艾奇逊石墨化炉的节能
大直流改内串炉
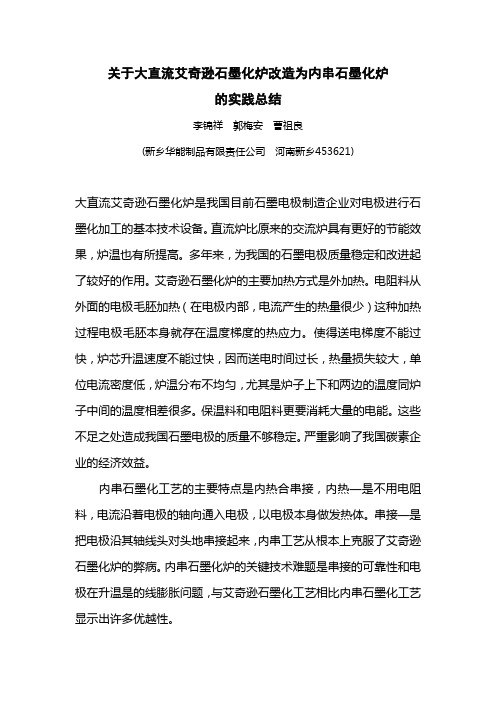
关于大直流艾奇逊石墨化炉改造为内串石墨化炉的实践总结李锦祥郭梅安曹祖良(新乡华能制品有限责任公司河南新乡453621)大直流艾奇逊石墨化炉是我国目前石墨电极制造企业对电极进行石墨化加工的基本技术设备。
直流炉比原来的交流炉具有更好的节能效果,炉温也有所提高。
多年来,为我国的石墨电极质量稳定和改进起了较好的作用。
艾奇逊石墨化炉的主要加热方式是外加热。
电阻料从外面的电极毛胚加热(在电极内部,电流产生的热量很少)这种加热过程电极毛胚本身就存在温度梯度的热应力。
使得送电梯度不能过快,炉芯升温速度不能过快,因而送电时间过长,热量损失较大,单位电流密度低,炉温分布不均匀,尤其是炉子上下和两边的温度同炉子中间的温度相差很多。
保温料和电阻料更要消耗大量的电能。
这些不足之处造成我国石墨电极的质量不够稳定。
严重影响了我国碳素企业的经济效益。
内串石墨化工艺的主要特点是内热合串接,内热—是不用电阻料,电流沿着电极的轴向通入电极,以电极本身做发热体。
串接—是把电极沿其轴线头对头地串接起来,内串工艺从根本上克服了艾奇逊石墨化炉的弊病。
内串石墨化炉的关键技术难题是串接的可靠性和电极在升温是的线膨胀问题,与艾奇逊石墨化工艺相比内串石墨化工艺显示出许多优越性。
内串石墨化炉升温速率高。
送电周期短.由于内串工艺利用电极本身作为发热体,电极内部电流和温度分布比较均匀,热应力小,这就使得内串工艺可以用比艾奇逊炉快多的升温曲线而不致产生裂纹。
电耗较低.由于内串炉送电时间短.不用加热电阻料,这使内串炉的工艺电耗大大降低.一般可节电25%左右,每年还可节省大量的用于作电阻料的冶金焦和石墨化焦,经济效益十分显著。
电极质量均匀而且稳定。
在内串石墨化过程中电极温度可达3000℃,电极边缘和中心间的温度差别很小,两头与中间的温度差别更小。
因此,电极质量稳定,炉电极的比电阻比较一致。
特别适合生产大规格的石墨电极。
用内串炉生产直径400mm以上的石墨化电极,一是能提高单炉产量:二是电极直径越大工艺技术指标越好;三是能满足大规格高功率,超高功率电极石墨化的需要。
艾奇逊石墨化炉的节能
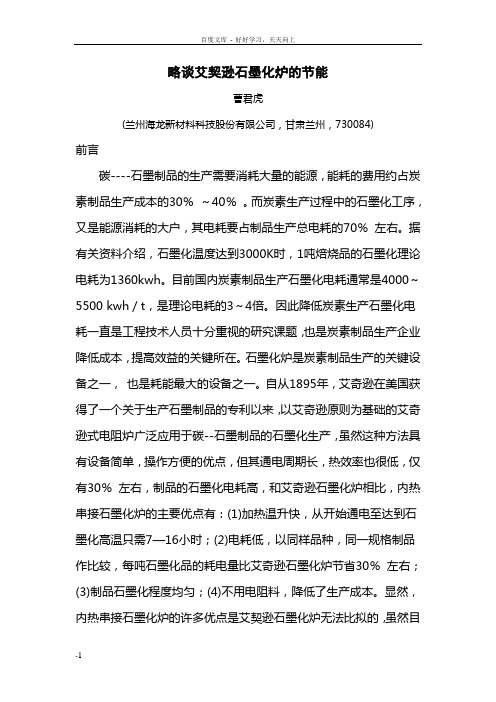
略谈艾契逊石墨化炉的节能曹君虎(兰州海龙新材料科技股份有限公司,甘肃兰州,730084)前言碳----石墨制品的生产需要消耗大量的能源,能耗的费用约占炭素制品生产成本的30%~40%。
而炭素生产过程中的石墨化工序,又是能源消耗的大户,其电耗要占制品生产总电耗的70%左右。
据有关资料介绍,石墨化温度达到3000K时,1吨焙烧品的石墨化理论电耗为1360kwh。
目前国内炭素制品生产石墨化电耗通常是4000~5500 kwh/t,是理论电耗的3~4倍。
因此降低炭素生产石墨化电耗一直是工程技术人员十分重视的研究课题,也是炭素制品生产企业降低成本,提高效益的关键所在。
石墨化炉是炭素制品生产的关键设备之一,也是耗能最大的设备之一。
自从1895年,艾奇逊在美国获得了一个关于生产石墨制品的专利以来,以艾奇逊原则为基础的艾奇逊式电阻炉广泛应用于碳--石墨制品的石墨化生产,虽然这种方法具有设备简单,操作方便的优点,但其通电周期长,热效率也很低,仅有30%左右,制品的石墨化电耗高,和艾奇逊石墨化炉相比,内热串接石墨化炉的主要优点有:(1)加热温升快,从开始通电至达到石墨化高温只需7—16小时;(2)电耗低,以同样品种,同一规格制品作比较,每吨石墨化品的耗电量比艾奇逊石墨化炉节省30%左右;(3)制品石墨化程度均匀;(4)不用电阻料,降低了生产成本。
显然,内热串接石墨化炉的许多优点是艾契逊石墨化炉无法比拟的,虽然目前国内也有企业采用内热串接石墨化工艺生产碳一石墨制品,但内热串接石墨化炉现在还不能完全取代艾契逊石墨化炉,艾奇逊石墨化炉仍然是碳---石墨制品生产的主要热工设备之一。
因此,充分发挥艾奇逊石墨化炉的潜力,降低其石墨化生产过程中的能源消耗,对于炭素制品生产企业来说,也是降低生产成本,提高经济效益的有效手段之一。
1 艾奇逊石墨化炉的能量平衡由于奇契逊石墨化炉是现行炭素工业石墨化生产的主要炉型,弄清楚艾契逊石墨化炉的电热效率和能量平衡,对于碳一石墨制品的石墨化生产和石墨化炉的节能有着十分重要的作用。
石墨化设备——五种类型石墨化炉介绍
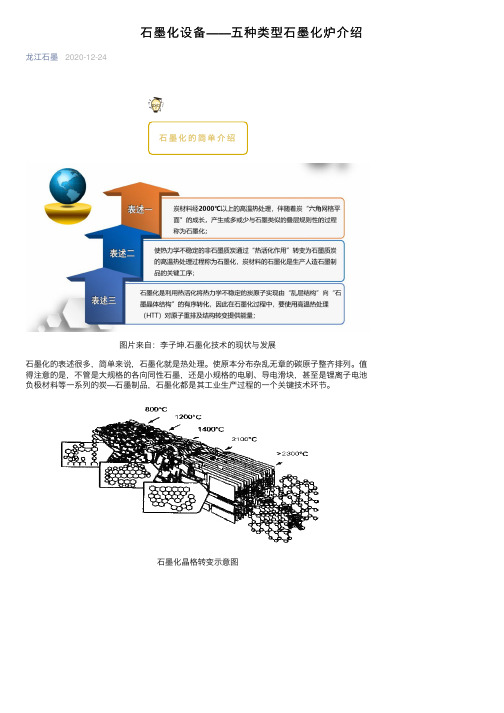
⽯图⽚来⾃:李⼦坤.⽯墨化技术的现状与发展⽯墨化的表述很多,简单来说,⽯墨化就是热处理。
使原本分布杂乱⽆章的碳原⼦整齐排列。
值得注意的是,不管是⼤规格的各向同性⽯墨,还是⼩规格的电刷、导电滑块,甚⾄是锂离⼦电池负极材料等⼀系列的炭—⽯墨制品,⽯墨化都是其⼯业⽣产过程的⼀个关键技术环节。
⽯墨化晶格转变⽰意图⽯墨化过程⾃动控制系统⽯墨化按照加热⽅式可分为直接法和间接法,按照运⾏⽅式可分为间歇式和连续式。
⽯墨化⼯艺是炭⽯墨类锂离⼦电池负极材料⽣产的重要⼯艺,⽯墨化度是锂离⼦电池负极材料的重要指标。
在⽯墨化温度提⾼到接近2200℃时,锂离⼦电池负极材料的杂质基本上已经被排除。
要对材料进⾏⽯墨化,就要⽤到加⼯设备——⽯墨化炉。
五种类型⽯墨化炉介绍图⽚来⾃:李⼦坤.⽯墨化技术的现状与发展⽯墨化设备按不同的⽅式分为两⼤类:即按加热⽅式分为直接加热炉和间接加热炉。
直接加热炉以待受热处理的物料直接作为发热体;间接加热炉是物料只是受热体,热量来⾃于物料外围的发热体。
按运⾏设计⽅式分类分为艾奇逊⽯墨化炉、内串式⽯墨化炉、真空⽯墨化炉、连续式⽯墨化炉以及箱体式⽯墨化炉五种主要类型。
艾奇逊⽯墨化炉1985年,E.G.艾奇逊发明⽯墨化炉,随着⼯业的发展,⽯墨化炉的结构也有了很⼤的发展。
艾奇逊炉有了直流电炉和交流电炉。
这种炉⼦结构简单、坚固耐⽤、容易维修。
图⽚来⾃:李⼦坤.⽯墨化技术的现状与发展艾奇逊⽯墨化炉按加热⽅式分类,它属于直接加热式电炉。
直接加热式炉就是制品本⾝是导电体,通过电阻加热,从⽽使制品完成⽯墨化。
早期的艾奇逊⽯墨化炉采⽤的是交流电,但交流电存在功率⼩、电流密度低、功率因数低、送电时间长等缺点。
20世纪60年代后随着整流设备的快速发展,艾奇逊⽯墨化炉开始采⽤直流供电,⼤⼤降低了能耗。
⽯墨化炉中的电阻主要由电阻料提供,可见在整个⽯墨化过程中,热量主要是由电阻料传⼊制品的,进⼊制品的电流⽐率很⼩。
若电阻料的电阻不均匀,会造成炉芯温度不均匀,从⽽导致⽯墨化制品产⽣裂纹,成为废品。
石墨选矿节能报告
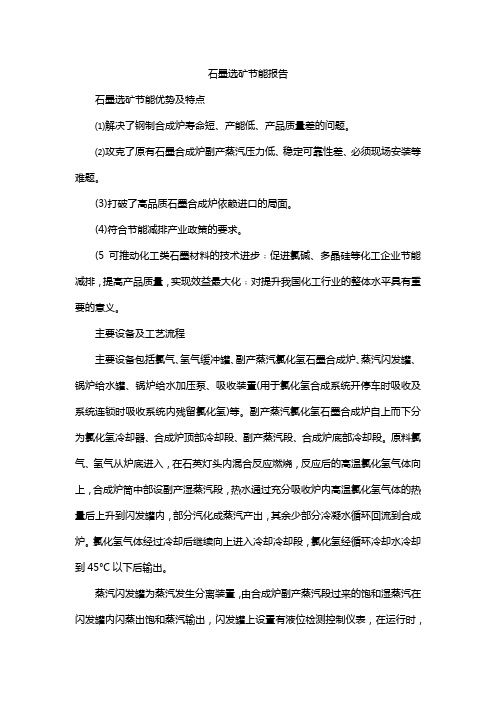
石墨选矿节能报告石墨选矿节能优势及特点⑴解决了钢制合成炉寿命短、产能低、产品质量差的问题。
⑵攻克了原有石墨合成炉副产蒸汽压力低、稳定可靠性差、必须现场安装等难题。
(3)打破了高品质石墨合成炉依赖进口的局面。
(4)符合节能减排产业政策的要求。
(5可推动化工类石墨材料的技术进步﹔促进氯碱、多晶硅等化工企业节能减排,提高产品质量,实现效益最大化﹔对提升我国化工行业的整体水平具有重要的意义。
主要设备及工艺流程主要设备包括氯气、氢气缓冲罐、副产蒸汽氯化氢石墨合成炉、蒸汽闪发罐、锅炉给水罐、锅炉给水加压泵、吸收装置(用于氯化氢合成系统开停车时吸收及系统连锁时吸收系统内残留氯化氢)等。
副产蒸汽氯化氢石墨合成炉自上而下分为氯化氢冷却器、合成炉顶部冷却段、副产蒸汽段、合成炉底部冷却段。
原料氯气、氢气从炉底进入,在石英灯头内混合反应燃烧,反应后的高温氯化氢气体向上,合成炉筒中部设副产湿蒸汽段,热水通过充分吸收炉内高温氯化氢气体的热量后上升到闪发罐内,部分汽化成蒸汽产出,其余少部分冷凝水循环回流到合成炉。
氯化氢气体经过冷却后继续向上进入冷却冷却段,氯化氢经循环冷却水冷却到45°C以下后输出。
蒸汽闪发罐为蒸汽发生分离装置,由合成炉副产蒸汽段过来的饱和湿蒸汽在闪发罐内闪蒸出饱和蒸汽输出,闪发罐上设置有液位检测控制仪表,在运行时,保证闪发罐内维持一定液位。
锅炉给水经过不断蒸发后.水中夹带的少量盐分会不断浓缩,达到一定浓度时,会产生结垢,影响设备运行,需要通过分析检测锅炉给水含盐量,适当排除部分含高浓度盐的锅炉给水,使系统内锅炉给水含盐量维持在较低水平。
由一级降膜吸收器、二级降膜吸收器、尾气处理塔组成的制酸系统、主要对开停车时氯化氢进行吸收及对系统连锁时残存的氯化氢进行吸收,还可制成高纯盐酸供离子膜制碱装置使用。
石墨化炉窑的节能分析及措施
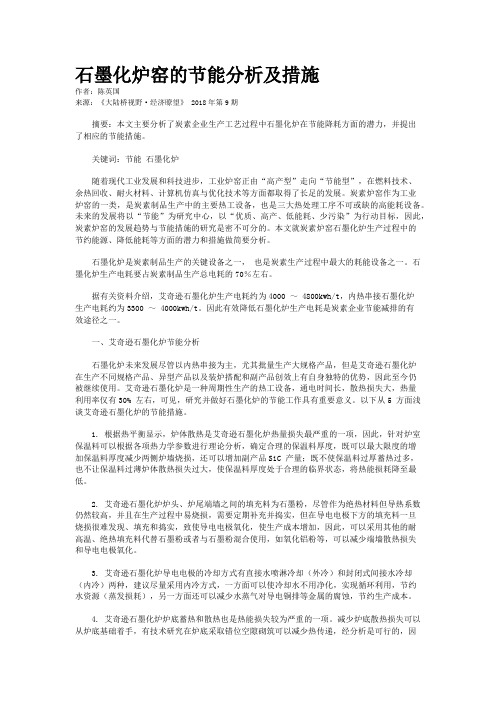
石墨化炉窑的节能分析及措施作者:陈英国来源:《大陆桥视野·经济瞭望》 2018年第9期摘要:本文主要分析了炭素企业生产工艺过程中石墨化炉在节能降耗方面的潜力,并提出了相应的节能措施。
关键词:节能石墨化炉随着现代工业发展和科技进步,工业炉窑正由“高产型”走向“节能型”,在燃料技术、余热回收、耐火材料、计算机仿真与优化技术等方面都取得了长足的发展。
炭素炉窑作为工业炉窑的一类,是炭素制品生产中的主要热工设备,也是三大热处理工序不可或缺的高能耗设备。
未来的发展将以“节能”为研究中心,以“优质、高产、低能耗、少污染”为行动目标,因此,炭素炉窑的发展趋势与节能措施的研究是密不可分的。
本文就炭素炉窑石墨化炉生产过程中的节约能源、降低能耗等方面的潜力和措施做简要分析。
石墨化炉是炭素制品生产的关键设备之一,也是炭素生产过程中最大的耗能设备之一。
石墨化炉生产电耗要占炭素制品生产总电耗的70%左右。
据有关资料介绍,艾奇逊石墨化炉生产电耗约为4000 ~ 4800kwh/t,内热串接石墨化炉生产电耗约为3300 ~ 4000kwh/t。
因此有效降低石墨化炉生产电耗是炭素企业节能减排的有效途径之一。
一、艾奇逊石墨化炉节能分析石墨化炉未来发展尽管以内热串接为主,尤其批量生产大规格产品,但是艾奇逊石墨化炉在生产不同规格产品、异型产品以及装炉搭配和副产品创效上有自身独特的优势,因此至今仍被继续使用。
艾奇逊石墨化炉是一种周期性生产的热工设备,通电时间长,散热损失大,热量利用率仅有30% 左右,可见,研究并做好石墨化炉的节能工作具有重要意义。
以下从5 方面浅谈艾奇逊石墨化炉的节能措施。
1. 根据热平衡显示,炉体散热是艾奇逊石墨化炉热量损失最严重的一项,因此,针对炉室保温料可以根据各项热力学参数进行理论分析,确定合理的保温料厚度,既可以最大限度的增加保温料厚度减少两侧炉墙烧损,还可以增加副产品SiC 产量;既不使保温料过厚蓄热过多,也不让保温料过薄炉体散热损失过大,使保温料厚度处于合理的临界状态,将热能损耗降至最低。
炭素炉窑的发展趋势及节能措施
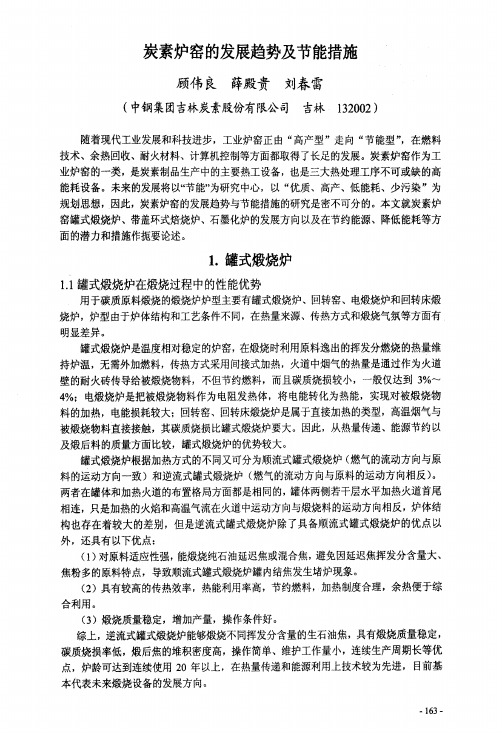
%
11.5l 4.74 0.1l 29.03 13.52 0.06 14.90 26.13 100
燃料燃烧化学热 燃料带入物料热
制品挥发分燃料化学热 填充料烧损化学热 热空气带入物料热
903.9 3.O 483.1 28.9 101.1
合计
1520
100
合计
2.2环式焙烧炉低温炉室挥发分及过剩燃料再利用
热Hale Waihona Puke ,节约燃料。表2环式焙烧炉热平衡
热收入 热量/(104kJ/t)
%
59.47 0.20 31.78 1.90 6.65
热支出 热量/(104kJ/t) 加热电极所需热量 加热填充料所需热量 物料中水分蒸发吸热 烟气带走物理热 烟气带走化学热 炉盖散热 炉墙传传 炉体蓄热及其他
175.0 72.1 1.6 441.3 205.5 0.9 226.5 397.1 1520
环式焙烧炉的发展及节龛爨进行深入探讨。
2。l带盖环式焙烧炉的发展趋势
隧羲市场对石墨制燕尺寸要求的变彳幺昶炭素炉窑技术的不断进步,未来环式焙烧炉
的发展应该囱大型化、节能化、宙动化方向发展,炉底烟道应该由U型陶环形烟道发展。 大型化蓠先是增加焙烧炉室数量,其优点是掰个系统运转可以增加待加热傺温炉室 个数,傻高温烟气熬热量得到充分利用;另外,在炉塞数量增热和受压允许的童骞况下簸
近年来,隧着电价的不断上涨,使炭紊行业的熬利窆闻不断压缝,应用煅烧妒麴高 温烟气通过余热锅炉进行动力发电是罐式激烧炉来来余热剩髑酶发鼹趋势,也是低碳环 保、节能创效值得研究的新课题,不仅可以使炭素行妲煦煎剃空闻得到释放,实瑰节艉 减摊、降耗增效,丽艇还熊取褥良好的经济效益、社会效益帮环境效益。据统计,缀痣 已经宠后有5家以上铝用炭阳极念业剥用煅烧炉的余热进行发电的实例,寝l为lO万t
内串石墨化工艺的研究

20090408
人连理l:人学硕十学位论文
摘要
内串石墨化炉是一种新型节能炉型,主要用于石墨电极高温热处理。与爱奇逊石墨 化炉比较,串接石墨化炉具有通电时问短,电耗低(每吨石墨化品电耗下降1000kW·h 左右),不用电阻料,炉芯温差小等特点。经石墨化的电极电阻率均质性好,如焙烧品 质量较好,串接及送电处理得当,基本不产生废品。由于内串石墨化炉的优点,内串石 墨化炉被困内外生产厂家关注和使用,研究内串石墨化生产工艺成为新的课题。
石墨化的方法按加热方式可分为直接法和I’日J接法。所谓直接法,就是指电流直接通 过被石墨化的焙烧品,制品本身就是导体通过电阻热使制品达到石墨化温度。生产石墨 电极所用的石墨化炉主要采用直接法。直接加热式石墨化炉有两种炉型,一种为有电阻 料的称爱奇逊石墨化炉,另一种为内热式串接石墨化炉英文简称LWG炉。而间接法是 电源和制品不直接接触,热能是通过感应或辐射的途径传递,制品可在炉子中自由移动, 用这种方法的很少,它只能生产一些较小规格的电炭制品。
power consumption reduction,without addition of electric resistance and the temperature difference of the core of the furnace is low,The electric resistivity of the graphitized productions is homogeneous.The waste product ratio is low or zero if the quality of the baked products,series connection condition and power supply can reach the demand for the operation specification of ideal graphite electrode production.Based on the above advantages, lengthwise graphitization furnace has been paid much attention by the domestic and oversea companies,and the process for the lengthwise graphitization is a new task.
高效节能的艾奇逊石墨化加热单元及加热系统[实用新型专利]
![高效节能的艾奇逊石墨化加热单元及加热系统[实用新型专利]](https://img.taocdn.com/s3/m/d7c0f2250a4e767f5acfa1c7aa00b52acfc79c90.png)
(19)中华人民共和国国家知识产权局(12)实用新型专利(10)授权公告号 (45)授权公告日 (21)申请号 201621108556.3(22)申请日 2016.10.10(73)专利权人 元氏县槐阳碳素有限公司地址 051137 河北省石家庄市元氏县苏阳乡南白娄村南(72)发明人 宋志涛 (51)Int.Cl.C01B 32/205(2017.01)F27B 21/00(2006.01)F27B 21/08(2006.01)H05B 3/02(2006.01)(54)实用新型名称高效节能的艾奇逊石墨化加热单元及加热系统(57)摘要本实用新型属于石墨炭化装置技术领域,提出了高效节能的艾奇逊石墨化加热单元及加热系统,包括并排设置的箱体一和箱体二,所述箱体一的两侧分别为加热电极一组和加热电极二组,所述箱体二的两侧分别为加热电极三组和加热电极四组,所述加热电极一组、所述加热电极三组分别与变压器输出端的正极、负极连接,所述加热电极一组和所述加热电极二组通过导电铝排一电连接,所述加热电极三组和所述加热电极四组通过导电铝排二电连接,所述加热电极二组和所述加热电极四组通过导电铝排三电连接,所述导电铝排一上设置有开关一,所述导电铝排二上设置有开关二。
本实用新型解决了现有技术中石墨炭化加热过程能量利用不够合理,加热效率有待提高的技术问题。
权利要求书1页 说明书5页 附图2页CN 206720744 U 2017.12.08C N 206720744U1.高效节能的艾奇逊石墨化加热单元,其特征在于,包括,并排设置的箱体一(21)和箱体二(22),所述箱体一(21)的两侧分别为加热电极一组(211)和加热电极二组(212),所述箱体二(22)的两侧分别为加热电极三组(221)和加热电极四组(222),所述加热电极一组(211)、所述加热电极三组(221)分别与变压器(23)输出端的正极、负极连接,所述加热电极一组(211)和所述加热电极二组(212)通过导电铝排一(24)电连接,所述加热电极三组(221)和所述加热电极四组(222)通过导电铝排二(25)电连接,所述加热电极二组(212)和所述加热电极四组(222)通过导电铝排三(26)电连接,所述导电铝排一(24)上设置有开关一(27),所述导电铝排二(25)上设置有开关二(28)。
- 1、下载文档前请自行甄别文档内容的完整性,平台不提供额外的编辑、内容补充、找答案等附加服务。
- 2、"仅部分预览"的文档,不可在线预览部分如存在完整性等问题,可反馈申请退款(可完整预览的文档不适用该条件!)。
- 3、如文档侵犯您的权益,请联系客服反馈,我们会尽快为您处理(人工客服工作时间:9:00-18:30)。
略谈艾契逊石墨化炉的节能曹君虎(兰州海龙新材料科技股份有限公司,甘肃兰州,730084)前言碳----石墨制品的生产需要消耗大量的能源,能耗的费用约占炭素制品生产成本的30%~40%。
而炭素生产过程中的石墨化工序,又是能源消耗的大户,其电耗要占制品生产总电耗的70%左右。
据有关资料介绍,石墨化温度达到3000K时,1吨焙烧品的石墨化理论电耗为1360kwh。
目前国内炭素制品生产石墨化电耗通常是4000~5500 kwh/t,是理论电耗的3~4倍。
因此降低炭素生产石墨化电耗一直是工程技术人员十分重视的研究课题,也是炭素制品生产企业降低成本,提高效益的关键所在。
石墨化炉是炭素制品生产的关键设备之一,也是耗能最大的设备之一。
自从1895年,艾奇逊在美国获得了一个关于生产石墨制品的专利以来,以艾奇逊原则为基础的艾奇逊式电阻炉广泛应用于碳--石墨制品的石墨化生产,虽然这种方法具有设备简单,操作方便的优点,但其通电周期长,热效率也很低,仅有30%左右,制品的石墨化电耗高,和艾奇逊石墨化炉相比,内热串接石墨化炉的主要优点有:(1)加热温升快,从开始通电至达到石墨化高温只需7—16小时;(2)电耗低,以同样品种,同一规格制品作比较,每吨石墨化品的耗电量比艾奇逊石墨化炉节省30%左右;(3)制品石墨化程度均匀;(4)不用电阻料,降低了生产成本。
显然,内热串接石墨化炉的许多优点是艾契逊石墨化炉无法比拟的,虽然目前国内也有企业采用内热串接石墨化工艺生产碳一石墨制品,但内热串接石墨化炉现在还不能完全取代艾契逊石墨化炉,艾奇逊石墨化炉仍然是碳---石墨制品生产的主要热工设备之一。
因此,充分发挥艾奇逊石墨化炉的潜力,降低其石墨化生产过程中的能源消耗,对于炭素制品生产企业来说,也是降低生产成本,提高经济效益的有效手段之一。
1 艾奇逊石墨化炉的能量平衡由于奇契逊石墨化炉是现行炭素工业石墨化生产的主要炉型,弄清楚艾契逊石墨化炉的电热效率和能量平衡,对于碳一石墨制品的石墨化生产和石墨化炉的节能有着十分重要的作用。
根据能量守恒定律,对于由电能转化为热能达到加热石墨制品的艾奇逊石墨化炉,可以从理论上由电能的数值计算出各个时刻石墨化炉芯内的温度,但是仅由焦耳---楞次定律Q= 0.24I2RT还不能完全求出炉芯内的温度。
因为,电阻热除了加热炉芯制品,升高炉芯温度之外,还有很大一部分热量通过各种途径散失掉了。
那么,总电能有多少用于加热炉芯?升高炉芯温度的能量是多少?通过各种途径散失的能量是多少?由能量守恒定律得知,这三者是平衡的。
即Q总=Ql+Q2Q 总——通电时间内供给炉内的能量;Q1 ——炉内吸收的能量;Q2 ——炉子散失的能量。
1.1 电平衡艾奇逊石墨化炉是以电作能源的工业电阻炉,在石墨化生产过程中,全部设备(包括变压器、石墨化炉)的电效率变化很大,石墨化开始通电时的电效率在70%~80%之间,通电结束时在50%~55%之间,平均在75%左右。
对于艾奇逊石墨化炉进行电气平衡的计算,有助于找出电能主要消耗在什么地方,主要损失在哪些环节上,可采用哪些有效措施节约电能。
石墨化炉供电网路电平衡,见图1。
从图1看到,当100%的电能支出到达石墨化炉芯的有效电能输入仅61.4%左右,从供电设备方面看,变压器要消耗一定的电量,除变压器外,从变压器低压侧到炉芯的电路各部位都要消耗不少电量,最大的电能损耗量在炉头导电电极上,高达17.8%,从主母线接到导电电极端面上的短网母线损耗量也很大,达到了12.9%。
1.2 热平衡艾契逊石墨化炉的生产是间歇性作业,一个生产周期内从低温升到高温,又从高温冷却低温,通电时,真正使产品加热升温所用的热量是很少的一部分,绝大部分通过传热、对流、辐射等方式损失掉了。
石墨化炉的热量平衡与周围的介质有关系,平均20%~26%的热量损失于周围介质,在通电结束时,有55%~75%的热量损失于周围介质。
石墨化炉的热量效率是按加热制品所消耗的有效热量与通电时总热量消耗的比值计算而成的,即rl热=Q有/Q总×100%。
艾契逊石墨化炉的热量平衡,见图2。
从图2石墨化炉热平衡可以看出,艾契逊石墨化炉是热效率比较低的工业电阻炉,加热整个炉芯的热量仅占39.65%,若除去加热电阻料的热量消耗,炉芯制品得到的热量仅为30.2%。
在工业艾契逊石墨化炉生产中,由于受各种因素的影响,石墨化炉的热效率实际上更低,最大的热损失是石墨化向周围介质散失的热量,高达28.4%,同时加热保温料、炉底、炉头尾端墙及侧墙也消耗一部分热量。
2 艾契逊石墨化炉的节能从艾契逊石墨化炉的电热平衡分析可知,石墨化炉是消耗电量很大的热工设备,因此如何在保证产品质量的前提下,减少电量消耗是石墨化炉节能的主要内容,也是降低石墨化生产成本的必由之路。
艾契逊石墨化炉的节能,制品的石墨化难易程度,也影响其石墨化工艺电量消耗,除了尽可能提高制品石墨化成品率,减少各种类型的废品外,我们还可以从石墨化工艺技术、工序管理等方面采取措施,以降低石墨化工艺电量消耗,节约能源。
2.1 石墨化炉芯温度监控艾契逊石墨化炉理想的停电方式应根据炉芯温度来确定,但由于石墨化炉炉芯温度的不均匀性,高温控制不容易,实现连续自动化测量困难等因素,因此,现行工业艾契逊石墨化炉均采用定功率配电的功率送电曲线来控制炉芯温度的上升速率,以累计电量最终达到计划电量为停电依据,这种方法有很多缺陷,极不科学。
有时经常会出现炉芯温度已达到,可送电量按规定尚未完结的多送电现象,极大地浪费了电量,达不到节能的目的。
或者相反,炉芯的温度还没有完全达到制品完成石墨化过程所需的高温,而送电量已经达到计划电量而停炉。
决定石墨化过程的是温度,电量消耗是考核炉芯温度是否达到规定温度的一种手段。
电量的消耗随着时间的延长而增多,而炉芯温度的高低除随时间的变化热量在逐渐积累外,还受着其它许多因素的影响。
石墨化炉芯温度并非总是随着通电时间的延长而提高,而炉内热量的散失又和通电时间延长成正比例地增长,所以用控制送电量的石墨化工艺制度很不合理和科学。
通常控制的电量值,总是偏高于制品完成石墨化过程所需要的电量,这样就造成了电能的较大浪费,增加了不必要的生产成本。
因此,石墨化炉在送电过程中,通过炉芯温度变化情况的监控,可以避免因电量控制产生的不必要的多耗电,通过控制炉芯温度上升的速度,就可以节约电能和提高产品质量。
现行工业艾契逊石墨化炉的测温技术,虽然不够准确或存在误差,但为了石墨化炉的节能和确保产品质量,我们在石墨化炉侧中部找出一个适宜点,安装了测温观察孔,通过测温仪定期观察石墨化炉送电过程中各阶段的温升速度,重点观察监控炉芯温度在2300℃左右的变化情况,再结合电量控制,即在最短的时间内,功率达到最高值,电流达到最大额定电流值,再维持一段时间,一直到石墨化炉的热散失与吸收的热量平衡时,炉芯温度不再升高,其电阻也不再降低时,功率、电流、电压等电气参数都趋于恒定,方可停止送电。
这样,通过监控石墨化炉通电过程中的炉芯温度变化,就可以减少热量损失,节约电量,达到石墨化炉的节能目的。
2.2 确定合理的石墨化通电周期艾契逊石墨化炉的最高温度是由变压器的最大输出电流,经石墨化炉芯电阻转化成的热量,与石墨化炉本身散失的热量相平衡而得到的。
石墨化炉的炉芯电阻主要是由电阻料提供的,石墨化炉开始通电时,电阻料的电阻约占炉芯电阻的99%左右,通电结束后,电阻料的电阻还要占到炉芯电阻的97%左右。
可见在整个石墨化过程中,热量主要是由电阻料传人制品的,进人制品的电流比率很小。
在制品内部,电流产生的热量很少,因此制品内外温度相差很大,制品内部温度分布很不均匀,热应力很大,为了减小这种不均匀的热应力对于制品晶体结构变化的影响,就要控制制品在不同石墨化温度阶段,对于温升速度的不同要求,因而石墨化通电周期很长。
对于艾契逊石墨化炉,要根据制品的品种、规格及质量状况来决定采用的电阻料类别,确定合理的石墨化工艺技术条件、功率送电曲线和电量,在保证产品质量的前提下,尽可能缩短石墨化炉通电周期,提高石墨化生产效率,降低石墨化工艺电量消耗,以节约能源,也就是石墨化生产工艺所服从的“高效与低耗并行”原则。
2.3 采用强化石墨化送电制度强化石墨化送电的实质,就是在保证产品质量的基础上,适当提高通入石墨化炉内的有效功率及其上升的速度,尽量减少最大功率下降的速度,以便保证炉芯单元体积及面积上对最大功率和电流密度的需要。
炭素制品在石墨化过程中的三个温度阶段是公认的:(1)室温至1300℃为重复焙烧阶段,采用较快的升温速度,制品也不会产生裂纹;(2)1300~1800℃为严控升温阶段,碳平面网格逐步转化为石墨晶格结构,促使应力过分集中,易产生裂纹,应减缓热应力作用,使制品处于较小的温度梯度;(3)1800℃至石墨化最高温度,为自由升温阶段,此时制品的石墨晶体结构已基本形成,升温速度对制品影响不大,此时就可以采取强化石墨化送电制度,减小最大功率的下降速度,增大炉芯的电流密度,以便使炉芯温度尽快达到制品完善石墨化过程所需要的最高温度。
在日常石墨化生产中,对于采用石墨化焦作电阻料生产大规格石墨制品,在石墨化送电后期,当变压器的输出功率、电流达到满负荷后,允许变压器的输出电流比额定输出电流超出10%运行数小时,以减小最大功率的下降速度,增加石墨化炉芯的电流密度,迅速提高石墨化炉芯的发热量,使炉芯温度达到2700℃以上,从而使制品在较短的时间内,完成石墨化过程,减小石墨化炉散热损失,减少石墨化炉的送电量,以达到石墨化节能的目的。
2.4 缩小炉芯制品组间距艾契逊石墨化炉通常采用炉芯制品立装法,这种装炉方法比较简便省力而且生产效率高,特别适合大中规格制品的石墨化生产,炉芯制品组间距一般为制品直径的20%左右,这也不尽合理,若炉芯制品组间距过大,则石墨化炉芯的制品装炉量就低,石墨化炉所消耗的辅助原料也多,制品的石墨化工艺电能消耗也高。
如果在保持石墨化炉芯截面不变的前提下,改进石墨化装炉工艺技术条件,适当缩小炉芯制品的组间距,在确保产品质量的同时,还可以达到石墨化炉增产、节焦、节电的目的。
若将φ350mm石墨电极的石墨化装炉炉芯制品的组间距由80mm调整为60mm,石墨化炉的热效率为30%,则石墨化炉的增产、节能效果分别为:增产:△c={(350+80)/(350+60)一1}X l00%=4.88%节焦:AK={1-(O.2146 X350+60)/(0.2146 X 350+8O)}X 100%=12.89%节电:△s ={1-[0.3+(350+60)/(350+80)(1-0.31)]}×100%=%2.5 适当扩大炉芯截面艾契逊石墨化炉的炉芯截面是炉中制品与其间填充的电阻料占据空间的截面积,同样,炉芯电流密度是指单位炉芯截面上的电流值。