纵轴式掘进机截割方法、路线与受力分析
掘进机截割头受力分析与掘进实例分析
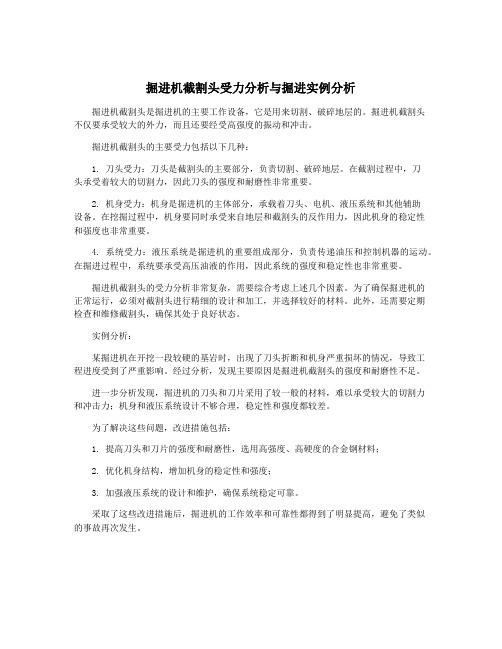
掘进机截割头受力分析与掘进实例分析掘进机截割头是掘进机的主要工作设备,它是用来切割、破碎地层的。
掘进机截割头不仅要承受较大的外力,而且还要经受高强度的振动和冲击。
掘进机截割头的主要受力包括以下几种:1. 刀头受力:刀头是截割头的主要部分,负责切割、破碎地层。
在截割过程中,刀头承受着较大的切割力,因此刀头的强度和耐磨性非常重要。
2. 机身受力:机身是掘进机的主体部分,承载着刀头、电机、液压系统和其他辅助设备。
在挖掘过程中,机身要同时承受来自地层和截割头的反作用力,因此机身的稳定性和强度也非常重要。
4. 系统受力:液压系统是掘进机的重要组成部分,负责传递油压和控制机器的运动。
在掘进过程中,系统要承受高压油液的作用,因此系统的强度和稳定性也非常重要。
掘进机截割头的受力分析非常复杂,需要综合考虑上述几个因素。
为了确保掘进机的正常运行,必须对截割头进行精细的设计和加工,并选择较好的材料。
此外,还需要定期检查和维修截割头,确保其处于良好状态。
实例分析:某掘进机在开挖一段较硬的基岩时,出现了刀头折断和机身严重损坏的情况,导致工程进度受到了严重影响。
经过分析,发现主要原因是掘进机截割头的强度和耐磨性不足。
进一步分析发现,掘进机的刀头和刀片采用了较一般的材料,难以承受较大的切割力和冲击力;机身和液压系统设计不够合理,稳定性和强度都较差。
为了解决这些问题,改进措施包括:1. 提高刀头和刀片的强度和耐磨性,选用高强度、高硬度的合金钢材料;2. 优化机身结构,增加机身的稳定性和强度;3. 加强液压系统的设计和维护,确保系统稳定可靠。
采取了这些改进措施后,掘进机的工作效率和可靠性都得到了明显提高,避免了类似的事故再次发生。
矿用纵轴式掘进机截割头结构力学分析
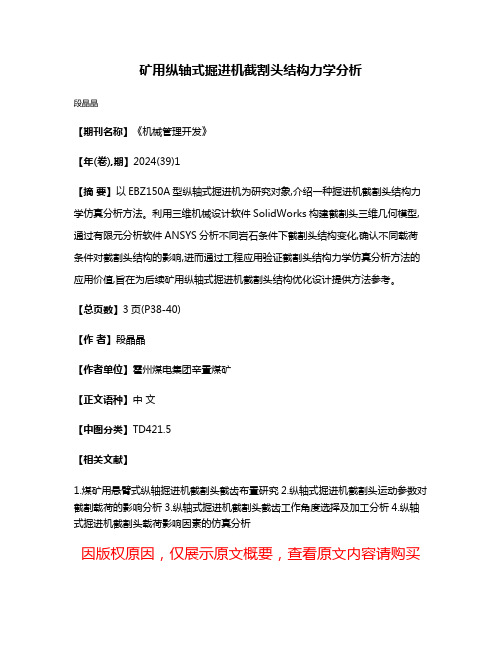
矿用纵轴式掘进机截割头结构力学分析
段晶晶
【期刊名称】《机械管理开发》
【年(卷),期】2024(39)1
【摘要】以EBZ150A型纵轴式掘进机为研究对象,介绍一种掘进机截割头结构力学仿真分析方法。
利用三维机械设计软件SolidWorks构建截割头三维几何模型,通过有限元分析软件ANSYS分析不同岩石条件下截割头结构变化,确认不同载荷条件对截割头结构的影响,进而通过工程应用验证截割头结构力学仿真分析方法的应用价值,旨在为后续矿用纵轴式掘进机截割头结构优化设计提供方法参考。
【总页数】3页(P38-40)
【作者】段晶晶
【作者单位】霍州煤电集团辛置煤矿
【正文语种】中文
【中图分类】TD421.5
【相关文献】
1.煤矿用悬臂式纵轴掘进机截割头截齿布置研究
2.纵轴式掘进机截割头运动参数对截割载荷的影响分析
3.纵轴式掘进机截割头截齿工作角度选择及加工分析
4.纵轴式掘进机截割头载荷影响因素的仿真分析
因版权原因,仅展示原文概要,查看原文内容请购买。
掘进机截割头受力分析与掘进实例分析

掘进机截割头受力分析与掘进实例分析【摘要】本文主要围绕掘进机截割头受力分析与掘进实例分析展开讨论。
首先介绍了掘进机截割头受力分析的基本原理和方法,包括受力分析模型的建立和计算过程。
随后通过掘进实例分析,具体探讨了掘进机在实际工作中的受力情况和影响因素。
实例分析结果指出了掘进机截割头设计存在的不足之处,为接下来的优化设计提供了参考依据。
最后对掘进机截割头受力分析与掘进实例分析进行了总结,同时对未来研究方向提出了展望。
通过本文的研究,有助于提高掘进机的工作效率和安全性,推动掘进技术的进步和应用。
【关键词】掘进机,截割头,受力分析,模型,实例分析,设计优化,总结,研究展望1. 引言1.1 掘进机截割头受力分析与掘进实例分析...在煤炭、矿石等矿山开采过程中,掘进机截割头是重要的装备之一。
掘进机截割头在矿山的地下工作环境中承受着复杂多变的受力情况,受力分析和设计优化对于提高掘进效率和延长设备使用寿命具有重要意义。
本文旨在对掘进机截割头受力分析与掘进实例分析进行深入探讨,为研究人员和工程师提供参考与借鉴。
首先将对掘进机截割头的受力特点进行分析,包括受力来源、受力方向和受力大小等方面,建立受力分析模型。
随后,将通过实例分析的方式,结合实际掘进情况,对不同受力情况下的掘进机截割头进行分析,并得出相应的实例分析结果。
对掘进机截割头的设计优化进行探讨,提出改进措施和建议。
通过本文的研究,可以更深入地了解掘进机截割头的受力特点和掘进实例分析,为相关岩石开采领域的研究和应用提供有益的参考。
2. 正文2.1 掘进机截割头受力分析掘进机截割头受力分析是对掘进机在进行截割作业时受到的各种力的分析和计算。
在进行截割作业时,掘进机需要面对来自岩石和煤层的不同受力情况,因此掘进机截割头的设计和性能至关重要。
掘进机截割头受力分析主要包括对截割头的受力情况、受力分布和受力大小的研究,以及如何合理设计和优化截割头的结构和材料。
在进行掘进机截割头受力分析时,需要考虑多种因素,包括岩石或煤层的物理性质、截割头的旋转速度、截割头的刀具形状和数量、截割头的工作角度等。
掘进机截割时受力分析
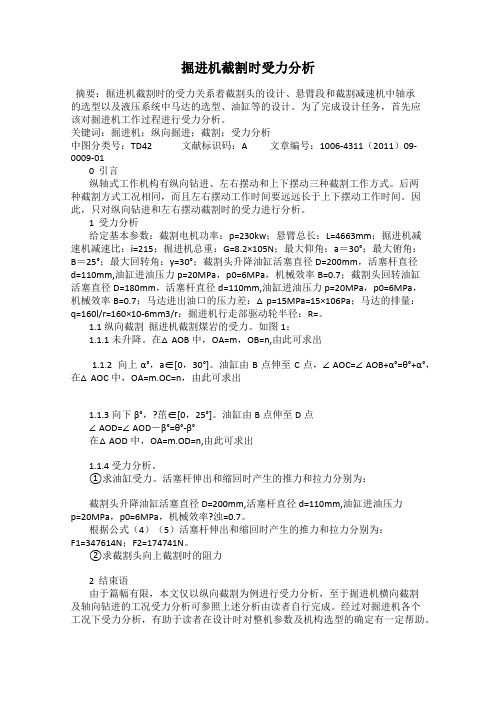
掘进机截割时受力分析摘要:掘进机截割时的受力关系着截割头的设计、悬臂段和截割减速机中轴承的选型以及液压系统中马达的选型、油缸等的设计。
为了完成设计任务,首先应该对掘进机工作过程进行受力分析。
关键词:掘进机;纵向掘进;截割;受力分析中图分类号:TD42 文献标识码:A 文章编号:1006-4311(2011)09-0009-010 引言纵轴式工作机构有纵向钻进、左右摆动和上下摆动三种截割工作方式。
后两种截割方式工况相同,而且左右摆动工作时间要远远长于上下摆动工作时间。
因此,只对纵向钻进和左右摆动截割时的受力进行分析。
1 受力分析给定基本参数:截割电机功率:p=230kw;悬臂总长:L=4663mm;掘进机减速机减速比:i=215;掘进机总重:G=8.2×105N;最大仰角:a=30°;最大俯角:B=25°;最大回转角:y=30°;截割头升降油缸活塞直径D=200mm,活塞杆直径d=110mm,油缸进油压力p=20MPa,p0=6MPa,机械效率B=0.7;截割头回转油缸活塞直径D=180mm,活塞杆直径d=110mm,油缸进油压力p=20MPa,p0=6MPa,机械效率B=0.7;马达进出油口的压力差:△p=15MPa=15×106Pa;马达的排量:q=160l/r=160×10-6mm3/r;掘进机行走部驱动轮半径:R=。
1.1 纵向截割掘进机截割煤岩的受力。
如图1:1.1.1 未升降。
在△AOB中,OA=m,OB=n,由此可求出1.1.2 向上α°,a∈[0,30°]。
油缸由B点伸至C点,∠AOC=∠AOB+α°=θ°+α°,在△AOC中,OA=m.OC=n,由此可求出1.1.3 向下β°,?茁∈[0,25°]。
油缸由B点伸至D点∠AOD=∠AOD-β°=θ°-β°在△AOD中,OA=m.OD=n,由此可求出1.1.4 受力分析。
纵、横轴式掘进机工作原理与结构特点
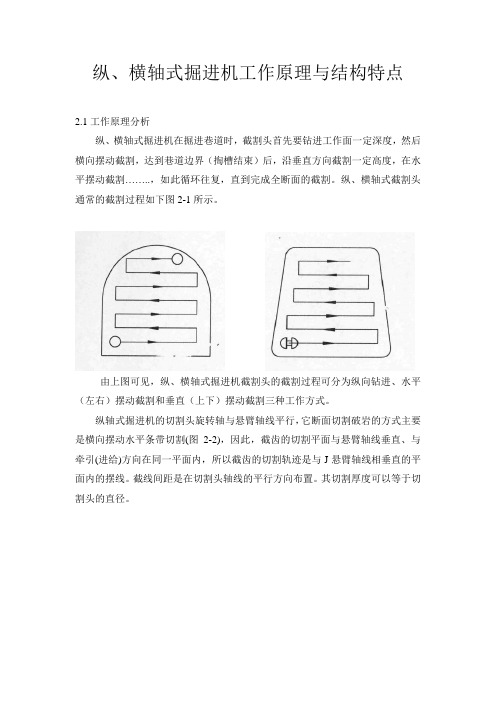
纵、横轴式掘进机工作原理与结构特点2.1工作原理分析纵、横轴式掘进机在掘进巷道时,截割头首先要钻进工作面一定深度,然后横向摆动截割,达到巷道边界(掏槽结束)后,沿垂直方向截割一定高度,在水平摆动截割……..,如此循环往复,直到完成全断面的截割。
纵、横轴式截割头通常的截割过程如下图2-1所示。
由上图可见,纵、横轴式掘进机截割头的截割过程可分为纵向钻进、水平(左右)摆动截割和垂直(上下)摆动截割三种工作方式。
纵轴式掘进机的切割头旋转轴与悬臂轴线平行,它断面切割破岩的方式主要是横向摆动水平条带切割(图2-2),因此,截齿的切割平面与悬臂轴线垂直、与牵引(进给)方向在同一平面内,所以截齿的切割轨迹是与J悬臂轴线相垂直的平面内的摆线。
截线间距是在切割头轴线的平行方向布置。
其切割厚度可以等于切割头的直径。
横轴式掘进机的切割头旋转轴与悬臂轴线相垂直,有两个切割头在输出轴的两端、相对于悬臂中心面对称布置(图2-3)。
它断面切割破岩的主要方式也是横向摆动水平条带切割。
截齿的切割平面与悬臂轴线相平行、与牵引方向相垂直,所以截齿的切割轨迹是一条中心线与悬臂轴线相垂直的螺旋线。
截线间距是在切割头的径向布置。
其切割头直径方向的切厚只能达到其直径的1/ 3左右。
4.2 纵、横轴式掘进机切割煤岩的方式分析图2表示纵轴式和横轴式工作过程不同,两类截割头的切削力FS、进给力Fp和摆动力F}的方向各异。
切削煤岩的阻力引起截割头的切削力,受切割机构功率限制,切入煤岩的阻力和保持截齿切削状态所需的力产生推进力Fe,其大小与切削力相关。
推进力Fe的方向并不都与摆动方向一致,在水平摆动过程中,纵轴式截割头的摆动力F,,的方向与截齿切削力FS和进给力Fa构成的切割平面相平行,类似横轴式切割头掏槽工况。
同样横轴式截割头在摆动切割时,摆动力凡的方向与截割平面垂直,类似纵轴式截割头掏槽工况。
如果摆动力方向平行于截割平面,进给力与切割头的摆动力则呈线性关系,摆动力过大,截齿磨擦增大。
掘进机截割头受力分析与掘进实例分析
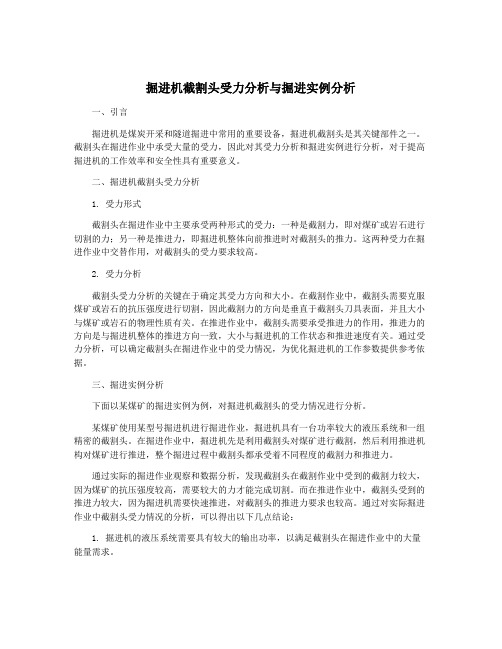
掘进机截割头受力分析与掘进实例分析一、引言掘进机是煤炭开采和隧道掘进中常用的重要设备,掘进机截割头是其关键部件之一。
截割头在掘进作业中承受大量的受力,因此对其受力分析和掘进实例进行分析,对于提高掘进机的工作效率和安全性具有重要意义。
二、掘进机截割头受力分析1. 受力形式截割头在掘进作业中主要承受两种形式的受力:一种是截割力,即对煤矿或岩石进行切割的力;另一种是推进力,即掘进机整体向前推进时对截割头的推力。
这两种受力在掘进作业中交替作用,对截割头的受力要求较高。
2. 受力分析截割头受力分析的关键在于确定其受力方向和大小。
在截割作业中,截割头需要克服煤矿或岩石的抗压强度进行切割,因此截割力的方向是垂直于截割头刀具表面,并且大小与煤矿或岩石的物理性质有关。
在推进作业中,截割头需要承受推进力的作用,推进力的方向是与掘进机整体的推进方向一致,大小与掘进机的工作状态和推进速度有关。
通过受力分析,可以确定截割头在掘进作业中的受力情况,为优化掘进机的工作参数提供参考依据。
三、掘进实例分析下面以某煤矿的掘进实例为例,对掘进机截割头的受力情况进行分析。
某煤矿使用某型号掘进机进行掘进作业,掘进机具有一台功率较大的液压系统和一组精密的截割头。
在掘进作业中,掘进机先是利用截割头对煤矿进行截割,然后利用推进机构对煤矿进行推进,整个掘进过程中截割头都承受着不同程度的截割力和推进力。
通过实际的掘进作业观察和数据分析,发现截割头在截割作业中受到的截割力较大,因为煤矿的抗压强度较高,需要较大的力才能完成切割。
而在推进作业中,截割头受到的推进力较大,因为掘进机需要快速推进,对截割头的推进力要求也较高。
通过对实际掘进作业中截割头受力情况的分析,可以得出以下几点结论:1. 掘进机的液压系统需要具有较大的输出功率,以满足截割头在掘进作业中的大量能量需求。
2. 截割头的材料和结构需要具有较高的强度和刚度,以承受截割力和推进力的作用。
3. 控制推进速度和截割参数,以保证截割头受力平衡和稳定,避免因受力过大造成截割头损坏或工作效率低下的问题。
掘进机截割头受力分析与掘进实例分析
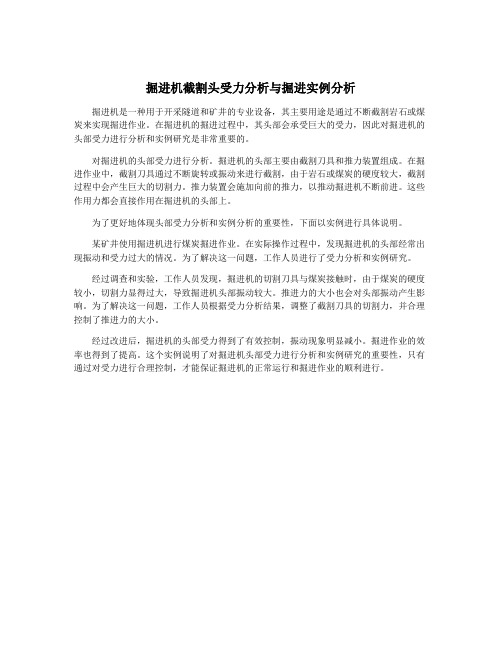
掘进机截割头受力分析与掘进实例分析
掘进机是一种用于开采隧道和矿井的专业设备,其主要用途是通过不断截割岩石或煤炭来实现掘进作业。
在掘进机的掘进过程中,其头部会承受巨大的受力,因此对掘进机的头部受力进行分析和实例研究是非常重要的。
对掘进机的头部受力进行分析。
掘进机的头部主要由截割刀具和推力装置组成。
在掘进作业中,截割刀具通过不断旋转或振动来进行截割,由于岩石或煤炭的硬度较大,截割过程中会产生巨大的切割力。
推力装置会施加向前的推力,以推动掘进机不断前进。
这些作用力都会直接作用在掘进机的头部上。
为了更好地体现头部受力分析和实例分析的重要性,下面以实例进行具体说明。
某矿井使用掘进机进行煤炭掘进作业。
在实际操作过程中,发现掘进机的头部经常出现振动和受力过大的情况。
为了解决这一问题,工作人员进行了受力分析和实例研究。
经过调查和实验,工作人员发现,掘进机的切割刀具与煤炭接触时,由于煤炭的硬度较小,切割力显得过大,导致掘进机头部振动较大。
推进力的大小也会对头部振动产生影响。
为了解决这一问题,工作人员根据受力分析结果,调整了截割刀具的切割力,并合理控制了推进力的大小。
经过改进后,掘进机的头部受力得到了有效控制,振动现象明显减小。
掘进作业的效率也得到了提高。
这个实例说明了对掘进机头部受力进行分析和实例研究的重要性,只有通过对受力进行合理控制,才能保证掘进机的正常运行和掘进作业的顺利进行。
纵轴式掘进机截割头的设计

纵轴式掘进机截割头的设计作者:廉浩冯健来源:《中国新技术新产品》2014年第03期摘要:本文介绍了纵轴式掘进机截割头的设计原则,讨论了提高截割头截割效率的合理方案,提供了设计用的主要数据。
关键词:截割头;设计原则;截割效率中图分类号:TD42 文献标识码:A1 概要本文以纵轴式掘进机的截割头为研究对象。
截割头是掘进机的关键部件,它直接参与对工作面的掘进工作。
其设计参数较多,这些参数之间互相影响和制约,同时截割头的设计质量的好坏决定了掘进机整机的截割性能,这对截割头的使用寿命,以及整机的稳定性和可靠性都有着直接的影响。
2 工作原理掘进机的工作过程是:操纵行走机构向工作面推进,使截割头在工作面的左下角钻入,水平摆动油缸使截割头横向截割到巷道的右侧。
然后利用升降油缸把截割头上升接近等于截割头直径的距离,并使截割头向巷道左侧截割。
如此往复截割运动,截割头就可以完成整个工作面的截割。
当然掘进机的截割方式与掘进巷道断面的大小,形状,煤岩的分布情况有关。
在截割头截落煤岩后,由装运机构将其装进掘进机中间的输送机构,再最终装进矿车或巷道输送机。
因此,纵向截割头通常的截割过程可以总结为纵向钻进、水平摆动截割和垂直摆动截割三种工作方式。
3 结构研究3.1 影响设计的因素如果能保证在旋转截割的过程中,使参加截割的每个截齿都截割相同大小的煤岩,让各截齿的受力相等、运行平稳,并且产生的磨损也基本相同,这样的截割头设计是最理想的。
但是有很多因素影响截割头的设计,主要有以下几个方面:(1)煤岩自身的性质,主要有抗截强度、硬度、磨蚀性、坚固性系数等;(2)截割头的结构参数,主要有截割头的几何形状、外形尺寸、截齿排列、截齿数量以及截线间距等;(3)截割头的工艺性参数,主要有摆动速度、截割头转速、切削厚度、切削深度等。
在截割头的设计上,这些因素的影响并不是孤立的,它们之间相互关联和制约。
3.2 结构形式3.2.1 外形截割头的外形是指截割头的几何形状,它是由截齿的齿尖所形成的外部轮廓,通常称为截割头包络面。
掘进机截割头受力分析与掘进实例分析
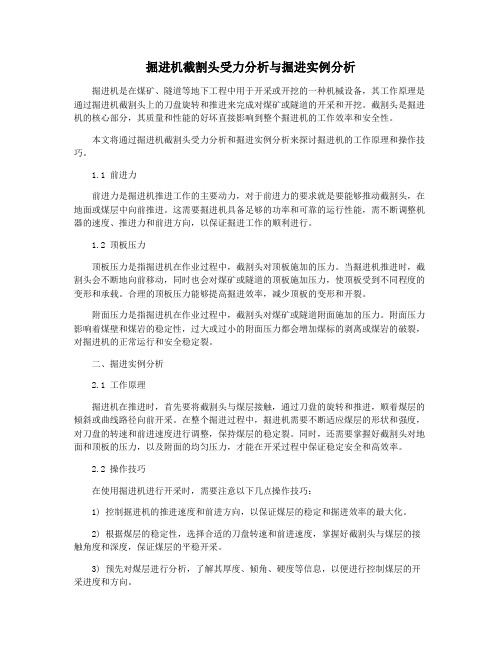
掘进机截割头受力分析与掘进实例分析掘进机是在煤矿、隧道等地下工程中用于开采或开挖的一种机械设备,其工作原理是通过掘进机截割头上的刀盘旋转和推进来完成对煤矿或隧道的开采和开挖。
截割头是掘进机的核心部分,其质量和性能的好坏直接影响到整个掘进机的工作效率和安全性。
本文将通过掘进机截割头受力分析和掘进实例分析来探讨掘进机的工作原理和操作技巧。
1.1 前进力前进力是掘进机推进工作的主要动力,对于前进力的要求就是要能够推动截割头,在地面或煤层中向前推进。
这需要掘进机具备足够的功率和可靠的运行性能,需不断调整机器的速度、推进力和前进方向,以保证掘进工作的顺利进行。
1.2 顶板压力顶板压力是指掘进机在作业过程中,截割头对顶板施加的压力。
当掘进机推进时,截割头会不断地向前移动,同时也会对煤矿或隧道的顶板施加压力,使顶板受到不同程度的变形和承载。
合理的顶板压力能够提高掘进效率,减少顶板的变形和开裂。
附面压力是指掘进机在作业过程中,截割头对煤矿或隧道附面施加的压力。
附面压力影响着煤壁和煤岩的稳定性,过大或过小的附面压力都会增加煤标的剥离或煤岩的破裂,对掘进机的正常运行和安全稳定裂。
二、掘进实例分析2.1 工作原理掘进机在推进时,首先要将截割头与煤层接触,通过刀盘的旋转和推进,顺着煤层的倾斜或曲线路径向前开采。
在整个掘进过程中,掘进机需要不断适应煤层的形状和强度,对刀盘的转速和前进速度进行调整,保持煤层的稳定裂。
同时,还需要掌握好截割头对地面和顶板的压力,以及附面的均匀压力,才能在开采过程中保证稳定安全和高效率。
2.2 操作技巧在使用掘进机进行开采时,需要注意以下几点操作技巧:1) 控制掘进机的推进速度和前进方向,以保证煤层的稳定和掘进效率的最大化。
2) 根据煤层的稳定性,选择合适的刀盘转速和前进速度,掌握好截割头与煤层的接触角度和深度,保证煤层的平稳开采。
3) 预先对煤层进行分析,了解其厚度、倾角、硬度等信息,以便进行控制煤层的开采进度和方向。
纵轴式掘进机截割头截齿工作角度的确定及工艺实现

越 利于纵向钻进 ,当 s= 9 0 。 时 ,其最利 于纵 向钻进 。但 是 , 在截 割头摆 动截 割 时则使 截 齿无 法楔 人 岩体 ,导致 齿 身、 齿座 等与岩体严 重摩 擦 ,以至 于无法 正常 截割 。因此 ,截 齿 的倾 斜角应考虑截齿的相对截割头的位置进行 确定。 由倾斜角的定义可知 ,倾斜角 为两个面之 间的夹角 ,随
/ _ 0 B C… c l a n ( 7 )
当截割 角很小 或 为 0 。 时( 图3 a ) ,齿尖 较易 楔人 岩体 ,
岩体受到较大的拉伸和剪切应力 ,但压应力很 小 ,很难 形成 密实核。从理论上分析 ,此时截割阻力、截割 比能耗 和产尘 量均较小 ,破岩效果较好 ,但 由于实际工况 的限制 ,这 时齿 体与岩体 之间产生严重 的摩擦 ,反而使截割力 、截割 比能耗 和产尘量很大 ,截齿寿命大大降低 。因而 ,为了使得截齿 具
f
有较好 的截割性 能 ,常使截 割角 6> ( 为截齿合 金头半锥
角) 。此 时( 图3 b ) 截齿切削刃对 岩体的力指 向 自由面 ,岩 体 受压形成发育不充分的密实核 ,且岩石的破碎是 由挤 压、剪 切和拉伸联合作用完成的 ,如果角度设计合理 ,避免齿体 与 图 4 静态截齿工作角度示意 图 根据 图 4 ,由几何关 系可得 :
截 割角 :
一 …
角, 聊 为倾 斜角 。
2 工 作 角度 的确 定方 法
2 . 1 截割 角的确 定 方法
截割角 6 是一 个重 要 的工作 角 度 ,为使 截 齿具 有较 好 的截 割效 果 ,应从 截割 阻力 、截割 比能耗 以及 产尘 量 和避 免齿体 与岩体产 生摩擦 等 方面 对截 割角 占进 行 分析 。截 割 角对截 割效果 的影 响如 图 3所示 。
纵轴式掘进机截割头的设计

工 业 技 术
Ne W T e e h n o l o  ̄ i e s a n d P r o掘进 机截割头 的设 计
廉 浩 冯 健
( 北 方重 工集 团有 限公 司。辽 宁 沈阳 1 1 0 1 4 1 )
摘 要: 本 文介 绍 了纵轴 式掘 进机 截割 头 的设计 原 则 , 讨论 了提 高截 割 头截割 效 率的合 理 方案 , 提 供 了设 计 用的主要 数据 。 关键 词 :截割 头 ;设 计原 则 ;截割 效率 中 图分 类号 : T D 4 2 文 献标 识码 :A
1概 要
3 . 2 . 1 外 形
截割力 矩 为 :
M C =95 5 0×N
本 文 以纵 轴 式 掘 进 机 的 截 割 头 为研
究对 象。截割头是掘进机 的关键部件 , 它 直 接参 与对 工 作 面 的掘 进 工 作 。 其设
计 参 数较 多 ,这 些 参 数 之 间 互 相影 响 和 制 约 , 同时 截 割 头 的 设 计 质 量 的好 坏决 定 了 掘进 机 整 机 的截 割 性 能 ,这对 截割 头 的使 用 寿命 ,以 及 整 机 的 稳 定性 和 可 割头 自身主轴转动就形成 了截割头的空 靠 性都 有 着直 接 的影响 。 问曲面轮廓。 2工作 原理 3 . 2 . 2 组 成 纵 轴 式 掘 进 机截 割 头 主 要 由截 割 头 掘 进 机 的工 作 过 程 是 :操 纵 行 走机 构 向工 作 面推 进 ,使 截 割 头 在 l T作 面 的 体 、截 齿 、截 齿 座 、螺 旋 叶 片 、喷 嘴 、 左 下 角钻 入 ,水 平 摆 动 油 缸使 截 割 头横 耐 磨 块 等 组 成 。在 截 割 头 体 上 焊 接 螺 旋 向截 割 到 巷 道 的右 侧 。 然 后 利 用 升 降油 叶 片 ,将 截 齿 座 按 照 设 计 要 求 焊 接 在 螺 缸 把 截 割 头 上 升 接 近 等 于 截 割 头 直 径 的 旋 叶 片 上 ,截齿 安 装 在 齿 座 里。 喷 嘴 的 距离 ,并使截割头 向巷道左侧截割。如 位 置 指 向截 齿 齿 尖方 向 ,这 有 利 于 在 截 此 往 复 截 割 运 动 ,截 割 头 就 可 以完 成 整 割 时 对 工 作 面 的 灭尘 。因 为 煤 岩 体具 有 个 工 作 面 的截 割 。 当 然 掘 进机 的截 割方 磨蚀性 ,所 以在截割头体上焊接耐磨块 式 与掘 进 巷 道 断面 的大 小 ,形 状 ,煤 岩 的分 布情况 有关 。 在截 割头 截落 煤岩 后 , 由装 运 机 构 将 其 装 进 掘 进 机 中 间 的输 送 机 构 ,再最 终 装进 矿 车 或 巷道 输 送 机 。 因此 ,纵 向 截 割 头 通 常 的 截割 过程 可 以 总 结 为 纵 向钻 进 、水 平摆 动截 割 和垂 直 摆 动截 割三 种工 作方 式 。 3 结 构研 究 3 . 1 影 响设计 的 因素 如果能保证在旋转截割的过程中, 使 参 加 截 割 的 每 个 截 齿都 截割 相 同大 小 的煤岩 , 让 各截 齿 的受力 相等 、 运 行平 稳 , 来进 行保 护 。 3 . 2 . 3尺寸 参数 掘进 机截 割头 的尺 寸参 数 主要 包 括 : 截 割 头 长 度 、截 割 头 直 径 、螺旋 头数 和 升 角等 。 ( 1 ) 截 割头 长度 纵 轴式 掘进 机 截 割 头 的 长 度 是 指从 截 割头 顶 端到 底端 在 轴线 方 向上 的距 离 。 截 割 头设 计 的过 长 ,截 齿 的 截 割 阻力 增 大, 导致 截 割机 构的摆 动速 度受 到影 响 , 截 割 能 耗 也会 增 加 ,如 果 截 割 功率 不 相 适 应 会 影 响 掘 进 速度 。反 之 ,截 割头 长 并 且 产 生 的磨 损 也 基 本 相 同 ,这 样 的截 度 过 短 时 ,虽 然 可 以 充 分 利 用 自由 面 和 割 头 设 计 是 最 理 想 的 。但 是 有 很 多 因素 地 压 的 作 用 ,减 小 截 割 阻 力 ,但 是 截 割 截 割的工 作循 环次 数加 大 , 影 响 截 割 头 的 设 计 ,主要 有 以下 几 个 方 时 间会加 长 。 面: 使得生产效率降低。所以在截割 头长度 ( 1 ) 煤 岩 自身 的性 质 ,主要 有抗 截 的设 计 中 ,应 予 以综 合 考虑 。 ( 2 )截割 头直 径 强度 、硬度 、磨蚀 性 、坚 固性 系数 等 ; 截 割头 的直 径 主 要 影 响 掘进 机 的截 ( 2) 截 割 头 的结构 参 数 ,主 要有 截 割力 和_ T作循 环时 问 。 截割 头直 径过 大 , 割 头的几 何形 状 、 外形 尺 寸 、 截齿 排列 、 截齿 数量 以及 截线 间距 等 ; 则 切向截割力降低 ,当截割力 降到低于 ( 3) 截 割 头 的工艺 性 参数 ,主要 有 煤 岩 的截 割 阻力 时 ,截 割头 就 无 法 正 常 摆 动 速 度 、截割 头转 速 、切 削 厚 度 、切 工 作 ;而 当 截 割 头 直 径 太 小 ,截 割 头 切 削深 度等 。 向截割力增大 ,但 是由于掘进机截割 的 在 截 割 头 的设 计 上 ,这 些 因素 的 影 循 环 时 间变 长 ,同 样影 响掘 进 机 的掘 进 响 并 不 是 孤立 的 ,它 们 之 间 相 互 关 联 和 速 度 。当截割 功率 和截 割头 转速 一定 时 , 单 个 截 齿 的平 均 截 割 力 受 到截 割 头 直 径 制约 。
掘进机截割头受力分析与掘进实例分析
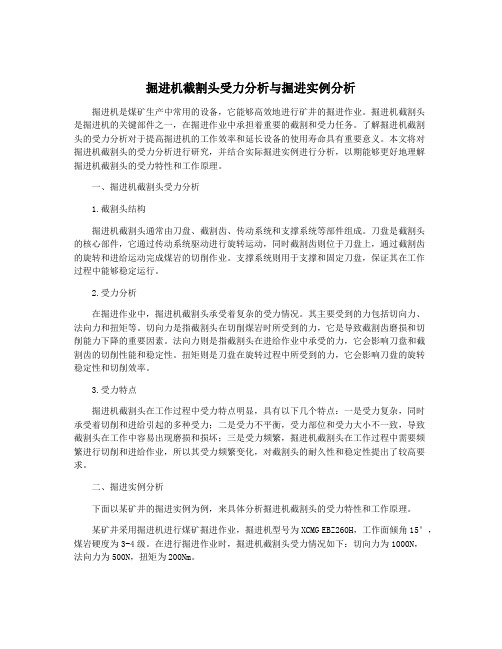
掘进机截割头受力分析与掘进实例分析掘进机是煤矿生产中常用的设备,它能够高效地进行矿井的掘进作业。
掘进机截割头是掘进机的关键部件之一,在掘进作业中承担着重要的截割和受力任务。
了解掘进机截割头的受力分析对于提高掘进机的工作效率和延长设备的使用寿命具有重要意义。
本文将对掘进机截割头的受力分析进行研究,并结合实际掘进实例进行分析,以期能够更好地理解掘进机截割头的受力特性和工作原理。
一、掘进机截割头受力分析1.截割头结构掘进机截割头通常由刀盘、截割齿、传动系统和支撑系统等部件组成。
刀盘是截割头的核心部件,它通过传动系统驱动进行旋转运动,同时截割齿则位于刀盘上,通过截割齿的旋转和进给运动完成煤岩的切削作业。
支撑系统则用于支撑和固定刀盘,保证其在工作过程中能够稳定运行。
2.受力分析在掘进作业中,掘进机截割头承受着复杂的受力情况。
其主要受到的力包括切向力、法向力和扭矩等。
切向力是指截割头在切削煤岩时所受到的力,它是导致截割齿磨损和切削能力下降的重要因素。
法向力则是指截割头在进给作业中承受的力,它会影响刀盘和截割齿的切削性能和稳定性。
扭矩则是刀盘在旋转过程中所受到的力,它会影响刀盘的旋转稳定性和切削效率。
3.受力特点掘进机截割头在工作过程中受力特点明显,具有以下几个特点:一是受力复杂,同时承受着切削和进给引起的多种受力;二是受力不平衡,受力部位和受力大小不一致,导致截割头在工作中容易出现磨损和损坏;三是受力频繁,掘进机截割头在工作过程中需要频繁进行切削和进给作业,所以其受力频繁变化,对截割头的耐久性和稳定性提出了较高要求。
二、掘进实例分析下面以某矿井的掘进实例为例,来具体分析掘进机截割头的受力特性和工作原理。
某矿井采用掘进机进行煤矿掘进作业,掘进机型号为XCMG EBZ260H,工作面倾角15°,煤岩硬度为3-4级。
在进行掘进作业时,掘进机截割头受力情况如下:切向力为1000N,法向力为500N,扭矩为200Nm。
掘进机截割头受力分析与掘进实例分析

掘进机截割头受力分析与掘进实例分析掘进机截割头是掘进机的核心部件之一,它可以在地下矿井、隧道等场合中,对岩石或土壤进行截割,起到掘进和开采的作用。
在现代化的采矿和隧道工程中,掘进机截割头已经成为掘进机的主要组成部分,如何分析其受力情况,对于提高采矿效率和保证采矿安全有着至关重要的作用。
掘进机截割头受力分析主要从以下几个方面进行:1、刀盘的运动以及截割头的旋转运动所产生的惯性力。
2、截割头与矿岩接触面的摩擦力,主要取决于矿岩的硬度和截割头的尺寸、角度等因素。
3、截割头的重量及其所带来的重力。
4、矿岩强度、结构、矿脉情况等因素对截割头的影响。
通过以上受力分析,可以得到掘进机截割头在实际应用中的受力特点:1. 切削力掘进机截割头在截割时,主要承受来自切削力的作用,切削力可以概括为沿切削面方向的力。
一般情况下,切削力与矿岩硬度、钢刃类型及质量、切削深度、截割头旋转速度等因素有关。
在较软的矿岩中,切削力相对较小,而在较硬的矿岩中,截割头的切削力会相应增大。
2. 摩擦力掘进机截割头在截割时,刀盘旋转产生了旋转摩擦力,在切削时,与矿岩接触的区域产生了切削面摩擦,同时随着刀盘旋转速度的增大,摩擦力也增大。
在实际操作中,控制截割头与矿岩的接触角度可以有效控制摩擦力的大小。
3. 冲击力在掘进机截割矿岩时,由于截割头与矿岩的接触面积较小,当截割头与矿岩接触时产生的冲击力较大。
同时,当截割头旋转速度过高,冲击力也会增加,从而影响截割头的寿命。
下面以一台采用截割头的掘进机为例,对掘进机截割头在实际应用中的受力特点进行分析。
该掘进机工作位置为深度530米以下处,岩体为砾岩和泥质砾岩,硬度在50~200MPa之间。
1. 截割机切削面法向力的测量在该工程中,通过悬挂载重器的测力传感器,测试了截割头切削时产生的法向力大小。
测量结果显示:截割头切削时的法向力为34.8kN~58.5kN之间。
3. 截割头工作时的振动测试对掘进机截割头工作时的振动进行测试,并分析了振动产生的原因。
关于纵轴式掘进机截割头主要参数的研究
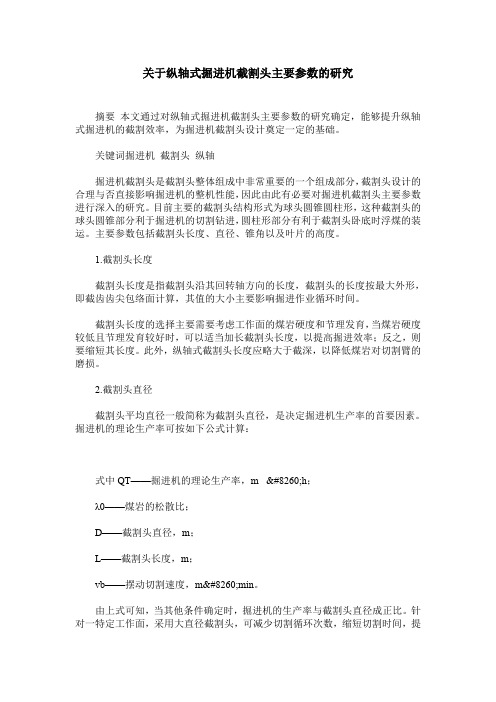
关于纵轴式掘进机截割头主要参数的研究摘要本文通过对纵轴式掘进机截割头主要参数的研究确定,能够提升纵轴式掘进机的截割效率,为掘进机截割头设计奠定一定的基础。
关键词掘进机截割头纵轴掘进机截割头是截割头整体组成中非常重要的一个组成部分,截割头设计的合理与否直接影响掘进机的整机性能,因此由此有必要对掘进机截割头主要参数进行深入的研究。
目前主要的截割头结构形式为球头圆锥圆柱形,这种截割头的球头圆锥部分利于掘进机的切割钻进,圆柱形部分有利于截割头卧底时浮煤的装运。
主要参数包括截割头长度、直径、锥角以及叶片的高度。
1.截割头长度截割头长度是指截割头沿其回转轴方向的长度,截割头的长度按最大外形,即截齿齿尖包络面计算,其值的大小主要影响掘进作业循环时间。
截割头长度的选择主要需要考虑工作面的煤岩硬度和节理发育,当煤岩硬度较低且节理发育较好时,可以适当加长截割头长度,以提高掘进效率;反之,则要缩短其长度。
此外,纵轴式截割头长度应略大于截深,以降低煤岩对切割臂的磨损。
2.截割头直径截割头平均直径一般简称为截割头直径,是决定掘进机生产率的首要因素。
掘进机的理论生产率可按如下公式计算:式中QT——掘进机的理论生产率,m ⁄h;λ0——煤岩的松散比;D——截割头直径,m;L——截割头长度,m;vb——摆动切割速度,m⁄min。
由上式可知,当其他条件确定时,掘进机的生产率与截割头直径成正比。
针对一特定工作面,采用大直径截割头,可减少切割循环次数,缩短切割时间,提高生产率。
式中T—截割头转矩,N∙m;P—切割功率,kW;n—切割转速,r⁄min;F—切割力(平均直径处的)。
如上式所示,切割力与切割功率成正比,与截割头直径、切割转速成反比。
所以与截割头长度参数类似的,当选用的截割头直径过大时,会降低每个截齿的切割能力,必要时,可以通过减小截割头直径来提升切割力。
掘进机纵轴式截割头截割效率的优化设计

纵 轴 式 截 割 头 设 计 原 则
力并使 传动比降 低,且截割臂尺 寸亦随之减 小。一股
与钻爆法掘进相比 ,综掘机机械割煤法更加经济 在 50'--80 cm范 罔选择。
安全 .且截割效率更高。因此在设计截 割头时应首要
截 割头主要参 数选择
考虑满足被割煤层或岩石的 自身物理性质 、计划截割
Vg
=
(2)
式中 v 一截割头横 向移动速度 ,rrmt/min; n一馘割头转动速度 ,r/min; N一 单排截齿数最 。 4.截割速度 掘进机 的截割速度主要视截割的煤岩性质决定。 对于普通 煤层 .常取 3 ̄4.5 m/s,速度过快 则会造成 粉尘浓度 过大 ,影响施 工 ;遇到较 硬岩层则 正常截 割速度一般 为 1 ̄2 nl/s,其截割速度过快则会造成截 齿 磨 损严 重 。 此外 ,截 割效率并非 随着截割速度 的增大 而增 加 ,煤层 的截 割厚度还 与切割挤压 的时间长短相关 。
B一截齿的 刀具角 ,(。 ); K一 岩石脆性 系数。 上式 中,针 对某范 罔内岩性岩石 来 说,掏枘钻 深
配,则微小的误蓐就会造成截齿极易磨损破坏 ,上作 hs及截齿刀具角 B均 由试验得出 ,参数基本确定不变。
效率降低。故截割头 设计时需 考虑 截割 头尺寸大 小、 因此截割 力的大小主要 取决于岩石 的抗拉强度 、脆 性
外的探索 经验及现场情 况对悬臂式掘进 机纵轴式截割 锥 面线 素线垂直 的原 则 ,主要依靠横 面半 移截 割 ,掏
头的优化提 出一些设计建议和方法。对以后截割头的 槽钻进辅助推进 ,使截割巷道段 面呈平直 。
设计具有借鉴意义。
在满足生产要求及截割头结构设计原则的情况下 , 截割头 的设 计直径应 越小越好 ,这样 _J。提高 单刀截割
掘进机截割头受力分析与掘进实例分析
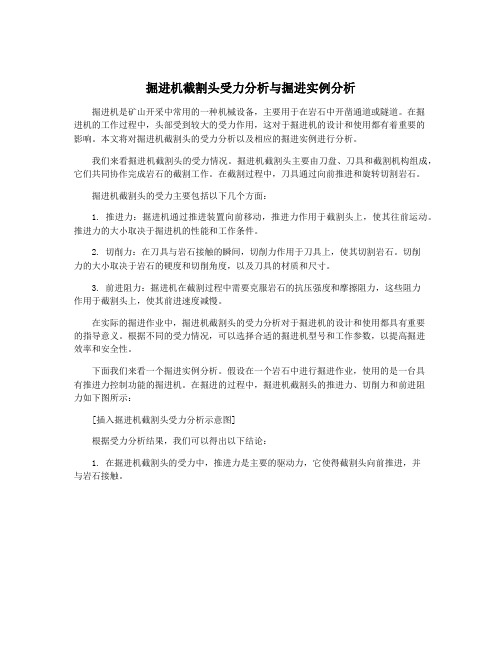
掘进机截割头受力分析与掘进实例分析掘进机是矿山开采中常用的一种机械设备,主要用于在岩石中开凿通道或隧道。
在掘进机的工作过程中,头部受到较大的受力作用,这对于掘进机的设计和使用都有着重要的影响。
本文将对掘进机截割头的受力分析以及相应的掘进实例进行分析。
我们来看掘进机截割头的受力情况。
掘进机截割头主要由刀盘、刀具和截割机构组成,它们共同协作完成岩石的截割工作。
在截割过程中,刀具通过向前推进和旋转切割岩石。
掘进机截割头的受力主要包括以下几个方面:1. 推进力:掘进机通过推进装置向前移动,推进力作用于截割头上,使其往前运动。
推进力的大小取决于掘进机的性能和工作条件。
2. 切削力:在刀具与岩石接触的瞬间,切削力作用于刀具上,使其切割岩石。
切削力的大小取决于岩石的硬度和切削角度,以及刀具的材质和尺寸。
3. 前进阻力:掘进机在截割过程中需要克服岩石的抗压强度和摩擦阻力,这些阻力作用于截割头上,使其前进速度减慢。
在实际的掘进作业中,掘进机截割头的受力分析对于掘进机的设计和使用都具有重要的指导意义。
根据不同的受力情况,可以选择合适的掘进机型号和工作参数,以提高掘进效率和安全性。
下面我们来看一个掘进实例分析。
假设在一个岩石中进行掘进作业,使用的是一台具有推进力控制功能的掘进机。
在掘进的过程中,掘进机截割头的推进力、切削力和前进阻力如下图所示:[插入掘进机截割头受力分析示意图]根据受力分析结果,我们可以得出以下结论:1. 在掘进机截割头的受力中,推进力是主要的驱动力,它使得截割头向前推进,并与岩石接触。
纵轴式掘进机截割系统的动力学分析及试验研究
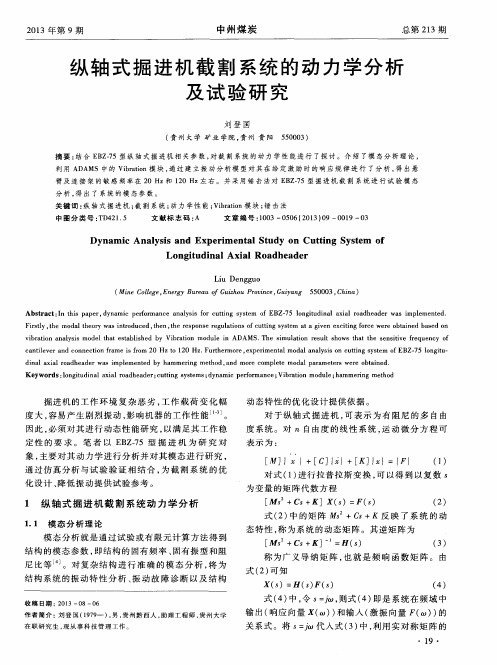
因此 , 必 须对 其进 行 动态性 能 研究 , 以满足 其工 作稳
定性 的 要 求 。笔 者 以 E B Z - 7 5 型 掘 进 机 为 研 究 对
2 0 1 3年第 9 期
中州 煤 炭
总第 2 1 3 期
纵 轴 式 掘 进 机 截 割 系 统 的 动 力 学 分 析 及 试 验 研 究
刘 登 国
( 贵 州大学 矿业学院 , 贵州 贵阳 5 5 0 0 0 3 ) 摘要 : 结合 E B Z . 7 5型纵 轴 式 掘进 机 相 关 参 数 , 对 截 割 系 统 的动 力 学 性 能 进 行 了探 讨 。 介 绍 了模 态分 析 理 论 ,
中 图分 类 号 : T D 4 2 1 . 5 文献标志码 : A 文章编号 : 1 0 0 3—0 5 0 6 ( 2 0 1 3 ) 0 9— 0 0 1 9—0 3
Dy n a mi c Ana l y s i s a n d Ex p e r i me nt a l St ud y o n Cu t t i ng Sy s t e m o f
利用 A D A MS中 的 V i b r a t i o n模 块 , 通 过 建 立振 动 分 析 模 型 对 其 在 给 定 激 励 时 的 响应 规 律 进 行 了分 析 , 得 出 悬
臂及连 接架的敏感频率在 2 0 H z 和 1 2 0 H z 左 右 。 并 采 用 锤 击 法对 E B Z 一 7 5型掘 进 机 截 割 系 统 进 行 试 验 模 态 分析 , 得 出 了系 统 的模 态 参 数 。 关键 词 : 纵 轴 式 掘 进机 ; 截 割系统; 动力学性 能; V i b r a t i o n模 块 ; 锤 击法
掘进机截割头受力分析与掘进实例分析
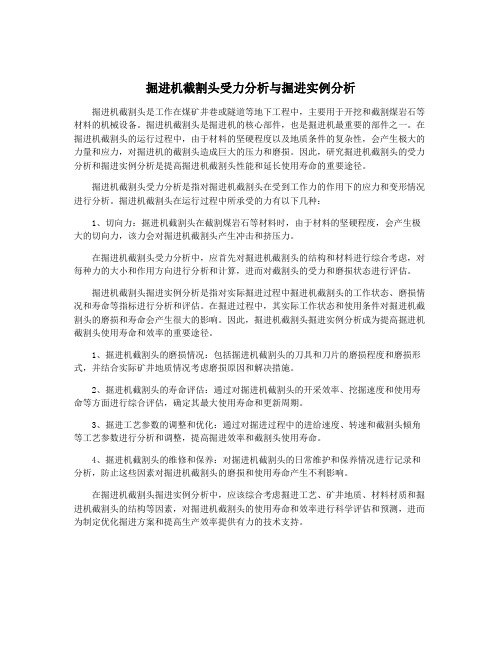
掘进机截割头受力分析与掘进实例分析掘进机截割头是工作在煤矿井巷或隧道等地下工程中,主要用于开挖和截割煤岩石等材料的机械设备。
掘进机截割头是掘进机的核心部件,也是掘进机最重要的部件之一。
在掘进机截割头的运行过程中,由于材料的坚硬程度以及地质条件的复杂性,会产生极大的力量和应力,对掘进机的截割头造成巨大的压力和磨损。
因此,研究掘进机截割头的受力分析和掘进实例分析是提高掘进机截割头性能和延长使用寿命的重要途径。
掘进机截割头受力分析是指对掘进机截割头在受到工作力的作用下的应力和变形情况进行分析。
掘进机截割头在运行过程中所承受的力有以下几种:1、切向力:掘进机截割头在截割煤岩石等材料时,由于材料的坚硬程度,会产生极大的切向力,该力会对掘进机截割头产生冲击和挤压力。
在掘进机截割头受力分析中,应首先对掘进机截割头的结构和材料进行综合考虑,对每种力的大小和作用方向进行分析和计算,进而对截割头的受力和磨损状态进行评估。
掘进机截割头掘进实例分析是指对实际掘进过程中掘进机截割头的工作状态、磨损情况和寿命等指标进行分析和评估。
在掘进过程中,其实际工作状态和使用条件对掘进机截割头的磨损和寿命会产生很大的影响。
因此,掘进机截割头掘进实例分析成为提高掘进机截割头使用寿命和效率的重要途径。
1、掘进机截割头的磨损情况:包括掘进机截割头的刀具和刀片的磨损程度和磨损形式,并结合实际矿井地质情况考虑磨损原因和解决措施。
2、掘进机截割头的寿命评估:通过对掘进机截割头的开采效率、挖掘速度和使用寿命等方面进行综合评估,确定其最大使用寿命和更新周期。
3、掘进工艺参数的调整和优化:通过对掘进过程中的进给速度、转速和截割头倾角等工艺参数进行分析和调整,提高掘进效率和截割头使用寿命。
4、掘进机截割头的维修和保养:对掘进机截割头的日常维护和保养情况进行记录和分析,防止这些因素对掘进机截割头的磨损和使用寿命产生不利影响。
在掘进机截割头掘进实例分析中,应该综合考虑掘进工艺、矿井地质、材料材质和掘进机截割头的结构等因素,对掘进机截割头的使用寿命和效率进行科学评估和预测,进而为制定优化掘进方案和提高生产效率提供有力的技术支持。
- 1、下载文档前请自行甄别文档内容的完整性,平台不提供额外的编辑、内容补充、找答案等附加服务。
- 2、"仅部分预览"的文档,不可在线预览部分如存在完整性等问题,可反馈申请退款(可完整预览的文档不适用该条件!)。
- 3、如文档侵犯您的权益,请联系客服反馈,我们会尽快为您处理(人工客服工作时间:9:00-18:30)。
纵轴式掘进机截割方法、路线与受力分析
摘要:随着煤矿行业的迅速发展,对掘进机的需求量也随之增多,如今掘进机的发展已由煤岩向半煤岩和岩巷的方向发展。
本文重点介绍纵轴式掘进机截割方法、路径与截割部受力分析。
关键词:掘进机截割方法受力
由于整个掘进机在工作时,首先是由截割头上的截齿来完成。
在截齿进行截割时,煤或岩石带来的阻力和冲击力通过截齿传递至截割头、截割部主轴及主轴承。
由于截割头、截割部主轴以及轴承的连接均为刚性连接。
因此随着其截割岩石硬度的增大,主轴和轴承所承受的冲击载荷必然会随之增大,特别是在掘进机进行钻进工作时,整个截割头所受轴向力几乎是由截割部主轴承来承受。
1 截割方法与截割路径
1.1 截割方法
掘进机在开始截割时,首先应利用截割头伸缩油缸或开动行走部,使截割头切入工作面煤壁(岩壁)一定深度,然后通过机体的回转运动和截割头的升降运动,即可切割出所要求的巷道断面形状。
对于纵轴式掘进机来说,切入工作面时,主要依靠截割头的钻进,其截深可根据岩、煤性质取为略小于、等于或略大于截割头长度。
值得注意的是,在截割头钻进煤、岩壁时,推进速度不可过大,每切入一定深度后要停
止推进,让旋转的截割头清理掉截落的小煤岩块,然后再继续推进机体或截割部,如此反复进行,直至达到所要求的截深为止。
1.2 截割路径
一般情况下,当截割较软的煤壁时,采用左右循环向上的截割方法,当截割稍硬岩石时,可采用由下向上左右截割的方法。
无论采用哪种方法,要尽可能的利用从下而上截割方法,避免由上向下进行截割,这样极易造成机体颤动,不稳定,对紧固件和部分零部件造成损坏,而且自上向下截割,特别是遇到坚硬岩石时,会使机体大部分重量压在截割部上,这样对截割部和其轴承伤害极大。
当遇见硬岩时,不应勉强进行截割,对有部分露头硬岩时,应当先截割其周围部分,使其坠落。
2 工作时掘进机截割头部的受力
根据掘进机现场工况,掘进机大部分工作是作回转截割运动,同时也存在截割头钻进运动。
此时截割头所受的切向力是由截割减速机截割扭矩作用在截割头上产生的截割切向力。
通过上述受力分析可知:在掘进机作回转截割工作时。
截割部主要承受以径向动载荷为主的径、轴向载荷;掘进机在作钻进工作时,截割部主要承受以轴向载荷为主的径、轴向载荷。
因此,掘进机在进行受力部件的结构设计和主轴承的选型时,要充分考虑这些因素,它关系着整个掘进机截割的强度和稳定性。
3 结语
井巷掘进是回采工作的先行作业,随着回采工作面机械化水平的提高,回采速度的加快,巷道掘进也必须相应加快,这样对掘进机正确使用显得尤为重要,要求掘进机司机在使用掘进机时,采用正确的截割方法和合理的截割路线,以及懂得掘进机相关知识,才能提高掘进的工作效率和延长机器的使用寿命。
参考文献
[1] 朱真才,韩振铎.采煤机械与液压传动(第2版)[M].徐州:中国
矿业大学出版社,2006(2):273~274.
[2] 黄日恒.悬臂式掘进机[M].徐州:中国矿业大学出版社,1996.。