PECVD)等多种类型,其中PECVD 是在较低温度下进行,适用于对温度敏感的衬底材料。
6. 行业应用:除了光伏行业,CVD技术还广泛应用于半导体、LED、先进陶瓷等领域,用于制造各种高性能薄膜材料。
综上所述,光伏CVD工艺是太阳能电池制造中的一项关键技术,它通过化学气相沉积过程在硅片表面形成高质量的薄膜,以提高电池的性能和效率。
随着光伏技术的不断进步,CVD工艺在提升太阳能电池性能方面发挥着越来越重要的作用。
cvd镀膜工艺

cvd镀膜工艺哎呀,说起CVD镀膜工艺,这玩意儿可真是个技术活儿,跟咱们平时做饭差不多,只不过咱们用的是锅碗瓢盆,他们用的是各种高大上的仪器和化学品。
不过别急,我这就给你细细道来。
首先,CVD,全名叫化学气相沉积,听着挺玄乎的,其实就是把一堆气体扔到一起,让它们发生化学反应,最后在基底上形成一层薄膜。
这层膜啊,可不简单,它得有金刚不坏之身,耐磨、耐腐蚀,还得能反射光,或者透光,总之得有特殊功能。
咱们先说说这个“扔气体”的过程。
想象一下,你把一堆面粉、糖、鸡蛋和牛奶混在一起,然后搅拌搅拌,最后放到烤箱里烤,出来的就是蛋糕。
CVD镀膜也差不多,不过咱们用的不是面粉,而是一些特制的气体,比如甲烷、氢气、氮气之类的。
好了,现在咱们来聊聊这个“搅拌搅拌”的过程。
在实验室里,这些气体会被送进一个真空室,里面有个加热的基底,比如硅片。
然后,这些气体就会在基底上发生化学反应,形成一层薄膜。
这个过程有点像你在锅里炒菜,火候得控制好,不然要么糊了,要么不熟。
说到火候,CVD工艺中的温度控制可是关键。
温度太高,气体反应太快,膜层质量就差;温度太低,反应太慢,膜层就长不出来。
所以,工程师们得像大厨一样,精准控制火候,才能做出完美的“菜”。
接下来,咱们得聊聊这层膜的厚度。
这就像你做蛋糕,面糊倒多了,蛋糕就厚;倒少了,蛋糕就薄。
在CVD过程中,薄膜的厚度可以通过控制气体的流量和反应时间来调节。
工程师们得像艺术家一样,精心设计,才能得到理想的厚度。
最后,咱们得说说这层膜的用途。
比如,它可以用于太阳能电池板,提高光能转换效率;也可以用于半导体芯片,提高电子器件的性能。
这就像你做的蛋糕,可以当早餐,也可以当下午茶。
总之,CVD镀膜工艺就像是一场科学和艺术的盛宴,需要精确的控制和巧妙的设计。
虽然听起来很复杂,但只要掌握了其中的门道,就能做出既实用又美观的薄膜。
就像咱们做饭一样,多练习,多尝试,总会有进步的。
- 1、下载文档前请自行甄别文档内容的完整性,平台不提供额外的编辑、内容补充、找答案等附加服务。
- 2、"仅部分预览"的文档,不可在线预览部分如存在完整性等问题,可反馈申请退款(可完整预览的文档不适用该条件!)。
- 3、如文档侵犯您的权益,请联系客服反馈,我们会尽快为您处理(人工客服工作时间:9:00-18:30)。
NH3在过量的情况下,HCl与NH3继续反应:HCl+ NH3 = NH4Cl
合并为:10NH3+ 3SiH2Cl2 = Si3N4 + 6H2 + 6NH4Cl
目前我们生产使用的温度是780℃,压力为375mt。
在VLSL工艺中,由于沿器件有源区方向上的场氧侵蚀和场注入杂质的横向扩散,使得LOCOS工艺受到很大的限制,场氧的横向侵蚀使LOCOS氧化层和栅氧的交界面形成类似鸟嘴的结构,随着工艺条宽的不断减少,鸟嘴的大小必须加以控制,而SI3N4与硅之间的应力很大,为了避免对硅表面的应力损伤,在硅表面与SI3N4膜之间插入一层薄的SIO2作为应力缓冲层。因此我们常用的方法是通过改变SIN与二氧的厚度比来减少鸟嘴大小,其中鸟头的高度和鸟嘴的宽度与SI3N4的厚度成反比,与应力缓冲层SIO2的厚度成正比。一般来说该比例越大,鸟嘴越小,但比例过大又影响到硅岛侧壁和表面的缺陷密度而引起漏
二、低压化学气相淀积Si3N4
LP Si3N4在工艺中主要作为局部氧化的掩蔽膜,电容的介质膜等。CMOS工艺最常用的隔离技术就是LOCOS(硅的选择氧化),它以氮化硅为掩膜实现了硅的选择氧化,在这种工艺中除了形成有源晶体管的区域外,其他所有重掺杂硅区上均生长一层厚的氧化层,该厚氧化层通常称为场氧。在工艺中我们通常使用的气体是:NH3+ DCS(SiH2Cl2)。这两种气体的反应生成的Si3N4质量高,副产物少,膜厚均匀性极佳,而且是气体源便于精确控制流量,是目前国内外普遍采用的方法。
间的距离,可以很小,那是因为这个系统是操作在表面反应速率限制的模式下。
在低压化学气相沉积法的反应器中,反应压力
約为
1
托耳以下,在此压力下,反应物气体的扩散系数约为在常压下的一千倍,而这是部份由于压力降低的平方根的调整,因
此这净效应是反应物传输至基板表面的速率增加超过十倍,所以速率限制步骤是表面反应。通常表面反应速率会随著表面反应
物浓度的增加而增加,及气相浓度分布不均匀而增加。而这气相浓度不均匀是因为某处反应物被空乏掉所造成的,举一个例子
說明这个效应,当晶片被放置在靠反应物的出气端時,因而曝露在较低的反应物浓度环境中,比进气端低许多,而造成炉管的
前后端沉积的厚度不均匀,因此为了沉积薄膜的均匀性,在反应炉管的前后两端,沉积的温度必须正确的调整。
一般而言,因为化学气相沉积的制程,包含了热的传达、边界层的扩散
(boundary-layer diffusion)
,吸附于基板表面,
反应物分解、表面扩散、副产物脱离表面等许多步骤,所以有很多个参数会影响沉积作用,如反应温度、压力、反应物流量、
晶片摆置的位置和反应物的混合比例都是对是否能沉积出高品质的薄膜非常重要的因素。因为上述的化学气相沉积制程的几个
b.多晶硅薄膜的电学性质:多晶硅的电阻率或薄层电阻随淀积温度的增加而降低。多晶硅的电阻率随厚度增加而明显减少,而外延单晶硅的电阻率与厚度无关。
★多晶的淀积:600℃-700℃
化学反应式为:SiH4------------- Si + 2H2270MT
影响淀积的主要工艺参量是温度,硅烷流量及反应压力。
的反应物流量,因此沉积二氧化硅的常压反应器,操作温度約为
400℃,是落在物质传输限制的区域,所以被应用的反应器设计
是水平摆置晶片的方式,以提供一均匀的气体供应。
五、
LPCVD
工艺控制
5.1
拉恒温区控制温度
定期拉恒温区以得到好的温度控制,保证炉管内各处的生长速率趋向平衡,基本上我们安排一个月拉一次恒温,每
入会令多晶侧壁损伤,
因此我们经常使用
LDD
注入和
SPACER
层保护来减少短沟道效应的影响和对多晶侧壁的损伤,
具体步骤为:
1
,在源,漏注入前先进行
LDD
注入,通常注入浓度为
10E+13
,
2
然后淀积一层
LPTEOS,Βιβλιοθήκη 3去TEOS
,由于台阶的影响,会在多晶
侧壁保留有一层
TEOS
,将起到保护的作用,
3
再开出源,漏的窗口,进行源,漏注入(浓度一般为
电等不良后果。处于不同工艺要求的考虑,不同公司有各自的做法。我们公司最常用的搭配有:200A的氧化层+ 1175A SIN和400A的氧化层+ 1500A SIN,还有很多其他减少鸟嘴大小的办法,例如隔离槽填充等。
二、低压淀积多晶硅(LPPOLY)
20世纪60年代作为初期生产的铝栅MOSFET,它的速度,集成度,电源电压,与双极电路的兼容性都已无法满足应用的需要,因此开始使用多晶硅薄膜作为自对准绝缘栅场效应晶体管的栅极材料和互连材料。随着集成电路的发展,多晶的应用也越来越广,如用于差值氧化以简化工艺流程;用于负载电阻以缩小电路单元等等。
★多晶硅薄膜的特性:
a.多晶硅薄膜的物理和机械特性:多晶硅的结构与掺杂剂或杂质,淀积温度及随后的热处理等因素有密切关系。低于575℃所淀积的硅是无定形非晶硅;高于625℃淀积的硅是多晶,具有针状结构;当非晶或针状结构多晶硅经高温退火后,会产生结晶,同时晶粒要长大。多晶硅的晶粒大小与生长温度,多晶硅膜厚及掺杂情况有关。在600℃-650℃之间淀积的多晶硅,具有针状结构,晶粒尺寸在0.03至0.3UM之间,具有{110}晶向。多晶硅的腐蚀速率及热氧化速率与掺杂剂浓度有关,腐蚀及氧化的反应速率由掺杂多晶硅的表面自由载流子浓度有关。
步骤是连续的,那个步骤是最慢的速率,将会決定此化学气相沉积的速率,亦即是速率決定步骤。速率決定步骤,一般可分成
两大类,一类是气相质量输运
(gas-phase process)
,另一类是表面反应
(surface process)
。
对于气相质量输运最主要的考量
点是反应气体撞击到基板。这个模型要考虑气体横越过边界层
(boundary-layer)
的速度。而此边界层就是气体大量流动和基板
表面之间的范围。反应物的传输过程是藉著气相的扩散来达成,而此气相扩散的速率,正比于扩散系数和横越此边界层的的浓
度梯度
(concentration gradient)
。因此物质传输的速率受沉积温度的影响比较小。另外一方面,在比较低的沉积温度時,表
★
目前
VTR-2
和
C-3
设备上淀积多晶的条件:
a.
淀积温度:由于
LPPOLY
的淀积温度限制在
600
℃
-650
℃之间,因为温度过高,气相反应会生成粗糙,
疏松的沉积物,并可能由于硅烷的输送不足,使淀积不均匀。在温度低于
600
℃时形成的为无定形硅。
多晶膜厚随温度的变化较敏感,
VTR-2
上每变化
1
℃膜厚约变化
c.
反应压力:多晶硅的淀积速率随反应压力的增加而加大。目前
VTR-2
上淀积
多
晶的反应压力为
200MT,C-3
上淀积多晶的反应压力为
270MT
。
三、
低压沉积
TEOS
LP TEOS
主要用于
SPACER
层及电容氧化层。
在工艺中,由于注源,漏时杂质的横向扩散会产生短沟道效应,使
MOS
管的开启电压产生变化,而且会使高能量的离子注
能保持固定沉积速率的条件,也就是說,在任何地方,任一片晶片上的表面温度必须保持固定。此外,在这个情況下,反应物
到达晶片表面的速度就不是非常重要,因为它们的浓度不会限制沉积的速率,因此它的反应器的设计就不是那么必要设计成能
在每一片晶片上有相等的反应物流量。因此我们可以看出在低压化学气相沉积系统中,欲沉积的晶片可以垂直摆置而片与片之
10E+15
)
。
我们在工艺时使用的气体为
TEOS
也就是
Si
(
O C
2
H
5
)
4
学名正硅酸乙脂,又称四乙氧基硅烷,常温下为液态,由携带气
体
N2
带入炉管内,
TEOS
分压及流量分别由
TEOS
源瓶的温度及通过源瓶的小
N2
流量来控制。
Si
(
O C
2
H
5
)
4
→
SiO
2
+4C
2
H
4
+2H
2
O
四、
LPCVD
工艺参数
沉积的影响参数
于因在表面反应所消耗的,在这种沉积情況下,就称为物质传输限制
(mass-transport limited)
。在实际的制程中,从一种限
制区域到另外一种限制区域的温度決定于这个反应的活化能
(activation energy)
和在反应器內反应物的流量。
一个制程当它
是在表面反应速率限制的条件下,沉积的温度就是一个很重要的参数,要在整个反应器內有一很均匀的沉积速率,需要有一个
.1 LPCVD(低压CVD)
一、LPCVD工艺简介
LPCVD(Low Pressure Chemical Vapor Deposition):低压气相淀积,是在27-270Pa的反应压力下进行的化学气相淀积。它的特点是:膜的质量和均匀性好,产量高,成本低,易于实现自动化。
一般工艺流程:装片——进舟——对反应室抽真空——检查设备是否正常——充N2吹扫并升温——再抽真空——保持压力稳定后开始淀积——关闭所有工艺气体,重新抽真空——回冲N2到常压——出炉。
100A
左右。生长速率约
94A/min
。
C-3
上三温区的淀积速率都为