基于道路谱的汽车车身疲劳分析
浅谈重型卡车载荷谱采集与疲劳分析
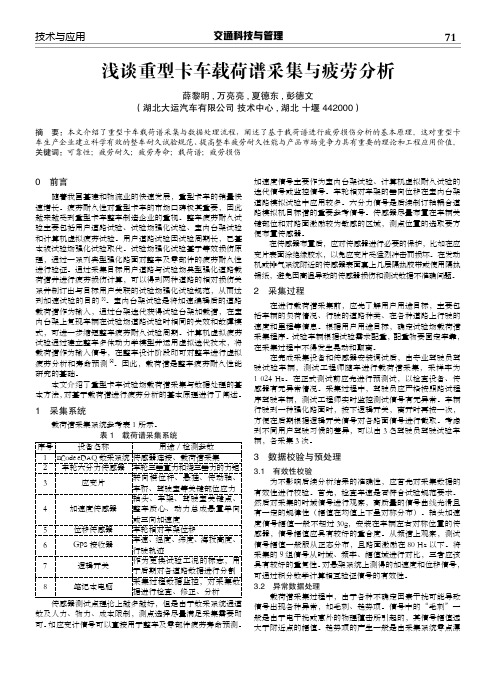
交通科技与管理71技术与应用0 前言 随着我国基建和物流业的快速发展,重型卡车的销量快速增长。
疲劳耐久性对重型卡车的市场口碑极其重要,因此越来越受到重型卡车整车制造企业的重视。
整车疲劳耐久试验主要包括用户道路试验、试验场强化试验、室内台架试验和计算机虚拟疲劳试验。
用户道路试验因试验周期长,已基本被试验场强化试验取代。
试验场强化试验基于等效损伤原理,通过一系列典型强化路面对整车及零部件的疲劳耐久性进行验证。
通过采集目标用户道路与试验场典型强化道路载荷谱并进行疲劳损伤计算,可以得到两种道路的相对损伤关系并制订出与目标用户关联的试验场强化试验规范,从而达到加速试验的目的[1]。
室内台架试验是将加速编辑后的道路载荷谱作为输入,通过台架迭代获得试验台架加载谱,在室内台架上复现车辆在试验场道路试验时相同的失效和故障模式,可进一步缩短整车疲劳耐久试验周期。
计算机虚拟疲劳试验通过建立整车多体动力学模型并运用虚拟迭代技术,将载荷谱作为输入信号,在整车设计阶段即可对整车进行虚拟疲劳分析和寿命预测[2]。
因此,载荷谱是整车疲劳耐久性能研究的基础。
本文介绍了重型卡车试验场载荷谱采集与数据处理的基本方法,对基于载荷谱进行疲劳分析的基本原理进行了阐述。
1 采集系统 载荷谱采集系统参考表1所示。
表1 载荷谱采集系统序号设备名称用途/检测参数1nCode eDAQ 数采系统传感器连接、载荷谱采集2车轮六分力传感器车轮三垂直力和绕三垂力的力矩3应变片转向横位杆、悬挂、传动轴、车桥、驾驶室等关键部位应力4加速度传感器轴头、车架、驾驶室关键点、整车质心、动力总成悬置单向或三向加速度5位移传感器车轮相对车架位移6GPS 接收器车速、经度、纬度、海拔高度、行驶轨迹7逻辑开关作为更换试验工况的标志,用于后期对各道路数据进行分割8笔记本电脑采集过程数据监控,对采集数据进行检查、修正、分析 传感器测试点理论上越多越好,但是由于数采系统通道数及人力、物力、成本限制,测点选择尽量满足采集需要即可。
路谱采集与疲劳分析在当今汽车研发中的应用

路谱采集与疲劳分析在当今汽车研发中的应用随着汽车的不断普及,人们对汽车的安全性、舒适度等方面的要求也越来越高。
这就要求汽车制造商和相关研发机构在汽车设计和制造中,充分考虑驾驶员的体验和安全性。
在这一过程中,路谱采集和疲劳分析技术正逐渐成为研发中的必需品。
路谱采集是指收集不同道路场景下的驾驶行为数据,通过模拟和测试将这些数据整理成“路谱”,以便更好地研究车辆的行驶特性和进行驾驶员疲劳分析。
根据收集的数据,可以分析驾驶员在行驶过程中所遭受到的振动、加速度等信息,以便进行舒适性和安全性的优化。
在实际应用中,路谱采集可通过车载精密仪器和软件完成,同时也可以结合现场扫描和摄像等技术手段获取更全面和准确的数据。
收集的数据可通过数据分析和处理工具进行综合分析和评估,将分析结果反馈给车辆的制造商和设计师,以便更好地制定优化措施。
疲劳分析是指在长时间驾驶行驶过程中分析驾驶员的身体反应、血液流量、血氧含量、心率等指标,判断驾驶员是否出现疲劳或疾病,从而降低发生交通事故的概率。
现在,一些汽车制造商已经开始将各种传感器和测量设备集成到车内,以便实时监测驾驶员的健康状况。
同时,在疲劳分析中,还可以通过路谱采集所得到的数据进行更全面的分析和研究,识别并纠正行驶过程中所产生的不适,改善驾驶员舒适性和安全性。
这种技术的应用不仅可以帮助降低事故率,减少交通事故带来的人员伤亡和财产损失,还能提升车辆的竞争力,增加其市场需求。
需要注意的是,尽管路谱采集和疲劳分析技术在汽车制造和研发中具有广泛应用前景,但这些技术需要对数据进行隐私保护和安全性控制。
保障驾驶员的隐私和数据安全,是研发者和制造商应该考虑的一项重要问题。
总而言之,路谱采集和疲劳分析技术在当今汽车研发中的应用,可以帮助提升车辆的舒适性和安全性,优化驾驶体验、降低交通事故的发生率、提升车辆市场竞争力,具有很大的前景和潜力。
在未来的汽车发展中,这些技术肯定会发挥越来越重要的作用,成为汽车行业的重要发展方向。
基于路谱频域的车身疲劳分析

基于路谱频域的车身疲劳分析吴涛;茆汉湖;戴轶【摘要】针对车身疲劳分析中静载法无法考虑结构动力学响应,瞬态分析法无法求解过长时间域的问题,将这2种方法与频域法进行比较,发现用频域法对大规模有限元模型进行动态疲劳分析相对容易,并能完全描述动力学响应过程.根据频域法进行振动疲劳分析的理论和计算过程,给出基于路谱频域的车身疲劳分析流程.基于功率谱密度(Power Spectral Density,PSD)载荷谱的传递函数法求解某车关键部件的疲劳寿命,求解结果与疲劳试验结果比较一致.结果表明基于路谱频域的振动疲劳分析方法在汽车结构疲劳计算中的应用可行.【期刊名称】《计算机辅助工程》【年(卷),期】2012(021)002【总页数】4页(P50-52,83)【关键词】整备车身;振动疲劳;功率谱密度;路谱;频域【作者】吴涛;茆汉湖;戴轶【作者单位】上海汽车集团股份有限公司技术中心,上海201804;上海汽车集团股份有限公司技术中心,上海201804;上海汽车集团股份有限公司技术中心,上海201804【正文语种】中文【中图分类】U463.821;TB115.10 引言汽车市场竞争日趋激烈,各厂家越来越重视汽车的疲劳寿命问题,随着科学技术的进步,汽车设计部门可以在设计阶段就考虑产品的疲劳寿命问题,摆脱以往只能在产品验证阶段通过试验对产品寿命进行评估的单一手段.有限元法在设计中的应用极大地提高设计手段:最初,设计师通过模拟汽车在最差路面上的一些极限工况(如Potholes,3g Bumper和Kerbing等)进行静力学的极限强度计算,观察车辆在这些极限工况条件下是否断裂,从而评估结构的疲劳情况;后来,通过有限元法得到车辆结构的全场应力和应变历史来计算全场疲劳情况的方法逐渐成为主流.1 时域法和频域法金属材料由于受交变应力和应变的作用而发生疲劳失效,计算疲劳的理论基础,无论是名义应力寿命法,还是局部应变寿命法,都需要计算结构各部分受到的应力和应变历史.采用有限元法计算应力和应变历史的方法有准静态法和瞬态法,这2种方法都可用于求解结构在时域的应力和应变场,但也都有各自适用的范围.当激励载荷频率远小于所分析结构的自然频率时,结构不具有动力学响应,其应力状态可通过线性缩放,多通道地通过线性叠加的方法进行准静态法求解.反之,如果施加的载荷频率接近结构的固有频率,结构具有动力学响应,同时各载荷作用相互耦合,更宜选择瞬态法求解.对于具有几十万单元白车身级别的疲劳分析,即使只对线性系统进行几十秒的瞬态分析也很难完成,工程中常采用准静态法线性缩放结构的应力和应变场.对于一般的疲劳试验路面,波长和车速已知,来自路面的载荷频率通常小于6 Hz,远小于白车身的固有频率,因此准静态法适用.当疲劳路面为激励共振路面(如鹅卵石和搓板路面)时,路面波长短,在车辆达到一定速度时加载频率显著提高,有必要考虑其动力学响应.此时,使用频域法具有优势,频率响应(传递函数)分析获取功率谱密度的应力信号通常比获取时域的应力信号容易得多.2 振动疲劳分析理论和计算过程对于振动疲劳分析,输入载荷的频域表述(载荷的功率谱密度(Power Spectral Density,PSD))是时域信号的一种有效表达方式,也可通过一系列转换用频域对固定的随机过程做出统计性描述,这种统计得到每个应力幅值在一定时间范围内发生的概率分布,同样可根据传统疲劳计算方法由Miner累计损伤法则求得疲劳损伤.因此,在频域中进行振动疲劳分析,同样需要材料的S-N曲线.[1]2.1 时域信号向频域信号的转化输入载荷y=y(t)是关于时间的函数,可将其描述成一系列变幅、频率和相位的正弦波总和,即傅里叶展开式.用复数理论表达傅里叶展开式:计算复数因数时将因数规格化,规格化的因数采用不同频率下的密度函数形式进行表达;从Δf(各因数间的频率间隔)范围内密度函数下的区域获得傅里叶因数;通过傅里叶因数并根据一系列转换可得到傅里叶变换y(f),记为FFT.2.2 PSD 的矩PSD下的区域代表正弦曲线波组分(时间历程)的均方值,将其与FFT谱计算的均方值相等,可确定PSD与FFT之间的转换.PSD的矩Mndf表示PSD函数的第n个积率,一些非常重要的统计学特性(如每秒的零交叉点和峰值)可以从PSD的矩中得到,并可由这些特性计算不规则因数.这些特性在时域信号中很容易通过计数得到.这样就建立PSD信号与时域信号在统计学上的联系.2.3 概率密度函数频域中评估疲劳需要得到某种应力幅值的概率分布,根据时域信号和PSD的矩所描述的一些统计学上的共性,可推导出概率分布.[2]相关理论中应用较广泛的有窄带假设和Dirlik求解:窄带假设理论假设所有函数值为正的波峰后跟着一个对应的、数值相等的波谷,不考虑实际中是否构成应力循环,比较保守;Dirlik求解的应用更广泛[3],它也根据PSD的矩表示概率密度函数.3 基于路谱频域求解车身疲劳基于载荷谱的结构疲劳分析方法主要有静载法、瞬态应变分析法和振动疲劳分析法等.对于白车身疲劳分析,最简单和常用的方法是静载法:建立车辆的整备车身模型,在车身与底盘的连接点处分别施加单位载荷,然后应用惯性释放的方法求解多种工况下的应力分布.将每个通道单位载荷的应力分布与相关载荷(时间历程)进行简单的线性组合,获取应力场的时域分布,计算流程见图1中的静载法,静载法无法考虑结构的动力学响应.对于瞬态分析法,在面对白车身这种大模型时,用其求解过长的时间域也不现实,基于PSD载荷谱的振动疲劳频域分析方法是较好的选择,其计算流程见图1中的频域法.基于PSD载荷谱进行振动疲劳分析的方法有传递函数法和随机振动分析法.传递函数法利用模型应力传递函数和PSD表示的输入载荷,通过疲劳分析软件求得模型的振动疲劳特性,即先对有限元模型载荷输入点的各个自由度分别施加单位激励,输出车身钣金件的应力传递函数;传递函数是模型的基本特性,与输入载荷无关;试验所得载荷通常为时域的加速度载荷,可将其转化为用频域PSD表示的动态载荷;将这2个主要参数和材料疲劳特性曲线一起输入到振动疲劳分析模块,即可进行响应的损伤寿命分析.随机振动分析法将动载的PSD作为输入载荷,通过有限元软件进行随机振动分析,直接求得应力PSD[4],然后将应力PSD和材料特性直接输入到振动疲劳分析模块,分析模型的疲劳寿命.图1 静载法和频域法求解疲劳的流程Fig.1 Processes of solving fatigue with static load method and frequency domain method本文针对某整备车身和底盘的有限元模型(见图2),采用基于PSD载荷谱的传递函数法进行疲劳求解.由图2可知,整备车身主要包括带前后玻璃的车身模型,车身上具有附件的质量和惯量信息;附件包括车门、前舱盖、行李箱盖、散热器、车灯、电池、备胎、座椅、转向系统、仪表台和车身非结构质量附件等.模型的建立方法与车身模态计算模型一致.输入点为车轮轮心位置,每个输入点对应整车坐标3个方向的力和力矩,通道数目为24个.输入载荷采用疲劳试验中直接测得的车轮轮心处的六分力.由于目前的疲劳软件仅支持20个通道的耦合分析,简化掉4个通道以满足软件计算要求.在4个轮心处分别施加5个单位的激励(另外一个被简化掉),利用MD Nastran进行传递函数分析,每个传递函数对应一个PSD动态载荷谱.激励输入到振动疲劳分析模块后,结合材料S-N特性进行模型的损伤和寿命分析. 图2 有限元模型Fig.2 Finite element model作用于左后轮轮心x向的动载时域信号和由此转换来的PSD见图3,可知,由PSD分析得到的该通道载荷频率范围为0~30 Hz.通常白车身第1阶模态约为28 Hz,因此采用振动疲劳分析法考虑其动力学响应比采用静载法好.图3 x向载荷时域信号及其PSDFig.3 Time domain signal and its PSD of x direction load由于20个通道的载荷同时作用,应设置20个载荷同时作用的多载荷分析,构建PSD载荷矩阵进行计算.如需考虑每个载荷的相关性,可通过MSC Fatigue中的MFRA考虑各载荷的相关性以构建PSD载荷相关性矩阵.[5-6]受计算机能力限制,输出时可只考虑一些重点关注的零件寿命.一些关键零件的疲劳寿命云图见图4,可知,危险区域多在承重和底盘接附点位置附近,最小寿命为0.85 h,位于后悬架扭转梁左前接附点安装位置.在疲劳耐久试验中,该处在路试15 h后检查已经出现破裂,见图5.图4 一些关键零件的疲劳寿命云图,hFig.4 Fatigue life contour of some key parts,h图5 试验得到的开裂位置Fig.5 Crack position obtained by test4 结束语分别介绍有限元计算疲劳问题的时域法和频域法,简介用频域法计算疲劳的理论和计算过程.通过基于PSD载荷谱的传递函数法分析汽车道路谱振动疲劳寿命,分析结果与实际疲劳试验结果比较一致,证明基于路谱频域进行汽车结构疲劳计算可行. 参考文献:【相关文献】[1]武秀根,郑百林,杨青,等.柴油机曲轴的多柔体动力学仿真与疲劳分析[J].计算机辅助工程,2007,16(2):1-4.WU Xiugen,ZHENG Bailin,YANG Qing,et al.Multi-flexible body dynamics simulation and fatigue analysis on diesel engine crankshaft[J].Comput Aided Eng,2007,16(2):1-4.[2]隋允康.MSC Nastran有限元动力分析与优化设计实用教程[M].北京:科学出版社,2004:18-80.[3]HALFPENNY A.基于功率谱密度信号的疲劳寿命估计[J].中国机械工程,1998,9(11):16-19.HALFPENNY A.A frequency domain approach for fatigue life estimation[J].China Mech Eng,1998,9(11):16-19.[4]林晓斌.一套完整的疲劳分析设计试验管理系统nSoft[J].中国机械工程,1998,9(11):8-11.LIN Xiaobin.An integrated software system for fatigue analysis,design,test and management-nSoft[J].China Mech Eng,1998,9(11):8-11.[5]HEYES P J.基于有限元的疲劳设计分析系统MSC Fatigue[J].中国机械工程,1998,9(11):12-16.HEYES P J.Finite element based fatigue design and analysis system-MSC Fatigue[J].China Mech Eng,1998,9(11):12-16.[6]周传月,郑红霞,罗慧强,等.MSC Fatigue疲劳分析应用与实例[M].北京:科学出版社,2005:27-70.[7]BENDAT J S.Probability functions for random responses,NASA-5-4590[R].1964.。
基于道路谱的汽车车身疲劳分析
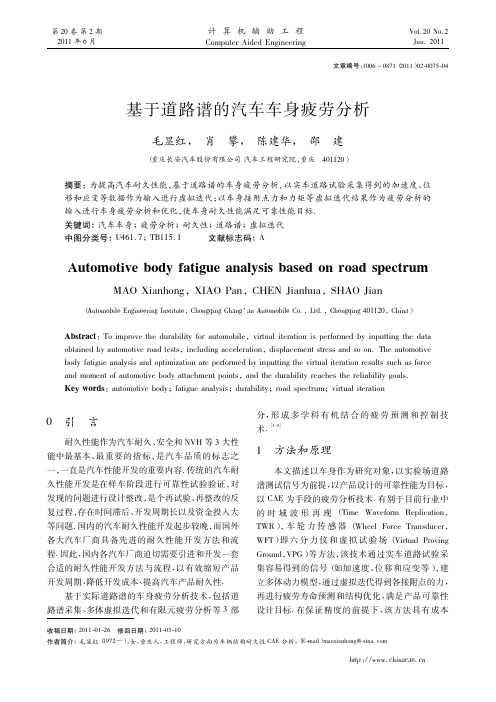
图 2 虚拟迭代原理 Fig. 2 Theory of virtual iteration
虚拟迭代首先由白噪声得到系统的传递函数 F,求逆得出逆函数 F - 1 ,再由试验采集得到的信号
求得一组初始驱动载荷并施加在多体动力学模型
MBS 上,计算得到所有输出通道的响应,包括迭代
信号、控制信号和信息信号等. 比较响应与采集的原
道路谱采集主要包含道路谱采集方案制定、采 集前的测试准备、道路谱采集、数据确认和采集数据 后处理等 5 项工作.
根据设计车的结构特点,制定一个科学可行的 道路谱采集方案是该技术的关键. 采集方案包含采 集内容、信号标定、采集设备及传感器要求、传感器 布置方式、采集线路及驾驶工况要求等.
道路谱采集前的测试准备包含零部件打磨、加 工,传感器布置,传感器标定,采集系统调试和整车 配重等.
0引言
耐久性能作为汽车耐久、安全和 NVH 等 3 大性 能中最基本、最 重 要 的 指 标,是 汽 车 品 质 的 标 志 之 一,一直是汽车性能开发的重要内容. 传统的汽车耐 久性能开发是在样车阶段进行可靠性试验验证,对 发现的问题进行设计整改,是个再试验、再整改的反 复过程,存在时间滞后、开发周期长以及资金投入大 等问题. 国内的汽车耐久性能开发起步较晚,而国外 各大汽车厂商具备先进的耐久性能开发方法和流 程. 因此,国内各汽车厂商迫切需要引进和开发一套 合适的耐久性能开发方法与流程,以有效缩短产品 开发周期、降低开发成本、提高汽车产品耐久性.
疲劳分析通过保留的 85 个通道,按照设计的可 靠性能目标里程,并根据疲劳累计损伤原理叠加 7 个典型路面的损伤,得到该车在实际道路谱下的疲 劳损伤值. 计算结果显示最大损伤在车身 A 柱右下 角焊缝部位,其值为 0. 45,小于设计目标值,车身其 余钣金结构疲劳损伤都小于 0. 2. 图 10 为车身疲劳 损伤云图.
基于实测载荷谱的整车疲劳开发与试验对比研究
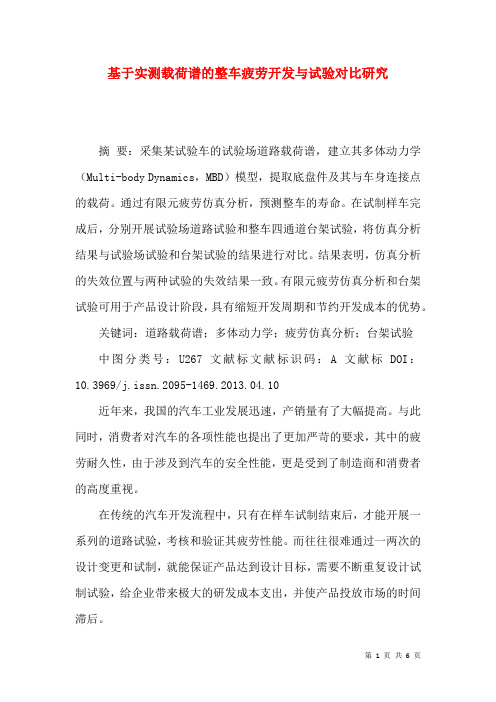
基于实测载荷谱的整车疲劳开发与试验对比研究摘要:采集某试验车的试验场道路载荷谱,建立其多体动力学(Multi-body Dynamics,MBD)模型,提取底盘件及其与车身连接点的载荷。
通过有限元疲劳仿真分析,预测整车的寿命。
在试制样车完成后,分别开展试验场道路试验和整车四通道台架试验,将仿真分析结果与试验场试验和台架试验的结果进行对比。
结果表明,仿真分析的失效位置与两种试验的失效结果一致。
有限元疲劳仿真分析和台架试验可用于产品设计阶段,具有缩短开发周期和节约开发成本的优势。
关键词:道路载荷谱;多体动力学;疲劳仿真分析;台架试验中图分类号:U267文献标文献标识码:A文献标DOI:10.3969/j.issn.2095-1469.2013.04.10近年来,我国的汽车工业发展迅速,产销量有了大幅提高。
与此同时,消费者对汽车的各项性能也提出了更加严苛的要求,其中的疲劳耐久性,由于涉及到汽车的安全性能,更是受到了制造商和消费者的高度重视。
在传统的汽车开发流程中,只有在样车试制结束后,才能开展一系列的道路试验,考核和验证其疲劳性能。
而往往很难通过一两次的设计变更和试制,就能保证产品达到设计目标,需要不断重复设计试制试验,给企业带来极大的研发成本支出,并使产品投放市场的时间滞后。
随着有限元技术、计算机硬件和数据采集技术的发展,基于实测道路载荷谱的疲劳性能开发技术,能够有效节约汽车产品研发成本,缩短研发周期。
其技术流程如图1所示。
本文以某轻型客车为例,论述了该技术路线中的道路载荷谱采集,有限元疲劳寿命预测和疲劳耐久台架试验等关键环节,并将仿真分析、台架试验和道路试验的结果相比较,验证了该方法的准确性和可行性。
1 道路载荷谱采集为了消除驾驶员的驾驶习惯和路面偶然因素对数据的影响[1],道路载荷谱采集工作由3名驾驶员进行,每人采集5次。
在试验场的强化路路段,使用MSC六分力传感器获取4个车轮轮心处承受的3个方向的力(Fx,Fy,Fz)和转矩(Mx,My,Mz),如图2所示。
基于实测道路谱的车身疲劳耐久性能改进

收稿日期:2019-12-02作者简介:张泽俊(1989 ),男,工程师,研究方向为车辆结构耐久性CAE分析㊂E⁃mail:csuftzhang@126 com㊂DOI:10 19466/j cnki 1674-1986 2020 04 004基于实测道路谱的车身疲劳耐久性能改进张泽俊,刘宗成,颜伏伍,王雪峰,冯广冬(东风小康汽车有限公司汽车技术中心,重庆402247)摘要:基于实测试验场道路载荷谱,结合多体虚拟迭代技术与CAE疲劳损伤分析技术再现某车型车身钣金和焊点疲劳失效㊂对车身结构进行改进,改进后的样车在后续可靠性试验中未出现车身疲劳失效问题㊂工程实践表明,该方法可用于车身开发过程中疲劳失效实际问题的改进,减少物理样车试验次数,节约开发成本㊂关键词:道路谱;白车身;虚拟迭代;损伤预测中图分类号:U463DurabilityImprovementofBIWBasedonMeasuredRoadSpectrumZHANGZejun,LIUZongcheng,YANFuwu,WANGXuefeng,FENGGuangdong(AutomotiveTechnicalCenter,DongfengSokonAutomobileCo.,Ltd.,Chongqing402247,China)Abstract:ThesheetmetalandweldingspotfatiguefailureinBIWwasreproducedbasedonthemeasuredroadloadspectrumandthecombinationmethodofvirtualiterationandCAEfatiguedamageanalysis.Thebodystructurewasimprovedbasedontheanalysisresults.AndthefatiguefailureinBIWnevershowedupinthesubsequentroadtests.Theengineeringpracticeindicatesthisapproachcanbeusedtoimprovethepracticalproblemsoffatiguefailure.Thetimesofexperimentcanbegreatlyreducedandalsothedevelopmentcostscanbesavedsignificantlyinthisway.Keywords:Roadspectrum;Whitebody;Virtualiteration;Fatiguedamageprediction0㊀引言面对日趋激烈的汽车市场,各大整车制造商不断延长整车质保里程或年限来提高产品竞争力,这样整车的疲劳耐久性能开发越来越受到重视㊂车身作为整车关键子系统之一,其耐久性能成为整车性能开发中的焦点之一[1]㊂车身是一切车身部件和底盘部件的安装基础,其结构和实际承受载荷的复杂多样性,给解决车身疲劳失效问题带来了极大的困难㊂一般是通过对样车进行可靠性道路试验和道路模拟试验来确保车辆达到耐久性能[2],但该手段存在开发周期长㊁资金投入大等问题㊂某新开发SUV车型,在整车道路模拟试验中,左右车身后门框处均出现钣金和焊点失效问题㊂通过试验场道路谱采集㊁建立多体动力学模型进行虚拟迭代并结合CAE疲劳分析技术,从仿真角度复现了车身疲劳失效问题,解决了车身开发过程中出现的疲劳失效问题,减少了开发成本及试验的盲目性,缩短了研发周期㊂1㊀车身失效情况简介及技术研究路线某SUV车型第一轮试制样车在整车四通道可靠性道路模拟试验完成63%时,发现左右后门框位置出现钣金开裂㊁焊点失效问题,如图1所示㊂检查发现裂纹断面存在磨损痕迹,说明车身左右侧后门框在试验小于63%时就出现了疲劳失效问题㊂意味着该SUV车身前期设计不能满足疲劳耐久性能要求,存在一定的安全隐患,需要对车身门框开裂位置进行优化设计,以达到指定的疲劳耐久性能㊂图1㊀车身门框失效通过实车在试验场采集载荷谱,并对采集的数据有效性进行检查,结合多体虚拟迭代技术和CAE分析技术再现物理试验疲劳失效点,并依据分析结果对车身结构进行改进㊂其技术路线如图2所示㊂图2㊀车身失效改进技术路线2 路谱采集及虚拟迭代2 1㊀采集工况简介采集车辆使用第一轮试制样车,在4个车轮上安装WFT六分力传感器,如图3(a)所示,采集车轮六分力信号;在车轮转向节轮心处安装加速度传感器,如图3(b)所示,采集轮心加速度信号;在前后车轮Topmount处安装加速度传感器,采集车身减震器塔顶处加速度信号;在前后减震器弹簧上布置应变计,测量前后弹簧应变信号;并安装GPS和陀螺仪,分别记录车辆行驶轨迹㊁车速和车身姿态㊂图3㊀车轮六分力传感器和轮心加速度传感器将样车配重至满载质量状态,依据路谱采集规范在某汽车试验场测量耐久试验路面(搓板路㊁卵石路㊁车身扭曲路等),GPS记录的车辆行驶轨迹如图4所示㊂图4㊀采集车辆行驶轨迹2 2㊀路谱采集结果及数据检查采集车辆布置传感器共计75个通道,各通道信号数据通过数据采集器记录和存储,每个样本采集3次㊂如图5所示,采集到的左后轮轮心的力和力矩㊂图5㊀采集到的左后轮轮心力和力矩在制动工况下,根据Fx和My的相互关系,可以判断采集到的六分力数据的正确性㊂如图6所示,左前轮在制动工况下Fx和My呈线性相关,且斜率在0 35左右,与轮胎的滚动半径一致㊂图6㊀制动力矩My和制动力Fx关系㊀㊀将采集到的4个车轮轮心Z向加速度做频谱分析,如图7所示,信号频率段主要集中在50Hz以下,与路面的激励频率一致,说明采集到的数据具备一定的有效性㊂图7㊀4个车轮轮心Z向加速度频谱2 3㊀多体虚拟迭代载荷分解采用多体虚拟迭代的方法获取车身各接附点的载荷,作为后续车身疲劳CAE分析的输入㊂将试验场采集到的载荷谱经过等效处理后,作为多体虚拟迭代的目标信号,搭建与采集样车状态一致的整车多体动力学模型,作为虚拟迭代的基础模型,如图8所示㊂图8㊀整车多体动力学模型虚拟迭代原理如图9所示,用白噪声驱动多体模型得到初始传递函数并求出反传递函数F-1,再根据试验采集的信号和反传递函数求得第一次迭代的驱动信号D1,该驱动信号再次驱动多体模型,可得到第一次的响应X1,对比X1与目标信号Xtarget,并修正公式(1)中的w,再迭代,直到满足收敛条件(Xn与Xtarget相对损伤值介于0 5 2之间[3])终止迭代㊂Dn+1=Dn+w㊃F-1㊃(Xtarget-Xn)(1)图9㊀虚拟迭代原理㊀㊀建立的多体动力学模型经过5次迭代后,迭代信号与目标信号的各通道相对损伤值范围在0 5 2之间,满足虚拟迭代精度要求㊂各次迭代收敛情况如图10所示㊂图10㊀各次迭代收敛情况通过最后一次迭代后,获取车身各接附点的力和力矩㊂图11所示为车身与后副车架连接左前接附点的力和力矩,获取的各接附点的载荷谱作为车身疲劳耐久CAE分析的输入㊂图11㊀车身与后副车架左前接附点力和力矩载荷谱3 车身疲劳CAE分析及疲劳失效再现3 1㊀车身疲劳CAE分析模型搭建搭建车身TB有限元模型,五门一罩㊁油箱㊁备胎㊁天窗等采用集中质量模拟,车身附件采用非结构质量NSM配重至钣金件上㊂车身焊点采用刚性梁Bar单元模拟[4],直径为6mm,梁单元与车身钣金件采用共节点方式连接㊂在车身18个接附点处加载六向单位载荷,共计108个通道,采用惯性释放法计算得到疲劳计算所需要的白车身结构应力场和焊点单元力场㊂3 2㊀车身疲劳损伤预测车身焊点刚性梁单元传递的力和力矩用来计算结构应力[5],基于计算的焊点结构应力对车身焊点进行疲劳损伤预测㊂焊点的材料采用Spot_Nugget_Generic和Spot_Sheel_Generic[6]㊂采用FKM法修正平均应力㊂将车身结构应力场导入疲劳分析软件,基于名义应力SN的方法,对车身进行疲劳损伤评估,其中平均应力修正采用Goodman法㊂由于车身几何形状复杂且受到多轴疲劳载荷作用,故采用临界平面法㊂临界平面法计算原理为过某点取n个等夹角的平面,对每个平面上的正应力和剪应力进行等效组合,对每个平面的等效应力计算损伤,然后取n个平面中最大损伤值为该点的损伤㊂根据车身中不同材料牌号建立不同材料的SN曲线㊂SN曲线可以通过试验获得,在缺少试验SN曲线时,可以根据材料的特性参数进行拟合得到SN曲线㊂对于母材,可以通过输入材料的抗拉极限UTS拟合得到材料应力寿命SN曲线[7],其拟合曲线如图12所示㊂图中参数SRI1㊁b1和b2通过公式(2) (5)计算得到㊂图12㊀基于UTS拟合的SN曲线SRI1=2ˑS2/(Nc1)b(2)b1=[log(S2)-log(S1)]log(Nc1)-3(3)b2=b1(2+b1)(4)S1=0 9ˑUTS;S2=0 357ˑUTS(5)式中:UTS为材料抗拉强度;S1为1000次循环下的应力幅值;S2为Nc1循环次数下的应力幅值;SRI1为循环1次即失效时的应力幅;b1和b2分别为SN曲线第一阶段和第二阶段的斜率;Nc1为SN曲线第一个拐点的循环次数,对于普通钢材材料Nc1一般取1ˑ106㊂设置好疲劳分析参数后,在疲劳分析软件中对车身焊点和钣金进行疲劳损伤计算,计算得到损伤结果如图13所示㊂可以看出:门框拐角处焊点的损伤均大于目标值1,最大损伤达到5 2(经验表明车身焊点损伤值高于1即存在失效风险);门框钣金的最大损伤为0 246(经验表明钣金处损伤值高于0 2即存在开裂风险)㊂分析结果表明:门框焊点㊁钣金失效位置与道路模拟试验失效位置一致㊂图13㊀车身焊点和钣金损伤计算结果3 3㊀车身结构改进依据上述分析结果,延长门槛梁加强板结构,并增加焊点,增加门框局部刚度,车身结构改进示意如图14所示㊂图14㊀车身结构改进示意对改进后的车身结构重新计算疲劳损伤,如图15所示㊂改进后的车身疲劳失效点的损伤远低于目标值,疲劳耐久性能得到显著提高㊂在后续的可靠性试验中,未发现门框处的焊点和钣金失效问题㊂图15㊀车身结构改进后损伤计算结果4㊀结束语以某白车身为研究对象,以实测试验场载荷谱作为多体虚拟迭代的输入,获取车身各硬点载荷谱,并结合CAE疲劳损伤预测方法,复现了可靠耐久试验中车身疲劳失效问题㊂针对车身失效位置提出了改进方案,改进后的车身失效位置的疲劳损伤值显著降低,并在后续的可靠耐久试验中未出现疲劳失效问题㊂实践表明,通过该方法预测的疲劳风险点与物理样车试验风险点比较吻合㊂该方法可用于车身开发过程中实际疲劳失效问题的改进,也可用于产品开发阶段车身的疲劳损伤预测,以此减少试验验证的盲目性,节约开发成本㊂参考文献:[1]黄金陵.汽车车身设计[M].北京:机械工业出版社,2007.[2]林育正,毛庆平.建立整车疲劳寿命分析技术的程序方法[J].车辆研测资讯,2005(3):20-27.[3]RYUS.Astudyonobtainingexcitationloadofvirtualtestlabusingvirtualiterationmethod[R].SAEPaper,2010-01-0011,2010.[4]龙海强,胡玉梅,刘波,等.基于随机载荷的白车身焊点疲劳寿命预测[J].汽车工程,2016,38(8):1006-1010.LONGHQ,HUYM,LIUB,etal.Fatiguelifepredictionforthespotweldsofbody⁃in⁃whitebasedonrandomloadings[J].AutomotiveEngineering,2016,38(8):1006-1010.[5]杜中哲,朱平,何俊,等.基于有限元法的轿车车身结构及焊点疲劳寿命分析[J].汽车工程,2006(10):944-947.DUZZ,ZHUP,HEJ,etal.FatiguelifeanalysisofcarbodystructureandspotweldbasedonFEM[J].AutomotiveEngineering,2006(10):944-947.[6]郜慧超.某重型载货汽车车架的疲劳分析及优化[D].北京:北京理工大学,2016.[7]毛显红,肖攀,陈建华,等.基于道路谱的汽车车身疲劳分析[J].计算机辅助工程,2011,20(2):75-78.MAOXH,XIAOP,CHENJH,etal.Automotivebodyfatigueanalysisbasedonroadspectrum[J].ComputerAidedEngineering,2011,20(2):75-78.L3级自动驾驶难落地?针对场景开发,发挥OTA价值是正解当前,L2级自动驾驶技术已经实现大规模的商业化运用,进一步向上突破,实现L3及以上自动驾驶汽车落地,成为了行业共同努力的方向㊂但同时也有一些车企宣称直接跃过L3级别,投入L4级自动驾驶的研发和量产㊂在自动驾驶领域,以腾讯为代表的软件和云服务提供方,对于量产落地的实现路径,有怎么样的投入和布局?日前,腾讯自动驾驶产品负责人王明明,分享了腾讯对自动驾驶落地应用的破局思路㊂从需求出发让用户早日体验到自动驾驶的便利性以用户的需求为出发点,提供场景化的自动驾驶服务,解决用户痛点,分场景㊁分需求逐步实现自动驾驶落地㊂解决高速场景中的自动驾驶,就可以在很大程度上满足用户解放双手的需求㊂另外,高速和封闭的城市快速路,道路地面标识相对清晰,路况相对简单,可以成为自动驾驶落地应用的第一步㊂除了高速和快速路,泊车也是在目前道路条件下可以比较快速实现的辅助驾驶场景㊂从2019年开始,腾讯自动驾驶团队针对高速及泊车场景进行了产品化开发,并预计在今年下半年推出针对这两种场景的自动驾驶量产解决方案,以分场景㊁分需求的方式逐步推动自动驾驶功能的量产落地㊂充分发挥腾讯的算法和云服务的优势,通过OTA让用户体验持续升级腾讯认为,实现数据闭环是自动驾驶系统不断优化的关键㊂在车辆硬件条件满足㊁算力保证的基础之上,腾讯可以结合自身的软件能力和云服务的优势,通过数据回传,尤其是cornercase的累积,实现算法的不断优化㊂经过OTA升级的方式更新软件,不断向用户开放更多自动驾驶能力,形成良性循环,为用户及车企合作伙伴带来持续的价值㊂软件定义汽车,差异化创造价值在数字化浪潮下,软件定义汽车的说法一再被提及,汽车电子软件爆炸式增长,随之而来的就是电子电气构架的变革㊂集中式架构取代传统的分布式架构,已经成为汽车电子电气架构公认的未来㊂集中式架构是方向,但是真正实现用一个或几个 大脑 来操控全车,面临着不少的挑战㊂硬件架构日趋相同,功能/体验的差异化更多通过软件的差异化实现㊂AI㊁大数据㊁云计算的发展,带来千人千面的定制化体验的潜力,使产品在硬件之外的增值变为可能㊂在这个过程中,腾讯希望聚焦自动驾驶软件,充分发挥自身的算法优势,提供模块化软件解决方案,做好数字化的工具箱,为合作伙伴提供助力㊂新基建推动产业互联网发展腾讯自动驾驶驶入快车道智慧出行领域,特别是自动驾驶产业链庞大且复杂,量产落地需要技术+政策+产业链共同驱动㊂腾讯一直在跟踪自动驾驶相关法规的进展,并力求在法规允许的范围内,为用户提供更好的产品体验㊂与此同时,腾讯也在积极推进法规建设㊂目前,腾讯正在与国家智能网联汽车(长沙)测试区㊁北京智能车联创新中心等行业机构密切合作,提升自动驾驶汽车的测试效率,共同探索测试评价的配套升级㊂自动驾驶和智能网联汽车领域将成为这一轮新基础建设加速的重点落地场景之一,腾讯自拥抱产业互联网以来,也早已布局了包含5G网络应用㊁车联网㊁自动驾驶等领域的智慧出行业务版图,连接丰富的出行服务生态,与政府部门㊁车企乃至整个汽车行业展开深入的合作,发挥自身的用户服务和生态连接能力,为智慧出行产业发展提供助力㊂(来源:互联网)。
基于实测载荷谱的副车架疲劳寿命估算方法

基于实测载荷谱的副车架疲劳寿命估算方法副车架是汽车底盘的一部分,是连接车轮、传动系统和悬架系统的主要构成部分。
它不仅要支撑整个汽车的重量,还要承受路况不良和载荷变化造成的负荷。
因此,副车架的疲劳寿命是汽车安全性和使用寿命的重要因素。
本文将讨论一种基于实测载荷谱的副车架疲劳寿命估算方法。
首先,测量和记录副车架在不同驾驶情况下的载荷变化。
它可以通过安装传感器来完成,该传感器可以记录副车架在不同路面、加速、刹车和转向等情况下的荷载。
这些测量结果可以作为载荷谱输入到疲劳寿命估算模型中。
其次,根据实验室测定得到的应力奋斗历程进行疲劳寿命试验,以获得副车架在该应力状况下的疲劳寿命。
然后可以使用疲劳寿命测试数据建立基于副车架所受载荷的疲劳寿命曲线,以估算不同载荷情况下副车架的疲劳寿命。
最后,将谱法理论应用于载荷谱中的副车架负载,得到当期载荷对应的等效疲劳载荷,并应用于副车架疲劳寿命曲线中以估算副车架的疲劳寿命。
根据所得到的结果,可以给出推荐的维护和更换周期。
然而,该方法存在的主要问题是,载荷谱的随机性质使得结果存在一定的误差。
此外,由于不同车辆的操作条件和使用环境不同,因此需要考虑实测数据的个体差异。
因此,建立一个可重复性高、可靠性强的疲劳寿命估算方法是当前研究的重点。
综上所述,随着计算机技术的不断发展,副车架的疲劳寿命估算方法将不断完善。
应在实践中运用合理的负载谱获取方法并结合疲劳寿命测试结果,以实现对汽车底盘的安全使用和长寿命的保障。
除了基于实测载荷谱的副车架疲劳寿命估算方法之外,还有一些其他方法可以用来评估副车架的疲劳寿命。
例如,可以使用计算机模型来模拟驾驶循环,并预测副车架在不同载荷下的应力状态。
它可以基于模拟结果建立疲劳寿命模型,以估算副车架的疲劳寿命。
此外,还可以使用裂纹扩展方法,以测定裂纹在副车架上扩展的速度。
通过中断试验,可以根据49CFR 393.207标准来估算副车架的疲劳状态,以确定是否需要维修或更换。
基于道路模拟激励的汽车下摆臂多轴疲劳分析

1. 2
道路模拟试验结果及迭代精度 为使迭代顺利进行, 一般将路谱分段后分别进
最后将各段迭代结果连接起来。 迭代结束 行迭代, 后, 比较轴头处测量的响应信号与试验场得到的目 标响应信号的接近情况。图 1 为其中一段响应信号 的迭代过程与结果。
1
1. 1
轮胎激励的获取
道路模拟原理及过程
道路模拟技术即以迭代的方式, 不断修正试验 台四立柱对轮胎的激励, 使室内测量的响应信号不 断接近试验场路试得到的目标响应信号 。 系统的频率响应函数的计算表达式为 -1 H( f) = X w ( f) Y w ( f) ( 1)
图2
强化路面左前轮胎接触面位移激励信号
2012 ( Vol. 34 ) No. 3
钱立军, 等: 基于道路模拟激励的汽车下摆臂多轴疲劳分析
· 251 ·
2
2. 1
整车刚柔耦合多体动力学仿真
有限元模型和刚柔耦合模型的建立 在 Hyperwoks 中对汽车下摆臂进行网格划分,
得到下摆臂的有限元模型, 见图 3 。 在下摆臂与汽 车其他零部件连接处建立超单元, 调用模态综合法 提交 OptiStruct 计 和设置输出模态中性文件的卡片, 算得到下摆臂的柔性体模型 ( 模态中性文件 ) 。 采 用替换法, 即将多刚体动力学模型中的下摆臂替换 为柔性体, 并以 ADAMS / Car Ride 中的四立柱为试 验台, 建立整车刚柔耦合模型, 见图 4 。
前言
* 国家重大技术装备研制和重大产业技术开发专项( 发改办高技[ 2007] 2823 号) 资助。 原稿收到日期为 2011 年 4 月 2 日, 修改稿收到日期为 2011 年 5 月 19 日。
· 250 ·
汽
不同试验场道路对车身疲劳损伤的贡献度分析研究开题报告

不同试验场道路对车身疲劳损伤的贡献度分析研究开题报告一、选题背景及研究意义随着国民经济的发展和交通工具的普及,车辆行驶里程愈来愈大,对车辆的安全及使用寿命的要求也相应提高。
然而,长期高强度的使用却不可避免地使车辆产生疲劳损伤。
车辆的疲劳寿命是指在允许的使用寿命范围内,在一定的载荷作用下经历多少次循环载荷,就会出现裂纹扩展,导致车辆结构破坏的寿命。
因此,评估车辆在不同道路环境下的疲劳损伤程度,对于确保车辆的安全性和使用寿命具有重要的意义。
二、研究目的及内容本研究旨在分析不同试验场道路对车身疲劳损伤的贡献度,并探讨影响其疲劳寿命的主要因素。
研究内容主要包括:1. 对不同试验场道路进行调查和评估,了解其基本情况、地质条件、道路类型、水准标准等相关信息。
2. 对不同载荷条件下进行试验,测量车辆的振动响应,得到车身的加速度时间历程,并对试验数据进行处理和分析。
3. 基于试验数据,使用有限元软件对车身进行建模,模拟车辆在不同道路环境下的载荷作用,分析不同道路对车身疲劳损伤的贡献度。
4. 探究影响车辆疲劳寿命的主要因素,包括载荷条件、道路类型、车型等因素,以提出改善车辆疲劳寿命的建议和措施。
三、研究方法及技术路线1. 调查不同试验场道路的基本情况,记录相关数据,对道路进行评估。
2. 设计不同载荷条件的试验,分别进行试验测量。
3. 对试验数据进行处理和分析,得到车身的加速度时间历程。
4. 建立车身的有限元模型,进行高频和低频的静态和动态分析。
5. 分析不同道路对车身疲劳损伤的贡献度,探索疲劳寿命的主要影响因素。
6. 提出改善车辆疲劳寿命的建议和措施。
四、预期成果及创新性本研究预期能够分析不同试验场道路对车身疲劳损伤的贡献度,并探究影响车辆疲劳寿命的主要因素,得到以下成果:1. 能够评估不同试验场道路的基本情况和地质条件,为车辆试验提供技术支持。
2. 能够客观地测量车身的振动响应和加速度时间历程,分析其对车身疲劳损伤的影响。
基于相对疲劳损伤谱的整车疲劳耐久试验加速方法研究

基于相对疲劳损伤谱的整车疲劳耐久试验加速方法研究李伟;端木琼;赵成刚【摘要】The authors propose a durability test acceleration method based on relative fatigue damage spectrum (RDS). Taking a vehicle as the research object, they acquire the spindle acceleration signal and shock-absorber displacement signal. They take the RDS of structural durability test procedures as a target to optimize the test proce-dure through optimizing algorithm. And under the premise of guaranteeing the RDS consistent, they try to shorten the test cycle as possible.%提出一种基于相对疲劳损伤谱的疲劳耐久试验加速方法。
以某轿车为研究对象,在试验场采集轴头加速度信号和减振器位移信号,以结构耐久性试验程序的相对疲劳损伤谱为目标,通过优化算法对试验程序进行优化,在保证相对疲劳损伤谱一致前提下,最大限度地缩短试验周期。
【期刊名称】《客车技术与研究》【年(卷),期】2016(038)002【总页数】4页(P46-48,55)【关键词】整车疲劳;耐久试验;相对疲劳损伤谱;加速方法【作者】李伟;端木琼;赵成刚【作者单位】中国汽车技术研究中心汽车工程研究院,天津 300300;中国汽车技术研究中心汽车工程研究院,天津 300300;中国汽车技术研究中心汽车工程研究院,天津 300300【正文语种】中文【中图分类】U467.4+97在整车开发流程中,车辆的疲劳耐久性是厂商重点关注的性能指标,直接影响到客户的满意度和车辆的三包成本。
基于道路载荷谱的车身疲劳寿命改进研究
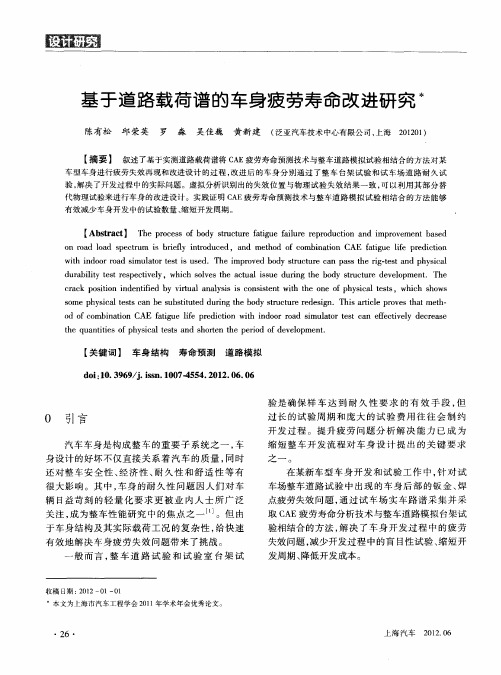
整 车室 内道 路 模 拟试 验 分 为轮 耦 合 型道路 模 拟 试验 和轴 耦 合型 道 路模 拟 试 验 两种 类 型 。失 效
位 置 的损 伤 贡献 分 析 结 果 表 明 , 身 失 效 位 置 处 车 占比 9 % 以上 的损 伤 发生在 以垂 向激励 为 主 的各 8 种 粗糙 路 面上 , 因此 本 课 题 中采 用 轮 耦 合 方 式 的
目
—
架试 验加 载信 号 驱 动 台架 , 各 监 测 点 处 采 集 应 在 变响 应信 号 , 后 与 实 际道 路 上 采 集 的 信 号进 行 然 比较 , 图 3所 示 , 算 出误 差 信 号 , 此 修 正 驱 如 计 据
动信 号并 再 次 完 成 加 载 , 此 循 环 下 去 。当迭 代 如 点 响应 与 目标 之 间 的 误 差 达 到 允 许 范 围之 内 时 ,
9 % 以 上 的粗 糙 路 面 采 集 的 信 号 进 行 迭 代 , 流 8 其
程 图见 图 2 。
1 代1 r嘉 模 _ 嚣 拟I . 迭- 1 - ' 膝 等
图 1 车 身 开 裂 研 究 技 术 路 线
2 1 典型 路面 道路 谱 采集 .
研 究 过 程 中采 用 虚拟 试 验 台 的形 式来 建 立 目 标 车辆 的耐 久 性 虚 拟 分 析 模 型 , 虚 拟 模 型 的边 该
界输 入 条件 为轮 轴 六 分 力 信 号 和轮 轴 位 移 信 号 , 而 此信 号必 须 通 过 实 车 的道 路 载 荷 谱 采 集 得 到 。
此外 , 虑 到后期 室 内道 路 模 拟 试 验 和 C E耐久 考 A
分 析 的需要 , 车 场 道 路 试 验 采 集 的 信 号 包 括 车 试
基于实测载荷谱的白车身疲劳寿命计算
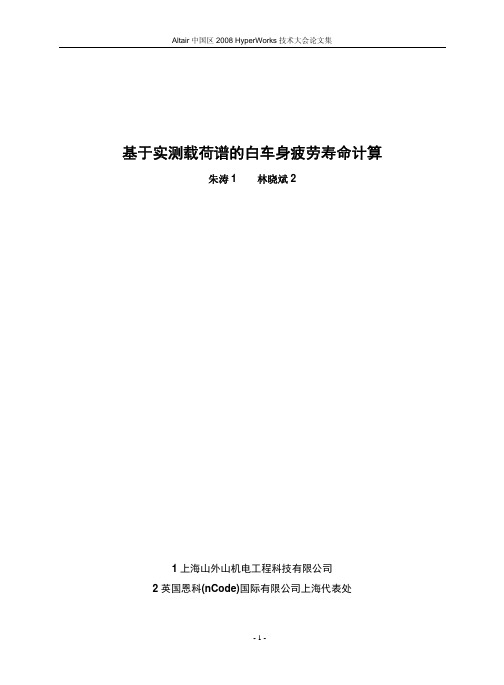
基于实测载荷谱的白车身疲劳寿命计算朱涛1 林晓斌21上海山外山机电工程科技有限公司2英国恩科(nCode)国际有限公司上海代表处基于实测载荷谱的白车身疲劳寿命计算朱涛1 林晓斌21上海山外山机电工程科技有限公司2英国恩科(nCode)国际有限公司上海代表处摘要:汽车白车身疲劳分析由于缺乏真实载荷谱的输入而显得没有说服力,计算分析的结果往往与试车场或用户使用时发生的失效没有关联,这样导致了虚拟疲劳分析的强大作用无法发挥。
本文通过六分力轮测试系统实测了某型乘用车在试车场的载荷谱数据,以此作为输入,并综合了多种CAE手段,包括有限元网格划分、有限元分析、多体动力学分析和疲劳分析,对该乘用车的白车身在实测载荷谱作用下的疲劳寿命分布进行了计算分析,获得了有价值的结果。
同时给出了更符合真实工况的试验与虚拟相结合的白车身一体化疲劳分析流程。
关键词:白车身,虚拟疲劳分析,道路载荷谱,有限元网格划分,有限元分析,多体动力学分析1 前言汽车结构疲劳的话题在当前各大整车制造企业越来越受到重视,几乎每种新开发的车型都需要考察其疲劳耐久性能。
以前传统的方法,汽车企业对于新车型疲劳寿命的评估都是利用实车在各道路试车场进行路试[1],该方式虽然是最直接且最准确的,但测试时间却十分冗长且耗费人力与经费甚巨,即使发现了问题往往也很难去修改。
近年来计算机软硬件的迅速发展,计算机辅助工程(CAE)分析技术在静态、碰撞、振动噪音等领域均有了相当不错的应用成果,但疲劳耐久性分析需要综合有限元应力分析和动力学载荷分析等专业技术,仍需花费非常大的计算量,且计算的准确性由于没有真实的道路载荷谱(RLD)作为计算输入而缺乏说服力。
本文针对上述问题,基于在国内汽车企业已经开始成熟运用的六分力轮测试技术实测获得的某乘用车在试车场的道路载荷谱数据[2],以此作为输入,驱动建立好的整车多刚体动力学仿真模型,获取作用在白车身各连接点上的载荷谱,同时对白车身进行有限元应力场分析。
基于路谱频域的车身疲劳分析

Absr c :As t e e e b d aiu a a y i ta t o v hil o y f tg e n lss,a sr e u e d n mis e p n e ( l n [b o im’d n tu t r y a c r s o s : l o e e nsd e i a sa i o d n t 0 t t .1a i g meh d,a d ta se ta ay i t o ( n n tb p le n t ou i n wih a v ro g ( n r n in n l ssmeh d : o e a p id o he s l to t n o e ln a
T 1tv I a v t)u e fe ue c o i t o ( . a i v s ( s r q n y d man me h d t )pef r d n mi ftg e a ay i ) a g s ae fn t ro m y a c a iu n l ss‘ l re c l i ie n
第 21巷 第 2期
2 2 年 4 月 01
助
工
程
VO . NO. 1 2j 2
4p . 2 2 r 0l
Eng n e i g i e rn
文 毒 编 号 :0 6—0 7 ( 0 2 0 —00 0 10 8 1 2 1 )2 05 —3
基 于路 谱 频 域 的车 身 疲 劳 分 析
i ‘Ie1f rav h ce b d s sl ( b e il o v,a d t e r s lsa e r ltv l o it n t a iu e tr s t . ti e sbl v n h e u t r e ai ey c nsse twih f t e t s e ul I sf a i e g s
基于六分力载荷谱的汽车车身及焊点疲劳分析

! 理论方法
!"! #$%&' 法则 疲劳累积损伤理论是疲劳分析的关键理论。目前
名义应力法主要应用于应力水平较低而破坏循环
4
次数较高(一般高于 10次)的高周疲劳破坏。名义应力
[6]
法的工具是 S-N曲线 ,该曲线纵坐标为加载于试件上
的恒定应力幅值(max),横坐标为试件材料在该恒定应 力作用下的疲劳循环次数的对数值(),如图 1所示。
在工程中广泛使用的是线性疲劳累积损伤理论中具有 由图 1可以看出,当所加交变应力小于疲劳极限值
[4]
代表性的 Miner法则 ,该法则假设:当结构所吸收的
(R)时,该试件可承受无限次循环而不断裂。
- -
应力幅值 max/MPa
2第0260(期6)
Design-Innovation
疲劳极限值 R/MPa
a 扭转
b 弯曲
图 白车身有限元模型 阶模态结果云图
表 1示出 1阶扭转模态与弯曲模态的分析结果与
循环次数依次为 1,2,3…,则疲劳损伤值 为:
=1 1
2
2
…
!
"
(1)
当 =1时,表明结构所吸收的总能量达到结构破
坏时的极限能量,此时结构发生疲劳破坏。式(1)即为
[5]
Miner法则的疲劳累积损伤理论方程 。
!"( 名义应力法
值,为设计者在项目开发初期的车身及焊点疲劳寿命
随着汽车工业的发展,车身及焊点的疲劳耐久性
[1]
能逐渐成为衡量汽车性能的重要指标 。传统的汽车疲
劳耐久性主要通过试车场试验、道路试验以及台架试
基于道路谱的整车疲劳分析

MAX
设置分析 参数
保存Group信息文件
保存Channel MAX信息文件 保存分析任 文件
提交分析
疲劳分析操作流程图
疲劳计算 实车路试对比
三、FEMFAT软件在长安开发 架疲劳仿真
扭力梁 架疲劳仿真
稳定杆 架疲劳仿真
悬架系统 架疲劳仿真
2 模型检查 计算TB状态模型的模态,对模型进行检查
3 静力分析,采用惯性释放方法,计算各通道6方向的静力结果
某款汽车接附点编号示意图
二、基于道路谱的车身疲劳分析
5.在FEMFAT中计算基于道路谱的车身疲劳损伤
新建任
导入分析 模型
生成通道临时文件
后处理
按照材料 分Group
导入材料并指 定Group材料
速度及在Z向
的位移 根据此原则路普采集试验一般安装以 传感器用于相关信号采集 1 变片 标定出车 X Y方向力 标定出减震器 或弹簧 Z方向力 2 位移传感器 测量 心Z向位移 3 速度传感器 测量 心处X Y Z方向 速度 测量车身 毂包处Z方向
速度 4 GPS 测量试验车纬度 经度 海拔 车速等
某款汽车数据采集路线示意图
某款汽车选择的9段特征路面
3. 多体动力学仿真
根据选择的特征路面,进行载荷谱迭代,载荷分解及工况仿真计算
二、基于道路谱的车身疲劳分析
4.计算单位载荷 的 力分布
1 计算单位 力的模型准备
1 一般用TB状态的模型
2 焊点焊缝的处理
3 接附点编号
4 配重保持 多体模型一
5 按照材料对模型进行分组
踏板 架耐久仿真
车 弯曲疲劳 架耐久仿真
三、FEMFAT软件在长安开发体系中的应用
基于道路谱的多体仿真迭代疲劳载荷技术_沙大亮

2 整车虚拟样机建立 整车虚拟样机的质量直接影响到能否获取可 信了车身及底盘零部件的疲劳载荷。整车模型与实 际样车差距较大将导致迭代所需的传递函数的不 能反映真实车辆状态,线性性也不能满足要求,甚 至会导致仿真迭代不能正常进行。首先,根据样车 底盘参数(硬点、零部件质量、弹簧刚度、减振器 阻尼以及衬套的刚度数据等) 和配重数据, 用 Adams 建立该车的多体动力学模型。模型中不含有轮胎, 这是由于迭代的位移和力均作用在轮心处,作为整 车的驱动信号,直接驱动整车模型运动。其次在道 路测试之前,应该测量车辆的轮胎载荷、重心位置 和悬架限位器间隙等参数,并根据测量结果对模型 进行修正。第三是建立驱动信号通道。在多体模型 的轮心处建立垂向的位移 (Point Motion)驱动作为 垂向的位移驱动信号(如多通道的还需建立横向和 纵向的力驱动) 。位移数据以 Spline 形式通过函数 输入,例如 CUBSPL(time,0,SPLINE_DZ_FL, 0)。最后
基于道路谱的多体仿真迭代疲劳载荷技术
作者:沙大亮 卲建 陈建华 王俊翔
单位:重庆长安汽车工程研究院 CAE 工程所
摘要: 对于疲劳载荷谱的获取一直是疲劳分析中极为重要的一个部分, 直接决定疲劳分析的结果是否准确。 本文介绍一种实用性强、精度高、经济可靠的疲劳载荷获取方法。这种技术是用应标定技术获取真实道路 谱,通过驱动 Adams 建立的车辆虚拟样机进行迭代,使车辆虚拟模型的相应通道逼近实测道路谱信号,从 而实现虚拟样机重现实际道路过程, 进而获取车身及其零部件道路谱疲劳载荷, 为疲劳分析提供载荷输入。 关键字:道路谱 ADAMS 迭代 疲劳载荷
该技术是通过标定样车进行道路试验,采集得 到的路谱信号(如加速度、位移、应变等) ,利用 多体动力学软件(Adams)建立车辆虚拟样机,然 后通过迭代软件 FemFat-Lab 调用 ADAMS 的求解器 对样机模型进行迭代计算,并通过各个信号通道控 制,使车辆虚拟样机状态逼近样车实际状态,进而
基于道路谱的整车疲劳分析

2 模型检查 计算TB状态模型的模态,对模型进行检查
3 静力分析,采用惯性释放方法,计算各通道6方向的静力结果
某款汽车接附点编号示意图
二、基于道路谱的车身疲劳分析
5.在FEMFAT中计算基于道路谱的车身疲劳损伤
新建任
导入分析 模型
生成通道临时文件
后处理
按照材料 分Group
导入材料并指 定Group材料
某款汽车传感器布置示意图
二、基于道路谱的车身疲劳分析
2.载荷信号采集及数据后处理
1 采集 根据路试道路规划进行多次 少2次以 典型路面载荷采集 2 数据减缩 根据相对损伤值进行数据减缩,确保减缩后的数据 原数据的相对 损伤值相当 3 路普选择 1 该路普多数通道最大值均大于另外的路谱 2 该路谱多数通 道相对损伤值均大于另外的路谱 3 该路谱 存在 合理数据
速度及在Z向
的位移 根据此原则路普采集试验一般安装以 传感器用于相关信号采集 1 变片 标定出车 X Y方向力 标定出减震器 或弹簧 Z方向力 2 位移传感器 测量 心Z向位移 3 速度传感器 测量 心处X Y Z方向 速度 测量车身 毂包处Z方向
速度 4 GPS 测量试验车纬度 经度 海拔 车速等
某款汽车数据采集路线示意图
某款汽车选择的9段特征路面
3. 多体动力学仿真
根据选择的特征路面,进行载荷谱迭代,载荷分解及工况仿真计算
二、基于道路谱的车身疲劳分析
4.计算单位载荷 的 力分布
1 计算单位 力的模型准备
1 一般用TB状态的模型
2 焊点焊缝的处理
3 接附点编号
4 配重保持 多体模型一
5 按照材料对模型进行分组
基于道路谱的整车疲劳分析 ——长安汽车
- 1、下载文档前请自行甄别文档内容的完整性,平台不提供额外的编辑、内容补充、找答案等附加服务。
- 2、"仅部分预览"的文档,不可在线预览部分如存在完整性等问题,可反馈申请退款(可完整预览的文档不适用该条件!)。
- 3、如文档侵犯您的权益,请联系客服反馈,我们会尽快为您处理(人工客服工作时间:9:00-18:30)。
Aut m o i e b d a i u n l ss b s d o o d s c r m o tv o y f tg e a a y i a e n r a pe t u
MA0 Xin o g a h n ,XI a AO P n,CHEN Ja h a HAO in in u ,S Ja
集容易得到的信号 ( 如加速度、 位移 和应变 等) 建 ,
立多体动力模型, 通过虚拟迭代得到各接附点的力 ,
Байду номын сангаас
基于实际道路谱 的车身疲劳分析技术 , 包括道
再进行疲劳寿命预测和结构优化 , 满足产品可靠性 设计 目标. 在保证精度 的前提下 , 方法具有成本 该
( uo oi n ier gIstt, hnqn hn ’nA tm bl C . t. C ogig4 12 ,C ia A tm bl E g e n tue C ogigC ag a uo oi o ,Ld , h nqn 0 0 hn ) e n i ni e 1
Absr c t a t:T mp o e t e d r b l y fr a tmo ie,vru l i r t n s pef r d b np t n h aa o i r v h u a ii o u o b l t i a t ai i ro me y i ut g t e d t t e o i o t i e y a tmo ie r a e t n l di c e e ain,d s l c me tsr s nd S n b a n d b uo t o d t ss,i cu nga c lr to v ip a e n te sa O o .Th u o tv e a tmoie
,一
直是汽车性能开发的重要内容. 传统的汽车耐
久性能开发是在样 车阶段进行可靠性试验验证 , 对
发 现 的问题进 行设计 整 改 , 个再 试验 、 是 再整 改 的反
谱测试信号为前提 , 以产品设计 的可靠性能为 目标 ,
以 C E为手段 的疲 劳分 析技 术. 别 于 目前行 业 中 A 有 的 时 域 波 形 再 现 ( ie Tm Waeo R pi tn vfr m elao , ci
O 引 言
耐 久性 能作 为汽 车耐久 、 全和 N H等 3大性 安 V 能 中最 基本 、 重 要 的指 标 , 汽 车 品质 的 标 志 之 最 是
一
分 , 成 多 学 科 有 机 结 合 的 疲 劳 预 测 和 控 制 技 形
术 .1] [2 -
1 方 法 和 原 理
本 文 描 述 以车 身作 为研 究对 象 , 以实 验场 道 路
复过程 , 存在时间滞后 、 开发周期长以及资金投入大 等问题. 国内的汽车耐久性能开发起步较晚 , 而国外 各大汽车厂商具备先进 的耐久 性能开发方法 和流 程. 因此 , 国内各汽车厂商迫切需要引进和开发一套 合适的耐久性能开发方法与流程 , 以有效缩短 产品
开 发周 期 、 降低 开发成 本 、 提高 汽车产 品 耐久性 .
T ) 车 轮 力 传 感 器 ( elFr r sue, WR , Whe o e Ta dcr c n
wF )即 六 分 力 仪 和 虚 拟 试 验 场 ( iu rv g T Vr a Poi tl n
Gon ,P ) rud V G 等方法 , 该技术通过实车道路试验采
第2 0卷 第 2期
2 l 年 6月 01
计 算 机 辅 助 工 程
C mp t rAi e gn e i g o u e d d En i e rn
Vo . 0 N . I2 o 2
Jn 0 l u .2 l
文章编号 :0 6—0 7 (0 1 0 —05 0 10 8 12 1 )2 0 7 .4
b d ai u n lssa d o t z t n a e p r r d b p t n e vru li r t n r s l u h a o c o y f t e a a y i n p i ai r e o me y i ut g t i a e a i e u t s c sfr e g mi o f n i h t t o s a d mo n fa t mo ie b d t c me t on s n h u a i t e c e h ei b l y g a s n me to u o t o y a t h n i t ,a d t e d r b l y r a h st e rl i t o l. v a p i a i Ke r s u o t e b d ;f t u n lss u a i t y wo d :a t moi o y a i e a a y i ;d r b l y;r a p cr m ;v r a tr t n v g i o d s e tu i u li ai t e o
基 于道 路 谱 的汽 车车 身 疲 劳 分 析
毛显红 , 肖 攀 , 陈建华, 邵 建
( 重庆长安汽车股份有 限公 司 汽车 工程研 究院, 重庆 4 1 2 ) 0 10
摘要: 为提高汽车耐久性能, 基于道路谱的车身疲 劳分析 , 以实车道路试验采集得到的加速度、 位 移和应变等数据作为输入进行虚拟迭代; 以车身接附点力和力矩等虚拟迭代 结果作为疲 劳分析 的 输入进行车身疲劳分析和优化, 使车身耐久性能满足可靠性能 目 标. 关键词: 汽车车身; 疲劳分析 ; 耐久性 ; 道路谱 ; 虚拟迭代 中 图分类 号 : 4 17 T 15 1 U 6 . ; B 1. 文献标 志码 : A