球化退火工艺-方法很多
gcr15轴承钢球化退火工艺

gcr15轴承钢球化退火工艺GCr15轴承钢是一种高强度、高硬度的钢材,广泛应用于制造轴承等高精度机械零件。
由于其材料性质的特殊性,需要进行球化退火处理,以达到更好的加工性能和使用寿命。
本文将从GCr15轴承钢的特性、球化退火工艺的原理和方法、球化退火后的性能及应用等方面进行介绍。
一、GCr15轴承钢的特性GCr15轴承钢是一种具有高温强度、高耐磨性、高弹性模量和良好的抗腐蚀性能的钢材。
其主要成分为碳、铬、锰、硅、磷、硫等元素,其中铬的含量达到了1.5%-2.5%以上。
铬的加入可以增加钢的硬度和耐磨性,使其具有更好的抗腐蚀性能。
同时,硬度的提高也会导致钢的脆性增加,因此需要进行球化退火处理。
二、球化退火工艺的原理和方法球化退火是一种使钢材中的碳元素在钢中形成球状晶粒的热处理工艺。
球化退火的原理是在高温下,钢材中的碳元素会扩散到钢的晶界上,形成一定的厚度。
当温度升高到一定程度时,碳元素会在晶界上形成球状晶粒,使钢的硬度降低,同时也能改善钢的可加工性。
球化退火的过程包括加热、保温和冷却三个阶段。
加热的温度一般为780℃-820℃,保温时间一般为2-4小时,冷却速度不宜过快,一般为自然冷却或慢冷。
球化退火的工艺参数需要根据钢材的具体情况进行调整,以达到最佳的效果。
三、球化退火后的性能及应用球化退火处理后,GCr15轴承钢的硬度降低,但韧性和可加工性得到了改善。
此外,球化退火还能提高钢材的抗疲劳性能和耐磨性能,延长其使用寿命。
因此,球化退火处理是制造高精度机械零件的必要工艺之一。
GCr15轴承钢球化退火后,可以应用于制造各种高精度轴承、齿轮、传动轴等机械零件。
此外,还可以用于制造汽车、航空航天、船舶、机床等领域的重要零件。
球化退火处理的应用范围广泛,对于提高机械零件的精度和使用寿命具有重要意义。
综上所述,GCr15轴承钢球化退火工艺是制造高精度机械零件的必要工艺之一。
球化退火处理能够改善钢材的加工性能和使用寿命,提高其抗疲劳性能和耐磨性能。
球化退火的工艺
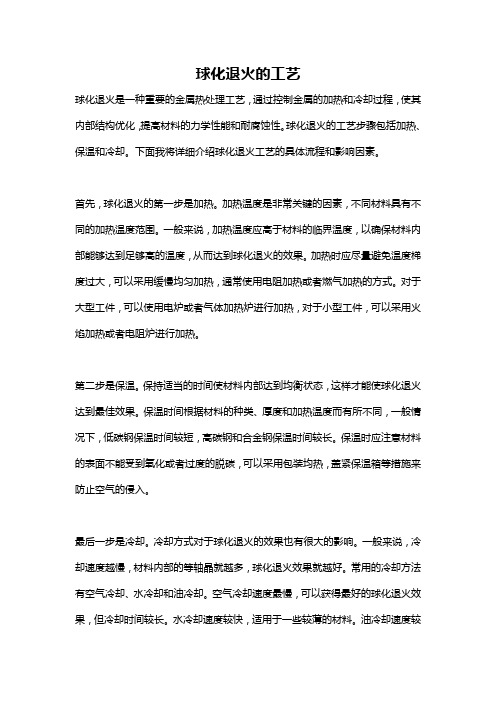
球化退火的工艺球化退火是一种重要的金属热处理工艺,通过控制金属的加热和冷却过程,使其内部结构优化,提高材料的力学性能和耐腐蚀性。
球化退火的工艺步骤包括加热、保温和冷却。
下面我将详细介绍球化退火工艺的具体流程和影响因素。
首先,球化退火的第一步是加热。
加热温度是非常关键的因素,不同材料具有不同的加热温度范围。
一般来说,加热温度应高于材料的临界温度,以确保材料内部能够达到足够高的温度,从而达到球化退火的效果。
加热时应尽量避免温度梯度过大,可以采用缓慢均匀加热,通常使用电阻加热或者燃气加热的方式。
对于大型工件,可以使用电炉或者气体加热炉进行加热,对于小型工件,可以采用火焰加热或者电阻炉进行加热。
第二步是保温。
保持适当的时间使材料内部达到均衡状态,这样才能使球化退火达到最佳效果。
保温时间根据材料的种类、厚度和加热温度而有所不同,一般情况下,低碳钢保温时间较短,高碳钢和合金钢保温时间较长。
保温时应注意材料的表面不能受到氧化或者过度的脱碳,可以采用包装均热,盖紧保温箱等措施来防止空气的侵入。
最后一步是冷却。
冷却方式对于球化退火的效果也有很大的影响。
一般来说,冷却速度越慢,材料内部的等轴晶就越多,球化退火效果就越好。
常用的冷却方法有空气冷却、水冷却和油冷却。
空气冷却速度最慢,可以获得最好的球化退火效果,但冷却时间较长。
水冷却速度较快,适用于一些较薄的材料。
油冷却速度较慢,但可以防止材料的氧化,冷却效果相对较好。
球化退火的工艺参数还包括退火温度、保温时间和冷却速度等。
退火温度要根据材料的化学成分、组织结构和性能要求来确定。
保温时间一般取决于材料的厚度和球化退火温度。
冷却速度也要根据材料的种类、形状和需求来确定。
此外,球化退火还受到金属的硬度、形变程度和表面处理等因素的影响。
总之,球化退火是一种重要的金属热处理工艺,通过控制加热、保温和冷却过程,使金属材料内部的组织结构发生变化,从而提高材料的力学性能和耐腐蚀性。
通过合理选择工艺参数和优化工艺流程,可以获得理想的球化退火效果,满足不同材料的应用需求。
球化退火工艺

球化退火工艺
球化退火工艺是一种常用的金属材料热处理工艺,通常用于改善
材料的机械性能和耐腐蚀性能。
球化退火工艺的基本原理是将金属加
热至一定温度,保持一定时间后,冷却速率适中,使内应力得到消除,晶粒得到细化。
这样可以提高金属的延展性、塑性和硬度,并改善其
耐腐蚀性能。
球化退火工艺适用于多种金属材料,如钢材、铜材、铝材等。
一
般来说,球化退火工艺可以分为两种类型:全球化处理和局部球化处理。
全球化处理是将整个材料进行加热和冷却,常用于改善材料的均
匀性和稳定性。
而局部球化处理则是只对材料的局部区域进行加热和
冷却,常用于处理材料的局部结构不均匀的问题。
球化退火工艺可以在不改变材料基本化学成分的情况下实现材料
性能的改善,被广泛应用于制造业中,如汽车、机械、航空航天、电
子等领域。
球化退火
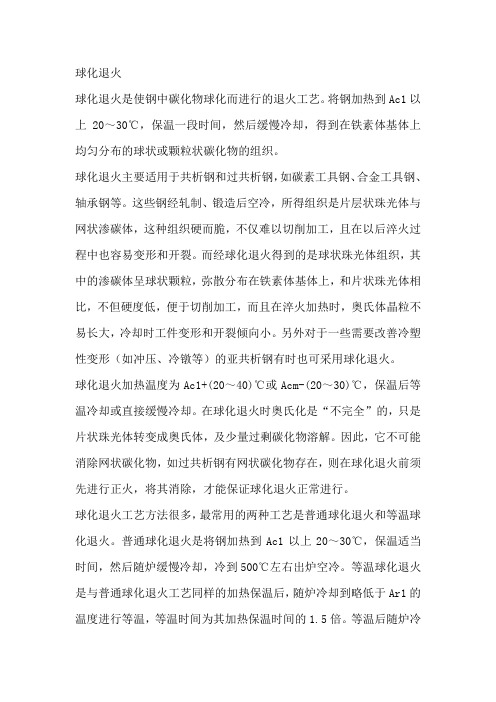
球化退火
球化退火是使钢中碳化物球化而进行的退火工艺。
将钢加热到Ac1以上20~30℃,保温一段时间,然后缓慢冷却,得到在铁素体基体上均匀分布的球状或颗粒状碳化物的组织。
球化退火主要适用于共析钢和过共析钢,如碳素工具钢、合金工具钢、轴承钢等。
这些钢经轧制、锻造后空冷,所得组织是片层状珠光体与网状渗碳体,这种组织硬而脆,不仅难以切削加工,且在以后淬火过程中也容易变形和开裂。
而经球化退火得到的是球状珠光体组织,其中的渗碳体呈球状颗粒,弥散分布在铁素体基体上,和片状珠光体相比,不但硬度低,便于切削加工,而且在淬火加热时,奥氏体晶粒不易长大,冷却时工件变形和开裂倾向小。
另外对于一些需要改善冷塑性变形(如冲压、冷镦等)的亚共析钢有时也可采用球化退火。
球化退火加热温度为Ac1+(20~40)℃或Acm-(20~30)℃,保温后等温冷却或直接缓慢冷却。
在球化退火时奥氏化是“不完全”的,只是片状珠光体转变成奥氏体,及少量过剩碳化物溶解。
因此,它不可能消除网状碳化物,如过共析钢有网状碳化物存在,则在球化退火前须先进行正火,将其消除,才能保证球化退火正常进行。
球化退火工艺方法很多,最常用的两种工艺是普通球化退火和等温球化退火。
普通球化退火是将钢加热到Ac1以上20~30℃,保温适当时间,然后随炉缓慢冷却,冷到500℃左右出炉空冷。
等温球化退火是与普通球化退火工艺同样的加热保温后,随炉冷却到略低于Ar1的温度进行等温,等温时间为其加热保温时间的1.5倍。
等温后随炉冷
至500℃左右出炉空冷。
和普通球化退火相比,球化退火不仅可缩短周期,而且可使球化组织均匀,并能严格地控制退火后的硬度。
球化退火与软化退火
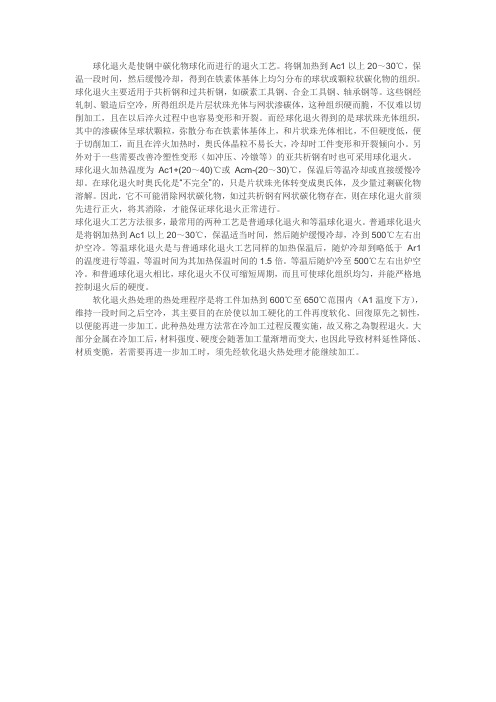
球化退火是使钢中碳化物球化而进行的退火工艺。
将钢加热到Ac1以上20~30℃,保温一段时间,然后缓慢冷却,得到在铁素体基体上均匀分布的球状或颗粒状碳化物的组织。
球化退火主要适用于共析钢和过共析钢,如碳素工具钢、合金工具钢、轴承钢等。
这些钢经轧制、锻造后空冷,所得组织是片层状珠光体与网状渗碳体,这种组织硬而脆,不仅难以切削加工,且在以后淬火过程中也容易变形和开裂。
而经球化退火得到的是球状珠光体组织,其中的渗碳体呈球状颗粒,弥散分布在铁素体基体上,和片状珠光体相比,不但硬度低,便于切削加工,而且在淬火加热时,奥氏体晶粒不易长大,冷却时工件变形和开裂倾向小。
另外对于一些需要改善冷塑性变形(如冲压、冷镦等)的亚共析钢有时也可采用球化退火。
球化退火加热温度为Ac1+(20~40)℃或Acm-(20~30)℃,保温后等温冷却或直接缓慢冷却。
在球化退火时奥氏化是“不完全”的,只是片状珠光体转变成奥氏体,及少量过剩碳化物溶解。
因此,它不可能消除网状碳化物,如过共析钢有网状碳化物存在,则在球化退火前须先进行正火,将其消除,才能保证球化退火正常进行。
球化退火工艺方法很多,最常用的两种工艺是普通球化退火和等温球化退火。
普通球化退火是将钢加热到Ac1以上20~30℃,保温适当时间,然后随炉缓慢冷却,冷到500℃左右出炉空冷。
等温球化退火是与普通球化退火工艺同样的加热保温后,随炉冷却到略低于Ar1的温度进行等温,等温时间为其加热保温时间的1.5倍。
等温后随炉冷至500℃左右出炉空冷。
和普通球化退火相比,球化退火不仅可缩短周期,而且可使球化组织均匀,并能严格地控制退火后的硬度。
软化退火热处理的热处理程序是将工件加热到600℃至650℃范围内(A1温度下方),维持一段时间之后空冷,其主要目的在於使以加工硬化的工件再度软化、回復原先之韧性,以便能再进一步加工。
此种热处理方法常在冷加工过程反覆实施,故又称之為製程退火。
大部分金属在冷加工后,材料强度、硬度会随著加工量渐增而变大,也因此导致材料延性降低、材质变脆,若需要再进一步加工时,须先经软化退火热处理才能继续加工。
中碳碳素结构钢S55C的球化退火工艺
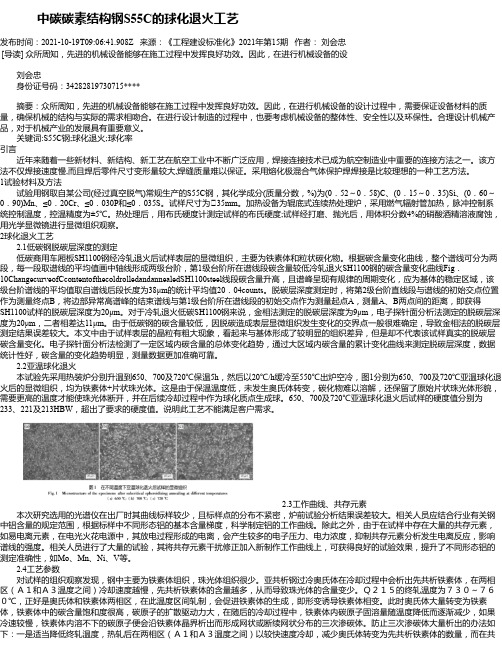
中碳碳素结构钢S55C的球化退火工艺发布时间:2021-10-19T09:06:41.908Z 来源:《工程建设标准化》2021年第15期作者:刘会忠[导读] 众所周知,先进的机械设备能够在施工过程中发挥良好功效。
因此,在进行机械设备的设刘会忠身份证号码:34282819730715****摘要:众所周知,先进的机械设备能够在施工过程中发挥良好功效。
因此,在进行机械设备的设计过程中,需要保证设备材料的质量,确保机械的结构与实际的需求相吻合。
在进行设计制造的过程中,也要考虑机械设备的整体性、安全性以及环保性。
合理设计机械产品,对于机械产业的发展具有重要意义。
关键词:S55C钢;球化退火;球化率引言近年来随着一些新材料、新结构、新工艺在航空工业中不断广泛应用,焊接连接技术已成为航空制造业中重要的连接方法之一。
该方法不仅焊接速度慢,而且焊后零件尺寸变形量较大,焊缝质量难以保证。
采用熔化极混合气体保护焊焊接是比较理想的一种工艺方法。
1试验材料及方法试验用钢取自某公司(经过真空脱气)常规生产的S55C钢,其化学成分(质量分数,%)为(0.52~0.58)C、(0.15~0.35)Si、(0.60~0.90)Mn、≤0.20Cr、≤0.030P和≤0.035S。
试样尺寸为 35mm。
加热设备为辊底式连续热处理炉,采用燃气辐射管加热,脉冲控制系统控制温度,控温精度为±5℃。
热处理后,用布氏硬度计测定试样的布氏硬度;试样经打磨、抛光后,用体积分数4%的硝酸酒精溶液腐蚀,用光学显微镜进行显微组织观察。
2球化退火工艺2.1低碳钢脱碳层深度的测定低碳商用车厢板SH1100钢经冷轧退火后试样表层的显微组织,主要为铁素体和粒状碳化物。
根据碳含量变化曲线,整个谱线可分为两段,每一段取谱线的平均值画中轴线形成两级台阶,第1级台阶所在谱线段碳含量较低冷轧退火SH1100钢的碳含量变化曲线Fig.10ChangecurveofCcontentofthecoldrolledandannealedSH1100steel线段碳含量升高,且谱峰呈现有规律的周期变化,应为基体的稳定区域,该级台阶谱线的平均值取自谱线后段长度为38μm的统计平均值20.04counts。
球化退火介绍

提问者: 映月沙丘- 江湖新秀最佳答案球化退火球化退火是使钢中碳化物球化而进行的退火工艺。
将钢加热到Ac1以上20~30℃,保温一段时间,然后缓慢冷却,得到在铁素体基体上均匀分布的球状或颗粒状碳化物的组织。
球化退火主要适用于共析钢和过共析钢,如碳素工具钢、合金工具钢、轴承钢等。
这些钢经轧制、锻造后空冷,所得组织是片层状珠光体与网状渗碳体,这种组织硬而脆,不仅难以切削加工,且在以后淬火过程中也容易变形和开裂。
而经球化退火得到的是球状珠光体组织,其中的渗碳体呈球状颗粒,弥散分布在铁素体基体上,和片状珠光体相比,不但硬度低,便于切削加工,而且在淬火加热时,奥氏体晶粒不易长大,冷却时工件变形和开裂倾向小。
另外对于一些需要改善冷塑性变形(如冲压、冷镦等)的亚共析钢有时也可采用球化退火。
球化退火加热温度为Ac1+(20~40)℃或Acm-(20~30)℃,保温后等温冷却或直接缓慢冷却。
在球化退火时奥氏化是“不完全”的,只是片状珠光体转变成奥氏体,及少量过剩碳化物溶解。
因此,它不可能消除网状碳化物,如过共析钢有网状碳化物存在,则在球化退火前须先进行正火,将其消除,才能保证球化退火正常进行。
球化退火工艺方法很多,最常用的两种工艺是普通球化退火和等温球化退火。
普通球化退火是将钢加热到Ac1以上20~30℃,保温适当时间,然后随炉缓慢冷却,冷到500℃左右出炉空冷。
等温球化退火是与普通球化退火工艺同样的加热保温后,随炉冷却到略低于Ar1的温度进行等温,等温时间为其加热保温时间的1.5倍。
等温后随炉冷至500℃左右出炉空冷。
和普通球化退火相比,球化退火不仅可缩短周期,而且可使球化组织均匀,并能严格地控制退火后的硬度。
等温球化退火的工艺路线
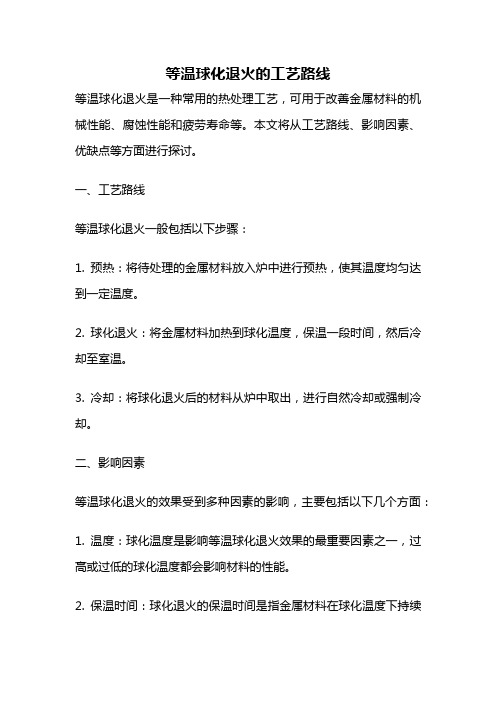
等温球化退火的工艺路线等温球化退火是一种常用的热处理工艺,可用于改善金属材料的机械性能、腐蚀性能和疲劳寿命等。
本文将从工艺路线、影响因素、优缺点等方面进行探讨。
一、工艺路线等温球化退火一般包括以下步骤:1. 预热:将待处理的金属材料放入炉中进行预热,使其温度均匀达到一定温度。
2. 球化退火:将金属材料加热到球化温度,保温一段时间,然后冷却至室温。
3. 冷却:将球化退火后的材料从炉中取出,进行自然冷却或强制冷却。
二、影响因素等温球化退火的效果受到多种因素的影响,主要包括以下几个方面:1. 温度:球化温度是影响等温球化退火效果的最重要因素之一,过高或过低的球化温度都会影响材料的性能。
2. 保温时间:球化退火的保温时间是指金属材料在球化温度下持续保温的时间,保温时间过短或过长都会影响球化效果。
3. 冷却方式:冷却方式包括自然冷却和强制冷却两种,选择合适的冷却方式对材料的性能影响较大。
4. 材料成分:不同成分的金属材料对等温球化退火的响应不同,因此需要针对不同的材料进行相应的处理。
三、优缺点等温球化退火具有以下优点:1. 可以改善金属材料的机械性能,提高其延展性和韧性。
2. 可以提高金属材料的腐蚀性能,减少材料的腐蚀损失。
3. 可以提高金属材料的疲劳寿命,延长材料的使用寿命。
等温球化退火也存在以下缺点:1. 工艺时间较长,需要耗费较多的能源和成本。
2. 球化后的材料容易出现晶界腐蚀等问题。
3. 对于一些特殊材料,球化退火可能无法起到明显的效果。
四、总结等温球化退火是一种常用的热处理工艺,可以改善金属材料的性能,但其效果受到多种因素的影响。
因此,在实际应用中需要根据不同材料的成分和工艺要求选择合适的球化温度、保温时间和冷却方式,以达到最佳的处理效果。
球化退火炉

一、化退火楷述球化退火主要的目的,是希望藉由热处理使钢铁材料内部的层状或网状碳化物凝聚成为球状,使改善钢材之切削性能及加工塑性,特别是高碳的工具钢,轴承钢更是需要此种退火处理。
常见的球化退火处理包括:(1)在钢材A1温度的上方、下方反覆加热、冷却数次,使A1变态所析出的雪明碳铁,继续附著成长在上述球化的碳化物上;(2)加热至钢材A3或Acm温度上方,始碳化物完全固溶於沃斯田体后急冷,再依上述方法进行球化处理。
使碳化物球化,尚可增加钢材的淬火后韧性、防止淬裂,亦可改善钢材的淬火回火后机械性质、提高钢材的使用寿命。
二、球化退火(spheroidizeannealing)将钢中珠光体内的片层状渗碳体和先共析渗碳体转化为均匀分布于铁素体基体上的球状或粒状碳化物以获得球状珠光体的热处理方法,是不完全退火的一种。
因为片状渗碳体表面积大,处于不稳定状态,硬度比较高,切削加工后零件的表面粗糙度高,淬火过程中工件容易变形和开裂。
而球状碳化物有最小界面,能量最低,处于稳定的平衡状态,硬度低,切削性能好,韧性高,冷加工能力大,淬火时工件不易变形和开裂。
因此,碳素工具钢、一部分合金工具钢和滚珠轴承钢钢材都应经过球化退火才能交货。
根据钢种和退火目的,球化退火可分以下几种:(1)普通球化退火,即将钢加热到730~740℃保温足够时间,然后以小于20℃/h的速度缓冷到650℃出炉。
这种退火工艺适用于共析成分附近的碳素工具钢。
(2)周期球化退火,也叫循环退火。
它是在A、点附近的温度反复进行加热和冷却,一般进行3~4个周期,使片状珠光体在几次溶解一析出的反复过程中,碳化物得以球化。
该工艺生产周期较长,操作不方便,难以控制,适用于片状珠光体比较严重的钢。
(3)等温球化退火。
一般加热到800±l0℃,保温后快冷到700±10℃(A1附近)再进行较长时间保温,之后,以30~50℃/h的速度冷却到600℃出炉。
一般轴承钢多采用此工艺。
热处理工艺介绍——表面淬火、退火工艺、正火工

表面淬火•钢的表面淬火有些零件在工件时在受扭转和弯曲等交变负荷、冲击负荷的作用下,它的表面层承受着比心部更高的应力。
在受摩擦的场合,表面层还不断地被磨损,因此对一些零件表面层提出高强度、高硬度、高耐磨性和高疲劳极限等要求,只有表面强化才能满足上述要求。
由于表面淬火具有变形小、生产率高等优点,因此在生产中应用极为广泛。
根据供热方式不同,表面淬火主要有感应加热表面淬火、火焰加热表面淬火、电接触加热表面淬火等。
•感应加热表面淬火感应加热就是利用电磁感应在工件内产生涡流而将工件进行加热。
感应加热表面淬火与普通淬火比具有如下优点:1。
热源在工件表层,加热速度快,热效率高2。
工件因不是整体加热,变形小3。
工件加热时间短,表面氧化脱碳量少4。
工件表面硬度高,缺口敏感性小,冲击韧性、疲劳强度以及耐磨性等均有很大提高。
有利于发挥材料地潜力,节约材料消耗,提高零件使用寿命5。
设备紧凑,使用方便,劳动条件好6。
便于机械化和自动化7。
不仅用在表面淬火还可用在穿透加热与化学热处理等。
•感应加热的基本原理将工件放在感应器中,当感应器中通过交变电流时,在感应器周围产生与电流频率相同的交变磁场,在工件中相应地产生了感应电动势,在工件表面形成感应电流,即涡流。
这种涡流在工件的电阻的作用下,电能转化为热能,使工件表面温度达到淬火加热温度,可实现表面淬火。
•感应表面淬火后的性能1。
表面硬度:经高、中频感应加热表面淬火的工件,其表面硬度往往比普通淬火高2~3个单位(HRC)。
2。
耐磨性:高频淬火后的工件耐磨性比普通淬火要高。
这主要是由于淬硬层马氏体晶粒细小,碳化物弥散度高,以及硬度比较高,表面的高的压应力等综合的结果。
3。
疲劳强度:高、中频表面淬火使疲劳强度大为提高,缺口敏感性下降。
对同样材料的工件,硬化层深度在一定范围内,随硬化层深度增加而疲劳强度增加,但硬化层深度过深时表层是压应力,因而硬化层深度增打疲劳强度反而下降,并使工件脆性增加。
42CrMo材料球化退火工艺
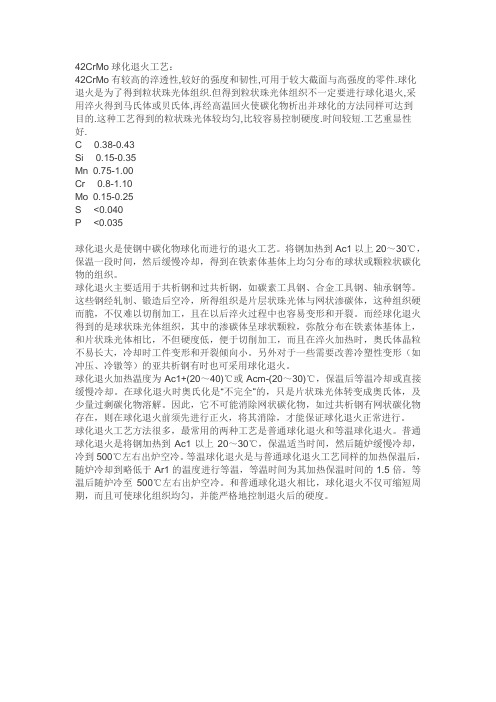
42CrMo球化退火工艺:42CrMo有较高的淬透性,较好的强度和韧性,可用于较大截面与高强度的零件.球化退火是为了得到粒状珠光体组织.但得到粒状珠光体组织不一定要进行球化退火,采用淬火得到马氏体或贝氏体,再经高温回火使碳化物析出并球化的方法同样可达到目的.这种工艺得到的粒状珠光体较均匀,比较容易控制硬度.时间较短.工艺重显性好.C 0.38-0.43Si 0.15-0.35Mn 0.75-1.00Cr 0.8-1.10Mo 0.15-0.25S <0.040P <0.035球化退火是使钢中碳化物球化而进行的退火工艺。
将钢加热到Ac1以上20~30℃,保温一段时间,然后缓慢冷却,得到在铁素体基体上均匀分布的球状或颗粒状碳化物的组织。
球化退火主要适用于共析钢和过共析钢,如碳素工具钢、合金工具钢、轴承钢等。
这些钢经轧制、锻造后空冷,所得组织是片层状珠光体与网状渗碳体,这种组织硬而脆,不仅难以切削加工,且在以后淬火过程中也容易变形和开裂。
而经球化退火得到的是球状珠光体组织,其中的渗碳体呈球状颗粒,弥散分布在铁素体基体上,和片状珠光体相比,不但硬度低,便于切削加工,而且在淬火加热时,奥氏体晶粒不易长大,冷却时工件变形和开裂倾向小。
另外对于一些需要改善冷塑性变形(如冲压、冷镦等)的亚共析钢有时也可采用球化退火。
球化退火加热温度为Ac1+(20~40)℃或Acm-(20~30)℃,保温后等温冷却或直接缓慢冷却。
在球化退火时奥氏化是“不完全”的,只是片状珠光体转变成奥氏体,及少量过剩碳化物溶解。
因此,它不可能消除网状碳化物,如过共析钢有网状碳化物存在,则在球化退火前须先进行正火,将其消除,才能保证球化退火正常进行。
球化退火工艺方法很多,最常用的两种工艺是普通球化退火和等温球化退火。
普通球化退火是将钢加热到Ac1以上20~30℃,保温适当时间,然后随炉缓慢冷却,冷到500℃左右出炉空冷。
等温球化退火是与普通球化退火工艺同样的加热保温后,随炉冷却到略低于Ar1的温度进行等温,等温时间为其加热保温时间的1.5倍。
低碳钢丝球化退火工艺的探讨及应用
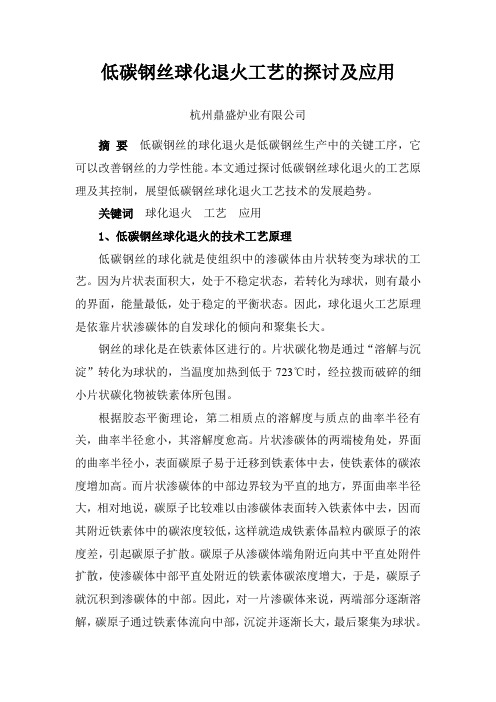
低碳钢丝球化退火工艺的探讨及应用杭州鼎盛炉业有限公司摘要低碳钢丝的球化退火是低碳钢丝生产中的关键工序,它可以改善钢丝的力学性能。
本文通过探讨低碳钢丝球化退火的工艺原理及其控制,展望低碳钢丝球化退火工艺技术的发展趋势。
关键词球化退火工艺应用1、低碳钢丝球化退火的技术工艺原理低碳钢丝的球化就是使组织中的渗碳体由片状转变为球状的工艺。
因为片状表面积大,处于不稳定状态,若转化为球状,则有最小的界面,能量最低,处于稳定的平衡状态。
因此,球化退火工艺原理是依靠片状渗碳体的自发球化的倾向和聚集长大。
钢丝的球化是在铁素体区进行的。
片状碳化物是通过“溶解与沉淀”转化为球状的,当温度加热到低于723℃时,经拉拨而破碎的细小片状碳化物被铁素体所包围。
根据胶态平衡理论,第二相质点的溶解度与质点的曲率半径有关,曲率半径愈小,其溶解度愈高。
片状渗碳体的两端棱角处,界面的曲率半径小,表面碳原子易于迁移到铁素体中去,使铁素体的碳浓度增加高。
而片状渗碳体的中部边界较为平直的地方,界面曲率半径大,相对地说,碳原子比较难以由渗碳体表面转入铁素体中去,因而其附近铁素体中的碳浓度较低,这样就造成铁素体晶粒内碳原子的浓度差,引起碳原子扩散。
碳原子从渗碳体端角附近向其中平直处附件扩散,使渗碳体中部平直处附近的铁素体碳浓度增大,于是,碳原子就沉积到渗碳体的中部。
因此,对一片渗碳体来说,两端部分逐渐溶解,碳原子通过铁素体流向中部,沉淀并逐渐长大,最后聚集为球状。
对于低碳钢而言,球化处理使渗碳体呈粒状,与片状相比,它具有较低的流变应力和屈服强度,因而具有较高的均匀变型量和总变型量;同时,它还具有较高的断裂强度和解理强度,因而在冷加工时不易开裂。
球化处理改善了钢丝的综合力学性能,显著提高了钢丝的冷顶锻工艺性能。
2、低碳钢丝球化退火的应用众所周知:钢铁材料的性能取决于内部组织结构,组织结构取决于成分、冶炼、热加工、冷加工,特别是热处理工艺。
要选择合理、高效、经济的热处理工艺,必须了解材料性能与组织结构,显微组织与热处理工艺之间的关系,以及显微组织的种类和热处理的基本原理。
45钢 等温球化退火
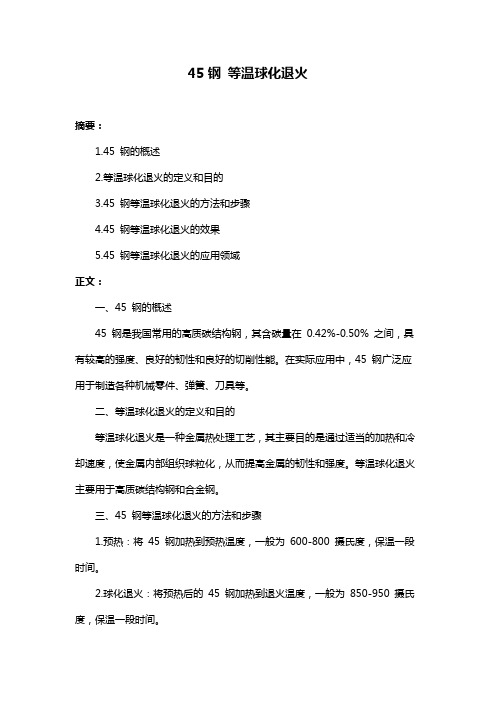
45钢等温球化退火
摘要:
1.45 钢的概述
2.等温球化退火的定义和目的
3.45 钢等温球化退火的方法和步骤
4.45 钢等温球化退火的效果
5.45 钢等温球化退火的应用领域
正文:
一、45 钢的概述
45 钢是我国常用的高质碳结构钢,其含碳量在0.42%-0.50% 之间,具有较高的强度、良好的韧性和良好的切削性能。
在实际应用中,45 钢广泛应用于制造各种机械零件、弹簧、刀具等。
二、等温球化退火的定义和目的
等温球化退火是一种金属热处理工艺,其主要目的是通过适当的加热和冷却速度,使金属内部组织球粒化,从而提高金属的韧性和强度。
等温球化退火主要用于高质碳结构钢和合金钢。
三、45 钢等温球化退火的方法和步骤
1.预热:将45 钢加热到预热温度,一般为600-800 摄氏度,保温一段时间。
2.球化退火:将预热后的45 钢加热到退火温度,一般为850-950 摄氏度,保温一段时间。
3.等温处理:将球化退火后的45 钢放入等温炉中,在规定的温度下进行等温处理。
4.冷却:等温处理后的45 钢进行空冷或水冷,使其冷却到室温。
四、45 钢等温球化退火的效果
经过等温球化退火处理的45 钢,其内部组织形成球粒状,可以显著提高其韧性和强度,同时保持良好的切削性能。
一种3cr2w8v热锻模具的等温球化退火工艺
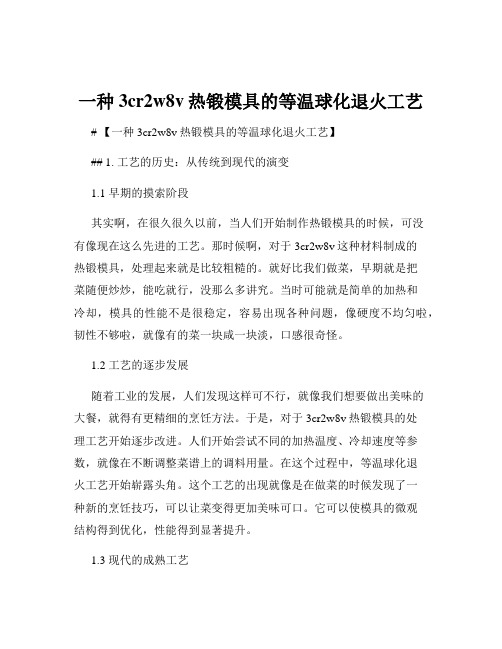
一种3cr2w8v热锻模具的等温球化退火工艺# 【一种3cr2w8v热锻模具的等温球化退火工艺】## 1. 工艺的历史:从传统到现代的演变1.1 早期的摸索阶段其实啊,在很久很久以前,当人们开始制作热锻模具的时候,可没有像现在这么先进的工艺。
那时候啊,对于3cr2w8v这种材料制成的热锻模具,处理起来就是比较粗糙的。
就好比我们做菜,早期就是把菜随便炒炒,能吃就行,没那么多讲究。
当时可能就是简单的加热和冷却,模具的性能不是很稳定,容易出现各种问题,像硬度不均匀啦,韧性不够啦,就像有的菜一块咸一块淡,口感很奇怪。
1.2 工艺的逐步发展随着工业的发展,人们发现这样可不行,就像我们想要做出美味的大餐,就得有更精细的烹饪方法。
于是,对于3cr2w8v热锻模具的处理工艺开始逐步改进。
人们开始尝试不同的加热温度、冷却速度等参数,就像在不断调整菜谱上的调料用量。
在这个过程中,等温球化退火工艺开始崭露头角。
这个工艺的出现就像是在做菜的时候发现了一种新的烹饪技巧,可以让菜变得更加美味可口。
它可以使模具的微观结构得到优化,性能得到显著提升。
1.3 现代的成熟工艺到了现在,这种3cr2w8v热锻模具的等温球化退火工艺已经相当成熟了。
就像我们现在有了标准化的菜谱,只要按照步骤来,就能做出一道色香味俱全的菜肴。
现在的工艺在温度控制、时间把握等方面都非常精准,能够根据不同的需求生产出性能优良的热锻模具。
## 2. 制作过程:一场微观世界的奇妙之旅2.1 准备工作在开始这个等温球化退火工艺之前啊,就像我们做饭之前要准备食材一样,得先把3cr2w8v热锻模具的毛坯准备好。
这个毛坯要保证没有明显的缺陷,就像我们挑菜的时候要挑新鲜的一样。
然后把它放在合适的设备里,这个设备就像是我们的厨房炉灶一样,用来给模具毛坯加热。
2.2 加热阶段接下来就是加热啦。
这个过程可不能马虎,就像煎牛排的时候火候很重要一样。
要把模具毛坯加热到一个特定的温度范围,这个温度就像是煎牛排时的合适温度。
球化退火
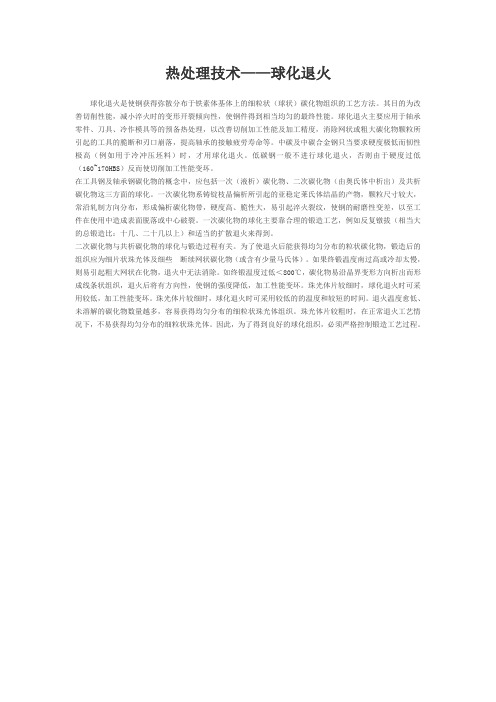
热处理技术——球化退火球化退火是使钢获得弥散分布于铁素体基体上的细粒状(球状)碳化物组织的工艺方法。
其目的为改善切削性能,减小淬火时的变形开裂倾向性,使钢件得到相当均匀的最终性能。
球化退火主要应用于轴承零件、刀具、冷作模具等的预备热处理,以改善切削加工性能及加工精度,消除网状或粗大碳化物颗粒所引起的工具的脆断和刃口崩落,提高轴承的接触疲劳寿命等。
中碳及中碳合金钢只当要求硬度极低而韧性极高(例如用于冷冲压坯料)时,才用球化退火。
低碳钢一般不进行球化退火,否则由于硬度过低(160~170HBS)反而使切削加工性能变坏。
在工具钢及轴承钢碳化物的概念中,应包括一次(液析)碳化物、二次碳化物(由奥氏体中析出)及共析碳化物这三方面的球化。
一次碳化物系铸锭枝晶偏析所引起的亚稳定莱氏体结晶的产物,颗粒尺寸较大,常沿轧制方向分布,形成偏析碳化物带,硬度高、脆性大,易引起淬火裂纹,使钢的耐磨性变差,以至工件在使用中造成表面脱落或中心破裂。
一次碳化物的球化主要靠合理的锻造工艺,例如反复镦拔(相当大的总锻造比:十几、二十几以上)和适当的扩散退火来得到。
二次碳化物与共析碳化物的球化与锻造过程有关。
为了使退火后能获得均匀分布的粒状碳化物,锻造后的组织应为细片状珠光体及细些断续网状碳化物(或含有少量马氏体)。
如果终锻温度南过高或冷却太慢,则易引起粗大网状在化物,退火中无法消除。
如终锻温度过低<800℃,碳化物易沿晶界变形方向析出而形成线条状组织,退火后将有方向性,使钢的强度降低,加工性能变坏。
珠光体片较细时,球化退火时可采用较低,加工性能变坏。
珠光体片较细时,球化退火时可采用较低的的温度和较短的时间。
退火温度愈低、未溶解的碳化物数量越多,容易获得均匀分布的细粒状珠光体组织。
珠光体片较粗时,在正常退火工艺情况下,不易获得均匀分布的细粒状珠光体。
因此,为了得到良好的球化组织,必须严格控制锻造工艺过程。
过共析钢的等温球化退火工艺
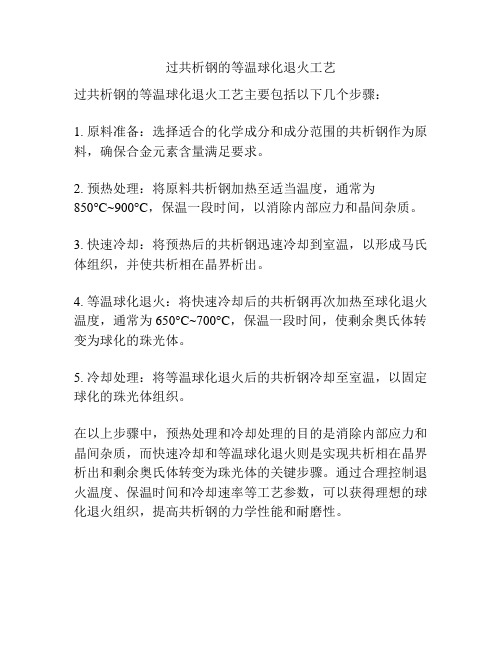
过共析钢的等温球化退火工艺
过共析钢的等温球化退火工艺主要包括以下几个步骤:
1. 原料准备:选择适合的化学成分和成分范围的共析钢作为原料,确保合金元素含量满足要求。
2. 预热处理:将原料共析钢加热至适当温度,通常为
850°C~900°C,保温一段时间,以消除内部应力和晶间杂质。
3. 快速冷却:将预热后的共析钢迅速冷却到室温,以形成马氏体组织,并使共析相在晶界析出。
4. 等温球化退火:将快速冷却后的共析钢再次加热至球化退火温度,通常为650°C~700°C,保温一段时间,使剩余奥氏体转变为球化的珠光体。
5. 冷却处理:将等温球化退火后的共析钢冷却至室温,以固定球化的珠光体组织。
在以上步骤中,预热处理和冷却处理的目的是消除内部应力和晶间杂质,而快速冷却和等温球化退火则是实现共析相在晶界析出和剩余奥氏体转变为珠光体的关键步骤。
通过合理控制退火温度、保温时间和冷却速率等工艺参数,可以获得理想的球化退火组织,提高共析钢的力学性能和耐磨性。
六角合金工具钢s2的球化退火工艺
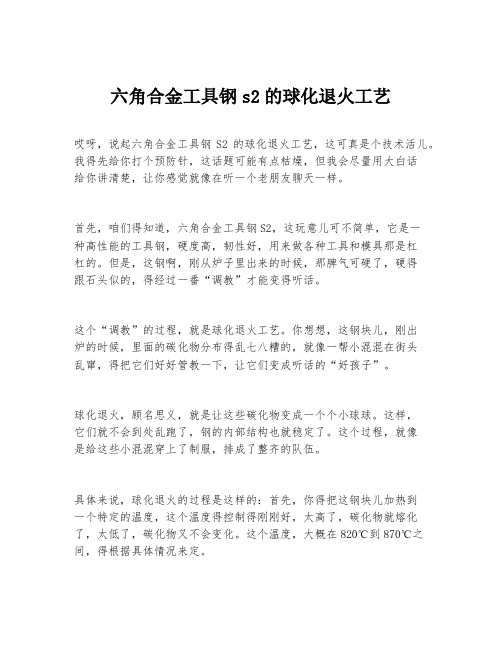
六角合金工具钢s2的球化退火工艺哎呀,说起六角合金工具钢S2的球化退火工艺,这可真是个技术活儿。
我得先给你打个预防针,这话题可能有点枯燥,但我会尽量用大白话给你讲清楚,让你感觉就像在听一个老朋友聊天一样。
首先,咱们得知道,六角合金工具钢S2,这玩意儿可不简单,它是一种高性能的工具钢,硬度高,韧性好,用来做各种工具和模具那是杠杠的。
但是,这钢啊,刚从炉子里出来的时候,那脾气可硬了,硬得跟石头似的,得经过一番“调教”才能变得听话。
这个“调教”的过程,就是球化退火工艺。
你想想,这钢块儿,刚出炉的时候,里面的碳化物分布得乱七八糟的,就像一帮小混混在街头乱窜,得把它们好好管教一下,让它们变成听话的“好孩子”。
球化退火,顾名思义,就是让这些碳化物变成一个个小球球。
这样,它们就不会到处乱跑了,钢的内部结构也就稳定了。
这个过程,就像是给这些小混混穿上了制服,排成了整齐的队伍。
具体来说,球化退火的过程是这样的:首先,你得把这钢块儿加热到一个特定的温度,这个温度得控制得刚刚好,太高了,碳化物就熔化了,太低了,碳化物又不会变化。
这个温度,大概在820℃到870℃之间,得根据具体情况来定。
然后,你得让这钢块儿在这个温度下待上一段时间,让碳化物慢慢变成球状。
这个过程,就像是给小混混们上思想教育课,让他们慢慢改变。
接下来,就是冷却了。
你得让这钢块儿慢慢冷却,不能急,急了,碳化物又会变回原来的样子。
这个过程,就像是让小混混们慢慢适应新的生活,不能一下子逼得太紧。
最后,等钢块儿冷却到室温,这球化退火就算完成了。
这时候,你再去看这钢块儿,里面的碳化物已经变成了一个个小球球,整整齐齐的,就像一队队训练有素的士兵。
这个过程,虽然听起来简单,但实际操作起来,那可是需要相当的技术和经验的。
温度控制不好,时间掌握不好,都会影响到最终的效果。
所以,这六角合金工具钢S2的球化退火工艺,虽然听起来有点枯燥,但其实是一门很深的学问。
就像生活中的很多事情一样,看起来简单,做起来难。
- 1、下载文档前请自行甄别文档内容的完整性,平台不提供额外的编辑、内容补充、找答案等附加服务。
- 2、"仅部分预览"的文档,不可在线预览部分如存在完整性等问题,可反馈申请退款(可完整预览的文档不适用该条件!)。
- 3、如文档侵犯您的权益,请联系客服反馈,我们会尽快为您处理(人工客服工作时间:9:00-18:30)。
球化退火工艺方法很多,最常用的两种工艺是普通球化退火和等温球化退火。
普通球化退火是将钢加热到Ac1以上20~30℃,保温适当时间,然后随炉缓慢冷却,冷到500℃左右出炉空冷。
等温球化退火是与普通球化退火工艺同样的加热保温后,随炉冷却到略低于Ar1的温度进行等温,等温时间为其加热保温时间的1.5倍。
等温后随炉冷至500℃左右出炉空冷。
和普通球化退火相比,等温球化退火不仅可缩短周期,而且可使球化组织均匀,并能严格地控制退火后的硬度。
球化退火主要用于过共析的碳钢及合金工具钢(如制造刃具,量具,模具所用的钢种)。
其主要目的在于降低硬度,改善切削加工性,并为以后淬火作好准备。
这种工艺有利于塑性加工和切削加工,还能提高机械韧性。
尤其对于轴承钢、工具钢等钢种而言,如在淬火前实施球化退火,即可获得下列效果:硬度分为:①划痕硬度。
主要用于比较不同矿物的软硬程度,方法是选一根一端硬一端软的棒,将被测材料沿棒划过,根据出现划痕的位置确定被测材料的软硬。
定性地说,硬物体划出的划痕长,软物体划出的划痕短。
②压入硬度。
主要用于金属材料,方法是用一定的载荷将规定的压头压入被测材料,以材料表面局部塑性变形的大小比较被测材料的软硬。
由于压头、载荷以及载荷持续时间的不同,压入硬度有多种,主要是布氏硬度、洛氏硬度、维氏硬度和显微硬度等几种。
③回跳硬度。
主要用于金属材料,方法是使一特制的小锤从一定高度自由下落冲击被测材料的试样,并以试样在冲击过程中储存(继而释放)应变能的多少(通过小锤的回跳高度测定)确定材料的硬度。
2硬度分类划痕硬度1722年,法国的R.-A.F.de列奥米尔首先提出了极粗糙的划痕硬度测定法。
此法是以适当的力使被和材料在一根由一端硬渐变到另一端软的金属棒上划过,根据棒上出现划痕的位置确定被测材料的硬度。
1822年,F.莫斯以十种矿物的划痕硬度作为标准,定出十个硬度等级,称为莫氏硬度。
十种矿物的莫氏硬度级依次为:金刚石(10),刚玉(9),黄玉(8),石英(7),长石(6),磷灰石(5),萤石(4),方解石(3),石膏(2),滑石(1)。
其中金刚石最硬,滑石最软。
莫氏硬度标准是随意定出的,不能精确地用于确定材料的硬度,例如10级和9级之间的实际硬度差就远大于2级和1级之间的实际硬度差。
但这种分级对于矿物学工作者野外作业是很有用的。
压入硬度用一定的载荷将规定的压头压入被测材料,根据材料表面局部塑性变形的程度比较被测材料的软硬,材料越硬,塑性变形越小。
压入硬度在工程技术中有广泛的用途。
压头有多种,如一定直径的钢球、金刚石圆锥、金刚石四棱锥等。
载荷范围为几克力至几吨力(即几十毫牛顿至几万牛顿)。
压入硬度对载荷作用于被测材料表面的持续时间也有规定。
主要的压入硬度有布氏硬度、洛氏硬度、维氏硬度和显微硬度等。
洛氏硬度这种硬度测定法是美国的S.P.洛克韦尔于1919年提出的,它基本上克服了布氏测定法的上述不足。
洛氏硬度所采用的压头是锥角为120°的金刚石圆锥或直径为1/16英寸(1英寸等于25.4毫米)的钢球,并用压痕深度作为标定硬度值的依据。
测量时,总载荷分初载荷和主载荷(总载荷减去初载荷)两次施加,初载荷一般选用10千克力,加至总载荷后卸去主载荷,并以这时的压痕深度来衡量材料的硬度。
洛氏硬度记为HR,所测数值写在HB后,洛氏硬度值计算公式为:式中h表示塑性变形压痕深度(毫米);k是规定的常量;分母中的0.002(毫米)是每洛氏硬度单位对应的压痕深度。
对应于金刚石圆锥压头的k=0.20(毫米),对应于钢球压头的k=0.26(毫米)。
为了适应极宽阔的测量范围,可采用改变载荷和更换压头两种办法。
不同的载荷和压头组成不同的洛氏硬度标尺,常用的标尺有A、B、C三种。
标尺B用于中等硬度的金属材料,如退火的低碳钢和中碳钢、黄铜、青铜和硬铝合金;压头为直径1/16英寸的钢球;载荷为100千克力。
其标尺范围是由HRB0到HRB100,硬度高于HRB100时钢球可能被压扁。
标尺C用于硬度高于HRB100的材料,如淬火钢、各种淬火和回火合金钢。
压头为顶角120°的金刚石圆锥;载荷为150千克力。
标尺C的使用范围是从HRC20到HRC70,标尺B和C是洛氏硬度的标准标尺。
标尺A用于钨、硬质合金及其他硬材料,还用于淬硬的薄钢带。
由于大载荷容易损坏金刚石压头,所以载荷改为60千克力。
标尺A是所有洛氏硬度标尺中唯一能在退火黄铜直到硬质合金这样广阔的硬度范围内使用的标尺。
洛氏硬度试验采用三种试验力,三种压头,它们共有9种组合,对应于洛氏硬度的9个标尺。
这9个标尺的应用涵盖了几乎所有常用的金属材料。
最常用标尺是HRC、HRB和HRF,其中HRC标尺用于测试淬火钢、回火钢、调质钢和部分不锈钢。
这是金属加工行业应用最多的硬度试验方法。
HRB标尺用于测试各种退火钢、正火钢、软钢、部分不锈钢及较硬的铜合金。
HRF标尺用于测试纯铜、较软的铜合金和硬铝合金。
HRA标尺尽管也可用于大多数黑色金属,但是实际应用上一般只限于测试硬质合金和薄硬钢带材料。
表面洛氏硬度试验采用三种试验力,两种压头,它们有6种组合,对应于表面洛氏硬度的6个标尺。
表面洛氏硬度试验是对洛氏硬度试验的一种补充,在采用洛氏硬度试验时,当遇到材料较薄,试样较小,表面硬化层较浅或测试表面镀覆层时,就应改用表面洛氏硬度试验。
这时采用与洛氏硬度试验相同的压头,采用只有洛氏硬度试验几分之一大小的试验力,就可以在上述试样上得到有效的硬度试验结果。
表面洛氏硬度的N标尺适用于类似洛氏硬度的HRC、HRA和HRD测试的材料;T标尺适用于类似洛氏硬度的HRB、HRF和HRG测试的材料。
HRC标尺的使用范围是20~70HRC,当硬度值小于20HRC时,因为压头的圆锥部分压入太多,灵敏度下降,这时应改用HRB标尺。
尽管HRC标尺被规定的上限值为70HRC,但是当试样硬度大于67HRC时,压头尖端承受的压力过大,金刚石容易损坏,压头寿命会大大缩短,因此一般应改用HRA标尺。
HRA标尺的使用范围是20-88HRA,由美国标准ASTME140可以获得以下换算关系:27HRA≈30HRB60HRA≈100HRB≈20HRC85.6HRA≈68HRC可见,HRA标尺的测试范围涵盖了从软钢(HRB)、硬钢(HRC)到硬质合金的硬度范围。
然而,事实上HRA标尺很少用于测试软钢,主要用于测试薄硬钢板、深层渗碳钢和硬质合金。
在硬质合金方面,由于技术进步,有些材料硬度已达到93-94HRA,这已超出标准规定。
工程上超出HRA高端的测量范围已成为惯例。
HRA 标尺有一个特殊用途。
在使用洛氏硬度计测试钢试样时,如果不知试样是软钢还是硬钢,可先用HRA标尺试测一下,当硬度值小于60HRA时可改用HRB标尺,当硬度值大于60HRA时可改用HRC标尺。
HRB标尺的使用范围是20~100HRB,当硬度值低于20HRB时,由于钢球的压入深度过大,金属蠕变加剧,试样在试验力作用下的变形时间延长,测试值准确度降低,此时应改用HRF标尺。
当硬度值大于100HRB时,因为钢球压入深度过浅,灵敏度降低,精度下降,此时应改用HRC标尺。
在使用HRB标尺测试钢试样时,一个特别值得注意的地方是:当预先不知道试样是软钢还是硬钢时,决不可使用HRB标尺做测试,因为用钢球压头误测了淬火钢,钢球就可能会变形,钢球压头就会损坏,这是钢球压头损坏的主要原因。
遇到这种情况时应先用金刚石压头,用HRA标尺测试一下,再决定是用HRB还是用HRC。
HRF标尺的使用范围是60~100HRF。
HRF标尺是国外使用较多的一个标尺,它是测试纯铜和较软的铜合金材料很好的检测手段。
但是在我国,也存在标准硬度块短缺的问题,它的应用也受到了限制。
HRG标尺适用于HRB值接近100的材料,对于铍青铜、磷青铜、可锻铸铁这些硬度范围介于HRB标尺的高端和HRC标尺低端的材料,如果改用HRG标尺,就可以大大改善测试的灵敏度,提高测试精度。
其他1.HRC含意是洛氏硬度C标尺,2.HRC和HB在生产中的应用都很广泛3.HRC适用范围HRC20--67,相当于HB225--650若硬度高于此范围则用洛氏硬度A标尺HRA。
若硬度低于此范围则用洛氏硬度B标尺HRB。
布氏硬度上限值HB650,不能高于此值。
4.洛氏硬度计C标尺之压头为顶角120度的金刚石圆锥,试验载荷为一确定值,中国标准是150公斤力。
布氏硬度计之压头为淬硬钢球(HBS)或硬质合金球(HBW),试验载荷随球直径不同而不同,从3000到31.25公斤力。
5.洛氏硬度压痕很小,测量值有局部性,须测数点求平均值,适用成品和薄片,归于无损检测一类。
布氏硬度压痕较大,测量值准,不适用成品和薄片,一般不归于无损检测一类。
6.洛氏硬度的硬度值是一无名数,没有单位。
(因此习惯称洛氏硬度为多少度是不正确的。
)布氏硬度的硬度值有单位,且和抗拉强度有一定的近似关系。
7.洛氏硬度直接在表盘上显示、也可以数字显示,操作方便,快捷直观,适用于大量生产中。
布氏硬度需要用显微镜测量压痕直径,然后查表或计算,操作较繁琐。
8.在一定条件下,HB与HRC可以查表互换。
其心算公式可大概记为:1HRC≈10HB。
布氏硬度布氏硬度是瑞典工程师J.A.布里涅耳于1900年提出的。
它在工程技术特别是机械和冶金工业中广泛使用。
布氏硬度的测量方法是用规定大小的载荷P,把直径为D的钢球压入被测材料表面,持续规定的时间后卸载,用载荷值(千克力,1千克力等于9.80665牛顿)和压痕面积(平方毫米)之比定义硬度值。
布氏硬度HB的计算式为:式中d为压痕的直径。
1908年德国的E.迈耶尔指出,若要使不同直径的钢球在同一材料上测得同样的硬度,就需要改变载荷值,使压痕保持几何相似,相似条件为:式中P1、D1和P2、D2分别为两组测量条件中的载荷值和钢球直径。
若D=10毫米,P=3000千克力,载荷持续时间10秒,则硬度数可直接写在布氏硬度符号后面,例如HB250。
若是其他测定条件,则应将条件用小号字写在布氏硬度符号后面,例如,HB5/250/30100表示在D=5毫米、P=250千克力、载荷持续时间为30秒的条件下测得布氏硬度数为100。
布氏硬度测定法只能在硬度不高于HB450的情况下使用。
因为太硬的材料会使钢球明显变形。
布氏硬度测定法比较费时。
为了在测定时得到清晰的压痕,试样必须经过表面准备和打磨等处理。
在制作完毕的机械零件上作布氏硬度测定,会由于压痕过大影响零件的正常装配和使用性能。
因此布氏硬度测定法不适于检测大批量生产的零件。
布氏硬度(HB)一般用于材料较软的时候,如有色金属、热处理之前或退火后的钢铁。
洛氏硬度(HRC)一般用于硬度较高的材料,如热处理后的硬度等等。