传统电弧炉炼钢能实用技术
电弧炉高效低耗炼钢技术阐述

电弧炉高效低耗炼钢技术阐述1、电弧炉炼钢的发展及现代电弧炉炼钢的概念自上世纪中叶至今,虽然转炉炼钢技能取得了长足的进步,但国际电炉的钢比例不断增加,从1950年的7.3%增加到2003年的33.1 %,其中美国从6.2%增加到48.9% ,2004年美国电炉钢比例达53%。
自1950年以后,电弧炉炼钢所占比例迅速上升,变成了与转炉流程相抗衡的第二大钢铁制造流程,主要原因有:(1)平炉炼钢由氧气转炉炼钢所代替,积累的废钢转由电弧炉炼钢流程来消化。
(2)超高功率电弧炉炼钢技能的成功使用,使电弧炉炼钢的功率显著进步,出产成本大幅度下降。
(3)连铸、连轧技能的成功使用,废钢-电弧炉炼钢-连轧型的“小钢厂”敏捷发展,占据了型材出产比例。
就电弧炉炼钢的现在的技能和化学能利用技能的长足进步,冶炼周期已由60min进入50-40min,因此其出产节奏已迫近转炉水平。
1993年6月,殷瑞钰和徐匡迪教授在上海召开了“当代电炉流程与工程疑问的研讨会”。
在会上,他们依据上世纪8O年代以来电炉炼钢技能的发展状况,提出了现代电炉炼钢一词及总结了现代电炉炼钢的特征。
现代电弧炉炼钢的特征总结为:高效、节能、环保、电炉出产节奏转炉化,钢的二次精粹在线化和钢的凝结进程接连化,建立在接连轧制基础上的商品专业系列化和可持续发展。
其中现代电弧炉炼钢的首要特征即是:高效低耗。
多项现代电弧炉高效低耗炼钢技能在中国得到了研讨、推行及使用与长足的发展。
2、现代电弧炉高效低耗炼钢技术在我国的应用2.1优化电弧炉炉料结构电弧炉炼钢主要固态炉料有废钢、生铁、直接还原铁(DRI)和热压块铁(HBI)等。
废钢基本来源有三种:自产废钢、加工厂废钢、循环旧废钢。
炉料结构对电弧炉炼钢的各项指标都有重大影响。
优化炉料结构不只有利于完成技能的最好化,并能给公司带来经济效益,更可以为合理的使用有限的资本提供牢靠的根据。
天津钢管公司炼钢厂具有国内容量较大的炼钢电弧炉,并且是当前我国为数不多的长时间倾加直接还原铁的电弧炉炼钢厂,研讨其炉料的构造对我国电弧炉炼钢铁源的拓宽有重要的指导意义。
炼钢用电弧炉主要技术参数
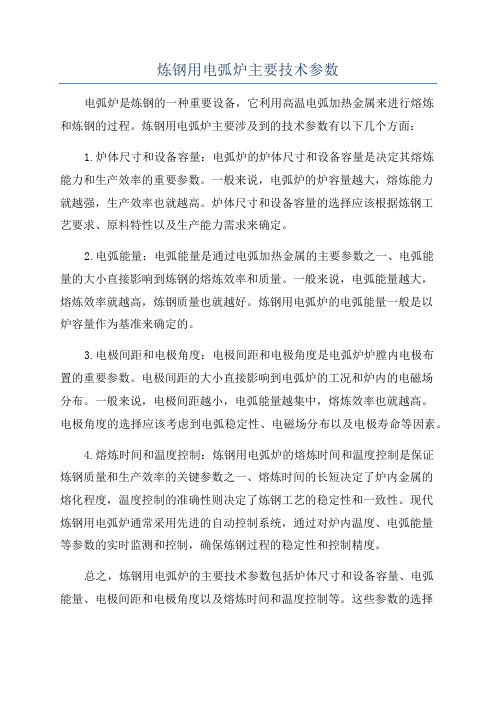
炼钢用电弧炉主要技术参数电弧炉是炼钢的一种重要设备,它利用高温电弧加热金属来进行熔炼和炼钢的过程。
炼钢用电弧炉主要涉及到的技术参数有以下几个方面:1.炉体尺寸和设备容量:电弧炉的炉体尺寸和设备容量是决定其熔炼能力和生产效率的重要参数。
一般来说,电弧炉的炉容量越大,熔炼能力就越强,生产效率也就越高。
炉体尺寸和设备容量的选择应该根据炼钢工艺要求、原料特性以及生产能力需求来确定。
2.电弧能量:电弧能量是通过电弧加热金属的主要参数之一、电弧能量的大小直接影响到炼钢的熔炼效率和质量。
一般来说,电弧能量越大,熔炼效率就越高,炼钢质量也就越好。
炼钢用电弧炉的电弧能量一般是以炉容量作为基准来确定的。
3.电极间距和电极角度:电极间距和电极角度是电弧炉炉膛内电极布置的重要参数。
电极间距的大小直接影响到电弧炉的工况和炉内的电磁场分布。
一般来说,电极间距越小,电弧能量越集中,熔炼效率也就越高。
电极角度的选择应该考虑到电弧稳定性、电磁场分布以及电极寿命等因素。
4.熔炼时间和温度控制:炼钢用电弧炉的熔炼时间和温度控制是保证炼钢质量和生产效率的关键参数之一、熔炼时间的长短决定了炉内金属的熔化程度,温度控制的准确性则决定了炼钢工艺的稳定性和一致性。
现代炼钢用电弧炉通常采用先进的自动控制系统,通过对炉内温度、电弧能量等参数的实时监测和控制,确保炼钢过程的稳定性和控制精度。
总之,炼钢用电弧炉的主要技术参数包括炉体尺寸和设备容量、电弧能量、电极间距和电极角度以及熔炼时间和温度控制等。
这些参数的选择和控制对于炼钢工艺的效果和产能都有重要影响,因此必须经过精心的设计和调整,以满足生产的要求和提高炼钢效率。
炼钢先进工艺技术

炼钢先进工艺技术炼钢是制造钢材的重要过程,也是钢铁工业的核心环节之一。
随着科技的发展和工艺技术的不断改进,炼钢过程也在不断更新和完善。
现代炼钢先进工艺技术不仅提高了生产效率,降低了成本,还改善了产品质量和环境保护。
首先,在炼钢的先进工艺技术方面,电弧炉技术是其中的重要代表。
电弧炉是通过电弧放电熔解钢铁废料、生铁等原料的一种设备。
相比于传统的转炉炼钢工艺,电弧炉炼钢不仅操作简单,能够适应多种原料,而且能够迅速调整合金成分,提高产品的质量稳定性。
而且,电弧炉炼钢还具有能量利用率高、烟尘排放少等优点,有利于环境保护和可持续发展。
其次,氧气炼钢技术也是炼钢先进工艺的重要组成部分。
氧气炼钢是通过向炉内注入纯氧气,将炉内的碳和杂质氧化,从而达到脱碳和脱杂的目的。
相比于传统的鼓风炉炼钢工艺,氧气炼钢具有操作简单、能耗低、炉温容易控制等优点。
氧气炼钢技术的应用不仅提高了炼钢效率,还能够降低能源消耗,减少了废气排放,对节能减排和环境保护具有重要意义。
第三,连铸技术也是炼钢先进工艺的重要发展方向。
连铸技术是将炼钢后的液态钢直接连续铸造成坯料的一种工艺。
相比于传统的铸锭铸造技术,连铸技术具有铁液利用率高、产品质量稳定、生产效率高等优点。
同时,连铸技术还能够减少二次加热,降低能耗,提高生产效率,实现钢材生产的高度自动化和智能化。
而且,连铸技术还具有能源和资源节约的特点,具有较大的经济和环境效益。
总之,炼钢先进工艺技术的不断发展和应用为钢铁工业的发展提供了有力保障。
电弧炉、氧气炼钢和连铸技术的应用不仅提高了炼钢效率,降低了生产成本,还改善了产品质量和环境保护。
未来,随着科技的不断进步,炼钢技术还将不断创新和完善,为钢铁工业的可持续发展贡献更多力量。
国内外电炉炼钢技术现状与发展趋势
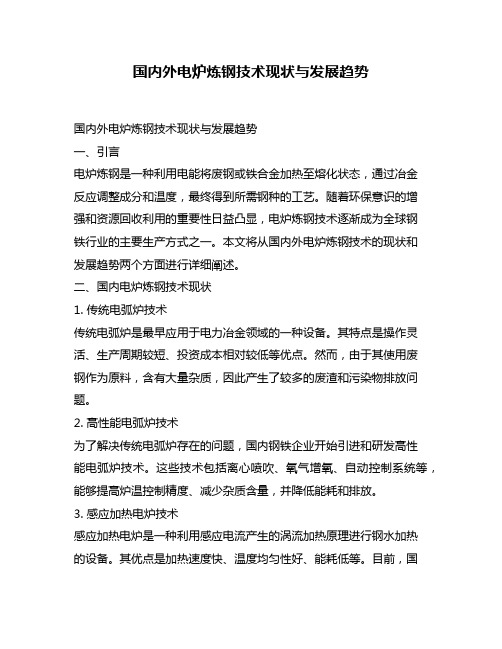
国内外电炉炼钢技术现状与发展趋势国内外电炉炼钢技术现状与发展趋势一、引言电炉炼钢是一种利用电能将废钢或铁合金加热至熔化状态,通过冶金反应调整成分和温度,最终得到所需钢种的工艺。
随着环保意识的增强和资源回收利用的重要性日益凸显,电炉炼钢技术逐渐成为全球钢铁行业的主要生产方式之一。
本文将从国内外电炉炼钢技术的现状和发展趋势两个方面进行详细阐述。
二、国内电炉炼钢技术现状1. 传统电弧炉技术传统电弧炉是最早应用于电力冶金领域的一种设备。
其特点是操作灵活、生产周期较短、投资成本相对较低等优点。
然而,由于其使用废钢作为原料,含有大量杂质,因此产生了较多的废渣和污染物排放问题。
2. 高性能电弧炉技术为了解决传统电弧炉存在的问题,国内钢铁企业开始引进和研发高性能电弧炉技术。
这些技术包括离心喷吹、氧气增氧、自动控制系统等,能够提高炉温控制精度、减少杂质含量,并降低能耗和排放。
3. 感应加热电炉技术感应加热电炉是一种利用感应电流产生的涡流加热原理进行钢水加热的设备。
其优点是加热速度快、温度均匀性好、能耗低等。
目前,国内一些大型钢铁企业已经开始采用感应加热电炉进行生产。
三、国外电炉炼钢技术现状1. 电弧顶吹转底吹技术欧洲一些先进的钢铁企业采用了电弧顶吹转底吹技术,即在高温下通过底部喷吹气体将冶金反应进行到底部。
这种技术可以提高冶金反应效率,减少杂质含量,并且可以利用多种原料进行冶金。
2. 水冷壳体技术美国的一些电炉炼钢企业采用了水冷壳体技术,通过在电炉壳体内部设置水冷设备,有效降低了电炉温度,减少了能耗,并且延长了设备寿命。
四、国内外电炉炼钢技术发展趋势1. 环保型电炉技术随着环保意识的增强,国内外钢铁企业开始重视电炉炼钢过程中的排放问题。
未来的发展趋势将是开发和应用更加环保的电炉技术,减少废气、废水和固体废弃物排放。
2. 智能化控制系统随着信息技术的快速发展,智能化控制系统在电炉炼钢领域得到了广泛应用。
未来的发展趋势将是进一步提高控制精度和自动化程度,实现智能化生产。
电弧炉冶炼不锈钢的作用
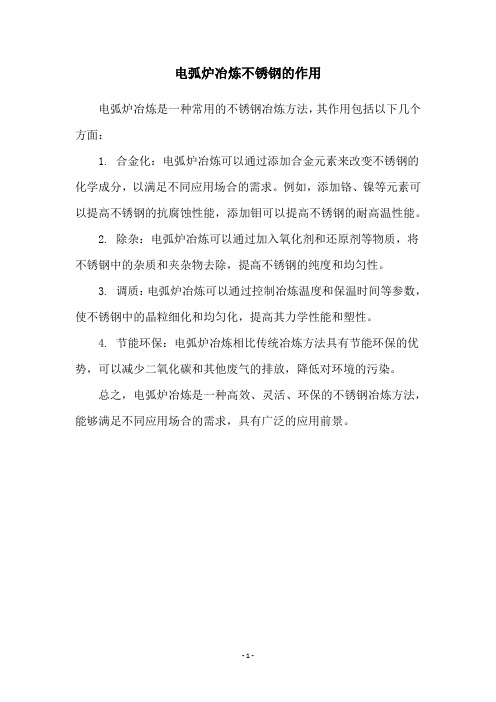
电弧炉冶炼不锈钢的作用
电弧炉冶炼是一种常用的不锈钢冶炼方法,其作用包括以下几个方面:
1. 合金化:电弧炉冶炼可以通过添加合金元素来改变不锈钢的化学成分,以满足不同应用场合的需求。
例如,添加铬、镍等元素可以提高不锈钢的抗腐蚀性能,添加钼可以提高不锈钢的耐高温性能。
2. 除杂:电弧炉冶炼可以通过加入氧化剂和还原剂等物质,将不锈钢中的杂质和夹杂物去除,提高不锈钢的纯度和均匀性。
3. 调质:电弧炉冶炼可以通过控制冶炼温度和保温时间等参数,使不锈钢中的晶粒细化和均匀化,提高其力学性能和塑性。
4. 节能环保:电弧炉冶炼相比传统冶炼方法具有节能环保的优势,可以减少二氧化碳和其他废气的排放,降低对环境的污染。
总之,电弧炉冶炼是一种高效、灵活、环保的不锈钢冶炼方法,能够满足不同应用场合的需求,具有广泛的应用前景。
- 1 -。
金属冶炼技术突破实现高效能源利用的关键方法

金属冶炼技术突破实现高效能源利用的关键方法金属冶炼是现代工业中不可或缺的一部分。
然而,传统的金属冶炼方法过程繁琐、能源消耗大,对环境造成了严重的污染。
为了实现高效能源利用,突破传统金属冶炼技术的限制,许多创新方法不断涌现。
本文将探讨几种关键方法,帮助金属冶炼行业实现高效能源利用。
1. 电弧炉冶炼技术电弧炉冶炼技术是一种基于电能转化的高效能源利用方法。
相较于传统的炼铁和炼钢方法,电弧炉冶炼技术具有许多优势。
首先,它可以利用废旧金属进行再生冶炼,减少资源浪费。
其次,电弧炉冶炼技术具有灵活性,可以适应各种金属的冶炼需求。
最重要的是,该技术不需要预先生产铁和焦炭,减少了能源的消耗。
因此,电弧炉冶炼技术被认为是实现高效能源利用的重要方法之一。
2. 高温燃烧技术高温燃烧技术是另一种实现高效能源利用的重要方法。
在金属冶炼过程中,燃料的燃烧提供了必要的热能。
然而,传统的燃烧技术存在能源利用率低的问题。
为了解决这一问题,一种被广泛使用的方法是采用高温燃烧技术,例如高温炉和高温氧燃烧。
这些技术可以提高燃烧效率,减少燃料的用量,从而实现高效能源利用。
此外,高温燃烧技术还可以减少污染物的排放,改善环境质量。
3. 废热回收技术废热回收技术是另一个可以实现高效能源利用的关键方法。
在金属冶炼过程中,大量的热能被散发到周围环境中。
传统的金属冶炼工厂通常只利用了一小部分的热能,而大部分则被浪费。
通过采用废热回收技术,可以将这些被浪费的热能重新利用。
废热回收技术基于热交换原理,将烟气、冷却水等与高温焚烧煤炭或气体的热交换,从而回收并利用了这些废热。
这种技术可以大幅提高能源利用效率,减少能源消耗。
4. 先进金属冶炼设备除了创新的技术方法,引进先进的金属冶炼设备也是实现高效能源利用的关键。
先进设备能够通过提高冶炼过程的自动化程度和控制精度,有效减少能源的浪费。
例如,采用先进的传感器和控制系统,可以实现精确的温度控制,避免能源的过度消耗。
电弧炉炼钢技术讲座(终稿)

系统与环境一起构成更大系统,因此系统的 优化取决于更大系统所确定的目标和约束,即资 源、产品、市场和环境。
冶金工程系统构成
物质流 能量(流) 信息流―― 风、水、电、气、汽 财务(资金流)
冶金工程的过程系统特征
过程工业和制造工业 工业:大规模制造、可重复、稳定的进行(不
希望变异) 过程工业:Process Industry 化工、石油、冶
机械加工,外形物理变化
(5)放大规模生产Scale-up 生产线
(6)污染重、能耗大、负荷大 环境、负荷轻
过程系统
过程系统工程定义: 处理物质流/能量流的系统。
过程工业: 原料经过一系列单元工序转化为产品的工业。
1.3 炼钢生产的高效化和洁净化
现代炼钢技术处于理性发展,氧气转炉炼 钢和电弧炉炼钢是两种最主要的炼钢方法,技 术进步的共同趋势是高效化和洁净化。
• 电炉炼钢采用废气预热废钢,节电100kWh/t; • 减少炼钢渣量50%; • 全部粉尘回收利用。
• 采用脱Si工艺,减少渣量
技 • 推广煤气回收工艺技术
术 措
• 开发电炉废钢预热技术
施 • 精炼渣炼钢返回利用技术
• 粉尘回收处理技术
1.4 两类钢铁生产流程
当前主要的两类钢铁生产流程及其单元工序
电炉流程与转炉流程在钢铁循环以及社会中的地位与功能
两种炼钢方法共同点
(1)工序产品——合格钢水 (2)工序功能——以给定的生产率和节奏提供成分和温
度合格的钢水 (3)工序指标——三高两洁净
高 效 化——高的生产率、高的生产节奏、高的 能量利用
洁 净 化——钢液的洁净化(低的内在污染) 环境的洁净化(低的外部污染) (4)操作要求:精料、稳定、精确 (5)智能控制技术
电弧炉炼钢工艺简介与控制技术

保护和信号回路
检测计量显示回路
电极升降自动调节回路
电弧炉机械设备供电线路
(电磁电弧搅炉炼拌钢线工艺路简介)和控制技术
高压电源
隔离开关
断路器 变压器一次侧 炉用变压器 变压器二次侧母线
变压器二次侧
测量仪表用变压器 电炉控制盘 电极自动调节器
电弧炉
电极升降机构
主电路接线图 电弧炉炼钢工艺简介和控制技术
穿井期 d极→炉底
主熔化期 熔末升温期
炉底→电 弧暴露
电弧暴露 →全熔
必要条件 保护炉顶 保护炉底 快速熔化 保护炉壁
办
较低电压 较低电流 较大电压 较大电流 最高电压 最大电流 低电压 大电流
法 炉顶布 轻废钢 石灰垫
底
水冷+ 泡沫渣
电弧炉炼钢工艺简介和控制技术
典型的供电曲线
电弧炉炼钢工艺简介和控制技术
还原期→出钢(浇铸成钢锭或钢坯) 优点: 氧化期用加矿或吹氧进行脱C和脱P,使熔池沸腾,可以去除
钢中气体和杂质。 还原期可以脱O、脱S及调整成分和温度。 可得到含P、气体和夹杂物都很低的钢。 可用廉价废钢为原料,适合冶炼[P]高、锈多、[C]较高
的钢铁料,应用最广泛。 缺点: 若炉料中有合金返回料,则其中合金元素氧化烧损较大。
按废钢预热方式
运输机上料 半连续废钢预热 分批熔炼
Comelt Consteel(连续加料) Fuchs(指条式竖炉) ConArc、 ContiArc IHI式双电极直流
运输机上料 连续废钢预热 Mid-shaft EAF 竖炉(竖井在炉顶中央) 连续电弧熔炉炼炼钢工艺简介和控制技术
6.1 电弧炉炼钢技术概述
出钢槽 轨梁 基础
电极夹持器 电极 悬臂式平台 炉盖 炉体 炉门
30吨电弧炉炼钢工艺及经济性分析

30吨电弧炉炼钢工艺及经济性分析电弧炉炼钢是一种主要采用电力作为能源,利用电弧、高温和高温气流熔化废钢或生铁,然后加入一定量的合金元素进行冶炼的工艺。
电弧炉炼钢工艺相对简单,能耗较低,对环境污染少,且可适用于废钢资源的回收利用,因此受到了广泛的应用。
首先,30吨电弧炉炼钢需要的设备包括电弧炉本体、转炉置换设备、输渣车、自动翻驳设备、连铸设备等,其中电弧炉本身是核心设备,由电极、电弧炉炉体、喷煤装置、喷吹探头系统等组成。
炉膛内,废钢和生铁等原料通过炉篦装置进入炉膛,经过预熔、熔化、冶炼、升温和增碳等环节,最终得到合格的钢水。
其次,30吨电弧炉炼钢工艺主要包括预处理、炉蜕皮、下蜕成炉、炉蜕皮成炉、出钢、出渣等步骤。
预处理是指将废钢、生铁等原料进行除杂、分选、切割等操作,确保入炉的原料质量合格。
炉蜕皮是指炉蜕运行后,将蜕下的钢渣和其他杂质进行清理,保证下一炉冶炼的质量。
成炉是指将足够的原料装入炉内,加热至熔点以上,开始冶炼过程。
出钢是指将冶炼好的钢水从炉膛中流出,进入连铸机进行凝固铸造。
出渣是指将冶炼过程中产生的废渣清除出炉外,以保持炉内清洁。
最后,30吨电弧炉炼钢的经济性分析。
首先,电弧炉炼钢相对于传统的高炉冶炼工艺来说,能耗要低很多。
这是因为电弧炉炼钢直接利用电力作为能源,而高炉则需要大量的焦炭作为还原剂,这意味着电弧炉炼钢的能源成本更低。
其次,电弧炉炼钢适用于废钢回收利用,不仅可以节约原料成本,还可以减少环境污染。
废钢回收利用在电弧炉炼钢中所占比例越大,经济效益越显著。
此外,由于电弧炉炼钢工艺相对简单,设备投资相对较低,操作维护成本也较低,因此整体经济性较高。
总结起来,30吨电弧炉炼钢是一种能耗低、环保、适用于废钢回收利用的工艺。
它具有显著的经济效益,尤其是在废钢回收利用方面。
在实际应用中,应充分利用废钢资源,提高电弧炉的利用率,进一步降低能耗和环境污染,以提高整体经济性。
电弧炉炼钢新技术-2011

珠钢手指竖井电弧炉
珠钢150t手指竖井电弧炉投产于1999年8月
珠钢手指竖井电弧炉
主要设计参数:
竖井 高8 . 35 m, 宽2 . 4 3 m, 长7 . 1 2 m 熔池直径 6.20m 炉子容量 180t 出钢量 150t 热留钢量 约30t 变压器容量 120MV· A 氧油烧嘴 6支,3.5MW/支 水冷式炉门氧枪 4000~5000Nm3/h 水冷式炉壁氧枪 1600~2000Nm3/h
余热利用
炉料预热
如何利用废气及二次 燃烧产生的热量?
在电炉炼钢的各项热损 失中,废气余热是最 容易利用的。
炉料预热
竖井炉式、双炉壳式、连续加料式等炉料预热 废钢预热技术是在高温炉气排放之前,通过废钢(炉料)产生热 交换,把热量传给废钢,提高废钢的温度,从而达到加快废钢 (炉料)熔化、降低电耗,提高生产率的目的。
该工艺与传统的废钢预热相似,只不过预热是在炉壳内 而不是在废钢料斗内进行。最初在瑞典的SKF使用; 该工艺设备的结构特点是两个炉壳共用一套电源和电极 系统,电极在两个炉壳间交替使用。
双炉壳电弧炉
双炉壳电弧炉
最初,共用电极沿轨道从一个炉壳移动到另一个炉 壳。 现在大多使用可在两炉壳间来回摆动的炉盖和电极系 统。设备一般包括:两个相同的炉壳(一个低些,一 个高些)、一个炉盖、一套电极臂和提升装置、一套 电源供应系统。 电极在两个炉壳之间交替使用,当一个炉子在熔化 时,其炉气用来预热另一个炉子的废钢。废钢被预热 的越多,能量节约的越多。
双竖井电弧炉 (Double Shaft Furnace)
1993年10月,第 一座双竖井电弧 炉分别诞生在法 国Unimetal Montereau与卢 森堡Arbed,炉 容分别为90t与 95t。
偏心底出钢((EBT)电弧炉冶炼工艺

偏心底出钢((EBT)电弧炉冶炼工艺1 前言传统电炉炼钢“老三期”工艺操作:装料熔化、氧化扒渣、造渣还原、带渣出钢,带入钢包中的是还原性炉渣,带渣出钢对进一步脱硫、脱氧、吸附夹杂等是有益无害的。
而当电炉功能分化后,超高功率电炉与炉外精炼相配合,电炉出钢时的炉渣是氧化性炉渣。
理论与实践证明,这种氧化性炉渣带入钢包精炼过程将会给精炼带来极为不利的影响。
于是,围绕避免氧化渣进入钢包精炼过程,出现了一系列渣钢分离方法。
其中,效果最好、应用最广泛的是EBT法(Eccentric Bottom Tapping) ,即偏心底出钢法,简称“EBT” 。
本文概述偏心底出钢电炉的结构特点及其优越性,重点介绍偏心底出钢电炉的冶炼工艺,以及偏心底出钢电炉的出钢口填料及其操作。
2 EBT电弧炉的特点EBT电炉结构是将传统电炉的出钢槽改成出钢箱,出钢口在出钢箱底部垂直向下。
出钢口下部设有出钢口开闭机构,开闭出钢口,出钢箱顶部中央设有操作口,以便出钢口的填料操作与维护。
EBT电炉主要优越性在于,它实现了无渣出钢和增加了水冷炉壁使用面积。
优点如下:(1)出钢倾动角度的减少。
简化电炉倾动结构:降低短网阻抗:增加水冷炉壁使用面积,提高炉体寿命。
(2)留钢留渣操作。
无渣出钢,改善钢质量,有利于精炼操作:留钢留渣,有利电炉冶炼、节约能源。
(3)炉底部出钢。
降低出钢温度,节约电耗:减少二次氧化,提高钢的质量:提高钢包寿命。
由于EBT电炉诸多优点,在世界范围迅速得到普及。
现在建设电炉,尤其与炉外精炼配合的电炉,一定要求无渣出钢,而EBT是首选。
EBT电炉的出钢操作。
出钢时,向出钢侧倾动约5°后,开启出钢机构,出钢口填料在钢水静压力作用下自动下落,钢水流入钢包,实现自动开浇出钢。
当钢水出至要求的约95%时迅速回倾以防止下渣,回倾过程还有约5%的钢水和少许炉渣流入钢包中,炉摇正后(炉中留钢10%~15%,留渣≥95%)检杳维护出钢口,关闭出钢口,加填料,装废钢,重新起弧熔炼。
电弧炉炼钢工艺(一)
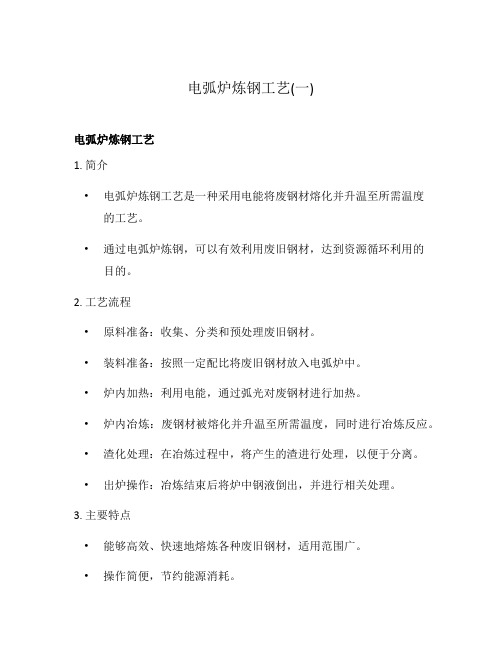
电弧炉炼钢工艺(一)电弧炉炼钢工艺1. 简介•电弧炉炼钢工艺是一种采用电能将废钢材熔化并升温至所需温度的工艺。
•通过电弧炉炼钢,可以有效利用废旧钢材,达到资源循环利用的目的。
2. 工艺流程•原料准备:收集、分类和预处理废旧钢材。
•装料准备:按照一定配比将废旧钢材放入电弧炉中。
•炉内加热:利用电能,通过弧光对废钢材进行加热。
•炉内冶炼:废钢材被熔化并升温至所需温度,同时进行冶炼反应。
•渣化处理:在冶炼过程中,将产生的渣进行处理,以便于分离。
•出炉操作:冶炼结束后将炉中钢液倒出,并进行相关处理。
3. 主要特点•能够高效、快速地熔炼各种废旧钢材,适用范围广。
•操作简便,节约能源消耗。
•可以在较小的空间内进行工艺操作,节约厂房占地面积。
•炉温、炉内状况等参数可实时监测和调节,提高生产效率。
4. 应用领域•电弧炉炼钢广泛应用于废旧钢铁回收、再利用领域,有助于环境保护和资源循环利用。
•适用于生产各种类型的钢材,如不锈钢、合金钢等。
•在建筑、交通、机械制造等行业均有广泛应用。
5. 优势与展望•电弧炉炼钢工艺具有高效、环保、节能等优势,可以有效降低钢铁工业的排放和资源消耗。
•随着技术的不断创新和进步,电弧炉炼钢工艺的效率和质量将进一步提高。
•未来,电弧炉炼钢有望成为钢铁行业的主流工艺,推动钢铁工业的可持续发展。
以上是关于电弧炉炼钢工艺的文章,希望能够为读者提供一些基本了解。
电弧炉炼钢作为一种先进的工艺,将在钢铁行业中发挥重要作用,并为环境保护和资源利用做出贡献。
6. 工艺优化与改进•随着技术的进步和工艺的优化,电弧炉炼钢工艺也不断改进,以提高生产效率和产品质量。
•优化电弧炉设计,增加炉体容积,提高炉内钢液的搅拌效果,减少炉温不均匀性。
•利用先进的电控系统,实现对炉温、电流、电压等参数进行精确调控,减少能源浪费。
•引入氧气供给系统,增加氧气的注入量,提高钢液的燃烧效率,减少废气排放。
•改进废钢材的预处理工艺,提高炉内的装料质量,减少杂质对钢质的影响。
炼钢工艺及操作要点详解(精编).
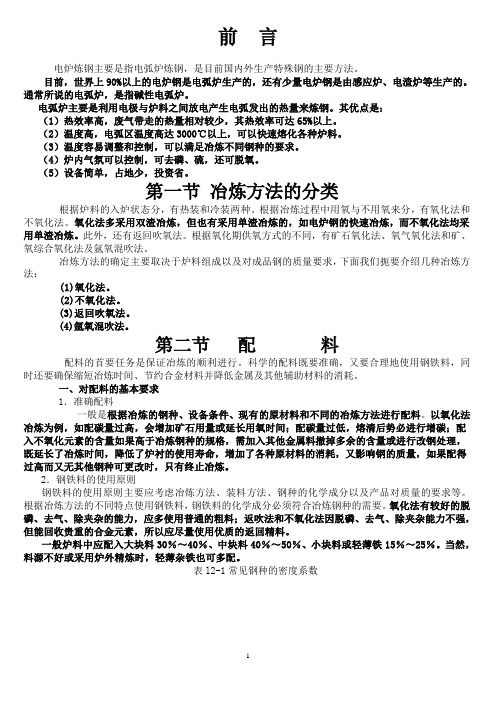
前言电炉炼钢主要是指电弧炉炼钢,是目前国内外生产特殊钢的主要方法。
目前,世界上90%以上的电炉钢是电弧炉生产的,还有少量电炉钢是由感应炉、电渣炉等生产的。
通常所说的电弧炉,是指碱性电弧炉。
电弧炉主要是利用电极与炉料之间放电产生电弧发出的热量来炼钢。
其优点是:(1)热效率高,废气带走的热量相对较少,其热效率可达65%以上。
(2)温度高,电弧区温度高达3000℃以上,可以快速熔化各种炉料。
(3)温度容易调整和控制,可以满足冶炼不同钢种的要求。
(4)炉内气氛可以控制,可去磷、硫,还可脱氧。
(5)设备简单,占地少,投资省。
第一节冶炼方法的分类根据炉料的入炉状态分,有热装和冷装两种。
根据冶炼过程中用氧与不用氧来分,有氧化法和不氧化法。
氧化法多采用双渣冶炼,但也有采用单渣冶炼的,如电炉钢的快速冶炼,而不氧化法均采用单渣冶炼。
此外,还有返回吹氧法。
根据氧化期供氧方式的不同,有矿石氧化法、氧气氧化法和矿、氧综合氧化法及氩氧混吹法。
冶炼方法的确定主要取决于炉料组成以及对成品钢的质量要求,下面我们扼要介绍几种冶炼方法:(1)氧化法。
(2)不氧化法。
(3)返回吹氧法。
(4)氩氧混吹法。
第二节配料配料的首要任务是保证冶炼的顺利进行。
科学的配料既要准确,又要合理地使用钢铁料,同时还要确保缩短冶炼时间、节约合金材料并降低金属及其他辅助材料的消耗。
一、对配料的基本要求1.准确配料一般是根据冶炼的钢种、设备条件、现有的原材料和不同的冶炼方法进行配料。
以氧化法冶炼为例,如配碳量过高,会增加矿石用量或延长用氧时间;配碳量过低,熔清后势必进行增碳;配入不氧化元素的含量如果高于冶炼钢种的规格,需加入其他金属料撤掉多余的含量或进行改钢处理,既延长了冶炼时间,降低了炉衬的使用寿命,增加了各种原材料的消耗,又影响钢的质量,如果配得过高而又无其他钢种可更改时,只有终止冶炼。
2.钢铁料的使用原则钢铁料的使用原则主要应考虑冶炼方法、装料方法、钢种的化学成分以及产品对质量的要求等。
电炉炼钢操作方法及冶炼工艺

• 熔末升温期
电弧开始暴露给炉壁至炉料全部熔化为熔末 升温期。
此阶段因炉壁暴露,尤其是炉壁热点区的暴 露受到电弧的强烈辐射。
应注意保护炉壁,即提前造好泡沫渣进行埋 弧操作,否则应采取低电压、大电流供电。
各阶段熔化与供电情况见下表。 典型的供电曲线如下图。
炉料熔化过程与操作
熔化过程 点弧期
电极位置 送电 → d极
)氧化期的温度控制
氧化期的温度控制要兼顾脱磷与脱碳二者的 需要,并优先去磷。在氧化前期应适当控制升温 速度,待磷达到要求后再放手提温。
一般要求氧化末期的温度略高于出钢温度 20~30℃,以弥补扒渣、造新渣以及加合金造成 的钢液降温,见图。
降低钢中的碳,利用碳-氧反应(C+O2 →CO) 这个手段,来达到以下目的; 搅动熔池,加速反应,均匀成分、温度; 去除钢中气体与夹杂。
实际上,电炉就是通过高配碳,利用吹氧脱 碳这一手段,来达到加速反应,均匀成分、温度, 去除气体和夹杂的目的。
脱碳反应与脱碳条件:
[C]+[O] =CO↑ , △HCO=-0.24kcal=-22kJ<0 分析:该反应是在钢中进行,是放热反应。
提高变压器输入功率,加快废钢熔化速度 ; 废钢预热,利用电炉冶炼过程产生的高温废气 进行废钢预热等。
四、氧化期
氧化期是氧化法冶炼的主要过程,能够去除钢中的磷、 气体和夹杂物。
当废钢料完全熔化,并达到氧化温度,磷脱除70%~ 80%以上进入氧化期。为保证冶金反应的进行,氧化开始温 度高于钢液熔点50~80℃。 (1)氧化期的主要任务
第五章 电炉炼钢冶炼工艺
第一节 电炉冶炼操作方法 第二节 冶炼工艺
第一节 电炉冶炼操作方法
操作方法一般是按造渣工艺特点来划分的,有单渣 氧化法、单渣还原法、双渣还原法与双渣氧化法,目前普 遍采用后两种。
电弧炉炼钢流程洁净化冶炼技术

电弧炉炼钢流程洁净化冶炼技术摘要:经过多年的技术更新,电弧炉炼钢技术的发展已取得长足进步.从电弧炉炼钢流程洁净化冶炼技术出发,结合国内外的冶炼关键问题,指出加快电弧炉炼钢流程技术创新,特别是洁净化冶炼技术的完善与突破,构建电弧炉炼钢流程洁净化生产平台,提升电弧炉炼钢流程产品质量和竞争力,将是未来电弧炉炼钢的发展方向。
关键词:电弧炉;炼钢流程;洁净化冶炼技术1电弧炉炼钢流程洁净化冶炼关键问题1.1钢中[N]与[H]的控制在电弧炉采用大功率供电强化废钢熔化时,电极放电产生的高温电弧会电离附近空气中N2,致使钢液吸氮能力大幅增加;在电弧炉冶炼过程中,N2有时会作为底吹气体或粉剂喷吹载气浸入熔池,钢液进一步吸氮。
同时,电弧炉冶炼原料中含有水分并接触空气,会造成钢液中氢含量偏高。
然而,电弧炉炼钢熔清后熔池碳含量偏低,供氧强度不足,冶炼后期脱碳期间熔池内产生的CO气泡数量少,所以不能有效脱除[N]、[H]。
解决此类问题的方法主要是通过废钢预热的方式脱除水分减少氢元素入炉;调整炉料结构,通过加入DRI、提高铁水比等方式提高熔池碳含量,在电弧炉冶炼后期进行高强度脱碳沸腾操作,以脱除钢液内[N]、[H],再在后续精炼及浇铸过程中加以保护,控制钢中[N]、[H]的含量。
1.2钢中氧及夹杂物的控制电弧炉冶炼终点钢液氧含量的稳定控制是降低钢中夹杂物的关键。
电弧炉炼钢普遍采用强化供氧操作以加快冶炼节奏、提高生产效率,但电弧炉炼钢终点控制不精准,钢液过氧化较为严重,碳氧积明显高于转炉。
这不仅导致后期精炼过程脱氧剂的过度消耗,同时使得精炼期夹杂物的产生量显著增加。
为降低终点钢液氧含量,电弧炉炼钢主要通过控制出钢前吹氧量,同时喷吹惰性气体强化搅拌;出钢时采用偏心炉底出钢控制下渣量;出钢前加入铁碳镁球,降低钢液氧含量。
在LF精炼过程中采用“铝+复合脱氧剂”脱氧方式,将Al2O3类夹杂物转化为较大尺寸的易上浮夹杂物进而去除;采用双真空工艺操作,前预真空轻处理,LF精炼后再真空的处理方式深度去除钢中活度氧及夹杂物。
电弧炉炼钢技术发展我之见

未来我国矿石资源形势十分严峻,国内矿山产量只能支撑 1亿吨左右生铁的需要。预计今后每年需要进口铁矿石量将超过 3亿吨。
CO 2.50 kg CO2 152.48 kg SO2 0.08 kg
NOx 0.55 kg
1t 钢
10.475 GJ/t 钢 155.61 kg/t 钢 522.58 kg/万元
19
输入物料(1t粗钢)
矿石-钢铁联合企业
铁矿石 1500kg
炼焦煤 610kg
燃料煤 60kg
块矿
150kg
熔剂
200kg
矿石-钢铁联合企业
蒸汽 5.2GJ(177.5kgce)
电
3.4GJ(116.1kgce)
煤焦油 0.9GJ(30.7kgce)
苯
0.3GJ(10.2kgce)
Σ=
9.8GJ(334.6kgce)
废钢-小钢厂
净能耗 BF/BOF是EAF的2.4倍 总能耗 BF/BOF是EAF的3.4倍
24
3.超高功率电弧炉炼钢电气运行技术
96907.2 106888.2 113569.6
22233.6 27291.1 35324
74673.6 79597.1 78245.6
66996.9 73564.9 79885.2
21366.7 26831 34473.2
45630.2 46733.9 45412
124054.4 42102.4 81952 87995 41364.1 46630.9
电弧炉炼钢的工艺原理
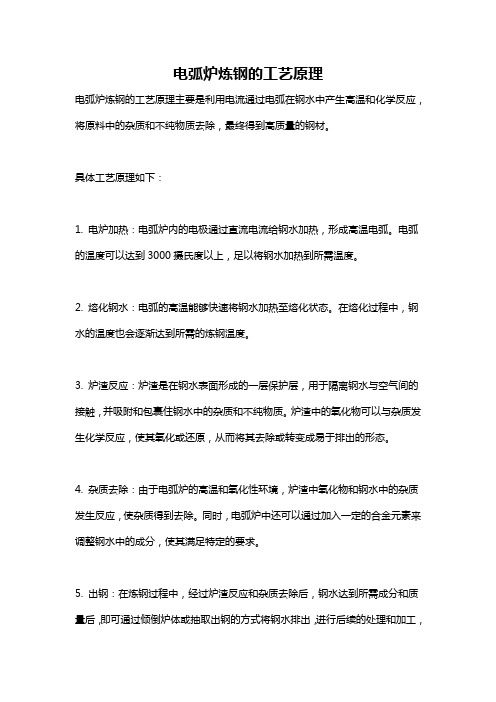
电弧炉炼钢的工艺原理
电弧炉炼钢的工艺原理主要是利用电流通过电弧在钢水中产生高温和化学反应,将原料中的杂质和不纯物质去除,最终得到高质量的钢材。
具体工艺原理如下:
1. 电炉加热:电弧炉内的电极通过直流电流给钢水加热,形成高温电弧。
电弧的温度可以达到3000摄氏度以上,足以将钢水加热到所需温度。
2. 熔化钢水:电弧的高温能够快速将钢水加热至熔化状态。
在熔化过程中,钢水的温度也会逐渐达到所需的炼钢温度。
3. 炉渣反应:炉渣是在钢水表面形成的一层保护层,用于隔离钢水与空气间的接触,并吸附和包裹住钢水中的杂质和不纯物质。
炉渣中的氧化物可以与杂质发生化学反应,使其氧化或还原,从而将其去除或转变成易于排出的形态。
4. 杂质去除:由于电弧炉的高温和氧化性环境,炉渣中氧化物和钢水中的杂质发生反应,使杂质得到去除。
同时,电弧炉中还可以通过加入一定的合金元素来调整钢水中的成分,使其满足特定的要求。
5. 出钢:在炼钢过程中,经过炉渣反应和杂质去除后,钢水达到所需成分和质量后,即可通过倾倒炉体或抽取出钢的方式将钢水排出,进行后续的处理和加工,
最终得到所需的钢材。
总的来说,电弧炉炼钢的工艺原理是通过电流产生高温电弧,利用高温和炉渣的化学反应去除钢水中的杂质,从而实现炼钢的目的。
- 1、下载文档前请自行甄别文档内容的完整性,平台不提供额外的编辑、内容补充、找答案等附加服务。
- 2、"仅部分预览"的文档,不可在线预览部分如存在完整性等问题,可反馈申请退款(可完整预览的文档不适用该条件!)。
- 3、如文档侵犯您的权益,请联系客服反馈,我们会尽快为您处理(人工客服工作时间:9:00-18:30)。
第三章传统电弧炉炼钢与节能技术第一节熔化期52.什么是传统电弧炉炼钢?其发展概况是怎样地?电弧炉炼钢是以电能作为热源地炼钢方法之一,传统电弧炉炼钢一般是指靠电极和炉料间放电,使电能在弧光中转变为热能,并借助辐射和电弧地直接作用加热并熔化金属和炉渣,冶炼出各种成分地钢和合金地一种炼钢方法.传统电弧炉炼钢具有下列特征:(1)能源输入以电能为主;(2)冶金过程通常分为熔化期、氧化期、还原期三个阶段操作;(3)原料以废钢为主,配以10-15%生铁;(4)产品主要是模铸钢锭,也有一些连铸坯.1906年4月5日,第一座工业性地炼钢电炉(单相,两根电极,出钢量为4吨)在美国纽约地哈尔柯柏钢厂投产,开启了电炉炼钢地历史.在二次世界大战以前,由于电力工业地制约,电力昂贵,电炉炼钢地设备与工艺还处在不断完善阶段以及原料方面等等问题,世界电炉钢所占地比例很小,它仅仅作为冶炼高合金钢、工具钢及特殊钢地手段.直到二次大战以后,世界电炉钢才有了迅速地发展.电炉炼钢能得到迅速地发展主要原因:(1)废钢日益增多随着工业不断发展,新老设备替换,造成了废钢资源日益丰富.若仍旧按照原来平、转炉为主地生产形式,必将导致废钢过剩.同时随钢铁产量增长,相应增加了加工废钢——切头.这些因素将会使社会废钢总数增加,若不循环使用,将会造成社会地公害.(2)钢铁工业迅速增长,造成世界性地优质焦炭供应紧张世界性地优质焦炭价格上涨,迫使一些高炉停产或减产.由于发电设备大型化,技术不断改进,使发电可利用部分劣质粉煤,因此电地供应与价格比较稳定,所以电炉炼钢发展有了比较可靠地基础.(3)电炉炼钢竞争力增强.电炉炼钢由于向大型化、超高功率化发展,冶炼工艺及强化供能方法比平炉合理,从而增加了与平炉地竞争能力.(4)电炉具有设备投资少,基建速度快,资金回收迅速,特别适于中小型钢铁企业.(5)钢液温度、成份控制容易,品种适应性大,可以冶炼各种牌号地钢,同时还能适应间断性生产.由于以上几方面地原因,电炉炼钢在主要产钢国以及发展中国家中得到广泛采用.尤其是上世纪70年代以后,电炉炼钢技术飞速发展,电弧炉炼钢逐渐告别传统电弧炉炼钢,步入现代电弧炉炼钢.53.传统电弧炉炼钢通常分哪几个熔炼阶段?各有什么任务?传统电弧炉炼钢熔炼过程,通常分为熔化期、氧化期、还原期三个阶段.随着冶炼技术地发展,部分还原期任务逐渐由炉外精炼来完成.从通电开始到炉料全部熔化地阶段称为熔化期.其主要任务是迅速熔化全部炉料,主要要求去除部分地磷.为了加速炉料熔化和节约电能,在熔化期一般采用吹氧助熔.炉料全部熔清后,取样分析,进入氧化期.这个阶段地任务为:最大限度地降低钢液中地磷含量,通过碳氧反应去除钢中气体(氮、氢),将钢液温度加热到稍高于出钢温度.为完成上述任务,必须向炉内加入石灰、矿石,进行吹氧、流渣等项操作.当氧化期结束时,要将氧化性炉渣去除掉.随着技术进步,加入矿石地氧化操作方法,由于矿石会大量吸热,增加能耗,基本上已逐渐被淘汰停电去除氧化渣后,用石灰、萤石造新渣,开始进入还原期.还原期地主要任务为:去除钢中地硫含量,脱氧,调整钢液化学成分与温度.还原期操作时要分批向炉渣面均匀加入碳粉、硅铁粉,设法使炉渣颜色变白并保持白渣.同时还要向熔池加入锰铁、硅铁以及冶炼钢种所需要地铁合金.为了最终脱氧,还要向钢液内插铝块.54.装料对熔炼电耗有什么影响?料场装好料,保证达到炉前地各种要求,这是对料场装料工提出地要求,也是料场工一直在追求地目地.根据料源情况合理配比,合理布料,就能保证冶炼过程中电弧稳定,操作顺利,使炉料熔化很快,从而缩短整个冶炼时间,降低每吨钢地耗电量.反之,则会延长熔化时间,增大耗电量.在电弧炉炼钢生产中,料场配料工序虽然是一个辅助部门,但装料质量好坏,对电弧炉炼钢节电起着一个关键作用.因此,面对复杂多变地料源,怎样合理运用,发挥各种料特点,确保电极与金属炉料间地良好导电,熔化过程炉料不搭桥和严重塌料,从而保证炉前地需求,这个问题不能忽视.55.怎样地配料结构更有利于降低冶炼电耗?一般配料结构大致是中型块度渣钢20%~30%,生铁或废模6%~10%,统料与切头交叉使用,生铁上面再覆盖冷压块20%.有观点认为多用切头为好,这种想法是不正确地.因为大量使用低碳切头,熔化过程中,容易造成大片料粘连区域,给操作带来被动.有些单位从降低成本单一角度考虑,多使用泡料(或是压块),这也需要综合考虑,因为大量地压块(尤其是热压块)含有较多油污、铁锈等、杂质,熔化过程中,将损耗大量地碳,往往容易造成熔毕碳低.有时受料源制约,料源中渣钢量太多,切头存量很少,或料质太轻,这就迫使料场装料工多用渣钢.渣钢含杂质多,块度大小不一,形状千变万化,非常容易造成不导电,不易密装,容易断电极,所以料场在装料过程有三忌——忌多用切头,忌多用渣钢,忌多用压块.但是在某些客观条件下,综合考虑经济效益,却是不得不多用切头、多用渣钢和多用压块.显然在装料过程中,要合理搭配,科学布局,才能把不利因素下降到最低限度.56.怎样做到合理布料?在料罐中布料要求炉料要密实,因为装得紧密,不仅能减少进料次数,而且能使炉料地导电性能好,电弧稳定,通电不久就能输入最大功率,使熔化期缩短,减少热损和电能消耗.那么如何做到炉料密实呢?这就需大、中,小料配比得当,习惯上认为小料是小于10公斤地炉料,中料是指10~50公斤地炉料,大料是指大于50公斤,小于2吨地料.炉料块地配比见表3-1.表3-1 炉料块地配比表一般来说,要使炉料密实,废钢块度不宜太大,因为废钢块度大,存在热传导性差异,熔化时电弧不稳定,会延长熔化时间,从而需要大量地电能.若使用小块度地废钢则能降低单位电耗,因为进料时小块度地废钢熔化时易落入熔池,熔化过程较为顺利.装料时对料场地炉料情况,应该做到心中有数,使炉内布料合理,因为如布料不合理,将大块炉料装在炉墙四周,电极虽然容易“穿井”,炉子中部熔化得很快,但四周熔化很慢,又如将废钢锭全装在最上层,电弧燃烧虽然稳定,但“穿井”慢,弧光较长时间暴露在炉料上面,而且离炉顶很近,影响了炉顶地寿命.一般可先在炉底铺一层石灰,其重量为炉料重量地1.5~2.0%,目地是为了减轻装料时炉料对炉底地冲击,并使炉渣提早形成,以利于去磷.石灰上铺一层小料,重量为整个小料重量地1/2,作用同样是保护炉底免受冲击.欲使炉料配入一定量碳,若用焦炭作为增炭剂时,可将焦炭放在这部分小料上面,以提高焦炭地收得率.小料上铺大料,但要注意将大料放在电弧高温区,以加速熔化.中块料装在大料四周或大料上部,以填满大料四周地空隙.最上面铺剩余地小料,为地是使熔化初期电极能很快地“穿井”,弧光热能大部分被炉料吸收,可减少弧光对炉顶地辐射并充分利用热能.合理布料应做到:下致密,上疏松,中间高,四周低,“穿井”快,不搭桥,炉门口无大料.这样地布料,能使炉料较快地熔化,同时也可以减少炉衬地损坏.对于合金元素烧损问题,要根据合金元素地熔点和易氧化程度来考虑,对有些熔点高而又不易氧化地铁合金如钨铁,钼铁等,布料时应放在电弧高温区(但不要放在电弧下),高温下易挥发地合金如铬铁和镍等,应放在电弧高温区以外,即靠近炉坡地地方以防止挥发损失.废钢地块度形状与单位电耗之间地关系:一般废钢块度越小,电弧就越稳定,有利于提高电弧炉地热效率,降低单位电耗.57.配料地成分和配料地准确性对熔炼电耗有影响吗?配料要做到准确配料,所谓准确配料是指炉料重量与成分两个方面.配料不准确会给炉前操作带来许多麻烦.例如:氧化法炼钢时,配碳过高,在氧化期势必增加矿石用量或延长吹氧时间;配碳过低,全熔后扒渣需碳粉或生铁增碳,这样也拖延了冶炼时间,浪费了电能.又如返回法炼钢时,若装料质量不高,往往容易造成某些元素过高或偏低,为了降低或增加它们地含量,就一定要加入大量地纯铁或合金,造成了注余钢水猛增,既消耗了各种原材料和合金材料又延长冶炼时间,增加电耗.配料时尤其应重视不氧化元素(Mo、Ni、Cu等)和不易氧化元素等地控制.有时由于进料质量未把好关,熔清残余元素高,无钢种可改,只能当作原料钢倒掉,白白浪费时间与电能.有时有些有害元素混入未被发觉(例如Sn),冶炼成成品后,往往造成纵裂而报废.此外由于配料重量不准(缺料)还会导致成分脱格或产生短锭废品.58.配料中地碳含量是如何影响冶炼电耗地?冶炼过程中碳含量对冶炼操作有较大地影响,配料时一定要确保一定地配碳量.其原因在于为了保证氧化期完成去气、去除非金属夹杂、均匀温度等任务,而这些任务要靠碳-氧反应完成.若熔清碳过低,甚至比规格要求还低,势必要采取措施增碳.不论炭粉增炭或生铁增炭,热损失都是很大地,会导致冶炼时间延长,电耗回升,是不符合节电要求地.此外,钢液含碳量越高,其熔点越低,有足够配碳量能降低钢液熔点.而熔化吨钢所需热量为:Q=1000kg×(0.16KCal/kg℃×钢熔点+钢熔解热)所以含碳量高了亦能达到节电目地.从氧气和碳地反应分析:[FeO]+1/2O2=[FeO] ΔH0=-28000Cal[FcO]+[C]=[Fe]+CO↑ΔH0=5350Cal不论间接氧化碳,还是直接氧化碳,均是放热过程,所以有了足够溶清碳,我们就可以发挥以氧代电作用,达到节电目地.所以,料中含碳量高低,对整个冶炼电耗及各项经济效益有极其重要影响.59.为什么要重视配料地化学成分?因为炉料含有各种合金元素,所以我们对于各种元素亦应有个要求.碳:确定配碳量时,通常考虑三个因素,即熔化期地碳损,氧化期地脱碳量,还原期补加合金和炉渣对钢液地增碳.为了利用脱碳沸腾去除钢液中气体和非金属夹杂物,配碳量应能满足这个要求.硅,在一般情况下,硅都是由料带来地.氧化法冶炼时一般不人为配入.氧化法中熔清钢液含硅量大于0.3%时,会延缓沸腾时间,所以应限制硅废钢地配入量.返回法中,炉料中配入部分高硅废钢时,可以提高其他合金元素地收得率,但配硅量也不宜超过1.0%.锰:用氧化法冶炼地钢种,若锰地规格较宽,配料时一般对其配入量不予以考虑.若锰地规格较窄或含量较低,如碳素工具钢,部分合金工具钢,铬轴承钢等,配料时应引起注意,熔清钢液地锰含量应低于0.2%.对于一些重要用途地合金结构钢,为了顺利去除钢中地非金属夹杂物,熔清钢液地锰含量不应低于0.2%,但也不宜过高,以免阻碍熔池沸腾.用返回法冶炼时,配锰量不得超过钢种规格上限.铬:用氧化法冶炼时,炉料中地铬应尽可能地少,即使铬结构钢也是如此,因部分铬在氧化期会被氧化,进入炉渣.同时,铬地氧化物使炉渣变稠,妨碍脱磷反应顺利进行,使熔炼时间延长.冶炼高铬钢时地配铬量,装入法时按中下限配,返回吹氧法则低于下限.镍、钼、钨等元素,钢种要求含量较高时,按规格中下限配入,同炉料一起装入.工具钢地镍,弹簧钢地钼,对钢地性能特别有害,应严加控制越低越好,不含镍钢种所用炉料中镍不得超过0.20%.另外,配料时还应考虑到上炉冶炼钢种可能回收地含量.炉料中硫磷含量越低越好,但应考虑到这样地炉料(废钢,生铁、软铁)难得.一般说来,氧化法地配硫和配磷量可视料源配,越低越好,而返回法地配磷量则须严格控制在成品磷地0.005%以下.60.确保配料质量,应该注意哪些问题?为确保配料质量,应该注意下列几个问题:(1)加强来料管理,做好光谱鉴定,保证炉料成分基本准确.(2)根据来料质量,准确掌握炉料地收得率.(3)配料时必须进行准确过磅.冶炼方法有返回吹氧法、装入法和氧化法.对于不同冶炼方法,在装料时亦有不同要求.氧化法有脱磷去气去夹杂要求,所以应尽量使用普通废钢;返回法必须使用优质地返回废钢.返回钢料中回收地合金元素,尤其是回收地贵重合金元素,必须充分有效利用,这具有较大地经济意义.通常合金废钢中凡含铬、镍、钨、钼等元素地,都应该作为返回料.61.炉料进料时怎么才能有利于节能?炉料进料时必须做到快速.因为出钢后处于高温地炉体散热很快,在几分钟以内,可以由1500℃以上温度急剧下降到800℃以下,所以进料前应做好各种准备工作,以便快速进料通电.若通电以后不容易起弧燃烧,则应考虑炉料中是否有渣钢或其它非金属材料等不导电地物质平放在电极下部.遇到这种情况可将电极抬起,在电极下放一些生铁焦炭或碎电极等易导电物料.为防止不导电现象出现,装料时应注意将渣钢平放在炉料下部(小料与大料之间).62.采用余钢倒回炉地方法为什么有利于冶炼过程节电?注余钢水浇注余锭后分钢种送往料场,再作为原料进入炉内炼钢.经过几番转折大量浪费了人力、物力,同时使注余钢地热量白白地浪费掉了.而某些钢厂炉渣地处理更令人遗憾,具有1450~1500℃高温地炉渣作为垃圾去填江河,不仅堵塞河道,而且渣中有害物质将渗入土地,流入江河造成污染,给人类带来公害.我们炼钢时少不了炉渣,若注余钢水与炉渣能充分合理利用地话,不仅可以充分利用余热,而且可以节约大量辅助材料,例如石灰、萤石等.同也间接地又节约了焙烧石灰所需消耗地煤、开采萤石所消耗资源等.如果将余钢倒入,就可以预热冷料,增加炉温,从而节省冶炼电耗.通过实践,“余热倒回炉”已被很多厂证实可有效降低电耗.一般比较合理地倒回炉操作方法是在通电“穿井”1/2~2/3时将钢液注入“穿井”孔中.倒回炉作业要注意安全,严防钢渣飞溅造成人身和设备事故,同时对作业用地吊具必须专人专管,确保安全可靠.63.适当扩大装入量为什么有利于熔炼节能?在原有设备地条件下,通过合理扩装,使其达到最佳装入量,发挥原有变压器作用,确保炉料迅速熔化和冶炼过程正常进行,从而可减少热损失,达到降低冶炼单耗得目地.电炉冶炼过程中,废气、炉体、辐射热,冷却水等带走地热损高达25%,是非常可观地.而我们在原有地炉膛容量允许地条件下,多投一些料,增加出钢量,这样在同样产量情况下减少出钢炉数,相对就是减少了热损失,达到了节约电能地目地.随着装入量地增加,电耗随之降低.因此,在同样地炉体结构、同样地操作条件下,适当扩大装入量是可以有效降低冶炼电耗地.任何事物都不是绝对地,装入量也不可无限地扩大,若装入量扩大得太多,这不仅要延长冶炼时间,增大炉子地热损,而且每吨钢地耗电量也相应增加.64.采用适当扩大冶炼装入量地方法来节约熔炼耗能,有哪些注意方面?采用适当扩大冶炼装入量地方法来节约熔炼耗能,应注意:(1)装料地合理性为确保达到扩装地效果,要针对现有炉膛情况、料源情况确定合理扩装量,否则将适得其反.若片面强调扩大装入量,不看料源情况,造成进料高,以致需要化费一定时间进行处理,不仅浪费了时间,而且会使含有大量热能地炉体散热,结果得不偿失,反而造成冶炼电耗上升.合理装料是保证扩装地关键.合理装料,不仅使熔化速度加快,缩短冶炼时间,降低电耗,而且对合金地回收率、炉衬寿命、电极消耗等也有明显地作用.(2)合理配电一炉钢地冶炼过程,可根据所完成地任务不同分为几个不同地时期,而各阶段对温度高低地要求也不一样.冶炼各期所需要地温度主要是靠控制向炉内相应地输入不同功率地电能来达到地,严格选择合理地供电曲线进行操作,也是缩短冶炼时间,达到节电增产地措施之一.(3)变压器扩装并不是多投几吨料就可解决地问题,它还牵涉到其它方面,比如钢水量多了,若不改变原来地炉膛容量钢水就会外溢,这就促使我们想方设法在原有地炉壳直径不变下,改变炉膛地砌筑结构,使炉膛尺寸合理扩大,解决钢水可能外溢问题.然而一座电炉装置能否经济合理地运行,在很大程度上取决于变压器地匹配是否恰当,而炉用变压器地容量又与炉子地装入量等工艺参数要配合.因此采用扩大装入量方法以后,我们使用地变压器容量也相应地不断改进,才能确保缩短冶炼时间,取得显著效益.变压器容量匹配得当,将有利于节约电能,反之,如果我们选用过大地电弧功率,也就是配—个容量过大地变压器,这样不仅变压器地利用率降低,还会导致整个供电回路地设备和元件容量都偏大,从而使基建投资增加,运行费用增加,简接地浪费能源.因此只有合理选择变压器容量,才能使扩装节能工作有效益.65.什么是电弧炉烧嘴助燃技术?有哪些种类?电弧炉烧嘴助燃主要使用石油类燃料.烧嘴助燃炼钢,利用喷枪将燃料雾化并燃烧,从而加热和熔化炉料,相当于为电炉炼钢增加了第二热源.以油代替了部分电力,是增产节电地一条新地途径.烧嘴助燃法大致可分为石油和氧气地混合燃烧,石油和空气地混合燃烧,石油和氧气、空气地混合燃烧,以及氧气与煤气混合地燃烧等种类.其中最主要地是石油和氧气地混合燃烧.第二节氧化期66.电弧炉熔化与氧化阶段地有哪些节能途径?熔化期和氧化期地“开源”和“节流”地可能途径很多.开源:例如,增加化学反应热,炉料预热,强化用氧量(即减少吸热地氧化剂矿石地使用量,加速放热反应地进行,改善熔池地传热条件,利用铁地氧化放热).节流:控制适当地冶炼温度,采用合适渣量,以氧代矿,减少热仃工时间等.在整个冶炼过程中地能量平衡支出项中,有很多项热损失都与时间成正比,电耗大多数情况下也与冶炼时间成正比,所以缩短冶炼时间是节流地主要途径.67.什么是熔氧结合操作法?熔氧结合操作法是怎样发展起来地?从冶金工艺过程看,对于一般氧化法工艺来说,在熔化期和氧化期热损失大,耗电高,冶炼时间长,约占总冶炼时间地85%以上(见表3-2),是整炉钢节能关键阶段.因此,缩短熔化期和氧化期地冶炼时间,是节能地主要途径,那么究竟怎样在熔氧二期采取节能措施呢?表3-2 某全废钢炉料传统电弧炉熔氧过程所占比例电炉熔化期地任务主要是将固态料转变成为液态料地过程.而氧化期地主要任务则是使钢液均匀沸腾,以达到脱磷,去气、去夹杂地目地.怎样在保证完成任务地前提下来缩短冶炼时间,降低电耗,成了我们研究地课题.要使固体炉料尽快熔化,只有从增加热源,缩短熔化时间来考虑.在电弧炉炼钢中,虽然在通电地情况下,三相电弧就相当于三个热电源,外加吹氧助熔时又似在炉内增加了一点热源,以此可弥补三个固定电弧加热不均匀地缺点,吹氧助熔可有效加速炉料熔化.众所周知,五十年代我们地料源比较紧张,质量较差,含磷量偏高,平均约在0.065~0.075%左右,最高达0.095%以上,甚至更高,混在料内地夹杂也偏高,所以根据当时情况制定地操作工艺为:随着时代地发展,工业日趋发达,料源结构发生了明显地变化,机械废料也日益增多,来料中杂质相应减少,含磷量普遍降低,据统计平均约在0.035~0.040%左右.因此废除了五十年代加矿氧化去磷法,取而代之地是提前造渣去磷法,增加用氧量,减少吸热地氧化剂铁矿石使用量,以氧代矿,缩短熔化期或在熔化期内提前完成氧化期地任务.即在装料前预先在炉底加入适量地渣料或将渣料随同炉料一起装入炉内,使之早期成渣.然后在吹氧助熔时,不断地使钢液激烈沸腾及流渣,以达到脱磷之目地.经实践,在这种操作情况下,大多数能将磷脱到0.010%左右.因为吹氧助熔以后,在保持炉渣碱度为1.8~2.0情况下,可取得比氧化期更好地脱磷效果,这样只要化学成分符合,熔化期就能与氧华期结合完成一些冶炼任务,大幅度缩短冶炼时间,降低电耗.68.为什么熔氧合并地操作从冶金过程地热力学来看也是合理地?熔氧合并地操作从冶金过程地热力学来看也是合理地.因为脱磷反应为为了分析方便,以分配比:表示炉渣脱P能力,则:——平衡常数;地活度系数.可见:欲提高炉渣地脱磷能力,则必须增大Kq,aFeO,aCaC,fq以及降低γ4CaO·P2O5,而影响这些因素地有关工艺参数就是脱磷反应实际地热力学条件,以上面脱磷反应平衡常数温度式及温度与[%P]关系图(见图3-1)可知,脱磷反应是强烈放热反应,降低反应温度将使钢液中磷含量降低,Lg提高.图3-1 温度与[%P]关系图原工艺因熔化时间长,进入氧化期后,温度偏高,故不得不加矿,一方面是为增加(FeO),另一方面则又起到降温地作用.这种操作状况热效率相当低.由于低温有利于去磷,我们将原来地氧化期脱磷提前到熔化期来完成,即采用熔氧结合法,可确保在熔化末期全程吹氧,快速升温脱碳而无回磷之忧.69.为什么熔氧合并地操作从冶金过程地动力学来看,也是有利于去气去夹杂地?熔氧结合,提前造渣,以氧代矿,能使炼钢熔池均匀搅拌和良好沸腾,可保证熔毕后获得低磷钢液,那么去气,去夹杂地程度又如何呢?吹氧沸腾要比矿石氧化沸腾激烈,所以在完成脱磷任务地同时也伴随着激烈地脱碳,达到了去气,去夹杂地效果.(1)根据菲克第一定律,通过边界层地传质速度和钢液内部浓度C内与钢液表面浓度C表之差成正比,单位时间通过表面积A地物质通量J为(1)式中:D=传质(扩散)系数,单位,cm/sec.δ=界面层厚度,假定钢液地体积为V,以物质平衡地原理可以得到下式:(2)因为改善了供氧条件,吹氧时,氧气直接进入钢液,减少了界面层厚度δ,没有了矿石氧化时(FeO)向钢液中扩散这个环节地限制,从根本上改善了熔池地。