氨分解工艺流程
氨分解操作规程2
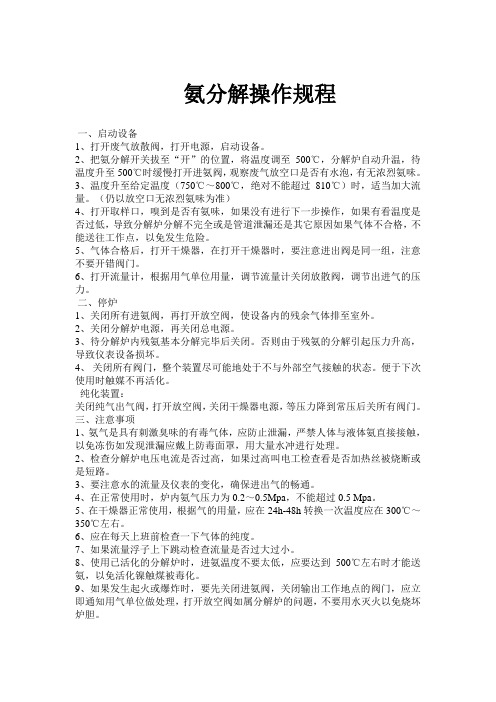
氨分解操作规程一、启动设备1、打开废气放散阀,打开电源,启动设备。
2、把氨分解开关拔至“开”的位置,将温度调至500℃,分解炉自动升温,待温度升至500℃时缓慢打开进氨阀,观察废气放空口是否有水泡,有无浓烈氨味。
3、温度升至给定温度(750℃~800℃,绝对不能超过810℃)时,适当加大流量。
(仍以放空口无浓烈氨味为准)4、打开取样口,嗅到是否有氨味,如果没有进行下一步操作,如果有看温度是否过低,导致分解炉分解不完全或是管道泄漏还是其它原因如果气体不合格,不能送往工作点,以免发生危险。
5、气体合格后,打开干燥器,在打开干燥器时,要注意进出阀是同一组,注意不要开错阀门。
6、打开流量计,根据用气单位用量,调节流量计关闭放散阀,调节出进气的压力。
二、停炉1、关闭所有进氨阀,再打开放空阀,使设备内的残余气体排至室外。
2、关闭分解炉电源,再关闭总电源。
3、待分解炉内残氨基本分解完毕后关闭。
否则由于残氨的分解引起压力升高,导致仪表设备损坏。
4、关闭所有阀门,整个装置尽可能地处于不与外部空气接触的状态。
便于下次使用时触媒不再活化。
纯化装置:关闭纯气出气阀,打开放空阀,关闭干燥器电源,等压力降到常压后关所有阀门。
三、注意事项1、氨气是具有刺激臭味的有毒气体,应防止泄漏,严禁人体与液体氨直接接触,以免冻伤如发现泄漏应戴上防毒面罩,用大量水冲进行处理。
2、检查分解炉电压电流是否过高,如果过高叫电工检查看是否加热丝被烧断或是短路。
3、要注意水的流量及仪表的变化,确保进出气的畅通。
4、在正常使用时,炉内氨气压力为0.2~0.5Mpa,不能超过0.5 Mpa。
5、在干燥器正常使用,根据气的用量,应在24h-48h转换一次温度应在300℃~350℃左右。
6、应在每天上班前检查一下气体的纯度。
7、如果流量浮子上下跳动检查流量是否过大过小。
8、使用已活化的分解炉时,进氨温度不要太低,应要达到500℃左右时才能送氨,以免活化镍触煤被毒化。
氨分解的基本操作

氨分解的基本操作1开机前的准备工作:1、准备200kg/瓶的液氨2瓶。
2、提供能够承受电压交流380V,50Hz,功率40Kw电源,机壳接地。
3、检查电气元件接头处有无松动,例如:电流表、温控仪、电炉、热电偶、交流接触器、熔断器等所有电气元件。
2原始开机1、打开废气放空阀,接通电源,此时总电源指示灯亮。
2、将氨分解开关拨向“开”位置,设定温控仪温度200℃(升温曲线见下表、温控仪设定见温控仪说明书)进行镍触媒活化,分解炉内装的镍触媒在出厂时已经还原,但因设备在运输,库存期间总有水分、氧气等介入,镍触媒活性略有下降,因此原始开机时还要进行镍触媒的活化。
镍媒的活化将关系到镍触媒的分解效果及寿命,请严格按照上表操作!样气检验:可用化学分析或经验方法,其中经验方法是从放空口嗅不到明显的氨臭味或观察分解气燃烧时,火焰呈橙色,若符合上述现象则分解气合格。
3、干燥器内5A分子筛活化再生:氨分解开车正常后,取小部分合格的氢、氮混合气送入干燥器Ⅱ,吸附干燥其中的水分、残氨(处低负荷工作),利用这部分气体来加热冲洗干燥器Ⅰ中的5A分子筛,此时干燥器升温选择开关拨向Ⅰ组,这部分气体经“再生Ⅰ出”阀放空。
具体操作如下:打开阀“工作Ⅱ进”、“工作Ⅱ出”、“再生Ⅰ进”、“再生Ⅰ出”,并调节再生流量处于3m³/h。
将干燥器升温选择开关拨向Ⅰ组,其升温过程如下。
4、干燥器Ⅰ活化(再生)结束后,所有阀门不变,只需关掉Ⅰ组的加热开关,就可继续用干燥器Ⅱ纯化的小气量吹冷干燥器Ⅰ至室温(也可让Ⅰ组干燥器自然冷却至室温):然后关闭“工作Ⅱ进”、“工作Ⅱ出”、“再生Ⅰ进”、“再生Ⅰ出”,Ⅰ组干燥器即可正常工作。
5、Ⅱ组干燥器再生活化步骤与Ⅰ组相同,但阀门相应变为“工作Ⅰ进”、“工作Ⅰ出”、“再生Ⅱ进”、“再生Ⅱ出”。
3正常开机:氨分解部分:1、打开废气放空阀,接通电源,此时总电源指示灯亮。
2、将氨分解开关拨向“开”位置,设定温度仪温度200℃,分解炉自动升温,待温度升至200℃时,保温1小时,再设定温控仪温度400℃,分解炉自动升温,待温度升至400℃时,保温1小时,再设定温控仪温度600℃,分解炉自动升温,待温度升至600℃时,保温1小时,再设定温控仪温度800℃,分解炉自动升温,待温度升至800℃时,保温半小时,打开进氨阀,调节减压阀压力,略开打压力阀(减压阀逆时针减下,顺时针增大),观察废气放空口,有气流出,将该放空口的放空管放入水中,注意水泡产生现象,此时,温控仪的温度会慢慢下降,为正常现象。
洗氨、蒸氨、氨分解工段安全规程(三篇)

洗氨、蒸氨、氨分解工段安全规程洗氨、蒸氨、氨分解是化工生产过程中常用的工段,也是安全风险较大的工段。
为了确保生产过程中的安全,制定并执行一套严格的安全规程是必要的。
下面是一份关于洗氨、蒸氨、氨分解工段的安全规程,供参考。
一、工段概述洗氨、蒸氨、氨分解工段是指将氨气从原料中分离出来的工序,主要由洗氨、蒸氨和氨分解这三个环节组成。
二、安全守则1. 严格遵守操作规程,不得随意更改操作步骤。
2. 操作人员必须熟悉工艺流程和设备原理,并熟悉仪表设备的使用方法。
3. 使用安全阀、爆破片等安全装置时,必须保持其良好运行状态。
4. 现场工作人员必须穿戴符合规定的劳动防护用品,包括防护眼镜、安全帽、耐酸碱手套等。
5. 禁止擅自操作、调试设备,如需调试必须由专业技术人员进行。
6. 严禁携带易燃易爆物品进入作业现场。
7. 不得在作业现场吸烟、使用明火或进行其他火源操作。
三、洗氨操作规程1. 确保洗氨塔内的洗液温度和氨气温度均处于安全范围内。
2. 定期检查洗氨塔的进气阀、出气阀和冷凝器的工作状态,确保其正常运行。
3. 在清洗洗氨塔之前,必须停止进气,关闭进气阀,并确保洗氨塔内无残余气体。
4. 洗氨塔内液位上升过快时,应减少进气量并加强冷却,以防止液体波动和氨气泄露。
四、蒸氨操作规程1. 确保蒸氨设备的工作温度、压力和流量处于正常范围内。
2. 定期检查蒸氨设备的安全阀、压力表和液位计的工作状态,确保其正常运行。
3. 在蒸氨过程中,严禁打开蒸氨设备的进气阀,以防止氨气泄露。
4. 蒸氨操作结束后,必须停止加热,关闭进气阀,并排空蒸氨管路中的气体,确保设备内无残余气体。
五、氨分解操作规程1. 在氨分解过程中,必须确保分解塔内的温度、压力和液位处于正常范围内。
2. 定期检查氨分解设备的安全阀、压力表和液位计的工作状态,确保其正常运行。
3. 氨分解过程中,严禁随意调整分解塔的温度和压力,以防止设备发生事故。
4. 分解结束后,必须关闭进气阀,排空分解塔内残余气体,并做好对设备的检查和维护。
硫酸氨分解

硫酸氨是一种重要的化工原料,在许多工业应用中都发挥着重要作用。
然而,硫酸氨在分解过程中可能会产生一些有害物质,对环境和人体健康造成一定的影响。
因此,在分解硫酸氨时需要采取适当的措施,确保安全和环保。
硫酸氨分解的过程可以大致分为以下几个步骤:1. 溶解:将硫酸氨粉末加入水中,形成硫酸氨溶液。
这个过程需要控制溶液的浓度和温度,以确保硫酸氨能够充分溶解。
2. 氧化:在适当的温度和压力下,将溶解后的硫酸氨溶液进行氧化反应,生成硫酸和一氧化氮气体。
这个过程需要控制反应条件,以确保生成的硫酸和一氧化氮气体能够充分分离。
3. 还原:将生成的硫酸和一氧化氮气体进行还原反应,生成二氧化氮气体和硫酸钠固体。
这个过程需要控制反应条件和还原剂的用量,以确保二氧化氮气体和硫酸钠固体能够充分生成。
4. 排放:将生成的二氧化氮气体进行排放处理,以避免对环境和人体健康造成影响。
在分解硫酸氨的过程中,需要注意以下几点:1. 环保:在分解过程中会产生一些有害物质,如二氧化氮气体等,需要采取适当的措施进行排放和处理,以避免对环境和人体健康造成影响。
2. 安全:在分解过程中需要控制反应条件和还原剂的用量,以避免发生危险事故。
同时,需要确保操作人员的安全和健康,如穿戴适当的防护装备等。
3. 经济性:在分解硫酸氨时需要考虑经济因素,如选择合适的工艺路线、优化反应条件和降低成本等,以确保生产的经济效益。
总的来说,硫酸氨分解是一个复杂的过程,需要综合考虑环保、安全和经济等因素。
在实际操作中,需要根据具体情况选择合适的工艺路线和设备,并严格控制反应条件和操作流程,以确保安全、环保和经济地生产硫酸氨。
此外,还需要注意一些潜在的风险和挑战,如设备故障、操作失误、原料质量不稳定等。
这些因素都可能对硫酸氨分解过程产生不利影响,因此需要加强设备维护和管理、提高操作技能和意识,以及确保原料的质量稳定。
总之,硫酸氨分解是一个涉及多个环节的过程,需要全面考虑各种因素,并采取适当的措施确保安全、环保和经济地生产硫酸氨。
氨分解安全操作规程

氨分解安全操作规程背景介绍氨分解是化工生产中的一项重要工艺。
它可以将氨气分解成氢气和氮气等组分,常用于合成氢气、制取氮气等工艺上。
不过,氨气的本身是有毒性的,在氨分解的操作过程中需要特别注意安全,以避免可能的意外事故。
氨分解操作要点氨分解的操作要点包括操作环境、操作人员、设备和方案等。
操作环境氨分解需要在通风、阳光充足、温度适宜等条件下进行。
操作空间要充分考虑通风状况,避免氨气积聚造成爆炸、中毒危险。
同时,氨分解过程中会产生大量热量,需要合理配置散热管道和配套设备,以保障操作安全。
操作人员氨分解需要专业化的操作人员。
操作人员应当具备化学工艺相关专业知识,熟悉氨气的危险性和防范措施。
同时,操作人员应当穿着防护服及防护眼镜等,避免氨气对身体的刺激和伤害。
设备氨分解设备应当具备高原、反应器、泵阀、计量仪表等各项设施,且设备应当定期进行检测、维修和清洗工作。
设置专用氯离子监测仪等设备,实现气体检测报警,在操作过程中对危险情况迅速进行反应和处理。
方案流程针对氨分解的情况,应当制定相应的方案流程。
方案流程中包括实验操作指南、应急预案、工作量及物料清单等。
在实际操作过程中,严格按照方案流程操作,并随时关注各项监控设备信息,以及注意气体的状态和流动,掌握实验过程中的情况。
氨分解实验安全操作步骤1.检查操作环境,确保通风、照明、加热、冷却、液位、液压等设施设备均符合操作指南。
2.阅读并熟悉实验操作指南和应急预案,戴上防护套装。
3.校正、调试并校验仪表仪器,以及避免、解决安全隐患。
4.将氨气放置在安全位置,根据方案规定逐步加热,同时注意加热和冷却系统的维护、调整、设定,以及掌握气体流动情况。
5.实验中注意监控判断气体、液体的成分和流动,尽可能做到实时监测和处理安全隐患。
6.实验结束后,关闭所有设备,戴上防护套装,检查并清洗设备和其他操作用品,并尽快放置气体。
注意事项1.氨气具有腐蚀性和毒性等危险性,应当根据操作环境、条件等合理配置和调整。
氨分解安全操作规程
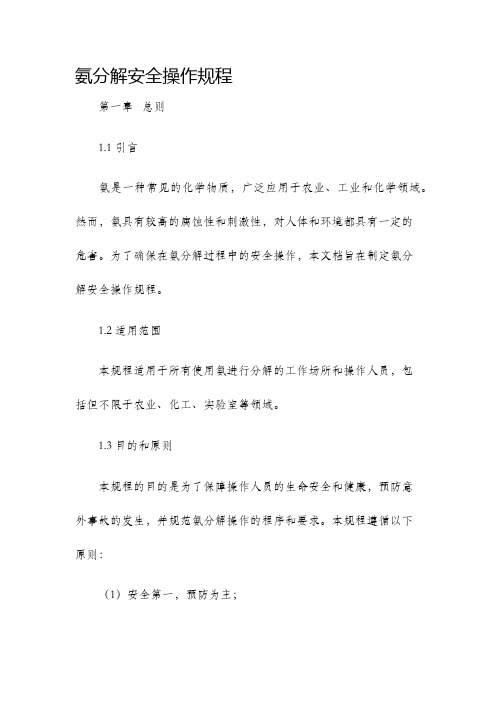
氨分解安全操作规程第一章总则1.1 引言氨是一种常见的化学物质,广泛应用于农业、工业和化学领域。
然而,氨具有较高的腐蚀性和刺激性,对人体和环境都具有一定的危害。
为了确保在氨分解过程中的安全操作,本文档旨在制定氨分解安全操作规程。
1.2 适用范围本规程适用于所有使用氨进行分解的工作场所和操作人员,包括但不限于农业、化工、实验室等领域。
1.3 目的和原则本规程的目的是为了保障操作人员的生命安全和健康,预防意外事故的发生,并规范氨分解操作的程序和要求。
本规程遵循以下原则:(1)安全第一,预防为主;(2)严格按照操作规程进行操作;(3)合理使用个人防护设备;(4)确保操作人员有必要的技能和知识。
第二章前期准备2.1 前期风险评估在进行氨分解操作之前,必须进行全面的风险评估。
评估应包括分解设备的状态、潜在的安全隐患和操作环境条件等方面的分析,以确定应采取的控制措施。
2.2 设备检查和维护在操作前,对氨分解设备进行必要的检查和维护,确保设备处于良好的工作状态。
任何存在安全隐患的设备都应当暂停使用,并进行修理或更换。
2.3 工作区域准备在工作区域内设置明显的警示标识,并确保工作区域的通风条件良好。
清除工作区域内的杂物,确保工作区域干净整洁。
2.4 个人防护装备操作人员在进行氨分解操作时必须佩戴合适的个人防护装备,包括防护眼镜或面罩、防护手套、防护服等。
个人防护装备应经常检查并确保其正常工作。
第三章操作流程3.1 开始操作前操作人员在进行操作前必须进行必要的准备工作,包括检查设备是否工作正常、检查个人防护装备是否完好,并确保操作人员已经接受过相关的培训和指导。
3.2 操作步骤(1)打开设备的进气阀门,将氨气引入反应容器内。
(2)控制进气阀门,保持适当的进气流速。
(3)根据反应条件,控制设备的温度、压力和反应时间等参数。
(4)使用仪器仔细监测反应过程,并根据监测结果调整操作条件。
(5)完成反应后,关闭进气阀门,将残留的氨气排空。
氨回收工艺步骤
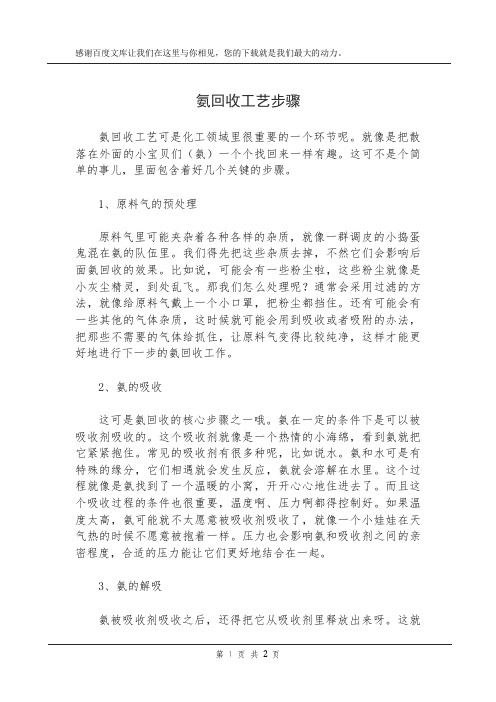
氨回收工艺步骤氨回收工艺可是化工领域里很重要的一个环节呢。
就像是把散落在外面的小宝贝们(氨)一个个找回来一样有趣。
这可不是个简单的事儿,里面包含着好几个关键的步骤。
1、原料气的预处理原料气里可能夹杂着各种各样的杂质,就像一群调皮的小捣蛋鬼混在氨的队伍里。
我们得先把这些杂质去掉,不然它们会影响后面氨回收的效果。
比如说,可能会有一些粉尘啦,这些粉尘就像是小灰尘精灵,到处乱飞。
那我们怎么处理呢?通常会采用过滤的方法,就像给原料气戴上一个小口罩,把粉尘都挡住。
还有可能会有一些其他的气体杂质,这时候就可能会用到吸收或者吸附的办法,把那些不需要的气体给抓住,让原料气变得比较纯净,这样才能更好地进行下一步的氨回收工作。
2、氨的吸收这可是氨回收的核心步骤之一哦。
氨在一定的条件下是可以被吸收剂吸收的。
这个吸收剂就像是一个热情的小海绵,看到氨就把它紧紧抱住。
常见的吸收剂有很多种呢,比如说水。
氨和水可是有特殊的缘分,它们相遇就会发生反应,氨就会溶解在水里。
这个过程就像是氨找到了一个温暖的小窝,开开心心地住进去了。
而且这个吸收过程的条件也很重要,温度啊、压力啊都得控制好。
如果温度太高,氨可能就不太愿意被吸收剂吸收了,就像一个小娃娃在天气热的时候不愿意被抱着一样。
压力也会影响氨和吸收剂之间的亲密程度,合适的压力能让它们更好地结合在一起。
3、氨的解吸氨被吸收剂吸收之后,还得把它从吸收剂里释放出来呀。
这就像是把住在小窝里的氨小宝贝再请出来一样。
这个解吸的过程通常需要改变一些条件。
比如说升高温度或者降低压力。
就像给氨住的小窝施点魔法,让它觉得这个小窝不太舒服了,然后氨就会从吸收剂里跑出来。
解吸出来的氨这时候就比较纯净了,就像经过洗礼后的小天使一样。
4、氨的精制虽然经过解吸后的氨已经比较纯净了,但可能还会有一点点小杂质。
这时候就需要对氨进行精制啦。
精制的方法有很多种,比如说可以用精馏的方法。
就像把氨放在一个特殊的楼梯上,不同的杂质和氨因为它们自身的特性,会在这个楼梯的不同位置停留,这样就可以把最后的一点杂质去掉,得到非常纯净的氨啦。
氨分解活化、再生工艺

一.原理氨分解气体发生装置以液氨为原料,经汽化后将氨气加热到一定的温度,在催化剂作用下,氨发生分解成氢氮混合气体,液氨气化预热后进入装有催化剂的分解炉,在一定温度压力和催化剂的作用下氨即分解,产生含氢75%、氮25%的混合气,气体经热交换器和冷却器及流量计后,可进行纯化处理或直接使用。
氨分解的化学反应式:2NH3=3H2+N2-22080卡即在标准状况下,1千摩尔氨完全分解能产生氢氮混合气体44.8Nm3,并吸收热量11040Kcal,也就是1kg液氨完全分解能产生2.46Nm3氢氮混合气体,根据化学反应式,氨分解气体由75%H2和25%H2组成。
要使氨气获得充分分解,必须具备下列条件:1.及时充分地供给大量热源。
2.较好的催化剂。
3.液氨的纯度为99.8%以上。
氨分解在工作装置条件下不可能完全分解,存在一定量的残余氨。
另一方面制取高纯氨的代价是比较昂贵。
由于工业液氨中含有一定量的水,因此一个完整的氨分解气制取装置必须有装满吸附的净化塔,根据吸附剂的物理吸附现象,氨分解气体必须满足低温高压的条件,才能使净化后的氨分解气体中含水量尽可能降低,满足工业生产的需要。
由于吸附剂吸附量的是有限性,为保证连续供应高纯度氨分解气体,必须有两个吸附净化装置交换使用。
一个完整的氨分解工艺流程还包括液氨的汽化和氨分解气体的冷却过程。
二.操作规范1.运行前准备:⑴初次使用前,应对装置的全部件严格检查,包括对气体密性、绝缘程度、电器元件机械执行元件的可靠性、灵敏性等,逐项检查。
⑵初次使用前,在逐项检查后,打开“分解气排空阀”,从液氨蒸发器进口通氮气排空。
之后应对催化剂进行活化处理,活化工艺曲线参照图一,活化气可采用纯氢或气氨,有条件时应优先选择纯氢,活化气体用量选择,纯氢用量为分解炉额定气量的1/4~1/3。
气氨用量为分解炉额定耗量的1/3~1/2。
⑶初次使用前,应对净化塔内的吸附剂分子筛进行再生干燥,以保证分子筛的吸附效果,首次再生应先用干燥的纯氮或氮分解气,再生气量为净化处理量的1/10左右,再生工艺曲线见图二。
氨分解工艺流程

氨分解工艺流程
《氨分解工艺流程》
氨分解工艺是一种将氨气分解成氢气和氮气的化学工艺。
氨气通常是从氨水中制得,而氨水则是从合成氨中产生的。
氨分解工艺可以将氨气转化为更有用的物质,因此在许多工业生产过程中都有重要的应用。
氨分解工艺流程一般分为以下几个步骤:
1. 氨气输入:将氨气通过管道输送到反应器中。
氨气的纯度和流量是影响分解反应效果的重要因素。
2. 反应器:在反应器中,氨气与催化剂进行反应,发生氨分解反应。
常用的催化剂有镍、铁等金属,它们可以加速氨气的分解反应。
3. 产物分离:在反应器中产生的氢气和氮气混合物需经过分离处理,将其中的氢气和氮气分别提取出来。
这通常是通过冷凝和吸附等方法来实现的。
4. 产品收集:收集分离后的氢气和氮气并进行储存或进一步的加工利用。
氨分解工艺流程虽然简单,但是需要严格的控制和维护,以确保产物的纯度和产量。
此外,对反应温度、压力等工艺条件的控制也是至关重要的,这些条件将直接影响氨分解反应的效率
和产物的质量。
总的来说,氨分解工艺流程是一种重要的化学工艺,它为氨气的再利用和资源化提供了重要的手段,有着广泛的应用前景。
附录 氨分解炉操作手册

附录:AQ/FC系列液氨制氢炉/纯化装置操作指导手册1、液氨制氢炉概述氨分解总流程:液氨瓶→液氨汇流排→双回路液氨减压装置→液氨分气缸→液氨制氢炉/纯化装置→氢气分气缸→氢气氮气配比器→烧结炉高纯度的氢氮混合气是一种良好的还原性保护气体,可用于零件退火,脱碳处理及铜基、铁基粉末冶金烧结.液氨制氢炉工作原理:液氨气化后(氨气压力:<0.1MPa)在750℃—850℃情况下,经催化剂(镍催化剂)作用,分解为氢气和氮气,并吸收热量.2NH3→3H2+N2液氨制氢炉需注意的安全事项:⑴、液氨进入液氨制氢炉必须是气态的!为达到此目的,有以下3个措施:液氨储罐出口须装有减压阀,经有效减压后氨气压力小于0。
2MPa;液氨储罐和液氨制氢炉连接管路距离大于5m;液氨制氢炉设备装有汽化器,并能有效工作。
⑵、氨气是一种对人体粘膜有刺激性的化学气体,分解后的氮气是一种使人窒息的气体,氢气是一种易燃、易爆还原性极强的气体,因此,设备现场必须良好通风,5m范围内不得有明火,所有氨源处必须配置水源,作为氨泄露的应急措施.⑶、液氨制氢炉必须安全可靠接地,接地电阻<0。
5欧姆。
2、液氨制氢炉设备基本参数AQ/FC系列液氨制氢炉/纯化装置设备基本参数:工作压力:<0。
1Mpa;工作温度:800℃—850℃液氨消耗:12kg/h原料氨气:符合《液体合成氨》规定一级品要求;含水量:≤2000PPm纯化后氨分解混合气:露点:≤—10℃残氨: ≤5PPm出口压力:<0。
1Mpa;3、液氨制氢炉/纯化装置设备工作原理:AQ液氨制氢炉采用镍催化剂加热分解液氨;FC纯化装置采用专用干燥剂物理吸附混合气中水分和残氨.其工作流程如下图:AQ 液氨制氢炉为单式流程:液氨→汽化器→减压阀→热交换器→制氢炉炉胆(镍催化剂加热分解液氨)→热交换器→冷却器→分解氨其中:冷却器后设放空阀旁路,方便停炉时分解氨排放。
为实现热交换,设备配置冷却水。
水冷却流程:冷却水→冷却器进水口→冷却器→冷却器出水口→汽化器进水口→汽化器→汽化器进水口→室外(液氨瓶水池)FC纯化装置为复式流程:Ⅰ组工作,Ⅱ组再生,通过阀门操作可进行工作再生切换.FC纯化装置Ⅰ组工作流程:冷却器分解氨→Ⅰ组进工作阀→干燥器(专用干燥剂物理吸附混合气中水分和残氨)→Ⅰ组出工作阀→纯气出口阀→纯气流量计→纯化后氨分解混合气其中:纯气出口阀前设取样阀,用于检测纯化后氨分解混合气的露点及残氨含量。
氨分解操作规程范文

氨分解操作规程范文1.概述氨分解是一种常见的实验操作,通过将氨气转化为有毒气体氮气和水蒸气来处理氨。
本操作规程旨在确保实验人员的安全,并确保操作的顺利进行。
2.实验前准备2.1实验场地应保持清洁、通风良好,确保实验人员的安全。
2.2实验室应配备急救设备和适量的灭火器材。
2.3实验人员应佩戴防护眼镜、防护手套和实验服,预防事故发生。
3.实验器材和试剂3.1氨溶液3.2高温加热装置3.3冷凝器3.4安全瓶废气处理设备(如气体洗涤塔)3.5温度计3.6安全杯4.操作步骤4.1实验人员应将氨溶液置于安全杯中,量取适量的溶液。
4.2实验人员通过高温加热装置加热溶液,使其分解产生氢气和水蒸气。
4.3将产生的氢气和水蒸气通过冷凝器冷却,并将冷凝后的水蒸气排放至安全废气处理设备中。
4.4实验人员应时刻观察反应过程的温度,避免过高的温度导致实验失控。
4.5实验结束后,关闭高温加热装置,停止氨分解反应。
5.安全措施5.1实验操作时应做到细心并保持警惕。
5.2使用氨溶液时,应注意其浓度,避免过高的浓度造成不必要的风险。
5.3高温加热装置应设置在稳定的台面上,避免倾斜和滑动。
5.4实验室应保持干燥,避免水分接触高温加热装置,防止意外发生。
5.5实验人员不得单独进行氨分解实验,应有其他人员在场协助。
6.废气处理6.1废气处理设备应具备良好的处理效果,确保废气排放不对环境和人体造成危害。
6.2废气处理设备应定期清洗和维护,确保其正常工作。
6.3长时间连续操作时,应考虑对排放废气进行监控,保证废气排放符合安全标准。
7.废弃物处理7.1操作结束后,将废气处理设备中收集的液体废弃物进行适当的处理,遵循当地有关废弃物处理的规定。
7.2废弃物应存放在标有危险品标志的容器中,并进行妥善密封。
8.急救措施8.1发生意外时,应立即停止实验操作,并向周围的人员发出警报。
8.2如有人员受伤,应立即进行急救处理,并及时送往医院。
8.3如有火灾发生,应立即用灭火器进行灭火,并通知相关人员。
氨分解说明书

精心整理第一部分氨分解部分一、化工原理:1摩尔氨气在一定的压力和温度及镍触媒催化作用下可分解为1.5摩尔的氢气和0.5摩尔的氮气并吸收一定的热量。
气化学方程式如下。
2NH3→3H2+N2-Q1231、额定产气量:50立方米/小时2、气体纯度露点≤-103、分解炉操作温度800~850?C4、分解炉额定功率45kw5、额定氨耗20kg/h6、冷却耗量2.5立方米/小时7、电源50Hz380V8、设备总重3500kg五、操作方法:1、原始开车:1)仔细阅读使用说明书,熟悉设备的原理和构造。
2)检查气,电各系统是否通畅,消除泡,冒,点,漏,并接通电源。
3)镍触媒的活化:分解炉内装的镍触媒在出厂时已经还原,但因设备在运输,库存期间总有水分,氧气等介入,触媒活性略有下降,因此原始开车时要进行触媒的活化。
421)接通电源,温度在800~850?C为操作温度,温度已处于自动控制。
2)通氨放空:打开放空阀,然后慢慢打开进氨阀,使氨进入分解炉,约放空半小时。
3)正常送气:约放空半小时后,经样气检验合格后,即可打开分解气阀,向使用点送出合格分解气,并关闭放空阀,分解炉进入稳定运转状态。
4)停车:切断电源后先关进氨阀后再关分解气阀。
2日常维护:1)经常检查并消除泡,冒,点,漏,使设备处于完好状态。
2)经常检查自动温度控制仪,严防温控仪失灵。
一旦发生温控仪及热电偶测量失灵,应立即停车检修。
3)注意:严防有毒气体(如SPH2S极大量水气和氧气)进入分解炉,分解炉温度不能升的过高(一般不超过850?C),否则触媒活性很容易降低,甚至完全失去活性。
4)当分解炉短期停车(不通氨,不往外送分解气)需要保温时,温控仪温度设定在400?C以下,否则将使局部触媒因过热而烧坏。
5)触媒使用一段时间后,由于衰老而引起破碎现象,这种现象在气氨进口处尤为明显,它会6)2、保持装置气路系统的气密性,氨气有刺激性臭味,并且分解气有百分之七十五的氢气,氢气无色无味,却是易燃气体。
氨分解工艺流程

氨分解工艺流程氨分解是一种常见的工艺流程,用于将氨气分解为氮气和氢气。
下面是一种常见的氨分解工艺流程。
首先,将氨气输送到反应器中。
反应器通常是一个高压容器,其中包含催化剂。
催化剂的选择很重要,因为它能够加速反应速度并提高产量。
在反应器中,氨气经过催化剂,发生氨的分解反应。
这个反应是一个放热反应,并且需要高温才能促使反应进行。
通常,反应温度在800-1000摄氏度之间。
分解反应产生的产物包括氮气和氢气。
氮气是一种惰性气体,不参与其他反应。
而氢气是一种重要的化工原料,可以用于合成氨水、石油加氢等。
在反应器中,由于高温,氮气和氢气以及一些未反应的氨气会被带着一起从反应器中排出。
为了回收氮气和氢气,需要进行冷却和分离。
首先,将氨气、氮气和氢气混合物进行冷却,使其温度降低。
在低温下,氮气和氢气可以通过凝固和液化的方式将其分离。
这种分离过程通常使用低温冷却器。
在低温冷却器中,氮气和氢气以液态形式收集,从而可以更容易地将其分离。
通过控制温度和压力,可以达到最大的分离效果。
分离出的液体氮气和氢气可以进行进一步的处理和利用。
氮气可以用于保护大气或制造液氧、合成氨等。
氢气可以用于制造肥料、化学品和燃料电池等。
整个氨分解工艺流程需要严格控制反应温度、压力和产物的分离过程。
这可以通过调节反应器温度和压力、冷却器温度和压力以及分离设备的操作参数来实现。
总之,氨分解是一种重要的工艺流程,可以将氨气分解为氮气和氢气。
通过控制反应条件和分离过程,可以实现高效的分解和产物回收。
这种工艺广泛应用于化工、冶金和能源等领域。
氨分解制氢工艺技术规程
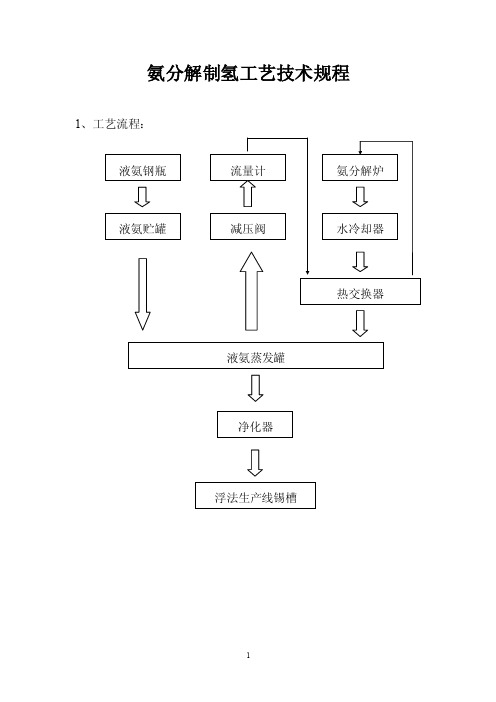
氨分解制氢工艺技术规程1、工艺流程:2.工艺技术指标:2.1氢气送往锡槽的压力~0.20Mpa2.2氢气送往锡槽的流量0~90m3/h(分解气 0~120 m3/h)2.3氢气残氧量≤5ppm2.4氢气残氨量≤2ppm2.5氢气露点温度≤-60℃3.工艺技术要求:3.1原料液氨必须符合GB536-65液体合成氨的一级品纯度的要求。
3.1.1液氨(NH3)≥99.8%3.1.2水分、油含量≤0.2%3.2脱硫器、净化器应装满吸附剂。
脱硫吸附剂应采用活性炭,净化吸附剂采用5A分子筛。
3.3分解炉应装满催化剂,催化剂采用镍基催化剂。
3.4工艺系统所有的容器及管路应无焊渣、铁锈、油污。
耐压强度试验和气密性试验应达到要求。
3.5安全阀以及报警系统、自控系统、电器、仪表、仪器、机器、装置应能正常工作。
3.6空置的液氨系统在充注液氨前应用纯度为≥99.9%的氮气吹扫置换里面的空气,当各吹扫出口的氮气纯度≥99.9%时为合格。
3.7工艺气路系统在开车前或停车后应用纯度≥99.9%的氮气吹扫置换,当各吹扫出口的氮气纯度≥99.9%时为合格。
3.8分解系统的冷却器在开车前要同入冷却水,冷却水出口应有适量的水流出。
运行中不能中断冷却水。
冬季如果停车时间较长,要放净冷却器的存水。
3.9液氨容器灌装液氨量最多不能超过容器的80%,在密闭状态下,其周围环境温度最高不能超过50℃,容器中压力最高不能超过1.96Mpa。
3.10液氨系统在工作时,压力应控制在0.3~0.7Mpa,氨气减压阀后的压力应控制在0.20 Mpa.3.11分解炉的工作温度应控制在800~850℃之间。
3.12新催化剂在第一次使用前要经过还原活化,活化可在分解炉内用纯度≥99.8%的氨气或钢瓶氢气进行。
3.13在还原活化催化剂时,要严格控制气体流量和升温速度,以保证催化剂充分活化。
具体事项按表1的技术要求进行。
表13.14出分解炉的气体残氨量应≤1000ppm(V)。
氨分解操作规程

氨分解操作规程
《氨分解操作规程》
一、目的
本操作规程旨在规范氨分解的操作流程,确保操作安全、高效,并提高产品质量。
二、适用范围
适用于所有进行氨分解操作的人员。
三、操作程序
1. 检查设备:在进行氨分解操作前,需检查分解塔、加热炉、冷却系统等设备,确保设备完好无损。
2. 通风准备:在操作前,要开启通风系统,确保室内空气流通。
3. 加料:将适量的含氨溶液加入分解塔中。
4. 加热:启动加热炉,对分解塔内的溶液进行加热。
5. 冷却:在氨分解完成后,开启冷却系统,将产生的氢气以及水蒸汽冷凝。
6. 收集产物:将分解后的氨气、氢气和水蒸汽进行分离和收集。
四、安全措施
1. 操作人员应佩戴防护眼镜、手套等个人防护装备。
2. 操作过程中,严禁吸烟、使用明火等火源。
3. 发现异常情况,立即停止操作,并通知相关人员进行处理。
五、注意事项
1. 严禁逆行操作,遵守操作流程。
2. 对设备进行定期维护,确保设备的正常运行。
3. 操作人员需熟悉氨的特性和安全操作规程。
六、责任归属
该操作规程由生产部门负责执行,相关人员需严格遵守规程要求。
七、附则
本操作规程经生产部门批准后执行,如有违反规程的情况,视情节轻重给予相应的处罚。
水洗氨及氨分解工艺简述
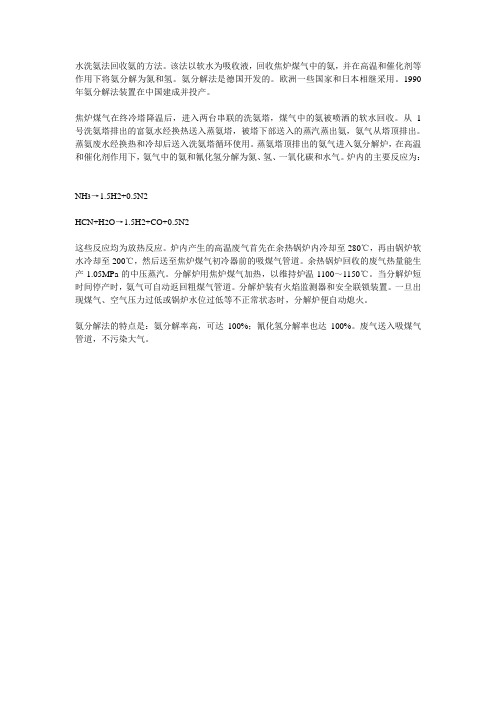
水洗氨法回收氨的方法。
该法以软水为吸收液,回收焦炉煤气中的氨,并在高温和催化剂等作用下将氨分解为氮和氢。
氨分解法是德国开发的。
欧洲一些国家和日本相继采用。
1990年氨分解法装置在中国建成并投产。
焦炉煤气在终冷塔降温后,进入两台串联的洗氨塔,煤气中的氨被喷洒的软水回收。
从1号洗氨塔排出的富氨水经换热送入蒸氨塔,被塔下部送入的蒸汽蒸出氨,氨气从塔顶排出。
蒸氨废水经换热和冷却后送入洗氨塔循环使用。
蒸氨塔顶排出的氨气进入氨分解炉,在高温和催化剂作用下,氨气中的氨和氰化氢分解为氮、氢、一氧化碳和水气。
炉内的主要反应为:
NH3→1.5H2+0.5N2
HCN+H2O→1.5H2+CO+0.5N2
这些反应均为放热反应。
炉内产生的高温废气首先在余热锅炉内冷却至280℃,再由锅炉软水冷却至200℃,然后送至焦炉煤气初冷器前的吸煤气管道。
余热锅炉回收的废气热量能生产1.05MPa的中压蒸汽。
分解炉用焦炉煤气加热,以维持炉温1100~1150℃。
当分解炉短时间停产时,氨气可自动返回粗煤气管道。
分解炉装有火焰监测器和安全联锁装置。
一旦出现煤气、空气压力过低或锅炉水位过低等不正常状态时,分解炉便自动熄火。
氨分解法的特点是:氨分解率高,可达100%;氰化氢分解率也达100%。
废气送入吸煤气管道,不污染大气。
008氨分解工艺及风险辨识管控

氨分解工艺及风险辨识管控氨分解工艺作为热处理工艺的辅助工艺,在金属热处理制造的生产现场经常被使用,氨分解工艺由于涉及到氨气、氢氮混合气以及氨气分解炉,处理工艺过程还涉及到压力容器等特种设备,相对一般的工贸行业生产工艺具有较高的危险性。
下面我们针对其工艺原理、风险辨识及管控措施等方面进行简单的讲解一、氨分解的工艺原理及流程根据氨分解的反应式2NH3—3H2+N2一22080卡,可见1摩尔氨(气态)在一定的压力和温度及镍触媒催化下,可分解为3/2摩尔的氢气和1/2摩尔的氮气,并吸收一定的热量。
一般的工艺流程为:氨瓶中流出的液态氨首先进入氨汽化器。
汽化采用水浴加热的形式,汽化器为一管板式换热器,管程通氨,壳程为由电热器加热的热水,热水和液氨进行换热,使液氨汽化至45℃左右,压力为1.5Mpa的气态氨。
(随着温度的升高,氨气压力也相应升高),形成的氨气进入氨罐或缓冲罐,输出的氨气在0.05MPa左右由调节阀调节控制。
氨气在进入分解炉前先通过流量计和热交换器进行预热在进入氨分解炉进行分解反应,通常预热的热量来自分解炉反应后的分解气。
在炉内,氨气加热至800-850℃,在镍催化剂的作用下,分解为氢氮混合气体。
然后经热交换器,通入中间罐进行水冷却,再通入纯化罐在纯化系统中除去未反应完全的残氨,在纯化系统中装有的分子筛可以同时除去杂质水份和残氨。
之后用氢氮压缩机使分解气增压至0.75-0.8MPa后进入缓冲罐和混配罐,在送至需要使用气体的工艺。
此过程中每斤氨可产生2.6M3混合气体。
二、氨分解风险辨识1、物料的风险液氨、氨气:氨气是一种无色透明而具有刺激性气味的气体。
极易溶于水,水溶液呈碱性。
相对密度0.60(空气=1)。
气氨加压到0.7~0.8MPa时就变成液氨,同时放出大量的热,相反液态氨蒸发时要吸收大量的热,所以氨可作制冷剂,接触液氨可引起严重冻伤。
氨与空气混合到一定比例时,遇明火能引起爆炸,其爆炸极限为15.7%~27.4%。
氨分解活化、再生工艺

一.原理氨分解气体发生装置以液氨为原料,经汽化后将氨气加热到一定的温度,在催化剂作用下,氨发生分解成氢氮混合气体,液氨气化预热后进入装有催化剂的分解炉,在一定温度压力和催化剂的作用下氨即分解,产生含氢75%、氮25%的混合气,气体经热交换器和冷却器及流量计后,可进行纯化处理或直接使用。
氨分解的化学反应式:2NH3=3H2+N2-22080卡即在标准状况下,1千摩尔氨完全分解能产生氢氮混合气体44.8Nm3,并吸收热量11040Kcal,也就是1kg液氨完全分解能产生2.46Nm3氢氮混合气体,根据化学反应式,氨分解气体由75%H2和25%H2组成。
要使氨气获得充分分解,必须具备下列条件:1.及时充分地供给大量热源。
2.较好的催化剂。
3.液氨的纯度为99.8%以上。
氨分解在工作装置条件下不可能完全分解,存在一定量的残余氨。
另一方面制取高纯氨的代价是比较昂贵。
由于工业液氨中含有一定量的水,因此一个完整的氨分解气制取装置必须有装满吸附的净化塔,根据吸附剂的物理吸附现象,氨分解气体必须满足低温高压的条件,才能使净化后的氨分解气体中含水量尽可能降低,满足工业生产的需要。
由于吸附剂吸附量的是有限性,为保证连续供应高纯度氨分解气体,必须有两个吸附净化装置交换使用。
一个完整的氨分解工艺流程还包括液氨的汽化和氨分解气体的冷却过程。
二.操作规范1.运行前准备:⑴初次使用前,应对装置的全部件严格检查,包括对气体密性、绝缘程度、电器元件机械执行元件的可靠性、灵敏性等,逐项检查。
⑵初次使用前,在逐项检查后,打开“分解气排空阀”,从液氨蒸发器进口通氮气排空。
之后应对催化剂进行活化处理,活化工艺曲线参照图一,活化气可采用纯氢或气氨,有条件时应优先选择纯氢,活化气体用量选择,纯氢用量为分解炉额定气量的1/4~1/3。
气氨用量为分解炉额定耗量的1/3~1/2。
⑶初次使用前,应对净化塔内的吸附剂分子筛进行再生干燥,以保证分子筛的吸附效果,首次再生应先用干燥的纯氮或氮分解气,再生气量为净化处理量的1/10左右,再生工艺曲线见图二。