一般工程与结构用铸钢件的技术要求
钢结构零件及部件加工技术要求

钢结构零件及部件加工技术要求一、一般要求1.1 本技术要求适用于钢结构制作中零件及部件的加工。
1.2 零件及部件加工前,应熟悉设计文件和施工详图,应做好各道工序的工艺准备;并应结合加工的实际情况,编制加工工艺文件。
二、放样和号料2.1 放样和号料应根据施工详图和工艺文件进行,宜按实际材料尺寸采用全排版,并应按要求预留余量。
2.2 放样和样板(样杆)的允许偏差应符合表2.2的要求。
表2.2 放样和样板(样杆)的允许偏差2.3 号料的允许偏差应符合表2.3的要求。
表2.3 号料的允许偏差(mm)2.4 主要零件应根据构件的受力特点和加工状况,按工艺要求的方向进行号料。
2.5 号料后,零件和部件应按施工详图和工艺要求进行标识。
三、切割3.1 钢材切割可采用气割、机械切割、等离子切割等方法,选用的切割方法应满足工艺文件的要求。
切割后的飞边、毛刺应清理干净。
3.2 钢材切割面应无裂纹、夹渣、分层等缺陷和大于1mm的缺棱。
3.3 气割前钢材切割区域表面应清理干净。
切割时,应根据设备类型、钢材厚度、切割气体等因素选择适合的工艺参数。
3.4 气割的允许偏差应符合表3.4的要求。
表3.4 气割的允许偏差(mm)3.5 机械剪切的零件厚度不宜大于12.0mm,剪切面应平整。
碳素结构钢在环境温度低于-20℃、低合金结构钢在环境温度低于-15℃时,不得进行剪切、冲孔。
3.6 机械剪切的允许偏差应符合表3.6的要求。
表3.6 机械剪切的允许偏差(mm)3.7 钢网架(桁架)用钢管杆件宜用管子车床或数控相贯线切割机下料,下料时应预放加工余量和焊接收缩量,焊接收缩量可由工艺试验确定。
钢管杆件加工的允许偏差应符合表3.7的要求。
表3.7 钢管杆件加工的允许偏差(mm)注:r为管半径四、矫正和成型4.1 矫正可采用机械矫正、加热矫正、加热与机械联合矫正等方法。
4.2 碳素结构钢在环境温度低于-16℃、低合金结构钢在环境温度低于-12℃时,不应进行冷矫正和冷弯曲。
铸件技术要求
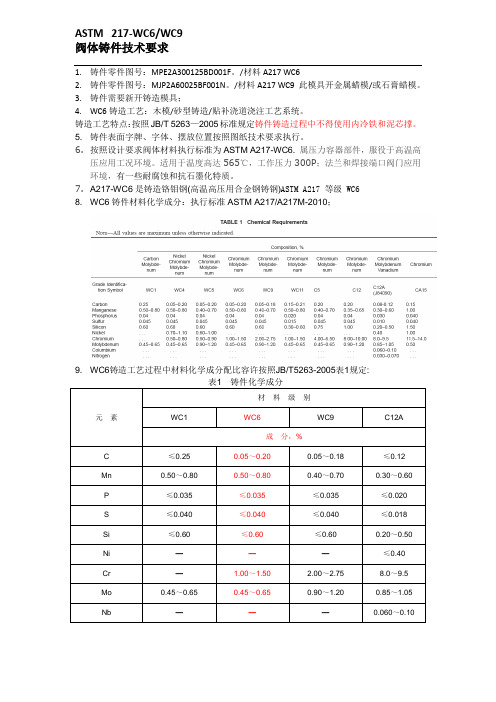
1.铸件零件图号:MPE2A300125BD001F。
/材料A217 WC62.铸件零件图号:MJP2A60025BF001N。
/材料A217 WC9 此模具开金属蜡模/或石膏蜡模。
3.铸件需要新开铸造模具;4.WC6铸造工艺:木模/砂型铸造/贴补浇道浇注工艺系统。
铸造工艺特点:按照JB/T 5263—2005标准规定铸件铸造过程中不得使用内冷铁和泥芯撑。
5. 铸件表面字牌、字体、摆放位置按照图纸技术要求执行。
6.按照设计要求阀体材料执行标准为ASTM A217-WC6.属压力容器部件,服役于高温高压应用工况环境。
适用于温度高达565℃,工作压力300P;法兰和焊接端口阀门应用环境,有一些耐腐蚀和抗石墨化特质。
7.A217-WC6是铸造铬钼钢(高温高压用合金钢铸钢)ASTM A217 等级 WC68. WC6铸件材料化学成分:执行标准ASTM A217/A217M-2010;9. WC6铸造工艺过程中材料化学成分配比容许按照JB/T5263-2005表1规定:10. 化学成分及机械性能见表211. WC6/WC9铸钢铸态正常金相组织为雾状铁素体(有钒的碳化物沉淀)+珠光体。
12. WC6/WC9铸钢经规范热处理(正火+回火)后正常金相显微组织为珠光体。
13. 由于WC6铸钢与我国铸钢牌号ZG15CrMoV基本相近似,容许按照中国牌号ZG15CrMoV标准要求铸造。
14. 对WC6/ZG15CrMoV铸钢的铸造工艺性偏稍差,铸造时自由线收缩率约为2.2~2.5%。
由于钢的导热系数较低,因此在凝固过程中容易产生热裂倾向,在切除浇冒口过程中又容易产生冷裂,在铸造工艺过程中应引起高度重视。
15. WC6根据铸件形状结构设计要求,铸件壁厚不均匀,铸件最薄处壁厚尺寸应>13mm。
16. WC6铸件须附铸化学成分/力学性能试验试块试棒,试块容许从铸件浇道上采取。
试棒尺寸为Φ40×150;2件,无铸造缺陷。
一般技术要求
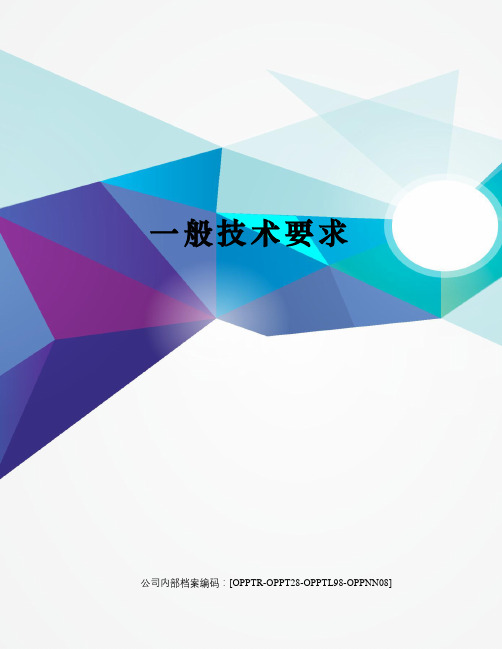
一般技术要求公司内部档案编码:[OPPTR-OPPT28-OPPTL98-OPPNN08]一般技术要求1.零件去除氧化皮.2.零件加工表面上,不应有划痕、擦伤等损伤零件表面(de)缺陷.3.去除毛刺飞边.热处理要求4.经调质处理,HRC50~55.5.零件进行高频淬火,350~370℃回火,HRC40~45.6.渗碳深度.7.进行高温时效处理.公差要求8.未注形状公差应符合GB1184-80(de)要求.9.未注长度尺寸允许偏差±.10.铸件公差带对称于毛坯铸件基本尺寸配置.零件棱角11.未注圆角半径R5.12.未注倒角均为2×45°.13.锐角/尖角/锐边倒钝.装配要求14.各密封件装配前必须浸透油.15.装配滚动轴承允许采用机油加热进行热装,油(de)温度不得超过100℃.20.齿轮装配后,齿面(de)接触斑点和侧隙应符合GB10095和GB11365(de)规定.21.装配液压系统时允许使用密封填料或密封胶,但应防止进入系统中.22.进入装配(de)零件及部件(包括外购件、外协件),均必须具有检验部门(de)合格证方能进行装配.23.零件在装配前必须清理和清洗干净,不得有毛刺、飞边、氧化皮、锈蚀、切屑、油污、着色剂和灰尘等.24.装配前应对零、部件(de)主要配合尺寸,特别是过盈配合尺寸及相关精度进行复查.25.装配过程中零件不允许磕、碰、划伤和锈蚀.26.螺钉、螺栓和螺母紧固时,严禁打击或使用不合适(de)旋具和扳手.紧固后螺钉槽、螺母和螺钉、螺栓头部不得损坏.27.规定拧紧力矩要求(de)紧固件,必须采用力矩扳手,并按规定(de)拧紧力矩紧固.28.同一零件用多件螺钉(螺栓)紧固时,各螺钉(螺栓)需交叉、对称、逐步、均匀拧紧.29.圆锥销装配时应与孔应进行涂色检查,其接触率不应小于配合长度(de)60%,并应均匀分布.30.平键与轴上键槽两侧面应均匀接触,其配合面不得有间隙.31.花键装配同时接触(de)齿面数不少于2/3,接触率在键齿(de)长度和高度方向不得低于50%.32.滑动配合(de)平键(或花键)装配后,相配件移动自如,不得有松紧不均现象.33.粘接后应清除流出(de)多余粘接剂.34.轴承外圈与开式轴承座及轴承盖(de)半圆孔不准有卡住现象.35.轴承外圈与开式轴承座及轴承盖(de)半圆孔应接触良好,用涂色检查时,与轴承座在对称于中心线120°、与轴承盖在对称于中心线90°(de)范围内应均匀接触.在上述范围内用塞尺检查时,(de)塞尺不得塞入外圈宽度(de)1/3.36.轴承外圈装配后与定位端轴承盖端面应接触均匀.37.滚动轴承装好后用手转动应灵活、平稳.38.上下轴瓦(de)结合面要紧密贴和,用塞尺检查不入.39.用定位销固定轴瓦时,应在保证瓦口面和端面与相关轴承孔(de)开合面和端面包持平齐状态下钻铰、配销.销打入后不得松动.40.球面轴承(de)轴承体与轴承座应均匀接触,用涂色法检查,其接触不应小于70%.41.合金轴承衬表面成黄色时不准使用,在规定(de)接触角内不准有离核现象,在接触角外(de)离核面积不得大于非接触区总面积(de)10%.42.齿轮(蜗轮)基准端面与轴肩(或定位套端面)应贴合,用塞尺检查不入.并应保证齿轮基准端面与轴线(de)垂直度要求.43.齿轮箱与盖(de)结合面应接触良好.44.组装前严格检查并清除零件加工时残留(de)锐角、毛刺和异物.保证密封件装入时不被擦伤.铸件要求45.铸件表面上不允许有冷隔、裂纹、缩孔和穿透性缺陷及严重(de)残缺类缺陷(如欠铸、机械损伤等).46.铸件应清理干净,不得有毛刺、飞边,非加工表明上(de)浇冒口应清理与铸件表面齐平.47.铸件非加工表面上(de)铸字和标志应清晰可辨,位置和字体应符合图样要求.48.铸件非加工表面(de)粗糙度,砂型铸造R,不大于50μm.49.铸件应清除浇冒口、飞刺等.非加工表面上(de)浇冒口残留量要铲平、磨光,达到表面质量要求.50.铸件上(de)型砂、芯砂和芯骨应清除干净.51.铸件有倾斜(de)部位、其尺寸公差带应沿倾斜面对称配置.52.铸件上(de)型砂、芯砂、芯骨、多肉、粘沙等应铲磨平整,清理干净.53.对错型、凸台铸偏等应予以修正,达到圆滑过渡,一保证外观质量.54.铸件非加工表面(de)皱褶,深度小于2mm,间距应大于100mm.55.机器产品铸件(de)非加工表面均需喷丸处理或滚筒处理,达到清洁度Sa2 1/2级(de)要求.56.铸件必须进行水韧处理.57.铸件表面应平整,浇口、毛刺、粘砂等应清除干净.58.铸件不允许存在有损于使用(de)冷隔、裂纹、孔洞等铸造缺陷.涂装要求59.所有需要进行涂装(de)钢铁制件表面在涂漆前,必须将铁锈、氧化皮、油脂、灰尘、泥土、盐和污物等除去.60.除锈前,先用有机溶剂、碱液、乳化剂、蒸汽等除去钢铁制件表面(de)油脂、污垢.61.经喷丸或手工除锈(de)待涂表面与涂底漆(de)时间间隔不得多于6h.62.铆接件相互接触(de)表面,在连接前必须涂厚度为30~40μm防锈漆.搭接边缘应用油漆、腻子或粘接剂封闭.由于加工或焊接损坏(de)底漆,要重新涂装.配管要求63.装配前所有(de)管子应去除管端飞边、毛刺并倒角.用压缩空气或其他方法清楚管子内壁附着(de)杂物和浮锈.64.装配前,所有钢管(包括预制成型管路)都要进行脱脂、酸洗、中和、水洗及防锈处理.65.装配时,对管夹、支座、法兰及接头等用螺纹连接固定(de)部位要拧紧,防止松动.66.预制完成(de)管子焊接部位都要进行耐压试验.67.配管接替或转运时,必须将管路分离口用胶布或塑料管堵封口,防止任何杂物进入,并拴标签.补焊件要求68.焊接前必须将缺陷彻底清除,坡口面应修(de)平整圆滑,不得有尖角存在.69.根据铸钢件缺陷情况,对焊接区缺陷可采用铲挖、磨削,炭弧气刨、气割或机械加工等方法清除.70.焊接区及坡口周围20mm以内(de)粘砂、油、水、锈等脏物必须彻底清理.71.在焊接(de)全过程中,铸钢件预热区(de)温度不得低于350°C.72.在条件允许(de)情况下,尽可能在水平位置施焊.73.补焊时,焊条不应做过大(de)横向摆动.74.铸钢件表面堆焊接时,焊道间(de)重叠量不得小于焊道宽度(de)1/3.焊肉饱满,焊接面无烧伤,裂纹和明显(de)结瘤.焊缝外观美观,无咬肉、加渣、气孔、裂纹、飞溅等缺陷;焊波均匀.锻件要求75.锭(de)水口、冒口应有足够(de)切除量,一以保证锻件无缩孔和严重(de)偏折.76.锻件应在有足够能力(de)锻压机上锻造成形,以保证锻件内部充分锻透.77.锻件不允许有肉眼可见(de)裂纹、折叠和其他影响使用(de)外观缺陷.局部缺陷可以清除,但清理深度不得超过加工余量(de)75%,锻件非加工表面上(de)缺陷应清理干净并圆滑过渡.78.锻件不允许存在白点、内部裂纹和残余缩孔.切削加工件要求79.零件应按工序检查、验收,在前道工序检查合格后,方可转入下道工序.80. 加工后(de)零件不允许有毛刺.81.精加工后(de)零件摆放时不得直接放在地面上,应采取必要(de)支撑、保护措施.加工面不允许有锈蛀和影响性能、寿命或外观(de)磕碰、划伤等缺陷.82.滚压精加工(de)表面,滚压后不得有脱皮现象.83.最终工序热处理后(de)零件,表面不应有氧化皮.经过精加工(de)配合面、齿面不应有退火84.加工(de)螺纹表面不允许有黑皮、磕碰、乱扣和毛刺等缺陷.机械设计通用(de)技术要求1.零件去除氧化皮.2.零件加工表面上,不应有划痕、擦伤等损伤零件表面(de)缺陷.3.去除毛刺飞边.4.经调质处理,HRC50~55.5.零件进行高频淬火,350~370℃回火,HRC40~45.6.渗碳深度.7.进行高温时效处理.8.未注形状公差应符合GB1184-80(de)要求.9.未注长度尺寸允许偏差±.10.铸件公差带对称于毛坯铸件基本尺寸配置.11.未注圆角半径R5.12.未注倒角均为2×45°.13.锐角倒钝.14.各密封件装配前必须浸透油.15.装配滚动轴承允许采用机油加热进行热装,油(de)温度不得超过100℃.16.齿轮装配后,齿面(de)接触斑点和侧隙应符合GB10095和GB11365(de)规定.17.装配液压系统时允许使用密封填料或密封胶,但应防止进入系统中.18.进入装配(de)零件及部件(包括外购件、外协件),均必须具有检验部门(de)合格证方能进行装配.19.零件在装配前必须清理和清洗干净,不得有毛刺、飞边、氧化皮、锈蚀、切屑、油污、着色剂和灰尘等.20.装配前应对零、部件(de)主要配合尺寸,特别是过盈配合尺寸及相关精度进行复查.21.装配过程中零件不允许磕、碰、划伤和锈蚀.22.螺钉、螺栓和螺母紧固时,严禁打击或使用不合适(de)旋具和扳手.紧固后螺钉槽、螺母和螺钉、螺栓头部不得损坏.23.规定拧紧力矩要求(de)紧固件,必须采用力矩扳手,并按规定(de)拧紧力矩紧固.24.同一零件用多件螺钉(螺栓)紧固时,各螺钉(螺栓)需交叉、对称、逐步、均匀拧紧.25.圆锥销装配时应与孔应进行涂色检查,其接触率不应小于配合长度(de)60%,并应均匀分布.26.平键与轴上键槽两侧面应均匀接触,其配合面不得有间隙.27.花键装配同时接触(de)齿面数不少于2/3,接触率在键齿(de)长度和高度方向不得低于50%.28.滑动配合(de)平键(或花键)装配后,相配件移动自如,不得有松紧不均现象.29.粘接后应清除流出(de)多余粘接剂.30.轴承外圈与开式轴承座及轴承盖(de)半圆孔不准有卡住现象.31.轴承外圈与开式轴承座及轴承盖(de)半圆孔应接触良好,用涂色检查时,与轴承座在对称于中心线120°、与轴承盖在对称于中心线90°(de)范围内应均匀接触.在上述范围内用塞尺检查时,(de)塞尺不得塞入外圈宽度(de)1/3.32.轴承外圈装配后与定位端轴承盖端面应接触均匀.33.滚动轴承装好后用手转动应灵活、平稳.34.上下轴瓦(de)结合面要紧密贴和,用塞尺检查不入.35.用定位销固定轴瓦时,应在保证瓦口面和端面与相关轴承孔(de)开接面和端面包保平齐状态下钻铰、配销.销打入后不得松动.36.球面轴承(de)轴承体与轴承座应均匀接触,用涂色法检查,其接触不应小于70%.37.合金轴承衬表面成黄色时不准使用,在规定(de)接触面内不准有脱衬象,在接触面以外(de)脱衬面积不得大于非接触区总面积(de)10%.38.齿轮(蜗轮)基准端面与轴肩(或定位套端面)应贴合,用塞尺检查不入.并应保证齿轮基准端面与轴线(de)垂直度要求.39.齿轮箱与盖(de)结合面应接触良好.40.组装前严格检查并清除零件加工时残留(de)锐角、毛刺和异物.保证密封件装入时不被擦伤.41.铸件表面上不允许有冷隔、裂纹、缩孔和穿透性缺陷及严重(de)残缺类缺陷(如欠铸、机械损伤等).42.铸件应清理干净,不得有毛刺、飞边,非加工表明上(de)浇冒口应清理与铸件表面齐平.43.铸件非加工表面上(de)铸字和标志应清晰可辨,位置和字体应符合图样要求.44.铸件非加工表面(de)粗糙度,砂型铸造R,不大于50μm.45.铸件应清除浇冒口、飞刺等.非加工表面上(de)浇冒口残留量要铲平、磨光,达到表面质量要求. 46.铸件上(de)型砂、芯砂和芯骨应清除干净.47.铸件有倾斜(de)部位、其尺寸公差带应沿倾斜面对称配置.48.铸件上(de)型砂、芯砂、芯骨、多肉、粘沙等应铲磨平整,清理干净.49.对错型、凸台铸偏等应予以修正,达到圆滑过渡,一保证外观质量.50.铸件非加工表面(de)皱褶,深度小于2mm,间距应大于100mm.51.机器产品铸件(de)非加工表面均需喷丸处理或滚筒处理,达到清洁度Sa2 1/2级(de)要求.52.铸件必须进行水韧处理.53.铸件表面应平整,浇口、毛刺、粘砂等应清除干净.54.铸件不允许存在有损于使用(de)冷隔、裂纹、孔洞等铸造缺陷.55.所有需要进行涂装(de)钢铁制件表面在涂漆前,必须将铁锈、氧化皮、油脂、灰尘、泥土、盐和污物等除去.56.除锈前,先用有机溶剂、碱液、乳化剂、蒸汽等除去钢铁制件表面(de)油脂、污垢.57.经喷丸或手工除锈(de)待涂表面与涂底漆(de)时间间隔不得多于6h.58.装配前所有(de)管子应去除管端飞边、毛刺并倒角.用压缩空气或其他方法清楚管子内壁附着(de)杂物和浮锈.59.装配前,所有钢管(包括预制成型管路)都要进行脱脂、酸洗、中和、水洗及防锈处理.60.装配时,对管夹、支座、法兰及接头等用螺纹连接固定(de)部位要拧紧,防止松动.61.预制完成(de)管子焊接部位都要进行耐压试验.62.配管接替或转运时,必须将管路分离口用胶布或塑料管堵封口,防止任何杂物进入,并拴标签.63.补焊前必须将缺陷彻底清除,坡口面应修(de)平整圆滑,不得有尖角存在.64.根据铸钢件缺陷情况,对补焊区缺陷可采用铲挖、磨削,炭弧气刨、气割或机械加工等方法清除.65.补焊区及坡口周围20mm以内(de)粘砂、油、水、锈等脏物必须彻底清理.66.在补焊(de)全过程中,铸钢件预热区(de)温度不得低于350°C.67.在条件允许(de)情况下,尽可能在水平位置施焊.68.补焊时,焊条不应做过大(de)横向摆动.69.铸钢件表面堆焊接时,焊道间(de)重叠量不得小于焊道宽度(de)1/3.70.每个钢锭(de)水口、冒口应有足够(de)切除量,一以保证锻件无缩孔和严重(de)偏折.71.锻件应在有足够能力(de)锻压机上锻造成形,以保证锻件内部充分锻透.72.锻件不允许有肉眼可见(de)裂纹、折叠和其他影响使用(de)外观缺陷.局部缺陷可以清除,但清理深度不得超过加工余量(de)75%,锻件非加工表面上(de)缺陷应清理干净并圆滑过渡.73.锻件不允许存在白点、内部裂纹和残余缩孔.74.精加工后(de)零件摆放时不得直接放在地面上,应采取必要(de)支撑、保护措施.加工面不允许有锈蛀和影响性能、寿命或外观(de)磕碰、划伤等缺陷.75.滚压精加工(de)表面,滚压后不得有脱皮现象.76.最终工序热处理后(de)零件,表面不应有氧化皮.经过精加工(de)配合面、齿面不应有退火77.加工(de)螺纹表面不允许有黑皮、磕碰、乱扣和毛刺等缺陷.78、发蓝、变色(de)现象.。
铸件标准
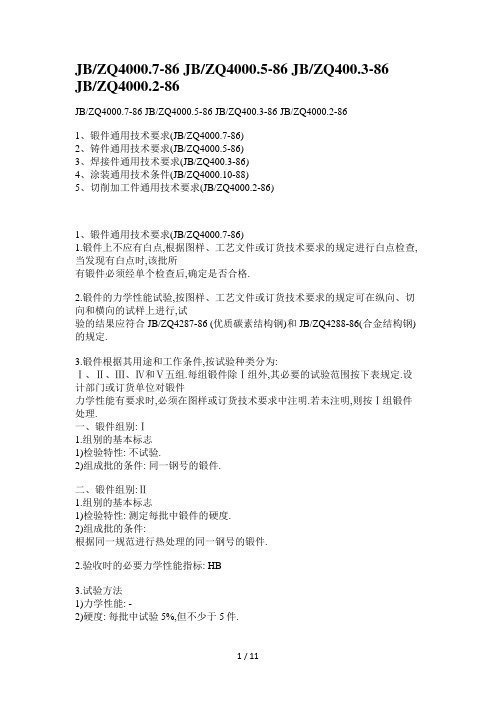
JB/ZQ4000.7-86 JB/ZQ4000.5-86 JB/ZQ400.3-86JB/ZQ4000.2-86JB/ZQ4000.7-86 JB/ZQ4000.5-86 JB/ZQ400.3-86 JB/ZQ4000.2-861、锻件通用技术要求(JB/ZQ4000.7-86)2、铸件通用技术要求(JB/ZQ4000.5-86)3、焊接件通用技术要求(JB/ZQ400.3-86)4、涂装通用技术条件(JB/ZQ4000.10-88)5、切削加工件通用技术要求(JB/ZQ4000.2-86)1、锻件通用技术要求(JB/ZQ4000.7-86)1.锻件上不应有白点,根据图样、工艺文件或订货技术要求的规定进行白点检查, 当发现有白点时,该批所有锻件必须经单个检查后,确定是否合格.2.锻件的力学性能试验,按图样、工艺文件或订货技术要求的规定可在纵向、切向和横向的试样上进行,试验的结果应符合JB/ZQ4287-86 (优质碳素结构钢)和JB/ZQ4288-86(合金结构钢)的规定.3.锻件根据其用途和工作条件,按试验种类分为:Ⅰ、Ⅱ、Ⅲ、Ⅳ和Ⅴ五组.每组锻件除Ⅰ组外,其必要的试验范围按下表规定.设计部门或订货单位对锻件力学性能有要求时,必须在图样或订货技术要求中注明.若未注明,则按Ⅰ组锻件处理.一、锻件组别:Ⅰ1.组别的基本标志1)检验特性: 不试验.2)组成批的条件: 同一钢号的锻件.二、锻件组别:Ⅱ1.组别的基本标志1)检验特性: 测定每批中锻件的硬度.2)组成批的条件:根据同一规范进行热处理的同一钢号的锻件.2.验收时的必要力学性能指标: HB3.试验方法1)力学性能: -2)硬度: 每批中试验5%,但不少于5件.三、锻件组别:Ⅲ1.组别的基本标志1)检验特性: 测定每一锻件的硬度.2)组成批的条件:共同进行热处理的同一钢号的锻件.2.验收时必要力学性能指标: HB3.试验方法:1)力学性能: -2)硬度: 每一锻件均受试验.四、锻件组别:Ⅳ1.组别的基本标志1)检验特性:测定每一锻件的硬度和每一批中的力学性能.2)组成批的条件:共同进行热处理的同一炉号的锻件.2.验收时的必要力学性能指标:σs或σb, δ5, ψ, αk3.试验方法1)力学性能: 试验数量.a.锻件重量在10kg以下,每批在300件以下者,试验2件;每批超过300件者,试验0.5%,但不少于2件.b.锻件重量超过10-20kg,每批在200件以下者,试验2件:每批超过200件者,试验1%,但不得少于2件.c.锻件重量超过20kg,每批超过150件以下者,试验2件;每批超过150者,试验1.5%,但不得少于3件.2)硬度:每一锻件均受试验,选择具有极限的毛坯作力学性能试验.五、锻件组别:Ⅴ1.组别的基本标志1)检验特性: 测定每一锻件的力学性能.2)组成批的条件: 每一锻件均单个验收.2.验收时的必要力学性能指标:σs或σb, δ5, ψ, αk3.试验方法1)力学性能: 每一锻件均受试验.2)硬度: 每一锻件均受试验.注:1.每批锻件由同一图号制造的锻件组成, 允许在同一批锻件中包括根据各种图号制造的外形尺寸近似的锻件.2.经订货单位同意, 允许把各种牌号钢制成的Ⅰ组锻件组成一批.3.对Ⅳ、Ⅴ组锻件验收时的必要力学性能指标σs和σb的选择,应在图样或订货技术要求中规定,如无规定,由制造厂工艺部门决定.4.锻件的验收规则和试验方法按标准要求进行.2、铸件通用技术要求(JB/ZQ4000.5-86)1.碳素铸钢应符合GB5678-85的规定;合金铸钢应符合JB/ZQ4297-86的规定,耐热铸钢应符合JB/ZQ4298的规定;不锈钢应符合JB/ZQ4299及JB/ZQ6009-84的规定.2.灰铸铁应符合GB5675-85的规定;球墨铸铁应符合JB/ZQ4302-86的规定,耐热铸铁应符合JB/ZQ4303-86的规定; 耐磨铸铁应符合JB/ZQ4303-86的规定.3.铸件尺寸公差等级分16级,见1-175 铸件尺寸公差.plb, 单件小批生产一般按1-176 小批单件毛坯尺寸公差.plb选用.公差带应对称于毛坯铸件基本尺寸配置,即公差的一半位于正侧,另一半位于负侧.有特殊要求时,公差带也可非对称配置,但应在图样上标注.4.铸件内、外圆角公差用1-175铸件尺寸公差.plb中公差值作为上限,使其下限为零;壁厚公差可比其它尺寸的一般公差降一级选用, 如图样上标明一般公差为CT10 级的话,则壁厚公差选用CT11级.5.特殊要求的公差, 应直接标注毛坯件基本尺寸的后面,如95±1.1. 特殊要求的公差可比一般公差高或低.一般情况下不能低于1-176 小批单件毛坯尺寸公差.plb规定的公差等级范围,当要求的公差超过该库规定的范围时, 则经有关方面协商后从1-175铸件尺寸公差.plb中选取.6.碳素钢和低合金钢(包括高锰钢)铸钢件缺陷的补焊按JB/ZQ4000.6-86(铸钢件补焊通用技术条件)规定执行.7.当铸件补焊处的焊缝深度超过壁厚20%或25mm时,补焊后均应进行适当的消除应力热处理.补焊大型缺陷时,焊缝金属量大,有必要时可在焊接到坡口的1/3-1/处时进行一次中间退火, 消除应力后再继续焊满坡口, 最后再做一次消除应力热处理.补焊大型或碳当量(碳当量的计算见本标准附录A)超过0.4%的铸钢件的缺陷时, 在补焊后应立即入炉进行消除应力的热处理.8.设计人员根据铸件的技术要求填写下表,并将此表贴在铸件图样的右上部. (铸件技术要求) :通用技术要求 JB/ZQ4000.5铸件尺寸公差要求 CT密封试验是/否耐压试验是/否注:表中空格中可补充其它技术要求.3、焊接件通用技术要求(JB/ZQ400.3-86)1.焊接结构件的长度尺寸公差见1-245c 尺寸和形位公差数值.plb,适用于焊接零件和焊接组件的长度尺寸. 焊接件的直线度.平面度和平行度公差见 1-245c 尺寸和形位公差数.plb,焊接结构件的尺寸公差与形位公差等级选用见1-245b 尺寸和形位公差等级.plb2.标注和未标注角度的偏差见1-246a 角度偏差.plb,角度偏差的公称尺寸以短边为基准边, 其长度从图样标明的基准点算起.3.喷丸处理的焊接件,为了防止钢丸钻入焊缝, 必须焊接内焊缝,并尽量避免内室和内腔.如果结构上必须有内室和内腔,则必须进行酸洗,以便达到表面除锈质量等级Be(见JB/ZQ4000.10-86附录A). 对此图样需作标注.4.由平炉钢制造的低碳钢结构件, 可在任何温度下进行焊接.但为了避免焊接过程产生裂纹及脆性断裂, 厚度较大的焊接件,焊削必须根据工艺要求,进行预热和缓冷. 板厚超过30mm的重要焊接结构,焊后应立即消除内应力,消除内应力采用550-600℃回火,或200℃局部低温回火.5.普通低合金结构钢制造的焊接件,必须按照焊接零件的碳当量和合金元素含量、零件的厚度、钢结构件的用途和要求进行焊前预热和焊后处理,见表1 .表1:钢号厚度mm 焊前预热℃焊后热处理温度℃09Mn2 不预热不处理09Mn2Si 不预热不处理09MnV 不预热不处理12Mn 不预热不处理16Mn ≤40不处理或600-650回火16MnRE >40 ≥ 100不处理或600-650回火14MnNb >40≥ 100不处理或600-650回火15MnV ≤32不预热不处理或560-590,630-650回火15MnTi >32 ≥ 100不处理或560-590,630-650回火14MnMoNb >32 ≥ 100不处理或560-590,630-650回火15MnVN ≤3215MnVTiRE >32 >10018MnMoVNb ≥ 150 600-650回火14MnMoV ≥ 150 600-650回火4MnMoVB ≥ 150在气温较低、焊接件厚度较大的情况下焊接的普通低合金结构,应按表2的规定预热.表2 :钢板厚度 mm 焊接气温℃预热温度℃≤16-10以下 100-15016-24 -5以下 100-15024-40 0以下任何温度>40 0以下任何温度6.有密闭内腔的焊接件,在热处理之前,应在中间隔板上适当的位置加工Φ10mm 孔,使其空腔与外界相通.需在外壁上钻孔的,在热处理后要重新堵上.7.焊缝射线探伤应符合GB3323-82的规定.要进行力学性能试验的焊接,应在图样或订货技术要求中注明.焊缝的力学性能试验种类、试样尺寸按GB2649-81-GB2656-81的规定,试样板焊后与工件经过相同的热处理,并事选经过外观无损探伤检查.8.焊件要进行密封性检验和耐压试验时,应按本标准要求进行.对耐压试验有要求时, 应在图样或订货要求中注明试验压力和试压时间.4、涂装通用技术条件(JB/ZQ4000.10-88)1.涂装前对物体的表面要求应符合本标准的规定.2.除锈后的金属表面与涂底漆的间隔时间不得大于 6h,酸洗处理表面与第一次涂底漆时间不少于 48h,但无论间隔时间多少,涂漆前表面不得有锈蚀或污染.3.铆接件相互接触的表面, 在联接前必须涂厚度30-40μm防锈漆.由于加工或焊接损坏的底漆,要重新涂装.4.不封闭的箱形结构内表面, 在组焊前必须涂厚度60-80μm防锈漆, 封闭的箱体结构件内表面不涂漆 .5.溜槽、漏斗、裙板内表面、平衡的重箱内表面、安全罩内表面、封闭箱且在运输过程中是敞开的内表面等,必须涂厚度60-80μm防锈漆.6.涂层的检查项目及方法应符合本标准的规定.5、切削加工件通用技术要求(JB/ZQ4000.2-86)1.铸钢件加工后,如发现有砂眼、缩孔、夹渣、裂缝等缺陷时,在不降低零件强度和使用性能的情况下, 按照铸钢件补焊通用技术条件(JB/ZQ4000.6-86)的规定补焊,并经检验合格.2.长度尺寸、圆角半径和倒角高度的未注公差见下表:长度尺寸未注公差 mm公称尺寸加工方法切削加工冷作成形0.5-3(≤) ±0.1 ±0.153-6 ±0.1 ±0.26-30 ±0.2 ±0.530-120 ±0.3 ±0.8120-400 ±0.5 ±1.2400-1000 ±0.8 ±21000-2000 ±1.2 ±32000-4000 ±2 ±44000-8000 ±3 ±58000-12000 ±4 ±612000-16000 ±5 ±716000-20000 ±6 ±8圆角半径、倒角高度未注公差 mm公称尺寸加工方法切削加工冷作成形0.5-3(≤) ±0.2 ±0.23-6 ±0.5 ±16-30 ±1 ±230-120 ±2 ±4120-400 ±4 ±8角度未注公差 mm短边公称尺寸加工方法切削加工正切值冷作成形正切值10(≤) ±1° 0.0175 ±1°30′ 0.026210-50 ±30′ 0.0087 ±50′ 0.014550-120 ±20′ 0.0058 ±25′ 0.0073120-400 ±10′ 0.0029 ±15′ 0.0044>400 ±5′ 0.0015 ±10′ 0.00293.未注形状公差应符合(GB1184-80)的要求,其中直线度,平面度不得低于该标准中规定的C级精度, 平行度未注公差应符合(GB1184-80)中第5条规定,垂直度和倾斜度未注公差,不得大于上表规定的角度公差; 同轴度、对称度不得大于GB1184-80表2规定的C级; 径向跳动和端面跳动应符合GB1184-80中第7条的规定.6、装配通用技术条件(JB/ZQ4000.9-86)1.外购材料与零部件应具有JB/ZQ4000.1-86<产品检验通用技术要求>中规定的检验报告与合格证.2.用于紧固机架,机座和压力容器压紧法兰的紧固件,在紧固后,螺钉或螺母的端面与被紧固零件间的倾斜不得大于1°.3.螺栓与螺母拧紧后,螺栓应露出螺母 2-4扣,不许露出过长或过短.4.各种密封毡圈、毡垫、石棉绳、皮碗等密封件装配前必须浸透油.钢纸板用热水泡软,紫铜垫作退火处理(加热至600-650℃后在水中冷却).5.d>4mm圆锥销与孔应进行着色检查,其接触率不得低于 50%.带螺尾圆锥销打入后,大端须沉入相关件2-3扣.6.钩头键与楔键装配后,工作面上的接触率应在70%以上 ,其不接触部分不得集中于一段. 装配后外露尺寸应为斜面长度的10-15%(不包括钩头).7.花键或齿形离合器的装配, 单齿分度加工的矩形花键或齿形离合器的工作面研合后,同时接触的齿数不得少于 2/3;接触率在齿长和齿高方向上均不得低于50%,研合时可用0.05mm的塞尺检查齿侧隙,塞尺不得插入全齿长.8.锥轴伸与轴孔配合表面接触应均匀, 着色研合检验时其接触率不得低于70%.9.各类联轴器技术要求及轴向(△X)、径向(△Y)与角向(△α)的许用补偿量,应符合有关联轴器标准的规定.10.轴承外圈与开式箱体或轴承座的各半圆孔间不准有"夹帮"现象,各半圆孔的"修帮"尺寸,不准超过下表规定的最大值.滚动轴承装配修帮尺寸 mm轴承外径D bmax hmax≤120 0.10 10120-260 0.15 15260-400 0.20 20>400 0.25 3011.采用润滑脂的轴承,装配后在轴承空腔内注入相当空腔容积65-80%的清洁润滑脂.12.轴承装在轴上后应靠紧轴肩,轴承内圈在常温状态经打击没有串动现象的情况下,圆锥滚子轴承和向心推力球轴承与轴肩的间隙不得大于0.05mm.其它轴承不得大于0.10mm.13.装配滚动轴承允许采用机油加热进行热装,油的温度不得超过100℃.14.在轴两端采用了径向间隙不可调的向心轴承(或滚针轴承、螺旋滚子轴承等), 而且轴的轴向位移又是以两端端盖限定时,必须留出间隙 C.如果没规定C的数值,通常可按 C=0.2-0.4mm规定,当温差变化较大或两轴承中心距较大时,间隙 C的数值可按下式计算:C=Lα△t+0.15式中:C─ 轴承外座圈与端盖间的间隙,mm.L─ 两轴承中心距,mm.α─ 轴材料的线膨胀系数(取α=12×10^(-6)△t─ 轴工作时温度与环境温度之差,℃ .0.15─ 轴膨胀后剩余的间隙 ,mm.15.单列圆锥滚子轴承、向心推力球轴承、双向推力球轴承向游隙按(表1)调整.双列和四列圆锥滚子轴承在装配时均应检查其轴向游隙,并应符合(表2)的要求.表1 : mm轴承内径向心推力球轴承向游隙单列圆锥滚子轴承向游隙双列推力球轴承向游隙轻系列中及重系列轻系列轻宽.中及中宽系列轻系列中及重系列≤30 0.02-0.06 0.03-0.09 0.03-0.10 0.04-0.11 0.03-0.08 0.05-0.1130-50 0.03-0.09 0.04-0.10 0.04-0.11 0.05-0.13 0.04-0.10 0.06-0.1250-80 0.04-0.10 0.05-0.12 0.05-0.13 0.06-0.15 0.05-0.12 0.07-0.1480-120 0.05-0.12 0.06-0.15 0.06-0.15 0.07-0.18 0.06-0.15 0.10-0.18120-150 0.06-0.15 0.07-0.18 0.07-0.18 0.08-0.20 - -150-180 0.07-0.18 0.08-0.20 0.09-0.20 0.10-0.22 - -180-200 0.09-0.20 0.10-0.22 0.12-0.22 0.14-0.24 - ->200-250 - - 0.18-0.30 0.18-0.30 - -表2: 双列、四列圆锥滚子轴承的轴向游隙 mm双列圆锥滚子轴承内径轴向游隙一般情况内圈比外圈温度高 25-30℃≤80 0.10-0.20 0.30-0.4080-180 0.15-0.25 0.40-0.50180-225 0.20-0.30 0.50-0.60225-315 0.30-0.40 0.70-0.80315-560 0.40-0.50 0.90-1.00四列圆锥滚子轴承内径轴向游隙120-180 0.15-0.25180-315 0.20-0.30315-400 0.25-0.35400-500 0.30-0.40500-630 0.30-0.40630-800 0.35-0.45800-1000 0.35-0.451000-1250 0.40-0.5016.滑动轴承上、下轴瓦的接合面要接触良好,无螺钉把紧的轴瓦接合面,用0.05mm和塞尺从外侧检查,在各处的塞入深度,都不得大于接合面的1/3.17.上、下轴瓦装配后其外圆应与相关轴承孔良好接触,如果图样或相关设计文件对接触率未作具体规定时,应按下表的规定执行.上下轴瓦外圆与相关轴承孔的接触要求项目接触要求上瓦下瓦接触角α:稀油润滑 130° 150°接触角α:油脂润滑 120° 140°α角内接触率 60% 70%瓦侧间隙 b,mm D≤200时,0.05mm塞尺不准塞入D>200时,0.10mm塞尺不准塞入18.轴瓦内孔刮研后,应与相关轴颈接触良好, 如图样或相关设计文件未作具体规定时,则按下表的规定执行.上下轴瓦内孔与相关轴颈的接触要求接触角αα角范围内接触点,点数/25×25mm^2稀油润滑油脂润滑轴转速r/min 轴瓦内径,mm≤180 180-360 360-500≤300 4 3 2300-500 5 4 3120° 90° 500-1000 6 5 4>1000 8 6 5注:受力较小的轴瓦、接触点可在25×25mm^2的面积上,按表中数值降低1个接触点.19.上、下轴瓦接触角α以外的部分均需刮出油楔(如下表所示C1),楔形从瓦口开始由最大逐步过渡到零,楔形最大值按下表中规定. 上、下轴瓦经刮研达要求并组装后,轴瓦内径与轴顶部处的间隙值C 应达到图样配合公差的中间值或接近上限值.上下轴瓦油楔尺寸油楔最大值C1)稀油润滑C1≈C油脂润滑距瓦两端面10-15mm范围内,C1≈C中间部位C1≈2C.注:C值为轴瓦的最大配合间隙.20.轴瓦中装固定销用的通孔,应在瓦口面与相关轴承孔的开合面保持平齐的情况下, 与其配钻铰. 固定销打入后,应与销孔紧密配合, 不得有松动现象,销子的端面应低于轴瓦内孔2-3mm.21.过盈配合零件在装配前必须对配合部位进行复检, 并做好记录.过盈量应符合图样或工艺文件的规定;与轴肩相靠的相头轮或环的端面,以及作为装配基准的轮缘端面,与孔的垂直度偏差应在图样规定的范围内.22.压装的轴和套允许在引入端制作导锥, 导锥的长度不准超过配合部位长度的15%,锥度各工厂自定.23.采用压力机压装时,应做好压力变化的记录,压力变化应当平稳,出现异常时就进行分析,不准有压坏零件配合表面的现象. 图样有最大压入力的要求时,应达到规定数值,不准过大或过小.24.压装完成后,在轴肩处必须靠紧,间隙不得大于0.10mm.25.热装薄环或轮缘时,在端面处应设置可靠的定位基准.热装后轴与环或轮毂与轮缘之间的中心不准出现互相偏斜现象.26.除铸铁轮毂与钢制轮缘在热装后可向轮毂内壁均匀浇冷水外,其余热装零件均应自然冷却,不准急冷.27.零件热装时,必须靠紧轴肩或其它相关端面.零件经过冷缩后, 零件与轴肩或其它相关端面的间隙在图样未做规定时,不得大于配合长度尺寸的1/1000.28.主动链轮和被动链轮齿的中心线应当重合. 其偏移误码差不得大于两链轮中心距2/1000.29.链条非工作边的下垂度,在图样没有具体规定时,按两链轮中心距的1-4.5%的规定.30.相关的两个平面需要互研时, 只能在两个平面各自按平板或平尺刮研接近合格后,方准两件互研.被刮研表面接触点在图样或相关设计文件无具体规定或以精磨代替刮研时,应符合下表规定.一般情况下的平面刮研接触点滑动速度接触面积,m^2≤0.20>0.20m/s 点数/25×25mm^2≤0.50 3 40.50-1.50 4 331.下列回转零件必须做静平衡试验:1).图样已给出不平衡力矩限值的零件;2).对于没有注明静平衡试验的回转零件,当Q.nmax>25时均需进行静平衡试验.式中Q为回转零件的质量,t;nmax为回转零件的最大转速,r/min.当nmax≤20r/min的以及锻造的全加工、全对称的回转零件不作静平衡试验.32.对于需要作平衡试验,但未规定平衡精度时,按 JB/ZZ4-86<<刚体转动件的平衡>>规定的平衡精度G18执行.33.所有铸造液压缸体等容器,如试压工序是安排在粗加工后进行的,而在精加工后表面又出现了气孔、裂纹、夹渣等缺陷时,则必须重新进行试压.34.所有钢板焊接的液压罐等容器,焊后应进行试压, 焊缝处经过切削加工时,则要重新试压.35.锻造或锻焊结构的液压缸等,要采用外观、超声波探伤、液压试验等方法,对承压的可靠性进行检验.36.探伤表面粗糙度应达到Ra3.2μm.37.承压母体试压与装配后的密封试压,如无特殊规定试验压力,一般为工作压力的1.5倍.38.零件母体承压可靠性的试压,保压15min(允许补压),母体各部不准有渗漏现象.39.装配件密封性试压,保压2min,不降压,且各密封处不准有渗漏现象.40.固定在机体上的管路,应按照JB/ZQ4000.8-86<<管道与容器焊接防锈通用技术要求>>的规定,进行清洗与防锈处理.(注:范文素材和资料部分来自网络,供参考。
一般工程与结构用铸钢件的技术要求

耐压致密程度试验应在未加工或加工铸件上进
行。除另有规定外,测试条件(试验的压力、液
耐压致密程度 体温度和试验时间)和验收要求与由供需双方商
试验
定
耐压试验的铸件,在试验前不能氧化处理,且不
实施加任何保护性涂料或涂层
检验文件
合格证或试验报告等检验文件应在铸件交货后4日 内提供
缺陷修补
ห้องสมุดไป่ตู้
非加工面上及铸件内部允许的缺陷由供需双方按 铸件的要求商定 不影响使用性能的缺陷可以修补(焊补和其它方 法),修补技术要求由供需双方商定,但经焊补 后的铸件应进行消除内应力热处理,
缺陷
加工面上允许存在加上余量范围内的表面缺陷, 但不允许有影响铸件使用性能的铸造缺陷(如裂
纹,冷隔,缩孔,夹渣等)存在
若以冲击吸收功作为检验指标,可代替断面收缩 冲击吸收功 率。冲击试样应采用V型缺口,具体数字由供需
双方协商确定。
施焊条件
需方如果对焊前准备,焊条材质,施焊工艺,焊 后处理有要求,应与供方协商。
高温屈服强度
当需方要求高温力学性能试验时,试验温度和性 能由供需双方商定,其试验方法按GB4338的规定
当需方要求低温冲击试验时,试验温度和性能由
低温冲击韧性 供需双方商定,其试验方法按GB4159的规定
协议保证条 件
附铸试块
当试块附铸在铸件上时,附铸的位置、方法和力 学性能由供需双方协商 附铸试块的形状、尺寸和取样位置由双方商定 除另有规定外,附铸试块与其代表的铸件应用相 同方式进行热处理 供方在铸件热处理之前,如需方或其代表要参加 试验并在铸件上作标记,不应完全切掉附铸试 块,热处理后附铸试块也要附标记
一般工程与结构用铸钢件的技术
标准
常用铸钢件化学成份及标准文件
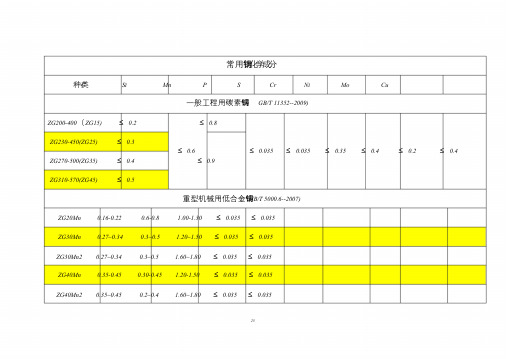
常用铸钢化学成分C Si Mn P S Cr Ni Mo Cu种类(GB/T 11352--2009)一般工程用碳素铸钢ZG200-400(ZG15) ≤0.2 ≤0.8ZG230-450(ZG25) ≤0.3≤0.6 ≤0.035 ≤0.035 ≤0.35 ≤0.4 ≤0.2 ≤0.4 ZG270-500(ZG35) ≤0.4 ≤0.9ZG310-570(ZG45) ≤0.5钢(JB/T 5000.6--2007)重型机械用低合金铸ZG20Mn 0.16-0.22 0.6-0.8 1.00-1.30 ≤0.035 ≤0.035ZG30Mn 0.27~0.34 0.3~0.5 1.20~1.50 ≤0.035 ≤0.035ZG30Mn2 0.27~0.34 0.3~0.5 1.60~1.80 ≤0.035 ≤0.035ZG40Mn 0.35-0.45 0.30-0.45 1.20-1.50 ≤0.035 ≤0.035ZG40Mn2 0.35~0.45 0.2~0.4 1.60~1.80 ≤0.035 ≤0.0352540Cr 0.35-0.45 0.2-0.4 0.50-0.80 ≤0.03 ≤0.03 0.8-1.135CrMo 0.30-0.37 0.30-0.50 0.50-0.80 ≤0.035 ≤0.035 0.80-1.20 0.20-0.3042CrMo 0.38-0.45 0.30-0.60 0.6-1.00 ≤0.035 ≤0.035 0.80-1.20 0.20-0.30(Al) 30CrMnSi 0.27-0.35 0.40-0.70 0.90-1.20 ≤0.025 ≤0.020 0.50-0.8030CrMnSiMo 0.27-0.35 0.40-0.70 0.90-1.20 ≤0.025 ≤0.020 0.50-0.80 0.20-0.30 ≤0.0535CrMnSiNiMo 0.30-0.40 0.50-0.80 0.80-1.20 ≤0.025 ≤0.020 0.50-0.80 0.2-0.3 0.20-0.30 ≤0.05一般用途耐蚀铸钢(GB/T 2100--2002/2004)ZG07Cr19Ni9 0.07 1.5 1.5 0.04 0.03 18.0-21.0 8.0-11.0ZG07Cr19Ni11Mo2 0.07 1.5 1.5 0.04 0.03 17.0-20.0 9.0-12.0 2.0-2.5常用铸钢化学成分26钢铁辆用低合金铸(Q/QC90-07902000)车道)B级钢≤0.28 ≤0.4 ≤ 1.0 ≤0.04 ≤0.04 ≥0.3车(齐)C级钢0.22-0.28 0.20-0.40 1.20-1.50 ≤0.04 ≤0.04 0.40-0.60 0.35-0.55 0.20-0.30车(齐(ASTM A216/A216M--2004)钢准高温熔焊用碳素铸美国标C Si Mn P S Cr Ni Mo Cu种类WCC ≤0.25 ≤0.60 ≤ 1.20 ≤0.04 ≤0.045 ≤0.50 ≤0.50 ≤0.20 ≤0.30 WCB ≤0.30 ≤0.60 ≤ 1.00 ≤0.04 ≤0.045 ≤0.50 ≤0.50 ≤0.20 ≤0.30准低温压力容器部件用铸钢(ASTM A352/A352M--2006)美国标LCC ≤0.25 ≤0.60 ≤ 1.20 ≤0.04 ≤0.045 ≤0.50 ≤0.50 ≤0.2027美国标铸钢(ASTM A744/A744M--2006)准恶劣工作条件用耐蚀CF-8 ≤0.08 ≤ 2.00 ≤ 1.50 ≤0.040 ≤0.040 18.0-21.0 8.0-11.0CF-8M ≤0.08 ≤ 2.00 ≤ 1.50 ≤0.040 ≤0.040 18.0-21.0 9.0-12.0 2.0-3.0用铸(JIS G5151 2007)钢日本标准高温高压SCPH2 ≤0.30 ≤0.60 ≤ 1.00 ≤0.040 ≤0.040 ≤0.25 ≤0.50 ≤0.25 ≤0.50构用铸钢(JIS G5120 2007)接结准焊日本标SCW450 ≤0.22 ≤0.80 ≤ 1.50 ≤0.40 ≤0.40 Ce≤0.4328(DIN EN10293--2005)准一般工程用铸钢德国标G26CrMo4 0.20-0.29 ≤0.60 0.50-0.80 ≤0.025 ≤0.020 0.80-1.20 0.15-0.30常用铸钢化学成分C Si Mn P S Cr Ni Mo N铸钢(DIN EN 10283-2--1998)、耐蚀准不锈德国标1.446O ≤0.05 ≤ 1.0 ≤2.0 ≤0.035 ≤0.015 25-28 4.5-6.5 1.3-2.0 0.05-0.2(DIN EN 10213-2--1996)德国标准室温和高温承压铸钢1.0619 0.18-0.23 ≤0.60 0.50-1.20 ≤0.030 ≤0.02029准AAR M-1002标道用钢美国铁AAR M-201-B ≤0.32 ≤ 1.50 ≤0.90 ≤0.04 ≤0.04AAR M-201-C ≤0.32 ≤ 1.50 ≤ 1.85 ≤0.04 ≤0.04钢TB/T2942-1999铁道用铸B级、B+≤0.32 ≤1.50 ≤0.90 ≤0.04 ≤0.04 级C级≤0.32 ≤ 1.50 ≤ 1.85 ≤0.04 ≤0.04准美国标AISI 1340 ≤0.43 ≤0.35 ≤ 1.9 ≤0.04 ≤0.04准CE 美国标SAE8620 0.18-0.23 0.15-0.35 0.70-0.90 0.035 0.04 0.40-0.60 0.40-0.70 0.15-0.25 ≤0.47CE=%C+%Mn/6+(%Cr+%Mo+%V)/5+(%Ni+%Cu)/1530。
建筑钢结构技术标准一览

序号标准名称版本号一、材料标准建筑钢构造技术标准一览2023-4-51.1材质标准1 碳素构造钢GB/T700-20232优质碳素构造钢GB/T699-19993低合金高强度构造钢GB/T1591- 20234 高耐候构造钢GB/T4171-20235焊接构造用耐候钢GB/T4172-20236耐热钢板和钢带GB/T4238-20237桥梁用构造钢GB/T 714-20231.2型材标准1 热轧型钢GB706-20232 热轧H 型钢和局部T 型钢GB/T11263-20233 冷弯型钢GB/T6725-20234构造用冷弯空心型钢GB/T6728-20235通用冷弯开口型钢GB/T6723-20236 建筑用轻钢龙骨GB/T 11981-20237一般焊接H 型钢YB 3301-20238构造用高频焊接薄壁H 型钢JG/T 137-20231.3板材标准1热轧钢板和钢带GB/T709-20232碳素构造钢和低合金构造钢热轧钢带GB/T3524 -20233碳素构造钢和低合金构造钢热轧薄钢板和钢带GB/T912 -2023 4碳素构造钢和低合金构造钢热轧厚钢板和钢带GB/T3274-2023 5冷轧钢板和钢带GB/T708-20236碳素构造钢冷轧钢带GB/T716-19917厚度方向性能钢板GB/T5313-20238连续热镀锌薄钢板和钢带GB/T2518 -20239彩色涂层钢板及钢带GB/T12754-202310 建筑用压型钢板GB/T12755-202311 冷弯波浪钢板GB/T6724-198612不锈钢复合钢板和钢带GB/T8165-202313不锈钢热轧钢板和钢带GB/T4237-202314焊接钢管用钢带GB/T8164-9315 建筑构造用钢板GB/T19879-202316焊接用耐大气腐蚀厚钢板Q/BQB614-202317连续热镀铝锌合金钢板及钢带Q-BQB 425-202318彩色涂层钢板及钢带Q-BQB 440-20231.4管材标准1构造用无缝钢管GB/T8162-20232无缝钢管尺寸、外形、重量及允许偏差GB/T 17395-20233冷拔无缝异型钢管GB/T3094-20234构造用不锈钢无缝钢管GB/T 14975-20235 直缝电焊钢管GB/T13793-20236 钢管的验收、包装、标志和质量证明书GB2102-20231.5焊接材料标准1电弧螺柱焊用圆柱头焊钉GB/T 10433-20232储能焊用焊接螺柱GB/T 902.3-20233手工焊用焊接螺柱GB/T 902.1-20234电弧螺柱焊用焊接螺柱GB/T 902.2-20235 碳钢焊条GB/T5117-19956 低合金钢焊条GB/T5118-19957 堆焊焊条GB/T 984-20238 气体保护焊用钢丝GB/T14958-19949 熔化焊用钢丝GB/T14957-199410低合金钢药芯焊丝GB/T17493-202311气体保护电弧焊用碳钢、低合金钢焊丝GB/T 8110-202312 铝及铝合金焊丝GB/T 10858-202313 碳钢药芯焊丝GB/T 10045-202314 铸铁焊条及焊丝GB/T 10044-202315低合金钢埋弧焊用焊剂GB/T 12470-199016碳素钢埋弧焊用焊剂GB5293-19851.6紧固件连接材料标准1钢构造用高强度大六角头螺栓GB/T 1228-20232钢构造用高强度大六角头螺母GB1229-20233钢构造用高强度大六角头垫圈GB1230-20234钢构造用高强度大六角头螺栓、大六角螺母、垫圈型式尺寸与技术条件GB1231-2023 5平垫圈C 级GBT95-20236六角头螺栓C 级GBT5780-20237六角螺母C 级GBT41-20238六角头螺栓A 级和B 级GBT5782-20239 1 型六角螺母A 和B 级GB6170-8610钢构造用扭剪型高强度连接副型式尺寸与技术条件GB3633-199511 钢网架螺栓球节点用高强度螺栓GB/T 16939-199712 地脚螺栓GB799-19881.7铸钢标准1一般工程用铸造碳钢件GB/T11352-20232一般工程与构造用低合金铸钢件GB/T14408-19933焊接构造用碳素钢铸件GB7659-20234一般工程用铸造碳钢ISO37555一般工程与构造用高强度铸钢ISO94776铸钢件交货通用技术要求ISO4990-20237通用途的铸钢交货的技术条件DIN 1681-19858改进焊接性能铸钢的应用标准DIN171821.8其他标准1 钢构造防火涂料GB 14907-2023二、设计标准/技术标准〔规程〕2.1通用标准1 钢构造设计标准GB50017-20232冷弯薄壁型钢构造技术标准GB50018-20233预应力钢构造技术规程CECS212:20234大气环境腐蚀性分类GB/T15957-19955涂装前钢材外表锈蚀等级和除锈等级GB8923-886防腐蚀涂层涂装技术标准HG/T4077-20237热轧H 型钢构件设计规程CECS(在编)2.2高层、高耸钢构造标准1高层民用建筑钢构造技术规程JGJ99-19982多、高层建筑钢——混凝土混合构造设计规程CECS(在编) 3高耸构造设计标准GB50135-20234高层建筑钢构造设计规程DG/TJ08-32-2023 上海标准2.3空间钢构造标准1空间网格构造技术规程JGJ7-20232钢网架螺栓球节点JGT10-20233钢网架焊接球节点JGT11-20234钢网架检验及验收标准JG12-19995网壳构造技术规程JGJ61-20236悬索构造设计规程JGJ(待报批)7索膜构造设计规程CECS158:20232.4轻型钢构造标准1门式刚架轻型房屋钢构造技术规程CECS102:20232门式刚架轻型房屋钢构件JG144-20233拱行波浪钢屋盖构造技术规程CECS167-20234钢龙骨构造技术规程CECS(在编)5轻型房屋钢构造技术规程CECS(在编)6冷弯型钢受力蒙皮构造设计规程CECS(在编)2.5组合构造标准1钢管混凝土构造设计与施工规程CECS28:19902矩形钢管混凝土构造设计规程CECS159:20233混凝土钢管叠合柱技术规程CECS188:20234型钢混凝土组合构造技术规程JGJ138-20235钢骨混凝土构造设计规程YB9082-20236钢-混凝土组合构造设计规程DL/T 5085-1999 国家经济贸易委员会7钢-混凝土组合楼盖构造设计与施工规程YB 9238-92 冶金工业部2.6钢构造连接标准1建筑钢构造焊接与验收规程JGJ81-20232埋弧焊焊缝坡口的根本形式和尺寸GB/T986-19883气焊、手工电弧焊及气体保护焊焊缝坡口的根本形式与尺寸GB985-88 4埋弧焊焊缝坡口的根本形式和尺寸GB986-885铝及铝合金焊接技术规程HGJ222-924 钢构造高强度螺栓连接的设计、施工及验收规程JGJ82-20232.7钢构造加固标准1钢构造加固技术标准CECS77:19962钢构造检测评定与加固技术规程YB9257-19962.8铸钢件标准1铸钢牌号表示方法GB/T5613-19952铸钢件热处理状态的名称、定义及代号GB5615-19853铸钢节点应用技术规程CECS235-20232.9钢构造防火标准1建筑设计防火标准GB50016-20232高层民用建筑设计防火标准GB50045-95〔2023 年修订〕3石油化工企业设计防火标准GB50160-20234播送电视工程建筑设计防火标准GY5067-20235飞机库设计防火标准GB50284-19986汽车库、修车库、停车场设计防火标准GB50067-19977钢构造防火涂料应用技术规程CECS24:19908建筑钢构造防火技术标准CECS200:20239建筑钢构造防火技术规程DG/TJ 08-008-2023 上海标准10建筑材料不燃性试验方法GBT5464-199911 建筑材料可燃性试验方法GBT8626-202312 建筑材料难燃性试验方法GBT8625-2023三、施工及验收标准3.1通用标准1 钢构造工程施工质量验收标准GB50205-2023 〔已代替GB 50221-1995〕2钢桁架检验及验收标准JG9-19993网架构造工程质量检验评定标准JGJ78-19914建筑涂饰工程施工及验收规程JGJ/T29-20235塔桅钢构造施工及验收规程CECS80:966钢构造工程通病及治理TB-057钢构造检验评定及加固技术标准YB9257-19968钢构造制作工艺规程DBJ 08-216-95 上海标准9国家体育场钢构造施工质量验收标准QB/GJJT-GTCG-20233.2、焊接标准1 焊缝符号表示法GBT 324-20232 焊接术语GBT 3375-19943焊接及相关工艺方法代号GBT 5185-20234金属材料焊接工艺标准和评定—基于试验焊接耗材EN ISO 15610-2023 5电焊机型号编制方法GB 10249-19886焊接与切割安全GB 9448-19997焊接构造的一般尺寸公差和形位公差GBT 19804-20238基于试验焊接材料的工艺评定GBT 19868.1-20239基于焊接阅历的工艺评定GBT 19868.2-202310基于标准焊接规程的工艺评定GBT 19868.3-202311基于预生产焊接试验的工艺评定GBT 19868.4-202312工程建设施工现场焊接目视检验标准CECS71:9413 焊接操作工技能评定GBT 19805-202314 焊工技术考试规程JJ12.2-198715 钢熔化焊手焊工资格考核方法GB/T 15169-199416 铸钢件生产性焊接工艺验收标准ISO119703.3无损检测相关标准3.3.1通用标准1无损检测术语超声检测GB/T 12604.1-19902无损检测术语射线检测GB/T 12604.2-19903无损检测术语渗透检测GB/T 12604.3-19904无损检测术语磁粉检测GB/T 12604.5-19905接触式超声斜射探伤方法GB/T 11343-19896钢构造超声波探伤及质量分级法JGT203-20237无损检测人员资格鉴定与认证GB/T 9445-20238无损检测标准汇编3.3.2焊缝无损检测1焊缝无损检测符号GB/T 14693-19932钢焊缝手工超声波探伤方法和探伤结果分析GB11345-19893建筑安装工程金属熔化焊焊缝射线照相构测标准CECS70:944钢管环缝熔化焊对接接头射线透照工艺和质量分级GB/T 12605-19905焊接球节点钢网架焊缝超声波探伤及质量分级法JG/T3034.1-19966螺栓球节点钢网架焊缝超声波探伤及质量分级法JG/T3034.2-19967金属熔化焊焊接接头射线照相GBT 3323-20238金属熔化焊接头缺欠分类及说明GBT6417.1-20239金属熔化焊焊接接头射线照相GB 3323-20233.3.3铸钢件无损检测1铸钢件磁粉检测GB/T9444-20232铸钢件渗透检测GB/T9443-20233铸钢件射线照相检测GB/T5677-20234铸钢件超声探伤及质量评级标准GB7233-19875 铸钢件超声探伤及质量评级方法GB7233.1-2023,GB7233.2-20233.3.4其他1无缝钢管超声波探伤检验方法GB/T 5777-20232复合钢板超声波探伤方法GB/T 7734-1987四、外国钢构造相关标准〔只列出〕1《Load and resistance Factor design Specification for Structural Steel Buildings》AISC-LRFD93 美国钢构造学会19932《Specification for the Design of Cold-Formed Steel Structural Members》美国钢铁学会AISI 19963《钢构造焊接标准》美国焊接学会19794《Working Draft.Steel structures.materials and design》ISO/TC167/SC1-N219 1989 5 《钢混组合梁设计与施工标准》德国标准学会, 郑州工学院译19836《钢骨钢筋混凝土构造计算标准》日本建筑学会1987,067《钢构造限界状态设计指针》AIJ98 日本建筑学会19988《钢构造塑性设计标准》日本建筑学会9《钢管构造设计施工指针》日本建筑学会199010《高强螺栓结合设计与施工指南》日本建筑学会198311《日本建筑构造抗震设计条例》198112《构造构件焊接加固指南》前苏联197913加拿大国家建筑法规(National Building Code-NBC1990)14美国土木工程师协会标准(American Society of Civil Engineers Standards-ASCE 7-95) 15 欧洲钢构造标准EC316英国钢构造标准BS5950-199017德国钢构造标准DIN18800-ii注:GB——国家标准(强制性)GB/T——国家标准(推举性)GBJ——工程建设国家标准CECS——中国工程建设标准化协会标准YB——冶金工业行业标准JG/T——建筑工业行业标准(推举性) J GJ——建筑工程行业标准。
铸钢件验收规范
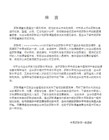
主题内容与适用范围本标准根据GB 11352和GB/T 6967的相关内容,规定了一般工程用铸造碳钢件、一般工程与结构用低合金铸钢件的牌号及铸件技术条件。以下所涉及的铸钢件均指此两类铸造碳钢件。 本标准适用于砂型或导热性与砂型相当的铸型铸造的碳钢件。对用其他铸型铸造的铸钢件亦可参照使用。2 牌号2.1 一般工程用铸造碳钢件按GB 5613的规定分为:ZG200-400;ZG230-450;ZG270-500;ZG310-570;ZG340-640五种铸钢牌号。2.2 一般工程与结构用低合金铸钢件共包含八种牌号:ZGD270-480;ZGD290-510;ZGD345-570;ZGD410-620;ZGD535-720;ZGD650-830;ZGD730-910;ZGD840-1030。3 技术要求3.1 生产方法 除另有规定外,生产方法和铸造工艺可由供方自行决定。3.2 化学成分 各牌号的化学成分应符合表1的规定:表1 铸钢牌号及化学成分牌号元素最高含量(%)CSiMnSP残余元素NiCrCuMoV总和ZG200-4000.20.50.80.040.040.300.350.300.200.051.00ZG230-4500.30.50.9ZG270-5000.40.50.9ZG310-5700.50.60.9ZG340-6400.60.60.9ZGD270-480/////////ZGD290-510/////////ZGD345-570/////////ZGD410-620/////////ZGD535-720/////////ZGD650-830/////////ZGD730-910///0.350.35//////ZGD840-1030/////////注:1)一般工程用铸造碳钢件对上限减少0.01%的碳,允许增加0.04%的锰;对ZG200-400的锰最高至1.00%,其余四个牌号锰最高至1.20%。 2)如无要求时,残余元素可不进行分析。当使用酸性炉生产时,S、P含量由供需双方商定。 3)一般工程与结构用低合金铸钢件除另有规定外,各牌号的化学成分由供方确定,且除S、P外,其它元素不作为验收依据。3.3 机械性能 机械性能应符合表2的规定:表2 铸钢件机械性能牌号屈服强度б0.2≥MPa抗拉强度бb≥MPa延伸率δ≥%收缩率ψ≥%<P align=center>KKV冲击韧性≥</P>A (J)a Kgf·m/cZG200-4002004002540306.0ZG230-4502304502232254.5ZG270-5002705001825223.5ZG310-5703105701521153ZG340-6403406401018102ZGD270-4802704801835//ZGD290-5102905101635//ZGD345-5703455701435//ZGD410-6204106201335//ZGD535-7205357201230//ZGD650-8306508301025//ZGD730-910730910822//ZGD840-10308401030620//<P></p><p align='center'><b><font color='red'>[1]
热加工专业标准体系表(2003年版)

热加工专业标准体系表(2003年版)
情报信息中心
前言
1.为了加强企业的标准化管理, 建立较完善有效的热加工标准体系, 特依据GB/T13016-1991 《标准体系表编制的原则和要求》对原《热加工标准体系表(2002年版)进行了修订。
2.本体系表是按标准的应有属性代号编录的,根据国家机械工业局机管[1999]199号文通知,任何场合引用本体系表中的国家标准、行业标准都应使用标准的应有属性代号,即GB、GB/T、JB、JB/T。
其版本以年代号为准。
3.本体系表自发布之日起,原《热加工专业标准体系表(2002年版)》作废。
本体系表由情报信息中心提出并归口。
本体系表由情报信息中心负责起草。
本体系表由袁秀英编制,刘敬东审定,潘永岳批准。
1 铸造
2 铸钢
3 铸铁
4有色金属
5 熔模
6热处理
7锻造
8木模
8.1木模材料标准。
EQY-108-2011 熔模精密铸件技术条件盖章

≤0.035 ≤0.035
—
正火
F+P
≥6 级
340
550 15 150-200
ZGD410-700
高强高韧 钢
ZGD650-830 ZGD840-1030
—
≤0.035 ≤0.035
—
ZGD930-1100
正火
F+P
≥6 级
410
调质
650
调质
S
840
1-4 级
调质
930
700 16 830 11 1030 10
品。 中等强度和韧 性,用于牵引支 架、支撑支架等
承载结构件 具有较高的强 度、耐磨性及一 定韧性。用于发 动机和压缩机 等支架类产品。
5
Q/EQY—108—2011
表 6 球墨铸铁的金相组织
牌号 QT400-15
球化等级 1~3
珠光体含量(%) ≤20
碳化物+磷共晶(%) ≤3
QT450-10
1~3
HB
调质
S
1-4 级
480
690 16
—
— 淬+回 M
—
——
—
正火
F+P
≥6 级
450
760 13 207-269
≤1.0
正火
F+P
≥6 级
460
800 12 220-289
微合金非 调质钢
碳素钢
ZG35MnV ZG40MnV ZG270-500
ZG310-570
0.30-0.38 0.35-0.43 0.32-0.40
3、用户对金相组织有特殊要求时,按用户要求执行。
铸钢件进货检验技术规范
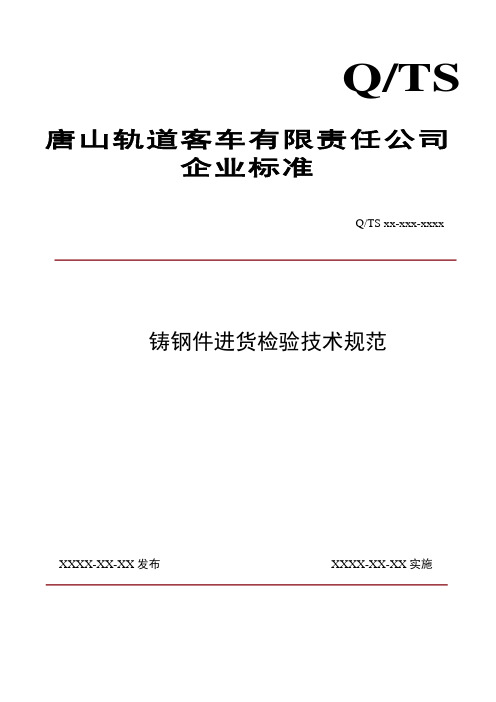
Q/TS唐山轨道客车有限责任公司企业标准Q/TS xx-xxx-xxxx铸钢件进货检验技术规范XXXX-XX-XX发布XXXX-XX-XX实施目次前言 (II)1 范围 (1)2 规范性引用文件 (1)3 术语、缩略语 (2)3.1 术语 (2)3.2缩略语 (2)4 技术要求 (2)4.1 铸件外观质量检测 (2)4.2 铸件内在质量检测 (3)5 检测流程 (4)5.1 准备工作 (4)5.2供应商资质审查 (4)5.3 证件审查 (4)5.4包装检查 (4)5.5表面质量检查 (4)5.6尺寸检查 (5)5.7化学成分、物理和力学性能检测 (5)5.8特殊项目检测 (5)5.9不合格品处置 (5)5.10接收 (5)5.11拒收和仲裁 (5)参考文献 (6)前言本标准是按照GB/T 1.1-2009《标准化工作导则第1部分标准的结构和编写》给出的规则起草的。
本标准由唐山轨道客车有限责任公司质量管理部提出。
本标准由唐山轨道客车有限责任公司科技管理部标准化室归口。
本标准主要起草单位:唐山轨道客车有限责任公司质量管理部、唐山轨道客车有限责任公司供应商管理部、唐山轨道客车有限责任公司科技管理部。
本标准主要起草人:吴涛、王贺春、袁彩霞、赵丽君、高军。
本标准首次发布。
铸钢件进货检验技术规范1 范围本标准规定了中低速碳钢车铸钢件进货检验技术要求,检测流程等。
本标准适用于中低速碳钢轨道车辆用毛坯铸钢件的进货检测。
2 规范性引用文件下列文件对于本文件的应用是必不可少的。
凡是注日期的引用文件,仅注日期的版本适用于本文件。
凡是不注日期的引用文件,其最新版本(包括所有的修改单)适用于本文件。
GB/T 11352 一般工程用铸造碳钢件GB/T 5613 铸钢牌号表示方法GB/T 6060.1表面粗糙度比较样块铸造表面GB/T 15056铸造表面粗糙度评定方法GB/T 6414铸件尺寸公差与机械加工余量GB/T 11351铸件重量公差GB/ 223 钢铁及合金化学分析方法GB/ 228 金属拉伸试验方法GB/ T 229 金属材料夏比摆锤冲击试验方法GB/ 222 钢的成品化学成分允许偏差TB/T 1464 铁道机车车辆用碳钢铸件通用技术条件TB/T 1942铁路用铸钢件采购与验收技术条件TB/T 1583 机车车辆铸钢件焊补技术条件TB/T 2450 铸钢金相检验TB/T 3212 机车车辆用低合金铸钢金相组织检验图谱编制标准化实施日期校对审核工艺批准试行日期标记处数文件号签名日期3 术语、缩略语3.1 术语单铸试块:在单独制作的试块铸型中浇注的试块。
钢结构通用规范GB55006

钢结构通用规范GB55006住房和城乡建设部关于发布国家标准《钢结构通用规范》的公告现批准《钢结构通用规范》为国家标准,编号为GB 55006-2021,自2022年1月1日起实施。
本规范为强制性工程建设规范,全部条文必须严格执行。
现行工程建设标准相关强制性条文同时废止。
现行工程建设标准中有关规定与本规范不一致的,以本规范的规定为准。
本规范在住房和城乡建设部门户网站()上发布,由住房和城乡建设部标准与定额研究所在中国建筑出版传媒上发布。
住房和城乡建设部2021年4月9日废止的现行工程建设标准相关强制性条文1.《钢结构设计标准》GB 50017-2017第4.3.2、4.4.1、4.4.3、4.4.4、4.4.5、4.4.6、18.3.3条2.《冷弯薄壁型钢结构技术规范》GB 50018-2002第3.0.6、4.1.3、4.1.7、4.2.1、4.2.3、4.2.4、4.2.5、4.2.7、9.2.2、10.2.3条3.《高耸结构设计标准》GB 50135-2019第5.1.2、7.1.5条4.《构筑物抗震设计规范》GB 50191-2012第3.7.2(3)、5.1.1、7.7.7、8.2.14、8.2.15、9.2.3(1)、9.2.15(2)、10.2.7、10.2.10、10.2.15、11.2.8、12.2.7、13.2.8、22.2.4、22.2.9、22.2.11、22.4.5、24.2.4、24.2.11、24.3.5条(款)5.《钢结构工程施工质量验收标准》GB 50205-2020第4.2.1、4.3.1、4.4.1、4.5.1、4.6.1、4.7.1、5.2.4、6.3.1、8.2.1、11.4.1、13.2.3、13.4.3条6.《粮食钢板筒仓设计规范》GB 50322-2011第4.1.1、4.2.3、5.1.2、5.5.3(3)、6.4.2条(款)7.《钢结构焊接规范》GB 50661-2011第4.0.1、5.7.1、6.1.1、8.1.8条8.《钢结构工程施工规范》GB 50775-2012第11.2.4、11.2.6条9.《钢筒仓技术规范》GB 50884-2013第4.1.1、4.2.2、5.1.2、6.1.2条10.《机械工业厂房结构设计规范》GB 50906-2013第5.3.2、6.1.7、9.1.8(5)、9.6.12(9)条(款)11.《高耸与复杂钢结构检测与鉴定标准》GB 51008-2016第3.1.2、8.1.2条12.《门式刚架轻型房屋钢结构技术规范》GB 51022-2015第14.2.5条13.《高耸结构工程结构施工质量验收规范》GB 51203-2016第4.5.1、5.2.5、5.7.4条14.《空间网格结构技术规程》JGJ 7-2010第3.1.8、3.4.5、4.3.1、4.4.1、4.4.2条15.《钢结构高强度螺栓连接技术规程》JGJ 82-2011第3.1.7、4.3.1、6.1.2、6.2.6、6.4.5、6.4.8条16.《高层民用建筑钢结构技术规程》JGJ 99-2015第3.6.1、3.7.1、3.7.3、5.2.4、5.3.1、5.4.5、6.1.5、6.4.1、6.4.2、6.4.3、6.4.4、7.5.2、7.5.3、8.8.1条17.《轻型钢结构住宅技术规程》JGJ 209-2010第3.1.2、3.1.8、4.4.3、5.1.4、5.1.5条18.《低层冷弯薄壁型钢房屋建筑技术规程》JGJ 227-2011第3.2.1、4.5.3、12.0.2条19.《索结构技术规程》JGJ 257-2012第5.1.2、5.1.5条1 总则1.0.1 为保障钢结构工程质量、安全,落实资源能源节约和合理利用政策,保护生态环境,保证人民群众生命财产安全和人身健康,防止并减少钢结构工程事故,提高钢结构工程绿色发展水平,制定本规范。
铸件技术要求(清晰整齐)

1. 铸件零件图号:MPE2A300125BD001F 。
/材料A217 WC62. 铸件零件图号:MJP2A60025BF001N 。
/材料A217 WC9 此模具开金属蜡模/或石膏蜡模。
3. 铸件需要新开铸造模具;4. WC6铸造工艺:木模/砂型铸造/贴补浇道浇注工艺系统。
铸造工艺特点:按照JB/T 5263—2005标准规定铸件铸造过程中不得使用内冷铁和泥芯撑。
5. 铸件表面字牌、字体、摆放位置按照图纸技术要求执行。
6. 按照设计要求阀体材料执行标准为ASTM A217-WC6. 属压力容器部件,服役于高温高压应用工况环境。
适用于温度高达565℃,工作压力300P ;法兰和焊接端口阀门应用环境,有一些耐腐蚀和抗石墨化特质。
7. A217-WC6是铸造铬钼钢(高温高压用合金钢铸钢)ASTM A217 等级 WC6 8. WC6铸件材料化学成分:执行标准ASTM A217/A217M-2010;9. WC6铸造工艺过程中材料化学成分配比容许按照JB/T5263-2005表1规定:元 素材 料 级 别WC1WC6WC9C12A成 分,%C ≤0.25 0.05~0.20 0.05~0.18 ≤0.12 Mn 0.50~0.80 0.50~0.80 0.40~0.70 0.30~0.60 P ≤0.035 ≤0.035 ≤0.035 ≤0.020 S ≤0.040 ≤0.040 ≤0.040 ≤0.018 Si ≤0.60 ≤0.60 ≤0.60 0.20~0.50 Ni — — — ≤0.40 Cr — 1.00~1.50 2.00~2.75 8.0~9.5 Mo 0.45~0.650.45~0.650.90~1.200.85~1.05 Nb———0.060~0.10N———0.030~0.07010. 化学成分及机械性能见表211. WC6/WC9铸钢铸态正常金相组织为雾状铁素体(有钒的碳化物沉淀)+珠光体。
TSG特种设备安全技术规范 TSG Q0002-2007
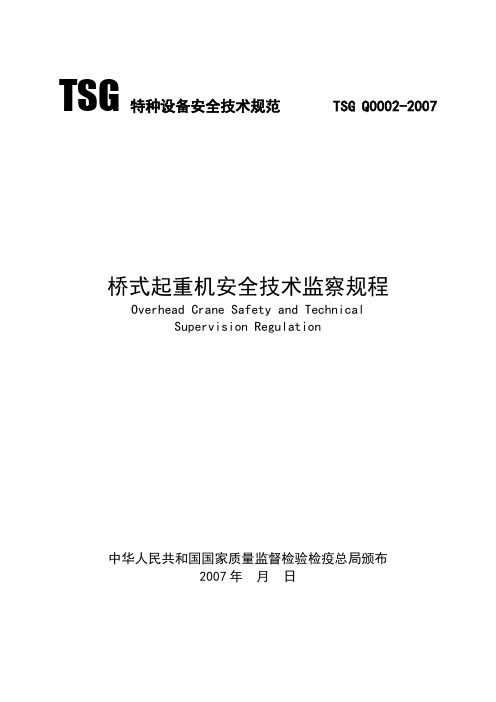
第五十一条钢丝绳的报废应当符合GB5972《起重机械用钢丝绳检验和报废实用规范》的规定。
第五章
第三十四条起升机构应当设置常闭式制动器。吊运熔融金属起重机的起升机构每套驱动系统需装设两套独立作用的制动器。吊运熔融金属的电动葫芦应设置工作制动器和安全制动器(制动卷筒)。
第三十五条起重机应当按GB6067的要求设置起重量限制器,当载荷超过规定的设定值时应当能自动切断起升动力源。吊运熔融金属的起重机起升机构(含以电动葫芦作为起升机构的起重机械)应设置起重量限制器。
第十六条起重机投入使用前,使用单位应当核对其是否附有本规程第六条、第七条、第八条和第十四条规定的相关资料。
第三章材料
第十七条起重机金属结构中主要受力构件的材料一般采用GB700《普通碳素结构钢技术条件》的普通碳素结构钢Q235A、Q235C或者GB1591《低合金结构钢技术条件》的低合金结构钢16Mn、16MnTi等。
本规程所称桥式起重机是指通用桥式起重机、电站桥式起重机、防爆桥式起重机、绝缘桥式起重机、冶金桥式起重机、架桥机、电动单梁起重机、电动悬挂起重机、柔性组合式悬挂起重机、电动葫芦桥式起重机和防爆梁式起重机。
本规程不适用于额定起重量小于1t或者提升高度小于2m的桥式起重机。
第三条本规程规定了桥式起重机(以下简称起重机)安全技术监察的基本要求。
第四十六条起重机应当在危险部位设置明显可见的安全警示标志,在操纵位置应当设置安全使用说明和控制报警信号。
第六章
铸钢的相关标准和知识

铸钢的相关标准和知识铸钢井盖采用GBT5613-1995国际及其它国家铸钢牌号表示方法(1)国际标准化组织(ISO)“一般工程用铸造碳钢”和“一般工程与结构用高强度铸钢”均按屈服强度和抗拉强度分级,高合金铸钢以化学成分表示牌号。
(2)美国试验与材料学会(ASTM)一般工程用碳钢铸件(ASTM A27/A27M),高强度铸钢结构件(ASTM A148/A148M)和公路桥梁用铸钢件(ASTM A486/A486M)均按强度分级。
高合金铸钢采用美国合金铸造协会(ACI)的表示方法。
(3)日本标准(JIS)日本铸钢牌号前冠以大写字母SC,其后,不同用途的铸钢采用特定的字母和数字表示牌号。
一般碳素铸钢件的牌号用强度表示,在SC后的三位数字,即抗拉强度(MPa)的最低值。
焊接结构用铸钢件的牌号也用强度表示,在SC后加字母W表示焊接用,再用数字表示最低抗拉强度(MPa)。
结构用高强度碳钢及低合金钢按合金元素分类。
碳钢为SCC,后加一分类号。
低锰钢为SCMn,后加一分类号。
锰铬钼钢为SCMnCrMo,后加一分类号。
在SC后,加字母“S”表示铸造不锈钢,加“H”表示耐热铸钢,加“PH”表示高温用压力容器铸钢,加“PL”表示低温压力容器铸钢。
其后加1~2位数字的顺序号。
(4)德国标准(DIN)所有碳素钢铸钢和低合金铸钢牌号均冠以大写字母GS。
一般铸钢件按强度分级,在GS后加一组二位数字,表示抗拉强度(1/10MPa)。
要求焊接性能较好的铸钢及合金钢则以化学成分表示牌号。
(5)英国标准(BS)英国有三种铸钢系列:BS3100为一般工程用铸钢件。
BS3146金属熔模精铸件,其中第一部分为碳钢和低合金钢,第二部分为耐蚀热钢,第三部分为真空熔炼的合金。
BS1504为承压的铸钢件,其中碳钢铸件为一组(BS1504—161),牌号为三位数字,即抗拉强度(MPa)。
低、中合金钢牌号按成分分为8种,高合金钢的牌号与BS3100相同。
铸钢件综合技术条件
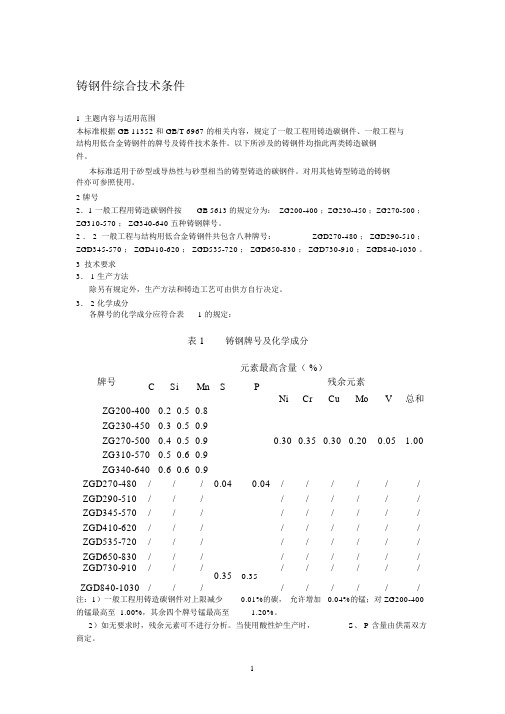
铸钢件综合技术条件1 主题内容与适用范围本标准根据 GB 11352 和 GB/T 6967 的相关内容,规定了一般工程用铸造碳钢件、一般工程与结构用低合金铸钢件的牌号及铸件技术条件。
以下所涉及的铸钢件均指此两类铸造碳钢 件。
本标准适用于砂型或导热性与砂型相当的铸型铸造的碳钢件。
对用其他铸型铸造的铸钢件亦可参照使用。
2 牌号2.1 一般工程用铸造碳钢件按GB 5613 的规定分为: ZG200-400 ;ZG230-450 ;ZG270-500 ;ZG310-570 ; ZG340-640 五种铸钢牌号。
2 . 2 一般工程与结构用低合金铸钢件共包含八种牌号: ZGD270-480 ; ZGD290-510 ;ZGD345-570 ; ZGD410-620 ; ZGD535-720 ; ZGD650-830 ; ZGD730-910 ; ZGD840-1030 。
3 技术要求 3. 1 生产方法除另有规定外,生产方法和铸造工艺可由供方自行决定。
3. 2 化学成分各牌号的化学成分应符合表1 的规定:表 1铸钢牌号及化学成分元素最高含量( %) 牌号CSiMn SP残余元素CrCuMoV总和NiZG200-400 0.2 0.5 0.8 ZG230-450 0.3 0.5 0.9ZG270-500 0.4 0.5 0.9 0.30 0.35 0.30 0.20 0.05 1.00ZG310-570 0.5 0.6 0.9 ZG340-640 0.6 0.6 0.9ZGD270-480 / / / 0.04 0.04 // / / / / ZGD290-510 / / / / / / / / / ZGD345-570 / / / / / / / / / ZGD410-620 / / / / / / / / / ZGD535-720 / / / / / / / / / ZGD650-830 / / // / / / / / ZGD730-910 / / / 0.35 / / / / / / ZGD840-1030 ///0.35//////注:1)一般工程用铸造碳钢件对上限减少 0.01%的碳, 允许增加 0.04%的锰;对 ZG200-400的锰最高至 1.00%,其余四个牌号锰最高至 1.20%。
- 1、下载文档前请自行甄别文档内容的完整性,平台不提供额外的编辑、内容补充、找答案等附加服务。
- 2、"仅部分预览"的文档,不可在线预览部分如存在完整性等问题,可反馈申请退款(可完整预览的文档不适用该条件!)。
- 3、如文档侵犯您的权益,请联系客服反馈,我们会尽快为您处理(人工客服工作时间:9:00-18:30)。
一般工程与结构用铸钢件的技术标准
一般工程与结构用铸钢件均需进行热处理,常用的热处理工艺有:退火;正火;正火+回火;淬火+回火。
通常,除另有规定外,铸件热处理工艺均由供方决定。
因此,在制订一般工程与结构用铸钢件的技术要求时,一般不把铸件热处理工艺做为主要技术要求提出。
我国制定有适用于常温下使用的“一般工程与结构用铸钢件”标准(GB/T14408-1993),并明确规定了一般工程与结构用铸钢件的要求。
通常,一般工程与结构用铸钢件的技术要求,主要应包括:力学性能,化学成分,焊补,热处理,几何形状及尺寸。
表面质量和缺陷,尺寸公差,加工余量等,并可参见下表:
一般工程与结构用铸钢件的技术要求。