REC5-053.3SRWZH6SMD中文资料
905中文说明书

3.3 3.3.1 3.3.2 3.3.3
连接 MSB 设备 ..................................................................... 12 连接配液器 .......................................................................... 13 连接搅拌器或滴定台 ........................................................... 13 安装遥控盒 .......................................................................... 14
8.4 电磁兼容性(EMC) ............................................................ 34
8.5 环境温度 ............................................................................... 34
905 Titrando
■■■■■■■■ III
目录
■■■■■■■■■■■■■■■■■■■■■■
3.5.6 连接 iConnect ....................................................................... 23 3.5.7 电位差计 .............................................................................. 24
常用三极管参数大全
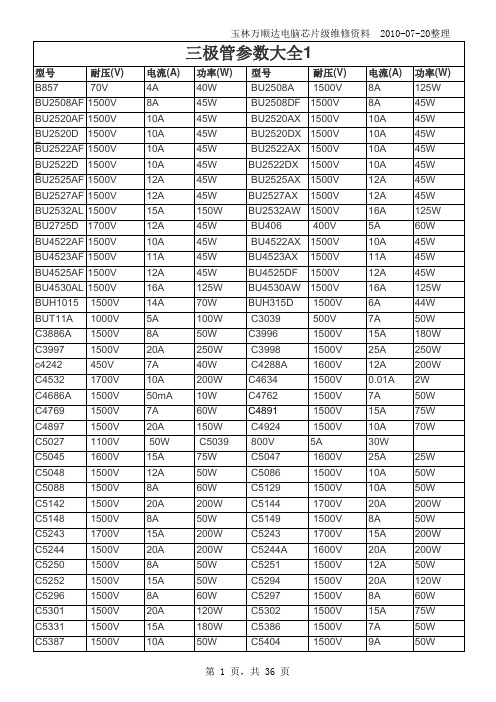
玉林万顺达电脑芯片级维修资料 2010-07-20整理玉林万顺达电脑芯片级维修资料 2010-07-20整理玉林万顺达电脑芯片级维修资料 2010-07-20整理玉林万顺达电脑芯片级维修资料 2010-07-20整理玉林万顺达电脑芯片级维修资料 2010-07-20整理玉林万顺达电脑芯片级维修资料 2010-07-20整理玉林万顺达电脑芯片级维修资料 2010-07-20整理玉林万顺达电脑芯片级维修资料 2010-07-20整理玉林万顺达电脑芯片级维修资料 2010-07-20整理玉林万顺达电脑芯片级维修资料 2010-07-20整理玉林万顺达电脑芯片级维修资料 2010-07-20整理玉林万顺达电脑芯片级维修资料 2010-07-20整理玉林万顺达电脑芯片级维修资料 2010-07-20整理玉林万顺达电脑芯片级维修资料 2010-07-20整理玉林万顺达电脑芯片级维修资料 2010-07-20整理玉林万顺达电脑芯片级维修资料 2010-07-20整理玉林万顺达电脑芯片级维修资料 2010-07-20整理玉林万顺达电脑芯片级维修资料 2010-07-20整理玉林万顺达电脑芯片级维修资料 2010-07-20整理玉林万顺达电脑芯片级维修资料 2010-07-20整理玉林万顺达电脑芯片级维修资料 2010-07-20整理玉林万顺达电脑芯片级维修资料 2010-07-20整理玉林万顺达电脑芯片级维修资料 2010-07-20整理玉林万顺达电脑芯片级维修资料 2010-07-20整理玉林万顺达电脑芯片级维修资料 2010-07-20整理玉林万顺达电脑芯片级维修资料 2010-07-20整理玉林万顺达电脑芯片级维修资料 2010-07-20整理玉林万顺达电脑芯片级维修资料 2010-07-20整理玉林万顺达电脑芯片级维修资料 2010-07-20整理玉林万顺达电脑芯片级维修资料 2010-07-20整理。
W39V080APZ资料

W39V080A Data Sheet1M × 8 CMOS FLASH MEMORYWITH LPC INTERFACE Table of Contents-1.GENERAL DESCRIPTION (3)2.FEATURES (3)3.PIN CONFIGURATIONS (4)4.BLOCK DIAGRAM (4)5.PIN DESCRIPTION (4)6.FUNCTIONAL DESCRIPTION (5)6.1Interface Mode Selection and Description (5)6.2Read (Write) Mode (5)6.3Reset Operation (5)6.4Boot Block Operation and Hardware Protection at Initial- #TBL & #WP (5)6.5Sector Erase Command (6)6.6Program Operation (6)6.7Dual BIOS (6)6.8Hardware Data Protection (6)6.9Write Operation Status (7)7.TABLE OF OPERATING MODES (10)7.1Operating Mode Selection - Programmer Mode (10)7.2Operating Mode Selection - LPC Mode (10)7.3Standard LPC Memory Cycle Definition (10)8.TABLE OF COMMAND DEFINITION (11)8.1Embedded Programming Algorithm (12)8.2Embedded Erase Algorithm (13)8.3Embedded #Data Polling Algorithm (14)8.4Embedded Toggle Bit Algorithm (15)8.5Software Product Identification and Boot Block Lockout Detection Acquisition Flow..169.DC CHARACTERISTICS (17)9.1Absolute Maximum Ratings (17)9.2Programmer interface Mode DC Operating Characteristics (17)9.3LPC interface Mode DC Operating Characteristics (18)9.4Power-up Timing (18)10.CAPACITANCE (18)11.PROGRAMMER INTERFACE MODE AC CHARACTERISTICS (19)Publication Release Date: Dec. 28, 2005W39V080A11.1AC Test Conditions (19)11.2AC Test Load and Waveform (19)11.3Read Cycle Timing Parameters (20)11.4Write Cycle Timing Parameters (20)11.5Data Polling and Toggle Bit Timing Parameters (20)12.TIMING WAVEFORMS FOR PROGRAMMER INTERFACE MODE (21)12.1Read Cycle Timing Diagram (21)12.2Write Cycle Timing Diagram (21)12.3Program Cycle Timing Diagram (22)12.4#DATA Polling Timing Diagram (22)12.5Toggle Bit Timing Diagram (23)12.6Sector Erase Timing Diagram (23)13.LPC INTERFACE MODE AC CHARACTERISTICS (24)13.1AC Test Conditions (24)13.2Read/Write Cycle Timing Parameters (24)13.3Reset Timing Parameters (24)14.TIMING WAVEFORMS FOR LPC INTERFACE MODE (25)14.1Read Cycle Timing Diagram (25)14.2Write Cycle Timing Diagram (25)14.3Program Cycle Timing Diagram (26)14.4#DATA Polling Timing Diagram (27)14.5Toggle Bit Timing Diagram (28)14.6Sector Erase Timing Diagram (29)14.7GPI Register/Product ID Readout Timing Diagram (30)14.8Reset Timing Diagram (30)15.ORDERING INFORMATION (31)16.HOW TO READ THE TOP MARKING (31)17.PACKAGE DIMENSIONS (32)17.132L PLCC (32)17.232L STSOP (8x14mm) (32)17.340L TSOP (10 mm x 20 mm) (33)18.VERSION HISTORY (34)W39V080APublication Release Date: Dec. 28, 20051. GENERAL DESCRIPTIONThe W39V080A is an 8-megabit, 3.3-volt only CMOS flash memory organized as 1M × 8 bits. For flexible erase capability, the 8Mbits of data are divided into 16 uniform sectors of 64 Kbytes. The device can be programmed and erased in-system with a standard 3.3V power supply. A 12-volt VPP is required for accelerated program. The unique cell architecture of the W39V080A results in fast program/erase operations with extremely low current consumption. This device can operate at two modes, Programmer bus interface mode and LPC bus interface mode. As in the Programmer interface mode, it acts like the traditional flash but with a multiplexed address inputs. But in the LPC interface mode, this device complies with the Intel LPC specification. The device can also be programmed and erased using standard EPROM programmers.2. FEATURESy Single 3.3-volt operations: − 3.3-volt Read − 3.3-volt Erase − 3.3-volt Programy Fast Program operation:− VPP = 12V− Byte-by-Byte programming: 9 μS (typ.)y Fast Erase operation:− Sector erase 0.9 Sec. (tpy.) y Fast Read access time: Tkq 11 nS y Endurance: 30K cycles (typ.) y Twenty-year data retention y 16 Even sectors with 64K bytes y Any individual sector can be erased y Dual BIOS function− Full-chip Partition with 8M-bit or Dual-block Partition with 4M-bit y Hardware protection:− #TBL supports 64-Kbyte Boot Blockhardware protection− #WP supports the whole chip except Boot Block hardware protectiony Ready/#Busy output (RY/#BY)− Detect program or erase cycle completion y Hardware reset pin (#RESET)− Reset the internal state machine to the read mode y VPP input pin− Acceleration (ACC) function accelerates program timingy Low power consumption− Read Active current: 15 mA (typ. for LPC mode)y Automatic program and erase timing withinternal V PP generation y End of program or erase detection − Toggle bit − Data pollingy Latched address and data y TTL compatible I/Oy Available packages: 32L PLCC, 32L STSOP,40L TSOP(10 x 20 mm), 32L PLCC Lead free, 32L STSOP Lead free and 40L TSOP (10 x 20 mm) Lead freeW39V080A3. PIN CONFIGURATIONS4. BLOCK DIAGRAM5. PIN DESCRIPTIONINTERFACESYM.PGM LPCPIN NAMEMODE * *Interface Mode Selection #RESET * *Reset #INIT *Initialize#TBL *Top Boot Block Lock #WP *Write Protect CLK *CLK InputGPI[4:0] *General Purpose Inputs ID[3:0] *Identification InputsPull Down with Internal ResistorsLAD[3:0] *Address/Data Inputs #LFRAME *LPC Cycle InitialD/#F *Dual Bios/Full ChipPull Down with Internal Resistors U/#L *Upper 4M/Lower 4MPull Down with Internal ResistorsR/#C * Row/Column Select A[10:0]* Address Inputs DQ[7:0]* Data Inputs/Outputs #OE * Output Enable #WE * Write Enable RY/#BY * Ready/Busy VDD * *Power Supply VSS * *Ground RSV * *Reserve Pins NC * *No ConnectionW39V080A6. FUNCTIONAL DESCRIPTION6.1 Interface Mode Selection and DescriptionThis device can be operated in two interface modes, one is Programmer interface mode, and the other is LPC interface mode. The MODE pin of the device provides the control between these two interface modes. These interface modes need to be configured before power up or return from #RESET. When MODE pin is set to high position, the device is in the Programmer mode; while the MODE pin is set to low position, it is in the LPC mode. In Programmer mode, this device just behaves like traditional flash parts with 8 data lines. But the row and column address inputs are multiplexed. The row address is mapped to the higher internal address A[19:11]. And the column address is mapped to the lower internal address A[10:0]. For LPC mode, It complies with the LPC Interface Specification Revision 1.1 Through the LAD[3:0] and #LFRAME to communicate with the system chipset .6.2 Read (Write) ModeIn Programmer interface mode, the read(write) operation of the W39V080A is controlled by #OE (#WE). The #OE (#WE) is held low for the host to obtain (write) data from(to) the outputs(inputs). #OE is the output control and is used to gate data from the output pins. The data bus is in high impedance state when #OE is high. As in the LPC interface the “bit 1 of CYCLE TYPE+DIR” determines mode, the read or write. Refer to the timing waveforms for further details.6.3 Reset OperationThe #RESET input pin can be used in some application. When #RESET pin is at high state, the device is in normal operation mode. When #RESET pin is at low state, it will halt the device and all outputs will be at high impedance state. As the high state re-asserted to the #RESET pin, the device will return to read or standby mode, it depends on the control signals.6.4 Boot Block Operation and Hardware Protection at Initial- #TBL & #WPThere is a hardware method to protect the top boot block and other sectors. Before power on programmer, tie the #TBL pin to low state and then the top boot block will not be programmed/erased. If #WP pin is tied to low state before power on, the other sectors will not be programmed/erased.In order to detect whether the boot block feature is set on or not, users can perform software command sequence: enter the product identification mode (see Command Codes for Identification/Boot Block Lockout Detection for specific code), and then read from address FFFF2(hex). You can check the DQ2/DQ3 at the address FFFF2 to see whether the #TBL/#WP pin is in low or high state. If the DQ2 is “0”, it means the #TBL pin is tied to high state. In such condition, whether boot block can be programmed/erased or not will depend on software setting. On the other hand, if the DQ2 is “1”, it means the #TBL pin is tied to low state, then boot block is locked no matter how the software is set. Like the DQ2, the DQ3 inversely mirrors the #WP state. If the DQ3 is “0”, it means the #WP pin is in high state, then all the sectors except the boot block can be programmed/erased. On the other hand, if the DQ3 is “1”, then all the sectors except the boot block are programmed/erased inhibited.To return to normal operation, perform a three-byte command sequence (or an alternate single-byte command) to exit the identification mode. For the specific code, see Command Codes for Identification/Boot Block Lockout Detection.Publication Release Date: Dec. 28, 2005W39V080A6.5 Sector Erase CommandSector erase is a six-bus cycles operation. There are two "unlock" write cycles, followed by writing the "set-up" command. Two more "unlock" write cycles then follows by the Sector erase command. The Sector address (any address location within the desired Sector) is latched on the rising edge of R/#C in programmer mode, while the command (30H) is latched on the rising edge of #WE.Sector erase does not require the user to program the device prior to erase. When erasing a Sector, the remaining unselected sectors are not affected. The system is not required to provide any controls or timings during these operations.The automatic Sector erase begins after the erase command is completed, right from the rising edge of the #WE pulse for the last Sector erase command pulse and terminates when the data on DQ7, Data Polling, is "1" at which time the device returns to the read mode. Data Polling must be performed at an address within any of the sectors being erased.Refer to the Erase Command flow Chart using typical command strings and bus operations.6.6 Program OperationThe W39V080A is programmed on a byte-by-byte basis. Program operation can only change logical data "1" to logical data "0." The erase operation, which changed entire data in main memory and/or boot block from "0" to "1", is needed before programming.The program operation is initiated by a 4-byte command cycle (see Command Codes for Byte Programming). The device will internally enter the program operation immediately after the byte-program command is entered. The internal program timer will automatically time-out (9μS typ. - T BP) once it is completed and then return to normal read mode. Data polling and/or Toggle Bits can be used to detect end of program cycle.6.7 Dual BIOSThe W39V080A provides a solution for Dual-BIOS application. In LPC mode, when D/#F is low, the device functions as a full-chip partition of 8M-bit which address ranges from FFFFFh to 00000h with A[19:0]. If D/#F is driven high, the device functions as a dual-block partition that each block consists of 4M-bit. For dual-block partition, there is only one 4M-bit block, either upper or lower, can be accessed. The U/#L pin selects either upper or lower 4M-bit block and its address ranges from 7FFFFh to 00000h with A[19:0]. When U/#L is low, the lower 4M-bit block will be selected; while, U/#L is high, the upper 4M-bit block will be selected.6.8 Hardware Data ProtectionThe integrity of the data stored in the W39V080A is also hardware protected in the following ways:(1) Noise/Glitch Protection: A #WE pulse of less than 15 nS in duration will not initiate a write cycle.(2) V DD Power Up/Down Detection: The programming and read operation are inhibited when V DD isless than 2.0V typical.(3) Write Inhibit Mode: Forcing #OE low or #WE high will inhibit the write operation. This preventsinadvertent writes during power-up or power-down periods.W39V080APublication Release Date: Dec. 28, 20056.9 Write Operation StatusThe device provides several bits to determine the status of a program or erase operation: DQ5, DQ6, and DQ7. Each of DQ7 and DQ6 provides a method for determining whether a program or erase operation is complete or in progress. The device also offers a hardware-based output signal, RY/#BY in programmer mode, to determine whether an Embedded Program or Erase operation is in progress or has been completed.DQ7: #Data PollingThe #Data Polling bit, DQ7, indicates whether an Embedded Program or Erase algorithm is in progress or completed. Data Polling is valid after the rising edge of the final #WE pulse in the command sequence.During the Embedded Program algorithm, the device outputs on DQ7 and the complement of the data programmed to DQ7. Once the Embedded Program algorithm has completed, the device outputs the data programmed to DQ7. The system must provide the program address to read valid status information on DQ7. If a program address falls within a protected sector, #Data Polling on DQ7 is active for about 1 S, and then the device returns to the read mode. During the Embedded Erase algorithm, #Data Polling produces “0” on DQ7. Once the Embedded Erase algorithm has completed, #Data Polling produces “1” on DQ7. An address within any of the sectors selected for erasure must be provided to read valid status information on DQ7.After an erase command sequence is written, if all sectors selected for erasing are protected, #Data Polling on DQ7 is active for about 100S, and then the device returns to the read mode. I f not all selected sectors are protected, the Embedded Erase algorithm erases the unprotected sectors, and ignores the selected sectors that are protected. However, if the system reads DQ7 at an address within a protected sector, the status may not be valid.Just before the completion of an Embedded Program or Erase operation, DQ7 may change asynchronously with DQ0-DQ6 while Output Enable (#OE) is set to low. That is, the device may change from providing status information to valid data on DQ7. Depending on when it samples the DQ7 output, the system may read the status or valid data. Even if the device has completed the program or erase operation and DQ7 has valid data, the data outputs on DQ0-DQ6 may be still invalid. Valid data on DQ7-DQ0 will appear on successive read cycles.RY/#BY: Ready/#BusyThe RY/#BY is a dedicated, open-drain output pin which indicates whether an Embedded Algorithm is in progress or complete. The RY/#BY status is valid after the rising edge of the final #WE pulse in the command sequence. Since RY/#BY is an open-drain output, several RY/#BY pins can be tied together in parallel with a pull-up resistor to VDD.When the output is low (Busy), the device is actively erasing or programming. When the output is high (Ready), the device is in the read mode or standby mode.DQ6: Toggle Bit IToggle Bit I on DQ6 indicates whether an Embedded Program or Erase algorithm is in progress or complete. Toggle Bit I may be read at any address, and is valid after the rising edge of the final #WE pulse in the command sequence (before the program or erase operation), and during the sector erase time-out.During an Embedded Program or Erase algorithm operation, successive read cycles to any address cause DQ6 to toggle. The system may use either #OE to control the read cycles. Once the operation has completed, DQ6 stops toggling.W39V080A After an erase command sequence is written, if all sectors selected for erasing are protected, DQ6 toggles for about 100 S, and then returns to reading array data. If not all selected sectors are protected, the Embedded Erase algorithm erases the unprotected sectors, and ignores the selected sectors which are protected.The system can use DQ6 to determine whether a sector is actively erasing. If the device is actively erasing (i.e., the Embedded Erase algorithm is in progress), DQ6 toggles. If a program address falls within a protected sector, DQ6 toggles for about 1 μS after the program command sequence is written, and then returns to reading array data.Reading Toggle Bits DQ6Whenever the system initially starts to read toggle bit status, it must read DQ7-DQ0 at least twice in a row to determine whether a toggle bit is toggling or not. Typically, the system would note and store the value of the toggle bit after the first read. While after the second read, the system would compare the new value of the toggle bit with the first one. If the toggle bit is not toggling, the device has completed the program or erase operation. The system can read array data on DQ7-DQ0 on the following read cycle.However, if after the initial two read cycles, the system finds that the toggle bit is still toggling, the system also should note whether the value of DQ5 is high or not(see the section on DQ5). If DQ5 is high, the system should then determine again whether the toggle bit is toggling or not, since the toggle bit may have stopped toggling just as DQ5 went high. If the toggle bit is no longer toggling, the device has successfully completed the program or erase operation. If it is still toggling, the device did not completed the operation, and the system must write the reset command to return to reading array data.Then the system initially determines that the toggle bit is toggling and DQ5 has not gone high. The system may continue to monitor the toggle bit and DQ5 through successive read cycles, and determines the status as described in the previous paragraph. Alternatively, the system may choose to perform other system tasks. In this case, the system must start at the beginning of the algorithm while it returns to determine the status of the operation.DQ5: Exceeded Timing LimitsDQ5 indicates whether the program or erase time has exceeded a specified internal pulse count limit. DQ5 produces “1” under these conditions which indicates that the program or erase cycle was not successfully completed.The device may output “1” on DQ5 if the system tries to program “1” to a location that was previously programmed to “0.” Only the erase operation can change “0” back to “1.” Under this condition, the device stops the operation, and while the timing limit has been exceeded, DQ5 produces “1.”Under both these conditions, the system must hardware reset to return to the read mode. REGISTERThere are two kinds of registers on this device, the General Purpose Input Registers and Product Identification Registers. Users can access these registers through respective address in the 4Gbytes memory map. There are detail descriptions in the sections below.General Purpose Inputs RegisterThis register reads the GPI[4:0] pins on the W39V080A.This is a pass-through register which can read via memory address FFBC0100(hex), or FFBxE100(hex). Since it is pass-through register, there is no default value.W39V080APublication Release Date: Dec. 28, 2005GPI Register TableBIT FUNCTION7 − 5 Reserved4 Read GPI4 pin status 3 Read GPI3 pin status 2 Read GPI2 pin status 1 Read GPI1 pin status 0Read GPI0 pin statusProduct Identification RegistersThere is a software method to read out the Product Identification in both the Programmer interface mode and the LPC interface mode. Thus, the programming equipment can automatically matches the device with its proper erase and programming algorithms.In the full-chip(8Mb) LPC interface mode, a read from FFBC, 0000(hex) can output the manufacturer code, DA(hex). A read from FFBC, 0001(hex) can output the device code D0(hex).For dual-BIOS(4Mbx2) LPC mode , a read from FFBC, 0000(hex) can output the manufacturer code, DA(hex). A read from FFBC,0001(hex) can output the device code 90(hex).In the software access mode, a JEDEC 3-byte command sequence can be used to access the product ID for programmer interface mode. A read from address 0000(hex) outputs the manufacturer code, DA(hex). A read from address 0001(hex) outputs sequence or an alternate one-byte command sequence (see Command Definition table for detail).the device code, D0(hex).” The product ID operation can be terminated by a three-byte command.Identification Input Pins ID[3:0]These pins are part of mechanism that allows multiple parts to be used on the same bus. The boot device should be 0000b. And all the subsequent parts should use the up-count strapping. Memory Address MapThere are 8M bytes space reserved for BIOS Addressing. The 8M bytes are mapped into a single 4M system address by dividing the ROMs into two 4M byte pages. For accessing the 4M byte BIOS storage space, the ID[2:1] pins are inverted in the ROM and are compared to address lines [21:20]. ID[3] can be used as like active low chip-select pin. The 32Mbit address space is as below:BLOCK LOCK ADDRESS RANGE4M Byte BIOS ROM None FFFF, FFFFh: FFC0, 0000hThe ROM responds to top 1M byte pages based on the ID pins strapping according to the followingtable:ID[2:1] PINSROM BASED ADDRESS RANGE00x FFFF, FFFFh: FFF0, 0000h 01x FFEF, FFFFh: FEF0, 0000h 10x FFDF, FFFFh: FFD0, 0000h 11xFFCF, FFFFh: FFC0, 0000hW39V080A7. TABLE OF OPERATING MODES7.1 Operating Mode Selection - Programmer ModeMODE PINS#OE#WE#RESETADDRESSDQ.Read V IL V IH V IH AIN Dout Write V IH V ILV IHAIN DinStandby X X V IL XHigh ZWrite Inhibit V IL X V IH X High Z/DOUT X V IH V IH X High Z/DOUTOutput DisableV IH X V IH XHigh Z7.2 Operating Mode Selection - LPC ModeOperation modes in LPC interface mode are determined by "cycle type" when it is selected. When itis not selected, its outputs (LAD[3:0]) will be disable. Please reference to the "Standard LPC Memory Cycle Definition".7.3 Standard LPC Memory Cycle DefinitionFIELDNO. OF CLOCKSDESCRIPTIONStart 1 "0000b" appears on LPC bus to indicate the initialCycle Type & Dir 1 "010Xb" indicates memory read cycle; while "011xb" indicates memory write cycle. "X" mean don't have to care. TAR2Turned Around TimeAddr. 8Address Phase for Memory Cycle. LPC supports the 32 bits address protocol. The addresses transfer most significant nibble first and leastsignificant nibble last. (i.e. Address[31:28] on LAD[3:0] first , and Address[3:0] on LAD[3:0] last.) Sync. N Synchronous to add wait state. "0000b" means Ready, "0101b" meansShort Wait, "0110b" means Long Wait, "1001b" for DMA only, "1010b"means error, other values are reserved. Data 2 Data Phase for Memory Cycle. The data transfer least significant nibblefirst and most significant nibble last. (i.e. DQ[3:0] on LAD[3:0] first ,then DQ[7:4] on LAD[3:0] last.)W39V080APublication Release Date: Dec. 28, 20058. TABLE OF COMMAND DEFINITIONCOMMAND NO. OF 1ST CYCLE 2ND CYCLE 3RD CYCLE 4TH CYCLE 5TH CYCLE 6TH CYCLE DESCRIPTION Cycles (1) Addr. Data Addr. DataAddr. DataAddr. DataAddr. DataAddr. DataRead 1 A IN D OUT Sector Erase 6 5555 AA 2AAA 555555 80 5555 AA 2AAA 55SA (5) 30Byte Program 4 5555 AA 2AAA 555555 A0 A IN D INProduct ID Entry 3 5555 AA 2AAA 555555 90 Product ID Exit (4) 3 5555 AA 2AAA 555555 F0Product ID Exit (4)1XXXX F0Notes: 1. The cycle means the write command cycle not the LPC clock cycle. 2. The Column Address / Row Address are mapped to the Low / High order Internal Address. i.e. Column Address A[10:0] are mapped to the internal A[10:0], Row Address A[7:0] are mapped to the internal A[19:11] 3. Address Format: A14−A0 (Hex); Data Format: DQ7-DQ0 (Hex) 4. Either one of the two Product ID Exit commands can be used. 5. SA: Sector AddressSA = FXXXXh for Unique Sector15 (Boot Sector) SA = 7XXXXh for Unique Sector7 SA = EXXXXh for Unique Sector14 SA = 6XXXXh for Unique Sector6 SA = DXXXXh for Unique Sector13 SA = 5XXXXh for Unique Sector5 SA = CXXXXh for Unique Sector12 SA = 4XXXXh for Unique Sector4 SA = BXXXXh for Unique Sector11 SA = 3XXXXh for Unique Sector3 SA = AXXXXh for Unique Sector10 SA = 2XXXXh for Unique Sector2 SA = 9XXXXh for Unique Sector9 SA = 1XXXXh for Unique Sector1 SA = 8XXXXh for Unique Sector8SA = 0XXXXh for Unique Sector0W39V080A 8.1 Embedded Programming AlgorithmW39V080A 8.2 Embedded Erase AlgorithmPublication Release Date: Dec. 28, 2005W39V080A 8.3 Embedded #Data Polling AlgorithmW39V080A 8.4 Embedded Toggle Bit AlgorithmPublication Release Date: Dec. 28, 2005W39V080A 8.5 Software Product Identification and Boot Block Lockout DetectionAcquisition FlowNotes for software product identification/boot block lockout detection:(1) Data Format: DQ7−DQ0 (Hex); Address Format: A14−A0 (Hex)(2) A1−A19 = V IL; manufacture code is read for A0 = V IL; device code is read for A0 = V IH.(3) The device does not remain in identification and boot block lockout detection mode if power down.(4) The DQ[3:2] to indicate the sectors protect status as below:DQ2 DQ30 64Kbytes Boot Block Unlocked by #TBL hardwaretrapping Whole Chip Unlocked by #WP hardware trapping Except Boot Block1 64Kbytes Boot Block Locked by #TBL hardwaretrapping Whole Chip Locked by #WP hardware trapping Except Boot Block(5) The device returns to standard operation mode.(6) Optional 1-write cycle (write F0 (hex.) at XXXX address) can be used to exit the product identification/boot block lockoutdetection.W39V080APublication Release Date: Dec. 28, 20059. DC CHARACTERISTICS9.1 Absolute Maximum RatingsPARAMETER RATING UNITPower Supply Voltage to V SS Potential -0.5 to +4.0 V Operating Temperature 0 to +70 °C Storage Temperature-65 to +150 °C D.C. Voltage on Any Pin to Ground Potential -0.5 to V DD +0.5 V V PP Voltage-0.5 to +13 V Transient Voltage (<20 nS) on Any Pin to Ground Potential-1.0 to V DD +0.5VNote: Exposure to conditions beyond those listed under Absolute Maximum Ratings May adversely affect the life and reliabilityof the device.9.2 Programmer interface Mode DC Operating Characteristics(V DD = 3.3V ± 0.3V, V SS = 0V, T A = 0 to 70° C)LIMITSPARAMETER SYM. TEST CONDITIONSMIN.TYP. MAX.UNITPower Supply Current (read)ICC1 In Read or Write mode, all DQs openAddress inputs = 3.0V/0V, at f = 3MHz- 15 20 mAPower Supply Current (erase/ write)ICC2 In Read or Write mode, all DQs openAddress inputs = 3.0V/0V, at f = 3MHz - 35 45mA Input Leakage Current ILIVIN = VSS to VDD- - 90 μA Output Leakage CurrentILO VOUT = VSS to VDD - - 90 μA Input Low Voltage VIL - -0.5- 0.8 V Input High Voltage VIH-2.0 - VDD +0.5 V Output Low Voltage VOL IOL = 2.1 mA - - 0.45 V Output High VoltageVOH IOH = -0.1mA2.4--VW39V080A9.3 LPC interface Mode DC Operating Characteristics(V DD = 3.3V ± 0.3V, V SS= 0V, T A = 0 to 70° C)LIMITS PARAMETER SYM. TESTCONDITIONSMIN. TYP. MAX.UNITPower Supply Current (read) I CC1All I out = 0A, CLK = 33 MHz,in LPC mode operation.- 15 20mAPower Supply Current (erase/write) I CC2All I out = 0A, CLK = 33 MHz,in LPC mode operation.- 35 45 mAStandby Current 1 Isb1 #LFRAME = 0.9 V DD, CLK = 33MHz,all inputs = 0.9 V DD / 0.1 V DDno internal operation- 20 50uAStandby Current 2 Isb2 #LFRAME = 0.1 V DD, CLK = 33MHz,all inputs = 0.9 V DD /0.1 V DDno internal operation.- 3 10mAInput Low Voltage V IL - -0.5-0.3V DD VInput Low Voltage of #INIT V ILI - -0.5-0.2V DD VInput High Voltage V IH - 0.5V DD- V DD +0.5VInput High Voltage of #INIT Pin V IHI - 1.35V-V DD +0.5VOutput Low Voltage V OL I OL = 1.5 mA - - 0.1 V DD VOutput High Voltage V OH I OH = -0.5 mA 0.9 V DD- - V9.4 Power-up TimingPARAMETER SYMBOLTYPICALUNIT Power-up to Read Operation T PU. READ 100 μSPower-up to Write Operation T PU. WRITE 5 mS10. CAPACITANCE(V DD = 3.3V, T A = 25° C, f = 1 MHz)PARAMETER SYMBOLCONDITIONS MAX. UNITI/O Pin Capacitance C I/O V I/O = 0V 12 pfInput Capacitance C IN V IN = 0V 6 pf。
维沙耶芯片电阻说明书
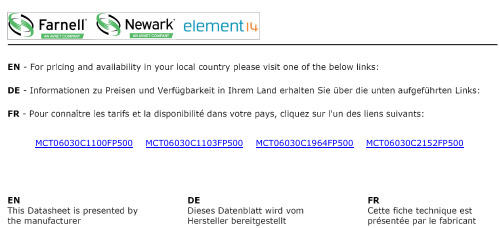
Document Number: 28744For technical questions, contact: *************************** MCS 0402 VG01, MCT 0603 VG01, MCU 0805 VG01 andMCA 1206 VG01 thin film flat chip resistors with establishedreliability are the perfect choice for all high-reliabilityapplications typically found in military, aircraft and spacecraftelectronics. These versions supplement the families ofprofessional and precision thin film flat chip resistorsMCS 0402, MCT 0603, MCU 0805 and MCA 1206.∙Established reliability, failure rate level E6∙Advanced thin film technology ∙Pure Sn termination on Ni barrier layer ∙Single lot date code ∙Material categorization: For definitions of complianceplease see /doc?99912APPLICATIONS∙Military ∙Avionics ∙Space Notes•These resistors do not feature a limited lifetime when operated within the permissible limits. However, resistance value drift increasing over operating time may result in exceeding a limit acceptable to the specific application, thereby establishing a functional lifetime.•The failure rate level E6 (10-6/h, πQ = 0.3), corresponding to MIL Level P, is superior to level E5 (10-5/h, πQ = 1) and thus may be used as areplacement.METRIC SIZE IMPERIAL0402060308051206EN/CECC RR1005M RR1608M RR2012M RR3216M TECHNICAL SPECIFICATIONSDESCRIPTIONMCS 0402 VG01MCT 0603 VG01MCU 0805 VG01MCA 1206 VG01EN/CECC style (size)RR1005M RR1608M RR2012M RR3216MResistance range10 Ωto 1 M Ω; 0Ω 1 Ωto 1 M Ω; 0ΩResistance tolerance± 1 %; ± 0.1 %T emperature coefficient± 50ppm/K; ± 15 ppm/K Rated dissipation, P 700.063W 0.1W 0.125W 0.25W Operating voltage, U max. AC/DC50V 75 V 150V 200V Permissible film temperature, ϑF max.125︒C Operating temperature range- 55 °C to 125 °C Max. resistance change at P 70for resistance range, |∆R /R| max. after:10 Ωto 1 M Ω 1 Ωto 1 M Ω1000h≤ 0.25 %8000h≤ 0.5 %225000h≤ 1.5 %Permissible voltage against ambient(insulation):1 min; U ins75V 100V 200V 300V Continuous75V 75V 75V 75V Assessed failure rate levelE6 = 10-6/h Quality factor, πQ0.3Failure rate: FIT observed < 0.1 x 10-9/h For technical questions, contact: ***************************Document Number: 28744Notes•The products can be ordered using either the PART NUMBER or the PRODUCT DESCRIPTION.•Products within a packaging unit are single lot date code.TYPE/SIZEVERSION TCR RESISTANCE TOLERANCE PACKAGING MCS 0402MCT 0603MCU 0805MCA 1206H = EN 140401-801,“Version E”;failure rate level E6 C = ± 50 ppm/K E = ± 15 ppm/K Z = Jumper 3 digit value 1 digit multiplier MULTIPLIER8 = *10-29 = *10-10 = *1001 = *1012 = *1023 = *1034 = *1040000 = Jumper F = ± 1 %B = ± 0.1 %Z = JumperE1E0P1P5Product Description: MCT 0603-50 1% VG01 P5 287KProduct Description: MCT 0603 VG01 P5 0R0MCT 0603-50 1 %VG01P5287K MCT 0603--VG01P50R0TYPE/SIZETCR T OLERANCE VERSION PACKAGING RESISTANCE MCS 0402MCT 0603MCU 0805MCA 1206± 50 ppm/K ± 15 ppm/K ± 1 %± 0.1 %VG01 = EN 140401-801,“Version E”;failure rate level E6E1E0P1P549R9 = 49.9 Ω287K = 287 k Ω0R0 = JumperMC T 0603H Z 0000Z P 50006032873500Document Number: 28744For technical questions, contact: *************************** Note•The ordering information according to EN 140401-801:2007 shown above succeeds and replaces the ordering information according to earlier versions of the detail specification EN 140401-801 or its predecessor CECC 40401-801, for example:CECC 40401-801 EZ RR1608M C 287K F E6CECC 40401-801 S RR1608M C 287K F E6with EZ; S Assessment level, where EZ is successor to and superior replacement for SRR1608M Style, with suffix M for “metric”C Temperature coefficient, according to the detail specificationC = ± 50 ppm/K; E = ± 15 ppm/K Note•According to EN 140401-801, resistance values are to be selected from the E96 series for ±1% tolerance and from the E192 series for ±0.1 % tolerance.EN140401-801EZRR1608M-0R00-E6The elements used in the component number have the following meaning:EN140401-801EZRR1608MR287KF E6EN detail specification number Assessment level for the zero-defect approach Style (size)T emperature coefficient, according to EN 60062R = ± 50 ppm/K; P = ± 15 ppm/K Resistance, according to EN 60062, 4 characters T olerance on rated resistance, according to EN 60062F = ± 1 %; B = ± 0.1 %Failure rate level according to EN 60115-1, annex ZRTEMPERATURE COEFFICIENT AND RESISTANCE RANGEDESCRIPTIONRESISTANCE TCRTOLERANCE MCS 0402 VG01MCT 0603 VG01MCU 0805 VG01MCA 1206 VG01± 50 ppm/K± 1 %10 Ωto 1 M Ω 1 Ωto 1 M Ω1Ωto 1 M Ω1Ωto 1 M Ω± 15 ppm/K± 0.1 %100Ωto 33.2 k Ω100Ωto 47.5 k Ω100Ωto 100k Ω43.2Ωto 332k ΩJumper ≤ 20m Ω; I max. = 0.63 A ≤ 20m Ω; I max. = 1 A ≤ 20m Ω; I max. = 1.5 A≤ 20m Ω; I max. = 2 A PACKAGINGTYPECODE QUANTITY CARRIER TAPE WIDTH PITCH REEL DIAMETER MCS 0402 VG01E11000Paper tape acc. IEC 60286-3T ype I 8 mm 2 mm 180 mm/7"E010 000MCT 0603 VG01P110008 mm 4 mm P55000MCU 0805 VG01P11000P55000MCA 1206 VG01P11000P55000 For technical questions, contact: ***************************Document Number: 28744Note•Resistors MCA 1206 VG01 and MCU 0805 VG01 are marked using to the four-character code system of IEC 60062, 4.2.3.Resistors MCT 0603 VG01 and MCS 0402 VG01 do not show any marking on their light blue protective coating.Note•The given solder pad dimensions reflect the considerations for board design and assembly as outlined e.g. in standards IEC 61188-5-x, or in publication IPC 7351. They do not guarantee any supposed thermal properties, however, they will be found adequate for most general applications.DIMENSIONS AND MASSTYPEH (mm)L (mm)W (mm)W T (mm)T b (mm)T t (mm)MASS (mg)MCS 0402 VG010.32 ± 0.05 1.0 ± 0.050.5 ± 0.05> 75 % of W 0.2 ± 0.10.2 + 0.1/- 0.150.6MCT 0603 VG010.45 + 0.1/- 0.05 1.55 ± 0.050.85 ± 0.10.3 + 0.15/- 0.21.9MCU 0805 VG010.45 + 0.1/- 0.052.0 ± 0.11.25 ± 0.150.4 + 0.1/- 0.2 4.6MCA 1206 VG010.55 ± 0.1 3.2 + 0.1/- 0.2 1.6 ± 0.150.5 ± 0.259.2RECOMMENDED SOLDER PAD DIMENSIONSTYPE WAVE SOLDERINGREFLOW SOLDERING G(mm)Y (mm)X (mm)Z (mm)G (mm)Y (mm)X (mm)Z(mm)MCS 0402 VG01----0.350.550.55 1.45MCT 0603 VG010.551.10 1.102.750.650.700.95 2.05MCU 0805 VG010.801.25 1.50 3.300.900.90 1.402.70MCA 1206 VG011.40 1.50 1.90 4.40 1.50 1.15 1.753.80grade ceramic (Al2O3) substrate and conditioned to achieve the desired temperature coefficient. Specially designed inner contacts are deposited on both sides. A special laser is used to achieve the target value by smoothly cutting a meander groove in the resistive layer without damaging the ceramics. For the high ohmic range, optimized cermet products provide comparable properties. The resistor elements are covered by a protective coating designed for electrical, mechanical and climatic protection. The terminations receive a final pure tin on nickel plating.The result of the determined production is verified by an extensive testing procedure performed on 100 % of the individual resistors. This includes pulse load screening for the elimination of products with a potential risk of early life failures according to EN 140401-801, 2.1.2.2 (feasible for R≥ 10 Ω). Only accepted products are laid directly into the paper tape in accordance with EN 60286-3 (3), Type I.Products within a packaging unit are from the same production lot and carry the same date code.ASSEMBLYThe resistors are suitable for processing on automatic SMD assembly systems. They are suitable for automatic soldering using wave, reflow or vapour phase as shown in IEC61760-1 (3). Solderability is specified for 2 years after production or requalification. The permitted storage time is 20 years.The resistors are RoHS compliant; the pure tin plating provides compatibility with lead (Pb)-free soldering processes. The immunity of the plating against tin whisker growth has been proven under extensive testing.The encapsulation is resistant to all cleaning solvents commonly used in the electronics industry, including alcohols, esters and aqueous solutions. The suitability of conformal coatings, if applied, shall be qualified by appropriate means to ensure the long-term stability of the whole system.∙2000/53/EC End of Vehicle life Directive (ELV) and Annex II (ELV II)∙2011/65/EU Restriction of the use of Hazardous Substances directive (RoHS)∙2002/96/EC Waste Electrical and Electronic Equipment Directive (WEEE)APPROVALSThe resistors are approved within the IECQ-CECC Quality Assessment System for Electronic Components to the detail specification EN140401-801 which refers to EN60115-1, EN140400 and the variety of environmental test procedures of the IEC 60068 (3)series.Conformity is attested by the use of the CECC logo () as the mark of conformity on the package label.Vishay BEYS C HLAG has achieved “Approval of Manufacturer” in accordance with IEC QC001002-3, clause 2. The release certificate for “Technology Approval Schedule” in accordance with CECC240001 based on IEC QC001002-3, clause 6 is granted for the Vishay BEYSCHLAG manufacturing process.The Vishay BEYSC HLAG production facility is registered with the CAGE code D9539.RELATED PRODUCTSA wider range of TCR, tolerance and resistance values, plus the option of values from a different E series is available with products approved to EN 140401-801, Version A, without established reliability, nominal failure rate level E0 (quality factor πQ = 3). See the datasheets:∙“Professional Flat Chip Resistors”(/doc?28705)∙“Precision Flat Chip Resistors”(/doc?28700)Notes(1)Global Automotive Declarable Substance List, see .(2)CEFIC (European Chemical Industry Council), EECA (European Electronic Component Manufacturers Association), EICTA (European tradeorganisation representing the information and communications technology and consumer electronics), see /index.php?id=1053&id_article=340.(3)The quoted IEC standards are also released as EN standards with the same number and identical contents.Document Number: 28744For technical questions, contact: *************************** For technical questions, contact: ***************************Document Number: 28744Document Number: 28744For technical questions, contact: *************************** •“Precision Flat Chip Resistors”, document no. 28700EN 140400, sectional specificationEN 140401-801, detail specificationFor further information on the tests and requirements ofthese products please refer to the specifications mentionedabove, and to the following datasheets:•“Professional Flat Chip Resistors”(/doc?28705)•“Precision Flat Chip Resistors”(/doc?28700)HISTORICAL 12NC INFORMATION∙The resistors had a 12-digit code starting with 2312∙The subsequent 4 digits indicated the resistor type,specification and packaging; see the 12NC table∙The remaining 4digits indicate the resistance value:-The first 3digits indicated the resistance value-The last digit indicated the resistance decade inaccordance with the resistance decade table RESISTANCE DECADE Historical 12NC ExampleThe 12NC of a MC T 0603 VG01 resistor, value 287K andTCR 50 with ± 1 % tolerance, supplied in cardboard tape of5000units per reel was: 2312 215 02874.RESISTANCE DECADE LAST DIGIT 1Ω to 9.99Ω810Ω to 99.9Ω9100Ω to 999Ω11 k Ωto 9.99k Ω210k Ω to 99.9k Ω3100k Ω to 999k Ω41M Ω5HISTORICAL 12NC - Resistor type and packagingDESCRIPTION2312........CARDBOARD TAPE ON REEL TYPE TCRTOL.E1 1000 PIECES E0 10 000 PIECES MCS 0402 VG01± 50 ppm/K± 1 %260 0....275 0....± 15 ppm/K± 0.1 %262 0....277 0....Jumper262 90001277 90001TYPE TCRTOL.P11000 PIECES P5 5000 PIECES PW 20 000 PIECES MCT 0603 VG01± 50 ppm/K± 1 %200 0....215 0....205 0....± 15 ppm/K± 0.1 %202 0....217 0....-Jumper202 90001217 90001207 90001MCU 0805 VG01± 50 ppm/K±1 %240 0....255 0....245 0....± 15 ppm/K± 0.1 %242 0....257 0....-Jumper242 90001257 90001247 90001MCA 1206 VG01± 50 ppm/K± 1 %No 12NC assigned to MCA 1206 VG01± 15 ppm/K± 0.1 %Jumper“Vishay”), disclaim any and all liability for any errors, inaccuracies or incompleteness contained in any datasheet or in any other disclosure relating to any product.Vishay makes no warranty, representation or guarantee regarding the suitability of the products for any particular purpose or the continuing production of any product. To the maximum extent permitted by applicable law, Vishay disclaims (i) any and all liability arising out of the application or use of any product, (ii) any and all liability, including without limitation special, consequential or incidental damages, and (iii) any and all implied warranties, including warranties of fitness for particular purpose, non-infringement and merchantability.Statements regarding the suitability of products for certain types of applications are based on Vishay’s knowledge of typical requirements that are often placed on Vishay products in generic applications. Such statements are not binding statements about the suitability of products for a particular application. It is the customer’s responsibility to validate that a particular product with the properties described in the product specification is suitable for use in a particular application. Parameters provided in datasheets and/or specifications may vary in different applications and performance may vary over time. All operating parameters, including typical parameters, must be validated for each customer application by the customer’s technical experts. Product specifications do not expand or otherwise modify Vishay’s terms and conditions of purchase, including but not limited to the warranty expressed therein.Except as expressly indicated in writing, Vishay products are not designed for use in medical, life-saving, or life-sustaining applications or for any other application in which the failure of the Vishay product could result in personal injury or death. Customers using or selling Vishay products not expressly indicated for use in such applications do so at their own risk. Please contact authorized Vishay personnel to obtain written terms and conditions regarding products designed for such applications. No license, express or implied, by estoppel or otherwise, to any intellectual property rights is granted by this document or by any conduct of Vishay. Product names and markings noted herein may be trademarks of their respective owners.Material Category PolicyVishay Intertechnology, Inc. hereby certifies that all its products that are identified as RoHS-Compliant fulfill the definitions and restrictions defined under Directive 2011/65/EU of The European Parliament and of the Council of June 8, 2011 on the restriction of the use of certain hazardous substances in electrical and electronic equipment (EEE) - recast, unless otherwise specified as non-compliant.Please note that some Vishay documentation may still make reference to RoHS Directive 2002/95/EC. We confirm that all the products identified as being compliant to Directive 2002/95/EC conform to Directive 2011/65/EU.Vishay Intertechnology, Inc. hereby certifies that all its products that are identified as Halogen-Free follow Halogen-Free requirements as per JEDEC JS709A standards. Please note that some Vishay documentation may still make reference to the IEC 61249-2-21 definition. We confirm that all the products identified as being compliant to IEC 61249-2-21 conform to JEDEC JS709A standards.Revision: 02-Oct-121Document Number: 91000。
SMD机器PM指引(胶水机 丝印机 贴片机 回流焊)(A-0526)

指示表
1、版本
2、目录
3、4、5 SMD机器PM指引
概括:本保养指引包括胶水机、丝印机、贴片机、回流焊、指引内容分每日保养,每周保养,每月保养,每年保养。
一、每日保养:
1、清洁: A)机器内外表面干净。
B)点胶机点胶头,贴片机吸咀清洁干净。
C)机器感应器清洁干净。
2、检查: A)检测机器主气压根据机器后气压表显示检查机器主气压应为0.5MPa±0.1MPa
B)安全感应器是否正常。
C)指示灯是否工作正常。
D)回流焊焊抽风机正常工作与否。
E)丝印机刮刀水平,无变形。
1、加润滑油:
B)传动齿轮加高温油润滑
2、清洁:A)清洁所有散热风扇
B)清洁物料识别系统
3、测真空压:
A)进入机器测试菜单:三星机测量结果应为:400MMHg(+200MMHg/-50MMHg),
YAMAHA PHILIPS显示LEVEL值为:100(+50/-20)。
1、清洁:A)清洁所有控制板及板上风扇
B)清洁真空电磁阀
2、检查:A)检查皮带张力及磨损善状况
B)检查丝杆及取置轴的磨损状况
C)检查丝印台水平
3、校正:
A)校正取置头与照相系统。
四、年保养:
1、对电脑扫毒
2、润滑所有需加油部位
3、机器所有参数调校
4、请根据年保养记录报表作好年终保养。
APXW005A0X3-SRZ;中文规格书,Datasheet资料

RoHS Compliant Applications
Industrial equipment Distributed power architectures Intermediate bus voltage applications Telecommunications equipment
Document No: DS09-009 ver. 1.11 PDF name: APXW005A0X_DMay 26, 2011
9-36V ProLynxTM 5A: Non-isolated DC-DC Power Modules 9 – 36Vdc input; 3Vdc to 18Vdc output; 5A to 2.5A output current
Electrical Specifications (continued)
Parameter Output Voltage Set-point Output Voltage (Over all operating input voltage, resistive load, and temperature conditions until end of life) Adjustment Range (elected by an external resistor) (Some output voltages may not be possible depending on the input voltage – see Feature Descriptions Section) Output Regulation Line (VIN=VIN, min to VIN, max) Load (IO=IO, min to IO, max) Temperature (Tref=TA, min to TA, max) Remote Sense Range Output Ripple and Noise on nominal output (VIN=VIN, nom and IO=IO, min to IO, max Co = 0.1μF // 10 μF ceramic capacitors) Vout=3.3V, Vin=28V Peak-to-Peak (5Hz to 20MHz bandwidth) RMS (5Hz to 20MHz bandwidth) Vout=18V, Vin=28V Peak-to-Peak (5Hz to 20MHz bandwidth) RMS (5Hz to 20MHz bandwidth) External Capacitance ESR ≥ 1 mΩ ESR ≥ 10 mΩ With the Tunable Loop ESR ≥ 0.15 mΩ ESR ≥ 10 mΩ Output Current (Vo=3V) Vo=5V Vo=12V Vo=18V Output Current Limit Inception (Hiccup Mode ) Output Short-Circuit Current (VO≤250mV) ( Hiccup Mode ) Efficiency (IO=IO, max , VO= VO,set) VIN= 12Vdc, TA=25°C VIN= 12Vdc, TA=25°C VIN= 28Vdc, TA=25°C VIN= 28Vdc, TA=25°C VO, set = 3.3Vdc VO, set = 5Vdc VO,set = 12Vdc VO,set = 18Vdc η η η η 91.0 93.3 94.7 95.9 % % % % 12Vin 28Vin 25C
R05J09中文资料

Dual Output TypesRxxG055/12±5±1007127RxxG095/12±9±557435DIP14 RxxG125/12±12±427542RxxG155/12±15±337641RxxG0524/48±5±10080/7045RxxG0924/48±9±557052/58DIP14 RxxG1224/48±12±427065/68RxxG1524/48±15±337070/75RxxH055/12±5±1007127RxxH095/12±9±557435SIP7 RxxH125/12±12±427542RxxH155/12±15±337641RxxH0524/48±5±10070/8045RxxH0924/48±9±557052/58SIP7 RxxH1224/48±12±427065/68RxxH1524/48±15±337070/75Absolute Maximum RatingsInput Voltage V IN5V types 7V typ.12V types 15V typ.24V types 24V typ.48V types48V typ.Short Circuit Duration 1)1s Internal Power Dissipation560mW Lead Temperature (1.5 mm from case for 10 seconds)300 °C1).Supply voltage must be discontinued at the end of the short circuit duration.Input Voltage Range V IN (continuous operation)5V input types 4.5VDC min./ 5.5VDC max.12V input types 10.8VDC min./ 13.2VDC max.24V input types 28VDC max.48V input types54VDC max.Reflected Ripple Current (depending on the type)20 mA p-p min.to 40 mA p-p max.Voltage Set Point Accuracy See Tolerance EnvelopeLine Regulation1.0% / 1.2% of V INLoad Voltage Regulation (10% load to 100% full load)single output types 6.7% min./ 15% max.dual output types 6.8% min./ 10% max.Ripple & Noise (20MHz band limited)single output types 32mVp-p min./ 80mVp-p max.dual output types24mVp-p min./ 40mVp-p max.Isolation Voltage (for 1 minute)3000VDC min.Test Voltage (50Hz,10 seconds)3000 Vpk min.Resistance (Viso = 1000V)10 G Ωtyp.Switching Frequency at Full Load (depending on the type)V IN 5V output types 120kHz min./ 135kHz max.V IN 12V output types 150kHz min./ 170kHz max.V IN 24V output types 150kHz max.V IN 48V output types150kHz max.Package Weight2.11 gOperating Temperature Range (all output types)–40°C min.to +85°C max.(see graph)Storage Temperature Range–50°C min.+125°C max.Case Temperature Above Ambient (depending on the type)5V output types+28°C max.all other output types +25°C max.MTTF 1) (depending on the type)–40°C,single output types 303kHrs min./ 2938kHrs max.+25°C,single output types 252kHrs min./ 2414kHrs max.+85°C,single output types 212kHrs min./ 1961kHrs max.–40°C,dual output types 185kHrs min./ 2068kHrs max.+25°C,dual output types 154kHrs min./ 1697kHrs max.+85°C,dual output types130kHrs min./ 1368kHrs max.1).Calculated using MIL-HDBK-217F with nominal input voltage at full load.Please contact us,if you need exact parameters for the converter you have selected.Electrical Specifications (measured at T A = 25°C,at nominal input voltage and rated output current unless otherwise specified)Package Style and Pinning (mm)。
50S中文手册

KSP75-FP-004707(1)目录前言 (6)产品说明 (8)1. 熔接机的配置 (8)2. 熔接操作的其他必备品 (9)3. 熔接机的部件名称和功能 (10)基本操作 (12)1. 电源连接 (12)2.开机 (16)3.设置热缩管中央定位设备 (17)4. 清洁光纤涂层 (17)5. 套光纤热缩管 (17)6. 光纤的剥除和清洁 (17)7. 切割光纤 (18)8. 放置光纤 (19)9. 熔接操作 (20)10.取出光纤 (26)11.左手在此处持光纤 (26)12. 加固熔接点 (26)熔接质量维护 (28)1. 熔接前的清洁和检查 (28)2. 定期的检查和清洁 (30)菜单命令 (33)菜单命令 (34)1. 熔接模式 (34)2. 加热模式 (48)3. 放电校正 (52)4. 熔接选项 (54)5. 熔接结果 (56)目录管理菜单 (60)1. 改变操作方向 (62)2. 省电菜单 (63)3. 菜单加锁/开机选项/其他选项 (64)维护菜单 (66)1. 更换电极 (67)2. 稳定电极 (68)3. 清除放电计数 (68)4. 电池放电 (69)5. 日历设置 (70)6. 传感器值 (70)7. 诊断测试 (71)8. 灰尘检查 (72)9. 马达校准 (72)10. 马达驱动 (73)11. 维护信息 (73)出错信息表 (74)问题和故障排除 (82)1. 供电 (82)2. 熔接操作 (83)3. 加热操作 (85)4. 高级操作 (85)5. 其他功能 (86)保证书和联系地址 (87)1. 保证书 (87)2. 联系方式 (88)警告和注意事项FSM-50S 是为熔接通信用玻璃光纤设计的,除此外不能熔接任何物质。
藤仓公司 考虑到使用者的安全,提供了很多的安全注意事项。
如果错误操作将会导致电击,火灾和人身伤害。
务必了解所有警告和注意标志。
遇到故障时请立即联系维修中心。
SMD、SMG、SFG 搅拌器和推流器 50 Hz 安装和使用说明书

SMD, SMG, SFGMixers and flowmakers50 Hz安装和使用说明书GRUNDFOS说明书中文 (CN)2中文 (CN) 安装和使用说明书中文版本这些安装和操作说明介绍了格兰富SMD、SMG、SFG 搅拌器和推流器。
章节1-6介绍了以安全的方式拆包、安装并启动本产品所需的信息。
章节7-11介绍了有关产品的重要信息,以及有关服务、故障查找和产品处置的信息。
目录页1. 一般信息本手册包含关于格兰富SMD、SMG搅拌器和SFG推流器的安装、操作和维护的说明。
这些产品设计用于低粘度到中等粘度 (≤ 500 mPas) 液体中的各种搅拌应用,例如搅拌均匀和保持悬浮。
1.1 本文献中所用符号2. 安全指导2.1 安全概述1.一般信息21.1本文献中所用符号22.安全指导22.1安全概述23.接收产品33.1运输产品33.2检查产品33.3储存产品34.安装产品34.1扭矩34.2搅拌器和推流器定位44.3安装一台搅拌器54.4安装一台推流器85.电气连接135.1电机保护135.2齿轮箱/机封室保护145.3过载继电器145.4启动方式155.5SMG和SFG的接线图155.6接线图165.7转动方向195.8电化学腐蚀的防护196.启动该产品197.产品介绍197.1产品描述197.2应用207.3标识218.维护228.1污染的搅拌器或推流器228.2服务一览表238.3机油248.4换油249.故障查找2510.技术数据2710.1一般技术数据2710.2电机2710.3齿轮箱,仅SMG、SFG 2710.4机封2710.5桨叶2710.6声压级2711.回收处理27警告装机前,先仔细阅读本安装操作手册。
安装和运行必须遵守当地规章制度并符合公认的良好操作习惯。
注意AMD.07.18.1410搅拌器有单独的安装与操作指导。
参见 网页, 出版号 96526302 。
关于Ex版本AMD、AMG和AFG的信息,请参见上编号为96498078的文件。
SR05_05资料

Forward Voltage vs. Forward Current
10 9 8 7 6 5 4 3 2 1 0 0
Waveform Parameters:
tr = 8µs td = 20µs
5 10 15 20 25 30 35 40 45 50 Forward Current - IF (A)
Applications
USB Power & Data Line Protection Ethernet 10BaseT I2C Bus Protection Video Line Protection T1/E1 secondary IC Side Protection Portable Electronics Microcontroller Input Protection WAN/LAN Equipment ISDN S/T Interface
2. The SR05 can be isolated from the power supply by adding a series resistor between pin 4 and VCC. A value of 10kΩ is recommended. The internal TVS and steering diodes remain biased, providing the advantage of lower capacitance.
Array of surge rated diodes with internal TVS Diode Protects two I/O lines Low capacitance (<10pF) for high-speed interfaces Low clamping voltage Low operating voltage: 5.0V Solid-state silicon-avalanche technology
WW5中文资料

元器件交易网
PRODUCT BULLETIN WW-SERIES
FLAMEPROOF WIREWOUND RESISTORS
1 TO 10 WATT 0.1% THRU 10% TOLERANCE SILICONE COATED HIGH PURITY CERAMIC CORE STAINLESS STEEL END CAPS TINNED COPPER-CLAD STEEL LEADS WELDED CONSTRUCTION PACKAGED TAPE & REEL OR BULK AVAILABLE IN NON-INDUCTIVE STYLE MEETS REQUIREMENTS FOR MIL-R-26
* ALSO AVAILABLE IN .020
Temperature
TC20 = ±20PPM/°C, 10 ohm and above. TC50 = ±50PPM/°C, 1 ohm - 9.9 ohm. TC90 = ±90PPM/°C, below 1 ohm.
How to Order
Sample Part Number WW1 TC20 7.5K ±1% S
S = Standard
元器件交易网
ENVIRONMENTAL SPECIFICATIONS
LOAD LIFE MOISTURE RESISTANCE THERMAL SHOCK SHORT TIME OVERLOAD DIELECTRIC STRENGTH LOW TEMP. STORAGE HIGH TEMP. EXPOSURE TERMINAL STRENGTH SHOCK VIBRATION
CHARACTERISTIC
常用三极管参数excel

玉林万顺达电脑芯片级维修资料 2010-07-20整理玉林万顺达电脑芯片级维修资料 2010-07-20整理玉林万顺达电脑芯片级维修资料 2010-07-20整理玉林万顺达电脑芯片级维修资料 2010-07-20整理玉林万顺达电脑芯片级维修资料 2010-07-20整理玉林万顺达电脑芯片级维修资料 2010-07-20整理玉林万顺达电脑芯片级维修资料 2010-07-20整理玉林万顺达电脑芯片级维修资料 2010-07-20整理玉林万顺达电脑芯片级维修资料 2010-07-20整理玉林万顺达电脑芯片级维修资料 2010-07-20整理玉林万顺达电脑芯片级维修资料 2010-07-20整理玉林万顺达电脑芯片级维修资料 2010-07-20整理玉林万顺达电脑芯片级维修资料 2010-07-20整理玉林万顺达电脑芯片级维修资料 2010-07-20整理玉林万顺达电脑芯片级维修资料 2010-07-20整理玉林万顺达电脑芯片级维修资料 2010-07-20整理玉林万顺达电脑芯片级维修资料 2010-07-20整理玉林万顺达电脑芯片级维修资料 2010-07-20整理玉林万顺达电脑芯片级维修资料 2010-07-20整理玉林万顺达电脑芯片级维修资料 2010-07-20整理玉林万顺达电脑芯片级维修资料 2010-07-20整理玉林万顺达电脑芯片级维修资料 2010-07-20整理玉林万顺达电脑芯片级维修资料 2010-07-20整理玉林万顺达电脑芯片级维修资料 2010-07-20整理玉林万顺达电脑芯片级维修资料 2010-07-20整理玉林万顺达电脑芯片级维修资料 2010-07-20整理玉林万顺达电脑芯片级维修资料 2010-07-20整理玉林万顺达电脑芯片级维修资料 2010-07-20整理玉林万顺达电脑芯片级维修资料 2010-07-20整理玉林万顺达电脑芯片级维修资料 2010-07-20整理。
2SC3356中文资料(RENESAS)中文数据手册「EasyDatasheet - 矽搜」

芯片中文手册,看全文,戳
2SC3356
电气特性(T
参数 直流特性 集电极截止电流 发射极截止电流
DC电流增益
射频特性 增益带宽产品 插入功率增益 噪声系数 反向传输电容
A = +25°C)
符号
测试条件
ICBO IE B O h Note 1
FE
VCB = 10 V, I E = 0 mA时 VEB = 1.0 V, I C = 0 mA时 VCE = 10 V, I C 能力= 20 mA
和信息.瑞萨电电子不承担由您或因使用上述电路,软件以及相关信息而引起任何损失承担任何责任.
5. 当导出本文档中描述产品或技术,您应遵守适用出口管制 法律,法规,并按照这些法律和法规规定程序.你不应该使用瑞萨 电子产品或技术本文档中描述由军方关于军事应用或使用任何用途,包括但不限于大规模杀伤武器发展.瑞萨电子产品和 技术不得用于或纳入任何产品或系统制造,使用,销售或根据任何适用国内或外国法律或法规禁止.
防止它们之间物理损伤一个故障情况下所造成火灾可能性,和伤害或损害 瑞萨电子产品,如安全设计硬件和软件,包括但不限于冗余度,防火和防故障,老化退化或其他任何适当措施,适当治 疗.因为单独微机软件评价是非常困难,请评价您所生产最终产品或系统安全性.
10. 请联系瑞萨电子销售处细节,以环境问题,如环境 每个瑞萨电子产品兼容性.请使用瑞萨电子产品符合所有适用 调控受控物质列入或使用,包括但不限于欧盟RoHS法规 指示.瑞萨电子承担对于因您不遵守适用法律法规而导致损害或损失不承担任何责任.
50 100
15 (dB)
2
|21e 10
插入功率增益 主场迎战集电极电流
VCE = 10 V F = 1 GHz的
SMD Rework Station说明书

TM SMD Rework Station21-10125 EU & 21-10125 UKUser Manual TMPlease read this manual before operating the equipment.Keep manual in accessible place for future reference.What’s IncludedControl Unit 1 No.Nozzle 1 No.Bracket 1 No.Power Cord (UK or EU) 1 No.User ManualSpecificationsPower Voltage : 220V / 50HzPower Consumption : 560W (Max.)Pump : Diaphragm PumpCapacity : 23L/min (Max.)Hot Air Temperature : 100°C to 480°CUsageSuit for most de-soldering of SMD, such as SOIC, CHIP, QFP, PLCC, BGA etc.Chart of TemperatureTemp. Knob12345678Temp. (°C)100130190250310380440480Indicators flickers denotes that heating element is being heated up, when it extinguishes denotes that temperature has reached the setting one.Before OperationSelect the Nozzle that matches the size of the ICAttach the Nozzle when both the Pipe and the Nozzle are cool. Should either be warm, check to make sure that the Temperature check to make sure that the Temperature Control Knobs set to1.Loosen the screw on the NozzleAttach the NozzleDo not force the nozzle or pull on the edge of the Nozzle by pliers. Also, do not re-tighten the screw too tightly. TMOperating InstructionsQFP- De-solderingPlug the power cord into the power supply.After connection, the automatic blowing function will start sending air through the pipe, but the Heating Element remains cool Turn the Power switch on.The Power Switch may be turned on at any time while the automatic blowing function is operating. Once the Power Switch is turned on, the Heating Element will begin to warm up.Adjust the Air Flow and Temperature Control Knobs.After adjusting the Air Flow and Temperature Control Knob, wait for the temperature to stabilize for a short period of time. Melt the solder.Hold the iron so that the Nozzle is located directly over, but not touching the IC and allow the hot air to melt the solder. Be careful not to touch the leads of the IC with the Nozzle.Remove the IC.Once the solder has melted, remove the IC by lifting the plier.Turn the Power Switch off.After the Power Switch is turned off, an automatic blowing function begins sending cool air through the pipe in order to cool both the heating element and the handle. So do not disconnect the plug during this cooling process. In case you don’t use the unit for a long time, disconnect the plug.Note: After turn off the Power Switch of about 1 minute later, power is automatically shut off.Remove any remaining solder.After removing the IC, remove remaining solder with a wick or de-soldering tool.Note: After turn off the Power Switch of about 1 minute later, power is automatically shut off.QFP SolderingApply the solder paste.Apply the proper quantity of solder paste and install the SMD on the PCB.Preheat SMD.Refer to the photo to preheat SMD.SolderingHeat the lead frame evenly.WashingWhen soldering is completed, wash away the fluxNote: While here is a merit to solder by Hot air, it’s also possible to cause the defects such as solder balls, older bridges. We recommend you to examine the conditions of soldering sufficiently.PrecautionsBefore attach the nozzle, make sure that both the heating tube and the nozzle are cool down.Caution High Temperature OperationDo not use the unit near ignitable gases, paper, or other inflammable materials. Both the nozzle and the heated air are ex-tremely hot and can cause painful burns. Never touch the heater pipe or allow the heated air to blow against your skin. Initially, the iron may emit white smoke, but this will soon disappear.After use, be sure to cool the unit.After turning off the power switch, the unit will automatically blow cool air through the pipe for a short period of time .Do not disconnect the plug during this cooling process.TM Important Notice : This data sheet and its contents (the “Information”) belong to the members of the Premier Farnell group of companies (the “Group”) or are licensed to it. No licence is granted for the use of it other than for information purposes in connection with the products to which it relates. No licence of any intellectual property rights is granted. The Information is subject to change without notice and replaces all data sheets previously supplied. The Information supplied is believed to be accurate but the Group assumes no responsibility for its accuracy or completeness, any error in or omission from it or for any use made of it. Users of this data sheet should check for themselves the Information and the suitability of the products for their purpose and not make any assumptions based on information included or omitted. Liability for loss or damage resulting from any reliance on the Information or use of it (including liability resulting from negligence or where the Group was aware of the possibility of such loss or damage arising) is excluded. This will not operate to limit or restrict the Group’s liability for death or personal injury resulting from its negligence. Tenma is the registered trademark of the Group. © Premier Farnell Limited 2016.Never drop or sharply joint the unit.The pipe contains quartz glass, which can break if the unit is dropped or jolted sharply.Do not disassemble the pump.Disconnect the plug when you don’t use the unit for a long time.When the power cord is connected into the power supply, the unit has a little flow of electricity, even the Power Switch is in off position. So when you don’t use the unit for a long time, disconnect the plug.Replacing the Heating ElementRemove the screws, slide the tube.Remove the 3 screws, which secure the Handle and slide the cord tube.Open the Handle.Disconnect the ground wire sleeve and remove the pipe. In the pipe. The quartz glass and heat insulation is installed. Do not drop or miss it.Remove the Heating Element.Disconnect the terminal and remove the Heating Element.Insert a new Heating Element.Handle it with care. Never rub the Heating Element wire. Insert a new Heating Element and reconnect the terminal. Reconnect the ground wire after replacing the element. Assemble the Handle in the reverse order of disassembly. Insert the Handle’s projection into the hole in the pipe.Interchangeable PartsNumberName Specifications 1144Heating Element 100V/ 250W 1146Heating Element 110V/ 250W 1144A+Heating Element 100V/ 250W 1146A+Heating Element 110V/ 250W。
SMD 510 magazine 说明书

ORIGINAL OPERATING INSTRUCTIONSSMD510magazineIt is essential that the operating instructionsare read before the tool is operated for thefirst time.Always keep these operating instructionstogether with the tool.Ensure that the operating instructions arewith the tool when it is given to otherpersons.1These numbers refer to the corresponding illustra-tions.The illustrations can be found on the fold-outcover pages.Keep these pages open while studyingthe operating instructions.Operating controls and parts of the magazine1@Depth gauge;Screw length adjustment button=Screw length marks%Screwdriving depth adjustment thumbwheel&Release buttons(Strip guide)Transport latch+Lockbutton for sustained operation§Strip releaseDANGERDraws attention to imminent danger that could leadto serious bodily injury or fatality.WARNINGDraws attention to a potentially dangerous situationthat could lead to serious personal injury or fatality.CAUTIONDraws attention to a potentially dangerous situationthat could lead to slight personal injury or damage tothe equipment or other property.NOTEDraws attention to an instruction or other usefulinformation.Warning signsGeneralwarningWarning:electricity1Obligation signs Wear eye protection Wear a hard hat Wear ear protection Wear protective glovesSymbols Return waste material for recycling.Read theoperatinginstructionsbefore use.Location of identification data on the toolThe type designation and the serial number arestamped on the rear of the magazine.Make a noteof this data in your operating instructions and al-ways refer to it when making an enquiry to your Hiltirepresentative or service department.Type:Serial no.:The SMD 50 m agazine is an accessory used for driving collated screws.The magazine is suitable for use with the Hilti SF 4000/SF 4000‑A /SD 2500/SD 4500/SD 5000/SD 5000‑A22/SD 4500‑A18and SD 45screwdrivers.The magazine and Hilti screwdrivers are optimally matched to each other.In the safety rules in these operating instructions,the designation “power tool”refers to the magazine.Modification of the power tool is not permissible.Observe the information printed in the operating in-structions concerning operation,care and mainten-ance.To avoid the risk of injury,use only genuine Hilti accessories and insert tools.The power tool and its ancillary equipment maypresent hazards when used incorrectly by untrained personnel or when used not as directed.The power tool is designed for professional use and may be operated,serviced and maintained only by trained,authorized personnel.This personnel must be informed of any special hazards that may be encountered.The power tool and its ancillary equip-ment may present hazards when used incorrectly by untrained personnel or when used not as directed.The working environment may be as follows:con-struction site,workshop,renovation,conversion or new construction.Working on materials hazardous to the health (e.g.asbestos)is not permissible.1Magazine1S ‑MBL 116PH2bit1Operating instructions1Cardboard boxS ‑MBL 116PH2bitSME extension2SMD 50 m agazine 22Magazine unit,complete 3829053Depth gauge 5.Technical dataRight of technical changes reserved.Magazine SMD 50Weight Without screwdriver,Without screw strip:0.77 l b /0.35kg Length Contact pressure to 40N (4.0kp)Screw capacity (screws per strip)50Suitable drywall screw types SMD 50Length Thread inside diameter Head diameter Drive type Philips no.2(S ‑MBL 116PH2)Philips no.2can be driven with the following Hilti screwdrivers SF 4000/SF 4000‑A /SD 5000/SD 2500/SD 4500/SD 5000‑A22/SD 4500‑A18/SD 45a)Stay alert,watch what you are doing and use common sense when operating a power tool.Do not use a power tool while you are tired or under the influence of drugs,alcohol or medication.A moment of inattention while operating power tools may result in serious personal injury.b)Dress properly.Do not wear loose clothing or jewellery.Keep your hair,clothing and gloves away from moving parts.Loose clothes,jewellery or long hair can be caught in moving parts.c)Use safety equipment.Always wear eye pro-tection.Safety equipment such as dust mask,non-skid safety shoes,hard hat,or hearing pro-tection used for appropriate conditions will reduce personal injuries.a)Use the power tool,accessories and tool bits etc.,in accordance with these instructions and in the manner intended for the particular type of power tool,taking into account the working conditions and the work to be e of the power tool for operations different from those intended could result in a hazardous situation.b)Maintain power tools.Check for misalignment or binding of moving parts,breakage of parts and any other condition that may affect the power tool’s operation.If damaged,have the power tool repaired before use.Many accidents are caused by poorly maintained power tools.c)Store idle power tools out of the reach of children and do not allow persons unfamiliar with the power tool or these instructions to operate the37.3 i nches /186 m m1"–2"4232424Magazine spring 3876741/8...3/16 i nch /3…4.5mm5/16 i nch /7.5…8.6mmpower tool.Power tools are dangerous in the hands of untrained users.a)Observe the operating instructions and the safety rules contained for the magazine and the screw-driver used.b)Always work with the screwdriver running at maximum speed.Accordingly,use the switch lockbutton on the screwdriver.c)Do not hold the SMD 50magazine in the area of the depth gauge.d)Each screwdriving stroke must be completed infull.Interruption of the magazine stroke or releaseof pressure half way through the screwdrivingoperation may lead to malfunctions.e)Change the screw strip only when the screwdriveris switched off.f)Wear eye protection,especially when working overhead.g)Use only genuine Hilti S ‑MBL 116PH2bits.Check that the bits are in good condition.h)Use only genuine Hilti screw strips and screws.i)Always work at right angles to the surface of theworkpiece to be fastened.j)Store the screw strips in a straight position,asthey are in the original package.CAUTION Disconnect the screwdriver’s supply cord from the electric supply before fitting the magazine.1.Remove the depth gauge and bit holder from the screwdriver. 2.Fit the bit into the screwdriver.NOTE The bit clicks into position.3.Push the magazine onto the screwdriver in the desired working position until it is heard to en-gage.NOTE The magazine can be engaged on the toolin various positions (every 15°).NOTE Check to ensure that the screwdriver is setto “forward”rotation.1.Adjust the depth gauge to suit the length of the screws to be driven.2.Press the button and slide the depth gauge back or forward.3.Set the depth gauge to one of the 5length marks corresponding to the length of the screws.NOTE The correct screw length setting is very important for trouble-free magazine operation.1.Slide the screw strip through the guide and the channel until the first screw is in position at the mark or until the end of the strip is flush with the upper surface of the magazine at the exit opening.2.Check that the screw strip has engaged by tryingto pull it back gently.1.Set the optimum screwdriving depth by turningthe thumbwheel.2.Turning the thumbwheel counterclockwise causes the screw to be driven deeper.3.Drive a screw to test the screwdriving depthsetting.4.Readjust the setting if necessary.NOTE Each audible click of the thumbwheelcorresponds to an adjustment of 0.2mm (0.008inch).45.Turning the thumbwheel clockwise causes the screw to be driven less deeply.CAUTIONDisconnect the screwdriver’s supply cord from the electric supply.1.Release the strip retainer by pressing the transport latch. 2.Pull the screw strip back.NOTE Alternatively,the screw strip can be pulledupwards,out of the magazine,without pressingthe transport latch.CAUTIONDisconnect the screwdriver’s supply cord from theelectric supply before removing the magazine.The magazine can be removed by pressing the releasebuttons and,at the same time,pulling it away fromthe screwdriver.NOTE Dirt and dust (especially from plaster)may have an adverse effect on operation of the magazine.CAUTION Do not,under any circumstances,lubricate the magazine with mineral oil /grease or graphite sprays.This would increase the risk of malfunc-tions.Clean the magazine simply by blowing out the dirt and dust with compressed air.NOTE It is recommended that the magazine is cleaned by washing it out with warm water after a long period ofheavy use. 1.Remove the screw strip as described in the section “Moving the screw strip back”.2.Remove the magazine as described in the section “Removing the magazine from the screwdriver”.3.Press the release spring together with the aid ofpliers or a similar tool.The transport mechanism,including the depth gauge,can then be removed from the casing.You now have three assem-blies in your hand:the transport mechanism,the pressure spring and the casing.4.If necessary,the depth gauge can also be separ-ated from the other parts by pulling it out while pressing the screw length adjustment button.NOTE Take care to avoid pinching your fingers.5.The parts can then be cleaned thoroughly withwarm water.NOTE We recommend use of a nylon brush (an old toothbrush)to remove stubborn deposits.Assembly is carried out in the reverse order.Operate the transport movement once or twice tocheck that the magazine is functioning correctly aftercleaning and reassembly.5Most of the materials from which Hilti tools or appliances are manufactured can be recycled.The materials must be correctly separated before they can be recycled.In many countries,Hilti has already made arrangements for taking back old tools and appliances for recycling.Ask Hilti customer service or your Hilti representative for further information.Hilti warrants that the tool supplied is free of defectsin material and workmanship.This warranty is valid so long as the tool is operated and handled correctly,cleaned and serviced properly and in accordance with the Hilti Operating Instructions,and the technical system is maintained.This means that only original Hilti consumables,components and spare parts may be used in the tool.This warranty provides the free-of-charge repair orreplacement of defective parts only over the entire lifespan of the tool.Parts requiring repair or replace-ment as a result of normal wear and tear are not covered by this warranty.Additional claims are excluded,unless stringent na-tional rules prohibit such exclusion.In particular,Hilti is not obligated for direct,indirect,incidental or consequential damages,losses or expenses in connection with,or by reason of,the use of,or inability to use the tool for any purpose.Implied warranties of merchantability or fitness for a par-ticular purpose are specifically excluded.For repair or replacement,send the tool or related parts immediately upon discovery of the defect to the address of the local Hilti marketing organization provided.This constitutes Hilti’s entire obligation with regardto warranty and supersedes all prior or contempor-aneous comments and oral or written agreementsconcerning warranties.6*424721*424721Hilti CorporationLI-9494SchaanTel.:+423/2342111Fax:+423/2342965Hilti =registered trademark of Hilti Corp.,Schaan W 3739051000-Pos.31Printed in Liechtenstein ©2010Right of technical and programme changes reserved S.E.&O.424721/A。
- 1、下载文档前请自行甄别文档内容的完整性,平台不提供额外的编辑、内容补充、找答案等附加服务。
- 2、"仅部分预览"的文档,不可在线预览部分如存在完整性等问题,可反馈申请退款(可完整预览的文档不适用该条件!)。
- 3、如文档侵犯您的权益,请联系客服反馈,我们会尽快为您处理(人工客服工作时间:9:00-18:30)。
Notes :
For the REC5-05xxS_DRW/H4/H6 series, Load = 90%max. when Vin=4.5VDC. * add suffix "/H4" for 4kVDC isolation or "/H6" for 6kVDC isolation * add suffix "/A" or "/C" for Pinning, see next page * add suffix "/M" for metal case
3
(2W) 40 20 0
Safe Operating Area
-40
75 100 125 105 95 Operating Temperature °C
0
25
50
}
Detailed Information see Application Notes chapter "MTBF"
Typical Characteristics
80%
100%
0% 20% 40% 60% Total Output current (%)
80%
100%
Single
Efficiency / Load
100 80 60 40
Dual
Efficiency / Load
100 80 60
4805
4812
1209
2415 4812 2405
483.3 Efficiency %
元器件交易网
Features
Regulated Converters
● ● ● ● ● ● ● ● ●
UL-60950-1 / CSA C22.2 certified 5W DIP Package 4kVDC & 6kVDC Isolation Regulated Output Continuous Short Circuit Protection Wide Input 2:1 & 4:1 UL94V-0 Package Material 100% Burned In Efficiency to 86%
5 Watt DIP24 & SMD Single & Dual Output
EN-60950-1 Certified UL-60950-1 Certified EN-60601-1 Certified
4:1 Input (REC5-S/DRWZ(H4/H6)) xx = 9-36Vin = 24 xx
(Ambient Temperature)
4000VDC min. see Application Notes 6000VDC min. see Application Notes 60pF typ. 1 GΩ min.
Output Power (%)
100 80 (3W) 60
Description
This series offers high isolation of 4kVDC (= option "/H4") or 6kVDC (= option "/H6") making it ideal for medical applications and other sophisticated industrial applications. Packaging can be either DIP-24 non-conductive plastic or 5-side-shielded DIP24 metal case (= option "M") as well as DIP24-SMD case (= option "SMD"). For all the above variants, 2 industry-standard pinouts (= option "A" or "C") are available.
Continuous, Auto Restart -40°C to +75°C (see Graph) -55°C to +125°C 95% RH Non-Conductive Plastic 20°C/W for metal case 13g 850 x 10 hours 206 x 103hours
Single
Efficiency / Load
100 80 60 40
Single
Efficiency / Load
100 80 60
1212
1209
2412
2405
1205
123.3 Efficiency %
40 20 0
243.3
Efficiency %
20 0
0% 20% 40% 60% Total Output current (%)
November 2006
1
元器件交易网
ECONOLINE
DC/DC-Converter
Specifications (Core Operating Area)
Input Voltage Range Output Voltage Accuracy Line Regulation (HL-LL)
* add suffix "/SMD" for SMD package
e.g. REC5-xxxxSRWZ/H4/AM = 4kVDC isol. / Pinout "A" / metal case ** 24V 4:1 Wide Range Input Types (REC5-24xxS_DRWZ(/H4/H6)) should be derated Vin= 9 Vin : 3.3Vout / 1100mA max., 5Vout / 900mA max.. If the options "/M" for metal case and "/SMD" for SMD pinout are combined the maximum allowed isolation voltage is 2kVDC because of the shorter distances between the pins and the metal-case so the only available SMD-option in metal-case is "/H2". DIP-24 through-hole case and SMD-plastic case are not affected and offer the full isolation barriers of 4kVDC for "/H4" option and 6kVDC for "/H6".
ECONOLINE
DC/DC-Converter
REC5S_DRW/H4, H6 Series
Efficiency (%) 75-77 79-81 72 82-83 73 84-85 74 85-86 75 79-81 72 84-85 74 85-86 75 75-76 81-82 82-83 83-84 84-85 81-82 82-83 84-85
Selection Guide
Part Number DIP24 (SMD) REC5-xx3.3SRW (H4/H6) REC5-xx05SRW (H4/H6) (See Notes) REC5-xx09SRW (H4/H6) (See Notes) REC5-xx12SRW (H4/H6) (See Notes) REC5-xx15SRW (H4/H6) (See Notes) REC5-xx05DRW (H4/H6) (See Notes) REC5-xx12DRW (H4/H6) (See Notes) REC5-xx15DRW (H4/H6) (See Notes) REC5-xx3.3SRWZ (H4/H6) REC5-xx05SRWZ (H4/H6) REC5-xx09SRWZ (H4/H6) REC5-xx12SRWZ (H4/H6) REC5-xx15SRWZ (H4/H6) REC5-xx05DRWZ (H4/H6) REC5-xx12DRWZ (H4/H6) REC5-xx15DRWZ (H4/H6) 2:1 Input (REC5-S/DRWH4/H6) xx = 4.5-9Vin = 05 xx = 9-18Vin = 12 xx = 18-36Vin = 24 xx = 36-72Vin = 48 Input Voltage (VDC) 9 - 18, 18 - 36, 36 - 72 9 - 18, 18 - 36, 36 - 72 4.5 - 9 9 - 18, 18 - 36, 36 - 72 4.5 - 9 9 - 18, 18 - 36, 36 - 72 4.5 - 9 9 - 18, 18 - 36, 36 - 72 4.5 - 9 9 - 18, 18 - 36, 36 - 72 4.5 - 9 9 - 18, 18 - 36, 36 - 72 4.5 - 9 9 - 18, 18 - 36, 36 - 72 4.5 - 9 9 - 36**, 18 - 72 9 - 36**, 18 - 72 9 - 36, 18 - 72 9 - 36, 18 - 72 9 - 36, 18 - 72 9 - 36, 18 - 72 9 - 36, 18 - 72 9 - 36, 18 - 72 Output Voltage (VDC) 3.3 5 9 12 15 ±5 ±12 ±15 3.3 5 9 12 15 ±5 ±12 ±15 Max. Cap. Load (µF) 2200 1000 470 220 120 ±470 ±100 ±68 2200 1000 470 220 120 ±470 ±100 ±68 Output Current (mA) 1200 1000 556 420 340 ±500 ±210 ±170 1200 1000 556 420 340 ±500 ±210 ±170