新型纺纱加工技术及应用
纺纱新技术发展现状及趋势

纺纱新技术发展现状及趋势摘要探讨纺纱新技术的发展现状及趋势。
分析了近年来环锭纺纱新技术和新型纺纱新技术的发展现状,综述了环锭纺、转杯纺和喷气涡流纺在纺纱方法、自动化智能化以及器材与专件等方面的进展,展望了纺纱新技术在全流程连续化、短流程、节能降耗、提高纺纱速度等方面的发展趋势,介绍了梳并联、细纱自动接头、超大牵伸、节能集聚纺、多级气圈、双分梳转杯纺和离心纺等新技术,并给出了对未来纺纱技术的预期。
认为:加强纺纱理论研究是纺纱新技术发展的基础,多学科特别是信息学科与纺纱结合将为纺织行业进步提供强大动力,螺旋式发展模式是纺纱新技术进步的特征。
关键词纺纱新技术;环锭纺;新型纺纱;智能化;短流程;节能纺纱活动伴随着人类文明的推进而发展。
回顾纺纱技术的发展历程,离不开开松、梳理、牵伸和加捻四大原理,目前纺纱技术也基本没有完全突破这些原理,只是在实现方式上有所区别或者在细节方面有所丰富。
从动力驱动和控制技术的角度来看,由于蒸汽机、电动机、变频技术和伺服电机等的应用,极大提高了纺纱效率和成纱质量的稳定性。
当前的纺纱产业界,环锭纺仍占主导地位,而转杯纺和喷气涡流纺也得到了迅速发展,成为新型纺纱中的主力军。
环锭纺的发展出现了集聚纺、低扭矩纺、全聚纺、聚纤纺、赛络纺和数码纺等,而新型纺纱技术中出现了静电纺、转杯纺、摩擦纺、喷气涡流纺、自捻纺和离心纺等新方法。
本文分别就环锭纺纱与新型纺纱两种体系来分析近年来纺纱新技术的进展,并展望未来的发展趋势。
1纺纱新技术的进展1.1环锭纺纱新技术的发展现状迄今为止,环锭纺依然是纺纱技术应用的主体,其优点和不足均非常明显。
环锭纺的优势体现在成纱结构合理、适纺号数范围广等方面,尤其是在特细号纱领域。
其缺点是工序长、纺纱速度受限、卷装尺寸受限、用工相对较多。
以下从3方面阐述环锭纺新技术的发展。
1.1.1环锭纺的改良技术近年来,集聚纺、低扭矩纺(假捻纺)、柔洁纺、复合纺和数码纺等技术的涌现和应用,使环锭纺纱技术得以进步与改良,成纱质量得到提高与改善。
环锭纺、气流纺、喷气纺、涡流纺、赛络纺、紧密纺简介

环锭纺、气流纺、喷气纺、涡流纺、赛络纺、紧密纺简介环锭纺、气流纺、喷气纺、涡流纺、赛络纺、紧密纺简介环锭纺环锭纺纱是现时市场上用量最多,最通用之纺纱方法,条子或粗纱经牵伸后的纤维条通过环锭钢丝圈旋转引入,筒管卷绕速度比钢丝圈快,棉纱被加捻制成细纱.广泛应用于各种短纤维的纺纱工程.如普梳,精梳及混纺,钢丝圈由筒管通过纱条带动绕钢领回转.进行加捻,同时,钢领的摩擦使其转速略小于筒管而得到卷绕.纺纱速度高,环锭纱的形态,为纤维大多呈内外转移的圆锥形螺旋线,使纤维在纱中内外缠绕联结,纱的结构紧密,强力高,适用于制线以及机织和针织等各种产品。
环锭纺(精梳)流程:清花间--梳棉--预并条--条并卷--精梳--头道并条--二道并条--粗纱--细纱--络筒环锭纺(普梳)流程:清花间--梳棉--头道并条--二道并条--粗纱--细纱--络筒气流纺气流纺不用锭子,主要靠分梳辊、纺杯、假捻装置等多个部件。
分梳辊用来抓取和分梳喂入的棉条纤维,同过他的高速回转所产生的离心力可把抓取的纤维甩出。
纺杯是个小小的金属杯子,他的旋转速度比分梳辊高出10倍以上,由此产生的离心作用,把杯子里的空气向外排;根据流体压强的原理,使棉纤维进入气流杯,并形成纤维流,沿着杯的内壁不断运动。
这时,杯子外有一根纱头,把杯子内壁的纤维引出来,并连接起来,再加上杯子带着纱尾高速旋转所产生的钻作用,就好像一边“喂”棉纤维,一边加纱线搓捏,使纱线与杯子内壁的纤维连接,在纱筒的旋绕拉力下进行牵伸,连续不断的输出纱线,完成气流纺纱的过程。
气流纺的特征气流纺纱有速度大、纱卷大、适应性广、机构简单和不用锭子、钢领、钢丝圈的优点,可成倍的提高细纱的产量。
气流纺与环锭纺的区别气流纺与环锭纺一个是新型纺织技术,一个是老式纺纱技术。
气流纺是气流纺纱,而环锭纺则是机械纺,就是由锭子和钢铃、钢丝圈进行加捻,由罗拉进行牵伸。
而气流纺则是由气流方式输送纤维,由一端握持加捻。
一般来说,环锭纱毛羽较少,强度较高,品质较好。
浅析喷气涡流纺纱技术
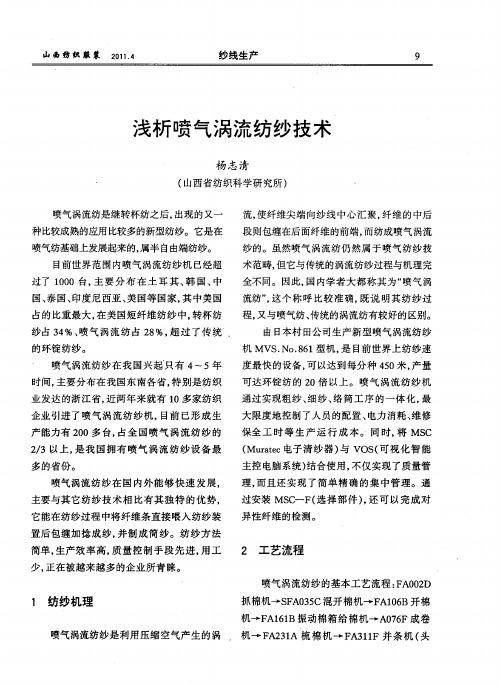
流, 使纤维尖 端 向纱 线 中心 汇 聚 , 维 的 中后 纤 段 则包缠在后面纤 维的前端 , 纺成喷气 涡流 而 纱的。虽然 喷气涡 流纺 仍然 属 于 喷气纺 纱 技 术 范畴 , 但它与传统 的涡流纺纱过 程与机理 完 全不 同。因此 , 内学者 大都 称其 为“ 国 喷气 涡 流纺 ” 这 个 称 呼 比较 准 确 , 说 明其 纺 纱过 , 既 程, 又与喷气纺 、 传统 的涡 流纺有较好 的区别。 由 日本村 田公 司生产 新型 喷气 涡流 纺纱 机 MV . .6 型 机 , 目前世 界上 纺纱 速 S No 8 1 是
度 最快 的设备 , 以达 到 每分 种 4 0米 , 量 可 5 产
可达 环锭 纺 的 2 0倍 以上 。 喷气 涡 流 纺 纱 机
通过 实现粗 纱 、 纱 、 筒 工 序 的 一体 化, 细 络 最 大 限度地 控制 了人员 的配置 、 电力 消耗 、 修 维 保全 工 时 等 生 产 运 行 成 本 。 同 时。 MS 一 将 C
过 了 10 0 0台, 要 分 布 在 土 耳 其 、 国 、 主 韩 中 国、 国、 泰 印度 尼西 亚 、 国等 国家 , 中美 国 美 其 占的 比重 最大 , 美 国短 纤 维纺纱 中, 在 转杯 纺 纱 占 3 %、 4 喷气 涡流 纺 占 2 %, 过 了传 统 8 超 的环锭纺 纱 。 喷气 涡流 纺纱 在 我 国 兴起 只 有 4 ~5年 时 间, 主要 分布 在 我国东 南各 省 , 特别 是纺 织 业发达 的浙江 省 , 两年 来就 有 1 近 0多 家纺 织 企业 引进 了 喷气 涡 流 纺纱 机 , 目前 已形 成 生 产能力 有 2 0多 台 , 0 占全 国 喷气 涡 流 纺纱 的 2 3以上 , 我 国拥 有 喷气 涡流 纺 纱 设 备 最 / 是 多的 省份 。 喷气涡流 纺纱 在 国 内外 能 够 快 速 发 展 ,
环锭纺、气流纺、喷气纺、涡流纺、赛络纺、紧密纺简介

环锭纺、气流纺、喷气纺、涡流纺、赛络纺、紧密纺简介环锭纺环锭纺纱是现时市场上用量最多,最通用之纺纱方法,条子或粗纱经牵伸后的纤维条通过环锭钢丝圈旋转引入,筒管卷绕速度比钢丝圈快,棉纱被加捻制成细纱.广泛应用于各种短纤维的纺纱工程.如普梳,精梳及混纺,钢丝圈由筒管通过纱条带动绕钢领回转.进行加捻,同时,钢领的摩擦使其转速略小于筒管而得到卷绕.纺纱速度高,环锭纱的形态,为纤维大多呈内外转移的圆锥形螺旋线,使纤维在纱中内外缠绕联结,纱的结构紧密,强力高,适用于制线以及机织和针织等各种产品。
环锭纺(精梳)流程:清花间--梳棉--预并条--条并卷--精梳--头道并条--二道并条--粗纱--细纱--络筒环锭纺(普梳)流程:清花间--梳棉--头道并条--二道并条--粗纱--细纱--络筒气流纺气流纺不用锭子,主要靠分梳辊、纺杯、假捻装置等多个部件。
分梳辊用来抓取和分梳喂入的棉条纤维,同过他的高速回转所产生的离心力可把抓取的纤维甩出。
纺杯是个小小的金属杯子,他的旋转速度比分梳辊高出10倍以上,由此产生的离心作用,把杯子里的空气向外排;根据流体压强的原理,使棉纤维进入气流杯,并形成纤维流,沿着杯的内壁不断运动。
这时,杯子外有一根纱头,把杯子内壁的纤维引出来,并连接起来,再加上杯子带着纱尾高速旋转所产生的钻作用,就好像一边“喂”棉纤维,一边加纱线搓捏,使纱线与杯子内壁的纤维连接,在纱筒的旋绕拉力下进行牵伸,连续不断的输出纱线,完成气流纺纱的过程。
气流纺的特征气流纺纱有速度大、纱卷大、适应性广、机构简单和不用锭子、钢领、钢丝圈的优点,可成倍的提高细纱的产量。
气流纺与环锭纺的区别气流纺与环锭纺一个是新型纺织技术,一个是老式纺纱技术。
气流纺是气流纺纱,而环锭纺则是机械纺,就是由锭子和钢铃、钢丝圈进行加捻,由罗拉进行牵伸。
而气流纺则是由气流方式输送纤维,由一端握持加捻。
一般来说,环锭纱毛羽较少,强度较高,品质较好。
气流纺工序短,原料短绒较多,纱线毛,支数和拈度不能很高,价格也较低。
新型纺纱技术

(1)自控程度高 (1)自控程度高
涡流纺整个纺纱过程受到电子系统的监控, 电子清纱器发现纱疵时即自动去除疵点,并立 即应用自动接头装置将纱接起来,因此整个纺 纱过程是全自动、连续式的。此外,每个锭子 的纱都受到自动接头器的监控,如有异常,可 实现单锭自动停止纺纱。
(2)工艺流程短 (2)工艺流程短
2、涡流纺的主要特点
涡流纺无高速回转机件采用旋转涡流加捻成纱,比 机械式加捻效率高,高速回转的涡流只作用在纤维 上,与前罗拉引出的纤维的功能一起形成对纤维的 加捻作用,高速涡流除了完成加捻任务外,并不影 响纱线支数的高低,因此可实现高速纺纱,最高纺 速实际可达380m/min,每锭的产量相当于环锭纺单 锭产量的22倍左右。由于纤维受到具有声速的喷气 涡流及卷取罗拉作用而形成真捻,因此这种特殊的 加捻作用是其它纺纱机械不能取代的,纱线高的回 旋速度下的成纱结构比环锭纱线的结构更为紧密和 稳定。
3、紧密纱线的特点
毛羽少,光洁度高。其毛羽一般比普通纱减少 70%-80%; 强度高,捻度减少。同样的纱支捻度减5%-15%, 而强力却提高约15%-25% ; 条干好。由于纤维的利用率得以提高,乌斯特条干能 够达到3%-5%; 能代替股线。由于紧密纱的强度高,其单纱可以替代 传统股线。如 16.2tex的紧密纱与8.1×2tex的传统股 线具有同等强度,在生产工艺上可以减少合股工序;
从以上紧密纱的特点可以看出它是一种与 众不同的高品质纱。由于它的优良特性给纺 纱、准备、织造、印染等一系列后道加工带 来了工艺创新,降低了后加工流程和成本, 尤其是减少了浆纱和烧毛对环境造成的工业 污染。
总之,紧密纺纱技术是目前环锭细纱机关键的重 要技术进步。纱线质量及生产费用等方面的优势,将 使紧密环锭纺纱技术不但本身具有高档产品的特征, 而且将逐步取代传统环锭纺纱技术,使纺织工业及时 装工业具有更开阔的产品开发空间,使服装设计可以 从紧密纱纺纱到最终产品进行一系列的设计,这种独 特的生产优势,一方面提高了产品档次,另一方面也 考虑了产品的经济性、生态环境特性、创新性及独特 性等。现在, 性等。现在,紧密纱在市场上的售价比传统环锭纱每公 斤高1 3.5美元,经济效益十分可观,更重要的是消费 斤高1-3.5美元,经济效益十分可观,更重要的是消费 者非常欢迎。因此,紧密纺纱技术将得到快速发展。
(完整版)主要新型纺纱的比较

主要新型纺纱的比较1、成纱原理:转杯纺依靠调整回转的纺杯,将纱尾贴紧在纺杯内壁聚槽内,而头端为引纱罗拉握持并连续输出加捻成纱。
喷气纺靠两只喷嘴喷射相反方向的回旋气流,对由牵伸装置输出的须条先加捻后解捻,表面纤维形成包缠成纱。
摩擦纺一般用两只同向回转的摩擦元件,对其楔形区的纤维施加摩擦力偶,使纤维束滚动而加捻成纱。
2、成纱截面中纤维根数不同:喷气纱中最少纤维根数略高于环锭纱,可纺中低线密度纱;摩擦纺和转杯纺中的最少纤维根数较多。
3、对纤维性能要求不同:影响转杯纱强力的主要因素是纤维的强力和线密度,摩擦纱则是纤维的摩擦因数和强力。
4、纺纱速度和成纱线密度:环锭纺的可纺线密度覆盖面最广,但产量太低,各种新型纺纱的纺纱速度都比环锭纺高,但可纺线密度有局限性5、新型特点:新型纺纱取消了锭子、筒管、钢领、钢丝圈等加捻卷绕元件,并将加捻和卷绕作用分开完成,具有产量高,细纱机的产量取决于锭子的速度,而锭速的提高,一方面受钢丝圈速度的限制,另一方面受气圈张力的限制;卷装大,环锭细纱机上增大卷装的途径是增加筒管长度和加大钢领直径,但筒管加长则气圈高度加长,钢领加大则钢丝圈线速度增大,这些都会导致断头增多,而新型纺纱方法将加捻和卷绕分开进行,可直接纺成筒子纱;工艺流程短,新型纺纱采用条子喂入,直接纺成筒子纱,省去粗纱、络筒两道工序。
转杯纺1、原理:纺杯高速旋转,纺杯内便产生离心力,离心力可使从分流腔转移到纺杯内的棉纤维产生凝聚而成为须条,须条被加捻后便成为纱条。
2、工艺过程:条子从条筒中引出送入喂给罗拉,喂给罗拉与喂给板将条子向前输送,经分梳辊分梳成单纤维,被补风口和引纱管的气流吸入纺纱杯,沿纺纱杯壁滑入凝聚槽形成凝聚须条,由于纺纱杯高速回转产生的离心力使引纱纱尾贴附于凝聚槽面而与须条连接,并被纺纱杯摩擦握持而加捻成纱。
3、转杯纱结构与性能:转杯纱由纱芯与外包缠纤维两部分组成,内层的纱芯比较紧密,外层的包缠纤维结构松散;环锭纱没有纱芯,纤维在纱中大多呈螺旋线排列。
新材料与新技术在纺织工程中的应用

新材料与新技术在纺织工程中的应用摘要:纺织材料的开发与利用是提高我国经济发展水平和人民生活质量的重要基础。
随着新材料和新技术的高效率、成本低等优点使得纺织工程在国际市场上占据着越来越大的份额。
传统纺织工艺对环境造成了极大污染并且存在资源浪费问题;因此将新型环保材料和技术应用于现代纺织品中具有非常现实的意义。
本文针对纺织工程阐述了新纺织材料与新工程技术的应用及发展前景。
关键词:纺织业;新材料;新技术;应用研究;引言纺织材料及其技术的发展是人类文明进步和经济社会快速增长不可或缺的重要因素。
在技术不断创新和时代不断更新的背景下,新技术和新材料已成为现代先进制造工艺、现代复合材料集成技术、信息处理等高新技术领域必不可少的工具和载体。
中国纺织业目前正在进行世界纺织业的结构调整,并将在很长一段时间内保持快速增长。
在国际市场上,中国正在逐步参与全球纺织品配额,这对纺织企业提出了更高的要求,对纤维原材料的需求也在增加。
新材料和新技术在纺织工程中发挥着重要作用,将成为纤维工业未来发展的重要因素。
一、纺织面料的发展趋势1.纺织面料交叉材料织物交叉是指在纺织技术的应用下,将具有不同功能的材料(如金属丝网)混合在一起,以达到满足一种或多种性能要求的状态。
新型纤维材料适用于各种功能要求,如抗菌、保湿和抗紫外线财产,其中新工艺包括表面处理和染色技术。
随着新技术的应用,新面料发生了重大变化。
然而,由于现代科学技术的快速发展和对纺织品质量的日益增长的需求,传统的织物表面处理方法已不适合现代生产和日常需求;新材料的出现为纺织复合材料开辟了广阔的前景,这种材料利用高强度、耐磨性和良好的抗紫外线性等特性来改进织物表面处理工艺,增强纤维机理。
2.季节性纺织面料的使用观念被打破新材料和新技术的出现对纺织品市场产生了巨大影响。
在传统信仰中,人们认为只要能生产出高质量的产品,但随着科学技术的快速进步,这种观念就会逐渐被打破。
人们越来越关注气候条件和生态环境的变化对服装的负面影响,传统纺织品的季节性变化往往是由气候和环境等因素引起的,导致产品不符合市场需求;而新材料和新技术可以通过反射自然光(紫外线)实现表面装饰效果,为人们提供了一种新的“绿色”消费理念,降低了劳动力成本和原材料消耗,为企业发展提供了良好的经济效益和社会效益。
新一代环锭紧密纺纱技术

张力最小 , 只能 使一部 分纤维 聚集在 一起 , 这就 导
致 了纱线毛 羽 的 产生 。 而在 紧 密 性纺 纱 过 程 中 .
维普资讯
,
饽甜 技
4 5
纤维 柬在 加捻前 先 凝 聚在 一 起 , 因而 不存 在 加捻 三 角区 , 有纤维都 被 聚集在 一起 , 样纱 的毛羽 所 这 数量就 显著 下 降 。在 紧密 性 纺纱 过 程 中 , 细纱 断
收藕 日期 :0 l o —2 20 — 7 5
在, 使加捻 三 角 区的纤 维在外 层所 受 张力晟 大 。 该 侧 纤维能几 乎 全 部 聚集 在 一起 , 中心 纤 维所 受 而
作 者 筒 舟 : 博 (96 . , 士 , 赵 16 一)男 硕 中原 工学 院 讲 师 . 主要 从 事 纺 织生 产 技 术 及 产 品 开 发 工 作 , 及 纺 织 工 程 学 科 以 的 教 学 与研 究 工 作 。
在 紧密性纺 纱 过 程 中 , 由于在 牵 伸 机构 中 的 预拉 伸和 真空 区域 作 用 下 , 使纤 维 在 机 械 和气 动 作用 下被 “ 聚起 来” 经 过这 种纺纱 系统 纺纱 后 。 凝 , 纱线变 得 紧密 , 维 明 显平 行 排 列 , 面 接 近 圆 纤 截 形, 良好 的纤 维 聚集和均 匀的纤 维排 列 , 使纤 维 得 到充分利用 , 图 1 示 。从 图 1中 可 以明 显 看 如 所 出 , 密性 纱 的毛 羽数量小 于传 统环 锭纱 , 紧 这是 因 为在传统 环锭 纺 纱过 程 中 , 由于 加捻 三 角 区的存
新 型纺纱 方法 。然 而 环锭纺仍 是 占压倒 优 势 的重 要纱 线生 产工艺 , 在其 长久 的发展期 间 , 工艺 无 该 论从 多种 应用 可能 性 来看 , 还是 从成 品纱 的质量 来看, 都是 比较完美 的 , 大多数 产品仍 然必 须用 环 锭纺纱 工艺 所生 产 的高质 量 纱 来进 行 生 产 加 工。 尽管 环锭纱 有许 多 显 著优 点 , 且是 衡 量 其 它类 并 型纱线 质量 的标准 , 是 它并不是 完美无 缺 的 , 但 特 别是纱 线表 面毛 羽 根数 多 这一 问题 , 近年 来 一 直
新型纺纱技术的发展与传统环锭纺纱技术的进步
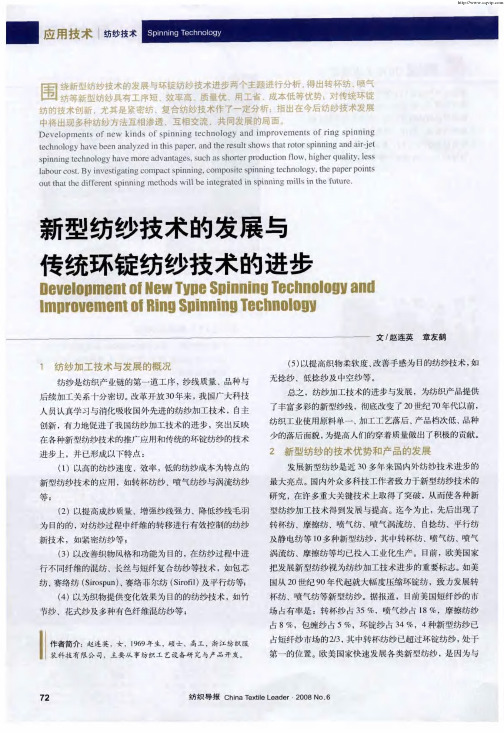
、 、
在 纺 纱 过 程 中进
,
涡流纺
、
摩 擦 纺 等 均 已 投 入 工 业 化生 产
目前
欧美国家
。
长 丝 与 短 纤 复 合 纺 纱 等技 术
n
、
如 包芯
把 发 展 新 型 纺 纱 视 为 纺 纱加 工 技 术进 步 的 重 要 标 志 如 美
国从 2 0 世 纪 9 0 年 代 起 就 大 幅 度 压 缩 环 锭 纺 杯纺
工省 、成本 低的 优势 。
( )纱 线的 耐摩性 优 于环锭 纱 5
因为喷 气纱 、 气涡 流纱 均有 纱芯和 外 包纤维 两部 分 喷 组成 , 条表 面包 有 不规 则的缠 绕纤 维 ,不 易解体 , 纱 纱 且 线表 面摩擦 系数大 , 在织 物 中纱 与纱之 间的 抱合 良好 ,不
装科枝 有 限 公 司
主要从 事纺织
艺 设 备 研 究 与产 品 开 发
第
一
的位 置
。
欧 美 国 家快 速 发 展 各 类 新 型 纺 纱
,
是 因为 与
72
纺织导报
C h in
a
T e x t ile L e
a
de
r
.
2 0 0 8 No
.
6
重庆维普
传统的环 锭纺 纱 比较具 有工 序短 、 产效率 高 、 生 质量优 、 用
2
。
并 已形 成 以 下特 点
、
:
新 型 纺 纱 的技 术 优 势 和 产 品 的 发展
发展新 型 纺纱是近
。
( 1 ) 以高 的 纺纱 速 度
效率
,
新型纺纱3

• 各种纤维形态的产生过程分析: ⒈顺向纺纱纤维凝聚状态:顺向纺纱是指纤维的喂入 方向与成纱的输送方向一致。 ⑴当喂入纤维的一端碰到纱尾时,由于接触状态具有 随机性,没有立即被捻入纱尾而作短暂的停顿,最 终造成纤维沿纱线输出方向的“超喂”现象,使纤 维被突然减速而折皱、屈曲(如图所示)。纤维以这种 不规则形态捻入纱尾,其结果是形成卷缠、打圈纤 维。
(二)摩擦纺纱存在的问题 摩擦纺纱的成纱强力低是影响其成纱质量最主要的 问题。 • 摩擦纺成纱强力低的原因有: ⑴纱线本身的结构所决定,纤维无内外层转移,纱线结 构松散,纤维间抱合力较小,在拉伸过程中易发生相 对滑动; ⑵纤维在纱线中的伸直度和定向性很差,因而使纱线结 构较松散,强力较低 ⑶摩擦纺成纱中各截面上的捻度分布与环锭纱不同,其 各层捻度由外向内几乎是线性增加的,内层的捻度大 约是外层的2倍,整个纱体呈现内紧外松的特点,其 成纱结构比环锭纱膨松得多。 • 结论:摩擦纺的加工方法和纱线结构决定其成纱中纤 维长度利用系数较低,大约为61%左右;纤维径向压 力小,抱合力差,纤维间的断裂不同时性增大,因而 导致成纱强力低。
⑵当喂入纤维一端碰到纱尾时,立即被捻入纱尾且喂 入伸直的纤维落入凝棉槽时平行于纱尾,即纤维的 头端和尾端基本上同时接触纱尾,其结果形成较规 则的圆锥形或圆柱形螺旋线纤维(②图所示),其方向 性较好。 ⑶喂入伸直的纤维,与纱尾接触时的位置是顺着纱线 的输出方向(③图所示),其结果是纤维头端a沿锥形 纱尾包卷成螺旋状,而尾端b则由于追赶头端而又未 能超越头端的位置(沿输出方向)而被甩在纱尾之外, 容易与外层新喂入的纤维纠缠在一起而形成后端卷 缠的形态,纤维的伸直度在捻入过程中受到破坏。
dv
dv
c Xv
• 结论:摩擦纺成纱内外层纤维捻度不同的根本原 因是它们的加捻开始点的位置不同,及纱条在轴 向各点位置的绕纱轴的转速不同。 • 在这里最外层纤维上的捻度就是输出纱线的轴向 捻度(TL),由捻度公式可知: ND ND
新型纺纱技术东华大学纺纱学精品PPT课件

B
紧密纺成纱品质
紧密纺毛羽明显减少,尤其是3mm以上的毛羽, 提高了成纱强力,与同特数的环锭纱相比,毛 羽降低70%,细纱强力提高5-10%。
二、塞络纺纱
一种在细纱机上加工股 线的方法。把细纱、络 筒、并纱、和捻线合为 一体。
➢ 原理:两根粗纱以一定 的间距平行喂入环锭细纱 机的同一牵伸机构被牵伸。
第五节 新型纺纱技术
本节主要内容:
一、紧密纺纱 ** 二、赛络纺纱 * 三、赛络菲尔纺 四、缆型纺纱 五、转杯纺纱 ** 六、喷气纺纱 ** 七、喷气涡流纺纱 八、摩擦纺纱 * 九、涡流纺纱 * 十、自捻纺纱 **
环锭改革的纺纱新技术 紧密纺纱 赛络纺纱 赛络菲尔纺 缆型纺 自由端纺纱
新型纺纱新技术 非自由端纺纱:喷气纺、自捻纺 转杯纺纱 喷气纺纱 摩擦纺纱 喷气涡流纺 涡流纺纱 自捻纺纱
➢ 工艺过程:两根平行的粗 纱经导纱器进入牵伸区, 经前罗拉牵伸后输出,形 成一个三角区,并汇集到 一点,合并后由锭子和钢 丝圈回转给纱线加捻。
三、塞络菲尔纺
由一根经牵伸后的须条 与一根不经牵伸但具有 一定张力的复丝在加捻 三角区复合加捻形成的 复合纱。
原理:长丝经前罗拉喂 入,在前罗拉出口处 长丝和经过牵伸的短 纤维束保持一定的间 距输出。
3、Rotocraft RoCos®纺纱装置
机械式纺纱装置: 优点:机构简单。 缺点:成纱毛羽指标不如前者。
3、 RoCos纺纱装置特征
(1)在原牵伸区前增加一个机械集束区。 (2)前罗拉前加2个胶辊。第一胶辊与前罗拉组成握持钳 口,
第二胶辊与前罗拉组成牵伸钳口。1、2胶辊间有集合器。 集合器为须条的集束区。 (3)集合器依靠磁性贴于前罗拉表面,依靠机械作用使须条 紧密集合,避免了依靠吸风负压所必须的分析、吸风管、 网格圈等。
各种纺纱方法简介

各种纺纱方法简介中国是纺织大国,也是纺织技术的发源地之一,纺织在我国有着悠久的历史。
今天主要来谈一下,纺纱技术的分类,纺织发展到今天主要的纺纱技术还是环锭纺,但也呈现出越来越多新形式,总结起来主要有如下一些:(1)环锭纺纱(ring spinning),是现时市场上用量最多,最通用之纺纱方法,条子或粗纱经牵伸后的纤维条通过环锭钢丝圈旋转引入,筒管卷绕速度比钢丝圈快,棉纱被加拈制成细纱。
广泛应用于各种短纤维的纺纱工程。
如普梳,精梳及混纺,钢丝圈由筒管通过纱条带动绕钢领回转。
进行加拈同时,钢领的摩擦使其转速略小于筒管而得到卷绕。
纺纱速度高,环锭纱的形态,为纤维大多呈内外转移的圆锥形螺旋线,使纤维在纱中内外缠绕联结,纱的结构紧密,强力高,适用于制线以及机织和针织等各种产品。
环锭纺(精梳)流程:清花间--梳棉--预并条--条并卷--精梳--头道并条--二道并条--粗纱--细纱--络筒环锭纺(普梳)流程:清花间--梳棉--头道并条--二道并条--粗纱--细纱--络筒(2)无拈纺纱(twistless processing)使用粘合剂使纤维条中的纤维互相粘合成纱的一种纺纱方法。
粗纱经牵伸装置牵伸后,须条被送到加捻滚筒上,回滚筒上来自槽箱中的薄层粘合剂接触。
纤维条由数根回转的小压辊与滚筒一起向前输送,其中一根小压辊还同时作轴向往复运动,将纤维条搓成圆形截面,并使每根纤维都能均匀地接触到粘合剂。
圆形纤维条通过加热器烘燥,纤维互相粘牢成纱。
纺纱速度可比常规纺纱方法大2~4倍,制成的纱可供织造用。
(3)自拈纺纱(self-twist spinning)一种非传统纺纱方法。
(siro yarn类同)将两根纤维条经牵伸装置拉细,由前罗拉、搓捻辊输出,在导纱钩处合。
搓捻辊除回转外,并快速轴向往复运动,搓转纱条,使搓捻辊前后的纱条获得方向相反的捻回。
在导纱钩处合后的两根纱条,依靠它们本身的抗扭力矩自行拈合成双股自拈纱(ST纱),卷绕成筒子。
新型纺纱技术的发展与传统环锭纺纱技术的进步
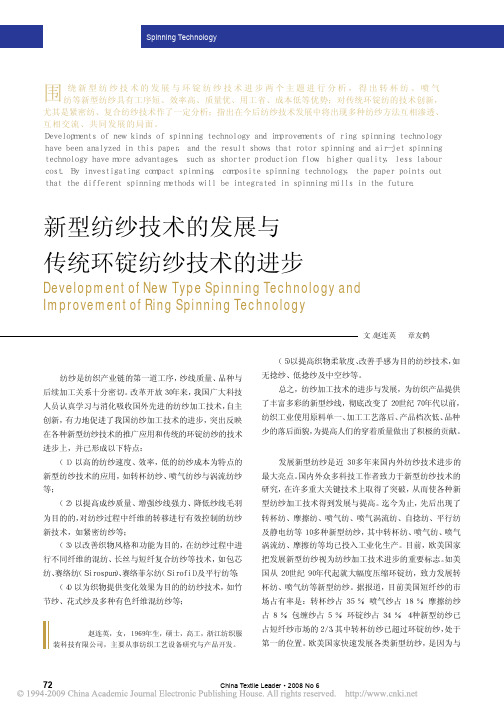
纺纱技术|应用技术Suessen(绪森)公司的依丽纺(Elite)、瑞士Rieter(立达)公司的卡摩纺(Com4)、德国Zinser(青泽)公司(现并入Oerlikon Schlafhorst) — Tex700集聚纺等。
在国内外已批量生产的紧密纺细纱机及紧密纺装置还有:经纬纺机榆次公司生产的1530型、上海二纺机生产的138JCB型、东台马佐里生产的139型、海军4806工厂生产的ZJ1298型、日本Toyota(丰田)EST紧密纺以及瑞士RoCos磁紧密纺等紧密纺细纱机以及宁波韵升集团德昌纺机自主研发的紧密纺装置与江阴华方科技公司生产的紧密纺装置等。
其中经纬纺机榆次公司紧密纺细纱机配置Suessen公司依丽纺装置。
东台马佐里紧密纺细纱机多数是配德昌的紧密纺装置。
纵观已在生产中使用的紧密纺细纱机,虽其型号不一,形式多样,除RoCos磁性紧密纺装置外,都是在加捻三角区采用负压集聚原理,即在前罗拉加装一套控制元件来加强对纤维的控制,其中下罗拉有吸风集聚作用,使须条较紧密地排列,大大减少了传统细纱机中加捻三角区中须条宽度,以利于将须条中的纤维捻卷到纱条中,从而可较大幅度减少成纱中尤其是3 mm以上的有害毛羽。
同时,负压吸风也有利于纤维在加捻卷绕时有一次的伸直机会,使纱线强力得以提高。
从众多使用厂实践证实,在同样半制品的条件下,采用紧密纺细纱比原环锭细纱机成纱毛羽减少80 %左右,强力可提高5 % ~ 10 %。
同时,因纱的条干均匀度改善,纱疵减少,纺纱时断头率降低,使生产效率也可提高10 %左右。
由于紧密纺纱线强力提高,毛羽减少,在后续工序中,整经时断头率可降低30 %,浆纱时可减少上浆率,织造时经纬纱断头率可分别降低50 %与30 %,从而提高布机生产效率。
紧密纺纱线在针织机上加工时,可免去上蜡,减少布面的起毛起球,提高针织物质量。
紧密纺纱技术虽然在国内推广应用时间还较短,但以其独特的纺纱机理、优良的成纱性能、较好的经济回报受到纺纱企业的高度重视,其发展速度将会加快。
新型纺纱技术

3、紧密纱线的特点
毛羽少,光洁度高。其毛羽一般比普通纱减少 70%-80%;
强度高,捻度减少。同样的纱支捻度减5%-15%, 而强力却提高约15%-25% ;
条干好。由于纤维的利用率得以提高,乌斯特条干能 够达到3%-5%;
能代替股线。由于紧密纱的强度高,其单纱可以替代 传统股线。如 16.2tex的紧密纱与8.1×2tex的传统股 线具有同等强度,在生产工艺上可以减少合股工序;
(1)清花工艺
▪ 采用“多梳少打,以梳代打,少落快喂” 的工艺路线,尽量减少开松对纤维的损伤。 适当降低各打手速度,一般A036打手速度 不高于550r/min,A076C打手速度不高于 950 r/min。同时增加风扇速度与打手速度 之比,保证棉流顺利输送,减少棉结。
(2)梳棉工艺
▪ 为减少纤维损伤,梳棉采用:“轻定量、低速度、 大隔距、小张力”工艺原则,以使纤维得到充分 梳理和良好转移。针布的选用应考虑强化梳理、 转移、减少棉结和纤维损伤,达到提高针布间的 分梳、转移能力,使纤维在梳理过程中获得最佳 的梳理质量。适当提高刺辊速度,增强刺辊和开 松梳理作用,同时提高刺辊纤维向锡林的转移能 力,达到减少棉结和改善成纱条干的效果。适当 增加锡林与道夫间速比,实现快转移,可明显提 高生条的纤维伸直度,减少纤维弯钩的产生,改 善涡流纺纱质量。
❖ 还有一种紧密纺纱系统不采用吸风而采用机械磁铁原理工作, 如罗卡斯紧密纺系统装置,其 前胶辊和引纱胶辊置于前下罗拉之上, 磁性紧 密器置于两个胶辊之间,共同形成紧密区。紧 密器与下罗拉之间紧密接触,没有间隙,上、 下罗拉一起形成一个完全封闭的负压区,其底 部的弧度与下罗拉表面完全一致,纤维束与罗 拉同步移动,通过紧密器的纤维通道,被安全 地输送到引纱钳口。
简述赛络纺成纱的工艺过程
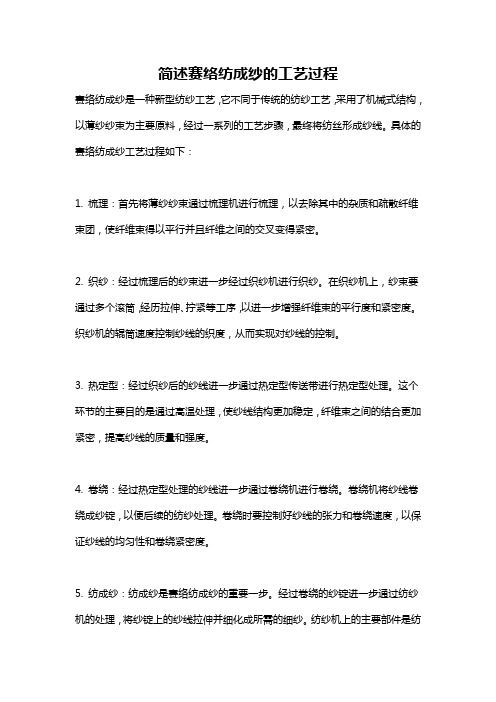
简述赛络纺成纱的工艺过程赛络纺成纱是一种新型纺纱工艺,它不同于传统的纺纱工艺,采用了机械式结构,以薄纱纱束为主要原料,经过一系列的工艺步骤,最终将纺丝形成纱线。
具体的赛络纺成纱工艺过程如下:1. 梳理:首先将薄纱纱束通过梳理机进行梳理,以去除其中的杂质和疏散纤维束团,使纤维束得以平行并且纤维之间的交叉变得紧密。
2. 织纱:经过梳理后的纱束进一步经过织纱机进行织纱。
在织纱机上,纱束要通过多个滚筒,经历拉伸、拧紧等工序,以进一步增强纤维束的平行度和紧密度。
织纱机的辊筒速度控制纱线的织度,从而实现对纱线的控制。
3. 热定型:经过织纱后的纱线进一步通过热定型传送带进行热定型处理。
这个环节的主要目的是通过高温处理,使纱线结构更加稳定,纤维束之间的结合更加紧密,提高纱线的质量和强度。
4. 卷绕:经过热定型处理的纱线进一步通过卷绕机进行卷绕。
卷绕机将纱线卷绕成纱锭,以便后续的纺纱处理。
卷绕时要控制好纱线的张力和卷绕速度,以保证纱线的均匀性和卷绕紧密度。
5. 纺成纱:纺成纱是赛络纺成纱的重要一步。
经过卷绕的纱锭进一步通过纺纱机的处理,将纱锭上的纱线拉伸并细化成所需的细纱。
纺纱机上的主要部件是纺杆,它和纺纱盘一起协作,通过旋转运动将纱线进行拉伸和放松的过程,最终形成细纱。
6. 加工:经过纺成纱后的细纱还需要经过一系列的加工工艺,以增强纱线的美观度和品质。
这些加工工艺包括拧捻、浸染、整理等。
拧捻可增加纱线的强度和弹性;浸染可使纱线着色,增加纱线的色彩饱和度;整理则是通过一些熨烫、拉伸等工艺,使纱线达到预期的外观和手感。
总的来说,赛络纺成纱是一种机械化纺纱工艺,其主要特点是使用薄纱纱束,同时经过梳理、织纱、热定型、卷绕、纺成纱等多个工艺步骤,最终形成纱线。
这种工艺过程能够高效地生产出高质量的纱线,被广泛应用于纺织工业中。
新材料技术在纺织面料中发展浅谈
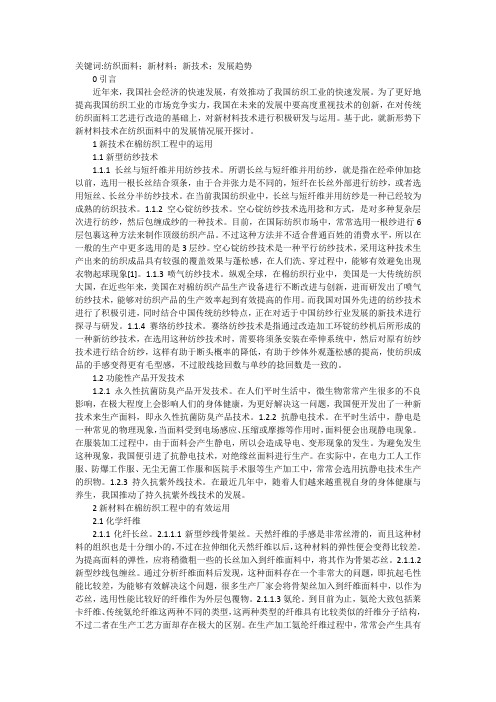
关键词:纺织面料;新材料;新技术;发展趋势0引言近年来,我国社会经济的快速发展,有效推动了我国纺织工业的快速发展。
为了更好地提高我国纺织工业的市场竞争实力,我国在未来的发展中要高度重视技术的创新,在对传统纺织面料工艺进行改造的基础上,对新材料技术进行积极研发与运用。
基于此,就新形势下新材料技术在纺织面料中的发展情况展开探讨。
1新技术在棉纺织工程中的运用1.1新型纺纱技术1.1.1长丝与短纤维并用纺纱技术。
所谓长丝与短纤维并用纺纱,就是指在经牵伸加捻以前,选用一根长丝结合须条,由于合并张力是不同的,短纤在长丝外部进行纺纱,或者选用短丝、长丝分半纺纱技术。
在当前我国纺织业中,长丝与短纤维并用纺纱是一种已经较为成熟的纺织技术。
1.1.2空心锭纺纱技术。
空心锭纺纱技术选用捻和方式,是对多种复杂层次进行纺纱,然后包缠成纱的一种技术。
目前,在国际纺织市场中,常常选用一根纱进行6层包裹这种方法来制作顶级纺织产品。
不过这种方法并不适合普通百姓的消费水平,所以在一般的生产中更多选用的是3层纱。
空心锭纺纱技术是一种平行纺纱技术,采用这种技术生产出来的纺织成品具有较强的覆盖效果与蓬松感,在人们洗、穿过程中,能够有效避免出现衣物起球现象[1]。
1.1.3喷气纺纱技术。
纵观全球,在棉纺织行业中,美国是一大传统纺织大国,在近些年来,美国在对棉纺织产品生产设备进行不断改进与创新,进而研发出了喷气纺纱技术,能够对纺织产品的生产效率起到有效提高的作用。
而我国对国外先进的纺纱技术进行了积极引进,同时结合中国传统纺纱特点,正在对适于中国纺纱行业发展的新技术进行探寻与研发。
1.1.4赛络纺纱技术。
赛络纺纱技术是指通过改造加工环锭纺纱机后所形成的一种新纺纱技术,在选用这种纺纱技术时,需要将须条安装在牵伸系统中,然后对原有纺纱技术进行结合纺纱,这样有助于断头概率的降低,有助于纱体外观蓬松感的提高,使纺织成品的手感变得更有毛型感,不过股线捻回数与单纱的捻回数是一致的。
新型纺纱与花式纱线

《新型纺纱与花式纱线》是现代纺织技术专业的主干课程之一,在理论教学体系中占有重要地位。
随着纺织产业结构调整和纺织市场个性化需求的变化,各种新型纺纱纺制的纱线及具有特殊结构和性能的花式纱线都呈现出极为广阔的市场前景。
目前,在沿海经济发达地区的花式纱线已占有相当的份额,广泛应用于服装、装饰、产业等各类制品。
为了满足教学和纺织工业快速发展的需要,我们做了广泛的市场调研,在分析研究大量相关资料和论文、论著的基础之上,编写了《新型纺纱与花式纱线》一书。
《新型纺纱与花式纱线》由肖丰任主编,尚亚力任副主编,具体分工如下。
第一章、第六章由河南工程学院王秋霞执笔,第二章、第五章由河南工程学院肖丰执笔,第三章、第四章由河南工程学院李营建执笔,第七章、第八章由河南工程学院苏玉恒执笔。
第九章、第十一章由河南工程学院陈理执笔,第十章、第十三章第二节一第五节、第十四章由南通纺织职业技术学院张曙光执笔,第十二章、第十三章第一节由常州纺织服装职业技术学院尚亚力执笔。
全书由肖丰、尚亚力统稿修改完成。
本书附带多媒体光盘由河南工程学院李营建制作。
本书在编写过程中得到了中国纺织工程学会信息专业委员会和河南嵩岳纺织集团的大力支持,在此一并表示感谢。
由于编者的水平有限,而且花式纱线生产技术发展迅猛,生产设备更新很快,书中难免有疏漏或错误,敬请广大读者批评指正。
编者2007年12月第九章花式纱线概iS.本章知识点1.花式纱线的定义。
2.花式纱线的分类。
3.花式纱线的发展及应用情况。
第一节花式纱线的发展及其意义一、花式纱线的发展历史花式纱线在我国有着悠久的历史,早期在色织和粗毛纺产品中都有应用。
20世纪70年代以来新型纱线已成为国际纺织产品市场上一大品种,其用途广泛。
特别是近几年以来,花式纱线的应用越来越广泛,在服装、家纺、产业等领域都有开发利用。
在大连、上海、北京等地举办的纺织品博览会上,花式纱线产品占据了相当高的比例。
国际上采用花式纱线制织的时装面料也是越来越多,根据对2001年意大利女装500块毛纺织面料分析,其中用花式纱线织造的织物占到30%以上。
纺纱技术的研究和开发一直未曾停止过

纺纱技术的研究和开发长泾成教谢劼纺纱技术的研究和开发一直未曾停止过。
近几年来,对传统环锭纺的缺陷出现了许多新的纺纱技术,如聚集纺纱(compact spinning 或condenser spinning)等;通过在传统环锭纺的基础上进行少量改动而形成的,如赛络纺(sirospun)、赛络菲尔纺(sirofil)、缆股纺(solospun)等。
这些纺纱技术的出现和成熟,对于提高纺纱质量、丰富成纱风格和产品开发起到了积极有利的促进作用。
一.新型纺纱技术(一)集聚纺纱集聚纺纱最大的工艺特点,即消除了加捻三角区。
这种纺纱的牵伸形式是对前罗拉输出的须条再加上一对控制罗拉。
其中,下罗拉有吸风聚集作用,使须条较紧密地排列,大大减少了传统环锭纺加捻三角区中须条带的宽度,有利于将须条中纤维可靠地捻卷到纱条中,从而可较大幅度地减少毛羽,同时,吸风也有利于纤维在加捻卷绕时有再一次的伸直机会,从而较大提高成纱强力。
集聚纺纱的牵伸形式,代表了牵伸理论的一种革命趋势,即牵伸和集合的分离。
牵伸区中无集合作用,集合区中无牵伸作用,从而避免了牵伸区中由于集合作用的存在而影响了摩擦力界的分布,而牵伸后的须条再经集合后,减少了须条宽度,增加了紧密度,有利于改善成纱质量。
集聚纺纱的主要优点:1.纱线毛羽及条干的CV值得到了降低,毛羽可降低15-20%,其中大于3mm的长毛羽几乎为零。
2.纱线的断裂强度可提高8-15%。
3.纱线强力不变,捻度可降低10-20%。
单纱的捻系数越低,生产股线时需要加的捻度就越少,从而降低了生产成本。
4.耐磨性比传统的纱线提高40-50%。
5.经络筒工序后,集聚纱毛羽的增加量不足传统环锭纱的50%;集聚纱的棉结数增加10-20%,而环锭纱则要增加40-50%。
6.集聚纺细特股线通常可省去烧毛工序,这意味着原料可以节省6-10%,同时也可以省去为去除传统股线上的烧毛残余物而进行的倒筒工序。
7.整经断头可降低30%,提高整经机效率及产量,经向断头降低50%,纬向断头降低30%,降低织造成本,减少人工接头数量。
- 1、下载文档前请自行甄别文档内容的完整性,平台不提供额外的编辑、内容补充、找答案等附加服务。
- 2、"仅部分预览"的文档,不可在线预览部分如存在完整性等问题,可反馈申请退款(可完整预览的文档不适用该条件!)。
- 3、如文档侵犯您的权益,请联系客服反馈,我们会尽快为您处理(人工客服工作时间:9:00-18:30)。
~10 Cl,a_左右,但梳理前的原料(精干麻)中,最长
的纤维长度可达20 crp.以上,显然,过长或过短的 纤维都将影响加工工艺的选择和产品质量。因
包芯纱 图1中空纱示意图
・
此,苎麻加工中通常采用开松和梳麻来拉断长纤
维(新工艺),或者切断长纤维(老工艺)。其加工
12・
主题报告篇 路线分别为: 老工艺:精干麻一软麻工序一大(中)切工序 一圆梳工序一排麻工序一延展工序(2道)一制条 工序一预并工序(1道~2道)一(精梳工序)一针 梳工序(3道~4道)一粗纱工序一细纱工序. 新工艺:精干麻一软麻工序一开松工序一梳 麻工序一预并工序(2道)一精梳工序一针梳工序 一复精梳工序一针梳工序(3道~4道)一粗纱工 序一细纱工序。 由于老工艺的劳动强度大,生产效率低,用工 多,因此,目前已很少采用.而苎麻的新工艺,主 要是借鉴精梳毛纺的工艺与设备而形成的。 但实际上,新工艺对苎麻来说,也不尽合理, 它为了将苎麻纤维控制在一定的长度,并分离成 单纤维状,采用了开松和梳麻工序,但经过这两道 图3牵切机示意图 长度指标见表1。 因此,苎麻采用牵切技术后,不仅可以大大提 高成纱质量,还可取消原来机构复杂、对纤维损伤 大、生产效率低的梳麻等工序,降低了劳动强度, 纺纱加工流程也相应缩短,用工减少。 苎麻牵切纺纱工艺流程如图3所示。 精干麻一软麻工序一牵切工序一预并工序(1 道)一精梳工序一针梳工序(3~4道)一粗纱工序 一细纱工序。
绢丝等)拉断成条,可以省去开清和梳理工序,大 大减少了对纤维的损伤,也减少了成纱粒子(棉 结),从而提高了成纱的质量。例如,以前主要是 采用精梳落麻与棉纤维混纺,主要目的是利用麻
・
13
・
主题报告篇 成纱中不同纤维分布对纱的阻燃性能的影响 见表7.
襄7纱中不局纤维分布对纱的阻燃性能的影响
Fl F2 17.1 0.0 16.8 F3 7.7 0.0 15.8 F4 11.2 O.0 17.0 F5 5.5 0.0 8.5
cm
Siro纺和包芯纱技术的应用 应用水溶性维纶纺制特种纱水溶性维纶是在
生产维纶时未经过缩甲醛化的聚乙烯醇纤维,由 于其未经缩甲醛处理,故其长链分子上有许多对 水有很强亲和力的羟基,吸湿性好,溶解在一定条 件下的水溶液中。目前我国主要生产在90度水 溶液中溶解的维纶,日本能生产溶解在40度、60 度、75度等多种低温水溶液中的维纶纤维.利用 水溶性维纶,可纺制出各种特殊的纱、线。
强力/oN 强力Cv/%
16.16 20.61
断裂伸长/%
2.8 ቤተ መጻሕፍቲ ባይዱ.4
条干cv/%
20.34 20.21
粗节/个・km。 细节/个・km-1 麻粒/个・kml
355 180 218 168 340 180
常规纱 牵切(非滑溜牵伸)
657.2 693.1
可见,牵切可以提高纤维的长度整齐度,减少 短纤维率,从而能提高成纱的质量,尤其是减少粒 子和毛羽等。 与棉纺厂最相关的是,将长纤维(如苎麻、毛、
1.1.1空心纱
采用包芯纺纱技术(如图l所示),将水溶性 维纶作为芯纱,棉或其他纤维作为外包纱。纺成纱 后,再将其中的芯纱(水溶性维纶)溶解掉。 1.1.2沟槽纱 由于包芯纱中,水溶性维纶被紧密地包在纱 芯。故影响了其溶解程度,一般溶解率为70%左 右,而采用siro纺的技术(如图2所示),使水溶性 维纶与棉或其他纤维交替地成纱.就可以更发便 地将维纶溶解掉,形成的纱表面为沟槽型,织成织 物后,也可形成具有储存静止空气的空问,达到保 暖的目的。
放电能力的测试:结果如图12。
?
a
色
X
续燃时问/s 阴燃时问/s 损毁长度/ram
0.0 0.0
嚣
丑 跖 拉 纱芯 全截面
4.8
表面
图12导电纤维吉量和位置对放电能力的影响
从图12中可看出,不论导电纤维在纱线中如 何分布,电晕放电能力(即抗静电能力)都随着纱 线中导电纤维含量的增加而增大f在导电纤维含 量相同时,都是以导电纤维分布在纱线表面的电 晕放电能力最大。 电阻率测试:在标准温湿度条件下测定纱的 导电性能。结果如图13所示.
表2
同锭纺常规纱与牵切滑溜牵伸纱对比 强力/cN 强力cv/% 断裂伸长/%
2.7 2.2
条干cv/%
19.74 19.61
粗节/个・kml 细节/个・km‘1 麻粒/个・kml
330 270 210 192 450 420
常规纱
牵切(滑溜牵伸)
634.2 628.7
20.31 21.68
表3
同锭纺常规纱与牵切非滑溜牵伸纱对比
・17・
e
●
a
色
,一
×
圈
科 丑 醛 控
器黪@
Ca)包苍 (b)均匀 Co)表面 图10导电纤维在纱中的不同分布 图11导电纤维在纱中“断路”
图13纱线的体积比电阻与导电纤维含量和 位置的关系 电阻率可用来表达含导电纤维织物的抗静电 性能,一般来说,纱线的体积比电阻小于1010(1/ cr]f1.,即具有较好的抗静电性。 从图1z可以看出,含有导电纤维的纱线的体 积比电阻都远小于lOlO&'),/cm,约为103(I/cm左 右,因而说明它们都具有非常好的导电性。在导 电纤维含量相同的条件下,纱线的体积比电阻以 导电纤维分布在纱线表面为最小.纱线的体积比 电阻随着导电纤维含量的增加而降低。
表1
苎麻牵切前后条子中的纤维长度指标
条子1(单精抗) 常规麻条 牵切麻条
79.3
条子2(复精桅) 常规麻条
104.5
42
牵切麻条
92.4
33.4 3.O
平均长度/ram
83.5 43.1 10.2 22.5
长度不匀/%
短纤维率/%
33.2 8.3 13.9
3.8 35.2
长纤维牢/%
22.5
牵切纱测试结果(见表2、表3)(均为同锭纱 对比,27.8 tex)
2008,中国纱线质量暨新产品开发技术论坛文集
新型纺纱加工技术及应用
郁崇文
(东华大学纺织学院)
纺纱技术的发展.不仅使成纱的质量得到改
善,也为开发各种新型纱线产品提供了基础,本文 主要结合一些新型的纺纱技术,讨论其在新型纱 线产品开发中的应用。
l传统环锭纺纱中的新技术
传统的环锭纺纱中,目前已有了较多的革新,
siro纱
如赛罗纺纱、集聚纺纱等,这些发展.给开发新的
纱线产品带来了契机。
1.1
图2沟榴纱示意图
1。1.3特细号股线 在纺特细号纱时,毛纺和苎麻纺中通常利用 水溶性维纶伴纺来纺纱,纺成后再将混在纱中的 维纶溶解掉,使纱的细度得到提高.但此法不利于 加工单纱,在加工股线时较有效。 1.2牵切加工技术 缩短纺纱加工流程是纺纱技术的发展方向。 目前。已有将化纤原料经牵拉后形成短纤的条子, 这种工艺又称为牵切,再将条子经过并条、粗纱和 细纱就可以直接成纱了,省去了开清棉、梳理工 序。也就意味着缩短了加工工序、减少了纤维损 伤、改善了成纱质量。 目前,苎麻行业中正在研究这种纺纱技术,并 已取得一定的成果。 苎麻是我国所特有的纺织原料,我国苎麻纤 维原料的生产占世界的90%~95%。由于其具 有强度高、吸放湿快、织物透气性强和硬挺等特 性,是高档的服装面料。但同时,苎麻纤维又有着 纤维粗、硬,纤维长度长。且长度不匀大(通常达 80%左右)等缺陷。因此.在纺纱中,引起许多加 工、生产不适应等方面的问题,导致其成纱的质量 不高,从而严重制约了其作为高档产品的应用。 苎麻纤维(精梳后)的平均长度一般在9
工序后,原来基本伸直的精干麻中的纤维反而被
打乱,成团或结粒,而梳麻后的苎麻纤维长度离散 度仍很大,超长的纤维数量多,超出平均长度一倍 以上的纤维占5%左右,同时短纤维的数量也很 多,主要是加工中对纤维的损伤造成的。从而不 仅使后续的精梳和针梳工序中排除麻粒的负担增 大(新工艺中,不得不采用2道精梳即复精梳以尽 量减少麻粒),还使后续的精梳、针梳、粗纱、细纱 等工序不得不采用较大的隔距,但较大的隔距又 会使在制品中的短纤维运动无法控制,造成短纤 维在加工中不能得到良好的梳理和牵伸,从而使 成纱的均匀度较差。苎麻牵切前后条子中的纤维