热熔自攻丝FDS工艺简介
“流钻螺钉”(FDS)工艺
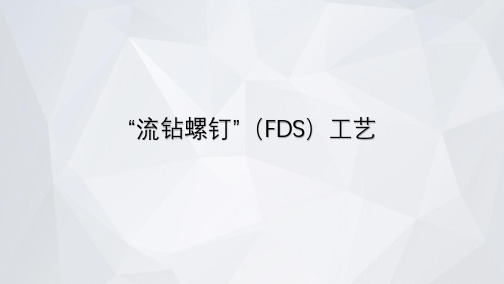
BMW 8 Series Coupe
Jaguar I-PACE
五、 FDS工艺的优、缺点
优点: 1、可连接的材料种类多,包括超高强钢、铝镁合金、复合材料在内 的异种材料; 2、单面操作,可用于封闭型腔结构、壁厚大或封闭腔体,无法使用 SPR或Clinching; 3、板件被加热,板件与螺钉接触好,连接强度大。 4、 螺钉可拆卸,回收方便,可使用公制螺栓进行返修。 5、工作环境清洁,无火花、碎屑,几乎无噪声。 缺点 1、设备系统成本远高于电阻点焊,铆钉成本高(单价 0.15 欧元) ; 2、单面施力,连接时需要高强度刚性支撑; 3、工艺完成后材料正反面均有较大凸起,同时大量使用会增加车身 自重(M5单个螺钉重4~5g,而SPR铆钉约0.3~0.8g) 4、CT时间长,约为2~6S(部分设备优化可达到1.5~3S,取决于板材 厚度)
六、FDS常见缺陷:
Hale Waihona Puke 缺失/位置错误螺栓断裂/破损
边距过小
头部间隙
FDS返修方法: 在缺陷螺钉附近重新打一个螺钉。
七、设备系统组成:
4.
2.
FDS两种标准枪
Standard Length
Reduced Length
二、 FDS工艺历史
FDS发明于1990年,1996年首次应用于莲花轿车车身框架的连接。由于当时采用的主 要是手持夹具进行装夹,整个装配过程的时间和精度不好控制,使得该工艺使用受到限 制。 20世纪90年代末,巍博(Weber)为EJOT公司开发了RSF20S螺钉驱动系统,此系 统的问世实现了FDS工艺的自动化生产,并可以增大连接的板材总厚度,于2000年首次 应用在奥迪A4后轮罩的连接上。
三、 FDS工艺的过程
FDS连接工艺过程包括六个阶段:旋转(加热)→穿透→通孔→攻螺纹→拧螺纹→紧固。
铝合金车身连接技术及应用实例
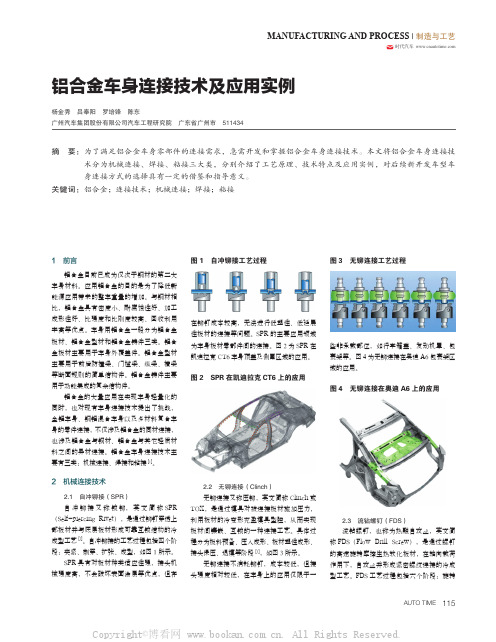
AUTO TIME115MANUFACTURING AND PROCESS | 制造与工艺时代汽车 铝合金车身连接技术及应用实例杨金秀 吕奉阳 罗培锋 陈东广州汽车集团股份有限公司汽车工程研究院 广东省广州市 511434摘 要: 为了满足铝合金车身零部件的连接需求,急需开发和掌握铝合金车身连接技术。
本文将铝合金车身连接技术分为机械连接、焊接、粘接三大类,分别介绍了工艺原理、技术特点及应用实例,对后续新开发车型车身连接方式的选择具有一定的借鉴和指导意义。
关键词:铝合金;连接技术;机械连接;焊接;粘接1 前言铝合金目前已成为仅次于钢材的第二大车身材料。
应用铝合金的目的是为了降低新能源应用带来的整车重量的增加。
与钢材相比,铝合金具有密度小、耐腐蚀性好、加工成形性好、比强度和比刚度较高、回收利用率高等优点。
车身用铝合金一般分为铝合金板材、铝合金型材和铝合金铸件三类。
铝合金板材主要用于车身外覆盖件。
铝合金型材主要用于前后防撞梁、门槛梁、纵梁、横梁等断面规则的简单结构件。
铝合金铸件主要用于功能集成的复杂结构件。
铝合金的大量应用在实现车身轻量化的同时,也对现有车身连接技术提出了挑战,全铝车身、钢铝混合车身以及多材料复合车身的零件连接,不仅涉及铝合金的同材连接,也涉及铝合金与钢材、铝合金与其它轻质材料之间的异材连接。
铝合金车身连接技术主要有三类:机械连接、焊接和粘接[1]。
2 机械连接技术2.1 自冲铆接(SPR)自冲铆接又称锁铆,英文简称SPR (Self-piercing Rivet),是通过铆钉穿透上部板材并与底层板材形成可靠互锁结构的冷成型工艺[2]。
自冲铆接的工艺过程包括四个阶段:夹紧、刺穿、扩张、成型,如图1所示。
SPR 具有对板材种类适应性强,接头机械强度高,不会破坏表面涂层等优点,但存在铆钉成本较高,无法进行低塑性、低延展性板材的连接等问题。
SPR 的主要应用领域为车身板材零部件间的连接。
图2为SPR 在凯迪拉克CT6车身顶盖及侧围区域的应用。
汽车车身快速试制与质量改进
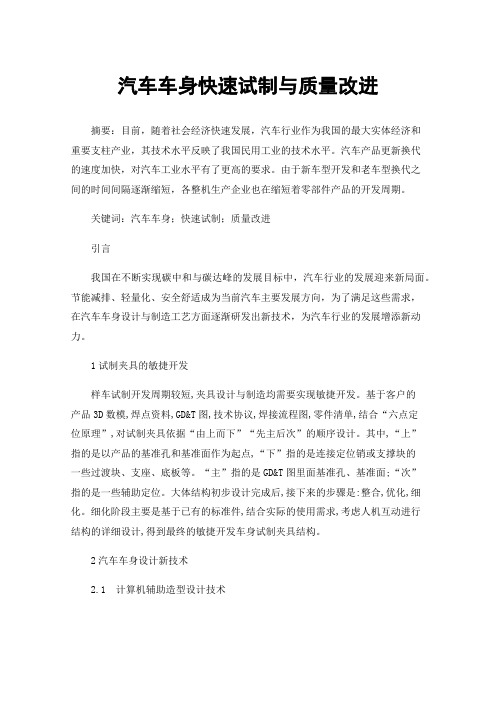
汽车车身快速试制与质量改进摘要:目前,随着社会经济快速发展,汽车行业作为我国的最大实体经济和重要支柱产业,其技术水平反映了我国民用工业的技术水平。
汽车产品更新换代的速度加快,对汽车工业水平有了更高的要求。
由于新车型开发和老车型换代之间的时间间隔逐渐缩短,各整机生产企业也在缩短着零部件产品的开发周期。
关键词:汽车车身;快速试制;质量改进引言我国在不断实现碳中和与碳达峰的发展目标中,汽车行业的发展迎来新局面。
节能减排、轻量化、安全舒适成为当前汽车主要发展方向,为了满足这些需求,在汽车车身设计与制造工艺方面逐渐研发出新技术,为汽车行业的发展增添新动力。
1试制夹具的敏捷开发样车试制开发周期较短,夹具设计与制造均需要实现敏捷开发。
基于客户的产品3D数模,焊点资料,GD&T图,技术协议,焊接流程图,零件清单,结合“六点定位原理”,对试制夹具依据“由上而下”“先主后次”的顺序设计。
其中,“上”指的是以产品的基准孔和基准面作为起点,“下”指的是连接定位销或支撑块的一些过渡块、支座、底板等。
“主”指的是GD&T图里面基准孔、基准面;“次”指的是一些辅助定位。
大体结构初步设计完成后,接下来的步骤是:整合,优化,细化。
细化阶段主要是基于已有的标准件,结合实际的使用需求,考虑人机互动进行结构的详细设计,得到最终的敏捷开发车身试制夹具结构。
2汽车车身设计新技术2.1 计算机辅助造型设计技术随着汽车技术的不断发展与改进,人们审美能力与需求的不断提高,汽车造型也随着时代潮流变化而不断更新,由最初的箱型逐渐朝着多元化的流线型造型演变。
汽车造型设计师需要确保设计出的汽车造型不仅满足汽车驾驶功能需求,还需要符合人们的审美要求。
随着计算机图形学与几何设计的不断发展,在车身造型设计中引入计算机辅助系统(CAD/CAM软件),借助计算机构建车身三维数字化模型。
计算机辅助造型技术主要应用在车身造型的草图设计与自由曲面设计中,一是草图设计,主要是满足设计师传统手绘习惯衍生出的造型技术,是传统CAD系统与工业设计的桥梁,借助人机交互技术模拟设计手绘,并采用草图重建技术建立草图CAD系统对车身造型进行设计。
热熔自攻丝连接工艺的分析与优化

第1期2019年1月组合机床与自动化加工技术ModularMachineTool&AutomaticManufacturingTechniqueNo.1Jan.2019文章编号:1001-2265(2019)01-0141-03㊀㊀㊀㊀DOI:10.13462/j.cnki.mmtamt.2019.01.038收稿日期:2018-03-21ꎻ修回日期:2018-04-22㊀∗基金项目:国家科技支撑项目(2012BAF06B01)ꎻ国家智能制造装备发展专项项目(发改办高技[2011]2548号)作者简介:林巨广(1963 )ꎬ男ꎬ安徽六安人ꎬ合肥工业大学教授ꎬ博士生导师ꎬ研究方向为汽车自动化装备㊁汽车试验台ꎻ通讯作者:钱让发(1992 )ꎬ男ꎬ安徽池州人ꎬ合肥工业大学硕士研究生ꎬ研究方向为白车身连接工艺㊁机器人技术及应用ꎬ(E-mail)qianrangfa@163.comꎮ热熔自攻丝连接工艺的分析与优化∗林巨广aꎬ钱让发aꎬ袁㊀波aꎬ周建君bꎬ潘伟涛b(合肥工业大学a.机械工程学院ꎬ合肥㊀230009ꎻb.智能制造研究院ꎬ合肥㊀230009)摘要:以铝合金板件6111及6082-T6为研究对象ꎬ采用正交实验的方法ꎬ通过对连接接头的剖面进行观察和极差法分析ꎬ研究轴向下压力(downholder力)㊁螺钉转速和拧紧扭矩三组过程参数对热熔自攻丝工艺连接接头参数的影响权重ꎬ并给出了1.2mm6111+3mm6082 ̄T6搭接的最优过程参数组合ꎮ实际应用表明ꎬ分析得出的参数权重能够指导选择合适的热熔自攻丝过程参数ꎬ减少试验次数ꎬ提高生产效率ꎮ关键词:热熔自攻丝ꎻ轴向下压力ꎻ转速ꎻ拧紧扭矩中图分类号:TH162ꎻTG506㊀㊀㊀文献标识码:AAnalysisandOptimizationofFlowDrewScrewTechnologyLINJu ̄guangaꎬQIANRang ̄faaꎬYUANBoaꎬZHOUJian ̄junbꎬPANWei ̄taob(a.SchoolofMechanicalEngineeringꎻb.IntelligentManufacturingInstituteꎬHefeiUniversityofTechnologyꎬHefei230009ꎬChina)Abstract:TheFlowDrillScrewdriving(FDS)connectionofaluminum6111and6082 ̄T6wasstudied.Thedesignoforthogonalexperiment(DOE)methodwasused.Afterobservationandrangemethodanaly ̄sisofthejointprofileꎬtheinfluenceweightofthreemainprocessparameters:downholderforceꎬscrewspeedandtighteningtorqueontheparametersofFlowDrillScrewdrivingprocesswereinvestigated.Theoptimalprocessparameter㊀of1.2mm6111+3mm6082 ̄t6wasgiven.ThepracticalapplicationshowsthattheparameterweightobtainedbytheanalysiscanguidetheselectionofthesuitableprocessparametersoftheFlowDrillScrewdrivingprocessꎬreducethenumberofexperimentsandimprovetheproductioneffi ̄ciency.Keywords:flowdrillscrewdrivingꎻdownholderforceꎻscrewspeedꎻtighteningtorque0㊀引言汽车产量以及保养量的增加带来了安全㊁污染㊁能耗等问题ꎬ为提高能源利用率ꎬ达到节能减排的效果ꎬ提出了汽车轻量化设计理念ꎮ美国铝业公司数据显示ꎬ汽车中典型铝质零件的一次减重效果可达30%~40%ꎬ二次减重可进一步提高到50%[1 ̄2]ꎮ采用铝制车身可以减少汽车增长带来的环境与能源压力ꎬ达到汽车轻量化的设计要求ꎮ在铝车身连接工艺中ꎬ热熔自攻丝㊁铝点焊㊁自冲铆被广泛使用ꎮ但由于铝合金化学活性强㊁极易形成氧化膜㊁线膨胀系数大㊁导热强ꎬ给焊接带来困难[3]ꎻ自冲铆工艺需要根据不同材料性质㊁板件厚度来选择不同的钉/铆搭接方式ꎬ增加人工及试验成本ꎮ热熔自攻丝(FlowDrillScrewdriving简称FDS)[3]是一种新型的连接工艺ꎮ它综合了摩擦钻孔以及螺纹成型技术ꎬ在工作过程中紧固螺钉既作为钻孔工具ꎬ又作为紧固件ꎬ避免以上工艺的连接限制ꎮ在连接过程中螺钉只需与板件单面接触ꎬ大大提高了空间利用率ꎬ保证设计的灵活性ꎮ在国外ꎬ一些公司对FDS工艺已经进行深入的研究ꎮSkovronJ等[4]详细地介绍了FDS工艺流程ꎬ并着重研究拧紧力与钻孔速度对FDS影响ꎻMiller等[5]对摩擦钻孔的过程进行了一系列详细的研究与分析ꎻJo ̄hanKolstøSønstabø等[6]通过一系列FDS连接件的剥落剪切试验ꎬ研究连接件的强度以及失效形式ꎬJEGOULD等[7]将FDS工艺与其他铝合金连接工艺进行比较ꎮ目前ꎬ我国对FDS工艺研究比较少ꎬ因此对FDS工艺参数研究具有重要意义ꎮ本文提出通过正交试验设计方法对热熔自攻丝工艺进行优化ꎬ研究FDS的轴向下压力㊁螺钉转速㊁拧紧扭矩对接头连接质量影响规律ꎬ为热熔自攻丝工艺参数优化提出有益的参考ꎬ具有重要实践与指导意义ꎮ1㊀热熔自攻丝(FDS)简介1.1㊀FDS用紧固螺钉介绍试验使用阿诺德公司制造的螺钉ꎬ如图1所示ꎬ它是由五部分组成:螺钉头部㊁底面沟槽㊁紧固螺纹㊁攻丝螺纹和尖部ꎮ螺钉头部采用的是一种特殊的法兰头ꎬ它与FDS机器中相应的刀头紧密地啮合在一起ꎮ其下方有一圈沟槽ꎬ用来容纳连接过程中由于板件变形向上流出的板材ꎮ螺钉的主体部分由紧固螺纹和攻丝螺纹构成ꎬ确保上下层板件紧密连接在一起ꎮ螺钉的尖端经过特殊的热处理ꎬ硬度大且耐高温ꎬ能够保证其在板件上形成孔洞ꎮ图1㊀FDS紧固螺钉1.2㊀FDS工艺过程简介热熔自攻丝是一个连续的自动化工程ꎬ它可以连接多种不同的材料ꎮ在整个过程中它使用专用的螺钉作为工具和紧固件ꎬ来完成刺穿㊁挤压㊁形成螺纹㊁产生扭矩的连续过程ꎬ来达到连接板件ꎬ产生夹紧力ꎮFDS整个工艺过程(见图2)由五步组成:(1)准备:紧固螺钉与FDS机器啮合ꎻ(2)形成孔洞:在机器的带动下ꎬ紧固螺钉在连接的上层板材表面高速旋转ꎬ使连接区域上层板加热塑化ꎮ紧固螺钉在压力作用下进入板件ꎬ同时在工件表面形成披锋(凸台)[8]ꎻ(3)形成螺纹:在孔洞形成之后ꎬ紧固螺钉转速降低ꎮ其螺纹成型区域在板件中形成母螺纹ꎻ(4)螺纹旋入:当深度传感器检测到攻螺纹阶段结束后ꎬ为了保证新形成的母螺纹不被损坏ꎬ紧固螺钉的转速进一步降低ꎻ(5)拧紧:拧紧螺钉ꎬ使其达到设定的扭矩ꎮ0准备㊀㊀㊀1成孔㊀㊀2形成螺纹㊀3螺纹旋入㊀4最后拧紧图2㊀FDS工艺流程1.3㊀FDS连接质量的评价标准在实际生产中ꎬ对FDS连接板件质量评估主要分为外观检测和剖面形状检测ꎮ由于外观检测存在着主观性ꎬ为了定量的了解各连接参数对连接结果的影响ꎬ本文采用剖面形状检测方法来判断连接质量ꎮ㊀㊀在进行剖面检测前ꎬ需要将连接件沿着螺钉中心剖开ꎮ通过显微镜检测剖面的状态以及螺纹形状(见图3)ꎬ检测标准主要分为以下几个方面:(1)测量螺钉头部底座与上层板之间的间隙ꎬ记做d/mmꎮ间隙不能过大ꎬ一般不超过0.3mmꎻ(2)测量板与板之间的间隙ꎬ记做b/mꎻ(3)观察下层板的螺牙个数ꎬ并测量有效螺牙的高度记做a/mmꎮ图3㊀剖面测试示意图2㊀FDS实验设计2.1㊀试验目的通过试验确定FDS工艺连接中轴向下压力㊁螺钉转速㊁拧紧扭矩这三个过程参数对连接结果的影响程度ꎬ为以后的生产中提供参考ꎮ2.2㊀试验仪器准备(1)试验用板件用于汽车车身板的常见铝合金有2000系㊁5000系以及6000系铝合金[9]ꎮ本次实验采用型号为6111与6082 ̄T6的板材ꎬ其规格为40mmˑ40mmꎬ板材厚度以及材料的力学性能如表1所示ꎮ根据阿诺德公司给出的技术要求ꎬ将6111板材放置在上层ꎬ6082 ̄T6板材放置于下层ꎮ这样能够提高下层板件中有效螺纹长度ꎬ提升连接强度ꎮ表1㊀铝合金板件的力学性能材料厚度/mm屈服强度/MPa拉伸强度/MPa61111.51602906082 ̄T63.0140245(2)试验用仪器在试验中使用的是Deprag公司提供的FDS连接设备㊁阿诺德公司的5ˑ24mm紧固螺钉㊁专业的金相切割设备以及显微镜ꎬ如图4所示ꎮ(a)FDS连接设备㊀㊀㊀㊀㊀(b)显微测量设备图4㊀试验设备241 组合机床与自动化加工技术㊀第1期2.3㊀正交实验设计(1)确定影响试验结果的因子及水平影响FDS连接强度的三个因素分别为:螺钉转速(A)㊁轴向下压力(B)㊁拧紧扭矩(C)ꎮ假设三个因素之间互不影响ꎬ根据实际经验ꎬ确定各因素采用的水平如表2所示ꎮ表2㊀正交表格各因素及水平水平因素螺钉转速/rpm轴向下压力/N拧紧扭矩/N m140006008260009001038000120012㊀㊀(2)制定合适的正交表格试验中各因素有三个水平ꎬ故选用L9(33)的正交实验ꎬ设计出表3所示的试验方案ꎮ表3㊀FDS试验正交表格试验组别螺钉转速/rpm轴向下压力/N拧紧扭矩/N M1400060082400090010340001200124600060010560009001266000120087800060012880009008980001200103㊀实验结果分析与处理根据表3中提供的数据ꎬ在不同的螺钉转速㊁轴向下压力以及拧紧扭矩下进行试验ꎬ得到如图5所示的剖面图ꎮ(a)1号试验㊀㊀(b)2号试验㊀㊀(c)3号试验(d)4号试验㊀㊀(e)5号试验㊀㊀(f)6号试验(g)7号试验㊀㊀(h)8号试验㊀㊀(i)9号试验图5㊀6111+6082 ̄T6连接件剖面检测3.1㊀观察分析各工艺参数对测试结果影响分析图5ꎬ可以得到以下结论:(1)拧紧扭矩对螺钉头部间隙有显著的影响ꎮ1号㊁6号㊁8号试验中螺钉头部间隙普遍偏大ꎬ这显然是因为拧紧扭矩过小ꎻ在2号㊁4号㊁9号试验中ꎬ拧紧扭矩增加ꎬ螺钉头部间隙显著减小ꎮ试验2中由于螺钉转速偏低ꎬ虽然扭矩增加ꎬ螺钉头部仍然有较大的间隙ꎮ(2)轴向下压力是影响板件间隙的重要因素ꎮ对比1号㊁4号㊁7号与2号㊁5号㊁8号两组实验ꎬ可以看出ꎬ随着轴向下压力增加ꎬ板件间隙变小ꎮ在轴向下压力相同时(1号㊁4号㊁7号试验)ꎬ拧紧扭矩及螺钉转速的增加能够降低板件间隙ꎮ(3)对剖面图分析可知ꎬ1号㊁2号㊁6号㊁8号试验中螺钉头部间隙偏大(大于0.3mm)ꎬ1号㊁2号㊁4号㊁7号试验中板件间隙偏大ꎬ均不满足生产要求ꎮ故在实际生产中ꎬ拧紧扭矩和轴向下压力不能设置过小ꎮ3.2㊀极差法分析工艺参数对测试结果影响为进一步研究工艺参数对连接结果的影响ꎬ按照图3给出的方法在光学显微镜下对接头的几个参数进行测量ꎬ得到的测量数据如表4所示ꎮ表4㊀各参数测量结果组别板间间隙b/mm螺牙深度a/mm螺钉头部间隙d/mm10.970.512.2020.870.711.4530.660.55040.870.58050.520.71060.420.611.4370.850.64080.660.591.590.520.580分别用A㊁B㊁C表示螺钉转速㊁轴向下压力和拧紧扭矩ꎬb㊁a㊁d表示板间间隙㊁螺牙深度㊁螺钉头部间隙ꎮ根据表4中测量的数据ꎬ计算I㊁II㊁III测量参数结果的差异ꎬ反映各排因素(工艺参数)取不同水平时对测量的结果影响ꎮ表5中R代表极差ꎮ表5㊀测量参数极差计算结果极差bABCAaBCAdBCI2.502.692.051.771.731.713.652.205.13II1.812.052.261.92.011.871.432.951.45III2.031.62.031.811.641.91.51.430R0.691.090.230.130.370.192.151.523.68分析表5中数据ꎬ可以得到以下结论:(1)各工艺参数对接头的测量结果影响ꎮ由表5知ꎬ对于板件间隙bꎬ轴向下压力影响最大ꎬ螺钉转速次之ꎬ拧紧扭矩影响最小ꎬ即B>A>Cꎻ对于螺牙深度aꎬ轴向下压力影响最大ꎬ拧紧扭矩次之ꎬ螺钉转速影响最小ꎬ即B>C>Aꎻ对于螺钉头部间隙ꎬ拧紧扭矩影响最大ꎬ螺钉转速次之ꎬ轴向下压力影响最小ꎬ即C>A>Bꎮ(2)相对于螺钉头部间隙㊁板件间隙ꎬ三种工艺参数对螺牙高度影响较小ꎮ在试验中可以优先考虑三种工艺参数对螺钉头部㊁板件间隙的影响ꎻ(3)确定较好的工艺参数组合ꎮ板件间隙b越小ꎬ连接效果越好ꎬ根据表5计算ꎬA2B3C3为最佳组合ꎻ螺牙深度越大ꎬ连接效果越好ꎬ故A2B2C3为最佳组合ꎻ螺钉头部间隙越小ꎬ越满足连接效果ꎬ故A2B3C3为最佳组合ꎮ综合以上数据ꎬ选取A2B3C3达到最佳效果ꎮ(下转第146页)341 2019年1月㊀㊀林巨广ꎬ等:热熔自攻丝连接工艺的分析与优化3㊀加工试验为了验证该加工方法的可靠性ꎬ在相同条件ꎬ拟采用等间距直线逼近法㊁等步长直线逼近法㊁圆弧逼近轮廓法进行试验验证ꎮ通过实际加工检测ꎬ上述3种逼近方法加工结果对比如表1所示ꎮ表1㊀3种逼近方法的加工结果对比表逼近方法精度(尺寸㊁形位)表面粗糙度(μm)等间距直线逼近IT8-106.3等步长直线逼近IT6-73.2圆弧逼近IT5-60.4从表1中可以看出ꎬ圆弧逼近的精度和表面质量远高于直线逼近的精度和表面质量ꎮ将设计出的两个程序在FANUC0i ̄TC机床上运行后ꎬ轨迹显示见图3ꎬ加工出的实物见图4ꎬ经检验零件尺寸精度㊁形位精度符合设计要求ꎮ图3抛物线轨迹㊀㊀㊀图4内抛物面实物4㊀结论基于圆弧插补原理ꎬ编制宏程序ꎬ在FANUC0i ̄TC数控机床上ꎬ进行加工验证ꎮ结果表明ꎬ采用等间距直线逼近法对零件内抛物面进行粗加工ꎬ圆弧逼近法对零件内抛物面进行精加工ꎬ使零件尺寸精度提高了两个公差等级ꎬ表面粗糙度达到0.4μmꎬ有效的保证了高精度零件的加工质量ꎬ这对同类复杂形面零件的加工具有较高的参考价值ꎮ[参考文献][1]刘繄.几种典型非圆曲线编程误差变步长控制算法[J].机床与液压ꎬ2009ꎬ37(6):53-55.[2]岳秋琴.宏程序在非圆曲线数控车削加工中的应用[J].煤矿机械ꎬ2013ꎬ34(7):131-133.[3]吕孝敏.抛物线插补指令的设计与应用[J].安徽农业大学学报ꎬ2013ꎬ40(2):326-331.[4]赫焕丽.圆弧逼近法在车削加工非圆曲线中的应用研究[J].煤矿机械ꎬ2013ꎬ34(8):151-153.[5]刘振超.在数控车床上加工偏置抛物线回转孔[J].煤矿机械ꎬ2013ꎬ34(6):126-128.[6]程启森.非圆曲线的宏程序编制方法应用研究[J].现代制造工程ꎬ2010(3):46-48.[7]廖效果.数控技术[M].武汉:湖北科技出版社ꎬ2000.[8]刘海涛ꎬ姜海林.一种新的加工椭圆曲线的方法[J].机床与液压ꎬ2010ꎬ38(14):50-51.[9]王红梅ꎬ王文友ꎬ葛晓阳.利用数控车床加工椭圆曲线的方法[J].机床与液压ꎬ2012ꎬ40(22):13-14ꎬ45.[10]陈艳红.非圆曲线轮廓的数控加工方法研究[J].机床与液压ꎬ2011ꎬ39(10):23-25.(编辑㊀李秀敏)(上接第143页)4㊀结论本文通过几组正交试验ꎬ对热熔自攻丝工艺的过程参数进行分析ꎬ得出以下结论:(1)对于1.5mm6111与3mm6082 ̄T6铝合金板件的连接工艺ꎬ采用6000r/min的螺钉转速㊁1200N的轴向下压力㊁12N的拧紧扭矩能够达到最佳的连接效果ꎻ(2)通过正交试验表:拧紧扭矩是影响螺钉头部间隙的最重要因素ꎬ随着拧紧扭矩增加ꎬ螺钉头部间隙减小ꎻ轴向下压力是影响板件间隙的重要因素ꎬ随着轴向下压力增加ꎬ板件间隙减小ꎻ轴向下压力对螺牙啮合高度影响最大ꎬ轴向下压力偏大㊁偏小均使啮合高度降低ꎬ需要通过试验选择合适参数ꎻ(3)在实际生产中ꎬ不能只考虑剖面检测结果参数ꎬ还需要考虑过程参数是否合理ꎮ如拧紧扭矩过大会使螺钉断裂ꎬ轴向下压力过大会使板件变形ꎮ[参考文献][1]马鸣图ꎬ马露露.铝合金在汽车轻量化中的应用及其前瞻技术[J].新材料产业ꎬ2008(9):43-50.[2]范子杰ꎬ桂良进ꎬ苏瑞意.汽车轻量化技术的研究与进展[J].汽车安全与节能学报ꎬ2014ꎬ5(1):1-16.[3]吴松ꎬ王敏ꎬ程轩挺ꎬ等ꎬ铝合金电阻点焊研究现状及工业应用[J].电焊机ꎬ2013ꎬ43(9):10 ̄16.[4]SkovronJꎬMearsLꎬUlutanDꎬetal.CharacterizationofFlowDrillScrewdrivingProcessParametersonJointQuality[J].SAEInt.J.Mater.Manfꎬ10.4271/2014-01-2241.[5]SFMillerꎬAJShihꎬPJBlau.Microstructuralalterationsassociatedwithfrictiondrillingofsteelꎬaluminumꎬandtita ̄nium[J].Mater.Eng.Performꎬ2005ꎬ14(5):647-653.[6]JohanKolstøSønstabøꎬPetterHenrikHolmstrømꎬMacro ̄scopicstrengthandFailurepropertiesofFlow ̄DrillScrewConnections[J].JournalofMaterialsProcessingTechnologyꎬ2015(8):1-12[7]JEGOULDꎬJoiningAluminumSheetintheAutomotiveIn ̄dustry-A30YearHistory[J].WeldingResearchꎬ2012(1):23-34.[8]雷宇航.热熔钻原理及其在机械加工中的应用[J].内江科技ꎬ2011(6):91 ̄92.[9]王孟君ꎬ黄电源ꎬ姜海涛.汽车用铝合金的进展[J].金属热处理ꎬ2006ꎬ31(9):34-38.(编辑㊀李秀敏)641 组合机床与自动化加工技术㊀第1期。
铝车身连接工艺介绍、铝连接技术介绍
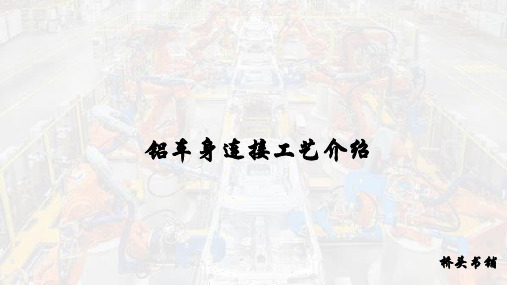
30
4. Clinch/TOX连接特点:
优点:
1、可不同板材连接 2、无耗材 3、对产品连接表面没有特殊要求 4、不会损伤产品表面镀层 5、几乎无噪音、无火花碎屑等污染;
缺点:
1、设备成本较高 2、TOX连接强度较弱,车身上主要应用 在门盖内外板连接,以及压铆部分螺母 3、空间需求较大 4、凹凸面明显
(3)、铝热硅处合理金可强化此的合铝金合加金入了硅,所以抗磨损性佳。含有铜、锰或镍,耐热性能高。 铸(造40铝0合0系金列) 常用于锻造活塞或者高温零件。
适于熔融状态下充填铸型获得一定形状和尺寸铸件毛坯的铝合金。
铸造铝铝镁合合金金分为:非热处理铝合金中,强度最高,焊接性、耐腐蚀性都最好。
((1)、50铝00硅系系列合)金 常用于海事船舶、建材、汽车、飞机等焊接件。
抽芯铆钉
铝车身的连接方法— (2)流钻工艺FDS
19
铝车身的连接方法— (2)流钻工艺FDS
20
1.FDS工艺形式:
热熔自攻丝FDS 过程示意
FDS剖切图
(无预转孔连接)
“流钻螺钉”工艺,(别称:热熔自攻丝/热熔紧固系统), 英文有两种翻译:Flow drill screws(FDS) Flow Form screws(FFS)
铝车身的连接方法— (3)Clinch/TOX连接
31
5. Clinch/TOX连接常见缺陷及返修方法:
常见缺陷:
没有互锁 值
连接偏心
颈部裂纹
凹模侧连接断 裂
连接点开
返修方法: 裂
连接不充 分
凸模侧凹 陷
凸模侧凸 起
1、二次冲压: 在不合格点附近增加一个连接点。
2、去除连接点,使用连接件: 通过冲孔、钻孔方式去除不合格点,使用抽芯拉铆连接。(只有在不影响外观和功能条件下使用)
铝车身连接工艺方法大全
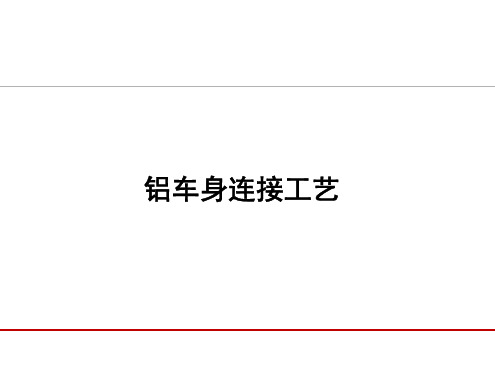
D
铝点焊焊接形式及焊接原理与普通钢板点焊相同只是焊接设 备控制功能不同
D
2、普通铝点焊焊接设备
普通铝点焊对钣件焊接边宽度要求更宽D=20~25mm(普通钢板14~16),其它 焊钳通过空间同普通钢板点焊
4、普通铝点焊焊接特点及优点
1、结合铝特性,普通铝点焊焊接铝板厚度有限(小于2mm),普通铝点焊只 适合焊接门盖(如:克莱斯勒RS前盖,福特F150前盖)等铝薄板焊接;且容易产生 焊接质量问题;
结合铝本身焊接特性,要求铝焊接设备主要输出参数具备如下特征: 1、焊接电流: 30KA~50KA(普通点焊8KA~15KA) 2、焊接压力:500~700公斤力(普通点焊: 200~450 ) 3、焊接时间:5~10周波(普通点焊8~25) 控制更迅速、精确 4、电极头及时清理防止 氧化物粘连,电极水冷速度是普通点焊的2倍 以上要求对焊接控制器要求极高,目前国内只有进口美国梅达铝点焊 焊接控制器
钢板
铝型材 铝型材 铝冲压件 CT6前保:铝型材拉弯成形 CT6侧边梁:铝型材
整体铸铝件
特斯拉铝下车身
铝车身连接工艺— 车身结构
铝车身连接工艺— 焊装工序及工艺方法
1、铝车身结构 结合现有几款铝车身:
1)前后4个减震器座 均采用整体铸铝加工件, 2)前后纵梁采用普通铝型材(捷豹XFL后纵梁采用热成型高强钢板) 3)电动车地板结构简单(横平竖直) 侧边梁,横梁 直接采用铝型材 4)发苍部分横梁 采用铝型材 拉弯 ,结构复杂的 采用铸铝加工件 5)上车身因造型复杂 大部分 采用 铝冲压件 6)B柱加强板 采用高强钢板 或热成型高强钢板
2 3 4 5 6 7
流钻工艺FDS 冷金属过渡焊 接CMT 普通铝点焊 DeltaSpot电 阻焊 Clinch连接 /TOX连接 铝板连接黏合 剂
FDS 工艺介绍

设备易损件寿命
Screw Driver拧紧头约 1万次
Collet Jaw 夹紧头约 1万次
Sleeve铜衬套约 1万次
FDS Matrix—设备
设备采购
价格: 约80万/System (FDS GUN + AUTO Feeder + Controller)
采购周期: 18周 (含运输)
FDS Matrix—标准
缺点:FDS工艺的局限性
1. 连接点处需要高的刚性支撑 2. Cycle Time时间长,约为5-8秒 3. 铆钉成本的piece cost 0.15Euro/Rivet
4. 设备系统成本远高于电阻点焊 800K人民币/system 5. 工艺完成后铆钉正反面均有较大凸起保留 6. 正面铆接方向需要留出大的进枪空间 7. 铆钉选用、工艺参数跟铆接材料、铆接姿态相关性强
工艺要求MR材料、厚度匹配要求
1. 接头不能含脆性材料(如玻璃、脆性塑料) 2. 底层材料(die侧)通常是1.5mm-3.5mm的铝型材或者 3mm左右的铸铝件 3. 上层板材可以7mm的prehole引导孔或者没有引导孔 4. 没有引导孔时,不同材质铆接原则: 软材质铆向硬材质 薄材质铆向厚材质
工艺要求铆钉选择要求
工艺要求MR接头设计要求
工艺参数
工艺参数
n: 转速
F: 压紧力
M: 扭矩
设备系统组成
4.
2.
设备FDS两种标准枪
Standard Length
Reduced Length
设备FDS枪组成结构
设备送钉方式
设备应用方式
Robotic System Prefer
质量标准 推荐标准
在线依靠自动监控系统100%反馈质量,外观检查,扭矩检查 破检,拉伸试验
全铝及钢-铝混合车身轻量化连接技术
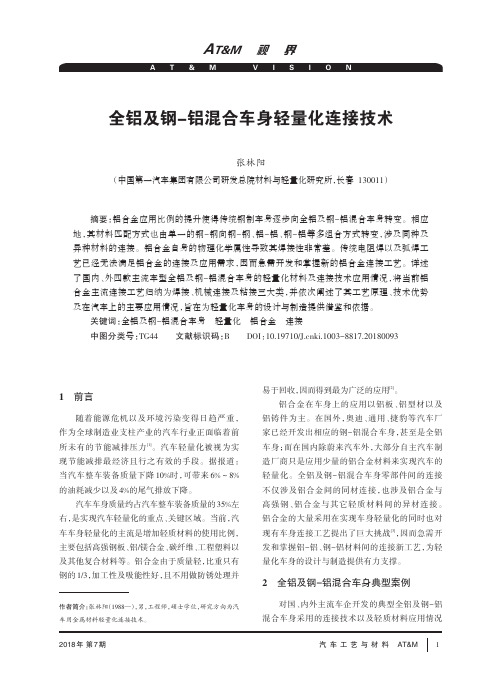
摘要:铝合金应用比例的提升使得传统钢制车身逐步向全铝及钢-铝混合车身转变。
相应地,其材料匹配方式也由单一的钢-钢向钢-钢、铝-铝、钢-铝等多组合方式转变,涉及同种及异种材料的连接。
铝合金自身的物理化学属性导致其焊接性非常差。
传统电阻焊以及弧焊工艺已经无法满足铝合金的连接及应用需求,因而急需开发和掌握新的铝合金连接工艺。
详述了国内、外四款主流车型全铝及钢-铝混合车身的轻量化材料及连接技术应用情况,将当前铝合金主流连接工艺归纳为焊接、机械连接及粘接三大类,并依次阐述了其工艺原理、技术优势及在汽车上的主要应用情况,旨在为轻量化车身的设计与制造提供借鉴和依据。
关键词:全铝及钢-铝混合车身轻量化铝合金连接中图分类号:TG44文献标识码:BDOI :10.19710/ki.1003-8817.20180093全铝及钢-铝混合车身轻量化连接技术张林阳(中国第一汽车集团有限公司研发总院材料与轻量化研究所,长春130011)作者简介:张林阳(1988—),男,工程师,硕士学位,研究方向为汽车用金属材料轻量化连接技术。
1前言随着能源危机以及环境污染变得日趋严重,作为全球制造业支柱产业的汽车行业正面临着前所未有的节能减排压力[1]。
汽车轻量化被视为实现节能减排最经济且行之有效的手段。
据报道:当汽车整车装备质量下降10%时,可带来6%~8%的油耗减少以及4%的尾气排放下降。
汽车车身质量约占汽车整车装备质量的35%左右,是实现汽车轻量化的重点、关键区域。
当前,汽车车身轻量化的主流是增加轻质材料的使用比例,主要包括高强钢板、铝/镁合金、碳纤维、工程塑料以及其他复合材料等。
铝合金由于质量轻,比重只有钢的1/3,加工性及吸能性好,且不用做防锈处理并易于回收,因而得到最为广泛的应用[2]。
铝合金在车身上的应用以铝板、铝型材以及铝铸件为主。
在国外,奥迪、通用、捷豹等汽车厂家已经开发出相应的钢-铝混合车身,甚至是全铝车身;而在国内除蔚来汽车外,大部分自主汽车制造厂商只是应用少量的铝合金材料来实现汽车的轻量化。
FDS热融自攻丝铆接系统

热融自攻丝FDS铆接系统Stoger 7501 FSF系统外观图热融自攻丝FDS铆接系统(Flow drill screw, FDS)发明于1990年,1996年首次应用于莲花轿车车身框架的连接。
由于采用手持夹具进行装夹,整个装配过程的时间和精度不好控制,使得该工艺使用受到限制。
20世纪90年代末,Weber Schraubautomaten为EJOT公司开发了RSF20S螺钉驱动系统,RSF20S的问世实现了FDS工艺的自动化生产,并增大了可连接板材的厚度,于2000年首次用于Audi A4后轮罩连接。
在过去五年中,许多欧洲汽车厂商开始使用FDS技术,如捷豹XK和X150,奥迪R8, A8, TT Coupe,A6等,其中新奥迪A8上有多达740个流钻螺钉。
欧洲的尼桑、路虎、保时捷、宝马等众多汽车品牌也都引入了流钻螺钉连接工艺。
目前全球已经有德国、意大利、英国、丹麦、匈牙利、波兰六个国家在汽车中使用了该技术。
如图所示,FDS工艺通过螺钉的高速旋转软化待连接板材,并在巨大的轴向压力作用下挤压并旋入待连接板材,最终在板材与螺钉之间形成螺纹连接,而中心孔处的母材则被挤出并在下层板的底部形成一个环状套管。
其优点是:①因为螺钉不需要变形,因此可以用来连接包括超高强钢、铝镁合金、复合材料在内的任何材料及异种材料;②螺钉高速旋转可以软化金属,因此可在较小变形的情况下实现单边连接,使得连接更加方便;③铆钉可以拆卸,回收方便。
但是该方法也有其明显的缺点:①因为下层板要钻穿,因此接头的防腐蚀能力会降低;②工艺结束后螺钉前端必须露出于挤出套管之外,加上尖头的过渡部分,使得螺钉尺寸较长,如果大量使用会增加车身自重,同时过长的露出部分也会对车身的设计与制造产生影响。
除WEBER外,又一世界重量级装配连接系统专家-STOGER推出重量级FDS产品7501 FSF 系统:德国STOGER热融自攻丝铆接系统铆头FSF系统的控制单元各种各样的热融自攻丝紧固件。
热熔工艺-课题资料 - 百度

四、热熔常见缺陷以及对策。
缺陷 原因 高温 热保压时间过长 拉丝 感温线松动、脱落、温度检测失真 感温线接错、反接 对策 降温、检修电路 减少热保压时间 检修电路 检修电路
工艺部-HKY1015895809@
五、热熔设备。
1、热熔机
挂载热熔模具设备,主要有温控系统、液压传动系 统。温控系统目前最多支持80路同时加热;液压传动系 统未完全伺服化,最新机台速度、压力均是百分比表示。
A面要求
壁厚≥3倍热铆底座壁厚 铆接翻边直径 BOSS柱外直径 BOSS柱壁厚 BOSS柱有效热铆 高度 大于等于1.3倍安装孔直径 6mm 1mm 10mm 防止A面顶白 保证强度
工艺部-HKY1015895809@
三、厂内热熔产品。
1、厂内常见结构-空心翻边铆接式
搭接件
铆柱外径大过4mm时,采用空心铆柱外翻边结构,可获得紧固连接同时不需要熔化过多材料缩短周期。而且 便于压机压力卸向铆柱两侧,保护产品A面,避免顶白。
工艺部-HKY1015895809@
三、厂内热熔产品。
小型热熔柱铆接效果
工艺部-HKY1015895809@
三、厂内热熔产品。
大型热熔柱铆接效果
大型热熔柱铆接效果
工艺部-HKY1015895809@
狗洞底部最小截面面积 越大,承载力越好,越 不容易被压塌。
工艺部-HKY1015895809@
• 焊接:锁紧状态较热铆稳定很多,结构限制较少,但设备投入较大, 高端车型才适用。
工艺部-HKY1015895809@
一、热熔定义。
• 利用预留在塑料件上固有的塑料铆柱(boss柱)、筋条,在穿过 的钣金件、塑料件背面上热压锁紧。铆柱(boss柱)、筋条在温 度受控特质的金属铆接头挤压下,重新成型夹紧。 • 通过热量将部分塑料件结构软化、挤压变形、重塑后与其他零件 搭接在一起的工艺。 厂内热熔棒 • 热铆接比较准确
热融自攻丝技术-一种新型的连接技术
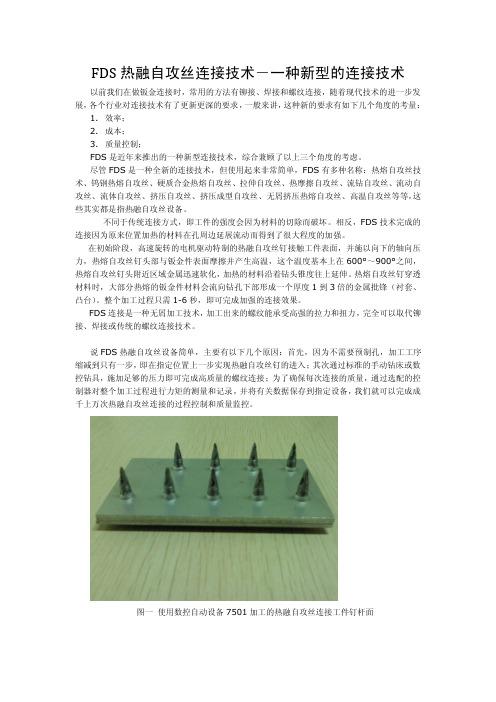
FDS热融自攻丝连接技术-一种新型的连接技术以前我们在做钣金连接时,常用的方法有铆接、焊接和螺纹连接,随着现代技术的进一步发展,各个行业对连接技术有了更新更深的要求,一般来讲,这种新的要求有如下几个角度的考量:1.效率;2.成本;3.质量控制;FDS是近年来推出的一种新型连接技术,综合兼顾了以上三个角度的考虑。
尽管FDS是一种全新的连接技术,但使用起来非常简单,FDS有多种名称:热熔自攻丝技术、钨钢热熔自攻丝、硬质合金热熔自攻丝、拉伸自攻丝、热摩擦自攻丝、流钻自攻丝、流动自攻丝、流体自攻丝、挤压自攻丝、挤压成型自攻丝、无屑挤压热熔自攻丝、高温自攻丝等等,这些其实都是指热融自攻丝设备。
不同于传统连接方式,即工件的强度会因为材料的切除而破坏。
相反,FDS技术完成的连接因为原来位置加热的材料在孔周边延展流动而得到了很大程度的加强。
在初始阶段,高速旋转的电机驱动特制的热融自攻丝钉接触工件表面,并施以向下的轴向压力,热熔自攻丝钉头部与钣金件表面摩擦并产生高温,这个温度基本上在600°~900°之间,热熔自攻丝钉头附近区域金属迅速软化,加热的材料沿着钻头锥度往上延伸。
热熔自攻丝钉穿透材料时,大部分热熔的钣金件材料会流向钻孔下部形成一个厚度1到3倍的金属批锋(衬套、凸台)。
整个加工过程只需1-6秒,即可完成加强的连接效果。
FDS连接是一种无屑加工技术,加工出来的螺纹能承受高强的拉力和扭力,完全可以取代铆接、焊接或传统的螺纹连接技术。
说FDS热融自攻丝设备简单,主要有以下几个原因:首先,因为不需要预制孔,加工工序缩减到只有一步,即在指定位置上一步实现热融自攻丝钉的进入;其次通过标准的手动钻床或数控钻具,施加足够的压力即可完成高质量的螺纹连接;为了确保每次连接的质量,通过选配的控制器对整个加工过程进行力矩的测量和记录,并将有关数据保存到指定设备,我们就可以完成成千上万次热融自攻丝连接的过程控制和质量监控。
FDS技术在钢铝混合车身上的应用
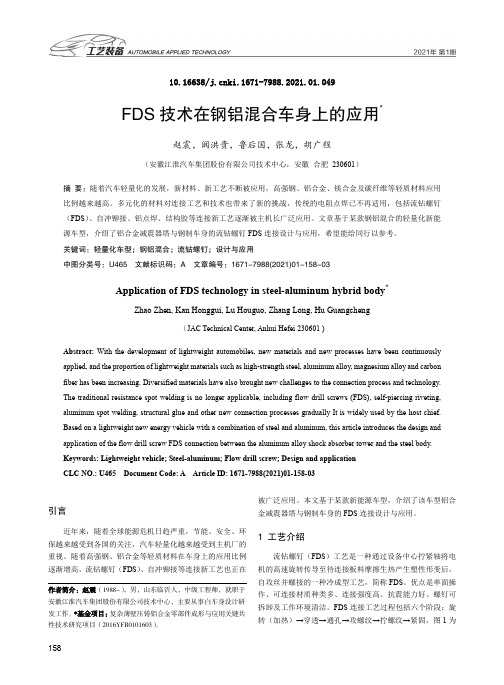
10.16638/ki.1671-7988.2021.01.049FDS技术在钢铝混合车身上的应用*赵震,阚洪贵,鲁后国,张龙,胡广程(安徽江淮汽车集团股份有限公司技术中心,安徽合肥230601)摘要:随着汽车轻量化的发展,新材料、新工艺不断被应用,高强钢、铝合金、镁合金及碳纤维等轻质材料应用比例越来越高。
多元化的材料对连接工艺和技术也带来了新的挑战,传统的电阻点焊已不再适用,包括流钻螺钉(FDS)、自冲铆接、铝点焊、结构胶等连接新工艺逐渐被主机长广泛应用。
文章基于某款钢铝混合的轻量化新能源车型,介绍了铝合金减震器塔与钢制车身的流钻螺钉FDS连接设计与应用,希望能给同行以参考。
关键词:轻量化车型;钢铝混合;流钻螺钉;设计与应用中图分类号:U465 文献标识码:A 文章编号:1671-7988(2021)01-158-03Application of FDS technology in steel-aluminum hybrid body*Zhao Zhen, Kan Honggui, Lu Houguo, Zhang Long, Hu Guangcheng(JAC Technical Center, Anhui Hefei 230601 )Abstract:With the development of lightweight automobiles, new materials and new processes have been continuously applied, and the proportion of lightweight materials such as high-strength steel, aluminum alloy, magnesium alloy and carbon fiber has been increasing. Diversified materials have also brought new challenges to the connection process and technology. The traditional resistance spot welding is no longer applicable, including flow drill screws (FDS), self-piercing riveting, aluminum spot welding, structural glue and other new connection processes gradually It is widely used by the host chief. Based on a lightweight new energy vehicle with a combination of steel and aluminum, this article introduces the design and application of the flow drill screw FDS connection between the aluminum alloy shock absorber tower and the steel body. Keywords: Lightweight vehicle; Steel-aluminum; Flow drill screw; Design and applicationCLC NO.: U465 Document Code: A Article ID: 1671-7988(2021)01-158-03引言近年来,随着全球能源危机日趋严重,节能、安全、环保越来越受到各国的关注,汽车轻量化越来越受到主机厂的重视。
热融自攻丝连接技术 从一颗FDS螺钉谈起
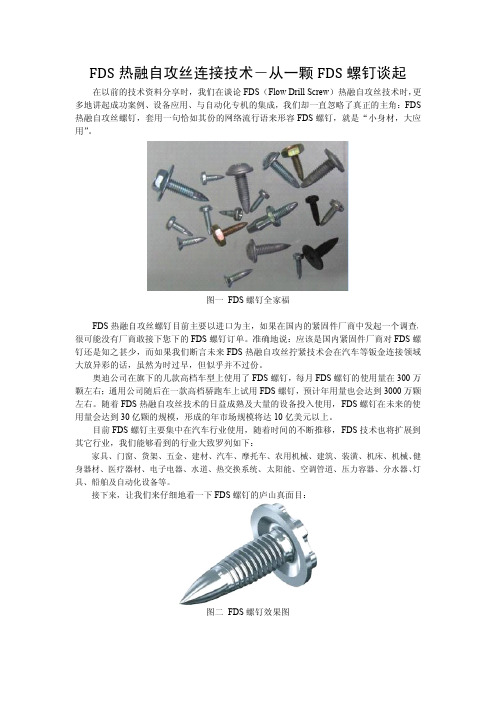
FDS热融自攻丝连接技术-从一颗FDS螺钉谈起在以前的技术资料分享时,我们在谈论FDS(Flow Drill Screw)热融自攻丝技术时,更多地讲起成功案例、设备应用、与自动化专机的集成,我们却一直忽略了真正的主角:FDS 热融自攻丝螺钉,套用一句恰如其份的网络流行语来形容FDS螺钉,就是“小身材,大应用”。
图一FDS螺钉全家福FDS热融自攻丝螺钉目前主要以进口为主,如果在国内的紧固件厂商中发起一个调查,很可能没有厂商敢接下您下的FDS螺钉订单。
准确地说:应该是国内紧固件厂商对FDS螺钉还是知之甚少,而如果我们断言未来FDS热融自攻丝拧紧技术会在汽车等钣金连接领域大放异彩的话,虽然为时过早,但似乎并不过份。
奥迪公司在旗下的几款高档车型上使用了FDS螺钉,每月FDS螺钉的使用量在300万颗左右;通用公司随后在一款高档骄跑车上试用FDS螺钉,预计年用量也会达到3000万颗左右。
随着FDS热融自攻丝技术的日益成熟及大量的设备投入使用,FDS螺钉在未来的使用量会达到30亿颗的规模,形成的年市场规模将达10亿美元以上。
目前FDS螺钉主要集中在汽车行业使用,随着时间的不断推移,FDS技术也将扩展到其它行业,我们能够看到的行业大致罗列如下:家具、门窗、货架、五金、建材、汽车、摩托车、农用机械、建筑、装潢、机床、机械、健身器材、医疗器材、电子电器、水道、热交换系统、太阳能、空调管道、压力容器、分水器、灯具、船舶及自动化设备等。
接下来,让我们来仔细地看一下FDS螺钉的庐山真面目:图二FDS螺钉效果图熟悉网络的朋友看到上面的图片一定会知道,这是一张做过“美容手术”的图片,或者说是“PS”过的,那么下面列出的图片一定会让你一睹FDS螺钉的“写真照片”。
图二实际使用于一款GM汽车白车身的FDS螺钉FDS螺钉与其它螺纹紧固件,特别是各类自攻丝螺钉的区别主要在以下三点:1.特别厚实的帽沿;2.钉帽与钉杆连接处的凹槽;3.特别的材质;下面我们分别来讲讲这三个特点背后的深层原因。
某纯电动汽车电池包系统振动疲劳仿真分析研究

10.16638/ki.1671-7988.2020.15.007某纯电动汽车电池包系统振动疲劳仿真分析研究周丽杰(爱驰汽车(上海)有限公司,上海200090)摘要:为了迎合市场对续驶里程提高的要求,续驶里程超过400公里已成为国内纯电动汽车市场的主流,受电池材料和能量密度极限的影响,电池包重量也会相应超过350kg,电池包振动疲劳的挑战全方位倍增,对电池包系统箱体结构性能要求越来越高,建立适用的电池包系统振动疲劳仿真分析的企业标准,为整车开发性能考核提供依据,降低开发风险和费用。
关键词:纯电动汽车;电池包;振动疲劳;企业标准中图分类号:U469.72 文献标识码:A 文章编号:1671-7988(2020)15-19-04The Light Weigh and Optimization Analysis of the Front Sub-frame of a VehicleZhou Lijie(AIWAYS Automobile (Shanghai) Co., Ltd, Shanghai 200090)Abstract:In order to meet the requirement of the market for increasing driving mileage, driving mileage over 400 kilometers has become the mainstream of the domestic pure electric vehicle market. Due to the influence of battery materials and energy density limit, the weight of battery pack will correspondingly exceed 350 kilograms. The challenge of vibration fatigue of battery pack will be multiplied in all directions. The structural performance of battery pack system is increasingly demanded, and suitable battery pack system will be established. The enterprise standard of vibration fatigue simulation analysis provides a basis for vehicle development performance evaluation and reduces development risk and cost.Keywords: Battery electric vehicle1; Pack; Vibration fatigue; Enterprise StandardCLC NO.: U469.72 Document Code: A Article ID: 1671-7988(2020)15-19-04引言纯电动汽车市场的快速增长,离不开国家政策的支持、消费者消费观念的转变以及车企技术的提升。
热融自攻丝连接技术 从一颗FDS螺钉谈起
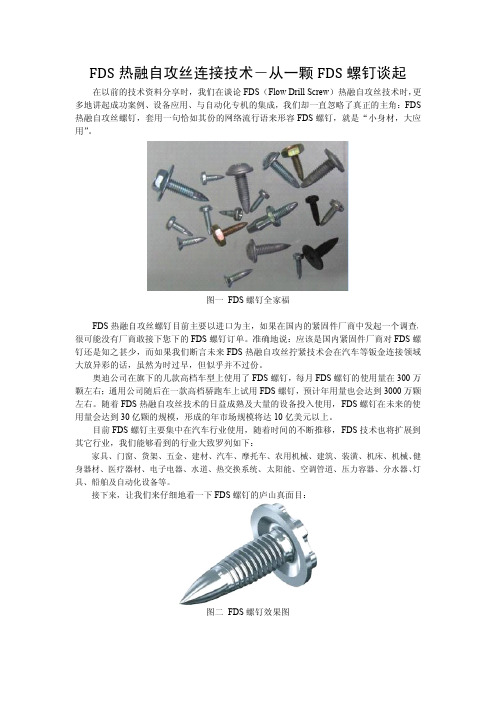
FDS热融自攻丝连接技术-从一颗FDS螺钉谈起在以前的技术资料分享时,我们在谈论FDS(Flow Drill Screw)热融自攻丝技术时,更多地讲起成功案例、设备应用、与自动化专机的集成,我们却一直忽略了真正的主角:FDS 热融自攻丝螺钉,套用一句恰如其份的网络流行语来形容FDS螺钉,就是“小身材,大应用”。
图一FDS螺钉全家福FDS热融自攻丝螺钉目前主要以进口为主,如果在国内的紧固件厂商中发起一个调查,很可能没有厂商敢接下您下的FDS螺钉订单。
准确地说:应该是国内紧固件厂商对FDS螺钉还是知之甚少,而如果我们断言未来FDS热融自攻丝拧紧技术会在汽车等钣金连接领域大放异彩的话,虽然为时过早,但似乎并不过份。
奥迪公司在旗下的几款高档车型上使用了FDS螺钉,每月FDS螺钉的使用量在300万颗左右;通用公司随后在一款高档骄跑车上试用FDS螺钉,预计年用量也会达到3000万颗左右。
随着FDS热融自攻丝技术的日益成熟及大量的设备投入使用,FDS螺钉在未来的使用量会达到30亿颗的规模,形成的年市场规模将达10亿美元以上。
目前FDS螺钉主要集中在汽车行业使用,随着时间的不断推移,FDS技术也将扩展到其它行业,我们能够看到的行业大致罗列如下:家具、门窗、货架、五金、建材、汽车、摩托车、农用机械、建筑、装潢、机床、机械、健身器材、医疗器材、电子电器、水道、热交换系统、太阳能、空调管道、压力容器、分水器、灯具、船舶及自动化设备等。
接下来,让我们来仔细地看一下FDS螺钉的庐山真面目:图二FDS螺钉效果图熟悉网络的朋友看到上面的图片一定会知道,这是一张做过“美容手术”的图片,或者说是“PS”过的,那么下面列出的图片一定会让你一睹FDS螺钉的“写真照片”。
图二实际使用于一款GM汽车白车身的FDS螺钉FDS螺钉与其它螺纹紧固件,特别是各类自攻丝螺钉的区别主要在以下三点:1.特别厚实的帽沿;2.钉帽与钉杆连接处的凹槽;3.特别的材质;下面我们分别来讲讲这三个特点背后的深层原因。
热熔自攻丝铆接特征参数对钢铝连接铆点质量影响

摘要:热熔自攻丝铆接因其在钢铝连接上的优势,而被广泛应用在白车身连接领域中。
以通用标准GMW3032系列钢板和铝合金6061-T6为主要研究对象,参照目前主机厂的铆接工艺标准,研究了热熔自攻丝铆接中钻孔下压力、钻孔刀头最大转速、锁紧扭矩3个主要特征参数在铆接过程中的变化,讨论了不同搭接匹配下特征参数设置对钢铝连接铆点质量的影响,可对实际车身连接工艺优化提供有益借鉴。
关键词:热熔自攻丝铆接钢铝连接白车身连接中图分类号:TG938文献标识码:B热熔自攻丝铆接特征参数对钢铝连接铆点质量影响王有道1叶雪洋2刘岩1刘羽1凌宝1(1.大连奥托股份有限公司技术中心,大连116050;2.上海巍博自动化设备有限公司,上海20020)作者简介:王有道(1985年—),男,工程师,硕士学位,研究方向为白车身连接工艺、汽车轻量化。
基金项目:国家外专局引智项目:锁铆技术在轿车白车身生产线上的应用(编号SN20162102018)。
1前言在新能源汽车发展以及白车身轻量化过程中,铝合金被越来越广泛的使用[1]。
在钢铝连接方面,传统点焊实施较为困难。
半空心自冲铆接(Self-Piercing Riveting ,SPR)和热熔自攻丝铆接(Flow Drill Screwdriving ,FDS)凭借其在钢/铝连接方面的优势,逐渐在全球各大主机厂奥迪、奔驰等普及应用[2,3]。
国外学者对两种铆接的工艺特性[4,5]以及其工艺过程模拟[6,7]进行广泛地研究;国内学者对与半空心自冲铆的研究较为充分[8,9],而对于热熔自攻丝铆接的研究较少。
热熔自攻丝铆接是一种适合于连接多层板、异质板的单侧成型铆接方式,其过程分为预热定位、钻孔、扩孔、攻丝、拧丝、锁死六步(图1)。
预热过程中,铆钉转速范围会达到1500~8000r/min ,材料表面温度能够达到150~250℃。
随后设备施加压力,通常最大可达3.5kN ,瞬间完成钻孔和扩孔。
最后由铆钉自带的攻丝螺纹完成攻丝过程并按预设的锁紧扭矩将铆钉锁死在板材上。