EM488M1644LBB-75F中文资料
迪赛拜金属电压分辨率领导电阻说明书
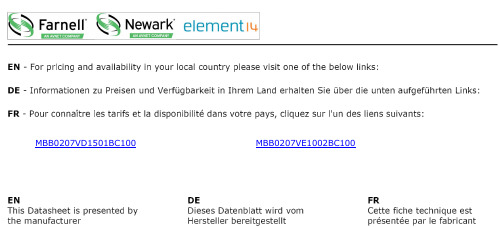
MBB0207VD1501BC100MBB0207VE1002BC100MBA/SMA 0204, MBB/SMA 0207, MBE/SMA 0414 - PrecisionVishay BeyschlagPrecision Metal Film Leaded ResistorsLINKS TO ADDITIONAL RESOURCESDESCRIPTIONMBA/SMA 0204, MBB/SMA 0207, and MBE/SMA 0414 precision leaded thin film resistors combine the proven reliability of the professional products with an advanced level of precision and stability. Therefore they are perfectly suited for applications in the fields of test and measuring equipment along with industrial and medical electronics.FEATURES•IECQ-CECC approved according to EN 140101-806•Superior overall stability: class 0.05•Wide precision ohmic range: 10 Ω to 1.5 M Ω•Radial version available for MBB/SMA 0207•Material categorization: for definitions of compliance please see /doc?99912APPLICATIONS•Test and measuring equipment •Industrial electronics•Medical electronicsNotes•MB_ series has been merged with the related SMA series to form one series “MB_/SMA__”(1)Please refer to APPLICATION INFORMATION below3D 3D3D ModelsTECHNICAL SPECIFICATIONSDESCRIPTION MBA/SMA 0204MBB/SMA 0207MBE/SMA 0414DIN size 020*********CECC size AB DResistance range 22 Ω to 332 k Ω10 Ω to 1 M Ω22 Ω to 1.5 M ΩResistance tolerance ± 0.25 %; ± 0.1 %Temperature coefficient ± 25 ppm/K; ± 15 ppm/KRated dissipation, P 700.25 W 0.40 W 0.65 W Operating voltage, U max. AC RMS /DC 200 V 350 V 500 V Operating temperature range (1)-55 °C to +125 °CPermissible film temperature, ϑF max. (1)125 °CPermissible voltage against ambient (insulation):1 min; U ins 300 V 500 V 800 V Continuous75 V75 V 75 VFailure rate: FIT observed≤ 0.1 x 10-9/hMBA/SMA 0204, MBB/SMA 0207, MBE/SMA 0414 - PrecisionVishay BeyschlagAPPLICATION INFORMATIONThe power dissipation on the resistor generates a temperature rise against the local ambient, depending on the heat flow support of the printed-circuit board (thermal resistance). The rated dissipation applies only if the permitted film temperature is not exceeded. Furthermore, a high level of ambient temperature or of power dissipation may raise the temperature of the solder joint, hence special solder alloys or board materials may be required to maintain the reliability of the assembly.These resistors do not feature a limited lifetime when operated within the permissible limits. However, resistance value drift increasing over operating time may result in exceeding a limit acceptable to the specific application, thereby establishing a functional lifetime. The designer may estimate the performance of the particular resistor application or set certain load and temperature limits in order to maintain a desired stability.Note•The presented operation modes do not refer to different types of resistors, but actually show examples of different loads, that lead to different film temperatures and different achievable load-life stability (drift) of the resistance value. A suitable low thermal resistance of the circuit board assembly must be safeguarded in order to maintain the film temperature of the resistors within the specified limitsNotes•Radial version (RB, UB) cannot be qualified according to CECC so these can only be ordered with variant N or S (1)Approval is according to EN 140101-806, version A, or the approved IECQ-CECC resistance range, please refer to: /doc?28945MAXIMUM RESISTANCE CHANGE AT RATED DISSIPATIONOperation mode PrecisionStandardClimatic category-10 °C / +85 °C / 56 days-55 °C / +125 °C / 56 daysRated dissipation, P 70MBA/SMA 02040.07 W 0.25 W MBB/SMA 02070.11 W 0.40 W MBE/SMA 04140.17 W 0.65 W Permissible film temperature, ϑF max.85 °C 125 °C Max. resistance change at rated dissipation |ΔR /R max.|, after:MBA/SMA 0204100 Ω to 100 k Ω100 Ω to 100 k Ω1000 h ≤ 0.05 %≤ 0.25 %8000 h ≤ 0.1 %≤ 0.5 %225 000 h ≤ 0.3 %≤ 1.5 %MBB/SMA 0207100 Ω to 270 k Ω100 Ω to 270 k Ω1000 h ≤ 0.03 %≤ 0.15 %8000 h ≤ 0.1 %≤ 0.5 %225 000 h ≤ 0.3 %≤ 1.5 %MBE/SMA 0414100 Ω to 470 k Ω100 Ω to 470 k Ω1000 h ≤ 0.05 %≤ 0.2 %8000 h ≤ 0.1 %≤ 0.4 %225 000 h ≤ 0.3 %≤ 1.2 %TEMPERATURE COEFFICIENT AND RESISTANCE RANGE (1)TYPE / SIZETCR TOLERANCE RESISTANCE (2)E-SERIESMBA/SMA 0204± 25 ppm/K± 0.25 % 22 Ω to 332 k ΩE96; E192± 0.1 %43 Ω to 332 k Ω± 15 ppm/K ± 0.25 %22 Ω to 221 k Ω± 0.1 %43 Ω to 221 k ΩMBB/SMA 0207± 25 ppm/K± 0.25 %10 Ω to 1 M Ω± 0.1 %10 Ω to 1 M Ω± 15 ppm/K ± 0.25 %10 Ω to 1 M Ω± 0.1 %10 Ω to 1 M ΩMBE/SMA 0414± 25 ppm/K± 0.25 %22 Ω to 1.5 M Ω± 0.1 %43 Ω to 1 M Ω± 15 ppm/K± 0.25 %22 Ω to 1 M Ω± 0.1 %43 Ω to 1 M ΩMBA/SMA 0204, MBB/SMA 0207, MBE/SMA 0414 - PrecisionVishay BeyschlagNote•For details related to packaging specs, refer datasheet link /doc?28721Note•The products can be ordered using either the PRODUCT DESCRIPTION or the PART NUMBERPACKAGINGTYPE / SIZE CODE QUANTITY PACKAGING STYLE WIDTH PITCH PACKAGING DIMENSIONS MBA/SMA 0204C11000Taped acc. to IEC 60286-1fan-folded in a box 53 mm5 mm184 mm x 75 mm x 42 mmCT 5000330 mm x 75 mm x 55 mm MBB/SMA 0207C11000Taped acc. to IEC 60286-1fan-folded in a box 53 mm5 mm184 mm x 74 mm x 42 mmCT 5000 324 mm x 77 mm x 82 mmMBB/SMA 0207 UB = 2.5 mm pitchN44000Taped acc. to IEC 60286-2fan-folded in a box -12.7 mm330 mm x 262 mm x 45 mm R44000Taped acc. to IEC 60286-2on a reel -330 mm x 253 mm x 48 mmMBB/SMA 0207 RB = 5.0 mm pitchN44000Taped acc. to IEC 60286-2fan-folded in a box -330 mm x 262 mm x 45 mmR44000Taped acc. to IEC 60286-2on a reel -330 mm x 253 mm x 48 mmMBE/SMA 0414C11000Taped acc. to IEC 60286-1fan-folded in a box63 mm 5 mm 374 mm x 84 mm x 47 mmPART NUMBER AND PRODUCT DESCRIPTION - CECC APPROVED PRODUCTSPart Number: MBB0207VD1001BCT00TYPE / SIZEVERSION TCRRESISTANCE TOLERANCE PACKAGINGSPECIALMBA0204 =MBA/SMA 0204MBB0207 =MBB/SMA 0207MBE0414 =MBE/SMA 0414V = CECC 06N = RB radial 5 mm for MBB/SMA 0207S = UB radial 2.5 mm for MBB/SMA 0207E = ± 15 ppm/K D = ± 25 ppm/K3 digit value 1 digit multiplier MULTIPLIER B = ± 0.1 %C = ± 0.25 %CT C1N4R400 = standard L0 = welding joint not lacquered for MBB/SMA 0207KL = lacquered welding joint for MBA/SMA 02049 = *10-1 0 = *100 1 = *1012 = *1023 = *1034 = *104Product Description: MBB/SMA 0207-25 0.1 % CECC 06 CT 1K0MBB/SMA 0207-250.1 %CECC 06CT 1K0TYPE / SIZE TCR TOLERANCE VERSION PACKAGINGRESISTANCE MBA/SMA 0204MBB/SMA 0207MBE/SMA 0414± 15 ppm/K ± 25 ppm/K± 0.1 %± 0.25 %CECC 06CECC 06 L0CECC 06 KLCT C1N4R41K0 = 1 k Ω51R1 = 51.1 ΩB 2V D 10BC T 0BM 701000MBA/SMA 0204, MBB/SMA 0207, MBE/SMA 0414 - Precision Vishay BeyschlagDESCRIPTIONProduction is strictly controlled and follows an extensive set of instructions established for reproducibility. A homogeneous film of metal alloy is deposited on a high grade ceramic body and conditioned to achieve the desired temperature coefficient. Plated steel termination caps are firmly pressed on the metallized rods. A special laser is used to achieve the target value by smoothly cutting a helical groove in the resistive layer without damaging the ceramics. Connecting wires of electrolytic copper plated with 100 % pure matte tin are welded to the termination caps. The resistor elements are covered by a light blue protective coating designed for electrical, mechanical and climatic protection. F our or five color code rings designate the resistance value and tolerance in accordance with IEC 60062.The result of the determined production is verified by an extensive testing procedure performed on 100 % of the individual resistors. Only accepted products are stuck directly on the adhesive tapes in accordance with IEC 60286-1 or for the radial versions in accordance with IEC 60286-2.MATERIALSVishay acknowledges the following systems for the regulation of hazardous substances:•IEC 62474, Material Declaration for Products of and for the Electrotechnical Industry, with the list of declarable substances given therein (1)•The Global Automotive Declarable Substance List (GADSL) (2)•The REACH regulation (1907/2006/EC) and the related list of substances with very high concern (SVHC) (3) for its supply chainThe products do not contain any of the banned substances as per IEC 62474, GADSL, or the SVHC list, see /how/leadfree.Hence the products fully comply with the following directives:•2000/53/EC End-of-Life Vehicle Directive (ELV) and Annex II (ELV II)•2011/65/EU Restriction of the Use of Hazardous Substances Directive (RoHS) with amendment 2015/863/EU•2012/19/EU Waste Electrical and Electronic Equipment Directive (WEEE)Vishay pursues the elimination of conflict minerals from its supply chain, see the Conflict Minerals Policy at /doc?49037.ASSEMBLYThe resistors are suitable for processing on automatic insertion equipment and cutting and bending machines. Excellent solderability is proven, even after extended storage. They are suitable for automatic soldering using wave or dipping.The resistors are completely lead (Pb)-free, the pure matte tin plating provides compatibility with lead (Pb)-free and lead-containing soldering processes. The immunity of the plating against tin whisker growth, in compliance with IEC 60068-2-82, has been proven under extensive testing. The encapsulant is resistant to cleaning solvent specified in IEC 60115-1(3). The suitability of conformal coatings, if applied, shall be qualified by appropriate means to ensure the long-term stability of the whole system.All products comply with GADSL (1) and the IEC 62474 (2) list of legal restrictions on hazardous substances. This includes full compliance with the following directives:•2000/53/EC End of Vehicle Life Directive (ELV) and Annex II (ELVII)•2011/65/EU Restriction of the use of Hazardous Substances Directive (RoHS)•2002/96/EC Waste Electrical and Electrical Equipment Directive (WEEE)APPROVALSThe resistors (CECC version) are approved within the IECQ-CECC Quality Assessment System for Electronic Components to the detail specification EN 140101-806 which refers to EN 60115-1 and EN 60115-2 and the variety of environmental test procedures of the IEC 60068 series. Conformity is attested by the use of the CECC logo () as the Mark of Conformity on the package label for the CECC version.Vishay Beyschlag has achieved “Approval of Manufacturer” in accordance with IECQ 03-3-1, clause 2. The release certificate for “Technology Approval Schedule” in accordance with CECC 240001 based on IECQ 03-3-1, clause 6 is granted for the Vishay Beyschlag manufacturing process.RELATED PRODUCTSF or a corelated range of professional TCR and tolerance specifications see the datasheet:•“Professional Thin F ilm Leaded Resistors”, /doc?28766For products approved to EN 140101-806, version E, with established reliability and failure rate level E7 (Quality factor πQ = 0.1), see the datasheet: •“Established Reliability Thin F ilm Leaded Resistors”, /doc?28768Notes(1)Global Automotive Declarable Substance List, see (2)CEF IC (European Chemical Industry Council), EECA (European Electronic Component Manufacturers Association), EICTA (Europeantrade organization representing the information and communications technology and consumer electronics), see /SearchResults.aspx?Search=eicta.All products comply with the IEC 62474, Material Declaration for Products of and for the Electrotechnical Industry(3)Other cleaning solvents with aggressive chemicals should be evaluated in actual cleaning process for their suitabilityMBA/SMA 0204, MBB/SMA 0207, MBE/SMA 0414 - PrecisionVishay BeyschlagFUNCTIONAL PERFORMANCEDeratingRise of the surface temperature.Temperature RiseCurrent Noise A 1 in accordance with IEC 60195Ambient Temperature in °CP o w e r i n %2004060801000W40K 600.2200.10.30.40.50.60.70.8Load PT e m p e r a t u r e R i s e T r0.010.11100:µV/V1K10K 100K 1M 10M Resistance Value RC u r r e n t N o i s e A 1MBA/SMA 0204, MBB/SMA 0207, MBE/SMA 0414 - Precision Vishay Beyschlag TEST PROCEDURES AND REQUIREMENTSAll tests are carried out in accordance with the following specifications:•IEC 60115-1, generic specification•IEC 60115-2, sectional specification•EN 140101-806, detail specification•IEC 60068-2-xx, test methodsThe components are approved under the IECQ-CECC quality assessment system for electronic components. The parameters stated in the Test Procedures and Requirements table are based on the required tests and permitted limits of EN 140101-806. The table presents only the most important tests, for the full test schedule refer to the documents listed above. However, some additional tests and a number of improvements against those minimum requirements have been included. The testing also covers most of the requirements specified by EIA/ECA-703 and JIS-C-5201-1. The tests are carried out under standard atmospheric conditions in accordance with IEC 60068-1, 4.3, whereupon the following values are applied:•Temperature: 15 °C to 35 °C•Relative humidity: 25 % to 75 %•Air pressure: 86 kPa to 106 kPa (860 mbar to 1060 mbar) A climatic category LCT / UCT / 56 is applied, defined by the lower category temperature (LCT), the upper category temperature (UCT), and the duration of exposure in the damp heat, steady state test (56 days). The components are mounted for testing on printed circuit boards in accordance with IEC 60115-1, 5.5, unless otherwise specified.TEST PROCEDURES AND REQUIREMENTSIEC 60115-1 CLAUSE(3)IEC60068-2TESTMETHOD(3)TESTPROCEDUREREQUIREMENTS PERMISSIBLE CHANGE(ΔR max.)Stability for product types:STABILITYCLASS 0.05STABILITYCLASS 0.1STABILITYCLASS 0.25MBA/SMA 0204100 Ω to 100 kΩ43 Ω to 221 kΩ22 Ω to 332 kΩMBB/SMA 0207100 Ω to 270 kΩ43 Ω to 510 kΩ10 Ω to 1 MΩMBE/SMA 0414100 Ω to 470 kΩ43 Ω to 1 MΩ22 Ω to 1.5 MΩ6.1-Resistance-± 0.25 %; ± 0.1 % 12.2-Voltage proof U RMS = U ins; 60 s No flashover or breakdown6.2-TemperaturecoefficientAt 20/LCT/20 °C and20/UCT/20 °C± 25 ppm/K; ± 15 ppm/K8.1-Short timeoverloadRoom temperature;U = 2.5 x orU = 2 x U max.; 5 s± (0.01 % R + 0.01 Ω)no visible damage± (0.02 % R + 0.01 Ω)no visible damage± (0.05 % R + 0.01 Ω)no visible damage9.521 (Ua1)21 (Ub)21 (Uc)Robustness ofterminationsTensile, bending and torsion± (0.01 % R + 0.01 Ω)± (0.02 % R + 0.01 Ω)± (0.05 % R + 0.01 Ω)11.120 (Ta)Solderability+235 °C; 2 ssolder bath method;SnPb40Good tinning (≥ 95 % covered, no visible damage) +245 °C; 3 ssolder bath method;SnAg3Cu0.511.220 (Tb)Resistance tosoldering heatUnmounted components;(270 ± 3) °C;(10 ± 1) s± (0.01 % R + 0.01 Ω)no visible damage± (0.02 % R + 0.01 Ω)no visible damage± (0.05 % R + 0.01 Ω)no visible damage10.114 (Na)Rapidchange oftemperature30 min at LCT = -55 °C30 min at UCT = 125 °C5 cycles± (0.01 % R + 0.01 Ω)no visible damage± (0.02 % R + 0.01 Ω)no visible damage± (0.05 % R + 0.01 Ω)no visible damage MBA/SMA 0204: 500 cyclesMBB/SMA 0207: 200 cyclesMBE/SMA 0414: 100 cycles± (0.25 % R + 0.05 Ω)no visible damage± (0.25 % R + 0.05 Ω)no visible damage± (0.25 % R + 0.05 Ω)no visible damage9.11 6 (Fc)Vibration 10 sweep cycles per direction;10 Hz to 2000 Hz1.5 mm or 200 m/s2± (0.01 % R + 0.01 Ω)± (0.02 % R + 0.01 Ω)± (0.05 % R + 0.01 Ω) P70 x RMBA/SMA 0204, MBB/SMA 0207, MBE/SMA 0414 - PrecisionVishay BeyschlagNotes(1)± (0.03 % R + 0.01 Ω) for MBB/SMA 0207(2)± (0.15 % R + 0.05 Ω) for MBB/SMA 0207(3)The quoted IEC standards are also released as EN standards with the same number and identical contents10.3Climatic sequence:± (0.05 % R + 0.01 Ω)no visible damage ± (0.1 % R + 0.01 Ω)no visible damage ± (0.25 % R + 0.05 Ω)no visible damage10.3.4.22 (Bb)Dry heat 125 °C; 16 h 10.3.4.330 (Db)Damp heat,cyclic55 °C; 24 h;90 % to 100 % RH;1 cycle10.3.4.4 1 (Ab)Cold -55 °C; 2 h 10.3.4.513 (M)Low air pressure 8.5 kPa; 2 h;15 °C to 35 °C10.3.4.630 (Db)Damp heat,cyclic 55 °C; 5 days;95 % to 100 % RH; 5 cycles 10.3.4.7DC loadApply rated power for 1 min10.478 (Cab)Damp heat,steady state (40 ± 2) °C;56 days;(93 ± 3) % RH± (0.05 % R + 0.01 Ω)± (0.1 % R + 0.01 Ω)± (0.25 % R + 0.05 Ω)7.1-Endurance at 70 °C:Precision operation mode U =orU = U max.;1.5 h on; 0.5 h off70 °C; 1000 h ± (0.05 % R + 0.01 Ω) (1)± (0.1 % R + 0.01 Ω)-70 °C; 8000 h± (0.1 % R + 0.01 Ω)± (0.2 % R + 0.01 Ω)--Endurance at 70 °C:Standard operation mode U =orU = U max.;1.5 h on; 0.5 h off70 °C; 1000 h --± (0.25 % R + 0.05 Ω) (2)70 °C; 8000 h --± (0.5 % R + 0.05 Ω)7.3-Endurance atupper category temperature 85 °C; 1000 h 125 °C; 1000 h -± (0.05 % R + 0.01 Ω)-± (0.1 % R + 0.01 Ω)-± (0.25 % R + 0.05 Ω)11.345 (XA)Component solvent resistance Isopropyl alcohol +23 °C or +50 °C; toothbrush method Marking legible;No visible damage8.5-Electrostatic discharge (human body model)IEC 61340-3-1;3 pos. + 3 neg.MBA/SMA 0204: 2 kV MBB/SMA 0207: 4 kV MBE/SMA 0414: 6 kV± (0.5 % R + 0.05 Ω)TEST PROCEDURES AND REQUIREMENTSIEC60115-1CLAUSE(3)IEC60068-2TESTMETHOD (3)TESTPROCEDUREREQUIREMENTS PERMISSIBLE CHANGE(ΔR max.)Stability for product types:STABILITY CLASS 0.05STABILITY CLASS 0.1STABILITY CLASS 0.25MBA/SMA 0204100 Ω to 100 k Ω43 Ω to 221 k Ω22 Ω to 332 k ΩMBB/SMA 0207100 Ω to 270 k Ω43 Ω to 510 k Ω10 Ω to 1 M ΩMBE/SMA 0414100 Ω to 470 k Ω43 Ω to 1 M Ω22 Ω to 1.5 M ΩP 70 x R P 70 x RMBA/SMA 0204, MBB/SMA 0207, MBE/SMA 0414 - PrecisionVishay BeyschlagDIMENSIONSNote(1)For 7.5 ≤ M < 10.0 mm, use version MBB/SMA 0207... L0 (welding joint not lacquered)MBB/SMA 0207 WITH RADIAL TAPINGLEAD SPACING (UB = 2.5 mm), SIZE 0207LEAD SPACING (RB = 5.0 mm), SIZE 0207DIMENSIONS- Leaded resistor types, mass and relevant physical dimensionsTYPE / SIZE D max.(mm)L max.(mm)d nom.(mm)I min.(mm)M min.(mm)MASS (mg)MBA/SMA 0204 1.6 3.60.529.0 5.0125MBB/SMA 0207(1) 2.5 6.50.628.010.0 (1)220MBE/SMA 04144.211.90.831.015.0700DIMENSIONS in millimetersPitch of components P 12.7 ± 1.0Lead spacingF 2.5 + 0.6 / - 0.1Width of carrier tape W 18.0 + 1.0 / - 0.5Body to hole center H 18.0 ± 2.0Height for cutting (max.)L 11Height for bending C 2.5 + 0 / - 0.5Height for insertion (max.)H132Direction of unreelingDIMENSIONS in millimetersPitch of components P 12.7 ± 1.0Lead spacing F 5.0 + 0.6 / - 0.1Width of carrier tape W 18.0 + 1.0 / - 0.5Body to hole center H 18.0 ± 2.0Lead crimp to hole center H 016.0 ± 0.5Height for cutting (max.)L 11Height for bending C 2.5 + 0 / - 0.5Height for insertion (max.)H 132MBA/SMA 0204, MBB/SMA 0207, MBE/SMA 0414 - PrecisionVishay BeyschlagHISTORICAL 12NC INFORMATION•The resistors had a 12-digit numeric code starting with 2312•The subsequent 4 digits indicated the resistor type, specification and packaging; see the 12NC table •The remaining 4 digits indicated the resistance value:-The first 3 digits indicated the resistance value-The last digit indicated the resistance decade in accordance with resistance decade table shown belowResistance DecadeHistorical 12NC ExampleThe 12NC code of a MBA 0204 resistor, value 47 k Ω and TCR 25 with ± 0.1 % tolerance, supplied on bandolier in a box of 5000 units was: 2312 906 74703.RESISTANCE DECADELAST DIGIT10 Ω to 99.9 Ω9100 Ω to 999 Ω11 k Ω to 9.99 k Ω210 k Ω to 99.9 k Ω3100 k Ω to 999 k Ω41 M Ω to 9.99 M Ω5HISTORICAL 12NC - Resistor type and packagingDESCRIPTION 2312 ... ..... (BANDOLIER)AMMOPACKREEL TYPETCR TOL.C1 1000 UNITSCT 5000 UNITSR1 1000 UNITSR2 2500 UNITSRP 5000 UNITSMBA 0204± 25 ppm/K± 0.25 %901 6....906 6....701 6....-806 6....± 0.1 %901 7....906 7....701 7....-806 7....± 15 ppm/K ± 0.25 %902 6....907 6....702 6....-807 6....± 0.1 %902 7....907 7....702 7....-807 7....MBB 0207± 25 ppm/K± 0.25 %911 6....916 6....711 6....-816 6....± 0.1 %911 7....916 7....711 7....-816 7....± 15 ppm/K ± 0.25 %912 6....917 6....712 6....-817 6....± 0.1 %912 7....917 7....712 7....-817 7....MBE 0414± 25 ppm/K± 0.25 %921 6....--826 6....-± 0.1 %921 7....--826 7....-± 15 ppm/K± 0.25 %922 6....--827 6....-± 0.1 %922 7....--827 7....-Legal Disclaimer Notice VishayDisclaimerALL PRODU CT, PRODU CT SPECIFICATIONS AND DATA ARE SU BJECT TO CHANGE WITHOU T NOTICE TO IMPROVE RELIABILITY, FUNCTION OR DESIGN OR OTHERWISE.Vishay Intertechnology, Inc., its affiliates, agents, and employees, and all persons acting on its or their behalf (collectively,“Vishay”), disclaim any and all liability for any errors, inaccuracies or incompleteness contained in any datasheet or in any other disclosure relating to any product.Vishay makes no warranty, representation or guarantee regarding the suitability of the products for any particular purpose or the continuing production of any product. To the maximum extent permitted by applicable law, Vishay disclaims (i) any and all liability arising out of the application or use of any product, (ii) any and all liability, including without limitation special, consequential or incidental damages, and (iii) any and all implied warranties, including warranties of fitness for particular purpose, non-infringement and merchantability.Statements regarding the suitability of products for certain types of applications are based on Vishay's knowledge of typical requirements that are often placed on Vishay products in generic applications. Such statements are not binding statements about the suitability of products for a particular application. It is the customer's responsibility to validate that a particular product with the properties described in the product specification is suitable for use in a particular application. Parameters provided in datasheets and / or specifications may vary in different applications and performance may vary over time. All operating parameters, including typical parameters, must be validated for each customer application by the customer's technical experts. Product specifications do not expand or otherwise modify Vishay's terms and conditions of purchase, including but not limited to the warranty expressed therein.Hyperlinks included in this datasheet may direct users to third-party websites. These links are provided as a convenience and for informational purposes only. Inclusion of these hyperlinks does not constitute an endorsement or an approval by Vishay of any of the products, services or opinions of the corporation, organization or individual associated with the third-party website. Vishay disclaims any and all liability and bears no responsibility for the accuracy, legality or content of the third-party website or for that of subsequent links.Except as expressly indicated in writing, Vishay products are not designed for use in medical, life-saving, or life-sustaining applications or for any other application in which the failure of the Vishay product could result in personal injury or death. Customers using or selling Vishay products not expressly indicated for use in such applications do so at their own risk. Please contact authorized Vishay personnel to obtain written terms and conditions regarding products designed for such applications. No license, express or implied, by estoppel or otherwise, to any intellectual property rights is granted by this document or by any conduct of Vishay. Product names and markings noted herein may be trademarks of their respective owners.© 2023 VISHAY INTERTECHNOLOGY, INC. ALL RIGHTS RESERVEDRevision: 01-Jan-20231Document Number: 91000MBB0207VD1501BC100MBB0207VE1002BC100。
工业微波开关电源.

WepeX Link
24V输入 RS485接口,支持数据上传 一拖18路电源,每个电源端口 就是其物理位置 五位拔码开关,单一RS485接 口支持32个中继板联机操作
WepeX 1600A: 风冷220V 输入,数字通讯,功率可调
WepeX 1280A:风冷, 220V输入,无数字接口,恒 定功率
传统变压器的可靠性问题
传统变压器在以下情况易烧坏:
➢ 电压过高或过低或者波动比较大 ➢ 元器件选的型号不匹配 ➢ 空间环境温度过高 ➢ 环境灰尘多覆盖变压器表面
一旦出现问题,体积 大,重量重,线路复 杂,故障定位和维修 非常困难
WepeX更耐用更易维护
WepeX的可靠性有如下优势:
➢ 对电网适应力强,能承受电压波动 ➢ 一体化设计,不存在元配件不兼容问题 ➢ 散热效率高,不外加风道时工作环境温度也可高达50度 ➢ 拥有铝制外壳保护,无视粉尘灰尘
1664.4 1272.9
0
170 180 190 200 210 220 230 240 264
输入电压(V)
工频变压 器
Wepex
➢ WepeX对电网适应性非常强,在165V~264V范围内稳定工 作;工频变压器工作范围较窄,仅在180V~240V范围内可工作
➢ WepeX在210V~264V区间,功率稳定性可做到+/-20W ; 工频变压器在 210V~264V区间,功率波动达到400W
传统电源方案问题:
➢ 效率低,耗电大 ➢ 电网适应性差(无法功率输出恒定)、兼容性差(无法自适应不同地区电网频率) ➢ 发热量过大,需油冷\风冷装置,成本高 ➢ 分体原件构成,需至少8根线材及接头,加工工时多,可生产性差,可靠性差,故障率高
麦格米特WepeX方案
EM482M1684LBA-75FE中文资料(Eorex)中文数据手册「EasyDatasheet - 矽搜」
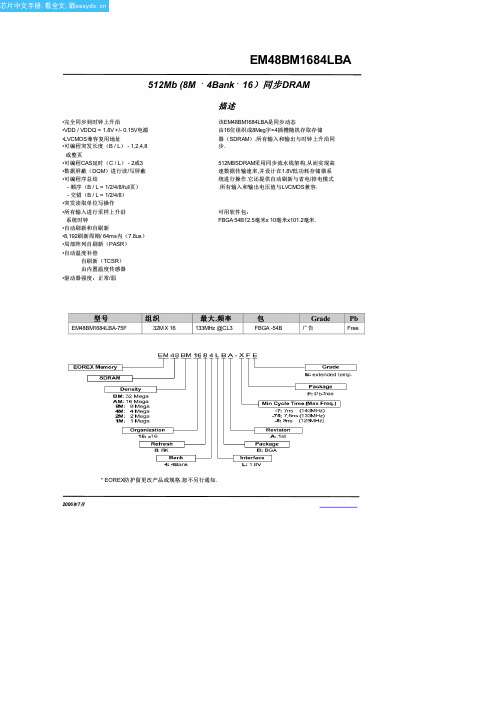
Min.
Typ.
2.0
2.0
3.5
Max.
Units
4.5
pF
4.5
pF
6.0
pF
推荐DC工作条件(T
符号
参数
V DD
电源电压
V DDQ
电源电压(I / O缓冲区)
VIH
输入逻辑高电压
VIL
输入逻辑低电压
Note: *所有电压简称为V
SS.
* V IH (最大)= VDD+ 0.8V脉冲宽度为4ns
0≤V I V DDQ , V DDQ =V DD
所有其它引脚不被测= 0V
0≤V O V DDQ , D OUT 被禁用
IO=-0.1mA
IO=+0.1mA
Min. Typ. Max. Units
-2
+2 uA
-1.5 VDDQ -0.2
+1.5 uA V
0.2 V
(插槽地址)
选择哪家插槽是活跃.
(行地址选通)
闩锁与/ RAS"L"CLK正上升沿行地址.启用行访问和预充 电.
(列地址选通) 锁存器地址栏上产品极上升沿
CLK与/ CAS低.启用列访问.
(写使能) 锁存器地址栏上产品极上升沿
CLK与/ CAS低.启用列访问. (数据输入 /输出掩码) DQM控制I / O缓冲区.
(地址)
行地址(A0至A12)由A0至A12级在插槽活动命令循环CLK上升 沿决定. CA(CA0至CA9)由A0确定至A9水平处读或写命令周期CLK上升沿.
这列地址变成突发存取起始地址. A10限定预充电模式.当A10 =高预充电命令周期,所 有插槽都预充电. 但是,当A10 =低预充电命令周期,仅选择由BA0 / BA1,该行被预充电.
超米特电子有限公司产品说明书

1US Headquarters TEL +(1) 781-935-4850FAX +(1) 781-933-4318 • Europe TEL +(44) 1628 404000FAX +(44) 1628 404090Asia Pacific TEL +(852) 2 428 8008FAX +(852) 2 423 8253South America TEL +(55) 11 3917 1099FAX +(55) 11 3917 0817Superior elongation and tensilestrength help to prevent tearing in use due to mishandling. Typical properties for CHO-SEAL 1310 and 1273 materi-al are shown on pages 33 and 32respectively.High Shielding PerformanceCHO-SEAL 1310 material provides more than 80 dB of shielding effectiv-ness from 100 MHz to 10 GHz, while CHO-SEAL 1273 material provides more than 100 dB.Low Volume ResistivityBoth materials have exceptionally low volume resistivity, which makes them well suited for grounding appli-cations in which a flexible electrical contact is needed.Low Compression GasketSpacer gaskets are typicallydesigned to function under low deflec-tion forces. Chomerics uses design tools such as Finite Element Analysis (FEA) to accurately predict compres-sion-deflection behavior of various cross section options. Refer to page16.LCP Plastic SpacerLiquid crystal polymer (LCP)spacers, including those made with Vectra A130 material, provide aCHO-SEAL ®1310 or 1273Conductive ElastomersWith EMI spacer gaskets, shielding and grounding are provided by Chomerics’CHO-SEAL 1310 and 1273 conductive elastomers, specifi-cally formulated for custom shape molded parts. They provide excellent shielding and isolation against electro-magnetic interference (EMI), or act as a low impedance ground path between PCB traces and shielding media. Physically tough, these elas-tomers minimize the risk of gasket damage, in contrast to thin-walled extrusions or unsupported molded gaskets.Silicone-based CHO-SEAL 1310and 1273 materials offer excellent resistance to compression set over a wide temperature range, resulting in years of continuous service. CHO-SEAL 1310 material is filled with silver-plated-glass particles, while 1273 utilizes silver-plated-copper filler to provide higher levels of EMI shielding effectiveness.EMI Spacer GasketsThe unique design of Chomerics’EMI spacer gaskets features a thin plastic retainer frame onto which a conductive elastomer is molded. The elastomer can be located inside or outside the retainer frame, as well as on its top and bottom surface. EMI spacer gaskets provide a newapproach to designing EMI gaskets into handheld electronics such as dig-ital cellular phones. Board-to-board spacing is custom designed to fit broad application needs. Customized cross sections and spacer shapes allow for very low closure forcerequirements and a perfect fit in any design or device.Robotic InstallationSpacer gaskets can be installed quickly by robotic application. Integral locater pins in the plastic spacer help ensure accuratepositioning in both manual and pick-and-place assembly. Benefits include faster assembly and lower labor costs.The integrated conductive elastomer/plastic spacer gasket is a low cost,easily installed system for providing EMI shielding and grounding in small electronic enclosures.Figure 1Single Piece EMI Gasket/Locator PinsCHO-SEAL 1310 or 1273 Conductive Elastomer (Inside)Plastic Spacer Around Outsideor InsideApplications for EMI Spacer GasketsThe spacer gasket concept is especially suited to digital and dual board telephone handsets or other handheld electronic devices. It provides a low impedance path between peripheral ground traces on printed circuit boards and components such as:•the conductive coating on a plastic housing•another printed circuit board •the keypad assemblyTypical applications for EMI spacer gaskets include:•Digital cellular, handyphone and personal communications services (PCS) handsets •PCMCIA cards•Global Positioning Systems (GPS)•Radio receivers•Other handheld electronics, e.g.,personal digital assistants (PDAs)•Replacements for metal EMI shield-ing “fences” on printedcircuit boards in wireless tele-communications devicesstable platform for direct, highprecision molding of conductive elas-tomers. The Vectra A130 material described in Table 1 has excellent heat deflection temperature character-istics (489°F, 254°C). For weight con-siderations, the LCP has aspecific gravity of only 1.61. This plas-tic is also 100% recyclable.Typical EMI Spacer Gasket Design ParametersThe EMI spacer gasket concept can be considered using the design parameters shown in Table 2. Some typical spacer gasket profiles are shown below.Figure 2Typical Spacer Gasket Profiles3US Headquarters TEL +(1) 781-935-4850FAX +(1) 781-933-4318 • Europe TEL +(44) 1628 404000FAX +(44) 1628 404090Asia Pacific TEL +(852) 2 428 8008FAX +(852) 2 423 8253South America TEL +(55) 11 3917 1099FAX +(55) 11 3917 0817Finite Element AnalysisChomerics, a division of the Parker Hannifin Corporation’s Seal Group, is the headquarters of Parker Seal’s Elastomer Simulation Group. This unit specializes in elastomer finite element analysis (FEA) using MARC K6 series software as a foundation for FEA capability.Benefits of FEA include:•Quickly optimizing elastomer gasket designs•Allowing accurate predictions of alternate elastomer design concepts •Eliminating extensive trial and error prototype evaluationTypical use of FEA in EMI spacer gasket designs is to evaluate the force vs. deflection requirements of alternate designs.For example, onespacer design features a continuous bead of con-ductive elastomer molded onto a plastic spacer. An alternative designemploys an “interrupted bead,” where the interrup-tions (gaps left on the plastic frame) are sized to maintain the requiredlevel of EMI shielding. Figure 4illustrates these alternative designs.Gasket DeflectionFigure 5 compares the effect of continuous and interrupted elastomer gasket designs in terms of the force required to deflect the conductive elastomer. This actual cellular handset application required a spacer gasket with interrupted bead to meet desired deflection forces.Chomerics Designand Application ServicesChomerics will custom design a spacer for your application. Advice,analysis and design assistance will be provided by Chomerics Applications and Design engineers at no additional fee. Contact Chomerics directlyat the locations listed at the bottom of the page.Figure 3FEA Example of an EMISpacer Gasket Cross SectionFigure 4Continuous (top) and InterruptedElastomer GasketsFigure 5Typical Spacer Gasket Deflection。
三菱电机 第4代大型DIPIPM 应用手册
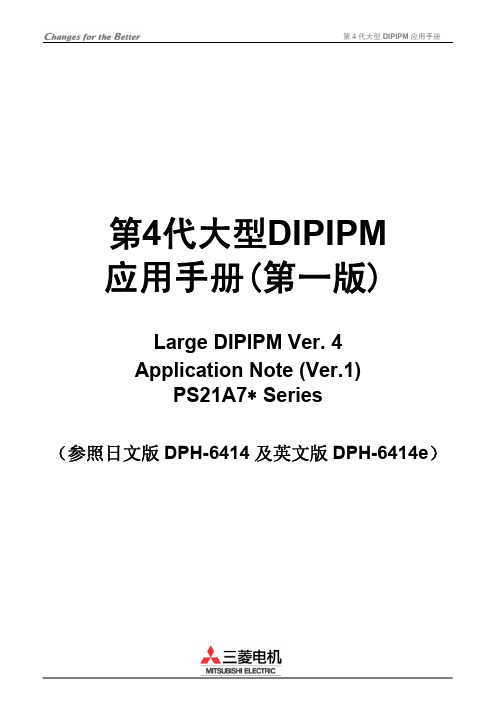
三菱电机株式会社和三菱电机机电(上海)有限公司拥有本手册内所有资料的版权。 任何个人和企业在未得到书面许可的情况下,不得传播、复制、转载、出版和出售涉及本手册的任何内 容。如有违反,我们将保留追究其法律责任的权利。敬请留意。
2009 年 3 月
第 4 代大型 DIPIPM 应用手册
目录
第 1 章 产品概要 ......................................................................................................................................... 1
2.2 保护功能及其工作时序.......................................................................................................................... 9 2.2.1 短路保护......................................................................................................................................... 9 2.2.2 控制电源欠压保护(UV) ..................................................................................................... 12 2.2.............................................................................................. 13
MEMORY存储芯片MT48H32M16LFBF-75 ITB中文规格书
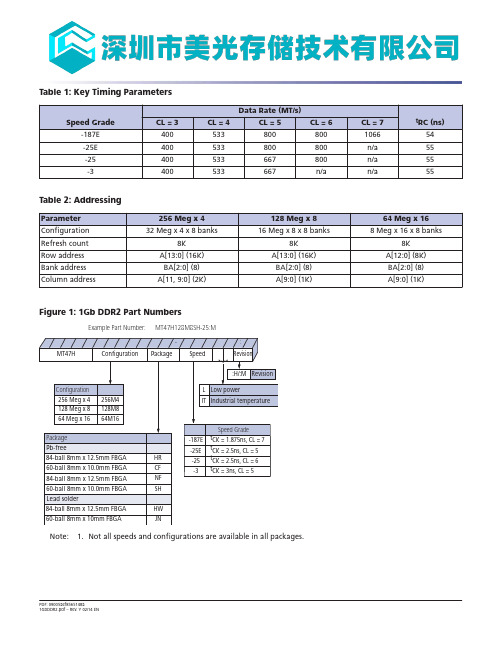
Table 1: Key Timing ParametersTable 2: AddressingFigure 1: 1Gb DDR2 Part NumbersExample Part Number:MT47H128M8SH-25:MNote: 1.Not all speeds and configurations are available in all packages.Functional DescriptionThe DDR2 SDRAM uses a double data rate architecture to achieve high-speed opera-tion. The double data rate architecture is essentially a 4n-prefetch architecture, with aninterface designed to transfer two data words per clock cycle at the I/O balls. A singleREAD or WRITE operation for the DDR2 SDRAM effectively consists of a single 4n-bit-wide, two-clock-cycle data transfer at the internal DRAM core and four correspondingn-bit-wide, one-half-clock-cycle data transfers at the I/O balls.A bidirectional data strobe (DQS, DQS#) is transmitted externally, along with data, foruse in data capture at the receiver. DQS is a strobe transmitted by the DDR2 SDRAMduring READs and by the memory controller during WRITEs. DQS is edge-aligned withdata for READs and center-aligned with data for WRITEs. The x16 offering has two datastrobes, one for the lower byte (LDQS, LDQS#) and one for the upper byte (UDQS,UDQS#).The DDR2 SDRAM operates from a differential clock (CK and CK#); the crossing of CKgoing HIGH and CK# going LOW will be referred to as the positive edge of CK. Com-mands (address and control signals) are registered at every positive edge of CK. Inputdata is registered on both edges of DQS, and output data is referenced to both edges ofDQS as well as to both edges of CK.Read and write accesses to the DDR2 SDRAM are burst-oriented; accesses start at a se-lected location and continue for a programmed number of locations in a programmedsequence. Accesses begin with the registration of an ACTIVATE command, which is thenfollowed by a READ or WRITE command. The address bits registered coincident withthe ACTIVATE command are used to select the bank and row to be accessed. The ad-dress bits registered coincident with the READ or WRITE command are used to selectthe bank and the starting column location for the burst access.The DDR2 SDRAM provides for programmable read or write burst lengths of four oreight locations. DDR2 SDRAM supports interrupting a burst read of eight with anotherread or a burst write of eight with another write. An auto precharge function may be en-abled to provide a self-timed row precharge that is initiated at the end of the burst ac-cess.As with standard DDR SDRAM, the pipelined, multibank architecture of DDR2 SDRAMenables concurrent operation, thereby providing high, effective bandwidth by hidingrow precharge and activation time.A self refresh mode is provided, along with a power-saving, power-down mode.All inputs are compatible with the JEDEC standard for SSTL_18. All full drive-strengthoutputs are SSTL_18-compatible.Industrial TemperatureThe industrial temperature (IT) option, if offered, has two simultaneous requirements:ambient temperature surrounding the device cannot be less than –40°C or greater than85°C, and the case temperature cannot be less than –40°C or greater than 95°C. JEDECspecifications require the refresh rate to double when T C exceeds 85°C; this also requiresuse of the high-temperature self refresh option. Additionally, ODT resistance, input/output impedance and I DD values must be derated when T C is < 0°C or > 85°C.General Notes•The functionality and the timing specifications discussed in this data sheet are for theDLL-enabled mode of operation.•Throughout the data sheet, the various figures and text refer to DQs as “DQ.” The DQterm is to be interpreted as any and all DQ collectively, unless specifically stated oth-erwise. Additionally, the x16 is divided into 2 bytes: the lower byte and the upper byte.For the lower byte (DQ[7:0]), DM refers to LDM and DQS refers to LDQS. For the up-per byte (DQ[15:8]), DM refers to UDM and DQS refers to UDQS.•A x16 device's DQ bus is comprised of two bytes. If only one of the bytes needs to beused, use the lower byte for data transfers and terminate the upper byte as noted:–Connect UDQS to ground via 1kΩ* resistor–Connect UDQS# to V DD via 1kΩ* resistor–Connect UDM to V DD via 1kΩ* resistor–Connect DQ[15:8] individually to either V SS or V DD via 1kΩ* resistors, or floatDQ[15:8].*If ODT is used, 1kΩ resistor should be changed to 4x that of the selected ODT.Table 39: Truth Table – Current State Bank n – Command to Bank mNotes: 1.This table applies when CKE n - 1 was HIGH and CKE n is HIGH and after t XSNR has beenmet (if the previous state was self refresh).2.This table describes an alternate bank operation, except where noted (the current stateis for bank n and the commands shown are those allowed to be issued to bank m, as-suming that bank m is in such a state that the given command is allowable). Exceptionsare covered in the notes below.3.Current state definitions:Idle:The bank has been precharged, t RP has been met, and any READburst is complete.Row active: A row in the bank has been activated and t RCD has been met.No data bursts/accesses and no register accesses are in progress.Read: A READ burst has been initiated with auto precharge disabledand has not yet terminated.Write: A WRITE burst has been initiated with auto precharge disabledand has not yet terminated.READ with auto precharge enabled/ WRITE with auto precharge enabled:The READ with auto precharge enabled or WRITE with auto pre-charge enabled states can each be broken into two parts: the ac-cess period and the precharge period. For READ with auto pre-charge, the precharge period is defined as if the same burst was executed with auto precharge disabled and then followed with the earliest possible PRECHARGE command that still accesses all of the data in the burst. For WRITE with auto precharge, the pre-charge period begins when t WR ends, with t WR measured as if auto precharge was disabled. The access period starts with regis-tration of the command and ends where the precharge period (or t RP) begins. This device supports concurrent auto precharge such that when a READ with auto precharge is enabled or a WRITE with auto precharge is enabled, any command to other banks is allowed, as long as that command does not interrupt the read or write data transfer already in process. In either case, all other related limitations apply (contention between read da-ta and write data must be avoided).The minimum delay from a READ or WRITE command with auto precharge enabled toa command to a different bank is summarized in Table 40 (page 77).4.REFRESH and LOAD MODE commands may only be issued when all banks are idle.5.Not used.6.All states and sequences not shown are illegal or reserved.7.READs or WRITEs listed in the Command/Action column include READs or WRITEs withauto precharge enabled and READs or WRITEs with auto precharge disabled.8. A WRITE command may be applied after the completion of the READ burst.9.Requires appropriate DM.10.The number of clock cycles required to meet t WTR is either two or t WTR/t CK, whicheveris greater.Table 40: Minimum Delay with Auto Precharge EnabledDESELECTThe DESELECT function (CS# HIGH) prevents new commands from being executed bythe DDR2 SDRAM. The DDR2 SDRAM is effectively deselected. Operations already inprogress are not affected. DESELECT is also referred to as COMMAND INHIBIT.。
高科特实际产品说明书
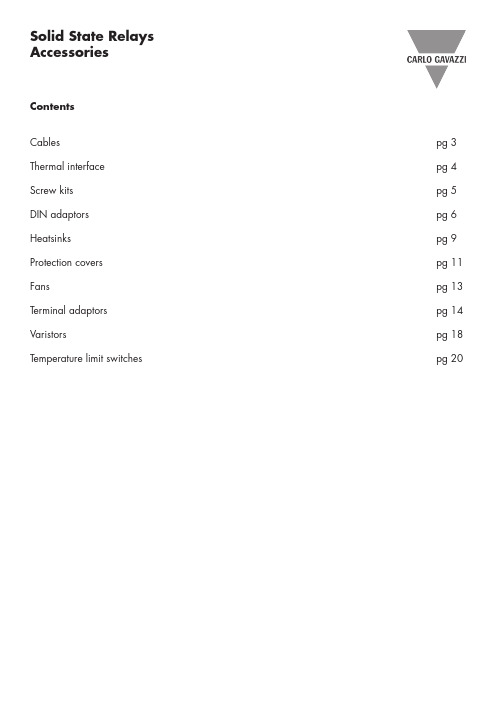
4
Specifications are subject to change without notice (21.06.2021)
Solid State Relays Accessories, Screw Kits Types SRWKIT…
Ordering Key
Screw Kit Screw size Screw length
0.5 Nm -20° to + 70°C [-4 to +158°F] -40° to + 100°C [-40° to +212°F] DIN EN 50022, 50035
DIN Adaptor for 1-phase SSRs
DIN rail adaptor module for mounting the 1-phase SSR series RA, RD, RM, RS and RAM directly on DIN rail.
Type
UL style 2547 UL style 2464 UL style 2464 UL style 2464 UL style 2464 UL style 2464
Cable size
0.14mm2 0.14mm2 0.14mm2 0.25mm2 0.14mm2 0.14mm2
Termination
- Width x Height x Thickness = 35 x 43 x 0.25 mm
- Packing qty. 50 pcs.
RZHT
- Graphite thermal pad for RZ3 series with adhesive on one side
- Width x Height x Thickness = 70 x 77 x 0.25 mm
MEMORY存储芯片MT46V16M16FG-75IT中文规格书
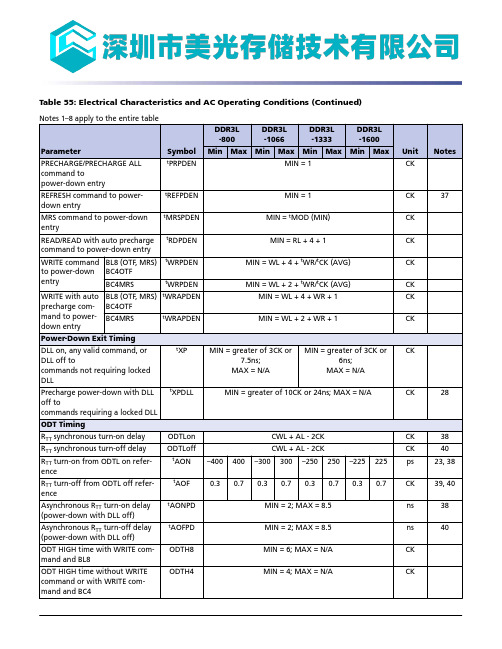
Table 55: Electrical Characteristics and AC Operating Conditions (Continued)Table 55: Electrical Characteristics and AC Operating Conditions (Continued)Notes: 1.AC timing parameters are valid from specified T C MIN to T C MAX values.2.All voltages are referenced to V SS .3.Output timings are only valid for R ON34 output buffer selection.4.The unit t CK (AVG) represents the actual t CK (AVG) of the input clock under operation.The unit CK represents one clock cycle of the input clock, counting the actual clock edges.5.AC timing and I DD tests may use a V IL -to-V IH swing of up to 900mV in the test environ-ment, but input timing is still referenced to V REF (except t IS, t IH, t DS, and t DH use the AC/DC trip points and CK, CK# and DQS, DQS# use their crossing points). The minimum slew rate for the input signals used to test the device is 1 V/ns for single-ended inputs and 2 V/ns for differential inputs in the range between V IL(AC) and V IH(AC).6.All timings that use time-based values (ns, µs, ms) should use t CK (AVG) to determine the correct number of clocks (Table 55 (page 80) uses CK or t CK [AVG] interchangeably). In the case of noninteger results, all minimum limits are to be rounded up to the nearest whole integer, and all maximum limits are to be rounded down to the nearest whole integer.7.Strobe or DQS diff refers to the DQS and DQS# differential crossing point when DQS is the rising edge. Clock or CK refers to the CK and CK# differential crossing point when CK is the rising edge.8.This output load is used for all AC timing (except ODT reference timing) and slew rates.The actual test load may be different. The output signal voltage reference point is V DDQ /2 for single-ended signals and the crossing point for differential signals (see Figure 28 (page 72)).1Gb: x4, x8, x16 DDR3L SDRAM Electrical Characteristics and AC Operating Conditions9.When operating in DLL disable mode, Micron does not warrant compliance with normal mode timings or functionality.10.The clock’s t CK (AVG) is the average clock over any 200 consecutive clocks and t CK (AVG)MIN is the smallest clock rate allowed, with the exception of a deviation due to clock jitter. Input clock jitter is allowed provided it does not exceed values specified and must be of a random Gaussian distribution in nature.11.Spread spectrum is not included in the jitter specification values. However, the inputclock can accommodate spread-spectrum at a sweep rate in the range of 20–60 kHz with an additional 1% of t CK (AVG) as a long-term jitter component; however, the spread spectrum may not use a clock rate below t CK (AVG) MIN.12.The clock’s t CH (AVG) and t CL (AVG) are the average half clock period over any 200 con-secutive clocks and is the smallest clock half period allowed, with the exception of a de-viation due to clock jitter. Input clock jitter is allowed provided it does not exceed values specified and must be of a random Gaussian distribution in nature.13.The period jitter (t JITper) is the maximum deviation in the clock period from the averageor nominal clock. It is allowed in either the positive or negative direction.14.t CH (ABS) is the absolute instantaneous clock high pulse width as measured from onerising edge to the following falling edge.15.t CL (ABS) is the absolute instantaneous clock low pulse width as measured from one fall-ing edge to the following rising edge.16.The cycle-to-cycle jitter t JITcc is the amount the clock period can deviate from one cycleto the next. It is important to keep cycle-to-cycle jitter at a minimum during the DLL locking time.17.The cumulative jitter error t ERRnper, where n is the number of clocks between 2 and 50,is the amount of clock time allowed to accumulate consecutively away from the average clock over n number of clock cycles.18.t DS (base) and t DH (base) values are for a single-ended 1 V/ns slew rate DQs and 2 V/nsslew rate differential DQS, DQS#; when DQ single-ended slew rate is 2V/ns, the DQS dif-ferential slew rate is 4V/ns.19.These parameters are measured from a data signal (DM, DQ0, DQ1, and so forth) transi-tion edge to its respective data strobe signal (DQS, DQS#) crossing.20.The setup and hold times are listed converting the base specification values (to whichderating tables apply) to V REF when the slew rate is 1 V/ns. These values, with a slew rate of 1 V/ns, are for reference only.21.When the device is operated with input clock jitter, this parameter needs to be deratedby the actual t JITper (larger of t JITper (MIN) or t JITper (MAX) of the input clock (output deratings are relative to the SDRAM input clock).22.Single-ended signal parameter.23.The DRAM output timing is aligned to the nominal or average clock. Most output pa-rameters must be derated by the actual jitter error when input clock jitter is present,even when within specification. This results in each parameter becoming larger. The fol-lowing parameters are required to be derated by subtracting t ERR10per (MAX): t DQSCK (MIN), t LZDQS (MIN), t LZDQ (MIN), and t AON (MIN). The following parameters are re-quired to be derated by subtracting t ERR10per (MIN): t DQSCK (MAX), t HZ (MAX), t LZDQS (MAX), t LZDQ MAX, and t AON (MAX). The parameter t RPRE (MIN) is derated by subtract-ing t JITper (MAX), while t RPRE (MAX) is derated by subtracting t JITper (MIN).24.The maximum preamble is bound by t LZDQS (MAX).25.These parameters are measured from a data strobe signal (DQS, DQS#) crossing to its re-spective clock signal (CK, CK#) crossing. The specification values are not affected by the amount of clock jitter applied, as these are relative to the clock signal crossing. These parameters should be met whether clock jitter is present.26.The t DQSCK (DLL_DIS) parameter begins CL + AL - 1 cycles after the READ command.27.The maximum postamble is bound by t HZDQS (MAX).1Gb: x4, x8, x16 DDR3L SDRAM Electrical Characteristics and AC Operating Conditions。
WEBs 应用手册说明书

WEBs 应用手册关于霍尼韦尔霍尼韦尔是一家《财富》全球500 强的高科技企业。
我们的高科技解决方案涵盖航空、汽车、楼宇、住宅和工业控制技术,特性材料,以及物联网。
我们致力于将物理世界和数字世界深度融合,利用先进的云计算、数据分析和工业物联网技术解决最为棘手的经济和社会挑战。
在中国,霍尼韦尔长期以创新来推动增长,贯彻“东方服务于东方”和“东方服务于全球”的战略。
霍尼韦尔始创于1885 年,在华历史可以追溯到1935 年,在上海开设了第一个经销机构。
目前,霍尼韦尔四大业务集团均已落户中国,上海是霍尼韦尔亚太区总部,在华员工人数约11,000 人。
同时,霍尼韦尔在中国的30 多个城市拥有50 多家独资公司和合资企业,其中包括20 多家工厂,旨在共同打造万物互联、更智能、更安全和更可持续发展的世界。
欲了解更多公司信息,请访问霍尼韦尔中国网站www. ,或关注霍尼韦尔官方微博和官方微信。
霍尼韦尔霍尼韦尔智能建筑科技集团我们在全球拥有23,000 多名员工。
我们的产品、软件和技术已在全球超过1,000 万栋建筑中使用。
我们的技术确保商业楼宇业主和用户的设施安全、节能、具有可持续性与高生产力。
霍尼韦尔智能建筑科技集团深耕中国40 多年来,参与了30 多个城市的150 多条地铁的建设,为500 多座机场的智慧和安全保驾护航,为600 多家酒店提供智能管理系统,为1000多家医院提供了数字化解决方案。
目录第一部分 (4)霍尼韦尔智慧楼宇系统架构示意图 (4)霍尼韦尔智慧能源管理解决方案 (6)WEBs N4管理软件 (9)霍尼韦尔智慧触控屏 (13)第二部分 (17)系统控制器 WEB 8000 系列 (17)系统控制器 WEB 8000 VAV 专用系列 (21)边缘数据管理器 (24)增强型可编程通用控制器 (27)可编程通用控制器 (30)可编程通用控制器扩展模块 (33)BACnet 可编程通用 / VAV 控制器 (36)Lonworks 可编程通用 / VAV 控制器 (39)VAV 控制器 (43)BACnet 通用控制器 (46)Sylk TM I/O 扩展模块 (49)MVCweb 控制器 (52)UB系列独立控制器 (55)第三部分 (59)房间温控单元 (59)变风量末端墙装模块 (63)WTS3/6 系列温控器 (65)WTS8/9 系列温控器 (69)WS9 系列墙装模块 (73)建筑网络适配器 (76)智能电表 (78)4Ethernet / LANBACnet MS/TP Modbus RTU LonworksKNXSylk BusLightingModbus TCP BACnet IPBACnet IPAlarm Console clientWEB 8000 Web ControllerWEBStation Supervisor智慧触控屏Sylk I/O ModuleLonworks Spyder边缘数据管理器Spyder Universal ControllerPUC BACnet MS/TP Controller霍尼韦尔智慧楼宇系统架构示意图系统示意图仅用于显示设备在系统中的层次关系以及支持的通讯协议具体配置细节请结合实际项目情况,联系霍尼韦尔技术工程师进行架构设计5ElectricitySubmeterBACnet IPBACnet IPHTTPs , BACnet IP , oBIX , SNMP , …WEBs Enterprise Security WEBs Energy AnalyticsHAQ61增强型 BACnet IP ControllerFCU Wall ModuleVAV Controller EM Bus I/O ModuleSylk Bus Wall Module增强型 BACnet IP ControllerEM Bus6霍尼韦尔智慧能源管理解决方案智能高效,机器自学习功能准确分析,快速发现能耗异常功能全面,基于能耗大数据采集、趋势分析、评估诊断和流程控制的闭环管理功能数据准确,具有180多年计量仪表生产、安装与服务的专业知识灵活易用,云平台或本地部署灵活配置和迁移,操作简便扩展性好通过能源可见性、积极应对能耗异常和提高管理人员参与度,用户可以:★ 避免能耗异常波动★ 确保节能投资的投资回报率(ROI)符合预期★ 提高管理效率和降低运营成本研究显示,更多的企业为合规地实现节省成本、提高效率,越来越关注能源管理系统。
EM48AM1644VTE-75FE中文资料(Eorex)中文数据手册「EasyDatasheet - 矽搜」
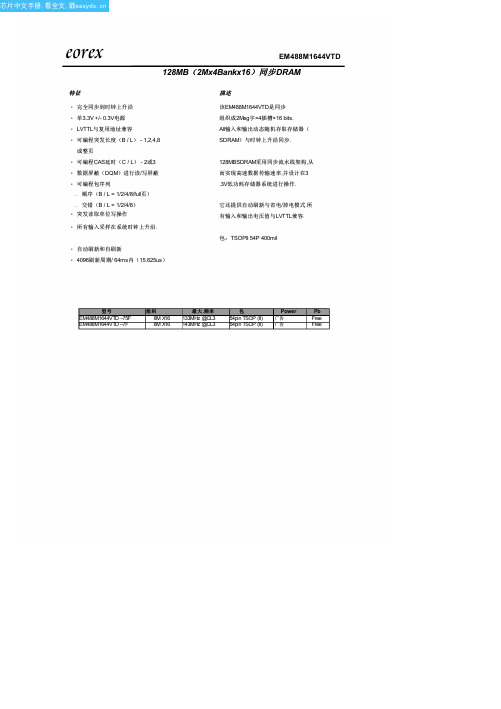
t
预充电至有效命令周期
t
ACTIVE读/写延迟时间
t
ACTIVE(一个)为ACTIVE(另一个)命令
t
读/写命令读/写
t
-7
-7.5 Units
最小最大值 .最小 .最大 .
7
7.5
ns
7.5
10
ns
5.4
5.4 ns
Notes
5.4
6 ns
2.5
2.5
ns
2.5
2.5
ns
3
3
ns
ns 3 7 3 7 ns
____________________________________________
EM488M1644VTD
推 荐 DC工 作 条 件
(VDD = 3.3V +/- 0.3 V,大= 0〜70°C)
参数 工作电流
预充电待机 目前在掉电
mode
预充电待机 电流在非动力 关闭模式
当前待机模式电流 在掉电模式 当前待机模式电流 在非断电
芯片中文手册,看全文,戳
____________________________________________
EM488M1644VTD
128MB(2Mx4Bankx16)同步DRAM
特征
• 完全同步到时钟上升沿
• 单3.3V +/- 0.3V电源 • LVTTL与复用地址兼容 • 可编程突发长度(B / L) - 1,2,4,8
0 ~ 70 -55 ~ 125
1 50
Units V V °C °C W mA
Note: 小心设备暴露在压力超过上述绝对最大额定值可能会造成永久性损害.该装置不意味着在本说 明书操作单元中描述范围之外条件下进行操作.暴露在绝对最大额定值条件下工作会影响 器件可靠性.
微专米 G.Fast 双频通道线驱动器数据表说明书
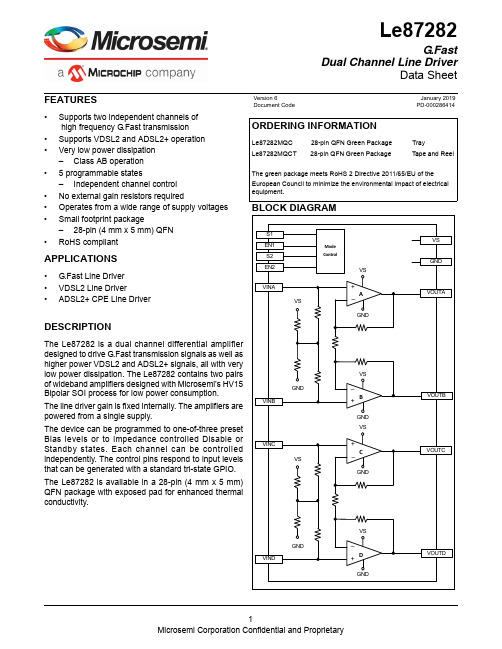
Le87282G.FastDual Channel Line DriverData Sheet FEATURES•Supports two independent channels ofhigh frequency G.Fast transmission•Supports VDSL2 and ADSL2+ operation•Very low power dissipation–Class AB operation• 5 programmable states–Independent channel control•No external gain resistors required•Operates from a wide range of supply voltages•Small footprint package–28-pin (4 mm x 5 mm) QFN•RoHS compliantAPPLICATIONS•G.Fast Line Driver•VDSL2 Line Driver•ADSL2+ CPE Line DriverDESCRIPTIONThe Le87282 is a dual channel differential amplifierdesigned to drive G.Fast transmission signals as well ashigher power VDSL2 and ADSL2+ signals, all with verylow power dissipation. The Le87282 contains two pairsof wideband amplifiers designed with Microsemi’s HV15Bipolar SOI process for low power consumption.The line driver gain is fixed internally. The amplifiers arepowered from a single supply.The device can be programmed to one-of-three presetBias levels or to impedance controlled Disable orStandby states. Each channel can be controlledindependently. The control pins respond to input levelsthat can be generated with a standard tri-state GPIO.The Le87282 is available in a 28-pin (4 mm x 5 mm)QFN package with exposed pad for enhanced thermalconductivity.ORDERING INFORMATIONLe87282MQC 28-pin QFN Green Package TrayLe87282MQCT 28-pin QFN Green Package Tape and ReelThe green package meets RoHS2 Directive2011/65/EU of theEuropean Council to minimize the environmental impact of electricalequipment.Version 6 January 2019Document Code PD-000286414TABLE OF CONTENTSFeatures. . . . . . . . . . . . . . . . . . . . . . . . . . . . . . . . . . . . . . . . . . . . . . . . . . . . . . . . . . . . . . . . . . . . . . . . . .1 Applications . . . . . . . . . . . . . . . . . . . . . . . . . . . . . . . . . . . . . . . . . . . . . . . . . . . . . . . . . . . . . . . . . . . . . . .1 Description . . . . . . . . . . . . . . . . . . . . . . . . . . . . . . . . . . . . . . . . . . . . . . . . . . . . . . . . . . . . . . . . . . . . . . . .1 Ordering Information. . . . . . . . . . . . . . . . . . . . . . . . . . . . . . . . . . . . . . . . . . . . . . . . . . . . . . . . . . . . . . . . .1 Block Diagram . . . . . . . . . . . . . . . . . . . . . . . . . . . . . . . . . . . . . . . . . . . . . . . . . . . . . . . . . . . . . . . . . . . . .1 Connection Diagram. . . . . . . . . . . . . . . . . . . . . . . . . . . . . . . . . . . . . . . . . . . . . . . . . . . . . . . . . . . . . . . . .3 Pin Descriptions . . . . . . . . . . . . . . . . . . . . . . . . . . . . . . . . . . . . . . . . . . . . . . . . . . . . . . . . . . . . . . . . . . . .4 Absolute Maximum Ratings . . . . . . . . . . . . . . . . . . . . . . . . . . . . . . . . . . . . . . . . . . . . . . . . . . . . . . . . . . .5 Thermal Resistance . . . . . . . . . . . . . . . . . . . . . . . . . . . . . . . . . . . . . . . . . . . . . . . . . . . . . . . . . . . .5 Package Assembly. . . . . . . . . . . . . . . . . . . . . . . . . . . . . . . . . . . . . . . . . . . . . . . . . . . . . . . . . . . . .5 Operating Ranges . . . . . . . . . . . . . . . . . . . . . . . . . . . . . . . . . . . . . . . . . . . . . . . . . . . . . . . . . . . . . . . . . .5 Device Specifications. . . . . . . . . . . . . . . . . . . . . . . . . . . . . . . . . . . . . . . . . . . . . . . . . . . . . . . . . . . . . . . .6 State Control. . . . . . . . . . . . . . . . . . . . . . . . . . . . . . . . . . . . . . . . . . . . . . . . . . . . . . . . . . . . . . . . . . . . . . .7 Applications . . . . . . . . . . . . . . . . . . . . . . . . . . . . . . . . . . . . . . . . . . . . . . . . . . . . . . . . . . . . . . . . . . . . . . .7 Line Driver Protection. . . . . . . . . . . . . . . . . . . . . . . . . . . . . . . . . . . . . . . . . . . . . . . . . . . . . . . . . . .8 Physical Dimensions . . . . . . . . . . . . . . . . . . . . . . . . . . . . . . . . . . . . . . . . . . . . . . . . . . . . . . . . . . . . . . . .9 28-pin QFN . . . . . . . . . . . . . . . . . . . . . . . . . . . . . . . . . . . . . . . . . . . . . . . . . . . . . . . . . . . . . . . . . .9CONNECTION DIAGRAMNote:1.Pin 1 is marked for orientation.2.The Le87282 device incorporates an exposed die pad on the underside of its package. The pad acts as a heat sink and must be connectedto a copper plane through thermal vias, for proper heat dissipation. It is electrically isolated and maybe connected to GND.PIN DESCRIPTIONSPin #Pin Name Type Description1IREF Input Device internal reference current. Connect a resistor (R REF ) to GND.2VINA Input Non-inverting input of amplifier A 3VINB Input Non-inverting input of amplifier B 4GND Ground Reference ground5GND 6VINC Input Non-inverting input of amplifier C 7VIND InputNon-inverting input of amplifier D 8NC No internal connection 9S2Input Channel 2 state control 10VOUTD Output Amplifier D output11EN2Input Enable Channel 2 transmission 12VOUTC Output Amplifier C output13NC No internal connection14NC 15NC 16NC 17GND GroundReference ground 18VS PowerPower Supply19VS 20VS 21GND GroundReference ground22NC No internal connection23NC 24NC 25VOUTB Output Amplifier B output26EN1Input Enable Channel 1 transmission 27VOUTA Output Amplifier A output 28S1InputChannel 1 state controlExposed padElectrically isolated thermal conduction pad, can be groundedABSOLUTE MAXIMUM RATINGSStresses above the values listed under Absolute Maximum Ratings can cause permanent device failure.Functionality at or above these limits is not implied. Exposure to absolute maximum ratings for extended periods can affect device reliability .Notes:1.Continuous operation above 145°C junction temperature may degrade device reliability.2.See Thermal Resistance .3.No air flow.Thermal ResistanceThe thermal performance of a thermally enhanced package is assured through optimized printed circuit board layout.Specified performance requires that the exposed thermal pad be soldered to an equally sized exposed copper surface, which, in turn, conducts heat through multiple vias to larger internal copper planes.Package AssemblyThe green package devices are assembled with enhanced, environmental compatible lead-free, halogen-free, and antimony-free materials. The leads possess a matte-tin plating which is compatible with conventional board assembly processes or newer lead-free board assembly processes.Refer to IPC/JEDEC J-Std-020 Table 4 for recommended peak soldering temperature and Table 5-2 for the recommended solder reflow temperature profile.OPERATING RANGESMicrosemi guarantees the performance of this device over the industrial (-40°C to 85°C) temperature range by conducting electrical characterization over each range and by conducting a production test with single insertion coupled with periodic sampling. These characterization and test procedures comply with the Telcordia GR-357-CORE Generic Requirements for Assuring the Reliability of Components Used in Telecommunications Equipment.Storage Temperature-65 ≤ T A ≤ +150°C Operating Junction Temperature (Note 1)-40 ≤ T j ≤ +150°C VS with respect to GND-0.3 V to +16 V Control inputs with respect to GND -0.3 V to 4 V Continuous Driver Output Current100 mA Maximum device power dissipation, continuous (2) - T A = 85°C, P D 1.7W Junction to ambient thermal resistance (2,3), θJA 36.0°C/W Junction to board thermal resistance (2), θJB18.3°C/W Junction to case bottom (exposed pad) thermal resistance, θJC (BOTTOM)8.9°C/W Junction-to-top characterization parameter (2), ψJT 1.2°C/WESD Immunity (Human Body Model)JESD22 Class 2 compliant ESD Immunity (Charge Device Model)JESD22 Class IV compliantAmbient temperature T A-40°C to +85°C Power SupplyVS with respect to GND:Typical usage+8V to +15V,+12V ± 5%DEVICE SPECIFICATIONSTypical Conditions: As shown in the basic test circuit (Figure 1) with VS = +12 V, R REF = 75 k Ω, and T A = 25°C.Min/Max Parameters: T A = -40 to +85°C.Figure 1.Basic Test Circuit - Channel 1 ShownTable 1.Electrical SpecificationsSymbolParameter Description ConditionMinTyp Max Unit NotesSupply Characteristics P VS Supply Power (per channel)Transmission, P LINE = 4 dBm 470600mW Receive period, Disable state 175250mW I VSSupply Current (per channel)Standby State11.5mAControl Input (S1, S2, EN1, EN2 ) Specifications V IH Input High Voltage 2.03.3 3.6V V IM Input Middle Voltage 1.5V V ILInput Low Voltage -0.300.8V Enable Time 500ns Disable TimeDisable state500nsAmplifier CharacteristicsDifferential Gain VOUT/VIN 18.318.819.1dB Gain Flatness2 − 106 MHz-1.51dB 1V O Output Voltage 10V I O Output Current 150mA 1Z I Input Impedance Differential 131518k ΩZ O Output Impedance Disable state 60ΩAmplifier Dynamic CharacteristicsNoise Input Referred Noise 2 - 106 MHz915nV/1TSDThermal Shutdown Temperature170°CNotes: 1. Not tested in production. Guaranteed by characterization and design.HzSTATE CONTROLS1, EN1 and S2, EN2 pins are used as combinatorial logic inputs to control the line driver operating states. Table 2 and Table 3 show the programmable states for each channel.S1, EN1 and S2, EN2 are tri-state inputs that accept three operating levels. These pins have internal resistors tied to +1.5 V which force a middle logic input level when the control to these pins is tri-stated.Table 2.Channel 1 Control MatrixS1EN1State ApplicationX0DisableX Open Standby01Enable Low Bias ADSL2+Open1Enable Medium Bias VDSL211Enable Full Bias G.FastTable 3.Channel 2 Control MatrixS2EN2State ApplicationX0DisableX Open Standby01Enable Low Bias ADSL2+Open1Enable Medium Bias VDSL211Enable Full Bias G.FastDisable State: Amplifier output = VS/2. The Disable state should be used during the receive period. The device presents a controlled low impedance to the line during this state.Standby State: Amplifier bias current removed. This is the lowest power state. Amplifier output is high impedance. Gain-setting feedback resistors are still connected across amplifier output pins, creating 1300ohm differential impedance at pins.Bias States: Line Driver is active for transmission. States are different only in the amount of bias current to the amplifiers, and therefore power consumption. There is a trade-off between bias current and bandwidth. APPLICATIONSThe Le87282 integrates two sets of high-power line driver amplifiers that can be connected for half-duplex differential line transmissions. The amplifiers are designed to be used with signals up to 106 MHz with low signal distortion. The Le87282 can be used for G.Fast applications as illustrated in Figure 2, or it can be used for VDSL2 or ADSL2+ applications. For VDSL2 or ADSL2+ applications, the output resistor values need to be reduced in order to achieve the desired load power of these applications.Figure 2 shows a G.Fast application circuit with amplifiers A and B in transmission and amplifiers C and D in the receive period (Disable state). Amplifiers C and D drive 0 ohms in the Disable state.Figure 2.Typical G.Fast Application CircuitInput ConsiderationsThe driving source impedance should be less than 100 nH to avoid any ringing or oscillation.Output Driving ConsiderationsThe internal metallization is designed to carry up to about 100 mA of steady DC current and there is no current limit mechanism. The device does feature integrated thermal shutdown protection however with hysteresis. Driving lines with no series resistor is not recommended.Power Supplies and Component PlacementThe power supplies should be well bypassed close to the Le87282 device. A 2.2 µF tantalum capacitor and a 0.1 µF ceramic capacitor for the VS supply is recommended.Line Driver ProtectionHigh voltage transients such as lightning can appear on the telephone lines. Transient protection devices should be used to absorb the transient energy and clamp the transient voltages. The series output termination resistors limit the current going into the line driver and internal clamps. The protection scheme depends on the type of data transformer used and the line protection components used in the front of the data transformer.PHYSICAL DIMENSIONSNote:Packages may have mold tooling markings on the surface. These markings have no impact on the form, fit or function of the de-vice. Markings will vary with the mold tool used in manufacturing.Information relating to products and services furnished herein by Microsemi Corporation or its subsidiaries (collectively “Microsemi”) is believed to be reliable. However, Microsemi assumes no liability for errors that may appear in this publication, or for liability otherwise arising from the application or use of any such information, product or service or for any infringement of patents or other intellectual property rights owned by third parties which may result from such application or use. Neither the supply of such information or purchase of product or service conveys any license, either express or implied, under patents or other intellectual property rights owned by Microsemi or licensed from third parties by Microsemi, whatsoever. Purchasers of products are also hereby notified that the use of product in certain ways or in combination with Microsemi, or non-Microsemi furnished goods or services may infringe patents or other intellectual property rights owned by Microsemi.This publication is issued to provide information only and (unless agreed by Microsemi in writing) may not be used, applied or reproduced for any purpose nor form part of any order or contract nor to be regarded as a representation relating to the products or services concerned. The products, their specifications, services and other information appearing in this publication are subject to change by Microsemi without notice. No warranty or guarantee express or implied is made regarding the capability, performance or suitability of any product or service. Information concerning possible methods of use is provided as a guide only and does not constitute any guarantee that such methods of use will be satisfactory in a specific piece of equipment. It is the user’s responsibility to fully determine the performance and suitability of any equipment using such information and to ensure that any publication or data used is up to date and has not been superseded. Manufacturing does not necessarily include testing of all functions or parameters. These products are not suitable for use in any medical and other products whose failure to perform may result in significant injury or death to the user. All products and materials are sold and services provided subject to Microsemi’s conditions of sale which are available on request.For more information about all Microsemi productsvisit our website at TECHNICAL DOCUMENTATION – NOT FOR RESALE© 2019 Microsemi Corporation. All rights reserved. Microsemi and the Microsemi logo are trademarks of Microsemi Corporation. All other trademarks and service marks are the property of their respective owners.Microsemi Corporation (NASDAQ: MSCC) offers a comprehensive portfolio of semiconductor solutions for: aerospace, defense and security; enterprise and communications; and industrial and alternative energy markets. Products include mixed-signal ICs, SoCs, and ASICs;programmable logic solutions; power management products; timing and voice processing devices; RF solutions; discrete components; and systems. Microsemi is headquartered in Aliso Viejo, Calif. Learn more at .Microsemi Corporate HeadquartersOne Enterprise, Aliso Viejo CA 92656 USA Within the USA: +1 (949) 380-6100Sales: +1 (949) 380-6136。
GP-M系列环境抗干扰型内置放大器压力传感器说明书

96M11843 Environment Resisting TypeBuilt-in-amplifier Pressure SensorsGP-M SeriesInstruction ManualRead this instruction manual before using the product in order to achieve maximum performance.Keep this instruction manual in a safe place after reading it so that it can be used at any time.SymbolsIn this instruction manual, the following symbols will be used to so that important points can be understood at one glance.Be sure to read these messages carefully.It indicates tips for better understanding or useful information.Safety Information for GP-M SeriesCE MarkingKEYENCE Corporation has confirmed that this product complies with the essential requirements of the applicable EC Directives, based on the following specifications. Be sure to consider the following specifications when using this product in the Member States of European Union.z EMC Directive (2004/108/EC)•Applicable standards EMI: EN61326-1, Class AEMS: EN61326-1RemarksThese specifications do not give any guarantee that theend-product with this product incorporated complies with the essential requirements of EMC Directive.The manufacturer of the end-product is solely responsible for the compliance on the end-product itself according to EMC Directive.1.We cannot guarantee the functions and/orperformance in the event that the product isused outside the standards of thespecification, or if the product is modified.2.When using our product in combination withanother product, based on such factors asconditions of use and surroundingenvironment, sometimes functions andperformance may not be fully realized. In sucha case, use after adequate examination.Precautions on Regulations and Standards NOTICECSA CertificateGP-M Series complies with the following CSA and UL standards and has been certified by CSA.•Applicable standard CAN/CSA C22.2 No.61010-1UL61010-1Be sure to consider the following specifications when using this product as a product certified by CSA.•Overvoltage category: 1•Use this product under pollution degree 2.•Use this product at the altitude of 2000 m or less.•Indoor use only.•Use CSA/UL certified power supply that provides Class 2 output as defined in the CEC (Canadian Electrical Code) and NEC(National Electrical Code), or CSA/ULcertified power supply that has been evaluated as a Limited Power Source as defined in CAN/CSA-C22.2 No. 60950-1/UL60950-1.•Do not use the GP-M Series for poizonous fluid.Caution when handlingPrecautions for wiringOther precautionse an insulated stabilizing supply for thepower supply.2.Do not pull strongly on the cable.3.Ensure that the cable tip is not submersed inwater during wiring work.4.Isolate the cable from power supply lines orpower lines.5.Isolate the cable as far as possible from anysource of noise.1.The power ON reset time for the GP-M Series is2 seconds after power is turned on. Do not useoutputs from the sensor during this period.2.Initial drift may occur after supplying power tothe GP-M Series. To detect a minute differencein the pressure, let the GP-M Series warm upfor approximately 15 to 30 minutes.3.Do not bring a strong magnet or magnetic fieldclose to the main body of the GP-M Series.NOTICENOTICE4.Do not remove the seal of the air hole of theGP-M001/M010/M025. It will no longer bewaterproof.5.When condensation occurs, it may becomeimpossible to make measurements, or,damage may occur. Take measures such asthe following to prevent condensation.•Ensure that the ambient temperature is the sameor lower than the fluid temperature.•Remove moisture via air conditioning•Separate the sensor 30 cm or more from thecooling pipes using the connector pipe.6.When conducting maintenance, use a softbrush so as not to damage items such as thedetection surface or the O-Ring.7.When replacing the O-Ring, clean all of thedebris from the surface that will be in contactwith the O-Ring.Checking the Packed ItemsGP-M001/M010/M025Sensor x 1 Instruction manual x 1O-Ring x 1 (OP-87287)GP-M100/M250/M400Sensor x 1 Instruction manual x 1O-Ring set x 1 (OP-87288)NOTICE* Only for the GP-M001/M010/M025Piping•Use the adapter for matching with thediameter of the piping.•When using a replacement adapter, attachthe O-Ring included with the Main Unit to thegroove of the G3/4 female screw part.(Refer to the diagram below)•Inquire to us when connecting the pipes directly using the GP-M Series with a G3/4 female screw.•The body may be rotated horizontally to 330°. When rotating, hold the clasp in place with something such as a and Function of Each PartPiping/InstallationAdapterAdapterDOWN button (V )Precautions when installingz Attaching the couplingThe recommended tightening torque when installing the adapter to the main body of the sensor is 20 N•m. It is recommended to apply grease to the G3/4 screw part in order to avoid scorching.z Grounding of metal partsThe metal parts of the main body, the internal circuits 0 V are insulated.z Other precautions•Regardless of whether the power Array of the device is ON or OFF, do nottouch the main part of thepressure detector, if the if thepressure detector is touched,damage may occur due to staticelectricity.•If using a non-conductive liquid such as oil, and plastic piping are used, the risk of an offset change will become greater. Insuch a case, it is recommended to ground the metal housing.•In the case that noise causes malfunction, grounding the metal housing may improve performance.•After installation, conduct an atmospheric correction by making the applied pressure the same as regular roompressure. (Refer to page 10)•When there is condensation, Arrayseparate the sensor from coolingpipe by at least 30 cm using theconnecting pipe.Output diagramz When choosing an NPN output(control output) only.z When choosing a PNP output(control output) only. Analog output diagramPin *When Choosing AnLG of the Function of Output 2 only.M12 Connector Cable (Optional) Pin PositionWiring, Output Diagram1Brown 2White 3Blue 4BlackWhen turning the power ON for the first time after delivery, set the initial settings according to the outline below.Unit ”. By using UV, ,, *1, and *2. *1Except GP-M100/M250/M400*2Except GP-M001Function for correcting the measurement value to 0 due to problems such as long term use.pressure the same as regular room pressure.•The air pressure correction is effective within a range of ±10 of F .S. If it is executed outside of that range, “----” is displayed and no correction will occur.Initial Settings at the Time of DeliveryU briefly will return you toAtmospheric Pressure Correction•The atmospheric pressure correction will be reflected on the analog output.Function for preventing operation error.Key Lock•If the Key Lock is enabled, the setting value change (the detail settings from pressing and holding the MODE button) is not available. (“Loc ” will display as blinking”)•If “PASS ” is set to a value other than “0000 (initial value)” via the extended function (page 16), when the Key Lock is disabled a password will be requested. (Refer to below)Activate/Deactivate Key LockFrom the main screen, press and hold the MODE button and the U button (or the V button) simultaneously.If “Loc ” is displayed while blinking, the Key Lock is enabled. With the same operation it can be disabled (“unL ” will be displayed while blinking).Disabling the Key Lock with Password1.From the main screen press and hold the MODE button simultaneously with the U button (or the V button).“PASS ” and a number value alternately is displayed.2.Select a password with the UV and press the MODE button to select.If the correct password is entered:“unL ” will appear as a blinking display, and Key Lock will be disabled.If an incorrect password is entered:“ErP ” will appear as a blinking display, Key Lock will not be disabled, and the screen will return to the main screen.Changing the Setting Value of Output 1Change the setting value of output 1. The changing of setting values of output 2 is done by pressing and holding the MODE button. (Refer to page 15)Display Pressure Unit/Hold DisplayDisplay Pressure UnitIf the MODE button is pressed briefly on the main screen, the pressure unit will display.If it is not used for 2 seconds it will return to the main screen.Display Peak and Bottom HoldIf the MODE button + the U (V) button are pressed briefly on the main screen, the peak (bottom) hold value will display. (“P_H” (“b_H”) and hold value will blink alternately.)Unit ”. By using UV, , ,*1, and *2.*1Except GP-M100/M250/M400*2Except GP-M001is pressed briefly on the P-n appear.•Peak (bottom) hold value will be stored into EEPROM every 45 seconds.•If the U and V buttons are pressed and heldsimultaneously on the peak (bottom) hold screen, the peak (bottom) hold value of the initial reset will be cleared.•To return to the previous screen, press the MODE button briefly.Initial Reset (Initialization)U at the same time will return to theInitialization Value ListItem Default value (by model)Model GP-M001GP-M010GP-M025GP-M100GP-M250GP-M400Unit kPa MPaSP1/FH1(Switch-on point 1)40.00.400 1.000 4.0010.0016.00 rP1/FL1(Switch-off point 1)20.00.2000.500 2.00 5.008.00 SP2/FH2(Switch-on point 2)100.0 1.000 2.50010.0025.0040.00 rP2/FL2(Switch-off point 2)80.00.800 2.0008.0020.0032.00 ASP (Analog startpoint (4 mA))-100.00.0000.0000.000.000.00 AEP (Analog endpoint (20 mA))100.0 1.000 2.50010.0025.0040.00Item Default value (for all models) ou1 (detection mode of output 1)Hnoou2 (detection mode of output 2)HnoCoF (offset correction)No correctiondS1/dr1/dS2/dr2 (direct timer)0.00 (s)SPEd (responsiveness) 3 (ms)Eco (power-save mode)oFFHYS (presence of hysterisis when in window mode)ondiS.U (display renew cycle)200 (ms)diS.r (display inversion)noPASS (password)0000Settings of Each Setting Function••and UDetection mode and setting valueThe GP-M Series has two types of detection modes which are described below.When the selected function of output 2 is out (control output), the output 1 and output 2 can be set separately.Hysteresis mode (Hno /HnC )Considering Sp-rP = hysteresis, it is the mode for changing the setting value when ON and when OFF .•When the output is OFF (right diagram 1), and the measuredvalue becomes more SP than itwill turn on (right diagram 2).•When the output is ON, and the measuring value becomes less than rP , it will turn OFF (rightdiagram 3).Window mode (Fno /FnC )This mode determines whether the measured value is within or outside the area of FH to FL .•If the detection value of theoutput OFF condition in the rightdiagram 1 is more than (FL +HYS ) or less than FH , it will turn ON (right diagram2).•From that condition the measured value is larger than FH (right diagram 3), or, less than FL , the right diagram will be OFF .•If the measured value of the condition in the diagram on the right is less than (FH - HYS ) or more than FL , it will be ON.Explanation of All FunctionsIf HYS is fixed at 0.5% of F .S., the presence or absence of hysterisis can be selected by the extended function (page 16).Free range analog outputSet the pressure value for the respective free range analog start point and end point. The function of the output 2 can be selected at the time of AnLG (analogue output). ASP and AEP can be set freely within the measured range. Operation is as follows.1.When ASP < AEP•When ASP becomes AEP : 4 mA becomes 20 mA•If the measurement value falls below ASP , output will be up to 3.8 mA•If the measurement value rises above AEP , output will be up to 20.5 mA 2.When ASP > AEP•When ASP becomes AEP : 4 mA becomes 20 mA•If the measurement value falls below AEP , output will be up to 20.5 mA•If the measurement value rises above ASP , output will be up to 3.8 mAThe name of the setting values depending on the mode and output are as follows.When system error (ErS ) occurs, 2 mA will be output.*Selection is possible when the selection function of output 2(control output) is out .Output Detection Mode Switch on point Switch off point Output 1when choosing hysteresis mode SP1rP1Output 2SP2*rP2*Output 1when choosing window modeFH1FL1Output 2FH2*FL2*Offset correctionConcerning the value at the time of shipping, there may be as much as ±10%F .S. offset correction.This activates in the case of a margin of error in the displayed pressure value and the actual pressure value.The pressure value after the offset correction is displayed on thesetting screen and can be adjusted with the UV buttons.Delay timerThe delay timer can be set within the range of 0.00 to 50.00(s)When the function selection of output 2 is out (control output) the delay timer for output 1 and output 2 can be set separately.*The setting of the dS2, dr2 is possible when the function of output 2 is selected as out (control output).Offset correction works in conjunction with “Atmospheric pressure correction”.•If the UV buttons are pressed and held simultaneously on the offset correction screen, the offset correction value and the air pressure correction value will revert to the condition at shipping (no correction).Setting item MeaningdS1/dS2Concerning the ON delay timer of output 1/output 2. When the judgment switches from OFF to ON, the set delay time will elapse.dr1/dr2Concerning the OFF delay time of output 1/output 2. When the judgment switches from ON to OFF , the set delay time will elapse.ResponsivenessThe time until 100% response of the internal judgment value can be set from within the range of 3 to 5000 (ms).The response time of the analog output (90% response) will be an additional 2 ms from this point.Power Save ModeWhen on is selected, if the key operation does not occur for 15 seconds (Power Save) will be displayed.The “-”at the time of power save display will move from the left to the right, and the operation indicator will operate normally. To return the display status to normal, press any key. When there is an error, regardless of whether power save mode is on /oFF , the error will be displayed.Display Renewal CycleSet the interval to renew the display contents. When a value is increased, only for that time the value will continue to be displayed the same. From after the renewal until the next renewal, the measurement value will be averaged so as to control fluctuations in the display value. However, there will be no influence on the control output and the analog output.Display inversionWhen no is selected: regular displayWhen YES is selected: The display will be inverted vertically 180°.Time chartError Display and Countermeasures Errordisplay Cause Measures----At the time of atmosphericpressure correction there is±10% F.S. applied pressure.Return the air to the roompressure, once again setthe sensitivity setting.ErC There is too much current flowingthrough the control output.Check the load, and returnto the rated range.oL Outside possible displayrange (above)Return to the ratedpressure range.uL Outside possible displayrange (below)Return to the ratedpressure range.ErP An incorrect password wasentered at the time of theKey Lock release.Enter the correctpassword. If the passwordhas been forgotten contactyour nearest sales office.ErE Write/load to EEPROMerrorDo an initial reset. If in thatcase the problem has notbeen fixed please contact us.ErS System error Contact the nearest sales office. Output Condition at the Time of Error.Errordisplay Output judgment Analog output ----Regular operation Regular operation ErC OFF Regular operation oL Operation at the maximum possible display range uL Operation at the minimum possible display range ErP Regular operation Regular operation ErE Regular operation Regular operation ErS OFF 2 mASpecifications (Differs by model type)Model GP-M001GP-M010GP-M025GP-M100GP-M250GP-M400Rated pressure -100 to+100kPa-0.1 to+1MPa-0.1 to+2.5MPa0 to +10MPa0 to +25MPa0 to +40MPaPossible display range -120.0 to+120.0kPa-0.210 to+1.110MPa-0.360 to+2.760MPa-1.00 to+11.00MPa-2.50 to+27.50MPa-4.00 to+44.00MPaAllowablepressure400 kPa 4 MPa10 MPa30 MPa50 MPa50 MPaBurstpressure 1.5 MPa15 MPa35 MPa 100MPa100MPa100MPaDisplayresolution0.1 kPa0.001 MPa0.01 MPaFluid type Gas or liquid that will notcorrode the liquid contactpartLiquid that will not corrodethe liquid contact partSpecifications (All model types are the same)Type of pressure Gage pressurePrecision*1±1.0% of F.S. or less Repeatability*2±0.3% of F.S. or lessTemperaturecharacteristics±0.6% of F.S./10°CZero-cut pressurevalue±0.5% of F.S.Connection diameter G3/4 (Changes to the R1/8 male, R1/4 male, R3/8 male, G1/4 female, NPT1/8 male, and NPT1/4 male option adapters are available.)Box rotation angle Maximum 330°Medium temperature -20 to +100°C (no freezing/condensation)*3 *6Power supplyvoltage 10-30 VDC, Ripple (P-P): 10% max,Class 2 or LPSCurrentconsumption 50 mA or less (when 24 V: 32 mA or less, when 12 V: 48 mA or less. Excluding output)*4Display method4 column digital LED red/Vertical inversion display possible Operation displaylight Operation indicator (output 1) (orange)Operation indicator (output 2) (orange)HysteresisDuring hysteresis mode: variable (Difference between switch-on point andswitch-off point is hysteresis)During window mode: fixed (0.5% of F .S.)ResponseControl outputSelectable from 3 to 5000 ms Analog output As above + 2 ms (90% response)Output 1control output NPN/PNP open collector (Selectable)30 V or less, Max. 250 mAResidual voltage for the Main Unit is 1 V or less, N.O./N.C. selectable Output 2(replace -ment type )Control outputAnalog output 4-20 mA, maximum load resistance 500 Ω(When the electric voltage is more than 20 V)*5Environmental resistance Ambient temperature -20 to +80°C (no freezing/condensation)*6Relativehumidity35 to 85% RH (no condensation)*6VibrationIEC60068-2-6 20 G (10 to 2000 Hz In each direction of X, Y, Z for 2 hours)ShockIEC60068-2-27 50 G (11 msIn each direction X, Y, Z 3 times)Enclosure protection IP67R a t i n gO u t p u t*1This is the value when considering linearity + hysterisis + repeatabilityin a stable environment of 23°C.*2The repeatability, based on consistent conditions, is the difference inthe detection points at the time of fluctuations in the repetition.*3When the temperature of the piping exceeds 80°C, do not connect the cable.*4Consumption current including output is 0.6 A and under.*5The maximum load resistance R will be the values below in response tothe electric voltage E.When 10-23V: R = (38 x (E-10) + 128) ΩWhen 23-30V: R = 622 Ω*6Take measures such as the following to prevent condensation.•Ensure that the ambient temperature is equal or lower than the fluid temperature.•Dehumidify using an air-conditioner•Separate the sensor from the cooling pipe by at least 30 cm using the connecting pipe.Also, it is recommended that ambient temperature and relative humidity should*7Material propertiesWettedpart Pressure port: SUSXM7/Diaphragm pressure port: Al 2O 3/O-Ring: FKM Other partsHousing metal portion: SUS304, SUS303Housing plastic portion: PPSU Air hole *7: PTFE, nickel-plated brass.Applicable cableM12 connector 4 pinWeightApp. 150 gDimensionsO-ringfor GP-M001/M010/M025 useO-ring setfor GP-M100/M250/M400 useWarranties and Disclaimers(1)KEYENCE warrants the Products to be free of defects in materials andworkmanship for a period of one (1) year from the date of shipment. If any models or samples were shown to Buyer, such models or samples were used merely to illustrate the general type and quality of theProducts and not to represent that the Products would necessarilyconform to said models or samples. Any Products found to bedefective must be shipped to KEYENCE with all shipping costs paid by Buyer or offered to KEYENCE for inspection and examination. Upon examination by KEYENCE, KEYENCE, at its sole option, will refund the purchase price of, or repair or replace at no charge any Productsfound to be defective. This warranty does not apply to any defectsresulting from any action of Buyer, including but not limited to improper installation, improper interfacing, improper repair, unauthorizedmodification, misapplication and mishandling, such as exposure toexcessive current, heat, coldness, moisture, vibration or outdoors air.Components which wear are not warranted.(2)KEYENCE is pleased to offer suggestions on the use of its variousProducts. They are only suggestions, and it is Buyer's responsibility to ascertain the fitness of the Products for Buyer’s intended use.KEYENCE will not be responsible for any damages that may result from the use of the Products.(3)The Products and any samples ("Products/Samples") supplied to Buyerare not to be used internally in humans, for human transportation, as safety devices or fail-safe systems, unless their written specifications state otherwise. Should any Products/Samples be used in such amanner or misused in any way, KEYENCE assumes no responsibility, and additionally Buyer will indemnify KEYENCE and hold KEYENCE harmless from any liability or damage whatsoever arising out of any misuse of the Products/Samples.(4)OTHER THAN AS STATED HEREIN, THE PRODUCTS/SAMPLESARE PROVIDED WITH NO OTHER WARRANTIES WHATSOEVER.ALL EXPRESS, IMPLIED, AND STATUTORY WARRANTIES,INCLUDING, WITHOUT LIMITATION, THE WARRANTIES OFMERCHANTABILITY, FITNESS FOR A PARTICULAR PURPOSE,AND NON-INFRINGEMENT OF PROPRIETARY RIGHTS, AREEXPRESSL Y DISCLAIMED.IN NO EVENT SHALL KEYENCE AND ITS AFFILIATED ENTITIES BE LIABLE TO ANY PERSON OR ENTITY FOR ANY DIRECT,INDIRECT, INCIDENTAL, PUNITIVE, SPECIAL ORCONSEQUENTIAL DAMAGES (INCLUDING, WITHOUT LIMITATION, ANY DAMAGES RESULTING FROM LOSS OF USE, BUSINESSINTERRUPTION, LOSS OF INFORMATION, LOSS OR INACCURACY OF DATA, LOSS OF PROFITS, LOSS OF SAVINGS, THE COST OF PROCUREMENT OF SUBSTITUTED GOODS, SERVICES ORTECHNOLOGIES, OR FOR ANY MATTER ARISING OUT OF OR IN CONNECTION WITH THE USE OR INABILITY TO USE THEPRODUCTS, EVEN IF KEYENCE OR ONE OF ITS AFFILIATEDENTITIES WAS ADVISED OF A POSSIBLE THIRD PARTY’S CLAIM FOR DAMAGES OR ANY OTHER CLAIM AGAINST BUYER. In some jurisdictions, some of the foregoing warranty disclaimers or damage limitations may not apply.BUYER'S TRANSFER OBLIGATIONS:If the Products/Samples purchased by Buyer are to be resold ordelivered to a third party, Buyer must provide such third party with a copy of this document, all specifications, manuals, catalogs, leaflets and written information provided to Buyer pertaining to the Products/ Samples.E 1101-3。
MEMORY存储芯片MT46V8M16TG-75IT中文规格书
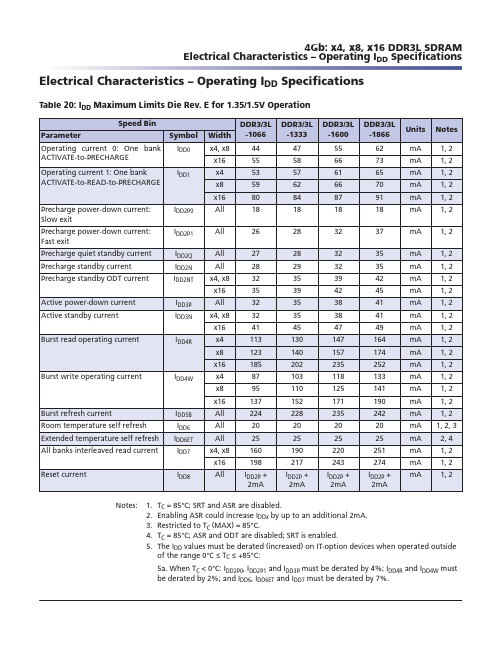
ACT
001100000F0
–
D
100000000F0
–
D
100000000F0
–
D#
111100000F0
–
D#
111100000F0
–
Repeat cycles nRC + 1 through nRC + 4 until nRC + nRCD - 1; truncate if needed
RD
0 1 0 1 0 0 0 0 0 F 0 00110011
nRC + nRAS
1
2 × nRC
2
4 × nRC
3
6 × nRC
4
8 × nRC
5 10 × nRC
6 12 × nRC
7 14 × nRC
ACT
00110000000
–
D
10000000000
–
D
10000000000
–
D#
11110000000
–
D#
11110000000
–
Repeat cycles 1 through 4 until nRCD - 1; truncate if needed
Repeat sub-loop 0, use BA[2:0] = 6
Repeat sub-loop 0, use BA[2:0] = 7
Notes:
1. DQ, DQS, DQS# are midlevel unless driven as required by the RD command. 2. DM is LOW. 3. Burst sequence is driven on each DQ signal by the RD command. 4. Only selected bank (single) active.
MAX1978中文数据手册

用于Peltier模块的集成温度控制器概论MAX1978 / MAX1979是用于Peltier热电冷却器(TEC)模块的最小, 最安全, 最精确完整的单芯片温度控制器。
片上功率FET和热控制环路电路可最大限度地减少外部元件, 同时保持高效率。
可选择的500kHz / 1MHz开关频率和独特的纹波消除方案可优化元件尺寸和效率, 同时降低噪声。
内部MOSFET的开关速度经过优化, 可降低噪声和EMI。
超低漂移斩波放大器可保持±0.001°C的温度稳定性。
直接控制输出电流而不是电压, 以消除电流浪涌。
独立的加热和冷却电流和电压限制提供最高水平的TEC保护。
MAX1978采用单电源供电, 通过在两个同步降压调节器的输出之间偏置TEC, 提供双极性±3A输出。
真正的双极性操作控制温度, 在低负载电流下没有“死区”或其他非线性。
当设定点非常接近自然操作点时, 控制系统不会捕获, 其中仅需要少量的加热或冷却。
模拟控制信号精确设置TEC 电流。
MAX1979提供高达6A的单极性输出。
提供斩波稳定的仪表放大器和高精度积分放大器, 以创建比例积分(PI)或比例积分微分(PID)控制器。
仪表放大器可以连接外部NTC或PTC热敏电阻, 热电偶或半导体温度传感器。
提供模拟输出以监控TEC温度和电流。
此外, 单独的过热和欠温输出表明当TEC温度超出范围时。
片上电压基准为热敏电阻桥提供偏置。
MAX1978 / MAX1979采用薄型48引脚薄型QFN-EP 封装, 工作在-40°C至+ 85°C温度范围。
采用外露金属焊盘的耐热增强型QFN-EP封装可最大限度地降低工作结温。
评估套件可用于加速设计。
应用光纤激光模块典型工作电路出现在数据手册的最后。
WDM, DWDM激光二极管温度控制光纤网络设备EDFA光放大器电信光纤接口ATE特征♦尺寸最小, 最安全, 最精确完整的单芯片控制器♦片上功率MOSFET-无外部FET♦电路占用面积<0.93in2♦回路高度<3mm♦温度稳定性为0.001°C♦集成精密积分器和斩波稳定运算放大器♦精确, 独立的加热和冷却电流限制♦通过直接控制TEC电流消除浪涌♦可调节差分TEC电压限制♦低纹波和低噪声设计♦TEC电流监视器♦温度监控器♦过温和欠温警报♦双极性±3A输出电流(MAX1978)♦单极性+ 6A输出电流(MAX1979)订购信息* EP =裸焊盘。
瑞特拉电子产品购买指南说明书

241For additional technical information visit Metric measurements for this product are exact, imperial measurements are rounded to the nearest whole numberUseful Cooling Capacity: 2400 - 5794 BTU (703 - 1697 W)Part No. with basic controller 3303.1042)3303.1142)3304.1043304.1143304.1443305.1043305.1143305.144Part No. with comfort controller 3303.5042)3303.5142)3304.5043304.5143304.5443305.5043305.5143305.544Voltage V , Hz230, 50/60115, 60230, 50/60115, 60400, 50/ 460, 60, 3~230, 50/60115, 60400, 50/ 460, 60, 3~Dimensions inches (mm)H x W x D24 x 11 x 12 (620 x 285 x 298)40 x 16 x 14 (1020 x 405 x 358)Useful cooling capacity Q KBTU (W)T i 131 T a 1312400 (703)3916 (1147)5794 (1697)Useful cooling capacity Q K to DIN 3168 BTU (W)T i 95 T a 951708/2083(500/610)1708 (500)3415/3620 (1000/1060)5123/5157 (1500/1510)T i 95 T a 122956/1195(280/350)956 (280)2698/2869 (790/840)4201/4269 (1230/1250)Rated current maximum 2.6/2.6 A 5.7 A 5.4/5.0 A 10.6/11.1 A 2.8/2.9 A 6.0/6.5 A 12.1/13.6 A 2.6/2.9 A Starting current 5.1/6.4 A 11.5 A 12.0/14.0 A 26.0/28.0 A 11.5/12.7 A 22.0/24.0 A 42.0/46.0 A 12.2/11.3 A Pre-fuse T 10.0 A 10.0 A 10.0 A 16.0 A 10.0 A 1)16.0 A 20.0 A 10.0 A 1)Power consumption Pel toDIN 3168T i 95 T a 95360/380 W 470 W 700/650 W 725/680 W 580/550 W 850/1000 W 880/1050 W 800/980 W T i 95 T a 122420/390 W500 W 750/710 W 780/750 W 660/680 W 1000/1160 W 1040/1200 W 960/1150 W Cooling coefficient j =Q K /PelT i 95 T a 95 1.4 1.7 1.8 1.7 1.9Refrigerant R134a, 6.0 oz (170 g)R134a, 17.6 oz (500 g)R134a, 21.1 oz (600 g)Maximum allowable operating pressure 406 psi (28 bar)363 psi (25 bar)Temperature and setting range Comfort Controller - 68 to 131° F (+20 to +55° C) / Basic Controller - 86 to 131° F (+30 to +55° C)Environmental ratings UL Type 4X (IP 66)Duty cycle 100%Type of connection Plug-in terminal strip Weight lb (kg)55.1 (25)108.2 (49)119.0 (54)110.2 (50)112.4 (51)123.5 (56)114.6 (52)Material Type 304 stainless steelAir displacement offans External circuit 203 cfm (345 m 3/h)530 cfm (900 m 3/h)530 cfm (900 m 3/h)Internal circuit 182 cfm (310 m 3/h)353 cfm (600 m 3/h)471 cfm (800 m 3/h)Temperature control Basic or comfort controller (factory setting 95° F [+35° C])Accessories PU Page Door-operated switch 14127.010–Master/slave cable for comfortcontroller13124.100–3124.100267RiDiag II including cables for comfortcontroller13159.100267Interface card for comfort controller 13124.200268Condensate hose 13301.6103301.6122731) Motor circuit breaker. 2)Internal condensate evaporator not included. Special voltages and technical modifications available on request.Wallmounted UL T ype 4X Air ConditionerCon guration:Fully wired ready for connection, including drilling template and assembly parts. With nano-coated condenser and integrated condensate evaporator.Protection Ratings:UL and cUL recognized, CSA UL Type 4XUL file: SA8250 Material:Type 304 stainless steel Note:Air conditioner with comfortcontroller may be integrated into a monitoring system with an optional interface card 3124.20 (RS 232, RS 485, RS 422 and PLC interface). See page 268. Made in the USA.000C o u r t e s y o f C M A /F l o d y n e /H y d r a d y n e ŀ M o t i o n C o n t r o l ŀ H y d r a u l i c ŀ P n e u m a t i c ŀ E l e c t r i c a l ŀ M e c h a n i c a l ŀ (800) 426-5480 ŀ w w w .c m a f h .c o242For additional technical information visit Metric measurements for this product are exact, imperial measurements are rounded to the nearest whole numberUseful Cooling Capacity: 8706 - 10525 BTU (2550 - 3083 W)Part No. with basic controller 3328.1043328.1143328.1443329.1043329.1143329.144Part No. with comfort controller 3328.5043328.5143328.5443329.5043329.5143329.544Rated operating voltage V , Hz 230, 50/60115, 50/60400, 50/460, 60, 3~230, 50/60115, 50/60400, 50/460, 60, 3~Dimensions inches (mm)H x W x D 65 x 16 x 15 (1650 x 405 x 388)Useful cooling capacity Q K BTU (W)T i 131 T a 1318706 (2550)10525 (3083)Useful cooling capacity Q K to DIN 3168 BTU (W)T i 95 T a 956860/8025 (2000/2350)8538/9392 (2500/2750)T i 95 T a 1224952/5772 (1450/1690)5464/5977 (1600/1750)Rated current max. 7.5 A/9.1 A 14.7 A/17.3 A 2.8 A/3.3 A 8.6 A/10.6 A 17.0 A/22.0 A 3.7 A/3.8 A Start-up current 22.0 A/26.0 A36.0 A/39.0 A6.8 A/7.8 A 21.0 A/21.0 A44.0 A/42.0 A6.8 A/7.6 A Pre-fuse T16.0 A25.0 A 10.0A/10.0 A 1)16.0 A 25.0 A 10.0 A/10.0 A 1)Power consumption Pel to DIN 3168 T i 95 T a 951025/1200 W 1085/1250 W 1050/1275 W 1450/1675 W 1500/1725 W 1425/1625 W T i 95 T a 1221250/1350 W1300/1410 W1275/1525 W1625/2000 W1675/2065 W1675/1975 WCooling coefficient j = Q K /Pel T i 95 T a 951.72.31.92.0RefrigerantR134a, 31.7 oz (900 g)Maximum allowable operating pressure 406 psi (28 bar)Temperature and setting range Comfort Controller - 68 to 131° F (+20 to +55° C) / Basic Controller - 86 to 131° F (+30 to +55° C)Protection rating UL Type 4X (IP 66)Duty cycle 100%Type of connection Plug-in terminal stripWeight lb (kg)176.4 (80)191.8 (87)176.4 (80)183.0 (83)198.4 (90)183.0 (83)MaterialType 304 stainless steelAir displacement of fans External circuit 377 cfm (640 m 3/h)418 cfm (710 m 3/h)Internal circuit324 cfm (550 m 3/h)377 cfm (640 m 3/h)Temperature control Basic or comfort controller (factory setting 95° F [+35° C])Accessories PU Page Door-operated switch14127.010–Master/slave cable for comfort controller13124.100267RiDiag II including cables for comfort controller 13159.100267Interface card for comfort controller 13124.200268Condensate hose13301.6122731)Motor circuit breaker. Special voltages available on request. We reserve the right to make technical modifications.Wallmounted UL T ype 4X Air ConditionerCon guration:Fully wired ready for connection, including drilling template and assembly parts. With nano-coated condenser and integrated condensate evaporator.Protection Ratings: UL and cUL recognized UL Type 4X UL file: SA8250Material:Type 304 stainless steelNote:Air conditioner with comfortcontroller may be integrated into a monitoring system with an optional interface card 3124.200(RS 232, RS 485, RS 422 and PLC interface). See page 268. Made in the USA.C o u r t e s y o f C M A /F l o d y n e /H y d r a d y n e ŀ M o t i o n C o n t r o l ŀ H y d r a u l i c ŀ P n e u m a t i c ŀ E l e c t r i c a l ŀ M e c h a n i c a l ŀ (800) 426-5480 ŀ w w w .c m a f h .c o。
EM641FV8FS中文资料
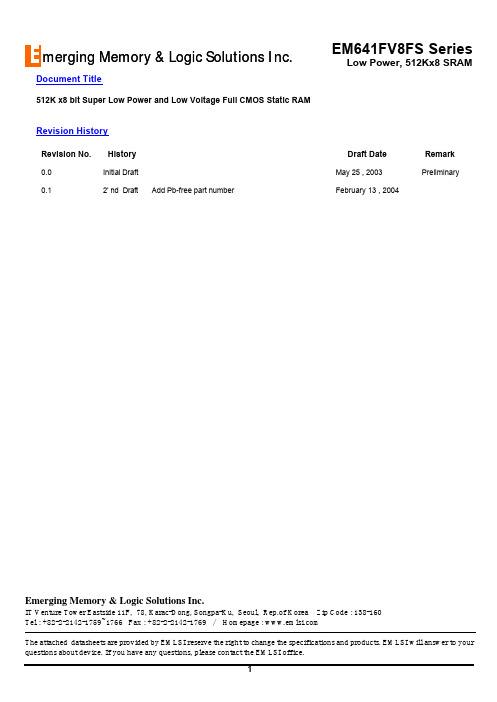
Document Title512K x8 bit Super Low Power and Low Voltage Full CMOS Static RAMRevision HistoryRevision No. History Draft Date Remark0.0Initial Draft May 25 , 2003 Preliminary0.12’nd Draft Add Pb-free part number February 13 , 2004Emerging Memory & Logic Solutions Inc.IT Venture Tower Eastside 11F, 78, Karac-Dong, Songpa-Ku, Seoul, Rep.of Korea Zip Code : 138-160Tel : +82-2-2142-1759~1766 Fax : +82-2-2142-1769 / Homepage : The attached datasheets are provided by EMLSI reserve the right to change the specifications and products. EMLSI will answer to your questions about device. If you have any questions, please contact the EMLSI office.FEATURES•Process Technology : 0.18µm Full CMOS •Organization : 512K x 8 bit•Power Supply Voltage : 2.7V ~ 3.6V •Low Data Retention Voltage : 1.5V(Min)•Three state output and TTL Compatible •Package Type : 32-sTSOP1GENERAL DESCRIPTIONThe EM641FV8FS families are fabricated by EMLSI’s advanced full CMOS process technology. The families support industrial temperature range and Chip Scale Package for user flexibility of system design. The fami-lies also supports low data retention voltage for battery back-up operation with low data retention current.PRODUCT FAMILYProduct Family Operating Temperature Vcc Range SpeedPower DissipationPKG TypeStandby (I SB1, Typ)Operating (I CC1.Max) EM641FV8FSIndustrial (-40 ~ 85o C)2.7V~3.6V551) / 70ns1 µA 2)3 mA32- sTSOP1Name FunctionName FunctionCS Chip select inputs WE Write Enable input O E Output Enable input Vcc Power Supply A 0~A 18Address InputsVssGroundI/O 1~I/O 8 Data Inputs/outputsNC No Connection R o w S e l e c tI/O Circuit Column SelectDataCont Data ContPre-charge CircuitMemory Array 2048 x 2048A 1A 2A 3A 4A 5A 6A 7A 0A 8A 9A 11A 12A 13A 14A 15A 16A 18W E O E C SI/O1 ~ I/O4I/O5 ~ I/O8V C C V SSControl LogicFUNCTIONAL BLOCK DIAGRAM1. The parameter is measured with 30pF test load.A 10A 17PIN DESCRIPTION1234567891011121314151632313029282726252423222120191817A11A9A8A13WE A17A15VCC A18A16A14A12A7A6A5A4OE A10C S IO8I O 7IO6IO5IO4VSS I/O3I/O2I/O1A0A1A2A332 - sTSOP Type1 - Forward2. Typical values are measured at Vcc=3.3V, T A =25o C and not 100% tested.ABSOLUTE MAXIMUM RATINGS *Parameter Symbol Ratings Unit Voltage on Any Pin Relative to Vss V IN, V OUT-0.2 to Vcc+0.3(Max.4.0V)V Voltage on Vcc supply relative to Vss V CC-0.2 to 4.0V V Power Dissipation P D 1.0W Operating Temperature T A-40 to 85o C*Stresses greater than those listed under “Absolute Maximum Ratings” may cause permanent damage to the device. Functional operation should be restricted to recommended operating condition. Exposure to absolute maximum rating conditions for extended periods may affect reliability.FUNCTIONAL DESCRIPTIONCS OE WE I/O Mode PowerH X X High-Z Deselected Stand byL H H High-Z Output Disabled ActiveL L H Data Out Read ActiveL X L Data In Write ActiveNote: X means don’t care. (Must be low or high state)RECOMMENDED DC OPERATING CONDITIONS 1)1. TA= -40 to 85o C, otherwise specified2. Overshoot: V CC +2.0 V in case of pulse width < 20ns4. Overshoot and undershoot are sampled, not 100% tested .ParameterSymbol Min Typ Max Unit Supply voltage V CC 2.7 3.3 3.6V GroundV SS 000V Input high voltage V IH 2.2-V CC + 0.22)V Input low voltageV IL-0.23)-0.6VCAPACITANCE 1) (f =1MHz, T A =25o C)1. Capacitance is sampled, not 100% testedItemSymbol Test ConditionMin Max Unit Input capacitance C IN V IN =0V -8pF Input/Ouput capacitanceC IOV IO =0V-10pFDC AND OPERATING CHARACTERISTICSNOTES1. Typical values are measured at Vcc=3.3V, T A =25o C and not 100% tested.ParameterSymbol Test Conditions Min Typ Max Unit Input leakage current I LI V IN =V SS to V CC-1-1µA Output leakage current I LO CS=V IH or OE =V IH or WE=V IL , V IO =V SS to V CC-1-1µA Operating power supplyI CC I IO =0mA, CS =V IL , V IN =V IH or V IL--3mA Average operating currentI CC1Cycle time=1µs, 100% duty, I IO =0mA,CS<0.2V, V I N <0.2V or V IN >V CC -0.2V--3 mA I CC2Cycle time = Min, I IO =0mA, 100% duty,CS=V IL , V IN =V IL or V IH 55ns --25mA 70ns--20 Output low voltage V OL I OL = 2.1mA --0.4V Output high voltage V OH I O H = -1.0mA2.4--V Standby Current (TTL)I SB CS=V IH , Other inputs=V IH or V IL --0.3mAStandby Current (CMOS)I SB1CS>V CC -0.2V, Other inputs=0~V CC(Typ. condition : V C C =3.3V @ 25o C) (Max. condition : V CC =3.6V @ 85o C)LL LF-11)12µAEM641FV8FS SeriesLow Power, 512Kx8 SRAMmerging Memory & Logic Solutions Inc.ParameterSymbol55ns 70nsUnitMin Max Min Max Read cycle time t RC 55-70-ns Address access time t AA -55-70ns Chip select to outputt co -55-70ns Output enable to valid output t OE -25-35ns Chip select to low-Z output t LZ 10-10-ns Output enable to low-Z output t OLZ 5-5-ns Chip disable to high-Z output t HZ 020025ns Output disable to high-Z output t OHZ 020025ns Output hold from address changet OH10-10-nsParameterSymbol55ns 70nsUnitMin Max Min Max Write cycle timet WC 55-70-ns Chip select to end of write t CW 45-60-ns Address setup timet As 0-0-ns Address valid to end of write t AW 45-60-ns Write pulse width t WP 40-50-ns Write recovery time t WR 0-0-ns Write to ouput high-Z t WHZ 020020ns Data to write time overlap t DW 25 30 ns Data hold from write time t DH 0-0-ns End write to output low-Zt OW5-5-nsREAD CYCLE (V cc =2.7 to 3.6V, Gnd = 0V, T A = -40o C to +85o C)WRITE CYCLE (V cc =2.7 to 3.6V, Gnd = 0V, T A = -40o C to +85o C)AC OPERATING CONDITIONSTest Conditions (Test Load and Test Input/Output Reference)Input Pulse Level : 0.4 to 2.2V Input Rise and Fall Time : 5nsInput and Output reference Voltage : 1.5V Output Load (See right) : CL = 100pF+ 1 TTL CL 1) = 30pF + 1 TTL 1. Including scope and Jig capacitance 2. R 1=3070Ω, R 2=3150Ω3. V TM =2.8VCL 1)V TM 3)R 12)R 22)t AddressCSOEData Outt COt OHt OEHigh-ZTIMING WAVEFORM OF READ CYCLE(2) (WE = V IH )Data ValidOLZt LZAAHZt RCAddresst AA Data Validt OHPrevious Data ValidTIMING WAVEFORM OF READ CYCLE(1). IL IH )Data OutTIMING DIAGRAMSNOTES (READ CYCLE)1. t HZ and t OHZ are defined as the outputs achieve the open circuit conditions and are not referanced to output voltage levels.2. At any given temperature and voltage condition, t HZ (Max.) is less than t LZ (Min.) both for a given device and from device to device interconnection.t WR (4)t WCAddressCSWEData inData outt CW (2)t A Wt WP (1)t AS (3)High-Zt DWt DHHigh-Z t OWt WHZData UndefinedTIMING WAVEFORM OF WRITE CYCLE(1) (WE CONTROLLED)Data Validt WCAddressCSWEData inData outt CW (2)t WR (4)t AW t WP (1)t DWt DHTIMING WAVEFORM OF WRITE CYCLE(2) (CS CONTROLLED)tAS(3)High-Z High-ZData ValidNOTES (WRITE CYCLE)1. A write occurs during the overlap(t WP ) of low CS and low WE. A write begins at the latest transition among CS goes low and WE goes low. A write ends at the earliest transition when CS goes high and WE goes high. The t WP is measured from the beginning of write to the end of write.2. t CW is measured from the CS going low to end of write.3. t AS is measured from the address valid to the beginning of write.4. t WR is measured from the end or write to the address change. t WR applied in case a write ends as CS or WE going high.DATA RETENTION CHARACTERISTICSNOTES1. See the I SB1 measurement condition of datasheet page 4.2. Typical values are measured at T A =25o C and not 100% tested.ParameterSymbolTest ConditionMinTyp 2)MaxUnitV CC for Data Retention V DR I SB1 Test Condition (Chip Disabled) 1)1.5- 3.6V Data Retention CurrentI DR V CC =1.5V, I SB1 Test Condition (Chip Disabled) 1)-0.5-µAChip Deselect to Data Retention Time t SDR See data retention wave form0--nsOperation Recovery Timet RDRt RC--V cc 2.7V2.2V V DR CSGNDDATA RETENTION WAVE FORMCS Controlled13.40+/-0.20Unit : millimeters/InchesPACKAGE DIMENSIONS ( 32-sTSOP1-0813.4F )1. EMLSI Memory2. Device Type3. Density 5. Technology 8. Version 9. Packages 10. Speed7. Orgainzation1. Memory Component2. Device Type6 ------------------------ Low Power SRAM7 ------------------------ STRAM 3. Density1 ------------------------- 1M2 ------------------------- 2M 4 ------------------------- 4M 8 ------------------------- 8M 16 ----------------------- 16M 32 ----------------------- 32M 64 ----------------------- 64M4. Mode Option 0 -------- Dual CS 1 -------- Single CS2 -------- Multiplexed Address3 -------- Single CS with LB,UB (tBA=tOE)4 -------- Single CS with LB,UB (tBA=tCO)5 -------- Dual CS with LB,UB (tBA=tOE)6 -------- Dual CS with LB,UB (tBA=tCO)5. TechnologyBlank ------------------ CMOSF ------------------------ Full CMOS 6. Operating Voltage Blank ------------------- 5VV ------------------------- 2.7V~3.6V U ------------------------- 3.0V S ------------------------- 2.5V R ------------------------- 2.0V P ------------------------- 1.8V4. Option 11. Power 7. Orginzation8 ---------------------- x8 bit 16 ---------------------- x16 bit 32 ---------------------- x32 bit8. VersionBlank ----------------- Mother Die A ----------------------- First revision B ----------------------- Second revision C ----------------------- Third revision D ----------------------- Fourth revision E ----------------------- Fifth revision F ----------------------- Sixth revision 9. PackageBlank ---------------------- FPBGAS ---------------------------- 32 sTSOP1 T ---------------------------- 32 TSOP1 U ---------------------------- 44 TSOP2 W ---------------------------- Wafer10. Speed45 ---------------------- 45ns 55 ---------------------- 55ns 70 ---------------------- 70ns 85 ---------------------- 85ns 10 --------------------- 100ns 12 --------------------- 120ns11. PowerLL ---------------------- Low Low PowerLF ---------------------- Low Low Power (Pb-free) L ---------------------- Low PowerS ---------------------- Standard Power。
亿芯存储器选型手册2010

低速低功耗SRAM 高速SRAM● DRAMSDRAM DDR-ⅠS DRAM DDR-Ⅱ SDRAMMobile SDRAM Mobile DDR-ⅠS DRAM● FLASHNOR FLASH NAND FLASH● EEPROMI2C总线系列 Microwire总线系列 SPI总线系列1 2亿芯伟业来扬包装数量表托盘和管装 Tray and Tube卷带包装 Tape and Reel3 4亿芯伟业力晶半导体股份有限公司—华人地区最大的内存晶圆厂Powerchip Semiconductor Corp.力晶半导体股份有限公司于1994年12月创立于台湾新竹科学园区,业务范围涵盖DRAM 制造、NAND FLASH 闪存制造和晶圆代工三大类别。
目前为全球领先之全方位内存公司,不仅拥有最先进制程技术,更具备世界级水准之产品良率及品质。
自1996年第一座8英寸晶圆厂投入生产,力晶持续投入巨资,扩大生产规模。
2002年第一座12英寸晶圆厂正式量产,2005年第二座12英寸晶圆厂投入生产,2006年力晶花费53亿新台币购入旺宏半导体晶圆三厂,2007年与日本尔必达合资设立的瑞晶电子第一座12英寸晶圆厂启用,2008年开始动工兴建第四、五座12英寸晶圆厂。
一连串购厂、建厂的作为,展现出力晶半导体积极投资、拓展全球市场的决心与行动力。
5 6亿芯伟业产品简介:串行E 2PROM 是可在线电擦除和电写入的存储器,具有体积小、接口简单、数据保存可靠、可在线改写、功耗低等特点,而且为低电压写入,在单片机系统中应用十分普遍。
Aplus 公司的串行E 2PROM 兼容工业上最受欢迎的三种总线:I 2C 总线、Microwire 总线及SPI 总线。
Aplus 公司的产品提供1~256K 的高密度存储,以及1.8V~5.5V 的宽电压操作范围。
产品特性:● 支持标准和快速I 2C 协议、兼容SPI/Microwire 总线 ● 宽工作电压:1.8~5.5V ● 工业级温度范围● 对全部存储器进行硬件写保护 ● 可编程/擦除100万次 ● 数据保存期100年NOR FLASH78亿芯伟业低压差电压稳压器LDO电荷泵白光LED驱动器升压型白光LED驱动器降压型DC/DC转换器锂电池充电电路智能电源开关9 10亿芯伟业时钟电路低速低功耗S R A M 代换表11 12亿芯伟业高速S R A M 代换表DRAM产品代换表13 14亿芯伟业音频放大器的分类音频放大器的目的是以要求的音量和功率水平在发声输出元件上重新产生真实、高效和低失真的输入音频信号。
EM488M1644VBA-75F资料
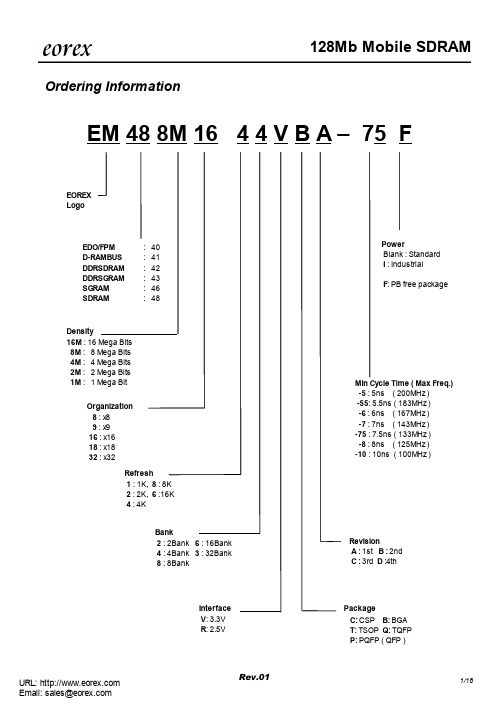
Feature
synchronous to positive clock edge 2.8V~3.6V power supply • Programmable Burst Length (B/ L) - 1,2,4,8 or full page • Programmable CAS Latency (C/ L) - 2 or 3 • Data Mask (DQM) for Read / Write masking • Programmable wrap sequence - Sequential ( B/ L = 1/2/4/8/full page ) - Interleave ( B/ L = 1/2/4/8 ) • Burst read with single-bit write operation • All inputs are sampled at the rising edge of the system clock. • Auto refresh and self refresh • 4,096 refresh cycles / 64ms
6/18
元器件交易网
128Mb Mobile SDRAM
Address Input for Mode Register Set
BA1 BA0 A11
A10
A9
A8
A7
A6
A5
A4
A3 BT
A2
A1
A0
Operation Mode
CAS Latency
Burst Length
1 VSS DQ14 DQ12 DQ10 DQ8 UDQM NC A8 VSS 2 DQ15 DQ13 DQ11 DQ9 NC CLK A11 A7 A5 3 VSSQ VDDQ VSSQ VDDQ VSS CKE A9 A6 A4 7 VDDQ VSSQ VDDQ VSSQ VDD CAS BA0 A0 A3 8 DQ0 DQ2 DQ4 DQ6 LDQM RAS BA1 A1 A2 9 VDD DQ1 DQ3 DQ5 DQ7 WE CS A10 VDD
布德电子产品说明书

17Use on Bud Cabinet Racks: Series 60, Series 2000, ValuRack, Classic II and Economizer. 12 Gauge Steel. Sold in pairs. Rail mounting hardware included. (Uses #7346 equipment mounting screws - order separately.) Finish: BlackMounting RailsChassisSupport BracketsAttaches to panel mounting rail accessory flange, heavy duty 14 ga. steel. Finish: Black. Sold in pairs. Requires two pairs of panel mounting rails per cabinet rack.Catalog No.Length Weight (Lbs.)Cable Management Bracket SetsHeavy gauge steel bracket mounts in any direction with one screw mounting. Package contains six brackets, six 12˝ Velcro cable straps and all mounting hardware. Management panels occupy 1U (1.75˝)of panel space height, and are available for both 19˝ and 23˝ panel widths. Comes complete with 8˝ Velcro cable straps and all mounting hardware. 1.70˝LengthAdapter Bracketchassis support brackets for use on open rack. Package Catalog No.Est. Weight (Lbs.)Catalog No.Style Size (W × L)Wt. Oz.CMS-2218-BB.75˝ × 18.00˝4.6CableManagement StrapsVelcro cable straps in two styles. Comes in packages of 25 straps. Color: BlackStyle AStyle BCatalog No.18Panel ExtenderHeavy gauge steel brackets extend panels 5.00˝ beyond normal panel mounting rails. Panel mounting holes on EIAuniversal spacing. Finish: Black. Sold in pairs. Includes all mounting hardware.racks. Heavy gauge steel Available in Black. Includes all Cable BracketHeavy gauge steel brackets occupy 1U (1.75˝) of panel space. Finish: Black. Includes all mounting hardware.Cable Management Designed for 19˝ panel width racks. Heavy 18 gauge formed steelpanel, with twelve plastic cable clips. Finish: Black. Includes all mounting hardware. Accessories: Additional plastic cable clips catalog No. CM-1229. Twelve clips per package.Cable Management PanelDesigned for 19˝ panel width racks. Heavy 18 gauge formed steel panel withtwenty-four plastic cable clips and three CM-1220 cable rings. Finish: Black. Includes all mounting hardware. Accessories: Additional plastic cable clips catalog No. CM-1229. Twelve clips per package.Cableway CoverFormed steel covers mount to the front and rear of cableway rings to protect cables and present afinished look to your cabling installation. Finish: Black. Used on 7’ tall open racks. Sold in pairs. Includes all mounting hardware.Equipment Tie Down BracketHeavy gauge steel bracket, in 19˝ panel width, will secure your equipment within open or enclosed cabinet racks. Frontpanels are 1U (1.75˝) high.Black Texture (BT) or Metallic Gray (MG) Includes all mounting hardware.Catalog No.Panel HeightEst. Weight Lbs.PE-1600 3.50˝1Catalog No.Size (W × D)Est. Weight Lbs.Catalog No.Size (W × D)Est. Weight Lbs.Catalog No.Size (H × W)Est. Weight Lbs.CM-12273.50˝ × 19.00˝3Catalog No.Size (W × D)Est. Weight Lbs.CM-12231.75˝ × 3.50˝1See our online rack and accessory selector guide at /rackguide.htmlCable ManagementSnap-in spring steel cableclips available in two sizes.In packages of 3 clips.AdapterMountingBrackets16-gauge steelbrackets used formounting 19˝ wideequipment into open rackswith 23˝ and 24˝ wide panel spaces and enclosed cabinet rackswith 24˝ wide panel spaces. Mounting hole locations conform to EIAspecs. Finish is Black Texture (BT). Comes complete with all mountingAllows for the organizationand protection of cables onslide-mounted equipment.Mounts to panel mountingrail at rear of cabinet rack,and can be used on both theleft and right sides of thecabinet. Wide support arms allow for the use of either ribbon cableStationaryKeyboard/MouseShelfHeavy gauge steel shelfmounts to any 19˝ panelwidth open rack. Comeswith 9.00˝ × 7.00˝ mousetray that can be bolted on to either the left or right hand side of theshelf. Takes up 1U (1.75˝) of panel space. Finish: Black Texture (BT) orMetallic Gray (MG). Includes all mounting hardware.gauge steel shelf mountsto any 19˝ or 23˝ panelwidth open rack. Includes4.00˝ high × 10.50˝ wideintegrated switch box compartment.Finish: BlackTexture (BT) or Metallic Gray (MG). Includes allmounting hardware.Sliding Keyboard/Mouse ShelfSliding keyboard shelf fits19˝ and 23˝ panel widthracks. Mouse pad slides outfrom underneath the shelf ineither the right or left side.Takes up 2U (3.50˝) of panel space. Overalldepth: 12.50˝. Black Texture (BT) orMetallic Gray (MG). Includes all mounting hardware.Catalog No.Size (W × D)Weight Lbs.CM-2220.56˝ × 3.75˝.5See our online rack andaccessory selector guide at/rackguide.html19。
集成电路英文代码对照

集成电路英文代码及中文对照〔一〕我的文摘2021-11-21 11:32:53 阅读111 评论0 字号:大中小订阅产品名称型号规格性能说明LMLM24J 四运放(军用级)LM148J 通用四运放LM1875T 无线电控制/接收器LM224J 四运放(工业级)LM258N 别离式双电源双运放LM2901N 四电压比拟器LM2904N 四运放LM301AN 通用运算放大器LM308N 单比拟器LM311P 单比拟器LM317L 可调三端稳压器/100mALM317TLM317K 可调三端稳压器/3ALM318 高速宽带运放LM324K 通用四运放LM331N V-F/F-V转换器基准电压电路LM336 5V 基准电压电路LM337T 基准电压电路1ALM338K 可调三端稳压器5ALM339N 四比拟器LM348N 四741运放LM358N 低功耗双运放LM361N 高速差动比拟器LM386N 声频功率放大器LM3914N 十段点线显示驱动LM393N 低功耗低失调双比拟器LM399H 精细基准源(6.9)LM723CN 可调正式负稳压器LM733CN 视频放大器LM741J 单运放LM741CN 双运放NENE521 高速双差分比拟器NE5532 双运放NE5534 双运放NE555N 单运放NE555J 时基电路军品极NE556 双级型双时基电路NE564 锁相环NE565 锁相环NE567 音调译码器NE592 视频放大器OPOP07 低噪声运放OP27 超低噪声精细运放OP37 超低噪声精细运放光电耦合4N25 晶体管输出4N25MC 晶体管输出4N26 晶体管输出4N27 晶体管输出4N28 晶体管输出4N29 达林顿输出4N30 达林顿输出4N31 达林顿输出4N32 达林顿输出4N33 达林顿输出4N33MC 达林顿输出4N35 达林顿输出4N36 晶体管输出4N37 晶体管输出4N38 晶体管输出4N39 可控硅输出6N135 高速光耦晶体管输出6N136 高速光耦晶体管输出6N137 高速光耦晶体管输出6N138 达林顿输出6N139 达林顿输出MOC3020 可控硅驱动输出MOC3021 可控硅驱动输出MOC3023 可控硅驱动输出MOC3030 可控硅驱动输出MOC3040 过零触发可控硅输出MOC3041 过零触发可控硅输出MOC3061 过零触发可控硅输出MOC3081 过零触发可控硅输出TLP521-1 单光耦TLP521-2 双光耦TLP521-4 四光耦TLP621 四光耦TIL113 达林顿输出TIL117 TLL逻辑输出PC814 单光耦PC817 单光耦H11A2 晶体管输出H11D1 高压晶体管输出H11G2 电阻达林顿输出LFLF347N 宽带JFET输入四运放LF351N 宽带JFET输入运放LF353N JFET输入宽带运放LF355N JFET输入运放LF357N JFET宽带非全裣运放LF398N 采样/保持电路LF412N 低偏向飘移输入运放MCMC1377 彩色电视编码器MC1403 精细电压基准源(2.5)MC1413 周边七段驱动阵列MC1416 周边七段驱动陈列MC14409 二进制脉冲拨号器MC14433 3位半A/D转换器MC14489 多字符LED显示驱动器MC145026 编码器VD5026 编码器MC145027 译码器VD5027 译码器MC145028 译码器MC145030 编码译码器MC145106 频率合成器MC145146 4位数据总线TLTL062 低功耗JEFT输入双运放TL072 低噪声JEFTTL082TL084TL431TL494ULNULN2003 周边七段驱动陈列ULN2004 周边七段驱动陈列ULN2803 周边八段驱动陈列ULN2804 周边八段驱动陈列ICLICL7106 3位ADC/驱动LCDICL7107 3位半ADC/驱动LEDICL7109 4位半ADC/驱动LEDICL7129 4位半ADC/LCD驱动ICL7135 ADC/LCD驱动BCD输出ICL7136 3位半CMOSADC/LCD驱动ICL7218 CMOS低功耗运算放大器ICL7650 整零运放斩波ICL7652 整零运放斩波ICL7660 CMOS直流-直流转换器ICL8038 函数信号发生器ICL8049 反对数放大器CACA3140 单BIMOS运行CA3240 单BIMOS运行UCUC3842 WM电流型控制器UC3845 PWM电流型控制器DSDS12887 非易失实时时钟芯片L3845 中继接口电路SGSG3524 PWM解调调制器SG3525 PWM解调调制器20216 前置放大器MTMT8814 8x12模拟交换矩阵MT8816 8x模拟交换矩阵MT8870 综合DTMF接收器MT8870 综合DTMF接收器MT8880 综合DTMF发生接收器MIC24LC01 128x8串行EEPROM24LC02 256x8串行EEPROM24LC04 512x8串行EEPROM24LC16 2Kx8串行EEPROM93LC46 64x16串行EEPROM93LC56 256x16串行EEPROM93LC66 512x8 256x16 EEPROMPIC16C52 384x12 单片机PIC16C54 512x12 单片机PCI16C56 512x12 单片机PIC16C57 2048x12 单片机ATAT24C01 128x8串行EEPROMAT24C02 256x8串行EEPROMAT24C04 512x8串行EEPROMAT24C16 2Kx8串行EEPROMAT93C46 64x16串行EEPROMAT93C56 256x16串行EEPROMATF16V8 FLASH200门ATF20V8 FLASH300门高速ATF22V10 FLASH500门高速低电流AT28C16 2Kx8CMOS并行EEPROMAT28C17 2Kx8CMOS并行EEPROMAT28C64 8Kx8并行EEPROMAT28C256 32Kx8并行EEPROMAT28F010 128Kx8并行EEPROMA29C040 512Kx8 FLASH EEPROMHM6116 2Kx8 CMOS 静态PAMHY6264 8Kx8 CMOS 静态RAMHM6264 8Kx8 CMOS 静态RAMIS62C64 8Kx8 高速CMOS 静态RAMHY62256 32Kx8 CMOS 静态RAMHM62256 32Kx8 CMOS 静态RAMHM628128 128Kx8 CMOS 静态RAMHM628256 256Kx8 CMOS 静态RAMHM628512 512Kx8 CMOS 静态RAMHM628512 512Kx8 CMOS 静态RAM TCMTCM5087 双音调发生器MM5832 实时钟电路TCTC14433 3位半A/D转换器TC232 并行/串行接口电路TC7106 3位半ADC/LCD驱动TC7107 3位半ADC/LED驱动TC7116 3位半ADC/LCD驱动带保TC7129 4位半ADC/LCDTC7135 4位半ADC/LCD,BCD输出TC7650 整零运放斩波7575107 四差分线驱动器75174 四差分线驱动器75175 三态四差分接收器75176 差分总线接收器75188 四线驱动器75189 四线驱动器75451 双外围驱动器75452 双外围驱动器集成电路英文代码及中文对照〔二〕我的文摘2021-11-21 11:37:11 阅读191 评论0 字号:大中小订阅。
- 1、下载文档前请自行甄别文档内容的完整性,平台不提供额外的编辑、内容补充、找答案等附加服务。
- 2、"仅部分预览"的文档,不可在线预览部分如存在完整性等问题,可反馈申请退款(可完整预览的文档不适用该条件!)。
- 3、如文档侵犯您的权益,请联系客服反馈,我们会尽快为您处理(人工客服工作时间:9:00-18:30)。
3 A B C D E F G H J
7 VDDQ VSSQ VDDQ VSSQ VDD /CAS BA0 A0 A3 DQ0 DQ2 DQ4 DQ6
8 VDD DQ1 DQ3 DQ5 DQ7 /WE /CS A10 VDD
9
LDQM /RAS BA1 A1 A2
54ball TFBGA / (8mm × 8mm)
Recommended DC Operating Conditions (TA=0°C ~70°C)
Symbol VDD VDDQ VIH Parameter Power Supply Voltage Power Supply Voltage (for I/O Buffer) Input Logic High Voltage Min. 1.65 1.65 0.8*VDD -0.3 Typ. 1.8 1.8 Max. 1.95 1.95 VDD+0.3 0.3 Units V V V V
F3
CKE
H7,H8,J8,J7,J3, J2,H3,H2,H1,G3, H9,G2
A0~A11
G7,G8 F8
BA0, BA1 /RAS
F7
/CAS
F9 F1/E8 A8,B9,B8,C9,C8, D9,D8,E9,E1,D2, D1,C2,C1,B2,B1, A2 A9,E7,J9/ A1,E3,J1 A7,B3,C7,D3/ A3,B7,C3,D7 E2,G1
May. 2007 2/19
元器件交易网
eorex
Pin F2 G9 Name CLK /CS
Preliminary
EM488M1644LBB
Pin Description (Simplified)
Function (System Clock) Master clock input (Active on the positive rising edge) (Chip Select) Selects chip when active (Clock Enable) Activates the CLK when “H” and deactivates when “L”. CKE should be enabled at least one cycle prior to new command. Disable input buffers for power down in standby. (Address) Row address (A0 to A11) is determined by A0 to A11 level at the bank active command cycle CLK rising edge. CA (CA0 to CA8) is determined by A0 to A8 level at the read or write command cycle CLK rising edge. And this column address becomes burst access start address. A10 defines the pre-charge mode. When A10= High at the pre-charge command cycle, all banks are pre-charged. But when A10= Low at the pre-charge command cycle, only the bank that is selected by BA0/BA1 is pre-charged. (Bank Address) Selects which bank is to be active. (Row Address Strobe) Latches Row Addresses on the positive rising edge of the CLK with /RAS “L”. Enables row access & pre-charge. (Column Address Strobe) Latches Column Addresses on the positive rising edge of the CLK with /CAS low. Enables column access. (Write Enable) Latches Column Addresses on the positive rising edge of the CLK with /CAS low. Enables column access. (Data Input/Output Mask) DQM controls I/O buffers. (Data Input/Output) DQ pins have the same function as I/O pins on a conventional DRAM. (Power Supply/Ground) VDD and VSS are power supply pins for internal circuits. (Power Supply/Ground) VDDQ and VSSQ are power supply pins for the output buffers. (No Connection) This pin is recommended to be left No Connection on the device.
/WE UDQM/LDQM
DQ0~DQ15
VDD/VSS VDDQ/VSSQ NC
May. 2007 3/19
元器件交易网
eorex
Absolute Maximum Rating
Symbol VIN, VOUT VDD, VDDQ TOP TSTG PD
Ordering Information
Part No
EM488M1644LBB-75F EM488M1644LBB-75FE
Organization
8M X 16 8M X 16
Max. Freq
133MHz @CL3 133MHz @CL3
Package
TFBGA -54B TFBGA -54B
元器件交易网
eorex
Features
Preliminary
EM488M1644LBB
128Mb (2M×4Bank×16) Synchronous DRAM
Description
The EM488M1644LBB is Synchronous Dynamic Random Access Memory (SDRAM) organized as 2Meg words x 4 banks by 16 bits. All inputs and outputs are synchronized with the positive edge of the clock. The 128Mb SDRAM uses synchronized pipelined architecture to achieve high speed data transfer rates and is designed to operate at 1.8V low power memory system. It also provides auto refresh with power saving / down mode. All inputs and outputs voltage levels are compatible with LVCMOS. Available packages: TFBGA-54B(8mmx8mm)
Capacitance (VCC=3.3V, f=1MHz, TA=25°C)
Symbol CCLK CI CO Parameter Clock Capacitance Input Capacitance for CLK, CKE, Address, /CS, /RAS, /CAS, /WE, DQML, DQMU Input/Output Capacitance Min. 2 2 3 Typ. Max. 4 4 5 Units pF pF pF
Preliminary
EM488M1644LBB
Item Input, Output Voltage Power Supply Voltage Operating Temperature Range Storage Temperature Range Power Dissipation
Rating -1 ~ +2.6 -1 ~ +2.6 Commercial 0 ~ +70 Extended -25 ~ +85 -55 ~ +150 1
• Fully Synchronous to Positive Clock Edge • Single 1.8V ±0.1V Power Supply • LVCMOS Compatible with Multiplexed Address •Programmable Burst Length –1/2/4/8/ full Page • Programmable CAS Latency (C/L) - 2 or 3 • Data Mask (DQM) for Read / Write Masking • Programmable Wrap Sequence – Sequential (B/L = 1/2/4/8/full Page) – Interleave (B/L = 1/2/4/8) • Burst Read with Single-bit Write Operation • Deep Power Down Mode. • Auto Refresh and Self Refresh • Special Function Support. – PASR (Partial Array Self Refresh) – Auto TCSR (Temperature Compensated Self Refresh) • Programmable Driver Strength Control – Full Strength or 1/2, 1/4 of Full Strength • 4,096 Refresh Cycles / 64ms (15.625us)