亚铁离子对磷化膜质量影响的研究
磷化质量影响因素及其提高途径

磷化质量影响因素及其提高途径引言磷化是一种化学与电化学反应形成磷酸盐化学转化膜的过程。
早在1869年W. A. Ross 就申请了磷化专利技术 [ 2 ] ,随着科技的不断进步,金属磷化处理作为传统的表面处理技术在金属防护、减磨耐磨及涂层打底等方面得到广泛的发展和应用。
磷化处理有多种分类方法:按成膜体系可分为锌系、锌锰系、锰系、铁系、锌钙系及非晶相铁系等六大类;按磷化处理温度可分为常温(不加温)、低温(30~45℃)、中温(60~70℃)、高温(大于80℃)四类;按材质可分为钢铁件、铝件、锌件以及混合件磷化;其它的还有按磷化膜厚度或促进剂类型等分类。
用于防锈磷化的主要有铁系磷化、锌系磷化、锰系磷化三种;用于耐磨减磨磷化的种类有锌系磷化和锰系磷化;而锌锰系和锌钙系主要用于漆前磷化。
一磷化基本原理磷化成膜是一个化学动态平衡,目前,大多数学者认同的磷化原理由以下四个步骤组成:首先是金属的溶解过程。
当金属浸入磷化液中时,先与磷化液中的磷酸作用,生成一代磷酸铁,并有大量的氢气析出。
其化学反应为;Fe –2e→Fe2+2H+ + 2e→H2上式表明,磷化开始时,仅有金属的溶解,而无膜生成。
第二是促进剂加速形成磷化膜。
其化学反应式为:[O]+[H] → [R]+H2OFe2++[O] → Fe3++[R]式中[O]为促进剂(氧化剂),[R]为还原产物,由于促进剂氧化掉第一步反应所产生的氢原子,加快了反应(1)的速度,进一步导致金属表面H+浓度急剧下降。
同时也将溶液中的Fe2+氧化成为Fe3+。
第三是磷酸根的多级离解。
H3PO4→H2PO4-+H+→HPO42-+2H+→PO43-+3H+由于金属表面的H+浓度急剧下降,导致磷酸根各级离解平衡向右移动,最终离解为PO43-。
最后磷酸盐沉淀结晶成为磷化膜当金属表面离解出的PO43-与溶液中(金属界面)的金属离子(如Zn2+、Mn2+、Ca2+、Fe2+)达到溶度积常数Ksp时,就会形成磷酸盐沉淀Zn2++ Fe2++ PO43-+H2O→Zn2Fe(PO4)2·4H2O↓ (4)3Zn2++2PO43-+4H2O=Zn3(PO4)2·4H2O↓ (5)磷酸盐沉淀与水分子一起形成磷化晶核,晶核继续长大成为磷化晶粒,无数个晶粒紧密堆集形而上学成磷化膜。
磷化处理常见质量问题及排除方法

磷化处理常见质量问题及排除方法
质量问题
产生原因
排除方法
磷化膜结晶粗糙多孔
1、游离酸含量多
1、调整游离酸
2、硝酸根不足 2、补充硝酸根含量
3、工件表面有残酸 3、加强中和和清洗
4、亚铁离子含量过高 4、用促进剂调整
5、工件表面过腐蚀 5、控制酸浓度和腐蚀时间 膜层过薄、
无明显结
晶
1、酸总量过高
1、加水稀释或磷酸盐调整酸比
2、工件表面有硬化层
2、进行喷砂或强酸腐蚀
3、亚铁离子过低
3、补充磷酸二氢铁
4、温度过低
4、升温至规定温度 磷化膜耐蚀性差、生锈
1、磷化晶粒过粗或过细
1、调整酸比
2、游离酸含量过高 2、降低游离酸含量
3、基体金属被腐蚀
3、控制酸浓度和腐蚀时间
4、溶液中磷酸盐含量不足 4、补充磷酸盐含量
5、工件表面有残酸 5、加强中和及清洗 磷化膜有
白色沉淀
1、溶液中沉淀物过多
1、找出原因,排除沉淀
2、硝酸根不足
2、补充硝酸根含量
3、锌、铁、五氧化二磷含量过高
3、降低锌、铁、五氧化二磷的含量 磷化膜不1、工件表面有硬化层
1、进行喷砂或强酸腐蚀
易形成2、硫酸根含量高2、用钡盐处理
3、溶液中有杂质3、排除杂质或更换槽液
4、五氧化二磷含量低4、补充磷酸盐
磷化膜不均匀、发花1、脱脂不净1、加强脱脂
2、工件部分表面处于钝化状态2、加强喷砂或酸洗
3、工件热处理方法不对3、改进热处理方法
冷挤压后磷化膜产生条状脱
落1、肥皂填充液中有杂质1、清理溶液
2、皂化前工件表面有杂质和沉淀物2、重新磷化。
影响金属磷化膜效果的因素
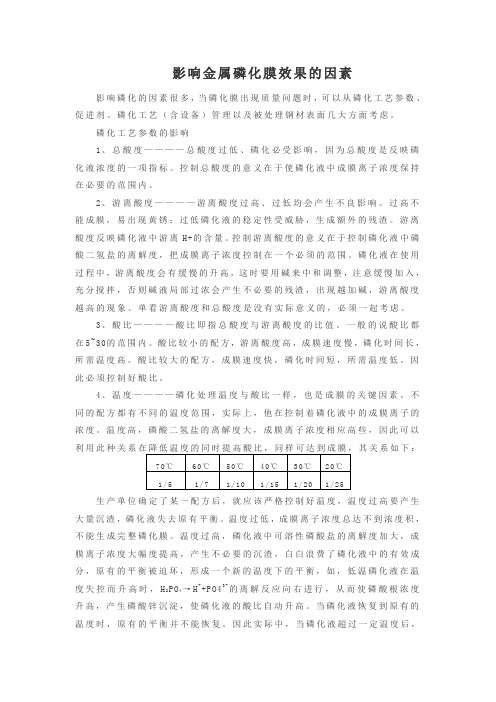
影响金属磷化膜效果的因素影响磷化的因素很多,当磷化膜出现质量问题时,可以从磷化工艺参数、促进剂、磷化工艺(含设备)管理以及被处理钢材表面几大方面考虑。
磷化工艺参数的影响1、总酸度————总酸度过低、磷化必受影响,因为总酸度是反映磷化液浓度的一项指标。
控制总酸度的意义在于使磷化液中成膜离子浓度保持在必要的范围内。
2、游离酸度————游离酸度过高、过低均会产生不良影响。
过高不能成膜,易出现黄锈;过低磷化液的稳定性受威胁,生成额外的残渣。
游离酸度反映磷化液中游离H+的含量。
控制游离酸度的意义在于控制磷化液中磷酸二氢盐的离解度,把成膜离子浓度控制在一个必须的范围。
磷化液在使用过程中,游离酸度会有缓慢的升高,这时要用碱来中和调整,注意缓慢加入,充分搅拌,否则碱液局部过浓会产生不必要的残渣,出现越加碱,游离酸度越高的现象。
单看游离酸度和总酸度是没有实际意义的,必须一起考虑。
3、酸比————酸比即指总酸度与游离酸度的比值。
一般的说酸比都在5~30的范围内。
酸比较小的配方,游离酸度高,成膜速度慢,磷化时间长,所需温度高。
酸比较大的配方,成膜速度快,磷化时间短,所需温度低。
因此必须控制好酸比。
4、温度————磷化处理温度与酸比一样,也是成膜的关键因素。
不同的配方都有不同的温度范围,实际上,他在控制着磷化液中的成膜离子的浓度。
温度高,磷酸二氢盐的离解度大,成膜离子浓度相应高些,因此可以利用此种关系在降低温度的同时提高酸比,同样可达到成膜,其关系如下:70℃60℃50℃40℃30℃20℃1/5 1/7 1/10 1/15 1/20 1/25生产单位确定了某一配方后,就应该严格控制好温度,温度过高要产生大量沉渣,磷化液失去原有平衡。
温度过低,成膜离子浓度总达不到浓度积,不能生成完整磷化膜。
温度过高,磷化液中可溶性磷酸盐的离解度加大,成膜离子浓度大幅度提高,产生不必要的沉渣,白白浪费了磷化液中的有效成分,原有的平衡被迫坏,形成一个新的温度下的平衡,如,低温磷化液在温度失控而升高时,H2PO4→H++PO43-的离解反应向右进行,从而使磷酸根浓度升高,产生磷酸锌沉淀,使磷化液的酸比自动升高。
常见的磷化质量问题及解决方法
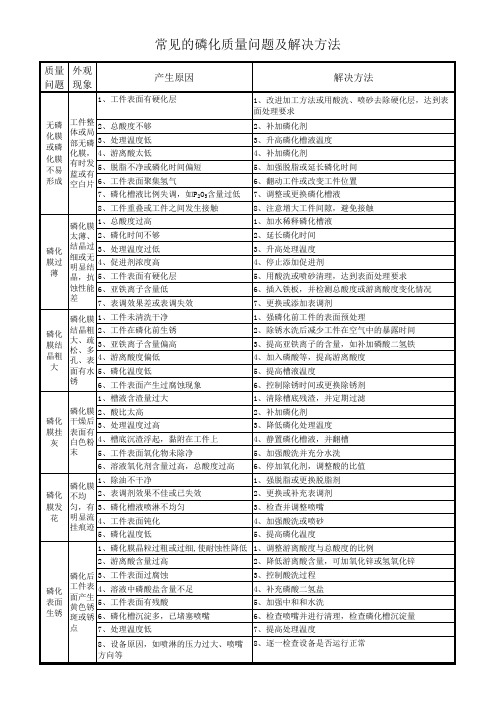
质量 外观 问题 现象 产生原因
1、工件表面有硬化层 无磷 化膜 或磷 化膜 不易 形成 工件整 体或局 部无磷 化膜, 有时发 蓝或有 空白片 2、总酸度不够 3、处理温度低 4、游离酸太低 5、脱脂不净或磷化时间偏短 6、工件表面聚集氢气 7、磷化槽液比例失调,如P2O5含量过低 8、工件重叠或工件之间发生接触 磷化膜 太薄、 结晶过 磷化 细或无 膜过 明显结 薄 晶,抗 蚀性能 差 磷化膜 磷化 结晶粗 大、疏 膜结 松、多 晶粗 孔、表 大 面有水 锈 1、总酸度过高 2、磷化时间不够 3、处理温度过低 4、促进剂浓度高 5、工件表面有硬化层 6、亚铁离子含量低 7、表调效果差或表调失效 1、工件未清洗干净 2、工件在磷化前生锈 3、亚铁离子含量偏高 4、游离酸度偏低 5、磷化温度低 6、工件表面产生过腐蚀现象 1、槽液含渣量过大 磷化膜 2、酸比太高 磷化 干燥后 3、处理温度过高 膜挂 表面有 灰 白色粉 4、槽底沉渣浮起,黏附在工件上 5、工件表面氧化物未除净 末 6、溶液氧化剂含量过高,总酸度过高 1、除油不干净 磷化膜 磷化 不均 2、表调剂效果不佳或已失效 膜发 匀,有 3、磷化槽液喷淋不均匀 花 明显流 4、工件表面钝化 挂痕迹 5、磷化温度低 2、游离酸含量过高 磷化后 工件表 磷化 面产生 表面 黄色锈 生锈 斑或锈 点 3、工件表面过腐蚀 4、溶液中磷酸盐含量不足 5、工件表面有残酸 6、磷化槽沉淀多,已堵塞喷嘴 7、处理温度低 8、设备原因,如喷淋的压力过大、喷嘴 方向等
1、补加表调剂,或重新配槽 2、补加AC-131 3、检查喷嘴 4、调整链速 5、换板材
质 量外 观 问 题现 象
产生原因
解决方法
1、注意不用铜挂具,用铁屑置换除去或用硫化处理, 调整酸度 2、加强酸洗过程的质量控制 1、停加促进剂 2、充分搅拌,使之均匀 3、补加脱脂剂
磷化溶液中离子浓度对磷化液的影响

磷化槽中的离子浓度对液体的影响分析分析离子浓度对磷化液的影响,是关系到磷化膜质量的好坏,也关系到后续工艺中电泳成膜的影响。
在整个电泳工艺中,每一个步骤处理的好坏都关系到电泳质量的好坏,有时候为了避免由于电泳质量差带来的问题,对每个步骤的分析处理都显得很有必要。
下面我们就来说说在磷化槽中离子的浓度对磷化液有何影响。
磷化液中有铁离子、锰离子、锌离子、酸根离子等等。
(1)Fe2+离子,在常温和中温磷化液中保持一定数量的Fe2+离子,能提高磷化膜厚度和抗蚀性能。
但Fe2+离子易被氧化成Fe3+而沉淀。
当它转变成磷酸高铁,溶液呈乳白色时,磷化膜几乎不能生成,膜的质量恶化。
Fe2+离子含量过高,会使磷化膜晶粒粗大表面白色浮灰,耐蚀性和耐热性能降低。
一般中常温磷化中Fe2+离子宜控制在NaH0.5~2.5g/L之间。
过多的Fe2+离子可用H2O2除去,每降低1gFe2+约需加30﹪H2O21mL和ZnO0.5g.在高温磷化液中,Fe2+很不稳定,易氧化成Fe3+离子,并转变为Fe(PO4)3沉淀,使磷化液变浑浊游离酸度升高,需过滤和调整溶液成分后才能使用。
(2)Mn2+离子Mn2+能提高磷化膜硬度结合力和耐蚀性,并能使膜层结晶均匀呈深灰色,但在常温和中温磷化液中Mn2+离子含量不宜过高,否则磷化膜不易生成。
(3)Zn2+离子Zn2+离子可加快磷化速度,使膜层致密,闪烁有光。
Zn2+离子含量过高时使膜层晶粒粗大、脆弱、表面呈灰白色。
Zn2+离子含量过低时,膜层疏松且发暗。
内容不够完整,我来补充下:(1)No3-离子No3-离子可加快磷化速度,降低磷化槽液工作温度。
在适当条件下它与Fe作用生成少量No-,促使Fe2+离子稳定,No3-离子是常、中温磷化液的重要组成部分,但含量过高就会使磷化膜层粗而薄,易出现黄点或白点。
(2)No2-离子能大大提高常温磷化液的磷化速度,促使磷化膜结晶细致,减少孔隙,提高抗蚀性。
含量过多时,膜层易出现白点。
磷化溶液成分对磷化膜层质量的影响

磷化溶液成分对磷化膜层质量的影响成分作用与影响锌离子可加快磷化速度能,磷化膜致密,含锌盐的磷化溶液允许较宽的范围。
锌离子含量低时,磷化膜疏松发暗。
锌离子高时(特别是氟离子和五氧化二磷较高时),磷化膜脆,晶粒粗大锰离子可提高磷化膜的硬度、附着力和耐蚀性,并能使磷化膜的颜色加深,结晶均匀。
但中温和常温磷化溶液中锰离子含量过高时,磷化膜不易生成铁离子在高温磷化溶液中亚铁离子很不稳定,容易被氧化成三价铁离子并转化成磷化铁而沉淀,使磷化溶液浑浊,游离酸度升高。
在常温和中温磷化液中,保持一定数量的亚铁离子,能大大提高磷化层的厚度、机械强度和防护能力,工作范围较宽。
但当亚铁离子转化为三价铁离子并以磷酸铁沉淀出来时,磷化结晶不能生成,磷化膜的质量差。
当亚铁离子含量含量过高时,会使中温磷化膜结晶粗大,表面有灰白浮灰,防护能力降低,膜的耐热性下降。
五氧化二磷能加快磷化速度,磷化膜致密。
其主要来源于磷酸二氢盐,含量低时,磷化膜致密性和耐蚀性均差,甚至磷化不上。
含量高时,磷化膜结晶排列紊乱,附着力下降,工件表面灰白色浮灰较多硝酸根离子可加快磷化速度,提高磷化膜的致密性。
可在降低磷化溶液温度的条件下进行磷化处理。
在适当条件下,硝酸根与钢铁作用生成少量一氧化氮,有利于亚铁离子的稳定,因此他是磷化溶液中(特别是中温和常温)的一个重要成分。
硝酸根含量过高,会使高温磷化膜变薄;使中温磷化液中亚铁离子集聚过多;使常温磷化膜易出现黄色锈迹氟离子可加快磷化结晶核的生成速度,使结晶致密,耐蚀性增强。
在常温磷化溶液中其重要性尤为突出。
氟离子过多,使中温磷化工件表面易出现白色浮灰;使常温磷化溶液的寿命缩短亚硝酸根离子亚硝酸根在常温磷化溶液中可大大加快磷化速度,并能减少磷化膜的空隙,使结晶细致,提高膜的耐蚀性。
含量过高,磷化膜表面易出现白点项目高温磷化中温磷化低温磷化溶液操作温度(℃)90~98 50~70 室温。
关于磷化工序的浅解

关于钢丝〔盘条〕磷化的浅解1.0磷化的目的和基本原理:1.1钢丝表面涂着物的特性:钢丝的加工和使用,要求材料在保存或加工过程和加工结束后的一定时间段内,材料表面不产生锈蚀或表面涂着物不产生潮解;在加工过程中得到低的摩擦系数。
钢丝因再加工和使用的需要,钢丝表面选择的涂着物有:涂石灰、涂硼砂或其类似物、电镀金属、磷化等。
电镀金属仅是在一些特殊产品的要求而使用。
涂石灰是早期钢丝生产工艺中广泛使用的方式,它成本低;但是这种方式在再加工时产生粉尘有害健康且不适应高速拉拔。
涂硼砂是适用于高速拉拔且成本低廉的方式。
虽然它易于潮解,但对涂后的中间品有适当的管理措施是可以避免的。
且特别在涂后直接拉拔的工艺是被广泛选用。
目前国外虽开始限制使用硼砂产品,因此出现其类似物。
但是这种涂层只适用于中间产品的表面而不适用于最终产品的表面;因为它抗锈蚀能力差,但强于石灰涂层。
磷化的涂着层具有一定的抗锈蚀能力,和具有一定的电抗;在后加工过程中得到低的摩擦系数。
好的磷化膜本身具有很好的塑性,在变形中能够很好地保持其连续性;同时,它不仅能和皂——硬脂酸钠,发生反应产生更有利于润滑的金属皂类,而且其表面又可以很好地附着皂液和润滑剂;这有利减小变形摩擦因数、减少模具磨损。
1.2 磷化膜的形成和特性:1.2.1 磷化技术的机理:磷化处理过程是化学与电化学反应过程,主要是由下述步骤组成:a.酸的浸蚀使基体金属表面 H+ 离子浓度降低。
当金属表面与酸性磷化液接触时,钢丝表面被溶解,使金属与溶液中酸反应产生氢,从而使界面的 PH 值上升,以致磷酸锌〔以锌系为例〕沉积于钢丝表面。
由于亚铁在溶液中的存在,不论因酸后的带入还是在槽内反应产生,磷酸铁锌也同时沉积于钢丝表面。
其总反应方程如下:5Zn(H2P04)2+Fe(H2P04)2+8H20--+ Zn 3(P04)2。
4H20+ Zn 2Fe(P04)2。
4H20+ 8 H3P04磷酸盐沉淀的副反应将形成磷化沉渣,即亚铁离子被氧化后同磷酸反应生成磷酸铁在溶液中沉淀:Fe³¯+ P04³¯==FeP04但是在这钢丝表面的二种磷膜沉积物有不同的特性;称前者Zn 3(P04)2。
影响磷化膜质量的因素

影响磷化膜质量的因素1、前言现代工业的迅速发展,市场对涂装要求急剧增加,涂装行业将会得到更快的发展,而涂装质量的好坏在一定程度取决于涂装前处理技术的高低,而磷化又是涂装前处理的关键,磷化膜的性能好坏直接关系到涂装质量的优劣,因此我们需要详细地了解影响磷化膜质量的因素。
2、影响磷化膜质量的因素2.1. 总酸度(TA)TA是反映磷化槽浓度的一项指标,是指槽液中配合酸(HSO42-)和FA浓度的总和。
控制TA的目的在于保持磷化槽液中成膜离子的浓度在规定的工艺范围内。
TA过高,磷化膜生成困难,磷化膜结晶粗燥,耐腐蚀性差。
2.2 游离酸度(FA)FA是指槽液中游离酸度H+浓度。
FA促使工件溶解产生晶核,使生成磷化膜容易。
控制FA的目的在于控制槽液中磷酸二氢盐的离解度,把成膜离子浓度控制在一个必须范围内。
FA过高,反映加快。
工件与槽液界面的离子浓度被破坏,届面PH值过低,造成成膜困难,成膜时间延长,结晶粗大多孔。
耐腐蚀性低。
FA过低,工件腐蚀缓慢,界面PH值升高,磷化膜薄甚至难以形成,膜成表面易产生浮粉(Zn(PO4) 2沉淀),磷化液易产生异常沉淀,导致Zn2+含量急剧降低。
2.3. 磷化温度磷化温度是形成磷化膜的一个关键因素,适当的提高温度不仅可以激活能量低的点形成“活化中心”使晶核数目增多,结晶速度提高,成膜速度加快,同时可以在枝晶上产生新的结晶,结晶密度提高,形成完整结晶的磷化膜,但温度过高,反映速度太快,膜层晶核粗大,孔隙较大,槽液稳定性差,易浑浊,形成含渣的超重灰磷化膜,耐腐蚀性低。
当温度过低,由于磷化是吸热反应,当所需的热量得不到足够补偿时,成膜速度缓慢,甚至磷化反映难以进行,在家和摩配行业磷化中,多以低温和常温磷化磷化为主。
由于温度低,反映相应减慢,因此必须通过其他途径来调节槽液的酸比,促进剂含量,浓度来补偿温度低而对磷化速度的影响,为满足批量生产,加你最好采用低温磷化为宜。
2.4. 磷化时间不同的磷化液,具有不同的磷化时间要求,随着磷化时间的不同,所获得磷化膜的外观,厚度,耐腐蚀性也不同,磷化时间与膜重不成线形关系,根据不同的板材来确定磷化时间,以获得理想的确凿磷化膜。
常见磷化质量问题及解决方法

常见磷化质量问题及解决方法深圳雷邦磷化液编辑摘要:磷化生产中经常会遇到一些质量问题,现将一些常见的问题和产生的原因及解决方法总结归纳。
序号质量外观外观现象产生原因解决方法1 无磷化膜或磷化膜不易形成工件整体或局部无磷化膜,有时发蓝或有空白片1.工件表面有硬化层2.总酸度不够3.处理温度低4.游离酸太低5.脱脂不净或磷化时间偏短6.工件表面聚齐氢气7.磷化槽液比例失调,如P2O5含量过低8.工件重叠或工件之间发生接触1.改进加工方法或用酸洗、喷砂去除硬化层,达到表面处理要求2.补加磷化剂3.升高磷化槽液温度。
4.补加磷化剂5.加强脱脂或延长磷化时间6.翻动工件或改变工件位置7.调整或更换磷化槽液8.注意增大工件间间隙,避免接触2 磷化膜过薄磷化膜太薄,结晶过细或无明显结晶,抗蚀性能差1.总酸度过高2.磷化时间不够3.处理温度过低4.促进剂浓度高5.工件表面有硬化层6.亚铁离子含量低7.表调效果差或表调失效1.加水稀释磷化槽液2.延长磷化时间3.升高处理温度4.停止添加促进剂5.用酸洗或喷砂清理,达到表面处理要求6.插入铁板,并检测总酸度或游离酸度变化情况7.更换或添加表调剂3 磷化膜结晶粗大磷化膜结晶粗大、疏松、多孔、表面有水锈1.工件未清洗干净2.工件在磷化前生锈3.亚铁离子含量偏低4.游离酸度偏低5.磷化温度低6.工件表面产生过腐蚀现象1.强磷化前工件的表面预处理2.除锈水洗后减少工件在空气中的暴露时间3.提高亚铁离子的含量,如补充磷酸二氢铁4.加入磷酸等,提高游离酸度5.提高槽液温度6.控制除锈时间或更换除锈剂4 磷化膜挂灰磷化膜干燥后表面有白色粉末1.槽液含渣量过大2.酸比太高3.处理温度过高4.槽液沉渣浮起,黏附在工件上5.工件表面氧化物未除净6.溶液氧化剂含量过高,总酸度过高1.清除槽底残渣,并定期过滤2.补加磷化剂3.降低磷化处理温度4.静置磷化槽液,并翻槽5.加强酸洗并充分水洗6.停加氧化剂,调整酸的比值5 磷化膜发花磷化膜不均1.除油不干净2.表调剂效果不佳或已失效1.强脱脂或更换脱脂剂2.更换或补充表调剂匀,有明显流挂痕迹3.磷化槽液喷淋不均匀4.工件表面钝化5.磷化温度低3.检查并调整喷嘴4.加强酸洗或喷砂5.提高磷化温度6 磷化膜发黑局部呈黑条状,膜黑且粗糙1.促进剂浓度太低2.酸洗过度1.加促进剂2.控制酸洗时间7 磷化表面生锈磷化后工件表面产生黄色锈斑或锈点1.磷化膜晶粒过粗或过细,使耐蚀性降低2.游离酸含量过高3.工件表面过过腐蚀4.溶液中磷酸盐含量不足5.工件表面有残酸6.磷化槽沉淀多,已堵塞喷嘴7.处理温度低8.设备原因,如喷淋的压力过大、喷嘴方向等1.调整游离酸度与总酸度的比例2.降低游离酸含量,可加氧化锌或氢氧化锌3.控制酸洗过程4.补充磷酸二氢盐5.加强中和水洗6.检查喷嘴并进行清理,检查磷化槽沉淀量7.提高处理温度8.逐一检查设备是否运行正常8 磷化膜发红磷化膜红但不是锈1.铜离子渗入磷化液2.酸洗液中的铁渣附着1.注意不用铜挂具,用铁屑置换除去或用硫化处理,调整酸度2.加强酸洗过程的质量控制9 膜呈彩虹花斑用指甲划过无划痕,对光观察呈彩虹色1.促进剂浓度过高2.促进剂分布不均匀3.除油不彻底1.停加促进剂2.充分搅拌,使之均匀3.补加脱脂剂10 磷化槽液变黑磷化槽液变黑浑浊1.槽液温度低于规定温度2.溶液中亚铁离子过量3.总酸度过低1.停止磷化,升高槽液温度至沸点,保持1-2h,并用空气搅拌,直至灰色原色2.氧化剂,如高锰酸钾等3.补充硝酸锌,提高总酸度11 磷化膜发蓝磷化膜部分表面产生紫蓝色彩表调剂的PH值不在工艺范围2.表调与磷化间隔区的水务喷嘴堵塞3.磷化槽液的锌离子含量不足4.磷化槽液的促进剂含量不够1.补加表调剂或补加Na2CO3,以提高PH值2.检查、清扫水务喷嘴3.补加磷化液或硝酸锌4.补加促进剂12 涂膜气泡涂装后,涂膜发生起泡现象1.磷化后水洗不充分2.清洗水被污染3.纯水的水质不好4.吊架或传送带上滴落水1.检查喷嘴或水洗方法2.增加供水量,控制清洗水的电导率在150μS/cm以下3.控制纯水的电导率在5μS/cm以下4.消除这类滴水。
常见磷化和喷塑质量问题及解决方法

②光泽偏高;③光泽上下波动;
④光泽突然降低。
①检查烘烤温度是否偏高,或烘烤时间是否偏长,向粉厂咨询烘烤条件,另可检查粉末的含水率和喷房的温度;
②核定烘烤温度和时间,可与①对照,检查光泽、工件厚度及烘烤条件;③是否直接燃气炉,检查是否有混粉及喷涂环境温度变化。检查烘道及烘箱温度是否稳定;
④检查温度是否失控,检查空压系统、油水分离器工作是否正常,检查是否混入其他粉。
④检查并更换;
⑤联系设备供应商,检查并更换;
⑥检修悬挂链,使之匀速;
⑦检查流化情况,并检修多孔板。
问题点
主要原因
解决措施
7)砂粒
①均匀密集出现;
②呈突起的圆形,数量不多;
③少量砂粒,大小不一;
④工件表面有杂质,有时呈放射状或细长型;
⑤少量黑色颗粒。
①测定膜厚是否符合工艺要求;
②检查粉末质量,是否存在胶化粒子,另检查磷化后工件表面是否干净无杂质;
③粉末带电性差,边缘上粉少;
④粉末熔融粘度太低;
⑤粉末的胶化时间太长。
①喷涂前修理工件边角,使成圆弧形:
②适当提高固化温度(须注意粉末的耐温性是否良好);
③增加电压,缩短喷枪与工件的距离或适当延长对边缘的喷涂时间;
④粉末厂必须修正配方;
⑤粉末厂必须修正配方。
4.静置磷化槽液,并翻槽
5.加强酸洗并充分水洗
6.停加氧化剂,调整酸的比值
5
磷化膜发花
磷化膜不均匀,有明显流挂痕迹
1.除油不干净
2.表调剂效果不佳或已失效
3.磷化槽液喷淋不均匀
4.工件表面钝化
5.磷化温度低
1.强脱脂或更换脱脂剂
2.更换或补充表调剂
3.检查并调整喷嘴
磷化常见问题及处理方法

磷化常见问题及处理方法常见故障原因分析1、磷化膜结晶粗糙多孔:原因:1)游离酸过高。
2)硝酸根不足。
3)零件表面有残酸,加强中和及清洗。
4)Fe2+过高,用双氧水调整。
5)零件表面过腐蚀,控制酸洗浓度和时间。
2、膜层过薄,无明显结晶:原因:1)总酸度过高,加水稀释或加磷酸盐调整酸的比值。
2)零件表面有硬化层,用强酸腐蚀或喷砂处理。
3)亚铁含量过低,补充磷酸二氢铁。
4)温度低。
3、磷化膜耐腐蚀性差和生锈原因:1)磷化晶粒过粗或过细,调整游离酸和总酸度比值。
2)游离酸含量过高。
3)金属过腐蚀。
4)溶液中磷酸盐含量不足。
5)零件表面有残酸。
6)金属表面锈没有出尽。
4、磷化零件表面有白色沉淀:原因:1)溶液中沉淀物过多。
2)硝酸根不足。
3)锌、铁、P2O5含量高。
5、磷化膜不易形成:原因:1)零件表面有加工硬化层2)溶液里SO-2含量高,用钡盐处理。
3)溶液渗入杂质,更换磷化溶液。
4)P2O5含量过低,补充磷酸盐。
6、磷化层不均、发花:原因:1)除油不净、温度太低。
2)零件表面有钝化状态,加强酸洗或喷砂。
3)零件因热处理加工方法不同。
7、冷挤压后磷化膜产生条状脱落:原因:1)肥皂溶液里有杂质。
2)皂化前零件表面有杂质和沉淀物,重新磷化。
8、磷化膜发红抗蚀能力下降:原因:1)酸洗液里铁渣附在表面。
2)铜离子渗入磷化液磷化常见故障及处理方法磷化膜结晶粗大的原因及处理方法原因:①亚铁离子含量过多;②零件表面带有残酸;③溶液里硝酸根不足;④溶液里硫酸根含量增高;⑤零件表面过腐蚀。
处理方法:①用压缩空气搅拌,或用双氧水降低亚铁离子含量,升高温度;②加强中和或水洗;③添加硝酸锌;④用碳酸钡处理硫酸根;⑤控制酸的浓度和时间。
质量问题外观现象产生原因解决方法1、无磷化膜或磷化膜不易形成工件整体或局部无磷化膜,有时发蓝或有空白片(1)工件表面有硬化层;(2)总酸度不够;(3)处理温度低(4)游离酸太低(5)脱脂不净或磷化时间偏短;(6)工件表面聚集氢气;(7)磷化槽液比例失调,如P2O5含量过低;(8)工件重叠或工件之间发生接触方法:(1)改进加工方法或用酸洗、喷砂去除硬化层、达到表面处理要求;(2)补加磷化剂:(3)升高磷化槽液温度;(4)补加磷化剂;(5)加强脱脂或延长磷化时间;(6)翻动工件或改变工件位置;(7)调整或更换磷化槽液;(8)注意增大工件间隙,避免接触2、磷化膜过薄磷化膜太薄、结晶过细或无明显结晶,抗蚀性能差。
汽车涂装磷化成膜影响因素的研究

《装备维修技术》2021年第9期汽车涂装磷化成膜影响因素的研究巩 庆(山西吉利汽车部件有限公司,山西 晋中 030600)摘 要:在我国科技不断进步的背景之下,汽车涂装技术已经逐渐成熟。
对于表面涂装材料来说,磷化成膜形貌特征对整个涂装表面质量起到了决定性作用。
本篇论文将简单阐述汽车涂装磷化成膜影响因素的相关内容。
关键词:汽车涂装;磷化成膜;影响因素当前我国汽车涂装行业发展较为迅速,其中最为主要的工艺手段就是通过磷化成膜的形式进行汽车涂装工作。
经过众多实验得知,磷化后的磷化膜形貌特征随着生产温度的变化而变化,同时表面PH值也影响到整体磷化膜的质量。
要保证整个汽车涂装磷化成膜的质量,需要对加工工厂温度、PH值等综合外部因素进行控制,同时加强内部制度管理,保证涂装作业的高效率进行。
1 影响汽车涂装质量的主要因素1.1涂层材料的影响当前我国汽车行业所采用的涂层漆料,主要属于市场上常见的金属漆。
一般对于金属漆来说,包括丙烯酸、聚酯氨基树脂材料作为基本原料。
在单色漆的喷涂方面,往往会由于化学原料性质的差异,导致在涂抹过程中没有完全利用聚酯氨基树脂的基础特性。
同时,当前常用的混合金属漆,一方面能够提升涂抹本身的装饰性,增加涂膜自身的抗氧化性。
能够保证在强光照射下,汽车漆面不会受到影响。
同时,也在性能方面,有着较大程度上的提高。
底漆主要通过阴极电泳涂料作为基本原料,相对于之前的阳极电泳涂料来说,后者在涂装过程中具有工艺自动化、二次回收率较高等特点,有利于实现可持续发展。
同时从另一方面来说,能够降低了生产成本。
阴极电泳是当前新生产出的水性涂料,使用过程中较为安全,同时对于环境的污染程度较小。
但是在实际生产过程中,需要相关技术工人做好防护工作,防止其中的杂离子、油气等混入涂料当中,从而影响到了涂料本身的质量。
1.2涂料工艺的影响当前我国国内主要生产汽车涂料工厂,主要通过自动化流水线实现汽车喷涂工作。
这个过程是全自动的,不需要人工进行手工操作。
浅谈钢管防腐的磷化处理工艺
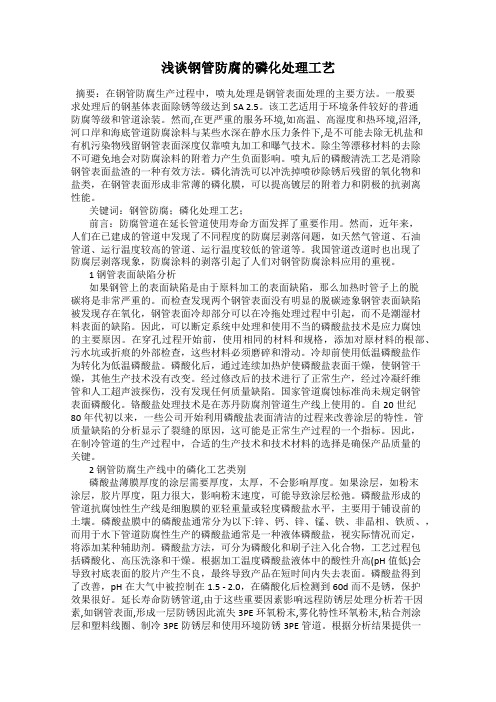
浅谈钢管防腐的磷化处理工艺摘要:在钢管防腐生产过程中,喷丸处理是钢管表面处理的主要方法。
一般要求处理后的钢基体表面除锈等级达到SA 2.5。
该工艺适用于环境条件较好的普通防腐等级和管道涂装。
然而,在更严重的服务环境,如高温、高湿度和热环境,沼泽,河口岸和海底管道防腐涂料与某些水深在静水压力条件下,是不可能去除无机盐和有机污染物残留钢管表面深度仅靠喷丸加工和曝气技术。
除尘等漂移材料的去除不可避免地会对防腐涂料的附着力产生负面影响。
喷丸后的磷酸清洗工艺是消除钢管表面盐渣的一种有效方法。
磷化清洗可以冲洗掉喷砂除锈后残留的氧化物和盐类,在钢管表面形成非常薄的磷化膜,可以提高镀层的附着力和阴极的抗剥离性能。
关键词:钢管防腐;磷化处理工艺;前言:防腐管道在延长管道使用寿命方面发挥了重要作用。
然而,近年来,人们在已建成的管道中发现了不同程度的防腐层剥落问题,如天然气管道、石油管道、运行温度较高的管道、运行温度较低的管道等。
我国管道改道时也出现了防腐层剥落现象,防腐涂料的剥落引起了人们对钢管防腐涂料应用的重视。
1 钢管表面缺陷分析如果钢管上的表面缺陷是由于原料加工的表面缺陷,那么加热时管子上的脱碳将是非常严重的。
而检查发现两个钢管表面没有明显的脱碳迹象钢管表面缺陷被发现存在氧化,钢管表面冷却部分可以在冷拖处理过程中引起,而不是潮湿材料表面的缺陷。
因此,可以断定系统中处理和使用不当的磷酸盐技术是应力腐蚀的主要原因。
在穿孔过程开始前,使用相同的材料和规格,添加对原材料的根部、污水坑或折痕的外部检查,这些材料必须磨碎和滑动。
冷却前使用低温磷酸盐作为转化为低温磷酸盐。
磷酸化后,通过连续加热炉使磷酸盐表面干燥,使钢管干燥,其他生产技术没有改变。
经过修改后的技术进行了正常生产,经过冷凝纤维管和人工超声波探伤,没有发现任何质量缺陷。
国家管道腐蚀标准尚未规定钢管表面磷酸化。
铬酸盐处理技术是在苏丹防腐剂管道生产线上使用的。
自20世纪80年代初以来,一些公司开始利用磷酸盐表面清洁的过程来改善涂层的特性。
磷化成膜机理研究

磷化成膜机理研究磷化成膜机理研究磷化成膜机理比较复杂,至今尚没有统一完整的理论,不同的磷化体系,不同材质的磷化,反应原理不同。
首先,磷化剂在水溶液中发生电离,随温度的升高,离解度增大。
在一定的温度下处于平衡状态。
当金属与磷化液接触时,钢铁受游离酸的侵蚀而发生反应,产生的氢气被溶液中的氧化剂氧化成水,同时部分 Fe2离子也被溶液中的氧化剂氧化成 Fe3Fe3与 PO43-生成FePO4 成为残渣,部分 Fe2参与成膜反应。
这些反应都是发生在金属表面。
由于反应的发生,反应的平衡被打破,平衡向右移动,同时,反应的发生加速了溶液的电离,电离出越来越多的 Zn2和 PO43-使得金属表面附近的 Zn2、PO43-和 Fe2的浓度过饱和,当大于 Zn3PO4 2 或 Zn2FePO4 2 的溶度积时,不溶性的磷酸正盐就沉积在溶液与金属的界面上,由此形成磷化膜。
在生成磷化膜的同时,由于消耗掉 Zn2及 PO43-使得反应平衡继续右移,这样,从 ZnH2PO4 2 中又电离出 2 3-H 、Zn PO4 等离子,溶液又处于新的平衡中。
可以看出,磷化液就是一种缓冲溶液,在生产中,它一直处于一种动态平衡状态中,金属表面的活性点增多,即晶核增多,有利于磷化膜的结晶,这也是表面调整的理论基础。
实际的磷化反应比上面描述的过程复杂得多,因为磷化液中有不同的氧化剂、催化剂、络合剂、促进剂等,还有许多副反应发生,因而就会有沉渣及絮状物的产生,需要定期对槽液进行调整、过滤、沉淀。
磷化成膜机理初探金属溶解反应导致局部阴极区域界面液的酸度下降,从而形成过饱和溶液,在 pH4,5 时,出现磷化液中磷酸盐的起始沉淀点PIP,出现起始沉淀点的 pHZn2比值的升高而提高。
最先形成的不完善的磷酸铁、氧化铁值随溶液中PO43-,混合物组成的钝化膜,也可作为供磷化膜增长的晶核。
由金属表面结构来看,表面存在着供磷化膜生产的―活性中心‖,该活性中心具有一定的能级、数量和表面分布,活性中心的能级决定晶核生成的难易程度,活性中心的数量和表面分布影响到晶核的数量和分布,从而影响磷化膜的粗细和致密性,晶核生成速率随活性中心数量而增加,但主要的制约因素还是活性中心的能级。
磷化液中亚铁离子的测定与控制方法

磷化液中亚铁离子的测定与控制方法1 前言在表面处理过程中,磷化液的亚铁离子浓度范围应控制在1.5~3.0g/L,当溶液中亚铁离子不断升高达到2.5g/L时,磷化膜结晶粗大,膜层性质和性能降低。
溶液中Fe2+和P2O5较高时,磷化膜结晶排列紊乱,脆弱且其白灰较多。
为了确保磷化质量,对磷化液中亚铁离子进行测定是非常必要的。
介绍了快速测定磷化液中亚铁离子含量的2.2'-联吡啶光度法及亚铁离子的控制方法。
2 亚铁离子的测定2.1 原理在pH=4的醋酸-醋酸钠缓冲介质中,二价铁与2,2'-联吡啶生成红色络合物,借此进行亚铁离子含量的测定。
2.2 试剂(1)pH=4醋酸-醋酸钠缓冲溶液取冰醋酸120ml,加无水醋酸钠160g,用水稀释至1L。
(2)1%的2,2'-联吡啶溶液取试剂1g溶于盐酸1ml中,用水稀释至100ml。
(3)2g/L的铁标准溶液准确称取纯铁2g,溶于(1+l)的盐酸中,以水稀释至1L。
2.3 方法在125ml具塞锥形瓶中,加人醋酸-醋酸钠缓冲溶液10ml,2,2'-联吡啶溶液10ml,水30ml,置沸水浴中加热至40℃。
抽取0.3ml试液于锥形瓶中,立即以水作参比,选用S53滤光片、标准减光板(E)1、2cm比色皿,测量吸光度。
标准曲线的绘制取不同量的铁标准溶液于125ml锥形瓶中,加人醋酸-醋酸钠缓冲溶液10ml、2,2'-联吡啶溶液10ml、水30ml,按照同样的方法测量吸光度,绘制标准曲线。
2.4 讨论(1)磷化液中的铁以二价和三价的形式存在,但三价铁很少,只分析二价铁。
(2)在pH=3~9的范围内,2,2’-联吡啶与亚铁离子生成红色络合物。
锌虽然生成络合物,但无色不干扰测定,只是稍微多消耗一些显色剂。
试验表明,在0.3ml试液中,加人2,2’-联吡啶溶液(l%)10ml可发色完全。
(3)温度对磷化液中铁发色略有影响,当温度低于30℃时,1min内发色不完全;当高于30℃时,lmin内能发色完全,且络合物十分稳定。
Fe_2_离子对磷化液的影响
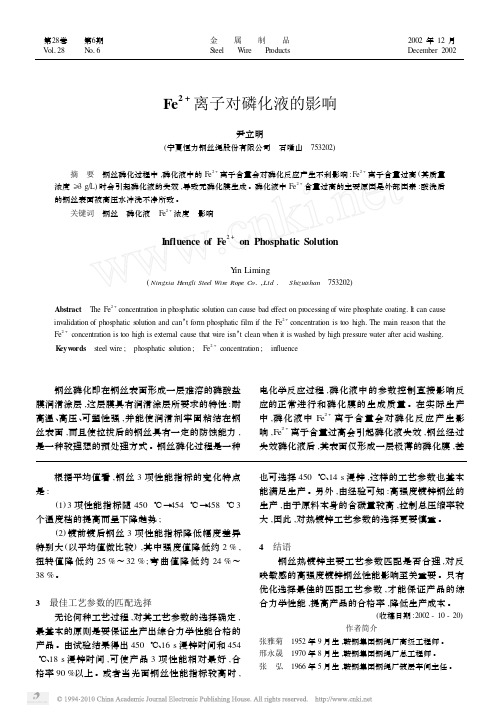
作者简介 张雅菊 1952 年 9 月生 ,鞍钢集团钢绳厂高级工程师 。 邢永晟 1970 年 8 月生 ,鞍钢集团钢绳厂总工程师 。 张 弘 1966 年 5 月生 ,鞍钢集团钢绳厂镀层车间主任 。
・26 ・
金 属 制 品
第 28 卷
至于无磷化膜形成 ,导致钢丝拉拔无法正常运行 ,严 重影响生产效率和产品质量 。
第 28卷 第6期 Vol128 No16
金 属 制 品 Steel Wire Products
2002 年 12 月 December 2002
Fe
2+
离子对磷化液的影响
尹立明
( 宁夏恒力钢丝绳股份有限公司 石嘴山 753202)
摘 要 钢丝磷化过程中 ,磷化液中的 Fe2 + 离子含量会对磷化反应产生不利影响 : Fe2 + 离子含量过高 ( 其质量
4 结语
2+
钢丝热镀锌主要工艺参数匹配是否合理 , 对反 映敏感的高强度镀锌钢丝性能影响至关重要 。只有 优化选择最佳的匹配工艺参数 , 才能保证产品的综 合力学性能 ,提高产品的合格率 ,降低生产成本 。
( 收稿日期 :2002 - 10 - 20)
无论何种工艺过程 ,对其工艺参数的选择确定 , 最基本的原则是要保证生产出综合力学性能合格的 产品 。由试验结果得出 450 ℃、 16 s 浸锌时间和 454 ℃、 18 s 浸锌时间 , 可使产品 3 项性能相对最好 , 合 格率 90 %以上 。或者当光面钢丝性能指标较高时 ,
表2 磷化工艺参数 溶液含量 总酸度/ 滴
30~80
温度/
-1
浸渍时间/
min 5~8
游离酸/ 滴
4~12
磷化液中亚铁离子的快速测定及控制方法

磷化液中亚铁离子的快速测定及控制方法
王秋景
【期刊名称】《材料保护》
【年(卷),期】2001(34)9
【摘要】介绍了过量亚铁离子在磷化液中的危害 ,研究了快速测定磷化中亚铁离子含量的2 ,2′ 联吡啶光度法[1] 及亚铁离子的控制方法。
【总页数】2页(P48-49)
【关键词】磷化液;表面处理;磷化;亚铁离子;2,2′-联吡啶光度法;快速测定
【作者】王秋景
【作者单位】桂林电力电容器总厂技术处
【正文语种】中文
【中图分类】TG178
【相关文献】
1.快速测定铁矿石中氧化亚铁含量的方法 [J], 张爱珍;付冉冉;鲍惠君
2.生产聚铁用添加剂硫酸亚铁中有害重金属离子量的快速测定 [J], 印德俊
3.用离子色谱法测定磷化液中的阴离子 [J], 王亚静;张迪
4.电感耦合等离子体发射光谱法快速测定磷化液中锌、镍、锰元素含量 [J], 杨帆;周瑜;齐杰华;张晓宇;张楠
5.低温磷化液中钙、锌、镍离子的快速测定 [J], 刘永
因版权原因,仅展示原文概要,查看原文内容请购买。
磷化影响因素
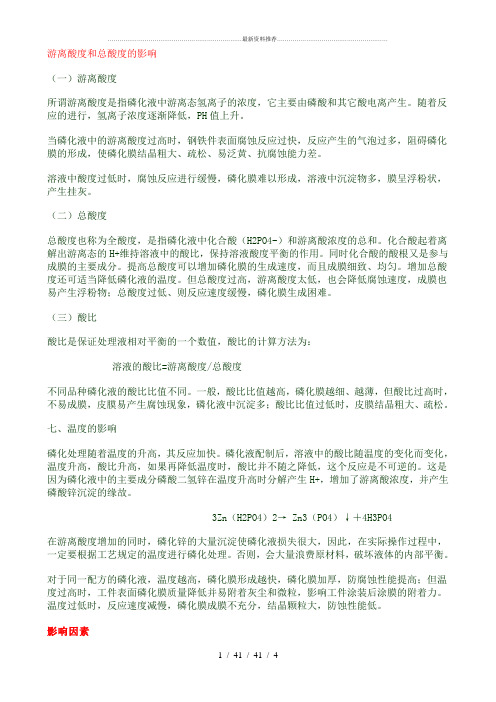
游离酸度和总酸度的影响(一)游离酸度所谓游离酸度是指磷化液中游离态氢离子的浓度,它主要由磷酸和其它酸电离产生。
随着反应的进行,氢离子浓度逐渐降低,PH值上升。
当磷化液中的游离酸度过高时,钢铁件表面腐蚀反应过快,反应产生的气泡过多,阻碍磷化膜的形成,使磷化膜结晶粗大、疏松、易泛黄、抗腐蚀能力差。
溶液中酸度过低时,腐蚀反应进行缓慢,磷化膜难以形成,溶液中沉淀物多,膜呈浮粉状,产生挂灰。
(二)总酸度总酸度也称为全酸度,是指磷化液中化合酸(H2PO4-)和游离酸浓度的总和。
化合酸起着离解出游离态的H+维持溶液中的酸比,保持溶液酸度平衡的作用。
同时化合酸的酸根又是参与成膜的主要成分。
提高总酸度可以增加磷化膜的生成速度,而且成膜细致、均匀。
增加总酸度还可适当降低磷化液的温度。
但总酸度过高,游离酸度太低,也会降低腐蚀速度,成膜也易产生浮粉物;总酸度过低、则反应速度缓慢,磷化膜生成困难。
(三)酸比酸比是保证处理液相对平衡的一个数值,酸比的计算方法为:溶液的酸比=游离酸度/总酸度不同品种磷化液的酸比比值不同。
一般,酸比比值越高,磷化膜越细、越薄,但酸比过高时,不易成膜,皮膜易产生腐蚀现象,磷化液中沉淀多;酸比比值过低时,皮膜结晶粗大、疏松。
七、温度的影响磷化处理随着温度的升高,其反应加快。
磷化液配制后,溶液中的酸比随温度的变化而变化,温度升高,酸比升高,如果再降低温度时,酸比并不随之降低,这个反应是不可逆的。
这是因为磷化液中的主要成分磷酸二氢锌在温度升高时分解产生H+,增加了游离酸浓度,并产生磷酸锌沉淀的缘故。
3Zn(H2PO4)2→ Zn3(PO4)↓+4H3PO4在游离酸度增加的同时,磷化锌的大量沉淀使磷化液损失很大,因此,在实际操作过程中,一定要根据工艺规定的温度进行磷化处理。
否则,会大量浪费原材料,破坏液体的内部平衡。
对于同一配方的磷化液,温度越高,磷化膜形成越快,磷化膜加厚,防腐蚀性能提高;但温度过高时,工件表面磷化膜质量降低并易附着灰尘和微粒,影响工件涂装后涂膜的附着力。