QRQC快速反应质量控制程序
QRQC教程原始版-快速反应质量控制

零缺陷
不要接 受不合 格品
不要 制造 不合 格品
不要提供不 合格品
12
FTA原因树分析
对问题的原因树分析 发生
因素 控制点 标准 实际数据
判断 标准 质量
决定
问题为什么 材料 会发生
基于sangenshugi 的原则来检查真实 数据
O O X X 将真实数据及测量
方法
值与标准进行对比
人员
确认标准(技术说 明、公差数据)
36
在生产线开展APU QRQC
APU 1 PPM Data A PPM Data B Pbm 1 Pbm 2 问题 Pbm 3
说明APU QRQC 流程
Line 1: OK PPM Data A
Line 2 : OK PPM Data A
PPM Data B
PPM Data B Line 4 : NOK PPM Data A
存在的形式:产品、工艺
齿合 产品POKA-YOKE
密封胶检查 工艺POKA-YOKE
28
QRQC与PDCA
QRQC通过分配任务给指定的人来支持QRQC 快速反应PDCA与分析PDCA必须通过工厂
QRQC的确认。
29
QCDM
质量
Q 成本 C M
人力
30
D
效率
5W+2H
发生了什么 为什么是个问题 什么时候发生的 谁发现的 哪里发现的 怎么发现的 多少
客户零缺陷。
23
工位对 应缺陷 描述
AQM 质量自控矩阵图
各工位
自控区
域
工位描
述 未自控 区域
24 Proprié téValeo - Reproduction interdite
QRQC管理办法全

QRQC管理办法XXXX1O目的为控制产品质量,提高工作效率,防止不良品向后续工序流动、对品质问题作出早期反应并在当日制订解决问题的对策,防止品质问题的再次发生。
QRQC强调〃三现〃主义,及现场,现物,现实,关键在于及时到达问题现场,确认问题,寻找问题种种迹象,为分析问题产生提供基于事实的依据;通过各相关部门的真诚协作搭建良好的合作与关系信赖,以达到高效率的解决问题。
2.0适用范围适用于公司所有生产线,它运用可视的方法显示重要的信息以解决重大的外部和内部的质量问题。
3.0定义QRQC:Quickresponsequa1ityCOntrO1快速反应质量控制。
主要以现场、现物、现实为基础,用5W2H、PDCA等质量工具,通过操作人员、班组长、QA组长,工艺工程技术员,SQA组长,及车间主管,QE工程师,工艺工程与SQE工程师用数据富有逻辑性的思考分析方法解决产生的质量问题。
主要体现在以下方面:1)反应的速度;2)深入的分析(5why),找准根本原因;3)根除质量问题的重复发生;4)增进横向交流。
三现主义:去事发现场(现场)了解发生了什么事情(现物)找到事实的真相(现实数据)。
1)现场:到真正发生问题的地方去;2)现物:合格品与不合品比较;3)现实数据:用真实的数据去描述事实。
4.0职责与权限4.1发现问题点部门(产线组长/OQCzIPQC/工艺工程技术员)负责通知QE与他们的直线主管,并由QE通知相关部门的人员(班组长,QA组长,工艺工程技术员,SQA组长)召开QRQC 会议,讨论围堵措施,分析根本原因,并制定纠正预防措施,并跟进改善的效果。
4.2生产部主管,品质部工程师,工艺工程部工程师与SQE工程师:改善措施涉及到相应的部门,相应的部门的工程师或主管需在36小时内签名确认改善措施的有效性,如果改善措施被拒绝,这个1ineQRAP需要重新填写新的改善措施。
4.3品质部:负责跟进各种质量问题,包括内外审不符合项快速解决、公司内部及外部质量事故,及时跟进各部门的改善行动方案和效果。
QRQC会议流程
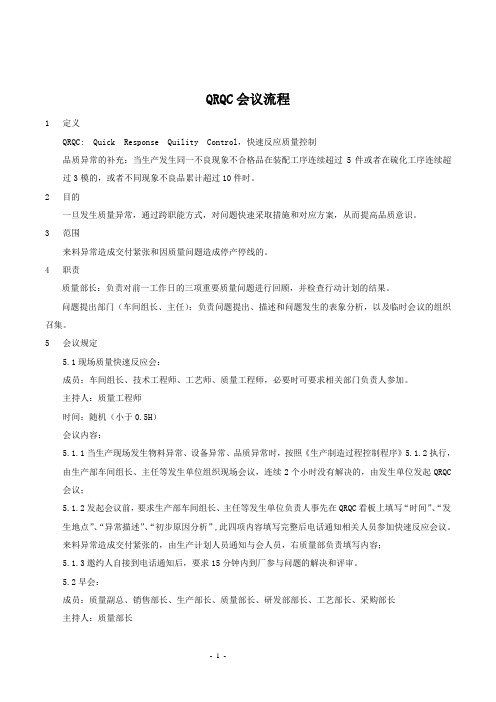
QRQC会议流程1定义QRQC: Quick Response Quility Control,快速反应质量控制品质异常的补充:当生产发生同一不良现象不合格品在装配工序连续超过5件或者在硫化工序连续超过3模的,或者不同现象不良品累计超过10件时。
2目的一旦发生质量异常,通过跨职能方式,对问题快速采取措施和对应方案,从而提高品质意识。
3范围来料异常造成交付紧张和因质量问题造成停产停线的。
4职责质量部长:负责对前一工作日的三项重要质量问题进行回顾,并检查行动计划的结果。
问题提出部门(车间组长、主任):负责问题提出、描述和问题发生的表象分析,以及临时会议的组织召集。
5会议规定5.1现场质量快速反应会:成员:车间组长、技术工程师、工艺师、质量工程师,必要时可要求相关部门负责人参加。
主持人:质量工程师时间:随机(小于0.5H)会议内容:5.1.1当生产现场发生物料异常、设备异常、品质异常时,按照《生产制造过程控制程序》5.1.2执行,由生产部车间组长、主任等发生单位组织现场会议,连续2个小时没有解决的,由发生单位发起QRQC 会议;5.1.2发起会议前,要求生产部车间组长、主任等发生单位负责人事先在QRQC看板上填写“时间”、“发生地点”、“异常描述”、“初步原因分析”,此四项内容填写完整后电话通知相关人员参加快速反应会议。
来料异常造成交付紧张的,由生产计划人员通知与会人员,右质量部负责填写内容;5.1.3邀约人自接到电话通知后,要求15分钟内到厂参与问题的解决和评审。
5.2早会:成员:质量副总、销售部长、生产部长、质量部长、研发部部长、工艺部长、采购部长主持人:质量部长时间:8:00-8:30会议内容:5.2.1 由质量部长总结汇报前一工作日工厂内部三项重要的质量异常跟踪解决情况;5.2.2由质量部长汇报前一工作日客户异常投诉和跟踪解决情况;5.2.3由生产部长汇报前一工作日对紧急交付产生影响的重要质量异常;5.2.4由工艺工程部部长汇报无法前一工作日无法解决的重要质量异常;5.2.5对于现场会议所提出的内容,必要时需要制定责任人和时间节点,由质量管理部负责跟踪;6 会议原则6.1有事需请假,并找代理人参加会议,无故迟到者,罚款5元/次;6.2参加早会者,每天应在签到表上签字;6.3分配任务不按照节点完成的,每项处罚10元。
QRQC品管快速反应机制Quick Reaction Quality Control

QRQC品管快速反应机制Quick Reaction Quality Control1.QRQC可以先拿个小组或车间来试点运行,取得成将效后再推广到其它小组;其它车间/部门,最后到全公司的QRQC.3个层级的QRQCA.生产线QRQC:关注于/每个生产线的不良--领导/组长---参与者/全体操作人员--频次/每次不良发生-- 可提供支持者/生产线管理员& 车间主管& 车间质量工程师.B.车间QRQC:关注于/车间里的主要问题--领导/车间主管--参与者/车间各职能人员+生产线管理员 --频次/每天--可提供支持者/车间主管+ 车间质量主管.C.工厂QRQC:关注于/安全问题&客诉问题---领导/工厂经理---参与者/职能部门人员--频次/每天---可提供支持者/公司总经理& 公司质量经理.QRQC 延伸:A.供应商QRQC:关注于/ C1, C2, C3 & WR 质量事故---领导/采购经理---参与者/采购员---可提供支持者/SQA & 供应商代表,总经理& 质量经理.B.物流QRQC:关注于/供应商& 客户物流事故---领导/物流经理---参与者/物流小组& 物流供应商---可提供支持者/工厂经理& 采购经理.C.项目QRQC:关注于/项目开发中的问题---领导/项目经理参与者/项目小组成员---可提供支持者/其他项目经理& R&D 经理.2."在实际开展中有很多问题。
"不太明白你说的具体问题?? ---------每天对所发生的问题进行统计分析,如果问题很多,先对关键的/不良率高的产品或项目进行原因分析/对策改善.一般为不良率高的前三项目即可.3.QRQC的San Gen Shugi 三现主义:. A-Real Place (Gen-ba) on shop floor;B-Real Parts (Gen-butsu) with real bad parts;C-. Reality (Gen-jitsu) with data.4.如何才能成功推行QRQC?---管理层参与& 清醒认识自己的弱项---根植于三现主义---从现场得到信息---逻辑性地思考方式:---什么问题?---根本原因是什么?(制造因+流出因)---遏制措施是什么?---遏制措施效果如何?---每天QRQC+在职培训---激励员工举例分析:车间的QRQC---Who attends ? :谁参加---APU Manager and APU Quality 车间主管和车间质保---Plant Manager & Quality Manager, for Customer Claims 厂长和质量经理---Supervisors 主管---Method, Maintenance 工艺,维修---Others as required : SQA, Project, Logistics…其他人,如需要:SQA, 项目,物流……---Contents :内容---Review impact of yesterday’s actions审查昨天的行动的影响---Review 3 most important problems of the Production (Choice done by Production Manager, Importance is based on criticity, complexity, recurrence and quantity of parts) 审查生产中3个最主要的问题(生产部经理的决定,根据严重度,复杂度,频度和产品的数量)---When ? :什么时候---Every day 每天---How ? :如何做---Using presentation boards with following information : 用带有以下数据的信息板---Action rules 行动规则---Quality consolidated results of APU车间质量巩固的数据---Results split by APU’s : for each APU, have every day result of the month, and monthly results 车间的数据:每个车间的日报,月报。
qrqc管理办法

qrqc管理办法QRQC,即Quick Response Quality Control,是一种快速响应质量控制方法,旨在对质量问题进行快速解决和改进。
QRQC方法的实施可以帮助企业迅速对质量问题进行定位、分析,并采取相应措施以确保产品质量和客户满意度。
本文将介绍QRQC管理办法的具体步骤和实施方法。
一、QRQC概述QRQC管理办法是一种集成了质量管理和问题解决的方法,可以帮助企业快速响应和解决质量问题。
QRQC方法主要分为4个步骤:问题定义(Question)、快速恢复(Quick Recovery)、原因分析(Root Cause)和对策制定(Permanent Countermeasure)。
通过这些步骤,企业可以有效地解决质量问题,并防止其再次发生。
二、QRQC管理办法步骤1. 问题定义(Question)在QRQC管理办法中,首先需要准确定义问题。
通过搜集和分析相关数据,明确问题的性质、范围和影响。
问题定义的关键是确保对问题有一个清晰的理解,为后续的解决措施提供基础。
2. 快速恢复(Quick Recovery)快速恢复是指在发现问题后,迅速采取措施来控制和修复问题。
这包括制定临时对策,解决最紧迫的问题并将生产恢复到正常状态。
快速恢复的目标是尽快减少负面影响,并确保客户不受影响。
3. 原因分析(Root Cause)原因分析是QRQC的重要环节,旨在找出问题发生的根本原因。
通过使用常用的质量工具如5W1H分析、鱼骨图等,可以辨识出问题的根本原因。
确切找到问题的原因可以有效避免反复发生类似问题。
4. 对策制定(Permanent Countermeasure)对策制定是为了根除问题的发生,确保类似问题不再出现。
通过制定并实施长期解决方案,企业可以对质量问题进行持续改进。
对策制定需要综合各方面的因素,确保解决方案的可行性和有效性。
三、QRQC管理办法实施方法1. 专门团队企业需要成立一个专门的QRQC团队,由跨部门的优秀人员组成。
QRQC快速响应质量控制程序(含表格)

QRQC快速响应质量控制程序(IATF16949-2016/ISO9001-2015)1.0目的:(1)为提高质量水平,降低PPM值,减少PRR的发生;(2)提高客户满意度;(3)提供系统问题的解决方法,改善对于质量问题的沟通,降低质量问题再发生的次数,保证所有质量问题都得到彻底解决。
2.0使用范围:本程序适用于本公司产品的内外部质量问题的解决及除质量问题。
3.0术语:快速反应:通过每日例会加强沟通和管理,采用目视管理方法展示重要信息,使应对重大的内、外部质量问题的反应标准化。
问题解决:一个系统化的用来识别、分析和消除现状和现行标准或期望之间的差距,并预防根本根本原因再次发生的过程。
经验总结:利用成功经验,防止错误重复出现。
4.0职责:(1)生产部负责快速反应会议,技术部质保部等给予支持。
(2)品质部负责人负责采用8D等方法、运用相应工具解决问题。
(3)各负责部门负责其相应经验教训活动,技术部负责文件归档和发布。
5.0快速反应会议:5.1开会时间,每天一次,每次10-25分钟,会上只对质量问题进行沟通。
5.2开会地点:生产现场看板前。
5.3参会人员:总经理及所有部门的相关责任人,因故不在候补出席。
5.4会议主题:应对每天的具体重大质量问题。
5.5会议准备:质量部每天找出过去24小时发生的重大质量问题,开会前详细描述在白板上。
具体问题包括:(1)客户关注的问题;(2)供应商关注的问题;(3)停线(内部或外部);(4)重复发生的质量问题;(5)班废品率超过综合废品率目标;(6)验证岗位中发现的问题;(7)分层审核中发现的问题;(8)其他内部质量问题。
5.6 会议内容:(1)总经理协调各方意见,确定新问题的责任人和关闭日期。
(2)旧问题负责人提交相关报告,报告具体进度,紧抓问题退出标准,由与会人员确认关闭。
(3)技术部根据当天情况,标明具体问题和每日Q图的状态。
5.7 会后工作:问题负责人运用8D等方法、相关工具解决问题,总结形成报告。
qrqc管理规定

qrqc管理规定QRQC管理规定是一种有效的问题解决方法,可以帮助组织在面对挑战和困难时快速、高效地解决问题。
本文将介绍QRQC管理规定的流程和具体实施步骤,以及它在实际应用中的好处和注意事项。
一、QRQC管理规定的概述QRQC(Quick Response Quality Control)是一种起源于日本的问题解决方法,主要用于解决生产过程中出现的质量问题。
QRQC管理规定的目标是快速、准确地找出问题的根本原因,并制定相应的改进措施,以防止问题的再次发生。
这一方法常被广泛应用于制造业,但也适用于其他领域。
二、QRQC管理规定的流程1. 确定问题:首先,需要明确发生的问题是什么,可以通过收集相关数据、观察现场、听取工人和客户的意见等方式来了解问题的具体情况。
2. 快速反应:一旦问题明确,团队需要迅速反应,将问题与负责人沟通,并启动QRQC管理规定的流程。
此时,团队成员应该专注于问题,并互相合作,以快速找出解决问题的方法。
3. 分析原因:在快速反应的基础上,团队应该对问题进行深入分析,找出造成问题的根本原因。
这一过程可以通过使用5W1H(What、When、Where、Who、Why、How)的方法来确定,以确保全面、准确地理解问题。
4. 制定改进措施:在分析原因的基础上,团队应该制定相应的改进措施,以解决问题,并防止问题的再次发生。
这一步骤需要确保改进措施具有可操作性,并能够从根本上解决问题。
5. 实施和验证:改进措施的实施与验证是QRQC管理规定的最后一步。
团队需要积极地实施改进措施,并通过对比前后数据、观察生产现场等方式,验证改进效果。
如果改进措施有效,问题得到解决,QRQC管理规定的流程就可以结束;如果改进措施没有达到预期效果,那么团队需要回到分析原因的步骤,重新制定改进措施。
三、QRQC管理规定的好处1. 快速解决问题:QRQC管理规定是一种快速、高效的问题解决方法,可以帮助组织快速找出问题的根本原因,并制定相应的改进措施。
qrqc管理办法

qrqc管理办法QRQC是指Quick Response Quality Control,即快速响应质量控制的管理办法。
它是一种用于进行质量问题解决的系统性方法,可以帮助企业高效地处理各种质量问题,以提升产品和服务的质量水平。
本文将介绍QRQC管理办法的具体内容和实施步骤。
一、QRQC管理办法的概述QRQC管理办法是一种迅速响应和解决质量问题的方法,它的目的是迅速定位和解决质量问题,以防止问题影响到生产和客户满意度。
QRQC管理办法以PDCA循环为基础,通过快速收集信息、快速分析问题、快速制定措施和快速验证效果等手段,帮助企业实现质量问题的快速解决。
二、QRQC管理办法的步骤1. 问题定义:首先,需要明确问题的定义,包括问题发生的时间、地点和涉及的具体内容等。
问题的准确定义可以帮助团队更好地理解问题和解决方案的范围。
2. 快速收集信息:团队成员需要快速采集相关信息,包括问题的发生频率、问题的影响范围、问题出现的原因等。
信息的收集可以通过观察、采访员工和查阅相关文件等方式进行。
3. 快速分析问题:在收集到足够的信息后,团队需要快速分析问题的原因。
可以使用5W1H(What、Where、When、Who、Why、How)方法进行问题分析,找出问题根本原因。
4. 快速制定措施:根据问题分析的结果,团队需要快速制定解决问题的措施。
措施应该具有可操作性、针对性和可验证性,以确保问题得到解决。
5. 快速验证效果:在措施实施后,团队需要快速验证措施的有效性。
可以使用PDCA循环的思路,通过实际操作和数据验证来评估措施的效果。
6. 标准化操作:当问题解决之后,团队需要将有效的措施进行标准化操作,并制定相应的操作规范和培训计划,以防止问题再次发生。
7. 持续改进:QRQC管理办法不仅仅是一种解决问题的方法,更是一种持续改进的理念。
团队应该时刻关注和分析质量问题,以不断改进工艺流程和产品质量。
三、QRQC管理办法的好处QRQC管理办法具有以下几个好处:1. 快速解决问题:QRQC管理办法可以帮助企业快速定位和解决质量问题,减少问题对生产和客户的影响。
qrqc管理办法

qrqc管理办法QRQC(快速反应质量控制)管理办法在现代工业生产中,质量控制是一项至关重要的任务。
为了提高产品质量和生产效率,许多企业采用了各种质量管理方法。
其中之一就是QRQC(快速反应质量控制),它是一种以问题解决为中心的管理方法。
本文将介绍QRQC的管理办法及其应用。
一、QRQC的概念QRQC是由日本汽车制造行业发展起来的管理方法,它的核心思想是解决生产过程中出现的问题,并推动持续改进。
QRQC注重快速反应,希望能够尽快地发现问题,并迅速采取解决措施。
与传统的质量管理方式相比,QRQC更加注重问题的根本原因,而不仅仅是解决表象问题。
二、QRQC的基本流程QRQC的基本流程包括以下几个阶段:问题的识别、问题的分析、问题的解决、解决方案的验证和复制,以及问题的预防。
在问题的识别阶段,团队成员需要通过观察和数据分析等方式,发现生产过程中存在的问题。
这些问题可能来自于产品的缺陷、设备的故障、材料的质量等各个方面。
团队成员需要准确地描述问题,并将其纳入到QRQC的管理范围之内。
在问题的分析阶段,团队成员需要深入研究问题,找出其根本原因。
这通常需要收集和分析大量的数据,并进行逐步深入的追溯。
通过分析问题的原因,团队可以更好地理解问题,并为解决问题制定对策奠定基础。
在问题的解决阶段,团队成员会根据问题的根本原因,制定并实施解决措施。
这些措施可能包括修复设备、改进工艺、培训员工等等。
团队成员需要密切合作,确保解决方案的有效实施。
在解决方案的验证和复制阶段,团队成员会对解决方案进行验证实验,确保其有效性和稳定性。
如果解决方案能够解决问题并持续有效,团队会将其复制到其他类似情况中应用,以提高整体的质量水平。
最后,在问题的预防阶段,团队成员会总结经验教训,并提出预防措施,以避免同类问题再次发生。
预防措施可能包括改进工艺、加强员工培训、改进设备维护等等。
通过预防措施的不断完善,企业可以逐渐提高整体的质量水平。
三、QRQC的优势和应用QRQC的管理办法具有以下几个优点:1.快速反应:QRQC注重快速反应和快速解决问题,能够帮助企业迅速应对生产中的质量问题,避免问题扩大化,减少经济损失。
QRQC质量问题快速反应

目 录
• 引言 • 质量问题快速反应流程 • 质量问题快速反应工具和技术 • 质量问题快速反应的案例研究 • 总结与展望
01
引言
目的和背景
随着市场竞争的加剧,质量问题对企业的影响越来越大。为 了快速响应质量问题,提高客户满意度和保持竞争优势,企 业需要建立有效的质量问题快速反应机制。
04
质量问题快速反应的案 例研究
案例一:生产过程中的质量问题快速反应
要点一
总结词
要点二
详细描述
及时发现、迅速解决
在生产过程中,某零件的硬度不符合标准,可能导致产品 性能下降。通过QRC小组的快速响应,立即停止生产线, 找出问题原因,调整工艺参数,确保产品质量。
案例二:售后服务中的质量问题快速反应
QRC(Quality Response Center)是一种质量问题快速反应 机制,通过集中管理、快速响应和有效沟通,确保质量问题得 到及时、准确的处理。
质量问题的定义和分类
质量问题是指产品或服务不符合规定 要求或标准,导致客户不满或投诉的 问题。
质量问题可以根据影响程度和紧急程 度进行分类,如轻微、一般、严重等。 针对不同类型的质量问题,QRC需要 采取不同的处理方式和优先级。
总结词
客户至上、主动服务
详细描述
客户反馈产品在使用过程中出现故障。售后服务团队迅 速响应,远程诊断问题,提供解决方案,同时安排维修 人员上门服务,及时恢复产品正常运行,赢得客户的高 度评价。
案例三:研发过程中的质量问题快速反应
总结词
创新思维、预防为主
详细描述
在研发新型产品的过程中,发现某元件的寿命不符合 预期。研发团队迅速组织专题会议,分析可能的原因 ,调整材料和工艺,提前解决潜在问题,确保产品顺 利上市。
QRQC快速反应质量控制管理培训资料

QRQC快速反应质量控制管理培训资料QRQC(Quick Response Quality Control)是快速反应质量控制的缩写,是一种快速反应质量问题并采取有效措施解决的管理方法。
下面是一份QRQC快速反应质量控制管理培训资料,内容如下:第一部分:QRQC基本概念和原理(300字)1.QRQC的定义:QRQC是一种快速反应质量控制方法,通过迅速发现、定位和解决质量问题,以实现及时交付高质量产品。
2.QRQC的原理:QRQC是基于以下原理:准确的问题识别、紧急的问题解决和广泛的员工参与。
3.QRQC的核心要素:QRQC的核心要素包括:快速反应、团队合作、问题分析、根本原因追溯和持续改进。
第二部分:QRQC实施步骤(400字)1.第一步:问题确认和描述。
团队成员应该集中精力确定问题的本质,并以简洁明了的方式对问题进行描述。
2.第二步:快速根本原因分析。
利用鱼骨图、五为一法等工具快速找出问题的根本原因,并确保团队对问题原因的一致认识。
4.第四步:对策效果确认。
执行纠正行动并进行效果验证,确保问题已经得到解决或得到明显改善。
5.第五步:对策标准化和持续改进。
通过制定和标准化解决方案,确保问题不再发生,并将解决方案纳入常规工作流程,实现持续改进。
第三部分:培养QRQC团队的关键要素(300字)1.团队合作意识:要培养团队成员的合作意识和责任感,让每个成员明确自己在整个过程中的角色和权责,以提高团队的协同效率。
2.快速问题解决能力:培养团队成员快速识别和解决问题的能力,强调及时反馈、快速决策和紧急行动。
3.基本分析工具的使用:培训团队成员运用常用问题分析工具,如鱼骨图、5W1H等,以帮助快速找出根本原因。
4.持续改进文化:培养团队成员对问题的持续改进意识,注重归因分析、学习型组织建设等方面的能力提升。
第四部分:QRQC案例分析与讨论(200字)在培训中,可以引入一些实际的QRQC案例,通过讨论和分析,加深学员对QRQC方法的理解。
QRQC质量控制快速反应管理办法

分发部门:■业务部□行政部■工程部■资材部■生产部■品质部□工模部□财务编制审核批准1. 目的对公司,车间内部或外部所发生的品质问题、生产异常、安全事故、纠正事项、内外审核不符合项等作出快速反应并制定纠正与预防方案,使存在问题得到快速、正确解决,促进生产工作的顺利进行。
特制定本管理办法。
2. 适用范围本管理办法适用于发现问题、收集信息、分析原因和确认改进的QRQC公司管理工作。
3. 规范性引用文件下列文件对于本文件的应用是必不可少的,凡是注日期的引用文件,仅注日期的版本适用于本文件。
凡是不注日期的引用文件,其最近版本(包括所有的修改单)适用于本文件。
4. 定义4.1 QRQC :英文Quick Response Quality Control 的缩写,中文为:快速反应质量控制,也就是品质保证PDCA 的快速运转;4.2 问题解决:系统化的用来识别、分析和消除现状与现行标准或期望之间的差距,并预防根本原因再次发生的过程管理4.3 三现主义:现时、现地、现物;在现场发现问题,在现场分析问题,在现场解决问题4.4 三不原则:不接受不良、不制造不良、不流出不良5. 管理作用及职责5.1 作用:5.1.1 收集、汇总和QRQC活动有关的所有情报,以保证产品交期为主要阶段目标,以各项异常事件为工作载体,在工厂范围内全面推进QRQC思想;5.1.2 组织召开公司级及班组的QRQC会议;5.1.3 制定、维护并执行公司QRQC事务的各项管理制度和流程;5.1.4 管理、维护QRQC记录和报告书;5.2 职责:5.2.1 生产部负责快速反应会议,由总经理担任最高议长;轮值班长:生产经理、品质经理轮流担任会议监督;下设专职QRQC专员。
6.2.2 供应商关注的问题; 6.2.3 停线(内部或外部); 6.2.4 废品率超过管理目标; 6.2.5 工序验证中发现的问题; 6.2.6 分层审核中重复发生的问题; 6.2.7其它内部质量问题;6.3 会议主要议程:6.4 会议内容:6.4.1 会议工程生产经理协调各方意见,确定新问题的责任人和关闭日期;6.4.2 旧问题负责人提交相关报告,报告具体进度,紧抓问题退出标准,由与会人员确认关闭; 6.4.3 会议主持根据当天情况,标明具体问题和日 Q 图的质量状况;6.5 会后工作:问题负责人运用 8D 、5WHY 等方法、相关工具解决问题,总结形成报告;6.6 其他定期工作:6.6.1 QRQC 快速反应跟踪表应记录所有产生的问题关闭检讨; 6.6.2 每月汇总公布问题发生的数据趋势图;6.6.3 超过 1 个月的改善课题必须每两周最少检讨一次;文件名称深圳市 XX 电子有限公司 QRQC 质量控制快速反应管理办法文件编号 XX-Q3-PG-09版本 A/0 页版次 第 7页共 8 页 发行日期 2019.09.21QRQC 会议解决。
QRQC快速反应质量控制

Da数ta据A:Ad: a每ta月p的er数m据onth 数D据atBa: B一: 月Da中ta每pe天r 的da数y 据
of month
消费局部
效果
PPM 数据 A
PPM 数据 B
Line 1: OK PPM 数据 A
DATE
D M Y MAX DATE D M Y FOR
PREPARED:
ANSWER:
ASSIGNM ENT ISSUED TO
Via: * IF THE DEFECT IS IN CAT. A OR B, GET
APPROVAL FROM TOP
M ANAGER
APU M GR QUALITY
SUB J ECT :
消费线上如何做QRQC? QUICK RESPONSE ACTION PLAN
What is root cause ? What are C/M ? What are expectations Resp When
确认
行动的确认
发现问题
红箱子
生产 线
QRQC
分析
停线分析
信息交流
质量自控矩阵 快速反应
行动计划板
Reality (Gen-jitsu) with data 真实的举动
March 2004
10
QRQC Introduction
. . .实施 〝Genjitsu〞 是指理想,而不是理想化 . 〝Genba 〞 是指到消费第一线去发现效果发生的根源。 〝
Genbutsu〞 , 参考不好的零件,和不合格品的处置方法 我们最先要做的是〝红箱子〞管理,那就是说把焦点集中
QRQC教程原始版-快速反应质量控制

POKA-YOKE
POKA-YOKE:是一种防差错的系统
错误的 装配
忘装零 件
26
POKA-YOKE
特点
任何情况下都应该尽可能使用POKA-POKE
简单 便宜
可靠 可节约时间
存在的形式:产品、工艺
27
POKA-YOKE
任务分配单
生产部问题记录表
Line 3 : OK PPM Data A
PPM Data B
PPM Data B
检查 任务分配表 分析PDCS
出现不合格品
37
工厂Plant QRQC 流程
发现
客户抱怨及工厂内部综合问 题
验证
跟踪 / 评审
交流
Plant QRQC
任务分配表
分析
根本原因 PDCA FTA
1.
24小时之内快速反应
43
QRQC步骤(二)
在采取临时的隔离措施之后。 第二步是了解问题的根本原因并解决它。为此,我 们要运用原因树分析工具FTA进行分析PDCA。 (包括为什么发生和为什么没发现两个PDCA分 析) 首先要通过原因分析树观察标准和实际数据
44
QRQC步骤(二)
在采取临时的隔离措施之后。 第二步是了解问题的根本原因并解决它,为此,我 们要运用原因树分析工具FTA进行分析PDCA。 首先要通过原因分析树观察标准和实际数据 并用五个为什么验证根本原因 Plan
20
5S 工作站
清洁
素养
整理
清扫
整顿
推行5S的目的
提供舒适 提高现场 的工作效 率
qrqc快速反应质量控制管理规范

QRQC/QRQE管理办法(IATF16949-2016)1、目的规定了公司QRQC活动开展的指导思想和实施方法。
2、范围适用于公司QRQC工作的管理。
3、术语QRQC—Quick response quality control,即快速反应质量控制。
是通过每日开展以QRQC信息中心为主体的现场质量问题快速改善活动,达到质量信息在全公司范围内的共享,消除产生不合格的主要原因,减少不合格品的发生,举一反三,避免类似质量问题的重复发生,同时规范现场质量管理,进而提高实物质量水平的一种方法。
4、组织机构4.1、组织成员4.1.1、公司QRQC小组成员:质量副总经理、品质保证部部长、现场质量室主任、现场质量工程师、供方质量工程师、市场信息管理室主任、研发中心主任、制造技术部部长、SCM部部长、装备部部长、各责任单位部长和质量工长4.1.2、各车间小组成员:作业部长、质量工长、装备部技术人员、制造技术部工艺员、品质保证部现场质量工程师、作业班长、生产协调人员4.2组织层级5、职责5.1品质保证部负责组织成立公司QRQC活动小组,组织各相关单位审议责任单位QRQC活动中原因分析和措施是否适当,判定是否提交QRQE进行处置;5.2各相关部门对涉及到本部门质量信息的处理和管理工作负责,及时成立QRQC小组快速对质量问题进行反应。
5.3现场质量工程师负责QRQC活动的组织、分析、验证,对质量信息关闭的有效性负责。
5.4QRQC推进员负责QRQC会议记录和评价6、控制要点6.1QRQC会议前信息的收集、传递和处理。
6.1.1各作业部各相关作业人员发现不良后反馈到本部门QRQC推进员,作业部QRQC推进员组织制造技术部工艺员、品质保证部现场质量工程师(必要时供方质量工程师参加)及作业班长分析原因并制定临时对策,然后填写《QRQC对策表》提交次日QRQC会讨论6.1.2品质保证部现场质量工程师组织公司QRQC小组对不良原因分析和措施进行论证,论证通过的由车间和现场质量工程师跟踪措施执行情况并根据现场品质合格率统计数据进行验证6.1.3判定需要通过技术手段进行完善和支持,转入QRQE;6.2质量信息管理层级判定标准6.3QRQC活动相关说明6.3.1品质保证部负责QRQC质量问题处理的汇总、分析、过程跟踪、结案登记,对信息处理过程中出现推诿、应付等的单位实施考核,并将管理考核提交给经营规划部。
QRQC质量问题的快速反应

• Key points 关键点 • Assess efficiency + speed 评估效率和速度
3. Summary总结
6
History 历史
• Invented by Nissan in the 90‘s 90年代由尼桑公司创造
Montage
Chaine Validation
Elect.
QV2
QV1
V2
V1
Objectif 6 MR
Decision to launch QRQC at Faurecia 决定在佛吉亚启动QRQC
2005 target : QRQC launched in all Faurecia sites worldwide 2005年目标:在全球的所有佛吉亚工厂启用QRQC
LINE /GAP QRQC
1. Problem N°问题编号, Who谁, When何时 2. Problem description 问题描述 3. Causes identified 原因识别 4. Action decided 行动计划的确定 5. Champion / Responsible 支持者及负责人 6. Date committed 忠于承诺的期限 7. Check 检查
2 different approaches to tackle an issue 2种不同的方法去解决一个问题
1. A first approach to problem solving 第一个解决问题的方法
• Key points关键点 • Assess efficiency + speed评估效率和速度
- 1、下载文档前请自行甄别文档内容的完整性,平台不提供额外的编辑、内容补充、找答案等附加服务。
- 2、"仅部分预览"的文档,不可在线预览部分如存在完整性等问题,可反馈申请退款(可完整预览的文档不适用该条件!)。
- 3、如文档侵犯您的权益,请联系客服反馈,我们会尽快为您处理(人工客服工作时间:9:00-18:30)。
QRQC快速反应质量控制程序
1.0目的
对公司、生产部门及生产车间内部或外部所遇到的品质问题、生产异常、安全事故、纠正事项、内外审核不符合项等作出快速反应并制定纠正与预防方案,使存在问题得到快速、正确解决,促进生产工作的顺利进行。
特制本管理办法。
2.0适应范围
本管理办法适用于发现问题、收集信息、分析原因和确认改进的QRQC会议管理。
3.0职责
3.1品管部经理负责公司范围的QRQC会议的组织召开,并负责对会议内容组织检查督导;
3.2生产部经理负责生产部的QRQC会议的组织召开,并负责对会议内容组织检查督导;
3.3 其他与会人员负责对相应工作区域内存在问题及时反馈到QRQC会议中,负责对QRQC会议中所制定的纠正与预防措施的实施与维持和及时反馈结果;
3.4指定人员负责QRQC会议现场布置,负责会议记录及会议签到存档等。
4.0 内容
4.1 QRQC要求简要
4.1.1准备工作:
4.1.1.1 让我们了解我们的现状和不足;
4.1.1.2 让我们改变思路;
4.1.1.3 指定人员负责QRQC会议现场布置;
4.1.1.4 指定人员负责收集当天需要审查的问题;
4.1.1.5 将当天问题提前书写在QRQC现场记录板上;
4.1.1.6会议前先在《会议培训签到表》上签到。
4.1.2会议时间:
4.1.2.1公司QRQC会议,原则上每周五晚上19:00(特殊情况另行安排,以临时通知为准);
4.1.2.2生产部QRQC会议,根据实际情况而定(凡发生重大品质事故时,必须及时召开)。
4.1.3会议地点:
4.1.3.1公司QRQC会议:办公楼二楼会议室;
4.1.3.2生产部QRQC会议:生产部作业现场。
4.1.4参加人员:
4.1.4.1公司QRQC会议:副总经理、人事行政部经理、技术部经理、品管部经理、生产部经理、车间主管、班组长、质检员、工程师、技术员、代理或指定人员;必要时,通知营销部与采购部派人参加。
4.1.4.2生产部QRQC会议:生产经理、车间主管,班组长、质检员、工程师、技术员。
4.1.5 QRQC领导:
4.1.
5.1公司QRQC领导:品管部经理主持;
4.1.
5.2生产部:生产部经理;
4.1.6会议内容:
4.1.6.1审查、跟进昨天的行动影响效果;
4.1.6.2审查公司、生产出现的若干个最主要的问题;
4.1.6.3提出改进措施与解决方案。
4.1.7实施做法:
得到公司客户投诉、品质异常、安全事故与内外审核不符合项;
4.1.7.2车间及班组质量准确的数据;
4.1.7.3得到车间及班组生产量的数据;
4.1.7.4确定行动规则;
4.1.7.5安排主要问题的任务分配;
4.1.7.6责任人对主要问题的回复;
4.1.7.7确认改善知识予系统的共享。
4.1.8会议签到:
4.1.8.1QRQC会议现场挂有《会议培训签到表》;
4.1.8.2每次会议前,所有参加人员均需在《会议培训签到表》上签名。
4.1.9管理条例:
会议人员迟到、早退每次扣5元教育金,缺席每次扣10元教育金,并及时公布。
4.2 QRQC内容须知简要
4.2.1 QRQC:
快速反应质量控制(Quick Response Quality Control);QRQC不是一个工具/体系,它是一种在每个领域(工厂、项目、供应商)都可以运用的质量文化;4.2.2 PDCA:
Plan( 计划):制定问题解决方案;DO(实施)严格按解决方案实施;Check(检查):及时检查实施结果;Actiong(总结)总结归纳并标准化;PDCA 不是工具,是
随处都可
运用的工作方法;
4.2.3 三现主义:
现场(Genba)是指到生产第一线去发现问题产生的根源,问题发生时,及时赶到现场;
现物(Genbutau):参考不好的零件及其处理方法,合格与不合格的产品都要得到;
现实(Genjitsu):是指现实,而不是理想化,得到真实的数据;
我们将按照San Gen Shugi(三现主义)来改变我们的文化。
4.2.4 FTA:因素树分析(Factor Tree Anaiysis)
4.2.5 4M1E: 问题因素归类为:材料(Material)、方法(Method)、人员(Man)、机器
(Machine)和环境(Environment)五大类;
4.2.6 QRQC的目的:为了改善现状、快速反应和PDCA的效果;
4.2.7 QRQC的基础:必须基于“三现主义(San Gen Shugi)”;
4.2.8 采用5W + 2H方法了解和描述发生的质量事故(问题);
What:问题是什么?
Why: 问题会产生什么影响?
When: 何时发现的?(日期、时间、频次)
Who: 谁发现的?(客户、内部)
Where:哪里发现的?(客户、内部)
How: 何时发现的?。