浅谈梯形螺纹的编程与加工
浅谈梯形螺纹在数控车床上的加工与编程
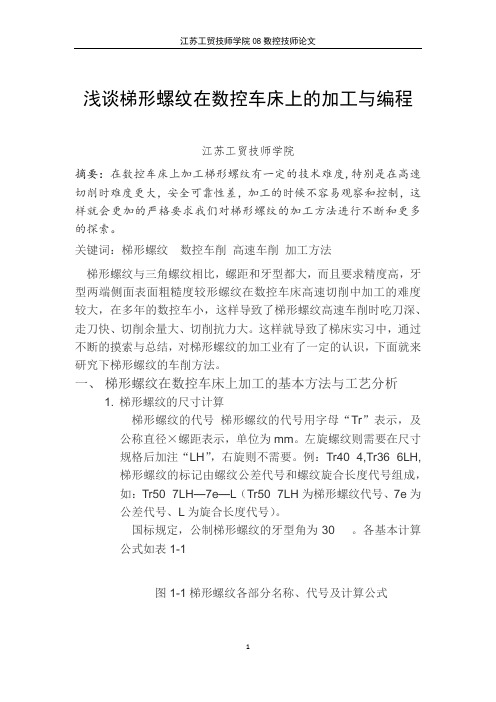
浅谈梯形螺纹在数控车床上的加工与编程江苏工贸技师学院摘要:在数控车床上加工梯形螺纹有一定的技术难度,特别是在高速切削时难度更大,安全可靠性差,加工的时候不容易观察和控制,这样就会更加的严格要求我们对梯形螺纹的加工方法进行不断和更多的探索。
关键词:梯形螺纹数控车削高速车削加工方法梯形螺纹与三角螺纹相比,螺距和牙型都大,而且要求精度高,牙型两端侧面表面粗糙度较形螺纹在数控车床高速切削中加工的难度较大,在多年的数控车小,这样导致了梯形螺纹高速车削时吃刀深、走刀快、切削余量大、切削抗力大。
这样就导致了梯床实习中,通过不断的摸索与总结,对梯形螺纹的加工业有了一定的认识,下面就来研究下梯形螺纹的车削方法。
一、梯形螺纹在数控车床上加工的基本方法与工艺分析1. 梯形螺纹的尺寸计算梯形螺纹的代号梯形螺纹的代号用字母“Tr”表示,及公称直径×螺距表示,单位为mm。
左旋螺纹则需要在尺寸规格后加注“LH”,右旋则不需要。
例:Tr40×4,Tr36×6LH,梯形螺纹的标记由螺纹公差代号和螺纹旋合长度代号组成,如:Tr50×7LH—7e—L(Tr50×7LH为梯形螺纹代号、7e为公差代号、L为旋合长度代号)。
国标规定,公制梯形螺纹的牙型角为30°。
各基本计算公式如表1-1图1-1梯形螺纹各部分名称、代号及计算公式2.梯形螺纹加工的基本方法(1)直进法。
螺纹车刀X向间歇进给到牙深处。
采用这种方法加工梯形螺纹时,螺纹车刀的三面都参加了切削,这样会导致加工是排削困难,切削力和切削热增加,刀尖磨损严重。
如果进刀量大时,有可能会出现“扎刀”现象。
这种方法在数控车床里用指令G92和G32来实现。
例:G32/G92单段螺纹切削指令G32/G92X(U)Z(W) FX(U)Z(W)为螺纹种点的坐标,F为导程。
G32/G92属于直进式切削方法,加工程序编写繁琐,工作量大。
(2)斜进法。
数控车床加工梯形螺纹的方法与技巧
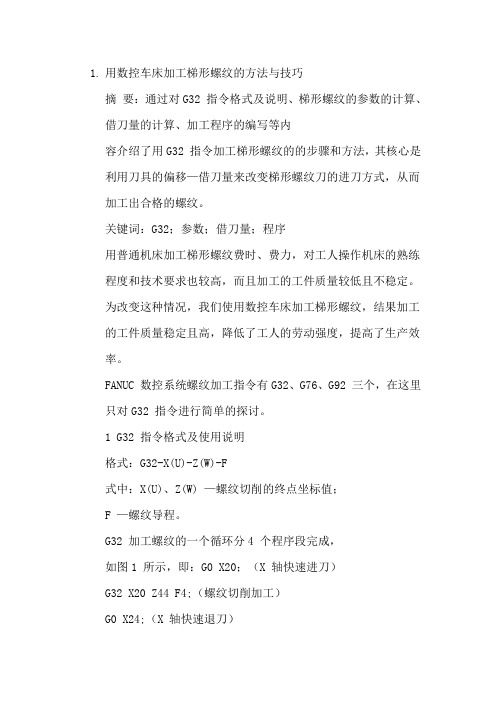
1.用数控车床加工梯形螺纹的方法与技巧摘要:通过对G32 指令格式及说明、梯形螺纹的参数的计算、借刀量的计算、加工程序的编写等内容介绍了用G32 指令加工梯形螺纹的的步骤和方法,其核心是利用刀具的偏移—借刀量来改变梯形螺纹刀的进刀方式,从而加工出合格的螺纹。
关键词:G32;参数;借刀量;程序用普通机床加工梯形螺纹费时、费力,对工人操作机床的熟练程度和技术要求也较高,而且加工的工件质量较低且不稳定。
为改变这种情况,我们使用数控车床加工梯形螺纹,结果加工的工件质量稳定且高,降低了工人的劳动强度,提高了生产效率。
FANUC 数控系统螺纹加工指令有G32、G76、G92 三个,在这里只对G32 指令进行简单的探讨。
1 G32 指令格式及使用说明格式:G32-X(U)-Z(W)-F式中:X(U)、Z(W) —螺纹切削的终点坐标值;F —螺纹导程。
G32 加工螺纹的一个循环分4 个程序段完成,如图1 所示,即:G0 X20;(X 轴快速进刀)G32 X20 Z44 F4;(螺纹切削加工)G0 X24;(X 轴快速退刀)G0 Z5;(Z 轴快速退刀),提醒注意:设定δ1、δ2 的数值要合适恰当。
图1 车刀走刀路线2 梯形螺纹参数的计算以图2 为例说明梯形螺纹参数的计算。
图2 零件图表1 梯形螺纹参数表名称代号计算公式计算结果/mm螺距牙顶间隙大径中径小径牙高Pacdd2d3h4 mm0.25 mm公称直径d2 =d-0.5Pd3=d-2hh=0.5P+ac40.25222017.502.253 采用偏移刀具的方法加工梯形螺纹G32 加工螺纹的进刀是直进法,如图3 所示,这种进刀法是车刀的三棱同时切削,容易产生震动和扎刀现象。
如采用偏移刀具的方法,即使车刀沿着Z轴方向移动一定的量(普通车床中的借刀量),那么车刀的进刀方式就变成图4 所示的方式,这样车刀的两棱切削能有效的防止震动和扎刀,提高了梯形螺纹的质量。
图3 车刀直进法图4 车刀斜进法以表2 为例说明借刀量的计算:总借刀量的计算:h×tan150=2.25×0.2679=0.603 mm每刀借刀量的计算:ap×tan150每刀借刀量的数值如表2 所示。
浅谈数控车削梯形螺纹的加工方法

浅谈数控车削梯形螺纹的加工方法摘要:梯形螺纹的加工是数控车削一个难点,本文介绍了直进法、左右切削法、斜进法和分层切削法四种梯形螺纹加工方法,分析了各个切削方法的特点得出分层切削法加工梯形螺纹较好。
用分层切削法编写切削加工程序实际案例,为车削合格梯形螺纹提供了参考。
关键词:梯形螺纹;分层切削;数控车削梯形螺纹较之三角螺纹,其螺距和牙型都大,且精度高,牙型两侧面表面粗糙度值较小,致使梯形螺纹车削时吃刀深、走刀快、切削余量大、切削抗力大。
用数控车床加工梯形螺纹比三角型螺纹更难,在加工时易产生扎刀现象。
下面通过实例来说明数控车削螺纹的三种常用方法。
1.数控车削梯形螺纹的三种常用方法在数控车床上高速直进法车削梯形螺纹时,车刀刀头宽度应等于牙槽底宽。
直进法加工梯形螺纹时车刀z向不作移动,x向间歇地进给,见图1,在多次行程中逐步车削至螺纹小径,同时保证螺纹中径及牙型两侧粗糙度。
采用此方法车削时,车刀三刃切削,导致加工切削力和切削热增加,排屑困难。
当切到一定深度或当进给量过大时,可能产生“扎刀”和“爆刀”现象。
该方法主要用于刀具材料和质量较好且加工螺距不大于6mm的梯形螺纹。
1.2 左右切削法在数控车床上用左右切削法车削梯形螺纹时,车刀尖宽度应比螺纹槽底宽度窄一点。
左右切削法加工梯形螺纹时螺纹车刀沿螺纹牙型角方向左右借刀,见图2,间歇地进给至牙深处,刀具沿螺纹的牙型线进行左、右切削,或左、中、右切削,切削深度很小。
此种方法可以防止因三个切削刃同时参加切削而产生振动和扎刀现象,从而保证螺纹的尺寸精度和表面粗糙度。
大导程的梯形螺纹因为牙型宽度较大,比较适合使用左、中、右分层进行切削的加工方法。
在数控车床上该种方法常采用宏程序编程来实现。
1.3 斜进法又称单面切削法,见图3。
螺纹车刀沿牙型角方向斜向间歇进给至牙深处,此种方法螺纹车刀始终只有一个侧刃参加切削,从而使排屑比较顺利,刀尖的受热和受力情况有所改善,在车削中不易引起扎刀现象,可以采用G76指令来实现。
浅谈车削梯形外螺纹的加工方法

浅谈车削梯形外螺纹的加工方法车削梯形外螺纹是机械加工中常用的一种方法,广泛应用于汽车、机械制造等行业。
本文将从加工原理、加工方法以及工艺优化等方面对车削梯形外螺纹进行讨论。
梯形外螺纹的加工原理相对简单,即利用车床进行螺纹车削。
所谓梯形外螺纹是指螺纹牙的截面形状呈梯形,具体可以分为M型和MJ型两种。
梯形螺纹的主要参数有螺距、齿顶直径、齿根直径和螺纹锥度等,加工时需要根据给定的参数进行设置。
对于梯形外螺纹的加工,常用的方法有单刀片车削法、双刀片车削法和索引盘车削法。
下面将分别介绍这三种方法的特点和应用。
首先是单刀片车削法。
单刀片车削法适用于一些中等精度的螺纹加工,加工效率较高。
它的特点是只需要一把刀具即可完成整个螺纹的加工,节约了成本。
但是由于只有一把刀具,所以无法进行深孔加工,适用于螺纹长度较短的工件。
其次是双刀片车削法。
双刀片车削法适用于一些高精度和较长长度的梯形外螺纹加工。
它的特点是可以同时进行齿顶和齿根的车削,提高了加工精度。
双刀片车削法需要两把刀具同时进行切削,因此较单刀片车削法来说,加工效率相对较低。
最后是索引盘车削法。
索引盘车削法适用于批量生产的梯形外螺纹加工,加工效率较高。
它的特点是利用索引盘进行分度,每次轮转一个螺纹牙的角度,然后进行车削。
索引盘车削法适用于螺纹长度较长的工件,但是需要专门设计制作索引盘,成本较高。
对于车削梯形外螺纹的加工过程中,有几点需要特别注意。
首先是刀具的选用和磨削。
由于梯形外螺纹的牙形较复杂,所以刀具的要求较高,需要选择质量好、刚性强的刀具。
其次是加工过程中的刀具进给和主轴转速的选择。
进给过大会导致切削力过大,加工质量下降;主轴转速过高则会增加工件的热变形。
最后是加工润滑液的选择和使用,润滑液的作用是冷却刀具和工件,减少摩擦阻力。
车削梯形外螺纹是一种常用的机械加工方法。
通过合理选择加工方法和刀具,控制加工参数和加工工艺,可以获得高精度、高效率的梯形外螺纹加工。
梯形螺纹数控车削编程与加工研究

梯形螺纹数控车削编程与加工研究摘要:对比普通车床加工梯形螺纹的工艺方法和数控车宏程序编程特点,应用宏程序中的变量运算、逻辑运算和条件转移,用分层切削方法,分粗车和精车对梯形螺纹分别编程,解决现有梯形螺纹宏程序粗车、精车不分的编程方式,与现有编程方法相比,此方法为达到高效、稳定地车削梯形螺纹提供参考。
标签:梯形螺纹;数控加工;分层法;精加工1 梯形螺纹加工工艺分析常用梯形螺纹车削方法如图1所示,a直进法适合用螺纹加工指令G32、G92编程,该方法梯形螺纹车刀的前、左、右三面切削,刀头部分切削力受力较大,而且排屑困难,刀尖磨损严重,产生“扎刀”现象,适合小螺距螺纹加工;b斜进式方法螺纹车刀沿牙型角方向斜向、间歇进给至牙底,车刀单刃切削,G76指令编程使用较多;c交错式车削加工是最常用的方法,该方法刀具左右两切削刃磨损、受力均匀,牙形正确,牙根清晰。
此法适用于加工螺距较大的螺纹。
2 梯形螺纹宏程序编程如图2所示梯形螺纹加工图,查阅现资料中,无论用螺纹加工指令(G92、G32、G76)编程还是宏程序编程,都极少用粗加工和精加工分开编程,因为螺纹加工指令不能单独实现精加工,宏程序编程计算比较麻烦,但是梯形螺纹加工不可能一次精车就能够达到尺寸要求,往往需要3-5次精加工才能达到合格要求,因此每次精车都要重复执行粗车的指令或语句,增加了辅助时间。
现以交错式分层切削方式,以粗车和精车分别对图2编程。
首先计算梯形螺纹各部分尺寸,依据表1,计算如下:螺纹大径d=36;螺纹中径d2=d-0.5P=36-3=33mm,查表确定其公差,故d2=33;螺纹牙高h3=0.5P+ac=3.5mm;螺纹小径d3=d-2h3=29mm,查表确定其公差,故d3=29;螺纹牙顶宽f=0.366P=2.196mm螺纹牙底宽W=0.366P-0.536ac=2.196-0.268=1.928mm梯形螺纹刀刀头宽b=1.8mm。
粗、精加工程序如下:粗车O0001;(程序名)N1;T0101;(1号梯形螺纹螺纹刀具)M3 S80;(正转80r/min)G0 X38 Z12; (起刀点)#1=0.8;(初始第一刀深度)#5=36;(被车工件的初始直径)#6=15;(导入空刀量)#7=-40;(螺纹长度)N10 #8=TAN[15]*3.5-TAN[15]*#1;(Z向借刀距离)G0 [#5-2*#1] Z[#6-#8];(Z向左借刀)G32 Z[#7-6] F6;(车左侧螺纹)G0 X40;(退刀)Z[#6+#8];(Z向右借刀)G0 X[#5-2*#1];(X切削深度)G32 Z[#7-6] F6;(Z向右借刀)G0 X40;(退刀)#5=#5-#1;(被车工件的直径减小量)#1=#1-0.1;(调整切削深度)IF[#5 GE 32.5] GOTO10;(条件判断是否小于等于32.5)G0 X100 Z100;(返回换刀点)M00;(暂停)N2;精车T0101;(1号梯形螺纹螺纹刀具)M3 S60;(正转60r/min)G0 X38 Z12; (起刀点)#1=0.1;(初始第一刀深度)#5=36;(被车工件的初始直径)#6=15;(导入空刀量)#7=-40;(螺纹长度)N10 #8=TAN[15]*3.5-TAN[15]*#1;(Z向借刀距離)G0 [#5-2*#1] Z[#6-#8];(Z向左借刀)G32 Z[#7-6] F6;(车左侧螺纹)G0 X40;(退刀)Z[#6+#8];(Z向右借刀)G0 X[#5-2*#1];(X切削深度)G32 Z[#7-6] F6;(Z向右借刀)G0 X40;(退刀)#5=#5-#1;(减小被车工件的直径)IF[#5 GE 29] GOTO10;(条件判断是否小于等于29)G0 X100 Z100;(返回换刀点)M05;(停主轴)M30;(结束程序)上述程序执行一次粗、精车后,螺纹尺寸仍有余量,可以从程序N2开始执行,只执行精车加工。
数控车床梯形螺纹切削及编程方法应用

数控车床梯形螺纹切削及编程方法应用[摘要] 从梯形螺纹在数控车床中的各种加工方法进行比较,从而找到既能达到加工精度,又便于在数控车床中编程,还能提高加工效率的加工方法。
[关键词] 数控车床梯形螺纹切削编程前言梯形螺纹加工是车削加工中一项基本技术,但由于数控车床的加工方式,特别是经济型数控车床在加工梯形螺纹中的局限较多,因此,梯形螺纹的编程及加工都成为了难加工技术。
本文中主要研究了在GSK980T数控系统中如何进行梯形螺纹编程、加工及精度控制。
一、梯形螺纹的切削方法车削加工梯形螺纹的切削方法有很多,一般有单刀完成和多刀完成两种。
图一1、单刀完成:这种方法对于螺距小于4mm的梯形螺纹可行,当螺距大于4mm后由于切削力和刀具磨损的影响,单刀完成则效果不好。
具体方法有以下几种:直进法:如图一a所示,刀具采用与牙型槽等宽的尺寸,加工时只做横向进刀。
这种方法在加工加工梯形螺纹时,螺纹的牙型精度较高,但由于三刀刃均参与切削,切削力过大容易导致加工变形,只在小螺距螺纹加工时采用。
斜进法:如图一b所示,刀具采用与牙型槽等宽的尺寸,加工中刀具纵向和横向做复合进刀。
这种方法在加工中刀具只有两面刀刃受力,可适当减小切削力,但由于两刃切削,刀具的磨损程度不同,加工中易出现刀尖角发生变化,而造成牙型精度较差。
这种方式只在梯形螺纹粗加工或螺纹精度不高时采用。
左右切削法:如图一c所示,刀具采用与牙型槽等宽的尺寸,加工中刀具纵向双向及横向做复合进刀。
这种方式加工刀具受力情况与斜进法相似,较易加工出梯形螺纹。
但该方式要求刀具纵向左右两侧移动结合横向进刀,对操作者技术要求较高,需多次操作后才能熟练掌握。
2、多刀组合法:一般梯形螺纹加工均采用这种方式。
组合方式很多,如单刀加工中的三种只做为粗加工,留一定余量后再采用精加工刀具完成加工。
再如图一d所示,这也是多刀组合中的一种,先用小切刀切直槽再用与牙型等宽的螺纹刀具加工。
二、螺纹编程指令在GSK980T数控系统中,提供了三个加工螺纹的编程指令,分别是逐段加工螺纹指令G32、螺纹加工循环指令G92、复合循环指令G76。
数控车床上加工梯形螺纹浅析
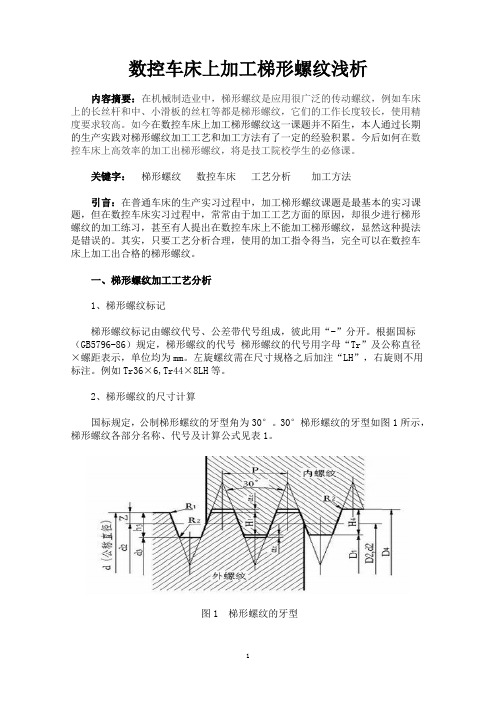
数控车床上加工梯形螺纹浅析内容摘要:在机械制造业中,梯形螺纹是应用很广泛的传动螺纹,例如车床上的长丝杆和中、小滑板的丝杠等都是梯形螺纹,它们的工作长度较长,使用精度要求较高。
如今在数控车床上加工梯形螺纹这一课题并不陌生,本人通过长期的生产实践对梯形螺纹加工工艺和加工方法有了一定的经验积累。
今后如何在数控车床上高效率的加工出梯形螺纹,将是技工院校学生的必修课。
关键字:梯形螺纹数控车床工艺分析加工方法引言:在普通车床的生产实习过程中,加工梯形螺纹课题是最基本的实习课题,但在数控车床实习过程中,常常由于加工工艺方面的原因,却很少进行梯形螺纹的加工练习,甚至有人提出在数控车床上不能加工梯形螺纹,显然这种提法是错误的。
其实,只要工艺分析合理,使用的加工指令得当,完全可以在数控车床上加工出合格的梯形螺纹。
一、梯形螺纹加工工艺分析1、梯形螺纹标记梯形螺纹标记由螺纹代号、公差带代号组成,彼此用“-”分开。
根据国标(GB5796-86)规定,梯形螺纹的代号梯形螺纹的代号用字母“Tr”及公称直径×螺距表示,单位均为mm。
左旋螺纹需在尺寸规格之后加注“LH”,右旋则不用标注。
例如Tr36×6,Tr44×8LH等。
2、梯形螺纹的尺寸计算国标规定,公制梯形螺纹的牙型角为30°。
30°梯形螺纹的牙型如图1所示,梯形螺纹各部分名称、代号及计算公式见表1。
图1 梯形螺纹的牙型表1 梯形螺纹基本尺寸计算公式3、梯形螺纹加工切削方法直进法螺纹车刀X向间歇进给至牙深处(如图2a)。
采用此种方法加工梯形螺纹时,由于两侧刃同时工作,切削力较大,而且排削困难,因此在切削时,切削刃容易磨损。
在切削螺距较大的螺纹时,由于背吃刀量较大,切削刃磨损较快,从而造成螺纹中径产生误差。
但是次法加工的牙形精度较高,因此一般多用于小螺距加工。
斜进法螺纹车刀沿牙型角方向斜向间歇进给至牙深处(如图2b)。
采用此种方法加工梯形螺纹时,螺纹车刀始终只有一个侧刃参加切削,切削刀具负载较小,从而使排屑比较顺利,并且背吃刀量为递减式。
浅谈梯形螺纹的加工方法和程序编制

中径 d2 d2=d一0.5P ,j、径 d3 d3=d一2h3=d—z(o.5p+ac1 牙 高 h3 h3=0.5P+ac 牙顶 宽 f f_0.366 P 牙 槽 底 宽 w w=O.366 P-O.536 ac
编 程 实例
FANuC系统 ,以 图 2为 例
TO101
M 03S600
GOOX35Z—l5
定 位 点
Байду номын сангаас#1=35
大 径
#2=29.5
小 径
WHILE[#1GE#2] DO1
#1-#1-0.1
GOOX[# ̄】
定 位 x定 位 Z
Z一15
G32Z一1O0F6
~
∞::
ac]mm 0.25 0.5 1
1 螺 纹车 刀材 料 的 选 择
外 螺 纹 大径 d公 称 直 径
常 用 的螺 纹 车 刀 材 料 有 高 速 钢 和 硬 质 合金 两 类 。 高 速 钢 螺 纹 车 刀 ,容 易 磨 得 锋 利 ,而 且 韧 性 较 好 ,刀 尖 不 易 崩 裂 , 车 出 的 螺 纹 表 面粗 糙 度 较 小 ,但 高 速 钢 的 耐 热 性较 差 。因 此 ,只适 用 于
故 该 指 令 多 用 于 小 螺 距螺 纹 的加 工 ,也 可 用 于 梯 形 螺 纹 的 加 工 。 3.2 G76螺 纹 切 削 复 合 固 定循 环 指令
图 2
G76 P精 车次 数 和 刀 尖 角 度 Q最 小 切 削 量 R精 加 工 余 量 6 G76 X Z P牙深 Q 第 一 次 背 吃 刀 量 F螺 距 X z 为 螺 纹 切 削 终 点 处 的坐 标 ;其 中 第 一‘行 的 Q 和 第 二 行 的 P、O 都 以微 米 为单 位 。 例如 G76 P030060 QlOO R0.1
浅谈车削梯形外螺纹的加工方法

浅谈车削梯形外螺纹的加工方法车削梯形外螺纹是机械制造中常见的一种加工方法,其具有许多特点和应用场景。
本文以梯形外螺纹的加工方法为主题,进行详细论述。
一、梯形外螺纹的基本概念和特点梯形外螺纹是一种具有梯形截面的螺纹,其形状类似于房子的楼梯,因此称为梯形螺纹。
梯形外螺纹具有以下几个基本特点:1. 梯形外螺纹的螺距是固定的,即单位长度上的螺纹齿数是固定的。
2. 梯形外螺纹的截面形状为梯形,其螺纹角度相对于齿距较小,通常为30度或45度。
3. 梯形外螺纹具有较高的强度和刚性,适用于承受较大的力矩和挤压力的场合。
4. 梯形外螺纹的加工精度要求较高,通常需要进行高精度的车削和螺纹度量。
二、梯形外螺纹的加工方法梯形外螺纹的加工主要有以下几种方法:1. 传统车削法:传统车削法是最常用的梯形外螺纹加工方法之一。
该方法使用梯形车刀进行车削,根据预定的工艺参数进行加工,如进给速度、车刀刀具角度等。
这种方法适用于小批量和单件生产,但加工效率较低。
2. 插刀车削法:插刀车削法是一种高效的梯形外螺纹加工方法。
该方法使用高速车刀进行插刀车削,具有较高的生产效率和加工精度。
插刀车削法适用于大批量生产,且要求加工精度较高的情况。
3. 加工中心车削法:加工中心车削法是一种在加工中心上进行梯形外螺纹加工的方法。
该方法使用加工中心的刀具库进行车削,可以实现多轴同时加工和自动换刀,大大提高了生产效率。
加工中心车削法适用于大批量生产和要求高精度的情况。
4. 车铣结合法:车铣结合法是一种综合利用车床和铣床进行梯形外螺纹加工的方法。
该方法先进行车削,然后通过铣床进行梯形外螺纹的修整和后续加工。
车铣结合法适用于单件和小批量生产,同时具有较高的加工精度和效率。
三、梯形外螺纹加工的工艺要点在梯形外螺纹的加工过程中,需要注意以下几个工艺要点:1. 选择合适的车刀和切削参数:根据加工材料和尺寸要求选择合适的车刀,并设置合理的切削参数,如切削速度、进给速度和切削深度等。
数控车工论文(梯形螺纹加工).
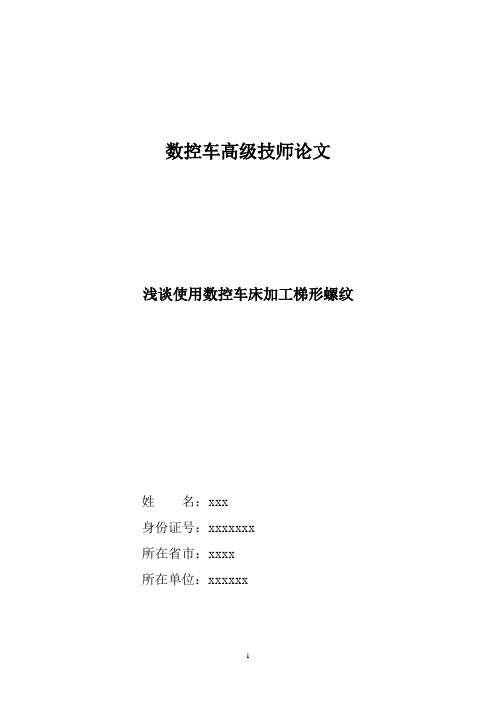
数控车高级技师论文浅谈使用数控车床加工梯形螺纹姓名:xxx身份证号:xxxxxxx所在省市:xxxx所在单位:xxxxxx摘要:在机床制造业中,梯形螺纹丝杠和螺母的应用较为广泛,它不仅用来传递一般的运动和动力,而且还要精确地传递位移,如车床的尾座、各种机床的进给机构、千斤顶、压力机等等。
梯形螺纹具有传动效率高、传动平稳可靠和加工方便等优点,且能够满足传动螺纹的使用要求。
梯形螺纹联接属间隙配合性质,在中径、大径、小径处都有一定的保证间隙,用以储存润滑油。
米制普通螺纹牙型是三角形,牙型角度为60度;米制梯形螺纹牙型为等腰梯形,角度为30度。
普通螺纹只是起到连接紧固作用,梯形螺纹主要用于传动和位置调整装置中。
关键词:梯形螺纹、配合、分析、加工1.梯形螺纹基本牙型梯形螺纹的特点是内、外螺纹仅中径公称尺寸相同,而小径和大径的公称尺寸不同,这与普通螺纹是不一样的。
梯形螺纹的牙型与基本尺寸按GB 5796.4—2005规定,基本尺寸的名称,代号及关系式见图1所示。
各直径基本尺寸系列可参阅相关国家标准。
直径和螺距见表6(梯形螺纹直径与螺距系列mm)所示。
表一图一公称直径:代表螺纹尺寸的直径。
大径:外螺纹的顶径、内螺纹的底径。
小径:外螺纹的底径、内螺纹的顶径。
中径:一个假想圆柱或圆锥的直径,该圆柱或圆锥的母线通过牙型上沟槽和凸起宽度相等的地方。
牙型角:在螺纹牙型上,两相邻牙侧间的夹角。
螺距:相邻两牙在中径线上对应两点间的轴向距离。
螺纹精度:由螺纹公差带和旋合长度共同组成的衡量螺纹质量的综合指标。
右旋螺纹:顺时针旋转时选入的螺纹。
左旋螺纹:逆时针旋转时选入的螺纹。
完整螺纹:牙顶和牙底具有完整形状的螺纹。
不完整螺纹:牙底完整而牙顶不完整的螺纹。
螺尾:向光滑表面过渡的牙底不完整的螺纹。
有效螺纹:由完整螺纹和不完整螺纹组成的螺纹,不包括螺尾。
单一中径:牙型上沟槽宽度等于1/2基本螺距的地方。
作用中径:在规定的旋合长度内,恰好包容实际螺纹的一个假想螺纹的中径,这个假想螺纹具有理想的螺距、螺纹半角、及牙型高度,并在牙顶和牙底留有间隙,不与实际螺纹大、小径发生干涉。
参数编程加工梯形螺纹浅析
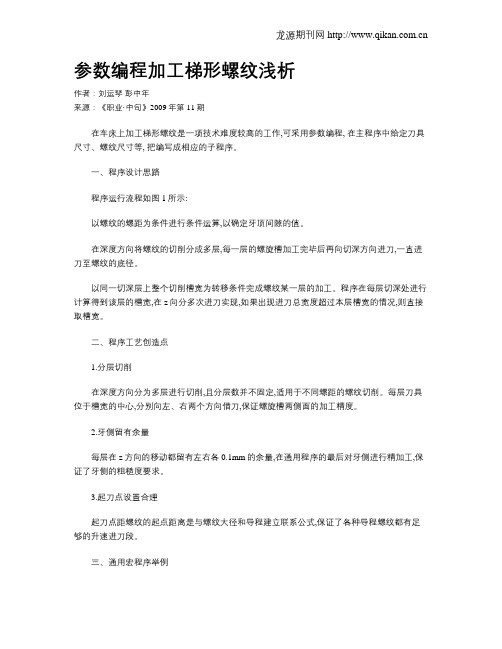
参数编程加工梯形螺纹浅析作者:刘运琴彭中年来源:《职业·中旬》2009年第11期在车床上加工梯形螺纹是一项技术难度较高的工作,可采用参数编程, 在主程序中给定刀具尺寸、螺纹尺寸等, 把编写成相应的子程序。
一、程序设计思路程序运行流程如图1所示:以螺纹的螺距为条件进行条件运算,以确定牙顶间隙的值。
在深度方向将螺纹的切削分成多层,每一层的螺旋槽加工完毕后再向切深方向进刀,一直进刀至螺纹的底径。
以同一切深层上整个切削槽宽为转移条件完成螺纹某一层的加工。
程序在每层切深处进行计算得到该层的槽宽,在z向分多次进刀实现,如果出现进刀总宽度超过本层槽宽的情况,则直接取槽宽。
二、程序工艺创造点1.分层切削在深度方向分为多层进行切削,且分层数并不固定,适用于不同螺距的螺纹切削。
每层刀具位于槽宽的中心,分别向左、右两个方向借刀,保证螺旋槽两侧面的加工精度。
2.牙侧留有余量每层在z方向的移动都留有左右各0.1mm的余量,在通用程序的最后对牙侧进行精加工,保证了牙侧的粗糙度要求。
3.起刀点设置合理起刀点距螺纹的起点距离是与螺纹大径和导程建立联系公式,保证了各种导程螺纹都有足够的升速进刀段。
三、通用宏程序举例下面用通用程序加工一个长度40mm,Tr36X6的梯形螺纹。
%2009T0101#2=0.5(牙顶间隙)#4=1(进刀次数)#5=1(每次下刀深度)#6=36(螺纹大径)#2=0.25endifif#8gt12#2=1#endif#11=0.366*#8-0.536*#2(牙底槽宽)#12=#6-#8-2*#2(螺纹小径)S400M03g00X[#6+2]Z[#8]while#7GE#12#3=0(借刀参数)#13=0(借刀参数)#10=[#8-0.366*#8]-tan[15*pi/180]*2*#4*#5(每层槽宽) G01X[#7]M98P1000while#3le[#10/2-#9/2](向左借刀)G00X[#7]w[-#3]M98P1000#3=#3+0.1ENDWWHILE#13LE[#10/2-#9/2] (向右借刀)G00X[#7]W[#13]M98P1000#13=#13+0.1ENDW在HNC-21/22T系统的数控车床上,利用本通用程序进行梯形螺纹的实际加工,取得了良好的效果。
浅谈梯形螺纹在数控车床上的加工
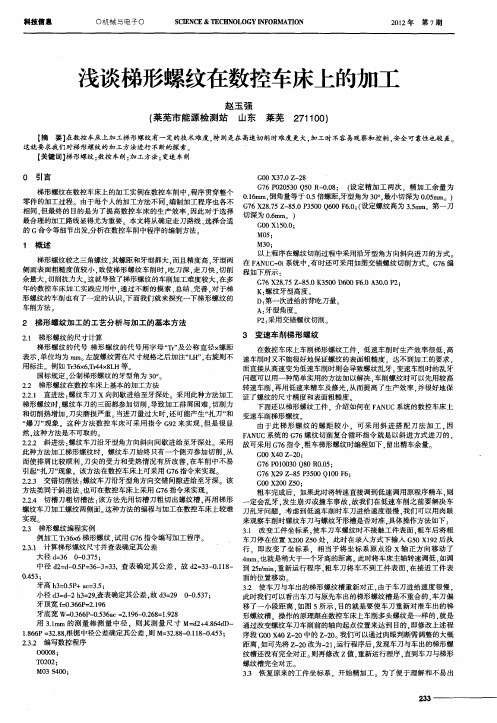
p: 2 采用交错螺 纹切 削。
3 变速车削梯形螺纹
在数控车床上车削梯形螺纹工件 .低速车削 时生产效 率很 低 . 高 速车削时又不能很好地保证螺纹的表面粗糙度 .达不到加 工的要 求 . 而直接从高速变为低速车削时则会 导致螺纹乱牙 。 变速车削时的乱牙 问题可 以用一种简单实用的方法加以解决 . 车削螺纹 时可以先用较高 转速车削 , 再用低速来精车及修光 , 从而提高 了生产效率 , 并很好地 保 证了螺纹的尺寸精度和表面粗糙度 下面还以梯形螺纹工件 .介绍如何在 F NU A C系统的数 控车床上 和切削热增加 . 刀尖磨损严重 。 当进刀量过大 时。 还可能产生 “ 扎刀 ” 和 变速车削梯形螺纹 “ 爆刀 ” 现象 这种方 法数控 车床可采 用指令 G 2 实现 . 9来 但是 很显 由 于此 梯形 螺 纹 的螺 距 较小 .可采 用斜 进 搭 配刀 法 加工 . 因 然 . 种方法是不可取 的。 这 F N C系统 的 G 6 A U 7 螺纹切 削复合循环 指令就是 以斜 进方式进 刀的 . 2 . 斜进法 : .2 2 螺纹车刀沿牙 型角方 向斜 向间歇进 给至牙深处 。采用 故可采用 G 6 7 指令 . 粗车梯形螺纹时编程如下 . 留出精车余量。 此种方法加工梯形螺纹时 .螺纹车刀始终只有一个侧 刃参 加切削 。 从 G0 0 Z- 0; 0 X4 2 而使 排屑 比较顺利 . 刀尖 的受力 和受热情况有 所改善 . 车削 中不易 在 G 6P 10 0Q 0R .5 7 0 0 3 8 00 ; 引起 “ 刀” 扎 现象 。该方法在数控 车床上可采用 G 6 7 指令来 实现 。 G 6X 9Z 8 30 O 6 7 2 - 5P 5 0QlOF ; 2 . 交错切削法 : .3 2 螺纹车刀沿牙型角方 向交错 间隙进 给至牙深 。该 G0 0 0; 0 X2 0 Z5 方法类 同于斜进法 . 也可在数控车床上采用 G 6 7 指令来 实现 。 粗车完成后 .如果此时将转速直接调到低速调用原程 序精 车 , 则 2 . 切槽 刀粗切槽法 : .4 2 该方法先 用切槽刀粗 切出螺纹槽 , 再用梯形 定会乱牙 . 发生崩刃或撞 车事故 . 我们在低速 车削之前要解 决车 故 螺纹车刀加工螺纹两侧面 。 这种方法 的编程与加工在数控车床上较难 刀乱牙问题 考虑到低速车削时车刀进给速度很慢 . 我们可 以用肉眼 实现 。 来观察车削时螺纹车刀与螺纹牙形槽是否对准 , 具体操作方法如下 : 2 梯形螺纹编程实例 - 3 3 改变工件 坐标 系 . . 1 使车刀车螺纹 时不接触 工件表面 . 车后将粗 粗 例加工 T3  ̄ 梯形螺 纹 , 用 G 6 r 6 6 试 7 指令编写加工程序。 车刀停在位置 X 0 5 处 .此 时在录入方式 下输入 G 0X 9 后 执 20 0 Z 5 12 2 . 计算梯形螺纹尺寸并查表确定其公差 .1 3 ’ 行 .即改变 了坐标 系 .相 当于将 坐标 系原 点沿 X轴 正方 向移动 了 大径 d 3 0 03 5 = 6 - .7 : 4 m 也就是稍大 于一个牙高 的距离 。 m 此时将车床主轴转速调低 , 如调 中径 d = 一 . = 6 3 3 . 表确 定其公 差 .故 d = 3 01 8 到 2 f i. 2 d0 P 3— =3 查 5 2 3— . — 1 5 m n 重新运行 程序 . 车刀将车 不到工件 表面 . 粗 在接近工 件表
浅析梯形螺纹的数控加工

浅析梯形螺纹的数控加工摘要 :主要介绍了利用左右切削法在数控车床上加工梯形螺纹的加工方法,梯形螺纹的加工是数控车削的一个难点,由于梯形螺纹加工工艺要求较高,在数控加工中往往会因为工艺不当而产生问题。
文章利用左右切削法解决了梯形螺纹在数控车床上加工编程困难的问题,在程序中巧妙地结合了普通车床车削梯形螺纹时应用的各种工艺技巧,采用左右进刀法车削、合理递减切削深度、螺纹切削粗精加工分段降低牙侧的粗糙度。
为数控车削梯形螺纹提供了一个实用合理的通用程序。
关键词:梯形螺纹工艺分析一、梯形螺纹零件图分析梯形螺纹常用于传动,精度要求较高。
在机床加工行业,三角形螺纹加工最为普遍,加工方法成熟易学。
梯形螺纹与三角形螺纹相比,螺距大、牙型高、切除余量大、切削抗力大,而且精度高,牙型角两侧表面粗糙度值较小,这就导致梯形螺纹加工时,吃刀深、走刀快,尤其是加工硬度较高的材料时,加工难度较大。
在数控车床上加工梯形螺纹,由于数控车床自动化程度高,加工过程由程序控制,这就要求车削梯形螺纹时,数控加工工艺设计要合理,程序编写要准确。
本文结合长期教学经历及生产实践,介绍用华中世纪星系统数控车床HNC-21/22T加工梯形螺纹的方法。
该零件是梯形螺纹轴,材料为中碳钢(45)。
零件最大外圆直径?64,总长80mm。
外圆及表面粗糙度为Ra1.6,零件的左端为Tr36单头螺纹,导程是6mm,螺纹两端倒角3x30°。
梯形螺纹根部退刀槽为?26x8,台阶圆柱直径?50,上偏差0,下偏差-0.1,台阶圆长12mm,台阶端面倒角1x45°。
零件右端直径?64,上偏差0,下偏差-0.1,长度20mm,上偏差0,下偏差-0.05,两端倒角0.5x45°。
根据要求分为两部分进行加工:(1)在该零件的加工中,为了便于装夹,选择先以毛坯材料左端定位,夹持毛坯外圆,用90°外圆车刀加工右端直径?64保证公差及粗糙度Ra1.6,倒角0.5x45°及右端面见光。
浅谈数控车床加工梯形螺纹
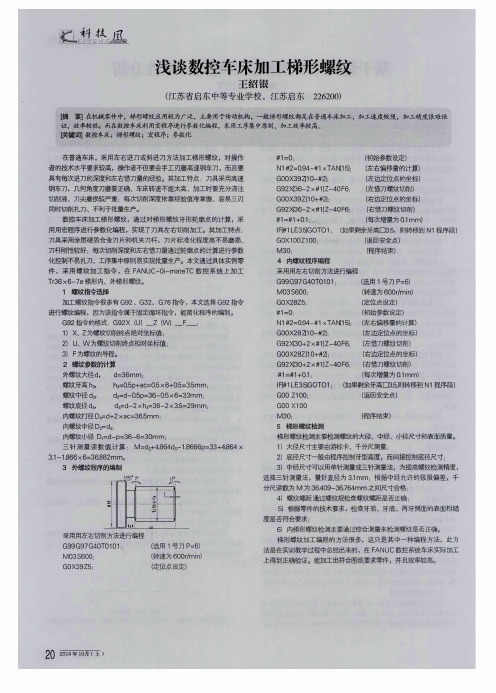
刀杆刚性较好 ;每次切削深度和左右借刀量通过轮廓点 的计算进行参数 化控制不易扎刀、工序集中原则 易实现批量生产。本 文通过具体实例零 件 ,采用 螺纹加 工指令 ,在 F A N U C 一 0 i — ma t e T C数控 系统 上加 工
_
_
浅谈数控车床加工梯形螺纹
王 绍银
( 江苏 省启 东 中等专 业学 校 ,江苏启 东 2 2 6 2 0 0 )
【 } 商 要】 在机械 零件 中, 梯形螺纹应 用较为 广泛,主要用于传动机构 , 一般梯形螺纹都是在普通 车床加 工,加工速 度 较慢 ,加工精 度很 难保 证 ,效率较低;而在数控车床利 用宏程序进行参教化编程 , 采用工序集 中 原则 , 加工效率较高。 薯 枣 词】 数控 车床 ; 梯形螺纹 ; 宏程序;参数化
GO O Z1 O O:
G O O×1 0 O
( 左边定位点 的坐标) ( 右边定位点的坐标) ( 右借刀螺纹切削)
( 每次增量为 Q 1 mm)
( 返 回安全点)
2 )U 、W 为螺纹切削终点相对坐标值:
3 )F 为螺纹的导程。 2 螺纹参数的计算 外螺纹大径d ,
Байду номын сангаас
( 左右偏移量的计算)
( 左边定位点的坐标 ) ( 左借刀螺纹切削) ( 右边定位点的坐标 ) ( 右借刀螺纹切削)
数控车床加工梯 形螺纹 ,通过对梯形螺纹牙形轮廓点的计 算,采 用用宏程序进行参数化编程 ,实现了刀具左右切削加工。其加工特点 :
刀具采用涂层硬质合金刀片和机夹刀杆 ,刀片标; 隹 化程度 高不易磨损、
B类宏程序加工梯形螺纹的方法和技巧

OCCUPATION2012 03166专业开发D evolopmentB类宏程序加工梯形螺纹的方法和技巧文/陈未峰一、B类宏程序在数控编程中的重要性在数控车削加工中,普通轴类零件的轮廓形状都可以利用G功能指令来完成加工。
但异形曲线和大螺距螺纹大大增加了零件的加工难度,G指令编程不好实现这类零件的有效加工。
例如梯形螺纹较之三角螺纹,螺距和牙型都大,而且精度高,牙型两侧表面粗糙度值较小,这样梯形螺纹车削时,吃刀深、走刀快、切削余量大、切削抗力大,导致梯形螺纹的车削加工难度较大。
与宏程序相比,一般程序的程序字为常量,一个程序只能描述一个几何形状,所以缺乏灵活性和适用性。
而用户宏程序本体中可以使用变量进行编程,还可以用宏指令对这些变量进行赋值、运算等处理,从而可以使用宏程序执行一些有规律变化的动作。
与A类宏程序相似,B类宏程序的变量也是由“#”符号和1至3位数字构成;但B类宏程序的数学运算可直接用数学符号完成,而不需采用G65语句,有效地提高了零件的编程灵活性和加工效率。
因此,使用B类宏程序加工有梯形螺纹的零件,对提高数控编程的效率是非常重要的。
二、球头梯形螺纹零件加工工艺分析1.球头梯形螺纹零件分析如图1所示,球头梯形螺纹轴由球面、曲面、退刀槽和梯形螺纹构成,其螺距为6mm,加工精度要求较高,球面和曲面加工简单。
在FANUC 0i数控系统机床上加工时,利用G73复合固定循环就可以进行有效加工,但由于梯形螺纹螺距较大和加工精度较高,致使梯形螺纹车削时,吃刀深、切削余量大、切削抗力大,车削加工难度较大。
利用普通G功能指令无法高质量、有效地完成该零件的加工,需利用B类宏程序进行切削加工。
2.计算相关尺寸,并查表确定公差该零件上梯形外螺纹为Tr36×6,螺距为6mm,公制梯形螺纹的牙型角为30°,梯形螺纹的牙型如图2所示,各基本尺寸计算结果如下:大径中径d 2=d -0.5P =36-3=33,查表确定其公差,故;牙高h 3=0.5P+ a c =3.5;小径d 3=d-2 h 3=29,查表确定其公差,故;牙顶宽f=0.366P=2.196;牙底宽W=0.366P-0.536a c =2.196-0.268=1.928螺纹中经三针测量法测量,如图3所示,用3.1mm的测量棒测量中径,则测量尺寸为M=d 2+4.864d D -1.866P=32.88,根据中径公差确定公差,则(其中d D 表示测量用量针的直径,P表示螺距)。
数控车床上梯形螺纹的加工
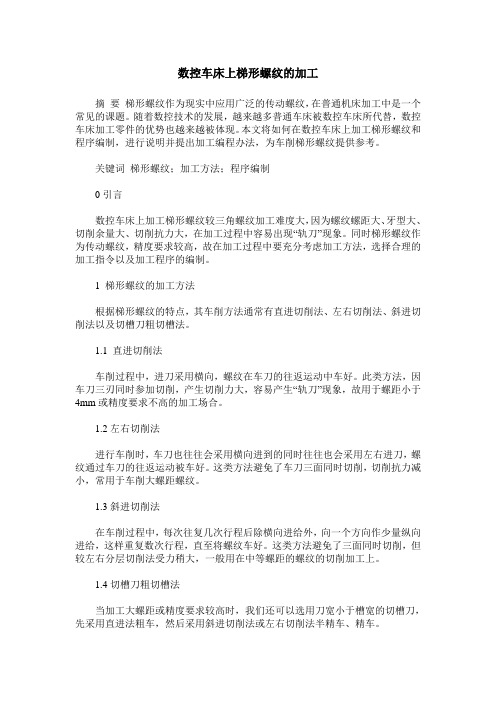
数控车床上梯形螺纹的加工摘要梯形螺纹作为现实中应用广泛的传动螺纹,在普通机床加工中是一个常见的课题。
随着数控技术的发展,越来越多普通车床被数控车床所代替,数控车床加工零件的优势也越来越被体现。
本文将如何在数控车床上加工梯形螺纹和程序编制,进行说明并提出加工编程办法,为车削梯形螺纹提供参考。
关键词梯形螺纹;加工方法;程序编制0引言数控车床上加工梯形螺纹较三角螺纹加工难度大,因为螺纹螺距大、牙型大、切削余量大、切削抗力大,在加工过程中容易出现“轨刀”现象。
同时梯形螺纹作为传动螺纹,精度要求较高,故在加工过程中要充分考虑加工方法,选择合理的加工指令以及加工程序的编制。
1 梯形螺纹的加工方法根据梯形螺纹的特点,其车削方法通常有直进切削法、左右切削法、斜进切削法以及切槽刀粗切槽法。
1.1 直进切削法车削过程中,进刀采用横向,螺纹在车刀的往返运动中车好。
此类方法,因车刀三刃同时参加切削,产生切削力大,容易产生“轨刀”现象,故用于螺距小于4mm或精度要求不高的加工场合。
1.2左右切削法进行车削时,车刀也往往会采用横向进到的同时往往也会采用左右进刀,螺纹通过车刀的往返运动被车好。
这类方法避免了车刀三面同时切削,切削抗力减小,常用于车削大螺距螺纹。
1.3斜进切削法在车削过程中,每次往复几次行程后除横向进给外,向一个方向作少量纵向进给,这样重复数次行程,直至将螺纹车好。
这类方法避免了三面同时切削,但较左右分层切削法受力稍大,一般用在中等螺距的螺纹的切削加工上。
1.4切槽刀粗切槽法当加工大螺距或精度要求较高时,我们还可以选用刀宽小于槽宽的切槽刀,先采用直进法粗车,然后采用斜进切削法或左右切削法半精车、精车。
2 数控车床上梯形螺纹实例以下图为例,在数控车床上加工梯形螺纹。
2.1 的编程指令3 结论在进行提醒螺纹车削时,需要考虑螺距大小、车刀以及机床情况的同时也应该考虑到应采用何种加工方法才最为合适,以便于编程的合理性。
梯形螺纹手工编程探讨
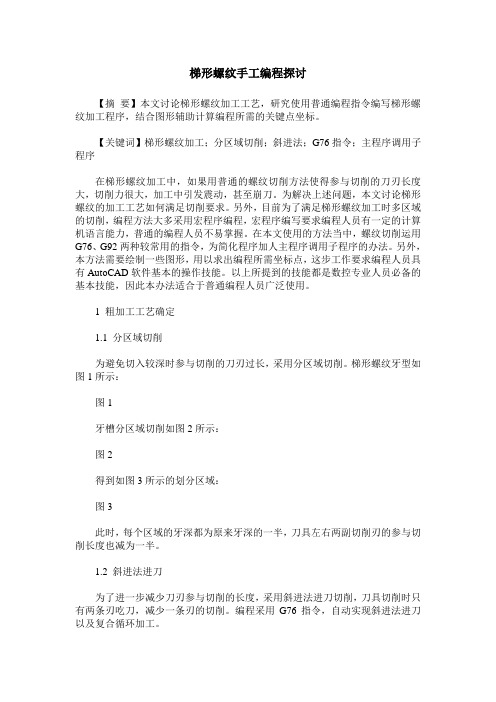
梯形螺纹手工编程探讨【摘要】本文讨论梯形螺纹加工工艺,研究使用普通编程指令编写梯形螺纹加工程序,结合图形辅助计算编程所需的关键点坐标。
【关键词】梯形螺纹加工;分区域切削;斜进法;G76指令;主程序调用子程序在梯形螺纹加工中,如果用普通的螺纹切削方法使得参与切削的刀刃长度大,切削力很大,加工中引发震动,甚至崩刀。
为解决上述问题,本文讨论梯形螺纹的加工工艺如何满足切削要求。
另外,目前为了满足梯形螺纹加工时多区域的切削,编程方法大多采用宏程序编程,宏程序编写要求编程人员有一定的计算机语言能力,普通的编程人员不易掌握。
在本文使用的方法当中,螺纹切削运用G76、G92两种较常用的指令,为简化程序加人主程序调用子程序的办法。
另外,本方法需要绘制一些图形,用以求出编程所需坐标点,这步工作要求编程人员具有AutoCAD软件基本的操作技能。
以上所提到的技能都是数控专业人员必备的基本技能,因此本办法适合于普通编程人员广泛使用。
1 粗加工工艺确定1.1 分区域切削为避免切入较深时参与切削的刀刃过长,采用分区域切削。
梯形螺纹牙型如图1所示:图1牙槽分区域切削如图2所示:图2得到如图3所示的划分区域:图3此时,每个区域的牙深都为原来牙深的一半,刀具左右两副切削刃的参与切削长度也减为一半。
1.2 斜进法进刀为了进一步减少刀刃参与切削的长度,采用斜进法进刀切削,刀具切削时只有两条刃吃刀,减少一条刃的切削。
编程采用G76指令,自动实现斜进法进刀以及复合循环加工。
2 粗加工关键点的图形制作初学G76指令者知道,如果对同一个螺纹多次使用G76指令,随便改动指令中的牙深参数的数值,或刀具起点不准确,切削中容易出现“乱牙”现象。
因此,我们在分区域切削时,每个区域的刀具起点位置要和区域在牙槽中的位置相对应,方法如下:首先根据梯形螺纹的几何参数绘制出牙槽,如图4。
然后,根据图5方法画出刀尖点在每个区域的终点位置1′~5′。
图4(a)刀尖点的画法(b)按图4所求刀尖点所划分的区域图5接着,根据进刀的角度,反求出刀尖在切削起点的位置1~5,如图6。
梯形螺纹零件的编程加工及工艺
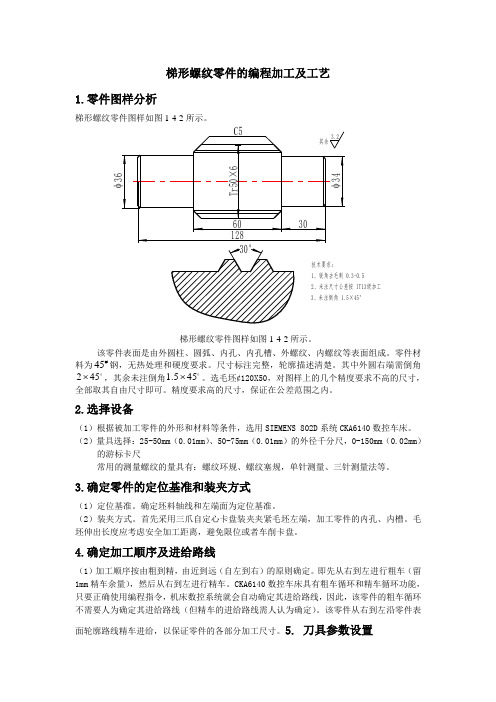
梯形螺纹零件的编程加工及工艺1.零件图样分析梯形螺纹零件图样如图1-4-2所示。
梯形螺纹零件图样如图1-4-2所示。
该零件表面是由外圆柱、圆弧、内孔、内孔槽、外螺纹、内螺纹等表面组成。
零件材45钢,无热处理和硬度要求。
尺寸标注完整,轮廓描述清楚。
其中外圆右端需倒角料为#2⨯,其余未注倒角455.1⨯。
选毛坯¢120X50,对图样上的几个精度要求不高的尺寸,45全部取其自由尺寸即可。
精度要求高的尺寸,保证在公差范围之内。
2.选择设备(1)根据被加工零件的外形和材料等条件,选用SIEMENS 802D系统CKA6140数控车床。
(2)量具选择:25-50mm(0.01mm)、50-75mm(0.01mm)的外径千分尺,0-150mm(0.02mm)的游标卡尺常用的测量螺纹的量具有:螺纹环规、螺纹塞规,单针测量、三针测量法等。
3.确定零件的定位基准和装夹方式(1)定位基准。
确定坯料轴线和左端面为定位基准。
(2)装夹方式。
首先采用三爪自定心卡盘装夹夹紧毛坯左端,加工零件的内孔、内槽。
毛坯伸出长度应考虑安全加工距离,避免限位或者车削卡盘。
4.确定加工顺序及进给路线(1)加工顺序按由粗到精,由近到远(自左到右)的原则确定。
即先从右到左进行粗车(留1mm精车余量),然后从右到左进行精车。
CKA6140数控车床具有粗车循环和精车循环功能,只要正确使用编程指令,机床数控系统就会自动确定其进给路线,因此,该零件的粗车循环不需要人为确定其进给路线(但精车的进给路线需人认为确定)。
该零件从右到左沿零件表面轮廓路线精车进给,以保证零件的各部分加工尺寸。
5. 刀具参数设置表 1.4.2数控刀具卡片6. 加工操作流程(1)开机、返回参考点。
(2)检查毛坯尺寸(3)装夹刀具、工件并找正工件、夹紧。
外圆粗车刀安装在1号刀位,外圆精车刀安装在2号刀位,外螺纹T形刀安装在3号位。
(4)建立工件坐标系:根据编程原点的确定原则,外圆刀和内孔车刀工件坐标系建立在该零件编程工件坐标系原点确定在零件端面与轴线的交点上。
浅谈梯形螺纹

浅谈梯形螺纹姓名:朱杰班级:074101学号: 31指导老师:张云阁单位:江苏省盐城技师学院邮编:224002 2010-03-10浅谈梯形螺纹摘要:在数控车床上加工梯形螺纹是一个比较难的课题,高速车削时不能很好地保证螺纹的表面粗糙度,达不到加工的要求,低速车削时生产效率又很低,而直接从高速变为低速车削时则会导致螺纹乱牙,然而掌握好方法加上多练习,多积累经验, 变速精加工也不在是难题。
关键词:梯形螺纹宏程序变速精加工测量扎刀一、梯形螺纹的标注及尺寸计算1.梯形螺纹的标注:例Tr42×6-7e,梯形螺纹的代号Tr,及公称直径×螺距-螺纹公差来表示,单位均为mm。
左旋螺纹需在尺寸规格之后加注“LH”,右旋则不用标注。
如Tr44×8LH表示公称直径为44的梯形左旋螺纹螺距为8mm。
国标规定,公制梯形螺纹的牙型角为30°如图1所示。
英M制梯形螺纹的牙型角为29°。
图1 梯形螺纹牙型和基本尺寸表 1 梯形螺纹的各部分名称代号及计算公式二、利用宏程序加工梯形螺纹在数控车床上加工梯形螺纹的程序有很多种:1.通过G32 调用子程序交错切削加工G32螺纹单一循环加工,通常加工小螺距的螺纹。
2.螺纹复合循环G76指令G76:螺纹复合循环格式:G76 P(m)(r)(a)Q(Δd m i n)R(d)G76 X(U)Z(W)R(i)P(k)Q(Δd)F(l)3 .利用宏程序加工编写车削梯形螺纹宏程序,图2所示:图2梯形螺纹加工实例宏程序加工梯形螺纹:相对来讲,运用宏程序加工梯形螺纹很方便。
宏程序基本上包含了所有加工信息,而且非常简明直观通过简单存储和调用,就可以很方便的呈现当时加工状态,给周期性的生产特别是不定期的间隔生产带来了极大便利。
4.变速精加工粗车完成后,如果此时将转速直接调到低速调用原程序精车,则一定会乱牙,发生崩刃或撞车事故,故我们在低速车削之前要解决梯形螺纹乱牙问题.经过反复的加工练习,在数控车床上变速车削梯形螺纹的方法是切实可行的,且取得了很好的加工效果。
- 1、下载文档前请自行甄别文档内容的完整性,平台不提供额外的编辑、内容补充、找答案等附加服务。
- 2、"仅部分预览"的文档,不可在线预览部分如存在完整性等问题,可反馈申请退款(可完整预览的文档不适用该条件!)。
- 3、如文档侵犯您的权益,请联系客服反馈,我们会尽快为您处理(人工客服工作时间:9:00-18:30)。
浅谈梯形螺纹的编程与加工摘要:梯形螺纹在数控车床上加工除了对操作要求严格以外,还要有一个合理准确的数控加工程序来保证加工过程有序而顺利的完成。
通过对梯形螺纹进行数控车削,采用分层切削的加工的方式有效的避免了梯形螺纹在切削过程中出现的“崩刀”和“扎刀”现象,同时利用宏程序程序简化编程。
关键词:宏程序车削梯形螺纹引言梯形螺纹较之三角螺纹,其螺距和牙型都大,而且精度高,牙型两侧面表面粗糙度值较小,致使梯形螺纹车削时,吃刀深、走刀快、切削余量大、切削抗力大,这就导致了梯形螺纹的车削加工难度较大。
1、梯形螺纹的车削工艺分析在加工梯形螺纹的加工有很多种:直进法、斜进法、左右切削法、车直槽法、分层法等等。
由于梯形螺纹较之三角螺纹,其螺距和牙型都大,而且精度高,牙型两侧面表面粗糙度值较小,致使梯形螺纹车削时,吃刀深,走刀快,切削余量大,切削抗力大。
再加工许多学校的数控车床刚性较差,这就导致了梯形螺纹的车削加工难度较大,在数控车工技能培训中难于掌握,容易产生“扎刀”和“扎刀”现象,进而对此产生紧张和害怕的心理。
在三年的数车工实习学习中,通过不断的学习、理论、总结,对于梯形螺纹的车削也有了一定的认知,自我认为利用宏程序进行分层切削,可以很好地解决出现的问题。
“分层法”车削梯形螺纹实际上是直进法和左右切削法的结合应用。
在车削较大螺距的梯形螺纹时,“分层法”通常不是一次性就把梯形槽切削出来,而是把牙槽分成若干层,每层深度根据实际情况而定。
转化成若干个较浅的梯形槽来进行切削,可以降低车削难度。
每一层的切削都采用左右交替车削的方法,背吃刀量很小,刀具只需沿左右牙型线切削,梯形螺纹车刀始终只有一个侧刃参加切削,从而使排屑比较顺利,刀尖的受力和受热情况有所改善,因此能加工出较高质量的梯形螺纹,容易掌握,程序简短,容易操作。
2、数控车削梯形螺纹方法的选用根据上述分析,数控车床车削梯形螺纹采用“分层法“比较合适。
分层法”车削梯形螺纹实际上是直进法和左右切削法的结应用。
在车削梯形螺纹时,“分层法”通常不是一次性就把梯形槽切削出来,而是把牙槽分成若干层(每层深度根据具体情况设定),转化成若干个较浅的梯形槽来进行切削,从而降低了车削难度。
每一层的切削都采用先直进后左右的车削方法,由于左右切削时槽深不变,刀具只须做向左或向右的纵向进给即可(如图1所示),因此它比上面提到的左右切削法的运动轨迹要简单得多。
第三刀右移刀切削第二刀左移刀切削第一刀直进刀切削图1 分层法车削梯形螺纹图3、宏程序编程车削梯形螺纹以加工一个下图所示的梯形螺纹(如图2所示)为例介绍用宏程序编写加工程序(采用FANUC 0i Mate TC 系统) 28010φ68T r 80X 10图2梯形螺纹零件图(1)数值计算①梯形螺纹加工尺寸计算表1 梯形螺纹的计算式及其参数值名称代号 计算公式及参数值(mm ) 牙顶间隙ac 0.5 大径d 公称直径Φ80 中径d2 d2=d-0.5P=75 小径d1 d3=d-2h=69 牙高h h=0.5P+ac=5.5 牙顶宽 f f=0.366P=3.66江苏工贸技师学院08数控技师牙槽底宽 w w=0.366P-0.536ac=3.392②左(右)移刀量的计算左(右)移刀量当前层背吃刀量如上图可以得出分层切削时左(右)移刀量计算式为1、当刀头宽度等于牙槽底宽时,左(右)移刀量=tan15°×(牙深—当前层背吃刀量);2、当刀头宽度小于于牙槽底宽时,左(右)移刀量=tan15°×(牙深—当前层背吃刀量)+(牙槽底宽—刀头宽度)/2(2)“分层法”车削梯形螺纹的刀具选择“分层法”车削梯形螺纹所用的粗车刀和精车刀与其它加工方法基本相同,只是粗车刀的刀头宽度小于牙槽底宽,刀具刀尖角略小于梯形螺纹牙型角。
(3)参考程序①编程分析用宏程序编程时变量的设置是核心内容,一是要变量尽可能少,避免影响数控系统计算速度,二是便于构成循环。
经过分析上图中有4个变量,#1为刀头到牙槽底的距离,初始值为5.5mm ,#2为背吃刀量(半径值),#3为(牙槽底宽—刀头宽度)/2,#4为每次切削螺纹终点X 坐标。
上图中编程关键技术是要利用宏程序实现分层切削和左右移刀切削。
利用G92螺纹加工循环指令功能,左右移刀切削只需将切削的起点相应移动0.268*[#1-#2]+#3(右移刀切削)或者-0.268*[#1-#2]-#3(左移刀切削)就可以实现。
分层切削的实现通过#1和#2变量实现,每层加工三刀后,用#1=#1-#2实现进刀,而在每层中螺纹的X 坐标不变,始终为#4=69.0+2*[#1-#2]。
②参考程序参考程序注 释 O0001;程序号 N10 T0101;换01号刀具,调用01号偏置值 N20 M08;打开切削液N30 M03 S180;主轴正转,转速为180r/minN40 G00 X90.0 Z10.0;刀具快速移动到点(90,10)N50 #1=5.5;#1为刀头到牙槽底的距离,初始值为5.5mmN60 #2=0.2;#2为背吃刀量(半径值)#3为(牙槽底宽—刀头宽度)/2N70 #3=(牙槽底宽—刀头宽度)/2;N80 WHILE [#1 GE 0.2] DO1;当#1≥0.2,执行循环1,底部留0.2mm的精车余量N90 #4=69.0+2*[#1-#2];#4为每次切削螺纹终点X坐标N100 G00 Z5.0 ;移动到直进刀切削的循环起点N110 G92 X#4 Z-286.0 F10.0;直进刀车削螺纹移动到右移刀切削的循环起点N120 G00Z[5+0.268*[#1-#2]+#3];N130 G92 X#4 Z-286.0 F10.0;右移刀车削螺纹N140 G00移动到左移刀切削的循环起点Z[5-0.268*[#1-#2]-#3];N150 G92 X#4 Z-286.0 F10.0;左移刀车削螺纹N160 #1=#1-#2;构成循环N170 END1;当#1<0.2,跳出循环1N180 G00 X200.0 Z150.0;快速退刀N190 M09;关闭切削液N200 M30;程序结束说明:①参考程序以工件右端面中心为编程原点。
②若螺纹的表面粗糙度要求不高,用一把粗车刀加工即可,执行完程序后进行测量,根据测量结果判断是否需要调整牙槽底宽的余量。
若中径尺寸未到,可以适当调整#3的数值,直至合格为止。
背吃刀量可以根据工件材料、刀具选择,只需修改#2的数值即可。
③若螺纹的表面粗糙度要求较高,先用粗车刀粗车,除底部留有余量外,侧面余量在#3变量上调节,要留余量则在#3=(牙槽底宽—刀头宽度)/2基础上减去所留余量,如0.3的侧面余量,则#3=(牙槽底宽—刀头宽度)/2-0.3;再用精车刀精车,依然使用该程序,只修改刀具指令和#3。
4、应用宏指令将梯形螺纹加工程序模块化用宏程序指令将左右移刀法加工梯形螺纹模块化,应用时将宏程序指令中的自变量赋值修改一下加工不同尺寸的梯形螺纹而宏程序中的内容不需修改。
通过上述程序和分析,梯形螺纹加工需要的自变量有:#1=(A)每一刀的进刀深度(半径值),(上图中初始值为牙高5.5mm);#2=(B)背吃刀量;(上图中为0.2mm)#3=(C)刀头宽度偏差=(牙槽底宽—刀头宽度)/2;#4=(I)螺纹小径;#5=(J)螺距;#6=(K)螺纹长度;(1)主程序O0002;程序号N10 T0101;选择刀具并调用刀具偏置值N20 M08;打开切削液N30 M03 S200 主轴正转,转速为200r/minN40 G65 P1000 A_ B_ C_ I_ J_ K_;宏指令调用程序O1000,并给变量赋值N50 G00 Z150.0;刀具快速沿Z轴退刀N60 G00 X200.0;刀具快速沿X轴退刀N70 M09;关闭切削液N80 M30;程序结束(2)宏程序O1000;程序号N10 #7=#4+2*[#1];计算出螺纹公称直径N20 G00 X[#7+5.0] Z15.0;刀具快速移动到工件外一点,准备加工螺纹N30 WHILE [#7 GT #4] DO1;当#7>#4时,执行循环1N40 #1=#1-#2;刀具每次进刀0.2mm,构成循环N50 #7=#4+2*[#1];计算出每一刀螺纹终点X坐标N60 G00 Z10.0;移动到直进刀切削的循环起点N70 G92 X#7 Z-[#6+2.0] F#5;直进刀车削螺纹移动到右移刀切削的循环起点N80 G00Z[10.0+0.268*[#1]+#3];N90 G92 X#7 Z-[#6+2.0] F#5;右移刀车削螺纹移动到左移刀切削的循环起点N100 G00Z[10.0-0.268*[#1]-#3];N110 G92 X#7 Z-[#6+2.0] F#5;左移刀车削螺纹N120 END1;当#7<#4时,跳出循环外N130 M99;子程序结束并返回主程序注意事项:(1)、在刃磨梯形螺纹刀时,为了能左右切削并保留精加工余量,刀头宽度应小于牙槽底宽,刀尖角应略小于牙型角、牙型半角应准确。
(2)、车削钢料时,应磨有6°---8°的径向后角和10°----15°的径向前角。
(3)、两侧的直线度要好,表面粗糙度值小,刀尖适当倒圆。
(4)、两侧后角,车右旋螺纹时,AfL=(3°--5°)+Φ、AfR=(3°--5°)-Φ。
(5)、车削时先用刀头宽度略小于牙槽底宽的车槽刀,用车直槽的方法车置接近中径处,在粗车两侧面。
5、结束语我们在FANUCOI系统的数控车床上,利用上述的程序进行了多次梯形螺纹的实际加工,取得了良好的效果。
上述程序应用基本上考虑全面,加工时只需要快速的将变量表中各项变量的值赋入程序便可以加工。
程序适应性广,工艺编制还算合理加工质量基本上还算不错,基本上可以解决梯形螺纹编程加工的诸多问题,可以直接将上述的程序编为子程序使用。
参考文献:1、王洪主编,数控加工程序编制,北京:机械工业出版社,20022、刘雄伟等编著,数控加工理论与编程技术,北京:机械工业出版社,20003、刘唐谦主编,数控加工工艺学,北京:中国劳动社会保障出版社,20004、任国兴主编,数控车床加工工艺与编程操作,北京:机械工业出版社,20025、王公安主编,车工工艺学[M].第一版,北京:中国劳动保障出版社,20056、关亮,张向京.数控车床操作与编程技能训练.高等教育出版社,2005(封面的身份证号?字体格式排版好,图形要弄弄显示出来)。