第三课-气固催化反应器-反应过程温度特征-反应器选型与操作方式讲诉
反应工程第一章
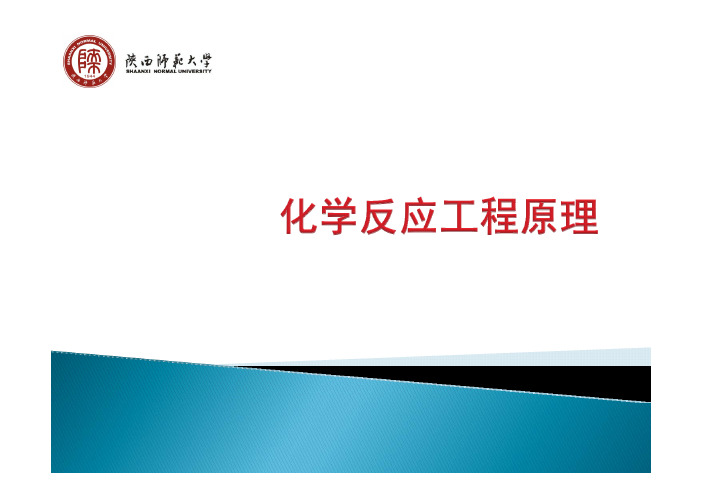
选用教材张濂,许志美,袁向前。
《化学反 应工程原理》。
华东理工大学出版社第一章 第二章 第三章 第四章 第五章 第六章 第七章 第八章 第九章 第十章 第十一章 第十二章绪论 反应动力学 化学反应动力学 反应器 理想间歇反应器 传递现象 理想管式反应器 连续流动釜式反应器 反应过程中的混合现象及其对反应的影响 反应器选型与操作方式 气固催化反应过程的传递现象 反应过程的温度特征和反应器的温度分布 热量传递与反应器的热稳定性 反应动力学的实验测定 反应过程研究实例分析参考书目1. 朱炳宸。
《化学反应工程》(第三版/第四版/第五版, 21世纪教材)。
化学工业出版社,2001/2006/2011 2. 陈甘棠。
《化学反应工程》(第三版,21世纪教材)。
化学工业出版社,2007 3. 李绍芬。
《反应工程》(第二版)化学工业出版社 4. 郭锴。
《化学反应工程》(第二版,21世纪教材)。
化 学工业出版社,2008 5. 程振民,朱开宏,袁渭康。
《高等反应工程教程》,华 东理工大学出版社,2010 6. Levenspiel O,《Chemical Reaction Engineering》,1962。
预备知识高等数学:微积分、代数方程及微分 方程的求解等 物理化学:动力学、热力学 化工原理:流体流动、传递过程课程安排6-18周,每周4节,45学时,2.5学分 授课方式:讲课与讨论相结合 成绩:平时成绩(30%)+ 课程考试(70%)绪论内容大纲01 化学反应工程的发展历史 化学反应工程的研究对象和目的 化学反应工程研究内容 化学反应工程研究方法 化学反应工程在工业反应过程开发中的作用 本章小结0203 04 05061.1 化学反应工程的发展历史萌芽阶段:1937年,丹克莱尔在实验数据十分贫乏的情况 下,较系统地论述了扩散、流体流动和传热对反应器产率 的影响,为化学反应工程的创立奠定了基础。
初步形成:1947年,出版了两本书:《化学过程原理》的第 三卷,专门讲述动力学与催化过程,《化学动力学中的扩散 与传热》; 正式命名:1957年,在荷兰首都举行了第一次欧洲化学反应 工程会议。
反应器型式和操作方式的选择
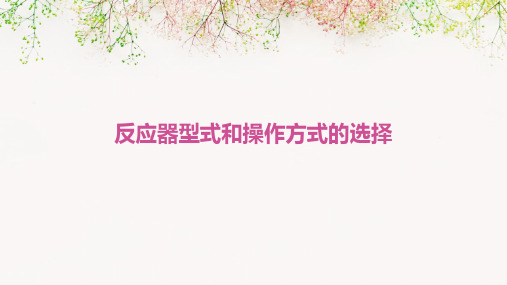
03
各类反应器适用场景及特点
釜式反应器
适用场景
适用于液-液、液-固相反应及反应过 程中有固体生成的场合,如酯化、硝 化、磺化等反应。
特点
结构简单,操作方便,传热面积大, 传热效果好,适用于间歇操作。
反应器分类
根据反应的特点和需求,反应器可分为釜式反应器、管式反应器 、塔式反应器、固定床反应器和流化床反应器等。
Байду номын сангаас
常见反应器型式介绍
釜式反应器
管式反应器
塔式反应器
固定床反应器
流化床反应器
适用于液相或气液相反应 ,具有结构简单、操作方 便、传热效果好等优点。
适用于气固相或气液相连 续反应,具有结构紧凑、 传热效率高、反应时间短 等特点。
适用于气固相或气液相逆 流接触反应,具有处理能 力大、传质效率高、操作 弹性大等优势。
适用于气固相或液固相反 应,具有催化剂不易磨损 、反应温度均匀、易于控 制等优点。
适用于气固相或液固相反 应,具有传热传质效果好 、催化剂活性高、操作灵 活等特点。
选型原则及影响因素
选型原则
在选择反应器型式时,应遵循满足工艺要求、保证产品质量、提高经济效益等 原则。
影响因素
反应器选型受到反应物性质、反应条件、催化剂性质、传热传质要求等多种因 素的影响。因此,在选型时需综合考虑这些因素,选择最适合的反应器型式。
02
操作方式选择依据
连续操作与间歇操作比较
连续操作
物料连续进入和离开反应器,反 应过程中各参数保持恒定,生产 效率高,产品质量稳定。
间歇操作
化学反应工程_第五章__气-固相催化反应工程

(6)径向位置:中心处ε↓,近壁处ε↑。
7、固定床的空隙率及径向流速分布
◆壁效应
器壁对空隙率的影响以及由此造成的对“三传、一 反”的影响,称为壁效应。 dt/dp ↓,壁效应↑,于是在反 应器设计时为了减小壁效应,应使dt/dp>8。 ◆流速分布:流速分布图见图5-14。
二、单相流体在固定床中的流动及压力降
原料气冷激
非原料气冷激
单段绝热式
x
平衡温度线
最佳温度线
T
多段固定床绝热反应器 产 品 原 料 (a)间接换热式 Ⅰ Ⅱ Ⅲ x
平衡温度线
最佳温度线
Ⅳ
T
多段固定床绝热反应器 产 品 原 料 (b)原料气冷激式
Ⅰ x Ⅱ
平衡温度线
Ⅲ
Ⅳ
最佳温度线
T
多段固定床绝热反应器 原 料 Ⅰ Ⅱ x
平衡温度线
VS s B 床层空隙体积 VB VS 1 1 1 W 整个床层体积 VB VB S W
B
7、固定床的空隙率及径向流速分布 ◆影响ε的因素
(1)颗粒形状:φs↑ε↓; (2)粒度分布:分布宽, ε↓
(3)表面粗糙度:粗糙度↑ε↑;
(4)填充方式:紧填充, ε↓ (5)dp / dt : dp / dt ↑ε↑;
列管式反应器优点:
① 传热较好,管内温度较易控制; ② 返混小、选择性较高; ③ 只要增加管数,便可有把握地进行放大; ④ 对于极强的放热反应,还可用同样粒度的惰性物料 来稀释催化剂。 适用于原料成本高,副产物价值低以及分离不是十分 容易的情况。
三套管并流式冷管催化床温度分布及操作状况
拟均相模型:化学动力学控制,不考虑颗粒内部
气固相催化反应的七个步骤

气固相催化反应的七个步骤一、反应物准备在进行气固相催化反应之前,首先需要准备好反应物。
反应物可以是气体和固体之间的反应,也可以是气体与固体催化剂之间的反应。
无论是哪种情况,反应物的准备都是必不可少的。
通常情况下,反应物会经过一系列的处理步骤,以确保其纯度和活性。
二、反应器选择选择合适的反应器对于气固相催化反应来说非常重要。
反应器的选择应该考虑到反应物的性质、反应条件、反应速率等因素。
常见的反应器包括管式反应器、固定床反应器、流化床反应器等。
不同的反应器有不同的优缺点,需要根据具体情况进行选择。
三、催化剂的选择催化剂是气固相催化反应中起关键作用的物质。
催化剂可以提高反应的速率和选择性,降低反应的温度和能量消耗。
选择合适的催化剂对于反应的成功进行非常重要。
催化剂的选择应考虑到反应物的性质、反应条件、催化剂的活性和稳定性等因素。
四、反应条件控制反应条件的控制对于气固相催化反应来说至关重要。
反应条件包括温度、压力、气体流速等。
不同的反应对于反应条件有不同的要求。
在确定反应条件时,需要考虑到催化剂的活性、反应物的稳定性和选择性等因素。
五、反应过程监控在进行气固相催化反应时,需要对反应过程进行监控。
监控反应过程可以了解反应的进行情况,及时调整反应条件,以达到预期的反应效果。
常用的监测手段包括温度、压力、气体流速等参数的监测,以及反应物和产物的分析等。
六、反应产物分离在气固相催化反应完成后,需要进行反应产物的分离。
反应产物的分离可以通过不同的物理和化学方法实现,如蒸馏、吸附、结晶等。
分离产物的纯度和收率对于反应的成功与否有着重要的影响。
七、反应废物处理气固相催化反应过程中会产生一些废物,这些废物可能对环境和人体健康造成潜在的危害。
因此,在进行气固相催化反应时,需要合理处理反应废物,以减少对环境的污染。
常见的处理方法包括回收利用和安全处置等。
通过以上七个步骤,可以完成气固相催化反应的整个过程。
每个步骤都有其重要性和特殊性,需要仔细考虑和操作。
化学反应工程第三章

5
• 对于平推流反应器,在恒温下进行,其 n 设计式为: x 1 x 1
P
n 1 kcA0 A A dxA * 0 1 xA
A
• 对于全混流反应器,在恒温下进行,其 n 设计式为: xA 1 A xA m n 1 • kcA0 1 xA • 二式相除,当初始条件和反应温度相同 n 时: 1 A xA
12
• 对任意第i釜中关键组分A作物料衡算。 • 对恒容、定常态流动系统,V0不变, V • V ,故有:
Ri 0 i
cA 0 xAi xAi 1 cAi 1 cAi i rA i rA i
• 对于N釜串联操作的系统,总空间时间:
1 2 N
0 VR FA
A2
xA 1
rA
• 式中,F’A0是一个虚拟的值,它由两部分 组成,新鲜进料FA0和循环回来的物流V3 中当转化率为0时应当具有的A的摩尔流 率。即: 0 V1cA 0 V0 V3 cA 0 FA
26
• 由此得到循环反应器体积:
dxA VR 1 FA 0 xA 2 r 1 A
35
36
反应器组合
• 为了使得反应器组的总体积最小,设计 这样一组反应器,在这组反应器中,反 应大部分控制在最高速率点或接近最高 速率点处进行。为此,可使用一个全混 釜式反应器,它可以不必经过较低反应 速率的中间组成,而直接控制在最高速 率组成下操作。然后再由平推流反应器 完成最终反应
cA 0 cP 0 cA cP c0
cP cA 0 cP 0 cA
30
• A组分的消耗速率为:
化学反应工程复习+公式指导

化学反应工程复习总结一、知识点1.化学反应工程的研究对象与目的,研究内容。
化学反应工程的优化的技术指标。
2.化学反应动力学转化率、收率与选择性的概念。
反应速率的温度效应和活化能的意义。
反应速率的浓度效应和级数的意义。
3.理想反应器与典型反应特征理想反应器的含义。
等温间歇反应器的基本方程。
简单不可逆反应和自催化反应的特征和计算方法。
可逆反应、平行反应和串联反应的动力学特征和计算方法。
4.理想管式反应器管式平推流反应器的基本方程典型反应的计算。
停留时间、空时和空速的概念。
膨胀因子和膨胀率的概念。
5.连续流动釜式反应器全混流模型的意义。
全混流反应器的基本方程全混流反应器的计算。
循环反应器的特征与计算方法。
返混的概念、起因、返混造成的后果。
返混对各种典型反应的利弊及限制返混的措施。
6.停留时间分布与非理想流动停留时间分布的意义,停留时间分布的测定方法。
活塞流和全混流停留时间分布表达式,固相反应的计算方法。
多釜串联模型的基本思想,模型参数微观混合对反应结果的影响。
7.反应器选型与操作方式简单反应、自催化和可逆反应的浓度效应特征与优化。
平行反应、串联反应的浓度效应特征与优化。
反应器的操作方式、加料方式。
8.气固催化反应中的传递现象催化剂外部传递过程分析,极限反应速率与极限传递速率。
Da和外部效率因子的定义及相互关系。
流速对外部传递过程的影响。
催化剂内部传递过程分析,Φ和内部效率因子的定义及相互关系。
扩散对表观反应级数及表观活化能的影响。
一级反应内外效率因子的计算。
内外传递阻力的消除方法。
9.热量传递与反应器热稳定性定态、热稳定性、临界着火温度、临界熄火温度的概念。
催化剂颗粒热稳定性条件和多态特性。
全混流反应器、管式固定床反应器热稳定条件。
最大允许温差。
绝热式反应器中可逆放热反应的最优温度分布。
二、具体内容解析 一、 绪论 1.研究对象是工业反应过程或工业反应器研究目的是实现工业反应过程的优化 2. 决策变量:反应器结构、操作方式、工艺条件 3.优化指标——技术指标:反应速率、选择性、能耗 掌握转化率、收率与选择性的概念 4.工程思维方法二、化学反应动力学1. 反应类型:简单反应、自催化、可逆、平行、串联反应基本特征、分析判断2. 化学反应速率的工程表示))((反应区反应时间反应量反应速率=3. 工业反应动力学规律可表示为:)()(T f C f r T i C i ⋅=a) 浓度效应——n 工程意义是:反应速率对浓度变化的敏感程度。
化工反应器分类、特征、应用及放大方法

化工反应过程的放大方法:
1、逐级经验放大法 2、数学模拟法 3、部分解析法 4、相似放大法
第一种 逐级经验放大法
定义: 运用物质模型从实验室规模的小试开始,经过逐 级放大的模型试验研究,直到将化工过程放大成为生产规 模。
依据:以前一级试验所取得的研究结果和数据为依据。
特点:比较原始,不够精确,不够经济,但有一定的价值
特点:用一组微分方程或一组代数方程,描述过
程的动态规律。是目前比较先进、科学的方法。
要求:即能描述过程,又简单便于应用。
一、数学模型 建立数学模型的思维方法
如反应器模型的基础: 热力学方程、反应动力学方程、三大传 递 物料衡算式、热量衡算式、动量衡算式 数学模型的简化 非理想流动模型—— 轴向分散模型、多釜 串联模型
考察设备内物料的流动与混合,传热和传质等物理过
程的规律。 反应器内各种物理过程的规律,只随反应器的型式或 结构的改变而改变,反应的类型不会改变传递规律。
综合化学反应特征和传递过程特征,建立函
数关系式,形成数学模型,预测工业反应器 性能。
只要反应器的型式结构和化学反应相同, 由数学模型表示的过程动态规律应不受设备 几何尺寸的限制,因此用数学模型进行工业 反应器的设计,应不存在放大效应。
数学模型的针对性
每一种数学模型都有一定的限制范围 。
例:管式反应器内物料的返混可以用扩散
模型描述,但扩散模型不能描述物料在管 式反应器的层流或湍流状态。
二、研究方法 以化学反应过程开发为例,按以下步骤 进行:
测定反应热力学和动力学的特征规律及其参数。
化学反应工程常见简答题

3.简述气固相催化反应的宏观动力学步骤?答:整个多相催化反应过程可概括为7个步骤:1、反应组分从流体主体向固体催化剂外表面传递;2、反应组分从外表面向催化剂内表面传递;3、反应产物从催化剂内表面向外表面传递;4、反应产物从催化剂的外表面向流体主体传递。
5.实验室中欲测取某气固相催化反应动力学,该动力学方程包括本征动力学和宏观动力学方程,试问如何进行?1消除内扩散和外扩散2测定本征动力学3在无梯度反应器内消除影响后测量6.本征化学反应速度在内外扩散阻力完全消除的情况下与宏观化学反应速度有何关系?答:相等。
第三章1.CSTR串联为何好于单个大体积的CSTR?是否工业上都用多个CSTR串联来代替单个CSTR?多釜串联是否串联级数越多越好?答:1.减少返混2.反应级数>0,多釡代替单釜;反应级数<0,则用单釜。
3.不是,要从成本和控制上来最终决定。
第四章1,理想流动模型有哪两种类型?其基本假定和特点各是怎样的?答:.平推流流动模型和全混流流动模型。
(1)平推流模型是一种假定返混量为零的极限流动模型。
特点:在定态情况下,沿物料流动方向,物料的浓度、温度、压力、流速等参数会发生变化,而垂直于流体流动方向任一截面上物料的所有参数都相同。
所有物料质点在反应器中都具有相同的停留时间。
(2)全混流模型假定反应器内物料质点返混程度为无穷大。
特点:所有空间位置物料的各种参数完全均匀一致,而且出口处物料性质与反应器内完全相同。
第五章请分析影响固定床层压力降的因素。
答:影响床层压力降的因素可分为二类:一类来自流体,如流体的粘度、密度等物理性质和流体的重量流速;另一类来自床层,如床层的高度、空隙率和颗粒的物理特性如粒度、形状、表面粗糙度等。
流体的重量流速对床层压降的影响较大,所以在设计和操作时都应该注意流速的改变会引起压降有多大的变化。
对于一定的催化剂体积,应尽可能降低床层高度,加大床层直径,即采用小的高径比结构,有利于降低床层的压力降。
化学反应工程第八章 气液固三相反应及反应器ppt资料
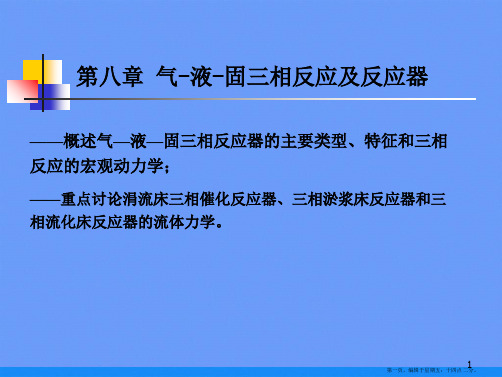
床层宏观反应动力学
15
第十五页,编辑于星期五:十四点 二分。
涓流床三相反应器
1、气、液并流向下通过固定床的流 体力学 (1)气,液稳定流动区——当气速较低 时,液体在颗粒表面形成滞流液膜, 气相为连续相, “涓流状”。气速增 加称为“喷射流”;
(2)过渡流动区——继续提高气体流速,床 层上部是喷射流,下部出现脉冲现象。
缺点——大型涓流床反应器低液速操作的液流径向分布不均匀, 局部过热,催化剂迅速失活。催化剂颗粒不能太小,而大颗粒催 化剂存在明显的内扩散影响;轴向温升,可能飞温。
6
第六页,编辑于星期五:十四点 二分。
悬浮床气—液—固反应器
①机械搅拌悬浮式; ②淤浆床鼓泡反应器,以气体鼓泡搅拌; ③不带搅拌的气、液两相流体并流向上,而颗粒不带出床外 的三相流化床反应器; ④三相携带床反应器,不带搅拌的气、液两相流体并流向上, 而颗粒随液体带出床外的三相输送床反应器;
(3)二个反应相,第三个是惰性相:液相为惰性相的气—固催化 反应,液相作为传热介质,如一氧化碳催化加氢生成烃类、醇类、 醛类、酮类和酸类的混合物;气体为惰性相的液—固反应,气体 起搅拌作用,例如硫酸分解硫铁矿槽式反应釜内用空气搅拌。
2
第二页,编辑于星期五:十四点 二分。
第三页,编辑于星期五:十四点 二分。
安静鼓泡区、湍流鼓泡区、栓塞流区。 上述流区间的过渡条件与液体特性、气体分布器的设计、 颗粒特性及床层尺寸等因素有关。
例如,对于高粘性的流体在很低的表观气速下可形成栓塞流。气
体分布器如采用微孔平均直径低于150um的素烧陶瓷板,当表 观气速达0.05一0.08m/s时,仍为安静鼓泡区,当多孔板孔径超 过1mm时,气泡分散区仅存在于很低的表观气速。
气-固相催化反应动力学课件.doc
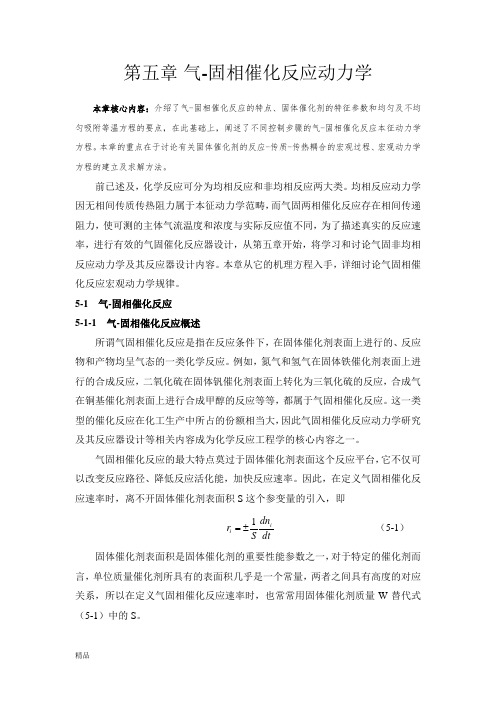
第五章 气-固相催化反应动力学本章核心内容:介绍了气-固相催化反应的特点、固体催化剂的特征参数和均匀及不均匀吸附等温方程的要点,在此基础上,阐述了不同控制步骤的气-固相催化反应本征动力学方程。
本章的重点在于讨论有关固体催化剂的反应-传质-传热耦合的宏观过程、宏观动力学方程的建立及求解方法。
前已述及,化学反应可分为均相反应和非均相反应两大类。
均相反应动力学因无相间传质传热阻力属于本征动力学范畴,而气固两相催化反应存在相间传递阻力,使可测的主体气流温度和浓度与实际反应值不同,为了描述真实的反应速率,进行有效的气固催化反应器设计,从第五章开始,将学习和讨论气固非均相反应动力学及其反应器设计内容。
本章从它的机理方程入手,详细讨论气固相催化反应宏观动力学规律。
5-1 气-固相催化反应 5-1-1 气-固相催化反应概述所谓气固相催化反应是指在反应条件下,在固体催化剂表面上进行的、反应物和产物均呈气态的一类化学反应。
例如,氮气和氢气在固体铁催化剂表面上进行的合成反应,二氧化硫在固体钒催化剂表面上转化为三氧化硫的反应,合成气在铜基催化剂表面上进行合成甲醇的反应等等,都属于气固相催化反应。
这一类型的催化反应在化工生产中所占的份额相当大,因此气固相催化反应动力学研究及其反应器设计等相关内容成为化学反应工程学的核心内容之一。
气固相催化反应的最大特点莫过于固体催化剂表面这个反应平台,它不仅可以改变反应路径、降低反应活化能,加快反应速率。
因此,在定义气固相催化反应速率时,离不开固体催化剂表面积S 这个参变量的引入,即dtdn S r ii 1±= (5-1) 固体催化剂表面积是固体催化剂的重要性能参数之一,对于特定的催化剂而言,单位质量催化剂所具有的表面积几乎是一个常量,两者之间具有高度的对应关系,所以在定义气固相催化反应速率时,也常常用固体催化剂质量W 替代式(5-1)中的S 。
气-固相催化反应动力学研究的目的就是要建立气固相催化反应动力学方程,为气固相催化反应器的开发设计、选型、优化操作与控制提供理论依据。
第三课-气固催化反应器-反应过程温度特征-反应器选型与操作方式讲诉

如果管径不是那么小,反应热也比较大,径向温 度往往可观,需考虑径向与轴向二维。
取一环形微元体积,对反应组分A作物料衡算
l面进入量+ r面进入量- l l面出去量- r r面出去量
=环体内反应掉的量
非等温衡算
r
类似可写出热量衡算式
l
上述基础方程组是对单一反应而言, 如果不止一个反应,不止一个反应组分,那 就需要对每一反应组分都分别列出。
(H )kCAf V UTmax
vCp U
最大允许温差决定了全混釜反应器的冷却介质温度条
件和控制要求。最小传热面积则决定了全混釜反应器
中传热面积的设置要求。
如果全混釜反应器中进 行某串连反应,要求控制在 中等转化率,则很可能处在B 点操作。此时为了满足热稳 定条件,必需提高冷却介质
温度Tc,并相应地增大UA,
全混釜的热平衡ห้องสมุดไป่ตู้件
以一级不可逆均相放热反应A→P为 例。
对组分A作物料衡算
vC A0 vC Af VR kCAf
C Af
CA0 1 k
反应过程的放热速率
Qg
(H )kCAfVR
(H
)k0CAf
VR
exp(
E RT
)
1
k0
exp(
E RT
)
由于反应速率常数与温度呈指数函
的逆流模型
三相模型
气汽相、汽晕相、固相三相均为平推流
四相模型
气汽相、汽晕相、上流相、下流相均为平推流
固定床的拟均相一维模型
等温平推流
仅需物料平衡式
FA0dxA (rA )dW
等温有轴向返混 c* De 2c*
(5)气固催化反应宏观动力学精品PPT课件

外扩散过程特征:
反应物A由气相主体扩散到催化剂颗粒的外表面;
在催化剂颗粒外表面上进行化学反应。
在定态操作中传质过程和化学反应过程的 速率不论在何种情况下必定相等,且等于整个过 程的表观速率R,即 kga(CbCes)kC ens 对一级反应 C es 1
Cb 1 k kga
在气固催化反应中,外扩散过程对化学反应的 影响,是由传质过程引起的反应表面与气流主 体间的浓度差异造成的;
效率因子法与表观动力学法的对比
基本共同点都是力图将反应速率和选择率表达成以实际
测量的气流主体温度Tb和cb气流主体浓度的函数,可以
统称为非均相反应的拟均相化。 。
根本区别:
效率因子法
以反应的本征动力学作为基础,它
的反应级数n和活化能E均为本征动力
学参数,而将传递过程的影响都归纳 在一个效率因子之中以作修正。因而 效率因子的大小清楚地显示传递过程 对反应结果影响的大小。
粒内的实际反应速率应取整个颗粒速率的平均值,
即
R
VP 0
kCinsdVP
所以
2
Vp 0
k cins dVp
k cbnVp
球形颗粒的内部效率因子
不同形状催化剂内部效率因子
2 与 L 的关系
,2 ,2
不同形状催化剂的曲线几乎是重合的。
L 0.4,2 1 认为内扩散影响可忽略
L
3,2
Cb
Da称为达姆克勒(Damkohler)准数,其物理意
义是极限反应速率与极限传质速率之比。
非均相的气固催化反应可采用易于反应工 程分析的效率因子法处理
RkC ens1kC bn
1 称为催化剂颗粒的外部效率因子
1
第五章气固相催化反应器课件

单管逆流式催化床及温度分布示意图
图中Tb催化剂层的轴向温度,Ta为内外冷管环隙内(或单冷管 管内)的气体温度,Ti为内冷管内的气体温度。
以是催化剂,也可以是固体反应物。或者
说凡是流体通过不动的固体物料所形成的
床层而进行反应的装置都称作固定床反应
器。
固定床催化反应器
单段绝热式 绝热式
多段绝热式
连续换热式 外热式 自热式
优缺点: • ①床层内流体流动接近平推流。(返混、催化剂少
和较小的反应器容积来获得较大的生产能力) • ②严格控制停留时间,温度分布可以适当调节,因
此特别有利于达到高的选择性和转化率。 • ③结构简单,操作方便,催化剂磨损小。 • ④传热较差。 • ⑤压力降大,因此压力降受限制。 • ⑥催化剂的更换必须停产进行。
间接换热式
多段绝热式固定床
原料气冷激式
冷激式
惰性气体冷激式
(a)间接换热式;(b)原料气冷激式;(c)非原料气冷激式
连续换热式固定床
双套管并流式催化床及温度分布示意图
图中Tb催化剂层的轴向温度,Ta为内外冷管环隙内(或单冷管 管内)的气体温度,Ti为内冷管内的气体温度。
三套管并流式催化床及温度分布示意图
图中Tb催化剂层的轴向温度,Ta为内外冷管环隙内(或单冷管 管内)的气体温度,Ti为内冷管内的气体温度。
二、反应器设计原则
xndn
xn dn
3、床层的空隙率、当量直径
反应器型式和操作方式对平行反应选择性的影响
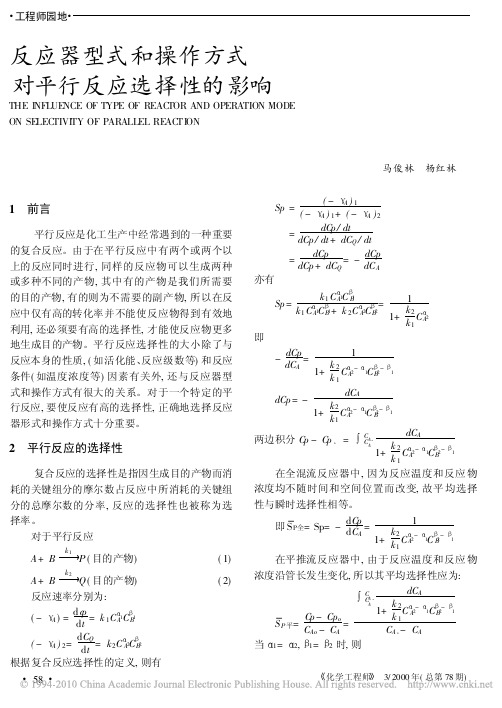
液相平行反应
A+ B k1 P( 目的产物)
k2
A+ B S 反应物 初始 浓度 CA。= CB。= 10mol/ L, k1 # k 2。求 A 的转化率为 80% 时, 目的产物 P 的选择 性。
4!2!1 当 1> 2, 1> 2 时, 设动力学方程分别为
r1=
-
d Cp dt
=
k1 CAC2Bmol/ ( L
不同型式的反应器其传递特征有较大的差异必然引起反应物浓度上的不同采用不同的操作方式也可以调整各反应组分浓度的高低及其变化以利于提高反应的选择性若要求cacb均维持在较高的水平可以选择间歇釜式反应器或平推流反应器组分同时加入或者采用多釜串联的全混流反应k1k2k2ca平行反应选择性的影响因素分析温度和反应物浓度是影响平行反应选择性的化学工程师如果要求cacb均维持在较低水平时可以选择组分一次加入沿管长分段加入平推流反应器或选用分级加入多釜串联反应器且维持在较低的转化率下进行并从最末一釜的出口物料中分离出么样的操作方式除依据以上分析外还应当考虑反应物反应物初始浓度的高低对最终转化率的要求以及控制调节等方面的要求412反应器型式和操作方式对选择性量比较以下面的例子作定量讨论液相平行反应则平均选择率为015cb016667sp平sp全选用平推流反应器比全混流反应器选择率提高25163学方程为dcp115molminr1dtdcsminr2caca015015cacb011624k2的转化率为80提高选择性可以减小反应物初始浓度mollmin115mollmin此时sp全08333sp平015k2cb设动力学方程为k1k2015dcminr2015015casp平cb60生产操作条件及对产品性原对照降塔内塔盘前后产品的质量及收率的变化情况列
气固相催化反应器ppt课件

1
令n
RT
;K
A
ka kd
n
1
KA pAn
称弗鲁德里希吸附等温式
焦姆金(Т Е М К И Н )吸附模型
ТЕМКИН模型认为吸附及脱附活化能与表面覆盖率呈线 性关系。即:
Ea Ed
Ea0 Ed0
针对不同具体情况,三个过程进行的速率各不 相同,其中进行最慢的称为控制步骤,控制步骤进 行的速率决定了整个宏观反应的速率。
5.2 气固非均相催化反应本征动力学
• 本征:完全没有扩散影响的,单纯的反应物及 产物在催化剂表面吸附脱附反应过程。其动力 学表达为本征动力学。
物理吸附和化学吸附 •物理吸附-吸附剂与被吸附物靠范德华力结合 •化学吸附-吸附剂与被吸附物之间可视为发生化学 反应
k( pA pB pR / KP ) (1 K A p A K B pB K R pR )2
kaA pAV kdA A
A K A p AV
kaB pBV kdBB
B K B pBV
表面反应 A B R
脱附
R R
kaR pRV kdRR
R K R pRV
V 1 A B R
式中
K A kaA kdA K B kaB kdB
k( pA pB pR / KP )
(1 K A p A K B pB K R pR )2 (1 K A p A K B pB K R pR )2
正反应速率
常数
k ks KAKB
反应化学
KP ks K AKB ( ks KR ) 平衡常数
第四章 气固催化及其反应器

当微孔直径远大于气体分子运动的平均自由程时,
气体分子相互碰撞的机会比与孔壁碰撞的机会多,这种
扩散称为容积扩散。
当微孔直径小于气体分子的平均自由程时,气体 分子与微孔壁碰撞的机会,比与其它分子碰撞的机会 多,这种扩散称为诺森扩散。
颗粒内表面上的催化反应速率取决于反应组分A
的浓度。在微孔口浓度较大,反应速率较快;在微孔 底浓度最小,反应速率也最小。在等温情况下,整个 催化剂颗粒内单位时间的实际反应量N1为:
第四章 气固催化反应及其反应器
气固相催化反应器
气固相催化反应是非均相反应。实际反应速率与 相接口的大小及相间扩散速率有关。 气固相催化反应过程是化工生产中最常见的非均 相反应过程,例如基本化工原料工业中的硫酸、硝酸 、合成氨、甲醇和尿素等的生产。
1.气固相催化反应过程
(1)气固相催化反应过程分析 七个步骤:
Kv—催化剂反应速度常数, s-1 De—内扩散系数m2· s-1
催化剂颗粒半径R越大,内孔越小,扩散系数De
越小,φ越大,而η越小,表明选用小颗粒、大孔径的
催化剂有利于提高内扩散速率;催化剂体积反应速率
常数kV越大,η越小,说明反应速率太大,内扩散对
整个过程的阻滞作用越严重。
(4)气固催化反应宏观动力学模型 气固催化反应各过程的速度必定相等,宏观反应速
令N1/N2=η,η称为催化剂颗粒的内扩散效率因子,则
k f ( c ) dS S A , S i 0 k S Si f (c A,S )
内扩散效率因子实际上是受内扩散影响的反应 速率与不受内扩散影响的反应速率之比。若内表面
S
利用率的值接近或等于1,反应过程为动力学控制;
若远小于1,则为内扩散控制。工业催化剂颗粒的
- 1、下载文档前请自行甄别文档内容的完整性,平台不提供额外的编辑、内容补充、找答案等附加服务。
- 2、"仅部分预览"的文档,不可在线预览部分如存在完整性等问题,可反馈申请退款(可完整预览的文档不适用该条件!)。
- 3、如文档侵犯您的权益,请联系客服反馈,我们会尽快为您处理(人工客服工作时间:9:00-18:30)。
数关系,放热速率Qg随反应温度的
变化呈S形曲线。
全混釜中的 Q~T关系
反应器的移热速率为通过器壁传热量与反应物流体 热焓变化带走的热量之和
Qr UA(T Tc ) vCp(T T0 )
如果略去反应过程中反应混合物密度、粘度、比热等物 性参数随温度的变化,同时为简化讨论,设 T0 Tc ,则
Qr (UA vCp)(T Tc )
反应器设计的任务正是要确定UA和Tc,也即要确定移热速
率线的位置。
在曲线Qg和直线Qr的交点处,Qg=Qr,此时反应器的
放热速率和移热速率相等,达到了热平衡要求,因此交 点就是反应系统的定态操作点。
全混釜反应器的热稳定性
在同样操作条件下,反应器内可能出现三种不同的操
参数灵敏性
所谓参数灵敏性指的是各有关参数如流量、进口温度 和冷却介质温度等作微小调整时,反应器内温度或反 应结果将会有多大变化? 如果反应器的参数灵敏性过高,那末对参数的调整就 会有过高的精度要求,使反应器的操作变得十分困难。 因此,在反应器的设计中,确定设备尺寸和工艺条件 时必需设法避免过高的参数灵敏性。
可逆放热反应的放热曲线
吸热反应的定态点
吸热反应的一个特点是定态为唯 一的,不存在多态。
操作参数对热稳定性的影响
•进料温度对全混釜反应
•加料流率对全混釜反应
器热稳定性的影响
器热稳定性影响
•当全混釜反应器中冷却介质温度TC降低,传热面积A 及传热系数U增大,都会增大移热速率,但超过一定的
限度,将使全混釜反应器处于低温稳定状态。
进行绝热反应,一次称为一段,如催化重整 多段绝热式反应器,按段间换热方式的不同又可分为气冷凝式 非原料气冷凝式 喷水、降温、分压
换热式反应器
比绝热式应用更多,更普遍。
特点是催化剂床在进行化学反应的同时,还与外界进 行热量交换,尤以列管式为多。通常在管内放催化剂, 管间走热载体 (若用高压水时,管内走高压流体)。 管径大小一般为25~50mm,根据反应热和允许温度 而定;催化剂粒径<1/8管径,一般为2~6mm。 热载体视所需控制的温度分为而异:
固定床反应器的基础数学模型
根据反应动力学可分为拟均相和非均相两类:
拟均相--把固体催化剂与流体当作一均相体系来考虑。 若为化学动力学控制,催化剂颗粒表面与内部的反应组分 浓度及温度都与气体主流一致。
非均相--同时考虑气体主流与颗粒外表面以及颗粒内表 面的浓度梯度和温度梯度。
根据温度和浓度分布状态又可分为一维模型和二维模型:
的逆流模型
三相模型
气汽相、汽晕相、固相三相均为平推流
四相模型
气汽相、汽晕相、上流相、下流相均为平推流
固定床的拟均相一维模型
等温平推流
仅需物料平衡式
FA0dxA (rA )dW
等温有轴向返混 c* De 2c*
W xA dxA
FA0 0 rA c*
( ) 0
L Z Z
高压水 100~300℃ 联苯,石油中烷基萘为200~350℃ 无机溶盐 300~400℃ 烟道气 600~700℃ 熔融金属 密封性要求高
热载体强制循环。列管式的传热较好,管内温 度较易控制,放大把握大,反应速度快。又分 为:
外热式 热载体
自热式 原料气
绝热式、换热式反应器结合使用,如合成氨, 先初期采用绝热式,迅速升温,rA↑,然后采 用换热式。
热稳定性
反应器是在某一平衡状态下设计并进行操作的,那么就传 热而言,这个反应器就是处于热平衡状态,即反应的放热 速率=移热的速率。只要这个平衡不被破坏,反应器内各 处温度将不随时间而变化,处于定常状态。
如果某个短暂的扰动使反应器内的温度产生了一个微小的 变化,例如有一个微小的上升,那么当扰动消失之后,原 来处于平衡状态下的反应器会发生怎样的变化呢?当然, 其变化不外乎两种情况:一是反应温度会自动返回原来的 平衡状态,此时称该反应器是热稳定的,或是有自衡能力 的;另一是该温度将继续上升直到另一个平衡状态为止, 则称该反应器是不稳定的,或为无自衡能力的。
绝热式反应器 换热式反应器
固定床反应器的代表:
催化重整 加氢精制 异构化 裂解
固定床反应器的优缺点
床层内流体流动接近 PFR,返混小,所以 rA↑,xA↑,较小容 积,较大生产能力;
催化剂不易磨损而可 长期使用;
易控制,如停留时间 可严格控制,温度分 布调节。
传热较差,催化剂属 导热不良物质,反应 结果对温度的依赖性 又很强,所以对于热 效应大的反应过程, 传热和控温是技术难 点和关键所在;
非均相要分别列出流体、粒子的物料衡算及热量衡算式,不少 学者做过许多研究后认为,在固定床反应器中,粒内、外各步 传递过程的重要性顺序为:
传热:层内>流体粒子内>粒内
传质:粒内>层内>流体-粒子内
在工业装置中,由于实用的流速往往足够高,所以流体与粒子 间的温差和浓度差,除少数快速强放热反应外,都可忽略,因 此重要的是处理层中的传热。另一方面,催化剂粒子内部的内 扩散过程是传质方面的主要因素,因此,只要把催化剂的效率 因子和床层的有效导热系数这两点解决,那么固定床反应器的 设计和放大就可采用拟均相模型而不致有太大的差错。而采用 非均相模型,计算量要大大增加,一般计算机还会承受不了, 其结果却又与拟均相模型的结果很接近,因此,除少数特殊情 况外,一般以用拟均相一维和二维模型最为合适。
最大允许温差
最大允许温差是热稳定性对全混釜反应器设计和操作
中的一个限制。将Qr对T求导,Qg对T求导,并代入
式 dQg dQr ,得全混釜的最大允许温差
dT dT
Tmax
(T
Tc )max
RT 2 E
C A0 C Af
反应器所需具有的最小传热面积为
Amin
Qg UTmax
vCp U
单段绝热式
还需热量衡算式
FCPdT (HrA )FA0dxA
绝热方程,即绝热操作时温度与转化率的关系
T2
T1
(H rA W
)(
FA0 FCP
)(xA1
dx xA2
A
xA2 )
FA
r xA1
A
与物料衡算式联立求解,即得床内轴向温度和转化率
变化情况。
固定床的拟均相二维模型
反应器的热稳定性和参数灵敏性
化学反应器内的传热问题与一般的加热、冷却或换热 过程中的传热问题有一个重要的区别,就是反应器内 的反应过程和传热过程之间相互交联作用。
对于放热反应过程,可能出现如下的恶性循环:
反应温度上升
反应加快
反应放热速率增大
当然,这种恶性循环是吸热反应所没有的,也是一般 换热过程中所不存在的一类特殊现象。这种现象的存 在对传热和反应器的操作、控制都提出了特殊的要求。
使移热线如图中Q’r线所示。
因此用于进行强放热反 应的反应器,其冷却介质必 须保持在较高温度。
全混釜的参数灵敏性
对全混釜反应器而言,在给定的工艺条件下,主要的
调节参数是冷却介质温度。因此考察反应温度T以及反 应结果对于冷却介质温度TC的灵敏性很有必要。
对于D点,如果对TC作微小的
下行调节,此时移热线将向
固体催化剂可往来输送,适 于催化剂迅速失活而需随时 再生的过程,如FCC,解决 大规模连续生产的关键;
可采用细粒子,使得内扩散 阻力↓,内表面利用率↑。
粒子运动接近全混流, 停留时间不一,使得 rA↓,xA↓,副反应↑; 气流状态不均,气固接 触不够有效,对高xA不 利;
催化剂易磨损,要有旋 风分离系统。
左平移,交放热线于D " 点, 即到了下操作点,相应的温 度为 TD" 。此时温度将发生剧 烈下降,反应结果也从高转
化率变为低转化率。此类现
象称为“熄火”,显示出很
强的灵敏性。
全混釜的“熄火”与 “飞温”
同理,在D点操作时,如果传热系数稍有增大,例如 搅拌强度或冷却介质流速增大,移热线斜率就增大,同 样会使操作点急剧移至下操作点而表现出极大的灵敏性。
如果管径不是那么小,反应热也比较大,径向温 度往往可观,需考虑径向与轴向二维。
取一环形微元体积,对反应组分A作物料衡算
l面进入量+ r面进入量- l l面出去量- r r面出去量
=环体内反应掉的量
非等温衡算
r
类似可写出热量衡算式
l
上述基础方程组是对单一反应而言, 如果不止一个反应,不止一个反应组分,那 就需要对每一反应组分都分别列出。
作温度TA、TB和TC,这就是反应器的多态现象,在数学 上称为多解。实际出现哪一个操作温度将取决于它的
起始状态。
反应系统的多态操作点,都满足Qg=Qr的热平衡条件,
但却具有不同的特性。A和C点具有热自衡能力,为稳
定的定态操作点; B点不具有热自衡能力,为不稳定
的定态操作点。
全混釜的热稳定条件是
dQg dQr dT dT
全混釜的热平衡条件
以一级不可逆均相放热反应A→P为 例。
对组分A作物料衡算
vC A0 vC Af VR kCAf
C Af
CA0 1 k
反应过程的放热速率
Qg
(H )kCAfVR
(H
)k0CAf
VR
exp(
E RT
)
1
k0
exp(
E RT
)
由于反应速率常数与温度呈指数函
一维--仅考虑流体流动方向(轴向)上的温度和浓度变化, 与流向垂直的截面(径向)上则认为是等温和等浓度的。
二维--不仅考虑了轴向,且还考虑了径向上的浓度和温 度变化。(对于管径大、热效应大的反应)