N-甲基吡咯烷酮技术简介
nmp溶剂生产工艺

nmp溶剂生产工艺NMP(N-甲基吡咯烷酮)是一种重要的溶剂,广泛应用于聚合物、电子材料、涂料、农药、药物和化工等领域。
NMP的生产工艺主要包括煤焦油提取法、气相法和合成法。
煤焦油提取法是目前NMP主要生产工艺之一。
该工艺以煤焦油为原料,经过洗涤、蒸馏等步骤,提取出其中的NMP。
首先,将煤焦油和洗涤剂混合,通过搅拌、加热等操作,使NMP与其他组分进行分离。
然后,通过蒸馏的方式,将含有NMP的部分分离出来。
最后,对分离出的NMP进行精馏和净化,得到高纯度的NMP溶剂。
这种方法的主要优点是原料易得,成本较低,但生产过程相对复杂,能耗较高。
气相法是新兴的NMP生产工艺之一,主要用于生产高纯度的NMP溶剂。
该工艺主要通过将大气中的空气、氮气等,在高温高压下与甲胺反应生成NMP。
首先,将气体原料与甲醛进行催化反应,生成甲酘。
然后,将甲酘与甲胺在高温高压下进行缩合反应,生成NMP。
最后,将反应产物进行精馏和净化,得到高纯度的NMP溶剂。
这种方法的主要优点是生产过程相对简单,能耗较低,且能够实现自动化生产,提高生产效率。
合成法是另一种常用的NMP生产工艺。
该工艺主要通过化学合成的方法制备NMP。
首先,将丙酮和甲胺进行缩合反应,生成N-甲基吡咯酮。
然后,将N-甲基吡咯酮进行脱水反应,生成NMP。
最后,通过精馏和净化,得到高纯度的NMP溶剂。
这种方法的主要优点是生产过程简单,原料易得,能耗较低。
然而,合成法需要使用催化剂和辅助溶剂,所以对环境要求较高。
综上所述,NMP的生产工艺主要包括煤焦油提取法、气相法和合成法。
煤焦油提取法是成本较低的传统工艺,气相法能够生产高纯度NMP溶剂,合成法更加简单易行。
随着科技的不断进步,相信NMP生产工艺将会不断创新,提高生产效率,提高产品质量,以满足市场的需求。
n-甲基吡咯烷酮标准

n-甲基吡咯烷酮:一种多功能溶剂的标准与应用一、引言n-甲基吡咯烷酮(NMP),化学式为C5H9NO,是一种无色、透明、高极性的液体,具有酰胺基团的结构特性,因此也被归类为酰胺类溶剂。
由于其出色的溶解性能和广泛的适用性,n-甲基吡咯烷酮在众多工业领域中发挥着重要作用。
本文将详细探讨n-甲基吡咯烷酮的标准及其应用。
二、n-甲基吡咯烷酮的物理化学性质n-甲基吡咯烷酮的分子结构中包含一个五元杂环和一个酰胺基团,这为其赋予了独特的物理化学性质。
它是一种极性溶剂,可以溶解许多有机和无机物质,包括许多高分子化合物。
此外,n-甲基吡咯烷酮具有较高的沸点(202°C)和闪点(95°C),较低的蒸汽压和粘度,以及良好的热稳定性和化学稳定性。
三、n-甲基吡咯烷酮的生产与质量标准n-甲基吡咯烷酮的生产主要通过吡咯烷酮的甲基化反应进行。
在生产过程中,需要严格控制原料质量、反应条件、后处理等环节,以保证产品的纯度和质量。
在国内外,已经有多家知名的化工企业生产和销售n-甲基吡咯烷酮。
为了保证n-甲基吡咯烷酮的质量和安全性,许多国家和地区都制定了相应的质量标准。
例如,美国食品药品监督管理局(FDA)规定n-甲基吡咯烷酮可用于食品、药品和其他用途,但必须符合其规定的质量标准。
欧洲化学品管理局(ECHA)也将n-甲基吡咯烷酮列为需要注册、评估、授权和限制的化学物质(REACH),对其生产、进口和使用都有严格的管理和限制。
在中国,国家标准化管理委员会也发布了n-甲基吡咯烷酮的国家标准,对其外观、纯度、水分、酸度等指标都有明确的规定。
此外,对于食品、医药等敏感领域的应用,还需要符合相关行业的质量标准和安全规定。
四、n-甲基吡咯烷酮的应用领域1. 高分子合成:n-甲基吡咯烷酮是一种重要的高分子合成溶剂,可用于聚合反应、共聚反应、交联反应等。
它可以溶解许多高分子单体和聚合物,有利于反应的进行和产物的分离纯化。
2. 电子工业:在电子工业中,n-甲基吡咯烷酮被用作清洗剂、剥离剂和光刻胶溶剂等。
N-甲基吡咯烷酮(NMP)MSDS

N-甲基吡咯烷酮(NMP)MSDSN-甲基吡咯烷酮化学品安全技术说明书1. 标识(1)化学名称:N-甲基吡咯烷酮(2)分子式:C5H9NO(4)相对分子量:99.15(5)CAS号:872-50-4(6)危险性类别100%中文名:N-甲基吡咯烷酮,NMP,1-甲基-2-吡咯烷酮2. 主要组成与性状(1)主要成分及其含量(2)外观与性状:透明液体有胺样气味3. 健康危害(1)侵入途径(2)健康危害:可燃性液体和蒸气。
会对皮肤、眼睛及呼吸道产生刺激。
吞入、吸入或透皮吸收均有害。
皮肤:会导致搔痒、发红、脱皮及荨麻疹。
可快速透皮吸收,能将其它溶解的毒素运至体内。
眼睛:对眼睛有刺激性并会造成角膜灼伤。
吸入:会产生呼吸道刺激、头痛、恶心、头晕以及困倦摄入:会导致头晕、困倦、恶心、呕吐、痛性痉挛以及寒战。
4. 急救措施皮肤接触:在脱掉受污染的衣物和安全鞋的同时用水冲洗皮肤至少15 分钟。
如产生刺激或任何其它症状应就医治疗。
眼睛:立即用大量水冲洗眼睛至少15 分钟。
需就医治疗。
吸入:将受害者移至新鲜空气中。
如呼吸停止,应施予人工呼吸。
如果呼吸困难,由具资质的人员给予氧气治疗。
需立即就医治疗。
摄入:如仍有意识,应用水漱口。
患者可通过喝水或牛奶来稀释胃溶物。
除非有医疗人士指导,不可自行催吐。
应立即就医治疗。
给医生的建议:无特别建议。
针对症状加以治疗。
5. 爆炸特性与消防(1)燃烧性(2)闪点(3)爆炸极限(4)引燃温度(5)危险特性(6)灭火方法:二氧化碳、干化学制品或泡沫灭火。
187℉(88℃)易燃上限(空气中的容积百分比%):9.5%易燃下限(空气中的容积百分比%): 1.3%6. 泄漏时的应急救援措施如果发生泼溅或其它泄漏事故:(时刻穿戴经推荐的个人防护设备。
)清除着火源。
隔离溢出区域。
如可能应使用工具装盛和回收溢出液。
用惰性物质将少量溢出液吸收并置于经许可的化学废品容器中。
对于大量的溢出液,应用惰性物质将溢出区域堤围,并转入与上面相同的容器。
n甲基吡咯烷酮合成工艺

n甲基吡咯烷酮合成工艺
n甲基吡咯烷酮(NMP)是一种重要的有机溶剂,广泛应用于
化工、医药、电子等领域。
下面将介绍一种常用的NMP合成
工艺。
NMP的合成主要有两种方法:吡咯烷酮法和N-甲基吡咯烷酮法。
其中,吡咯烷酮法是目前应用较广泛的一种方法。
吡咯烷酮法的合成步骤如下:
1. 原料准备:将吡咯烷和甲醛按一定比例混合,制备好反应物。
2. 反应装置准备:将反应釜充分清洗,并保持干燥。
同时,将冷却装置连接好,以便控制反应温度。
3. 反应过程:将制备好的反应物加入反应釜中,控制反应温度在100-120摄氏度之间,并进行搅拌。
根据需要,可以添加一
定量的催化剂来促进反应进程。
4. 反应结束:当反应达到一定时间后,停止搅拌,并将反应液进行冷却。
冷却后,反应液中会生成NMP。
5. 分离纯化:将反应液进行过滤或蒸馏,以分离出纯净的NMP。
同时,可以进行进一步的纯化处理,以提高NMP的纯度。
6. 产品收集与储存:将得到的纯净NMP收集起来,并进行适
当的储存,以便后续使用。
需要注意的是,在整个合成过程中,要注意安全操作,避免接触到反应物和产物。
同时,对于废弃物的处理也要符合环保要求。
以上就是一种常用的n甲基吡咯烷酮合成工艺。
通过这个工艺,可以高效地合成出纯净的NMP,满足不同领域的需求。
在实
际应用中,还可以根据具体情况进行工艺优化和改进,以提高产率和降低成本。
nmp相gpc条件

nmp相gpc条件NMP和GPC是两种不同的化学和分析技术。
NMP是N-甲基吡咯烷酮,是一种常用的有机溶剂,主要用于溶解和分散聚合物、树脂和涂料等化学物质。
在聚合物工业中,NMP被广泛应用于溶剂萃取、聚合反应和涂料配方中。
它具有高溶解度、低挥发性和热稳定性的特点,因此在高性能材料的生产中扮演着重要的角色。
而GPC代表凝胶渗透色谱法(Gel Permeation Chromatography),也被称为凝胶渗透层析法(Gel Filtration Chromatography),是一种用于聚合物分析的重要技术。
它通过将溶液中的聚合物分子按照大小分离出来,从而得到聚合物的分子量分布信息。
GPC通常用于研究聚合物的分子量、分子量分布、聚合度和聚合物结构等参数,对于聚合物材料的研发和质量控制具有重要意义。
从化学角度来看,NMP是一种有机化合物,其分子结构中含有甲基和吡咯烷酮基团,这使得它具有较强的溶解能力和稳定性。
而GPC则是一种分析技术,利用聚合物在凝胶柱中的渗透性差异进行分离和测定。
这两者在聚合物材料领域中有着密切的关联,NMP作为溶剂在聚合物制备过程中的应用,而GPC则用于分析所得聚合物的性质和质量。
从应用角度来看,NMP作为一种优良的溶剂,在聚合物工业中被广泛用于溶解和处理各种类型的聚合物。
而GPC则被广泛应用于聚合物材料的研发和质量控制中,通过分析聚合物的分子量分布等参数,帮助科研人员和工程师了解和控制所得聚合物的特性。
总的来说,NMP和GPC分别代表了一种化合物和一种分析技术,在聚合物材料的生产和研发中都具有重要的地位和作用。
它们的结合可以帮助人们更深入地了解和控制聚合物材料的特性,推动聚合物材料领域的发展和创新。
n-甲基吡咯烷酮 环境空气质量标准
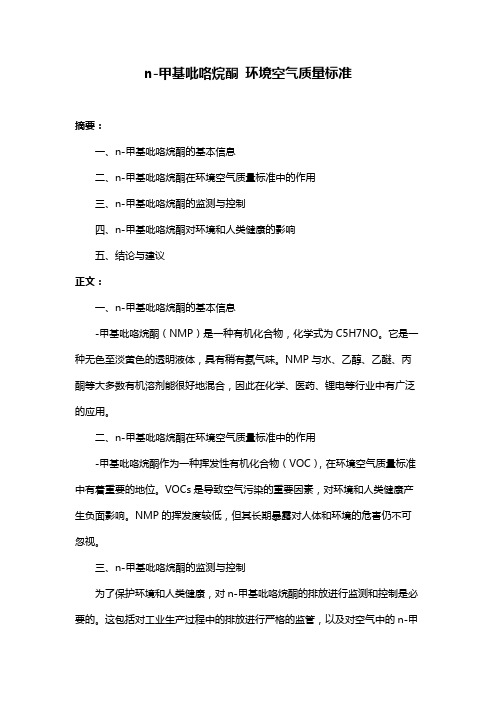
n-甲基吡咯烷酮环境空气质量标准摘要:一、n-甲基吡咯烷酮的基本信息二、n-甲基吡咯烷酮在环境空气质量标准中的作用三、n-甲基吡咯烷酮的监测与控制四、n-甲基吡咯烷酮对环境和人类健康的影响五、结论与建议正文:一、n-甲基吡咯烷酮的基本信息-甲基吡咯烷酮(NMP)是一种有机化合物,化学式为C5H7NO。
它是一种无色至淡黄色的透明液体,具有稍有氨气味。
NMP与水、乙醇、乙醚、丙酮等大多数有机溶剂能很好地混合,因此在化学、医药、锂电等行业中有广泛的应用。
二、n-甲基吡咯烷酮在环境空气质量标准中的作用-甲基吡咯烷酮作为一种挥发性有机化合物(VOC),在环境空气质量标准中有着重要的地位。
VOCs是导致空气污染的重要因素,对环境和人类健康产生负面影响。
NMP的挥发度较低,但其长期暴露对人体和环境的危害仍不可忽视。
三、n-甲基吡咯烷酮的监测与控制为了保护环境和人类健康,对n-甲基吡咯烷酮的排放进行监测和控制是必要的。
这包括对工业生产过程中的排放进行严格的监管,以及对空气中的n-甲基吡咯烷酮浓度进行实时监测。
四、n-甲基吡咯烷酮对环境和人类健康的影响-甲基吡咯烷酮对人体健康的影响主要表现在对神经系统、血液系统的毒害。
长期暴露在高浓度NMP环境中,可能导致人体健康问题。
此外,n-甲基吡咯烷酮还对环境产生危害,如对水体的污染、对生态系统的影响等。
五、结论与建议综上所述,n-甲基吡咯烷酮作为一种重要的环境污染物,有必要对其进行严格的监测和控制。
企业应当加强自律,降低生产过程中的排放。
政府部门应制定更严格的标准,加强对n-甲基吡咯烷酮污染的监管。
N-甲基吡咯烷酮

N-甲基吡咯烷酮1. 简介N-甲基吡咯烷酮(N-Methyl-2-Pyrrolidone,简称NMP)是一种无色透明液体,具有强烈的吸湿性。
它是一种极性有机溶剂,可溶于大多数有机溶剂和水。
NMP在工业中有广泛的应用,尤其在聚合物和化学品生产中起着重要作用。
2. 物理性质•外观:无色透明液体•分子式:C5H9NO•分子量:99.13 g/mol•熔点:-24 °C•沸点:202 °C•密度:1.03 g/cm³•闪点:95 °C•燃点:435 °C3. 化学性质3.1 溶解性NMP是一种极性溶剂,具有优良的溶解性能。
它可以与多种有机物和聚合物相溶,如橡胶、纤维素、塑料和染料等。
此外,NMP还能溶解一些无机盐和金属离子。
3.2 稳定性NMP在一般情况下是稳定的,但在高温、高湿度和阳光照射下会发生分解。
此外,NMP也对某些物质具有腐蚀性和氧化性。
3.3 反应性NMP是一种中性溶剂,不易发生反应。
然而,在一些特殊条件下,如氧化剂和催化剂的存在下,NMP可能会参与一些反应,如氧化反应和格氏反应。
4. 应用领域4.1 聚合物溶剂NMP作为一种优良的溶剂,在聚合物行业中有广泛的应用。
它可以作为聚合物的溶剂、增溶剂和反应介质,用于聚合物的溶解、合成、聚合和修饰等工艺。
4.2 化学品生产NMP作为一种重要的中间体化学品,被广泛应用于有机合成反应中。
它可以作为缩合剂、萃取剂和催化剂的溶剂,参与酯化、酰化、胺化、醇化等反应,用于有机化学品的合成和提纯。
4.3 电子材料NMP在电子材料领域有着重要的应用。
它可以作为溶剂和增塑剂,用于电子材料的制备和加工过程。
例如,NMP可用于制备电子级多晶硅、聚酰亚胺薄膜和锂离子电池电解液等。
4.4 医药工业NMP在医药工业中也有一定的应用。
它可以作为一种溶剂、增溶剂和稳定剂,用于药物的合成、提纯和稳定。
此外,由于其良好的渗透性和吸湿性,NMP还被用作药物传递系统和外用药物的载体。
N甲基吡咯烷酮技术简介

N甲基吡咯烷酮技术简介N-甲基吡咯烷酮技术简介专题论述N-甲基吡咯烷酮合成技术分析摘要:N-甲基吡咯烷酮是一种性能优良的化工溶剂。
该文简要分析了N-甲基吡咯烷酮的国内外市场情况,对比分析了γ-丁内酯与单甲基胺、混合甲基胺无催化及催化合成技术,以及丁二醇脱氢制γ-丁内酯-γ-丁内酯胺化一体化制N-甲基吡咯烷酮技术,提出了N-甲基吡咯烷酮技术发展建议。
关键词:N-甲基吡咯烷酮γ-丁内酯1,4-丁二醇生产技术Analysis of production technology for N-methyl pyrrolidone (Yizheng Chemical Fibre Co., Ltd., SINOPEC,Yizheng Jiangsu 211900,China) Abstract: N-methyl pyrrolidone is a good chemical industrial solvent. This paper analyzed the domestic and foreign market of N-methyl pyrrolidone and its synthesis technology, which consists of methods prepared from gamma-butyrolactone and monomethyl amine with or without catalyst , or using mixing methyl amine instead of monomethyl amine. In addition, an integration process from 1,4-butanediol to produce gamma-butyrolactone and furthermore to produce N-methyl pyrrolidone has also been analyzed. In the end, a suggestion about development of N-methyl pyrrolidone project has also been proposed.Key words: N-methyl pyrrolidone;; 1,4-butanediol; synthesis N-甲基吡咯烷酮[1,2,3,4](NMP)是一种极性非质子传递溶剂,具有高沸点、强极性、低粘度、强溶解能力、无腐蚀、毒性小、化学及热稳定性好等优点,主要用于芳烃萃取,乙炔、烯烃、二烯烃的纯化分离,聚合物溶剂以及聚合反应溶剂等领域。
n-甲基吡咯烷酮纯度级别

n-甲基吡咯烷酮纯度级别
n-甲基吡咯烷酮是一种有机化合物,其纯度级别通常根据其含杂质的种类和浓度来划分。
常见的n-甲基吡咯烷酮纯度级别包括以下几个:
1. 工业级:工业级n-甲基吡咯烷酮纯度相对较低,通常含有一定量的杂质。
这种级别的产品主要用于一些较低要求的工业应用,如有机合成反应中的溶剂或试剂。
2. 技术级:技术级n-甲基吡咯烷酮纯度比工业级稍高,其中的杂质含量较低。
这种级别的产品适用于一些需要较高纯度的实验室研究或工艺应用。
3. 分析级:分析级n-甲基吡咯烷酮纯度相对较高,其杂质含量非常低。
它通常用于分析测试、色谱、质谱或其他需要高纯度试剂的实验室应用。
4. 超净级:超净级n-甲基吡咯烷酮纯度最高,其中的杂质含量非常之低,甚至可以达到部分无法检测的程度。
这种级别的产品在许多高精度实验室和特殊工艺中使用。
值得注意的是,不同供应商或企业可能会有不同的纯度级别划分方法,而一般来说,纯度级别越高,产品的价格也会相应提高。
为了满足不同应用需求,选择合适纯度级别的n-甲基吡咯烷酮非常重要。
NMP工艺技术方案

NMP工艺技术方案NMP(N-甲基吡咯烷酮)工艺技术方案一、工艺概述NMP是一种重要的有机溶剂,具有无色透明、良好的溶解性、低粘度、低毒性等特点,在化工、电子、医药等行业有着广泛的应用。
本文将针对NMP的生产进行技术方案设计。
二、原料准备1. N-甲基2-吡咯烷酮(M-Pyrrolidone,简称MPD):通过氨与丙酮进行缩合反应制得。
2. 氨:通过水煤气制备得到高纯度氨。
三、反应工艺1. MPD与氨缩合反应:将MPD与氨按1:1的比例加入反应釜中,通过加热反应并搅拌,使反应物充分混合。
反应温度为110°C,反应时间为4小时。
反应结束后,进行中性化处理。
四、分离工艺1. 中性化处理:将反应物在碱性条件下进行中性化处理,可采用NaOH溶液对反应物进行中和。
中和完成后,得到中性产物混合物。
2. 脱色处理:将中性产物混合物加入脱色塔中,通过吸附剂吸附杂质,使产物得到立即脱色。
脱色塔可采用活性炭或其他吸附剂,脱色时间根据产物颜色决定。
3. 蒸馏分离:将经过脱色处理的产物进行高温蒸馏分离,得到NMP产品。
蒸馏采用精馏柱,分离温度根据产物的沸点进行调整。
五、产品收集和储存1. NMP产品可通过冷凝器进行冷却后收集,然后进行包装和储存。
2. 储存要求:NMP产品应存放在阴凉、干燥、密封的储存罐中,避免阳光直射和高温环境。
六、工艺优点1. 反应温度低:由于反应温度较低,能有效避免副反应的发生。
2. 工艺流程简单:只需经过中性化处理、脱色处理和蒸馏分离三个步骤即可得到高纯度的NMP产品。
3. 高效产出:由于蒸馏分离采用精馏柱,可以有效提高产物的回收率。
七、技术经济分析1. 原料成本低:NMP的主要原料MPD和氨价格相对较低,能够保证生产成本的控制。
2. 工艺简单可行:所需设备和生产线较为简单,投资成本相对较低。
3. 市场需求大:NMP作为重要的有机溶剂,在化工、电子、医药等行业有着广泛的应用市场。
八、安全环保措施1. 工艺过程中需要注意安全防护措施,包括工作人员戴好防护眼镜、手套和口罩等,防止接触和吸入NMP溶液。
n-甲基吡咯烷酮在合成中的应用

n-甲基吡咯烷酮在合成中的应用
N-甲基吡咯烷酮(NMP)是一种具有极性的有机溶剂,由于
其一系列良好的物化性质和可溶解性能,被广泛应用于化工合成过程中。
以下是N-甲基吡咯烷酮在合成中常见的应用:
1. 反应溶剂:N-甲基吡咯烷酮可作为优良的反应溶剂,可用
于高温、低温、高压和催化反应等多种反应体系。
它可以有效地溶解多种有机和无机物质,提高反应的速率和选择性。
2. 化学合成:N-甲基吡咯烷酮常被用作化学合成中的中间体。
它可以用于合成聚合物、染料、药物、涂料、塑料等化合物。
3. 溶剂萃取:N-甲基吡咯烷酮可以用于溶剂萃取过程中,提
取特定物质。
例如,它可以用于石油提炼和分离、天然气处理和萃取、废物处理等。
4. 电池生产:N-甲基吡咯烷酮可以在锂离子电池的制造过程
中用作溶剂和电解质。
它具有良好的锂离子传导性能和稳定性,可提高电池的性能和循环寿命。
5. 纺织工业:N-甲基吡咯烷酮可以用作织物的染色剂和溶剂。
它在纤维染色和印花工艺中具有较高的溶解度和催化性能,能够提供均匀和饱满的颜色。
总的来说,N-甲基吡咯烷酮在化工合成中具有广泛的应用,可以提高反应效率、改善产品性能,并满足不同行业的需求。
n-甲基吡咯烷酮 锂电 用途

n-甲基吡咯烷酮锂电用途
N-甲基吡咯烷酮是一种有机溶剂,常用于电池制造中的锂离子电池。
它在锂电池中的主要用途包括以下几个方面:
1. 电解液添加剂:N-甲基吡咯烷酮可以作为锂离子电池电解液中的添加剂。
它具有优异的化学稳定性和低闪点,可以提高电解液的溶解性和离子传递效率。
2. 电极材料制备:N-甲基吡咯烷酮可用于制备锂离子电池的正负极材料。
它可以作为溶剂将活性材料与导电剂、粘结剂等混合,并形成均匀的电极浆料。
3. 锂离子电池制造工艺:N-甲基吡咯烷酮可用作锂离子电池制造过程中的溶剂,如浸渍电解液、电池装配过程中清洗溶剂等。
总的来说,N-甲基吡咯烷酮在锂电池中的应用主要体现在电解液添加剂、电极材料制备和制造工艺等方面。
它可以提高电池的性能和稳定性,促进锂离子的传递和储存,从而提高电池的循环寿命和能量密度。
N-甲基吡咯烷酮(NMP)MSDS

N-甲基吡咯烷酮(NMP)MSDS导读:N-甲基吡咯烷酮化学品安全技术说明书1.标识(1)化学名称:N-甲基吡咯烷酮(2)分子式:C5H9NO(4)相对分子量:99.15(5)CAS号:872-50-4(6)危险性类别100%中文名:N-甲基吡咯烷酮,NMP,1-甲基-2-吡咯烷酮2.主要组成与性状(1)主要成分及其含量(2)外观与性状:透明液体有胺样气味3.健康危害(1)侵入途径(2)健康危害:N-甲基吡咯烷酮化学品安全技术说明书1. 标识(1)化学名称:N-甲基吡咯烷酮(2)分子式:C5H9NO(4)相对分子量:99.15(5)CAS号:872-50-4(6)危险性类别100%中文名: N-甲基吡咯烷酮,NMP,1-甲基-2-吡咯烷酮2. 主要组成与性状(1)主要成分及其含量(2)外观与性状:透明液体有胺样气味3. 健康危害(1)侵入途径(2)健康危害:可燃性液体和蒸气。
会对皮肤、眼睛及呼吸道产生刺激。
吞入、吸入或透皮吸收均有害。
皮肤:会导致搔痒、发红、脱皮及荨麻疹。
可快速透皮吸收,能将其它溶解的毒素运至体内。
眼睛:对眼睛有刺激性并会造成角膜灼伤。
吸入:会产生呼吸道刺激、头痛、恶心、头晕以及困倦摄入:会导致头晕、困倦、恶心、呕吐、痛性痉挛以及寒战。
4. 急救措施皮肤接触:在脱掉受污染的衣物和安全鞋的同时用水冲洗皮肤至少15 分钟。
如产生刺激或任何其它症状应就医治疗。
眼睛:立即用大量水冲洗眼睛至少15 分钟。
需就医治疗。
吸入:将受害者移至新鲜空气中。
如呼吸停止,应施予人工呼吸。
如果呼吸困难,由具资质的人员给予氧气治疗。
需立即就医治疗。
摄入:如仍有意识,应用水漱口。
患者可通过喝水或牛奶来稀释胃溶物。
除非有医疗人士指导,不可自行催吐。
应立即就医治疗。
给医生的建议:无特别建议。
针对症状加以治疗。
5. 爆炸特性与消防(1)燃烧性(2)闪点(3)爆炸极限(4)引燃温度(5)危险特性(6)灭火方法:二氧化碳、干化学制品或泡沫灭火。
NMP合成工艺技术
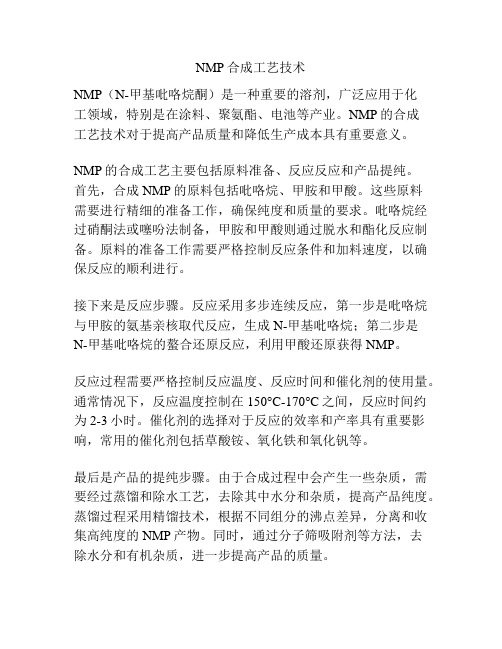
NMP合成工艺技术NMP(N-甲基吡咯烷酮)是一种重要的溶剂,广泛应用于化工领域,特别是在涂料、聚氨酯、电池等产业。
NMP的合成工艺技术对于提高产品质量和降低生产成本具有重要意义。
NMP的合成工艺主要包括原料准备、反应反应和产品提纯。
首先,合成NMP的原料包括吡咯烷、甲胺和甲酸。
这些原料需要进行精细的准备工作,确保纯度和质量的要求。
吡咯烷经过硝酮法或噻吩法制备,甲胺和甲酸则通过脱水和酯化反应制备。
原料的准备工作需要严格控制反应条件和加料速度,以确保反应的顺利进行。
接下来是反应步骤。
反应采用多步连续反应,第一步是吡咯烷与甲胺的氨基亲核取代反应,生成N-甲基吡咯烷;第二步是N-甲基吡咯烷的螯合还原反应,利用甲酸还原获得NMP。
反应过程需要严格控制反应温度、反应时间和催化剂的使用量。
通常情况下,反应温度控制在150°C-170°C之间,反应时间约为2-3小时。
催化剂的选择对于反应的效率和产率具有重要影响,常用的催化剂包括草酸铵、氧化铁和氧化钒等。
最后是产品的提纯步骤。
由于合成过程中会产生一些杂质,需要经过蒸馏和除水工艺,去除其中水分和杂质,提高产品纯度。
蒸馏过程采用精馏技术,根据不同组分的沸点差异,分离和收集高纯度的NMP产物。
同时,通过分子筛吸附剂等方法,去除水分和有机杂质,进一步提高产品的质量。
NMP合成工艺技术的改进主要集中在提高反应效率和产率、减少能耗和减少废物产生等方面。
例如,采用新型催化剂可以提高反应速率和选择性,减少催化剂的用量;改进反应条件和工艺参数,优化反应过程,从而提高产能和产品质量;引入新型分离技术,提高产品的纯度和提纯效率。
总之,NMP合成工艺技术的不断发展和改进,对于提高产品质量、降低生产成本以及改善环境污染等方面有着重要的意义。
随着科技的进步和工艺技术的不断创新,相信NMP合成工艺技术将会继续得到改进和完善,为化工产业的发展做出更大的贡献。
n-甲基吡咯烷酮 紫外吸收波长

n-甲基吡咯烷酮紫外吸收波长n-甲基吡咯烷酮是一种常用的光敏材料,广泛应用于光致变色、光致断裂、光致聚合等领域。
学习了解n-甲基吡咯烷酮的紫外吸收波长,可以为在应用中的选择提供参考。
n-甲基吡咯烷酮的分子式为C6H7NO,其主要的特性表现在其吸收光谱上。
它的分子量比较轻,因此吸收波长在紫外光区域。
在紫外光区域,n-甲基吡咯烷酮表现出强烈的吸收现象,其中最大的吸收波长位于287nm左右。
n-甲基吡咯烷酮在紫外光区域的吸收现象是由于它的电子能级分布的影响。
在n-甲基吡咯烷酮分子的分子轨道中,最外层的分子轨道是以非平面排列的形式存在的。
这种非平面排列的形式使电子的分布不均匀,其中部分的电子更加密集。
当n-甲基吡咯烷酮分子受到光的刺激时,这些密集的电子会产生电子激发,进而导致分子的能量水平上升。
在这个过程中,分子中原来处于基态的电子会移到高能级,吸收了特定波长的光线。
而这个特定波长的光线正是n-甲基吡咯烷酮吸收的最大波长,对应着287nm左右的吸收峰。
此外,还有一些n-甲基吡咯烷酮混合材料,在不同波长下的吸收峰会发生一些变化。
例如n-甲基吡咯烷酮和银离子混合材料,在387 nm处显示出一个特殊的吸收峰。
这个吸收峰是由于n-甲基吡咯烷酮的电子能级分布,和银离子的作用相互影响的结果。
总的来说,n-甲基吡咯烷酮在应用中广泛的使用,比如用于光盘记录材料、漆料、染料、薄膜、荧光材料等。
在这些应用中,针对不同的应用场景,需要考虑到n-甲基吡咯烷酮的吸收峰,选择合适的光源波长,从而达到最优效果。
对于科学研究人员来说,了解n-甲基吡咯烷酮在不同波长下的吸收峰,可以更好的理解其分子结构和性质,在相关领域的研究和应用中提供有价值的支持。
叔丁醇钾,nmp关环原理-概述说明以及解释

叔丁醇钾,nmp关环原理-概述说明以及解释1.引言1.1 概述叔丁醇钾和NMP是有机合成中常用的关键试剂和溶剂,它们在有机合成反应中发挥重要作用。
叔丁醇钾是一种有机金属化合物,可以作为强碱催化剂,广泛应用于醇类、醚类和羧酸类化合物的关环反应中。
NMP,即N-甲基吡咯烷酮,是一种无色透明的液体,具有良好的溶解性和稳定性。
它在有机合成中可作为溶剂、催化剂和中间体使用。
NMP 的应用范围十分广泛,包括有机合成反应、聚合物制备等领域。
本文旨在探讨叔丁醇钾和NMP在关环反应中的协同效应及其关环原理。
通过介绍叔丁醇钾和NMP的基本概念和性质,分析它们在关环反应中的应用领域和优势。
同时,阐述NMP在关环反应中的作用机理以及叔丁醇钾和NMP共同作用的协同效应。
最后,讨论叔丁醇钾与NMP关环原理的局限性和展望,为进一步研究和应用提供参考。
通过深入研究叔丁醇钾和NMP在关环反应中的作用机理,我们可以更好地理解它们的协同效应,并有助于优化反应条件,提高反应的效率和选择性。
同时,对叔丁醇钾与NMP关环原理的探索也将为相关领域的研究提供新的思路和方向。
1.2文章结构文章结构部分的内容可以描述整篇文章的组织架构和主要内容安排。
具体而言,可以包括以下方面的内容:文章结构部分:本文共分为3个主要部分:引言、正文和结论。
引言部分首先概述了叔丁醇钾和NMP的背景和意义。
接着,对文章结构和目的进行了简要阐述。
正文部分分为两个子部分,分别介绍了叔丁醇钾和NMP的相关知识。
叔丁醇钾部分包括对其基本性质、特点和应用领域的介绍。
然后,对叔丁醇钾的合成方法进行了探讨。
NMP部分首先介绍了其基本概念和性质。
然后,列举了NMP的主要应用领域。
最后,重点讨论了NMP在关环反应中的作用和机理。
结论部分对叔丁醇钾和NMP在关环反应中的协同效应进行了总结和分析。
然后,评述了叔丁醇钾和NMP的优势和局限性。
最后,展望了叔丁醇钾和NMP关环原理的未来发展方向。
n-甲基吡咯烷酮分子式
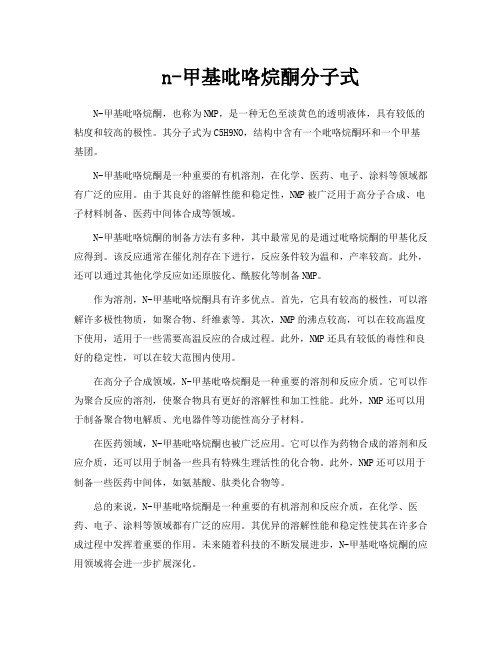
n-甲基吡咯烷酮分子式N-甲基吡咯烷酮,也称为NMP,是一种无色至淡黄色的透明液体,具有较低的粘度和较高的极性。
其分子式为C5H9NO,结构中含有一个吡咯烷酮环和一个甲基基团。
N-甲基吡咯烷酮是一种重要的有机溶剂,在化学、医药、电子、涂料等领域都有广泛的应用。
由于其良好的溶解性能和稳定性,NMP被广泛用于高分子合成、电子材料制备、医药中间体合成等领域。
N-甲基吡咯烷酮的制备方法有多种,其中最常见的是通过吡咯烷酮的甲基化反应得到。
该反应通常在催化剂存在下进行,反应条件较为温和,产率较高。
此外,还可以通过其他化学反应如还原胺化、酰胺化等制备NMP。
作为溶剂,N-甲基吡咯烷酮具有许多优点。
首先,它具有较高的极性,可以溶解许多极性物质,如聚合物、纤维素等。
其次,NMP的沸点较高,可以在较高温度下使用,适用于一些需要高温反应的合成过程。
此外,NMP还具有较低的毒性和良好的稳定性,可以在较大范围内使用。
在高分子合成领域,N-甲基吡咯烷酮是一种重要的溶剂和反应介质。
它可以作为聚合反应的溶剂,使聚合物具有更好的溶解性和加工性能。
此外,NMP还可以用于制备聚合物电解质、光电器件等功能性高分子材料。
在医药领域,N-甲基吡咯烷酮也被广泛应用。
它可以作为药物合成的溶剂和反应介质,还可以用于制备一些具有特殊生理活性的化合物。
此外,NMP还可以用于制备一些医药中间体,如氨基酸、肽类化合物等。
总的来说,N-甲基吡咯烷酮是一种重要的有机溶剂和反应介质,在化学、医药、电子、涂料等领域都有广泛的应用。
其优异的溶解性能和稳定性使其在许多合成过程中发挥着重要的作用。
未来随着科技的不断发展进步,N-甲基吡咯烷酮的应用领域将会进一步扩展深化。
n-甲基吡咯烷酮 酰化反应催化剂

n-甲基吡咯烷酮酰化反应催化剂
n-甲基吡咯烷酮(NMP)是一种常用的溶剂,可用作许多有机合
成反应的溶剂。
它在酰化反应中可以作为反应溶剂,但并不是催化剂。
酰化反应通常需要酸性或碱性条件下的催化剂来促进酯的形成。
常见的酰化反应催化剂包括Lewis酸(如氯化锌、三氯化铝)、酸
性离子交换树脂、酸性氧化剂(如对甲苯磺酸)、或碱性催化剂
(如氢氧化钠、碳酸钾)。
这些催化剂可以促进羧酸和醇之间的酯
化反应,生成酯化合物。
此外,NMP本身也可以参与一些反应,如亲核取代反应等,但
在酰化反应中通常不被用作催化剂。
因此,在进行酰化反应时,需
要选择适当的催化剂以促进所需的化学转化。
希望这个回答能够帮
助你理解关于n-甲基吡咯烷酮和酰化反应催化剂的相关知识。
n-甲基吡咯烷酮 助溶机理

n-甲基吡咯烷酮助溶机理
n-甲基吡咯烷酮(NMP,N-Methyl-2-pyrrolidone)是一种极性溶剂,在化学和工业领域中广泛应用。
它具有良好的溶解性和溶解能力,可以溶解多种有机物和无机物。
NMP的助溶机理主要包括以下几个方面:
1.极性溶剂性质:NMP是一种极性溶剂,具有较高的介电常
数和极性度。
这使它与许多极性或离子性化合物发生相互作用。
NMP分子中的氮原子带有较高的电负性,可以与带有正电荷的离子或极性分子中的部分负电荷进行静电相互作用。
2.氢键形成:NMP分子中的带负电荷的氮原子可以与其他分
子中的带正电荷的氢原子形成氢键。
氢键的形成可以促进NMP与其他物质之间的相互作用和溶解。
3.亲油性和亲水性:NMP既有一定的亲油性,又有较强的亲
水性,这使它能够与具有不同亲性的物质进行相互作用。
对于某些特定的化合物,NMP能够在油相和水相之间形成胶束结构,提供了较强的溶解能力。
总的来说,NMP作为助溶剂,其极性特性和分子结构使其能够与多种化合物发生相互作用,破坏或降低溶剂和溶质之间的相互作用力,从而促进溶解和溶解度的增加。
需要注意的是,对于不同的物质,NMP的溶解能力和效果可能有所不同。
因此,在实际应用中,需要根据溶质的特性和其他
相关因素,合理选择和使用NMP作为助溶剂。
同时,还应注意确保对NMP的使用符合相关的安全和环境要求。
- 1、下载文档前请自行甄别文档内容的完整性,平台不提供额外的编辑、内容补充、找答案等附加服务。
- 2、"仅部分预览"的文档,不可在线预览部分如存在完整性等问题,可反馈申请退款(可完整预览的文档不适用该条件!)。
- 3、如文档侵犯您的权益,请联系客服反馈,我们会尽快为您处理(人工客服工作时间:9:00-18:30)。
专题论述N-甲基吡咯烷酮合成技术分析摘要:N-甲基吡咯烷酮是一种性能优良的化工溶剂。
该文简要分析了N-甲基吡咯烷酮的国内外市场情况,对比分析了γ-丁内酯与单甲基胺、混合甲基胺无催化及催化合成技术,以及丁二醇脱氢制γ-丁内酯-γ-丁内酯胺化一体化制N-甲基吡咯烷酮技术,提出了N-甲基吡咯烷酮技术发展建议。
关键词:N-甲基吡咯烷酮γ-丁内酯 1,4-丁二醇生产技术Analysis of production technology for N-methyl pyrrolidone(Yizheng Chemical Fibre Co., Ltd., SINOPEC,Yizheng Jiangsu 211900,China)Abstract:N-methyl pyrrolidone is a good chemical industrial solvent. This paper analyzed the domestic and foreign market of N-methyl pyrrolidone and its synthesis technology, which consists of methods prepared from gamma-butyrolactone and monomethyl amine with or without catalyst , or using mixing methyl amine instead of monomethyl amine. In addition, an integration process from 1,4-butanediol to produce gamma-butyrolactone and furthermore to produce N-methyl pyrrolidone has also been analyzed. In the end, a suggestion about development of N-methyl pyrrolidone project has also been proposed.Key words: N-methyl pyrrolidone;; 1,4-butanediol; synthesisN-甲基吡咯烷酮[1,2,3,4](NMP)是一种极性非质子传递溶剂,具有高沸点、强极性、低粘度、强溶解能力、无腐蚀、毒性小、化学及热稳定性好等优点,主要用于芳烃萃取,乙炔、烯烃、二烯烃的纯化分离,聚合物溶剂以及聚合反应溶剂等领域。
随着国内聚酰胺、聚酰亚胺、聚苯硫醚等高强工程塑料及高强纤维的飞速发展,对N-甲基吡咯烷酮的质量及需求量都提出了更高的要求。
目前N-甲基吡咯烷酮工业化生产工艺主要有3种[1-4]:a)γ-丁内酯(GBL)与单甲基胺(MMA)反应合成N-甲基吡咯烷酮;b)γ-丁内酯和混合胺反应合成N-甲基吡咯烷酮;c)1,4-丁二醇脱氢-胺化制备N-甲基吡咯烷酮。
国外N-甲基吡咯烷酮的生产能力主要集中在少数几个大公司手中,国内有10多家企业从事N-甲基吡咯烷酮的生产,但装置规模相对较小,原料来源途径多,产品质量稳定性差,生产技术有待改进。
目前国内表观N-甲基吡咯烷酮的年产量为53 kt/a,且以每年6%~8%的速度增长,NMP的前景比较广阔。
笔者对国内外N-甲基吡咯烷酮的生产情况及生产技术进行了简要分析,提出了加快发展N-甲基吡咯烷酮建议。
1 国内外N-甲基吡咯烷酮生产情况N-甲基吡咯烷酮是一个大宗化学品,2007年以前世界总产能已达到130 kt,美国GAF公司、德国BASF公司、日本三菱化成公司以及北海道有机化工公司是主要的生产商,以年均约8%的速度在增长。
国内N-甲基吡咯烷酮生产厂家相对较多,但产能相对较小,主要生产厂家有:南京金龙化工有限公司(4 kt/a)、浙江联盛化学工业有限公司(10 kt/a)、河南濮阳市迈奇科技有限公司(4 kt/a)、泰州延龄精细化工有限责任公司(9 kt),此外还有四川天华富邦有限责任公司湖南省南岭化工有限责任公司、山东庆云长信化学科技有限公司、胜利油田东胜星润化工有限责任公司、焦作中维化工有限公司、南京瑞泽精细化工有限公司等。
2 N-甲基吡咯烷酮的生产技术N-甲基吡咯烷酮的生产技术主要有3种:γ-丁内酯与单甲基胺无催化合成工艺,γ-丁内酯与混合甲基胺连续无催化合成工艺、γ-丁内酯与单甲基胺催化合成工艺及1,4-丁二醇催化脱氢-胺化工艺。
2.1 γ-丁内酯与单甲基胺无催化合成N-甲基吡咯烷酮γ-丁内酯与单甲基胺无催化反应合成N-甲基吡咯烷酮是最经典的合成方法。
早在1936年,Spath和Lunder就介绍了在间歇反应器中、甲基胺远过量的情况下,合成得到转化率大于90%的NMP[5]。
1946年,Elvain和Vozza在美国化学协会会志中介绍了在间歇反应器中,温度为280 ℃,甲基胺过量1倍的情况下,NMP产率大于90%。
进入20世纪90年代,潘托希米股份有限公司(比利时),开发了γ-丁内酯与单甲基胺反应连续无催化合成N-甲基吡咯烷酮的工艺[5],如图1所示,该工艺具有以下两个特征:a)低的投资成本、产品NMP的高选择性以及原料MMA与GBL的高转化率;b)以连续的方式进行,低的MMA和GBL原料比,无需加入水,所得NMP纯度高(>99.5%),水含量低于0.05%。
宋国全[6]等人研究了生产工艺条件对原料转化率及产品选择性的影响,得到了优化的工艺生产条件。
14图 1 γ-丁内酯与单甲基胺连续无催化合成NMP流程示意 [5]1.胺化反应器;2.环化反应器;3.后续环化反应器;4.闪蒸罐;5.脱胺塔;6.脱轻组分塔;7.脱重组分塔;8.混合器;9.1#加热器;10.2#加热器;11.减压阀;12.甲基胺;13.GBL;14.水;15.轻质副产物;16.NMP;17.重质副产物图1中反应器类型为管型绝热式反应器,压力范围为30~90个大气压。
总的反应过程分成加成和环化两步反应(方程1),工业生产采用三步方法实现,第1步加成反应形成N-甲基-羟基丁酰胺(NMH),即新鲜的MMA原料和循环的MMA一起与GBL以摩尔比1.05~1.4:1的配比在混合器8中混合,混合物料在反应器1内停留5~30 min,反应器温度控制在150~220 ℃范围内;第2步NMH的环化:反应物流经预热器9加热至250 ℃后,在反应器2内停留1~3 h,反应温度控制在220~270 ℃内,发生分子内脱水反应;第3步NMH完全转化至NMP,反应物流经预热器10加热至280 ℃后在反应器3内停留0.5~2 h,反应温度250~310 ℃,获得NMP产品混合物。
该混合物流在闪蒸罐4中,0.9MPa下闪蒸,闪蒸得到的气、液两相进入到脱胺塔5中分离,塔顶分离得到的MMA循环使用,塔底液相在脱轻组分塔6及脱重组分塔7中进一步分离,分离出水,轻、重质副产物,获得高纯度NMP。
O CNH2CH3HO(CH2)3CONHCH3NCCH3+H2O(1)2.2γ-丁内酯与混合甲基胺连续无催化合成工艺氨和甲醇在胺化催化剂作用下,反应生成单甲基胺、二甲基胺(DMA)和三甲基胺(TMA)混合物,甲基胺的分离需采用到4~5个分馏塔,致使投资和运行成本增加。
21世纪初,德国BASF公司开发了利用混合胺为原料替代MMA制备N-甲基吡咯烷酮新工艺[7],该工艺具有投资低、原料价格低以及公用工程消耗低等优点,获得的NMP纯度大于99.5%,水含量低于0.05%。
BASF工艺(图2)与潘托希米股份有限公司甲基胺工艺类似,同样包含3个串联的反应工序。
原料混合甲基胺、GBL和水混合后,进入到反应阶段1,其中胺与GBL的摩尔比控制在1.05~1.5:1,温度控制在150~220 ℃,停留时间10~40 min;反应阶段1的产物经加热升温到250 ℃左右,进入反应阶段2,停留时间2 h左右,进行NMH环化反应;环化产品经加热到280 ℃进入反应阶段3,停留时间1.5 h,3个反应器的压力均控制在40~100大气压范围内。
后续的分离工序与甲基胺工艺相同。
由于该工艺采用的是混合甲基胺与γ-丁内酯加成、环化脱水工艺,即除GBL与MMA反应生成NMP和水之外,还存在GBL与DMA或TMA反应生成NMP以及相应摩尔甲醇的反应。
因此,反应产物中除含有NMP外,还含有未转化的胺、水、甲醇和轻、重副产物,塔5分离出反应产物中甲醇和未转化的胺,循环回胺化反应器,在反应器中氨和甲醇反应转化成混合甲基胺。
该工艺的创新之一是采用低成本的甲基胺装置,其装置如图3所示。
循环回来的胺和甲醇物流与补充的胺、补充的甲醇以及循环的富胺物流混合,经预热器1预热后,在胺化反应器2中反应。
反应流出物经预热器换热后,在冷却器3中冷却,冷凝物流入分离器中分离一氧化碳和氢气,冷凝液经脱胺塔分离并循环多余的氨后,再经分离塔塔顶分离出混合甲基胺物流,并通过管线送至NMP合成装置。
16图2 以γ-丁内酯和混合甲基胺作原料连续无催化合成NMP流程示意 [7]1.胺化反应器;2.环化反应器;3.后续环化反应器;4.闪蒸罐;5.脱胺塔;6.脱轻组分塔;7.脱重组分塔;8.混合器;9. 1#加热器;10.2#加热器;11.减压阀;12.原料水;13.混合胺;14.GBL;15.甲醇与甲基胺;16.水;17.轻质副产物;18.NMP;19.重质副产物图 3 生产混合胺的胺化反应器流程示意[7]1.换热器;2.胺化反应器;3.冷却器;4.脱一氧化碳塔;5.脱氨塔;6.产品分离塔;7.氨;8.甲醇; 9.胺; 10.一氧化碳与氢气; 11.甲基胺; 12.水2.3 γ-丁内酯和甲基胺连续催化合成N-甲基吡咯烷酮传统的由γ-丁内酯无催化转化合成N-甲基吡咯烷酮的方法往往需要高的温度、压力,对设备的要求高,能耗大,而采用催化剂则可以降低反应条件,节约能源。
韩国SK公司探索研究了分子筛催化合成工艺[8],缓和反应条件。
濮阳迈奇科技有限公司[9]引入新型ZSM分子筛-铈氧化物复合催化剂,稀土铈为主要活性催化组分,使γ-丁内酯反应极为充分,转化率、选择性均高。
该工艺采用纯度为99.0%以上的γ-丁内酯和40%的单甲胺溶液作原料,γ-丁内酯与甲胺的摩尔比为1:1.0~1.4,新型ZSM分子筛复合稀土铈催化剂的加入量为单甲胺溶液的0.01%~0.5%,其中稀土铈的含量为1%~10%,将γ-丁内酯与甲胺溶液按摩尔配比用高压计量泵连续打入套管式反应器中进行反应,温度为180~250 ℃,压力为4.0~6.0 MPa,停留时间为0.5~2.5 h,该反应的压力先由压力控制系统控制压力平衡罐的液位来稳定4.0~6.0 MPa的压力,在液位达到总液位的60%~70%后,再打入氮气退液位至总液位3%~10%液面,保持整个过程压力始终稳定在4.0~6.0 MPa,γ-丁内酯的转化率99.9%以上,获得的NMP的选择性达99%以上。