物料输送线plc控制系统设计
自动送料装车系统PLC控制设计

自动送料装车系统PLC控制设计在设计自动送料装车系统的PLC控制时,需要考虑以下几个方面。
首先是系统的硬件设计。
自动送料装车系统的硬件设备包括传感器、执行器、电机控制器等。
传感器用于检测物料的位置和状态,如光电传感器可以检测物料的到位和离开状态,压力传感器可以检测物料的重量和压力等。
执行器用于控制物料的移动和装载,如气缸可以用于推动物料的移动,电机可以用于驱动输送带的运动。
电机控制器用于控制电机的启停和速度调节。
在PLC控制设计中,需要根据实际需求选取合适的硬件设备,并配置相应的输入输出端口。
其次是系统的逻辑控制。
自动送料装车系统的逻辑控制包括物料的检测、移动和装载的逻辑控制。
通过光电传感器等传感器检测物料的位置和状态,PLC可以根据这些信号对电机和执行器进行控制,实现物料的移动和装载。
例如,当光电传感器检测到物料到位时,PLC可以控制执行器将物料推动到指定位置;当光电传感器检测到物料离开时,PLC可以控制电机停止运动。
在逻辑控制设计中,需要根据实际流程和要求,编写PLC的逻辑程序,明确各个信号的处理方式和相应的控制动作。
最后是系统的安全设计。
在自动送料装车系统中,安全性是一个非常重要的考虑因素。
系统设计应该考虑到可能出现的故障和意外情况,并采取相应的安全措施。
例如,可以在输送带上设置紧急停止按钮,一旦发生紧急情况,可以立即停止输送带的运动;可以在执行器上设置限位开关,一旦执行器超过了安全范围,可以自动停止运动。
同时,还应考虑到保护设备的安全性设计,如安装防护罩,避免人员接触到危险部位。
在安全设计中,需要充分考虑系统的各个环节和可能的风险,并采取相应的措施保障工作人员的安全。
综上所述,自动送料装车系统的PLC控制设计主要包括硬件设计、逻辑控制和安全设计。
通过科学合理地设计PLC控制系统,可以提高自动送料装车系统的稳定性和效率,实现工业生产的自动化控制。
基于PLC的物料分拣传送控制系统的设计与实现

基于PLC的物料分拣传送控制系统的设计与实现1. 引言1.1 背景介绍物料分拣传送系统是现代生产线中必不可少的一部分,它可以有效地提高物料分拣的效率和准确性,降低人工成本和错误率。
传统的物料分拣传送系统多采用人工操作或简单的机械传送装置,存在着工作效率低、错误率高、适应性差等问题。
随着科技的不断发展和进步,基于PLC的物料分拣传送控制系统应运而生,它利用先进的电气控制技术和自动化技术,实现了传统系统无法实现的功能和优势。
基于PLC的物料分拣传送控制系统具有高性能、可靠性强、灵活性好等特点,可以根据不同的需求和物料特性进行个性化定制,能够满足现代生产线对物料分拣传送的高效、精准要求。
在自动化生产中,PLC已经成为控制系统的核心部件,广泛应用于各种领域,包括工业自动化、交通运输、能源设备等。
因此,研究基于PLC的物料分拣传送控制系统的设计与实现具有重要的意义和价值。
通过此研究,可以提高生产线的自动化水平,提升生产效率,降低成本,实现智能化生产,促进工业的发展和进步。
1.2 研究意义基于PLC的物料分拣传送控制系统能够实现对物料的高效分拣和传送,提高了生产效率和质量,降低了人力成本,使生产过程更加智能化。
这对于促进制造业转型升级,提高企业竞争力具有重要意义。
基于PLC的物料分拣传送控制系统能够实现物料的实时监测和数据采集,为生产过程提供了重要的数据支撑。
通过数据分析和处理,可以实现生产过程的优化和智能化管理,提高生产效率和质量。
基于PLC的物料分拣传送控制系统具有灵活性强、可靠性高、成本低等诸多优点,适用于各种规模和类型的制造企业。
研究基于PLC 的物料分拣传送控制系统的设计与实现,对于推动工业自动化发展,提高制造业水平,具有重要的理论和实践价值。
1.3 研究目的本文旨在设计和实现一种基于PLC的物料分拣传送控制系统,旨在解决传统物料分拣传送系统中存在的一些不足之处,提高物料分拣传送效率和准确性。
具体目的包括:1. 研究分析传统物料分拣传送系统的设计原理和工作流程,总结其优缺点;2. 提出基于PLC的物料分拣传送系统设计方案,探讨其适用性和优势;3. 进行PLC编程与控制逻辑设计,确保系统能够稳定运行并实现准确的物料分拣传送;4. 设计物料传送控制系统的硬件,选择合适的传感器、执行器等设备,保证系统可靠性和稳定性;5. 进行系统实验并对实验结果进行分析,评估系统的性能和可靠性;6. 评估设计与实现的效果,找出存在的问题并提出改进方向;7. 展望未来,探讨如何进一步完善基于PLC的物料分拣传送控制系统,提高其智能化和自动化水平。
物料输送线plc控制系统设计

物料输送线plc控制系统设计内容摘要:物料输送线在工场中,生产车间内都起到了主要的地位。
他直接关系到工厂的生产运作,能否有效的正常进行。
为此,本文对物料输送线做了相关研究。
现代生活中实现自动化是必不可少的,这不仅可以让工人们的劳动力从重力劳动力种脱离,还为生产提高了效率是过程更加准确。
再在其中运用PLC可编程控制系统,来实现整个生产过程的全自动化。
关键字:物料输送线;PLC可编程控制系统;自动控制一、绪论1、国内外PLC的发展状况及发展趋势现国内外的发展状况都是再往集成和开放化的发展。
编程平台与计算机语言的相结合。
全集成自动化能把工厂的所有监控采集与控制用硬件和软件集成能够把整个工厂的所有设备连接起来,并使所有设备运行,生产的安排,机器和工厂情况等,数据采集查询,都能核算集成到一个系统里。
现在PLC的应用随着时间的推移已经运用到越来越多的领域,讲渗透到各个工厂工业领域。
目前PLC正朝着两个方向不断发展,一个是超小型化,微型化,另一个是朝超大规模化,功能更加齐全的方向发展。
近年来,它在工业自动化、机电一体化、传统产业技术等方面的应用越来越广泛,已广泛应用在机械,汽车,电力,冶金,石油,化工,交通,运输,轻工,纺织,建材,采矿以及家用电器等领域,取得了明显的技术经济效益,成为现代工业控制三大支柱之一。
2、课题的研究意义现今随着时代的发展,各种工厂中都应用输送线来带动生产,带动经济的发展。
同时,工厂中已经很少有工人来搬运运输,取之代之的则是皮带运输,因此,对物料输送线的研究变得很有必要。
物料输送线,顾名思义就是运用的皮带来输送物料。
但是现场的皮带控制还是有人工操作,为了提高在工作效率,节省人力,改善工作环境,将皮带改为自动化变得很有必要,从而达到节省人力,提高效率的作用。
设计一套可行的PLC控制系统,该技术可大量节省资金,大大节省人力。
3、主要研究内容和要求内容:本文主要是研究PLC如何对生产线进行准确的控制,PLC如何通行对整个工厂内的设备的控制。
基于PLC的传送带控制系统设计

基于PLC的传送带控制系统设计第一章:引言1.1 研究背景随着工业自动化的发展,传送带在各个行业中被广泛应用。
传送带控制系统是其中重要的组成部分,它通过精确的控制实现物品的运输和分拣,提高生产效率和质量。
PLC(可编程逻辑控制器)作为一种可编程电子系统,具备高性能和可靠性,逐渐成为控制传送带系统的首选。
1.2 研究目的和意义本文旨在设计一种基于PLC的传送带控制系统,通过对传送带的运行状态进行监测和控制,实现物品的准确分拣和运输。
这对于提高传送带系统的工作效率和减少人力成本具有重要意义。
同时,本文的研究成果可以为其他控制系统的设计和优化提供参考。
第二章:传送带的工作原理和要求2.1 传送带的工作原理传送带由电动机、驱动轮、输送带和支撑构架等部分组成。
电动机通过驱动轮带动输送带运行,物品通过传送带在不同工位之间进行传送。
传送带控制系统需要根据实际需求,对传送带的运行速度、方向和起停等进行准确控制。
2.2 传送带控制系统的要求传送带控制系统首先需要具备良好的稳定性和可靠性,能够长时间稳定运行。
其次,系统需要具备高度的灵活性和扩展性,能够适应不同工况和物品的运输需求。
还需要实现对传送带的自动监测和报警功能,及时发现和修复故障。
第三章:基于PLC的传送带控制系统设计3.1 系统结构设计基于PLC的传送带控制系统由PLC主控单元、输入输出模块、传感器和执行器组成。
PLC主控单元负责控制传送带的运行状态,输入输出模块用于与外界进行信号交互,传感器用于监测传送带的运行情况,执行器用于控制传送带的运行。
3.2 PLC程序设计PLC程序设计是传送带控制系统设计的核心。
根据控制需求,设计PLC程序实现传送带的控制逻辑。
程序需要根据传感器的信号进行判断,控制执行器的动作,精确控制传送带的运行速度、方向和起停等功能。
3.3 传感器选择和布置传感器是实现对传送带运行状态监测的重要组成部分。
本文选择xx型传感器,该传感器具有良好的稳定性和高度的灵敏度。
基于PLC的传送带控制系统设计

基于PLC的传送带控制系统设计第一章:引言1.1 研究背景传送带是工业生产中常用的一种输送装置,广泛应用于物流、制造业、矿山和港口等各个领域。
为了提高生产效率和操作安全性,设计一个高效可靠的传送带控制系统至关重要。
本章将介绍基于PLC的传送带控制系统设计的背景和意义。
1.2 研究目的本研究的目的是设计一个基于PLC的传送带控制系统,通过自动化控制实现传送带的启动、停止、速度调节、倾斜角度控制等功能。
同时,通过传感器和监控设备实时监测传送带的工作状态,并及时报警和记录异常情况,提高生产效率和安全性。
第二章:传送带控制系统的总体架构2.1 传送带控制系统概述传送带控制系统由传送带本体、传感器、PLC控制器、人机界面和监控设备等组成。
其中,PLC控制器作为核心部件负责接收传感器信号并根据设定的逻辑和算法实现对传送带的控制。
2.2 传送带控制系统的工作流程本节将详细介绍传送带控制系统的工作流程,包括传感器信号采集、PLC控制算法实现、控制指令发送和监控设备数据处理等环节,以及各环节之间的数据流动和逻辑关系。
第三章:传送带控制系统的详细设计3.1 传感器信号采集为了实现对传送带的状态监测和控制,需要采集传感器的信号,包括传送带的速度、倾斜角度、工作温度等信息。
本节将介绍常用的传感器类型和其工作原理,并设计合适的信号采集电路进行数据获取。
3.2 PLC控制算法实现PLC控制器负责接收传感器信号并进行逻辑判断和控制指令生成。
本节将详细阐述传送带控制的算法设计,包括启动和停止控制、速度调节、倾斜角度控制和异常情况处理等。
3.3 控制指令发送PLC控制器通过各类输出模块将控制指令发送给传送带的电机、液压装置等执行机构。
本节将设计合适的接口电路和通信协议实现可靠的指令传输。
3.4 监控设备数据处理监控设备负责实时监测传送带的工作状态,并及时报警和记录异常情况。
本节将介绍监控设备的选型和接口设计,以及数据处理算法的实现。
传送带PLC控制系统设计

传送带PLC控制系统设计一、本文概述Overview of this article随着工业自动化水平的不断提升,传送带作为物流和生产流程中的关键环节,其控制系统设计变得愈发重要。
本文将深入探讨《传送带PLC控制系统设计》的相关内容,旨在为读者提供一套全面、高效的传送带控制系统设计方案。
文章将首先介绍传送带PLC控制系统的基本概念、发展历程以及其在工业自动化领域的应用价值。
随后,文章将详细阐述PLC控制系统的硬件组成、软件编程以及系统调试等关键环节,并结合实际案例进行分析。
文章还将探讨传送带PLC控制系统设计中的常见问题及解决方案,为读者在实际应用中提供有益参考。
通过本文的阅读,读者将能够深入了解传送带PLC控制系统的设计原理和实践方法,为工业自动化领域的发展贡献力量。
With the continuous improvement of industrial automation level, the control system design of conveyor belts, as a key link in logistics and production processes, has become increasingly important. This article will delve into the relevant content of "Design of PLC Control System for ConveyorBelt", aiming to provide readers with a comprehensive and efficient design scheme for conveyor belt control system. The article will first introduce the basic concept, development history, and application value of PLC control system for conveyor belts in the field of industrial automation. Subsequently, the article will elaborate in detail on the hardware composition, software programming, and system debugging of the PLC control system, and analyze them in conjunction with practical cases. The article will also explore common problems and solutions in the design of PLC control systems for conveyor belts, providing useful references for readers in practical applications. Through reading this article, readers will be able to gain a deeper understanding of the design principles and practical methods of PLC control systems for conveyor belts, contributing to the development of industrial automation.二、传送带基础知识Fundamentals of conveyor belts传送带作为工业生产和物流运输中的关键设备,广泛应用于各个行业。
项目五 PLC实现物料输送线控制

任务四 PLC实现对物料输送线控制
16位计数器工作过 程示意图
任务四 PLC实现对物料输送线控制
2.32位双向计数器 32位双向计数器可以进行加计数或减计数,其地址为 C200~C234,其中C200~C219为断电复位型,C220~ C234为断电保持型。 32位双向计数器可用常数K或数据寄存器D的内容作为 设定值,设定的范围是:-2147483648~+2147483647。 使用数据寄存器设定计数值时,须使用两个地址相邻的数据 寄存器。 C200~C234分别对应特殊辅助继电器M8200~ M8234,当特殊辅助继电器接通(置1)时,双向计数器为 减计数器,断开(置0)时,为加计数器。
时序图
项目五 PLC实现对物料输送线控制
(5)PLS指令应用于通电延时
采用启保停电路的通电延时电路
SET、RST指令的通电延时电路
项目五 PLC实现对物料输送线控制
(6)PLF指令应用断电延时。
采用启保停电路的断电延时电路
采用SET、RST指令的断电延时电路
项目五 PLC实现对物料输送线控制
二、 LDP与LDF
(1)掌握物料输送线计数控制及计数器使用,熟悉实际应用中 的手动和自动控制 (2)掌握利用PLC进行对象控制时,I/O点的确定,能实际正 确接线。 (3)学会使用脉冲类指令触发控制并编写梯形图。
项目五 PLC实现对物料输送线控制
任务一 控制分析与硬件连接
一、 控制任务分析
图为物料输送线,要求运输带 电机启动2秒后,皮带秤电机才 能转动送料。同样地,只有当 皮带秤电机停止8秒后,输送带 上的物料才能运空,输送带电 机才能停止。
一、 PLS与PLF 1. PLS指令
时序图
物料输送线plc控制系统设计

张 苏 友
( 江 苏 城 市 职业 学 院张 家 港 办 学 点 , 江 苏 张家 港 现 国 内外 的发 展 状 况 都 是 往 集 成 和开 放 化 方 向发 展 , 编 程 平 台 与 计 算 机 语 言 相结 合 。 全集 成 自动化 能把 工 厂 的所 有 监 控 采 集 与 控 制 用 硬 件 和 软 件 集 成 ,把 整个 工 厂 的 所 有设 备 连接起来 . 并 使 所 有设 备 运 行 , 生 产 的安 排 、 机 器 和 工 厂 的 情 况等 . 通 过数 据 采 集 查 询 , 都 能 核 算 集成 到一 个 系 统 里 。
2 . P L C控 制 程 序 流 程 设 计
引入 P L C 可 编 程 控 制 器 可 以解 决 很 多 问题 。 其 具 有 的保 护 内 容有 : 胶 带 跑偏 , 胶 带 车 控 制 回路 故 障 , 胶 带 控 制 凹路 故 障 , 位 置信 号 丢 失 , 堆 料, 满 仓 信号 提 示 等 。 该 系统 的特 点 是 : 性 能 稳定 , 扩展能力强 . 技术含量高 , 维修 、 维护 、 系 统 改 造 方 便 灵 活, 遇到紧急事故能及时停车 , 发 出声 光 报 警 信 号 . 能 及 时 适 应 生 产现 场 需 要 , 确保 输送 机 的 安全 正 常 进行 。 具 有 广 泛 的适 应 性 和推 广 价 值 。 2 . 输 送 线的 日常 保 养 ( 1 ) 输 送 线 的 输送 带 负 荷过 大 出 现 打 滑 , 超 出 了 自身 的负 荷能力 。 此 时 应 当减 轻 输 送 物 料 的 运 输 量 或 者 增 加 输 送 机 的 本 身 的承 重 力 , 避 免打 滑 的现 象 出 现 。 ( 2 ) 输 送 线 的 启 动 速 度 太快 造成 打 滑 , 此 时 应 当慢 速 启 动 或 再 次点 动 两 下 后 重 新 启 动 , 可 以克 服 打 滑 的现 象 。 ( 3 ) 初张 力太 小 , 原 因是输送 带 在离开 滚筒 时的 张力不 够 , 造 成输送 带 打滑 , 此 时处 理的方 法是 调整拉 紧装 置 , 加 大初 张力 。 ( 4 ) 滚筒的轴承损坏而不运转 , 原 因可 能 是 轴 承 内部 灰 尘 积 聚 太 多 ,或 是 没 有 及 时 检 修 和 更 换 已被 严 重 磨 损 而 转 动不 灵 活 的部 件 , 造 成 阻力 增 大 而 打 滑 。 三、 P I 控 制 系 统 的 抗 干扰 设 计
PLC物料运输控制系统

PLC物料运输控制系统简介在工业生产过程中,物料的运输控制是一个至关重要的环节。
PLC(Programmable Logic Controller)物料运输控制系统作为一种可编程逻辑控制器,为物料的运输过程提供了可靠的控制和监测手段。
本文将介绍PLC物料运输控制系统的原理、组成和工作流程,同时探讨其在工业生产中的应用。
原理PLC物料运输控制系统的原理基于可编程逻辑控制器的运行。
PLC是一种专门设计用于工业自动化控制的计算机控制系统,其内部包含多种传感器、执行器和通信接口。
通过PLC 的编程软件,用户可以灵活地配置控制逻辑和运行参数,以实现对物料运输过程的精确控制。
组成PLC物料运输控制系统主要由以下组成部分构成:1.PLC主控单元:PLC主控单元是整个系统的核心,负责接收和处理传感器信号,同时根据用户编写的控制逻辑进行计算和决策。
PLC主控单元通常具有高性能的处理器和大容量的存储器,以支持复杂的控制算法和数据存储。
2.传感器:传感器用于感知物料运输过程中的各种参数,例如物料的位置、速度、温度等。
常见的传感器包括光电开关、压力传感器、温度传感器等。
通过与PLC主控单元的通信接口,传感器将实时采集到的数据发送给PLC进行处理。
3.执行器:执行器用于在物料运输过程中实施控制。
根据PLC主控单元的指令,执行器可以对物料进行推、拉、旋转等动作。
常见的执行器包括电动阀门、马达、气缸等。
4.通信接口:通信接口用于与其他设备进行数据交换和信息传递。
例如,PLC物料运输控制系统可以通过以太网接口与上位机通信,将采集到的数据上传到数据库,或接收来自上位机的控制指令。
工作流程PLC物料运输控制系统的工作流程通常包括以下几个步骤:1.传感器采集数据:传感器实时采集物料运输过程中的各种参数,如物料的位置、速度、温度等。
采集到的数据通过通信接口发送给PLC主控单元。
2.PLC主控单元处理数据:PLC主控单元接收传感器发送的数据,并根据用户编写的控制逻辑进行计算和决策。
基于PLC的物料运送控制系统的设计

基于PLC的物料运送控制系统的设计一、概述物料运送控制系统是指通过使用可编程逻辑控制器(PLC)来控制物料的运输过程,以提高生产效率和减少人力成本。
本文将介绍一个基于PLC的物料运送控制系统的设计方案。
二、系统架构该物料运送控制系统主要由以下组件组成:传感器、执行器、PLC和人机界面(HMI)。
传感器用于监测物料的位置和状态,执行器用于控制物料的运输,PLC用于收集传感器数据、进行逻辑控制和发送指令,HMI 用于显示系统状态和操作。
三、系统功能1.实时监测和控制物料位置:通过安装传感器,可以实时监测物料的位置,并将该信息传输给PLC。
PLC可根据传感器数据控制执行器来实现物料的精确定位和运输。
2.自动化物料运输:PLC可以通过编写逻辑控制程序自动控制物料的运输,如启动和停止执行器、调整执行器的运行速度等。
系统可以根据任务需求和进料情况自动调整物料的运输速度,以提高生产效率和降低物料损耗。
3.报警和异常处理:系统可以通过传感器监测物料的位置和状态,一旦发现异常情况(如物料脱落、堵塞等),PLC可以发送报警信号,并通过HMI向操作员显示详细信息。
操作员可以及时采取措施进行处理。
4.可编程性和灵活性:PLC具有高度的可编程性,可以根据生产需求进行灵活调整。
通过修改控制程序,系统可以适应不同的物料类型、运输方式和生产线布局。
四、系统设计步骤1.确定物料运输需求:根据工厂的物料运输需求和生产流程,确定物料运输的起点、终点、运输距离和速度要求。
2.选择传感器和执行器:根据需要监测的物料位置和状态,选择适合的传感器。
根据物料运输的要求,选择适合的执行器,如电动滚筒、输送带等。
3.设计PLC控制程序:根据物料运输的需求和执行器的特性,编写PLC控制程序。
程序应包括物料位置监测、执行器控制、报警处理等功能。
4.设计HMI界面:根据系统需求和操作员的操作习惯,设计直观、易用的HMI界面。
界面应包括系统状态显示、参数设置、报警信息显示等功能。
「自动送料装车系统PLC控制设计」

「自动送料装车系统PLC控制设计」自动送料装车系统是一种可以实现自动化物料输送和装车的系统。
PLC(可编程序逻辑控制器)是一种常用于工业自动化控制的设备,用于控制和管理自动化设备的运行。
在设计自动送料装车系统的PLC控制时,需要考虑以下几个方面:1.传感器和执行器的选择:传感器用于检测物料的位置、数量和状态,执行器用于控制物料的运动。
根据具体需求,可以选择适合的传感器和执行器,并将它们连接到PLC上。
2.输入和输出界面的设计:PLC通常具有输入和输出接口,用于与外部设备进行数据交换。
输入接口可用于接收来自传感器的信号,输出接口可用于控制执行器的运动。
设计输入和输出界面时,要考虑设备连接的类型和数量,并确定合适的接口类型和数量。
3.控制逻辑的编程:PLC控制逻辑的编程是实现自动送料装车系统的关键。
根据系统的工作流程和需求,设计适当的控制算法和逻辑,编写PLC程序。
程序中应包括物料输送的控制、装车操作的控制以及故障检测和处理等功能。
4.故障检测和处理机制的设计:自动送料装车系统在运行过程中可能会出现各种故障,如传感器故障、执行器故障等。
为了确保系统的稳定和可靠性,需要设计故障检测和处理机制。
可以通过监测传感器和执行器的状态来检测故障,并采取相应的措施进行处理,例如报警、停止系统运行等。
综上所述,自动送料装车系统的PLC控制设计需要考虑传感器和执行器的选择、输入和输出界面的设计、控制逻辑的编程以及故障检测和处理机制的设计。
通过合理的设计和编程,可以实现自动化物料输送和装车,提高生产效率和质量。
四节传送带PLC模拟控制系统

电机
驱动传送带运转的动力来源, 通常采用三相异步电机。
传送带
承载物料,通过连续运动将物 料从一个位置输送到另一个位 置。
控制系统
由PLC、继电器、接触器等组 成,用于控制电机启停、调节 传送带速度等。
工作原理
当物料放置在传送带上时,传感 器检测到物料的数量和位置信息。
PLC控制系统根据传感器反馈的 信息,控制电机的启停和转速,
进入20世纪后,随着自动化技术的不断发展,PLC等控制系 统的出现,传送带的发展也进入了新的阶段。四节传送带 PLC模拟控制系统就是其中的代表之一,它能够实现对传送 带的精确控制,提高了生产效率和产品质量。
02
四节传送带系统
系统构成
减速器
降低电机转速,增大扭矩,使 传送带能够平稳运行。
传感器
检测传送带上物料的数量、位 置等信息,为PLC控制系统提 供反馈。
特点
高可靠性、灵活性、易于编程和易于扩展等。
PLC的工作原理
输入采样
PLC读取输入端子的状态,并将 其存储在输入映像寄存器中。
程序执行
PLC按照从上到下的顺序扫描用户 程序,并根据输入映像寄存器中的 数据执行相应的逻辑运算或指令。
输出更新
在程序执行完成后,PLC将输出映 像寄存器中的数据写入到输出模块, 从而控制外部设备。
模拟控制系统的搭建
确定系统规模和要求
选择合适的PLC
根据实际需求,确定控制系统的规模和功 能要求,如控制节数、传送带速度、物料 检测等。
根据系统规模和要求,选择合适的PLC型号 和规格,确保其具有足够的输入输出点数 、处理速度和通讯能力。
配置输入输出模块
编写控制程序
根据实际控制需求,配置适当的输入输出 模块,如限位开关、传感器、电磁阀等。
基于S7-1200PLC的带式输送机自动控制系统设计

基于S7-1200PLC的带式输送机自动控制系统设计摘要:输送带在带式输送机中作为牵引及承载构件得到了广泛地应用,通过输送带的移动来实现的,实现高效输送物料的连续输送设备。
在现代工业不断发展,自动化水平不断提高的背景下,人们对生产过程的监控有了更多的需求。
S7-1200是西门子公司最新推出的一款可编程逻辑控制器(PLC),旨在满足各类用户对自动化控制任务的高精度和简单要求。
阐述带式输送机的工业应用及其发展趋势。
以西门子S7-1200PLC为例,搭建了保证带式输送机稳定工作的高效电气控制系统。
实际工程应用结果表明,本系统实现带式输送机自动控制,对带式输送机系统设备进行监测。
关键词:带式输送机;自动控制;S7-1200PLC引言带式输送机是一种广泛应用的运输设备,利用S7-1200PLC对带式输送机的智能控制系统进行设计。
本系统将PLC控制箱,视频监控等设备配置于带式输送机头部,对带式输送机作业过程中各项数据信息进行实时采集,及时发现作业过程中出现的问题并对故障进行检测和报警处理,还利用变频调速技术根据料流情况对带式输送机作业速度进行合理控制,从而有效减少能源消耗,使带式输送机实现无人值班,将蹲岗变成巡岗。
1系统控制要求通过西门子WinCC组态软件对现场输送机运行情况进行实时反馈,并与多种传感保护装置相配合最终组成带式输送机高效电气控制系统。
在现代工业不断发展,自动化水平不断提高的背景下,人们对生产过程的监控有了更多的需求。
该系统能够实时监测输送带跑偏检测设备,打滑检测设备,纵向撕裂防护设备,溜槽堵塞防护设备,料流检测设备,双向拉绳开关故障信号等,并通过控制驱动电机的起动,保护及停止等动作来实现自动化控制。
设计时充分考虑到可能存在的种种问题及解决办法,做到更完善、可靠。
现将具体条件限定如下。
(1)本实用新型提供一种输送带偏移检测设备。
如果皮带没有按规定时间纠偏至合适位置,表明输送带已经发生一定偏移。
基于PLC运输及控制系统的设计

【摘要】 (2)【前言】 (3)【三菱可编程控制器介绍】 (5)1.1FX2N系列PLC的结构特点 (6)1.2FX2N系列PLC的基本组成 (7)【FX2N系列可编程控制器内部元件及功能】 (8)1.21输入继电器(X0) (8)1.22输出继电器(Y) (8)1.23辅助继电器(M) (8)1.24状态器(S) (9)1.25定时器(T) (9)1.26计数器(C) (10)1.27数据寄存器(D) (11)1设计目的 (13)2设计思路 (13)3设计过程 (13)3.1PLC输入/输出端子接线图 (13)3.2程序设计 (14)3.3皮带传输机控制原理 (17)4系统调试与结果…………………………………………………………………………..18/4.1系统调试 (18)4.2调试结果 (18)5主要元器件与设备 (19)6课程设计体会与建议 (20)7参考文献 (21)8附录 (22)8.1指令语句表 (22)8.2梯形图 (24)摘要皮带运输机是当代最为得力的输送设备之一,在整个输送机范畴中,它是应用最为广泛的一种设备,它的产生已有上百年的历史了,现以成为冶金、矿山、水泥、码头、化工、粮食等行业最主要的运输工具。
早期皮带运输机由于其功率小、运距短、速度低,应用受到一定限制。
现针对皮带运输机控制系统中存在的问题,把可编程序控制器和变频器应用于皮带运输机控制系统上,利用可编程控制器取代继电器进行控制皮带运输机的起动和停止。
提高了系统的可靠性,系统的调速控制采用变频器进行变频调速,使调速性能更加稳定,保证了可靠。
输送机是在一定的线路上连续输送物料的物料搬运机械,又称连续输送机。
输送机可进行水平、倾斜和垂直输送,也可组成空间输送线路,输送线路一般是固定的。
输送机输送能力大,运距长,还可在输送过程中同时完成若干工艺操作,所以应用十分广泛。
可以单台输送,也可多台组成或与其他输送设备组成水平或倾斜的输送系统,以满足不同布置形式的作业线带式输送机是输送能力最大的连续输送机械之一。
PLC控制系统设计步骤_设计实例

PLC控制系统设计步骤_设计实例PLC(可编程逻辑控制器)控制系统是工业自动化中常用的控制技术之一,用于对工业设备和过程进行自动化控制。
PLC控制系统设计步骤主要包括需求分析、硬件设计、软件编程、测试和调试等环节。
下面将详细介绍PLC控制系统设计步骤,并给出一个设计实例。
1.需求分析在PLC控制系统设计前,我们首先需要进行需求分析。
这包括确定系统的功能需求、性能需求和特殊要求等。
例如,我们可能需要控制一个自动包装机,需求可能包括控制机械手的运动、监测传感器信号、实现自动物料进料等功能。
2.硬件设计在进行硬件设计之前,我们需要确定PLC的类型和规格。
根据需求分析的结果和实际应用场景,选择合适的PLC型号,并确定所需的输入输出(I/O)点数和通信接口等。
在硬件设计过程中,需要选择和配置适当的传感器、执行器、电源、连接器等设备,并进行布置和布线。
3.软件编程4.测试和调试5.系统部署和维护在完成测试和调试后,我们可以将PLC控制系统投入实际应用中。
在系统部署过程中,我们需要将PLC安装到设备或机柜中,并与其他设备进行连接和集成。
同时,我们还需要进行系统文档化、培训和备份等工作,以便后续的维护和升级。
接下来,我们将以一个简单的物料输送系统为例,说明PLC控制系统设计步骤。
假设我们需要设计一个物料输送系统,实现自动化的物料输送和分拣功能。
系统包括一个传送带、传感器检测装置和执行机构,其主要功能包括根据传感器信号控制传送带的启停和速度调节、将物料分拣到不同的出口等。
1.在需求分析阶段,我们确定了系统的功能需求和性能要求,并分析了系统实现的过程和约束条件。
2.在硬件设计过程中,我们选择了一款具有足够的输入输出点数和通信接口的PLC型号,并选择适当的传感器和执行器等设备。
3. 在软件编程阶段,我们使用Ladder Diagram编写了PLC程序,根据传感器信号对传送带进行控制,实现物料的自动输送和分拣。
4.完成软件编程后,我们进行了测试和调试。
基于PLC的生产线输送带控制系统设计设计

基于PLC的生产线输送带控制系统设计设计摘要目前,输送带系统在工业的各个领域有着广泛的应用。
其结构简单、运行平稳、运转可靠、能耗低、对环境污染小、便于集中控制和实现自动化、管理维护方便,在连续装载条件下可实现连续运输。
对于输送带的控制,它的控制形式也多种多样,它可以由单片机,PLC,以及计算机来控制,以前都采用接触继电器控制系统。
而接触继电器控制系统接线复杂、抗干扰能力差,易因接触不良而造成故障,而且功能扩展性差。
PLC 因其可靠性高、功能完善而越来越受到企业的青睐,传统的接触继电器控制系统已逐步为PLC所取代。
根据所学知识和文献资料对基于PLC的生产线输送带控制系统设计所采用的方法是PLC集中控制的办法,利用PLC内部存储来执行逻辑运算、顺序控制、定时、计数和算术运算等操作,并采用数字量,模拟量的输入和输出来完成控制过程,从而实现对传送带的智能控制。
而且PLC能把计算机的许多功能和继电控制系统结合起来,使PLC和组态控制软件的联系更加紧密,使其模拟量控制、位置控制控制等使其远程通信功能更加完善。
因此本次设计选择了用PLC来控制输送带的整个运行过程,利用PLC简单可视化的程序,实现自动控制的目的。
PLC的运用使得系统的电路变得简明清楚,而且十分便于日后的运行维护带式输送机。
关键词:PLC;输送带;集中控制Design Of The Conveyor Belt Control System For Production lineBased on PLCAbstractAt present, belt conveyor system in the industrial areas in which there is a wide range of applications. Its simple structure, smooth running, run reliable, low energy consumption and environmental pollution on small, easy to focus on control and automation, and ease of maintenance, and management in a continuous load conditions for transport. Conveyor belt for the control, it has a variety of forms of control, it can be done by single-chip Phone, as well as computer, PLC, have in the past to control relay control system with touch. Contact with relay control system wiring complex, anti-interference ability is poor, vulnerable to failure and poor contact, and scalability. PLC due to its high reliability, and functionality has been more and more enterprises, traditional contact relay control system has been replaced by PLC for step-by-step.Based on the knowledge-based information and documentation of PLC conveyor belt production line control system design is the method used by the centralized control PLC approaches, using PLC internal storage to perform logical operations, sequence control, timer, counting and arithmetic operations, such as volume, and adopts the digital, and analog input and output to complete control over the process, the conveyor belt of intelligent control. But PLC to many of the features of the computer and relay control systems into one, so that group mentality and PLC control software, and more closely connected to the analog control, position control, and control their remote communication is much more refined. Therefore this design choice PLC to control the use of the conveyor belt, used during the entire run PLC simple visualization of the process, the automatic control. Use the PLC The circuit makes the system more concise clear and 10 for easy future maintenance of the running belt conveyor.Keywords: PLC; conveyor belt; centralized control目录1 引言 (1)1.1 设计目的和意义 (1)1.2 国内外带式输送机技术现状及差距 (2)1.2.1 大型带式输送机的关键核心技术上的差距 (3)1.2.2 技术性能上差距 (4)1.2.3 控制系统上差距 (5)1.3 本文所做的工作 (5)2 基于PLC的生产线输送带控制系统方案设计 (6)2.1 胶带运输机 (6)2.1.1 胶带运输机的类型及适用条件 (6)2.1.2 胶带运输机结构 (6)2.2 方案比较 (7)2.3 方案确定 (8)2.3.1 设计任务 (9)2.3.2 系统设计思路 (10)3 基于PLC的生产线输送带控制系统硬件设计及选型 (12)3.1 可编程控制器PLC的选型 (12)3.1.1 PLC的组成结构 (12)3.1.2 PLC的工作原理 (13)3.1.3 机型的选择 (16)3.1.4 Siemens S7-200 介绍 (17)3.1.5 本设计的PLC配置 (18)3.1.5 本设计PLC的I/O配置及外围电路设计 (20)3.2 传感器选型 (22)3.2.1 光电传感器 (22)3.2.2 称重传感器 (22)3.2.2 跑偏开关 (24)3.3 被控装置的选择 (26)3.3.1 传送带电机 (26)3.3.2 电动推杆 (27)3.3.3 液压推杆 (29)3.3.4 滚筒电机 (30)4 基于PLC生产线输送带控制系统软件设计 (31)4.1 PLC程序设计 (31)4.1.1 编程软件介绍(STEP7 Micro/WIN) (31)4.1.2 软件编程分析及编程 (32)4.1.3 PLC编程 (32)4.2 上位机组态监控界面 (37)4.2.1 组态软件的系统构成及其简介 (37)4.2.4 系统方案的开发步骤 (39)4.2.5 系统组态界面 (40)5 系统仿真测试及结果 (42)5.1 传感器1#模块仿真 (42)5.2 传送带模块仿真 (43)5.3 称重比较模块仿真 (43)5.4 传感器2#模块仿真 (45)5.5 传感器3#模块仿真 (46)5.6 胶带跑偏保护和急停报警及报警复位 (47)5.7 系统运行指示 (48)5.8 仿真结果总分析 (48)6 结论与展望 (49)参考文献 (50)致谢 (51)1 引言1.1 设计目的和意义目前,输送带系统在工业的各个领域有着广泛的应用。
基于PLC的运料传送带的控制系统设计
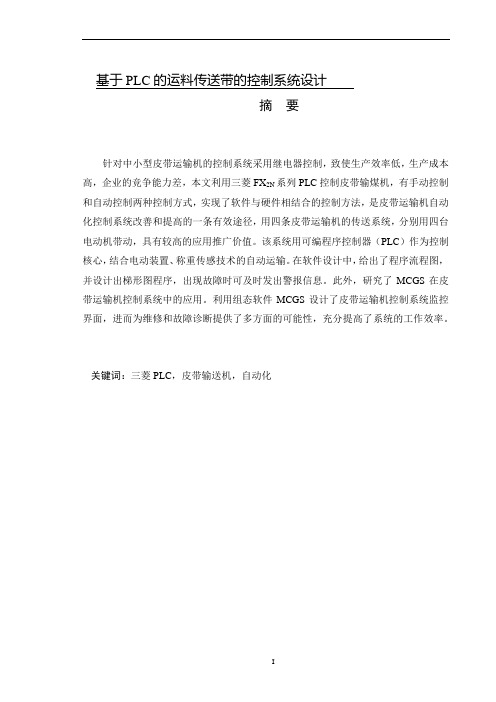
基于PLC的运料传送带的控制系统设计摘要针对中小型皮带运输机的控制系统采用继电器控制,致使生产效率低,生产成本高,企业的竞争能力差,本文利用三菱FX2N系列PLC控制皮带输煤机,有手动控制和自动控制两种控制方式,实现了软件与硬件相结合的控制方法,是皮带运输机自动化控制系统改善和提高的一条有效途径,用四条皮带运输机的传送系统,分别用四台电动机带动,具有较高的应用推广价值。
该系统用可编程序控制器(PLC)作为控制核心,结合电动装置、称重传感技术的自动运输。
在软件设计中,给出了程序流程图,并设计出梯形图程序,出现故障时可及时发出警报信息。
此外,研究了MCGS在皮带运输机控制系统中的应用。
利用组态软件MCGS设计了皮带运输机控制系统监控界面,进而为维修和故障诊断提供了多方面的可能性,充分提高了系统的工作效率。
关键词:三菱PLC,皮带输送机,自动化AbstractAccording to the control system of small and medium sized belt conveyor with relay control, resulting in low production efficiency, high production cost, the enterprise competition ability, this paper makes use of the MITSUBISHI FX2N series PLC control of belt conveyer, a manual control and automatic control two control mode, control method realizes the combination of software and hardware, is a belt conveyor an effective way to improve the automation control system, transmission system with four belt conveyer, respectively with four motor drive, has a higher application value. The system uses programmable logic controller (PLC) as the control core, and combines pneumatic technology, sensing technology and position control technology to control the automatic transportation of products on-site. In the software design, the program flow chart is given, and the ladder diagram program is designed. When the failure occurs, the alarm information can be sent out in time. In addition, the application of MCGS in the control system of belt conveyer is studied. The monitoring interface of belt conveyor control system is designed by using configuration software MCGS, which provides many possibilities for maintenance and fault diagnosis, and improves the working efficiency of the system.Key words: MITSUBISHI PLC, belt conveyor, automation目录1 总体方案设计 (1)1.1皮带运输机的结构 (1)1.2运输机的工作流程 (2)1.2.1 启动 (2)1.2.2 停止 (3)1.3系统的设计内容 (3)2 皮带运输机装置控制系统的硬件设计 (4)2.1可编程控制器(PLC)的选型 (4)2.2传感器的选择 (5)2.3电机选择 (5)2.4通信接口 (5)2.5触摸屏 (6)2.6中间继电器 (6)2.7热继电器 (6)2.8接触器 (7)3 皮带运输机软件以及调试设计 (7)3.1运输机软件的流程图框架 (7)3.2电机正反转程序设计 (8)3.3运行和调试 (11)3.4组态MCGS界面运行的设计 (11)3.4.1MCGS的简介 (11)3.4.2 建立MCGS组态画面 (11)结论 (17)致谢 (18)参考文献 (19)附录一PLC接线图 (20)附录二梯形图程序 (21)附录三输入/输出分配表 (30)本论文以矿用皮带机电气控制系统为研究对象,针对现有煤矿的需要,进行基于PLC的矿用皮带机电气控制系统的设计,使其达到高效率、高节能,高自动化的水平。
自动送料装车系统PLC控制设计

自动送料装车系统PLC控制设计自动送料装车系统主要由送料机构、输送线、装车台和控制系统等组成。
PLC作为整个系统的核心控制设备,负责接收和处理各个传感器、执行器的信号,并根据预设的程序控制装车过程的各个环节。
PLC控制设计的关键目标是提高系统的运行效率、安全性和可靠性。
首先,PLC控制设计需要合理规划系统的硬件结构。
根据自动送料装车系统的特点和需求,选择适合的PLC设备和通信模块,确保系统的稳定性和可扩展性。
同时,还需考虑各个设备之间的连接方式和通信协议,确保数据的可靠传输和实时监控。
其次,PLC控制设计需要编写合适的控制程序。
程序设计应考虑系统的工作流程和逻辑关系,设置合理的传感器触发条件和执行器动作。
同时,还需考虑异常情况的处理,如传感器故障、执行器堵塞等,以确保系统的安全性和可靠性。
在控制程序的编写过程中,需要充分利用PLC的各种功能模块和指令,如计时器、计数器、比较器等,以实现对系统任务的准确控制。
此外,还需考虑对系统运行状态的监测和记录,以便及时分析和排除故障。
除了基本的控制功能外,PLC控制设计还需要考虑人机界面的设计。
通过合理设置触摸屏或按钮等人机界面元素,方便操作员对系统进行监控和控制。
同时,还需提供相应的故障诊断和报警功能,以及操作员对系统参数进行设置和调整的接口。
最后,PLC控制设计还需要进行系统的仿真和调试。
通过利用PLC的仿真软件或专门的仿真设备,对控制程序进行模拟运行和调试,以确保系统的准确性和稳定性。
同时,还需进行实际系统的调试和优化,不断完善和提高系统的性能。
总之,自动送料装车系统PLC控制设计是一个复杂而关键的工作,需要考虑系统的硬件结构、控制程序、人机界面以及系统的仿真和调试等方面。
只有合理规划和设计,才能实现系统的高效、安全和可靠运行。
物料输送线plc控制系统设计.
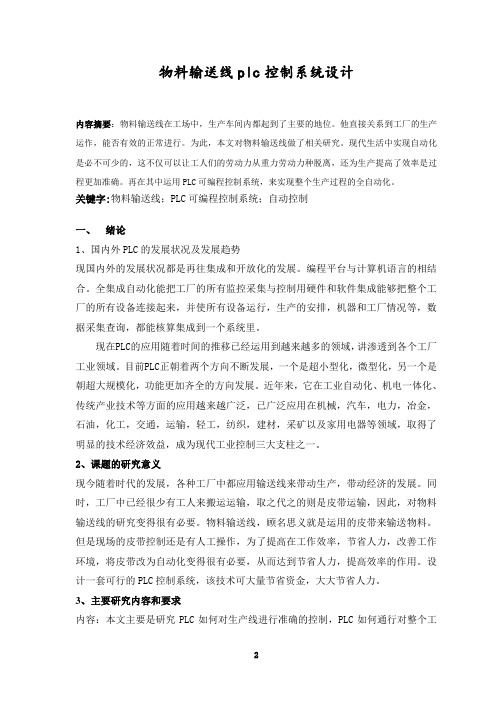
物料输送线plc控制系统设计内容摘要:物料输送线在工场中,生产车间内都起到了主要的地位。
他直接关系到工厂的生产运作,能否有效的正常进行。
为此,本文对物料输送线做了相关研究。
现代生活中实现自动化是必不可少的,这不仅可以让工人们的劳动力从重力劳动力种脱离,还为生产提高了效率是过程更加准确。
再在其中运用PLC可编程控制系统,来实现整个生产过程的全自动化。
关键字:物料输送线;PLC可编程控制系统;自动控制一、绪论1、国内外PLC的发展状况及发展趋势现国内外的发展状况都是再往集成和开放化的发展。
编程平台与计算机语言的相结合。
全集成自动化能把工厂的所有监控采集与控制用硬件和软件集成能够把整个工厂的所有设备连接起来,并使所有设备运行,生产的安排,机器和工厂情况等,数据采集查询,都能核算集成到一个系统里。
现在PLC的应用随着时间的推移已经运用到越来越多的领域,讲渗透到各个工厂工业领域。
目前PLC正朝着两个方向不断发展,一个是超小型化,微型化,另一个是朝超大规模化,功能更加齐全的方向发展。
近年来,它在工业自动化、机电一体化、传统产业技术等方面的应用越来越广泛,已广泛应用在机械,汽车,电力,冶金,石油,化工,交通,运输,轻工,纺织,建材,采矿以及家用电器等领域,取得了明显的技术经济效益,成为现代工业控制三大支柱之一。
2、课题的研究意义现今随着时代的发展,各种工厂中都应用输送线来带动生产,带动经济的发展。
同时,工厂中已经很少有工人来搬运运输,取之代之的则是皮带运输,因此,对物料输送线的研究变得很有必要。
物料输送线,顾名思义就是运用的皮带来输送物料。
但是现场的皮带控制还是有人工操作,为了提高在工作效率,节省人力,改善工作环境,将皮带改为自动化变得很有必要,从而达到节省人力,提高效率的作用。
设计一套可行的PLC控制系统,该技术可大量节省资金,大大节省人力。
3、主要研究内容和要求内容:本文主要是研究PLC如何对生产线进行准确的控制,PLC如何通行对整个工厂内的设备的控制。
- 1、下载文档前请自行甄别文档内容的完整性,平台不提供额外的编辑、内容补充、找答案等附加服务。
- 2、"仅部分预览"的文档,不可在线预览部分如存在完整性等问题,可反馈申请退款(可完整预览的文档不适用该条件!)。
- 3、如文档侵犯您的权益,请联系客服反馈,我们会尽快为您处理(人工客服工作时间:9:00-18:30)。
物料输送线plc控制系统设计容摘要:物料输送线在工场中,生产车间都起到了主要的地位。
他直接关系到工厂的生产运作,能否有效的正常进行。
为此,本文对物料输送线做了相关研究。
现代生活中实现自动化是必不可少的,这不仅可以让工人们的劳动力从重力劳动力种脱离,还为生产提高了效率是过程更加准确。
再在其中运用PLC可编程控制系统,来实现整个生产过程的全自动化。
关键字:物料输送线;PLC可编程控制系统;自动控制一、绪论1、国外PLC的发展状况及发展趋势现国外的发展状况都是再往集成和开放化的发展。
编程平台与计算机语言的相结合。
全集成自动化能把工厂的所有监控采集与控制用硬件和软件集成能够把整个工厂的所有设备连接起来,并使所有设备运行,生产的安排,机器和工厂情况等,数据采集查询,都能核算集成到一个系统里。
现在PLC的应用随着时间的推移已经运用到越来越多的领域,讲渗透到各个工厂工业领域。
目前PLC正朝着两个方向不断发展,一个是超小型化,微型化,另一个是朝超大规模化,功能更加齐全的方向发展。
近年来,它在工业自动化、机电一体化、传统产业技术等方面的应用越来越广泛,已广泛应用在机械,汽车,电力,冶金,石油,化工,交通,运输,轻工,纺织,建材,采矿以及家用电器等领域,取得了明显的技术经济效益,成为现代工业控制三大支柱之一。
2、课题的研究意义现今随着时代的发展,各种工厂中都应用输送线来带动生产,带动经济的发展。
同时,工厂中已经很少有工人来搬运运输,取之代之的则是皮带运输,因此,对物料输送线的研究变得很有必要。
物料输送线,顾名思义就是运用的皮带来输送物料。
但是现场的皮带控制还是有人工操作,为了提高在工作效率,节省人力,改善工作环境,将皮带改为自动化变得很有必要,从而达到节省人力,提高效率的作用。
设计一套可行的PLC控制系统,该技术可大量节省资金,大大节省人力。
3、主要研究容和要求容:本文主要是研究PLC如何对生产线进行准确的控制,PLC如何通行对整个工厂的设备的控制。
介绍了DCS分布式控制系统的基本结构的组成,发展状况。
并对其进行相关的分析。
还对物料输送线的工艺要求,工艺要求,进行了简单的介绍。
对物料输送线的日常的保养也做出了相应的介绍。
最后对PLC控制系统的抗干扰措施,I/O防干扰的措施进行了详细的分析与介绍。
要求:论文要紧贴题义,语言流畅,语句通顺。
有较强的文献资料收集查阅能力、逻辑思维能力和自学能力,有较好的专业基础知识和应用能力。
按照毕业设计(论文)时间安排,不抄袭、剽窃他人成果,保质保量完成各阶段任务,并主动按时提交相应的成果给助教老师。
二、系统整体设计1、控制系统的分析与确定DCS为集散控制系统的英文(DISTRIBUTED CONTROL SYSTEM)简称,如图2.1所示。
指的是控制危险分散、管理和显示集中。
它是基于计算机技术,控制技术,通讯技术图形显示技术,通过某种通讯网络将分布在工业现场附近的现场控制站、检测站、操作管理站、控制管理站及工程师站连接起来完成分散控制集中操作的综合控制系统。
DI AI DOAOV net图2.1 DCS系统基本结构上世纪七十年代中期问世的DCS系统的基本结构,由控制站、显示操作工作站(或称人机接口)、以及将控制站、显示操作站点连成一个总体的通信总线共3个部分组成。
随着微电子、计算机、通信尤其是工业网络等高新技术及产品的迅速发展以及工业应用需求的变迁。
使现DCS这三个组成部分的职责与相互关系在设计理念上有较大的变化。
设计DCS的初衷是“危险分散、信息集中”。
危险分散体现于早期的一个控制站或控制单元仅仅包含8至16个控制回路。
往往要配置多个控制单元才能满足现场一个机组或一套生产装置整体控制要求。
现代化的工业生产,由于采取能量回收措施以及配套的公用工程使工艺流程上、下游各单元设备之间存在物流与能量流之间的勾连而形成的一套生产装置或机组是一个有机的整体,该整体的安全平稳生产并非能由各控制单元分别实施局部分割控制所能确保的.因此,工业应用要求扩大控制站的I/O 容量与控制回路数,使之能覆盖一套生产装置(或机组)的控制需求而实现局部集中控制。
FCS为现场总线控制系统的英文(FIELDBUS CONTROL SYSTEM)简称,如图2.2所示。
现场的总线是连接智能化的设备和自动化的数字式,双向传输,多分支结构的通信网络。
它的关键在于能够支持双向,多节点,总线式,的全数字式通讯。
图2.2 FCS系统基本结构现场总线用于过程自动化、制造自动化、楼宇自动化等领域的现场智能设备互连通讯网络。
它作为通信网络的基础,现场总线技术是控制、计算机、通讯技术的交叉与集成,涉及的容十分广泛,现场总线是在80年代末、90年代初国际上发展形成的,现在自动化系统的网络化是发展的大趋势,现场总线技术受计算机网络技术的影响是十分深刻的。
2、总体结构的确定在一般的情况下,监控系统都是由现场控制级设备、过程控制级设备、监控管理级设备组成多级体系,它们通过网络互相连接。
过程及设备从过程对象采集实时数据,按预先组态好的控制策略,接受操作人员的控制指示,从而实现对过程对象实时控制;操作人员通过监控级设备,监视过程对象及控制装置的运行情况,并通过网络,向过程及设备发出指令,干预过程对象的控制,同时可进行数据分析和报表打印;管理级设备可以接受监控管理级按规定的格式远传过来的数据,提供统一调度。
本文的设计中,整个系统主要由就地控制箱、PLC集中控制柜及上位远程监控终端3部分组成。
三、输送线的工艺研究及保养1、输送线的工艺要求引入PLC可编程控制器可解决很多问题。
具有的保护容有:胶带跑偏,胶带车控制回路故障,胶带控制凹路故障,位置信号丢失,堆料,满仓信号提示等。
该系统的特点是:性能稳定,扩展能力强,技术含量高,维修,维护,系统改造方便灵活,遇到紧急事故能及时停车,发出声光报警信号,能及时适应生产现场需要,确保了输送机的安全正常进行,具有广泛地适应性和推广价值。
系统在运行中要实现连续不断还必须要求输送的可靠工作,输送可靠工作的条件是:(1)拖动皮带机的电机要安全可靠的运行1)电机的功率要满足输送负荷的要求;2)电机的工作是否正常应有检测装置。
(2)皮带机上的皮带是否工作正常1)皮带机上的皮带是否打滑;2)皮带机上的皮带是否跑偏。
2、输送线的工艺设计物料输送线控制系统的工艺流程图如图3.1所示。
图3.1 工艺流程图在物料的输送过程中有3部分需要检测,物料上皮带时要经过一个平的皮带,然后物料经过一段爬坡的皮带进入第三个皮带,该皮带也是一个平坦的皮带,经过这三段皮带就可以进入仓库了。
爬坡的皮带和第一条皮带有一些区别,因为爬坡所以电机的功率要相对大一些。
在爬坡时掉包的可能性最大,因此在爬坡时对产品进行计数是最合适的,在这条皮带的中间安装一个传感器用来对产品进行计数。
3、输送线的日常保养第一是输送线的输送带负荷过大出现打滑。
超出了自身的负荷能力,此时应当减轻输送物料的运输量或者增加输送机的本身的承重力,来防止打滑的现象。
第二是输送线的启动速度太快而造成打滑。
此时应当慢速启动或再次点动两下后再重新启动,也可以克服打滑的现象第三是初力太小。
原因是输送带在离开滚筒时的力不够,所造成输送带的打滑。
此时处理的方法是调整拉紧装置,加大初力。
第四是滚筒的轴承的损坏而不运转。
原因可能是轴承部灰尘积聚的太多或是没有及时检修和更换已被严重磨损而转动不灵活的部件,造成阻力增大而打滑。
第五是输送机传动的滚筒与输送带之间的摩擦力不够所造成打滑现象。
原因一般就是输送带上有水滴没有擦拭干净或作业环境潮湿。
此时应当在滚筒加入些许松香末。
来防止打滑现象的出现。
四、PLC控制系统的抗干扰设计1、抗电源干扰的措施很多情况证明,由电源引起的干扰造成PLC控制系统的故障的情况发生很多。
PLC日常的供电都是由电网来供电。
由于电网的覆盖面很广,所以他将受到空间中电磁的干扰在线路上电压和电流。
特别是电网部的变化尤其明显,造成大型电力设备起停、交直流传动装置引起的谐波、电网短路暂态冲击等,都通过输电线路传到电源。
所以可以采取一下的措施来减少因为电源的干扰造成PLC控制系统的故障。
(1)采用性能优良的,抑制电网引入的干扰,在PLC控制系统中,电源占有很重要的地位。
电网干扰串入PLC控制系统主要是通过PLC系统的供电电源(有CPU电源,I/O电源等),变送器供电的电源与PLC系统具有直接电气连接的仪表耦合进入的。
现在一般对PLC系统的供电电源,一般采用隔离性能较好的电源,而对变送器的供电的电源和PLC系统有直接的电气连接的仪表的供电电源,并没有受到足够的重视。
虽然有采取了一定的措施,但普遍还是不够的,主要使用的隔离变压器分布参数大,抑制能力差,经电源耦合串入共模干扰。
所以对变送器的和共用信号仪表供电应选择分布电容量小,一直带大的配电器,以减少PLC系统的干扰。
此外,为保障电网供电不中断,可采用不间断供电电源,提高供电安全可靠性。
并且还具有较强的干扰隔离的功能,是一种PLC控制系统的理想电源。
(2)硬件的滤波措施,在干扰较强或者可靠性要求较高的场合,应该使用带屏蔽层的隔离变压器对PLC系统供电。
还可以在隔离变压器一次侧串接滤波器,如图所示。
(3)正确选择地点,完善接地系统。
滤波器和隔离变压器同时使用2、防I/O干扰的措施由信号引入干扰会引起I/O信号工作异常和测量精度大大降低,严重时将引起元器件损伤。
对于隔离性能差的系统,还将导致信号间互相干扰,引起共地系统总线回流,造成逻辑数据变化、误动作或死机。
可采取以下措施以减小I/O干扰对PLC系统的影响。
(1)从抗干扰角度选择I/O模块(2)安装与布线时注意:①动力线、控制线以及PLC的电源线和I/O线应分别配线,隔离变压器与PLC和I/O之间应采用双绞线连接。
将PLC的I/O线和大功率线分开走线,如必须在同一线槽,可加隔板,分槽的走线最好,这不仅能使其有尽可能大的空间距离,并能将干扰降到最低限度。
②PLC 应远离强干扰源。
如电焊机、大功率硅整流装置和大型动力设备,不能与高压电器安装在同一个开关柜。
在柜PLC应远离动力线(二者之间距离应大于200mm)。
与PLC 装在同一个柜子的电感性负载,如功率较大的继电器、接触器的线圈,应并联RC电路。
③PLC的输入与输出最好分开走线,开关量与模拟量也要分开敷设。
模拟量信号的传送应采用屏蔽线,屏蔽层应一端接地,接地电阻应小于屏蔽层电阻的1/10。
④交流输出线和直流输出线不要用同一根电缆,输出线应尽量远离高压线和动力线,避免并行。
(3)考虑I/O端的接线:输入接线一般不要太长,但如果环境干扰较小,电压降不大时,输入接线可适当长些。
输入/输出线要分开。
尽可能采用常开触点形式连接到输入端,使编制的梯形图与继电器原理图一致,便于阅读。