铁水P含量对转炉炼钢成本的影响
08高级转炉炼钢工题库
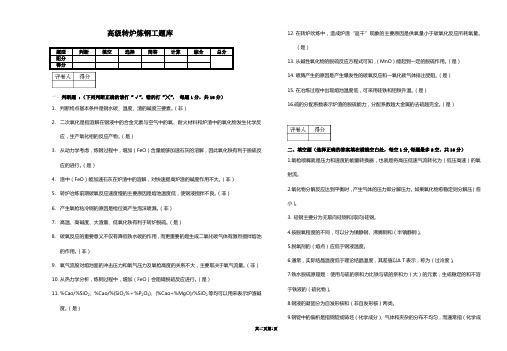
高级转炉炼钢工题库一、判断题 :(下列判断正确的请打“√”,错的打“╳”, 每题1分,共16分) 1. 判断终点基本条件是钢水碳、温度、渣的碱度三要素。
(非)2. 二次氧化是指溶解在钢液中的合金元素与空气中的氧、耐火材料和炉渣中的氧化物发生化学反应,生产氧化相的反应产物。
(是)3. 从动力学考虑,炼钢过程中,增加(FeO )含量能够加速石灰的溶解,因此氧化铁有利于脱硫反应的进行。
(是)4. 渣中(FeO )能加速石灰在炉渣中的溶解,对快速提高炉渣的碱度作用不大。
(非)5. 转炉冶炼前期碳氧反应速度慢的主要原因是熔池温度低,使钢液搅拌不良。
(非)6. 产生氧枪粘冷钢的原因是枪位高产生泡沫喷溅。
(非)7. 高温、高碱度、大渣量、低氧化铁有利于转炉脱硫。
(是)8. 碳氧反应的重要意义不仅有降低铁水碳的作用,而更重要的是生成二氧化碳气体有激烈搅拌熔池的作用。
(非)9. 氧气流股对熔池面的冲击压力和氧气压力及氧枪高度的关系不大,主要取决于氧气流量。
(非) 10. 从热力学分析,炼钢过程中,增加(FeO )会阻碍脱硫反应进行。
(是)11. %Cao/%SiO 2、%Cao/%(SiO 2%+%P 2O 5)、(%Cao+%MgO)/%SiO 2等均可以用来表示炉渣碱度。
(是) 12. 在转炉吹炼中,造成炉渣“返干”现象的主要原因是供氧量小于碳氧化反应所耗氧量。
(是) 13. 从碱性氧化物的脱硫反应方程式可知,(MnO )能起到一定的脱硫作用。
(是) 14. 喷溅产生的原因是产生爆发性的碳氧反应和一氧化碳气体排出受阻。
(是) 15. 在冶炼过程中出现熔池温度低,可采用硅铁和铝铁升温。
(是)16.硫的分配系数表示炉渣的脱硫能力,分配系数越大金属的去硫越完全。
(是)二、填空题(选择正确的答案填在横线空白处,每空1分,每题最多2空,共16分) 1.氧枪喷嘴就是压力和速度的能量转换器,也就是将高压低速气流转化为(低压高速)的氧射流。
降低钢铁料耗的攻关实践

降低钢铁料耗的攻关实践蔡霖山(福建泉州闽光钢铁有限责任公司炼钢厂,福建泉州362411)【摘要】在炼钢工序成本控制中,钢铁料耗的成本占比非常大,也是转炉冶炼工艺中一个重要的技术指标。
本文通过优化转炉冶炼过程中的原料结构、氧枪枪位流量操作模式,采取了少渣冶炼工艺、减少过程喷溅、缩短补吹时间,降低终渣铁损等相关措施,有效降低了钢铁料耗。
通过生产实践数据对比分析,经过技术攻关后,泉州闽光钢铁料耗由2020年1月份的1058.9kg/t 降到全年累计的1054kg/t 以下,12月份降至1052.23kg/t ,有效地降低了炼钢的生产成本。
【关键词】钢铁料耗成本金属铁Practical Research on Reducing Steel Material ConsumptionCai Linshan(Fujian Quanzhou Minguang Co.,Ltd.,Quanzhou 362411,Fujian )【Abstract 】In the cost control of steelmaking process,the cost of steel material consumption accounts for a very large proportion,and it is also the most important technical index in the converter smelting process.In this paper,through optimizing the raw material structure and oxygen lance flow operation mode in the converter smelting process,the relevantmeasures such as less slag smelting process,reducing process splashing,shortening blowing time,reducing final slag iron loss and so on were taken,which effectively reduced the iron and steel material consumption.Through the comparative analysis of production practice data,after tackling key technical problems,the material consumption of Quanzhou Min guang iron and Steel Ltd.has decreased from 1058.9kg/t steel in January 2020to 1054kg /t steel in the whole year,and to 1052.23kg/t steelin December.The production cost of steelmaking has been effectively reduced.【Keywords 】iron and steel consumption;cost;metal iron前言钢铁料耗是衡量炼钢技术高低的一个核心经济技术指标,其占炼钢工序总成本的80%以上。
2#转炉废钢比成本效益测算

转炉废钢比效益测算一、前提条件3、在钢铁料结构变化不大的情况下,近似认为冶炼1吨钢所需入炉原料的铁量和热量是一定值。
但硅含量变化引起的渣量变化和渣中铁损变化需计算。
4、铁水、废钢中非金属渣的SiO2按34%考虑。
二、评估转炉经济效益参数1、由于炼钢过程中,随着废钢比的增加,铁水所提供的能量将不足以满足炼钢的能量需要。
对转炉而言,就需要补充煤等燃料,由此带来氧气消耗的增加。
这些都会使冶炼周期延长。
因此,当废钢价格下降到一定程度后,随着废钢比的增加,尽管炼钢成本会降低,但生产效率将会下降,两者对炼钢经济效益的影响相反。
为合理评价废钢比变化对冶炼经济效益的最终影响,此处采用“工序效益”指标来评估炼钢经济效益。
定义Q为工序效益,即Q=B/Tt式中:B为吨钢水利润,元/t(钢);Tt为冶炼周期,min。
因此,工序效益Q为单位时间内转炉所产生的吨钢利润。
B和Tt是分别从两个不同方面来反映炼钢的经济效益的,B从成本费用角度来反映,而冶炼周期Tt则从生产效率也即生产规模效应来反映效益。
当废钢价格低于铁水价格一定程度后,随着废钢比的增加,炼钢成本会下降,吨钢水利润B会增加,而冶炼时间Tt则延长,生产效率下降,因此预计在某一废钢比时,Q可能会出现最大值,则此时的炼钢经济效益最大化,此时的炉料结构为最佳炉料结构,也即最佳废钢比。
2、炼钢吨钢水利润计算炼钢吨钢水的利润B按下式计算。
B=η*Ps-η铸坯成本式中:Ps为铸坯价格,元/t;η为钢水到铸坯的收得率,%;计算中原辅料和各种能源介质价格、铁合金等主要参考现有价格,价格统一采用税前价格。
3、转炉冶炼周期确定转炉冶炼时间(tL)包括吹氧时间(to)和辅助时间(ta)的确定。
辅助时间包括加废钢、兑铁水、测温取样、出钢、倒渣、补炉及溅渣护炉等操作,对于50t 转炉,此处综合取ta=15min。
设冶炼过程中转炉平均吹氧强度为qO2,供氧强度主要和转炉炉容量、炉容比及铁水成分有关。
铁水“三稳”供应对炼钢工艺的影响

铁水“三稳”供应对炼钢工艺的影响一、铁水温度对炼钢的影响铁水温度的高低对炼钢的影响很大,根据转炉冶炼工艺,转炉冶炼的热量基本来源于铁水的物理热和化学热,在化学热一定的情况下,铁水的物理热是决定冶炼能否顺利的关键因素。
铁水温度低造成吹损大,钢铁料消耗高,钢水质量无保障,炉龄下降等后果。
铁水温度不仅对炼钢工艺十分重要,对于铁水输送也有影响,如果铁水在输送过程中的温度过低,还会造成铁水罐车的结壳、结瘤,直接影响正常生产作业。
因此,铁水输送过程中的温降是冶金工作者普遍关注的问题。
多年来,国内外许多研究人员曾对这一问题进行研究。
铁水从高炉输送到炼钢厂转炉,要经过出铁、运输、扒渣、预处理、倒罐、空罐返回和等待等一系列工序,其中每一工序和铁水罐的自身状态对于铁水温降都有影响。
钢铁企业的特点一般是高炉多、铁水用户多、运输铁水的罐车多,而且铁水车在厂内各处游动,难以定位跟踪。
这些原因增加了控制铁水输送过程及减小铁水温降难度。
转炉冶炼工艺告诉我们,转炉冶炼的热量基本来源于铁水的物理热和化学热,在化学热一定的情况下,铁水的物理热是决定冶炼能否顺行的关键因素,特别是公司当前正处于低成本战略的关键时期,铁水温度如果波动大,常会影响转炉炉前一批料矿石摄入量不准确,造成终点温度过低或过高,导致钢水后吹严重,吹损大,钢铁料消耗高,成本高,钢水质量无保障,炉龄下降,并危及安全生产等严重后果。
所以,入炉铁水温度保持稳定对转炉工序意义重大。
二、铁水硅含量对炼钢工艺影响在实际生产中, 硅高时,点火开氧后便可加入造渣料,以形成具有一定碱度及脱磷效果的初渣,减少对炉衬的侵蚀,加强对金属液面的覆盖。
硅低时,由于先发生的是碳的氧化反应,没有早期生成的酸性初渣, 并且碳的氧化产物使渣中( FeO ) 减少,这时加入造渣料不但不会熔化,还由于造渣料的加入而形成很大的降温效应,从而起到一定的负面影响,这就是硅过低时造渣料加入过早使后期出现炉渣严重返干的原因,由于后期吹炼时主要是碳的氧化,不利形成有利化渣的( FeO )出现,降低渣的流动性,影响去硫、去磷效果,且渣不能很好的覆盖在金属液面上,加剧金属喷溅的发生,出现炉口、氧枪粘钢现象, 严重时甚至粘死烟道,造成停产事故。
转炉炼钢工初级考试(试卷编号131)

转炉炼钢工初级考试(试卷编号131)1.[单选题]转炉未燃法烟气主要成份是_。
A)COB)CO2C)N2答案:A解析:2.[单选题]物料平衡计算中,加入炉内参与炼钢过程的全部物料,除铁水、废钢、渣料外,还包括。
A)氧气B)被侵蚀的炉衬C)氧气和炉衬答案:C解析:3.[单选题]有底吹的复吹转炉溅渣的总量略高于顶吹转炉,溅渣量主要增加在炉衬的_____。
A)上部B)中部C)下部答案:C解析:4.[单选题]氧气顶吹转炉炼钢中,吹损的主要部分是( )。
A)机械损失B)化学损失C)炉渣中金属珠损失答案:B解析:5.[单选题]在转炉炉壳结构中钢板最厚的部位是( )。
A)炉口B)炉帽C)炉身D)炉底答案:C解析:6.[单选题]转炉炼钢回锰反应主要发生在冶炼( )期。
A)前B)中C)中后D)前中答案:C解析:7.[单选题]在氧化钙(CaO),氧化亚铁(FeO),二氧化硅(SiO2)三元状态图中,代表三元共晶点的渣系氧化物是 。
A)2CaOSiO2B)2FeOSiO2C)CaOFeOSiO2D)CaOFeO答案:C解析:8.[单选题]废钢是氧气转炉炼钢的金属料之一,冷却效应比较稳定,一般占装入量的( )。
A)10%~20%B)10%~30%C)20%~30%D)10%以下答案:A解析:9.[单选题]炉渣三元系相图中,常用____代替三个组元。
A)CaO、SiO2、MnOB)CaO、FeO、P2O5C)CaO、SiO2、FeOD)CaO、SiO2答案:C解析:10.[单选题]应用真空的炉外精炼方法主要以( )为目的。
A)脱氧B)脱硫C)脱气D)脱碳答案:C解析:11.[单选题]炼钢厂复吹采用了双环缝式底吹供气元件。
环缝式底吹供气元件特点____。
A)由多层不锈钢无缝钢管组成B)每个底吹供气元件的气量C)可以通过计算机单独检测与控制D)相对抽引提升钢水量小答案:A解析:12.[单选题]石灰的灼减量是衡量石灰的一个指标之一,它表示的是( )。
铁水锰对炼钢成本影响

1.铁水锰由5月0.553%提高到6月0.623%,转炉终点残锰由0.17%提高到0.18%。
铁水锰氧化量为:(0.623%-0.18%)*1000=4.43kg/t铁。
增加成本为:4.43*3.05=13.5元/吨。
转炉提高残锰降低硅锰成本为:(0.18%-0.17%)/(65%*90%)*1000*8.5=1.45元/t。
则提高铁水锰,转炉增加成本:13.5-1.45=1
2.06元/t。
2.铁水锰由6月0.623%提高到4月0.816%,转炉终点残锰由0.18%提高到0.19%。
铁水锰氧化量为:(0.816%-0.19%)*1000=6.26kg/t铁。
增加成本为:6.26*
3.05=19.09元/吨。
转炉提高残锰降低硅锰成本为:(0.19%-0.18%)/(65%*90%)*1000*8.5=1.45元/t。
则提高铁水锰,转炉增加成本:19.09-1.45=17.64元/t。
3.转炉出现成本增加主要是转炉终点碳控制太低,造成殘锰低,按常规HRB335、HRB400、HPB235终点碳控制在0.15%,终点殘锰将提高到0.28%以上。
但目前铁水P高,转炉采用双渣法和高拉补吹降低终点P, 双渣法倒掉部分高锰炉渣,降低了锰的还原,高拉补吹降低P的同时也降低了锰。
因此根据目前铁水P高的条件,还做不到拉高碳提高殘锰一倒直接出钢的条件。
转炉炼钢原料及装入制度
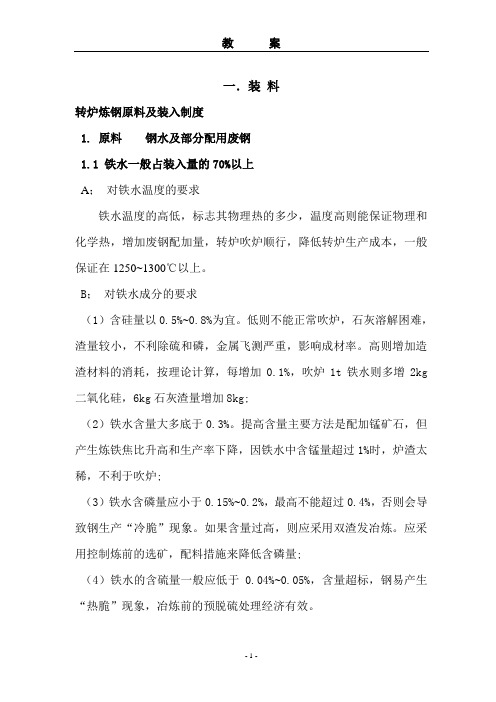
一.装料转炉炼钢原料及装入制度1. 原料钢水及部分配用废钢1.1 铁水一般占装入量的70%以上A;对铁水温度的要求铁水温度的高低,标志其物理热的多少,温度高则能保证物理和化学热,增加废钢配加量,转炉吹炉顺行,降低转炉生产成本,一般保证在1250~1300℃以上。
B;对铁水成分的要求(1)含硅量以0.5%~0.8%为宜。
低则不能正常吹炉,石灰溶解困难,渣量较小,不利除硫和磷,金属飞测严重,影响成材率。
高则增加造渣材料的消耗,按理论计算,每增加0.1%,吹炉1t铁水则多增2kg 二氧化硅,6kg石灰渣量增加8kg;(2)铁水含量大多底于0.3%。
提高含量主要方法是配加锰矿石,但产生炼铁焦比升高和生产率下降,因铁水中含锰量超过1%时,炉渣太稀,不利于吹炉;(3)铁水含磷量应小于0.15%~0.2%,最高不能超过0.4%,否则会导致钢生产“冷脆”现象。
如果含量过高,则应采用双渣发冶炼。
应采用控制炼前的选矿,配料措施来降低含磷量;(4)铁水的含硫量一般应低于0.04%~0.05%,含量超标,钢易产生“热脆”现象,冶炼前的预脱硫处理经济有效。
表1-1 国内一些钢厂的铁水成分 %1.2 废钢它是转炉炼钢的另一种金属炉料,作用为冷却剂消耗富余热量,调控熔池温度。
基本要求:情结、少锈、无混杂、不含有色金属,单重波动范围为150~2000kg。
2.转炉的装入制度制度包括:装入量、废钢、装料顺序。
2.1 装入量的确定①定量装入法; ②定深装入法; ③分阶段定量装入法。
表1-2 国内一些转炉的熔池深度表表1-4 太原钢厂原50吨转炉装入制度2.2 废钢比废钢的加入量占金属料装入量的百分比成为废钢比。
管理水平及冶炼品种不同,废钢比大多波动在10%~30%之间。
2.3 装料顺序一般情况下是先加废钢后兑铁水。
在炉役后期, 炉衬较薄, 为免受废钢直接冲击, 在确认废钢干燥及炉渣已倒净或已加入石灰稠化的前提下, 可先兑铁水后加废钢。
钢铁冶金学炼钢部分
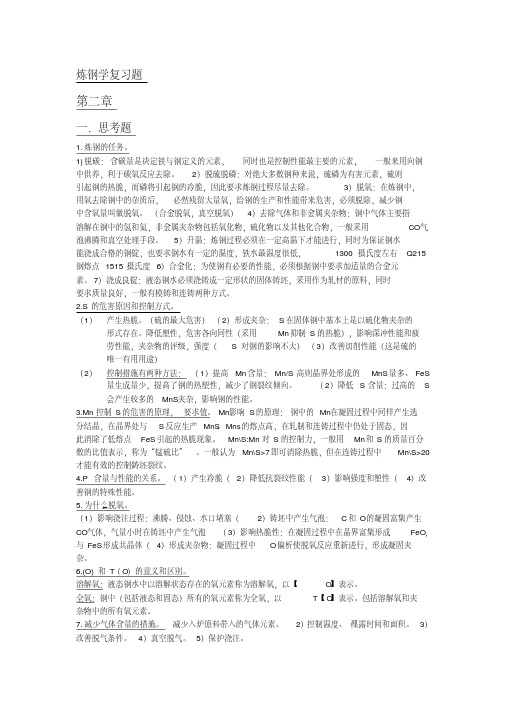
炼钢学复习题第二章一.思考题1.炼钢的任务。
1)脱碳:含碳量是决定铁与钢定义的元素,同时也是控制性能最主要的元素,一般来用向钢中供养,利于碳氧反应去除。
2)脱硫脱磷:对绝大多数钢种来说,硫磷为有害元素,硫则引起钢的热脆,而磷将引起钢的冷脆,因此要求炼钢过程尽量去除。
3)脱氧:在炼钢中,用氧去除钢中的杂质后,必然残留大量氧,给钢的生产和性能带来危害,必须脱除,减少钢中含氧量叫做脱氧。
(合金脱氧,真空脱氧)4)去除气体和非金属夹杂物:钢中气体主要指溶解在钢中的氢和氮,非金属夹杂物包括氧化物,硫化物以及其他化合物,一般采用CO气泡沸腾和真空处理手段。
5)升温:炼钢过程必须在一定高温下才能进行,同时为保证钢水能浇成合格的钢锭,也要求钢水有一定的温度,铁水最温度很低,1300摄氏度左右 Q215钢熔点1515摄氏度6)合金化:为使钢有必要的性能,必须根据钢中要求加适量的合金元素。
7)浇成良锭:液态钢水必须浇铸成一定形状的固体铸坯,采用作为轧材的原料,同时要求质量良好,一般有模铸和连铸两种方式。
2.S的危害原因和控制方式。
(1)产生热脆。
(硫的最大危害)(2)形成夹杂:S在固体钢中基本上是以硫化物夹杂的形式存在。
降低塑性,危害各向同性(采用Mn抑制S的热脆),影响深冲性能和疲劳性能,夹杂物的评级,强度(S对钢的影响不大)(3)改善切削性能(这是硫的唯一有用用途)(2)控制措施有两种方法:(1)提高Mn含量:Mn/S高则晶界处形成的MnS量多、FeS 量生成量少,提高了钢的热塑性,减少了钢裂纹倾向。
(2)降低S含量:过高的S 会产生较多的MnS夹杂,影响钢的性能。
3.Mn控制S的危害的原理,要求值。
Mn影响S的原理:钢中的Mn在凝固过程中同样产生选分结晶,在晶界处与S反应生产MnS。
Mns的熔点高,在轧制和连铸过程中仍处于固态,因此消除了低熔点FeS引起的热脆现象。
Mn\S:Mn对S的控制力,一般用Mn和S的质量百分数的比值表示,称为“锰硫比”。
铁水磷含量对转炉炼钢经济效益的影响分析
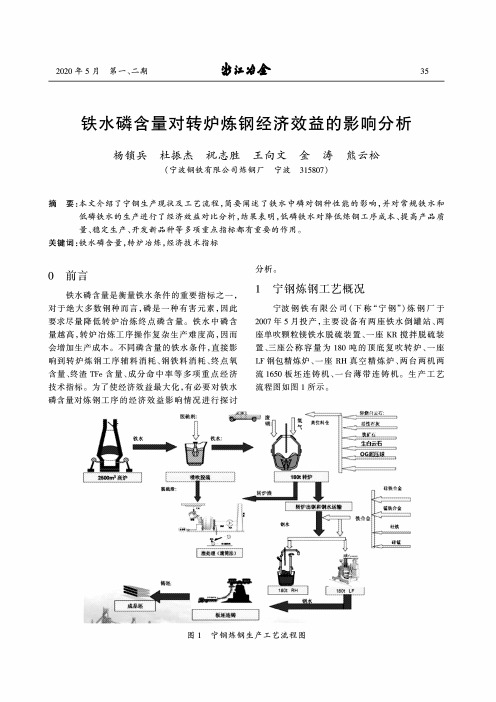
图1宁钢炼钢生产工艺流程图
36
2020年5月第一、二期
转炉造渣料以石灰和菱镁石为主,根据生产钢 种和铁水条件,适当采用石灰石替代部分石灰的炼 钢工艺,主要调温料为OG泥压球和烧结矿。
2铁水磷含量对转炉炼钢的影响
2.1铁水条件 铁水是转炉炼钢的主要原料,占入炉量的
70%〜100%,宁钢铁水比控制在86%左右。铁水 的物理热和化学热是转炉炼钢的基本热源,铁水成 分直接影响到炉内的温度、化渣情况和钢水质量。 铁水中的磷是冶炼过程重要的发热元素之一,但对 于绝大多数钢种来说,磷是有害元素,因此铁水含 磷量越低越有利于转炉冶炼工序脱磷控制。由于 磷在高炉中是基本不可能去除的元素,因此脱磷任 务主要由转炉工序承担,转炉冶炼要求进入转炉的 铁水磷含量较低且稳定。
表1铁水条件
元素平均含量/%
-平均温度/%
Si
P
S
0.35
0.130
0.039
1355
2.2铁水中的磷元素 高炉原料中的磷主要以磷酸钙Ca2(PO4)2形态
存在,有时也以蓝铁矿[(PO)3-P2O5]-8H20形态存 在。蓝铁矿脱水后比较容易还原,磷酸钙是很稳定 的化合物,它在高炉内首先进入炉渣,被炉渣中 SiO2置换出自由态的P2O5,再进行直接还原"I。
4铁水磷含量对转炉经济效益的影 响
4.1经济技术指标对比 宁钢常规铁水磷含量0.130%,曾有一段时间
铁水磷含量0.106%,铁水磷含量改变后,转炉重点 指标发生明显提升。为了分析铁水磷含量对转炉 炼钢经济效益的影响情况,对常规铁水条件和低磷 铁水条件的生产指标进行了对比分析,数据情况如 表2所75。
在高炉条件下,炉内有大量的C,炉渣中有过 量的SiO2,自由态的P2O5能够全部还原为P,还原 出来的P几乎全部溶解在生铁中,脱磷的任务只能 由炼钢工序去除。 2.3磷对钢种性能的影响
转炉车间进一步提升产品质量方案

转炉车间进一步提升产品质量方案为了进一步提升产品质量,根据当前物料、铁水等条件,我车间对存在问题和下一步如何提升产品质量做了深入分析,具体如下:一、存在问题1、铁水方面(1)铁水带渣量大:由于现行的生产节奏较快,能够进行扒渣的铁水罐数相对较少,另外从操作上看,铁水带入大量酸性渣,对于转炉工艺前期脱磷带来了很大影响,势必降低脱磷效果和增加石灰消耗。
(2)铁水P含量高:铁水P含量平均达到0.180%,比同行业平均水平高较多,转炉脱磷困难,特别是冶炼低P品种钢,为了脱磷,转炉只能采取双渣操作和补吹,导致吹损增大。
(3)铁水Si含量高,且波动大:给转炉炉前操作带来很大的难度,吹炼过程容易喷溅,终点成分、温度偏差较大。
(4)铁水装入量不稳定:由于供应的铁水每一罐的重量都不同,炉前兑铁只能凭借摇炉工按经验兑入,导致装入量不稳定,吹炼过程控制和终点控制方面的难度较大。
2、铁块、废钢方面(1)铁块装入量过大:按照目前的生产模式铁块的加入量占废钢总量的90%以上,给转炉操作带来的很大影响,特别是中后期铁块大量融化,容易产生喷溅,同时带入大量的P、S等有害元素,给转炉终点成分控制带来很大压力。
(2)铁块成份未知:铁块成分未知对转炉冶炼操作带来很大影响,特别是铁块S含量高,导致倒炉回S严重。
3、石灰质量方面当前我厂石灰活性度不到300ml,有效CaO不到85%,石灰自身含P量高等问题,导致了转炉脱磷效果较差。
4、脱氧剂方面现行脱氧剂结构不是很合理,建议采用一种含铝脱氧合金取代现行脱氧剂,避免直上钢水出现氧高质量问题。
5、合金、辅料供我厂合金、辅料含P、S高,生产低P、低S钢水时,容易导致过程增P、增S,特别是生产合金钢时,出钢过程增P较多。
6、氩站喂丝机、底吹氩问题氩站喂丝机不好用,底吹氩均为手动调节,效果不好,不利于直上工艺推行。
7、挡渣车设备故障多,挡渣命中率低,造成炉前出钢下渣,回P较严重。
经查大约80%的改判、改炼钢种都是由于下渣导致的。
铁水中磷增加对炼钢成本的影响

Si(%)Mn(%)P(%)S(%)T(℃)0.4660.3050.0960.0311300.21铁水(t)废钢(t)生铁(t)渣钢(t)68.96 5.547.93 1.88C(%)Mn(%)常规钢0.09340.1458品种钢0.14190.1174合计0.11510.13311、石灰消耗增加增加的成本6222468000*0.054%2830为废钢价格每炉的装入量:铁水:68吨,废钢+生铁+渣钢:16吨;成坯量平均为:76.5吨铁水中磷增加对转炉炼钢成本的影响一、现状炉渣中Tfe为15%2、吹损的增加造成的成本损失(2)由于渣量增加造成的金属损失:2.93*366/224*15%=0.7181kg/t折算成吹损0.7181*76.5*10-3/84*100%=0.0654%计算铁水中增加0.054%[P]需要增加的成本:增加石灰的消耗是68000*0.054%*224/62/84.69%/70%/76.5=2.93kg/t 增加的石灰成本是2.93kg/t*0.385元/kg=1.13元/t转炉熔池内脱磷的化学反应方程式为2[P]+5(FeO)+4(CaO)=(4CaO.P2O5)+5[Fe]所以吹损合计增加:0.1514+0.0654=0.2168%目前炼钢转炉使用的石灰的有效CaO是90%-3.2*1.66=84.69%;石灰的有效利用率为70%;76.5吨为炼钢(1)由于铁水磷的增加和终点碳锰的降低造成的吹损的增加量为:(68*0.054%+76.5*(0.1151-0.06)%+76.5*(0.1331-0.07)%)/84=0.1514%2011年元月1日至5月23日冶炼炉前的大致情况如下:1、铁水情况2、炉料结构3、终点控制二、使用高磷铁水后,对转炉炼钢成本的影响(所有的计算都是基于铁水磷提高,而其他条件不变)假设随着铁水中磷增加到0.150%,转炉炉前的终点碳综合平均只有到0.06%,终点锰综合平均只有0.07%;转炉炉前被迫使用双渣,冶炼周期增加3分钟/炉,周期延长转炉的温降增加,使用双渣,炉渣带走热量和金属;转炉炉前的吹损增加;由于石灰消耗增加,转炉炉内温度损失增加和金属料消耗增加;由于吹损提高造成少产钢增加的成本是84t*0.2168%*2830元/t/76.5t=6.80元/t7、由于铁水磷提高到0.150%造成的转炉炼钢成本增加为1.13+6.8+0.44+8.19+1.55+7.38+25+6.73+15=72.22元/t (2)由于周期延长3分钟,按5℃/分钟计算,造成温度损失为15℃,增加成本15元/t;(3)由于终点碳的下降会造成每炉钢的脱氧剂硅铝钙钡增加60公斤所增加的成本:60/1000*9400/76.5=7.38元/t;其中9400为硅铝钙钡的价格5、由于使用双渣操作,造成冶炼周期延长3分钟/炉,炉前满负荷生产平均周期35分钟,每天生产120炉钢;使用双渣后每天时间浪费360分钟,少炼360/35=10炉钢,按炉产76.5吨计算,少产钢765吨,按300元/t利润计算,由于少产钢造成的成本损失为765*300/120/76.5=25元/t;6、由于渣料增加和周期延长造成温度损失的成本增加为:(1)由于石灰增加造成每炉钢的温度损失为2.93kg/t*76.5t*30℃/吨/1000=6.73℃,每降低1℃增加成本1元计算,由于温度损失造成成本升高了6.73元/t;(1)终点锰下降造成硅锰成本的升高:76.5*(0.1331-0.07)%/90%/65%*7590/76.5=8.19元/t (2)终点碳下降造成石墨增碳剂成本的增加:76.5*(0.1151-0.06)%/75%/90%*1900/76.5=1.55元/t 式中90%为锰的回收率,65%为硅锰中锰的含量;7590为硅锰的价格式中75%为石墨的回收率,90%为石墨含量,1900为石墨价格4、由于终点碳锰的下降造成合金、石墨和脱氧剂增加造成的成本增加每炉钢增加的氧耗的成本:47.35m3/0.995*0.7元/m3/76.5t=0.44元/t3、增加的耗氧量是68000*0.054%*5*16/2/31/70%=67.66kg/炉一标准压力下(1atm)的氧气密度是1.429g/升,所以每炉的氧气消耗是67.66/1.429=47.35m3氧气利用率为70%。
电炉钢与转炉钢成本比较

电炉钢与转炉钢成本比较1引言钢铁生产可分为“从铁矿石到钢材”和“从废钢到钢材”两大流程。
相对于钢铁联合企业中以高炉-转炉为代表的常规流程而言,以废钢为主原料的电弧炉炼钢生产具有工序少、投资低和建设周期短的特点,因而被称为短流程。
近年来,我国废钢资源产生量增多,电力条件改善,国家政策导向支持为电炉钢的发展创造了一定的条件,但电炉钢的发展仍存在一些制约因素,一是废钢资源质量参差不齐,二是电炉钢成本竞争力不强,废钢与铁水价差不能长期支撑电炉钢成本竞争力,国内总体电价水平较高,石墨电极价格高且波动较大,造成电炉钢成本控制难度大。
钢铁企业排放指标要求越来越严,钢铁企业排放的污染物80%来自焦化、烧结等环节,长流程炼钢的弊端日渐明显。
系统的比较电炉钢和转炉钢成本,以及长短流程能耗与排放,可供发展电炉钢企业参考,具有重要意义。
2、电炉钢发展新技术电炉炼钢新技术主要有铁水+废钢冶炼技术、强化用氧技术、伸缩炉盖电炉技术、新型康斯迪电炉炼钢技术、新型量子电炉炼钢技术等。
未来电炉炉型的发展方向是能实现连续加料、废钢预热、绿色环保、余热回收及人工智能型炼钢的电炉。
目前,我国康斯迪电炉占总电炉数量70%左右,建设较早的电炉企业一般为非连续加料的普通电炉。
2.1伸缩炉盖电炉技术德国福克斯技术公司为实现电炉一篮料操作,开发了伸缩炉盖技术,在普通电炉基础上增加炉壳高度、增加炉盖的升降行程,有利于缩短非通电时间、提高生产率。
运行效果:吨钢吹氧小于30Nm3/t,天然气4 Nm3/t;电耗369 kWh/t,电极消耗0.91 kg/t,一篮料加料次数由40%增加至54%。
2.2新型康斯迪电炉炼钢技术新型康斯迪电炉,其主要特点及优越性:炉体称量装置安装位置,由倾动平台下四个滚轮内,改为安装在倾动平台上方的四个角,依四个称量单元来测量工作状态的炉体重量,该方式安装、维护方便,故障率小;缩短废钢预热段的长度,提高烟气出口温度;控制野风的混入,强化预热段内的二次燃烧,保证出口温度在800 ~ 900 °C,抑制二噁英的产生;电炉炉底设置底吹装置,在废钢下料区炉底设置底吹装置,改善熔池钢水温度偏差,缩短冶炼周期;在废钢预热段设置挡板,防止电极极心圆偏位。
降低钢铁料消耗的探索
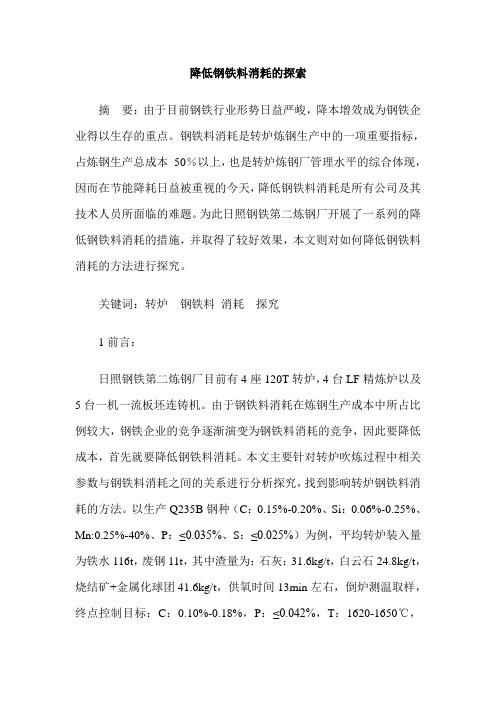
降低钢铁料消耗的探索摘要:由于目前钢铁行业形势日益严峻,降本增效成为钢铁企业得以生存的重点。
钢铁料消耗是转炉炼钢生产中的一项重要指标,占炼钢生产总成本50%以上,也是转炉炼钢厂管理水平的综合体现,因而在节能降耗日益被重视的今天,降低钢铁料消耗是所有公司及其技术人员所面临的难题。
为此日照钢铁第二炼钢厂开展了一系列的降低钢铁料消耗的措施,并取得了较好效果,本文则对如何降低钢铁料消耗的方法进行探究。
关键词:转炉钢铁料消耗探究1前言:日照钢铁第二炼钢厂目前有4座120T转炉,4台LF精炼炉以及5台一机一流板坯连铸机。
由于钢铁料消耗在炼钢生产成本中所占比例较大,钢铁企业的竞争逐渐演变为钢铁料消耗的竞争,因此要降低成本,首先就要降低钢铁料消耗。
本文主要针对转炉吹炼过程中相关参数与钢铁料消耗之间的关系进行分析探究,找到影响转炉钢铁料消耗的方法。
以生产Q235B钢种(C:0.15%-0.20%、Si:0.06%-0.25%、Mn:0.25%-40%、P:≤0.035%、S:≤0.025%)为例,平均转炉装入量为铁水116t,废钢11t,其中渣量为:石灰:31.6kg/t,白云石24.8kg/t,烧结矿+金属化球团41.6kg/t,供氧时间13min左右,倒炉测温取样,终点控制目标:C:0.10%-0.18%,P:≤0.042%,T:1620-1650℃,保证出钢过程为红包出钢,脱氧合金化顺序为:硅钙钡镁球、硅锰、硅铁、铝铁;挡渣采用挡渣塞+挡渣锥双重挡渣措施,严禁出钢下渣。
2 影响钢铁料消耗的原因分析第二炼钢厂2011年Q235B钢铁料消耗居高不下,全年累计消耗达到1076.5 kg /t。
通过不断的摸索和实践,2012年Q235B钢铁料消耗达到1048.4 kg /t。
,经统计分析认为影响钢铁料消耗的主要因素包括以下几个方面。
2.1 转炉入炉铁水Si、温度对钢铁料消耗的影响由于第二炼钢厂转炉车间没有混铁炉,铁水成分波动较大,Si 高时可以达到0.89%,低时只有0.05%,温度高时可以达到1429℃,低时只有1200℃,由于铁水条件较差,其Si 成分波动大,给转炉的操作带来很大的影响,高Si 铁水的大渣量冶炼,溢渣、喷溅频繁,遇到低Si 铁水时易因热量不充足、操作不当造成终点温度过低,后吹时间较长,使渣中氧化铁含量大增,增加了铁损。
炼钢原料配方
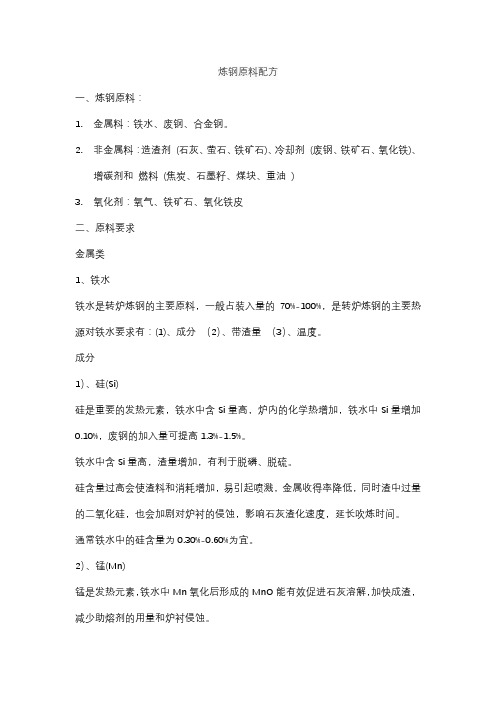
炼钢原料配方一、炼钢原料:1.金属料:铁水、废钢、合金钢。
2.非金属料:造渣剂(石灰、萤石、铁矿石)、冷却剂(废钢、铁矿石、氧化铁)、增碳剂和燃料(焦炭、石墨籽、煤块、重油)3.氧化剂:氧气、铁矿石、氧化铁皮二、原料要求金属类1、铁水铁水是转炉炼钢的主要原料,一般占装入量的70%-100%,是转炉炼钢的主要热源对铁水要求有:(1)、成分(2)、带渣量(3)、温度。
成分1)、硅(Si)硅是重要的发热元素,铁水中含Si量高,炉内的化学热增加,铁水中Si量增加0.10%,废钢的加入量可提高1.3%-1.5%。
铁水中含Si量高,渣量增加,有利于脱磷、脱硫。
硅含量过高会使渣料和消耗增加,易引起喷溅,金属收得率降低,同时渣中过量的二氧化硅,也会加剧对炉衬的侵蚀,影响石灰渣化速度,延长吹炼时间。
通常铁水中的硅含量为0.30%-0.60%为宜。
2)、锰(Mn)锰是发热元素,铁水中Mn氧化后形成的MnO能有效促进石灰溶解,加快成渣,减少助熔剂的用量和炉衬侵蚀。
同时铁水含Mn高,终点钢中余锰高,从而可以减少合金化时所需的锰铁合金,有利提高钢水纯净度。
转炉用铁水对锰与硅比值要求为0.8-1.0,目前使用较多的为低锰铁水,锰的含量为0.20%-0.80%3)、磷(P)磷是高发热元素,对一般钢种来说是有害元素,因此要求铁水磷含量越低越好,一般要求铁水P ≤0.20%。
4)、硫(S)除了含硫易切削以外,绝大多数钢种要求去除硫这一有害元素。
氧气转炉单渣操作的脱硫效率只有30%-40%。
我国炼钢技术规程要求入炉铁水的硫含量不超过0.05%。
对铁水带渣量的要求高炉渣中含硫、Si0、和A1,0;量较高,过多的高炉渣进入转炉内会导致转炉钢渣量大,石灰消耗增加,造成喷溅,降低炉衬寿命,因此,进入转炉的铁水要求带渣量不得超过0.5%。
2、废钢转炉和电炉炼钢均使用废钢,氧气顶吹转炉用废钢量一般是总装入量的10%-30%。
转炉炼钢对废钢的要求1)废钢的外形尺寸和块度应保证能从炉口顺利加入转炉。
转炉炼钢工高级考试(试卷编号181)

转炉炼钢工高级考试(试卷编号181)1.[单选题]脱氧元素的脱氧能力是以一定温度下与溶于钢液中一定量脱氧元素相平衡的钢液中氧的浓度来表示的。
和一定浓度的脱氧元素成平衡的氧含量越低,这种元素脱氧的能力( )。
A)越强B)越弱C)不变答案:A解析:2.[单选题]氧气顶吹转炉操作中,兑入炉内的铁水其物理热( )于化学热。
A)高B)低C)相近答案:C解析:3.[单选题]炉衬永久层的主要作用是( )。
A)对炉壳钢板起保护作用B)缓冲工作层受热膨胀时对炉壳的挤压作用C)承受因温度的激剧变化产生的热应力和其它外力的作用答案:A解析:4.[单选题]有关终点控制,下列说法正确的是( )。
A)终点控制实际上是指终点成分和温度的控制B)终点控制实际上是指终点氧含量和温度的控制C)终点控制实际上是指终点成分和钢水氧含量的控制答案:A解析:5.[单选题]脱碳速度加快,炉渣氧化性( )。
A)大大增强B)变化不大C)大大减弱答案:C解析:6.[单选题]有底吹的复吹转炉溅渣的总量略高于顶吹转炉,溅渣量主要增加在炉衬的_____。
C)下部答案:C解析:7.[单选题]当钢中碳含量升高时,对钢的性能影响是( )。
A)降低钢的硬度和韧性B)提高钢的强度和塑性C)焊接性能显著下降答案:C解析:8.[单选题]炉渣的氧化能力通常用(∑FeO%)表示,其具体含义为( )。
A)(FeO%)+1.35(Fe2O3%)B)FeO%C)(Fe%)×1.287答案:A解析:9.[单选题]钢液中气泡形成,上浮的条件是气泡的压力要( )外界大气压力,钢液静压力及表面张力之和。
A)小于B)等于C)大于答案:C解析:10.[单选题]炉渣泡沫化的形成主要原因是( )。
A)炉渣中(FeO)含量高B)炉渣温度高C)炉渣表面张力低及小气泡产生答案:C解析:11.[单选题]氧化物分解反应达平衡时,产生气体的压力称分解压力,如果氧化物愈稳定,则( )。
A)分解压愈大B)分解压愈小C)与分解压大小无关答案:B解析:B)扩散脱氧C)真空下脱氧答案:A解析:13.[单选题]活动烟罩的作用是( )。
转炉炼钢对铁水成分和温度有什么要求?
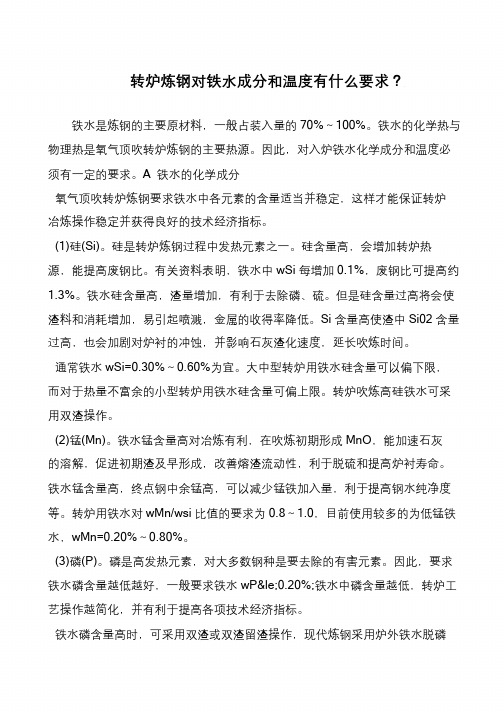
立志当早,存高远转炉炼钢对铁水成分和温度有什么要求?铁水是炼钢的主要原材料,一般占装入量的70%~100%。
铁水的化学热与物理热是氧气顶吹转炉炼钢的主要热源。
因此,对入炉铁水化学成分和温度必须有一定的要求。
A 铁水的化学成分氧气顶吹转炉炼钢要求铁水中各元素的含量适当并稳定,这样才能保证转炉冶炼操作稳定并获得良好的技术经济指标。
(1)硅(Si)。
硅是转炉炼钢过程中发热元素之一。
硅含量高,会增加转炉热源,能提高废钢比。
有关资料表明,铁水中wSi 每增加0.1%,废钢比可提高约1.3%。
铁水硅含量高,渣量增加,有利于去除磷、硫。
但是硅含量过高将会使渣料和消耗增加,易引起喷溅,金属的收得率降低。
Si 含量高使渣中Si02 含量过高,也会加剧对炉衬的冲蚀,并影响石灰渣化速度,延长吹炼时间。
通常铁水wSi=0.30%~0.60%为宜。
大中型转炉用铁水硅含量可以偏下限,而对于热量不富余的小型转炉用铁水硅含量可偏上限。
转炉吹炼高硅铁水可采用双渣操作。
(2)锰(Mn)。
铁水锰含量高对冶炼有利,在吹炼初期形成MnO,能加速石灰的溶解,促进初期渣及早形成,改善熔渣流动性,利于脱硫和提高炉衬寿命。
铁水锰含量高,终点钢中余锰高,可以减少锰铁加入量,利于提高钢水纯净度等。
转炉用铁水对wMn/wsi 比值的要求为0.8~1.0,目前使用较多的为低锰铁水,wMn=0.20%~0.80%。
(3)磷(P)。
磷是高发热元素,对大多数钢种是要去除的有害元素。
因此,要求铁水磷含量越低越好,一般要求铁水wP≤0.20%;铁水中磷含量越低,转炉工艺操作越简化,并有利于提高各项技术经济指标。
铁水磷含量高时,可采用双渣或双渣留渣操作,现代炼钢采用炉外铁水脱磷。
铁水扒渣工艺对转炉冶炼的影响研究

第29卷第4期2019年10月㊀㊀㊀㊀㊀㊀安徽冶金科技职业学院学报JournalofAnhuiVocationalCollegeofMetallurgyandTechnology㊀㊀㊀㊀㊀㊀Vol.29.No.4Oct.2019铁水扒渣工艺对转炉冶炼的影响研究宋㊀健ꎬ朱李艳ꎬ何宏涛ꎬ吴发达(马钢股份公司第一钢轧总厂㊀安徽马鞍山㊀243000)摘㊀要:通过分析铁水渣及转炉终点渣的成分ꎬ分别研究了扒渣量对转炉造渣料(石灰及镁球)消耗及转炉终点渣的影响ꎬ结合工业试验数据ꎬ得出如下结论:铁水扒渣工艺可以降低转炉造渣料及钢铁料消耗ꎬ减少转炉渣量ꎬ从而改善转炉的冶炼环境ꎬ提高钢水的冶炼质量ꎬ降低冶炼困难与成本ꎮ关键词:铁水扒渣ꎻ转炉ꎻ造渣料消耗中图分类号:TF546+.2㊀文献标识码:B㊀文章编号:1672-9994(2019)04-0028-03㊀㊀改善铁水质量是提高转炉技术经济指标的重要途径ꎬ因此铁水进入转炉前除了要经过脱硫㊁脱磷等预处理操作外ꎬ一般都要经过铁水扒渣处理ꎬ扒渣量对转炉造渣料的消耗ꎬ转炉终渣量ꎬ钢铁消耗量等都有影响ꎮ在高炉出铁过程中ꎬ虽然采取了多种措施降低铁水带渣量ꎬ但是一般高炉铁水中仍然存在2ɢ-5ɢ的铁水渣[1]ꎮ由于铁水渣的存在ꎬ恶化了转炉的冶炼条件ꎮ张定基[2]通过计算发现铁水扒渣50%时ꎬ转炉料中总的硫含量降低29%ꎮ工业实践[3]-[5]发现优化扒渣工艺能够减少扒渣铁损ꎬ降低转炉石灰粉及镁粉消耗ꎮ㊀㊀为了探索铁水扒渣工艺的发展趋势ꎬ优化转炉冶炼环境ꎬ提高钢水质量ꎬ特针对马钢一钢轧炼钢分厂铁水扒渣工艺进行理论分析与实践研究ꎮ2㊀铁水扒渣对转炉冶炼的影响分析㊀㊀马钢一钢轧的的铁水主要是由二铁厂提供ꎬ通过收集CSP类钢种2019年一季度铁水渣及转炉终点渣样数据ꎬ经过统计整理ꎬ其成分分别如表1ꎬ表2所示ꎮ铁水渣为低碱度ꎬ高硫渣ꎬ一般R=1.1-1.4ꎬ而转炉渣碱度R=3.5-4.0ꎬ铁水渣中大量的SiO2使转炉渣碱度降低ꎬ去除S㊁P的能力减弱ꎮ因此转炉兑铁水过程中ꎬ铁水渣的存在降低了转炉冶炼能力ꎮ表1㊀铁水渣成分(ω%)铁水渣成分CaOMgOSiO2FeOMnOSAl2O3其他实测值30~49.55.0~1420~45.80.1~0.220.09~0.20.9~1.39.5~23.8平均值39.947.9233.260.190.191.02215.61.88表2㊀转炉终点渣样成分(ω%)转炉渣成分CaOMgOSiO2TFeP2O5S其他实测值28.0~50.35.5~15.86.1~16.310~29.41.8~12.00.03~0.1平均值39.128.3311.5920.713.030.1017.22收稿日期:2019-09-20作者简介:宋㊀健(1990-)ꎬ男ꎬ马钢股份有限公司第一钢轧总厂ꎬ主要从事转炉炼钢工艺的研究ꎬ工程技术人员ꎮ㊀㊀该厂所用转炉造渣料石灰及镁球成分如表3所示ꎮ为了使转炉渣具有较好的冶金反应能力ꎬ必须保证转炉渣具有适合的碱度和较高的脱硫能力ꎬ因此当铁水渣进入转炉后ꎬ必须向转炉中加入大量的石灰ꎬ中和㊁稀释铁水渣带入的SiO2ꎮ表3㊀石灰及镁球成分(ω%)名称CaOMgOSiO2S烧碱石灰94.11/0.40.055.44镁球2.2704.5/23.32.1㊀铁水渣量对转炉原辅料消耗的影响㊀㊀根据三元碱度公式有:㊀㊀R=ω(CaO)+ω(MgO)ω(SiO2)(1)㊀㊀其中对于转炉冶炼过程有:㊀㊀ω(CaO)=ω(CaO)铁水渣+ω(CaO)石灰+ω(CaO)镁球(2)㊀㊀ω(MgO)=ω(MgO)铁水渣+ω(MgO)镁球(3)㊀㊀ω(SiO2)=ω(SiO2)铁水查+ω(SiO2)石灰+ω(SiO2)镁球(4)㊀㊀ω(CaO)转炉终渣ω(MgO)转炉终渣=ω(CaO)铁水渣+ω(CaO)石灰+ω(CaO)镁球ω(MgO)铁水渣+ω(MgO)镁球=39.128.33=4.70(5)㊀㊀由表2及公式(1)可知转炉渣碱度R=4.09ꎬ联立公式(1)-(5)ꎬ代入表1-表3数据可得ꎬ1kg/t的铁水渣可增加转炉消耗的石灰及镁球分别为0.81kg/tꎬ0.24kg/tꎮ㊀㊀引起转炉渣量为㊀㊀w=7.92%+0.24ˑ70%8.33%=2.97kg/t㊀㊀钢渣中含铁量约为20%ꎬ则铁水渣可增加0.594kg/t钢铁料消耗ꎮ2.2㊀不同因素对转炉冶炼造渣料影响的结果分析㊀㊀根据上述公式可知ꎬ影响转炉冶炼造渣料消耗的因素主要有铁水渣量ꎬ转炉渣CaO/MgO以及转炉渣碱度ꎮ㊀㊀当转炉渣碱度一定(R=4)ꎬ转炉终渣一定(CaO/MgO=4.5)时ꎬ探究铁水渣量对转炉冶炼造渣料消耗的影响ꎬ此时ꎬ由公式(1)-(5)计算结果如图1所示ꎮ由图可知ꎬ转炉冶炼造渣料(石灰㊁镁球)消耗随着铁水带渣量的增大逐渐增大ꎬ其中石灰消耗量增加的速率更快ꎬ这是因为铁水渣中含有大量的SiO2ꎬ需要加入过量的石灰来中和ꎮ图1㊀铁水渣量对转炉冶炼造渣料消耗的影响㊀㊀当转炉渣碱度一定为(R=4)ꎬ铁水渣量一定(W=1kg/t)时ꎬ探究转炉渣CaO/MgO对转炉冶炼造渣料消耗的影响ꎬ此时ꎬ由公式(1)-(5)计算结果如图2所示ꎮ由图可知ꎬ石灰消耗随着CaO/MgO的增大而缓慢增加ꎬ镁球消耗则随着CaO/MgO的增大而快速减小ꎬ因为CaO/MgO的增大是由于CaO增加的速率大于MgO增加的速率ꎬ当CaO增加的速度很慢甚至基本不变时ꎬMgO的值将会减小ꎮ图2㊀转炉渣CaO/MgO对转炉冶炼造渣料消耗的影响㊀㊀当铁水渣量一定(W=1kg/t)ꎬ转炉终渣一定(CaO/MgO=4.5)时ꎬ探究转炉渣碱度对转炉冶炼造渣料消耗的影响ꎬ此时ꎬ由公式(1)-(5)计算结果如图3所示ꎮ由图可知ꎬ转炉冶炼造渣料(石灰㊁镁球)消耗随着转炉渣碱度的增大而逐渐增大ꎬ其中石灰消耗量增加的速率更大ꎬ因为根据公式(1)可知ꎬ转炉渣碱度增加ꎬ说明CaO和MgO增加的速率要大于SiO2增加的速率ꎬ而SiO2需要大量的CaO来中和ꎮ图3㊀转炉渣碱度对转炉冶炼造渣料消耗的影响92 总第86期㊀㊀㊀㊀㊀㊀㊀㊀㊀宋㊀健ꎬ朱李艳ꎬ何宏涛ꎬ等:铁水扒渣工艺对转炉冶炼的影响研究2.3㊀铁水扒渣对转炉冶炼经济效益的影响㊀㊀由以上数据可知ꎬ每扒去1kg/t铁水渣可以降低石灰和镁球消耗分别为0.81kg/tꎬ0.24kg/tꎬ马钢一钢轧总厂CSP类钢种2018年产量为175万tꎬ冶金石灰价格为428元/tꎬ镁球价格700元/tꎬ铁水价格2320元/tꎬ扒渣铁损平均为0.22kg/tꎮ㊀㊀因此节约的石灰价格为㊀㊀428x0.81/1000x175万=60.7万元㊀㊀镁球价格为㊀㊀700x0.24/1000x175万=29.4万元㊀㊀降低钢铁料消耗成本为㊀㊀(0.594-0.22)/1000x2320x175万=151.8万元㊀㊀总共可以节约冶炼成本共241.9万元ꎮ3㊀工业试验㊀㊀为了验证理论计算过程铁水带渣量对转炉冶炼的影响ꎬ针对一钢轧3#转炉进行了铁水扒渣共6组现场工业试验ꎬ转炉渣平均碱度R=4ꎬ转炉渣CaO/MgO平均为4.7ꎬ每炉铁水扒渣量㊁石灰和镁球消耗量结果如表4所示ꎮ表4㊀工业试验数据结果炉次扒渣量/kg石灰/kg镁球/kg1043761216210003576976312003417934414003258889516003092838618002933791㊀㊀由表4可知ꎬ当转炉渣平均碱度为4ꎬ转炉渣CaO/Mg平均为4.7时ꎬ随着扒渣量的增加ꎬ转炉造渣料石灰和镁球消耗量逐渐减小ꎬ且平均单位减少量为0.80ꎬ0.235ꎬ这与前面理论分析计算相比ꎬ石灰和镁球消耗误差分别为1%ꎬ2%ꎮ4㊀结论㊀㊀本文根据马钢一钢轧总厂生产现状ꎬ铁水入转炉之前需经过扒渣处理ꎬ并通过理论分析结合工业试验验证ꎬ得出如下结论:㊀㊀通过理论计算可知ꎬ铁水扒渣工艺可以减少转炉原辅料消耗及渣量ꎬ其中1kg/t的铁水扒渣量可减少转炉消耗的石灰及镁球分别为0.81kg/tꎬ0.24kg/tꎬ增加转炉终点渣量为2.97kg/tꎬ增加0.594kg/t钢铁料消耗ꎮ㊀㊀影响转炉冶炼造渣料(石灰㊁镁球)消耗的因素主要有铁水渣量ꎬ转炉渣CaO/MgO以及转炉渣碱度ꎮ在一定条件下ꎮ石灰㊁镁球消耗随着铁水带渣量和转炉渣碱度的增大而逐渐增大ꎻ石灰消耗随着CaO/MgO的增大而缓慢增加ꎬ镁球消耗则随着CaO/MgO的增大而快速减小ꎮ㊀㊀铁水扒渣工业试验结果显示ꎬ随着扒渣量的增加ꎬ转炉造渣料石灰和镁球消耗量逐渐减小ꎬ且平均单位减少量为0.8kg/t0ꎬ0.235kg/tꎬ与理论计算相比ꎬ石灰和镁球消耗误差分别为1%ꎬ2%ꎮ参考文献[1]㊀于宏武.铁水扒渣工艺提高转炉冶炼质量[J].河北冶金ꎬ2007(04):36-37ꎻ72[2]㊀张定基.铁水扒渣的意义与方法[J].钢铁研究情报ꎬ1983(03):25-32[3]㊀李伟东ꎬ何海龙ꎬ舒耀.降低铁水预处理扒渣铁损的生产实践[J].鞍钢技术ꎬ2013(01):47-49[4]㊀李彦萍.本钢新建铁水脱硫扒渣站技术研究及应用[J].本钢技术ꎬ2011(03):16-20[5]㊀方敏ꎬ徐福泉ꎬ王文涛ꎬ刘鹏飞ꎬ魏元ꎬ曹祥.铁水预处理过程稳定控制实践[J].鞍钢技术ꎬ2016(01):47-50StudyontheInfluenceofHotMetalScrapingSlagofConverterSmeltingSONGJianꎬZHULi-yanꎬHEHang-taoꎬWUFa-da㊀㊀Abstract:Thispaperanalysesthecompositionofhotmetalslagandconverterendslagꎬandtheeffectsofslagscrapingamountontheconsumptionofslag-makingmaterials(limeandmagnesiumspheres)andthefinalslagofconverterwerestudiedrespectively.CombiningthedataofindustrialtestdataꎬThefollowingconclusionsaredraw:Hotmetalslaggingprocesscanreducetheconsumptionofconverterslagꎬironandsteelmaterialsꎬandtheamountofconverterslagꎬthusimprovingtheconvertersmeltingenvironmentꎬthequalityofmoltensteelꎬandthesmeltingdifficultiesandcosts.㊀㊀Keywords:HotmetalscrapingslagꎻConverterꎻSlagmaterialconsumption03 安徽冶金科技职业学院学报㊀㊀㊀㊀㊀㊀㊀㊀㊀㊀㊀㊀2019年第4期。
炼钢全流程降低钢铁料消耗的实践攻关
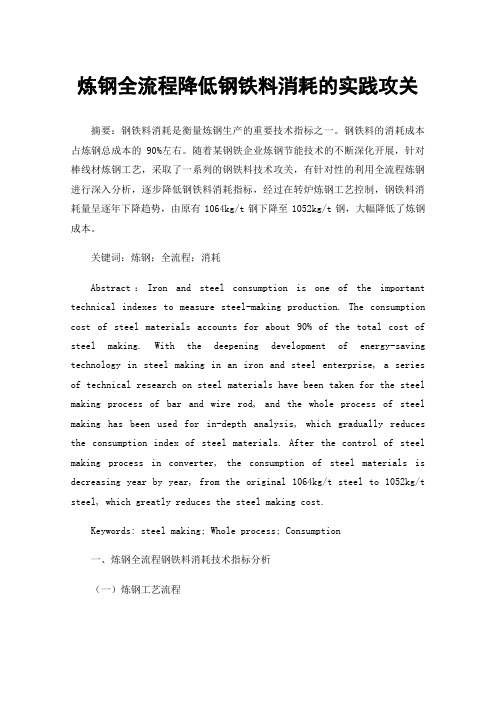
炼钢全流程降低钢铁料消耗的实践攻关摘要:钢铁料消耗是衡量炼钢生产的重要技术指标之一。
钢铁料的消耗成本占炼钢总成本的90%左右。
随着某钢铁企业炼钢节能技术的不断深化开展,针对棒线材炼钢工艺,采取了一系列的钢铁料技术攻关,有针对性的利用全流程炼钢进行深入分析,逐步降低钢铁料消耗指标,经过在转炉炼钢工艺控制,钢铁料消耗量呈逐年下降趋势,由原有1064kg/t钢下降至1052kg/t钢,大幅降低了炼钢成本。
关键词:炼钢;全流程;消耗Abstract:Iron and steel consumption is one of the important technical indexes to measure steel-making production. The consumption cost of steel materials accounts for about 90% of the total cost of steel making. With the deepening development of energy-saving technology in steel making in an iron and steel enterprise, a series of technical research on steel materials have been taken for the steel making process of bar and wire rod, and the whole process of steel making has been used for in-depth analysis, which gradually reduces the consumption index of steel materials. After the control of steel making process in converter, the consumption of steel materials is decreasing year by year, from the original 1064kg/t steel to 1052kg/t steel, which greatly reduces the steel making cost.Keywords: steel making; Whole process; Consumption一、炼钢全流程钢铁料消耗技术指标分析(一)炼钢工艺流程图1 某钢铁企业炼钢工艺流程简图(二)钢铁料消耗统计分析某钢铁企业第二钢扎厂钢铁料消耗统计口径如下:钢铁料消耗(kg/t)=(铁水+废钢)(kg)/合格钢坯产量(t)。
- 1、下载文档前请自行甄别文档内容的完整性,平台不提供额外的编辑、内容补充、找答案等附加服务。
- 2、"仅部分预览"的文档,不可在线预览部分如存在完整性等问题,可反馈申请退款(可完整预览的文档不适用该条件!)。
- 3、如文档侵犯您的权益,请联系客服反馈,我们会尽快为您处理(人工客服工作时间:9:00-18:30)。
U 刚 舌
足要 求 , 将 使造 渣 料 、 氧 气 消耗 量 加 大 , 同 时 随炉 渣 带走 的铁 量增 加 , 从 而影 响钢 铁 料 的 消 耗 , 另外 , 对
标 .
1 高炉铁水 P等元素含量
韶钢 2 0 1 2年 3~5月供 大转 炉用 铁水 成 分见 表
1 、 表2 、 表3 .
如果 铁水 中 P含 量较 高 , 为 使钢 水 中 P含 量满
表1 2 0 1 2年 5月供大转炉用铁水成分
收 稿 日期 : 2 0 1 2— 0 6— 3 0
t h e c o s t o f ma t e r i l a s u s e d or f a d j u s t m e n t w i l l b e i n c r e a s e d ls a o .B a s e d o n a g u e s s a n d e s t i m a t e , t h e c o s t o f c o n v e  ̄ e r s t e e l —
炉衬 的冲刷蚀 损 也有所 加 重 , 对 炉龄 有一 定影 响.
2 0 1 2年 5月 , 宝 钢集 团广 东 韶 关钢 铁 有 限公 司
( 以下 简称 “ 韶钢” ) 大 高 炉 系统 因配 用 高磷 瑞 典 粉
矿, 铁水 中 P含 量显 著升 高.
本文就 铁 水 P含 量 对 炼 钢 成 本 的 影 响 进 行 分
Ab s t r a c t :R e g a r d l e s s o f t h e c o s t o f ma t e ia r l s u s e d t o f o r m s l a g,a n d o x y g e n c o n s u mp t i o n o r i r o n nd a s t e e l c o n s u mp t i o n, t h e i mp a c t o f t h e c o n t e n t o f P i s r e l a t i v e l y s ma ll e r t h a n t h e c o n t e n t o f S i i n h o t me t 1 .I a f t h e c o n t e n t o f P i n h o t me t l a i n c r e a s e s ,
ma k i n g w i l l i n c r e a s e 0 . 7 Y u a n or f e a c h t o n w h e n t h e c o n t e n t o f P i n h o t me t a l i n c r e a s e s 0 . 0 1 p e r c e n t .
总第 1 9 2期 2 0 1 3年 6月
南
方
金
属
S u m. 1 92
S OUTHERN M ETALS
J u n e 2 0 1 3
文章编号 : 1 0 0 9— 9 7 0 0 ( 2 0 1 3 ) 0 3— 0 0 1 6— 0 5
铁 水 P含 量 对 转 炉 炼 钢 成 本 的影 响
ZENG Za n- x i ,W EN Hui ,L I N Sh a o — y un
( B a o s t e e l G r o u p G u a n g d o n g S h a o g u a n I r o n& S t e e l C o . , L t d . , Q u j i a n g , G u a n g d o n g , 5 1 2 1 2 3 , P . R.C h i n a )
作者简介 : 曾赞喜( 1 9 6 7一) , 男 ,1 9 8 9年 毕 业 于 武汉 大 学 物理 系金 属 物 理 专 业 , 高 级 工 程 师
总第 1 9 2期
曾赞喜 , 等: 铁水 P含量 对转 炉炼钢成本的影响
1 7
曾赞喜 , 文 晖, 林少云
( 宝钢集 团广东韶关钢铁有 限公 司, 广东 韶关 5 1 2 1 2 3) 摘 要: 无论是对造渣料消耗 , 还 是对 氧气 消耗 , 以至钢铁料消耗 , 铁 水 P含量 的影 响都较小 , 相反 , 铁水 s i 含量 的
影响大得多. 铁水 P含量升高 , 导致造渣料 、 氧气消耗增加 , 因渣 量增加 还导致钢铁 料消 耗增加. 据测算 , 铁水 P含 量每升高 0 . 0 1 %, 约增加炼钢成本 0 . 7元/ t . 关键词 : 铁水 ; P含量 ;炼钢 ; 成本
析, 为铁矿 采购 、 配用 , 以及炼钢 生 产提供 参考 依据 .
磷 是炼钢 过程 要 去 除 的 有 害Байду номын сангаас 素 . 氧 气 顶 吹转
炉 的脱 磷效率 在 8 5 %~ 9 5 %, 铁水 中磷 含量 越 低 , 转 炉 工艺 操作 越简 化 , 并 有利 于 提 高 各项 技 术 经 济 指
中 图分 类 号 : T F 5 3 文献标识码 : B
I mp a c t s o f t h e Co n t e nt o f P i n Ho t Me t a l o n t he Co s t o f Co n v e r t e r St e e l ma k i ng