TFPX旋转分配器说明书
分配器 说明书
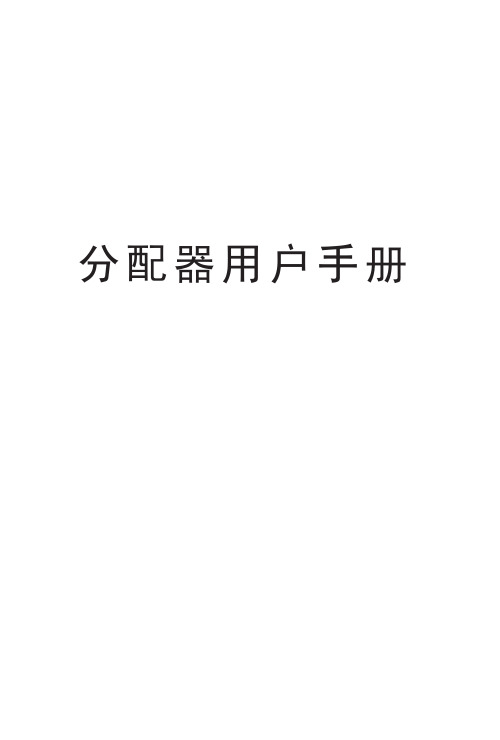
分配器用户手册目 录1、分配器-AV (1)1.1 AV-103分配器 (1)1.2 AV-108分配器 (1)2、分配器-DVI (2)2.1 DVI-1*2分配器 (2)2.2 DVI-1*4分配器 (3)3、分配器-V (4)3.1 Video-104分配器 (4)3.2 Video-1*16分配器 (4)4、分配器-VGA (5)4.1 VGA-0102分配器 (5)4.2 VGA-104分配器 (6)4.3 VGA-1*8分配器 (7)4.4 VGA0116分配器 (8)4.5 VGA-1*10/24分配器 (9)1 分配器-AV1.1 AV-103分配器AV-1*3分配器主要用以解决在多媒体投影工程中,将一路高分辨率音视频信号分配成三路高分辨率音视频信号。
AV-103后背板技术性能及指标:输入接口: 1路 BNC(VIDEO),1路RCA输出接口: OUTPUT1―3BNC; OUTPUT2―3 RCA阻 抗: 输入阻抗:75Ω输出阻抗:75Ω电 源: 220V /AC外形尺寸: 45×25×15mm(D×W×H)重 量: 0.3Kg配 件: 使用说明书1.2 AV-108分配器AV-1*8分配器主要用以解决在多媒体投影工程中,将一路高分辨率音视频信号分配成八路高分辨率音视频信号。
AV-108后背板技术性能及指标 :输入接口: 视频: 1路 BNC(VIDEO),音频:1路音频头(凤凰端子)输出接口: 视频:OUTPUT1―8BNC;音频:OUTPUT1―8 音频头(凤凰端子)阻 抗: 输入阻抗:75Ω输出阻抗: 75Ω电 源: 220V 50HZ的交流电源外形尺寸: 235×155×70mm(D×W×H)重 量: 1.3Kg配 件: 使用说明书2 分配器-DVI2.1 DVI-1*2分配器在许多多媒体应用系统中,往往需要把一个DVI信号源输送到中心机房进行处理,同时又需要在本地显示该信号。
Burkert 2051QT气动旋转执行器说明书

Pneumatic rotary actuatorDouble acting and spring return The 2051QT pneumatic rotary actuators are ofthe rack and pinion type where the linear kineticenergy is directly transformed into a “quarter turn” operation with a constant output torque over the full stroke.Both double acting and spring return actuators have twin pistons horizontally opposed and incorporate piston guides to ensure correct contact between the rack and pinion at all pressures.High quality materials are employed throughout the construction and the compact design is readily fitted to any type of ball valve, butterfly valve or other equipment requiring efficient pneumatic actuators.The actuator is suitable for mounting a full range of accessories, such as limit switches, solenoid valves, positioners and manual override gearbox.Extruded aluminium alloy, gold anodizedPressure die cast aluminium alloy, black epoxy coated Carbon steel, zinc platedType 6519NAMUR Solenoid valve Type 8792/93 Positioner SideControlType MV2650Ball valve Type 1062QTPosition feedbackType VV2670Butterfly valveFunctional principleDouble acting actuator (DA)Counter clockwise output operation is achieved by inserting pressure into Port ‘A’, to force piston apart thus rotating the actuator pinion counter clockwise. During the operation, air from the outer chambers is exhausted through Port ‘B’. Clockwise output operation is achieved by reverse of the above and inserting pressure into Port ‘B’.Single acting actuator (SR)Pressure applied to Port ‘A’ will cause the inner chambers to be pressurized, forcing the pistons outward to compress the springs. The pinion is rotated counter clockwise. Upon release of pressure through Port ‘A’ the springs will exert pressure to close the pistons and rotate the pinion clockwise rapidly. This action will often be used to close a 90oturn valve in shutdown mode.Pistons assembly variationsArrangement of springs for single acting actuatorActuator direction of rotation can be changed by switching both the pistons in accordance to the below diagramSprings can be added or removed according to torque requirement. It is recommended to install springs in accordance to the below diagramAir ConsumptionFree Air per stroke (Liters)Opening / Closing timeat 5.6 bar airWeight (kg)Torque Output (Nm) | Ordering Chart (other versions on request) Double acting actuator (DA)Torque Output (Nm) | Ordering Chart (other versions on request) Single acting actuator (SR)Dimensions [mm]AP01 to AP10 DA/ SR*** To be specified during order. Please refer to Ordering Chart.Parts listAP01 to AP10 DA/ SR* Suggested spare parts for routine maintenanceDimensions [mm]AP00 DAParts listAP00 DA* Suggested spare parts for routinemaintenanceDimensions [mm] - with accessoriesIn case of special application conditions,please consult for advice.We reserve the right to make technical changes without notice2051QT/EN/R1_12/2013With Type 6519 NAMUR solenoid valveWith declutchable manual override gearboxWith 879x positioner SideControlWith 1062QT position feedback。
最新分配器说明书上海金灿12资料

随机资料,使用前请务必仔细阅读!分配器/延长器/线控说明书精品文档目录前言 (2)一、分配器的使用说明 (3)1、分配器功能 (3)2、分配器分类 (3)3、装箱清单 (4)4、系统连接图 (6)5、输入、输出接口 (4)6、技术指标 (5)二、延长器的使用说明 (7)1、信号延长器简介 (7)2、信号延长器指标及连接图 (7)三、线控的使用说明 (16)1、线控简介 (16)2、线控接口 (16)3、技术指标 (17)4、连接图 (18)常见故障及维护 (19)精品文档前言感谢您使用本公司产品,使用时请注意以下事项:1.本产品所使用电源必须有电源保护地线,输入、输出设备的电源保护地线要为同一保护地线。
确保设备的输入电源为AC 100~240V/50Hz。
2.使用计算机控制本产品时必须保证控制计算机与本产品的连接电源保护地线是同一个地线。
3.使用本产品时严禁带电插拔输入、输出信号线及RS232通讯接口线。
4.严禁将本产品放在过热或过冷的地方工作,应保持工作环境通风良好。
严禁将化学物品洒在本产品上。
5.严禁对本产品的机械和电路设计进行更改或增减任何部件,否则厂家对此产生的任何结果不负责任。
6.严禁擅自打开机箱外壳,机器内有交流220V高压,以免发生触电危险,需要维修时应交厂家进行维修。
精品文档一、分配器的使用说明1、分配器功能分配器的功能是将一路输入信号源均等的分成多路输出,并且输出信号与输入信号完全相同、有些型号甚至还带有图像增益放大输出功能;输出信号与输入信号相比不会有衰减、延迟等不良的现象。
2、分配器分类根据输入信号的不同,有:纯视频分配器视音频分配器VGA分配器VGA+音频分配器RGB分配器网线分配器DVI分配器HDMI分配器等根据分配的端口数而分,有:0102 1进2出0104 1进4出0108 1进8出精品文档精品文档0116 1进16出 0132 1进32出 0164 1进64出等3、装箱清单4、输入、输出接口VGA: D-Sub15Pin (对含有VGA 的分配器)。
旋转分配器说明书

注入润滑油脂应适量。
蜗轮减速器运转前应加注润滑油至油表线以上,首次运转32小时,应更换润滑油,以后按减速器的使用说明书定期更换润滑油。
经常检查各易损件和机器零部件,有损坏或严重磨损时应及时修理或更换,其中易损件包括:端刷、内衬、滚轮系统。
常见故障
故障原因
排除方法
来函请寄“上海正诚机电制造有限公司(工程销售部)收”谢谢!
地址:上海市松江区茸北工业区茸兴路3-5号
ADDRESS:NO.3-5RONGXING RD.RONGBEI INDUSTRIAL ZONE SONGJIANG SHANGHAI
电话(TEL):021-;021- 传真(FAX):021-
邮编(ZIP):
电机启动
困难
1.电压过低
1.待电压正常后启动
2.断相
2.检查线路并正确联接
链条卡齿
运转不平稳
1.链轮齿部过厚
或无光滑过渡
1.将齿部倒角
2.链条过松
2.调整底座,收紧链条
物料流
量降低
1.落料管口与壳体
落料锥管口不在
同一平面内
1.调整调节块位置,使两者位于
同一水平面内
2.落料管口与壳体
落料锥管口虽在
同一平面内但不同轴
55°
0.76
Φ2200X2104
TFPX16(B)30
55°
0.76
TFPX18(B)30
55°
0.76
四操作注意事项
由于分配器属低速运转机器在,操作时掌握以下即可:
熟悉了解本机性能,结构及各个部件的作用和调整方法,检查各密封部位,拧紧各螺栓,确保密封无间隙,开机前检查所有螺栓紧固可靠,清理装配过程中残留在机内杂物。
阿尔法拉瓦尔CDNX系列旋转分心机产品介绍说明书

IntroductionFor drill slurry treatment, high-speed separation, barite recovery, system de-weighting and removal of ultrafine particles.ApplicationAlfa Laval decanter centrifuges are a key component in a top-quality drill slurry treatment process. This technology efficiently removes most of the fine particles that traditional slurry treatment equipment cannot deal with.Specially designed and built for heavy-duty jobs in this field, the Alfa Laval CDNX range of decanter centrifuges is able to handle large amounts of feed solids, as well as coping well with abrasive and coarse particles.CDNX decanter centrifuges are available with a range of modules ideally suited for every kind of solids separation job in conjunction with the drill slurries used on HDD drilling rigs, exploration rigs and Tunnel Boring Machines. These modules range from fully automated operation to simple “hands-on”capabilities, providing effective solutions to all your slurry treatment and separation issues.Operating principleSeparation takes place in a horizontal cylindrical bowl equipped with a screw conveyor. The feed enters the bowl through a stationary inlet tube and is accelerated smoothly by an inlet rotor. Centrifugal forces cause sedimentation of the solids on the wall of the bowl. The conveyor rotates in the same direction as the bowl, but at a different speed, thus moving the solids towards the conical end of the bowl.The CDNX design enables the decanter to scroll out high loads of solids without blockages caused by high levels of dryness. Only the very driest fraction of the sludge cake leaves the bowl through the solids discharge openings into the casing. Separation takes place along the total length of the cylindrical part of the bowl, and the clarified liquid leaves the bowl by flowing over adjustable plate dams into the casing.The CDNX decanter centrifuge can be adjusted to suit specific requirements by varying the bowl speed, the conveying speed, the pond depth and the feed rate.Process optimization•the bowl speed to ensure the exact G force required forthe most efficient separation,•the conveying speed for the best possible balancebetween liquid clarity and solids dryness.•the pond depth in the bowl for the best possible balance between liquid clarity and solids dryness.•the feed rate – the CDNX is designed to handle a widerange of flow rates.1: Gearbox2: Liquid outlet3: Screw conveyor4: Wall of the bowl5: Inlet distributor6: Conical end7: Cleaned slurry/muck outlet8: Feed inlet9: Discharge ports10: Feed tubeBenefits•Take advantage of CDNX solids separation technology•Maximum solids recovery•high G Force•newest design technologies•specially designed decanter geometry for larger processvolumes Achieve lower cut-point and optimize your solidsslurry treatment and drilling process. Improve fine removaland obtain better fluid clarity. Reduce mud costs.•Outstanding improved wear protection•patented feed zone design for optimal flow distribution•fully covered replaceable parts in tungsten carbide•improved solids outlet protection Increase the lifetime ofwear parts and reduce your maintenance cycles.•Drier solids•optimized conveyor and bowl geometries for increasedcompaction capabilities. Reduce your waste volumes.Reduce your disposal costs.•easy to troubleshoot and service, ensuring maximumcentrifuge uptime•compatible with multiple industry standards andcommunication protocols•consistent and has easy-to-use interfaces Improve youroperating reliability and optimize your processes. Savemanpower and training costs.•Unmatched flow rate capacity/diameter•new generation of decanter centrifuges. Latest optimizeddesigns•360-degree solids outlet. Treat larger process volumes insmaller machines and reduce your total costs per volumetreated.•Easier accessibility•Lighter and smarter cover design•Quick adjustable pond depth. Access easily the interior ofthe decanter. Optimize, service and clean faster, savingtime and money.Figure 2. CDNX 300, 400, 500, 700 Example of upgraded Conveyor wear protectionFigure 3. CDNX 100, 200 Standard ConveyorDirect driveThe drive system that is an integral part of the CDNX design was specially developed by Alfa Laval to make it possible to control the conveying speed automatically. This ensures the best possible balance between liquid clarity and solidsdryness, irrespective of any variations that may occur in the feed flow.The Direct Drive system comprises an exceptionally efficient gearbox and variable frequency drive, which together avoid exposing the bowl drive to parasitic braking power. It also simplifies the electrical installation and keeps powerconsumption and CO2 emissions to the absolute minimum. In addition, the Direct Drive is capable of accurate control within the complete range of differentials, with no need for changing belts or pulleys.Optional extras•New generation of wear protection for use with extra-harsh and abrasive feeds•A range of different power pack designs to optimise power consumption AutomationEach CDNX decanter centrifuge can be equipped with an Alfa Laval Automation control package as standard – pre-installed and factory-testedThe combination of Automation control systems and CDNX separation technology ensures that you get the most out of any CDNX installation, at the same time as keeping costs for installation, commissioning, operation and maintenance to aminimum.Figure 1. Alfa Laval spade able cakeDesignation CDNX 100CDNX 100 CS ***CDNX 200CDNX 200 CS***Bowl diameter200 mm / 8 inches200 mm / 8 inches280 mm / 11 inches280 mm / 11 inchesBowl speed (maximum)5300 rpm5300 rpm4400 rpm4400 rpmG-force (maximum)3140 G3140 G3030 G3030 GGross weight650 kg / 1433 lbs625 kg / 1378 lbs1200 kg / 2645 lbs1070 kg / 264 lbsLength (L)2150mm / 85 in1725 mm / 68 in3013 mm / 119 inches3013 mm / 119 inchesWidth (W)580 mm / 23 in580 mm / 23 in780 mm / 31 inches780 mm / 31 inchesHeight (H)762 mm / 30 in762 mm / 30 in1042 mm / 41 inches1042 mm / 41 inchesTotal installed power7 – 14 kW / 9 – 19 Hp4-11 kW / 5-15 hp18.5-26 kW / 25-35 hp18.5-26 kW / 25-35 hpMain drive size4-11 kW / 5-15 Hp4-11 kW / 5-15 hp11-18.5 kW / 15-25 hp11-18.5 kW / 15-25 hpBack drive size 3 kW / 4 hp7.5 kW / 10 hpDesignation CDNX 300CDNX 400CDNX 500CDNX 700Bowl diameter360 mm / 14 inches440 mm / 17 inches510mm / 20 inches650 mm / 25 inchesBowl speed (maximum)4200 rpm3800 rpm3250 rpm3100 rpmG-force (maximum)3550 G3551 G3011 G3491 GGross weight2250 kg / 5622 lbs3700 kg / 8157 lbs4650 kg / 10250 lbs6500 kg /14300 lbsLength (L)4280 mm / 169 inches4730mm / 120 inches UL 5340 mm / 21023 inches6385 mm/ 251 inchesWidth (W)990 mm / 39 inches1060 mm / 42 inches1150 mm / 46 inches1450 mm / 57 inchesHeight (H)1348 mm / 53 inches1500 mm / 59 inches1376 mm / 54 inches1834 mm / 72 inchesTotal installed power22-48 kW / 35-70 hp15-66 kW / 20-80 hp90 kW / 120 Hp83-205 kW / 109-273 hpMain drive size11-22 kW / 15-30 hp11-45 kW / 50 hp75 kW / 100 hp37-160 kW / 50-200 hpBack drive size 5.5-11 kW / 7 hp 5.5-15 kW / 7 hp15 kW / 20 hp15-30 kW / 20-40 hpCutpoint: D50: < 6μm, D90: < 60 μm for all sizes*** (CS) Countershaft Machine with fixed differential speedMeasurementCDNX 100, 100CS, 200, 200CSCDNX 300, 400, 500, 700This document and its contents are subject to copyrights and other intellectual property rights owned by Alfa Laval Corporate AB. No part of this document may be copied, re-produced or transmitted in any form or by any means, or for any purpose, without Alfa Laval Corporate AB’s prior express written permission. Information and services provided in this document are made as a benefit and service to the user, and no representations or warranties are made about the accuracy or suitability of this information and these services for any purpose. All rights are reserved.200001094-1-EN-GB© Alfa Laval Corporate ABHow to contact Alfa LavalUp-to-date Alfa Laval contact details for all countries are always availableon our website at 。
Proximity Series QV Quick-View 旋转位置指示器 开关说明说明书

Proximity Series QV Quick-View ®Rotary Position Indicators/Switches are produced with up to four individual mechanical or proximity switches. Instructions below include installation, as well as adjustment procedures for direct drive and lever drive models.INSTALLATION1. Mounting kits, when provided include couplers, lever arms and screws for mounting the position indicator to a valve or actuator. A position indicator is mount-ed using direct drive hardware for quarter turn applications (rotational) and lever drive hardware for converting linear motion to rotary. Tubular spacers are also pro-vided for some installations.2. For direct drive models, attach appropriate drive yoke or solid block onto the two pins, using a #6-32 X 1/4˝ screw provided. Do not attempt to fabricate your own yokes since this a special spring-tempered material. For direct drives, with the actuator shaft rotated to its counterclockwise position, spread the driving yoke and slip it down onto the square (or rectangular) shaft of the actuator. Attach bracket with two hex cap screws. Before tightening screws, operate control slowly with a wrench or power, and observe that drive shaft and drive yoke are concentric and perpendicular throughout the complete stroke. Adjust position as required and tighten all mounting screws. Check concentricity and perpendicularity.3. For lever drive models, attach the appropriate driving lever onto the shaft. Do not tighten. Attach switch and bracket to actuator, making sure that the lever is free to rotate over the entire range of the actuator stroke. Attach the driving pin or bolt through the lever arm if slotted, or on the driving side of the lever. (It may be nec-essary to loosen or remove the bracket mounting to accomplish this connection on some actuators.) Operate the actuator very slowly and observe movement of all pins and levers to be sure there are no interferences. Slide lever up or down on switch shaft to the most desirable position. When all motions are made and clear-ances are adequate, tighten clamp screw on lever that was left loose above. Now tighten all the mounting screws. Re-check the travel of all levers and pins for prop-er clearance throughout the complete stroke of the actuator.4. Push cover down, then turn it counterclockwise and lift straight up to remove.Remove inner cover window. Remove the indicator drum.5. Switches are set at the factory in the counterclockwise position listed below:2 Switch Unit #1 Open #2 Closed 4 Switch Unit #1,3 Open #2,4 Closed90° rotational travel will reverse all of the above positions.[77.79]1st Code (1st X) Number of Switches 0None+1One Switch+2Two Switches+3Three Switches+4Four Switches+2nd Code (2nd X) Switch Type 0No Switches+110A Mechanical Snap Switch 20.1A Mechanical Gold Contacts 32A Proximity Reed Switch+45-25 VDC Namur Sensor 510-30 VDC Inductive Sensor 610A Mechanical Snap Switch 4th Code (4th X) Driving Style 1Direct Drive+2Lever Drive+3Namur Drive+5th Code (5th X) Lighting Option 0None+128 VDC Lights6th Code (6th X) Visual Indication 0None1Standard (Open Closed)+2Upside Down (Open Closed)+7th Code (7th X) Additional Options EX Class I, Div. II, Groups A, B, C & D.Class II, Div. II Groups F & G.QV Model Number Prefix3rd Code (3rd X)0QV 2 1 0 1 0 1 - Example Popular Model Number + EX, Explosion-proof option available.QUICK-VIEW ®COMPLETE MODEL CHART SPECIFICATIONSMinimum Rotation Travel – Switches only:5°Maximum Rotation Travel – Switches only: 360°Temperature Limits: -40 to 180°F (-40 to 82°C).Switch Type:SPDT.Electrical SPDT Switch Ratings:QV-X1XXXX: 10A@125/250VAC;0.5A125VDC;********************.QV-X2XXXX: 1A@125VAC;*******************.QV-X3XXXX:2A@125VAC;*******************.QV-X4XXXX:5-25 VDC NAMUR sensor.QV-X5XXXX:10-30 VDC INDUCTIVE sensor.QV-X6XXXX:10A 125/250 VAC mech. switch.Lighting Supply Voltage:24-28 VDC.Enclosure Material: Polycarbonate housing and conduit.Conduit Entrance: One 3/4˝ NPT.Enclosure Rating: NEMA 4, 4X. Optional explosion-proof, rated: Class I, Groups A, B, C, D; Class II, Groups F & G; Div. 2.Maximum Altitude:2000 m (6560 ft).。
Festo DHTG 2018-02e 旋转索引表操作指南说明书

enOperating instructions80858602018-02e [8085862]Rotaring indexing tableDHTGDHTG2Festo – DHTG – 2018-02eTranslation of the original instructions DHTG-ENIdentification of hazards and instructions on how to prevent them:DangerImmediate dangers which can lead to death or serious injuriesWarningHazards that can cause death or serious injuriesCautionHazards that can cause minor injuriesOther symbols:NoteMaterial damage or loss of functionRecommendations, tips, references to other documentationEssential or useful accessoriesInformation on environmentally sound usageText designations:Activities that may be carried out in any order1.Activities that should be carried out in the order stated –General listsèResult of an action/References to more detailed informationDHTGFesto – DHTG – 2018-02e English 3English – Rotaring indexing table DHTGTable of contents1Operating elements and connections 4 (2)Function and application 5...................................................3Transport and storage 5.....................................................4Requirements for product use 5...............................................5Installation 6..............................................................5.1Mechanical assembly 6......................................................5.2Installing the pneumatic system 7..............................................5.3Electrical installation 9.......................................................6Commissioning 10.. (7)Operation 12...............................................................8Maintenance and care 13.....................................................9Dismantling and repairs 14...................................................10Accessories 16..............................................................11Troubleshooting 16. (12)Technical data 17............................................................13Characteristic curves 18......................................................DHTG4Festo – DHTG – 2018-02e English1Operating elements and connectionsFor all available product documentation è/pk12356789aJ 461Retaining screw for table bearing 2Threaded and pin hole for adapter 3Through hole for power supply 4Threaded and pin hole for plate5Centring/through hole and thread for fastening6Adjusting screw for setting the cushioning7Threaded hole for sensor for position sensing 8Supply port A and B forclockwise/anti-clockwise rotation 9Supply port C and D for reciprocatingoperation (sealed on delivery)aJ One-way flow control valve for speedregulationFig. 1DHTGFesto – DHTG – 2018-02e English52Function and applicationThe DHTG rotary indexing table is a double-acting rotary drive based on the toothed rack and pinion principle with forced locking (as from size DHTG-140 also with overload protection). When the compressed air ports are pressurised alternately, two toothed rod pistons move backwards and forwards. By means of a pinion, the pistons convert the linear movement into a rotary movement. A second pair of pistons controls the engagement of the pinion in the table gearing and the locking of the holding position. The integrated shock absorber brakes the rotary indexing table in the direction of rotation.Fig. 2The DHTG rotary indexing table is intended for turning the work load by a defined angle into a holding position.3Transport and storageTake the weight of the DHTG into consideration. It weighs up to 25 kg. Ensure the following storage conditions are met:–Short storage times and–Cool, dry, shaded, corrosion-resistant storage locations.4Requirements for product useNoteImproper handling can result in malfunctions.Be sure to always comply with the specifications in this chapter.Compare the maximum values specified in these operating instructions with those of your actual application (e. g. forces, torques, temperatures, masses, speeds).Only compliance with the load limits allows operation of the product in compliance with the relevant safety regulations.Take into consideration the ambient conditions at the location of use. Corrosive environments reduce the service life of the DHTG.Ensure that there is a supply of correctly prepared compressed air.Maintain the selected medium for the complete service life of the product. Example: Always use non-lubricated compressed air. Pressurise your entire system slowly.This will prevent uncontrolled movements from occurring.For slow start-up pressurisation use safety start-up valve type HEL.Comply with the regulations of the trade association, the German Technical Control Board or relevant national regulations.DHTG6Festo – DHTG – 2018-02e EnglishRemove all transport packing such as foils, caps, cartons (except for any sealing elements in the pneumatic connections and holes for the proximity switches). The packing is intended for recycling (except for: oiled paper = other waste).Use the product in its original condition without any unauthorised modifications.Take the tolerance of the tightening torques into account. Unless otherwise specified, the tolerance is ±20 %.5Installation5.1Mechanical assemblyMake sure there is sufficient space for the pneumatic connections, for conversion or for replacing the shock absorber.Fasten the DHTG with four screws and ZBH centring sleeves.Tightening torques è Tab. 1, Tab. 2.Direct mounting from above Size6590140220Screw M4M6M6M8Recess for centring sleeve [mm]7121215[mm]5888Tightening torque [Nm]2.99.99.924Tab. 1Direct mounting from below Size6590140220Screw M5M8M8M10Recess for centring sleeve [mm]7121215Tightening torque [Nm]5.9242447Tab. 2Fig. 3Fig. 4DHTGFesto – DHTG – 2018-02e English 7Fasten the blank plate with 6 screws and 2 centring pins.After fitting, the 6 screw recesses can be sealed with the cover caps supplied (press in until flush).Blank plate mounting Size6590140220ScrewM4M4M6M8Locating hole for centring pin [mm]4456Depth locating hole for centring pin [mm]5888Tightening torque [Nm]2.92.99.924Tab. 35.2Installing the pneumatic systemConnect the pneumatic ports A to D (if applicable remove sealing elements).Clockwise or anti-clockwise rotation 1)Size 6590140220Connection A Unlock and turnConnection BLock and return stroke Connecting thread M5G x Tightening torque1.5 Nm 7 Nm1)Modification è 9 Dismantling and repairsTab. 4Reciprocating operation 1)Size6590140220Connection A Unlock Connection B LockConnection C Clockwise rotation 2)Connection DAnti-clockwise rotation Connecting thread M5G x Tightening torque1.5 Nm 7 Nm1)Separate kit required (Accessories è /catalogue)2)Use external flow control valveTab. 5Fig. 5Fig. 7DHTGAs an example 4 interfaces are shown:Tab. 6NoteIf used in safety relevant applications, additional measures are necessary, e. g. inEurope the standards listed under the EU machine guidelines must be observed.Without additional measures in accordance with statutory minimum requirements, theproduct is not suitable for use in safety-related sections of control systems.8Festo – DHTG – 2018-02e EnglishDHTGFesto – DHTG – 2018-02e English 95.3Electrical installationIf proximity switches are used for position sensing:NoteFaulty switching or damage to the proximity switches due to being screwed in too far. Make sure the proximity switches arescrewed into the thread (U), (V) or (W) up to the following maximum depth.Max. screw-in depth Size6590140220Thread (U), (W)[mm]11.511.513.518.5Thread (V)[mm]19.7141621Tab. 8Screw the proximity switches into the following threaded holes:SensingDirection of rotation of plate Clockwise rotationAnti-clockwise rotation (reciprocating operation/flexible control)Direction of rotation (W)(U)Locking mechanism (V)(V)Piston end position (U)(W)Tab. 9When the DHTG is used with 3-part split (DHTG-140 and DHTG-220):NoteBased on the design, the rotating plate can engage in an intermediate position (corresponding to the 6-index stations).After an emergency stop / overload, make sure that the rotating plate is in the desired position before the system is placed back in operation.If the rotating plate is engaged in an intermediate position, bring the locked rotating plate into the desired position by jerking and twisting it against the overloadprotection.Fig. 8DHTG10Festo – DHTG – 2018-02e English6CommissioningWarningRisk of injury from rotating masses.Make sure nobody can place his/her hand in the positioning range of the DHTG and that no objects lie in its path (e. g. by providing a protective screen).NoteIncorrect functioning due to inaccurate toothed rod position. When the DHTG isexhausted, the resetting force of the shock absorber can push the rotary table out of the end position and into an undefined position.Before each commissioning procedure, pressurise the last pressurised connection:–Connection (B) for clockwise/anti-clockwise rotation–Connection (C) or (D) for reciprocating operation/flexible control.NoteClockwise rotation is controlled internally through the flow control valve aJ .Reciprocating operation must be controlled externally through an additional one-way flow control valve GRLA, Connection (C), Fig. 10 (è /catalogue).Screw the flow control screw aJ :–in completely,–then loosen one rotationSlowly pressurise the complete system with at least 4 bar. Start a test run Tab. 10.Check in a test run at low pulse frequency whether the following modifications are necessary:–Readjustment of the proximity switches–Increase the speed step-by-step by unscrewing the flow-control screw aJ –Set the cushioning.Fig. 10Direction of rotation of plateClockwise/anti-clockwise rotation Reciprocating operation/flexible control 1)Basic position: Connection (B) pressurised è see examples Tab. 11 to Tab. 131.Slowly pressurise connection (A)2.Provide clock pulses for the valve1)Internal flow control in one direction only (if necessary throttle different direction externally)Tab. 10Examples for reciprocating operation/flexible controlClockwise rotation ReactionBasic position: Connection (B) and (D) pressurised1.Pressurise connection (A)Unlock2.Pressurise connection (C)Pulse right3.Pressurise connection (B)Lock4.Pressurise connection (D) (continue with 1.)Return strokeTab. 11Anti-clockwise rotation ReactionBasic position: Connection (B) and (C) pressurised1.Pressurise connection (A)Unlock2.Pressurise connection (D)Pulse left3.Pressurise connection (B)Lock4.Pressurise connection (C) (continue with 1.)Return strokeTab. 122 x clockwise and 2 x anti-clockwise rotation ReactionBasic position: Connection (B) and (D) pressurised1.Pressurise connection (A)Unlock2.Pressurise connection (C)Pulse right 13.Pressurise connection (B)Lock4.Pressurise connection (D)Return stroke5.Pressurise connection (A)Unlock6.Pressurise connection (C)Pulse right 27.Pressurise connection (B)LockDirection of rotation change8.Pressurise connection (A)Unlock9.Pressurise connection (D)Pulse left10.Pressurise connection (B)Lock11.Pressurise connection (C)Return stroke12.Pressurise connection (A)Unlock13.Pressurise connection (D)Return stroke14.Pressurise connection (B) (continue with 1.)LockTab. 13Note the maximum permitted frequencies as a factor of the moment of mass inertia (è Technical specifications).The rotary indexing table must not strike hard against the end stops and the overload protection must not be triggered.End the test run.For setting the cushioning:Loosen the clamping element (K) one rotation.Screw in the adjusting screw 6 until the desired cushioning is achieved. The rotary indexing table must not strike hardagainst the end stops and the overload protection must notbe triggered. The maximum moment of mass inertia mustnot be exceeded.Fig. 11Adjusting screw direction of rotation 6ReactionClockwise1)Cushioning is increased Anti-clockwise Cushioning is reduced1)Screw in the adjusting screw until it is flushTab. 14Tighten the clamping element (K) again.Tightening torqueSize6590140220Width across flats 2.5 2.544Tightening torque[Nm]0.80.8 2.5 2.5Tab. 157OperationWarningRisk of injury from rotating masses.Make sure nobody can place his/her hand inthe positioning range of the DHTG and that noobjects lie in its path (e. g. by providing aprotective screen).Note the moment of mass inertia as a factor of the switching or cycle frequency (è Characteristic curves).–The maximum achievable switching frequency as a factor of the moment of mass inertia can be read in the diagram Switching frequency. The switching time can be calculated from thisby T = 60/f. The response time comprises: Switching time = unlocking, turning, locking and thereturn stroke of the work piston.–The maximum achievable cycle frequency as a factor of the moment of mass inertia can be read in the diagram Cycle frequency. The minimum possible cycle time can be calculated from this by T = 60/f.The actual cycle time is then calculated as follows:Cycle time = switching time + processing time + dwell time.–The processing time results from the time which the relevant customer application requires(e. g. time for removing components, press-in time, etc).–Dwell time may be necessary if the actual cycle time is less than the minimum possible cycle time (calculation example è Catalogue specifications).Note that the viscosity of the shock absorber oil decreases with increasing heat. The shock absorber might therefore strike through if the device is operated for too long a period. If necessary reduce the moment of mass inertia.Avoid the DHTG coming into contact with:–Aggressive media–Grinding dust–Glowing sparks or chips.These will damage the DHTG.8Maintenance and careSwitch off the power supplies:–Operating voltage–Compressed air supply.Cleaning:Only clean the DHTG using a soft cloth.All non-abrasive cleaning agents are permitted.Due to its service life lubrication the DHTG does not require any maintenance.Regular removal of the lubricating grease on the surface of the piston rod will reduce the service life.After a conversion (e. g. to reciprocating operation) lubricate the following components with LUB-E1:–piston, piston chamber, seal, lock, toothed rod, pinion, table bearing, dividing disc.We recommend the mechanical components are lubricated again after every 5 million switching cycles.Check the shock absorbers every 2 million strokes for:–Oil leakage–Hard knocking–Function (shock absorber head must not remain in the retracted end position).Dismantling the shock absorber (è Dismantling and repairs).Replace the shock absorber when it shows one of the following signs of wear, or every 10 million strokes at the latest.Check whether lubrication/testing must be carried out more frequently.This may be necessary in case of:–High temperatures–Excessive dirt–Fat solvent fluids or fumes in the vicinity.9Dismantling and repairsRecommendation: Return the product to our repair service for overhaul.The necessary fine adjustments and tests will then be taken into account.Information about spare parts and aids can be found at: /sparepartsSwitch off the power supplies:–Operating voltage–Compressed airExhaust the system and the product.Replacing the integrated shock absorber:1.Unscrew the flow-control screw aJ.2.Unscrew the fastening screws (M) on the sub-base.ing pliers, remove the retaining ring on the shock absorber.4.Replace the shock absorber.5.Fit the individual parts again in reverse sequence (tightening torque è Tab. 16).Fig. 13Tightening torqueSize6590140220Flow control screw aJ[Nm] 1.5 1.5 5.5 5.5 Fastening screws (M)[Nm] 2.9 2.99.99.9Tab. 16Conversion from clockwise rotation (as supplied) to anti-clockwise rotation:1.Loosen the clamping element (K) of the adjusting screw one rotation.2.Unscrew the adjusting screw 6 a few rotations.3.Unscrew flow control screw aJ and the fastening screws (M) from the sub-base.ing pliers, remove the retaining ring (S) on the shock absorber.5.Fit the following:–the shock absorber with the retaining ring in the adjacent hole–the O-ring (P) / buffer (for DHTG-65) in the adjacent groove–the distance piece (T) in the same hole (distance piece omitted for 2/3 index stations)–the sub-base with the fastening screws and the flow control screw in reverse sequence (tightening torque è Tab. 17).6.Unscrew the fastening screws (N) on the stop plate.7.Unscrew:–both locking screws (O) on the rear of the stop plate to begin with,–then screw them in again into the open holes (tightening torque è Tab. 17).The open holes (R) or (L) in Fig. 14 determine the direction of rotation(Holes (R) open: clockwise rotation).8.Screw the fastening screws (N) on the stop plate again (tightening torque è Tab. 17).The rotary indexing table remains pneumatically controlled as before.9.Screw in the adjusting screw 6 until the desired cushioning is achieved è Fig. 11.10.Tighten the clamping element (K) of the adjusting screw (tightening torque è Tab. 15).Fig. 14Tightening torqueSize6590140220 Flow control screw aJ[Nm] 1.5 1.5 5.5 5.5 Fastening screws (M)[Nm] 2.9 2.99.99.9 Plug screw (O)[Nm]0.5Fastening screws (N)[Nm] 1.5 2.9 5.9 5.9 Tab. 1710AccessoriesNotePlease select the appropriate accessories from our catalogue è /catalogue11TroubleshootingMalfunction Possible cause RemedyRotating plate does not move Overload protection is active Pressurise connection (B) and turnthe plate back against the directionof rotation as far as possible. Doingthis causes the overload protectionand the locking mechanism, ifapplicable, to engage audibly Audible leakage Send DHTG to FestoFlow-control screw closedcompletelyOpen screwRotating plate does not engage End position not reached Unscrew the adjusting screw for theshock absorber until the rotatingplate engagesOverload protection is activeè see aboveToothed disc and pinion stand toothon toothPlease contact Festo s TechnicalHotlineHard metal impact at the end position Adjusting screw for shock absorberunscrewed too farScrew in adjusting screwShock absorber defective Replace shock absorber(è 9 Dismantling and repairs)Hard metallic knocking in the locking mechanism Adjusting screw for shock absorberscrewed in too far (e. g. whenchanging the direction of rotation)Unscrew adjusting screwPlate position incorrect Overload protection engagedincorrectly at 180° (plate offset 30°)Force overload protection and turn until it re-engagesTab. 1812Technical data1)Parallelism of the plate surface relative to the housing support2)Measured on the surface of the plate at the edge of the plate in relation to the housing support3)Measured on the inner diameter of the plate in relation to the housingTab. 1913Characteristic curvesSwitching frequency f as a function of mass moment of inertia J Size 65J [kgm]Size 902Size 140f [1/m i n ]22 indexing stations3 indexing stations4 indexing stations 6 indexing stations 8 indexing stations 12 indexing stations 24 indexing stationsSwitching frequency f as a function of mass moment of inertia J Size 220f [1/m i n ]23 indexing stations4 indexing stations 6 indexing stations 8 indexing stations 12 indexing stations 24 indexing stationsMax. permissible cycle frequency f as a function of mass moment of inertia J Size 65f [1/m i n ]J [kgm 2]Size 90f [1/m i n ]J [kgm 2]2 indexing stations3 indexing stations4 indexing stations 6 indexing stations 8 indexing stations 12 indexing stations 24 indexing stationsMax. permissible cycle frequency f as a function of mass moment of inertia J Size 1402Size 220J [kgm 2]3 indexing stations4 indexing stations 6 indexing stations 8 indexing stations 12 indexing stations 24 indexing stationsDHTGFesto – DHTG – 2018-02e English21Reproduction, distribution or sale of this document or communication of its contents to others without express authorization is prohibited. Offenders will be liable for damages. All rights reserved in the event that a patent, utility model or design patent is registered.Copyright:Festo SE & Co. KGRuiter Straße 8273734 EsslingenGermanyPhone:+49 711 347-0Fax:+49 711 347-2144E-mail:******************************* Internet:。
液体分配器使用说明书

液体分配器使用说明书一、产品概述液体分配器是一种用于精确分配液体的设备。
它采用先进的技术和设计,可广泛应用于实验室、医疗、化工、生物科技等多个领域。
本说明书将详细介绍液体分配器的使用方法和注意事项,以确保用户正确操作并获得最佳的使用效果。
二、产品组成液体分配器由以下几个主要组成部分构成:1. 手柄:用于控制液体的分配,具有人性化的设计和舒适的握持感;2. 容量调节旋钮:用于调节分配器的容量,可根据需要进行精确的容量调节;3. 顶部按钮:用于启动分配器的液体释放;4. 液体进/出口:用于连接液体源和目标容器的管道接口。
三、使用步骤1. 准备工作:确保液体分配器和液体源、目标容器之间的连接正确并牢固。
检查管道接口是否紧固,避免泄漏。
2. 容量调节:根据所需的液体容量,旋转容量调节旋钮进行精确调节。
注意,每个液体分配器的容量范围可能会有所不同,请您在使用之前查看产品标识,确保所需容量在允许范围内。
3. 液体分配:将手柄握住,并将顶部按钮轻轻按下,使液体从液体源进入分配器。
根据所需的液体容量,适量按下顶部按钮,使液体从分配器流入目标容器。
请注意,每次按下按钮,液体分配器将释放相应容量的液体,因此请确保在操作过程中准确计量所需的容量。
4. 清洁保养:使用完毕后,及时清洗液体分配器。
按照产品说明书中提供的清洁方法和注意事项进行清洁保养,以确保分配器的长期使用寿命和性能稳定。
四、使用注意事项1. 严禁将液体分配器用于与其不兼容的化学物质,以免引起意外反应或损坏设备。
2. 使用前必须仔细阅读产品说明书,并按照说明书中的操作方法正确使用液体分配器。
3. 在使用液体分配器时,必须佩戴合适的防护手套和眼镜,以防止液体溅入皮肤或眼睛。
4. 分配器的部件需要经常进行维护和检查,以确保其正常工作。
如发现任何异常或故障,请立即停止使用,并联系售后服务部门进行维修处理。
5. 在操作过程中,请确保周围环境清洁,避免灰尘或其他杂质污染液体。
GLV流浆箱

GLV流浆箱流浆箱分配器说明3.BTF分配器说明分配器主要部分3.1BTF分配器主要部分BTF分配器主要部分是(见图4和5)1进浆管:准备焊接的管道,适用合适的流送管线。
一对无光泽的法兰盘可防止挂浆。
2BTF分配器锥形底座:在稳浆室前,进浆管被扩至分配器全径。
包含检查/清洗口。
3孔板:一个产生微小湍流的孔板,位于入口处。
它由超高分子量塑料制成(UHMW)。
4稳浆室:这一区域使浆料流速放慢,并均衡的分配浆料到各个分配管。
气垫吸收产生于流送系统的脉冲。
位于分配器顶部的一个或多个旋转喷淋水保持内部表面清洁。
带观察窗的检查/清洗口在分配器的顶部。
侧面的观察窗为检测液位变动提供了分配器内部的视野。
5分配区:位于分配器中间高度,分配管和稀释水管均匀地分布在分配器四周。
6稀释系统:连接稀释水管的是球阀。
阀门将用于为纸页横幅提供定量控制。
分配阀门可以为了自动控制被执行器改变。
7稀释水分配管:稀释系统提供的白水将被送入分配器顶部的环形分配管。
均匀分布的不锈钢管连接对应的阀门,稀释水管与浆料分配管中心对齐并位于其上方。
8浆料分配管:有韧性的管道均匀地布置并且等长,输送浆料从分配器到流浆箱。
这些管道由工业编制材料构成,可以容许广范围的压力和化学物质。
9分配管道:通过均等布置的不锈钢分配管道,从浆料分配管来的浆料被均匀的分布于流浆箱。
这些管道有圆变方的形状,使对着流浆箱的区域最大。
10BTF过渡室:分配管道连接的过渡连接将起混合/扩散的作用。
图4BTF分配器图53.2BTF分配器特征分配器内径: 1600mm分配器总体直径: 2642mm分配区数量: 78进浆管内径: 264.67mm分配器高度: 3650mm分配管内径: 63mm最大温度: 华氏180度最大内部压力; 32m水柱分配器设计流量: 110,000Lpm稀释水设计流量: 5200-9800Lpm注意;BTF通用分配器不能作为压力容器考虑。
稀释水控制阀3.3稀释水控制阀稀释水控制阀用来控制稀释水加入量。
洛ctite 气动分配器说明书
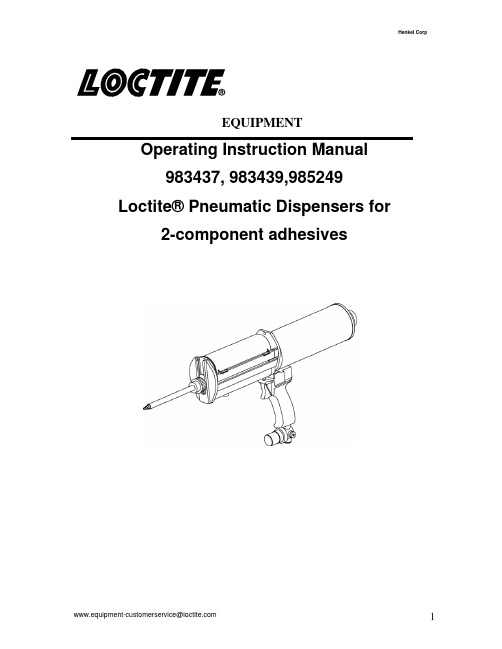
EQUIPMENTOperating Instruction Manual983437, 983439,985249 Loctite® Pneumatic Dispensers for 2-component adhesivesContents:1. Safety instructions 2-4Symbols used in the Operating Instruction ManualExplanation of the safety conceptIntended use2. Parts list for pneumatic dispenser 43. Preparing the dispenser for use 4-5Package contentsPreparation for useOperating principlePreparing the dispenser4. Operation of the dispenser 5-6Insert cartridgeConnect the dispenser to the compressed air supplyDispensing the adhesiveRemoving the cartridge5. Troubleshooting 66. Maintenance and Repair 7Ordering Spare Parts7. Technical data 78. Standards applied 79. Warranty 8Always keep this instruction manual easily accessible to users of the dispenser.1. Safety instructionsRead through this dispenser Operating Instruction Manual carefully. For safe andreliable operation, it is essential for users to understand and follow all the safetyinstructions provided in the Manual.Symbols used in the Manual and on the dispenserINFORMATIONImportant information on installation, operation or maintenance.DANGER / CAUTIONRisks or hazardous applications that can result in severe / fatal injuries or considerable material damage.WEAR GLOVESFailure to do so can result in serious personal injuryWEAR SAFETY GOGGLESFailure to do so can result in serious personalinjuryCEThe pneumatic dispenser is marked with the CEsymbol in compliance with the applicableEuropean directives.Do not use the dispenser until you have read and understood the operating procedure and the instructions contained in this Operating Instruction Manual. The dispenser operates under high pressure. Failure to follow these instructions can lead to inadvertent discharge of pressure or breakage of the dispenser at high pressure and may result in serious personal injury to the user or bystanders and/or property damage.The following instructions must be read and strictly observed:•The user of the dispenser and any persons standing in the vicinity must wear safety goggles and gloves at all times during operation of the dispenser.•The user should never point the barrel end of the dispenser at himself or in the direction of bystanders [animals] or objects during operation.•Never open the pneumatic drive or attempt to remove.•Handle the dispenser properly. Store in a cool dry place. Transport it carefully, with minimal vibration. Do not drop it to the ground or slam it on a bench or other workspace. •Safety devices must not be removed, worked around, bypassed or deactivated during operation.•Always comply with the warnings and notices on the device. Never, under any circumstances, remove these warnings and notices. Replace them immediately if theybecome detached or illegible.•Do not remove, tamper or manipulate pressure limiting valve and and strictly respect pressure limits.•Check the dispenser for visible damage and defects before each use. The dispenser must only be used if it is in good working order. If you have any doubt about the condition of the dispenser, or if there are any signs of breakage or other damage, immediately stop using the device and send it for inspection and repair by a site authorized by the manufacturer. •Keep the dispenser clean at all times. Failure to do so may result in malfunction of dispenser or bodily injury.•Do not attempt to modify or repair the dispenser. Maintenance and repairs must be carried out exclusively by qualified specialists. No such work may be carried out while thedispenser is connected to the compressed air supply.•Always follow safe workplace practices, such as making sure the air hoses are carefully routed so that neither you nor any other person can become entangled in the hoses or trip over them.•Be cautious connecting and disconnecting air pressure hose.•Always keep this instruction manual easily accessible to users of the dispenser.•Use only authentic Loctite® spare parts. Malfunctions or accidents may result if spare parts of other manufacturers are used, and any warranty claims against the manufacturer will be considered void.•Replace missing or damaged hazard warning labels / stickers.Modifications or changes to the dispenser by persons not authorized by the manufacturer and any failure to comply with the safety instructions given in the Operating Instruction Manual are dangerous and can lead to accidents with severe injuries and / or property damage.Intended use of the dispenserThe dispenser has been developed for mixing and applying 2-component adhesives of various different formulas. Any other or additional applications shall be considered as nonconforming, i.e. not conforming to the intended use. The intended use also includes compliance with the instructions in this Operating Instruction Manual as a basic requirement.2. Parts list for pneumatic dispenser:1. Cartridge guide2. Type designation and serial number3. Plunger4. Dispense volume indicator5. Pneumatic drive unit6. Piston rods7. Cartridge ejector button 8. Cartridge sleeve 9. Trigger10. Pressure limiting valve11. Compressed air supply fitting•983723 (packaged separately)12. Handle13. Red button (retract piston rod)3. Preparing the dispenser for use:Package contents•Dispenser• Cartridge sleeve• Mixer(sold separately)• Operating InstructionManualPreparation for useUsers must read and understand the Operating Instruction Manual before first useof the dispenser.Operating principleThe air pressure is reduced by the pressure reductionvalve (10). The piston rods (6) are pushed out of thehousing by the pneumatic piston of the drive unit (5),thereby forcing the component compounds A and Bthrough the mixer.The dispenser operates under high pressure. Failure to follow the instructions inthis Manual can lead to inadvertent release of pressure or breakage of thedispenser at high pressure and may result in serious personal injury to the useror bystanders and/or property damage.Preparing the dispenser•Remove the protective cap (11) from the pressure reduction valve (10).•Install the ¼" BSP adapter (external thread) on the inlet side of the pressure reduction valve, which will allow standard ¼” male connection to be madequick-release coupling.•The use of properly rated pneumatic hose and a quick-release coupling is also recommended.Caution: DANGER OF CRUSHING.Never place your hands or fingers between the plunger and the cartridge.The input pressure of the compressed air must not exceed max. 8 bar (max. 120psi). Requirements for the compressed air supply (see Technical Data).Strictly follow the manufacturer’s safety instructions for the 2-componentadhesive.4. Operation of the dispenserInsert cartridgeNever insert the cartridge while the dispenser is connected to thecompressed air supply.•Push the cartridge into the cartridge sleeve asshown in the drawing and press it down until it clicksinto position. To remove the cartridge stopper,unscrew the cap nut of the cartridge.•Fasten the mixer using the cap nut on the cartridgeoutlet thread.If the cartridge is not in the correct position, the trigger (9) cannot be pressed.•Connect the dispenser to the compressed air supplyDispensing the adhesivePress the trigger (9). Dispensing is started, and the red dispense volume indicator (4) moves forward. When the trigger (9) is released, dispensing stops.The dispense volume can be controlled by means of the pressure reducing valve (10).a) Pull the pressure reduction valve.b) Adjust the dispense volume by turning the adjuster in the + or –direction.c) Press the pressure reduction valve to confirm the set value.Do not remove, tamper or manipulate pressure limiting valve and strictly respect pressure limits.Removing the cartridgeRelease the trigger (9) and press the red button (13) until the feed plungers have retracted to the back end-stop. Using the release button (7), push the cartridge out of the cartridge retainer and pull it upwards out of the unit. Dispose of the cartridge and mixer in conformity with the m anufacturer’sspecifications.5. Troubleshooting:ProblemPotential Cause RemedyPlunger discs cannot enter the cartridgeCartridge not fully inserted in cartridge bedCheck that there is no foreign matter in the cartridge bed. Push the cartridge fully down into the cartridge bed. Mind your fingers.The cartridge cannot be removed from the dispenser .The plunger discs are still in position inside the cartridge . Press the red button to fully retract the plunger discs to theback end-stop.6 . Maintenance and repair:NoticesAll maintenance and repairs must only be carried out by sites authorized by themanufacturer and exclusively by qualified and suitably trained personnel.Always disconnect the compressed air supply from the dispenser duringmaintenance and repairs.Never open the pneumatic drive unit. If the pneumatic drive unit is or appears tobe in need of maintenance or repair, contact a Henkel authorized Service CenterKeep the dispenser clean at all times. Failure to do so may result inmalfunction of dispenser or bodily injury.Do not use aggressive cleaning products to clean the surface of the device.Information for ordering spare parts:Whenorderingspareparts,**************************************************information:•Dispenser Item numberFor 983437 Dispenser1:1/2:1 Cartridge tray- 983726For 983439 Dispenser1:1/2:1 Cartridge tray- 9837274:1 Conversion Kit - 984210For 985249 Dispenser10:1 Conversion Kit- 985287For all 3 units: ¼” BSP male to NPT female air line fitting - 9837237. Technical data:Operating pressure: max. 6 bar (max. 87 psi)Compressed air supply: max. 8 bar (max. 120 psi)Air requirements: ISO 8573-1.2.4.2Pressure adjustment: Variable 0- 6 bar (87 psi)Sound level: 83 dBAkg1.6Weight: 983437kg2.2983439/9852498. Standards applied:2006/42/EG:Machinery Directive97/23/EC:Pressure Equipment DirectiveISO 8573-1:Compressed air quality classes9 WARRANTYHenkel expressly warrants that all products referred to in this Instruction Manual for Loctite®Pneumatic Dual Cartridge Dispensers (hereafter called “Products”) shall be free from defects in materialsand workmanship. Liability for Henkel shall be limited, as its option, to replacing those Products which areshown to be defective in either materials or workmanship or to credit the purchaser the amount of thepurchase price thereof (plus freight and insurance charges paid therefore by the user). The purchaser’s soleand exclusive remedy for breach of warranty shall be such replacement or credit.A claim of defect in materials or workmanship in any Products shall be allowed only when it is submittedin writing within one month after discovery of the defect or after the time the defect should reasonably havebeen discovered and in any event, within (12) months after the delivery of the Products to the purchaser.No such claim shall be allowed in respect of products which have been neglected or improperly stored, transported, handled, installed, connected, operated, used or maintained. In the event of unauthorized modification of the Products including, where products, parts or attachments for use in connection with the Products areavailable from Henkel, the use of products, parts or attachments which are not manufactured by Henkel, noclaim shall be allowed.No Products shall be returned to Henkel for any reason without prior written approval from Henkel.Products shall be returned freight prepaid, in accordance with instructions from Henkel.NO WARRANTY IS EXTENDED TO ANY EQUIPM ENT WHICH HAS BEEN ALTERED, MISUSED, NEGLECTED, OR DAMAGED BY ACCIDENT.EXCEPT FOR THE EXPRESS WARRANTY CONTAINED IN THIS SECTION, HENKEL MAKES NO WARRANTY OF ANY KIND WHATSOEVER, EXPRESS OR IMPLIED, WITH RESPECT TO THE PRODUCTS.ALL WARRANTIES OF MERCHANTABILITY, FITN ESS FOR A PARTICULAR PURPOSE, ANDOTHER WARRANTIES OF WHATEVER KIND (INCLUDING AGAINST PATENT ORTRADEMARK INFRINGEMENT) ARE HEREBY DISCLAIMED BY HENKEL AND WAIVED BYTHE PURCHASER.THIS SECTION SETS FORTH EXCLUSIVELY ALL OF LIABILITY FOR HENKEL TO THEPURCHASER IN CONTRACT, IN TORT OR OTHERWISE IN THE EVENT OF DEFECTIVEPRODUCTS.WITHOUT LIMITATION OF THE FOREGOING, TO THE FULLEST EXTENT POSSIBLE UNDER APPLICABLE LAWS, HENKEL EXPRESSLY DISCLAIMS ANY LIABILITY WHATSOEVER FORANY DAMAGES INCURRED DIRECTLY OR INDIRECTLY IN CONNECTION WITH THE SALEOR USE OF, OR OTHERWISE IN CONNECTION WITH, THE PRODUCTS, INCLUDING, WITHOUT LIMITATION, LOSS OF PROFITS AND SPECIAL, INDIRECT OR CONSEQUENTIAL DAMAGES, WHETHER CAUSED BY NEGLIGENCE FROM HENKEL OR OTHERWISE.Henkel Corporation One Henkel Way Henkel Canada Corporation2225 Meadowpine BoulevardHenkel Capital, S.A. de C.V.Boulevard Magnocentro No. 8 Piso 252760 Huixquilucan, Estado de MexicoRocky Hill, CT 06067-3910 Mississauga, Ontario L5N 7P2® and ™ designate trademarks of Henkel Corporation or its affiliates. ® = registered in the U.S. and elsewhere. © Henkel Corporation, 2009. All rights reserved.Manual # 8902022, Date 07/2009。
FPX 564 SS 空间节省型气火炉产品说明书

564 SSSpace Saver Gas Fireplace564 SSSpace Saver Gas FireplaceOVERVIEW:The 564 SS (Space Saver) is FPX s newest gas fireplace. With its consistent, radiant and convective heat and reduced dimensions the unit is ideal for zone heating in bedrooms, dens and intimate spaces that do not require a great deal of heat.˚ Although the actual measurements of the 564 SS are reduced in size from the 864 line, the fireplace features a large fireviewing viewing area of 564 square inches of high quality, high clarity, tempered glass.The realistic flame of the fire,˚along with the heat output has the ability to be modulated by the convenience of the Comfort Control gas valve. This component allows you the ability to turn the burner from high to low, while maintaining the fire and glowing embers of the burner. This gives the fireplace the ability to be utilized and enjoyed year round, preventing overheating in zones and always assuring comfort.The 564 SS may be personalized for each owner and space. One can choose from something as simple as the basic grill to eleven different face options in various textures and rich colors. A reversible Ceramic Fireback option is available for complete customization and radiant heat output.˚ With a depth of only 16 1/2 inches, the 564 SS leaves a very small foot print within the room it is installed and has the ability to be sheetrocked up to the very face of the fireplace. The 564 SS not only provides an optimal heat source for your home but is also the perfect focal point in any room of the home.TECHNOLOGY:A two level pan burner system is included in the 564 SS.˚ The back burner provides the rear flame giving the fire its indisputable realistic color and shape with the flames interlaced throughout the exquisite hand-crafted, 5 piece ceramic log set. Meanwhile the front burner, illuminating the coal bed, gives the most realistic wood˚ fire a gas stove can produce. The 564 SS also features the option of adding a wall mounted thermostat or remote control. With the introduction of the Omega remote control later this Summer, you will also be able to regulate the flame height, blower speed and intensity of the accent light, all from one control. Additional features of the Omerga Control include on/off switch, timed shut off and child proof safety options.Designed for ultimate climate comfort in intimate settings, the 564 SS is certain to not only provide heat, but also enhance the decor of the home.SAME GREAT OPTIONS:Like the best-selling˚864 TRV and 864 HH˚the 564 SS offers˚a huge view of the fire, incredible heating efficiency, wall thermostat and remote control operation, and a wide range of beautiful, custom high-end faces and liners to choose from. The fireplace can be completed with the basic grill set, or with the homeowner s choice of one of 11 upgrade faces. A selection of andirons will be available at a later date.SAME EASY INSTALLATION:The 564 SS features easy to follow framing dimensions to allow builders fast and easy installation and venting. The 564 SS allows non-combustible material right up to the finish face.ECONOMICAL COST:The 564 SS is very economical. The 564 SS is targeted to retail for under $1,500, making it ideal for the builder market and those customers looking for a high quality entry-level gas fireplace for their home or remodel.Space Saver Gas FireplaceThe 564 SS offers you a heavier-built fireplace, improved burner system, greater turn-down and greater range of options over competitive brands on the market. ˚Your customers get the same great selection of upgrade faces and options that you and your sales staff are already familiar with on the 864 line-up.FOR THE CONSUMER:The heat is consistent, radiant, convective and gentle and is designed for zonal heat in the room where it is installed. Theflame and heat output can be adjusted to provide year-round fireplace enjoyment.bedroom or bathroom application. The 564 SS is also perfect for those who are looking for an economical fireplace,without a lot of heat.For an easy sales flow we highly recommend you have a minimum of two 564s on the floor . One burning fully dressed with all the options to include an upgrade face, accent light, remote control and one display model shown with basic grill package.If you can show the consumer and the builder they have the option to customize their fireplace and the cost,you increase your chance for sales over your competitors.Point Out the Extra Large Glass SizeThere are 564 sq. in. viewing area, same as on the 36 DV-XL. Mention advantages of tempered glass. Point out the screen as a safety feature for children. If the screen is not desired, point out that it can be removed.Explain the Two Level Pan BurnerThere is a realistic flame and fire, with no visible tubes to detract from the effect of the burner . The burner features two separate levels, front and rear . The 564 SS features the Travis Comfort Control “ valve that allows the user to turn down the flame (and heat) from 20,500 Btu s all the way down to 5,100 Btu s NG. You can turn the rear flame area off completely. This allows the user to enjoy the beauty of a fire year-round without all the heat.Demonstrate the Heat Capacity and Optional Twin 90 CFM Fan (180 Total CFM)The 564 SS is designed for gentle, even heating of your home. The fireplace gradually brings the temperature up in the home without over heating the room. You will get a constant, even heat that maintains the comfort level in the room which allows you to enjoy the fire longer .Demonstrate the optional Accent LightDemonstrate the rheostat control of the light, and the way it highlights the log set and brick liner with the fire on or off.Have a remote control installed and operatingPoint out the easy operation from any location in the room, chair or bed. Mention the fireplace will accept the new Omega Modulating Remote when it becomes available. This will allow you to demonstrate how you can modulate,from LOW , MEDIUM to HIGH, the flame height, blower speed and intensity of the Accent Light from the same control.Point out detail of hand carved logsBeautiful detail of logs adds to realism of fire and the fireplace. Cast from real hand-carved logs.Talk about customized lookYour customer can personalize their fireplace with a face, liner , accent lighting etc.Space Saver Gas FireplaceStandard 8 Simpson Current PipeEasy, inexpensive rear vent package available. Top vent can be reduced to 6 5/8 with adaptor .Easy to Adjust Air Shutter Both front and rear burners have external air shutter adjustment.Air and Exhaust RestrictorsSame configuration as found on the 864TRV . Makes it easy for installer since they are familiar with the 864TRV set-up. Aids in reproducing same showroom quality fire no matter the flue configuration.Wall Switch Standard The convenience of an on/off switch located on the wall at no additional cost.Elevated 5/8 solid steel grateDurable fire grate adds beauty and realism to the look of the fire.Valve Centered Easy access for servicing fan.Black Valve Cover Cleaner look with control cover open or closed.Face & Grill OptionsChoice of black basic grill kit or one of 13 upgrade faces¥ Arched black painted ¥ Artisan black painted ¥ Arched brushed nickel ¥ Artisan antique nickel ¥ Arched French Country black painted ¥ Artisan antique copper¥ Arched French Country antique gold ¥ Artisan black painted double door ¥ Metropolitan black painted ¥ Matrix brushed nickel ¥ Metropolitan brushed nickel ¥ New Traditions Arch ¥ New Traditions RectangularUpgrade faces also fit the 564 Electric fireplaceMantle ClearancesCloser clearances to mantle allows for a traditional fireplace look. No out-of-scale mantle restrictions. Graduated mantle clearance up to 12 total mantle depth.Standard Shut-off ValveA shut-off valve and 12 piece of flex line are provided with unit. Reduces installation cost and time for your installers.Optional Accent Lighting with Rheostat Control Adjustable light adds glow to the firebox when fire is burning. Adds drama to the firebox even when the fire is out, especially during non-burning season.Wall Thermostat option Wall mounted operation for automatically controlling room temperature.Remote Control Thermostat optionOperation of the fire from the convenience of a chair or bed. Features thermostat control, on/off, timed shut-off and child proof options. Compatible with Omega Modulating Remote Control. Soon to be available, this remote controls the flame height, blower speed and intensity of the accent light.8 Rear Vent Kit optionInexpensive kit makes for easy rear vent installation.Optional FirebackCeramic fireback reflects more heat out of the glass. The reversible herringbone/standard brick fireback is very realistic and complements any face and decor . A reversible Diamond Mosaic/Stucco fireback will be available later .564 SSSpace Saver Gas Fireplace564 SS - Space Saver Standard FeaturesBodySku 98500241• 564 Sq. In. tempered glass • Removable Safety screen in front of glass• Two level pan burner• Wall switch• Top or rear vent option on same unit• Sheet rock right up to the firebox5 Piece Ceramic Log Set Steel Grate Comfort Control Gas ValveCeramic Ember Bed• 8” Chimney• Air and exhaust restrictor • Easy to adjust air shutter • Shut-off Valve• 16 gauge steel construction• LP conversion kit564 SSSpace Saver Gas FireplaceModel 564 SS- Space Saver OptionsReversible - Straight Brick orHerringboneSku 96100179Accent LightsSku 94400100ConvectionFanSku 99000156Reversible - Diamond Mosaic or Plain StuccoSku 96100182FirebacksRemote ControlSku 99300651(No Blower or Light Control)99300677(ON/OFF & Thermostat)Omega Modulating Remotes (ETA Dec. 15th 2007)(Modulates Flame, Blowerand Lights)Sku - NG 99300679Sku - LP 99300678WallThermostat Sku - 99300650Arched Face Upgrade Kit(End Brackets)Sku 985006838” to 6 5/8” Flue Vent Reducer(Top Vent Only)Sku - 98900165Minimum 8”Rear Vent KitSku 98900168Arched Face Set-up TemplateSku 98500674Grill KitBasic Black Grill KitSku 96200808Upgrade FacesFrench CountyBlack Painted Sku 95400408Antique Gold Sku 95400409Classic ArchBlack Painted Sku 95400402Brushed NickelSku 95400405MetropolitanBlack Painted Sku 95400411Brushed Nickel Sku 95400413MatrixBrushed NickelSku 95400475ArtisanBlack Painted Sku 95400418Antique Nickel Sku 95400420Antique CopperSku 95400419New Traditions OnlaysBolts on front of New Traditions Double Doors9630078296300772Arts & Crafts Rect.Arts & Crafts ArchAntique Copper Finish9630078196300771Artisan Rect.Artisan Arch Hand-Hammered Antique Nickel Finish9630078096300770Classic Rect.Classic ArchBronze FinishSku 95400466Includes backing plate, doubledoors and screenNew TraditionsRectangular Double DoorSku 95400462New TraditionsArchedDouble Door Includes backing plate, doubledoors and screen564 SSSpace Saver Gas Fireplace。
分配器运行说明书

分配器运行图解说明书(14位为例)编制:申富国审核:步骤1:(1) 分配器内部柱塞全部推至右侧,油脂从进油口进入通过主油道与(1)油道连通,受泵压油脂通过a油道进入油腔推动柱塞A向左移动(2) 柱塞移动受压油脂通过b油道与(2)油道连通,油脂通过G柱塞右中部空段从r油道流入出油孔,从13出油口排出。
步骤2:(1) 步骤1已将柱塞A推向左侧。
油脂通过主油道,A柱塞右中部空段及斜油道(3)进入油腔推动柱塞B向左移动(2) 柱塞移动受压油脂通过斜油道(4),A柱塞左中部空段从d油道流入出油孔,从2出油口排出。
步骤3:(1) 步骤2已将柱塞B推向左侧。
油脂通过主油道,B柱塞右中部空段及斜油道(5)进入油腔推动C柱塞向左移动(2) 柱塞移动受压油脂通过斜油道(6),B柱塞左中部空段从f油道流入出油孔,从4出油口排出。
步骤4:(1) 步骤3已将柱塞C推向左侧。
油脂通过主油道,C柱塞右中部空段及斜油道(7)进入油腔推动D柱塞向左移动(2) 柱塞移动受压油脂通过斜油道(8),C柱塞左中部空段从h油道流入出油孔,从6出油口排出。
步骤5:(1) 步骤4已将柱塞D推向左侧。
油脂通过主油道,D柱塞右中部空段及斜油道(9)进入油腔推动E柱塞向左移动(2) 柱塞移动受压油脂通过斜油道(10),D柱塞左中部空段从m油道流入出油孔,从8出油口排出。
步骤6:(1) 步骤5已将柱塞E推向左侧。
油脂通过主油道,E柱塞右中部空段及斜油道(11)进入油腔推动F柱塞向左移动(2) 柱塞移动受压油脂通过斜油道(12),E柱塞左中部空段从o油道流入出油孔,从10出油口排出。
步骤7:(1) 步骤6已将柱塞F推向左侧。
油脂通过主油道,F柱塞右中部空段及斜油道(13)进入油腔推动G柱塞向左移动(2) 柱塞移动受压油脂通过斜油道(14),F柱塞左中部空段从q油道流入出油孔,从12出油口排出。
(3) 到此完成分配器递进循环半个循环周期步骤8:(1) 步骤7结束已将分配器内部柱塞全部推至左侧,油脂从进油口进入通过主油道与(2)油道连通,受泵压油脂通过b油道进入油腔推动柱塞A向右移动(2) 柱塞移动受压油脂通过a油道与(1)油道连通,油脂通过G柱塞左中部空段从s油道流入出油孔,从14出油口排出。
旋转分配器

二、技术参数
序号
名称
1 阀体
2 阀体内件
3 密封副:
材料
材料
碳钢、不锈钢; 不锈钢; 堆焊合金/聚四氟乙烯
名称 设计压力 设计温度 工作温度 适用介质 进油口数量
电机功率 工作电压 防爆等级 防护等级 最大输出转矩 控制定位精度 每转行程时间 使用环境温度 电气接口
三、型5.0Mpa; -40-250℃ -10~180℃; 各种非腐蚀性流体 6~16 个
连接接方式,可根据工艺要求,选择法兰连接、对焊连接及快速接头连接。 兰连接型详见图一,对焊连接型详见图二。
图一 法兰连接型
图二 对焊连接型
2、工作原理 控制器给出控制信号,旋转分配器主轴做匀速圆周运动(正转或反转),并
带动转臂也做同步的匀速圆周运动。当阀芯上口与被选出口接通时,被选出口与 底部进口联通。流体通过底部进口,经过阀门内部,进入被选择的工艺管线。需 要切换管线时,控制系统发出信号,电动执行器电机启动,转动阀芯至下一要选 择的出口。
图一法兰连接型图二对焊连接型2工作原理控制器给出控制信号旋转分配器主轴做匀速圆周运动正转或反转并带动转臂也做同步的匀速圆周运动
旋转分配器
一、概述
数控旋转分配器,是气体、液体的分配阀门,应用与各种计量、化工工艺、锅 炉吹灰工艺等。按工艺要求,实现流通分配。可实现远程及现场的自动控制。
1、主要组成 旋转分配器主要由阀体部分、连接组件、电动执行器、控制箱组成。
控制
180-370W 三相四线 380AC 50HZ dⅡBT4 IP65 600-2000 N•m ≤±0.5o ≤90S -40 oC~+70 oC; 2xG1"(内)
旋转分配器选型如下:
TFPX旋转分配器说明书

一、适用范围及性能特点1、适用范围TFPX系列旋转分配器是一种输送设备,通常将物料按需要分配至不同的去路、贮仓,适用于饲料加工厂、粮食加工厂或立筒库工作塔等场所。
2、性能特点TFPX系列旋转分配器结构紧凑,操作简单,安装方便,导向接料弯管转动缓慢,借助行程开关和定位槽的作用使其准确定位,且密封性能好。
二、外形和主要技术参数1、外形TFPX系列旋转分配器的外形见图一。
2、主要技术参数见表1表1三、结构特征与工作原理1、主要结构(见图一)(1)机上体:由机上壳、操作门、弯管调心装置和吊钩等部分组成。
(2)导向接料弯管:上面装有弹簧压紧装置、清料刷、密封圈和滚动轴承。
(3)机下体:由机下壳、自封轴承、传动轴、转刷、内外导轨、出料接管及一个排灰接管等组成;导轨上有定位槽。
(4)调节箱:它由箱体、接线盒、三个操作门、行程开关和触杆等组成。
(5)减速电机:双级摆线针轮减速机。
2、工作原理(见图二)本机由减速电机传动轴带动导向接料弯管沿导轨运行。
根据需要起动电机;运行到位后,触杆作用行程开关,立即切断电源,导向接料弯管立即停止在固定的位置上,同时弯管和机下壳压紧密封。
四、安装与调试1、设备安装前应进行全面检查,转动必须灵活。
2、设备吊装或支撑后,应基本保持水平,安装地脚尺寸见图一,如吊装后可以将机架拆掉。
3、连接各管道时不应影响原来的安装位置,连接的输送管道应设置观察口。
4、本机的出料口若不完全利用则应用铁板封口,排灰口应接出管道、密封,定期打开上检修口清灰。
5、安装后必须试运转,检查导向接料弯管、定位槽、行程开关和触杆的运动位置是否协调,并作必要的调整。
五、使用与操作1、使用前必须空运转,使弯管的停止位置和转换开关位置及工艺流程线路中的讯号一致,并编上相同的号码。
2、当需要改变出口时,必须先停止进料,然后起动按钮,待导向弯管旋转至预定出料口、停稳后再进料。
3、当弯管运转不平稳时,可打开机上体的顶盖,调节弯管的转动中心,直至运转平稳。
TFPX旋转分配器说明书
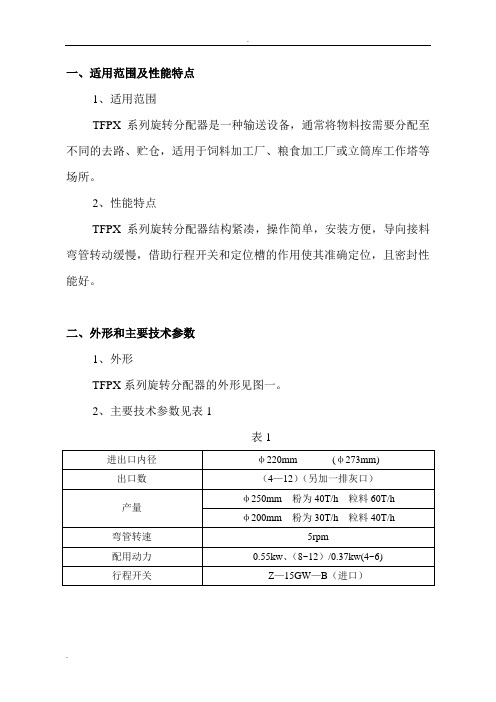
一、适用范围及性能特点1、适用范围TFPX系列旋转分配器是一种输送设备,通常将物料按需要分配至不同的去路、贮仓,适用于饲料加工厂、粮食加工厂或立筒库工作塔等场所。
2、性能特点TFPX系列旋转分配器结构紧凑,操作简单,安装方便,导向接料弯管转动缓慢,借助行程开关和定位槽的作用使其准确定位,且密封性能好。
二、外形和主要技术参数1、外形TFPX系列旋转分配器的外形见图一。
2、主要技术参数见表1表1三、结构特征与工作原理1、主要结构(见图一)(1)机上体:由机上壳、操作门、弯管调心装置和吊钩等部分组成。
(2)导向接料弯管:上面装有弹簧压紧装置、清料刷、密封圈和滚动轴承。
(3)机下体:由机下壳、自封轴承、传动轴、转刷、内外导轨、出料接管及一个排灰接管等组成;导轨上有定位槽。
(4)调节箱:它由箱体、接线盒、三个操作门、行程开关和触杆等组成。
(5)减速电机:双级摆线针轮减速机。
2、工作原理(见图二)本机由减速电机传动轴带动导向接料弯管沿导轨运行。
根据需要起动电机;运行到位后,触杆作用行程开关,立即切断电源,导向接料弯管立即停止在固定的位置上,同时弯管和机下壳压紧密封。
四、安装与调试1、设备安装前应进行全面检查,转动必须灵活。
2、设备吊装或支撑后,应基本保持水平,安装地脚尺寸见图一,如吊装后可以将机架拆掉。
3、连接各管道时不应影响原来的安装位置,连接的输送管道应设置观察口。
4、本机的出料口若不完全利用则应用铁板封口,排灰口应接出管道、密封,定期打开上检修口清灰。
5、安装后必须试运转,检查导向接料弯管、定位槽、行程开关和触杆的运动位置是否协调,并作必要的调整。
五、使用与操作1、使用前必须空运转,使弯管的停止位置和转换开关位置及工艺流程线路中的讯号一致,并编上相同的号码。
2、当需要改变出口时,必须先停止进料,然后起动按钮,待导向弯管旋转至预定出料口、停稳后再进料。
3、当弯管运转不平稳时,可打开机上体的顶盖,调节弯管的转动中心,直至运转平稳。
朴克自动炉工程公司流量分配器说明书
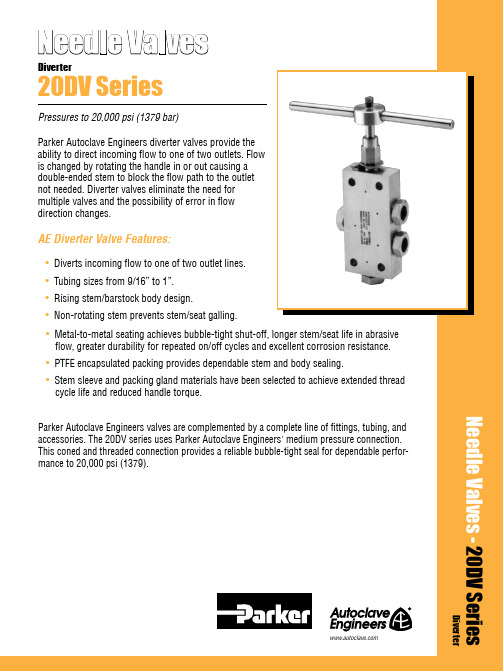
20DV SeriesPressures to 20,000 psi (1379 bar)To ensure proper fit use Parker Autoclave Engineers tubingGeneralized Flow Coefficient Curves (C v )% of rated C vN u m b e r o f t u r n s o p e n876543210Ordering Procedureyour Sales Representative. The 20DV Series valves are furnished complete with connection components, unless otherwise specified.9-9/16”12-3/4”16-1”07 - non-rotating Vee stem (on off service)7 - diverterFor extreme temperature and otheroptions, see Valve Options.Pattern TypeTube SizeSeriesAll general terms and conditions of sale, including limitations of our liability, apply to all products and services sold.2Tube Outside Pressure Diameter Orifice psi (bar) Size Connection Size Rated @ Room Inches Type Inches (mm) C v Temperature** 9/16 SF562CX 0.359 (9.12) 1.5 20,000 (1379) 3/4 SF750CX 0.516 (13.10) 2.9 20,000 (1379) 1 SF1000CX 0.562 (14.27) 4.5 20,000 (1379)Notes:** For complete temperature ratings see pressure/temperature ratingguide in Technical Information section.Valve OptionsValve MaintenanceExtreme TemperaturesStandard Parker Autoclave Engineers valves with PTFE packing may be operated to 450°F (232°C). High temperature packing and/or extended stuffing box is available for service from -423°F (-252°C) to 1200°F (649°C) by adding the following suffixes to catalog order number.HT extended stuffing box valve with graphite braided yarn packing to 1200°F (648°C).B standard valve with cryogenic trim materials and PTFE packing to -100°F (-73°C).LT extended stuffing box valve with PTFE packing and cryogenic trim materials to -423°F (-252°C).K anti-vibe collet gland assembly.Repair Kits: add “R” to the front of valve catalognumber for proper repair kit.(Example: R20DV16077)Valve Bodies: Valve bodies are available. Order using the eight (8) digit part number found on the valve drawing or contact your Sales Representative for information.Consult your Parker Autoclave Engineers representative for pricing on repair kits and valve bodies. Refer to the Tools, Installation, Operation and Mainte -nance section for proper maintenance procedures.G - Packing gland mounting hole drill size * H Dimension is with stem in closed position.For prompt service, ParkerG 1 - Bracket mounting hole sizeAll dimensions for reference only and subject to change. Autoclave Engineers stocks select Panel mounting drill size: 0.22” all valves. products. Consult factory.Block Catalog Stem Diameter Orifice Thick- Number Type Tube Diameter A B C D D 1 E F G G 1 H* M N nessDimensions - inches (mm)OutsideAll general terms and conditions of sale, including limitations of our liability, apply to all products and services sold.3ValvePattern02-0118SE January2013© 2013 Parker Hannifin Corporation | Autoclave Engineers is a registered trademark of the Parker Hannifin Corporation Parker Hannifin Manufacturing Ltd.Instrumentation Products Division, Europe Industrial Estate Whitemill Wexford, Republic of Ireland PH: 353 53 914 1566FAX: 353 53 914 1582Instrumentation Products Division Autoclave Engineers Operation 8325 Hessinger DriveErie, Pennsylvania 16509-4679 USA PH: 814-860-5700 FAX: WARNINGFAILURE, IMPROPER SELECTION OR IMPROPER USE OF THE PRODUCTS AND/OR SYSTEMS DESCRIBED HEREIN OR RELATED ITEMS CAN CAUSE DEATH, PERSONAL INJURY AND PROPERTY DAMAGE .This document and other information from Parker Hannifin Corporation, its subsidiaries and authorized distributors provide product and/or system options for further investiga tion by users having technical expertise. It is important that you analyze all aspects of your application and review the information concerning the product or system in the current product catalog. Due to the variety of operating conditions and applications for these products or systems, the user, through its own analysis and testing, is solely responsible for making the final selection of the products and systems and assuring that all performance, safety and warning requirements of the application are met. The products described herein, including without limitation, product features, specifications, designs, availability and pricing, are subject to change by Parker Hannifin Corporation and its subsidiaries at any time without notice.Offer of SaleThe items described in this document are available for sale by Parker Hannifin Corporation, its subsidiaries or its authorized distributors. Any sale contract entered by Parker will be governed by the provisions stated in Parker's standard terms and conditions of sale (copy available upon request).ISO-9001 CertifiedCaution! Do not mix or interchange parts or tubing with those of other manufacturers. Doing so is unsafe and will void warranty.Caution!Parker Autoclave Engineers Valves, Fittings and Tools are not designed to work with common commercial instrument tubing and will only work with tubing built to Parker Autoclave Engineers AES Specifications. Failure to do so will void warranty.。
- 1、下载文档前请自行甄别文档内容的完整性,平台不提供额外的编辑、内容补充、找答案等附加服务。
- 2、"仅部分预览"的文档,不可在线预览部分如存在完整性等问题,可反馈申请退款(可完整预览的文档不适用该条件!)。
- 3、如文档侵犯您的权益,请联系客服反馈,我们会尽快为您处理(人工客服工作时间:9:00-18:30)。
一、适用范围及性能特点
1、适用范围
TFPX系列旋转分配器是一种输送设备,通常将物料按需要分配至不同的去路、贮仓,适用于饲料加工厂、粮食加工厂或立筒库工作塔等场所。
2、性能特点
TFPX系列旋转分配器结构紧凑,操作简单,安装方便,导向接料弯管转动缓慢,借助行程开关和定位槽的作用使其准确定位,且密封性能好。
二、外形和主要技术参数
1、外形
TFPX系列旋转分配器的外形见图一。
2、主要技术参数见表1
表1
三、结构特征与工作原理
1、主要结构(见图一)
(1)机上体:由机上壳、操作门、弯管调心装置和吊钩等部分组成。
(2)导向接料弯管:上面装有弹簧压紧装置、清料刷、密封圈和滚动轴承。
(3)机下体:由机下壳、自封轴承、传动轴、转刷、内外导轨、出料接管及一个排灰接管等组成;导轨上有定位槽。
(4)调节箱:它由箱体、接线盒、三个操作门、行程开关和触杆等组成。
(5)减速电机:双级摆线针轮减速机。
2、工作原理(见图二)
本机由减速电机传动轴带动导向接料弯管沿导轨运行。
根据需要起动电机;运行到位后,触杆作用行程开关,立即切断电源,导向接料弯管立即停止在固定的位置上,同时弯管和机下壳压紧密封。
四、安装与调试
1、设备安装前应进行全面检查,转动必须灵活。
2、设备吊装或支撑后,应基本保持水平,安装地脚尺寸见图一,如吊装后可以将机架拆掉。
3、连接各管道时不应影响原来的安装位置,连接的输送管道应设置观察口。
4、本机的出料口若不完全利用则应用铁板封口,排灰口应接出管道、密封,定期打开上检修口清灰。
5、安装后必须试运转,检查导向接料弯管、定位槽、行程开关和触杆的运动位置是否协调,并作必要的调整。
五、使用与操作
1、使用前必须空运转,使弯管的停止位置和转换开关位置及工艺流程线路中的讯号一致,并编上相同的号码。
2、当需要改变出口时,必须先停止进料,然后起动按钮,待导向弯管旋转至预定出料口、停稳后再进料。
3、当弯管运转不平稳时,可打开机上体的顶盖,调节弯管的转动中心,直至运转平稳。
4、调节导向接料弯管上压紧弹簧的压力,可改变密封程度和减速电机负荷。
5、定期检查行程开关和导向接料弯管的工作状况,发现问题立即解决。
6、调节行程开关与触杆位置的位置,可改变导向接料弯管的停止位置点。
六、维护与保养
1、使用前应检查减速机内是否加注润滑脂,推荐使用特种润滑脂-2#、二硫化钼-2#或ZL-2锂基润滑脂,润滑脂的装入量为减速机容积的
1/3或1/2。
2、应定期检查各电器元器件、线路,保证发送讯号及时准确。
3、保持表面清洁,定期清理。
设备不得敲打碰撞等。
七、易损件
1、用户在使用本设备的过程中,零部件的正常磨损更换可到本公司订购,热情为您服务。
2、易损件(见表2)
说明:行程开关的数量n为旋转分配器出口的数量。
八、附图
1、图一:结构图
2、图二:电控原理图
第 5 页共9 页湖北三江航天机电设备有限公司
第 6 页共9 页湖北三江航天机电设备有限公司
合格证明书本机经检验合格准予出厂
编号
质量检验员
质检部
出厂日期
装箱单一、随机文件
二、随机附件
用户信息反馈单。