METRIX MODEL 5485C 说明书
METRIX振动变送器ST5484E选型说明

Vibration - Condition Monitoringand Protection2.14Vibration TransmittersST5484E Velocity 4-20 mA• Loop terminals w/Independent Polarity (IPT ®)1. Prevents incorrect wiring • Different mounting studs available • Available with fl ying leads, terminal block or MIL style connector • Most stable detection circuit • Temperature shock protected • Widest frequency range • High & low pass fi lters options • Built-in base & housing strain protection• Dynamic signal optionNotes:1. IPT ®(Independent Polarity Terminal) is a registered trademark of Metrix Instrument Co.Applications• Blowers • Centrifuges • Compressors • Engines • Fans• Generators • Motors • Pumps • Turbines• TurbochargersFeaturesModel ST5484E is the ideal solution for sensing vibration on most plant equipment. This precision case mounted vibration sensor and signal conditioner in a single package is built to provide years of reliable service. A simple two-wire loop signal proportional to velocity is generated for transfer to a programmable logic controller (PLC), distributed control system (DCS) or other 4-20 mA input devices. Simply mount the transmitter on the machine case, connect the 2-wire loop and read and/or record the vibration. Model ST5484E is made with our patented IPT ®1 technology which eliminates wiring polarity errors.Speci fi cations130[5.1]97[3.8]64[2.5]89[3.5]51[2.0]OPTIONAL CONDUIT ELBOW & REDUCER, MODEL 8200-001 or -0021” NPT (11 1/2 THRDS/IN.)33 [1.3] FLATS38[1.5]REFER TO “HOW TO SELECT B”SENSITIVE AXISTWO-WIRE CURRENT LOOP CONNECTIONS1” NPT with 3/4” NPT REDUCERWeight & DimensionsWeight: 0.7 kg (1.5 lbs.)ATEXLoop-powered TransmitterVibration - Condition Monitoringand Protection2.15Vibration TransmittersST5484E Velocity 4-20 mAST5484E-XXX-X21-XX With 4-24” fl ying leads.ST5484E-XXX-X20-XX With 2-24” fl ying leads. How To SelectST5484E - - -A CB DEFC ConnectionD High Pass FilterELow Pass FilterFAdditional Accessories - Page 2.32ST5484E-XXX-X33-XX Dynamic signal terminals provide buffered 100 mV/g connection for analysis.ST5484E-XXX -X32-XX With two slot terminal block.ST5484E-XXX-X14-XX With 2-pin MIL style connector. Optional Stud Adapters。
ioThinx 4500 (45M) 模块系列用户手册说明书
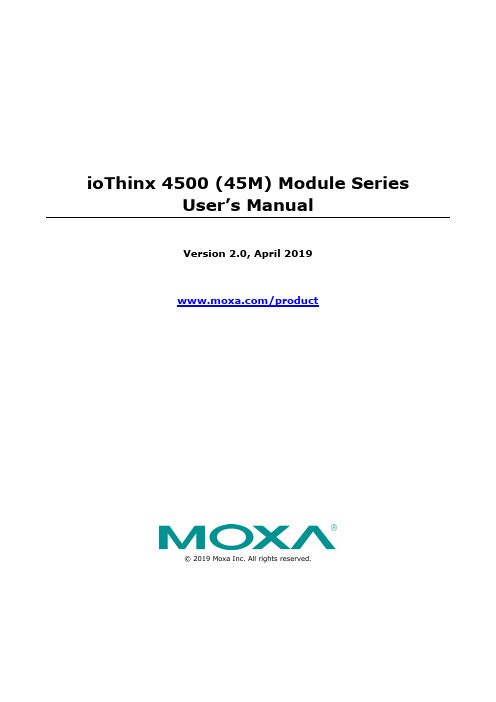
ioThinx 4500 (45M) Module SeriesUser’s ManualVersion 2.0, April 2019/product© 2019 Moxa Inc. All rights reserved.ioThinx 4500 (45M) Module SeriesUser’s ManualThe software described in this manual is furnished under a license agreement and may be used only in accordance withthe terms of that agreement.Copyright Notice© 2019 Moxa Inc. All rights reserved.TrademarksThe MOXA logo is a registered trademark of Moxa Inc.All other trademarks or registered marks in this manual belong to their respective manufacturers.DisclaimerInformation in this document is subject to change without notice and does not represent a commitment on the part of Moxa.Moxa provides this document as is, without warranty of any kind, either expressed or implied, including, but not limited to, its particular purpose. Moxa reserves the right to make improvements and/or changes to this manual, or to the products and/or the programs described in this manual, at any time.Information provided in this manual is intended to be accurate and reliable. However, Moxa assumes no responsibility for its use, or for any infringements on the rights of third parties that may result from its use.This product might include unintentional technical or typographical errors. Changes are periodically made to the information herein to correct such errors, and these changes are incorporated into new editions of the publication.Technical Support Contact Information/supportMoxa AmericasToll-free: 1-888-669-2872 Tel: +1-714-528-6777 Fax: +1-714-528-6778Moxa China (Shanghai office) Toll-free: 800-820-5036Tel: +86-21-5258-9955 Fax: +86-21-5258-5505Moxa EuropeTel: +49-89-3 70 03 99-0 Fax: +49-89-3 70 03 99-99Moxa Asia-PacificTel: +886-2-8919-1230 Fax: +886-2-8919-1231Moxa IndiaTel: +91-80-4172-9088 Fax: +91-80-4132-1045Safety SymbolsNOTE Indicates a potential malfunction which, if not avoided, however, will not result in damage to property. INFORMATION This information is important for preventing errors.Table of Contents1.Preface .............................................................................................................................................. 1-1Revision History ................................................................................................................................. 1-2 Relevant Models ................................................................................................................................. 1-2 Package Checklist ............................................................................................................................... 1-2 How to Use This Device ....................................................................................................................... 1-2 Safety Precautions .............................................................................................................................. 1-3 Additional Resources ........................................................................................................................... 1-4 2.Product Overview .............................................................................................................................. 2-1Technical Data.................................................................................................................................... 2-2 Common Specifications ................................................................................................................ 2-245MR-1600 Specifications ............................................................................................................ 2-245MR-1601 Specifications ............................................................................................................ 2-245MR-2404 Specifications ............................................................................................................ 2-345MR-2600 Specifications ............................................................................................................ 2-345MR-2601 Specifications ............................................................................................................ 2-345MR-2606 Specifications ............................................................................................................ 2-345MR-3800 Specifications ............................................................................................................ 2-445MR-3810 Specifications ............................................................................................................ 2-445MR-6600 Specifications ............................................................................................................ 2-545MR-6810 Specifications ............................................................................................................ 2-545MR-7210 Specifications ............................................................................................................ 2-545MR-7820 Specifications ............................................................................................................ 2-5 Appearance ........................................................................................................................................ 2-6 Front View (except the 45MR-7210) .............................................................................................. 2-6Front View (45MR-7210) .............................................................................................................. 2-6Dimensions................................................................................................................................. 2-7 LED Indicators .................................................................................................................................... 2-8 All Modules Except the 45MR-7210 ................................................................................................ 2-845MR-7210................................................................................................................................. 2-9 3.Hardware Installation ....................................................................................................................... 3-1Wiring I/O ......................................................................................................................................... 3-2 I/O Terminal Blocks ..................................................................................................................... 3-2Power Terminal Blocks ................................................................................................................. 3-245MR-1600 (-T) Wiring Guide ....................................................................................................... 3-345MR-1601 (-T) Wiring Guide ....................................................................................................... 3-445MR-2404 (-T) Wiring Guide ....................................................................................................... 3-545MR-2600 (-T) Wiring Guide ....................................................................................................... 3-645MR-2601 (-T) Wiring Guide ....................................................................................................... 3-745MR-2606 (-T) Wiring Guide ....................................................................................................... 3-845MR-3800 (-T) Wiring Guide ....................................................................................................... 3-945MR-3810 (-T) Wiring Guide ..................................................................................................... 3-1045MR-6600 (-T) Wiring Guide ..................................................................................................... 3-1145MR-6810 (-T) Wiring Guide ..................................................................................................... 3-1245MR-7210(-T) Wiring Guide ...................................................................................................... 3-1345MR-7820 (-T) Wiring Guide ..................................................................................................... 3-14 Mounting the Module ......................................................................................................................... 3-15 Installing the I/O Module on the DIN Rail ..................................................................................... 3-15Unmounting the I/O Module from the DIN Rail .............................................................................. 3-161PrefaceIn this document, we explain the scope of and how to use this document.The following topics are covered in this chapter:❒Revision History❒Relevant Models❒Package Checklist❒How to Use This Device❒Safety Precautions❒Additional ResourcesRevision HistoryVersion Change Datev1.0 First release. 2018-11-09v2.0 Added module 45MR-7210. 2019-03-31Relevant ModelsThis document applies to the following 45M modules:Model Name Features Operating Temp.45MR-1600 16 DIs, 24 VDC, PNP -20 to 60°C45MR-1600-T 16 DIs, 24 VDC, PNP -40 to 75°C45MR-1601 16 DIs, 24 VDC, NPN -20 to 60°C45MR-1601-T 16 DIs, 24 VDC, NPN -40 to 75°C45MR-2404 4 relays, form A -20 to 60°C45MR-2404-T 4 relays, form A -40 to 75°C45MR-2600 16 DOs, 24 VDC, sink -20 to 60°C45MR-2600-T 16 DOs, 24 VDC, sink -40 to 75°C45MR-2601 16 DOs, 24 VDC, source -20 to 60°C45MR-2601-T 16 DOs, 24 VDC, source -40 to 75°C45MR-2606 8 DIs, 24 VDC, PNP; 8 DOs, 24 VDC, source -20 to 60°C45MR-2606-T 8 DIs, 24 VDC, PNP; 8 DOs, 24 VDC, source -40 to 75°C45MR-3800 8 AIs, 0 to 20 mA or 4 to 20 mA -20 to 60°C45MR-3800-T 8 AIs, 0 to 20 mA or 4 to 20 mA -40 to 75°C45MR-3810 8 AIs, -10 to 10 V or 0 to 10 V -20 to 60°C45MR-3810-T 8 AIs, -10 to 10 V or 0 to 10 V -40 to 75°C45MR-6600 6 RTDs -20 to 60°C45MR-6600-T 6 RTDs -40 to 75°C45MR-6810 8 TCs -20 to 60°C45MR-6810-T 8 TCs -40 to 75°C45M4-7210 System and field power supply -20 to 60°C45M4-7210-T System and field power supply -40 to 75°C45MR-7820 Potential distribution module -20 to 60°C45MR-7820-T Potential distribution module -40 to 75°CPackage ChecklistThe following items are in the product package.• 1 x 45M module• 1 x quick installation guide (printed)• 1 x warranty cardHow to Use This Device45M modules cannot be used as standalone devices. The modules must be used with an ioThinx 45xx Series adapter. Refer to the ioThinx 45xx Series User’s Manual for details.Safety PrecautionsObserve the following safety precautions when installing or using the devices discussed in this document:Additional ResourcesRefer to following documents for additional information.•Datasheets for the following products:ioThinx 4510 SeriesioThinx 4500 Series (45MR) Modules•User’s Manual for the following product:ioThinx 4510 Series2Product OverviewIn this chapter, we give an overview of each of the 45M modules.The following topics are covered in this chapter:❒Technical DataCommon Specifications45MR-1600 Specifications45MR-1601 Specifications45MR-2404 Specifications45MR-2600 Specifications45MR-2601 Specifications45MR-2606 Specifications45MR-3800 Specifications45MR-3810 Specifications45MR-6600 Specifications45MR-6810 Specifications45MR-7210 Specifications45MR-7820 Specifications❒AppearanceFront View (except the 45MR-7210)Front View (45MR-7210)Dimensions❒LED IndicatorsAll Modules Except the 45MR-721045MR-7210ioThinx 4500 (45M) Module Series Product Overview Technical DataCommon SpecificationsPhysical CharacteristicsConnector: Removable Terminal blockWiring: 18 to 24 AWG (except the 45MR-7210)Dimensions: 19.5 x 99.0 x 60.5 mm (0.77 x 3.90 x 2.38 in)Installation: DIN-rail mountingEnvironmental LimitsOperating Temperature:Standard Models: -20 to 60°C (-4 to 140°F)Wide Temp. Models: -40 to 75°C (-40 to 167°F)45MR-1600 SpecificationsInput/Output InterfaceDigital Input Channels: 16Isolation: 3k VDC or 2k VrmsDigital InputsSensor Type:Dry ContactWet Contact (PNP)Dry Contact:On: short to FP+Off: openWet Contact (DI to FP-):On: 10 to 30 VDCOff: 0 to 3 VDCI/O Mode: DI or event counterNote: Only the first 4 channels support event counter mode.45MR-1601 SpecificationsInput/Output InterfaceDigital Input Channels: 16Isolation: 3k VDC or 2k VrmsDigital InputsSensor Type:Dry ContactWet Contact (NPN)Dry Contact:On: short to FP-Off: openWet Contact (DI to FP+):On: 10 to 30 VDCOff: 0 to 3 VDCI/O Mode: DI or event counterNote: Only the first 4 channels support event counter mode.45MR-2404 SpecificationsInput/Output InterfaceRelay Channels: 4Isolation: 3k VDC or 2k VrmsRelaysType: Form A (N.O.) power relayContact Current Rating: Resistive load: 2 A @ 30 VDC, 250 VACContact Resistance: 100 milli-ohms (max.)Initial Insulation Resistance: 1000 mega-ohms (min.) @ 500 VDCI/O Mode: Relay45MR-2600 SpecificationsInput/Output InterfaceDigital Output Channels: 16Isolation: 3k VDC or 2k VrmsDigital OutputsI/O Type: SinkVoltage: 12/24 VDCCurrent Rating: 500 mA per channelOver-Voltage Protection: 45 VDCShort-Circuit Protection: SupportedOver-Temperature Shutdown: 175°C (typical), 150°C (min.)I/O Mode: DO or pulse outputNote: Only the first 4 channels support pulse output mode.45MR-2601 SpecificationsInput/Output InterfaceDigital Output Channels: 16Isolation: 3k VDC or 2k VrmsDigital OutputsI/O Type: SourceVoltage: 12/24 VDCCurrent Rating: 500 mA per channelOver-Voltage Protection: 45 VDCShort-Circuit Protection: SupportedOver-Temperature Shutdown: 175°C (typical), 150°C (min.)I/O Mode: DO or pulse outputNote: Only the first 4 channels support event counter mode.45MR-2606 SpecificationsInput/Output InterfaceDigital Input Channels: 8Digital Output Channels: 8Isolation: 3k VDC or 2k VrmsDigital InputsSensor Type:Dry ContactWet Contact (PNP)Dry Contact:On: short to FP+Off: openWet Contact (DI to FP-):On: 10 to 30 VDCOff: 0 to 3 VDCI/O Mode: DI or event counterNote: Only the first 2 channels support event counter mode.Digital OutputsI/O Type: SourceVoltage: 12/24 VDCCurrent Rating: 500 mA per channelOver-Voltage Protection: 45 VDCShort-Circuit Protection: SupportedOver-Temperature Shutdown: 175°C (typical), 150°C (min.)I/O Mode: DO or pulse outputNote: Only the first 2 channels support event counter mode. 45MR-3800 SpecificationsInput/Output InterfaceAnalog Input Channels: 8Isolation: 3k VDC or 2k VrmsAnalog InputsI/O Type: DifferentialInput Impedance: 120 ohmsI/O Mode: CurrentInput Range:0 to 20 mA4 to 20 mA4 to 20 mA (with burn-out detection)Resolution: 16 bits45MR-3810 SpecificationsInput/Output InterfaceAnalog Input Channels: 8Isolation: 3k VDC or 2k VrmsDigital OutputsI/O Type: DifferentialInput Impedance: 10 mega-ohms (min.)Protection:Fault and over-voltage protection:-35 to +35 VDC (power off)-25 to +30 VDC (power on)I/O Mode: VoltageInput Range:±10 VDC0 to 10 VDCResolution: 16 bits45MR-6600 SpecificationsInput/Output InterfaceRTD Channels: 6Isolation: 3k VDC or 2k VrmsDigital OutputsInput Type:PT50, PT100, PT200, PT500 (-200 to 850°C)PT1000 (-200 to 350°C)JPT100, JPT200, JPT500 (-200 to 640°C)JPT1000 (-200 to 350°C)NI100, NI200, NI500 (-60 to 250°C)NI1000 (-60 to 150°C)NI120 (-80 to 260°C)Resistance of 310, 620, 1250, and 2200 ohmsInput Impedance: 625 kilo-ohms (min.)Resolution: 0.1°C or 0.1 ohm45MR-6810 SpecificationsInput/Output InterfaceThermocouple Channels: 8Isolation: 3k VDC or 2k VrmsDigital OutputsSensor Type: J, K, T, E, R, S, B, NMillivolt Type:±19.532 mV±39.062 mV±78.126 mVInput Impedance: 1 mega-ohms (min.)Resolution: 16 bits45MR-7210 SpecificationsInput/Output InterfaceSystem Power Input: 1Field Power Input: 1Isolation: 3k VDC or 2k VrmsWiring: 12 to 26 AWGNote:System Power: 12 to 48 VField Power: 12/24 VDC45MR-7820 SpecificationsInput/Output InterfaceVoltage Output Channels: 16Isolation: 3k VDC or 2k VrmsNote:Field Power 12/24 VDC: 8 channelsField Power 0 VDC: 8 channelsAppearanceFront View (except the 45MR-7210)Front View (45MR-7210)DimensionsAll Modules Except the 45MR-7210 Unit: mm (in)45MR-7210Unit: mm (in)LED IndicatorsAll Modules Except the 45MR-7210LabelUsageNo. of LEDs LED Color DescriptionStatusStatus1GreenSteady on: Module ReadySlow blinking: Booting up, module mismatch, or installed incorrectly Fast blinking: Locating RedSteady on: Module errorSlow blinking: Firmware is upgrading Fast blink: Safe mode (output modules only)DI0, DI1, DI2… DI 1 of each Green Steady on: Channel onOff: Channel off or no counter/pulse signal DO0, DO1, DO2… DO 1 of each Green Steady on: Channel onOff: Channel off or no counter/pulse signal RLY0, RLY1, RLY2… Relay 1 of each Green Steady on: Channel onOff: Channel off or no counter/pulse signal AI0, AI1, AI2… AI 2 of each Green Steady on: Channel enabledRed Steady on: Burn out & wire off when current mode TCxTC2 of each Green Steady on: Channel enabledRed Steady on: Burn out & wire off when current mode RTD0, RTD2, RTD3… RTD2 of eachGreen Steady on: Channel enabledRedSteady on: Burn out & wire off when current mode45MR-7210Label Usage No. of LEDs LED Color DescriptionStatus Status 1 GreenSteady on: Module ReadySlow blinking: Booting up, module mismatch,or installed incorrectlyFast blinking: LocatingRedSteady on: Module errorSlow blinking: Firmware is upgradingSP System Power 1 Green On: power on Off: power offFP Field Power 1 Green On: power on Off: power off3Hardware InstallationIn this chapter, we describe how to install the 45M modules.The following topics are covered in this chapter:❒Wiring I/OI/O Terminal BlocksPower Terminal Blocks45MR-1600 (-T) Wiring Guide45MR-1601 (-T) Wiring Guide45MR-2404 (-T) Wiring Guide45MR-2600 (-T) Wiring Guide45MR-2601 (-T) Wiring Guide45MR-2606 (-T) Wiring Guide45MR-3800 (-T) Wiring Guide45MR-3810 (-T) Wiring Guide45MR-6600 (-T) Wiring Guide45MR-6810 (-T) Wiring Guide45MR-7210(-T) Wiring Guide45MR-7820 (-T) Wiring Guide❒Mounting the ModuleInstalling the I/O Module on the DIN RailUnmounting the I/O Module from the DIN RailWiring I/OI/O Terminal BlocksWire range: 18 to 24 AWGWire strip length: 9 to 10 mmUnit: mm (in.)Power Terminal BlocksWire range: 12 to 26 AWG (Ferrule diameter: 2.0 to 0.4 mm)Wire strip length: 10 mmUnit: mm (in.)45MR-1600 (-T) Wiring Guide Description: 16 DIs, 24 VDC, PNP or dry contactSingle Channel (Dry Contact):Single Channel (PNP):All Channels (PNP):Description: 16 DIs, 24 VDC, NPN or dry contact Single Channel (Dry Contact):Single Channel (NPN):All Channels (NPN):Description: 4 Relays, form ASingle Channel (Resistive Load):Single Channel (Inductive Load):All Channels:NOTE To avoid over current damage, fuse is recommended.Description: 16 DOs, 24 VDC, sinkSingle Channel:All Channels:NOTE We recommend using a fuse to avoid damage from current spikes.Description: 16 DOs, 24 VDC, sourceSingle Channel:All Channels:NOTE We recommend using a fuse to avoid damage from current spikes.Description: 8 DIs, 24 VDC, PNP or dry contact, 8 DOs, 24 VDC, sourceSingle Channel (DI dry contact/DI PNP/DO source):All Channels:NOTE We recommend using a fuse to avoid damage from current spikes.Description: 8 AIs, 0 to 20 mA or 4 to 20 mA Single Channel (2-wire/3-wire/4-wire):All Channels:Description: 8 AIs, -10 to 10 V or 0 to 10 V Single Channel (3-wire/4-wire):All Channels:Description: 6 RTDsSingle Channel (2-wire/3-wire/4-wire):All Channels:Description: 8 TCsSingle Channel (TC Sensor/Voltage Source):All Channels:45MR-7210(-T) Wiring Guide Description: system and field power inputAll channels:45MR-7820 (-T) Wiring Guide Description: Potential distribution moduleSingle Channel:All Channels:Mounting the ModuleTake the following steps to mount the device on or unmount the device from a DIN rail.Installing the I/O Module on the DIN RailStep 1: Align the I/O module side by side with the head/CPU module, making sure that the upper and lower rails are hooked together.Step 2: Align the I/O module side by side with the network module and then push the I/O module until ittouches the DIN-rail. Next, apply more force until the module clips to the DIN-rail.NOTE After the module is firmly attached to the DIN-rail, the module connections to the internal bus will beestablished.INFORMATION With the I/O module inserted in place, the internal bus will establish a connection through the adjacent module(s).Unmounting the I/O Module from the DIN RailStep 1: Use your finger to lift the release tab on the lower part of the module.Step 2: Push the top of the release tab to latch it, and then pull the module out.NOTE Electrical connections for the internal bus will be disconnected when the I/O module is removed.。
称量仪表说明书
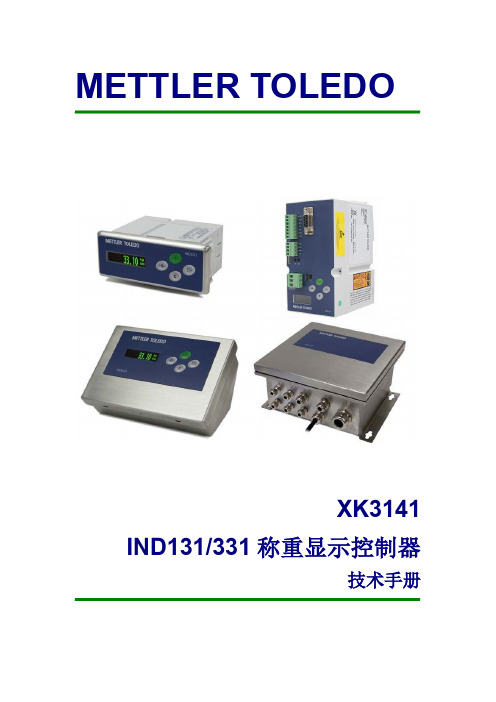
XK3141 IND131/331 称重显示控制器
技手册
目录
第 1 章 引言 .................................................................................................................................... 1 概述 .......................................................................................................................................... 1 性能指标........................................................................................................................... 1 型号 .......................................................................................................................................... 2 规格 .......................................................................................................................................... 2 危险场合的使用.....................................
远程测量仪 MT50 用户手册说明书
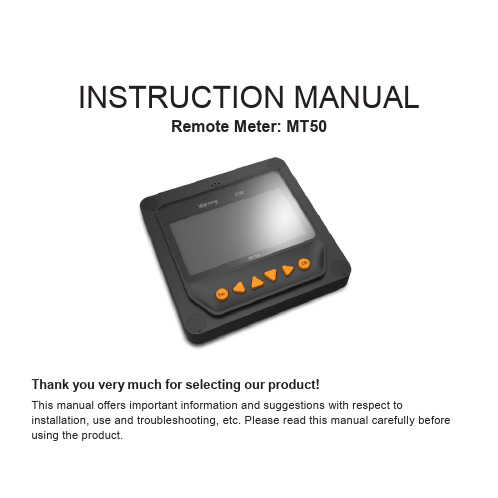
INSTRUCTION MANUALRemote Meter: MT50Thank you very much for selecting our product!This manual offers important information and suggestions with respect to installation, use and troubleshooting, etc. Please read this manual carefully before using the product.Remote MeterMT501 Important Safety Instructions (1)2 General Information (2)2.1 Features (2)2.2Main functions (3)2.3Recommendations (3)3 Installation (4)4 Product Features (8)5 Operation (12)5.1 Buttons (12)5.2 Main menu (13)5.3Real-time monitoring (14)5.4 Device information (16)5.5Test operation (16)5.6Control parameter (17)5.7Load setting (21)5.8Device parameter (24)5.9Device password (25)5.10Factory reset (25)5.11Failure information (26)5.12Meter parameter (27)6 T echnical Specifications (28)1 Important Safety InstructionsSAVE THESE INSTRUCTIONS:This manual contains important safety, installation and operating instructions for the Remote Meter.General safety information■Please inspect the MT50 thoroughly after it is delivered. If any damage is seen, please notify the shipping company or our company immediately. A photo of the damage may be helpful.■Read all instructions and cautions in the manual before starting the installation.■Keep the MT50 away from rain, exposure, severe dust, vibrations, corrosive gas and intense electromagnetic interference.■Do not allow water to enter remote meter.■There are no user serviceable parts inside the controller. Do not disassemble or attempt to repair it.2 General Information2.1 FeaturesThe new-generation remote display unit MT50 for the controllers is an associated display device which supports both the latest communication protocol and the voltage technology standard of solar controllers. The products have many excellent functions:■Automatic identify and display the type, model and relevant parameter data of controllers;■Real-time display the operational data and working status of the connection devices in digital, graphic and textual forms by a large-screen multifunction LCD;■Direct, convenient and rapid operation of six navigation function keys;■Both data and power flowing on the same lead, no need for external power;■Real-time data monitoring and remote load switchover of the controllers, and data browse and modification of device parameters, charge control parameters and load control parameters;■Real-time display of failure information of the connection devices;■Longer communication distance based on RS485.2.2 Main functionsFunctions like the real-time monitoring of the operational data and working status of a controller, the browse and modification of charge/discharge control parameters, the setting of device parameters and load control parameters and the restoration of factory defaults, based on LCD display and functional key operation.2.3 Recommendations■Please do not install MT50 in a situation with strong electromagnetic interference.3 InstallationFrame Mount Dimensions(mm)Wall installation steps:Step1: Locate and drill screw holesbased on the Frame Mounting dimensionof the base, and erect the plasticexpansion bolts;Step 2: Use four ST4.2×32 self-tappingscrews to fix the Frame;Frame MountingStep 3: Use four M4×8 pan head screws to mount MT50 Surface on the Frame;Step 4: Mount the four associated screw plugs into the screw holes.Surface MountingSteps of surface mounting:Step 1: Locate and drill screw holes based on the installation size of the Surface;Step 2: Use four M4×8 cross recessed pan head screws with M4 nuts to mount MT50 Surface onto the panel;Step 3: Mount the four associated white screw plugs into the screw holes.Surface mountingNote: Take full consideration of the plugging/unplugging space of the communication cable and the length of the cable during installation to see if they are appropriate.4 Product FeaturesRS485 communication and power interfaceRear ViewFailure indicatorFailure indicator flashes in case of failure of the connection devices. For failure information please check the Controller Manual.Communication indicatorIndicate communication status when MT50 is connected with the controller. Display screenMan-machine interaction operation interface.ButtonsThe Meter buttons includes four navigation buttons and two operational buttons. See the specific directions in the Operational Manual.RJ45 communication and power interfacesCommunication and power supply cable interfaces, used for communication connection with controllers.Note: Please use the communication plug which is marked with “MT”to connect MT50Monitoring screenDay and night icons-Night,- Day: The threshold voltage is 1V. Higher than 1V is daytime. Charge current iconThe icon is dynamically if there is charge current.Battery iconThe battery capacity is dynamically displayedNote: When the battery is in over discharge status, the icon displayed is“ ”.Battery status icons-Normal voltage, -Under voltage, -Over discharge.Load current iconThe icon is dynamically if there is discharge current.Load status icon- Load On, - Load Off.Note: In Manual Mode, pressing the "OK" button will switch the load status between "ON" and "OFF"5 Operation5.1 ButtonsThe buttons are respectively (from left to right) “ESC”,“Left”,“Up”,“Down”,“Right”and “O K “buttons, the operation is described in the schematic operation diagram below:Schematic operation diagramThe default entry page is the browse mode. Pressing button and inputting the correct password to enter the modification mode; and buttons could be used to move the cursor, and buttons could be used to modify the parameter values when the cursor is located at the current place;and buttons could be finally used to respectively confirm and cancel the modification of the control parameters.5.2 Main menuEnter the Main Menu by pressing "Esc".“Up”and “Down”buttons are respectively used to move the cursor to select the menu items, “OK”and “ESC”buttons are respectively used to enter or exit the corresponding pages of the menu items.5.3 Real-time monitoringThere are 14 pages under real-time monitoring. Please check it as below:17.5V 13.8V 13.8VOperational tips:Move between rows by pressing "Up" or "Down" buttons. Move along a row by pressing "Right" or "Left" buttons .5.4 Device informationThe product model, parameters and SN code of the controllers are displayed below:Operational tips: and buttons are respectively used to turn the browse page upward and downward.5.5 Test operationLoad switch test operation is conducted on the connection solar controller to see if the load output is normal. The test operation does not affect the working settings under actual load, which means that the solar controller will exit from the test mode when exiting the operational interface of the test.Operational tips: Enter the page and input correct password; use andbuttons to modify the On/Off status values, while use andbuttonsrespectively to confirm and cancel the test operation.5.6 Control parameterBrowse and modification operations are conducted over the control parameters of solar charge controller. See the scope of parameter modification in control parameters table, and the page of control parametersBattery voltage parameters(Parameters is in 12V system at 25℃ , please use X 2 in 24V, X 3 in 36 V, and X 4 in 48 V system)Notes:1. When the battery type is sealed, gel, flooded, the adjusting range of equalize duration is 0 to180min and boost duration is 10 to180min.2. The following rules must be observed when modify the parameters value in user battery type (factory default value is the same as sealed type):a) Over Voltage Disconnect Voltage > Charging Limit Voltage ≥ Equalize Charging Voltage ≥ Boost Charging Voltage ≥ Float Charging Voltage > Boost Voltage Reconnect.b) Over Voltage Disconnect Voltage > Over Voltage Reconnect Voltagec) Low Voltage Reconnect Voltage > Low Voltage Disconnect Voltage ≥ Discharging Limit Voltage.d) Under Voltage Warning Recover Voltage > Under Voltage Warning Voltage ≥ Discharging Limit Voltage.e) Boost Voltage Reconnect > Low Voltage Reconnect Voltage.NOTE: Please refer to user guide or contact with the sales for thedetail of setting operation.5.7 Load settingThe page of load setting could be used to set the four load working modes of the connection solar controller (Manual, Light on/off, Light on+timer, Time control)④Time control5.8 Device parameterThe software version information of solar charge controller could be checked via the page of device parameters, and device data like device ID, device LCD backlight time and device clock could be checked and modified. The page of device parameter in the diagram below:Note: the bigger the ID value of the connection device, the longer the Meter5.9 Device passwordThe password of the solar charge controller could be modified via the page of device password; the device password is a 6-digit figure which is required before entering the modification mode of “Control parameter”,“Load setting”, “Device parameter”,“Device password”,“Factory reset” pages. The page of device password in the diagram below:Note: Solar charge controller default password is”000000”5.10 Factory resetThe default parameter values of solar charge controller could be restored via the Factory reset page, which means the “Control parameter”,“Load setting”, “Charge mode” and “Device password” of the devices could be restored to the factory defaults (the factory default password of the devices is “000000”).5.11 Failure informationThe current failure information of the solar charge controller could be checked via the Failure information page (a maximum of 15 failure messages could be displayed); when the failures of solar charge controller are eliminated, the corresponding failure information will also be automatically eliminated.5.12 Meter parameterThe meter model, software and hardware version, and SN NO. could be checked via Meter parameter page. And the three parameters (Switch pages, Backlight) could be browsed and modified as well.Note: When the set up is accomplished, the auto switch page cannot6 Technical Specifications Electrical ParameterEnvironmental ParameterDefinitions of interface pinsData cable pin definitionsREMOTE METER DIMENSIONS (mm)Any changes without prior notice! Version number:V2.3。
Metrix 5485C高温速度传感器说明书

5485C HIGH-TEMPERATURE VELOCITY TRANSDUCER InstallaƟon ManualDOC # M8109 • REV K (Feb 2015)11802-PIN CONNECTOR VERSION(requires maƟ ng Model 4850-XXXX cable)FIXED ARMORED CABLE VERSIONOVERVIEWThe Metrix 5485C High-Temperature Veloc-ity Sensor is suitable for use in temperaturesup to 375ԨC. It is designed for gas turbines and other machinery with high surface tem-peratures where a velocity signal is desired.The sensor’s moving-coil design requires no external power as it self-generates a signal proporƟ onal to vibraƟ on velocity.FEATURES• Self generaƟ ng, no power required• Stainless Steel Housing • Zero fricƟ on - infi nite analog resoluƟ onAPPLICATIONS• Large industrial gas turbines • Furnace fan monitoringHAZARDOUS AREASUL intrinsically safe for Class 1, Div. 1, Grps (A-D); Non-incendive for Class 1, Div. 2, Grps. (A-D). CSA intrinsically safe for: Class 1, Div. 1, Grps (A-D); ATEX/IECEx intrinsically safe for: EEx ia IIC T1-T6 Ga.Doc# M8109 • REV K (Feb 2015) Page 2 of 8INSTALLATIONThe sensiƟ ve axis of the transducer can be oriented in any direcƟ on. To ensure clean response to high frequency vibraƟ ons, the transducer must be securely mounted to a fl at machined surface using four #6 (or 3mm) socket head screws. If a bracket is required, it should be of rigid construcƟ on to prevent spurious mechanical resonances in the pass band.WIRINGIn ordinary, nonhazardous locaƟ ons the transducer should be wired according to Page 4 (drawing 7623, Sheet 2).In hazardous locaƟ ons the wiring method depends upon the area classifi caƟ on.1.In Class I, Div 1, Groups A, B, C & D or IEC Zone 0, Group IIC hazardous locaƟ ons, thetransducer may be connected through a zener diode safety barrier to the safe area receiver in accordance with Page 5 (drawing 7623, Sheet 3).2.In Class I, Div 2, Groups A, B, C & D locaƟ ons the transducer may be wired as in (1), or it can be wired without a safety barrier if wired in accordance with Page 6 (drawing 8096).ATEX/IECEx INPUT ENTITY PARAMETERS• U i = 28v • I i = 120mA • P i = 625 mW • C i = 0•L i = 0.88mH max.SPECIFIC CONDITIONS OF USEIn order to ensure temperature classifi caƟ on and safety, the power supply must adhere to the following: • U o ≤ 28V • I o ≤ 120mA • P o ≤ 0.625WThe temperature classifi caƟons and ambient temperature range can vary as follows:Doc# M8109 • REV K (Feb 2015) Page 3 of 8Doc# M8109 • REV K (Feb 2015) Page 4 of 8Doc# M8109 • REV K (Feb 2015) Page 5 of 8Doc# M8109 • REV K (Feb 2015) Page 6 of 8Doc# M8109 • REV K (Feb 2015) Page 7 of 8SENSOR VERIFICATION CALIBRATION PROCEDUREMount the 5485C on a shaker table and verify the RMS output per table below.The test should be performed on a NIST traceable shaker at 1 ips, 150Hz.Metrix recommends that this procedure be performed every 3 years.NOTE: Due to the diffi culƟ es offi eld sensor verifi caƟ on, the +/- 5% sensiƟ vity specifi caƟ on is relaxed to +/- 10%. The sensor should be returned to Metrix, Houston, Texas for metrology verifi caƟ on of factory calibraƟ on.Doc# M8109 • REV K (Feb 2015) Page 8 of 8info@metrixvibraƟ www.metrixvibraƟ 8824 Fallbrook Dr. Houston, TX 77064, USA Tel: 1.281.940.1802 • Fax: 1.713.559.9421This electronic equipment was manufactured according to high quality stan-dards to ensure safe and reliable operaƟ on when used as intended. Due to its nature, this equipment may contain small quanƟ Ɵ es of substances known to be hazardous to the environment or to human health if released into the environ-ment. For this reason, Waste Electrical and Electronic Equipment (commonly known as WEEE) should never be disposed of in the public waste stream. The“Crossed-Out W aste Bin” label affi xed to this product is a reminder to dispose of this product in accordance with local WEEE regulaƟ ons. If you have quesƟ ons about the disposal pro-cess, please contact Metrix Customer Service.ENVIRONMENTAL INFORMATION。
波特克梅特曼15XP数字多功能仪说明书

Meterman DatasheetMODEL: 15XP DIGITAL MULTIMETER8-1/2" X 11" 2-3 pages (extended version for web)LOGO: Wavetek MetermanHEAD: The 15XP Digital MultimeterSUB: A compact meter for electronics and test applicationsPHOTO: (15XP)INSET PHOTO: (15XP with Voltect)LOGO: Voltect™ Non-Contact Voltage DetectorINSET PHOTO: (15XP with Magne-Grip holster)CAPTION: Magne-Grip holster frees hands for work.The Wavetek Meterman 15 XP digital multimeter provides superior features and accuracy in a smaller form factor. The 15 XP has unique features such as VolTect™ non-contact voltage(NCV) detection, logic test and our exclusive Magne-Grip™ holster that frees both hands for work. The 15XP is the right choice for electronics engineers and technicians.SUB:Features that help you take measurements, faster and easier.• 2000 count resolution provides more precise measurements• Autoranging display for faster measurements• VolTect™ Non-contact voltage detection lets you instantly detect dangerous AC voltage• Magne-Grip holster with magnetic hanging strap that frees both hands for work.• TTL logic test for digital circuits• Integrated tilt stand for easy bench use.• Resistance and continuity for troubleshooting bad connections• Diode test for component level troubleshooting• Data Hold freezes display to "hold" reading while you focus on your test leads• 750 V AC/ 1000 V DC - highest voltage rating in this class of meter• Triple safety rating protects against line surges and overvoltage conditions• CAT I 1000 V• CAT II 600 V• CAT III 300 VSUB: Product includes:• Model 15XP compact digital multimeter• Test leads• Magne-Grip holster with magnetic hanging strap• Manual• Battery (installed)SPECIFICATIONS• Display: 3½-digit liquid crystal display (LCD) with a maximum reading of 1999.• Polarity: Automatic, positive implied, negative polarity indication.• Overrange: (OL) or (-OL) is displayed.• Zero: Automatic.• Low battery indication: The "Ν" is displayed when the battery voltage drops below the operating level.• Auto power off: Approx. 10 minutes.• Measurement rate: 2 times per second, nominal.• Operating environment: 0°C to 50°C at <70% R.H.• Storage temperature: -20°C to 60°C, 0 to 80% R.H. with battery removed from meter.• Accuracy: Stated accuracy at 23°C ± 5°C, <75% relative humidity.• Temperature Coefficient: 0.1 × (specified accuracy) per °C. (0°C to 18°C, 28°C to 50°C).• Altitude: 6561.7 Feet (2000M).• Power: Single standard 9-volt battery, NEDA 1604, JIS 006P, IEC 6F22.• Battery life: 200 hours typical with carbon-zinc.• Dimensions: 155mm (H) ×72mm (W) ×32mm (D).• Weight: Approx. 210g including battery.• Accessories: One pair test leads TL245, Fuse 2A/1000V, 9V battery (installed) and Operating Instructions holster, magnet strap.• Safety: Designed to meet IEC 1010-1, Rev-2 CAT I 1000V, CAT II 600V, CAT III 300V, class 2 and pollution deg.2 indoor use comply with CE, CSA 22.2-1010-1.DC VOLTSRanges: 200mV, 2V, 20V, 200V, 1000VResolution: 100µVAccuracy: ± (0.5% rdg + 1 dgt)Input impedance: 400mV: >100MΩ; 4V: 10MΩ; 40V ~ 1000V: 9.1MΩOverload protection: 1000VDC or 750VAC rmsAC VOLTS (45Hz - 500Hz)Ranges:200mV, 2V, 20V, 200V, 750VResolution: 100µVAccuracy:± (1.5% rdg + 5dgts) 45Hz ~ 100Hz on 200mV range± (1.5% rdg + 5dgts) on 2V to 750V rangesInput impedance: 400mV: >100MΩ; 4V: 10MΩ; 40V ~ 1000V: 9.1MΩOverload protection: 1000 VDC or 750VAC rmsDC CURRENTRanges: 200µA, 2000µA, 20mA, 200mA, 2AResolution:0.1µAAccuracy:± (1.0% rdg + 2dgt) on 200µA to 200mA ranges± (2.0% rdg + 3 dgts) on 2A rangeInput protection:2A/1000V fast blow ceramic fuse 6.3×32mm on A inputBurden voltage: 500mV max. (2V max. on 2mA, 200mA ranges)AC CURRENT (45Hz - 500Hz)Ranges: 200µA, 2000µA,20mA, 200mA, 2AResolution: 0.1µAAccuracy:± (1.5% rdg + 5 dgts) on 200µA to 200mA ranges± (2.5% rdg + 5dgts) on 2A rangeInput protection: 2A/1000V fast blow ceramic fuse 6.3×32mm on A inputBurden voltage: 500mV max. (2V max. on 2mA, 200mA ranges)RESISTANCERanges: 200Ω, 2kΩ, 20kΩ, 200kΩ, 2MΩ, 20MΩResolution: 100mΩAccuracy:± (1.0% rdg + 4 dgts) on 200Ω to 2MΩ ranges± (3.0% rdg + 5 dgts) on 20MΩ rangeOpen circuit volts: -0.45V dc typical, (-1.2Vdc on 200Ω range)Overload protection: 1000VDC or 750VAC rmsCONTINUITYAudible indication: Less than 25ΩResponse time: 100msOverload protection:1000VDC or 750VAC rmsDIODE TESTTest current: 1.2mA (approximate)Accuracy: ±(1.5% rdg + 3 dgts)Resolution: 1mVOpen circuit volts: 3.0 dc typicalOverload protection: 1000VDC or 750VAC rmsLOGIC TESTLogic test: TTLThresholds Logic 1 ( Hi ): 2.8V ± 0.8VThresholds Logic 0 ( Lo): 0.8V ± 0.5VTest voltage:TTL 5VDCFrequency range: 20MHzPulse width: 25ns minDuty cycle limits: > 30% and < 70%Indication: 40ms beep at Logic 0 ( Lo)Overload protection:1000VDC or 750VAC rmsNON-CONTACT VOLTAGE INDICATORSense voltage 70V to 600VAC (50Hz ~ 60Hz) beeper chirps and big bright red LED comes on, works on all ranges. AUXILIARY FEATURESDATA HOLD: Freeze the latest reading on the display.RANGE: Execute manual range mode.AUTO Power off: After auto power off, press (RANGE), (HOLD) button to restart the meter, and the last reading of measurement will be maintained in the display.A JACK: Input warning detects wrong connection.。
密特电池检测仪说明书

菜单选项 .................................................................................................................... 5 菜单.................................................................. 5 主菜单................................................................ 5 电池组名称............................................................ 6 设置参数菜单.......................................................... 6 测试电池选项.......................................................... 7 显示设置参数菜单...................................................... 7 打印测试结果选项...................................................... 7 显示测试结果菜单...................................................... 7 输出测试数据选项...................................................... 8 更改参考值选项........................................................ 8 实用菜单.............................................................. 9
METRIX ASYC IV 多功能电压计说明书

METRIX ®revolutionizes multimeters !ASYC IVThe 1st multimeters with graphical color screensX In the lab or in the field, the reference for multimeters X Graphical display of trends and multiple parameters X 200 kHz bandwidth X 0.02 % basic accuracy X Multiple analytical tools: time/date-stamped MIN/MAX/AVG and PEAK monitoring... Plus unrivalled simplicity of use, as always!WITH AEMC INSTRUMENTSMTX 3290- MTX 3291- MTX 3292B - MTX 3293BERGONOMICS AND STRENGTHSId eal for both portable and benchtop use, the ASYC IV multimeters are simple and intuitive to use. A ccessible directly, the different measurements are indicated explicitly by pictograms on the electronic switch. T he display can be used to view the measurement results either as numeric values or as graphs showing the trend over time. Recorded m easurements can be displayed as a trace,with the possibility of positioning cursors and zooming on part of the recorded curve.Help in French and English is integrated into the instrument and provides information about the measurements in B communication is provided for transferring data to a PC, for recording and for programming with the LV/LW drivers. The instrument’s firmware can be upgraded by connecting to a PC and then accessing the website.A magnetic suspension system is available as an option for simple installation and viewing while freeing your hands for other tasks.Magnetized soft case suitable for the Multifix system.Audible alert when the cables are connected to the wrong inputs and automatic recognition of the function.For direct access to the function menus.By means of a function key which then lights up to remind you for intuitive configuration.Multiple parameters and 3 levels of backlighting which varies automatically according to the ambient lighting for better visibility and more comfortable reading.For excellent handling.•The ASYC IV models can be powered by normal batteries, rechargeable batteries or the mains supply.•The battery-powered ASYC IV models offer a battery life of up to 400 hrs for easier use in the field.•To optimize the ASYC IV’s consumption, the standby mode can be activated and the internal accelerometer allows you to wake up the instrument simply by touching its keyboard.SELECTION OF THE MEASUREMENT FUNCTIONDISPLAY WITH LARGE DIGITS IP 67 MOULDED CASING SECURE TERMINAL STRIP F1 → F4 FUNCTION KEYSAPPLICATIONST h e ASYC IV multimeters are ideal for many applications in industry, telecommunications and defense. T heir multiple functions make them easy to use for electrical and electronics maintenance, as well as machine maintenance. I n electronics, the ASYC IV models can be used both for wiring tests on computer or medical equipment and for component testing.In industry, they can be used for the applications encountered in departments dealing with automatic control systems and processes in a wide variety of sectors: food, plastics, concrete, metal, paper, wood, oil, nuclear, etc.The ASYC IV models are also useful for the maintenance of many industrial machines: numerical control, motors, generators, etc. Their versatility makes them ideal for the needs of expert electrical installers and professionals in the transport and energy sectors. The high-performance, accessible and ergonomic ASYC IV multimeters also have a key role to play in education and research.For metrology…Measurements on electrical cabinets… or After-Sales ServiceMTX 3290- MTX 3291- MTX 3292B - MTX 3293BMEASUREMENTSMEASUREMENTSThe TRMS measurements of AC voltages and currents are also accurate on non-linear signals.CAPACITANCEResistance can be measured up to 100 MΩ.RESISTANCEVoltage measurement can beperformed in total safety up to 1000 V.AC, DC OR AC+DC VOLTAGE The ASYC IV models measure the frequency upto 600 kHz (MTX 3290 and MTX 3291) and up to 5 MHz with the 2 top-of-the-range models,the MTX 3292B and MTX 3293B .FREQUENCYDepending on the models,J/K thermocouples or Pt100 / Pt1000 sensorscan be used to measure temperature.TEMPERATUREAC, DC and AC+DC current measurement with direct readings up to 10 A.The mV/A or A/A ratio can beFUNCTIONS used to express measurementsMTX 3290 & MTX 3291MTX 3292B & MTX 3293BMTX 3293B906211429 - E d . 5 - 11/20 - N o HX0059B HX0052C HX0053B1391•Fax(603)742-2346•E-mail:**************1(603)742-2346•E-mail:***************© Chauvin Arnoux ®, Inc. d.b.a. AEMC ®Instruments Instruments Technical Assistance Hotline for immediate consultation with an applications engineer: (800) 343-1391。
Metrix Vibration ST5484E 振动传感器数据手册说明书

ST5484E Seismic Velocity 4-20 mA TransmitterDatasheet2-Pin MIL Connector(Option D=4)The ST5484E is a self-contained seismic velocity transmitter that incorporates a piezoelectric accelerometer, signal integrator, RMS peak detector, and a 4-20 mA signal conditioner into a single package. It can be mounted directly on a machine case or bearing housing without intervening signal conditioning equipment. The amplitude of the integrated acceleration (velocity) signal is con -verted to a proportional 4-20 mA signal compatible with industrial process control instrumentation such as PLCs, DCSs, and SCADA systems that can provide trending and/or alarming capabilities for a simplified vibration monitoring strategy.When the flying lead or terminal block connector options are chosen, the transmitter does not need a separate environmental housing and can directly accept conduit. To reduce installed cost, it can be used with barriers for intrinsically safe installations, or wired directly to explosion-proof conduit fittings for explosion- proof installations.Need A Local Display?When continuous, local indication of vibra -tion levels is required at the transmitter, the Metrix ST5491E provides these capabilities.Its sensing and transmitter elements are similar to the ST5484E, but it includes a convenient 2½ digit LCD display in an integral conduit elbow and is rated for use in temperatures from -10o C to +70o C. Refer to Metrix datasheet 1004598 for ordering information and de -tailed specifications.A vibration transmitter may be appropriate in applications where a stand-alone monitoring system may not be warranted.The ST5484E handles general-purpose vibration measurements on a wide range of rotating and reciprocating machinery with ro -tative speeds between 120- and 6,000-rpm. Seismic measure -ments are suitable for machines with rolling-element bearings because shaft vibration in such machines is usually transmitted directly through the bearing to the bearing housing without sub -stantial damping or attenuation. Seismic transducers can also measure vibration that does not originate at the shaft, such as bearing-related wear and defects, footing/foundation problems, piping resonances that are coupled to the machine, etc.Why Measure Velocity?Acceleration and displacement levels are heavily influenced by the frequencies at which the vibration is occurring, while velocity levels are much less influenced. Thus, although acceleration,velocity, and displacement measurements are inter-related math -ematically, seismic velocity measurements tend to be more con -sistent over a wide range of frequencies than either displacement or acceleration. Consequently, broadband (sometimes called “overall” or “unfiltered”) velocity measurements are appropriate for monitoring many machines as a reliable indicator of damag -ing vibratory energy, with the notable exception of machines with fluid-film bearings, which are usually better addressed by shaft-observing proximity probes.Casing displacement is not a practical measurement to make directly and is typically just an integrated seismic velocity mea -surement. As such, the primary decision when selecting a seis -mic sensor will usually be whether to measure casing velocity or casing acceleration. As noted above, casing velocity will often be more appropriate because it tends to be a more reliable indicator of damaging vibratory energy over a broad frequency spectrum for low- to medium-speed machinery.Flying Leads(Option D=0, 1, 5, or 6) (2-wire shown; 4-wire also available)2-Pin Terminal Block(Option D=2)4-Pin Terminal Block(Option D=3)1180OVERVIEWAPPLICATIONSNote: Units sold with an explosion proof rating will in -clude a conduit elbow:8200-000 IEC for ATEX/IECEx/INMETRO/KOSHA/EAC8200-000 for CSAExplosion Proof Versionswith Option D≠4ST5484E Seismic Velocity 4-20 mA TransmitterDatasheetNOTE: For machines with fluid-film bearings, shaft- observing proximity probes will provide more effective vibration measurements than seismic transducers due to the rotor dynamics of the machine and the attenuation of vibratory energy through a fluid-film boundary. Accord -ingly, Metrix recommends and provides proximity probes and associated 4-20 mA transmitters or monitoring systems for such applications.For machines with rolling element bearings and running above 6,000 rpm, and/or where impulsive casing vibration occurs, acceleration may be a better measurement. In such situations, it is recommended that you consult witha Metrix sales professional who can review your application and assist with selection of the proper transducer type and associated transmitter or monitoring system.• RFI/EMI Immunity – Enhanced circuit design and installa -tion techniques aggressively filter out noise from common sources such as handheld radios•Excellent Moisture Resistance – The 2-pin MIL connec -tor version is hermetically sealed to provide an IP67-rated enclosure. Flying lead and terminal block versions are fully potted and rated to IP66 when installed with optional IEC conduit elbow• Hazardous Area Approvals – North American (CSA), Brazil -ian (INMETRO), and European (ATEX & IEC) approvals avail -able•Dynamic Signal Availability – 2-wire versions provide a 4-20 mA velocity- proportional signal for easy connection to PLCs, DCSs, and other plant control systems. Optional 4-wire ver -sions 1 also provide the raw acceleration signal (100 mV/g) for use with vibration data collectors and analyzers • Variety of Connection Options – Flying leads, terminal block, and MIL-type connectors available• Conduit-Ready 2 – Terminal block and flying lead options have conduit threads on top of sensor. No special housings are required for connection of conduit•Rugged, Industrial Design – Robust construction offers out -standing durability; built-in base and housing strain protec -tion helps ensure that over-torqueing sensor-to- machine and sensor-to-conduit connections won’t damage internals or body•High- and Low-Pass Filter Options – The ST5484E can be ordered with a wide variety of low- and high-pass filter options to precisely tailor the band over which vibration is measured•Polarity-Independent Wiring – Metrix patented IPT® tech -nology allows loop power to be connected without regard to voltage polarity, reducing field wiring errors and ensuring that the raw acceleration output 1 is not phase inverted • Multiple Mounting Options – Integral and removablemounting stud options available in both metric and English thread sizes; flat base mounting adapters are also available • Loop-Powered – Runs on nominal 24 V DC power supplied by the 4-20 mA current loop•Wide Supply Voltage Range – Accepts loop power voltages from 11 to 29.6 V DC (intrinsically safe) or 30.0 V DC (explosion proof & non-incendive)• RMS Amplitude Detection – Measures Root Mean Square (RMS) vibration amplitude. Options available for True RMS or scaled RMS (RMS x √2) for “derived peak”•Numerous Full Scale Ranges – The full scale ranges provid -ed in option AAA reflect frequently-ordered ranges; how -ever, many others (too numerous to list) are also available. Consult factory for applications requiring other full scale rangesNotes:1. Dynamic raw acceleration signal available with 4-wire versions only(ordering options D= 1 and D=3).2. Metrix recommends flexible (rather than solid) conduit when pos -sible. Solid conduit can introduce preload forces on the sensor andalter of the vibration response of the sensor.All specifications are at +25°C (+77°F) and +24 V DC supply voltage unless otherwise noted.FEATURESSPECIFICATIONSST5484E Seismic Velocity 4-20 mA TransmitterDatasheetST5484E Seismic Velocity 4-20 mA TransmitterDatasheetA A AB BCD -ST5484E- - -FE ORDERING INFORMATIONST5484E Seismic Velocity 4-20 mA TransmitterDatasheetNOTES:1. Smaller-diameter mounting studs are not able to withstand sus -tained ambient vibration levels above2.0 in/sec. Consult Table 2 for allowable combinations of A and B options.2. The ST5484E uses an RMS amplitude detection circuit. Full scaleranges in peak units use scaled RMS (i.e., RMS x √2). The “derived peak” measurements will equal true peak only under the special case of a pure sinusoid, not complex vibration signals.3. Hazardous Area Certifications are not compatible with all connec -tion types. Consult Table 3 for allowable combinations of C & D options.4. Some approvals require intrinsic safety barriers, others requireExplosion-Proof wiring practices. Refer to Table 4.5. Refer to the Accessories section of this document. Units sold withan explosion proof rating will include an 8200-000 IEC or 8200-000 explosion proof elbow that will be affixed at the factory.6. High- and Low-Pass filter corners for standard filters must beseparated by at least one octave (low-pass frequency must be at least twice the high-pass frequency). All combinations are allowed except E = 6 and F = 4, 5, or 6. Custom filters with closer separa -tion and/or different roll-offs may be available in some instances.Consult the factory if custom filters are required.Conduit elbows are used with flying leads and terminal block versions of the ST5484E transmitter. They are not compatible with MIL-connector versions of the transmitter. A variety of available configurations accommodate English and metric conduit thread sizes, hazardous area approvals, materials of construction, and IP ratings. Note that not all configurations are available with hazardous area approvals or IP ratings. Consult the ordering information below. For ST5484E’s that need an explosion proof (Ex d) rating, that are utiliz -ing flying leads, Option D=0, 1, 5, & 6, will have an attached 8200 conduit elbow and must be used with a certified junction box or other certified connection location. For ST5484E’s that need an explosion proof (Ex d) rating, utilizing integral terminal block, Option D=2 & 3, no junction box is necessary. Table 4 in the datasheet relates what hazardous area (Option C) is allowed per ST5484E Connection (Op -tion D). ST5484E sold with an explosion proof rating (Ex d) will include a 8200 explosion proof elbow and will be affixed at the factory.Copper-free aluminum elbows (all models except AAA=005)Elbow made from 6061-T6 aluminium which is considered a marine grade aluminium and powder coated in epoxy.Stainless steel elbows (models AAA=005)A A A -B 8200- NOTES:1. CSA approved through manufacturer (not Metrix) for the following areas:Class I, Div. 1 (Grps C & D) Class II, Div. 1 (Grps E, F & G) Class III2. B=IEC is only available for AAA=001, 003, and 008 at this time3. ATEX approved through manufacturer (not Metrix), (B=IEC)ITS09ATEX16417UEx II2G, Ex d IIC CML 16ATEX1325X Ex II2GD, Ex db IIB Gb, Ex tb IIIC Db IP65 minimum 4. IECEx approved through manufacturer (not Metrix)IECExITS09.0024UEx d IIC IECEx QPS 16.0012X Ex db IIB Gb, Ex tb IIIC IP665. Elbow 8200-AAA-IEC is required for ST5484E installations meetingATEX/IECEx/INMETRO/KOSHA/EAC Ex d (flameproof) hazardous area certificationsUL approved through manufacturer (not Metrix) for the following areas: Class I; Div. 1 (Grps. B, C, D)Class II; Div. 1 (Grps. E, F, G)NOTE: Dielectric grease must be applied on the rubber boot connector to prevent moisture ingression.NOTE: Dielectric grease must be applied on the rubber boot connectorST5484E Seismic Velocity 4-20 mA TransmitterDatasheet7084-001Flange Mount AdapterAdapts ½” NPT mounting stud on ST5484E to 3-hole flat-base pattern. Hole pattern is three equally spaced 0.26” diameter holes on 1.5” diameter circle. Adapter is 2” diameter x 0.75” thick. Material: 303 stainless steel 7084-002Flange Mount AdapterSame as 7084-001 except center hole adapts ¼” NPT stud on the 5484E.7084-005Flange Mount AdapterSame as 7084-001 except center hole adapts ⅜ x 24 UNF stud on the 5484E.8253-002½” NPT to ¼” NPT Reducer BushingAdapts ¼” NPT stud on ST5484E (B=0) to ½” NPT mounting hole.Material: 303 stainless steel93818-004Cable Grip Strain Relief FittingUsed primarily with 8978 cable assemblies where cable enters junction box. ¾” NPT male thread to cable grip. Fits cable diameters from 0.156” to 0.25”. Complete with sealing ring and locknut. Hot dip / mechanically galvanized fin -ish. Suitable for NEMA 4 junction boxes.93818-018Cable Grip Strain Relief FittingSimilar to 93818-004, but fits larger cable diameters from 0.4”to 0.5”, such as customer-supplied cables used with terminal block versions of ST5484E (D = 2 or 3).OUTLINE DIAGRAMSFigure 1: Outline dimensions of the ST5484E (all versions except MIL-Style Connector). Dimensions in mm [inches]. Optional* 8200-001 conduit elbow shown installed.* NOTE: 8200-000-IEC elbow is mandatory for ATEX/IECEx/INMETRO/KOSHA/EAC Ex d (flameproof) approved installations. The 8200-000 elbow is mandatory for CSA Ex d (flameproof) approved installations.Figure 2: Outline dimensions of theST5484E-XXX-XX4-XX (MIL-Style Connec -tor). Dimensions in mm [inches].ST5484E Seismic Velocity 4-20 mA TransmitterDatasheetWIRING CONNECTIONS+ AND – SYMBOLSARE NOT ON LABELFigure 3: Typical installation for a single ST5484E seismic vibration transmitter.Figure 4: Typical installation for multiple ST5484E seismic vibration transmitters.ADDITIONAL DOCUMENTATIONTrademarks used herein are the property of their respective owners.Data and specifications subject to change without notice.© 2014 Metrix Instrument Co., L.P .。
Metrix数字接近系统(DPS)数据手册说明书

DatasheetThe Metrix Digital Proximity System (DPS) combines the performance of a fully API 670 compliant eddy-current proximity measurement system with the flexibility of digital configurability. For the first time in our industry, users can configure their transducer system in the field using a custom field-generated curve as well as factory pre-configured calibrations for a variety of probe tip diameters, manufacturers, extension cable lengths, target materials, and linear ranges. Refer to page two of this datasheet for additional details on device configurability.The DPS consists of three elements: a Probe, Extension Cable, and Driver or Transmitter.MX8030 & MX2030 MX8031 & MX2031 PROBE DRIVER OR TRANSMITTERmV/μm, typically 7.87 mV/μm (200mV/mil).MX2034 4-20 mA TransmitterStatic Current Output (mA/µm or mA/mil)OVERVIEWDPSC USPROBE/CABLE0598DatasheetMetrix pioneered the patented technology used in the DPS which provides numerous performance and user-convenience benefits. Developed in 2005 for our vibration transmitters, the technology has proven itself in tens of thousands of installations worldwide. You can configure the device using the included software1 in three ways:- METHOD #1 - By ordering per this datasheet (refer pages 7 and 8).- METHOD #2 - By using the included software to change the configuration to any of the available options for MX2033 drivers and MX2034 transmitters (refer to pages 7 and 8 respectively).- METHOD #3 - Generate a custom curve in the field 2 by recording the gap voltage at increments specified by the software. A custom linearization table is then generated and loaded into the device.Digitally ConfigurableThe DPS Configuration Software features a simple, intuitive user interface that makes it easy to configure the driver & transmitter in the field. Users can select from a discrete list of factory pre-configured curves using drop-down boxes, or generate a custom linearization curve in the field by entering gap voltages at increments specified by the software.These configuration options provide the user with maximum flexibility and accuracy in adapting a single driver or transmitter device to the following parameters:• Target material (including unknown or undeterminedmaterials)• Probe series and tip diameters from various manufacturers • Extension cable lengths• Position, thrust, radial vibration or speed measurement 3• Full scale range 3• Upscale/downscale direction 3Configured DPS units can easily be identified in the field using the DPS configuration software and our optional Metrix User Label Kit P/N 100527 (see Accessories on page 11). The kit consists of specially shaped polycarbonate overlay labels and paper labels (Avery 6570). The customized details are printed on an Avery 6570 label, and this is affixed under a clear rectangular window in the polycarbonate overlay label, providing a weatherproof seal. Target material, probe type and series, system length, and output sensitivity can be recorded. We provide user-configurable fields where you can record installation- and device-specific details such as date of last calibration, instrument loop tag numbers, probe location (machine / bearing / angular orientation), and any other details useful to machinery and instrumentation personnel.The driver or transmitter is configurable via a USB port, protected under the baseplate of the device. The DPS configuration software is available as a free download at .NOTES:1. One can download the Metrix Digital Proximity System (DPS) software from .2. Custom curves assume standard supported probe types (MX2033/MX2034 option BB) and system lengths (MX2033/MX2034 option CC), and that mismatched systems will not be used, such a 7200 cable with an MX2030 probe. Certain material types may limit total available linear range and other specifications. These can be quantified when a material sample is provided to the factory.3. These settings are applicable to MX2034 transmitters only.4. Registered trademark(s) of Bently Nevada®.5. Registered trademark(s) of Metrix®.FEATURES AND BENEFITSUser LabelsDatasheetFull API 670 ComplianceThe DPS was designed to fully comply with API 670 for linear range, interchangeability, standard probe configurations, and all other details.Reduced Spare Parts InventoryThe DPS reduces the requirements for spare parts by allowing a single type of driver or transmitter to be field-configured for a wide range of probe types, cable lengths, and target materials.InterchangeabilityThe Metrix 10,000 Series MX8030 and MX2030 probes and MX8031 and MX2031 extension cables are fully interchangeable with BN 3300 and 3300XL 5mm/8mm probe systems. Such compatibility provides greater choice of suppliers without the need to replace installed probes, cables and drivers.Support for Older Probe SystemsReplacing a complete proximity transducer system including probes/cables buried inside a machine can be expensive and impractical when a machine must keep running. The ability to support older probe systems is becoming increasingly important as users push their plant outage intervals to more and more years. Imagine being able to support not only a multitude of older probe systems, cable lengths, and target materials, but to be able to do so with just a single driver or transmitter. MX2033 drivers and MX2034 transmitters allow the user to change the configuration in the field for use with virtually any Metrix or BN proximity probe and cable (see ordering information on page 7 and 8 for currently supported probe systems).The specifications on the following pages are based upon the following system components, target materials, gaps and temperatures 1, 2 within the Metrix 10,000 proximity probe and cable series:• MX2033 3-wire driver• MX8030/MX2030 8mm probe with 0.5m cable • MX8031/MX2031 4.5m extension cable• AISI 4140 steel target gapped at 50 mils (1.27mm) from probe tip • Temp = 22° C•17 m A RMS current loop noise floorSpecifications for MX2034 loop-powered transmitters assume the same probes, cables, target materials, temperatures, and current loop noise floor as shown above.Interchangeability and accuracy specifications assume the above Metrix products and target materials; they may differ when components from other manufacturers are mixed with Metrix components 3.A user-generated label can be printed in the field with all device characteristics as well as user-specific tagging and installation particulars.NOTES:1. The American Petroleum Institute (API) Standard 670 defines two temperature ranges for proximity probe systems: Testing Range and Operating Range. Except as otherwise noted, all specifications herein are for system performance at 22°C, in the middle of the API 670 Testing Range (0°C – 45°C).2. Target materials other than AISI 4140 steel may restrict the transducer system’s linear range and other specifications. Consult the factory whenever using a non-4140 target to ensure the transducer system will be suitable for the intended measurement range and accuracy requirements. The accuracy limitations on page 5 of this Datasheet should be increased by +/- 5% from the stated values when using a non-4140 target material.3. A manufacturer’s interchangeability specifications are based on statistical variations against their own reference transducer system. Because the reference transducer systems used by other manufacturers are not within the control of Metrix, interchangeability specifications for mixed systems cannot be guaranteed, but will generally be about twice as large as when all transducer system components come from a single manufacturer. However, where known, these differences can be compensated in the field using the transducer system’s configurability capabilities, allowing mixed system performance to meet or exceed that of a non-mixed system.FEATURES AND BENEFITS (Continued)SPECIFICATIONSDIGITAL PROXIMITY SYSTEM (DPS)DatasheetSPECIFICATIONS (Continued)ELECTRICALChannels:Driver or transmitter accepts one probe and extension cable Driver or TransmitterExcitation Voltage:(Reduced linear range will occur when voltage at the driver or transmitter terminal is more positive than -19 Vdc)Contact factory if you needother probes or cables.Driver or TransmitterMax CurrentConsumption:Driver or Transmitter Output Types:Field Wiring Gauge: Recommended: 0.8 mm 2 (18 AWG) Allowed: 0.2 to 1.3 mm 2 (16 to 24 AWG)Field Wiring Type: • MX2033: 3-conductor shielded cable • MX2034: 2-conductor shielded cable (4-20 mA) • RG-58 A/U coax cable (BNC connector)Max. Field Wiring Length: MX2033: 300 m (1000 ft) driver to monitor2 MX2034: 4-20 mA: 5000 m (16,400 ft) transmitter to Control System3Min. Target Size: 15.2 mm (0.6 in) diameter (assuming flat surface)Min. Shaft Diameter: Minimum: 50.8 mm (2.0 in), TightView-XY (to 12.7mm(0.5in))Linear Range: NOTES:1. For vibration and position the current output will be driven to the less than 3 mA if probe to target is out of 10-90 mil range for 5mm/8mm probe or 20-180 mil for MX8030 Extended Range and 11mm probe system.2. Length limit is imposed by distributed cable capacitance and corresponding frequency response roll-off. Assumes standard 18 AWG 3-conductor cable with capacitance of 290 pF/m, no I.S. barriers. Total cable capacitance in excess of 450 nF will limit frequency response at monitor to less than published 8-kHz specification. Consult the manual (Metrix Document 1093672) for further details.3. Length limit is imposed by distributed cable resistance and corresponding voltage drop at maximum current output. Assumes 18 AWG 2-conductor cable with resistance of 20 Ω/km, 24 V DC supply voltage, 250 Ω load resistance, no I.S. barriers. Consult the manual for further details.All Metrix proximity probes and cables fall under the 10,000 series.* Range starts at approx. 10 mils (250µm) gap (-1V)** Range starts at approx. 20 mils (500µm) gap (-1V)Suggested Probe Gap:Supported Probe Types: MX2033 driver and MX2034 transmitters are compatible with the probes andextension cables as shown.DIGITAL PROXIMITY SYSTEM (DPS)DatasheetNOTES:1. Values shown are for 5m systems. For 9m systems, allow an additional ±1.5%ISF and DSL variance. These variances assume a 4140 Target Material, seenote 2 page 3 for other materials.2. Use of proximity probe system components from other manufactures may introduce measurement errors. For other manufacturer Interchangeabilityerrors, when measured in increments of 0.25 mm (10 mils) over the linear range between 65°C and -35°C (API Operating Range), allow an additional±1.5% ISF and DSL variance.3. ISF shown assumes mV-type output and is valid for MX2033 and BNC con -nector on MX2034.4. Above ISF values for MX2034 transmitter pertain only to the BNC connector,however, the API 670 standard for ISF for the transmitter’s 4-20mA proportional output is attainable when configured for Position and Vibration (for vibrationcalibration checks, the design and calibration errors on the vibration input device must be included, typically for a shaker up to 8%). When an MX2034 transmitter is configured for speed, proportional output error is less than 1%.5. For these legacy systems, the ISF variance stated is for the API 670 Test Range-0°C to +45°C (+32°F to +110°F) with a 10-point custom calibration. Outside the Test Range, but within the API 670 Operating Range -35°C to +65°C (-30°Fto +150°F) the allowable variance is ±25%.SPECIFICATIONS (Continued)Incremental Scale Factor (ISF)1-4 andDeviation from Best-FitStraight Line (DSL):MECHANICALDriver and Transmitter Case Material:Connector Torque:Maximum: 0.565 N-m (5 in-lb)Recommended: finger tightWorking and Storage Temperature: Driver or Transmitter: -40°C to +85°C (-40°F to +185°F)Relative Humidity: 95%, non-condensingPatents: Digital performance curve technology in driver and transmitter: US patent number 7768258. RECOMMENDED BARRIERSPassive Zener: MX2033: MTL 7796- (or equivalent)MX2034: MTL 7787+ (or equivalent)Active Galvanic: MX2033: MTL 5531, P&F KFD2-VR4-Ex1.26, or equivalent MX2034 (DD=5): MTL 5541, P&F KFD2-STC4-Ex1, or equivalentMX2034 (DD=7): P&F KFD2-STC4-Ex1, or equivalent for terminals1+ & 3- P&F KFD2-VR-EX1.19-Y109129, or equivalent for BNC (terminals 4+ & 5- must not be used)ENVIRONMENTALPBT thermoplastic polymer blend(contains PBT, carbon fiber, and glass beads) Class I, Div 1, Grps A,B,C,D, T4 Class I, Div 2, Grps A,B,C,D, T4 KOSHA/Custom UnionII 1G Ex ia IIC T3 Ga -40°C ≤Ta≤ +177°C II 1G Ex ia IIC T4 Ga -40°C ≤Ta≤ +110°C Intrinsically SafeII 1G Ex ia IIC T4 Ga -40°C ≤Ta≤ +85°C II 3G Ex nA IIC T3 Gc -40°C ≤Ta≤ +177°C II 3G Ex nA IIC T4 Gc-40°C ≤Ta≤ +110°C Non-Incendive orIncreased SafetyII 3G Ex nA/ec IIC T4 Gc-40°C ≤Ta≤ +85°C CUSAll Metrix proximity probes and cables fall under the 10,000 series.WEIGHT AND DIMENSIONSDimensions:MX2033 Driver: See Fig 1, page 6MX2034 Transmitter: See Fig 2, page 9Weight:MX2033 Driver: 247 g (8.7 oz)MX2034 Transmitter: 247 g (8.7 oz)ACCESSORIESMounting Options for MX2033 and MX2034:- 35mm DIN rail (standard)- 4-hole flat base with 2” x 2” and 2.5” x 2.75” hole patterns (requires optional adapter P/N 9647)Intrinsically Safe*Non-Incendive or Increased Safety Note:* Intrinsically safe not available for MX2034 4-wire (EE=04, 05 & 06)0598DIGITAL PROXIMITY SYSTEM (DPS)DatasheetNOTES:1. AISI-SAE 4140 chromium molybdenum steel is the standard default calibration per API 670. If no material type is specified at time of ordering, a factory-standard AISI 4140 target will be used. Calibration to target materials other than 4140 may restrict linear range and other specifications. Consult the factory.2. Due to the electrical properties of this material, vibration measurement accuracy may be affected when using this target.3. Calibration to other material types is available upon request. Metrix will normally request that the customer supply a suitable sample of the material, allowing a machined target with appropriate surface finish to be produced.4. Compatible with BN 7200, 3300, 3300XL, NSv, and Metrix MX2030, MX8030 probes only.5. Compatible with BN NSv and RAM probes only.6. Compatible with BN 7200, 3300, 3300XL, and MX2030, MX8030 probes only.7. Compatible with 3000 series probes only.8. ETL, ATEX and IECEx hazardous area approvals.9. Can be used with the MX8030 TightView Probe System.10. Used to prevent cross talk when paired with an option BB=09 DPS (Shaft diameters <1.5 inches (37.5 mm)).HOW TO ORDER MX2033DIGITAL PROXIMITY SYSTEM (DPS)DatasheetDIGITAL PROXIMITY SYSTEM (DPS)Datasheet Figure 2: Dimensions in inches [mm] for MX2034 digital proximity transmitterNote: optional 4-hole baseplate mounting adapter shown (P/N 9647). 35mm dinrail mount is standard.DIGITAL PROXIMITY SYSTEM (DPS)DatasheetDPS User Label Kit for up to 16 devices (P/N 100527)Each MX2033 driver and MX2034 transmitter comes with the four factory-applied labels summarized below. The DPS User Label Kit allows the Left Sidewall Label to be replaced with a customized label containing installation-specific data, as depicted on page 3 of this datasheet. The User Label Kit contains enough materials for labeling up to 16 signal conditioners as follows:• 16 specially-shaped polycarbonate adhesive labels with a clear rectangular window and the Metrix logo. • A sheet of 32 standard 1.75” W x 1.25” H labels (Avery 6570).Using the Metrix DPS Configuration Software, the desired information is printed directly onto the Avery 6570 sheet using any Windows-compatible inkjet or laser printer. The printed Avery label is removed from the sheet, placed behind the window on the polycarbonate label, and both are then affixed to the left sidewall of the DPS signal conditioner. The polycarbonate label uses the same finish as all other factory-applied labels, providing protection from the elements and giving a clean, durable, and professional finish.Of the four labels affixed to each DPS signal conditioner, only the Left Sidewall Label is intended for customization and field replacement. The others are designed to remain permanently affixed to the device during its life and contain information that does not change with device configuration.1. Left Sidewall Label (Configured Devices)All devices ordered in a configured state will have this label affixed. The label will reflect the as-ordered configuration data. 2. Right Sidewall LabelThis is a factory-applied permanent label with the serial number, date of manufacture, model number and all approvals data.3. Front LabelThis is a factory-applied permanent label that indicates the connector for the probe and extension cable.4. Top LabelThis is a factory-applied permanent label that indicates the wiring terminals, model number, and (MX2034 only) BNC connection details. A machine tag label can be placed in an open space here.NOTE: The User Label Kit must be ordered separately and is not automaticallyincluded with driver or transmitter.DIN to 4-Hole Flat Base Mounting Adapter (P/N 9647)This adapter allows the 35mm DIN rail clip on MX2033 driver, and MX2034 transmitters to be compatible with a 4-hole flat base mounting method. The adapter has industry-standard hole patterns for both a 2” x 2” square and a 2.75” x 2.5” rectangle. The 2” x 2” pattern matches the holes on Metrix 5533 drivers and BN* 3300, 7200, and 3000 series Proximitor* devices. The 2.75” x 2.5” pattern matches the holes on Metrix 5465/5488 transmitters and BN* 990/991 transmitters. Material is 19 gauge mild steel (ASTM A366 or equal) with gold chromate zinc plating.The most recent versions of the Metrix DPS Configuration Software and the DPS user manual can be downloaded from the Metrix website, .NOTE: Manuals are published electronically in Adobe® PDF format and may be printed and freely distributed. Adobe Reader is required and can be downloaded free from .* Registered trademark(s) of Bently Nevada®.ACCESSORIESMANUALS AND SOFTWAREDimensions are inch [mm]。
真度METRIX血糖自测仪说明书

TRUE METRIX ®The McKesson TRUE METRIX® Self-Monitoring Blood Glucose System is intended for the quantitative measurement of glucose (sugar) in fresh capillary whole blood samples drawn from the fingertip or forearm. It is intended to be used by individual patients in home care settings or in facilities where the meter is not shared between patients. Featuring Triple Sense Technology™, the systems detect, analyze and correct for environmental and physiological variability, including hematocrit and temperature, resulting in improved precision and accuracy. Designed for use only with McKesson TRUE METRIX® Blood Glucose Test Strips and Control Solutions.Features and Benefits• No coding required • Results as fast as 4 seconds • Tiny 0.5 microliter sample size• Alternate site testing (fingertip or forearm)• Stores up to 500 results with time/date • Event tagging; analyzes environmental and physiological factors to better interpret tests • 4 testing reminder alarms• Audible fill detection for blood or control sample• Ketone test reminder•Easy-to-use "hands free" strip release buttonThe product information contained in this document, including the product images and additional product materials, was collected from various supplier sources. All product claims and specifications are those of the product suppliers and have not been independently verified by McKesson Medical-Surgical or its affiliates (“McKesson”). McKesson is not responsible for errors or omissions in the product information.The properties of a product may change or be inaccurate following the posting or printing of the product information in the document, either in the print or online version. Caution should be exercised when using or purchasing any products from McKesson’s online or print documents by closely examining the product packaging and the labeling prior to use.Due to product changes, information listed in this document is subject to change without notice. This information is placed solely for your convenience in ordering and McKessonIf you are not completely satisfied with any McKesson Brands product, you may return it for a full refund or credit.With McKesson Brands, you’ll never have to compromise. We deliver quality products at competitive prices, backed by our 100% satisfaction guarantee. We have decades of experience in the market, and we offer you support and work to help ensure you have the products you need, when you need them — making it even easier for you to provide the best care for your patients.Never Compromise on Care SM。
Те克特莱山 AC DC 电流测量系统 说明书
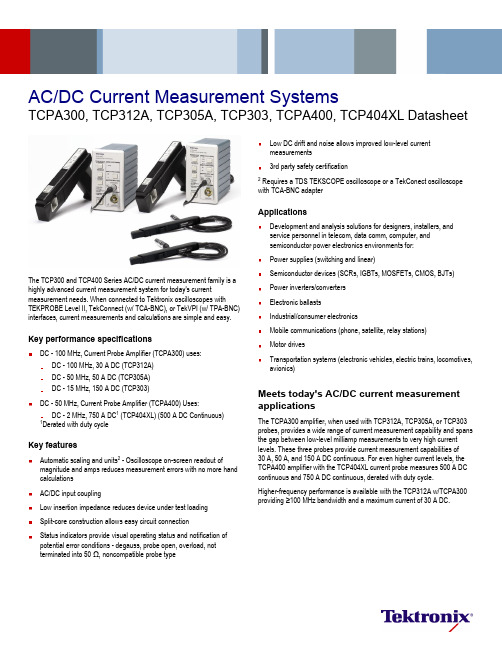
AC/DC Current Measurement SystemsTCPA300, TCP312A, TCP305A, TCP303, TCPA400, TCP404XL DatasheetThe TCP300 and TCP400 Series AC/DC current measurement family is a highly advanced current measurement system for today's current measurement needs. When connected to Tektronix oscilloscopes with TEKPROBE Level II, TekConnect (w/ TCA-BNC), or TekVPI (w/ TPA-BNC)interfaces, current measurements and calculations are simple and easy.Key performance specificationsDC - 100 MHz, Current Probe Amplifier (TCPA300) uses:DC - 100 MHz, 30 A DC (TCP312A)DC - 50 MHz, 50 A DC (TCP305A)DC - 15 MHz, 150 A DC (TCP303)DC - 50 MHz, Current Probe Amplifier (TCPA400) Uses:DC - 2 MHz, 750 A DC 1 (TCP404XL) (500 A DC Continuous)1Derated with duty cycleKey featuresAutomatic scaling and units 2 - Oscilloscope on-screen readout of magnitude and amps reduces measurement errors with no more hand calculations AC/DC input couplingLow insertion impedance reduces device under test loading Split-core construction allows easy circuit connectionStatus indicators provide visual operating status and notification of potential error conditions - degauss, probe open, overload, not terminated into 50 Ω, noncompatible probe typeLow DC drift and noise allows improved low-level current measurements3rd party safety certification2 Requires a TDS TEKSCOPE oscilloscope or a TekConect oscilloscopewith TCA-BNC adapterApplicationsDevelopment and analysis solutions for designers, installers, and service personnel in telecom, data comm, computer, and semiconductor power electronics environments for:Power supplies (switching and linear)Semiconductor devices (SCRs, IGBTs, MOSFETs, CMOS, BJTs)Power inverters/converters Electronic ballastsIndustrial/consumer electronicsMobile communications (phone, satellite, relay stations)Motor drivesTransportation systems (electronic vehicles, electric trains, locomotives,avionics)Meets today's AC/DC current measurement applicationsThe TCPA300 amplifier, when used with TCP312A, TCP305A, or TCP303probes, provides a wide range of current measurement capability and spans the gap between low-level milliamp measurements to very high current levels. These three probes provide current measurement capabilities of 30 A, 50 A, and 150 A DC continuous. For even higher current levels, the TCPA400 amplifier with the TCP404XL current probe measures 500 A DC continuous and 750 A DC continuous, derated with duty cycle.Higher-frequency performance is available with the TCP312A w/TCPA300providing ≥100 MHz bandwidth and a maximum current of 30 A DC.Measurement errors and manual calculations are now a thing of the pastWith this new series of current measurement tools, automatic control and on-screen scaling and units is provided for users of Tektronix TDS3000, TDS500, TDS600, TDS700, TDS5000, TDS6000, and TDS7000B series oscilloscope systems (the DPO3000, MDO/MSO/DPO4000, MSO/DPO5000, and DPO7000 series oscilloscopes, the TPA-BNC adapter is required).The TCP300/TCP400 current measurement systems seamlessly integrate with your TDS series oscilloscope.Even non-TEKPROBE systems can use the TCPA300/400 series to make proper current measurements by simply multiplying the measured output voltage on the oscilloscope by the TCPA300/400 series range setting.SpecificationsAll specifications apply to all models unless noted otherwise. Model overviewDatasheet2 CharacteristicsMaximum current ratingsHigh-current sensitivityLow-current sensitivityRange 1 A/V 5 A/V 5 A/V N/A DC (continuous) 5 A 25 A 25 A N/A RMS (sinusoidal) 3.5 A 17.7 A 17.7 A N/A Peak50 A50 A500 AN/APhysical characteristicsAmplifiersProbesMaximum conductor sizeCable length1.5 m (60 in)1.5 m (60 in)2 m (78.7 in)8 m (315 in)EMC environment and safetySafety complianceElectromagnetic compatibility,amplifiers only EC Council Directive 89/336/EEC, FCC Part 15, Subpart B Class A, AS/NZS 2064.1/2.TemperatureOperating 0 °C to +50 °C (32 °F to 122 °F)Nonoperating-40 °C to +75 °C (-40 °F to 167 °F)AC/DC Current Measurement Systems 3HumidityOperating5% to 95% R.H. to +30 °C (86 °F)5% to 85% R.H. +30 °C to +50 °C (86 °F to 122 °F)Nonoperating5% to 95% R.H. to +30 °C (86 °F)5% to 85% R.H. +30 °C to +75 °C (86 °F to 167 °F)AltitudeOperating2000 m (6800 ft.) maximumNonoperating12,192 m (40,000 ft.) maximumOrdering informationModelsProbesTCP312A Probe AC/DC current, DC to 100 MHz; 30 A DC (Requires TCPA300 amplifier)TCP305A Probe AC/DC current, DC to 50 MHz; 50 A DC (Requires TCPA300 amplifier)TCP303 Probe AC/DC current, DC to 15 MHz; 150 A DC (Requires TCPA300 amplifier)TCP404XL Probe AC/DC current, DC to 2 MHz; 500 A DC (750 A DC derated with duty cycle) (Requires TCPA400 amplifier) AmplifiersTCPA300 Amplifier AC/DC current probe, DC to 100 MHz, (Requires TCP305A or TCP312A or TCP303 probes)TCPA400 Amplifier AC/DC current probe, DC to 50 MHz, (Requires TCP404XL probe)Recommended accessoriesCover, large probe protective; (forTCP303, TCP404XL)016-1924-00Case, transit; currentmeasurement systems016-1922-0050 Ω feedthrough termination011-0049-0250 Ω BNC-to-BNC coaxial cable012-0117-00TEKPROBE interface cable,TCPA300 or TCPA400 amplifier toTDS series oscilloscopes012-1605-00Current loop, 1 turn, 50 Ω, BNCconnector (for TCP305A, TCP312A,TCP202A)067-2396-00Current loop, 1 turn, 50 Ω, BNCconnector (for TCP303, TCP404XL)015-0601-50TCPA300/TCPA400 amplifiercalibration adapter174-4765-00Power measurements deskew fixture for TCP202A, TCP305A, TCP312A, TCP303 probes 067-1478-00Datasheet4 WarrantyOne year parts and labor.Power requirementsAmplifiers90 V to 264 V, 47 to 440 Hz, 50 W; Maximum CAT II (auto switch)Probes TCP312A, TCP305A, TCP303 probes require a TCPA300 Amplifier; TCP404XL probe requires a TCPA400 Amplifier OptionsPower plug optionsOpt. A0North America power plug (115 V, 60 Hz)Opt. A1Universal Euro power plug (220 V, 50 Hz)Opt. A2United Kingdom power plug (240 V, 50 Hz)Opt. A3Australia power plug (240 V, 50 Hz)Opt. A5Switzerland power plug (220 V, 50 Hz)Opt. A6Japan power plug (100 V, 110/120 V, 60 Hz)Opt. A10China power plug (50 Hz)Opt. A11India power plug (50 Hz)Opt. A12Brazil power plug (60 Hz)Opt. A99No power cordServiceOptionsOpt. C3Calibration Service 3 YearsOpt. C5Calibration Service 5 YearsOpt. D1Calibration Data ReportOpt. D3Calibration Data Report 3 Years (with Opt. C3)Opt. D5Calibration Data Report 5 Years (with Opt. C5)Opt. R3Repair Service 3 Years (including warranty)Opt. R3DW Repair Service Coverage 3 Years (includes product warranty period). 3-year period starts at time of instrument purchase Opt. R5Repair Service 5 Years (including warranty)Opt. R5DW Repair Service Coverage 5 Years (includes product warranty period). 5-year period starts at time of instrument purchase Opt. SILV400Standard warranty extended to 5 years (TCP305A, TCP312A, TCPA300, TCPA400 )Opt. SILV600Standard warranty extended to 5 years (TCP303, TCP404XL)Tektronix is registered to ISO 9001 and ISO 14001 by SRI Quality System Registrar.AC/DC Current Measurement Systems 5DatasheetASEAN / Australasia (65) 6356 3900 Austria 00800 2255 4835*Balkans, Israel, South Africa and other ISE Countries +41 52 675 3777 Belgium 00800 2255 4835*Brazil +55 (11) 3759 7627 Canada180****9200Central East Europe and the Baltics +41 52 675 3777 Central Europe & Greece +41 52 675 3777 Denmark +45 80 88 1401Finland +41 52 675 3777 France 00800 2255 4835*Germany 00800 2255 4835*Hong Kong 400 820 5835 India 000 800 650 1835 Italy 00800 2255 4835*Japan 81 (3) 6714 3010 Luxembourg +41 52 675 3777 Mexico, Central/South America & Caribbean 52 (55) 56 04 50 90Middle East, Asia, and North Africa +41 52 675 3777 The Netherlands 00800 2255 4835*Norway 800 16098People's Republic of China 400 820 5835 Poland +41 52 675 3777 Portugal 80 08 12370Republic of Korea 001 800 8255 2835 Russia & CIS +7 (495) 6647564 South Africa +41 52 675 3777Spain 00800 2255 4835*Sweden 00800 2255 4835*Switzerland 00800 2255 4835*Taiwan 886 (2) 2722 9622 United Kingdom & Ireland 00800 2255 4835*USA180****9200* European toll-free number. If not accessible, call: +41 52 675 3777 Updated 10 April 2013 For Further Information. Tektronix maintains a comprehensive, constantly expanding collection of application notes, technical briefs and other resources to help engineers working on the cutting edge of technology. Please visit . Copyright © Tektronix, Inc. All rights reserved. Tektronix products are covered by U.S. and foreign patents, issued and pending. Information in this publication supersedes that in all previously published material. Specification and pricechange privileges reserved. TEKTRONIX and TEK are registered trademarks of Tektronix, Inc. All other trade names referenced are the service marks, trademarks, or registered trademarks of their respective companies.24 Apr 201360W-16458-7 。
PRO VIBRATION SWITCH FAMILY 安装手册说明书

PRO VIBRATION SWITCH FAMILYInstallation ManualOVERVIEWThe P RO440/6000 i s a v ersatile, p rogrammablevibration protection instrument. Within itsstandard configuration, the electronic switchis an economical single set point vibrationswitch loaded with standard features andpackaged in industrial grade housing.PRO switches can be configured via a realtime remote operator interface membranekeypad or a USB interface to a PC. Thiscapability allows users to tailor the switchspecifically to their monitoring needs. Inaddition, an isolated proportional 4-20 mAoutput and a buffered output give easyaccess to the machine vibration signal.The PRO switch accepts most accelerometeror velocity inputs. It can also accept and powera 4-20 mA loop powered sensor to becomea field monitor. When fully configured, theswitch provides local machine protectionwith an optional alphanumerical readout.Doc# 1010910 • REV L (May 2015)Doc# 1010910 • REV L (May 2015) Page 2 of 20GENERAL SAFETY SUMMARYReview the following safety precautions to avoid injury and prevent damage to this product or any products connected to it. To avoid potential hazards, use this product only as specified. Only qualified personnel should perform installation and un-installation procedures.CONNECT AND DISCONNECT PROPERLYDo not connect or disconnect this product while it is connected to the live power source.GROUND THE PRODUCTThe housing of this product should be connected to earth ground. Before attempting to turn on the product ensure the housing of this product is properly grounded.OBSERVE ALL TERMINAL RATINGSTo avoid fire or shock hazard, observe all ratings and markings on the product. Consult the product installation manual for further ratings information before making connections to the product.DO NOT OPERATE WITHOUT COVERDo not operate this product with cover removed.AVOID EXPOSURE TO CIRCUITRYDo not touch exposed electrical connections and components when power is present.DO NOT OPERATE WITH SUSPECT FAILURESIf you suspect there is damage to this product, have it inspected by qualified personnel.SAFETY TERMS AND SYMBOLSTerms that appear in this manual: WARNING: Warning statements identifyconditions or practices that could result in injury or loss of life.CAUTION: Caution statements identify conditions or practices that could result indamage to these products or other property.Symbols that may appear on the products:Danger High Voltage Attention Refer to Manual Protective (Earth)TerminalFunctionalGroundDoc# 1010910 • REV L (May 2015) Page 3 of 20INSTALLATION Mechanical HousingThere are two types of the housing for the vibration switch.PRO440 housing PRO6000 housingThe sensitive axis of the switch can be mounted on any radial axis, although the horizontal axis is preferred so that unit can see maximum vibrations. The horizontal axis also reducesthe temperature exposure as compared to the vertical axis.Figure 1: Placement of the switch within the ApplicationDoc# 1010910 • REV L (May 2015) Page 4 of 20The optional display can be rotated +/- 60 degree to bring it to a readable position.The switch is designed to dissipate internal heat by conduction through its base. Hence, it is important to keep the mounting surface at or below the switch max temperature limit of 185°F. If the equipment being monitored is going to exceed this limit, consideration should be given to either using one of the remote transducers, or thermally isolating the switch.Although seal tight and other flexible conduit have been used successfully, in areas of extreme humidity or moisture it is recommended that an “SO” type cable together with a suitable rain-tight CGB fitting be used.Figure 3NOTE: Do not install the switch in such a position that is difficult to connect to and to disconnect from the target machine/motor as shown in the Figure 3.WIRINGAlphanumerical display board must be removed to access the terminal strips / field interface.Remove the display board to allow wiring to the terminal strips on the switch.CONNECTOR FOR DISPLAY AND KEYPADPIN 1ALARM / SHUTDOWN BICOLOR LEDSENSOR OK/NOT OK BICOLOR LED’SUSB CONNECTOR J1BYPASS LEDFigure 4: Interface Board Top ViewPin No.Connections DescriptionL+AC L OR 24V +ve Live of Mains OR +ve terminal of 24V DC power supplyN-AC N OR 24V –ve Neutral of Mains OR –ve terminal of 24V DC power supplyG EARTH E Earth of mains OR Earth of DC power supplyNot used N/ANO1NO LIM1ALARM Relay NOC1COM LIM1ALARM Relay COMNC1NC LIM1ALARM Relay NCNO2NO LIM2SHUTDOWN Relay NOC2COM LIM2SHUTDOWN Relay COMNC2NC LIM2SHUTDOWN Relay NCTable 1: J3 Terminal strip for Power connectionsThe power required is indicated on the nameplate. The voltage supply must be within the following limits:• 24VDC: 22 to 26V DC• VAC: 85 to 265V AC, 50/60 HzCONNECTING ALARM & SHUTDOWN RELAY OUTPUTSPotential free contacts for Alarm and Shutdown signals are provided on the terminal blocks as shown in Table 1.At the LIM1 terminals, loads like enunciators, lamps etc. can be connected between NO1 & C1 or between NC1 & C1. Maximum load is 10A for both the outputs.The internal shutdown switch circuit is designed to be wired in series with the external shutdown circuit i.e. motor starter, contactor, etc. At LIM2 terminals the load should be connected.The maximum load that can be connected to the LIM1 OR LIM2 is 10A.Doc# 1010910 • REV L (May 2015) Page 5 of 20Doc# 1010910 • REV L (May 2015) Page 6 of 20Pin No.Connections Functions1 (RST+)RESET+ (signal)Reset Switch +Ve Terminal2 (RST-)RESET- (common)Reset Switch –Ve Terminal3 (BYP+)Bypass+ (signal)Bypass Switch +Ve Terminal4 (BYP-)Bypass- (common)Bypass Switch –Ve Terminal5 (mA-)Analog Output- (common)4-20 mA Common6 (mA+)Analog Output+ (signal)4-20 mA Output7 (OUT+)Buffer Output+ (signal)Buffer Output Signal8 (OUT-)Buffer Output – (common)Buffer Output Common9 (IN+)External Sensor+ (signal)External Sensor Input +Ve Terminal 10 (IN-)External Sensor- (common)External Sensor Input –Ve Terminal 11 (SHLD)External Sensor ShieldExternal Sensor Shield ConnectionTable 3: J2 Terminal on Interface Board Connection DescriptionsCONNECTING THE RESET INPUTIf remote reset capability is desired, connect the Reset terminals to the remotely located momentary NO (Normally Open) push button switch. User is expected to connect a potential free contact at these terminals. The necessary excitation for this Reset Switch is provided by the vibration switch. The RESET input clears all the latched alarms when the reset input is momentarily closed. The resetting of alarms occurs only after the input is below the alarm set points. The reset switch does not play any role in non latching type of alarms. To reduce the noise pick up, a shielded wire is preferred.Pin No.Connections FunctionsRST RESET +Reset Switch +Ve Terminal RESET - Common Reset Switch –Ve Terminal BYP Bypass +Bypass Switch +Ve Terminal Bypass - Common Bypass Switch –Ve Terminal mA-Analog O/P Common 4-20 mA Common mA+Analog O/P +4-20 mA OutputOUT+Buffer O/P +Input Signal Buffer Output OUT-Buffer O/P Common Buffer Output Common IN+Ext Sensor+_IN +ve terminal of Sensor Output IN-Ext Sensor-_IN -ve terminal of Sensor Output SHIELDShieldTable 2: J2 Terminal strip for I/O connectionsCONNECTING THE BYPASS INPUTThe bypass input forcefully disables the relays from entering into alarm or shutdown states. Connect Bypass terminals to the remotely located NO (Normally Open) toggle switch. Close the switch to short the bypass contacts and put the switch in bypass mode. The necessary excitation for this Bypass Switch is provided by the vibration switch. To reduce the noise pick up, a shielded wire is preferred.CONNECTING THE ANALOG OUTPUTProportional analog 4-20mA output is provided from the vibration switch. 4 mA corresponds to zero vibration; 20mA corresponds to full scale vibrations as set by range mA. The 4-20 mA output is self-powered (sourcing) and therefore requires no external power source. The 4-20 mA output is electrically isolated from the switch power supply. Shielded wire is recommended to reduce the noise pick up. In case of any malfunction like sensor not ok, the analog output is dropped to 3.6 mA.CONNECTING THE BUFFER OUTPUTRaw signal from the sensor is available at the terminal block. It is capable of driving a cable with a capacitance of up to 0.02uF. The buffered output provides connection terminals to access the “raw” output of the vibration sensor. Continuous short circuit protection is provided for the buffer output.CONNECTING THE EXTERNAL SENSORConnect external sensors between IN + & IN - terminals for acquisition. The following types of sensor can be connected to the switch:• External Accelerometer• Piezo-electric velocity• Electromechanical velocity (Metrix 5485C)• 4-20mA Transmitter inputWIRING RECOMMENDATIONSFor incoming power and switch outputs use approved wire of 14 AWG (1.5sq. mm) or smaller. For reset and bypass functions use a twisted pair cable to reduce electrical noise pick up. The dynamic sensor signal output is available at the terminal strip. For the Analog & Buffer dynamic signal outputs a shielded twisted pair cable is recommended. The shield should be common at the receiver end only. For the dynamic buffer signal output the capacitance of the cable run must not exceed 0.02uF. It is highly recommended that all power wiring should be routed separately from the output signals to reduce AC/transient noise pick up.No stress should be given on the terminal block wiring. If such protection is not provided by the conduit system, some form of stress relief must be installed where wiring exits the housings. To assure compatibility with EMC standards, any signal level wiring for transducer, reset or 4-20 mA, etc. should utilize shielded cable in EMI proof conduit, separate from any power wiring.Doc# 1010910 • REV L (May 2015) Page 7 of 20WIRING DIAGRAMDoc# 1010910 • REV L (May 2015) Page 8 of 20GND PointThe Earth wire from the input power supply should be connected to the Ground Point on the Switch Housing as shown above.CONFIGURATION / CALIBRATION OF THE PRODUCTWithin the Display, the user can configure the switch using alphanumeric display and keypad. If display is removed, the PRO configuration software (User software) is available to the customer for configuration and for diagnostic tests of the product. This software is availble as a free download at The interface between the product & PC is via USB. For this interface the USB connector is available on the interface board as shown in the “Figure 4: Interface Board Top View”. A USB cable is required.CONFIGURATION USING THE OPTIONAL DISPLAYInsert the power cord into the J3 terminal connector per Table 1 and switch ON the system. The power up sequence should be as mentioned below. After power up, the switch enters into Measurement Mode.With the optional display, the switch automatically displays the vibrations, read by the sensor as per the configuration. Type and Unit of measurement are displayed on the second line of the display.POWER UP SEQUENCEAfter switching ON the electronic switch the following start up sequence is displayed: PRO440 Housing PRO6000 HousingSENSRINP YYYYYYXX.XXAAABBBYYYYYY represents the sensor type as per theconfiguration.XX.XX represents measured value. AAA representsthe measurement unit. BBB represents themeasurement type i.e. RMS / PK.Figure 5: Power Up SequenceDoc# 1010910 • REV L (May 2015) Page 9 of 20Doc# 1010910 • REV L (May 2015) Page 10 of 20USER INTERFACE DESCRIPTIONThe user interface for the switch is a 2 line X 8 character alphanumeric display and 4 button keypad. Using this Keypad and display user can navigate through Trip Settings, Reset, Configuration, Diagnostic and Measurement mode.After powering on, the switch displays the configured sensor type and waits for the power up delay. The user can enable menu options by pressing the MENU key and then can navigate the menus and their options using other keys. The Default mode for the Switch is measurement mode. If a key is not pressed for 60 sec. it automatically goes into the measurement mode.KEYBOARD FUNCTIONSFigure 6: Keyboard and DisplayMenu Key: The MENU key can be used at anytime to return to the Main Menu for selection of different modes. When the MENU key is pressed the Main Menu options are displayed. There are 5 Main Menu options, described in later sections.(Down arrow key): By pressing this key the user can navigate through various menu andsub-menu options. This key also functions as an increment key during numerical entry. (Enter key): This key is used to enter into a selected menu. It is also used to confirm/store entered values.(Right arrow): This key is used to position the cursor at the desired place during numerical entry. The cursor moves in a left to right direction.MENUENTERALMOKBYPMETRIXDISPLAYALARM,SENSOR OK & MENU KEYDOWN ARROW KEYMAIN MENUThe GUI interface is menu driven. Each menu may have lower level submenus The GUI Main menu map is as follows.The default mode for the switch is measurement mode. The user can select a different mode by pressing MENU key, by pressing moving throught all modes.User can operate switch in one of the following modes:• Trip setting• Reset Alarms• Configuration• Diagnostic• Measurement modeSUB MENUSThe following sub-submenus will be displayed for each selected switch mode.TRIP SETTINGSIn this menu the user will be able to change parameter related to trip level and trip delay.Note: By pressing key the digit of a displayed number shall blink and same digit can be incremented using key. The edited number should confirmed by key.RESET ALARMSThe user can reset the alarms in latched condition by selecting Confirm Reset.CONFIGURATION MENUThe sub-menu and configuration options available to the user in configuration mode are as shown in the flowchart below.In the configuration, user is allowed to modify / alter the following parameters, depending upon the type of sensor:• Sensitivity• Sensitivity Unit• Measurement Unit• Full scale range• Alarm Setpoint• Shutdown Setpoint• Power On Delay• Trip Delay• Latching / Non Latching type of alarm• Energized / Non energized state of alarm• Measurement mode – RMS / True PeakINTERNAL SENSOR TYPE SELECTIONNote 1: By pressing key the sensor type shall selected and will display “SELECT SENSRINP” screen. For the switchs configured for Internal Accelerometer type of sensor no other choices are available.Note 2: By pressing key interface scrolls back to “SENSRINP INT ACEL” screen.EXTERNAL SENSOR TYPE SELECTION WITH OTHER PARAMETERSNote 1: By pressing key the sensor type shall selected and will display “SELECT SENSRINP” screen. (For conformation, by pressing desired setting will display by pressing back to “SELECT SENSRINP”).Note 2: By pressing key the interface scrolls through all sensor type choices.Note 3: By pressing key the measurement unit will be selected and shall display “SELECT M.UNIT” screen.Note 4: By pressing key interface scrolls back to all unit choices.Note X: Default Custom Unit is deg C or the custom unit will be as per the configuration sent via User software.Custom units are only applicable to 4-20mA inputs.UNIT” screen.Note 6: By pressing key interface scrolls back to “S.UNIT ips” screen.Note 7: By pressing key the digit of a displayed number shall blink and same digit can be incremented by using key. The edited number should be confirmed by key.Note 8: By pressing key the measurement mode shall get selected and shall display” SELECT M.MODE” screen.Note 9: By pressing key interface scrolls back to “MEASMODE RMS” screen.Note 10: By pressing Key the alarm type shall get selected and shall display “SELECT ALARMTYPE” screen.Note 11: By pressing key interface scrolls back to “LATCHING” screen.Note 12: By pressing Key the relay type shall selected and should display “SELECT RLY TYPE” screen.Note 13: By pressing key interface scrolls back to “ENERGIZED” screen.Note 14: By pressing key the configuration shall get updated and screen shall display “UPDATING”.Note 15: Changing unit, value and mode will reset the full scale value, as well as alarm and shut down level.Be sure to double check full scale for desired value before “Update Config”.CONFIGURATION PARAMETERS DEPENDENCYIf the user changes the configuration parameter such as sensor type, sensitivity, measurement unit etc, then some dependable parameters are also required to be changed.Configuration Parameter Dependable ParameterSensor Input Type Sensor SensitivityLoad ResistanceMeasurement UnitsFull Scale RangeTrip LevelsSensor Sensitivity Full Scale RangeTrip LevelsMeasurement Units Full Scale RangeTrip LevelsRMS or Peak Detection Trip levelsDIAGNOSTICDiagnostic tests shall be performed to test the Switch hardware functionality, using inbuilt diagnostic firmware as shown in flowchart below.Note 1: During the signal path check, the switch displays “SIG PATH CHK WAIT” on and internally conducts different self tests. If any no. of tests fails, the display will show the respective error messages in a sequence. These error messages are as follow:• SIG PATH CHK ERR• EEPROM SUM ERR• +24V FAIL ERR• SENSOR OK ERR• RELAY ERR• LED ERR• INT ERRIf there is no error the display shows “SIG PATH CHK OK” message.Note 2: By pressing key the display will turn ON all the pixels of the AlphanumericDisplay for a while as shown.MEASUREMeasure Mode is used to display the measured vibrations as per the configuration.Note: XX.XXX represents measured quantity. AAA represents the measurement unit. BBB represents the measurement type i.e. RMS / PK.************************ 8824 Fallbrook Dr. Houston, TX 77064, USA Tel: 1.281.940.1802 • Fax: 1.713.559.9421After Hours (CST) Technical Assistance: 1.713.452.9703This electronic equipment was manufactured according to high quality stan-dards to ensure safe and reliable operation when used as intended. Due to its nature, this equipment may contain small quantities of substances known to be hazardous to the environment or to human health if released into the environ-ment. For this reason, Waste Electrical and Electronic Equipment (commonly known as WEEE) should never be disposed of in the public waste stream. The “Crossed-Out Waste Bin” label affixed to this product is a reminder to dispose of this product in accordance with local WEEE regulations. If you have questions about the disposal pro-cess, please contact Metrix Customer Service.ENVIRONMENTAL INFORMATION。
metrix 1180 数字接近系统安装手册说明书

数字趋近式系统安装手册1180DPS (数字趋近式系统)家族由两种设备组态,分别是MX2033 和MX2034。
MX2033是一个传统的3线制前置器,MX2034是一个2线制回路供电变送器,带有可选的两线用于缓冲输出原始信号。
用户可以组态变送器去测量峰峰值振动,间隙距离或者转速。
这些产品与趋近式探头和延伸电缆一起用于测量机械轴的振动等级、间隙距离或转速。
用户也可以组态变送器通过USB电缆和组态软件.Doc# 100545 • REV D (May 2020)安全术语及符号出现在本手册中需要特别注意的术语包括:• 警告:警告声明识别可能导致伤害或生命损失的情况或做法。
• 告警:警告声明识别可能导致产品老化、数据丢失或损坏、环境或其他财产损坏的条件或做法• 注释: 注释识别对用户特别感兴趣或重要的材料,不包括警告或告警。
产品和/或本手册中可能出现的符号包括:存在高压危险或 当心安全接地一般安全总结功能接地注释检查以下安全措施,以避免伤害和防止损坏本产品或任何与之连接的产品。
• 仅按规定使用为避免潜在的危险,请仅按规定使用本产品。
只有合格的人员才能执行安装和卸载程序。
• 观察所有端子等级为了避免火灾或触电危险,请观察产品上所有的等级和标记。
在与产品建立联系之前,请参阅本手册的各个章节以获得进一步的评级信息。
• 避免暴露在电路中当有电源时,不要触摸外露的电气连接和元件。
• 不要在可疑故障是操作果你怀疑这个产品有损坏,请有资格的人员检查。
Doc# 100545 • REV D (May 2020) Page 2 of 18接收,检查,及处理系统探头,延长电缆,和变送器是分开来发货的,所以使用者必须在现场连接安装。
仔细拆开所有设备,并且检查所有设备是否有运送损坏。
如果发现运送损坏,向承运人索赔,并且提交一个拷贝给Metrix公司。
包括所有对应的部件号和序列号。
如果没有发现损坏,并且设备不马上投入使用,请把这些设备重新放回到运送箱里密封好,等到使用的时候在拆开。
metrix振动传感器说明书

metrix振动传感器说明书一、产品介绍地震传感器提供以mV/g或mV/in/sec为单位的动态交流信号输出。
具有这种类型输出的设备通常用于连接到独立的振动监测系统,而不是像PLC或DCS这样的通用自动化和控制仪器。
Metrix提供具有多种工作温度、频率响应、比例因子、外壳材料、连接器类型、安装选项和危险区域认证的地震传感器。
符合API 670要求的通用加速度计。
设计用于各种机器类型,具有0.5至10 kHz(+/-3dB)的宽频率响应、50g范围和13 kHz的安装共振。
内置放大器提供符合行业标准的100mV/g低阻抗恒流输出,与振动监测系统、电子开关和4-20mA信号调节器兼容。
二、产品概述由一个温度稳定的压电核心和一个放大器组成,它们一起封装在一个与传感电路电隔离的316不锈钢外壳中。
Metrix SA6350高温加速度计适用于高达325C的温度。
它专为燃气轮机和其他需要加速度*信号的表面温度高的机械而设计。
传感器的设计使用铠装一体式电缆将电荷放大器/线路驱动器与压电传感元件分开。
这使得传感元件可以直接安装在机器上,但电荷放大器可以安装在3m或5m以外的低温环境中。
电荷放大器额定高达120C;它的安装位置通常会使其暴露在适度升高的温度下,但这些温度通常远低于传感元件位置(例如燃气轮机外壳)处遇到的表面温度。
三、产品特点提供5 Hz至10 kHz的频率响应,具有25 kHz的安装谐振,并提供与振动监测系统、电子开关和4-20mA信号调节器兼容的行业标准100 mV/g低阻抗输出。
传感元件可提供3孔或4孔平底安装模式,旨在与其他几种工业标准高温传感器相匹配。
Metrix 5485C高温速度传感器适用于高达375°C的温度。
它专为需要速度信号的具有高表面温度的燃气轮机和其他机械而设计。
Metrix 5485C是大多数GE重型工业燃气轮机的标准设备,包括Frame 3、Frame 5、Frame 6、Frame 7和Frame 9。
Metrix位移探头电缆说明

mx2030探头系列mx2031电缆系列mx2034的420ma的变送器状态监测吨他setpoint系列产品包括基于机架的机械保护平台和在线状态监测软件搭载pi能够提供完整的api670的信息
接近
Metrix公司提供的探头,电缆和驱动程序是可以互换的具有竞争力的探 测系统的阵列。 ProxMatch可以帮助你确定你有正确的探头电缆连接到仪器的连接。
MX2033 3线驱动器 5533探头驱动
振动变送器
Metrix的接近振动变送器与本特利内华达3300系 列,7200和3000探头和电缆,以及我们自己的探头 和电缆兼容。灵活的Metrix的MX2034变送器可以重 新配置,以处理任何这些探针/电缆组合。
MX2034的4-20mA的变送器 TXR 5521 RPM变送器 TXR变送器 TXA变送器
数字感应系统 该Metrix的数字接近系统的可重新配置的数字在现 场几乎所有的探头/电缆和目标物质的组合工作。这 是完全API兼容670,并从各种制造商,包括本特利 内华达支持探头 的DPS由一个探头,延长线和信号 调理。
MX2030探头系列 MX2031电缆系列 MX2033 3线驱动器 MX2034的4-20mA的变送器
电缆
Metrix的电缆可与本特利内华达电缆系列3300, 7200,3000和可带或不带装甲的长度以满足您的系 统要求。
MX2031电缆系列 3000系列电缆 7200系列电缆(58毫米) 7200系列电缆(11毫米) 7200系列电缆(密封馈通)
司机
Metrix的接近司机可与本特利内华达3300系列, 7200和3000探头和电缆。灵活的Metrix的MX2033 驱动程序可以重新配置,以处理任何这些探针/电缆 组合。
Metrix Vibration 5550和5550G机械振动开关数据手册说明书

5550 & 5550G Mechanical Vibration SwitchesDatasheetModel 5550Model 5550G5550 and 5550G mechanical vibration switches provide basic, economi -cal vibration protection by means of a simple and highly reliable “over center” snap action mass and spring mechanism. In the presence of suf -ficient vibration along the switch’s sensitive axis, the switch snaps from a stable “untripped” state to a stable “tripped” state, allowing automatic machinery shutdown or alarming when excessive vibration occurs. Once tripped, the switch must be returned to its untripped state via its local reset plunger (5550 only), or via voltage applied to its remote reset coil (standard on 5550G, optional on 5550). A single set of silver-plated SPDT relay contacts are provided as standard for connecting the switch to a machine control or annunciation circuit. An option for DPDT contacts is also available, and for extremely corrosive environments, gold-plated re -lay contacts may be ordered.SELECTION CRITERIAThe 5550 and 5550G use identical internal mechanisms, but differ in their housing styles, mounting footprints, hazardous area ratings, and externally accessible features. While the housing used with the 5550G permits its use in the more highly explosive IIC gas group, it is not avail -able with a local reset plunger or with an externally accessible setpoint adjustment screw. The 5550G also occupies a larger mounting footprint. For these reasons, the 5550 is generally the preferred choice except in applications where the IIC gas group is present.SETPOINT ADJUSTMENTThe switch’s trip point can be adjusted between 0 and 16 g’s (peak) in increments of approx. 1 g (1/8th turn of setpoint adjustment screw). This adjustment screw is externally accessible on the 5550. On the 5550G, the housing’s cover must be removed to access the adjustment screw.A remote reset/startup delay feature is standard on the 5550G and op -tional on the 5550. When the switch’s reset terminals are energized, a solenoid is activated. This solenoid will reset the switch (if in its tripped state) and then hold it in this untripped state for approximately 30 sec -onds*, after which normal operation of the switch resumes. This feature is useful for machines that exhibit higher-than-normal vibration during startup and need to suppress tripping functions until normal operating speeds and conditions have been reached. The holding strength of this solenoid must be properly specified at time of ordering to ensure it can force the switch into an untripped position and hold it there for the du -ration of the startup delay, even in the presence of high vibration levels (see ordering option C).11801180NOTES:SPDT contacts are standard; DPDT contacts are optional. Reset coil is standard on 5550G, optional on 5550.NOTE: Mechanical vibration switches rely on inertial forces (acceleration) to actuate the trip mechanism. Consideration should be given to the amount of seismic acceleration that will occur under machinery malfunction conditions and whether it will be sufficient to reliably actuate a mechanical switch. For example, the relationship between acceleration, velocity, and displace -ment at low frequencies, very large peak-to-peak displacements (in excess of 100mm) are required to generate the acceleration amplitudes (1g or greater) detectable by a mechanical switch. Care should be taken when measuring vibration frequencies below 10 Hz (600 rpm) to understand the levels of structural displacement, velocity, and acceleration that are generated at the frequency(ies) of interest. These should be compared to maximum allowable vibration levels for the machine or structure to determine whether the setpoint adjustment resolution of a mechanical switch will provide suitable results for the application. A Metrix sales professional can review your application and assist with the selection of the proper instrumentation.* It is not possible to indefinitely prolong the duration of the startup delay by continuously applying voltage to the reset terminals. The duration is set at the factory for approximately 30 seconds and uses a thermistor circuit. Consult the manual for additional details and recommendations for using both the reset and startup delay features.WIRING DIAGRAMSPDTDPDTDPDT CONTACTS AND RESET COIL OPTIONOVERVIEWREMOTE RESET/START UP DELAY 1WIRING DIAGRAM5550 & 5550G Mechanical Vibration SwitchesDatasheetAll specifications are at +25C (+77° F) unless otherwise noted.SPECIFICATIONS5550 & 5550G Mechanical Vibration SwitchesDatasheet1. INMETRO approvals (A=11) available with silver relay contacts only(B=1 or B=2)2. UL US/CA approvals require tapered threads for conduit and arenot compatible with option E=4, E=6, or E=8.3. When options C=2 and D=3 are simultaneously specified (2g, 24Vdcreset coil), the switch sensitive axis (see Figure 1 for 5550 andFigure 2 for 5550G) MUST be oriented vertically with the cover fac-ing up. This coil lacks sufficient holding strength to support the trip plate when the switch is mounted horizontally or upside down. The switch may be mounted at any orientation for all other options.4. Consult Figure 1 for mounting plate dimensions corresponding toE options.5. If left blank, option 0 is provided.6. When D=0 (no reset /startup delay coil), the C option is ignoredregardless of which value is selected. All switches ship with a full-scale range of approximately 16gs.7. Options A=3, A=8, and A=10 were all for Ex d IIB T6 Gb. These arenow replaced by the A=4, and A=11, respectively, which reflect the same approvals but with addition of the H2 gas group.8. Consult Figure 2 for mounting dimensions.5550 & 5550G Mechanical Vibration SwitchesDatasheet Figure 1 – 5550 Mechanical Vibration Switch Figure 2 – 5550G Mechanical Vibration SwitchUnits: mm [in]Aprox. Weight: 1.8 kg (4 lbs)Units: mm [in]Aprox. Weight:2.5 kg (5.5 lbs)5550 OUTLINE & DIMENSIONS5550G OUTLINE & DIMENSIONS。