自动铺带技术在航空复合材料制造领域的应用
基于自动铺带技术的复合材料结构件强度评估研究

基于自动铺带技术的复合材料结构件强度评估研究引言:复合材料是一种由两种或两种以上材料组成的复合体,具有优异的力学性能和工程应用潜力。
在航空航天、汽车工业、能源等领域中,复合材料的应用广泛,其中复合材料结构件的强度评估是一个关键问题。
本文旨在研究基于自动铺带技术的复合材料结构件强度评估方法与技术。
一、自动铺带技术的原理与应用自动铺带技术是一种将预浸复合材料纤维排列在设计规定位置的技术。
其主要原理是通过控制复合材料纤维与树脂的比例、面积密度和纤维层次,实现复合材料结构件的定向排列和强度提升。
自动铺带技术具有高效、高精度和低浪费等优点,因此在航空航天和汽车工业等领域广泛应用。
二、复合材料结构件强度评估的重要性复合材料结构件的强度评估是确保结构件在实际工况下能够承受预期载荷的关键。
在设计和制造复合材料结构件之前,强度评估能够提前预测结构件的破坏行为,指导结构优化和性能改进。
因此,开展复合材料结构件强度评估研究具有重要的理论和实践意义。
三、基于自动铺带技术的复合材料结构件强度评估方法1. 宏观力学模型基于自动铺带技术的复合材料结构件强度评估可以采用宏观力学模型进行。
通过建立合适的力学模型,将复合材料结构件视为多层板,进行强度评估和应力分析。
该方法能够较为准确地预测结构件的破坏行为和强度性能。
2. 细观力学模型细观力学模型是一种更加精细的强度评估方法,通过考虑复合材料纤维和树脂的微观结构与相互作用,建立复杂的力学模型。
该方法考虑了材料的非线性和破坏行为,可以提供更为精确的强度评估结果。
然而,由于模型的复杂性,该方法对计算资源和计算时间的要求较高。
3. 数值模拟与有限元分析数值模拟与有限元分析是一种较为常用的强度评估方法。
通过将复合材料结构件离散化为多个小单元,利用有限元方法对结构件进行力学分析和强度评估。
该方法能够较为准确地模拟复合材料结构件在复杂载荷下的响应,定量地评估结构件的强度。
四、复合材料结构件强度评估的关键因素1. 材料性能复合材料的性能对结构件的强度评估具有重要影响。
复合材料在航空结构中的应用
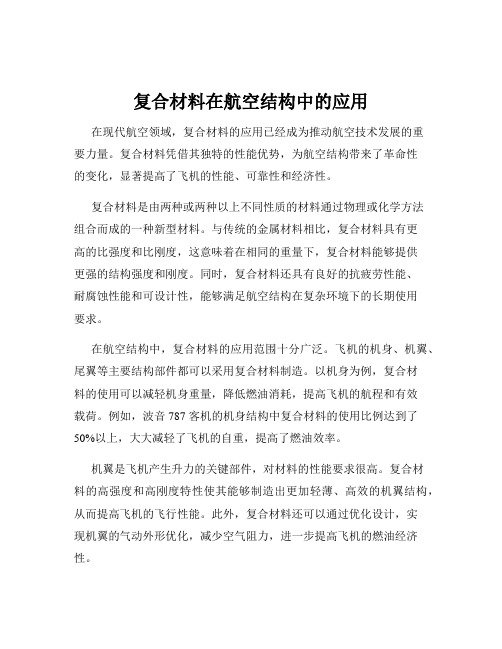
复合材料在航空结构中的应用在现代航空领域,复合材料的应用已经成为推动航空技术发展的重要力量。
复合材料凭借其独特的性能优势,为航空结构带来了革命性的变化,显著提高了飞机的性能、可靠性和经济性。
复合材料是由两种或两种以上不同性质的材料通过物理或化学方法组合而成的一种新型材料。
与传统的金属材料相比,复合材料具有更高的比强度和比刚度,这意味着在相同的重量下,复合材料能够提供更强的结构强度和刚度。
同时,复合材料还具有良好的抗疲劳性能、耐腐蚀性能和可设计性,能够满足航空结构在复杂环境下的长期使用要求。
在航空结构中,复合材料的应用范围十分广泛。
飞机的机身、机翼、尾翼等主要结构部件都可以采用复合材料制造。
以机身为例,复合材料的使用可以减轻机身重量,降低燃油消耗,提高飞机的航程和有效载荷。
例如,波音 787 客机的机身结构中复合材料的使用比例达到了50%以上,大大减轻了飞机的自重,提高了燃油效率。
机翼是飞机产生升力的关键部件,对材料的性能要求很高。
复合材料的高强度和高刚度特性使其能够制造出更加轻薄、高效的机翼结构,从而提高飞机的飞行性能。
此外,复合材料还可以通过优化设计,实现机翼的气动外形优化,减少空气阻力,进一步提高飞机的燃油经济性。
尾翼在飞机的飞行控制中起着重要作用,需要具备良好的强度和稳定性。
复合材料的应用可以使尾翼结构更加轻量化,同时提高其抗疲劳和耐腐蚀性能,确保飞机在长期飞行中的安全性和可靠性。
除了主要结构部件,复合材料在飞机的发动机部件、内饰、起落架等方面也有广泛的应用。
在发动机部件中,复合材料可以用于制造风扇叶片、机匣等部件,提高发动机的性能和可靠性。
飞机内饰采用复合材料可以减轻重量,提高舒适度和防火性能。
起落架部件使用复合材料则可以减轻重量,提高抗冲击性能。
然而,复合材料在航空结构中的应用也面临一些挑战。
首先,复合材料的成本相对较高,这在一定程度上限制了其大规模应用。
其次,复合材料的制造工艺较为复杂,需要高精度的模具和先进的成型技术,对制造设备和技术人员的要求较高。
自动铺带技术对复合材料构件冲击性能的影响研究
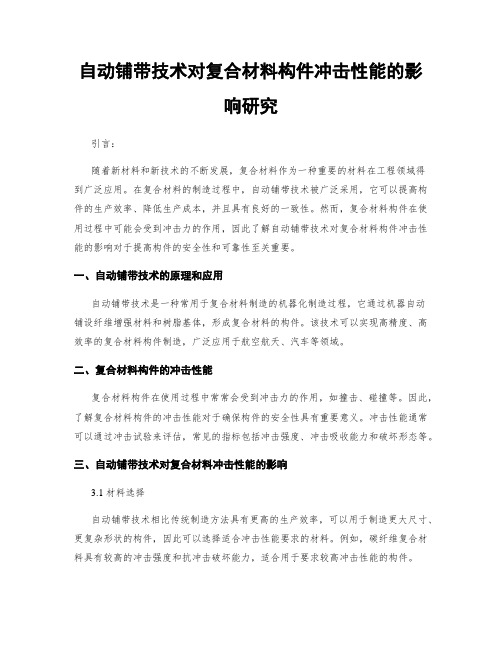
自动铺带技术对复合材料构件冲击性能的影响研究引言:随着新材料和新技术的不断发展,复合材料作为一种重要的材料在工程领域得到广泛应用。
在复合材料的制造过程中,自动铺带技术被广泛采用,它可以提高构件的生产效率、降低生产成本,并且具有良好的一致性。
然而,复合材料构件在使用过程中可能会受到冲击力的作用,因此了解自动铺带技术对复合材料构件冲击性能的影响对于提高构件的安全性和可靠性至关重要。
一、自动铺带技术的原理和应用自动铺带技术是一种常用于复合材料制造的机器化制造过程,它通过机器自动铺设纤维增强材料和树脂基体,形成复合材料的构件。
该技术可以实现高精度、高效率的复合材料构件制造,广泛应用于航空航天、汽车等领域。
二、复合材料构件的冲击性能复合材料构件在使用过程中常常会受到冲击力的作用,如撞击、碰撞等。
因此,了解复合材料构件的冲击性能对于确保构件的安全性具有重要意义。
冲击性能通常可以通过冲击试验来评估,常见的指标包括冲击强度、冲击吸收能力和破坏形态等。
三、自动铺带技术对复合材料冲击性能的影响3.1 材料选择自动铺带技术相比传统制造方法具有更高的生产效率,可以用于制造更大尺寸、更复杂形状的构件,因此可以选择适合冲击性能要求的材料。
例如,碳纤维复合材料具有较高的冲击强度和抗冲击破坏能力,适合用于要求较高冲击性能的构件。
3.2 材料排列方式自动铺带技术可以实现不同的纤维排列方式,如单向、双向和多向等。
纤维的排列方式对复合材料的冲击性能有着重要影响。
例如,单向纤维的构件在冲击作用下容易发生纤维断裂,而多向纤维排列可以提高冲击强度和吸能能力。
3.3 树脂基体的选择和浸润情况树脂基体的性能和浸润情况对复合材料的冲击性能也有显著影响。
自动铺带技术可以实现树脂基体的均匀浸润,从而提高复合材料的冲击性能。
同时,选择合适的树脂基体也可以提高构件的抗冲击破坏能力。
3.4 孔隙率和纤维体积分数复合材料构件的孔隙率和纤维体积分数也会对冲击性能产生影响。
自动铺带技术对复合材料构件尺寸和形状稳定性的影响分析
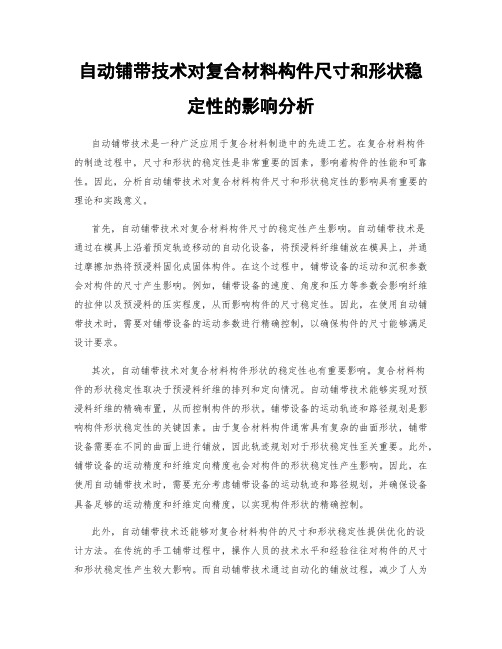
自动铺带技术对复合材料构件尺寸和形状稳定性的影响分析自动铺带技术是一种广泛应用于复合材料制造中的先进工艺。
在复合材料构件的制造过程中,尺寸和形状的稳定性是非常重要的因素,影响着构件的性能和可靠性。
因此,分析自动铺带技术对复合材料构件尺寸和形状稳定性的影响具有重要的理论和实践意义。
首先,自动铺带技术对复合材料构件尺寸的稳定性产生影响。
自动铺带技术是通过在模具上沿着预定轨迹移动的自动化设备,将预浸料纤维铺放在模具上,并通过摩擦加热将预浸料固化成固体构件。
在这个过程中,铺带设备的运动和沉积参数会对构件的尺寸产生影响。
例如,铺带设备的速度、角度和压力等参数会影响纤维的拉伸以及预浸料的压实程度,从而影响构件的尺寸稳定性。
因此,在使用自动铺带技术时,需要对铺带设备的运动参数进行精确控制,以确保构件的尺寸能够满足设计要求。
其次,自动铺带技术对复合材料构件形状的稳定性也有重要影响。
复合材料构件的形状稳定性取决于预浸料纤维的排列和定向情况。
自动铺带技术能够实现对预浸料纤维的精确布置,从而控制构件的形状。
铺带设备的运动轨迹和路径规划是影响构件形状稳定性的关键因素。
由于复合材料构件通常具有复杂的曲面形状,铺带设备需要在不同的曲面上进行铺放,因此轨迹规划对于形状稳定性至关重要。
此外,铺带设备的运动精度和纤维定向精度也会对构件的形状稳定性产生影响。
因此,在使用自动铺带技术时,需要充分考虑铺带设备的运动轨迹和路径规划,并确保设备具备足够的运动精度和纤维定向精度,以实现构件形状的精确控制。
此外,自动铺带技术还能够对复合材料构件的尺寸和形状稳定性提供优化的设计方法。
在传统的手工铺带过程中,操作人员的技术水平和经验往往对构件的尺寸和形状稳定性产生较大影响。
而自动铺带技术通过自动化的铺放过程,减少了人为因素对于构件尺寸和形状的影响,提供了更加稳定和可靠的制造方法。
同时,自动铺带技术还可以通过优化铺带设备的运动参数、路径规划和纤维定向等,进一步改善构件的尺寸和形状稳定性。
自动铺带技术在复合材料制造中的应用探索
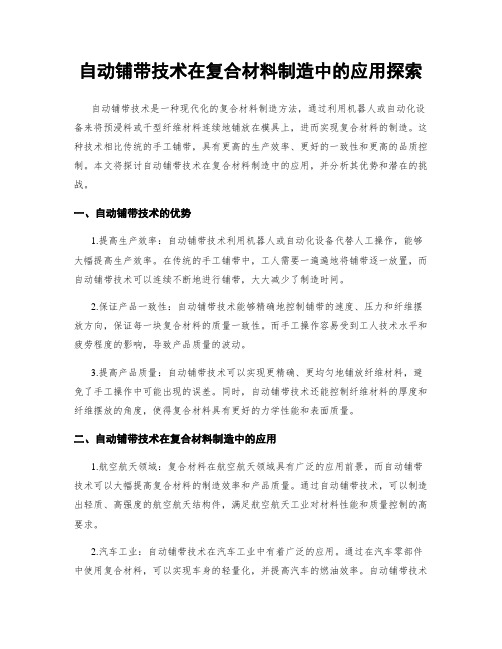
自动铺带技术在复合材料制造中的应用探索自动铺带技术是一种现代化的复合材料制造方法,通过利用机器人或自动化设备来将预浸料或干型纤维材料连续地铺放在模具上,进而实现复合材料的制造。
这种技术相比传统的手工铺带,具有更高的生产效率、更好的一致性和更高的品质控制。
本文将探讨自动铺带技术在复合材料制造中的应用,并分析其优势和潜在的挑战。
一、自动铺带技术的优势1.提高生产效率:自动铺带技术利用机器人或自动化设备代替人工操作,能够大幅提高生产效率。
在传统的手工铺带中,工人需要一遍遍地将铺带逐一放置,而自动铺带技术可以连续不断地进行铺带,大大减少了制造时间。
2.保证产品一致性:自动铺带技术能够精确地控制铺带的速度、压力和纤维摆放方向,保证每一块复合材料的质量一致性。
而手工操作容易受到工人技术水平和疲劳程度的影响,导致产品质量的波动。
3.提高产品质量:自动铺带技术可以实现更精确、更均匀地铺放纤维材料,避免了手工操作中可能出现的误差。
同时,自动铺带技术还能控制纤维材料的厚度和纤维摆放的角度,使得复合材料具有更好的力学性能和表面质量。
二、自动铺带技术在复合材料制造中的应用1.航空航天领域:复合材料在航空航天领域具有广泛的应用前景,而自动铺带技术可以大幅提高复合材料的制造效率和产品质量。
通过自动铺带技术,可以制造出轻质、高强度的航空航天结构件,满足航空航天工业对材料性能和质量控制的高要求。
2.汽车工业:自动铺带技术在汽车工业中有着广泛的应用。
通过在汽车零部件中使用复合材料,可以实现车身的轻量化,并提高汽车的燃油效率。
自动铺带技术可以大幅提高复合材料零部件的制造效率,满足汽车工业对大规模生产和高品质产品的需求。
3.建筑领域:自动铺带技术也可以应用于建筑领域的复合材料制造。
复合材料在建筑领域有着广泛的应用前景,可以用于制造建筑结构件、装饰材料等。
自动铺带技术可以提高建筑材料的生产效率,同时保证产品的一致性和质量,满足建筑行业对快速和高质量产品的需求。
自动铺带技术与大飞机复合材料结构成型

自动铺带技术与大飞机复合材料结构目前,飞机上的复合材料使用量已经成为衡量其先进性的重要标准。
波音787、空客A380飞机都大量采用复合材料,空客A350上复合材料的用量更超过50%。
作为中国拥有完全知识产权的大型民用客机项目,为了保证其客机的市场竞争力并促进国内复合材料产业的发展,也必将大量采用先进复合材料。
而自动铺带技术则是使用复合材料的关键技术之一。
先进复合材料的历史先进复合材料是20世纪60年代早期以单向带的形式推出的。
起初用手工铺贴,其工艺是劳动密集型的,容易引起质量问题。
20世纪60年代中期,航空工业的发展极大地推动了其自动化进程。
早期的设备是航空公司或加工车间在材料供应商的指导下自己制造的。
设备的构型涵盖了从手工辅助台式的原型机到由美国空军牵头、通用动力和Conrac公司合作研发的第一台全数控龙门式铺带机。
这台设备被用来为F-16生产复合材料零件,使用的是75mm 宽的带子。
20世纪70年代末期至80年代初,设备制造者生产了第一台商业化的平面和曲面数控铺带机,这些设备被用在军事项目上(如B-1和B-2轰炸机)制造飞机的零件。
曲面上带宽范围为75~150mm,平面可以高达300mm。
20世纪80年代末期,自动铺带开始广泛的使用于商用飞机上。
整个20世纪90年代,设备、编程技术、铺带技术和ATL复合材料的进一步发展使铺带工艺操作更简单、性能更可靠、界面更友好。
复合材料工艺综述单向碳环氧预浸带是在衬纸上成卷供应的,典型的宽度有75mm、150mm和300mm三种规格。
曲面应用使用75mm和150mm带宽,平面应用使用150mm和300mm带宽。
材料卷被装载在铺带的头部。
铺带头在平面应用时被安放在4轴台架上,曲面应用时安放在5轴台架上。
1 优点碳环氧预浸带极大地减少了手工铺层。
在平面装料的情况下,相对于手工铺贴,碳环氧预浸带可以减少的人工劳动时间高达70%~85%,铺层效率可以高达1000kg/周。
复合材料自动铺丝计算机辅助设计软件的设计与应用
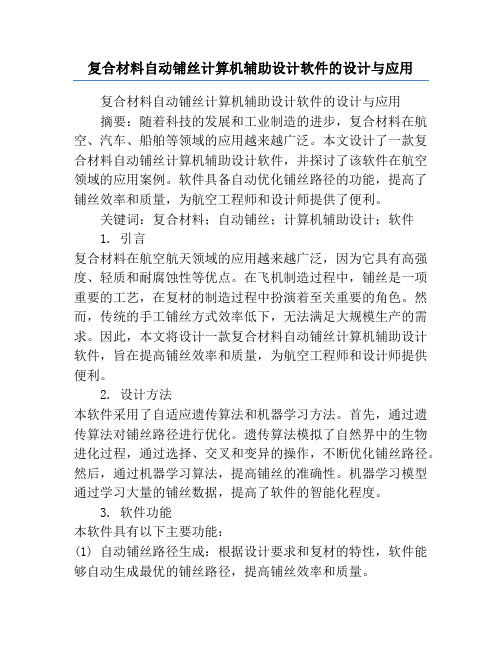
复合材料自动铺丝计算机辅助设计软件的设计与应用复合材料自动铺丝计算机辅助设计软件的设计与应用摘要:随着科技的发展和工业制造的进步,复合材料在航空、汽车、船舶等领域的应用越来越广泛。
本文设计了一款复合材料自动铺丝计算机辅助设计软件,并探讨了该软件在航空领域的应用案例。
软件具备自动优化铺丝路径的功能,提高了铺丝效率和质量,为航空工程师和设计师提供了便利。
关键词:复合材料;自动铺丝;计算机辅助设计;软件1. 引言复合材料在航空航天领域的应用越来越广泛,因为它具有高强度、轻质和耐腐蚀性等优点。
在飞机制造过程中,铺丝是一项重要的工艺,在复材的制造过程中扮演着至关重要的角色。
然而,传统的手工铺丝方式效率低下,无法满足大规模生产的需求。
因此,本文将设计一款复合材料自动铺丝计算机辅助设计软件,旨在提高铺丝效率和质量,为航空工程师和设计师提供便利。
2. 设计方法本软件采用了自适应遗传算法和机器学习方法。
首先,通过遗传算法对铺丝路径进行优化。
遗传算法模拟了自然界中的生物进化过程,通过选择、交叉和变异的操作,不断优化铺丝路径。
然后,通过机器学习算法,提高铺丝的准确性。
机器学习模型通过学习大量的铺丝数据,提高了软件的智能化程度。
3. 软件功能本软件具有以下主要功能:(1) 自动铺丝路径生成:根据设计要求和复材的特性,软件能够自动生成最优的铺丝路径,提高铺丝效率和质量。
(2) 工艺模拟:软件能够模拟复材的不同特性和材料的变化情况,为工程师提供了参考和决策依据。
(3) 优化算法:软件采用了自适应遗传算法,能够自动优化铺丝路径,提高了铺丝效率。
(4) 界面友好:软件界面简洁直观,易于操作和使用。
4. 应用案例本软件已成功应用于某型号客机的复合材料铺丝工艺中。
航空工程师使用该软件生成了最优的铺丝路径,并对路径进行了仿真模拟。
通过软件的帮助,工程师发现了一些潜在的问题并进行了修正,确保了复材在飞行过程中的安全性和稳定性。
5. 结果与讨论与传统的手工铺丝相比,本软件在铺丝效率和质量上都取得了显著的改进。
自动铺带技术对复合材料构件性能的影响研究
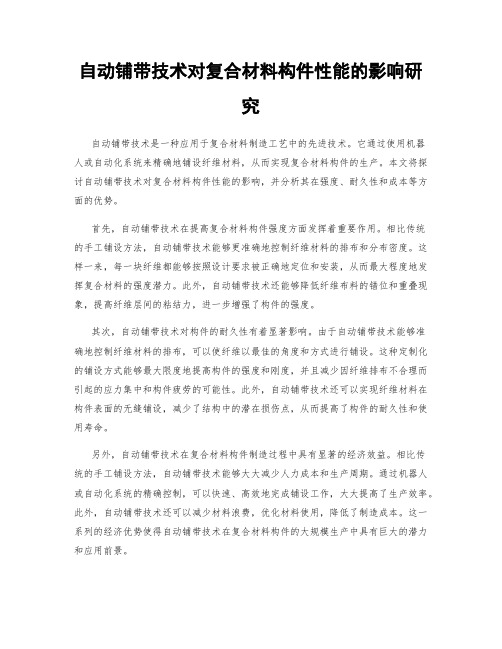
自动铺带技术对复合材料构件性能的影响研究自动铺带技术是一种应用于复合材料制造工艺中的先进技术。
它通过使用机器人或自动化系统来精确地铺设纤维材料,从而实现复合材料构件的生产。
本文将探讨自动铺带技术对复合材料构件性能的影响,并分析其在强度、耐久性和成本等方面的优势。
首先,自动铺带技术在提高复合材料构件强度方面发挥着重要作用。
相比传统的手工铺设方法,自动铺带技术能够更准确地控制纤维材料的排布和分布密度。
这样一来,每一块纤维都能够按照设计要求被正确地定位和安装,从而最大程度地发挥复合材料的强度潜力。
此外,自动铺带技术还能够降低纤维布料的错位和重叠现象,提高纤维层间的粘结力,进一步增强了构件的强度。
其次,自动铺带技术对构件的耐久性有着显著影响。
由于自动铺带技术能够准确地控制纤维材料的排布,可以使纤维以最佳的角度和方式进行铺设。
这种定制化的铺设方式能够最大限度地提高构件的强度和刚度,并且减少因纤维排布不合理而引起的应力集中和构件疲劳的可能性。
此外,自动铺带技术还可以实现纤维材料在构件表面的无缝铺设,减少了结构中的潜在损伤点,从而提高了构件的耐久性和使用寿命。
另外,自动铺带技术在复合材料构件制造过程中具有显著的经济效益。
相比传统的手工铺设方法,自动铺带技术能够大大减少人力成本和生产周期。
通过机器人或自动化系统的精确控制,可以快速、高效地完成铺设工作,大大提高了生产效率。
此外,自动铺带技术还可以减少材料浪费,优化材料使用,降低了制造成本。
这一系列的经济优势使得自动铺带技术在复合材料构件的大规模生产中具有巨大的潜力和应用前景。
除了上述优势,自动铺带技术还具有一些辅助性的影响。
例如,自动铺带技术能够实现对纤维材料的自动切割和粘接,减少了人工操作的繁琐程度,提高了生产效率。
同时,自动铺带技术还能够在铺设过程中实时监测和调节纤维材料的张力和排布,避免了因人为因素引起的误差,提高了构件的一致性和准确性。
这些辅助性的特点进一步加强了自动铺带技术在复合材料构件制造领域的竞争力和应用优势。
复合材料自动成型工艺进展及在航空中的应用

复合材料自动成型工艺进展 及在航空中的应用
Development and Aviation Application of Automated Processes for Composite
西北工业大学机电学院 史耀耀 阎 龙 莫 蓉
本文就复合材料飞机结构件的自动成型工艺进行了 综述,重点介绍了纤维铺放成型、带材铺叠成型的特点与 发展。复合材料自动成型工艺在航空领域的广泛应用,必 将大幅降低飞机结构件的制造成本,极大地促进航空工业 的发展。
带宽度的改变。
已成为世界上最大的纤维铺放设备 图 2)。因此,带材铺叠设备是具有
此外,铺放机的“单丝束控制” 供应商。
龙门结构运动与铺放头运动的多轴
能力使其能够实现锥形体表面(如飞
作为实现飞机复合材料结构件 机床。
机尾椎)的等厚度铺放。由于沿椎 自动成型的成熟工艺,纤维铺放成型
用于铺叠的芯模置于龙门架下
铺层的等厚度。
工艺已成为世界上主要飞机制造商 模表面 [3]。通过编程可实现带材形
2 纤维铺放成型的发展
的共同选择。
状及尺寸的精确控制。此外,相邻带
位于美国西部的 Hercules 宇航 公司(现在的 ATK 公司)对纤维铺放
带材铺叠成型
材间距离应控制在一定范围内,且不 允许出现带材重叠。
的研究始于 20 世纪 80 年代 [2,7]。该 1 带材铺叠成型的发展
(3)工艺过程人工干预程度的 降低:由于预浸料的铺放通过计算 机进行控制,因此无需专门的质检员 对铺层质量及铺层方向进行检验。
(4)制品的高质量和工艺过程 的可重复性:自动成型工艺过程的 实施可提高制品质量并保证工艺过 程的可重复。这是降低复合材料结 构件制造成本的又一重要因素。
复合材料自动铺带技术应用及方案示例

度和铺叠位置、方向、角度的准确性, 发自动铺带设备,完成了小型铺带机
(2)该 设 备 在 铺 层 时 能 够 对 铺
从而避免了人为铺放产生的偏差,如 的研制,并应用于复合材料结构件 层路径进行手动和自动设置,自动功
产品出现缺陷的几率大、零件制造质 的研制;北京航空制造工程研究所 能具有最佳的铺层路径,每层带可在
虽 然 备采用龙门式结构,主要包括带装夹
国 内 自 动 和释放 ( 开卷 ) 系统、衬纸带回卷系
铺 带 技 术 统、带缺陷检测传感系统、带对中和
研 究 起 步 导向系统、切带系统、铺带和压实系
较 晚,但 在 统、工作区域安全系统、铺带监控系
技术研究和 统、带卷装卸系统、工装定位及自动
空客西班牙Illescas用铺带工艺制造的平尾、方向舵
自动铺带作为典型的增料加工 成型技术,其成型设备的制造技术涉 及机电装备技术、C A D / C A M 软件 技术和材料工艺技术等多个研究领
大飞机复合材料制造技术 Composite Manufacturing Technology for Large Commercial Jet
域,可实现:
许多型号飞机上。
量重复性差、质量分散性大,以及尺 与 Forest-Line 公司合作研制的大 ±90°之间采取任意角度和任意方
寸精度和铺放位置准确度不能满足 型复合材料自动铺带机的调试工作 向的铺放。
大尺寸、高精度零件制造的要求等问
题。采用复合材料自动铺带技术可
在提高质量的同时,大幅度地节省原
材料,降低制造成本。同时,由于可
MTM44-1/HTS(12K)-134-35%RW MTM44-1/E-IMS65-24K 194-32%RW
新型复合材料在飞行器制造中的应用研究
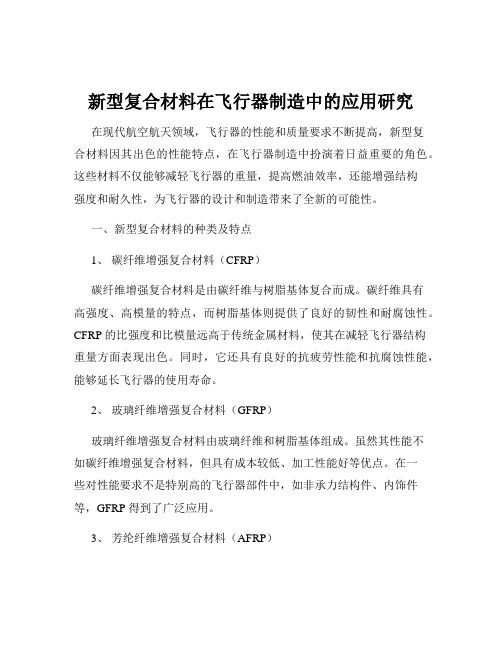
新型复合材料在飞行器制造中的应用研究在现代航空航天领域,飞行器的性能和质量要求不断提高,新型复合材料因其出色的性能特点,在飞行器制造中扮演着日益重要的角色。
这些材料不仅能够减轻飞行器的重量,提高燃油效率,还能增强结构强度和耐久性,为飞行器的设计和制造带来了全新的可能性。
一、新型复合材料的种类及特点1、碳纤维增强复合材料(CFRP)碳纤维增强复合材料是由碳纤维与树脂基体复合而成。
碳纤维具有高强度、高模量的特点,而树脂基体则提供了良好的韧性和耐腐蚀性。
CFRP 的比强度和比模量远高于传统金属材料,使其在减轻飞行器结构重量方面表现出色。
同时,它还具有良好的抗疲劳性能和抗腐蚀性能,能够延长飞行器的使用寿命。
2、玻璃纤维增强复合材料(GFRP)玻璃纤维增强复合材料由玻璃纤维和树脂基体组成。
虽然其性能不如碳纤维增强复合材料,但具有成本较低、加工性能好等优点。
在一些对性能要求不是特别高的飞行器部件中,如非承力结构件、内饰件等,GFRP 得到了广泛应用。
3、芳纶纤维增强复合材料(AFRP)芳纶纤维具有优异的抗冲击性能和耐高温性能,与树脂基体复合后形成的 AFRP 在防弹、抗冲击防护等方面具有独特的优势。
在飞行器制造中,AFRP 常用于制造飞机的舱门、机翼前缘等部位,以提高飞行器的抗冲击能力和安全性。
4、陶瓷基复合材料(CMC)陶瓷基复合材料具有耐高温、高强度、抗氧化等优异性能,适用于飞行器的高温部件,如发动机热端部件、燃烧室等。
CMC 能够承受高温燃气的冲刷和腐蚀,提高发动机的工作效率和可靠性。
二、新型复合材料在飞行器结构中的应用1、机翼和机身结构新型复合材料在机翼和机身结构中的应用可以显著减轻重量,提高结构效率。
例如,波音 787 客机的机身结构大量采用了 CFRP,其重量比传统铝合金机身减轻了 20%左右,大大降低了燃油消耗。
同时,复合材料的可设计性使得机翼和机身的气动外形能够得到更精确的优化,提高了飞行器的飞行性能。
自动铺带技术在复合材料结构件制造中的应用案例分析

自动铺带技术在复合材料结构件制造中的应用案例分析引言复合材料作为一种重要的材料,在航空航天、汽车、船舶等领域中得到了广泛应用。
复合材料的制造过程对于最终产品的质量和性能至关重要。
其中,自动铺带技术作为一种高效、精确的制造方法,被广泛应用于复合材料结构件的生产。
本文将分析自动铺带技术在复合材料结构件制造中的应用案例,并通过实例探讨其优势和挑战。
1. 自动铺带技术简介自动铺带技术是一种将预浸料纤维布按照设计要求排列、覆盖在模具上的制造方法。
该技术主要包括铺带过程、固化过程和模具脱模过程。
铺带过程中,机器人根据CAD文件或数控编程指令精确控制铺带头的运动,将预浸料纤维布覆盖在模具上。
固化过程中,通过烘烤或加热使得预浸料纤维布固化成为强度和刚度较高的复合材料。
脱模过程中,复合材料从模具上剥离,并进行后续加工。
2. 自动铺带技术在飞机制造中的应用案例2.1 A380机身板制造欧洲航天防务集团(EADS)使用自动铺带技术制造A380机身板。
铺带机器人根据设计要求,精确控制铺带头和纤维布的运动,将预浸料铺到模具上。
该技术不仅提高了生产效率,还保证了复合材料结构件的质量和一致性。
同时,相比于传统的手工操作,自动铺带技术减少了人力成本和人为误差,提高了产品质量。
2.2 波音787机翼制造波音公司采用自动铺带技术制造787机翼。
自动铺带机器人可以精确控制铺带头的运动,并快速、准确地排列纤维布。
该技术不仅提高了工作效率,还避免了手工操作中可能产生的纤维布错位、损坏等问题。
通过自动铺带技术,波音公司实现了大规模、高质量的机翼制造,为航空业带来了突破性的创新。
3. 自动铺带技术的优势和挑战3.1 优势(1)高效准确:自动铺带技术可以实现高速而精确的铺带,提高了生产效率和产品质量。
(2)一致性和可重复性:机器人通过程序控制,可以确保每次铺带过程的一致性,减少了人为误差。
(3)节约成本:相比于传统的手工操作,自动铺带技术可以减少人力成本,并大幅提高生产效率。
航空复合材料零件自动铺带技术研究
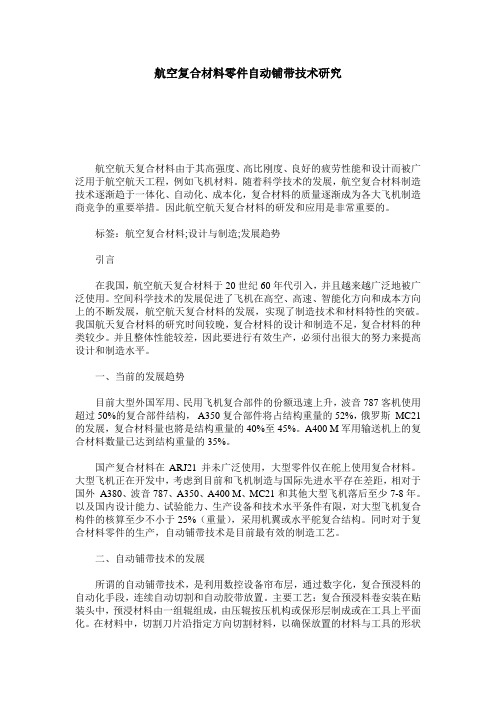
航空复合材料零件自动铺带技术研究航空航天复合材料由于其高强度、高比刚度、良好的疲劳性能和设计而被广泛用于航空航天工程,例如飞机材料。
随着科学技术的发展,航空复合材料制造技术逐渐趋于一体化、自动化、成本化,复合材料的质量逐渐成为各大飞机制造商竞争的重要举措。
因此航空航天复合材料的研发和应用是非常重要的。
标签:航空复合材料;设计与制造;发展趋势引言在我国,航空航天复合材料于20世纪60年代引入,并且越来越广泛地被广泛使用。
空间科学技术的发展促进了飞机在高空、高速、智能化方向和成本方向上的不断发展,航空航天复合材料的发展,实现了制造技术和材料特性的突破。
我国航天复合材料的研究时间较晚,复合材料的设计和制造不足,复合材料的种类较少。
并且整体性能较差,因此要进行有效生产,必须付出很大的努力来提高设计和制造水平。
一、当前的发展趋势目前大型外国军用、民用飞机复合部件的份额迅速上升,波音787客机使用超过50%的复合部件结构,A350复合部件将占结构重量的52%,俄罗斯MC21的发展,复合材料量也將是结构重量的40%至45%。
A400 M军用输送机上的复合材料数量已达到结构重量的35%。
国产复合材料在ARJ21并未广泛使用,大型零件仅在舵上使用复合材料。
大型飞机正在开发中,考虑到目前和飞机制造与国际先进水平存在差距,相对于国外A380、波音787、A350、A400 M、MC21和其他大型飞机落后至少7-8年。
以及国内设计能力、试验能力、生产设备和技术水平条件有限,对大型飞机复合构件的核算至少不小于25%(重量),采用机翼或水平舵复合结构。
同时对于复合材料零件的生产,自动铺带技术是目前最有效的制造工艺。
二、自动铺带技术的发展所谓的自动铺带技术,是利用数控设备帘布层,通过数字化,复合预浸料的自动化手段,连续自动切割和自动胶带放置。
主要工艺:复合预浸料卷安装在贴装头中,预浸材料由一组辊组成,由压辊按压机构或保形层制成或在工具上平面化。
自动铺丝技术及其在A350制造过程中的应用

自动铺丝技术及其在 A350
制造过程中的应用
郑广强,姚 锋,周晓芹
(中航复合材料有限责任公司,北京 101300)
[ 摘要 ] 介绍了自动铺丝技术的原理、特点、优势,并从铺丝设备、铺丝材料、铺丝工艺、应用等几个方面进行了阐述。 以空客 A350 复合材料制造技术为背景,分析了其机体结构的制造特点以及自动铺丝技术的应用。提出了复合材料 结构自动铺丝技术工程化应用关键问题。可为国内自动铺丝技术在大型客机复合材料结构成型中的应用提供参考。 关键词:复合材料;自动化制造;自动铺丝 DOI:10.16080/j.issn1671-833x.2017.16.076
复合材料用量的大幅提升离不 开自动化制造技术的强力支撑,尤其 是自动铺丝技术。自动铺带技术解 决 了 飞 机 小 曲 率 机 翼、尾 翼 等 翼 面 类复合材料结构的制造问题,将飞机 的复合材料用量提升到结构重量的 25% 左右;而自动铺丝技术解决了大 曲率机头、中机身、后机身、机翼大梁 等复杂结构的制造问题,将飞机的复 合材料用量提升到机体结构重量的 50% 左右,已经成为复合材料工程化 应用的里程碑。自动铺丝技术能有 效降低生产成本,提高生产效率,有 利于复合材料构件质量的可靠性和 稳定性,经济效益显著,已经成为机 身结构制造的典型工艺。大型客机
新视点
NEW VIEWPOINT
8% 其他
19% 铝合金
53% 碳纤维 复合材料
6% 钢 14% 钛合金
图1 空客A350机体材料应用情况 Fig.1 Material application of A350 airframe structure
图2 自动铺丝技术在A350中机身蒙皮上的 应用
(1)加工的零件尺寸没有限制。 自动铺丝技术对制件的尺寸大小几 乎 没 有 限 制,无 论 是 开 敞 的 曲 板 结 构,还是封闭的回转体筒段,设备制 造商都可以根据产品的尺寸大小和 结构形式开发合适的专用铺放设备。 因此,自动铺丝技术完全满足大型客 机复合材料结构件制造的尺寸需求。
复合材料自动铺带技术研究与应用

40航空制造技术·2011 年第 15 期FORUM复合材料自动铺带技术研究与应用中航工业北京航空制造工程研究所 周晓芹 曹正华 郑广强 薛向晨 梁宪珠 王永贵随着我国新型飞机项目的立项启动,复合材料用量以及大型整体构件的数量和尺寸不断增加,国内复合材料自动铺带技术得到迅速发展。
目前,北京航空制造工程研究所率先完成了我国首台大型复合材料构件自动铺带机的研制,并在此基础上深入开展了自动铺带技术研究。
周晓芹复合材料专业硕士研究生,工程师,主要从事复合材料自动铺带技术和纤维丝束自动铺放技术等方面的研究工作。
Research and Application of Automated Tape Laying Technology ofComposites坐标铺带头、高速移动横梁、高架桥式定位平台等组成,如图1所示。
除了传统数控机床X ,Y ,Z 三坐标定位以外,还有绕Z 轴方向的转动轴C 轴和绕X 轴方向摆动的A 轴,五轴联动以满足曲面铺带的基本运动要求。
● 自动铺带机联动坐标及行程范围:X :20000mm;Y:6500 mm。
● 自动铺带机坐标速度:X 、Y :60000 mm/min。
整机技术水平和性能指标达到了国外同类设备水平,能够满足新型飞机研制中大型复合材料构件的研制需求。
经过四十多年不断的发展与完善,自动铺带设备和技术在美国和欧洲已经成熟,并大规模应用于航空复合材料结构件的制造,如波音777飞机尾翼、水平和垂直安定面蒙皮,波音787翼面蒙皮,A340尾翼、水平安定面蒙皮,A380的安定面蒙皮和中央翼盒等。
自动铺带技术已经成为发达国家复合材料翼面类结构的典型制造技术之一。
随着我国新型飞机项目的立项启动,复合材料用量以及大型整体构件的数量和尺寸不断增加,国内复合材料自动铺带技术得到迅速发展。
目前,北京航空制造工程研究所率先完成了大型复合材料构件自动铺带机的研制,并在此基础上深入开展了自动铺带技术研究。
基于机器视觉的复合材料自动铺带技术发展现状及前景

基于机器视觉的复合材料自动铺带技术发展现状及前景复合材料自动铺带技术是基于机器视觉技术的一种先进技术,它通过利用计算机视觉系统自动识别工作场景和复合材料构件形状,并通过机器人系统实现自动化的复合材料铺带工艺。
随着制造业的快速发展,复合材料在航空航天、汽车、建筑等领域的应用越来越广泛,自动铺带技术的发展势在必行。
本文将从技术发展现状、应用领域和前景三个方面对基于机器视觉的复合材料自动铺带技术进行详细探讨。
首先,让我们来看一下基于机器视觉的复合材料自动铺带技术的发展现状。
目前,该技术已经取得了显著的进展。
传统的手工复合材料铺带工艺存在人工操作强度大、作业效率低等问题,而基于机器视觉的自动铺带技术可以实现高效、精准的复合材料铺带过程。
通过计算机视觉系统对复合材料构件的形状、尺寸和姿态进行三维成像和识别,再结合机器人系统的自动化操作,可以实现精确的铺带路径规划和操作,提高生产效率和质量。
目前,一些企业和研究机构已经成功开发了一些基于机器视觉的复合材料自动铺带系统,并在实际生产中取得了良好的效果。
其次,基于机器视觉的复合材料自动铺带技术在各个领域有广泛的应用。
航空航天是复合材料应用的重要领域之一,利用自动铺带技术可以实现飞机部件复合材料覆盖层的高效铺设和质量控制,提高飞机的性能和安全性。
汽车行业也是复合材料的重要应用领域,通过自动铺带技术可以实现汽车车身和零部件的轻量化设计,提升汽车的燃油经济性和碰撞安全性。
此外,建筑、船舶、电子等行业也都有复合材料的广泛应用,基于机器视觉的自动铺带技术能够为这些领域提供更加高效、精准的生产工艺。
最后,基于机器视觉的复合材料自动铺带技术有着广阔的发展前景。
随着复合材料应用的日益普及和工艺技术的不断进步,自动铺带技术将成为未来复合材料加工的主流方法之一。
随着计算机视觉和机器人技术的不断发展,自动铺带系统的成本将逐渐降低,性能将不断提高,为复合材料行业带来更多的可能性。
此外,自动铺带技术还可以与其他智能化技术相结合,如人工智能、物联网等,实现更加智能、高效的复合材料生产线。
复合材料成型工艺及其在航空航天上的应用

水溶性聚乙烯醇型砂 、金属框架+石膏表层 (3)缠绕机:缠绕线型准确。
立式缠绕机、卧式缠绕机、编程系统。
17
复合材料成型工艺及其在航空航天上的应用 1 缠绕成型技术
图 环向缠绕
图 螺旋缠绕
图 平面缠绕
18
复合材料成型工艺及其在航空航天上的应用 1 缠绕成型技术
拉挤成型工艺的缺点是产品形状单调,只能生产线形型材,而且横向强度不高。
28
复合材料成型工艺及其在航空航天上的应用
7 拉挤成型技术
(1)拉挤工艺用原材料 ①树脂基体: 不饱和聚酯树脂,约占本工艺树脂用量的90以上,另外还有环氧树脂、
乙烯基树脂、热固性甲基丙烯酸树脂、改性酚醛树脂、阻燃性树脂等; ②增强材料 :主要是玻璃纤维及其制品,如无捻粗纱、连续纤维毡等。为了满足制
如果能够使石墨的六角层平面沿着碳纤维的纤维轴方向择优取向,就会获得高轴向模量的碳纤维。
碳纤维是一个通用名称,它表示一系列由不同原材料和工艺方法制备、主要由碳元素 构成的纤维,如聚丙烯腈(PAN)基碳纤维、粘胶(Rayon)基碳纤维和沥青(Pitch) 基碳纤维,由于石墨层片的堆叠厚度和石墨层片与纤维轴的取向不同,使这些碳纤维的 性能不同。
6
复合材料成型工艺及其在航空航天上的应用 复合材料增强体-碳纤维
有机先驱体转化法:极高模量的碳(石墨)纤 维可以通过有机先驱丝氧化(或称不熔化)、碳化 和随后高温石墨化的方法来制造。有机先驱丝是碳 纤维的原材料,通常是一些特殊的高聚物纤维,它 们可以在不熔化条件下碳化。有机先驱纤维是由长 分子链(当它完全拉直时长度为0.1~1μm)按无规 方式排列构成的。
- 1、下载文档前请自行甄别文档内容的完整性,平台不提供额外的编辑、内容补充、找答案等附加服务。
- 2、"仅部分预览"的文档,不可在线预览部分如存在完整性等问题,可反馈申请退款(可完整预览的文档不适用该条件!)。
- 3、如文档侵犯您的权益,请联系客服反馈,我们会尽快为您处理(人工客服工作时间:9:00-18:30)。
自动铺带技术在航空复合材料制造领域的应用
先进复合材料已经成为航空航天器主要结构材料,各类飞机的复合材料用量近年来迅速增加。
飞机复合材料主承力构件主要采用预浸料成形技术制造,而自动铺放成形是替代人工铺叠、提高质量和生产效率的关键,在制造大型复合材料构件时优势极为突出。
以大型飞机为例,从A380到B787,A350,其复合材料用量大幅度增加,正是由于自动铺放技术的发展与应用起到了关键作用。
为此,在接下来的文章中,将围绕自动铺带技术在航空复合材料制造领域的应用方面展开详细分析,希望能够给相关人士提供重要的参考价值。
标签:自动铺带技术;航空;复合材料
引言:具有高效率、高质量和低成本优点的自动铺带铺放技术已经成为发达国家航空复合材料构件的成熟制造技术,这一制造技术在国内的引进和发展,也必将在国产大飞机的研制和生产中占有重要的地位,为国产大飞机的顺利升空提供强有力的技术支撑。
1. 自动铺带技术的发展
所谓自动铺带技术,就是采用数控铺层设备,通过数字化、自动化的手段实现复合材料预浸布、带的连续自动切割和自动铺放。
主要工作过程为:将复合材料预浸料卷安装在铺放头中,预浸材料由一组滚轮导出,并由压紧滚轮或可随形机构压紧在工装或上一层已铺好的材料上,切割刀将材料按设定好的方向切断,能保证铺放的材料与工装的外形相一致。
铺放的同时,回料滚轮将背衬材料回收。
自动铺带作为典型的增料加工成型技术,其成型设备的制造技术涉及机电装备技术、CAD/CAM软件技术和材料工艺技术等多个研究领域,可实现:第一,大限度地利用单向预浸带(优于手工铺层采用的预浸布),并可减轻结构重量;第二,可更自由地设计铺层,发挥复合材料可设计性优势,在应力梯度和应力异常的区域选择性铺放补强,实现了整个结构的零剩余强度;第三,提高工作质量和铺放效率。
采用该技术,可提高复合材料裁片外形、纤维方向等几何参数的精确度和铺叠位置、方向、角度的准确性,从而避免了人为铺放产生的偏差,如产品出现缺陷的几率大、零件制造质量重复性差、质量分散性大,以及尺寸精度和铺放位置准确度不能满足大尺寸、高精度零件制造的要求等问题。
采用复合材料自动铺带技术可在提高质量的同时,大幅度地节省原材料,降低制造成本。
同时,由于可以实现整个结构的零剩余强度设计,结构重量大大减轻。
2.自动铺带技术在航空复合材料制造领域的应用
2.1预浸料的选择
自动铺带技术所铺放的复合材料称为预浸料,它作为复合材料制造过程中的中间产品,直接影响到复合材料构件的质量。
预浸料主要由树脂与碳纤维构成,缠绕成卷,因初始有一定的黏性,为防止保存时相邻的预浸料带相互粘结,预浸
料背后有一层背衬纸,背衬纸起着传递预浸料带的作用。
预浸料带的技术指标主要包括黏性、铺覆性、树脂含量、单位面积纤维质量、存储期等,其中黏性与铺覆性对铺带机铺放成功与否至关重要。
预浸料带黏性是指预浸料带与模具或其他预浸料带之间形成粘结的能力,预浸料带黏性必须适中。
黏性过小,相邻料带之间无法顺利贴合,料带将无法精确铺放;黏性过大,铺带出现失误后,修改困难。
预浸料带的铺覆性是指预浸料带与不同曲率的模具表面之间的适应性,其中纤维和背衬纸是影响铺覆性的主要因素,若预浸料带铺覆性较差,料带则易断裂,或形成架桥、褶皱,导致自动铺带受阻,不易形成生产力。
此次蒙皮铺带的预浸料为T700/LT-03A高强碳纤维/中温固化环氧树脂干法预浸料,铺带温度的设置会影响预浸料的黏性和铺覆性。
一方面,在铺带加热温度范围内,随着温度升高,树脂粘度下降而流动性上升。
随着树脂流动性上升,树脂对预浸料界面的浸润能力提高,这样可以提高预浸料之间或者预浸料与模具之间的贴合能力,有利于铺放过程顺利进行。
但另一方面,随着温度的上升,预浸料变“软”,这样在铺放过程中增大预浸料在复杂模具表面形成架桥的机会,温度越高,预浸料越容易老化。
因此,在机翼蒙皮自动铺带中,加热温度的选取倾向于防止褶皱、架桥的产生和预浸料老化,一般设置在40℃~60℃。
2.2精确铺放控制
将铺层的每一片料带精确铺贴到位,针对自动铺带做控制设计,这是自动铺带技术应用的基础。
精确铺放控制需要做好以下几点工作,方能保证蒙皮按设计数模精确铺带出来,并达到工艺要求。
第一,铺带模具涂刷微量树脂。
首先用丙酮浸润料带,将稀释出的微量树脂混合丙酮均匀涂刷于模具上,保证模具有一定黏性,目的是将第一层按程序精确铺带至模具上。
第一层料带是否精确铺带,直接影响后续铺层的精确铺带、准确定位和间隙控制。
第二,超声切割刀调整调整好超声切割刀B1、B2的切割深度,防止过切导致料带断裂。
调整的方法应根据现场切割情况再做适应性调整。
第三,最小切割角度设置。
机翼蒙皮在切割形状时,最小切割角度的设计是否精准,将直接影响程序生成后置加工代码,零件铺层能否铺放成功。
通过选取材料T700/LT03A,分别进行1°、2°、3°、4°、5°切割角料带切割试验,其中铺放温度50℃。
经过实验可知,复杂形状切割铺放时,最小切割角度越小,切割及铺放成功率越低,T700/LT03A最小切割角度至少应大于等于3°[1]。
第四,铺带程序设计。
铺带机由150mm幅宽的预浸料带逐块铺满一个铺层,每一块的初始铺放和准确定位直接关系到了该条料片能否成功铺带,否则褶皱、搭接、间隙超差、定位不准,将导致料片裁剪变短或作废,并需重新再次铺叠。
因此在程序设计时,采取如下措施:其一,对于铺带足够长(目前经验参数约为200mm以上)或者料片有一端在零件余量线上的,加长SHOE 的工作长度,以加大料片与工装或上一铺层的接触面积;其二,铺带尾端为直角,且长度较短(约400mm以下)的可以不使用ROLLER的,不进行ROLLER切换,改为SHOE铺放后根据实际情况,单独进行二次压实;其三,对于长度短于200mm的复杂图形或特殊图形,铺叠难度较大,改用手铺或加长铺层长度。
2.3将程序默认的交叉异向铺带设计改为同向铺带
将默认的交叉异向铺带改进为同向铺带,提高了设备运行的可控性和安全
性。
交叉异向铺带每铺带完成一个料带,均会沿C轴旋转180°,持续操作设备时间较长的操作者,忽略此设备动作易造成工伤事故。
而同向铺带正好避免了这个问题,铺带均朝同一方向,提高了可控性和安全性。
2.4自动铺放与激光投影、自动下料技术配合使用
自动下料与激光投影技术配合使用,针对小铺层手工铺叠,解决了料片小、铺带定位难的问题,保证了零件制造的精确性。
采用上述的铺带设计和工艺方案,应用于某型无人机复合材料机翼蒙皮的制造,经过多架份的制造验证,机翼蒙皮的内部质量经超声检测合格,表面质量与随炉件力学性能合格,满足设计技术要求。
结论:
简而言之,虽然自动铺带技术已成功应用于某型无人机复合材料机翼蒙皮的制造,但铺带工装、零件铺层的设计会影响自动铺带技术的应用,所以要想自动铺带技术推广应用于各型机的铺带,需要与飞机设计单位协调沟通好铺层的设计,与工装设计单位协商好自动铺带机运行对工装型面的要求[2]。
参考文献:
[1]左龙彦,肖军,李勇,等.MFC环境下基于OpenGL的开孔圆筒的自动铺带建模与仿真[J].玻璃钢/复合材料,2018,29(3):24-26.
[2]张建宝,文立伟,肖军,等.自动铺带机送带控制技术[J].南京航空航天大學学报,2018,41(6):772-776。