6063牌号挤压工艺 常见问题解决办法
铝合金挤压型材强度影响因素及措施分析

铝合金挤压型材强度影响因素及措施分析6063铝合金型材是门窗、幕墙理想的结构和装饰材料,随着门窗、幕墙行业的发展,对6063铝合金型材的力学性能提出了更高的要求。
高强度的型材可减低设计壁厚,减少结构重量,更受市场欢迎。
6063铝合金系AI—Mg—Si系列可热处理强化型铝合金,塑性高,可高速挤压成断面复杂、壁厚各异的型材。
淬火温度宽,淬火敏感性低.可实现在线风冷强制淬火,经人工时效后有中等强度。
挤压后型材表面光洁,极易阳极氧化和着色,还可生产电泳、喷涂、氟碳喷漆、木纹、断桥隔热等型材,因此在建筑型材中具有垄断地位,在我国经济的快速发展,尤其是房地产市场的高速发展中得到极广泛的应用。
在Al-Mg-Si系合金中,主要强化相是Mg2Si,合金在淬火时,固溶于基体中的Mg2Si 越多,时效后的型材强度就越高,反之,则越低。
在实际生产中,铝合金挤压型材经常出现硬度偏低或不达标的现象出现。
影响型材硬度强度的原因是多方面的(见鱼骨图),下面结合我厂的生产实际,从工艺、设备、操作等方面分析和总结影响6063铝合金型材强度的因素及采取的措施。
1、6063铝合金化学成分的控制国家标准GB/T 3190-2008和“和平”公司内控标准对6063铝合金的化学成分规定如表l所示。
表1 6063铝合金化学成分(质量分数%)该合金主要元素足Mg和Si。
他们在合金中形成金属化合物Mg:Si是合会的主要强化相。
Mg2Si中Mg和Si的比为1.73。
当Mg:Si>1.73时,尚有过剩的Mg存在,它会显著降低Mg2Si相在固态铝中的溶解度,由于过剩Mg的这种影响,使Mg2Si相在热处理时的强化效果显著降低,从而影响型材的力学性能。
合金中Si含量的增加可以改善铸造性能和焊接性能。
当Mg:Si<1.73时,合金中有过剩Si存在,它可以与铝中的其它杂质Fe、Mn等生成化合物,增加强化效果。
因此对强度要求较高时,往往合金中控制过剩Si。
6063铝棒挤压工艺
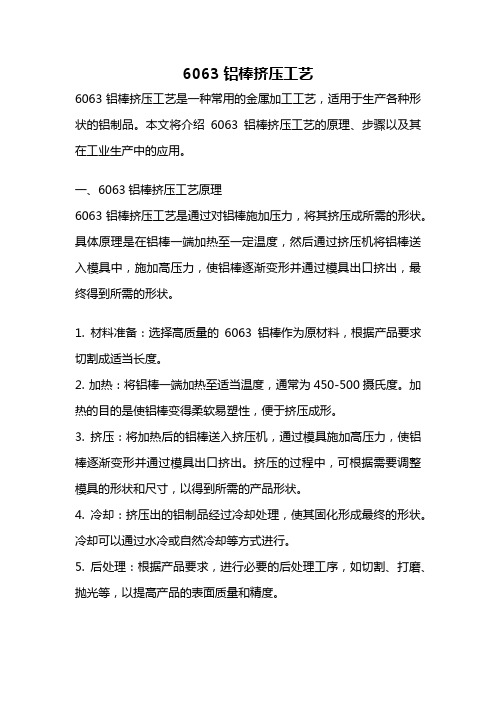
6063铝棒挤压工艺6063铝棒挤压工艺是一种常用的金属加工工艺,适用于生产各种形状的铝制品。
本文将介绍6063铝棒挤压工艺的原理、步骤以及其在工业生产中的应用。
一、6063铝棒挤压工艺原理6063铝棒挤压工艺是通过对铝棒施加压力,将其挤压成所需的形状。
具体原理是在铝棒一端加热至一定温度,然后通过挤压机将铝棒送入模具中,施加高压力,使铝棒逐渐变形并通过模具出口挤出,最终得到所需的形状。
1. 材料准备:选择高质量的6063铝棒作为原材料,根据产品要求切割成适当长度。
2. 加热:将铝棒一端加热至适当温度,通常为450-500摄氏度。
加热的目的是使铝棒变得柔软易塑性,便于挤压成形。
3. 挤压:将加热后的铝棒送入挤压机,通过模具施加高压力,使铝棒逐渐变形并通过模具出口挤出。
挤压的过程中,可根据需要调整模具的形状和尺寸,以得到所需的产品形状。
4. 冷却:挤压出的铝制品经过冷却处理,使其固化形成最终的形状。
冷却可以通过水冷或自然冷却等方式进行。
5. 后处理:根据产品要求,进行必要的后处理工序,如切割、打磨、抛光等,以提高产品的表面质量和精度。
三、6063铝棒挤压工艺的应用6063铝棒挤压工艺广泛应用于工业生产中,主要用于生产各种形状的铝制品,如铝型材、铝合金门窗、铝管、铝棚架等。
由于6063铝合金具有良好的耐腐蚀性、可塑性和机械性能,且重量轻、易加工,因此在建筑、航空航天、汽车、电子等领域得到广泛应用。
6063铝棒挤压工艺具有以下优点:1. 可生产各种复杂形状的铝制品,灵活性高。
2. 生产效率高,可以进行大批量生产。
3. 产品表面质量好,尺寸精度高。
4. 节约材料,减少废料产生。
5. 环保,无污染。
然而,6063铝棒挤压工艺也存在一些局限性:1. 产品长度有限,一般在6-12米之间。
2. 对模具的精度要求较高,制造成本较高。
3. 对材料的要求较高,需要选择优质的6063铝棒。
总结:6063铝棒挤压工艺是一种常用的金属加工工艺,通过对铝棒施加压力,将其挤压成所需的形状。
6063铝合金型材挤压工艺对型材表面质量的影响论文

降低、 不均匀, 在金属通过模孔时产生的摩擦力较大, 金属之间产生严重的流速不均, 也会造成表面挤压条
纹和表面粗糙严重。只要把模具的加热温度降低, 加
3 表面质量缺陷的产生原因
31 铝合金型材表面夹渣、 . 划痕的产生原因 一般认为型材表面夹渣及划痕是铸锭夹渣或夹 灰所造成的, 而实际生产过程中, 夹渣和划痕的产生
K w r . 5 1 G D cn rrpl cdr e o s D S03 A ; v t; e e y d C 0 ; o ee u o s
1 前
言
与挤压工艺控制不严有关。挤压时, 必须严格控制铸 锭表面洁净。如果铸锭表面带有一些废的铝屑或杂 质清理不净, 在高温挤压时这些杂质浮在型材表面或 挂在模具工作带上, 必将造成型材表面夹渣或划痕。 正常挤压时, 每天应采用专用清理垫, 把挤压筒内壁 的一些杂质清理干净, 以防止这些杂质卷人模孔中, 挂在模具的工作带上或浮在型材表面上, 造成型材表 面的划痕和夹渣。再者, 挤压铸锭的压余控制, 压余 过小, 一部分残余的氧化皮及杂质会流人模孔中, 在 连续挤压时也会使型材表面划伤或造成夹渣。严重
量查起。有些表面质量问题是能够解决的, 但有些表 面质量问题单从铸锭和模具去查找原因是解决不了 的, 因为影响型材表面质量的重要因素之一与型材的 挤压工艺有着直接关系。根据我公 司几年来的挤压 生产经验, 从挤压工艺方面进行分析并找出影响型材 表面质量的原因效果显著。下面简要论述挤压工艺 对型材表面质量的影响。
(en Dn a im .L .Tn h , i , 1 , a Bjg g A m u C ,t ,o zu Big 1 1 Ci ) i oy l n o d i u g o en 0 3 h j 1 n
6063挤压型材条纹缺陷产生原因分析及解决措施
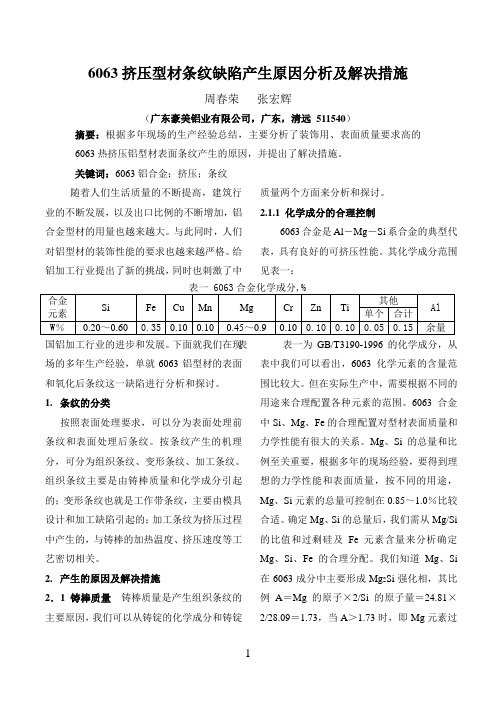
6063挤压型材条纹缺陷产生原因分析及解决措施周春荣张宏辉(广东豪美铝业有限公司,广东,清远511540)摘要:根据多年现场的生产经验总结,主要分析了装饰用、表面质量要求高的6063热挤压铝型材表面条纹产生的原因,并提出了解决措施。
关键词:6063铝合金;挤压;条纹随着人们生活质量的不断提高,建筑行业的不断发展,以及出口比例的不断增加,铝合金型材的用量也越来越大。
与此同时,人们对铝型材的装饰性能的要求也越来越严格。
给铝加工行业提出了新的挑战,同时也刺激了中国铝加工行业的进步和发展。
下面就我们在现场的多年生产经验,单就6063铝型材的表面和氧化后条纹这一缺陷进行分析和探讨。
1.条纹的分类按照表面处理要求,可以分为表面处理前条纹和表面处理后条纹。
按条纹产生的机理分,可分为组织条纹、变形条纹、加工条纹。
组织条纹主要是由铸棒质量和化学成分引起的;变形条纹也就是工作带条纹,主要由模具设计和加工缺陷引起的;加工条纹为挤压过程中产生的,与铸棒的加热温度、挤压速度等工艺密切相关。
2.产生的原因及解决措施2.1 铸棒质量铸棒质量是产生组织条纹的主要原因,我们可以从铸锭的化学成分和铸锭质量两个方面来分析和探讨。
2.1.1 化学成分的合理控制6063合金是Al-Mg-Si系合金的典型代表,具有良好的可挤压性能。
其化学成分范围见表一:表表一为GB/T3190-1996的化学成分,从表中我们可以看出,6063化学元素的含量范围比较大。
但在实际生产中,需要根据不同的用途来合理配置各种元素的范围。
6063合金中Si、Mg、Fe的合理配置对型材表面质量和力学性能有很大的关系。
Mg、Si的总量和比例至关重要,根据多年的现场经验,要得到理想的力学性能和表面质量,按不同的用途,Mg、Si元素的总量可控制在0.85~1.0%比较合适。
确定Mg、Si的总量后,我们需从Mg/Si的比值和过剩硅及Fe元素含量来分析确定Mg、Si、Fe的合理分配。
如何减轻6063铝合金挤压型材的表面条纹

如何减轻铝合金挤压型材的表面条纹易贤志(长沙振升铝材有限公司,湖南长沙$%"&’!)!"!#摘要:从熔铸工艺、挤压工艺、模具、挤压设备等方面分析了!"!#铝合金型材在挤压过程中产生表面条纹的原因,并提出了相应的对策。
关键词:!"!$铝合金型材;熔铸;挤压;模具;表面条纹中图分类号:%&"’(!)*+;%&$,-文献标识码:.文章编号:+/",0,*$(1*//$)/20""310"$()*+),-./-01-+2- 34/50.- 3+/-061)5!"!7894:;<;4:899)= >/)5;9-14567890:;7@20<A120 B2-<12-<A894:;<;4:@)C D E+F C D@20<A120$%G%’!D@2;<0H8I1+/0.+J%;<=8>?@AB79>C DE79F@= G<C?79F0>8B?79F H A@><BB I<J?A D B7@9H A@><BB I E7<I89E <J?A D B7@9E<K7>< A<B D C?79F79?;<B D A=8><B?A<8L B@= !/!$8C D G797D G8CC@M H A@=7C<B N<A<898C M:<E)%;<H A<>8D?7@98AM G<8B D A<B N<A<HD?=@A N8A E)K-=*)/F1J!O!$8C D G797D G8CC@M H A@=7C<P G<C?79F0>8B?79F P<J?A D B7@9P E7<P B D A=8><B?A<8L本文所说的挤压铝型材表面条纹是指型材表面上的焊合线、亮线、模线、氧化物条痕、组织条纹、咬痕、阴阳面等,从理论和实践上证明,挤压铝型材的有些表面条纹是不可能根本消除的。
6063铝合金挤压型材觉缺陷及其解决方法

6063铝合金挤压型材觉缺陷及其解决方法
1.毛刺:毛刺是挤压型材表面的突出物,会影响外观和触感。
毛刺的
主要原因是金属挤压时的不均匀变形和模具壁口的磨损。
解决方法包括增
加材料的充填比例,优化挤压工艺参数,增加模具壁口的滑移润滑剂等。
2.断裂:断裂是挤压型材在生产和使用过程中出现的一个严重问题。
断裂的原因可以是材料本身的强度不足、挤压工艺参数设置不当、模具设
计不合理等。
解决方法包括选择合适的6063铝合金型材,优化挤压工艺
参数,加强模具的冷却和加热控制等。
3.冷裂纹:冷裂纹是在挤压型材的表面或内部出现的长而细的裂纹。
冷裂纹的出现与材料的热处理过程和冷却速度不当有关。
解决方法包括优
化挤压工艺参数,控制冷却速度,合理设计材料的热处理过程等。
4.物理性能不稳定:6063铝合金挤压型材的物理性能,如硬度、抗
拉强度、延展性等,可能存在不稳定的情况。
这可能是由于挤压工艺中的
应力集中和不均匀变形导致的。
解决方法包括优化挤压工艺参数,增加冷
却控制,合理设计模具结构等。
5.起皮:起皮是指挤压型材表面出现的局部脱层现象,降低了型材的
使用寿命。
起皮的原因主要是模具的磨损和使用不当。
解决方法包括定期
检查和维护模具,增加模具的使用寿命,减少起皮现象的发生。
总之,6063铝合金挤压型材的觉缺陷可能会影响其质量和使用寿命。
通过合理选择材料、优化挤压工艺参数、改进模具设计和加强质量控制等
措施,可以有效地解决这些问题,提高挤压型材的质量和性能。
6063铝合金型材氧化过程中出现“白斑”的原因分析及解决

6063铝合金型材氧化过程中出现“白斑”的原因分析及解决1 关于白斑在实际生产中,加工率大(ε> 95 %) ,壁厚较薄(δ≤115 mm) 的T5 状态的6063 铝合金挤压型材在经硫酸阳极氧化处理后,其表面会呈现有规律(而有时无规律) 分布的白色斑点(或无光斑痕) ;严重时呈现深色斑痕———“白斑”。
“白斑”的分布规律及特征是:它是在平行于挤压方向的平面上大致等间距的、呈线状或扁四边形状或不规则星点(片) 状的、相对于基体表面有微小深度而呈凹槽形的一种表面缺陷[5 ,6 ] 。
白斑通常分布于型材的一个或几个表面,有时会分布在型材的所有表面(对薄壁空心型材,则是分布于某一平面或曲面的内外两侧) 。
2 原因分析从金属材料腐蚀的观点看来,白斑这种表面缺陷实质上是6063 铝合金材料发生“剥落腐蚀”的结果。
剥落腐蚀是一种浅表面的选择腐蚀,腐蚀是沿着金属表面发展的,其产物的体积往往比发生腐蚀的金属大得多,因而膨胀。
一般而言,当铝与呈阴极性的异种金属相邻接时, “剥落腐蚀”程度上升。
在电子显微镜下观察发现:“剥落腐蚀”通常沿不溶组成物(如Si , Mg2Si 等) ,或沿晶界进行.2.1 铸锭质量的影响6063 铝合金的主要相组成是:α(Al) 固溶体、游离Si (阳极相) 和FeAl3 (阳极相) ;当铁含量大于时,有β(FeSiAl) (阳极相) ;而当铁含量小于时,有α(FeSiAl) (阴极相) ;其他可能的杂质相是:MgZn2 、CuAl2 等。
生产中,由于非平衡结晶过程而获得的6063 铝合金铸锭往往存在宏观偏析或晶内偏析现象。
因此,铸锭中的Si 、Mg、Zn、Cu 等元素分布不均匀。
而一些铝型材加工企业缘于经济方面的因素,一般很少对小规格(如Φ100 mm 以下) 的铸锭进行均匀化退火处理,以消除偏析现象[2 ] ,从而为“白斑”的产生创造了条件。
2.2 挤压—热处理工艺的影响为提高生产效率,在生产操作中,常采用低温高速挤压,由于挤压速度引起的“热效应”使制品在模具出口处的淬火温度大大提高,而在固定出料台上与表面温度为80~110 ℃(或略低) 的石墨板(或轮) 接触时,型材表面就会因受到“急冷换热”作用而使该部分的合金元素Mg、Si 的浓度比正常部位的偏高一些。
6063铝合金型材表面麻点的成因及解决方法

收稿日期:2006-08-03 作者简介:杜新宇(1968-),男,河南南阳人,工程师。
6063铝合金型材表面麻点的成因及解决方法杜新宇(南阳市康远机器总厂,河南南阳473125)摘要:通过生产实践与试验分析,找出6063铝合金型材产生麻点缺陷的各种原因,提出了避免和减轻这一缺陷的方法。
关键词:6063铝合金;型材;麻点;挤压工艺;铸锭;挤压工具中图分类号:TG 379 文献标识码:A 文章编号:1007-7235(2006)12-0032-03Countermeasures and causes of point defects on 6063aluminiumalloy profile surfacesDU X in 2yu(N anyang K angyu an Machine Work ,N anyang 473125,China)Abstract :Through practice and test analysis ,the author of the paper has found out the various reas ons for the formation of the vice of rough points in the production of 6063aluminum alloy.Then he has suggested methods for av oiding or abating such a vice.K ey w ords :6063aluminum alloy ;profile ;rough point ;extrusion process ;ing ot ;extrusion implement 在6063合金挤压生产中,型材表面常出现麻点现象。
麻点的形状像彗星轨迹,好像缝衣针的针尖在型材表面剜挑的犁痕。
麻点头部小、尾部大,严重时用手摸可感觉麻点尾部有硬质点。
6063铝合金型材“闪烁花纹”的成因及对策

6063铝合金型材“闪烁花纹”的成因及对策1前言在6063铝合金建筑装饰型材的生产中,常会见到一些空心、半空心的,甚至是一些断面曲率较大的实心的挤压材,经过硫酸阳极氧化生产工艺处理后,其表面局部会出现一种沿纵向连续分布的,具有一定宽度的显示为粗糙不平(似梨皮状)的,清晰可见的闪烁晶粒状的表面缺陷—“闪烁花纹”(或称“光亮花样”)。
其分布规律是:①沿挤压方向,尾部比头部更明显可见,严重时,首尾都很明显;②沿垂直于挤压轴线的方向,“花纹”一般只出现在局部,尤其出现在型材曲率较大的部位,或是空心、半空心型材的焊缝区域,或是在型材的形成过程中6063铝合金承受摩擦阻力最大的部位。
2成因分析2.1氧化前处理工艺的影响某些挤压材经硫酸脱脂并水洗后,表面无异常变化,而当其在w Zn2+≥4×10-6的碱蚀液中经正常的浸蚀并随后立即有效水洗后,就会看到“闪烁花纹”的存在。
笔者对挤压材的挤压组织进行分析,结果表明:“闪烁花纹”对应的组织是晶粒度比正常部位的大得多的粗大等轴晶的再结晶组织——粗晶环,且晶粒越粗大,“闪烁花纹”越明显;这种现象也随着浸蚀的进行而越来越明显。
文献[1]指出:“闪烁花纹”的形成除了与合金成分(尤其是Zn)、挤压材(RCS状态)的组织状态有关外,还与碱蚀液中[Zn2+]有关。
实验证明:在合金中,当w Zn≥0.033%,且型材表面存在粗晶环的前提下,只要碱蚀液中w Zn2+≥4×10-6,就会产生“闪烁花纹”。
产生“闪烁花纹”的根本原因是碱蚀液中Zn污染引起的选择性晶间腐蚀[2]。
晶间腐蚀的机理是电化学的,是晶界内的局部原电池作用的结果。
沿晶粒边缘沉淀析出的第二相Mg2Si与贫乏的固溶体之间由于腐蚀电位的不同,在碱蚀电解质溶液中,形成了原电池α-Al-Mg2Si。
在实际生产中,一般都要求Si的含量过剩,则其晶间腐蚀敏感性增大,因为位于晶界及其附近区域的游离硅具有很强的阳极性[3]。
AL6063铝型材挤压变形机理研究及工艺参数优化
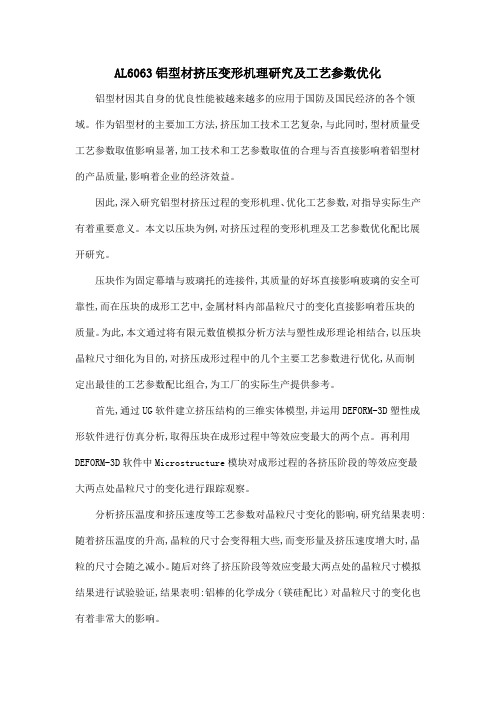
AL6063铝型材挤压变形机理研究及工艺参数优化铝型材因其自身的优良性能被越来越多的应用于国防及国民经济的各个领域。
作为铝型材的主要加工方法,挤压加工技术工艺复杂,与此同时,型材质量受工艺参数取值影响显著,加工技术和工艺参数取值的合理与否直接影响着铝型材的产品质量,影响着企业的经济效益。
因此,深入研究铝型材挤压过程的变形机理、优化工艺参数,对指导实际生产有着重要意义。
本文以压块为例,对挤压过程的变形机理及工艺参数优化配比展开研究。
压块作为固定幕墙与玻璃托的连接件,其质量的好坏直接影响玻璃的安全可靠性,而在压块的成形工艺中,金属材料内部晶粒尺寸的变化直接影响着压块的质量。
为此,本文通过将有限元数值模拟分析方法与塑性成形理论相结合,以压块晶粒尺寸细化为目的,对挤压成形过程中的几个主要工艺参数进行优化,从而制定出最佳的工艺参数配比组合,为工厂的实际生产提供参考。
首先,通过UG软件建立挤压结构的三维实体模型,并运用DEFORM-3D塑性成形软件进行仿真分析,取得压块在成形过程中等效应变最大的两个点。
再利用DEFORM-3D软件中Microstructure模块对成形过程的各挤压阶段的等效应变最大两点处晶粒尺寸的变化进行跟踪观察。
分析挤压温度和挤压速度等工艺参数对晶粒尺寸变化的影响,研究结果表明:随着挤压温度的升高,晶粒的尺寸会变得粗大些,而变形量及挤压速度增大时,晶粒的尺寸会随之减小。
随后对终了挤压阶段等效应变最大两点处的晶粒尺寸模拟结果进行试验验证,结果表明:铝棒的化学成分(镁硅配比)对晶粒尺寸的变化也有着非常大的影响。
然后,依据各工艺参数对晶粒尺寸变化的模拟结果,结合实际生产情况,采用正交试验方法对成形过程中影响压块晶粒尺寸变化的主要工艺参数进行优化。
选取铝棒的化学成分(镁硅配比)、挤压温度、挤压速度、挤压筒温、模具预热温度作为试验因素,设计了五因素四水平正交实验表L<sub>16</sub>(4<sup>5</sup>),通过对试验结果进行极差分析和方差分析,得出工艺参数对晶粒尺寸变化影响的主次顺序,并获得最优配比组合。
6063铝合金常见问题分析和处理

6063鋁合金常見問題分析及處理6063鋁合金型材以其良好的塑性、適中的熱處理強度、良好的焊接性能以及陽極氧化處理後表面華麗的色澤等諸多優點而被廣泛應用。
但在生產過程中經常會出現一些缺陷如:1 劃、擦、碰傷劃傷、擦傷、碰傷是當型材從模孔流出以及在隨後工序中與工具、設備等相接觸時導致的表面損傷。
1.1 主要原因鑄錠表面附著有雜物或鑄錠成分偏析。
鑄錠表面存在大量偏析浮出物而鑄錠又未進行均勻化處理或均勻化處理效果不好時,鑄錠內存在一定數量的堅硬的金屬顆粒,在擠壓過程中金屬流經工作帶時,這些偏析浮出物或堅硬的金屬顆粒附著在工作帶表面或對工作帶造成損傷,最終對型材表面造成劃傷;模具型腔或工作帶上有雜物,模具工作帶硬度較低,使工作帶表面在擠壓時受傷而劃傷型材;出料軌道或擺床上有裸露的金屬或石墨條內有較硬的夾雜物,當其與型材接觸時對型材表面造成劃傷;在叉料桿將型材從出料軌道上送到擺床上時,由於速度過快造成型材碰傷;在擺床上人為拖動型材造成擦傷;在運輸過程中型材之間相互摩擦或擠壓造成損傷。
1.2 解決辦法加強對鑄錠質量的控制;提高修模質量,模具定期氮化並嚴格執行氮化工藝;用軟質毛氈將型材與輔具隔離,盡量減少型材與輔具的接觸損傷;生產中要輕拿輕放,盡量避免隨意拖動或翻動型材;在料框中合理擺放型材,盡量避免相互摩擦。
2 機械性能不合格2.1 主要原因擠壓時溫度過低,擠壓速度太慢,型材在擠壓機的出口溫度達不到固溶溫度,起不到固溶強化作用;型材出口處風機少,風量不夠,導致冷卻速度慢,不能使型材在最短的時間內降到200℃以下,使粗大的Mg2Si過早析出,從而使固溶相減少,影響了型材熱處理後的機械性能;鑄錠成分不合格,鑄錠中的Mg、Si含量達不到標準要求;鑄錠未均勻化處理,使鑄錠組織中析出的Mg2Si相無法在擠壓的較短時間內重新固溶,造成固溶不充分而影響了產品性能;時效工藝不當、熱風循環不暢或熱電偶安裝位置不正確,導致時效不充分或過時效。
6xxx厚板粗晶层解决办法

6063挤压厚板粗晶环的研究及应用发布者:发布时间:2012/6/11 22:45:10 阅读:12次6XXX系合金的主要合金元素是镁和硅,组织也相当简单,主要组织组成物为Mg2Si相,在热处理状态下,Mg2Si固溶于铝中,使得合金有人工时效强化能力。
6063属Al-Mg-Si系铝合金中对应力腐蚀不敏感的合金,具有中等强度、优良的挤压性能、良好的耐蚀性、可焊性及良好的加工性能,因而得以广泛应用[1]。
随着科学技术的发展及应用市场的拓宽,有的客户对制品的要求越来越高,对晶粒度也提出了要求。
很多的铝合金挤压制品经热处理(淬火、退火)后,在制品的周边形成一层很深的粗大的再结晶晶粒环,且粗晶区和细晶区有着明显的界限,而且粗晶环的深度从挤压制品的前端到尾端是增加的。
粗晶环是铝合金挤压制品中的主要缺陷之一,当断面形成相当大部分的粗晶环区域时,材料的力学性能、疲劳强度显著降低。
而在对制品进行一些表面处理(氧化银白等)时,制品表面会出现线纹和花斑,影响装饰效果。
而6063铝合金在生产较厚的板材时,极易出现粗晶环。
本文将研究减少和控制6063铝合金在挤压厚板出现粗晶环的方法。
1.试验1.1试验材料选择40MN的正向挤压机,Φ305 mm×1000 mm规格的6063铝合金铸锭。
其化学成分见表1。
表1 6063铝合金化学成分(质量分数,下同)%批号Cu Fe Si Mg Mn Cr Zn Ti Al 国标0.10 0.35 0.20~0.6 0.45~0.90 0.10 0.10 0.10 0.10 余量试验≤0.03 ≤0.25 0.32~0.38 0.55~0.70 ≤0.04 ≤0.04 ≤0.03 ≤0.06 余量1.2试验目标粗晶环深度小于或等于1mm,晶粒度小于或等于三级,抗拉强度δb≥205Mpa,屈服强度δ0.2≥180Mpa,延伸率大于或等于8%。
1.3试验内容(1)熔铸圆铸锭对6063铝合金挤压厚板在线淬火状态下制品晶粒度的影响,采用均质和不均质两种不同热处理方式的圆铸锭来试验。
6063型铝材常见不足及改善

6063型铝材常见不足之处6063铝合金型材以其良好的塑性、适中的热处理强度、良好的焊接性能以及阳极氧化处理后表面华丽的色泽等诸多优点而被广泛应用。
但在生产过程中经常会出现一些缺陷而致使产品质量低下,成品率降低,生产成本增加,效益下降,最终导致企业的市场竞争能力下降。
因此,从根源上着手解决6063铝合金挤压型材的缺陷问题是企业提高自身竞争力的一个重要方面。
笔者根据多年的铝型材生产实践,在此对6063铝合金挤压型材常见缺陷及其解决办法作一总结,和众多同行交流,以期相互促进。
1 划、擦、碰伤划伤、擦伤、碰伤是当型材从模孔流出以及在随后工序中与工具、设备等相接触时导致的表面损伤。
1.1 主要原因①铸锭表面附着有杂物或铸锭成分偏析。
铸锭表面存在大量偏析浮出物而铸锭又未进行均匀化处理或均匀化处理效果不好时,铸锭内存在一定数量的坚硬的金属颗粒,在挤压过程中金属流经工作带时,这些偏析浮出物或坚硬的金属颗粒附着在工作带表面或对工作带造成损伤,最终对型材表面造成划伤;②模具型腔或工作带上有杂物,模具工作带硬度较低,使工作带表面在挤压时受伤而划伤型材;③出料轨道或摆床上有裸露的金属或石墨条内有较硬的夹杂物,当其与型材接触时对型材表面造成划伤;④在叉料杆将型材从出料轨道上送到摆床上时,由于速度过快造成型材碰伤;⑤在摆床上人为拖动型材造成擦伤;⑥在运输过程中型材之间相互摩擦或挤压造成损伤。
1.2 解决办法①加强对铸锭质量的控制;②提高修模质量,模具定期氮化并严格执行氮化工艺;③用软质毛毡将型材与辅具隔离,尽量减少型材与辅具的接触损伤;④生产中要轻拿轻放,尽量避免随意拖动或翻动型材;⑤在料框中合理摆放型材,尽量避免相互摩擦。
2机械性能不合格2.1 主要原因①挤压时温度过低,挤压速度太慢,型材在挤压机的出口温度达不到固溶温度,起不到固溶强化作用;②型材出口处风机少,风量不够,导致冷却速度慢,不能使型材在最短的时间内降到200℃以下,使粗大的Mg2Si过早析出,从而使固溶相减少,影响了型材热处理后的机械性能;③铸锭成分不合格,铸锭中的Mg、Si含量达不到标准要求;④铸锭未均匀化处理,使铸锭组织中析出的Mg2Si相无法在挤压的较短时间内重新固溶,造成固溶不充分而影响了产品性能;⑤时效工艺不当、热风循环不畅或热电偶安装位置不正确,导致时效不充分或过时效。
6063铝合金挤压型材质量影响因素及解决方法.ashx

容易在晶界上形成低熔点的三元共晶体,热脆性更 大。而当 2 3 ") *时,则产生熔点较高的包晶反应, 提高了脆性区的温度下限,能显著降低热裂倾向。 因此,应当首先控制好镁、硅、铁三元素的含 量及 相 互 关 系,既 保 证 合 金 中 能 够 形 成 足 够 的 ’ ) *强化相,又保证有一定量的硅过剩,且过剩 ( < 硅的含量要小于合金中铁的含量,合金中的铁的含 量还不能影响到氧化着色的质量。这样使得铸锭 既有一定强度,又降低了产生裂纹的倾向,同时, 提高氧化着色质量。 其他杂质元素虽然对铝型材性能的影响相对小 一些,但也不可忽视。综合考虑, ! " ! # 合金比较 理想的 化 学 成 分 为 (> :’ :" ; ? 1) 9 @ :!" 9 : : ( : ;’ / ;2 : ) * " 9 # : ! " 9 @ : ) * A . 9 # ! . 9 @ 3 " 9 ( ; ; ; ; . : !" 9 < " 8 6 #" 9 . " * #" 9 . " 4 5 #" 9 . " ;4 。 ’ 6 # " 9 . " 7 # " 9 . " 按照这个化学成分,’ B) * $" 9 ; " 1,且过 ( 剩的硅量小于铁含量,铁、锌、铜、钛、锰、铬的 含量也较低,对氧化膜的质量影响不大。既可以保 证熔体有良好的铸造性能及铸锭 的挤压性能,又 可以保证型材良好的力学性能和氧化膜质量及表面 质量,避免合金元素的浪费。 为确保合金中的杂质含量在控制的范围之内, 还应对熔炼原料的熔炼操作过程进行严格控制。杂 质元素主要来源于原料,特别是与原铝锭搭配使用 的废料中一般杂质元素含量较高,配料时应注意原 铝锭和废料的使用比例。一般采用重熔用铝锭,不 用或少用废铝,可以适量搭配 ! " ! # 铝合金废料。 另外,对熔炼炉的清炉、洗炉也很重要,这样有助 于清除炉内残留的杂质。熔炼过程中的操作有可能 增加铁的含量,应注意在操作工具表面涂覆隔离、 保护层。
6063铝合金挤压型材强度影响因素及措施分析.ashx_图文.

《铝加-r 2009年第5期总第190期技术工程6063铝合金挤压型材强度影响因素及措施分析陈新孟(贵州铝厂生产处,贵州贵阳550058摘要:从6063铝合会化学成分控制.均匀化退火、挤压系数选择、铝棒加热温度、淬火温度和速度、拉伸变形量控制、时效工艺选择等方面,结合本厂生产实际。
分析了影响6063铝合舍型材强度的冈素及生产中采取的措施。
关键词:6063铝合金;强度;均匀化退火;挤压系数;风冷淬火;拉伸;人工时效中图分类号:TG37。
TGl66.3文献标识码:B 文章编号:1005-4898(2009J 05—0049—036063铝合金属低合金化的AI—Mg—Si系列可热处理强化型铝合金.塑性高,可高速挤压成断面复杂。
壁厚各异的型材。
淬火温度宽,淬火敏感性低.可实现在线风冷强制淬火,经人工时效后有中等强度.挤压后型材表面光洁.极易阳极氧化和着色。
还可生产电泳、喷涂、木纹、断桥隔热等型材.因此在建筑型材中具有垄断地位。
在我国经济的快速发展。
尤其是房地产市场的高速发展中得到极广泛的应用。
在其它用途上。
由于6063型材比钢结构轻, 室温下具有中等强度和高的冲击韧性,适于制作常用结构件以承受一定的载荷11I。
加上6063型材具有良好的耐腐蚀性能和易实现的多姿多彩的表面处理,在家朋电器、灯箱、车船工业、隔断、仪器仪表等方面也得到广泛应用。
在AI—Mg—Si组成的三元系合金中,没有i元化合物,只有二元化合物MgzSi 和M92A13,在Al— Mg—si系合金中。
主要强化相是M92Si,合金在淬火时。
固溶于基体中的MgzSi越多。
时效后的型材强度就越高,反之,则越低。
从近年6063铝合金型材国家标准的变化和市场的各种要求看,型材的强度指标有提高的趋势。
而在实际生产中,各家的6063铝合金挤压型材均有强度偏低或不达标的现象出现。
我厂的6063铝合金型材生产线建成投产已多年。
其问装备和T 艺均有局部改变、调整和提高。
6063铝合金型材氧化缺陷原因分析及解决
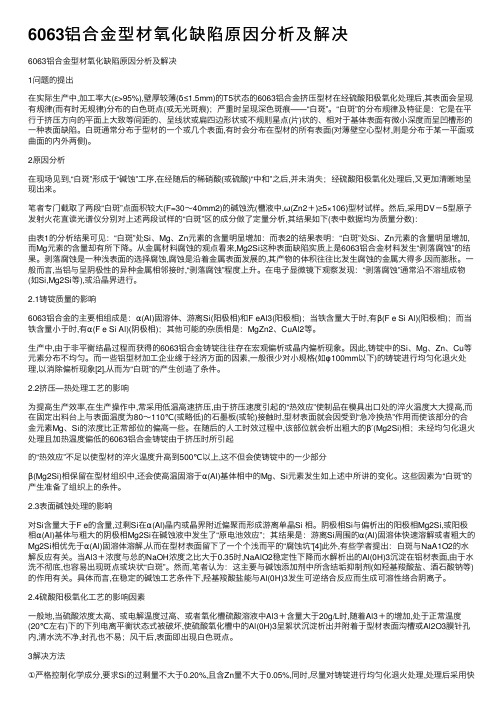
6063铝合⾦型材氧化缺陷原因分析及解决6063铝合⾦型材氧化缺陷原因分析及解决1问题的提出在实际⽣产中,加⼯率⼤(ε>95%),壁厚较薄(δ≤1.5mm)的T5状态的6063铝合⾦挤压型材在经硫酸阳极氧化处理后,其表⾯会呈现有规律(⽽有时⽆规律)分布的⽩⾊斑点(或⽆光斑痕);严重时呈现深⾊斑痕——“⽩斑”。
“⽩斑”的分布规律及特征是:它是在平⾏于挤压⽅向的平⾯上⼤致等间距的、呈线状或扁四边形状或不规则星点(⽚)状的、相对于基体表⾯有微⼩深度⽽呈凹槽形的⼀种表⾯缺陷。
⽩斑通常分布于型材的⼀个或⼏个表⾯,有时会分布在型材的所有表⾯(对薄壁空⼼型材,则是分布于某⼀平⾯或曲⾯的内外两侧)。
2原因分析在现场见到,“⽩斑”形成于“碱蚀”⼯序,在经随后的稀硝酸(或硫酸)“中和”之后,并未消失;经硫酸阳极氧化处理后,⼜更加清晰地呈现出来。
笔者专门截取了两段“⽩斑”点⾯积较⼤(F=30~40mm2)的碱蚀洗(槽液中,ω(Zn2+)≥5×106)型材试样。
然后,采⽤DV-5型原⼦发射⽕花直读光谱仪分别对上述两段试样的“⽩斑”区的成分做了定量分析,其结果如下(表中数据均为质量分数):由表1的分析结果可见:“⽩斑”处Si、Mg、Zn元素的含量明显增加:⽽表2的结果表明:“⽩斑”处Si、Zn元素的含量明显增加,⽽Mg元素的含量却有所下降。
从⾦属材料腐蚀的观点看来,Mg2Si这种表⾯缺陷实质上是6063铝合⾦材料发⽣“剥落腐蚀”的结果。
剥落腐蚀是⼀种浅表⾯的选择腐蚀,腐蚀是沿着⾦属表⾯发展的,其产物的体积往往⽐发⽣腐蚀的⾦属⼤得多,因⽽膨胀。
⼀般⽽⾔,当铝与呈阴极性的异种⾦属相邻接时,“剥落腐蚀”程度上升。
在电⼦显微镜下观察发现:“剥落腐蚀”通常沿不溶组成物(如Si,Mg2Si等),或沿晶界进⾏。
2.1铸锭质量的影响6063铝合⾦的主要相组成是:α(Al)固溶体、游离Si(阳极相)和F eAl3(阳极相);当铁含量⼤于时,有β(F e Si Al)(阳极相);⽽当铁含量⼩于时,有α(F e Si Al)(阴极相);其他可能的杂质相是:MgZn2、CuAl2等。
6063铝合金常见缺陷
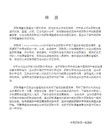
①加强风冷强度,避免摆床上型材的间隔过小,保证风冷的温度梯度;
②有条件的工厂应采用雾化水冷与风冷相结合的方法,可完全消除黑斑。
7 条纹 挤压型材的条纹缺陷种类比较多,形成因素也较复杂,这里仅就一些常见条纹的产生原因及解决方法加以论述。
7.2 组织条纹
7.2.1 主要原因 铸锭铸造组织不均匀,成分偏析,铸锭表皮下存在较严重的缺陷, 铸锭的均匀比处理不充分等,在随后的挤压过程中导致型材表面成分不均匀,从而使型材 氧化 后的着色能力不相同,形成组织条纹。
7.2.2 解决办法
①合理执行铸造工艺,消除或减轻组织偏析;
②铸锭表面车皮;
③认真进行铸锭均匀化处理。
7.3 金属亮纹 在氧化白料中表现发亮,大多数情况下为笔直条状且宽度不定,在氧化着色料中该条纹呈浅色条状。
7.3.1 主要原因 由于金属流动出现摩擦或变形极其剧烈时,金属局部温度会上升很高,另外金属流动不均匀也会导致晶粒发生剧烈破碎,然后发生再结晶,致使该处组织发生变 化,在随后的氧化处理中导致型材表面出现纵向的亮条纹,着色处理中致使型材着不上色或呈现浅色条纹。
③模具型孔布局不合理造成金属流动不均匀;
④导路不合适或未安装导路;
⑤润滑不合适。
9.2 解决办法
①修整模具工作带使金属流动均匀;
②采用合理的挤压工艺,在保证出口温度的前提下尽量采用低温挤压;
①由于摩擦力的原因使金属表层受到附加拉应力的作用,当附加拉应力大于表层金属抗拉强度时就会产生裂纹;
②挤压温度过高,金属表层抗拉强度下降,在摩擦力作用下产生裂纹;
③挤压速度过快时,金属表层所受的附加拉应力增加使型材产生裂纹。
6 黑斑 型材阳极氧化后局部出现近似圆形的黑灰色斑点,在型材纵向贴摆床的面上等距离分布,大小不一。
6063铝合金型材氧化过程中出现“白斑”的原因分析及解决

6063铝合金型材氧化过程中出现“白斑”的原因分析及解决1 问题的提出在实际生产中,加工率大(ε>95%),壁厚较薄(δ≤1.5mm)的T5状态的6063铝合金挤压型材在经硫酸阳极氧化处理后,其表面会呈现有规律(而有时无规律)分布的白色斑点(或无光斑痕);严重时呈现深色斑痕——“白斑”。
“白斑”的分布规律及特征是:它是在平行于挤压方向的平面上大致等间距的、呈线状或扁四边形状或不规则星点(片)状的、相对于基体表面有微小深度而呈凹槽形的一种表面缺陷[5,6]。
白斑通常分布于型材的一个或几个表面,有时会分布在型材的所有表面(对薄壁空心型材,则是分布于某一平面或曲面的内外两侧)。
2 原因分析在现场见到,“白斑”形成于“碱蚀”工序,在经随后的稀硝酸(或硫酸)“中和”之后,并未消失;经硫酸阳极氧化处理后,又更加清晰地呈现出来。
笔者专门截取了两段“白斑”点面积较大(F=30~40 mm2)的碱蚀洗(槽液中,ω(Zn2+)≥5×106)型材试样。
然后,采用DV-5型原子发射火花直读光谱仪分别对上述两段试样的“白斑”区的成分做了定量分析,其结果如下(表中数据均为质量分数):由表1的分析结果可见:“白斑”处Si、Mg、Zn元素的含量明显增加:而表2的结果表明:“白斑”处Si、Zn元素的含量明显增加,而Mg元素的含量却有所下降。
从金属材料腐蚀的观点看来,Mg2Si这种表面缺陷实质上是6063铝合金材料发生“剥落腐蚀”的结果。
剥落腐蚀是一种浅表面的选择腐蚀,腐蚀是沿着金属表面发展的,其产物的体积往往比发生腐蚀的金属大得多,因而膨胀。
一般而言,当铝与呈阴极性的异种金属相邻接时,“剥落腐蚀”程度上升。
在电子显微镜下观察发现:“剥落腐蚀”通常沿不溶组成物(如Si,Mg2Si等),或沿晶界进行[1]。
铝合金挤压生产知识

一、铝合金的挤压生产1.挤压时金属的变形过程分为几个阶段?分为:⑴填充挤压阶段;⑵平流压由阶段;⑶紊流压由阶段。
2、什么是挤压比(入)?挤压6063型材时,挤压比(入)在什么范围内最合适?挤压筒内铝棒的截面积与挤由型材的截面积之比,称为挤压比(入)或挤压系数(入)。
挤压系数是挤压工艺最重要的内容,根据制品外形和截面面积选择挤压筒的直径。
挤压系数一般〉9。
平模当入=9〜40时使用寿命较长,分流模的挤压系数应在20〜70范围内。
系数过小会产生焊接不良。
所以挤压空心型材的挤压系数比实心型材的大。
如挤压①101X25管材,当入=15时焊合不好,选择入=38时管材焊合良好。
挤压系数太大,挤压困难,而且因铝棒较短造成产品的成品率太低,影响经济技术指标。
3.生产过程中如何控制挤压温度?铝棒温度应保持在440〜520c之间(以6063为例),加热时间均在6小时以上。
挤压筒加热到400〜440C。
模具温度为400〜510C,保温时间1〜4小时。
4、选择挤压温度应遵循哪些原则?6063合金铝棒的挤压温度通常在470〜510之间,有时也可在较低温度下挤压。
选择铝棒温度的原则:⑴为获得较高的机械性能,应选择较高的挤压温度;⑵当挤压机能力不足,可通过提高铝棒温度来提高挤压速度;⑶当模具悬臂过大时,可提高铝棒温度,以减小铝棒对模具的压力及摩擦力;⑷挤压温度过高会使产生气泡、撕裂及由于模具工作带粘铝造成表面划痕严重;⑸为了获得高表面质量的产品,宜在较低温度下挤压5、如何控制挤压速度?挤压速度是影响生产率的一个重要指标。
挤压速度取决于合金种类、几何形状、尺寸和表面状态,同时也与铸锭质量息息相关。
要提高挤压速度,必需合理控制铝棒温度、模具温度、挤压筒温度。
6063铝合金挤压速度范围为:9〜80M/min,其中实心型材为:20〜80M/min,空心型材的挤压速度一般为实心型材挤压速度的0.5〜0.8倍。
6、什么是均匀化?通常将6063铝棒在560c保温6〜8小时,使合金的Mg2si相以细小质点均匀分布在整个金属基体中,且消除铸造应力,铸锭由炉后以较高速度冷却(水冷或风冷),这种热处理工艺称作均匀化。
- 1、下载文档前请自行甄别文档内容的完整性,平台不提供额外的编辑、内容补充、找答案等附加服务。
- 2、"仅部分预览"的文档,不可在线预览部分如存在完整性等问题,可反馈申请退款(可完整预览的文档不适用该条件!)。
- 3、如文档侵犯您的权益,请联系客服反馈,我们会尽快为您处理(人工客服工作时间:9:00-18:30)。
6063铝合金型材以其良好的塑性、适中的热处理强度、良好的焊接性能以及阳极氧化处理后表面华丽的色泽等诸多优点而被广泛应用。
但在生产过程中经常会出现一些缺陷而致使产品质量低下,成品率降低,生产成本增加,效益下降,最终导致企业的市场竞争能力下降。
因此,从根源上着手解决6063铝合金挤压型材的缺陷问题是企业提高自身竞争力的一个重要方面。
笔者根据多年的铝型材生产实践,在此对6063铝合金挤压型材常见缺陷及其解决办法作一总结,和众多同行交流,以期相互促进。
1 划、擦、碰伤划伤、擦伤、碰伤是当型材从模孔流出以及在随后工序中与工具、设备等相接触时导致的表面损伤。
1.1 主要原因①铸锭表面附着有杂物或铸锭成分偏析。
铸锭表面存在大量偏析浮出物而铸锭又未进行均匀化处理或均匀化处理效果不好时,铸锭内存在一定数量的坚硬的金属颗粒,在挤压过程中金属流经工作带时,这些偏析浮出物或坚硬的金属颗粒附着在工作带表面或对工作带造成损伤,最终对型材表面造成划伤;②模具型腔或工作带上有杂物,模具工作带硬度较低,使工作带表面在挤压时受伤而划伤型材;③出料轨道或摆床上有裸露的金属或石墨条内有较硬的夹杂物,当其与型材接触时对型材表面造成划伤;④在叉料杆将型材从出料轨道上送到摆床上时,由于速度过快造成型材碰伤;⑤在摆床上人为拖动型材造成擦伤;⑥在运输过程中型材之间相互摩擦或挤压造成损伤。
1.2 解决办法①加强对铸锭质量的控制;②提高修模质量,模具定期氮化并严格执行氮化工艺;③用软质毛毡将型材与辅具隔离,尽量减少型材与辅具的接触损伤;④生产中要轻拿轻放,尽量避免随意拖动或翻动型材;⑤在料框中合理摆放型材,尽量避免相互摩擦。
2、机械性能不合格2.1 主要原因①挤压时温度过低,挤压速度太慢,型材在挤压机的出口温度达不到固溶温度,起不到固溶强化作用;②型材出口处风机少,风量不够,导致冷却速度慢,不能使型材在最短的时间内降到200℃以下,使粗大的Mg2Si过早析出,从而使固溶相减少,影响了型材热处理后的机械性能;③铸锭成分不合格,铸锭中的Mg、Si含量达不到标准要求;④铸锭未均匀化处理,使铸锭组织中析出的Mg2Si相无法在挤压的较短时间内重新固溶,造成固溶不充分而影响了产品性能;⑤时效工艺不当、热风循环不畅或热电偶安装位置不正确,导致时效不充分或过时效。
2.2 解决办法①合理控制挤压温度和挤压速度,使型材在挤压机的出口温度保持在最低固溶温度以上;②强化风冷条件,有条件的工厂可安装雾化冷却装置,以期达到6063合金冷却梯度的最低要求;③加强铸锭的质量管理;④对铸锭进行均匀化处理;⑤合理确定时效工艺,正确安装热电偶,正确摆放型材以保证热风循环通畅。
3、几何尺寸超差3.1 主要原因①由于模具设计不合理或制造有误、挤压工艺不当、模具与挤压筒不对中、不合理润滑等,导致金属流动中各点流速相差过大,从而产生内应力致使型材变形;②由于牵引力过大或拉伸矫直量过大导致型材尺寸超差。
3.2 解决办法①合理设计模具,保证模具精度;②正确执行挤压工艺,合理设定挤压温度和挤压速度;③保证设备的对中性;④采用适中的牵引力,严格控制型材的拉伸矫直量。
1 化学成分的优化控制6063-T5建筑铝型材必须具备一定的力学性能。
在其他条件相同时,其抗拉强度、屈服强度随含量增加而升高。
6063台金的强化相主要是Mg2Si相,到底Mg、Si和Mg2Si的量应取多少为好?Mg2Si相是由2个镁原子同1个硅原子组成,镁的相对原子质量为24.3l,硅的相对原子质量为28.09,因此Mg2Si化合物中,镁硅的质量比为1.73:1。
因此,可根据以上分析结果,如果镁硅含量比值大于1.73,则合金中镁除形成Mg2Si 相外,还有过剩镁,反之比值小于1.73,则表明硅除形成Mg2Si相外,还有剩余硅。
镁过剩对合金力学性能是有害的。
镁一般控制在0.5%左右,Mg2Si总量控制在0.79%。
当硅过剩0.01%时合金的力学性能σb约为218Mpa,已大大超过国家标准性能,并过剩硅从0.01%提高到0.13%,σb可提高到250Mpa,即提高14.6%。
要形成一定量的Mg2Si,必须首先考虑到Fe与Mn等杂质含量造成的硅损失,即要保证有一定量的过剩硅。
为了使6063合金中的镁充分与硅匹配,实际配料时,必须有意识地使Mg:Si<1.73。
镁的过剩不仅削弱强化效果,而且又增加了产品成本。
因此,6063合金的成分一般控制为:Mg:0.45%-0.65%;Si:0.35%-0.50%;Mg:Si=1.25-1.30;杂质Fe控制在<0.10%-0.25%;Mn<0.10%。
2 优化铸锭均匀化退火工艺在民用挤压型材生产时,6063合金的高温均匀化退火规范为:560±20℃,保温4-6h,冷却方式为出炉强迫风冷或喷水急冷。
合金的均匀化处理能提高挤压速度,同未均匀化处理的铸锭相比,大约可使挤压力降低6%-10%。
均匀化处理后冷却速度对组织的析出行为有重要的影响。
对均热后快冷的铸锭,Mg2Si几乎能全部固溶于基体,过剩的Si也将固溶或以弥散析出的细小质点存在。
这样的铸锭可以在较低温度下快速挤压,并获得优良的力学性能和表面光亮度。
在铝型材挤压生产中,以燃油或燃气加热炉替代电阻加热炉可收到明显的节能降耗效果。
合理地选择炉型、燃烧器及空气循环方式可使炉子获得均匀稳定的加热性能,达到稳定工艺提高产品质量的目的。
燃烧式铸锭加热炉经几年来运行和不断改善,目前市场上已推出燃烧效率高于40%的炉型。
铸锭装炉后迅速升温到570℃以上,并经一段保温时间后,在出料区冷却到接近挤压温度时出炉挤压,铸锭在加热炉经历了半均匀化过程,这一过程称半均质处理,基本上符合6063合金热挤压工艺要求,从而可省单独的均匀化工序,可大大节省设备投资和能耗,是一种值得推广的工艺。
3 优化挤压和热处理工艺3.1 铸锭加热对挤压生产来说,挤压温度是最基本的且最关键的工艺因素。
挤压温度对产品质量、生产效率、模具寿命、能量消耗等都产生很大影响。
挤压最重要的问题是金属温度的控制,从铸锭开始加热到挤压型材的淬火都要保证可溶解的相组织不从固溶中析出或呈现小颗粒的弥散析出。
6063合金铸锭加热温度一般都设定在Mg2Si析出的温度范围内,加热的时间对Mg2Si 的析出有重要的影响,采用快速加热可以大大减少可能析出的时间。
一般来说,对6063合金铸锭的加热温度可设定为:未均匀化铸锭:460-520℃;均匀化铸锭:430-480℃。
其挤压温度在操作时视不同制品及单位压力大小来调整。
在挤压过程中铸锭在变形区的温度是变化的,随着挤压过程的完成,变形区的温度逐渐升高,而且随着挤压速度的提高而提高。
因此为了防止出现挤压裂纹,随着挤压过程的进行和变形区温度的升高,挤压速度应逐渐降低。
3.2 挤压速度挤压过程中必须认真控制挤压速度。
挤压速度对变形热效应、变形均匀性、再结晶和固溶过程、制品力学性能及制品表面质量均有重要影响。
挤压速度过快,制品表面会出现麻点、裂纹等倾向。
同时挤压速度过快增加了金属变形的不均匀性。
挤压时的流出速度取决于合金种类和型材的几何形状、尺寸和表面状况。
6063合金型材挤压速度(金属的流出速度)可选为20-100米/分。
近代技术的进步,挤压速度可以实现程序控制或模拟程序控制,同时也发展了等温挤压工艺和CADEX等新技术。
通过自动调节挤压速度来使变形区的温度保持在某一恒定范围内,可达到快速挤压而不产生裂纹的目的。
为了提高生产效率,在工艺上可以采取很多措施。
当采用感应加热时,沿铸锭长度方向上存在着温度梯度40-60℃(梯度加热),挤压时高温端朝挤压模,低温端朝挤压垫,以平衡一部分变形热;也有采用水冷模挤压的,即在模子后端通水强制冷却,试验证明可以提高挤压速度30%-50%。
近年来在国外用氮气或液氮冷却模具(挤压模)以增加挤压速度,提高模具寿命和改善型材表面质量。
在挤压过程中将氮气引到挤压模出口处放出,可以使被冷却的制品急速收缩,冷却挤压模和变形区金属,使变形热被带走,同时模子出口处被氮的气氛所控制,减少了铝的氧化,减少了氧化铝粘接和堆积,所以氮气的冷却提高了制品的表面质量,可大大的提高挤压速度。
CADEX是最近发展的一种挤压新工艺,它挤压过程中的挤压温度、挤压速度和挤压力形成一个闭环系统,以最大限度地提高挤压速度和生产效率,同时保证最优良的性能。
3.3 在线淬火6063-T5淬火是为了将在高温下固溶于基体金属中的Mg2Si出模孔后经快速冷却到室温而被保留下来。
冷却速度常和强化相含量成正比。
6063合金可强化的最小的冷却速度为38℃/分,因此适合于风冷淬火。
改变风机和风扇转数可以改变冷却强度,使制品在张力矫直前的温度降至60℃以下。
3.4 张力矫直型材出模孔后,一般皆用牵引机牵引。
牵引机工作时在给挤压制品以一定的牵引张力,同时与制品流出速度同步移动。
使用牵引机的目的在于减轻多线挤压时长短不齐和抹伤,同时也可防止型材出模孔后扭拧、弯曲,给张力矫直带来麻烦。
张力矫直除了可以使制品消除纵向形状不整外,还可以减少其残余应力,提高强度特性并能保持其良好的表面。
3.5 人工时效时效处理要求温度均匀,温差不超过±3-5℃。
6063合金人工时效温度一般为200℃。
时效保温时间为1-2小时。
为了提高力学性能,也有采用180-190℃时效3-4小时,但此时生产效率会有所降低。
3.6 铸锭长度的优化与计算铸锭长度的计算方法有体积法和质量法。
通过建立数学关系式,就很容易地选取出最佳的铸锭规格,大大提高型材的几何成品率。
(1) 体积法Vo=V1十VnAoLo=A1²L1十A²LnLo/Ko=L1/λ十LnLo=(L1/λ+Ln)²K (1)式中:Vo——铸锭体积(mm3);V1——型材体积(mm3);Vn——压余体积(mm3);Ao——铸锭面积(mm2);Lo——铸锭长度(mm);A1——型材截面积(mm2);L1——型材长度(mm);A——挤压筒面积(mm2);Ln——压余长度(mm);K=A/Ao 充填系数;λ=A/A1 挤压系数。
按照体积不变道理,经简化之后整理为公式(1),K与Ln可以认为是常数,只要求λ,确定Lmax,可方便地求出Lo,即铸锭长度。
(2)质量法mo=m1十mnρLoLo=L1²ρL1+mnLo=(L1²ρL1+mn)²PLo (2)式中:Lo 铸锭长度;L1 型材压出长度(m);ρL1 型材线密度(Kg/m);mn 压余重量(Kg);mo 铸锭重量(kg)m1 压出型材重量(kg)ρLo 铸锭线密度(Kg/m);(2)式还可以再变化一下,即:L1=n²L定+L12Lo=[²L定十L12)²ρL1+mn]²ρLo-1 (3)式中:n 定尺支数;L定定尺寸长度(m);L12 切头切尾长度(m)。