PE管材挤出模头的一般知识
挤出模头设计讲解

挤出模头设计的基本要求
➢1)要有正确的出口截面形状 ➢从模头挤出的异型材型坯的截面形状——不 是产品的最终截面形状——近似 ➢型坯挤出模头后受牵引经过气隙进入定型模 中,其至少还将受到3种不能忽略的作用:离 模膨胀、拉伸变形和冷却收缩,这些作用将 会改变型坯截面的形状和尺寸
挤出模头设计的基本要求
3 挤出机的性能
➢挤出机机型和规格不同,机筒和螺杆的结构 等方面都存在有差异。这些差异会影响被塑 化的模塑料的结构形态,及其所表现出来的 熔体黏弹性性能
4 型材挤出的速度
➢ 塑料异型材挤出的速度是挤出模具(包括模头和定型 模)设计的一个十分重要的参数。对于模头来说,随 着挤出速度的提高,熔体剪切速率γ,将提高,体积流 量Q将增加,模头压力降△p将增大。剪切速率γ 的提 高也将改变熔体的黏弹性状况,很明显,分流引起的 拉伸流动会强烈;熔体入口效应、离模膨胀等弹性现 象也都会增强,超过一定界限(临界剪切速率Y。)还 将会出现熔体破裂现象。因此,在较低挤出速度下已 获得平衡(料坯均匀挤出,截面形状正确)的挤出模 头,提高挤出速度后,将可能失去平衡,出现出料不 均现象和型坯形状的畸变
➢PVC-U模塑料熔体的性能,是由其复杂的配方 体系所决定的。模塑料配方不但决定着塑料熔 体的黏度,而且也影响着塑料熔体的弹性效应, 因此是影响挤出模头结构设计的重要因素。
➢ 挤出模塑料配方对挤出模头设计的影响,还 可能是这样的情况:对于一个已经实现均匀出 料的挤出模头,这时若模塑料的成分出现波动, 就会改变模塑料的黏弹性状况,破坏原先流道 保证的均匀出料的平衡状态。因此,挤出模头 的结构设计需要对模塑料成分的波动有更好的 适应性,能让均匀出料的平衡状态在型材挤出 过程中保持稳定。
➢(2) PVC-U模塑料配方的影响 : ( PVC-U模塑料需
PE管生产工艺模具的注意事项
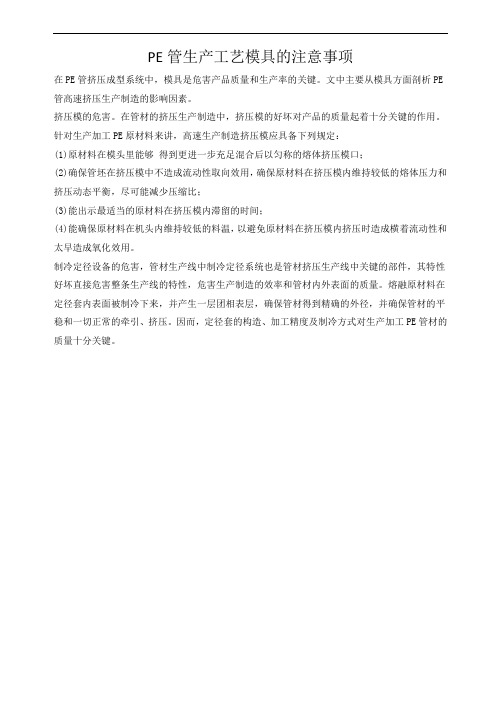
PE管生产工艺模具的注意事项
在PE管挤压成型系统中,模具是危害产品质量和生产率的关键。
文中主要从模具方面剖析PE 管高速挤压生产制造的影响因素。
挤压模的危害。
在管材的挤压生产制造中,挤压模的好坏对产品的质量起着十分关键的作用。
针对生产加工PE原材料来讲,高速生产制造挤压模应具备下列规定:
(1)原材料在模头里能够得到更进一步充足混合后以匀称的熔体挤压模口;
(2)确保管坯在挤压模中不造成流动性取向效用,确保原材料在挤压模内维持较低的熔体压力和挤压动态平衡,尽可能减少压缩比;
(3)能出示最适当的原材料在挤压模内滞留的时间;
(4)能确保原材料在机头内维持较低的料温,以避免原材料在挤压模内挤压时造成横着流动性和太早造成氧化效用。
制冷定径设备的危害,管材生产线中制冷定径系统也是管材挤压生产线中关键的部件,其特性好坏直接危害整条生产线的特性,危害生产制造的效率和管材内外表面的质量。
熔融原材料在定径套内表面被制冷下来,并产生一层团相表层,确保管材得到精确的外径,并确保管材的平稳和一切正常的牵引、挤压。
因而,定径套的构造、加工精度及制冷方式对生产加工PE管材的质量十分关键。
初级挤塑工应知应会

初级挤塑工应知应会初级挤塑工应知应会,这是每个挤塑工入门必须掌握的知识和技能。
挤塑工作是一项高难度和高风险的工作,只有掌握了一定的技能和知识,才能够有效地保证生产的质量和安全性。
本文将从挤塑工工作的概括、挤塑工的技能和知识、挤塑工作的注意事项三个方面阐述初级挤塑工应知应会的内容。
一、挤塑工作的概括挤塑工作是一项加工塑料成型的手工作业,是通过挤出机将塑料加热到一定的温度后,通过加压将塑料推动到模具中进行成型。
挤塑工作可分为加工前的准备工作和加工中的操作工作两部分。
加工前的准备工作包括准备模具和挤出机、调整挤出机的温度、角度和速度、准备好所需的原材料等。
加工中的操作工作包括观察机器状态、调整挤出机的温度和速度、加料和清理料斗、观察模具的运作和清理模具等。
二、挤塑工的技能和知识1. 熟悉挤出机的结构和原理挤塑工要熟悉挤出机的各种结构,包括发动机、减速器、温控系统、模头等,理解它们的工作原理和操作程序。
2. 熟悉原材料的特性和制品质量标准挤塑工必须掌握所用原材料的各种特性,包括塑料的种类、厚度、耐温、强度等,同时还需了解合格的制品和不合格的制品之间的差别,以便在加工中能够更好的把握工艺参数,保证制品的质量标准。
3. 熟悉操作流程和安全操作规程挤塑工需要了解与操作相关的所有过程和规程,并严格按照操作流程和安全操作规程进行操作。
同时还要按照制定的戴手套、戴口罩、戴护目镜等安全防护措施,确保人员的安全。
三、挤塑工作的注意事项1. 保证设备及环境的整洁和卫生挤塑工作需要在干燥、通风、清洁的环境中进行,保持设备和环境的整洁和卫生是保证产品质量的基础。
另外,每次操作完毕必须仔细检查设备和生产现场,将设备和生产环境清理干净。
2. 执行严格的操作规程在操作过程中,必须严格执行操作规程,确保各种工艺参数和操作流程的合理性。
特别是在调整机器参数和换模处理时,必须要做到安全稳妥,不得擅自更改机器的参数和流程。
3. 注重个人安全防护在操作过程中,要注重个人安全防护。
挤出机模头

挤出机模头挤出机模头是塑料加工行业中至关重要的一部分,它扮演着将塑料颗粒加热融化并挤出成型的关键角色。
挤出机模头的设计和制造对产品的质量、生产效率以及能耗等方面都有着重要影响,因此在塑料加工过程中,选择合适的挤出机模头至关重要。
首先,挤出机模头通常由进料口、螺杆、机筒以及模具等部分构成。
进料口的设计需要考虑塑料颗粒的均匀输送,避免出现堵塞或者不均匀加热的情况。
螺杆的设计则需要根据不同的塑料原料,调整螺杆的螺距、压力等参数,以确保塑料颗粒被充分融化并进行均匀挤出。
机筒的材质需要具备耐高温、耐磨损等特性,以保证挤出机的稳定运行。
而模具则决定了最终产品的形状和尺寸,需要根据产品的要求进行精准设计和加工。
在选择挤出机模头时,除了考虑其结构设计外,还需要考虑生产工艺、原料特性以及产品要求等因素。
不同的塑料原料需要不同类型的挤出机模头来加工,例如对于高粘度的塑料,需要选择高压力、高温度的挤出机模头,以确保塑料能够充分熔化并顺利挤出。
同时,在生产过程中,需要对挤出机模头进行定期清洗和维护,以保证其长期稳定运行。
另外,在挤出机模头的设计中,还需要考虑如何有效控制生产过程中的能耗和废品率。
通过优化挤出机模头的结构设计,提高加热效率和塑料流动性,可以降低生产过程中的能耗,减少废品率,提高生产效率。
同时,合理选择工艺参数,如挤出速度、温度等,也可以对产品的质量和成型效果产生重要影响。
总的来说,挤出机模头作为塑料加工产业中的关键设备,其设计和选择对产品质量、生产效率以及能耗等方面都有着重要影响。
通过合理选择挤出机模头、优化生产工艺以及加强设备维护等措施,可以提高塑料制品的生产质量,降低生产成本,推动塑料加工行业的可持续发展。
1。
PE管材挤出操作

四、管材的成型工艺
1、原料的预处理:聚烯烃是非吸水性材料,通常水分含量相当低, 可以满足挤出的需要。但当聚烯烃含吸湿性颜料,如炭黑时,对湿度 敏感,含水量增大。水分不仅导致管材内外表面粗糙,而且导致熔体 中出现气泡。通常,对于含炭黑的聚烯烃管材料应进行干燥处理。一 般通过除湿干燥处理。 2、温度的控制:挤出成型温度是促成成型物料塑化和塑料熔体流动 的必要条件,它对挤出成型过程中物料塑化和制品质量和产量均有十 分重要的影响。在挤出成型过程中,物料从粒状固态进入挤出机后, 要完成输送、压实、熔融、均化直到高温熔融型坯从机头中挤出。一 般的温度在160℃-220℃。 3.压力控制:塑料在挤出过程中需要的挤出压力,主要来至克服其在 机筒、螺槽、机头和口模等零部件中的流动阻力机自身内部的粘度摩 擦。一般讲,增加熔体压力,将降低挤出产量,而使产品密实,有利 于提高管材的质量。但压力过大,会带来安全问题。因此要密切关注 熔体压力。
5.2机器操作注意事项
a、机器开启前要检查机器外观是否有损伤或其它问题, 如有应向有 关部门或负责人员报告。必要时关闭主开关。
b、只有在所有保护设备、急停设备、隔音设备及吸料设备均工作正 常的前提才可运作机器。
c、开机前, 确保没有人在机器的转动部件上。向所有操作人员发出 警报, 避免采用任何可能产生危险的工作方式。
2. 机头部分的作用:
3. A、使熔融物料由螺旋运动变为直线运动。 B、产生必要的 成型压力,保证制品密实。 C、使物料通过机头得到进一步 塑化。
4. D.通过机头成型所需的断面形状和尺寸的制品。
5. 定径套的作用:保证成品具有正确的几何形状、尺寸和光滑 的表面。
6. 真空冷却的作用:通过定径套冷却定型后,进一步在真: 高密度聚乙烯(HDPE):PE80,PE100 中密度聚乙烯(MDPE)(PE-RT是其中的一种) 低密度聚乙烯(LDPE) 线性低密度聚乙烯(LLDPE) 2.聚丙烯: 均聚聚丙烯(PP-H) 无规共聚聚丙烯(PP-R) 嵌段共聚聚乙烯(PP-B)
PE管材挤出成型作业指导书
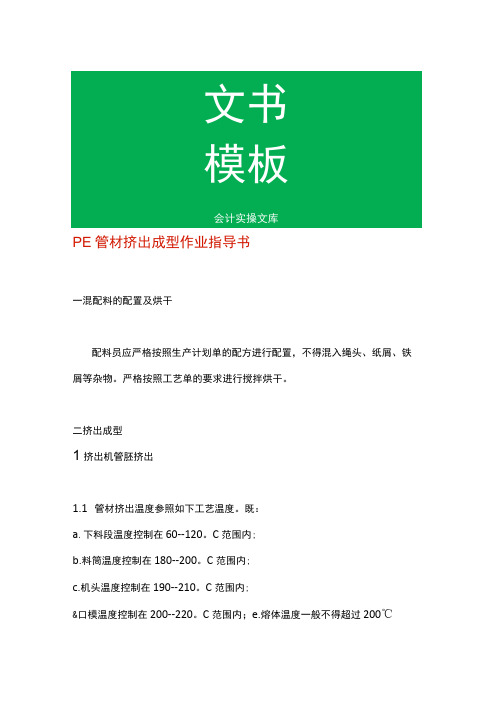
PE管材挤出成型作业指导书一混配料的配置及烘干配料员应严格按照生产计划单的配方进行配置,不得混入绳头、纸屑、铁屑等杂物。
严格按照工艺单的要求进行搅拌烘干。
二挤出成型1挤出机管胚挤出1.1管材挤出温度参照如下工艺温度。
既:a.下料段温度控制在60--120。
C范围内;b.料筒温度控制在180--200。
C范围内;c.机头温度控制在190--210。
C范围内;&口模温度控制在200--220。
C范围内;e.熔体温度一般不得超过200℃f.停机后重新升温开机,应分段加热;第一段将各区温度设置在与工艺温度相差50-6(ΓC,满值后稳定60min进行第二段加热,将各区温度设置在工艺温度范围,满值后稳定30minβ1.2螺杆a.螺杆转速应匹配生产速度,满足管材的尺寸要求。
扭矩不得高于85%ob.料筒应不定时予以清洗。
c.开机时挤出机转速应设置为零启动,主机加速过程中应缓慢提速,密切注意管胚和主机扭矩的变化,确保管胚稳定,严禁超出扭矩限制。
1.3模头口模及芯模尺寸a.严格按照生产实际选择模具。
b.模头生产时不允许漏料。
2真空定径及冷却2.1真空定径设备中心必须与挤出机中心线一致;2.2水质清洁,无颗粒杂物等;2.3定径套、真空箱及冷却水箱每月彻底清洗一次,去掉各类杂物;2.4高位水箱及到定径套的水路每季度清洗一次,对照开机验证表严格逐条验证:a.重点检杳真空定径水槽托轮和其他转动部分及水泵、真空泵是否工作正常;b.真空度根据不同管材规格在∙0.06~0.015MPa之间调节;c.PE管管坯从模头挤出,经由定径套进入真空箱,管材的外径,壁厚,表面质量初步定型。
所以定径套一定要保持水路畅通,无堵塞,表面无损伤、杂物。
不漏气;d.PE管管坯从熔融状态转为固态,需要释放出大量的热,因此冷却效果的好坏直接关系到生产效率的高低和产品性能的好坏。
根据成型调节水量大小,确保成型稳定、冷却充分。
3标识严格按照生产计划单的要求打印管材标识,标识必须清晰、完整,标识间距离符合标准。
聚乙烯管材挤出成型工艺参数需如何控制
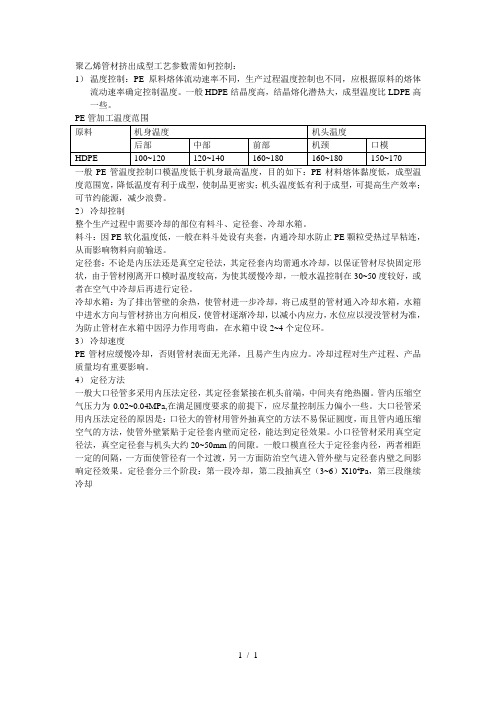
聚乙烯管材挤出成型工艺参数需如何控制:1)温度控制:PE原料熔体流动速率不同,生产过程温度控制也不同,应根据原料的熔体流动速率确定控制温度。
一般HDPE结晶度高,结晶熔化潜热大,成型温度比LDPE高一些。
一般PE管温度控制口模温度低于机身最高温度,目的如下:PE材料熔体黏度低,成型温度范围宽,降低温度有利于成型,使制品更密实;机头温度低有利于成型,可提高生产效率;可节约能源,减少浪费。
2)冷却控制整个生产过程中需要冷却的部位有料斗、定径套、冷却水箱。
料斗:因PE软化温度低,一般在料斗处设有夹套,内通冷却水防止PE颗粒受热过早粘连,从而影响物料向前输送。
定径套:不论是内压法还是真空定径法,其定径套内均需通水冷却,以保证管材尽快固定形状,由于管材刚离开口模时温度较高,为使其缓慢冷却,一般水温控制在30~50度较好,或者在空气中冷却后再进行定径。
冷却水箱:为了排出管壁的余热,使管材进一步冷却,将已成型的管材通入冷却水箱,水箱中进水方向与管材挤出方向相反,使管材逐渐冷却,以减小内应力,水位应以浸没管材为准,为防止管材在水箱中因浮力作用弯曲,在水箱中设2~4个定位环。
3)冷却速度PE管材应缓慢冷却,否则管材表面无光泽,且易产生内应力。
冷却过程对生产过程、产品质量均有重要影响。
4)定径方法一般大口径管多采用内压法定径,其定径套紧接在机头前端,中间夹有绝热圈。
管内压缩空气压力为0.02~0.04MPa,在满足圆度要求的前提下,应尽量控制压力偏小一些。
大口径管采用内压法定径的原因是:口径大的管材用管外抽真空的方法不易保证圆度,而且管内通压缩空气的方法,使管外壁紧贴于定径套内壁而定径,能达到定径效果。
小口径管材采用真空定径法,真空定径套与机头大约20~50mm的间隙。
一般口模直径大于定径套内径,两者相距一定的间隔,一方面使管径有一个过渡,另一方面防治空气进入管外壁与定径套内壁之间影响定径效果。
定径套分三个阶段:第一段冷却,第二段抽真空(3~6)X104Pa,第三段继续冷却1 / 1。
聚乙烯管材挤出技术
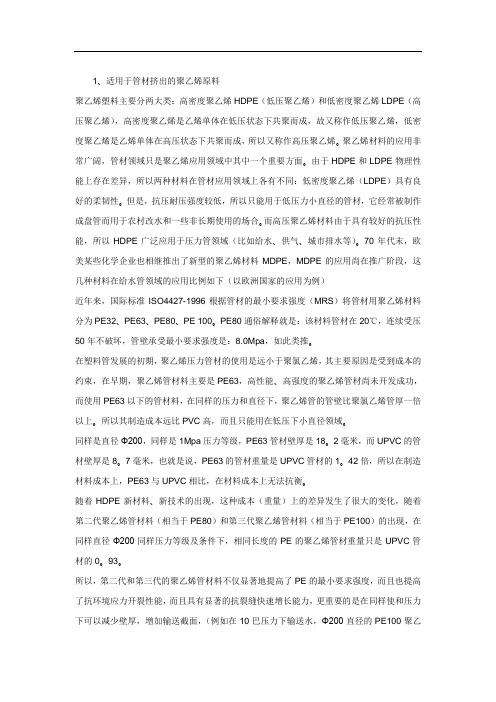
1、适用于管材挤出的聚乙烯原料聚乙烯塑料主要分两大类:高密度聚乙烯HDPE(低压聚乙烯)和低密度聚乙烯LDPE(高压聚乙烯),高密度聚乙烯是乙烯单体在低压状态下共聚而成,故又称作低压聚乙烯,低密度聚乙烯是乙烯单体在高压状态下共聚而成,所以又称作高压聚乙烯。
聚乙烯材料的应用非常广阔,管材领域只是聚乙烯应用领域中其中一个重要方面。
由于HDPE和LDPE物理性能上存在差异,所以两种材料在管材应用领域上各有不同:低密度聚乙烯(LDPE)具有良好的柔韧性。
但是,抗压耐压强度较低,所以只能用于低压力小直径的管材,它经常被制作成盘管而用于农村改水和一些非长期使用的场合。
而高压聚乙烯材料由于具有较好的抗压性能,所以HDPE广泛应用于压力管领域(比如给水、供气、城市排水等)。
70年代末,欧美某些化学企业也相继推出了新型的聚乙烯材料MDPE,MDPE的应用尚在推广阶段,这几种材料在给水管领域的应用比例如下(以欧洲国家的应用为例)近年来,国际标准ISO4427-1996根据管材的最小要求强度(MRS)将管材用聚乙烯材料分为PE32、PE63、PE80、PE 100。
PE80通俗解释就是:该材料管材在20℃,连续受压50年不破坏,管壁承受最小要求强度是:8.0Mpa,如此类推。
在塑料管发展的初期,聚乙烯压力管材的使用是远小于聚氯乙烯,其主要原因是受到成本的约束,在早期,聚乙烯管材料主要是PE63,高性能、高强度的聚乙烯管材尚未开发成功,而使用PE63以下的管材料,在同样的压力和直径下,聚乙烯管的管壁比聚氯乙烯管厚一倍以上。
所以其制造成本远比PVC高,而且只能用在低压下小直径领域。
同样是直径Φ200,同样是1Mpa压力等级,PE63管材壁厚是18。
2毫米,而UPVC的管材壁厚是8。
7毫米,也就是说,PE63的管材重量是UPVC管材的1。
42倍,所以在制造材料成本上,PE63与UPVC相比,在材料成本上无法抗衡。
随着HDPE新材料、新技术的出现,这种成本(重量)上的差异发生了很大的变化,随着第二代聚乙烯管材料(相当于PE80)和第三代聚乙烯管材料(相当于PE100)的出现,在同样直径Φ200同样压力等级及条件下,相同长度的PE的聚乙烯管材重量只是UPVC管材的0。
PE管材挤出模头的一般知识
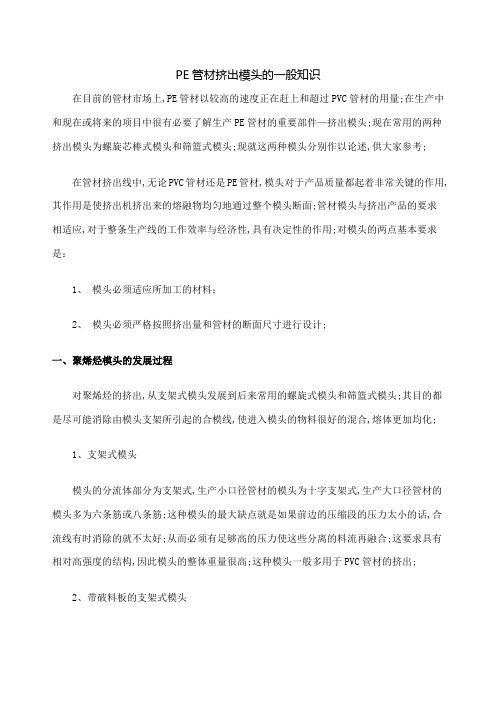
PE管材挤出模头的一般知识在目前的管材市场上,PE管材以较高的速度正在赶上和超过PVC管材的用量;在生产中和现在或将来的项目中很有必要了解生产PE管材的重要部件—挤出模头;现在常用的两种挤出模头为螺旋芯棒式模头和筛篮式模头;现就这两种模头分别作以论述,供大家参考;在管材挤出线中,无论PVC管材还是PE管材,模头对于产品质量都起着非常关键的作用,其作用是使挤出机挤出来的熔融物均匀地通过整个模头断面;管材模头与挤出产品的要求相适应,对于整条生产线的工作效率与经济性,具有决定性的作用;对模头的两点基本要求是:1、模头必须适应所加工的材料;2、模头必须严格按照挤出量和管材的断面尺寸进行设计;一、聚烯烃模头的发展过程对聚烯烃的挤出,从支架式模头发展到后来常用的螺旋式模头和筛篮式模头;其目的都是尽可能消除由模头支架所引起的合模线,使进入模头的物料很好的混合,熔体更加均化;1、支架式模头模头的分流体部分为支架式,生产小口径管材的模头为十字支架式,生产大口径管材的模头多为六条筋或八条筋;这种模头的最大缺点就是如果前边的压缩段的压力太小的话,合流线有时消除的就不太好;从而必须有足够高的压力使这些分离的料流再融合;这要求具有相对高强度的结构,因此模头的整体重量很高;这种模头一般多用于PVC管材的挤出;2、带破料板的支架式模头最简单的方法是将一破料板放在支架之后,由支架所引起的几道料流被分成众多更小的料流;因此,机械应力从支架部分向前推移,而合模线大体上被大量小的料流消除;这种PE 模头多用于低密度聚乙烯、小口径管材生产中;以前我公司在西厂生产的低密度PE排水灌溉用管材所用模头就为此种模头;现在这类模头已经趋于淘汰,在一些私营小厂还在用;3、螺旋芯棒式模头和筛篮式模头带破料板的支架式模头在现有的中高密度聚乙烯管材生产中已很少使用;而多用螺旋芯棒式模头和筛篮式模头;这两种机头已较好地解决了消除合模线的问题;螺旋芯棒式模头的核心是螺旋芯棒,筛篮式模头模头的核心部分是带有大量孔眼的管状体,即网叠;现把这两种常用模头的结构及工作原理分别说明;二、螺旋芯棒式模头的结构及工作原理图1螺旋芯棒式模头的结构及工作原理螺旋芯棒式模头又叫螺旋分流体模头;对于螺旋分流体模头,进入模头的熔体料流,首先通过分流体系--有的是若干星型孔或其他分流系统,分流到机头四周;然后熔体进入螺旋状环绕在芯模外面的流道;螺旋流道的深度随着靠近模头流出端而逐渐减小;同时,芯模与模头体型腔之间的间隙则逐渐增大;在这一区段,料流内部出现轴向与径向流动的重叠;沿着模头流出方向,径向流动的比例降低,而轴向流动的比例,则持续提高,最终全部的熔体沿轴向流动;采用这种方式,分流体流道的流动印记沿管材断面四周均匀分布,这就意味着不会出现局部的强度损失;沿管材断面四周熔体分流的质量受多种因素的影响;这些因素包括机头的几何尺寸,如流道的数量、流道缠绕扭曲角度、螺旋的螺距、螺槽深度与宽度、间隙宽度、所加工的原料,特别是其粘度,以及挤出量和物料温度;借助于计算机程序和操作者的经验,可以对螺旋分流体进行优化设计,以适应特定的应用范围;在这种情况下,壁厚分布非常均匀;这种模头除了很好地消除合料线外,还在以下几方面有优势:1、机械应力和热应力较低,制品有良好地机械强度;2、结构坚固,故适合高粘度材料的挤出,同时模头的装拆和操作简便;3、芯棒上易钻孔,故易采用内冷系统;以上的这些优点使螺旋芯棒式模头得到越来越广泛地应用;这种模头的缺点是:由于其相对复杂的结构,这种类型模头对原料的改变较敏感;即使是粘度和流变特性的细小变化都会引起螺旋体中流动情况的改变,管径的变化也有相似的影响;因此,要设计好螺旋的几何形状,使模头具有尽可能宽的加工范围,以适应不同的材料和挤出量;三、筛篮式模头的结构及工作原理在筛篮式模头上,料流首先通过支架或带有多星孔的料流分流体系;紧接着熔体流过多孔区段;这个元件,即筛篮,在这里料流不是沿轴向流过,而是沿径向从里向外流过;由于筛篮具有一定的长度,在机头直径较小的情况下,提供了很大的过流面积;因此,在相对较小的机头尺寸下,多孔区段的压力降低了;在筛篮区段内,熔体料流两次改变流向,然后变成轴向;单股料流之间能良好的混合,熔体更加均化;借助于一个阻滞元件以及相邻的松弛缓冲区,实现料流之间的融合;由于筛篮的断面面积比较大,筛篮式机头的机头压力要明显低于其他的结构形式;物料受到的负荷比较小,物料温度也比较低,可以较容易地提高挤出量;这种机头的最大优点是适应性比较好即使在很高的挤出量时,也能实现良好的均化;管材管径及壁厚的变化,PE原料的型号、物料粘度、背压的变化下,都能生产出高质量的管材;这种模头的最大缺点是模头内所有物料的融合、生产中清理、拆装模头不如螺旋芯棒式机头好和方便;我公司现用的PE管生产线是巴登震雄生产的,所用机头为筛篮式机头;生产实践中可以明显的看出这种机头的适应性较强,无论PE80、PE100还是PE63;我们另买一专用机头挤出PP-R管材,解决了经常清理机头的不便;总之,这两种模头各有利弊,建议在选购PE管材模头时,取长补短,根据自己的生产情况选用;生产原料的牌号不固定,生产量较大,不经常更换管材颜色而清理拆装模头时,最好选用筛篮式模头;要求管材壁厚较均匀、生产原料的牌号较固定,常更换管材颜色而清理拆装模头时,最好选用螺旋芯棒式模头;。
低密度聚乙烯管材挤出温度

低密度聚乙烯管材挤出温度
摘要:
一、低密度聚乙烯管材简介
1.低密度聚乙烯管材的定义
2.低密度聚乙烯管材的特点
二、低密度聚乙烯管材挤出温度的重要性
1.挤出温度的基本概念
2.挤出温度对管材性能的影响
三、低密度聚乙烯管材挤出温度的控制
1.挤出温度控制的基本方法
2.挤出温度控制的关键因素
四、低密度聚乙烯管材挤出温度的优化
1.优化挤出温度的意义
2.优化挤出温度的具体措施
正文:
低密度聚乙烯管材是一种应用广泛的塑料管材,由于其优异的物理性能和化学稳定性,被广泛应用于给排水、燃气、通信等领域。
在生产过程中,挤出温度是一个十分关键的参数,对管材的性能和质量有着直接的影响。
低密度聚乙烯管材的挤出温度是指在管材挤出过程中,原料从挤出机头挤出时的温度。
挤出温度对管材的物理性能、化学稳定性、成型效果等方面都有重要影响。
一般来说,挤出温度过高,会导致管材的色泽变深、透明度降低,
甚至可能引起分解和炭化;挤出温度过低,则会导致管材的硬度增加、韧性降低,影响管材的使用性能。
在实际生产过程中,挤出温度的控制是一个复杂的过程,需要综合考虑原料的性质、挤出机的类型、管材的规格和生产工艺等因素。
其中,原料的性质是影响挤出温度的主要因素,不同的低密度聚乙烯原料,其熔融特性、热稳定性等都有所不同,需要根据原料的性质来选择合适的挤出温度。
为了优化挤出温度,提高管材的质量和性能,可以从以下几个方面进行:一是选择适合的原料,二是优化挤出机的设定,三是改进生产工艺,四是加强温度监测和控制。
PE管材挤出机挤出过程中常见问题和解决方法

PE管材挤出机挤出过程中常见问题和解决方法塑料管材在生产线过程中,由于操作人员对工艺和机器操作不够熟练,常会致使塑料管材出现外表面粗糙,内部出现抖动环,壁厚不均,圆度不够等现象,所以要及时调整工艺,排除PE管材挤出机故障,才能提高产品质量。
1.PE管材挤出机故障:塑料管材外表面粗糙调整工艺温度;降低冷却水温,PE管*冷却水温为20~25℃;检查水路,是否存在堵塞或水压不足现象;检查机筒、机头等加热圈是否有损坏;调整定径套进水流量;检查原料的性能和批号;检查模具芯部温度,若高于口模区段温度,调低芯部温度;清理模具的集料;2.PE管材挤出机故障:塑料管材外表面出现沟痕调整定径套出水压力,出水量要求均衡;调整真空定型箱内喷嘴角度,使管材冷却均匀;检查口模、定径套、切割机等硬件是否存在杂物、毛刺等;3.PE管材挤出机故障:内表面出现沟痕检查内管是否进水,如进水则将刚出口模的管胚捏牢,使其内腔封闭;降低模具内部温度;清理并抛光模具;4.PE管材挤出机故障:管道内部出现抖动环调整定径套出水,使其出水均匀;调整二室真空度,使后室真空度略高于前室真空度;检查真空密封垫是否过紧;检查牵引机有否存在抖动现象;检查主机出料是否均匀;5.PE管材挤出机故障:无真空检查真空泵进水口是否堵塞,如堵塞,进行疏通;检查真空泵工作是否正常;检查真空管路是否漏气;检查芯模压紧螺钉中间的小孔是否堵塞,如堵塞,用细铁丝疏通;6.PE管材挤出机故障:管材外圆尺寸超差调整真空度大小可改变外园尺寸;调整牵引速度可改变外园尺寸;修正定径套内孔尺寸;7.PE管材挤出机故障:管材圆度超差调整真空定型机、喷淋箱内喷嘴角度,使管材冷却均匀;检查真空定型机、喷淋箱内水位高度、水压表压力,使喷淋量大而有力;检查真空定型机、喷淋箱水温状况,若>35℃,需配置冷冻水系统或增加喷淋冷却箱;检查水路,清洗过滤器;调整工艺;检查并修正定径套内孔园度;调整管材导向夹持装置,以修正管材的椭圆度;8.PE管材挤出机故障:管材壁厚不均匀在模具上调整壁厚;调整真空定型机及喷淋箱内喷嘴角度,使管材冷却均匀;调整定径套出水,使其出水均匀;拆开模具,检查模具内部螺钉是否松动,并重新拧紧;9.PE管材挤出机故障:塑化温度过高调整工艺;调整模具芯部加热温度,并对模具内部通风冷却;螺杆的剪切热太高,更换螺杆;10.PE管材挤出机故障:切割计长不准确检查计长轮是否压紧;检查计长轮是否摆动,并拧紧计长轮架固定螺栓;检查切割机行程开关有否损坏;检查旋转编码器是否损坏;旋转编码器接线有否脱焊(航空插头座接触是否良好);各单机外壳(PE端子)应各自引接地线到1个总接地点可靠接地,且该接地点应有符合电气接地要求接地桩,不允许各单机外壳(PE端子)串联后接地,否则将引入干扰脉冲,引起切割长度不准;11.PE管材挤出机故障:共挤标识条问题共挤标识条扩散:一般是由于用户使用的共挤料选择不当造成,应使用PE等料,必要时可降低挤出段温度;共挤标识条挤不出:将主挤出机停机,先开共挤机,开启共挤机10分钟左右再开主机;共挤标识条太细或太宽:一般是由于共挤机挤出量与管材牵引速度不匹配造成,应调节共挤机变频器频率或改变牵引速度使二者速度能匹配;其次是共挤机下料段冷却水套未通冷却水的原因;管材生产线在实际生产的过程中还会出现其它的异常情况,要根据实际情况即使处理。
公共基础知识挤出工艺基础知识概述
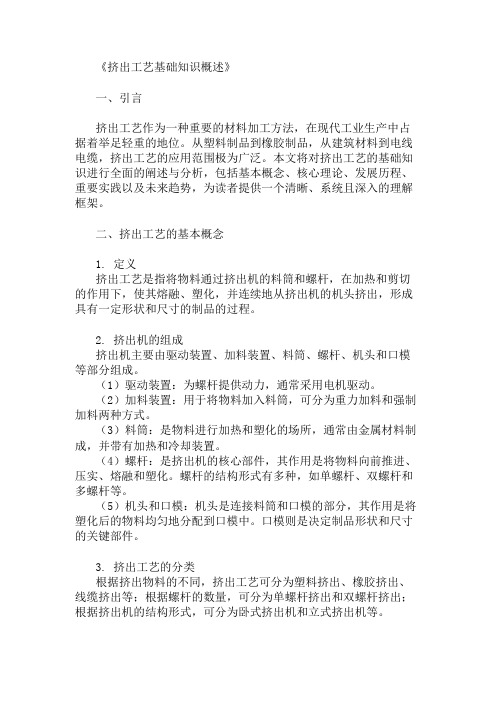
《挤出工艺基础知识概述》一、引言挤出工艺作为一种重要的材料加工方法,在现代工业生产中占据着举足轻重的地位。
从塑料制品到橡胶制品,从建筑材料到电线电缆,挤出工艺的应用范围极为广泛。
本文将对挤出工艺的基础知识进行全面的阐述与分析,包括基本概念、核心理论、发展历程、重要实践以及未来趋势,为读者提供一个清晰、系统且深入的理解框架。
二、挤出工艺的基本概念1. 定义挤出工艺是指将物料通过挤出机的料筒和螺杆,在加热和剪切的作用下,使其熔融、塑化,并连续地从挤出机的机头挤出,形成具有一定形状和尺寸的制品的过程。
2. 挤出机的组成挤出机主要由驱动装置、加料装置、料筒、螺杆、机头和口模等部分组成。
(1)驱动装置:为螺杆提供动力,通常采用电机驱动。
(2)加料装置:用于将物料加入料筒,可分为重力加料和强制加料两种方式。
(3)料筒:是物料进行加热和塑化的场所,通常由金属材料制成,并带有加热和冷却装置。
(4)螺杆:是挤出机的核心部件,其作用是将物料向前推进、压实、熔融和塑化。
螺杆的结构形式有多种,如单螺杆、双螺杆和多螺杆等。
(5)机头和口模:机头是连接料筒和口模的部分,其作用是将塑化后的物料均匀地分配到口模中。
口模则是决定制品形状和尺寸的关键部件。
3. 挤出工艺的分类根据挤出物料的不同,挤出工艺可分为塑料挤出、橡胶挤出、线缆挤出等;根据螺杆的数量,可分为单螺杆挤出和双螺杆挤出;根据挤出机的结构形式,可分为卧式挤出机和立式挤出机等。
三、挤出工艺的核心理论1. 物料的流动与变形在挤出过程中,物料在螺杆的推动下,经历了固体输送、熔融和均化三个阶段。
在固体输送阶段,物料主要依靠螺杆的旋转和摩擦力向前推进;在熔融阶段,物料在加热和剪切的作用下逐渐熔融;在均化阶段,物料被进一步混合和塑化,以保证挤出制品的质量均匀。
2. 螺杆的设计原理螺杆的设计是挤出工艺的关键,其主要参数包括螺杆直径、长径比、螺距、螺槽深度等。
螺杆的设计应根据物料的性质、挤出工艺的要求以及挤出机的性能等因素进行综合考虑,以实现物料的高效输送、熔融和塑化。
塑料管材挤出模具设计
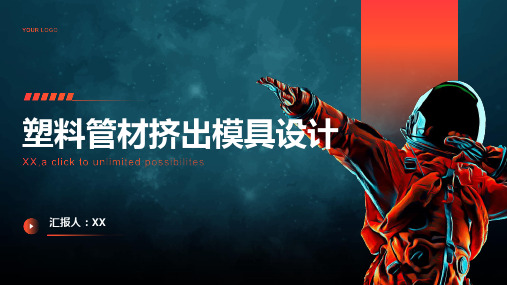
实例分析:对 PVC管材挤出模 具设计实例进行 深入分析,包括 设计要点、难点 及解决方案
经验总结:总结 PVC管材挤出模 具设计的经验教 训,提出优化建 议和未来发展方 向
实例二:PE管材挤出模具设计
模具结构:采用分流器、定 径套、机头等部件
模具温度控制:加热和冷却 系统对管材成型至关重要
模具材料:选择高强度、耐 磨性好的钢材
模具设计的原则和流程
模具设计应满足生产塑料管材的工艺要求,确保管材质量、尺寸和外观符合标准。 模具设计应考虑到生产效率、成本和安全性,以提高生产效益。 模具设计应遵循“一模多腔”的原则,以提高生产效率。 模具设计应注重冷却系统的设计,确保模具温度控制合理,提高管材质量。
塑料管材挤出模具设计要点
模具流道设计
数字化与信息化 技术:优化设计 流程,提高设计 精度
3D打印技术:个 性化定制,缩短 产品上市时间
绿色环保设计:降低能耗和减少废弃物排放的措施
采用新型材料:选择 可再生、可降解或环 保的材料,降低对环 境的污染。
优化结构设计:通过 改进模具结构,减少 生产过程中的能耗和 废弃物排放。
引入智能化技术:利 用先进的控制技术, 实现生产过程的自动 化和智能化,降低能棒加热,确保温度均匀分布,提高塑料管材的塑化效果 冷却系统:采用循环水冷却,快速降低模具温度,提高生产效率 温控系统:精确控制加热和冷却温度,保证产品质量和生产稳定性 安全保护:设置温度过高、过低自动报警和保护功能,确保生产安全
模具排气和溢料设计
模具排气:设计时需考虑模具的排气口位置和大小, 以确保在挤出过程中气体能够顺利排出。
产。
新型材料应用: 采用高强度、耐 高温、耐腐蚀等 新型材料,提高 模具的使用寿命
pe隔膜挤出参数

pe隔膜挤出参数
3. 挤出压力:挤出压力是指挤出机在挤出过程中施加的压力。挤出压力的选择应根据材料 的特性和产品要求进行调整,以确保薄膜的良好挤出和充盈。
4. 模头设计:模头是控制薄膜挤出形状和厚度的关键部件。对于PE隔膜的挤出,一般采 用平板式模头或圆形模头,具体的设计要根据产品要求和挤出机的能力进行选择。
5. 冷却方式:挤出后的PE隔膜需要进行冷却和固化。常见的冷方式包括水冷却和风冷 却,具体的冷却方式需根据产品要求和生产设备进行选择。
pe隔膜挤出参数
需要注意的是,以上参数仅供参考,实际的挤出参数需根据具体的生产设备、产品要求和 工艺条件进行调整和优化。在实际生产中,应进行试验和调试,根据产品的品质要求和生产 效率进行参数的优化和调整。
pe隔膜挤出参数
PE(聚乙烯)隔膜是一种常用的塑料薄膜材料,用于挤出成型的参数会受到具体的生产 设备、产品要求和工艺条件的影响。以下是一些常见的PE隔膜挤出参数:
1. 挤出温度:挤出温度是指挤出机筒和模头的温度。对于PE隔膜的挤出,一般挤出温度 范围为160-220摄氏度,具体的温度需根据材料的牌号和生产要求进行调整。
聚乙烯管材挤出成型工艺
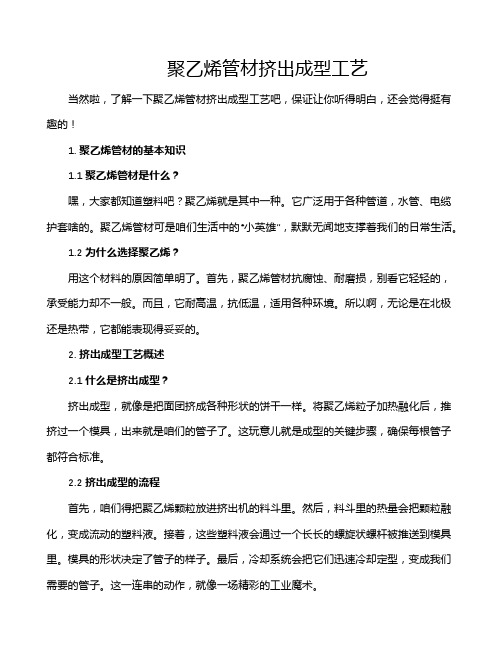
聚乙烯管材挤出成型工艺当然啦,了解一下聚乙烯管材挤出成型工艺吧,保证让你听得明白,还会觉得挺有趣的!1. 聚乙烯管材的基本知识1.1 聚乙烯管材是什么?嘿,大家都知道塑料吧?聚乙烯就是其中一种。
它广泛用于各种管道,水管、电缆护套啥的。
聚乙烯管材可是咱们生活中的“小英雄”,默默无闻地支撑着我们的日常生活。
1.2 为什么选择聚乙烯?用这个材料的原因简单明了。
首先,聚乙烯管材抗腐蚀、耐磨损,别看它轻轻的,承受能力却不一般。
而且,它耐高温,抗低温,适用各种环境。
所以啊,无论是在北极还是热带,它都能表现得妥妥的。
2. 挤出成型工艺概述2.1 什么是挤出成型?挤出成型,就像是把面团挤成各种形状的饼干一样。
将聚乙烯粒子加热融化后,推挤过一个模具,出来就是咱们的管子了。
这玩意儿就是成型的关键步骤,确保每根管子都符合标准。
2.2 挤出成型的流程首先,咱们得把聚乙烯颗粒放进挤出机的料斗里。
然后,料斗里的热量会把颗粒融化,变成流动的塑料液。
接着,这些塑料液会通过一个长长的螺旋状螺杆被推送到模具里。
模具的形状决定了管子的样子。
最后,冷却系统会把它们迅速冷却定型,变成我们需要的管子。
这一连串的动作,就像一场精彩的工业魔术。
3. 关键因素与注意事项3.1 温度与压力的控制在挤出成型过程中,温度和压力这两个“小伙伴”至关重要。
温度过高,塑料液会变得太稀,管子可能会有气泡或者质量问题;温度过低,塑料液太粘,挤出时可能会堵塞。
压力也是一样,必须精确控制,确保管子内外光滑均匀。
3.2 冷却与切割冷却是管子定型的最后一步,这个过程需要特别注意。
管子冷却得太快会导致裂纹,太慢又可能影响生产效率。
冷却后的管子还需要经过切割,切割得太短会导致使用问题,切割得太长则浪费材料。
4. 常见问题与解决办法4.1 生产中的小问题生产过程中,管子如果出现变形、厚薄不均等问题,通常是由于温度、压力或者模具的调整不到位。
这时,就需要检查设备设置,看看是否需要重新校准。
公共基础知识挤出质量控制基础知识概述
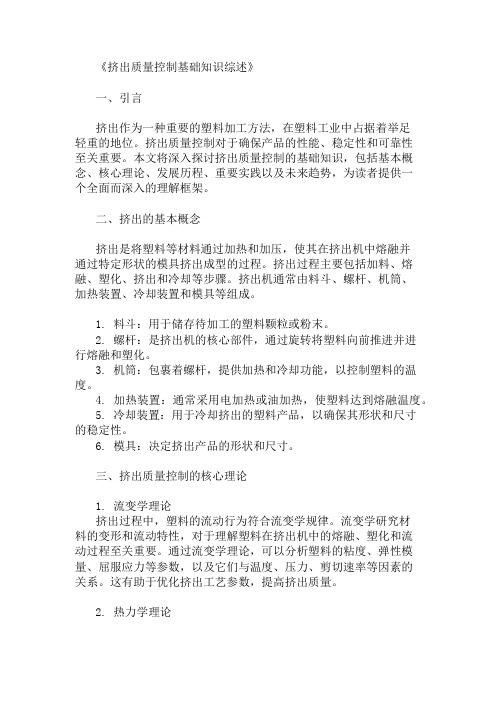
《挤出质量控制基础知识综述》一、引言挤出作为一种重要的塑料加工方法,在塑料工业中占据着举足轻重的地位。
挤出质量控制对于确保产品的性能、稳定性和可靠性至关重要。
本文将深入探讨挤出质量控制的基础知识,包括基本概念、核心理论、发展历程、重要实践以及未来趋势,为读者提供一个全面而深入的理解框架。
二、挤出的基本概念挤出是将塑料等材料通过加热和加压,使其在挤出机中熔融并通过特定形状的模具挤出成型的过程。
挤出过程主要包括加料、熔融、塑化、挤出和冷却等步骤。
挤出机通常由料斗、螺杆、机筒、加热装置、冷却装置和模具等组成。
1. 料斗:用于储存待加工的塑料颗粒或粉末。
2. 螺杆:是挤出机的核心部件,通过旋转将塑料向前推进并进行熔融和塑化。
3. 机筒:包裹着螺杆,提供加热和冷却功能,以控制塑料的温度。
4. 加热装置:通常采用电加热或油加热,使塑料达到熔融温度。
5. 冷却装置:用于冷却挤出的塑料产品,以确保其形状和尺寸的稳定性。
6. 模具:决定挤出产品的形状和尺寸。
三、挤出质量控制的核心理论1. 流变学理论挤出过程中,塑料的流动行为符合流变学规律。
流变学研究材料的变形和流动特性,对于理解塑料在挤出机中的熔融、塑化和流动过程至关重要。
通过流变学理论,可以分析塑料的粘度、弹性模量、屈服应力等参数,以及它们与温度、压力、剪切速率等因素的关系。
这有助于优化挤出工艺参数,提高挤出质量。
2. 热力学理论挤出过程涉及到塑料的加热和冷却,热力学理论可以帮助我们理解塑料的热传递、相变和热稳定性等问题。
通过控制加热和冷却过程,可以确保塑料在合适的温度范围内进行加工,避免过热或过冷导致的质量问题。
3. 机械设计理论挤出机的机械设计对挤出质量也有重要影响。
合理的螺杆结构、机筒设计、模具设计等可以提高塑料的熔融、塑化和挤出效率,减少压力波动和温度不均匀性,从而提高挤出产品的质量。
四、挤出质量控制的发展历程1. 早期阶段在挤出技术的早期阶段,质量控制主要依靠经验和简单的测量工具。
注塑、挤出基本知识
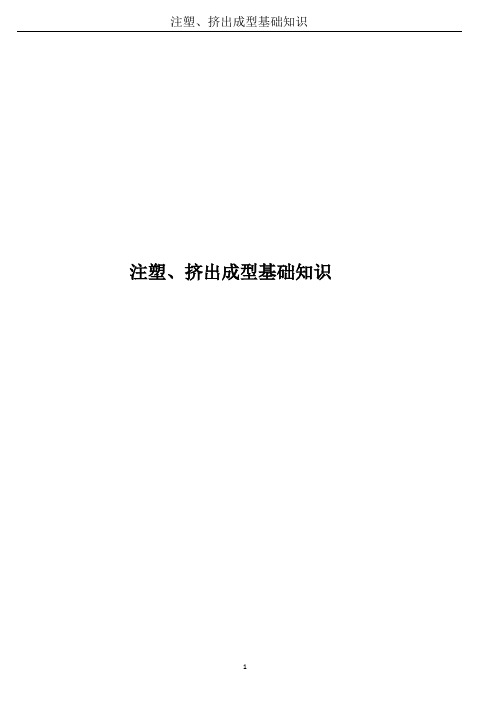
注塑、挤出成型基础知识前言基础耗材事业部是集模具设计与开发、介入导丝、医用管材、介入配件为一体的事业部。
耗材事业部自2012年5月23日成立至今,严格按照公司方针及耗材事业部总经理王建华总经理的要求,对生产过程进行规范和生产。
塑料作为一种新兴材料,发展十分迅速,已成为钢铁、木材、水泥和塑料四大工业材料中发展速度最快的一种材料。
塑料,如何熟悉、了解、认识、应用它,用好它,除及时跟进新兴原料,最重要的还是实际应用体验。
如对品种众多、性能各异的塑料原料如何从不同的需要开发进行合理选择;怎样利用简单实用的方法对塑料制品进行绿色设计;在塑件成型加工时需掌握哪些工艺知识;怎样合理把握工艺参数,保证产品质量等。
结合以往从事塑料加工十余年的工作体会,对常用塑料物性进行整理。
整理内容主要包含以下几点:(1)塑料应用。
(2)塑料的组成和分类。
(3)一般注塑和挤出成型。
受个人水平及能力,书中有不足之处敬请批评指正。
董海军第一章概述第一节塑料特性塑料是以人工合成高分子化合物(又称树脂)为主要成分,添加了各种不同功能的辅助材料(又称助剂,添加剂)后经混炼而成的一种高分子聚合物。
它与树脂是有区别的,但人们习惯上常将两者混淆称呼,,称塑料为合成树脂、合成材料等是不对的。
塑料可用各种性能的树脂和添加剂,通过各种合成和成型加工方法制成各种不同性能的塑料制品,其综合性能与金属、木材、玻璃等传统材料相比,更胜一筹。
在当今结构材料系统中是综合性能优良的一支材料体系。
1塑料的性能优点1.1质轻塑料一般都较轻,其密度在0.83~2.2g/cm³内,多数制品密度0.9~1.5g/cm³,因其密度低可以减轻产品质量,实现小型化及轻量化,提高运行能力,改善操作性和安全性,便于运输携带,提升美观效果,降低能耗及运行成本,减轻料劳动强度。
1.2比强度(比模量)高比强度(比模量)是指塑料的强度(或模量)与密度的比值。
塑料的密度及机械强度、刚性、硬度和弹性可采用填充不同填料、改变结晶取向,改进分子结构等方法在一定范围内进行调节,因此同一种塑料,可获得不同的刚性和强度。
管材挤出成型知识点注释

项目二管材挤出成型知识点注释单元1:管材挤出成型总体认识#塑料管材#是指由塑料制成一定长度的空心圆形制品,这类制品的厚度与长度之比一般都很小。
管材直径最小到几毫米,最大约到1.6米。
#塑料管材挤出成型生产流程#是指管材挤出生产线包括挤出机(extruder)、机头(die)、定型装置、冷却装置(cooling apparatus)、牵引(haul-off)、切割及堆放装置等。
其中硬管和软管挤出成型是管材生产工艺的典型代表。
#塑料管材挤出成型的主要设备#是指包括挤出机(extruder)、机头(die)、定型装置、冷却装置(cooling apparatus)、牵引(haul-off)、切割及堆放装置等设备。
#塑料管材挤出成型的主要工艺参数#是指指塑料管材挤出成型时的熔体温度、压力、定型参数、冷却参数、螺杆转速、挤出速度、牵引速度及管材的在线质量控制与后处理。
单元2:管材挤出成型的机头结构及设计#管材挤出成型机头的作用#管材挤出机头主要有下述四种作用:(1)使物料由料筒内的螺旋运动变为直线运动。
(2)产生必要的成型压力,保证制品密实。
(3)使物料通过机头得到进一步塑化。
(4)通过机头成型所需断面形状的塑料制品。
#管材挤出成型机头的结构组成#由口模和芯模;过滤板(多孔斑、栅板);分流器和分流器支架;机头体(模体);调节螺钉;定径套;橡皮塞组成。
#管材挤出成型机头三段分区#主要分为分流区、压缩区及成型区,如下图所示:#管材挤出成型机头的结构组成#主要分为直通式挤管机头、直角式机头、侧向机头(弯管式)及其他类型机头。
单元3:管材挤出成型的辅助设备#定型装置#是指从机头口模挤出的物料处于熔融状态,形状不能固定,因此需要经过定型装置对熔料加以冷却定型,使其达到管材精整尺寸的装置。
#冷却装置#是指从冷却定型套出来、未得到充分冷却管材,为防止其变形、排出管壁中的余热,使之达到或接近室温的装置。
#牵引装置#是指均匀将管材引出,并调节管壁厚度的装置。
聚乙烯管材的挤出技术

聚乙烯管材的挤出技术来源:ZZ91再生网标签:再生技术,废塑料,技术,聚乙烯1.适用于管材挤出的聚乙烯原料聚乙烯塑料主要分两大类:高密度聚乙烯HDPE(低压聚乙烯)和低密度聚乙烯LDPE(高压聚乙烯),高密度聚乙烯是乙烯单体在低压状态下共聚而成,故又称作低压聚乙烯,低密度聚乙烯是乙烯单体在高压状态下共聚而成,所以又称作高压聚乙烯。
聚乙烯材料的应用非常广阔,管材领域只是聚乙烯应用领域中其中一个重要方面。
由于HDPE和LDPE物理性能上存在差异,所以两种材料在管材应用领域上各有不同:低密度聚乙烯(LDPE)具有良好的柔韧性。
但是,抗压耐压强度较低,所以只能用于低压力小直径的管材,它经常被制作成盘管而用于农村改水和一些非长期使用的场合。
而高压聚乙烯材料由于具有较好的抗压性能,所以HDPE广泛应用于压力管领域(比如给水、供气、城市排水等)。
70年代末,欧美某些化学企业也相继推出了新型的聚乙烯材料MDPE,MDPE 的应用尚在推广阶段,这几种材料在给水管领域的应用比例如下(以欧洲国家的应用为例)近年来,国际标准ISO4427—1996根据管材的最小要求强度(MRS)将管材用聚乙烯材料分为PE32、PE63、PE80、PE100。
也就是说:PE80通俗解释就是:该材料管材在20℃,连续受压50年不破坏,管壁承受最小要求强度是:8。
0Mpa,如此类推。
在塑料管发展的初期,聚乙烯压力管材的使用是远小于聚氯乙烯,其主要原因是受到成本的约束,在早期,聚乙烯管材料主要是PE63,高性能、高强度的聚乙烯管材尚未开发成功,而使用PE63以下的管材料,在同样的压力和直径下,聚乙烯管的管壁比聚氯乙烯管厚一倍以上。
所以其制造成本远比PVC高,而且只能用在低压下小直径领域。
同样是直径Φ200,同样是1Mpa压力等级,PE63管材壁厚是18。
2毫米,而UPVC的管材壁厚是8。
7毫米,也就是说,PE63的管材重量是UPVC管材的1。
第四讲 型材挤出模具的基础知识
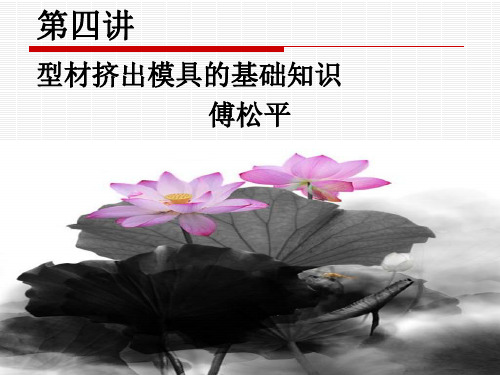
23
模头有关的技术参数和模头的基本结构要素
c.模口间隙:型坯的壁厚主要取决于模口间隙值( 模隙),其次还在一定程度上受配方、物料的塑化 情况、熔体压力、熔体温度、离模膨胀和牵伸比等 的影响。这些条件中任何一个发生变化,都会影响 壁厚的变化。在挤出PVC—U型材采用真空冷却定 型时,在一定范围内可通过调整牵引速度控制制品 的壁厚。
挤出模一般由模头(也称机头)、干式定型模(也称 定型器、定型套)以及湿式定型模(真空定型水箱、 敞式水槽)
16
异型材挤出模具原理和基本知识
17
异型材挤出模具原理和基本知识
18
模具各部分的结构及性能
19
模头的一般技术要求
a.材质与硬度:挤出模具尤其是挤出物料为改性聚氯乙烯的模 具,其成型零件一般采用不锈钢等具有抗腐蚀性的材质,并调 质至HRC 28~32,以保证一定的使用寿命。
压缩角;β扩张角;a'一分流角;β'一收敛角 ③分流角a'和收敛角β'。
第四讲
型材挤出模具的基础知识 傅松平
1
型材挤出模具的基础知识
挤出模具是PVC-U 异型材生产的关键模具 之一,是塑料异型材挤出成型系统中的重要 环节,是挤出生产线中的核心部分,对制品 的形状、尺寸精度、表面质量、理化性能、 挤出效率等都有一定的或决定性的影响。
挤出模具一般由模头(也称机头)、干式定 型模(也称的定型器、定型套)以及湿式定 型模(真空定型水箱、敞式水槽)三部分组 成。
稳态——流道中任何一点流动不随时间而变 化。
层流——出现雷诺准数(Re≤2100)以下的 分层流动。塑料熔体的雷诺数通常小于1。 挤出模头中的熔体流动通常设为层流。等温 一物料粒子在流动过程中都有相同的温度。
- 1、下载文档前请自行甄别文档内容的完整性,平台不提供额外的编辑、内容补充、找答案等附加服务。
- 2、"仅部分预览"的文档,不可在线预览部分如存在完整性等问题,可反馈申请退款(可完整预览的文档不适用该条件!)。
- 3、如文档侵犯您的权益,请联系客服反馈,我们会尽快为您处理(人工客服工作时间:9:00-18:30)。
P E管材挤出模头的一般知识
在目前的管材市场上,PE管材以较高的速度正在赶上和超过PVC管材的用量。
在生产中和现在或将来的项目中很有必要了解生产PE管材的重要部件—挤出模头。
现在常用的两种挤出模头为螺旋芯棒式模头和筛篮式模头。
现就这两种模头分别作以论述,供大家参考。
在管材挤出线中,无论PVC管材还是PE管材,模头对于产品质量都起着非常关键的作用,其作用是使挤出机挤出来的熔融物均匀地通过整个模头断面。
管材模头与挤出产品的要求相适应,对于整条生产线的工作效率与经济性,具有决定性的作用。
对模头的两点基本要求是:
1、模头必须适应所加工的材料;
2、模头必须严格按照挤出量和管材的断面尺寸进行设计。
一、聚烯烃模头的发展过程
对聚烯烃的挤出,从支架式模头发展到后来常用的螺旋式模头和筛篮式模头。
其目的都是尽可能消除由模头支架所引起的合模线,使进入模头的物料很好的混合,熔体更加均化。
1、支架式模头
模头的分流体部分为支架式,生产小口径管材的模头为十字支架式,生产大口径管材的模头多为六条筋或八条筋。
这种模头的最大缺点就是如果前边的压缩段的压力太小的话,合流线有时消除的就不太好。
从而必须有足够高的压力使这些分离的料流再融合。
这要求具有相对高强度的结构,因此模头的整体重量很高。
这种模头一般多用于PVC管材的挤出。
2、带破料板的支架式模头
最简单的方法是将一破料板放在支架之后,由支架所引起的几道料流被分成众多更小的料流。
因此,机械应力从支架部分向前推移,而合模线大体上被大量小的料流消除。
这种PE模头多用于低密度聚乙烯、小口径管材生产中。
以前我公司在西厂生产的低密度PE排水灌溉用管材所用模头就为此种模头。
现在这类模头已经趋于淘汰,在一些私营小厂还在用。
3、螺旋芯棒式模头和筛篮式模头
带破料板的支架式模头在现有的中高密度聚乙烯管材生产中已很少使用。
而多用螺旋芯棒式模头和筛篮式模头。
这两种机头已较好地解决了消除合模线的问题。
螺旋芯棒式模头的核心是螺旋芯棒,筛篮式模头模头的核心部分是带有大量孔眼的管状体,即网叠。
现把这两种常用模头的结构及工作原理分别说明。
二、螺旋芯棒式模头的结构及工作原理
图1??螺旋芯棒式模头的结构及工作原理
螺旋芯棒式模头又叫螺旋分流体模头。
对于螺旋分流体模头,进入模头的熔体料流,首先通过分流体系--有的是若干星型孔或其他分流系统,分流到机头四周。
然后熔体进入螺旋状环绕在芯模外面的流道。
螺旋流道的深度随着靠近模头流出端而逐渐减小。
同时,芯模与模头体型腔之间的间隙则逐渐增大。
在这一区段,料流内部出现轴向与径向流动的重叠。
沿着模头流出方向,径向流动的比例降低,而轴向流动的比例,则持续提高,最终全部的熔体沿轴向流动。
采用这种方式,分流体流道的流动印记沿管材断面四周均匀分布,这就意味着不会出现局部的强度损失。
沿管材断面四周熔体分流的质量受多种因素的影响。
这些因素包括机头的几何尺寸,如流道的数量、流道缠绕扭曲角度、螺旋的螺距、螺槽深度与宽度、间隙宽度、所加工的原料,特别是其粘度,以及挤出量和物料温度。
借助于计算机程序和操作者的经验,可以对螺旋分流体进行优化设计,以适应特定的应用范围。
在这种情况下,壁厚分布非常均匀。
这种模头除了很好地消除合料线外,还在以下几方面有优势:
1、机械应力和热应力较低,制品有良好地机械强度。
2、结构坚固,故适合高粘度材料的挤出,同时模头的装拆和操作简便。
3、芯棒上易钻孔,故易采用内冷系统。
以上的这些优点使螺旋芯棒式模头得到越来越广泛地应用。
这种模头的缺点是:由于其相对复杂的结构,这种类型模头对原料的改变较敏感。
即使是粘度和流变特性的细小变化都会引起螺旋体中流动情况的改变,管径的变化也有相似的影响。
因此,要设计好螺旋的几何形状,使模头具有尽可能宽的加工范围,以适应不同的材料和挤出量。
三、筛篮式模头的结构及工作原理
在筛篮式模头上,料流首先通过支架或带有多星孔的料流分流体系。
紧接着熔体流过多孔区段。
这个元件,即筛篮,在这里料流不是沿轴向流过,而是沿径向从里向外流过。
由于筛篮具有一定的长度,在机头直径较小的情况下,提供了很大的过流面积。
因此,在相对较小的机头尺寸下,多孔区段的压力降低了。
在筛篮区段内,熔体料流两次改变流向,然后变成轴向。
单股料流之间能良好的混合,熔体更加均化。
借助于一个阻滞元件以及相邻的松弛缓冲区,实现料流之间的融合。
由于筛篮的断面面积比较大,筛篮式机头的机头压力要明显低于其他的结构形式。
物料受到的负荷比较小,物料温度也比较低,可以较容易地提高挤出量。
这种机头的最大优点是适应性比较好即使在很高的挤出量时,也能实现良好的均化;管材管径及壁厚的变化,PE原料的型号、物料粘度、背压的变化下,都能生产出高质量的管材。
这种模头的最大缺点是模头内所有物料的融合、生产中清理、拆装模头不如螺旋芯棒式机头好和方便。
我公司现用的PE管生产线是巴登震雄生产的,所用机头为筛篮式机头。
生产实践中可以明显的看出这种机头的适应性较强,无论PE80、PE100还是PE63。
我们另买一专用机头挤出PP-R管材,解决了经常清理机头的不便。
总之,这两种模头各有利弊,建议在选购PE管材模头时,取长补短,根据自己的生产情况选用。
生产原料的牌号不固定,生产量较大,不经常更换管材颜色而清理拆装模头时,最好选用筛篮式模头。
要求管材壁厚较均匀、生产原料的牌号较固定,常更换管材颜色而清理拆装模头时,最好选用螺旋芯棒式模头。