煤气化工序中气化炉系统的节能分析与计算
煤气化工艺节能减排技术及应用

煤气化工艺节能减排技术及应用摘要近几年在可持续发展理念逐渐深入下,节能减排技术逐渐得到各界广泛关注,煤化工领域作为我国一个重要生产领域,若想要保证煤化工企业稳定发展,则需要加强节能减排技术应用,以实现煤炭最大限度利用,为企业发展提供良好前景。
基于此,下文主要分析煤化工领域节能减排技术,并探讨技术应用加强对策。
关键词煤气化工艺;节能减排技术;应用引言煤气化工艺是煤清洁高效处理的关键方式,是煤化工产品生产过程中必要的步骤。
目前,主流应用的煤气化工艺技术为高温高压的气流床气化技术,在气化技术的应用过程中,物料类型会对气化能耗产生一定的影响。
为了降低煤气化工艺的能耗,需要对不同原料煤质下煤气化工艺的能耗情况进行分析。
一、煤化工工艺节能减排技术1、二甲醛合成技术二甲醛能够替代作燃气和柴油进行运用,目前在技术上取得良好效果,应用潜力较大,而且随着二甲醛持续开发,现阶段市场需求也越来越大。
当前二甲醛合成技术主要采用一步法或者二步法方式合成,尽管还没有完全投入到煤化工生产之中,但是经过试验已经证明可行性,能够确保催化反应正常进行,可对操作成本进行科学控制,因此二甲醛合成技术逐渐当作现阶段节能减排技术主流趋势。
2、煤化工联产技术煤化工联产技术是指在煤炭工业生产过程中,将各种关键技术结合起来,实现综合发展。
煤化工联合发电是指在煤炭气化、液化技术的基础上,通过对各种工艺技术的综合优化,达到各种产品的综合利用,从而使工艺能源得到最大程度的发挥。
该技术主要表现出安全稳定以及清洁等特点,由于煤炭成分极为复杂,生产过程比较繁琐,所以联产技术在我国有着广阔的应用前景。
3、甲醛合成技术甲醛主要是无色且带有刺激性气味的一种气体,众所周知甲醛是一种有毒物质,当人体吸入的甲醛气体过量,则会给身体带来较大危害,属于致癌物质。
但是现在,在化学化工行业,甲醛是一种非常普遍的物质,我们可以用它来制造很多常用的产品,比如:多聚甲醛,聚甲醛,氨基树脂等。
煤气化技术及工艺过程中元素平衡分析

煤气化技术及工艺过程中元素平衡分析摘要:介绍了国内应用的典型煤气化技术;无论哪种煤气化工艺,元素平衡始终不变;分析了煤气化工艺过程中元素平衡及来源。
关键词:煤气化技术;元素;来源煤气化工艺是传统和现代煤化工的龙头和基础。
煤气化工艺是指把经过适当处理的煤送入反应器如气化炉内,在一定的温度和压力下,通过氧化剂(空气或氧气和蒸气)以一定的流动方式(移动床、流化床或气流床等)转化成气体,得到粗制水煤气,通过后续脱硫脱碳等工艺可以得到精制水煤气的过程[1]。
随着近几年煤气化工艺的不断发展,特别是国内开发出了多种能适应不同煤种的煤气化工艺。
但无论哪种煤气化工艺,元素平衡始终不能改变[2]。
因此,本文以某种长焰煤为例,分析了煤气化工艺过程中元素平衡及来源。
1煤气化技术大型工业化运行的煤气化技术,可分为固定床气化技术、流化床气化技术、气流床气化技术。
1.1 固定床气化技术在气化过程中,煤由气化炉顶部加入,气化剂由气化炉底部加入,煤料与气化剂逆流接触,相对于气体的上升速度而言,煤料下降速度很慢,甚至可视为固定不动,因此称之为固定床气化;而实际上,煤料在气化过程中是以很慢的速度向下移动的,比较准确的称其为移动床气化。
1.2 流化床气化技术以恩德炉、灰熔聚为代表的气化技术。
它是以粒度为0-10mm的小颗粒煤为气化原料,在气化炉内使其悬浮分散在垂直上升的气流中,煤粒在沸腾状态进行气化反应,从而使得煤料层内温度均一,易于控制,提高气化效率。
流化床气化技术是在温克勒粉煤流化床气化炉的基础上,经长期的生产实践,逐步改进和完善的一种煤气化工艺。
灰融聚流化床粉煤气化技术根据射流原理,在流化床底部设计了灰团聚分离装置,形成床内局部高温区,使灰熔聚气化反应装置灰渣团聚成球,借助重量的差异达到灰团与半焦的分离,在非结渣情况下,连续有选择地排出低碳量的灰渣。
1.3 气流床气化技术目前的主流技术,以GE水煤浆气化技术、四喷嘴水煤浆气化技术、壳牌干煤粉气化、GSP气化技术和航天炉气化技术等为代表。
煤制天然气工艺能耗分析及节能措施探讨

气化炉,减少了中压过热蒸汽的用量。
(2)变换冷却单元对粗煤气的热能进行分级利用,品味高 的热能利用余热回收器副产低压蒸汽,以回收热量;粗煤气低
位热能预热锅炉给水、脱盐水,以节省预热水所耗蒸汽,这样降
低了煤气冷却循环水消耗。
3.3 净化装置 (1)氨压缩的压缩机采用先进的高效离心式压缩机、蒸汽
铵、1#焦油、2#焦油、混合苯,粗酚等,为计算能耗方便,主副产 品产能均折合主产品 1000 Nm3SNG 产品为计算基准,小时天然 气产量为 166.7 Nm3/h。依据《煤制天然气单位产品能源消耗限 额(》GB 30179-2013),计算煤制天然气项目能耗见表 2 所示。
表 2 煤制天然气项目能耗
2. 2
2# 煤焦油
t
- 0. 04997 - 1. 988 - 0. 068
2. 3
混合苯
t
- 0. 01434 - 0. 615 - 0. 021
2. 4
粗酚
t
- 0. 01548 - 0. 305 - 0. 010
2. 5
硫磺
t
- 0. 04139 - 0. 384 - 0. 013
2. 6
硫铵
主 要 工 艺 单 元 装 置 包 括 :空 分 装 置 、煤 气 化 装 置 、净 化 装 置 、甲 烷 化 装 置 以 及 硫 回 收 装 置 等 其 工 艺 装 置 规 模 及 能 力 见 表 1。
表 1 工艺主要装置生产和处理能力
名称
单位
处理能 力
装置系列数
备注
说明
煤气化装置
t/ h
583 16台气化炉
直接影响煤制天然气项目的能耗。在技术选定的情况下,还需
用实际数据计算法计算煤气化指标以评价气化...

Ξ用实际数据计算法计算煤气化指标以评价气化操作的先进性郭 治 何建平(河北理工学院・唐山 063009) (河北冶金工业学校 050091)摘 要 本文介绍以煤气组成等实际数据为基准计算煤气发热量、气化效率、热效率等气化指标的方法,并举例说明。
根据计算结果可评价气化操作的先进性。
关键词 实际数据计算法 煤气化操作先进性1 前 言根据国家陶瓷行业技术政策,到2000年,陶瓷窑炉基本上做到使用洁净的气体或液体燃料,能耗指标将降低一半以上,近年来,许多陶瓷厂正是利用煤为原料,自制发生炉煤气,获得较好的经济效益与社会效益。
但由于自制发生炉煤气在陶瓷行业生产过程中属于较新的工艺技术,因此对正在工作的发生炉是否处于最佳工作状态人们常常认识不足,以至某些工厂生产的煤气从产量到质量出现波动,甚至影响到窑炉的正常生产。
为了对发生炉操作进行全面的综合评价,除了分析了解操作对气化过程影响外[1],,还可通过计算作指导。
实际数据法就是在已知发生炉煤气组成等条件的基础上,主要通过物料平衡与热量平衡,计算得出该炉的煤气发热量、产气量、气化剂耗量、气化效益以及热效率等重要的气化指标,进而以此作为评价发生炉操作先进与否的判据之一,由于计算能量化操作中的重要参数,为调节窑炉提供了重要的参考依据。
2 实际数据计算法实际数据计算法是以原料煤在试验或正式生产时测得的煤气组成为依据的计算。
根据原料煤的工业分析,元素分析及气化剂组成和操作条件等,计算确定煤气发热量、产气量、气化剂耗量、气化效率及热效率等气化指标,为评价气化炉操作或设计选择气化炉提供依据,它是常用的煤气计算方法之一。
211 计算步骤21111 收集和取定基本数据(1) 原料煤的工业分析与热值;(2) 干煤气的组成;(3) 出口煤气中水汽含量;(4) 煤气带出物的数量及组成;(5) 灰渣的组成;(6) 气化炉进出物料的温度;21112 物料衡算(1) 由碳平衡计算煤气产量。
(2) 由氮平衡计算空气耗量。
煤气化工艺流程(德士古气化炉)

激冷水经激冷水过滤器滤去可能堵塞激冷环的大颗粒,送入位于下降管上部的激冷环。激冷水呈螺旋状沿下降管壁流下进入激冷室。
激冷室底部黑水,经黑水排放阀送入黑水处理系统,激冷室液位控制在50--55%。在开车期间,黑水经黑水开工排放阀排向真空闪蒸罐。
在气化炉预热期间,激冷室出口气体由开工抽引器排入大气。开工抽引器底部通入蒸汽,通过调节预热烧嘴风门和抽引蒸汽量来控制气化炉的真空度,气化炉配备了预热烧嘴。
来自煤浆槽浓度为59%-62%的煤浆,由煤浆给料泵加压,投料前经煤浆循环阀循环至煤浆槽。投料后经煤浆切断阀送至德士古烧嘴的内环隙。
空分装置送来的纯度为99.6%的氧气经氧气缓冲罐,控制氧气压力为6.0~6.2MPa,在准备投料前打开氧气手动阀,由氧气调节阀控制氧气流量经氧气放空阀送至氧气消音器放空。投料后由氧气调节阀控制氧气经氧气上、下游切断阀送入德士古烧嘴。
烧嘴冷却水系统设置了一套单独的联锁系统,在判断烧嘴头部水夹套和冷却水盘管泄漏的情况下,气化炉必须立即停车,以保护德士古烧嘴不被损坏。烧嘴冷却水泵设置了自启动功能,当出口压力低则备用泵自启动。如果备用泵启动后仍不能满足要求,则出口压力低低使消防水阀打开。如果还不能满足要求即烧嘴冷却水总管压力低低,事故冷却水槽的事故阀打开向烧嘴提供烧嘴冷却水。五、锁斗系统
三、合成气洗涤系统1、Fra bibliotek统图2、工艺叙述
从激冷水浴出来饱和了水汽的合成气进入文丘里洗涤器,在这里与激冷水泵
送出的黑水混合,使合成气夹带的固体颗粒完全湿润,以便在洗涤塔内能快速除去。
水蒸汽和合成气的混合物进入洗涤塔,沿下降管进入塔底的水浴中。合成气向上穿过水层,大部分固体颗粒沉降到塔底部与合成气分离。上升的合成气沿下降管和导气管的环隙向上经过升气罩折流后,穿过四层冲击式塔板,与冷凝液泵送来的冷凝液逆向接触,洗涤掉剩余的固体颗粒。合成气在洗涤塔顶部经过旋流板式除沫器,除去气体中的雾沫,然后离开洗涤塔进入变换工序。
7-合理优化气化工艺,降低煤气成本消耗

合理优化气化工艺,降低煤气成本消耗王恩伟河南骏化发展股份有限公司随着碳资源的日趋紧张,煤价和电价都有不同程度的攀升,给以固定床间歇式气化工艺的氮肥企业带来了巨大挑战。
为了降低煤气生产成本,提高经济效益,加强煤气化工艺的优化工作显得尤其重要。
我公司目前总氨生产能力已达到50万t/a,煤气化工作在我公司生产中的地位是相当高的。
截止目前,我公司共有造气炉36台,自从2008年4月至今,公司就不停地在分工段进行煤气化改造。
通过改造,目前烧煤棒工艺的气体成分中,CO2含量由原来的11%以上降到了目前的7%以下,CO含量也由原来的25%提高到了30%以上,吨氨消耗由原来的1.7t以上降到了1.4t以下,取得了一定的成绩。
通过这两年的造气改造工作实践,笔者对造气工艺有了一些新的认识和看法,下面做一总结与大家交流。
1 型煤工艺改造为造气工艺水平的提高提供了必要前提我公司原来为碳化煤球工艺,由于煤球的热强度较差,造成带出物较多,使消耗偏高,同时给造气循环水系统带来了较大压力,直接影响了洗气塔的降温除尘效率,使热负荷后移,影响了整个合成氨工艺。
根据生产实际,我公司决定调整型煤工艺,由煤球工艺调整为煤棒工艺。
由笔者自行设计和组织施工新建了三套煤棒生产线,采用低位热能循环利用技术进行烘干,整套工艺实施在争取到国家碳减排资金补助的同时,又节约了大量热源燃料消耗,达到了节能和环保双收益目的。
目前,型煤生产能力已达到60万t/a,成型质量稳定,为造气水平的提高提供了必要前提。
2 煤气化工艺关键设备的选择是降低消耗的基础间歇式气化工艺是一种设备简单、工艺复杂的技术,关键设备尺寸发生微小的变化,都会对整个工艺系统产生较大的影响。
我公司对造气工艺改造非常的重视,专门成立了造气工艺攻关小组,由笔者任组长,经过多次讨论,我们制定了较为详细合理的技改方案。
我们的改造方案包括煤气炉高径比的调整、煤气化传统工艺流程的优化、蒸汽系统的优化、控制系统的优化、油路系统优化等几个方面。
IGCC气化炉性能计算及分析

1. 2 能量平衡计算 本文以气化炉进料到干煤气出口为系统如 图 1。
Y N 2 - 1. 013
对于用干法送煤的气化炉 , 氮平衡为: 空气 中带入氮量 + 煤中氮量 + 送煤的氮量 = 干煤气 中氮量 + 分离出的氮量 即: V k 0. 79+ 0. 8 整理上式有: V k = 1. 266 V g 式中: Y N 2 N2 f N2 s N ar + N 2 s = V g YN ar + N 2f
( 5) 湿煤气产率 V H 2 O V H2 O = V g 式中: 1+ H 2O ( 6)
Y CO 2 , Y CO, Y CH 4
蒸汽的密度, kg/ Bm 3 ;
一般当煤中挥发分小于 10 % 时, 可不考虑 焦油量的影响。即 Cj = 0 。 ( 3) 以氮平衡计算空气耗量 V k 据气化过程前后氮量为衡量有 : 空气中带入 氮量+ 煤中氮量= 干煤气中氮量。即 : V k 0. 79+ 0. 8 整理上式有: V k = 1. 266 Vg N ar = V g YN2 N ar ( 3)
13. 12 g/ 100g 煤 , 温度取 58 # 。 表1
C H N S O A sh 气化压 力/ M P a
气化剂中蒸汽的比热, kJ/ kg ∀# ;
Tb 气化剂中蒸汽温度。 ( 7) 气化剂中空气物理热 Q 4 = l Ck T k 式中: l Ck 空气量; 空气比热 , kJ/ kg ∀ # ; ( 13)
2
炉系统中能量的转化效率, 它与气化炉系统的热 煤气效率相差不很多。
[ 4]
即为气化炉 系统的热
煤气效率 。 式中: K 热量有效回收系数; QR 气化 1 kg 原料煤可回收热量总Байду номын сангаас, Q R = Q 2!+ Q3!+ Q4!。
煤炭气化方法—常压温克勒气化工艺流程及工艺条件和气化指标(煤气化技术课件)
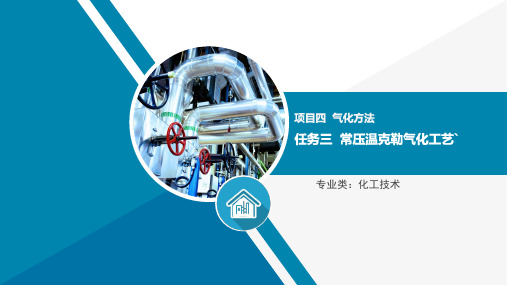
二次气化剂入口
a 单炉生产能力大;
c 可气化细颗粒煤;
e 运行可靠,开停 车容易。
b 气化炉结构简单;
d 出炉煤气基本上 不含焦油;
由于煤的干馏和气化是在相同温度下进行 的,相对于移动床的干馏区来讲,其干馏 温度高得多,所以煤气中几乎不含有焦油, 酚和甲烷的含量也很少,排放的洗涤水对 环境的污染较小。
a 气化温度低
为防止细粒煤粒中灰分在高 温床中软化和结渣,破坏气 化剂在床层截面上的均匀分 布,流化床气化时的操作温 度应控制在900℃左右,所 以必须使用活性高的煤为原 料,并因此限制了煤气产量 和碳转化率的进一步提高。
b 气化炉设备庞大
由于流化床上部固体物料处 于悬浮状态,物料运动空间 比固定床气化炉中燃料层和 上部空间所占的总空间大的 多,故流化床气化时以容积 计的气化强度比固定床时要 小得多。
1)进煤
将0-10mm的原料煤由螺旋加料器加入 圆锥部分的腰部。
加煤口 煤仓 供料螺旋
2)流化
A 炉箅安装在圆锥体部分,炉箅直径 比上部炉膛的圆柱形部分的直径小, 鼓风气流沿垂直于炉箅的平面进入炉 内。这样的结构为床层中的颗粒进行 正规和均匀的循环创造了良好条件。
B 气化剂自炉箅下部供入,由不同高 度的喷嘴环输入炉中。
③ 原料 粒度为0~10mm的褐煤、不黏煤、弱黏煤和长焰煤等均可使用,但要求具 有较高的反应性。 流化床气化时床层温度较低,碳浓度也较低,故不适宜使用低活性、低灰熔 点的煤料。
④二次气化剂用量及组成
气化炉身中部引入的二次气化剂用量和组成须 与被带出的未反应碳量成适当比例。
二次气化剂过少,则未反应碳得不到充分气化 而被带出,造成气化效率下降;
BGL碎煤加压熔渣气化炉运行情况分析

BGL碎煤加压熔渣气化炉运行情况分析摘要:BGL碎煤加压熔渣气化技术是一种煤适应性强、生产能力大、污水少、投资少的新工艺。
该技术较鲁奇气化炉更为先进,特别是污水处理和节省投资。
由于我国目前已经开发出了大量的优质煤,如烟煤、无烟煤,但其发展的空间十分有限,因此BGL碎煤加压熔渣气化技术将是我国褐煤的一种高效、经济的气化工艺。
BGL碎煤加压熔渣气化技术是一种有着广泛应用前景的理想气化工艺。
本文对公司BGL碎煤加压熔渣气化炉运行情况进行分析。
首先阐述了BGL碎煤加压熔渣气化技术工艺及流程,接着分析该技术气化特点,最后对气化炉运行中的制约因素给出解决措施。
关键词:BGL;碎煤加压熔渣;气化炉运行一、BGL碎煤加压熔渣气化炉工艺介绍BGL碎煤熔渣气化技术是20世纪70年代后期出现的一种新工艺。
这是基于英国燃气和德国鲁奇公司在原Lurgi固定床气化炉II、III及IV型的技术基础上研制的液态排渣固定床加压气化技术。
近年来,由于其气化强度高,单炉容量大,蒸汽消耗少,废水少等特点,在我国得到了广泛的重视,并已在工业上得到了推广。
在BGL气化炉内,将最大颗粒直径80毫米、加入了助溶剂(石灰石)的块煤经煤层顶部的煤锁送入气化炉。
在气化炉内,煤炭由上而下,逆流而上,依次经历干燥,干馏,气化,最后燃烧。
在气化炉的底部,由鼓风口向燃烧区喷射出大量的水蒸气和氧气,使其与残余的焦炭发生反应,使其产生局部超过2000摄氏度高温。
如此高的温度足以使灰烬熔化,并为气化反应提供热量。
所产生的原料气体通过气化炉上部集气管的环状空间排出,进入到文丘里洗涤器中洗去煤尘和焦油。
气化炉燃烧所产生的液态熔渣,间断排出炉外。
排出熔渣依次通过连接短接和激冷室,在连接短接和激冷室中,液态熔渣被循环激冷水淬冷,爆裂破碎为粒径3mm的固态渣,最后激冷后的固态渣通过渣锁间断排至渣沟,最终被排渣池来的冲渣水冲入渣池。
下图所示BGL工艺流程简图。
图1 BGL气化炉工艺流程简图二、BGL碎煤熔渣气化技术特点(一)装置投资少结合了高温熔渣气化技术高气化率和高气化强度优势和鲁奇固定床式加压气化技术氧耗低和炉体廉价的优势。
气化炉磨煤系统提效优化探索

气化炉磨煤系统提效优化探索发布时间:2022-08-10T02:05:13.952Z 来源:《建筑实践》2022年第41卷第6期3月(下)作者:刘帅[导读] 煤气化装置采用粉煤气化技术,以煤为原料生产合成气,设计生产有效气(CO+H2)140000m3/h,与之相配套的磨煤系统为3条77.57t/h的磨煤线,两开一备刘帅山东华鲁恒升化工股份有限公司山东省德州市253005摘要:煤气化装置采用粉煤气化技术,以煤为原料生产合成气,设计生产有效气(CO+H2)140000m3/h,与之相配套的磨煤系统为3条77.57t/h的磨煤线,两开一备。
磨煤系统自2008年5月投料试车以来,在长期运行过程中,通过不断技术改造,逐步解决了装置设备故障率较高,设备运转率较低,产品质量稳定性较差等问题,但随着运行周期的增长及国家对能耗、环境等方面要求的提升,磨煤系统逐渐暴露出能耗高、劳动力投入多、设备腐蚀加剧等问题。
关键词:气化炉;磨煤系统;提效优化 1问题分析1.1装置能耗较高煤化工设备配套设施的磨煤机采用中速辊式磨煤机。
生产线设计为两用一备。
干式系统软件立即采用自产自销的合成气。
磨煤机、循环系统离心风机等关键机械设备功率高。
在长期负荷工况下,如果单线不能有效满足制造要求,则被迫运行预留线,当两条线同时运行时,成本将大大增加。
为了获得含水量为1%~2%的煤粉,每条管线将消耗3000m3/h以内的合成气。
同时,合成气中的大量饱和水将被带入系统软件,以提高循环系统中蒸汽体的放空能力,这也增加了动能的消耗和破坏。
1.2磨煤机入口管堵煤严重自开车以来,煤化工设备先后选用了富源煤-贵州煤混合煤、富源煤-贵州精煤混合煤、富源煤-贵州精煤-煅烧石油焦混合煤、富源煤-贵州精煤-烟煤混合煤、富源煤-贵州煤-烟煤混合煤等。
,并多次对原材料结构进行了重大调整,包括青海、甘肃、陕西等地区煅烧石油焦(26~32MJ/kg)烟煤和不同热值的原煤(22~27.5MJ/kg)都增加了原有煤种的局限性。
煤气化工艺节能减排技术及应用
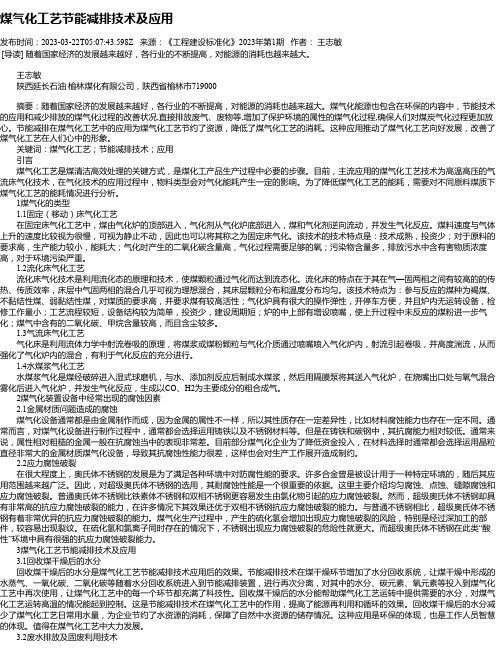
煤气化工艺节能减排技术及应用发布时间:2023-03-22T05:07:43.598Z 来源:《工程建设标准化》2023年第1期作者:王志敏[导读] 随着国家经济的发展越来越好,各行业的不断提高,对能源的消耗也越来越大。
王志敏陕西延长石油榆林煤化有限公司,陕西省榆林市719000摘要:随着国家经济的发展越来越好,各行业的不断提高,对能源的消耗也越来越大。
煤气化能源也包含在环保的内容中,节能技术的应用和减少排放的煤气化过程的改善状况,直接排放废气、废物等,增加了保护环境的属性的煤气化过程,确保人们对煤炭气化过程更加放心。
节能减排在煤气化工艺中的应用为煤气化工艺节约了资源,降低了煤气化工艺的消耗。
这种应用推动了煤气化工艺向好发展,改善了煤气化工艺在人们心中的形象。
关键词:煤气化工艺;节能减排技术;应用引言煤气化工艺是煤清洁高效处理的关键方式,是煤化工产品生产过程中必要的步骤。
目前,主流应用的煤气化工艺技术为高温高压的气流床气化技术,在气化技术的应用过程中,物料类型会对气化能耗产生一定的影响。
为了降低煤气化工艺的能耗,需要对不同原料煤质下煤气化工艺的能耗情况进行分析。
1煤气化的类型1.1固定(移动)床气化工艺在固定床气化工艺中,煤由气化炉的顶部进入,气化剂从气化炉底部进入,煤和气化剂逆向流动,并发生气化反应。
煤料速度与气体上升的速度比较视为很慢,可视为静止不动,因此也可以将其称之为固定床气化。
该技术的技术特点是:技术成熟,投资少;对于原料的要求高,生产能力较小,能耗大;气化时产生的二氧化碳含量高,气化过程需要足够的氧;污染物含量多,排放污水中含有害物质浓度高,对于环境污染严重。
1.2流化床气化工艺流化床气化技术是利用流化态的原理和技术,使煤颗粒通过气化而达到流态化。
流化床的特点在于其在气—固两相之间有较高的的传热、传质效率,床层中气固两相的混合几乎可视为理想混合,其床层颗粒分布和温度分布均匀。
该技术特点为:参与反应的煤种为褐煤、不黏结性煤、弱黏结性煤,对煤质的要求高,并要求煤有较高活性;气化炉具有很大的操作弹性,开停车方便,并且炉内无运转设备,检修工作量小;工艺流程较短,设备结构较为简单,投资少,建设周期短;炉的中上部有增设喷嘴,使上升过程中未反应的煤粉进一步气化;煤气中含有的二氧化碳、甲烷含量较高,而且含尘较多。
煤气发生炉气化过程能量分析与节能降耗的措施

煤气发生炉气化过程能量分析与节能降耗的措施当前常压固定床两段式煤气化技术应用广泛,文章通过分析常压固定床两段式煤气化炉气化过程的能量损失分布,探讨常压固定层煤气发生炉节能降耗的措施。
标签:煤气发生炉;固定床;气化过程;节能降耗引言氧化铝生产能耗是影响氧化铝生产成本的直接因素,能耗高即氧化铝的生产成本相应增加。
在氧化铝生产中气体悬浮焙烧炉以及熔盐炉,其燃料通常采用常压固定床两段式发生炉煤气,煤耗约占氧化铝生产成本的20%。
所以,降低常压固定层煤气发生炉能耗对降低氧化铝生产成本具有重要意义。
文章以型号D3.2BZ-Q型两段式混合煤气发生炉为例分析计算气化过程的能量损失,探讨常压固定层两段式煤气发生炉节能降耗的措施。
1 常压固定层两段式煤气发生炉气化过程及参数原料煤从上面逐渐加入向下移动,气化剂(空气和水蒸气的混合气体)由下面通入,向上移动,它们之间在炉内逆向流动进行热量交换和化学反应。
2 气化过程能量分析2.1 输入的热量气化过程输入的热量包含煤的潜热、煤的显热、蒸汽带入的热量和空气带入的显热四部分。
2.2 输出的热量气化过程输出的热量包含以下方面:辐射及对流的热损失、水套吸收的热量、灰渣显热损失、灰渣中未气化燃料的发热值损失、煤焦油所带出的热量、煤气和煤气产品中水蒸汽热含量的热量。
根据能量守恒定律,输入的热量与输出的热量二者存在平衡关系,Q输入=Q 输出。
要实现常压固定层两段式煤气发生炉的节能降耗可以通过高效利用输入的热量,充分回收输出的热量两方面着手。
3 節能降耗的措施3.1 提高发生炉生产效率,实现低能耗高产气3.1.1 严格控制入炉煤的质量。
固定床两段式煤气炉要严格控制入炉煤的质量,特别要对几个主要参数严格控制,如入炉煤粒度、含矸度、挥发分、固定碳含量、结渣性能、灰熔点、热稳定性、热值等,入炉煤的质量会严重影响发生炉的正常运行,或导致气化效率降低,煤气质量下降。
3.1.2 适当调节最佳饱和温度。
SHELL煤气化炉的工艺计算及结果分析

从 反 应 的 产 物 来 看, CO 2、CO、H 2、H 2O、N 2、 (H 2S+ CO S) 的体积占反应产物体积的 99. 8 % 以 上, 故可以近似地将其它成分忽略不计, 又因为 N 2 和 H 2S 是由反应物料及粉煤输送用气所决定的, 通 过 S、N 平衡可以计算合成气中的N 2 和 H 2S 的体积 分数, 建立以下几个平衡方程式:
流程简述: 原料煤输送至磨煤机, 磨煤机把原料 煤粉碎至合适有效的气化尺寸 (质量分数为 90 % 的 颗粒小于 100 Λm ) , 煤粉碎的同时用惰性气体干燥, 把蒸发后的水蒸气带走, 经内部分离器分级后, 合格 的煤粉被收集在沉降池里, 气化所需要的氧气由空 气装置提供, 空分装置来的氮气经压缩后为输煤系 统提供低压氮气和高压氮气。 干燥后的合格的煤粉 被氮气输送至煤加压及供料系统, 如需要, 加压后的 煤粉、氧气和蒸汽可以通过成对喷嘴进入气化炉, 气 化炉的操作压力为 3. 0 M Pa~ 4. 0 M Pa, 反应温度 高达 1 400 ℃~ 1 700 ℃, 熔渣自气化炉的下部流 出, 与水接触, 形成固体颗粒通过灰锁排出。 温度为 1 500 ℃的出口气体与冷激气混合后, 降至 900 ℃ 进入废锅, 经废热锅炉回收热量, 合成气温度降至 250℃, 再经陶瓷过滤器将合成气中的粉尘降至 3 m g m 3~ 5 m g m 3, 进入水洗塔, 使合成气中的粉 尘含量进一步降至 1 m g m 3 送后工序。
表 1 原料煤的干基组成
原料煤的干基 组成及热值
阳泉一矿
榆 次 古交 桃园
C H O N S 灰分
72. 00 3. 12 2. 77 1. 11 1. 40 19. 99
69. 72 3. 18 3. 24 1. 00 2. 34 20. 52
煤制甲醇工艺设备及能耗分析

煤制甲醇工艺设备及能耗分析发表时间:2017-09-29T09:42:19.343Z 来源:《基层建设》2017年第14期作者:陈伟[导读] 摘要:甲醇是重要的化工产品与原料,并定位于未来清洁能源之一,随着世界石油资源的减少和甲醇生产成本的降低陕西榆林凯越煤化有限责任公司陕西榆林 719000摘要:甲醇是重要的化工产品与原料,并定位于未来清洁能源之一,随着世界石油资源的减少和甲醇生产成本的降低,发展使用甲醇等新的替代燃料,已成为一种趋势。
从我国能源需求及能源环境的现实看,生产甲醇为新的替代燃料,减少对石油的依赖,也是大势所趋。
合成法生产甲醇,以天然气、石油和煤作为主要原料,中国是资源和能源相对匾乏的国家,少气,缺油,但煤炭资源相对丰富,大力发展煤化工,合理开发利用煤炭资源已成共识。
发展煤制甲醇,以煤代替石油,是国家能源安全的需要,也是化学工业高速发展的需求。
关键词:煤制甲醇工艺;设备;能耗随着世界石油资源的匾乏,急需要寻找一种新能源作为替代能源。
我国的煤炭能源储量非常丰富,为了缓解能源紧张的局面,可以通过煤制甲醇的工艺生产新能源甲醇,不仅可以解决能源危机,也可以改善环境污染。
目前,煤制甲醇工艺已经拥有非常完善的生产体系,具备很好的发展前景,煤制甲醇工艺已经成为甲醇生产的主流技术,但是在进行生产的过程中,仍然存在一些能耗、污染问题,所以必须加强煤制甲醇工艺的研究。
本文对煤制甲醇工艺设备及能耗进行针对性分析,希望为完善煤制甲醇工艺提供一些参考意见。
1 煤制甲醇工艺的工序、设备及能耗1.1 煤气化工序在煤气化的过程中,主要是把煤炭放在压力罐中,向灌中加水,把煤炭制作成浆状,然后进行加热和加压,把浆状的煤炭气化。
在这个工序中需要采用的设备是磨煤机、高压煤浆泵、高压、低压及真空闪蒸器、水煤气分离器、变换炉、废热锅炉、水分离器分离冷凝液、锅炉给水加热器、脱盐水加热器。
把工序细分开来可以分为制造煤浆、气化处理、灰水处理和变换工序等几步,在煤炭气化的过程中,会造成大量的煤炭损耗,一些废弃煤渣被排除,能耗最严重的是原煤,氧气和煤浆损耗也相当严重,其他一些能耗包括水、电力能源和水蒸汽。
气化工艺计算(16K)

气化工艺计算:一、计算依据二、计算过程:以100kg无水无灰基为基础。
1、将煤元素分析转化成无水无灰基x r=100x f÷(100-A f-W f) =100x f÷89.335C r H r O r N r S r ΣV r83.75 5.90 6.1611.34 2.85100 46.432、煤的发热量计算:Q r= 80C r + 300H r +10N r +40S r-(O r)2-0.5Vr= 80×83.75+300×5.90+10×1.34+40×2.85-6.162-0.5×46.43 = 8536.24kcal/100kg daf煤3、实际投煤量A r =100Af÷89.335 = 10.8kg/100kg daf煤W r =1.14 kg/100kg daf煤投煤量为100+ A r+W r=111.94kg水煤浆浓度为64.3%加入水量为111.94×35.7/64.3=62.15kg气化炉排渣:10.8×60%÷43%=15.07kg排灰量10.8×(1-60%)×80%=3.46kg4、物料平衡:设入气化炉氧量为x kmol/100kg daf煤出口煤气含CO =a kmol/100kg daf煤H2 =b kmol/100kg daf煤CO2=m kmol/100kg daf煤H2O=h kmol/100kg daf煤CH4=0.0005V kmol/100kg daf煤Σ千克=V kmol/100kg daf煤(1)、碳平衡:入气化炉煤:C入=83.75÷12=6. 98 kmol出气化炉:粗煤气中:C=a+m+0.0005V飞灰中:C= 10.8×40%×20%÷12=0.072 kmo l渣中含:C=10.8×60%×43%÷12=0. 23 k molC入= C出6.98=a+m+0.0005V+0.072+0.23a+m+0.0005V=6.678 ①(2)、氢平衡:入气化炉煤中含H2=5.9÷2=2.95 kmol/100kg daf煤煤中水含H2=100×1.02÷89.335÷18=0.06 kmol/100kg daf煤煤浆中水含H2=62.15÷18 = 3.45 kmol/100kg daf煤H入=2.95+0.06+3.45=6.46出气化炉:煤气中H2=b kmolCH4中H2=0.0005V×2=0.001V kmolH2S中含H2=2.85÷34=0.08 kmol水蒸汽中含H2=h kmolH出=b+0.001V+0.08+hH入=H出6.46= b+0.001V+0.08+hb+0.001V+h=6.38 ②(3)、氧平衡入气化炉氧入炉氧气:0.996x kmol煤中含O2=6.16÷32=0.19 kmol煤中H2O中O2=1.14÷(18×2)=0.03 kmol煤浆中H2O中O2=62.15÷(18×2)=1.73 kmolO入=0.996x+0.19+0.03+1.73=1.95+0.996x出气化炉CO含O2=0.5aCO2含O2= m蒸汽中含O2=0.5hO出=0.5a+m+0.5hO入=O出1.95+0.996x=0.5a+m+0.5ha+2m+h-1.922x=3.9 ③(4)、出口干气平衡CO =a kmol/100kg daf煤H2 =b kmol/100kg daf煤CO2=m kmol/100kg daf煤CH4=0.0005V kmol/100kg daf煤N2=1.34÷28=0.047H2S=2.85÷34=0.084Ar=0.004xV=a+b+m+0.0005V+0.047+0.084+0.004xa+b+m-0.9995V-0.004x=-0.131 ④(5)水煤气反应在3.0MPa及1350℃时反应平衡常数取0.53709mb=0.53709ah ⑤5、热量平衡:以0℃为基准A、求ΣQ输入(1)、煤的热值Qr=8536.24kcal输入热量:8536.24×100=853424 kcal/ 100kg daf煤(2)、煤带入显热量:c p煤’=0.265 kcal/kg.℃Q’煤= c p煤’×100×25=662.5 kcal/ 100kg daf煤灰带入热量:c’’=0.23 kcal/kg.℃Q’灰=0.23×10.8×25=62.1 kcal/ 100kg daf煤煤中水带入热量:c’水=1 kcal/kg.℃Q’水=1.14×1×25=28.5 kcal/ 100kg daf煤煤浆中水的显热Q水=62.15×1×25=1553.75kcal/ 100kg daf煤(3)、氧气的显热4.0MPa,35℃时c o2=0.977kJ/kg=7.30kcal/kg.℃Q O2=7.3x×35=270.1x kcal/ 100kg daf煤Q输入=855930.82+270.1xB、求ΣQ输出热(1)、Q煤气干煤气带出热CO H2H2S CH43034 3052 6100 9527Q煤气=22.4×(3034a+3052b+6100×0.084+9527×0.0005V)=67691.6a+68364b+11477.76+106.7V(2)、煤气的显热1350℃时CO CO2CH4 H2H2S N2Cp 7.78 12.41 16.23 7.25 9.7 7.69Q显热=1350×[7.78a+7.25b+12.41m+16.23×0.0005V+9.7×0.084+7.69×(0.047+0.004x)]=10503a+9787.5b+16753.5m+10.96V+41.53x+1587.91(3)、水蒸汽的潜热Q=597h(4)、水蒸汽的显热Q=13095h kcal/ 100kg daf煤(5)、灰渣带出显热Cp灰=0.262kcal/kg.℃Q灰=10.8×0.262×1350=3819.96 kcal/ 100kg daf煤(6)、灰渣和飞灰中未燃尽碳热量:Cp碳=0.404 kcal/kg.℃Qr碳=8536.24Q渣碳=10.8×60%×0.43/0.57×(0.404×1350+8536.24)= 44394.88 kcal/ 100kg daf煤Q飞灰=10.8×40%×0.2/0.8×(0.404×1350+8536.24)=9808.17kcal/ 100kg daf煤(6)、热损失:全部热损失按1%Q损=8536.24×1%=853.624kcal/ 100kg daf煤ΣQ输出=78194.6a+78151.5b+16753.5m+117.66V+13692.3h+41.53x+79544.92ΣQ输入=ΣQ输出78194.6a+78151.5b+16753.5m+117.66V+13692.3h-2285.7x=776385.93 ⑥以上物料平衡及热量平衡整理得如下方程组:a+m+0.0005V=6.678 ①b+0.001V+h=6.38 ②a+2m+h-1.922x=3.9 ③a+b+m-0.9995V-0.004x=-0.131 ④mb=0.53709ah ⑤78194.6a+78151.5b+16753.5m+117.66V+13692.3h-2285.7x =776385.93 ⑥解方程组得:1 0 0 0 0 42.8857 146.050 1 0 0 0 -40.8529 -130.1690 0 1 0 0 40.8937 136.670 0 0 1 0 -42.8653 -139.350 0 0 0 0 40.8489 -123.398a=146.05-42.8857xb=-130.169+40.8529xh=136.67-40.8937xm=-139.35+42.8653xV=-123.398+40.8489x代入mb=0.53709ah809.25x2-4916.81x+7418.38=0x1=3.286 kmolx2=2.789 kmol (舍去)最后得:a=5.128 kmolb=4.07 kmolh=2.29 kmolm=1.505 kmolV=10.8394 kmol一、煤耗:每1000m3煤气耗无水无灰基煤100÷242.592×1000=412.214 kg转化为无外水煤为:412.214÷0.89335=461.4258 kg 含8%外水的煤为:461.4258÷(1-0.08)=501.55 kg 每1000m3(CO+H2)消耗煤,煤气中CO+H2=83.62% 501.55÷83.62%=599.80kg二、氧耗:每100kg daf煤耗氧气为3.286kmol=73.61m3每1000m3煤气消耗氧为:501.55÷100×73.61=441.5m3。
基于单耗分析理论的IGCC系统节能分析

基于单耗分析理论的IGCC系统节能分析【摘要】以热力学第二定律为基础,应用单耗分析理论,对整体煤气化联合循环系统进行了分析和计算,建立了各主要设备的(火用)分析模型及单耗计算公式.以典型的案例为基准,计算了该系统的附加单耗分布情况,找出了整体煤气联合循环系统中薄弱环节,为系统的节能降耗提供理论指导,为设备及系统的优化提供方向.【关键词】整体煤气化联合循环;(火用);单耗分析;节能目前,能源资源和环境污染问题已经严重制约着我国经济社会的可持续发展。
我国煤炭资源相对丰富,煤现在是、将来(直到2050年或更晚)仍将是我国一次能源的主力[1]。
但目前燃煤发电存在污染严重,煤耗高等严重问题。
无法满足当今世界追求节能环保的需求.因而发展新型的清洁煤电技术显得尤为重要和迫切。
整体煤气化联合循环(integrated gasification combined cycle, igcc)系统是一种高效的洁净煤发电技术,被国际公认为21世纪最具发展潜力的煤电技术。
然而,传统的燃煤发电技术相比,igcc还不够成熟,比投资费用及发电成本较高,系统还存在较大的节能空间,系统还有待于进一步完善。
1 单耗分析理论单耗分析理论是建立在热力第二定律(火用)分析基础之上的能量分析理论和方法;它以煤耗作为单一分析指标,将产品(电能)的单耗分为理论最低单耗和附加单耗;理论最低单耗为产品蕴含的(火用)值与燃料所蕴含的(火用)值的比值[2]。
理论最低单耗:bmin= (f/ef)/(p/ep)其中,bmin——理论最低单耗f——燃料总(火用)值p——产品总(火用)值ef ,ep——单位燃料和单位产品的比(火用)在没有任何附加损失的理想系统中有:f = p,则bmin=ep / ef在实际系统中,不可避免的存在着各种附加损失,限于篇幅,这里省略附加单耗的推导过程,直接给出计算公式:bi= [( ep / ef)/p] / [eiin - eiout]其中,bi——设备i的附加单耗eiin,eiout——设备i的进口(火用)和出口(火用)2 igcc系统的(火用)平衡分析2.1 空分装置δeasu= ma1eas + maseas - m0e0 - mded - mnen其中,δeasu——空分系统的(火用)损kwma1, mas,m0,md, mn——空分系统各进出口的物流量kg/s eas, eas,e0,ed ,en——空分系统各进出口物流的单位(火用)kj/kg2.2 气化炉δegas = mcqhc + m0e0+ mses – mslagqslag – mfef其中,δegas——气化炉的(火用)损kwqhc——煤的高位发热量kj/kgqslag——炉渣的高位发热量kj/kgmc, m0,ms,mslag,mf——气化炉各进出口物流量kg/se0,es ,ef——气化炉各进出口物流单位(火用)kj/kg图1 空分及气化系统图2 燃气轮机系统2.3 压气机δeco = ma2ea2 – mcec - maseas + wc其中,ma2 = mas + mc,若为独立空分时,则mas = 0,这时,δec = mc (ea2 - ec ) + wcδeco——压气机(火用)损kwwc——压气机消耗轴功kwma2,mc,mas——压气机各进出口物流量kg/sea2 ,ec,eas——压气机各进出口物流单位(火用)kj/kg 2.4 燃烧室δecc = (mc-mas )ec + ef - mtet其中,δecc——燃烧室(火用)损kwmc,mas ,mt——燃烧室各进出口物流量kg/sec ,et——燃烧室各进出口物流单位(火用)kj/kgef——净化煤气的燃料(火用)kw2.5 燃气透平:δegt = mtet -meee -(wgt + wc)其中,δegt——透平(火用)损kwmt,me——透平进出口物流量kg/set ,ee——透平进出口物流单位(火用)kj/kgwgt——透平输出功kw图3 余热锅炉及蒸汽轮机系统2.7 余热锅炉δeh = mwew +me (ee - estack) - mstest其中,δeh——余热锅炉(火用)损kwmw,me ,mst——余热锅炉各进出口物流量kg/sew ,ee ,estack,est——余热锅炉各进出口物流单位(火用)kj/kg2.8 蒸汽轮机δest = mst(est -eout) -wst其中,δest——蒸汽轮机(火用)损kwwst——蒸汽轮机输出功kwmst——蒸汽轮机进气蒸汽流量kg/sest ,eout——蒸汽轮机进出口物流单位(火用)kj/kgbst = bmin[mst(est –eout)–wst]/(wst+wgt)3 案例计算3.1 案例分析根据以上平衡模型以及附加单耗公式,以某典型f级igcc系统为例,计算各主要设备的附加单耗分布情况。