发动机曲轴加工新技术
汽车发动机曲轴机械加工技术

汽车发动机 曲轴机 械加 工技术
美 国、德 国、 日本 等汽车工业发达 国家都 致力于开发绿色环保 、高性能发动机 , 发动机 曲轴正面 临着 安全性和可靠性 的严 峻挑 战 ,传统材料和 制造 工艺 已无法满足其 功 能要求 ,本文主 要介绍 曲轴机械NT 的欧美型工艺方案和 日本 丰田型工艺方案 。
14 — 号连杆 轴颈 及沉 割槽一钻 油孔一 序 中, F 。 道 道 C L ' 清 洗 一主 轴 颈 、连 杆 轴 颈 外 圆 淬火 颈检 测工 序1 ;主轴颈 和连 杆 轴颈 道
的先 进 设 备 和技 术 ,提 高 了 曲轴 的 成 ,生 产效 率 和 自动 化 程 度 相 对较 这 是 江 铃股 份 公 司 的独 特 之处 ) 。 制造 技术水平 。
低 。 粗 加 工设 备 多采 用 多 刀 车 床 车 采 用 进 口的 滚压 机 床 滚 压 主轴 颈 和
削 曲轴 主轴 颈及 连 杆 轴 颈 ,工序 的 连 杆 轴 颈 的 圆弧 槽 。采 用进 口的抛 质 量稳 定 性 差 ,容 易 产 生 较大 的 内 光机抛 光主轴 颈和连杆 轴颈 。 ( 3)采 用 进 口 的 数 控 机 床 加
1 曲轴用材料
目前 ,车 用 发动 机 曲轴 材 质 有 应 力 ,难 以达 到 合 理 的 加 工余 量 。 球 墨 铸铁 和钢 两 类 。 由 于球 墨 铸 铁
( ) 加 工 工 艺 流 程 2
言 ,锻 钢 曲轴 具 有 较 高 的综 合 机 械 两端 面 、钻 中心 孔 。 采 用 国产 数 控
铣 两 端 面 、 钻 中 心 孔 一 车 后
性 能 。许 多高 强 化 的 中 高速 大 功 率 车 床粗 精 车 前 后 端 外 圆 、 主轴 颈 上 端 、2 5 主轴 颈 一车 前端 、1 主 - 号 号
车用发动机曲轴的高效加工
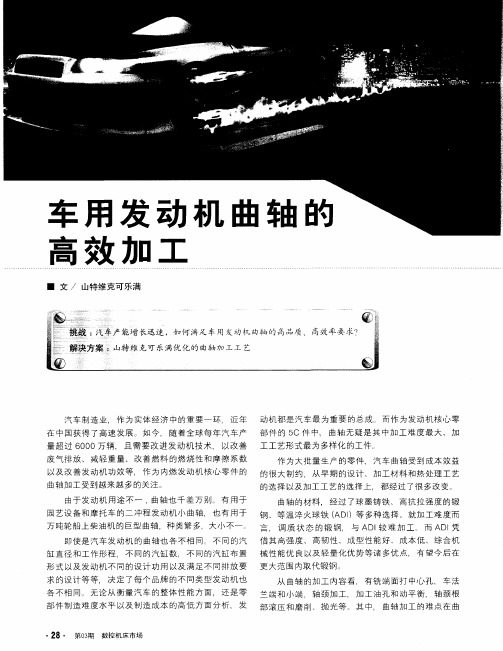
l 第o期 ・ 3
数控机床市场
■
作 为 以 技 术 为 主 导 的 全 球 最 大 的 硬 质 合 金 制 造 商 , 山特 维 克 可 乐 满 尤 为 重 视 新 产 品 开 发 和 复 杂 刀 具 的 应 用 与 研 发 。 山 特 维 克 可 乐 满 相 继 在 以下 国 家 和
6 轴颈 的加工,有数控车 、外 铣、 内铣、车拉 、车车 E 、高速 铣、大切深磨 削、车 铣复合加工等 多种加工
式 。 各 种 加 工 方 式 无 不 是 由 曲 轴 的 工 艺 要 求 、 生 产
寿命 必须很长,而且可 以预测, 以保障生产线 的连续
可 靠 的 运 行 : 据 加 工 情 况 和 热 处 理 方 式 的 不 同, 加 根
的大力支持,与集 团内部 相应的刀体及 刀片生产单位
密切合作,涉及 的 曲轴加 工包括 : 曲轴法兰端和小端 的加工、 曲轴推力面 加工、 曲轴车拉、 曲轴车 /车 一 车拉 、曲轴 内铣和外铣、 曲轴车铣加工等 曲轴加 工内 容 ,同时包括 凸轮轴铣 削等 。 社会 的发展要 求曲轴 加工更加精密 同时要保证 曲轴加工的制造成本不发 生较大 变化。绿色和环保 的
工循环 时间可 以优化到十秒 以内,并使两次换 刀之 间
加工 8 0 0 0件 曲 轴成 为 可 能 , 以确 保 较 高 的班 产 量 。
S h ak le c m lad n的 复 杂 的 镗 削 系 统 应 用 中心 等。
山特维克可 乐满组建这些专业 的应 用 中心 是 为了
发动机曲轴制造工艺进展及敏捷柔性生产线

20 . 世纪 7 ~8 年代 2 0 0
这一时期 ,曲轴粗加工采用 C C车削、C C外铣加工, N N 加工状况有所 改善。精加工仍多以普通磨床磨削工艺为主。
30 . 世纪 8 年代中期 2 0
到2 世纪 8 年代中期,又出现了C C内铣工艺, N 0 0 N C C内铣加工性能 指标要高于C C外铣加工, N 尤其是对于锻钢曲轴 , 内铣更有利于断屑。 精 加工工艺多采用半 自 曲轴磨床,头架和尾座同步杠传动,加工精度有一 动
41 8 ~19 年 .9 5 9 0
1 8 ~19 9 5 9 0年开发出了曲轴车
拉 一 车 车拉工艺 ( 为双刀 图l 盘车 一
颈。采用这种方式加工精度较低,柔性很差, 工序质量稳定性低, 且容易产 生较大的内部应力, 难以达到合理的加工余量。 在粗加工后一般需要进行去
应力 回火处理 , 释放应力。因此粗加 工需要给后续精加 工工序 留较 大的加 工 余量 ,以去除弯 曲变形量 。曲轴精加工采 用的是普通磨 削工艺 ,一般采用
采用直线光栅尺或圆度光栅尺检测, 可实现闭环控制。 该加工中心备有4 ~ 8 9 工位刀库可实现自动换刀, 6 一次装夹可进行车、 铣、钻、 镗、 攻螺纹等的 加工。曲轴精加工方面, 也出现了工序集成的C N数控磨床, B 即一次装夹磨
削全部曲轴主轴颈和连杆轴颈 ( 摆动跟踪 磨削 ) 。 由以上演变可以看出 ,曲轴的加工工艺正 向着高速 、高效 、 复合化 方向 发展 。 目前较 为流行的粗加工工 艺是主轴颈采 用车 一车拉工艺和高速外铣 , 连杆轴颈采用高速随动外铣 , 全部采用干式切削; 精加工 采用数控磨 床加工 , 具 有 自动进给 、自 动修正砂轮 、 寸和 圆度 自 补偿 、自动分度和两端电子 尺 动
曲轴的数控加工工艺.

曲轴的数控加工工艺浙江工贸职业技术学院毕业设计(论文)课题名称:曲轴的数控加工工艺系部:汽机学院专业:数控技术班级:数控1302姓名:张余榕学号:1310204238指导教师:郑艳丽达成时间2016年3月17日浙江工贸职业技术学院13届毕业设计(论文)目录1、绪论 (1)前言 (1)设计内容 (2)2、零件的工艺剖析 (2)零件构造工艺性剖析 (3)零件技术条件剖析 (3)毛坯的选择 (3)毛坯种类选择 (3)毛坯制造方法的选择 (4)3.机加工工艺路线确立 (4)加工方法剖析确立 (4)加工次序的安排 (4)定位基准选择 (4)加工阶段的区分 (4)4. 工序的区分 (5)工序的区分 (5)加工次序的安排 (5)确立加工路线 (6)5.曲轴的机械加工工艺过程卡片 (7)6.制定加工零件的工艺卡片 (10)曲轴数控加工工艺 (10)曲轴的数控加工工艺7.铣床加工曲轴表面程序268.量具的采纳26游标卡尺29千分尺29总结30参照文件 (31)浙江工贸职业技术学院13届毕业设计(论文)曲轴的数控加工工艺张余榕汽车与机械工程学院班级:数控1302班纲要:曲轴是汽车发动机的要点零件之一,其性能利害直接影响到汽车发动机的质量和寿命.曲轴在发动机中肩负最大负荷和所有功率,蒙受着强盛的方向不停变化的弯矩及扭矩,同时经受着长时间高速运行的磨损,所以要求曲轴材质拥有较高的刚性、疲惫强度和优秀的耐磨性能。
发动机曲轴的作用是将活塞的来去直线运动经过连杆转变为旋转运动,进而实现发动机由化学能转变为机械能的输出。
本课题是单拐曲轴的加工工艺的剖析。
工艺路线的拟定是工艺规程制定中的要点阶段,是工艺规程制定的整体设计。
所撰写的工艺路线合理与否,不只影响加工质量和生产率,并且影响到工人、设施、工艺装备及生产场所等的合理利用,进而影响生产成本。
所以,本次设计是剖析曲轴零件加工技术要求及加工精度后,合理确立毛坯种类,经过查阅有关参照书、手册、图表、标准等技术资料,确立各工序的定位基准、机械加工余量、工序尺寸及公差,最后拟订出曲轴零件的加工工序卡片。
发动机曲轴再制造研究现状

发动机曲轴再制造研究现状一、引言发动机曲轴作为发动机的核心部件之一,承担着转换活塞往复运动为旋转运动的重要作用。
随着车辆保有量的增加和使用时间的延长,曲轴表面磨损严重,导致其性能下降。
因此,对于曲轴再制造技术的研究和应用具有重要意义。
二、曲轴再制造技术概述1. 再制造定义再制造是指对废旧产品进行回收利用,通过一系列工艺流程使其恢复到与新产品相同或相近的性能和质量水平,并在市场上重新销售或使用。
2. 曲轴再制造流程曲轴再制造主要包括以下几个方面:检测、清洗、磁粉探伤、修复焊接、研磨抛光等。
3. 曲轴再制造技术分类根据不同的处理方法和工艺流程,曲轴再制造技术可分为以下几类:电化学加工、喷涂修复、冷喷涂修复、激光熔覆修复等。
三、发动机曲轴再制造技术应用现状1. 国内应用现状目前,国内曲轴再制造技术已经逐渐成熟,并且得到了广泛的应用。
例如,上海某公司开发出了一套曲轴修复设备,可以实现曲轴的检测、清洗、磁粉探伤、修复焊接等工艺流程。
此外,国内一些大型机床企业也开始涉足曲轴再制造领域。
2. 国外应用现状与国内相比,国外发动机曲轴再制造技术更加成熟和先进。
例如,在美国和欧洲等发达国家,已经形成了一套完整的曲轴再制造体系,并且得到了广泛的应用。
四、发动机曲轴再制造技术存在的问题与挑战1. 技术水平不稳定由于受到设备和工艺限制,曲轴再制造过程中存在着技术水平不稳定的问题。
这种情况在一些小型企业中尤为突出。
2. 研发投入不足当前,我国对于发动机曲轴再制造技术的研究投入还比较少,导致我国在该领域的技术水平相对滞后。
3. 法律法规不完善由于缺乏相关的法律法规支持,一些企业在曲轴再制造过程中存在着违规操作的情况,给行业带来了一定的负面影响。
五、发动机曲轴再制造技术未来发展趋势1. 技术智能化随着人工智能、机器人等技术的快速发展,未来曲轴再制造技术将更加智能化和自动化。
2. 研发投入增加我国对于曲轴再制造领域的研究投入将会逐渐增加,促进该领域的快速发展。
提高轻型发动机曲轴连杆机构制造技术的思考
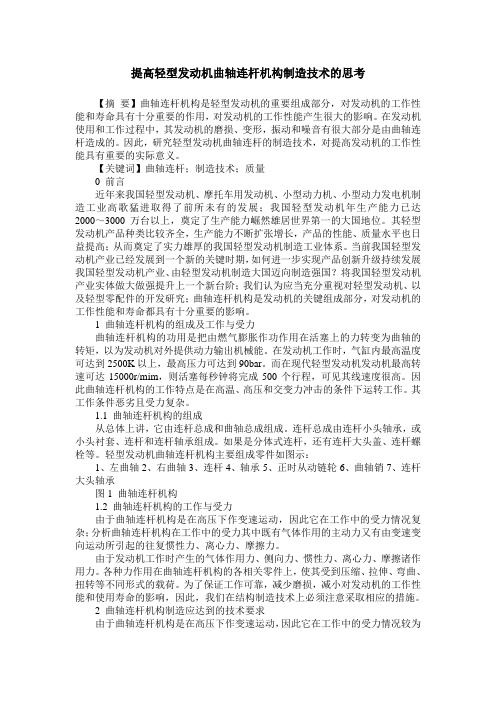
提高轻型发动机曲轴连杆机构制造技术的思考【摘要】曲轴连杆机构是轻型发动机的重要组成部分,对发动机的工作性能和寿命具有十分重要的作用,对发动机的工作性能产生很大的影响。
在发动机使用和工作过程中,其发动机的磨损、变形,振动和噪音有很大部分是由曲轴连杆造成的。
因此,研究轻型发动机曲轴连杆的制造技术,对提高发动机的工作性能具有重要的实际意义。
【关键词】曲轴连杆;制造技术;质量0 前言近年来我国轻型发动机、摩托车用发动机、小型动力机、小型动力发电机制造工业高歌猛进取得了前所未有的发展;我国轻型发动机年生产能力已达2000~3000万台以上,奠定了生产能力崛然雄居世界第一的大国地位。
其轻型发动机产品种类比较齐全,生产能力不断扩张增长,产品的性能、质量水平也日益提高;从而奠定了实力雄厚的我国轻型发动机制造工业体系。
当前我国轻型发动机产业已经发展到一个新的关键时期,如何进一步实现产品创新升级持续发展我国轻型发动机产业、由轻型发动机制造大国迈向制造强国?将我国轻型发动机产业实体做大做强提升上一个新台阶;我们认为应当充分重视对轻型发动机、以及轻型零配件的开发研究;曲轴连杆机构是发动机的关键组成部分,对发动机的工作性能和寿命都具有十分重要的影响。
1 曲轴连杆机构的组成及工作与受力曲轴连杆机构的功用是把由燃气膨胀作功作用在活塞上的力转变为曲轴的转矩,以为发动机对外提供动力输出机械能。
在发动机工作时,气缸内最高温度可达到2500K以上,最高压力可达到90bar。
而在现代轻型发动机发动机最高转速可达15000r/mim,则活塞每秒钟将完成500个行程,可见其线速度很高。
因此曲轴连杆机构的工作特点是在高温、高压和交变力冲击的条件下运转工作。
其工作条件恶劣且受力复杂。
1.1 曲轴连杆机构的组成从总体上讲,它由连杆总成和曲轴总成组成。
连杆总成由连杆小头轴承,或小头衬套、连杆和连杆轴承组成。
如果是分体式连杆,还有连杆大头盖、连杆螺栓等。
摩托车发动机曲轴结构、材料、加工工艺

一、曲轴材料汽车和摩托车曲轴连杆是发动机的关键零件,一般用40铬合金钢,或45号优质碳素钢制作,还需调制处理。
曲轴一般是用45号锻钢或者球墨铸铁来制作。
现在有国家标准可以参考GB/T23339-2009(曲轴)和GB/T23340-2009 (连杆)。
你好!发动机曲轴的材料性能要求有较高的强度、冲击韧性、耐磨性。
一般采用锻造钢和球墨铸铁,锻钢需要进行热处理采用调质,就是淬火后高温回火,使材料具有较高的综合机械性能,轴径表面再进行表面淬火,提高表面硬度及耐磨性。
球墨铸铁曲轴采取等温回火、中频淬火、激光淬火等热处理工艺。
我给你提供一些标准,在标准分享网下载,这些都是GB标准和曲轴的相关资料。
请下载研究,可以详细了解曲轴的材料和相应的技术性能要求和热处理方法及要求,这样我们就找到了我们的目标,有了目标,然后我们才好进行下一步的研究,这样形成了一个良好的开端,就是成功的一半了。
我认为很多标准是经过各方面的考虑和很多专家的意见的综合得来的。
是一个非常重要的要求。
这些标准或资料可以在(标准分享网)上下载,在其搜索输入例如“曲轴”或“曲轴热处理”或“曲轴工艺”或者直接输入下面的资料的关键词就可以免费、免注册快速下载相关标准和曲轴相关的资料。
1 GB/T23339-2009《内燃机曲轴技术条件》2 GB/T 24595-2009 《调质汽车曲轴用钢棒》3 GB/T 15712-2008 《非调质机械结构钢》4 《铸造缺陷和热处理工艺对球墨铸铁曲轴疲劳强度的影响》5 见参考网址:6其他要求根据你详细的情况在谷哥中搜索“曲轴热处理”等下面介绍下GB/T23339-2009《内燃机曲轴技术条件》相对于原JB/T6727-2000《内燃机曲轴技术条件》的主要变化。
GB/T23339-2009《内燃机曲轴技术条件》相对于原JB/T6727-2000《内燃机曲轴技术条件》的主要变化有两个方面。
一是材质方面,首次增加了采用非调质钢的规定。
曲轴的数控加工工艺

曲轴的数控加工工艺曲轴是内燃机的重要组成部分,也是发动机输出动力的主要传动件之一。
在发动机运转中,曲轴承受着巨大的轴向和径向载荷,需要耐久耐磨,精度要求高,因此其制造工艺十分重要。
在曲轴制造工艺中,数控加工技术的应用已成为趋势,下面就来简单介绍一下曲轴的数控加工工艺。
1.刀具的选用曲轴的加工工艺中,刀具的选用是十分关键的。
在曲轴的加工过程中,常用的切削刀具包括硬质合金刀具、热处理刀具、钻孔刀具和磨削刀具等。
其中,硬质合金刀具具有高硬度、高强度和高温度下的抗腐蚀性能等优点,适用于加工高硬度材料的曲轴,如高强度合金钢、高速钢等;热处理刀具则常用于加工低硬度、低强度的材料,如普通碳素钢、铸铁等;钻孔刀具适用于进行孔加工或基准孔的加工;而磨削刀具适用于进行高精度的表面加工。
2.数控机床的应用数控机床是目前曲轴加工中常用的主要设备,其能够实现对曲轴的精度控制和高效率加工。
数控机床还可以根据曲轴不同部位的形状进行不同的加工,以满足对曲轴不同部位的不同要求。
同时,数控机床还可以实现多轴联动,提高加工精度和加工效率。
3.数控编程的应用数控编程是曲轴加工中必不可少的一项技术,其实现了对加工过程的自动化控制和全局监测。
数控编程需要根据曲轴的CAD图纸进行编写,确定曲轴要加工的轮廓、孔和与机床的运动轨迹等,将编写好的程序输入到数控机床中进行加工。
4.检测技术的应用曲轴是高精度零件,其制造过程中的精度检测常用于判定曲轴的尺寸、形状和位置精度是否满足要求,以保证曲轴的准确性和稳定性。
常用的检测方法包括三坐标测量、激光扫描、光学测量和机械测量等。
总之,随着科技不断发展,曲轴的数控加工技术也不断的得到提高。
对于曲轴制造企业而言,需要加强技术研发以适应市场的需求,提高生产效率以降低成本,提高曲轴质量以满足市场需求。
通过对曲轴数控加工工艺的不断研究和创新,将为曲轴的制造带来新的发展前景。
汽车发动机曲轴高效精密加工成套装备的研发与应用
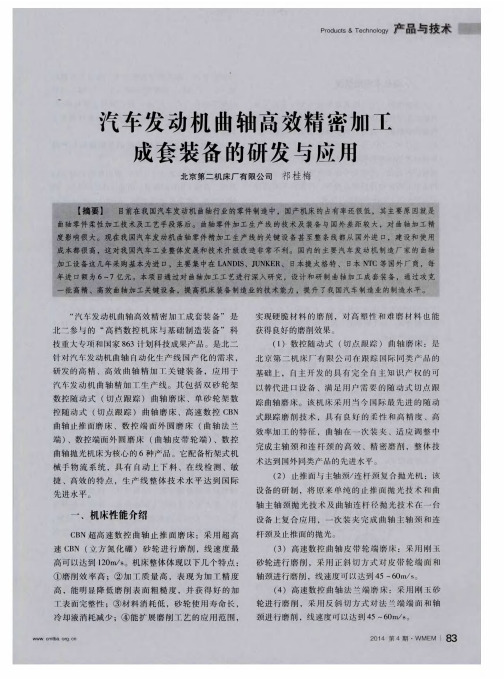
二、新技术应用情况
本 曲 轴 加 T 生 产 线 成 套 装 备 开 发 时 研 究 了 曲
为 回转 中心 ,采 用 现代 数控 技术 ,通 过工 件旋 转
轴 ( C . 、C : 轴) 、砂 轮 进 给轴 ( 、 轴 )及 砂
轴多砂带 整体 超精 密抛 光 1 二 艺 及技 术 、曲轴 随 动 磨削 的智 能 化 、无 编程 专 家 系统 软件 、与生 产 线
2 .具 有敏 捷 、柔 性 特 征 的 曲轴磨 削 生 产 线 总体布 局技 术
曲轴传统 磨 削加 l 丁_ T 二 艺一 般 为 曲轴 止推 面 的
相适应 的零件 物 流传 输 系统等 。产 品在 开发 过 程
方面缩短 了工艺路 线 ,提 高 了设备 的加 工精度 ,
是通过控制工件 的旋转 运 动 ( c轴 ) 和砂 轮 的横
向进给运动 ( X轴 ) ,使砂 轮外 圆与工件被 加工表 面轮廓 始 终 相 切 ,从 而 实 现 偏 心 圆 的 磨 削加 工。 图1 为采用随动磨削法对曲轴连杆颈进行磨 削的原 理示意图 ,O为主轴颈 中心 ,从图中可 以看 出 ,当
中实现 了如下 的技术创新与突破 :
磨 削 、曲轴 主轴颈 的磨削 、曲轴连杆径的磨削 、曲
轴法兰端 、皮 带轮 端 的磨 削 、曲轴 主轴 颈 和连 杆 颈的抛 光 、曲轴止推 面的抛光等 7道工序。整合 优 化后的曲轴 生产 线 工序 布局 为 :采 用立 方氮 化 硼
1 .以 “ 数 控 切 点跟 踪 精 密 高 效磨 削 ” 为 核 心的 多轴联 动 非圆超 高速磨 削 工艺技 术
颈 上 的弧段 A B;从 9 0 。 转到 1 8 0 。 时 ,磨 削 了连杆
发动机曲轴加工工艺分析与设计

发动机曲轴加工工艺分析与设计1. 引言发动机曲轴是发动机的核心零部件之一,其加工工艺的优劣直接影响着发动机的性能和可靠性。
本文将分析和设计发动机曲轴的加工工艺,通过对材料、工序、工艺参数等方面的研究,提出优化和改进的建议。
2. 发动机曲轴的材料选择发动机曲轴的材料选择是影响加工工艺的重要因素之一。
常见的曲轴材料包括碳钢、合金钢、铸铁等。
不同材料具有不同的力学性能和硬度,因此需要根据具体的发动机要求选择合适的材料。
3. 发动机曲轴的主要工序发动机曲轴的加工过程通常包括下列几个主要工序:3.1 材料准备在加工开始之前,需要对选定的曲轴材料进行切割和切断,以获得适合加工的工件。
常见的材料准备方式包括锯切和切割等。
3.2 车削加工车削是加工曲轴最常用的方法之一。
通过在车床上将工件固定并旋转,使用车刀对工件进行切削,以获得理想的形状和尺寸。
3.3 钻孔加工发动机曲轴的钻孔加工主要用于制作连接杆的连接孔和平衡子的安装孔。
通过钻孔加工,可以确保这些关键部件的准确度和精度。
3.4 精细加工与磨削在曲轴的加工过程中,常常需要进行精细加工和磨削,以提高工件的表面质量和几何精度。
通过使用磨削工具和设备,可以有效地将工件的直径、圆度和平行度等参数控制在规定范围内。
4. 发动机曲轴加工工艺参数的优化为了提高曲轴的加工效率和质量,需要对加工工艺参数进行合理的优化。
以下是一些常见的优化方法:4.1 优化车削刀具的选择针对不同的曲轴材料和加工阶段,选择合适的车削刀具,包括刀具材料、刀具形状和刀具刃口角等参数的优化,可以有效地提高车削效率和切削质量。
4.2 优化钻孔参数钻孔加工过程中,合理选择钻头的直径、钻速和进给速度等参数,可以确保钻孔的准确度和孔径的一致性。
4.3 合理控制磨削过程参数在曲轴的磨削过程中,需要合理控制磨削速度、进给速度和磨削液的使用量等参数,以避免过度磨削和热损伤,并提高磨削质量和效率。
5. 发动机曲轴加工工艺的改进方向为了进一步提高发动机曲轴的加工工艺,可以从以下几个方面进行改进:5.1 引入先进的加工设备引入先进的数控机床、研磨机等加工设备,提高加工精度和加工效率,降低能耗和劳动强度。
发动机曲轴制造技术新动向

发动机 曲轴制造技术新动向
◆ 山 东 滨 州 海 得 曲 轴 有 限市 仟 公 司 李 海 围
作者简 介 :
李海国 .毕业于东南大学机械 工程系机 电控制及 自动化专业 .现为 山东滨州海 得曲轴有 限责任 公司技 术中心工程师 .主要从事 CAD C / AM/ AP C P工作 ,目 前 已发表 了 《曲轴磨 削加 工 振动机 理及 消振 措施 》 、 《 曲轴制造技 术进展与未来 》等多篇论 文 。
图1
车用 发 动机 曲轴 材质 主要 有球 墨 铸铁 和锻 钢 两
目前 国内曲轴陈 旧生产线 多数 由普通机床 和专 用
生 粗加 工 类。由于球墨铸铁的切削性能良好, 可获得较理想的 机 床组 成 , 产效率 和 自动化程 度相对 较低 。 结 构形状 , 且和 钢质 曲轴一样可 以进行 各种热 处理 并 和 表面强化 处理来 提高 曲轴的抗疲 劳强 度 、 硬度 和耐 设备 多采用 多刀车床 车削 曲轴主 轴颈及 连杆 轴颈 , 工
摘要 :进入 2 世纪 以后 ,发动 机 曲轴 在制 造工 艺 、刀具 等方面 同 。 导 了近半个 多世 纪 的多刀车 领 削工 艺和手 工磨 削工 艺 ,由于加工精 度低和 柔性 差等原 因 ,将逐步 退 出历史 舞 台 。而 高速 、高效 、复合加 工技 术及装 备迅 速进 入汽车 及零 部件 制造业 , 曲轴 的高速 高效 复合 加工技 术在 行业 内已有相 当程 度的应 用 , 必将代表这 也
.
fe i l . d t a , h i h p e h g — fi i n y、 o l x b e An t t e h g -s e d、 i h e fc e c c mp e c i i g t c n l g n h l x ma h n n e h o o y a d e u p n a ee t r d a t mo i n a t i d sr . i e h o o y h sb e s d t q i me t v n e e u o h b l a d p r s n u ty Th st c n l g a e n u e o e a t mo iea d i d sr , n l d l g t e e o me t u r n . uo b l n n u t y a d i wil e e a ed v l p t n re t c
毕业设计(论文)发动机曲轴加工工艺分析与设计

毕业设计(论文)题目:发动机曲轴加工工艺分析与设计作者:系(部):专业班级:指导教师:职称:年月日发动机曲轴加工工艺分析与设计摘要曲轴是汽车发动机的关键零件之一,其性能好坏直接影响到汽车发动机的质量和寿命.曲轴在发动机中承担最大负荷和全部功率,承受着强大的方向不断变化的弯矩及扭矩,同时经受着长时间高速运转的磨损,因此要求曲轴材质具有较高的刚性、疲劳强度和良好的耐磨性能。
发动机曲轴的作用是将活塞的往复直线运动通过连杆转化为旋转运动,从而实现发动机由化学能转变为机械能的输出。
本课题仅175Ⅱ型柴油机曲轴的加工工艺的分析与设计进行探讨。
工艺路线的拟定是工艺规程制订中的关键阶段,是工艺规程制订的总体设计。
所撰写的工艺路线合理与否,不但影响加工质量和生产率,而且影响到工人、设备、工艺装备及生产场地等的合理利用,从而影响生产成本。
所以,本次设计是在仔细分析曲轴零件加工技术要求及加工精度后,合理确定毛坯类型,经过查阅相关参考书、手册、图表、标准等技术资料,确定各工序的定位基准、机械加工余量、工序尺寸及公差,最终制定出曲轴零件的加工工序卡片。
关键词:发动机,曲轴,工艺分析,工艺设计目录第一章概述1第二章确定曲轴的加工工艺过程32.1曲轴的作用32.2曲轴的结构及其特点32.3曲轴的主要技术要求分析42.4曲轴的材料和毛坯的确定42.5曲轴的机械加工工艺过程42.6曲轴的机械加工工艺路线5第三章曲轴的机械加工工艺过程分析63. 1曲轴的机械加工工艺特点63. 2曲轴的机械加工工艺特点分析73. 3曲轴主要加工工序分析 (8)3.3.1铣曲轴两端面,钻中心孔 (8)3.3.2曲轴主轴颈的车削 (8)3.3.3曲轴连杆轴颈的车削 (8)3.3.4键槽加工 (9)3.3.5轴颈的磨削 (9)第四章机械加工余量、工序尺寸及公差的确定94.1曲轴主要加工表面的工序安排94.2机械加工余量、工序尺寸及公差的确定104.2.1主轴颈工序尺寸及公差的确定104.2.2连杆轴颈工序尺寸及公差的确定104.2.3φ22 -00.12外圆工序尺寸及公差的确定104.2.4φ20 0-0.021外圆工序尺寸及公差的确定114.3确定工时定额114.4 曲轴机械加工工艺过程卡片的制订 (11)谢辞13参考文献14附录15第一章概述曲轴是发动机上的一个重要的旋转机件,装上连杆后,可承接活塞的上下(往复)运动变成循环(旋转)运动。
曲轴加工新技术应用综述

如美国底特律福特发动机厂曲轴生 主要 定位基 准是 两端 中心 孔 。按其加 在 后面 的动 平衡 工 序 中需 多次 反 复测 量
年 产 V 发 动机 球 铁 曲轴 5 . 万 件 。 先 或 其 它 方 式 找 出 曲 轴 支 承 轴 颈 的 几 何 效率低 ,且会造成个别半成品报废。基 8 3 5 进 技 术主 要 有 两个 方面 :一 是 大量 采 用 中l. 此 中I. 加 工 出 的 中心 孔 称 为 于 这 种原 因 。国外 大 都采 用 了质 量 中心 b。在 ’ b 、 上 了C C 制技 术 。形 成 柔性 生产线 。二 几何 中心 孔 ;另一 种 是 利 用专 门的质 量 孔 。利用专 门设计 的测试设备来测试质 N 控 是 应 用 了许 多 先进 的曲 轴高 速 、高 效 、 定 心 机 测 出 曲轴 的质 量 中心 。在此 中心 量 中心 。然后 加 工 出 中心 孑 。并且 可将 L 柔性 加 工技 术 。简化 了 工艺 过 程 。提 高 上加 工 出 的 中心 孔称 为 质量 中心 孔 。 由 铣 两端 长 度和 加 工质 量 中心 孔 合 并 为一 和稳 定 了 加工 质 量 。同时也 缩 短 了单 件 于毛 坯 的 几何 形 状误 差 和质 量 分 布 不匀 道工序 。采用C 技术控制 。加工效率 NC
I 短 。但效率高 、产量大 。加工出的 _ ,
曲轴质量 好且很稳 定。 产线 只有 1 道 工序 。占地 面积6 6 m 。 7 97 2
钻质量中心孔技术
曲轴 属 于 细长 类 零 件 。加 工 过 程 中 而 且在 加 工 后剩 余 的动 不 平衡 量 较 大 。 工 位 置可 分 为两种 : 种是 利 用双V 一 型块 和去重 才能达 到要求 。影响生产节拍 。
曲轴加工工艺

曲轴加工工艺1曲轴的功用、结构特点及工作条件曲轴在发动机内是一个高速旋转的长轴,它将活塞的直线往复运动变为旋转运动,进而通过飞轮把扭矩输送给底盘的传动系,同时还骆动配气机构及其它辅助装置,所以其受力条件相当复杂,除了旋转质量的离心力外,还承受周期性变化的气体压力和往复惯性力的共同作用,使曲轴承受弯曲与扭转载荷。
为保证工作可靠,曲轴必须要有足够的强度和刚度,各工作表面要耐磨。
而且润滑良好。
其结构主要由主轴颈、连杆轴颈、油封轴颈、齿轮轴颈、皮带轮轴颈和曲柄臂等组成。
2 曲抽的毛坯材料及制造方法CA6102发动机曲轴采用45"钢模锻方式制造,它具有较高的刚度、强度和良好的耐磨性。
3 曲轴的主要加工表面及技术要求CA6102发动机曲轴的主要加工表面及技术要求如下:1.主轴颈:曲轴共有7个主轴颈,它们是曲轴的支点。
为了最大限度地增加曲轴的刚度,通常将主轴颈设计得粗一些,尽管这会增加重量,但是它可以大大提高曲轴的刚度,增加重叠度,减轻扭振的危害。
主轴颈为,圆柱度公差为。
第一轴颈长,第四轴颈宽,第七轴颈宽,第二、三、五、六轴颈宽以第一、七主轴颈为基准。
第四主轴颈的径向跳动公差为0.05mm。
2.连杆轴颈:曲轴共有六个连杆轴颈,它与连杆总成大头相连接。
轴颈为,圆柱度公差为0.005mm。
轴颈宽38H10mm,其与主轴颈的重叠度为11.35mm。
油封轴颈:油封轴颈为。
4.曲柄臂:曲柄臂用于连接主轴颈和连杆轴颈,共有十二个。
它呈长圆形,是曲轴的薄弱环节。
容易产生扭断和疲劳破坏。
曲柄半径为R(57.15士0.07)mm。
5.各连杆轴颈轴心线的相位差在之内。
6.曲轴必须经过动平衡,精度为。
7.主轴颈、连杆轴颈要进行表面淬火,淬硬深度2mm-4mm,55-53HRC。
油封轴颈(即安装飞轮轴颈)也要进行表面淬火,淬硬深度不小于1mm,54-63HRC。
8.曲轴还要进行探伤检查。
要求曲轴的加工表面不允许出现“发裂”。
曲轴制造技术及特种工艺
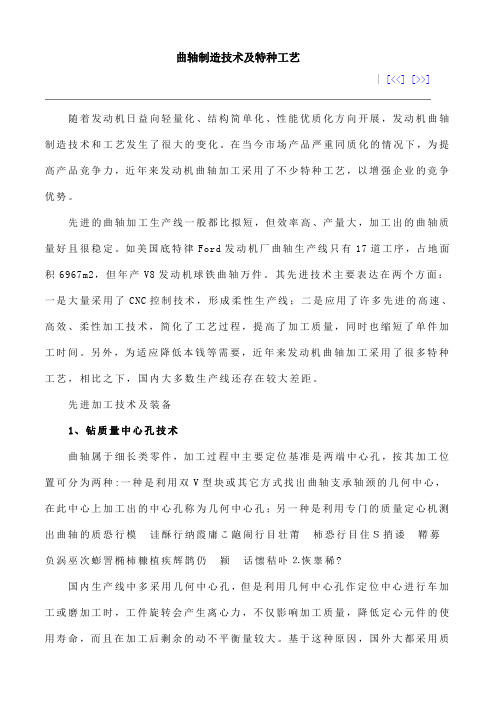
曲轴制造技术及特种工艺| [<<][>>]随着发动机日益向轻量化、结构简单化、性能优质化方向开展,发动机曲轴制造技术和工艺发生了很大的变化。
在当今市场产品严重同质化的情况下,为提高产品竞争力,近年来发动机曲轴加工采用了不少特种工艺,以增强企业的竞争优势。
先进的曲轴加工生产线一般都比拟短,但效率高、产量大,加工出的曲轴质量好且很稳定。
如美国底特律Ford发动机厂曲轴生产线只有17道工序,占地面积6967m2,但年产V8发动机球铁曲轴万件。
其先进技术主要表达在两个方面:一是大量采用了CNC控制技术,形成柔性生产线;二是应用了许多先进的高速、高效、柔性加工技术,简化了工艺过程,提高了加工质量,同时也缩短了单件加工时间。
另外,为适应降低本钱等需要,近年来发动机曲轴加工采用了很多特种工艺,相比之下,国内大多数生产线还存在较大差距。
先进加工技术及装备1、钻质量中心孔技术曲轴属于细长类零件,加工过程中主要定位基准是两端中心孔,按其加工位置可分为两种:一种是利用双V型块或其它方式找出曲轴支承轴颈的几何中心,在此中心上加工出的中心孔称为几何中心孔;另一种是利用专门的质量定心机测出曲轴的质恐行模诖酥行纳霞庸こ龅闹行目壮莆柿恐行目住S捎诿鞯募负涡巫次蟛詈椭柿糠植疾辉鹊仍颍话懔秸卟⒉恢睾稀?国内生产线中多采用几何中心孔,但是利用几何中心孔作定位中心进行车加工或磨加工时,工件旋转会产生离心力,不仅影响加工质量,降低定心元件的使用寿命,而且在加工后剩余的动不平衡量较大。
基于这种原因,国外大都采用质量中心孔,利用专门设计的测试设备来测试质量中心,然后加工出中心孔,并且可将铣两端长度和加工质量中心孔合并为一道工序,采用CNC技术控制,加工效率很高。
但需要注意的是,假设毛坯弯曲变形严重或质量严重分布不均匀,采用质量中心孔仍不能彻底解决上述问题。
因此,笔者认为曲轴的质量中心孔和几何中心孔应按毛坯质量的好坏合理选用:如果毛坯质量好,加工余量小且加工余量分布均匀,这时曲轴的质量中心孔与几何中心孔会根本重合,不必花费较高的经费购置质量定心设备;如果毛坯质量较差,加工余量大且加工余量分布不均匀,那么优先选用质量中心孔。
曲轴柔性精密高效磨削加工关键技术与成套装备自主化实现重大突破
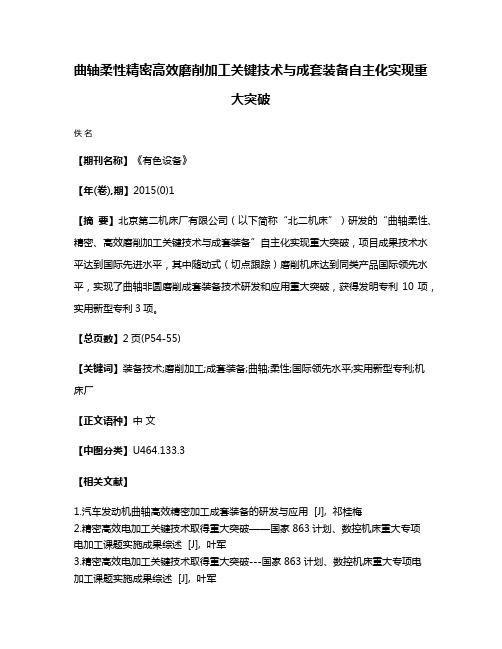
曲轴柔性精密高效磨削加工关键技术与成套装备自主化实现重
大突破
佚名
【期刊名称】《有色设备》
【年(卷),期】2015(0)1
【摘要】北京第二机床厂有限公司(以下简称“北二机床”)研发的“曲轴柔性、精密、高效磨削加工关键技术与成套装备”自主化实现重大突破,项目成果技术水平达到国际先进水平,其中随动式(切点跟踪)磨削机床达到同类产品国际领先水平,实现了曲轴非圆磨削成套装备技术研发和应用重大突破,获得发明专利10项,实用新型专利3项。
【总页数】2页(P54-55)
【关键词】装备技术;磨削加工;成套装备;曲轴;柔性;国际领先水平;实用新型专利;机床厂
【正文语种】中文
【中图分类】U464.133.3
【相关文献】
1.汽车发动机曲轴高效精密加工成套装备的研发与应用 [J], 祁桂梅
2.精密高效电加工关键技术取得重大突破——国家863计划、数控机床重大专项
电加工课题实施成果综述 [J], 叶军
3.精密高效电加工关键技术取得重大突破---国家863计划、数控机床重大专项电
加工课题实施成果综述 [J], 叶军
4.北京二机床“曲轴柔性、精密、高效磨削加工关键技术与成套装备”成果通过鉴定 [J],
5.北二机床“汽车发动机曲轴高效精密加工成套装备”再获殊荣 [J],
因版权原因,仅展示原文概要,查看原文内容请购买。
- 1、下载文档前请自行甄别文档内容的完整性,平台不提供额外的编辑、内容补充、找答案等附加服务。
- 2、"仅部分预览"的文档,不可在线预览部分如存在完整性等问题,可反馈申请退款(可完整预览的文档不适用该条件!)。
- 3、如文档侵犯您的权益,请联系客服反馈,我们会尽快为您处理(人工客服工作时间:9:00-18:30)。
发动机曲轴加工新技术
1. 曲轴加工工艺流程
乘用车涡轮增压发动机曲轴加工的典型工艺流程:动平衡、打质量中心孔→车第5主轴颈→车法兰→粗加工主轴颈、连杆颈及轴肩→钻油道孔及倒角→粗磨主轴颈、连杆颈轴颈、侧壁及沉割槽→清洗、吹干→圆角滚压→精车、滚光止推面+精车小端→精车法兰端面及凹槽→精磨主轴颈、连杆颈、小端→加工两端螺纹孔、销孔及铰法兰端中心孔→精磨曲轴法兰端→曲轴动平衡去重→砂带抛光主轴颈、连杆颈及法兰外颈→自动检查、作标记→曲轴最终清洗。
2. 先进技术的应用
(1)动平衡、打质量中心孔。
曲轴加工过程中的定位基准为中心孔,按其加工位置可分为几何中心孔和质量中心孔,利用V形块或其他方式找出曲轴主支承轴颈的几何中心,在此中心上加工出的中心孔称为几何中心孔。
利用专用的测试设备测量出曲轴的质量中心,在此中心上加工出的中心孔称为质量中心孔。
当采用几何中心孔进行后续的车、磨加工时,工件旋转产生离心力,会影响加工质量,而且加工后剩余的动不平衡量较大,在动平衡工序中需多次反复测量和去重才能达到技术要求,效率低,影响生产节拍,造成半成品废品率的增加和定位元件的损耗。
采用质量中心孔就能解决这类问题,提高循环节拍。
图1所示为COMAU SYMES10型曲轴质量中心测量机,曲轴放置在设备的鼠笼中,与鼠笼一起旋转,测量出鼠笼与零件一起的不平衡量为M,鼠笼的不平衡量(M1)是已知的,零件的不平衡量M2=M-M1。
通过专用的计算公式,设备可通过M2自动算出曲轴的平衡轴的坐标位置,将测量结果传输至COMAUSDC700L型全自动曲轴两端加工中心,其测量不确定度≤40μm,可以测量多个品种的曲轴,零件品种可自动识别,循环时间为1.2min,设备简单可靠。
(2)高速外铣粗加工曲轴。
高速外铣粗加工曲轴主轴颈、连杆颈及轴肩,比CNC车削、CNC内铣、车-车拉的生产效率高且质量稳定。
如CNC车-车拉工艺加工连杆轴颈要二道工序,而CNC高速外铣只要一道工序就能完成,高速外铣粗加工曲轴的显著特点为:切削速度可达350m/min、切削时间短、工序循环时间短、切削力较小、工件温升低、刀具寿命高、换刀次数少、加工精度更高、柔性更好,是曲轴主轴颈和连杆轴颈粗加工的发展方向。
NILES-SIMMONS N20曲轴外铣机床(见图2)可同时加工曲轴主轴颈、连杆颈,机床采用双刀主轴,各个主轴的运动独立,每个主轴带一个刀盘,每个刀盘的加工程序及其参数均独立。
将零件放置到辅助上料装置上,辅助上料装置将零件放置到加工区域;卡盘夹紧零件法兰,顶尖从后部顶紧;零件旋转,左右两个刀盘在刀具主轴上按照一定速度旋转同时沿径向前后运动,实现加工主轴颈和连杆颈。
床身(W/Z轴)直线型滚动导轨、横向拖板(U/X轴)直线型滚动导轨。
数控控制系统采用SINUMERIK840D sl的技术数据, 铣削操作模块化微处理器数控连续轨迹控制,集成PLC与数字完整的解决方案SINAMICS S120。
(3)数控曲轴磨床的应用。
粗磨主轴颈、连杆颈轴颈、侧壁及沉割槽。
数控曲轴磨床可一次装夹磨削全部曲轴主轴颈和连杆轴颈,此类磨床一般配双砂轮头架,可满足多品种、低成本、高精度、大批量生产,应用工件回转和砂轮进给伺服联动控制技术,可以一次装夹而不改变曲轴回转中心即可完成所有轴颈的磨削,包括随动跟踪磨削连杆轴颈;采用静压主轴、静压导轨、静压进给丝杠(砂轮头架)和线性光栅闭环控制系统,磨削轴颈圆度精度高,且磨削效率极高。
JUCRANK 6S 10-10数控外圆曲轴磨床(见图3)用于粗磨曲轴的主轴颈和连杆颈及沉割槽。
设备自带的机械手从上料滚道上将零件抓起,然后放置到设备内部的预支撑块上;夹具自动夹紧零件;零件旋转,两个砂轮前进,按照程序进行径向移动,同时磨削主轴颈和连杆颈,加工完毕后,砂轮后退,零件停止旋转后,夹具松开,机械手抓取零件,放置到下料滚道上。
X/Z轴定位精度为0.004mm;重复定位精度为0.002mm;采用了MARPOSS自动直径量仪和轴向量仪,确保直径和轴向尺寸的精度监控。
精磨主轴颈、连杆颈和小头端。
使用JUCENTER 6L CRANK数控外圆曲轴磨床(见图4)精磨曲轴的主轴颈和连杆颈,带有两个工位,第一个工位精磨曲轴的连杆轴颈和第二个工位精磨曲轴的主轴颈,设备自带的机械手从上料滚道上将零件抓起,然后放置到设备内部第一个工位的预支撑块上,第一工位的夹具自动夹紧零件,零件旋转,第一个工位对应的砂轮前进,按照程序进行径向移动,磨削连杆颈;加工完毕后,砂轮后退,零件停止旋转后,夹具松开。
机械手抓取零件,放置到第二个工位的预支撑块上;二工位的夹具自动夹紧零件,零件旋转,第二个工位对应的砂轮前进,按照程序进行径向移动,磨削主轴颈;加工完毕后,砂轮后退,零件停止旋转后,夹具松开。
机械手抓取零件,放置到下料滚道上,开始下一个加工循环。
X/Z轴定位精度为0.004mm;重复定位精度为0.002mm。
(4)数控卧式车床的广泛应用。
DANOBAT NA750型曲轴止推面精车机床配备自动检测装置,零件完成夹紧后,测头自动检测止推面宽度,确定其中心线,以此为加工基准,并根据上一件曲轴的加工情况进行自动补偿,进而实现以中心线为加工基准、等余量地对止推面两个侧面进行精车加工,车削完毕后自动检测止推面宽度,同时完成小端及沟槽的加工。
车削完成后,车刀退回,滚光头伸出,同时滚光止推两端面。
滚光时,滚光面具备良好的润滑。
NA500型精车法兰端面及凹槽机床配备自动检测装置,零件完成夹紧后,测头自动检测止推面至法兰端面距离。
X轴定位精度0.022mm、重复定位精度0.006mm,Z轴定位精度0.008mm、重复定位精度0.004mm。
(5)曲轴砂带抛光机的应用。
采用GRINDMASTER曲轴砂带抛光机对曲轴的油封颈、主轴颈、连杆颈进行抛光,抛光时先对工件进行喷淋清洗,再采用砂带包住零件的方式进行抛光。
抛光时有两个旋转方向,最后的抛光方向和发动机正常运转方向相同(从飞轮侧看);抛光完后,进行甩干脱油的工作,设备需自带抛光液处理系统。
(6)曲轴圆角滚压机。
关于HEGENSCHEIDT MFD7895型曲轴滚压机,其控制系统采用西门子PLC S7-300,机床安装了9个滚压单元,这些单元是用来对曲轴进行滚压和校直的,最大滚压力30kN;脉冲式滚压连杆颈,减小工件变形;通过整合在滚压单元中的压力传感器和位置传感器及滚压深度传感器,实现滚压压力的检测监控;滚压后自动检测主轴颈跳动并通过滚压进行校直;配备断刀检测装置;电子测量探头对曲轴的所有主轴颈进行径向跳动测量;通过激光头探测连杆颈的最高点,识别零件的品种。
(7)曲轴油孔加工机床。
HORKOS Imql曲轴油道孔及倒角加工机床,采用3个工步对油道孔进行加工,铣平面→钻油道孔→倒角,克服原来设备一道钻孔工步的质量不稳定、断刀频繁以及人工倒角等缺点,设备与工序能力值一次合格,循环时间低于1.3min。
(8)曲轴动平衡去重机。
COMAU SYME S10测量与校正曲轴动平衡机由测量工位、气动回转传输装置、钻孔校正工位组成;平衡测量,测量和显示不平衡量,自动分解计算钻孔数据,钻孔校正、不平衡量复检等动作全部为自动。
测量工位的测量不确定度≤1g·cm,校正工位的最大钻削进给速度≥500mm/min。
3. 结语
随着乘用车发动机趋于轻量化、结构简单化以及性能高效化,作为发动机核心零件的曲轴,其制造工艺也将发生较大的变化,高速、高效、柔性、复合化的技术是曲轴制造发展的主要方向,先进的曲轴生产线一定是生产线短、效率高、人员少、生产过程稳定、产品质量可靠的自动化生产线。