吹膜模头设计的一些见解
(第18讲)第四章 第四~五节 吹膜板材挤出机头设计

福建工程学院《塑料成型工艺及模具设计》
第四章 塑料挤塑成型模具
二、板片材挤出机头设计要点 1、T形机头流道设计
➢T形岐管截面较大,料流阻力小,熔体先沿岐管横向流动, 之后平缝挤出。
➢因岐管内压力梯度的存在,致使熔体通过平缝各点的流速 不相同,其流速不均匀性可用流动均匀性指数UI表示,一般 UI≥0.95。
膜管直径大者取大值,以减小机头的长度和重量。
2、十字形吹膜机头
➢结构:类似于挤管机头,熔 料从中心进入,被分流器支架 支撑筋分为多股,之后汇合。 ➢应用:适用于上吹、下吹和 平吹工艺。
福建工程学院《塑料成型工艺及模具设计》
第四章 塑料挤塑成型模具
2、十字形吹膜机头
➢为提高熔合质量,同样可在口模平直段开设环形缓冲 槽,并适当加长支撑筋到出口的距离。
▪芯棒尖至机头出料口的距离至少应为芯棒 直径的2倍;
▪在口模出口附近设置环形缓冲槽,有利于 消除熔接痕,也有利于熔体压力的均匀分布;
槽宽B=(15~30)S,槽深δ=(3.5~8)S。
福建工程学院《塑料成型工艺及模具设计》
第四章 塑料挤塑成型模具
1、芯棒式挤出机头
(4)芯棒扩张角α:一般取80°~90 °,最大取120°,
▪适用于吹塑大口径薄膜;
▪熔接痕多,机头流动阻力较大,不 适于高粘度和热敏性的树脂。
福建工程学院《塑料成型工艺及模具设计》
第四章 塑料挤塑成型模具
4、径向流道吹膜机头(多流道或莲花瓣机头)
不同挤出 直径范围
➢分配板吹膜机头:分配板上、下两面均开设有径向流动的六 根沟槽,并相互错开,最后汇聚在与分配板外圆面相邻的圆 环槽中,达到均匀分布的目的。
锁紧螺母调节上下段的压 紧程度,防止熔料溢出。
吹膜模具原理及应用

吹膜模具原理及应用吹膜模具是一种用于制造塑料薄膜的模具。
它是由一对金属模具组成,其中一个模具被称为吹气模具,另一个模具被称为挤出模具。
吹膜过程主要分为挤出和吹气两个阶段。
在挤出阶段,塑料颗粒经过加热和熔融,被挤出机挤出,形成一个圆柱状的薄膜原料(也称为膜管)。
这个原料通过挤出模具下的环状开槽进入吹气模具中央。
在吹气阶段,吹气模具的角处设有一个气流通道,通过这个通道,压缩空气被注入膜管中央,使其膨胀并紧贴吹气模具的内壁。
同时,膜管上下两侧的挤压辊推动膜管在吹气模具内壁上滑动,从而使膜管的直径越来越大,形成所需厚度和宽度的薄膜。
吹膜模具的应用非常广泛。
其中最常见的应用是制造塑料袋。
吹膜模具可以生产各种类型的塑料袋,如垃圾袋、购物袋、食品包装袋等。
此外,吹膜模具还可以制造一些特殊用途的薄膜,如农用覆盖膜、建筑膜、工业薄膜等。
在农业领域,农用覆盖膜是一种重要的农膜产品。
它可以用于温室建设、农田覆盖和作物保护等方面。
吹膜模具可以制造出具有良好透气性和抗紫外线能力的农用覆盖膜,保护作物不受恶劣环境的影响,提高农作物产量和品质。
在建筑领域,吹膜模具可以制造出建筑膜,被广泛应用于建筑工程中的防水、隔热、保温和保护等方面。
建筑膜可以起到有效的防水和隔热作用,提高建筑物的安全性和舒适性。
在工业领域,吹膜模具可以制造出工业薄膜,用于包装、保护和输送产品。
工业薄膜具有高拉伸强度和耐磨性,可以保护产品免受划伤和污染。
此外,吹膜模具还可以制造出具有特殊功能的工业薄膜,如防静电薄膜、防腐蚀薄膜、防紫外线薄膜等。
总之,吹膜模具是一种用于制造塑料薄膜的重要工具。
它的应用范围广泛,可以满足不同行业的需求。
随着科技的不断进步,吹膜模具的技术也在不断创新和改进,为塑料薄膜的制造提供更高效、更环保和更优质的解决方案。
设计吹塑模具时如何选择分模面

设计吹塑模具时如何选择分模面
设计吹塑模具时首先要考虑的一个问题是分模面的选择,选择分模面时一般应使两半模具对称,减小吹胀比,易于制品脱模。
因此,分模面的位置由吹塑制品的形状确定。
对横截面为圆形的容器,分模面通过其直径设置;对椭圆形容器,分模面应通过椭圆形的长轴对矩形容器,分模面可通过中心线或对角线,其中后者可减小吹胀比,但与分模面相对的拐角部位壁厚较小。
对某些制品,要设置多个分模面。
某些工业制件(例如汽车保险杠、外壳板)呈扁宽板状与双壁结构,从侧面看,分模面成L形、U 形或其他不规则形状。
容器把手应沿分模面设置。
把手的横截面应呈方形,拐角用圆弧过渡,以优化壁厚分布。
把手孔一般采用嵌块来成型,还可用注塑法单独成型把手。
LDPE吹膜生产工艺要点,及13大常见问题分析,99%的问题都解决了!

LDPE吹膜生产工艺要点,及13大常见问题分析,99%的问题都解决了!大多数热塑性塑料都可以用吹塑法来生产吹塑薄膜,吹塑薄膜是将塑料挤成薄管,然后趁热用压缩空气将塑料吹胀,再经冷却定型后而得到的筒状薄膜制品。
这种薄膜的性能处于定向膜同流延膜之间:强度比流延膜好,热封性比流延膜差。
吹塑法生产的薄膜品种有很多,比如低密度聚乙烯(LDPE)、聚丙烯(PP)、高密度聚乙烯(HDPE)、尼龙(PA)、乙烯一乙酸乙烯共聚物(EVA)等。
本文对常用的低密度聚乙烯(LDPE)薄膜的吹塑生产工艺及其常见故障进行简单的介绍。
01聚乙烯吹塑薄膜材料的选择1、选用的原料应当是用吹膜级的聚乙烯树脂粒子,含有适量的爽滑剂,保证薄膜的开口性。
2、树脂粒子的熔融指数(MI)不能太大,熔融指数(MI)太大,则熔融树脂的粘度太小,加工范围窄,加工条件难以控制,树脂的成膜性差,不容易加工成膜;此外,熔融指数(MI)太大,聚合物相对分子量分布太窄,薄膜的强度较差。
因此,应当选用熔融指数(MI)较小,且相对分子量分布较宽的树脂原料,这样既能满足薄膜的性能要求,又能保证树脂的加工特性。
吹塑聚乙烯薄膜一般选用熔融指数(MI)在2~6g/10min范围之间的聚乙烯原料。
02吹塑工艺控制要点吹塑薄膜工艺流程大致如下:料斗上料一物料塑化挤出→吹胀牵引→风环冷却→人字夹板→牵引辊牵引→电晕处理→薄膜收卷但是,值得指出的是,吹塑薄膜的性能跟生产工艺参数有着很大的关系,因此,在吹膜过程中,必须要加强对工艺参数的控制,规范工艺操作,保证生产的顺利进行,并获得高质量的薄膜产品。
在聚乙烯吹塑薄膜生产过程中,主要是做好以下几项工艺参数的控制:挤出机温度吹塑低密度聚乙烯(LDPE)薄膜时,挤出温度一般控制在160℃~170℃之间,且必须保证机头温度均匀,挤出温度过高,树脂容易分解,且薄膜发脆,尤其使纵向拉伸强度显著下降。
温度过低,则树脂塑化不良,不能圆滑地进行膨胀拉伸,薄膜的拉伸强度较低,且表面的光泽性和透明度差,甚至出现像木材年轮般的花纹以及未熔化的晶核(鱼眼)。
吹膜配方及工艺笔记——吹膜中常见问题分析解决

吹膜配方及工艺笔记——吹膜中常见问题分析解决吹膜中常见问题分析解决1薄膜的透明度1 一、原料a、不同的PE树脂,其薄膜的透明度不一,M-PE的透明度高于LDPE,LDPE的透明度高于LLDPE。
b、分子量低的PE透明度比分子量高的好c、原料中的各种助剂,如润滑剂、开口剂、抗氧化剂均影响透明度。
d、树脂粒子中含有大量水分,应充分干燥粒子二、加工工艺a、熔体温度偏低,塑化不完全,透明性较差。
b、挤出速度、牵引速度与温度等匹配不适当,使薄膜表面有微小的不平滑,造成光线散射。
c、吹胀比太小,冷却不够,均影响透明度。
d、冷却速度不够快,晶球较大、结晶区大,透明度差。
2晶点2 晶点是由于吹塑的薄膜中有未塑化的高聚物颗粒造成,晶点的分子量远高于周围的PE的分子量。
①原料树脂在生产过程中控制不严,造成一部分树脂分子量过高,生产中无法塑化造成。
②原料树脂中残留催化剂较多,在吹膜机料筒螺杆的高温下,催化剂继续发生作用,形成高聚合度分子,因此,原料选择很重要。
③一定时间后,加大螺杆速度,提高熔体挤出压力,带走析出物。
④定期清洁模口3开口性差3 ①原料开口剂不足。
开口剂一般为无机物,在塑膜表面形成凸点,避免了两层膜粘紧。
②原料滑爽剂不足。
如油酸酰胺等,受热后析出到膜面,起滑爽作用。
③生产时加工温度太高,冷却不足,应降低加工温度,增加风量。
④牵引速度过快。
应降速。
4薄膜松弛4 ①薄膜厚薄不均匀,引起收卷局部松紧。
②膜泡冷却风环冷却不当,冷却不均匀。
③膜泡进入夹棍前局部被冷却。
④模口与牵引辊中心不一致。
⑤切刀切边时,切刀锋刃不一致,角度不一致。
⑥收卷时压辊压力不一致。
⑦稳定板夹缝不均匀。
5横向厚度不均匀5 ①模口间隙不均匀,应按要求仔细调节。
②机头四周加热不均匀,检查风环是否堵塞,开度是否合理。
③机头四周加热不均匀,应检查加热器。
④吹胀比过大,调换模头或换规格。
⑤过滤网破损,按时更换。
⑥风环进风软管破损或扭曲,有温度差或长短过于悬殊,应加以调整更换。
吹风机头注射模设计

吹风机头注射模设计1.引言吹风机是我们日常生活中经常使用的电器之一,它通过电动机产生的强风,增加空气的流通速度,从而加快头发的干燥速度。
吹风机头注射模是用于制造吹风机头的模具,它的设计关乎到吹风机头的外观和功能。
本文将对吹风机头注射模的设计进行详细介绍。
2.吹风机头注射模的组成2.1模具底板模具底板是吹风机头注射模的基础部分,它承载着整个注射模的各个组成部分。
模具底板的材料通常选择优质的钢材,以保证模具的稳定性和耐用性。
2.2进料系统进料系统是指将熔化的塑料材料从注塑机注入到模具中的系统。
设计进料系统时需要考虑到塑料的流动性、温度控制、压力控制等因素,以确保塑料充分填充模具腔体,并得到所需的形状和尺寸。
2.3冷却系统冷却系统是为了在注塑过程中快速冷却和固化塑料,以便于从模具中取出成品。
通常使用冷却水管进行冷却,水管应布置在模具的关键部位,以确保整个模具能够均匀冷却。
冷却系统的设计需要考虑到冷却效果、冷却时间和冷却水的供应等因素。
2.4模腔和模芯模腔和模芯是用于成型塑料制品的关键部分。
模腔是吹风机头注射模中的凹模部分,它的形状和尺寸决定了成品的外观和尺寸。
模芯是吹风机头注射模中的凸模部分,它的形状和尺寸决定了成品内部的空间结构。
3.吹风机头注射模的设计要点在进行吹风机头注射模的设计时,需要注意以下几个要点:3.1结构设计3.2材料选择3.3流道设计流道设计是决定塑料充填的重要因素,它直接影响着成品的密度和质量。
流道应尽量简短,避免死角和过于复杂的变化,同时需要具备适当的直径和形状,以保证塑料充分流动。
3.4冷却系统设计冷却系统的设计应考虑到整个模具的冷却效果和冷却时间。
冷却水管应布置在模具的关键部位,以确保整个模具能够均匀冷却。
同时,冷却水的供应应稳定,并具备恰当的温度控制装置。
4.结论吹风机头注射模设计合理与否直接影响到吹风机头的质量和使用效果。
本文对吹风机头注射模的设计进行了详细介绍,包括其组成、设计要点等方面的内容。
吹膜横向拉力差脆的原因

吹膜横向拉力差脆的原因引言吹膜横向拉力差是指在吹膜过程中,膜材在横向方向的拉力表现不均匀,出现不同区域的拉力差异。
这种现象会导致膜材脆性增加,降低了产品的质量和可靠性。
本文将介绍吹膜横向拉力差脆的原因,并提出改善措施。
原因分析1.原料质量不均匀吹膜过程中使用的原料质量不均匀是导致横向拉力差脆的主要原因之一。
原料的成分和配比不均匀会导致膜材的物理性能差异,进而影响拉力的均匀性。
2.吹膜机参数设置不当吹膜机的参数设置不当也是导致吹膜横向拉力差脆的重要原因之一。
例如,过高的吹膜机挤出温度和过高的拉伸倍率都会导致膜材的拉力分布不均匀。
3.模头设计不合理模头是吹膜过程中非常关键的组成部分,其设计是否合理直接影响吹膜产品的质量。
模头的结构、出膜口尺寸和出膜速度等都需要合理设计,以确保膜材的拉力分布均匀。
4.吹膜工艺操作不规范吹膜工艺操作不规范也会导致横向拉力差脆的问题。
例如,过高的拉伸速度、不合理的冷却方式以及拉伸过程中的振动等都会对膜材的拉力均匀性产生负面影响。
改善措施1.选择优质的原料在吹膜过程中,选择优质的原料是保证产品质量的基础。
确保原料的配比均匀,避免不必要的杂质和颗粒,提高膜材的物理性能并减少拉力差异。
2.合理设置吹膜机参数根据产品要求和原料特性,合理设置吹膜机的挤出温度、挤出速度和拉伸倍率等参数,以确保膜材的拉力均匀性。
在生产过程中,及时监测和调整参数,以提高吹膜的一致性。
3.优化模头设计通过优化模头的结构和出膜口的尺寸设计,减少膜材在流动过程中的剪切和变形,从而改善横向拉力差脆的问题。
采用合适的模头技术和先进的成型工艺,提高吹膜产品的质量和稳定性。
4.规范吹膜工艺操作建立规范的吹膜工艺操作流程,操作人员需经过专业培训,熟练掌握各项操作要点。
注意控制吹膜过程中的拉伸速度、冷却方式和振动等因素,确保拉力分布均匀,从而降低横向拉力差脆的发生。
总结吹膜横向拉力差脆是吹膜过程中常见的问题,其原因包括原料质量不均匀、吹膜机参数设置不当、模头设计不合理以及吹膜工艺操作不规范等。
HDPE土工膜-圆模(吹膜)工艺与平模工艺比较

1.5mm单糙面膜的断裂强度可达37N/mm以上,比吹膜高68%。
二次加糙工艺不破坏膜的表面,力学性能与光面相当。
能应对沉降大,稳定性安全性要求高的场合。
糙面膜焊接边缘
通常无光边,灰尘不易清理干净,焊接质量会因此受影响。
有光边,易于清理,便于焊接。
焊接性能
厚度偏差大,影响焊接强度的均匀性
厚度偏差小,易控制,焊接质量均匀
规格品种
多(可吹至0.15mm厚度或更小),吹涨比越大,厚度越薄。
少(1.0mm以上挤工艺。
光面效率高;糙面需二次加工,效率稍低。
投资
一般
高
GM13断裂延伸率>100%,2.0mm单糙面膜的断裂强度仅为29N/mm.
1.5mm单糙面膜的断裂强度仅为22N/mm.
由于加入惰性气体,产生的气泡破裂后形成糙面,膜的表面被破坏并产生大的应力集中,力学性能比光面大幅度降低。
不适合有明显沉降的场合。
二次成型力学性能与光面膜相比无明显下降,断裂延伸率>600%,比吹膜的高5倍;
厚度偏差
10%,与厚度有关的指标受此影响较大。 如力学指标等。
可以达到5%,与厚度相关的指标能保证。
宽度控制
依靠模口直径,和吹涨比(类似吹气球),会产生应力。吹涨比越大,内应力越大,厚度均匀性越差,性能稳定性越低。内应力会导致土工膜提前或加速破坏。
模口宽度确定,无任何吹涨和应力,性能指标均匀稳定。
表面质量
圆模(吹膜)工艺与平板挤出工艺比较
特点
圆模工艺(吹膜工艺)
平挤工艺
模具结构
环型模口
平面模口
冷却方式
空气冷却,易受环境温度变化影响,冷却不均匀,易产生应力集中,控制难度大。
吹塑模具设计与加工
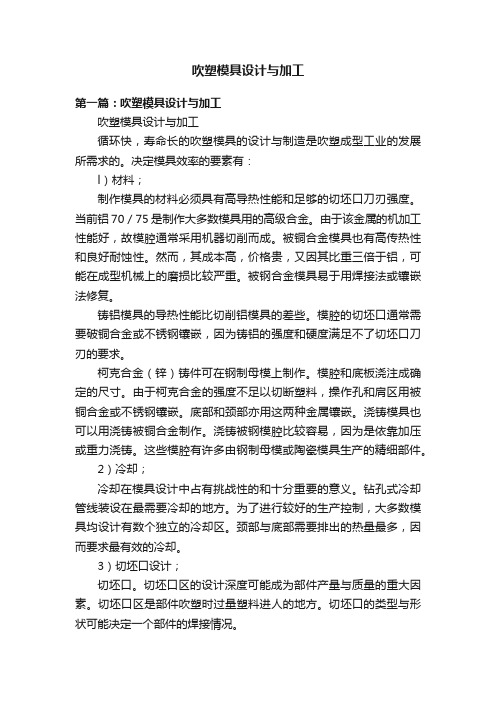
吹塑模具设计与加工第一篇:吹塑模具设计与加工吹塑模具设计与加工循环快,寿命长的吹塑模具的设计与制造是吹塑成型工业的发展所需求的。
决定模具效率的要素有:l)材料;制作模具的材料必须具有高导热性能和足够的切坯口刀刃强度。
当前铝70/75是制作大多数模具用的高级合金。
由于该金属的机加工性能好,故模腔通常采用机器切削而成。
被铜合金模具也有高传热性和良好耐蚀性。
然而,其成本高,价格贵,又因其比重三倍于铝,可能在成型机械上的磨损比较严重。
被钢合金模具易于用焊接法或镶嵌法修复。
铸铝模具的导热性能比切削铝模具的差些。
模腔的切坯口通常需要破铜合金或不锈钢镶嵌,因为铸铝的强度和硬度满足不了切坯口刀刃的要求。
柯克合金(锌)铸件可在钢制母模上制作。
模腔和底板浇注成确定的尺寸。
由于柯克合金的强度不足以切断塑料,操作孔和肩区用被铜合金或不锈钢镶嵌。
底部和颈部亦用这两种金属镶嵌。
浇铸模具也可以用浇铸被铜合金制作。
浇铸被钢模腔比较容易,因为是依靠加压或重力浇铸。
这些模腔有许多由钢制母模或陶瓷模具生产的精细部件。
2)冷却;冷却在模具设计中占有挑战性的和十分重要的意义。
钻孔式冷却管线装设在最需要冷却的地方。
为了进行较好的生产控制,大多数模具均设计有数个独立的冷却区。
颈部与底部需要排出的热量最多,因而要求最有效的冷却。
3)切坯口设计;切坯口。
切坯口区的设计深度可能成为部件产量与质量的重大因素。
切坯口区是部件吹塑时过量塑料进人的地方。
切坯口的类型与形状可能决定一个部件的焊接情况。
对于较硬的树脂而言,需要采用钢或被铜合金作切坯口材料。
有时候切坯口区要用气吹,以加速塑料冷却,去除多余的材料,防止部件畸变。
4)排气。
排气。
在部件吹塑成型时,为了使气体迅速逸出,必须使模具排气。
最常见而经济的排气方法是表面排气。
对模腔进行深度喷砂或纹理处理也有助于排气。
要排气的另一个重要原因(对那些塑料必须吹入到紧密窄小区间的部件而言)是为显示出细部。
第二篇:模具设计与加工复习题模具设计与加工复习题一、名词解释1、冷冲压;2、冲裁工序;3、变形工序;4、复合工序;5、塑性;6、塑性变形;7、黑色金属;8、有色金属;9、冲裁模;10、冲裁搭边;11、复合模;12、级进模;13、最小弯曲半径;14、冲压生产三要素;15、冲裁件的工艺性;16、挡料;17、导料;18、极性效应;19、正极性加工;20、负极性加工。
吹塑模具设计要点(新)概要
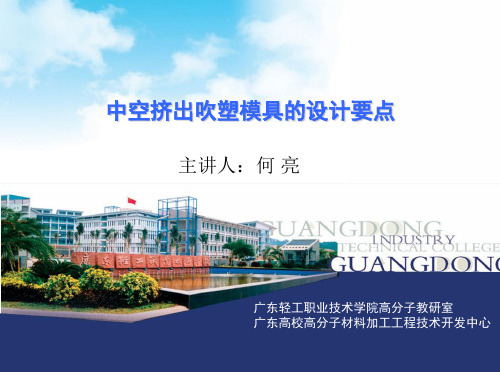
主讲人 广东高校高分子材料加工工程技术开发中心
四.中空挤出吹塑模具工艺设计要点
1. 模具型腔
• 型腔表面 许多吹塑制件的外表面都有一定的质量要求,因此, 要针对不同的要求对型腔表面采用不同的加工方式。 喷砂处理、镀铬抛光、电化学腐蚀等(吹塑PE的模具, 型腔表面应有些粗糙,易于排气,可做喷砂处理;工 程塑料的吹塑,型腔一般不能喷砂。) • 型腔尺寸 主要由制品的外形尺寸与塑料的收缩率确定。
然升温的方向流动。模面较大的冷却水通道内,可安装折流板来 引导水的流向,还可促进湍流的作用,避免冷却水流动过程中出 现死角。
6.模具冷却
吹塑模的模温一般控制在20℃~50℃左右。如果模温差 异太大会使制品的表面质量受影响,表面光泽的差异也随之 加大。 冷却方法可以参考注射模的循环水冷方式之外,还可以 选用喷淋冷却的方法:在模体背面铣出冷却水室,再用铜管 做成循环水路状,并在铜管上钻很多直径为0.1~0.3mm的 小孔,孔对着模体背面,水由孔中按照一定的方向喷出。此 方式适合于大型模具。
4.余料槽
• 在上下刃口附近开设 余料槽是为了容纳余 料。其大小应根据型 坯夹持后余料的宽度 和厚度来决定,以模 具能闭合严密为准。
5.排气问题
• 型坯吹胀时,必需把模腔表面和型坯表面之间 的空气排除,这些区域的空气不仅妨碍模具和 型坯的充分接触而降低冷却效率,而且妨碍型 坯从型腔上获得清晰的花纹或字码。 • 吹塑模具采用的排气方法很多: 模具表面喷砂处理、排气孔或沟槽(开设在型 腔易存气的部位,也可开设在分型面上)、嵌 棒排气、抽真空排气(常用在工程塑料)。
(a)凹形表面容器(b)三个分型面设置
3. 夹坯刃口
• 其作用是切除余料,同时 在吹胀以前还起着在模内 夹持和封闭型坯的作用。 • 夹坯刃口的角度和宽度对 吹塑件的质量影响很大(尤 其是上刃口)。 • 一般底部夹坯刃口宽度为 1~2mm,刃口角度为 15°~30°。
吹塑模具的设计
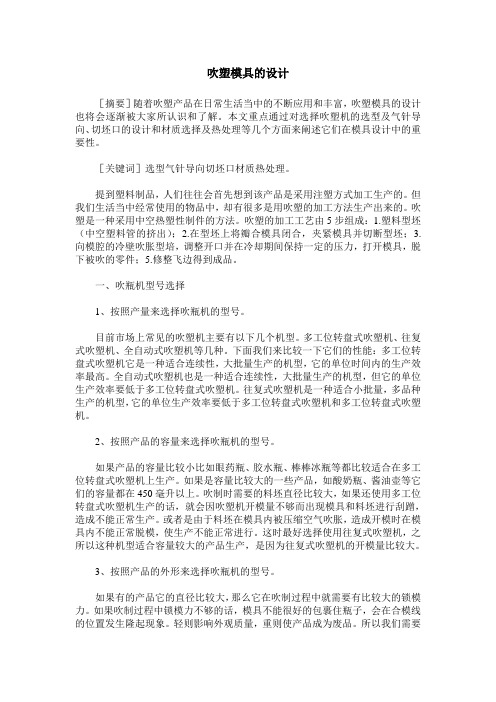
吹塑模具的设计[摘要]随着吹塑产品在日常生活当中的不断应用和丰富,吹塑模具的设计也将会逐渐被大家所认识和了解。
本文重点通过对选择吹塑机的选型及气针导向、切坯口的设计和材质选择及热处理等几个方面来阐述它们在模具设计中的重要性。
[关键词]选型气针导向切坯口材质热处理。
提到塑料制品,人们往往会首先想到该产品是采用注塑方式加工生产的。
但我们生活当中经常使用的物品中,却有很多是用吹塑的加工方法生产出来的。
吹塑是一种采用中空热塑性制件的方法。
吹塑的加工工艺由5步组成:1.塑料型坯(中空塑料管的挤出);2.在型坯上将瓣合模具闭合,夹紧模具并切断型坯;3.向模腔的冷壁吹胀型培,调整开口并在冷却期间保持一定的压力,打开模具,脱下被吹的零件;5.修整飞边得到成品。
一、吹瓶机型号选择1、按照产量来选择吹瓶机的型号。
目前市场上常见的吹塑机主要有以下几个机型。
多工位转盘式吹塑机、往复式吹塑机、全自动式吹塑机等几种。
下面我们来比较一下它们的性能:多工位转盘式吹塑机它是一种适合连续性,大批量生产的机型,它的单位时间内的生产效率最高。
全自动式吹塑机也是一种适合连续性,大批量生产的机型,但它的单位生产效率要低于多工位转盘式吹塑机。
往复式吹塑机是一种适合小批量,多品种生产的机型,它的单位生产效率要低于多工位转盘式吹塑机和多工位转盘式吹塑机。
2、按照产品的容量来选择吹瓶机的型号。
如果产品的容量比较小比如眼药瓶、胶水瓶、棒棒冰瓶等都比较适合在多工位转盘式吹塑机上生产。
如果是容量比较大的一些产品,如酸奶瓶、酱油壶等它们的容量都在450毫升以上。
吹制时需要的料坯直径比较大,如果还使用多工位转盘式吹塑机生产的话,就会因吹塑机开模量不够而出现模具和料坯进行刮蹭,造成不能正常生产。
或者是由于料坯在模具内被压缩空气吹胀,造成开模时在模具内不能正常脱模,使生产不能正常进行。
这时最好选择使用往复式吹塑机,之所以这种机型适合容量较大的产品生产,是因为往复式吹塑机的开模量比较大。
吹膜机模头
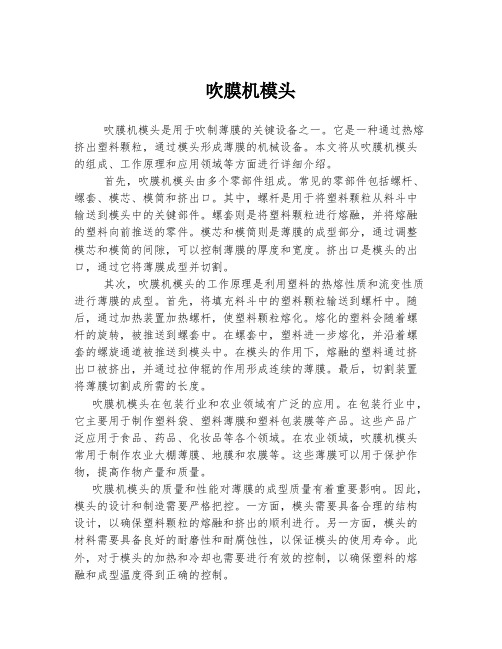
吹膜机模头吹膜机模头是用于吹制薄膜的关键设备之一。
它是一种通过热熔挤出塑料颗粒,通过模头形成薄膜的机械设备。
本文将从吹膜机模头的组成、工作原理和应用领域等方面进行详细介绍。
首先,吹膜机模头由多个零部件组成。
常见的零部件包括螺杆、螺套、模芯、模筒和挤出口。
其中,螺杆是用于将塑料颗粒从料斗中输送到模头中的关键部件。
螺套则是将塑料颗粒进行熔融,并将熔融的塑料向前推送的零件。
模芯和模筒则是薄膜的成型部分,通过调整模芯和模筒的间隙,可以控制薄膜的厚度和宽度。
挤出口是模头的出口,通过它将薄膜成型并切割。
其次,吹膜机模头的工作原理是利用塑料的热熔性质和流变性质进行薄膜的成型。
首先,将填充料斗中的塑料颗粒输送到螺杆中。
随后,通过加热装置加热螺杆,使塑料颗粒熔化。
熔化的塑料会随着螺杆的旋转,被推送到螺套中。
在螺套中,塑料进一步熔化,并沿着螺套的螺旋通道被推送到模头中。
在模头的作用下,熔融的塑料通过挤出口被挤出,并通过拉伸辊的作用形成连续的薄膜。
最后,切割装置将薄膜切割成所需的长度。
吹膜机模头在包装行业和农业领域有广泛的应用。
在包装行业中,它主要用于制作塑料袋、塑料薄膜和塑料包装膜等产品。
这些产品广泛应用于食品、药品、化妆品等各个领域。
在农业领域,吹膜机模头常用于制作农业大棚薄膜、地膜和农膜等。
这些薄膜可以用于保护作物,提高作物产量和质量。
吹膜机模头的质量和性能对薄膜的成型质量有着重要影响。
因此,模头的设计和制造需要严格把控。
一方面,模头需要具备合理的结构设计,以确保塑料颗粒的熔融和挤出的顺利进行。
另一方面,模头的材料需要具备良好的耐磨性和耐腐蚀性,以保证模头的使用寿命。
此外,对于模头的加热和冷却也需要进行有效的控制,以确保塑料的熔融和成型温度得到正确的控制。
总结起来,吹膜机模头是吹制薄膜的关键设备,它通过热熔挤出塑料颗粒,并通过模芯和模筒的作用进行成型。
模头质量和性能的好坏直接影响着薄膜的成型质量。
吹膜机模头在包装行业和农业领域有广泛的应用,为人们的生产和生活提供了便利。
吹塑模具设计要点概要

吹塑模具设计要点概要1.产品设计要点:在进行吹塑模具设计之前,首先需要对要生产的产品进行深入的分析和了解。
包括产品的形状、尺寸、容量、材质等要求。
这些数据将直接影响到模具的设计和制造。
2.模具结构设计要点:吹塑模具通常由芯棒、冷却系统、分模系统和出料系统等部分组成。
在进行模具结构设计时,需要考虑产品的形状和尺寸,并选择合适的结构形式。
如常用的两片式模具、多片式模具、套筒模具等。
3.材料选用要点:吹塑模具通常采用优质合金钢或特殊材料制造,以保证模具的耐磨性、强度和使用寿命。
在选择材料时,需要考虑模具的工作环境和要求,选择合适的材料,同时还需要考虑材料的可加工性和成本。
4.出料系统设计要点:吹塑模具的出料系统用于将熔融的塑料注入模具中,同时将成型品取出。
在出料系统设计时,需要考虑塑料的流动性、冷却性和断面均匀性等因素,以保证产品的质量和生产的效率。
5.冷却系统设计要点:吹塑模具在生产过程中需要进行冷却,以便塑料快速凝固并保持形状。
在冷却系统设计时,需要考虑到产品的不同部位的冷却速度不同,需合理安排冷却系统的布局和设计冷却水路。
6.模具加工要点:吹塑模具的制造需要经过多道工序,包括车床加工、铣床加工、电火花加工、线切割加工等。
在进行模具加工时,需要保证加工工艺和精度,尤其是对于塑件的尺寸和表面光洁度要求较高的模具。
吹塑模具设计的要点总结如上,不同类型的吹塑模具在设计和制造时会有一些特定的要求和注意事项,根据实际情况进行具体的分析和设计。
模具设计师需要熟悉吹塑工艺的原理和要求,结合实际的生产情况,进行综合考虑和优化设计,以提高模具的质量和生产效率。
吹膜模具结构
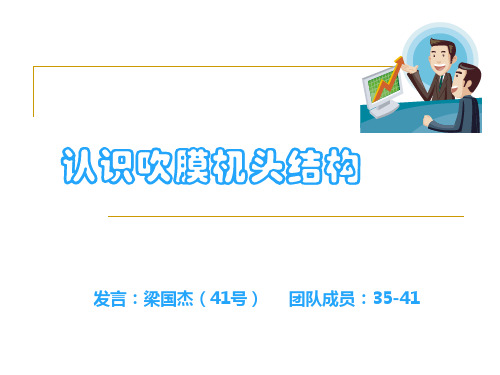
7
8
螺旋式机头
螺旋式机头 螺旋式机头按螺纹头数,可分为:单螺旋 芯棒中心进料与双螺旋芯棒中心进料式吹塑薄膜机头, 后者较常用。
特点是:①料流在机头内没有拼缝线;②由于机 头压力较大,薄膜性能好;③薄膜的厚度较均匀; ④机头的安装和操作方便;⑤机头坚固、耐用。 然而,由于料在机头中的停留时间较长,所以, 也不能加工热敏性塑料。
5
6
旋转机头
旋转机头 旋转机头是为提高薄膜的卷绕质量而发展的一种机头。
工作过程:通过口模或芯棒的转动,使模口唇隙中压力和流速不等的料层产生 一个“抹平”的机械作用,使薄膜的厚度公差(偏厚点)均匀地分布在薄膜四 周,从而实现了薄膜卷取乎整;同时,它可以改善薄膜厚度的不均匀性和消除 接合线,对宽幅薄膜的生产十分有利。 机头旋转方式有:口模旋转,芯棒不转;芯棒转动,口模不转;口模和芯棒一 起同向或逆向旋转。 旋转机头的作用:将模厚薄不均匀性较均匀地分布到薄膜四周,使薄膜厚度均匀 和易于卷取。 注意:运动件间的密封和耐磨。
螺旋式机头
不可用 适用
PP 膜 PS 膜
PA 膜 PC 膜
适用 适用
适用 适用
适用 可用
可用 可用
适用 可用
可用 可用
11
共挤出复合机头
共挤出复合吹塑是将不同种类的树脂或 不同颜色的树脂分别加入各台挤出机,通 过同一个机头同时挤出制成多层或多种颜 色的薄膜。复合薄膜可以弥补单层薄膜的 缺陷,发挥每层膜的长处,达到取长补短 的目的,可获得综合性能优越的复合材料。 复合机头有模内复合和模外复合两种形 式。
认识吹膜机头结构
发言:梁国杰(41号)
团队成员பைடு நூலகம்35-41
吹膜机膜头结构原理

吹膜机是一种用于制造塑料薄膜的设备,而膜头是吹膜机的一个重要组成部分。
膜头结构和原理的设计对于薄膜的质量和性能起着关键作用。
膜头通常由以下几个主要组成部分组成:
模具(也称为膜环):模具是形成薄膜管状的零件。
它由一个金属环或其他合适的材料制成,其内孔形状可以根据所需的薄膜形状进行设计。
空气环:空气环位于模具的上方,用于在薄膜形成过程中向模具内注入压缩空气。
空气环通过多个小孔或喷嘴将空气均匀地分布到模具内,使薄膜被吹膨胀并形成管状结构。
冷却装置:冷却装置主要用于快速冷却薄膜以增强其物理性能。
冷却装置可以包括水冷却系统或者气体冷却系统,通过控制温度来实现薄膜的冷却。
膜头的工作原理如下:
塑料原料(通常是熔融的聚乙烯、聚丙烯等)进入吹膜机的挤出机部分,并通过挤出机加热和压力使其变为熔融状态。
熔融塑料被挤出机推送到膜头部分,在膜头的模具内形成一个管状结构。
同时,压缩空气通过空气环进入模具内,将熔融塑料管吹膨胀并冷却,形成薄膜。
薄膜经过冷却装置快速冷却,以固化和增强其物理性能。
最后,薄膜通过牵引辊和收卷系统被拉伸和收卷起来,形成成品薄膜卷。
膜头的设计和调整对于薄膜的均匀性、厚度控制、缺陷减少等方面非常重要。
根据不同的应用需求,膜头可以进行调整和改变,以实现所需的薄膜特性。
矿产
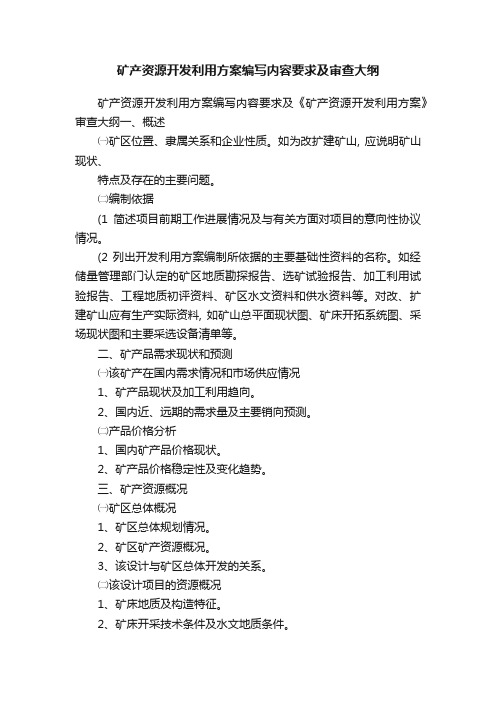
矿产资源开发利用方案编写内容要求及审查大纲
矿产资源开发利用方案编写内容要求及《矿产资源开发利用方案》审查大纲一、概述
㈠矿区位置、隶属关系和企业性质。
如为改扩建矿山, 应说明矿山现状、
特点及存在的主要问题。
㈡编制依据
(1简述项目前期工作进展情况及与有关方面对项目的意向性协议情况。
(2 列出开发利用方案编制所依据的主要基础性资料的名称。
如经储量管理部门认定的矿区地质勘探报告、选矿试验报告、加工利用试验报告、工程地质初评资料、矿区水文资料和供水资料等。
对改、扩建矿山应有生产实际资料, 如矿山总平面现状图、矿床开拓系统图、采场现状图和主要采选设备清单等。
二、矿产品需求现状和预测
㈠该矿产在国内需求情况和市场供应情况
1、矿产品现状及加工利用趋向。
2、国内近、远期的需求量及主要销向预测。
㈡产品价格分析
1、国内矿产品价格现状。
2、矿产品价格稳定性及变化趋势。
三、矿产资源概况
㈠矿区总体概况
1、矿区总体规划情况。
2、矿区矿产资源概况。
3、该设计与矿区总体开发的关系。
㈡该设计项目的资源概况
1、矿床地质及构造特征。
2、矿床开采技术条件及水文地质条件。
- 1、下载文档前请自行甄别文档内容的完整性,平台不提供额外的编辑、内容补充、找答案等附加服务。
- 2、"仅部分预览"的文档,不可在线预览部分如存在完整性等问题,可反馈申请退款(可完整预览的文档不适用该条件!)。
- 3、如文档侵犯您的权益,请联系客服反馈,我们会尽快为您处理(人工客服工作时间:9:00-18:30)。
模头设计的一些见解林楚漂2012年1 模头的设计趋向紧凑型设计,减小模头高度和直径,科学分布流道,从而缩短流道长度,减少熔体滞留时间;减少流道壁面面积,降低模内压力损失。
紧凑型模头设计一方面减少钢材用料,降低生产成本;另一方面有效提高薄膜质量和产量。
缩短流道减少滞留时间的作用:(1)使熔体不至于过烧形成晶点和流道线,保证薄膜质量;(2)降低熔体受流道壁加热而升高温度的影响。
模头加热温度的设定应使流道温度略高于熔体温度,提高熔体流动性,以使熔温和流动速率在圆周上分布均匀。
温度较高的流道壁将热量传递给熔体使之升温。
熔体温度升高将增大冷却负荷,降低模头产量;影响膜泡泡形,降低薄膜力学性能。
(3)缩短换料换色时间,降低生产成本。
降低模内压力损失的作用:(1)模头压力过大将对挤出机造成负荷。
高压下螺杆旋转挤出熔体会形成大量剪切热,提高熔体温度,也加大冷却风机负载。
压力回流降低挤出机产量。
(2)模头压力损失是模内熔体间以及熔体与流道壁间剪切应力的宏观表现。
熔体受剪切(摩擦)流动困难,延长滞留时间。
流动克服摩擦动能转化为热能使温度升高。
模头内压力损失并不是越小越好。
压力损失不可小于某一最小值(各种材料最小值不同)以保证足够大的熔体剪切速率,使得熔体不会粘附在流道壁上。
机器以较高产量正常开机时,各层压力约为30-35MPa为佳。
2 模头各部分流道的设计模头内流道基本可以分为4个部分:分配系统、螺旋部分、汇流部分、口模部分。
流道设计应遵循压力损失小、滞留时间短的原则。
(1)分配系统即是主流道至螺旋起始点之间的流道分配。
功能是实现熔体在圆周上均匀等分分配。
设计时应保证在1分2、2分4、4分8等各段流道内剪切速率一致,以使流动稳定,实现均匀等分。
剪切速率越低,压力损失越小。
剪切速率有最小值。
不同原料,最小剪切速率的值不同。
例如eva为3-5(s-1),LDPE8(s-1)。
根据流体力学理论,圆形截面流道压力损失与流道长度成正比,与流道直径成反比。
压力损失对流道直径的变化更加敏感。
所以,在满足输送能力和最小剪切速率的前提下,分配流道设计要尽量加大直径,缩短长度。
对于特定的模头,主流道入口与螺旋起始点的位置是相对固定的。
所以分配系统的设计应遵循“大而长,小而短”的原则。
即是说,大直径流道应尽可能拉长长度,小直径流道应尽可能缩短长度。
从而最大限度降低熔体流经分配系统的压力损失。
(2)螺旋部分流道设计目的是使熔体在圆周方向上得到均匀的温度和流动速度,从而得到高质量的薄膜。
该部分要求当改变物料、产量和料温等条件时,熔体沿圆周的分布仍然均匀。
熔体既在螺槽内沿螺槽流动,同时也在环形间隙(漏流间隙)内沿轴向流动。
螺槽内熔体流动速度在螺槽入口处最大,沿着螺槽流动速度逐渐减小直至为0。
环形间隙内的流速在入口处最小,沿着轴向逐渐变大。
随着螺槽的变浅和间隙的增大,熔体流动由主要沿螺槽的方向过渡到沿环形间隙的轴向流动。
该设计促使熔体在螺槽与环形间隙间交互流动,最终达到均化的目的。
流道总高度一般是螺距的6倍。
该高度范围内螺旋均起到作用的话足以达到均化熔体流动的目标。
为使流道在一开始就起作用,要求起始漏流间隙不得过小,最好在0.8以上。
起始漏流位置与螺槽起始处重叠。
此处设计最好经过模拟计算才能确定各项设计参数,得到一个较好的设计。
螺旋结束后较大间隙的储料段流道起到承接的作用:消除熔体沿圆周切线方向流动的影响;释放压力;储料段内熔体由于汇流段的高压阻而沿周向流动,为汇流段的均匀挤出做好准备。
(3)汇流部分流道处各层熔体贴合挤出。
该处的设计对薄膜质量有较大影响。
此处流道间隙一般很小,剪切速率大,长度不宜过长。
流道宽度应通过模拟计算来保证汇流时各层剪切速率相近,从而防止鲨鱼皮的产生。
各层熔体剪切不可能完全一致,汇流后需要一段直的成形段流道来得到稳定的层间边界。
然后才能进行流道的压缩或扩张进入口模。
(4)口模部分是最接近薄膜成型的一部分流道。
与薄膜的表面质量有直接关系。
为保证熔体稳定挤出口模,口模成形段流道之前同样需要一段储料段流道。
二者之间的过渡流道倾斜角度常取7.5°。
口模成型段应有足够长度以使流动取向稳定。
口模间隙一般在0.9-3.2间取值。
间隙小,模头产量低但是薄膜质量好,过小则薄膜表面会产生鲨鱼皮缺陷。
间隙大,模头产量高,过大则影响薄膜质量。
Opinions about die head design1 die head design tend to compact style,reduce height and diameter,distribution the channels scientifically and shorten the length of channels,reduce melt held up time;decrease channel walls area,reduce inner die pressure expense。
One side compact die head style design can reduce steels,decrease producing cost;the other side improve the film quality and output effectively。
The effect of shorten channels and reduce residence time:(1)The melt will not be over heated that form crystal dots and channel lines,ensure the quality of film;(2)Decreasing the effect of channel walls are heated up and the melt increase temperature。
Die head heat up temperature setting should make the channel temperature a little higher than melt`s,improve the flowability of melt,make the melting temperature and flow ratedistribute on the circle uniformity。
The higher temperature channel walls deliver the heat to melt and make the temperature rise。
Melt temperature rising up will increase cooling load and reduce the die head output;effect bubble shape,decrease mechanical property。
(3)shorten the time of changing material and colours,reduce producing cost。
Effects of reducing inner die pressure:(5)Too much die head pressure will cause a loading to extruder。
Under high pressure screw rotating extrude melt will form a mount of cutting heat,improve melting temperature and cooling fan loading 。
pressure backflow reduce the output of extruder。
(6)Macroscopic expression of die head pressure expense。
Melt flowing difficultly because of being cut ,so extend residence time。
Flowing put up with friction kinetic energy transform to heat and make the temperature rise。
Inner die head pressure expense is not the smaller the better。
Pressure expense cannot less than one of minimum(different material with different minimum)ensure the melt shearing rate is large enough,enable the melt will not adhere to the channel wall。
When the machine normal runs with higher output,each layer pressure is better with about 30-35MPa。
2 design of channelsDie head inner channel can be 4 parts:distribute system、spiral、conflux、die lip。
Channel design should follow the rule that little pressure expense and short resort time。
(1)Distribution system is the channel distribution from main channel to the between of spiral initial point。
The function is achieving melt uniformity distribution on the circle。
When designing we should ensure the shearing rate in 1 divides into 2、2 divides into 4、4 divides into 8 and each part of channel is accordance,enable the flowing steady and achieve aliquot uniformity。
The lower shearing rate,the less pressure expense。