球化剂孕育剂培训讲义
新型三明治覆盖法提高球化剂中Mg的吸收率

594F O U N D R V 工艺技术Vol-70 No.5 2021新型三明治覆盖法提高球化剂中M g的吸收率郭振峰,孙公军(中车大连机车车辆有限公司铸锻分公司,辽宁大连116022 )摘要:对冲入法球化处理时,球化剂、孕育剂、覆盖剂的装包方法进行了介绍。
合理称重后,采用分批分层,类似三明治形状的装包顺序,并采取逐层捣实、稍加覆盖的操作方法,可延缓球化反应起爆时间,延长球化反应时间,可使球化剂Mg的吸收率大幅度提高,球铁最终力学性能及金相组织均得到明显改善。
关键词:三明治覆盖法;球墨铸铁;球化剂Mg的吸收率冲入法球化处理由于其操作简单易行、设备投资少等特点至今仍然是铸造企业普遍使用的球化处理方法,但是采用冲入法球化处理工艺的缺点也很明显:一是镁的吸收率低,造成原材料的浪费和成本的增加;二是产品的质量不稳定,经常会出现球化不良情况;三是温度损失大,铁液含渣多,铸件废品率高等m。
为了解决这些问题,笔者根据二十多年的工作经验,结合相关资料,制定出了球化剂、孕育剂、覆盖剂等的精确定量装包方法。
作者简介:郭振峰(1975-),男,回族,技师,从事电炉冶炼研究工作。
E-m a il: daliangzf@ 163 .com中图分类号:TG143.5文献标识码:A文章编号:1001 -4977 (2021) 05-0594-04收稿曰期:2020-11-25收到初稿, 2020-12-31收到修订稿。
1工艺量化及球化剂装包方案的制定与实施1.1问题的提出冲入法球化处理球化剂中Mg的吸收率不高是一个普遍问题,其影响因素也非常 多:原铁液的含硫量、球化剂中Mg的含量、球化剂的粒度、球化剂与高温铁液接触 时间、球化反应温度、球化反应起爆时间、球化反应剧烈程度、球化反应时长、反 应后铁液残留Mg含量等,实际操作过程中每家企业都会根据自己操作习惯摸索改善 提升,以获取球化剂中最优的Mg吸收率121。
根据Mg的吸收率的相关计算公式:n= [0.75x (原铁液含S量-反应后铁液含S量)+残留Mg量](LxMg的加入量)(1 )式中:n.为Mg的吸收率;L为球化处理操作水平系数,一般取0.75〜0.95,操作水平越 高取值越大;Mg的加入量代表纯Mg的加入量,需要由球化剂加入量换算获取;反应 后铁液含S量一般控制在0.06%~0.1%以下,铁液残留Mg量一般控制在0.04%〜0.06%。
孕育剂怎么选
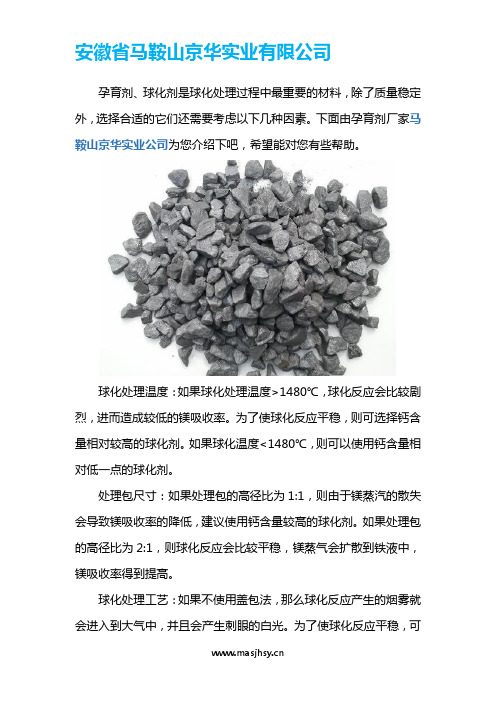
孕育剂、球化剂是球化处理过程中最重要的材料,除了质量稳定外,选择合适的它们还需要考虑以下几种因素。
下面由孕育剂厂家马鞍山京华实业公司为您介绍下吧,希望能对您有些帮助。
球化处理温度:如果球化处理温度>1480℃,球化反应会比较剧烈,进而造成较低的镁吸收率。
为了使球化反应平稳,则可选择钙含量相对较高的球化剂。
如果球化温度<1480℃,则可以使用钙含量相对低一点的球化剂。
处理包尺寸:如果处理包的高径比为1:1,则由于镁蒸汽的散失会导致镁吸收率的降低,建议使用钙含量较高的球化剂。
如果处理包的高径比为2:1,则球化反应会比较平稳,镁蒸气会扩散到铁液中,镁吸收率得到提高。
球化处理工艺:如果不使用盖包法,那么球化反应产生的烟雾就会进入到大气中,并且会产生刺眼的白光。
为了使球化反应平稳,可以采用低镁高钙的球化剂。
如果使用盖包法工艺,铁液不会飞溅,并且产生的烟雾较少,可使用高镁低钙的球化剂,以减少加入量,降低球化成本。
处理重量:如果处理铁液的重量小于500kg,那么可使用粒度较小的球化剂,推荐使用粒度12mm以下的球化剂。
如果处理铁液的重量在500~1000kg,可使用粒度较大的球化剂,如粒度为3~25mm的球化剂。
如果处理铁液的重量大于1000kg,则可以使用4~32mm的球化剂。
硅含量:如果铸造产品的工艺出品率较低或者废品率较高,想通过多加回炉料和废钢的方式进行熔炼,而最终铸件对铁水的硅含量有严格要求。
在孕育量没法进一步降低的前提下,可使用低硅球化剂进行处理,这样可使回炉料多加8%~15%,可降低铸造厂的生产费用。
原铁液硫含量:如果原铁液硫含量较高,如果不进行脱硫处理,则需要高镁高稀土的球化剂,并且加入量会较高,如果原铁液的硫含量较低,则可以使用低镁低稀土的球化剂,且加入量会较低,低镁低稀土的球化剂成本也会比较便宜。
马鞍山京华实业公司是炼钢、铸造用增碳剂、煅后石油焦以及石墨化增碳剂,孕育剂,碳化硅等专业生产厂家。
铸造篇

第四节 铸件中的气孔
一.析出性气孔: 见教材P47图2-12 高温液态吸收的气体凝固时溶解度降低,又来不及 排出,形成“针孔”。 防止:1.对金属液进行“除气处理”. 2.清除炉料中的油污和水分. 3.烘干浇注用具. 4.降低铸型含水量.
浸入性气孔: 二.浸入性气孔 浸入性气孔 砂型和型芯在浇注时产生的气体聚集在型腔内表层浸 入金属液内形成,多出现在铸件局部的上表面,尺寸 较大,呈椭圆形或梨形,孔内表面被氧化。 防止:1.提高型砂透气性. 2.减少型芯发气性. 反应性气孔: 三.反应性气孔: 反应性气孔 由高温金属液与铸型材料、冷铁、熔渣之间发生化学 反应产生的气体留在铸件内形成气孔。 防止:1.皮下气孔——见教材P48图2-13a. 降低砂型的 含水量。 2.冷铁气孔——见教材P48图2-13b. 清理冷铁表 面油污和铁锈。
震压式造型机
微震压实式造型机
3)射压造型机: 射砂—压实 见教材P65图2—25 垂直分型 无箱造型 优点:与配砂、浇注、落砂构成一个完整的 自动生产线,生产率高达240—300箱/h 缺点:垂直分型,下芯困难,对模具精度要 求高。 应用:大批量生产小型简单件。 4)射芯机: 见教材P66图2—27, 填砂与紧砂同时完成,生产率很高,既可用 于造芯,又可用于造型。 如热芯盒射芯机,冷芯盒射芯机,(采用特 种粘结剂)
二.机器造型: 机器造型: 1.优缺点: 1)优点: ①生产率高 ②劳动条件好 ③铸件尺寸精确、表面光洁、加工余量小. ④生产成本低(因批量大). 2)缺点: 设备、模板、专用砂箱投资大,一般情况下,造型 机、造芯机、机械化砂处理设备、浇注和落砂等工 序需共同组成流水线。 2.应用:目前已广泛应用于中、大批量的铸件生产. 3.机器造型(造芯)的基本原理: 见教材P57图2—24顶杆起模式震压造型机的工作过程。
喂丝球化孕育介绍

e) 线卷的米数在屏幕上可以显示出来(线卷余量在 500 米以上线卷显示为绿色,500 米到 200 米之间显示为黄色,少于 200 米显示为红色并闪烁)
f) 输入 FeSiMg 包芯线数据如下: 输入处理包内铁水的重量,铁水硫含量,温度,喂丝的速度 (取决于处理包的深度,铁水 的压力),镁的吸收率以及球化处理后的目标残余镁量。基于这些参数和包芯线内化学成 分进行计算,得出要达到目标残余镁量需要加入的包芯线长度以及喂丝时间(棕色)。
图 3.a、没有密闭处理室的喂丝处理站设计
图 3.b、每次处理三吨铁水的处理站两种不同的设计
图 3.c、每次处理五吨铁水的处理站设计 2、喂丝机 (1)、单线喂丝机
此设备的发动机带动一个喂丝口,由 CPU 控制。包芯线的喂入速度可以通过主控制软件 进行调整。要控制调整包芯线的速度,使包芯线可以达到处理包的底部, 然后才开始从最低层 金属液开始发生反应,以保证 Mg 可以最大程度的被吸收。喂丝机装有一个开关,设定了米数。 在包芯线的米数达到设定米数时,喂丝机自动停止并抽出包盖下方的包芯线。此设备用于小型 包的球化处理,没有孕育处理工艺。
kg/吨铁水 (25% Mg) 最少 最多
13
22
11
18
-
-
12
18
11
14
-
-
18
24
16
20
-
-
13
17
11
15
-
-
11
14
-
-
-
-
-
-
-
-
6
9
成本(6% Mg) (元/吨铁水)
(完整word版)球化剂(word文档良心出品)
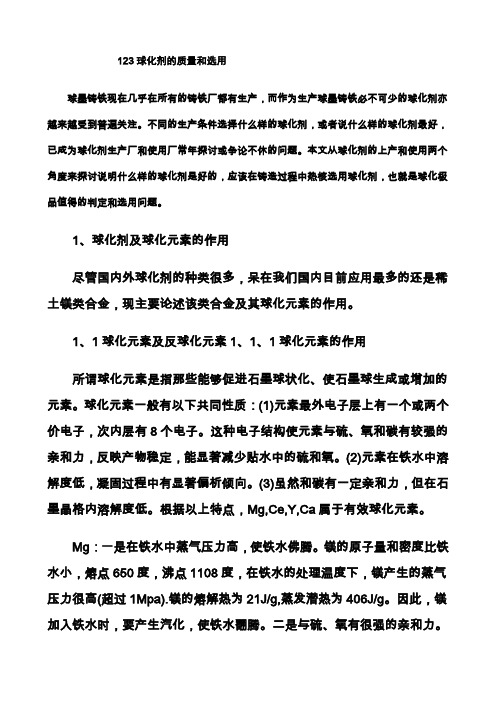
123球化剂的质量和选用球墨铸铁现在几乎在所有的铸铁厂都有生产,而作为生产球墨铸铁必不可少的球化剂亦越来越受到普遍关注。
不同的生产条件选择什么样的球化剂,或者说什么样的球化剂最好,已成为球化剂生产厂和使用厂常年探讨或争论不休的问题。
本文从球化剂的上产和使用两个角度来探讨说明什么样的球化剂是好的,应该在铸造过程中热核选用球化剂,也就是球化极品值得的判定和选用问题。
1、球化剂及球化元素的作用尽管国内外球化剂的种类很多,呆在我们国内目前应用最多的还是稀土镁类合金,现主要论述该类合金及其球化元素的作用。
1、1球化元素及反球化元素1、1、1球化元素的作用所谓球化元素是指那些能够促进石墨球状化、使石墨球生成或增加的元素。
球化元素一般有以下共同性质:(1)元素最外电子层上有一个或两个价电子,次内层有8个电子。
这种电子结构使元素与硫、氧和碳有较强的亲和力,反映产物稳定,能显著减少贴水中的硫和氧。
(2)元素在铁水中溶解度低,凝固过程中有显著偏析倾向。
(3)虽然和碳有一定亲和力,但在石墨晶格内溶解度低。
根据以上特点,Mg,Ce,Y,Ca属于有效球化元素。
Mg:一是在铁水中蒸气压力高,使铁水佛腾。
镁的原子量和密度比铁水小,熔点650度,沸点1108度,在铁水的处理温度下,镁产生的蒸气压力很高(超过1Mpa).镁的熔解热为21J/g,蒸发潜热为406J/g。
因此,镁加入铁水时,要产生汽化,使铁水翻腾。
二是与硫、氧有很强的亲和力。
所生成的MgO和MgS熔点高,密度也远小于铁,容易与铁水分离,因此镁处理后的铁水,硫和羊的含量都很低;三是在铁水凝固过程中有偏析于石墨的倾向,当其在铁水中的残留量超过0.035%时,使末就可以球化,但当镁残留量超过0.07%时,一部分镁偏析于晶界,并于晶界中的碳、磷等发生放热反应,生成MgC2、Mg2C3、Mg3P2等。
残留镁量更多时,晶间碳化物增多。
Re:稀土族元素对石墨球化有显著作用的是轻稀土元素中的铈和重稀土中的钇。
球化处理与孕育处理
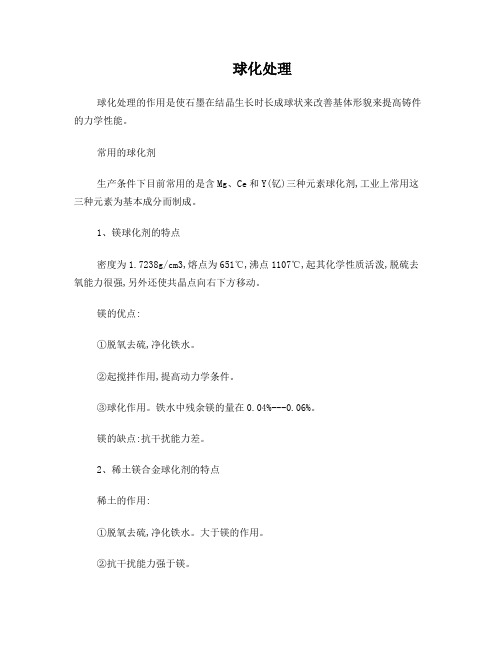
球化处理球化处理的作用是使石墨在结晶生长时长成球状来改善基体形貌来提高铸件的力学性能。
常用的球化剂生产条件下目前常用的是含Mg、Ce和Y(钇)三种元素球化剂,工业上常用这三种元素为基本成分而制成。
1、镁球化剂的特点密度为1.7238g/cm3,熔点为651℃,沸点1107℃,起其化学性质活泼,脱硫去氧能力很强,另外还使共晶点向右下方移动。
镁的优点:①脱氧去硫,净化铁水。
②起搅拌作用,提高动力学条件。
③球化作用。
铁水中残余镁的量在0.04%---0.06%。
镁的缺点:抗干扰能力差。
2、稀土镁合金球化剂的特点稀土的作用:①脱氧去硫,净化铁水。
大于镁的作用。
②抗干扰能力强于镁。
③球化作用。
小于镁的作用。
稀土的缺点:①白口倾向大②原子量大,动力学条件差③球化能力小于镁球化剂的处理方法:1.冲入法;该浇包分为凹坑式、堤坝式和复包式等。
2.型内球化法;该方法的优点是球化剂的吸收率高,所得球铁的性能比普通冲入法的高,特别是抗拉强度较高的情况下伸长率也高。
此外还克服了孕育衰退和球化衰退的问题。
3.盖包法。
优点:①比冲入法的镁利用率高10-20%;②球化剂加入的量少;③工作条件改善了。
4.自建压力加镁法;特点:①以纯镁作为球化剂,降低了成本;②镁的吸收率高,达到了60-80% ;③处理的铁液在3T以上。
④倒包补加铁液1/2-1/3,同时孕育处理。
⑤危险系数大5.转动包法;特点:①应用于含硫高的铁水,可处理含量为0.3%的铁液。
②镁的加入量为0.14-0.20%。
6.镁合金法;常用的合金有Si-Fe-Mg、Cu-Mg、Ni-Mg、Ni- Si-Mg等。
7.喂丝法;特点:①需要平底包,且H/D=1.5-2的细长包和加盖;②处理包有足够的空间供铁水沸腾;③处理的温度应尽可能的低;④要求有高的含镁量。
孕育处理孕育的目的是消除白口、增加共晶团和石墨球并细化、消除偏析、消除结晶过冷倾向等。
孕育效果的评定标准是:①白口倾向的减少。
使用不同球化剂生产QT400-18渣灌的对比试验
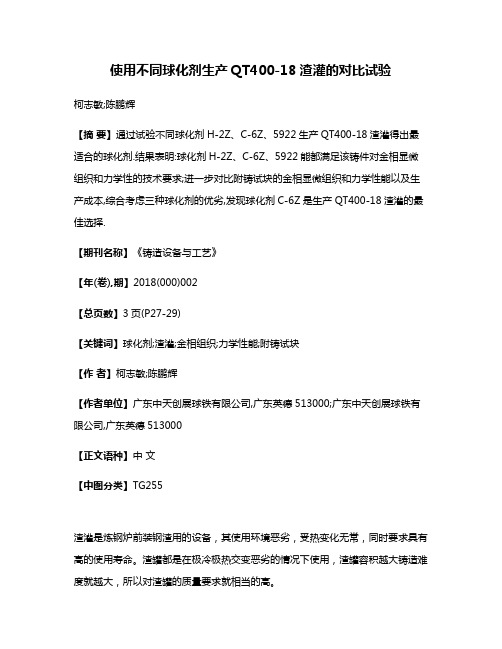
使用不同球化剂生产QT400-18渣灌的对比试验柯志敏;陈鹏辉【摘要】通过试验不同球化剂H-2Z、C-6Z、5922生产QT400-18渣灌得出最适合的球化剂.结果表明:球化剂H-2Z、C-6Z、5922能都满足该铸件对金相显微组织和力学性的技术要求;进一步对比附铸试块的金相显微组织和力学性能以及生产成本,综合考虑三种球化剂的优劣,发现球化剂C-6Z是生产QT400-18渣灌的最佳选择.【期刊名称】《铸造设备与工艺》【年(卷),期】2018(000)002【总页数】3页(P27-29)【关键词】球化剂;渣灌;金相组织;力学性能;附铸试块【作者】柯志敏;陈鹏辉【作者单位】广东中天创展球铁有限公司,广东英德513000;广东中天创展球铁有限公司,广东英德513000【正文语种】中文【中图分类】TG255渣灌是炼钢炉前装钢渣用的设备,其使用环境恶劣,受热变化无常,同时要求具有高的使用寿命。
渣罐都是在极冷极热交变恶劣的情况下使用,渣罐容积越大铸造难度就越大,所以对渣罐的质量要求就相当的高。
渣灌的技术要求:牌号为QT400-18,化学成分中的硅质量分数小于2.0%,力学性能抗拉强度350MPa~400 MPa,屈服强度大于230 MPa,延伸率大于18%;金相组织检验按GB/T9441《球墨铸铁金相检验》的规定进行,铸件本体和试块的球化级别不低于3级,基体组织中铁素体含量不低于95%,并且渣灌不允许出现冷隔、夹砂、气孔、砂眼、缩孔、粗晶、疏松、等缺陷。
渣灌铸件平均壁厚为50 mm,重量4 500 kg,如图1所示。
1 生产试验条件图1 渣灌铸件图球墨铸铁的碳质量分数一般为3.2%~3.8%,牌号为QT400-18的球铁含碳量取上限;硅是强烈促进石墨化的元素,增加石墨球数,但硅增加会增加球墨铸铁的脆性,为保证QT400-18球铁的延伸率,加之渣灌中技术要求规定硅质量分数控制在2.0%左右,为此确定原铁水硅质量分数为0.9%~1.0%;锰阻碍石墨化及阻碍铁素体的形成,影响延伸率,为此锰含量越低越好;磷易偏析形成磷共晶,降低塑性和韧性;而残余镁和稀土一般是通过球化剂球化后残余留下的,具有强烈形成白口的倾向,为此,在保证球化合格的前提下越低越好。
影响球化剂吸收率和球化稳定性的主要因素

影响球化剂吸收率和球化稳定性的主要因素冲入法处理球铁操作简便,安全可靠,处理铁水量灵活,而且冲入法无须特殊的工艺装备,容易上马,因而被越来越多地用于代替压力加镁法,成为目前应用最广泛的球化处理方法。
冲入法处理流程为:把球化剂(如块度15〜20毫米的稀土镁硅铁)堆放在铁水包一侧,稍加紧实,并根据铁水出炉温度不同加不同的覆盖剂(如硅铁粉、铁屑、铁板等),铁水包装载后预热至暗红色,将铁水包的另一侧对向出铁槽,球化示意图见图1。
球化处理时先出所需铁水总量的60%^75%待铁水与球化剂反应的翻腾基本结束后,再出余量铁水,同时冲入孕育剂,作孕育处理,然后搅拌、扒渣、浇注。
图1冲入法球化示意图1.铁水包2.球化剂3.覆盖剂对于处理少量铁水,可一次出完并作孕育处理,效果更好,温度损失也少。
冲入法球化工艺要保证铁水中残留适当含量的镁和稀土,并使二者有合适的比例,这是保证球化的必要条件。
铁水中残留镁量与稀土量的比例主要依靠球化剂中镁和稀土的比例来保证。
球化元素残留量的绝对值则取决于球化剂的加入量和吸收率。
在冲入法球化处理时,球化元素的主要损耗是氧化烧损和脱硫损耗。
影响球化剂吸收率和球化稳定性的主要因素如下:一、原铁水含硫量的影响原铁水含硫量越高,消耗在脱硫上的球化剂越多。
因此球化剂加入量必须随铁水含硫量增高而加大。
对于含Mg 8%〜10% Si 35%-40%勺稀土镁硅铁,在1380c〜1450c处理,对壁厚100毫米以下铸件,球化剂加入量与含硫量关系见表1。
表1 稀土镁硅铁加入量与原铁水含硫量的关系原铁水含硫量(衿<0.03 0.03〜0.05 0.05〜0.07 0.07〜0.10球化剂加入量(衿0.6〜0.8 0.8〜1.1 1.1〜1.3 1.3〜1.6二、处理温度的影响铁水温度是影响稀土镁硅铁冲入法处理球墨铸铁质量的一个重要因素。
由于球化剂、覆盖剂以及孕育剂的熔化需要耗费大量热量,使整个冲入法处理过程中铁水温度下降较大,1吨〜2吨包降低50c〜100C,大型浇包降温较少。
球墨铸铁中球状石墨相互粘连原因及预防措施何晓晨秦红李国乾黄学慧

球墨铸铁中球状石墨相互粘连原因及预防措施何晓晨秦红李国乾黄学慧发布时间:2023-07-04T10:04:15.303Z 来源:《中国科技信息》2023年8期作者:何晓晨秦红李国乾黄学慧[导读] 近年来球墨铸铁因其较为优良的性能受到越来越多的应用,而球墨铸铁中石墨的形态对性能有重要的影响。
为了保证球墨铸铁的优良性能,不仅要求石墨的球化率高,并且要求球状石墨分布均匀。
球墨铸铁中偶有出现球状石墨相互粘连的情况,该情况将会严重降低球墨铸铁构件的力学性能。
为避免该情况的出现,本文从原理及制造过程中分析出现该情况的原因,并提出相应的预防措施。
中车大连机车车辆有限公司辽宁大连 116041摘要:近年来球墨铸铁因其较为优良的性能受到越来越多的应用,而球墨铸铁中石墨的形态对性能有重要的影响。
为了保证球墨铸铁的优良性能,不仅要求石墨的球化率高,并且要求球状石墨分布均匀。
球墨铸铁中偶有出现球状石墨相互粘连的情况,该情况将会严重降低球墨铸铁构件的力学性能。
为避免该情况的出现,本文从原理及制造过程中分析出现该情况的原因,并提出相应的预防措施。
关键词:球墨铸铁;球状石墨;石墨粘连中图分类号:文献标识码:B前言球墨铸铁是20世纪50年代发展起来的一种材料,除具有铸铁本身拥有的优良的切削加工性能、铸造工艺性、消振性及耐磨性外,因其中石墨是以球状形态存在于基体组织中,对金属基体割裂作用相对最小,故球墨铸铁的强度和塑性较其他铸铁有了很大的提高[1]。
基于其优异的综合性能,目前球墨铸铁应用广泛。
轨道交通车辆中的曲轴、抱轴箱、机体等构件大多是球墨铸铁材质的。
但球墨铸铁在制造过程中会出现各种类型的缺陷,常见的有缩孔、缩松、皮下气孔等。
本人在工作中检测球墨铸铁试样时发现球墨铸铁中偶有出现球状石墨相互粘连的情况,该情况会导致石墨对金属基体的割裂加重,严重降低球墨铸铁构件的力学性能。
本文针对上述情况产生的原因加以分析,并提出相应的工艺优化提升措施。
球铁铸件缩孔、缩松的成因与防止
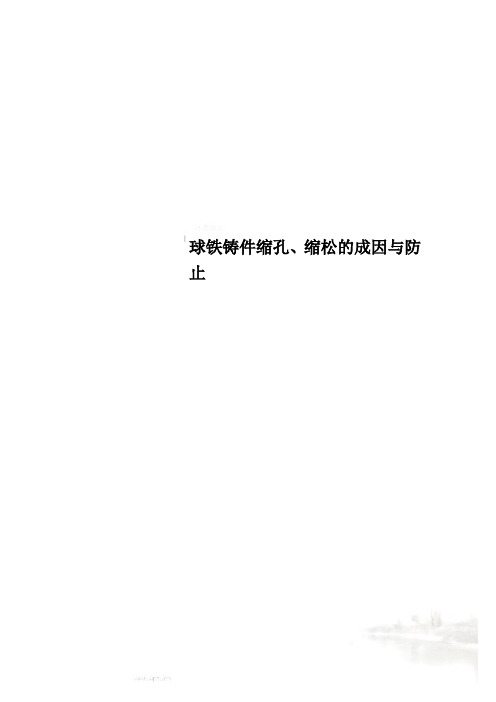
球铁铸件缩孔、缩松的成因与防止球铁铸件缩孔、缩松的成因与防止摘要:球墨铸铁大多数是共晶或过共晶成分,其糊状凝固方式使铸件外壳没有抵抗石墨化膨胀能力,因而铸型产生型壁迁移,增大铸件体积,极易产生内部缩孔、缩松。
球墨铸铁凝固时,在枝晶和共晶团间的最后凝固区域,收缩的体积得不到完全补充,留下的空洞形成宏观及微观缩松。
La 有助于消除缩松倾向。
分析缩孔缩松形成原因并提出相应的防止办法,有助于减少由此产生的废品损失。
关键词:球墨铸铁、收缩、缩孔、缩松1 前言1.1 缺陷形成原因球墨铸铁生产技术日臻完善,多年技术服务的实践表明,生产中出现的铸造缺陷,完全可以用成熟的经验予以消除。
据介绍:工业发达国家的铸造废品率可以控制在1%以下[1],国内先进水平也在2%左右,提高企业铸造技术水平,对减少废品十分重要。
1。
显微缩松显微镜观察微细连续缺失空间多角形疏松枝晶间、共晶团边界间众所周知,灰铸铁是逐层凝固方式,球墨铸铁是糊状凝固方式。
逐层凝固可以使铸件凝固时形成一个坚实的封闭外壳,铸件全封闭外壳的体积收缩可以减小壳体内的缩孔容积。
糊状凝固的特点是金属凝固时晶粒在金属液内部整个容积内形核、生长,固相与液相混合存在有如粥糊。
大多数球墨铸铁是共晶或过共晶成分,其糊状凝固方式使铸件外壳没有抵抗石墨化膨胀的能力,铸型产生型壁迁移,增大铸件体积,极易产生内部缩孔、缩松缺陷。
铸型冷却能力强,有利于铸件的容积凝固转变成逐层凝固,使铸件的分散缩松转变成集中缩孔。
然而,批量生产中湿砂型铸造很难被金属型或干砂型取代。
球墨铸铁凝固有以下三个特点,决定球墨铸铁是糊状凝固方式:①球化和孕育处理显著增加异质核心,核心存在于整个熔体,有利于全截面同时结晶。
②石墨球在奥氏体壳包围下生长,生长速度慢,延缓铸件表层形成坚实外壳;而片状石墨的端部始终与铁液接触,生长速度快,凝固时间短,促使灰铁铸件快速形成坚实外壳。
③球墨铸铁比灰铸铁导热率小 20%-30%,散热慢,外壳生长速度降低[3]。
厚大断面铸件专用球化剂, 孕育剂的开发与应用
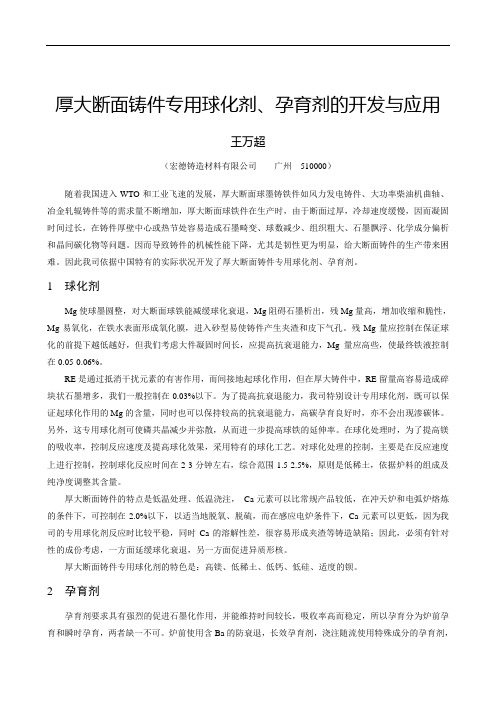
厚大断面铸件专用球化剂、孕育剂的开发与应用王万超(宏德铸造材料有限公司广州510000)随着我国进入WTO和工业飞速的发展,厚大断面球墨铸铁件如风力发电铸件、大功率柴油机曲轴、冶金轧辊铸件等的需求量不断增加,厚大断面球铁件在生产时,由于断面过厚,冷却速度缓慢,因而凝固时间过长,在铸件厚壁中心或热节处容易造成石墨畸变、球数减少、组织粗大、石墨飘浮、化学成分偏析和晶间碳化物等问题。
因而导致铸件的机械性能下降,尤其是韧性更为明显,给大断面铸件的生产带来困难。
因此我司依据中国特有的实际状况开发了厚大断面铸件专用球化剂、孕育剂。
1 球化剂Mg使球墨圆整,对大断面球铁能减缓球化衰退,Mg阻碍石墨析出,残Mg量高,增加收缩和脆性,Mg易氧化,在铁水表面形成氧化膜,进入砂型易使铸件产生夹渣和皮下气孔。
残Mg量应控制在保证球化的前提下越低越好,但我们考虑大件凝固时间长,应提高抗衰退能力,Mg量应高些,使最终铁液控制在0.05-0.06%。
RE是通过抵消干扰元素的有害作用,而间接地起球化作用,但在厚大铸件中,RE留量高容易造成碎块状石墨增多,我们一般控制在0.03%以下。
为了提高抗衰退能力,我司特别设计专用球化剂,既可以保证起球化作用的Mg的含量,同时也可以保持较高的抗衰退能力,高碳孕育良好时,亦不会出现渗碳体。
另外,这专用球化剂可使磷共晶减少并弥散,从而进一步提高球铁的延伸率。
在球化处理时,为了提高镁的吸收率,控制反应速度及提高球化效果,采用特有的球化工艺。
对球化处理的控制,主要是在反应速度上进行控制,控制球化反应时间在2-3分钟左右,综合范围1.5-2.5%,原则是低稀土,依据炉料的组成及纯净度调整其含量。
厚大断面铸件的特点是低温处理、低温浇注,Ca元素可以比常规产品较低,在冲天炉和电弧炉熔炼的条件下,可控制在2.0%以下,以适当地脱氧、脱硫,而在感应电炉条件下,Ca元素可以更低,因为我司的专用球化剂反应时比较平稳,同时Ca的溶解性差,很容易形成夹渣等铸造缺陷;因此,必须有针对性的成份考虑,一方面延缓球化衰退,另一方面促进异质形核。
球化剂孕育剂培训讲义
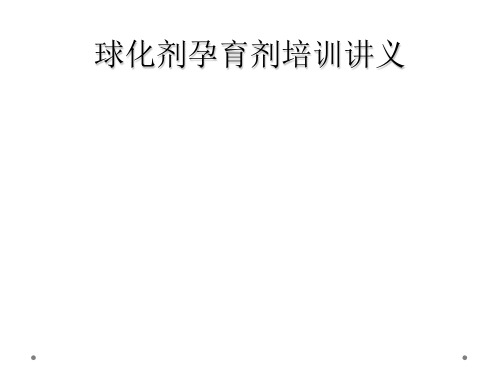
稀土镁硅铁合金加入量与原铁水含硫量的关系 压力加镁处理加镁量与原铁水含硫量的关系
孕育处理
• 作用
• 1. 提高球化率,细化石墨,改善 石墨圆整性。 • 2. 减少渗碳体,改变珠光体的相对含量
• 孕育剂
• 除前面介绍的外,还有硅钙(Si60%~65%,Ca25%~30%)、 硅铁-铋等,目前用得最多的仍是FeSi75。
铸铁的分类
• 铸铁是一系列主要由铁、碳和硅组成的合金的总称。 在这些合金中,碳的质量分数超过了在共晶温度时能 保留在奥氏体固溶体中的量。
• (一) 铸铁的分类 • 1. 根据碳在铸铁中的存在形式分类 • (1)白口铸铁 指碳主要以游离碳化铁形式出现的铸铁
,断口呈银白色。 • (2)灰铸铁 指碳主要以片状石墨形式出现的铸铁,断
球化剂孕育剂培训讲义
铁碳相图
• w(C)<2.06%铸钢 • w(C)>2.06%铸铁 • w(C)<4.26%为亚共
晶铸铁; w(C)=4.26%为共晶 铸铁;w(C)>4.26% ,为过共晶铸铁 • 实际应用的铸铁 w(C)含量在2.0%~ 4.5%的铸铁 • 同样,根据 w(C)=0.76把钢分为 亚共析钢、共析钢 和过共析钢
盖包法
在冲入法的处理包上部安装一个中间包将 其密封,处理包与中间包之间仅通过浇口 连接。预先将球化剂放在处理包内,然后 用中间包承接铁液,靠由中间包流入处理 包的铁液使处理包处于密闭状态,从而减 少反应烟尘和镁光外逸,提高镁的利用率
• 压力加镁法
特点:设备费用较高,操作较复杂;纯镁处 理,吸收率高70~80%,稳定球化;灰尘少无 镁光;适用于要求较高,较严格的铸件。
口呈灰色。它是工业中应用最广的铸铁。 • (3)麻口铸铁 指碳部分以游离碳化铁形式出现,部分
球墨铸铁件的缺陷和金相检验讲课文档
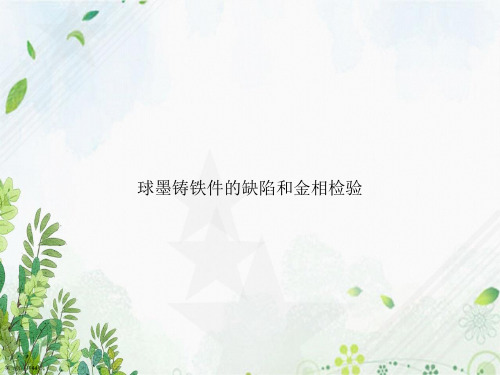
典型缺陷——皮下气孔
皮下气孔
特征:铸件表皮下2-3mm处均匀或蜂窝状分布的球 形、椭圆形或针孔状内壁光滑孔洞,直径0.5-3mm,在热 处理和抛丸后暴露,小件中较多。
原因:铁液表明形成的氧化膜阻碍气体析出,碳 化反应中形成的气体,镁残留量多形成的镁蒸汽, 炉料潮湿锈蚀等。
措施:球化保证条件下降低镁残留量,铁液平稳浇铸, 控制炉料干燥少锈,采用少氮或无氮树脂。
所以,石墨生长过程的控制是获得球状石墨的关键。
第八页,共44页。
第九页,共44页。
球墨铸铁孕育的目的
球墨铸铁的孕育是指向铁水中加入一定数量的球化剂 和孕育剂 ,通过球化及孕育处理使铁水在凝固时碳以球状石墨的形式形核和生 长。凝固后铸铁的组织中得到球状石墨的铸铁。一般在浇注之前,在 铁液中加入少量球化剂(通常为镁、稀土镁合金或含铈的稀土合金) 和孕育剂(通常为硅铁),使铁水凝固后形成球状石墨。球化处理和 孕育处理是生产球墨铸铁的重要环节。球墨铸铁进行孕育处理的目的 是为消除球墨铸铁的白口化倾向、消除过冷石墨、促进石墨化、细化 共晶团及减少晶间偏析等。
第二十七页,共44页。
薄壁铸件的凝固
在铸铁凝固时,存在石墨共晶与渗碳体共晶两种形式。在 平衡状态图中,前者的温度比后者高。为了要避免白口的产生 ,应使石墨共晶凝固过程在温度达到渗碳体共晶以前完成,这 就需要提高石墨共晶的凝固速率,而在一定的冷却速度下,球 铁共晶团的生长速度是一定的,因此提高石墨共晶的凝固速度 ,就必须增加共晶团数量。
石墨大部分呈团状,余为团絮状,允许 有极少量蠕虫状
石墨呈大部分絮状或团状,余为球状、 少量蠕虫状
石墨呈分散分布的蠕虫状、片状及球状、 团状、团絮状
石墨呈聚集分布的蠕虫状、片状及球状、 团状、团絮状
球墨铸铁的炉前球化和孕育处理工艺

球墨铸铁的炉前球化和孕育处理工艺
1球墨铸铁炉料按配料单数量,先后加入到感应电炉内,熔清,升温到出炉温度(1520℃),准备出炉。
其间可用炉前快速分析仪测定原铁水成分。
2浇注用的铁水球化包,要提前修好,筑好堤坝,并用木柴烘干烘透。
3球墨铸铁所用的球化剂、孕育剂要按每炉要求数量分别称好,备用。
4将球化剂放入铁水包堤坝一侧,盖上孕育剂量的60%(一次孕育),再盖上干净无锈的球铁屑,并注意捣实。
5铁水出炉时,要冲入堤坝的另一侧,防止球化剂过早反应。
铁水出尽,等球化反应完毕,扒净渣子,防止回硫。
再在铁水表面撒上孕育剂量的30%(二次孕育),略加搅拌,盖上覆盖剂。
起吊浇注。
6浇注过程尽量平稳迅速,浇注时间不应超过10分钟,以防止球化衰退。
浇注过程中,特别注意做好随流孕育(三次孕育),用量是孕育剂量的10%。
7浇注完毕,把铁水包中的剩余铁水倒尽,扒净渣子,以备再用。
8检测所需的试样、试块所用铁水,应取于浇注后期。
铸造球铁件,球化过程常见问题及解决方案
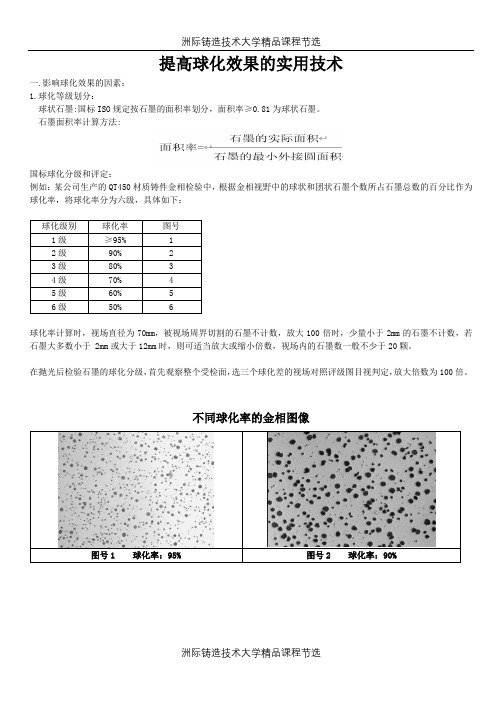
提高球化效果的实用技术一.影响球化效果的因素:1.球化等级划分:球状石墨:国标ISO规定按石墨的面积率划分,面积率≥0.81为球状石墨。
石墨面积率计算方法:国标球化分级和评定:例如:某公司生产的QT450材质铸件金相检验中,根据金相视野中的球状和团状石墨个数所占石墨总数的百分比作为球化率,将球化率分为六级,具体如下:球化率计算时,视场直径为70mm,被视场周界切割的石墨不计数,放大100倍时,少量小于2mm的石墨不计数,若石墨大多数小于 2mm或大于12mm时,则可适当放大或缩小倍数,视场内的石墨数一般不少于20颗。
在抛光后检验石墨的球化分级,首先观察整个受检面,选三个球化差的视场对照评级图目视判定,放大倍数为100倍。
不同球化率的金相图像图号1 球化率:95% 图号2 球化率:90%图号3 球化率:80% 图号4 球化率:70%图号5 球化率:60% 图号6 球化率:50%2.球化可能会出现的问题及解决方案:(1)球化不良:此不良主要体现在炉后成品的残镁分析值低于0.030%(一般标准残镁规格值按照小于0.030%为下限规格值),金相石墨型态一般体现在球状石墨和蠕虫状石墨共存在,或球状石墨、蠕虫状石墨和片状石墨共存在,或蠕虫状石墨和片状石墨共存在,或全部为片状石墨。
控制球化不良的发生,特别注意以下几点:A.添加球化剂重量的核对或喂丝球化线的喂丝长度核对,确保实际加入量与标准规定的相符。
B.三明治球化温度或喂丝温度一般在1480-1530℃。
C.三明治球化反应时间一般控制大于55秒,喂丝球化速度一般控制19-22米/分钟。
D.三明治球化出炉过程确保电炉的先期铁水冲入到球化包的缓冲室,等缓冲室铁水满后,铁水再漫过球化室。
(有很多出炉铁水冲入不当,造成铁水直接冲到球化室的,造成球化反应提前进行,总的球化反应时间短,导致球化不良。
)E.三明治球化需要在球化包之球化室中的球化剂上侧放置覆盖剂,覆盖剂一般为矽钢片,厚度一般控制在0.3-1.0mm,直径或单边长度为10-30mm,要求无油无锈无杂质。
- 1、下载文档前请自行甄别文档内容的完整性,平台不提供额外的编辑、内容补充、找答案等附加服务。
- 2、"仅部分预览"的文档,不可在线预览部分如存在完整性等问题,可反馈申请退款(可完整预览的文档不适用该条件!)。
- 3、如文档侵犯您的权益,请联系客服反馈,我们会尽快为您处理(人工客服工作时间:9:00-18:30)。
B
36
星状(或蜘蛛状)与
短片状石墨混合均7匀 分布
石墨长度的分级
B
8
灰铸铁的孕育处理
孕育是以少量材料加入熔融金属
,促进成核,以改善其组织和性 能的方法。加入的材料称为孕育 剂。常用的孕育剂是FeSi75,熔点 为1300℃,经孕育处理后的铸铁 称孕育铸铁。孕育铸铁的强度、 硬度比普通灰铸铁有显著提高。 孕育铸铁适用于对强度、硬度和 耐磨性要求较高的重要铸件,尤 其是厚大铸件,如床身、凸轮、 凸轮轴、气缸体和气缸套等。灰 铸铁的孕育处理
• (3)铁液含硫量。硫含量较高时,一般采用稀土和镁
含量较高的球化剂,如有条件,可进行脱硫处理。硫含 量较低时,可选用低稀土低镁的稀土硅铁镁球化剂。
• (4)铸件冷却条件。冷却速度较快的金属型铸造条件
下,可选用低稀土球化剂。冷却速度较慢的大型厚断面
铸件可选用钇基重稀土球化剂。
B
24
• 含镁量4%、5%、5.5%属于低镁球化剂,RE在1%-2%之间 ,多用于中频炉熔炼、低硫铁液的球化处理。它具有球化反 应和缓、球化元素易于充分吸收的优点。
B
灰铁的孕育处理
9
孕育处理的作用
• 促进石墨化,减小白口倾向 • 改善石墨形态和分布状况 • 增加共晶团数量,细化基体组织 • 改善断面均匀性
B
10
• Si、Ba、Ca、Al合金孕使育用范剂围的广选泛,择孕育效果十分理想且用
量少。钡是活性极强的元素,低钙钡的硅钡孕育剂,石墨化能 力强,是灰铸铁、球墨铸铁、蠕墨铸铁铸件的首选。
• 含镁量6%、7%属中镁系列球化剂,多用于冲天炉、电炉双 联熔炼,或中频炉熔炼珠光体型铸态球墨铸铁铸件。根据铸 件壁厚和原铁水含硫量,确定合适的球化剂加入量,适用范 围广,球化处理工艺宽泛。
• 高镁系列球化剂,适合冲天炉熔炼、含硫量0.06%-0.09%的 铁液,加入量在1.6%-2.0%之间。
• 低铝球化剂使用于容易产生皮下气孔缺陷的铸件,以及对铁 液含铝量有要求的铸件。
35mm
包装:25公斤塑编袋外加1吨或0.5B吨大袋;吨装塑编袋
32
代理埃肯产品
代理埃肯孕育剂
B
33
代理埃肯球化剂
B
34
增碳剂
B
35
增碳剂使用方法
• 1. 使用5吨以上的电炉,原料单一稳定,我们推 荐分散加入法。根据含碳量的要求按配料比, 将增碳剂与金属炉料随各批料一同加入电炉中 下部位。增碳剂在熔化时不要打渣,否则易裹 在废渣里,影响碳的吸收;
• 孕育剂的加入量
• 根据铸件壁厚、力学性能要求等决定,一般为铁水量
的0.3~0.6%,若要求铸态铁素体基体时,加入量可高
些,为0.8%~1.0%
B
29
球化效果炉前检验
B
30
委托生产的圣泉产品
粒度:0.2-0.7mm, 1-3mm, 3-6mm 包装:25公斤塑编袋
B
31
粒度:1-6mm、2-12mm、3-20mm、5-25mm、5-30mm、10-
• 纯Ce、纯La生产的球化剂,球化处理后铁液纯净夹杂物少、 石墨球圆整。钇基重稀土生产的球化剂适合于大断面铸件, 延缓球化衰退、防止块状石墨。含Sb球化剂用于珠光体型球 墨铸铁。
• 低硅球化剂适用于使用大量回炉料的铸造工厂;镍镁球化剂
则用于高镍奥氏体球墨铸铁。
B
25
常用球化处理方法
• 冲入法
特点:设备简单,操作方便;烟尘、闪光严重,吸收率低( 30~40),广泛应用。 要求:处理包的深度与内径之比在1.5~1.8之间,处理包要预 热到600~800℃,铁液温度应高于1400℃。
B
18
球化级别
B
19
石墨大小分级
B
20
球化和孕育处理
• 国内外常用球化剂类别及使用范围
B
21
B
22
稀土镁硅铁合金
B
23
球化剂的选择
• (1)对铸件铸态组织的要求。 铸态铁素体球墨铸铁选 用低稀土球化剂 ,铸态珠光体球墨铸铁选用含铜或镍
的球化剂。
• (2)铁液中干扰元素的含量。如果干扰元素,诸如钛 、钒、铬、锡、锑、铅、锌等含量较高,须选用稀土含 量较高的球化剂。如果干扰元素含量较低(总量小于 0.1%),可选用纯镁或镁合金球化剂。
• 专门生产的覆盖剂,成分纯净、粒度均匀,更利于获得稳定的 高品质铸件产品。
B
11
孕育剂系列及其特点、适用范围
孕育剂的粒度
• 孕育剂的粒度根据铁液量、铁液温度及孕育 处理方法确定;铁液温度一般不应低于 1400℃
B
14
炉内孕育和包内孕育方法
B
15
瞬时孕育方法
B
16
孕育效果的炉前检验与控制
铁液要求严格,浇注系统复杂,易夹渣,适
于大量流水线生产,低硫铁液 B
27
稀土镁硅铁合金加入量与原铁水含硫量的关系 压力加镁处理加镁量与原铁水含硫量的关系
B
28
孕育处理
• 作用
• 1. 提高球化率,细化石墨,改善 石墨圆整性。 • 2. 减少渗碳体,改变珠光体的相对含量
• 孕育剂
• 除前面介绍的外,还有硅钙(Si60%~65%,Ca25%~30%)、 硅铁-铋等,目前用得最多的仍是FeSi75。
• 稀土孕育剂对降低白口铸铁的脆性有特殊功效。对于高牌号亚 共晶灰铸铁,能够明显改善石墨形态,无需刻意降低含碳量, 也能提高铸铁强度,从而提高机械加工性能。
• 型内孕育块是最节约资源、孕育效果最好的处理方式,浇注系 统加装泡沫陶瓷过滤器,二者构成生产高质量铸件的组合。孕 育块将得到更多铸造企业青睐。
• (3)麻口铸铁 指碳部分以游离碳化铁形式出现,部分 以石墨形式出现,断口灰白相间。
B
3
2. 根据铸铁中石墨形态分类
(1)灰铸铁 石墨呈片状 (2)蠕墨铸铁 石墨呈蠕虫状
B
4
(3)可锻铸铁 石墨呈团絮状 (4)球墨铸铁 石墨呈球状
3. 根据铸铁的化学成分分类
(1)普通铸铁 (2) 合金铸铁
B
5
灰铁的牌号
• 普通灰铸铁 • HT100 • HT150 • HT200 • 孕育铸铁 • HT250 • HT300 • HT350
B
6
片状石墨形态
片状石墨均匀分布
片状与点状石墨聚集 成菊花状分布
部分带尖角状、粗大片状 初生石墨及小片状石墨
点、片状枝晶间石墨 呈无方向分布
短小片状枝晶间石墨 呈有方向B分布
球化剂和孕育剂 基础知识讲义
B
1
铁碳相图
• w(C)<2.06%铸钢
• w(C)>2.06%铸铁
• w(C)<4.26%为亚共 晶铸铁; w(C)=4.26%为共晶 铸铁;w(C)>4.26% ,为过共晶铸铁
• 实际应用的铸铁 w(C)含量在2.0%~ 4.5%的铸铁
• 同样,根据 w(C)=0.76把钢分为 亚共析钢、共析钢 和过共析钢
• 高级脱氧孕育剂,具有强脱氧作用,并且增硅,节约成本,用 于防止气孔和皮下气孔。
• 硅锶孕育剂在灰铸铁中不增加共晶团数,但石墨化效果好,防 止薄壁、厚薄不均铸件白口效果显著。
• 高铝低钙硅铁孕育剂,消除灰铁白口效果显著。含铋硅铁孕育 剂弥补单一加铋效果不明显的缺憾。硅锆孕育剂可细化奥氏体 枝晶提高铸铁强度。孕育剂加锰,可降低多元合金熔点便于在 铁液中扩散和吸收,硅钙钡锰孕育剂的功效在这方面尤为突出
B
2
铸铁的分类
• 铸铁是一系列主要由铁、碳和硅组成的合金的总称。 在这些合金中,碳的质量分数超过了在共晶温度时能 保留在奥氏体固溶体中的量。
• (一) 铸铁的分类
• 1. 根据碳在铸铁中的存在形式分类
• (1)白口铸铁 指碳主要以游离碳化铁形式出现的铸铁 ,断口呈银白色。
• (2)灰铸铁 指碳主要以片状石墨形式出现的铸铁,断 口呈灰色。它是工业中应用最广的铸铁。
盖包法
在冲入法的处理包上部安装一个中间包将
其密封,处理包与中间包之间仅通过浇口
连接。预先将球化剂放在处理包内,然后
用中间包承接铁液,靠由中间包流入处理
包的铁液使处理包处于密闭状态,从而减
少反应烟尘和镁光外逸,提高镁的利用率
B
26
• 压力加镁法
特点:设备费用较高,操作较复杂;纯镁处 理,吸收率高70~80%,稳定球化;灰尘少无 镁光;适用于要求较高,较严格的铸件。
• 三角试样法
• 根据孕育前后白口宽度的差值来决定孕育 剂的加入量;
• 只有孕育前白口宽度达到一定值,孕育后 才能达到足够的强度;
• 通常白口宽度控制在铸件壁厚的1/4~1/7;
• 铁水温度在1400~1430℃时,加入0.1%的 FeSi75可降低白口宽度1mm。
B
17
球铁的牌号
• QT900-2/QT900-2A • QT800-2/QT800-2A • QT700-2/QT700-2A • QT600-3/QT600-3A • QT500-7/QT500-7A • QT450-12/QT450-10 • QT400-18/QT400-18A/QT400-18L/QT400-18AL • QT350-22/QT350-22A/QT350-22L/QT350-22AL
转包法
反应室内装入纯镁或镁焦,转包横卧,接受铁液 ,立起,使铁液反应室与镁反应。镁的吸收 率可达到60~70%,烟尘及镁光较轻,可处理含 硫高达0.15%的铁液。缺点是需专用处理设备