锅炉炉排材料
锅炉本体的主要组成

锅炉本体的主要组成
炉子。
炉子是一种常用的锅炉燃烧设备,由炉排、炉膛和燃烧器组成。
锅筒。
锅筒又称汽包,上半部连接过热器管,下半部通过下降管、水冷壁管与联箱相连。
锅筒内部设有汽水分离装置,把饱和蒸汽与水分开。
水冷壁。
水冷壁是指分布在炉膛四周直径约为50〜80mm的管束,它吸收炉膛中髙温烟气的辐射热,使管内的锅水汽化,同时冷却炉墙起保护炉墙的作用。
蒸汽过热器。
蒸汽过热器是由一组蛇形管及进出口集箱组成。
它一般布置在烟气温度700°C〜800℃的烟道内,依靠对流换热吸收烟气的热量,使锅筒中产生的饱和蒸汽继续受热而成为过热蒸汽。
省煤器。
省煤器是由平行的蛇形管组成,是锅炉中常见的尾部附加受热面。
其作用是利用锅炉尾部低温烟气的热量预热给水,从而降低排烟温度,减少排烟带走的热量损失,提高锅炉效率,节约燃料消耗。
链条炉排锅炉用煤技术条件

链条炉排锅炉用煤技术条件英文回答:As for the technical requirements for coal used in chain grate boilers, there are several key factors to consider. Firstly, the coal should have a high calorific value to ensure efficient combustion and maximum heat output. This means that the coal should have a high carbon content and low moisture content.Secondly, the size of the coal particles is also important. The coal should be of a uniform size to allow for even distribution on the grate and proper air flow through the bed. If the coal particles are too large, they may not burn completely, leading to inefficient combustion and wasted energy. On the other hand, if the particles are too small, they may be carried away by the air flow before they can fully combust.In addition, the ash content of the coal is anotherimportant factor to consider. High ash content can lead to increased maintenance requirements and reduced boiler efficiency. Therefore, it is important to use coal with a low ash content to minimize these issues.Furthermore, the sulfur content of the coal should also be taken into account. High sulfur content can lead to the formation of sulfur dioxide during combustion, which is a major contributor to air pollution. Therefore, it is preferable to use coal with a low sulfur content to minimize environmental impact.In summary, the ideal coal for chain grate boilers should have a high calorific value, low moisture content, uniform particle size, low ash content, and low sulfur content to ensure efficient combustion and minimal environmental impact.中文回答:对于链条炉排锅炉使用的煤炭技术条件,有几个关键因素需要考虑。
锅炉生产工艺流程

锅炉生产工艺流程
《锅炉生产工艺流程》
锅炉是燃料燃烧产生的热能转化为蒸汽或热水的设备,广泛应用于工业生产、供暖和发电等领域。
其生产工艺流程通常包括以下几个主要步骤。
首先是原材料准备。
锅炉的主要原材料包括钢板、管子、炉排、保温材料、电控元件等。
这些原材料需要经过采购、检验、存储等环节,确保其质量符合要求。
接下来是零部件加工。
钢板需要进行切割、弯曲和焊接,制作成锅体和管子等组件。
炉排、保温材料和电控元件也需要进行加工和组装,以便后续的装配使用。
然后是装配和焊接。
经过零部件加工的组件被送到生产车间进行装配和焊接。
这是锅炉生产工艺的关键环节,需要严格按照工艺要求进行操作,确保焊接接头牢固、无渗漏。
随后是水压试验和耐压试验。
装配完成的锅炉需要进行水压试验和耐压试验,以测试其耐压性能和密封性能,确保其安全可靠。
最后是喷漆和包装。
锅炉经过测试合格后,需要进行喷漆和包装,以提高其外观质量和保护锅炉表面不受损坏。
综上所述,锅炉生产工艺流程包括原材料准备、零部件加工、
装配和焊接、水压试验和耐压试验、喷漆和包装等环节。
这个流程需要严格执行,确保锅炉的质量和性能符合标准要求,从而保障其在工业生产和生活供暖中的安全可靠性能。
锅炉型号字母表示意思
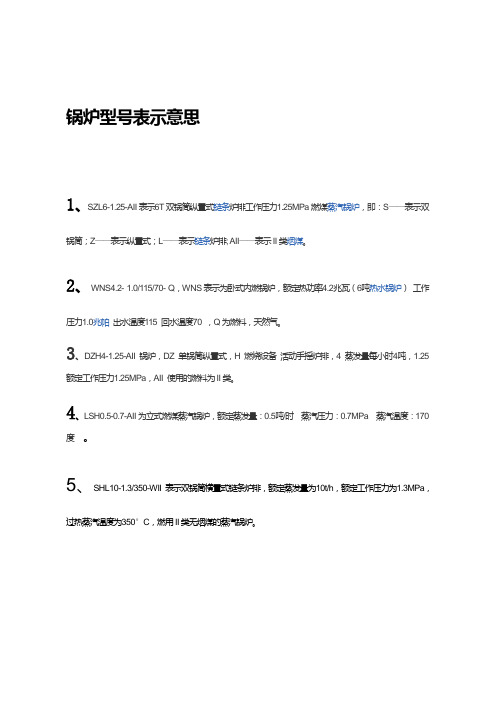
锅炉型号表示意思
1、SZL6-1.25-AII表示6T双锅筒纵置式链条炉排工作压力1.25MPa燃煤蒸汽锅炉,即:S——表示双锅筒;Z——表示纵置式;L——表示链条炉排; AII——表示II类烟煤。
2、WNS4.2- 1.0/115/70- Q,WNS表示为卧式内燃锅炉,额定热功率4.2兆瓦(6吨热水锅炉)工作压力1.0兆帕出水温度115 回水温度70 ,Q为燃料,天然气。
3、DZH4-1.25-AII锅炉,DZ 单锅筒纵置式,H 燃烧设备活动手摇炉排,4 蒸发量每小时4吨,1.25 额定工作压力1.25MPa,AII 使用的燃料为II类。
4、LSH0.5-0.7-AII为立式燃煤蒸汽锅炉,额定蒸发量:0.5吨/时蒸汽压力:0.7MPa 蒸汽温度:170度。
5、SHL10-1.3/350-WII 表示双锅筒横置式链条炉排,额定蒸发量为10t/h,额定工作压力为1.3MPa,过热蒸汽温度为350°C,燃用II类无烟煤的蒸汽锅炉。
锅炉材料消耗定额汇总

DZL2.8-1.0/95/70-AII
锅炉材料消耗定额
汇总表
陕西桥上桥锅炉有限责任公司
2004年编制
编制说明
一、为了加强物资管理工作,推进我厂物资管理工作走向科学化、规范化的进程,减少材料的浪费与流失情况,不断降低锅炉制造成本,物制定本定额。
二、这部锅炉材料消耗定额是根据有关技术文件、图纸,并结合我厂锅炉实际制造和试制情况编制的,采用的方法主要有技术计算法、实际查定法等。
三、锅炉主机材料消耗定额的部件有:锅炉本体、链条炉排、平台扶梯、炉墙外壳、煤斗、前烟箱、后烟箱和配套部分。
四、这部锅炉材料定额是我厂物资采购、投放以及领料和锅炉成本核算的重要参考依据。
五、在实际执行过程中,如发生实际消耗与消耗定额不符的,必须报经材料主管部门进行审核,经核定属实后乃按实际情况执行;
六、此定额自公布之日起实施。
二OO四年三月一日。
锅炉炉排施工方案

锅炉炉排施工方案一、施工前准备技术准备:组织技术团队熟悉施工图纸,明确施工要点和难点,制定详细施工方案。
材料准备:根据施工计划,提前采购所需材料,确保材料质量满足标准要求。
场地准备:清理施工现场,确保施工场地平整、无障碍物,并设置必要的施工标识。
二、设备检查与选型设备检查:对采购的设备进行全面检查,确保设备性能良好,符合设计要求。
设备选型:根据锅炉型号和实际需要,选择合适的炉排设备,确保炉排运行平稳、效率高。
三、基础施工与安装基础施工:按照图纸要求进行基础施工,确保基础牢固、平整。
设备安装:在基础施工完成后,按照设备安装说明进行设备安装,确保设备安装位置准确、固定牢固。
四、炉排组装与调试炉排组装:按照图纸要求进行炉排组装,确保组装过程中各部件配合紧密、无误差。
炉排调试:组装完成后进行炉排调试,检查炉排运行是否平稳、无卡涩现象,确保炉排运行正常。
五、管道连接与检查管道连接:按照图纸要求进行管道连接,确保管道连接牢固、无泄漏。
管道检查:对连接好的管道进行全面检查,确保管道无损坏、无泄漏。
六、安全防护与验收安全防护:施工现场设置必要的安全防护措施,确保施工人员安全。
验收工作:施工完成后进行验收工作,确保施工质量符合要求,验收合格后方可投入使用。
七、施工进度与人员施工进度:制定详细的施工进度计划,确保施工按时完成。
人员配置:根据施工进度计划合理配置施工人员,确保施工顺利进行。
八、质量保证与措施质量保证:施工过程中严格控制质量,确保施工质量符合设计要求。
质量措施:制定详细的质量保证措施,包括材料质量控制、施工工艺控制等,确保施工质量稳定可靠。
通过以上八个方面的详细规划和实施,可以确保锅炉炉排施工的顺利进行和高质量的完成。
在施工过程中,需要严格遵守相关规范和安全要求,确保施工人员的安全,同时注重质量控制,确保施工质量符合设计要求。
最终通过验收后,可以投入使用,为工业生产提供稳定的热源。
浅谈生物质能直燃发电站锅炉炉型和炉排

浅谈生物质能直燃发电站锅炉炉型和炉排生物质能直燃发电站是指利用生物质能源直接进行燃烧发电的一种发电设施。
而生物质能直燃发电站的核心设备,即锅炉,对于其发电效率和环保性具有至关重要的作用。
本文将从炉型和炉排两个方面进行浅谈,探讨生物质能直燃发电站锅炉的相关内容。
一、炉型生物质能直燃发电站的锅炉炉型主要分为层燃锅炉和循环流化床锅炉两种。
1. 层燃锅炉层燃锅炉是一种比较传统的生物质能直燃发电站锅炉炉型。
其特点是燃烧过程中燃料在炉膛内形成一定厚度的燃烧层,燃气从上到下穿过燃烧层,在燃烧过程中产生较高的热效率和燃烧效率。
层燃锅炉的设计工艺比较成熟,具有较高的稳定性和可靠性。
层燃锅炉的燃烧温度较高,易产生氮氧化物等有害气体,同时对燃料的要求也较高,不适合于所有类型的生物质能源。
2. 循环流化床锅炉循环流化床锅炉是一种先进的生物质能直燃发电站锅炉炉型。
其特点是采用流化床技术,将燃料置于流态床内进行燃烧,烟气通过循环气体固体分离器后被收集和净化。
循环流化床锅炉由于采用了流化床燃烧技术,其燃烧温度较低且燃烧效率高,同时对于燃料种类的适应性也较广。
循环流化床锅炉在燃烧过程中对燃料的严格要求较低,对于生物质能源的利用更加灵活。
循环流化床锅炉在生物质能直燃发电站中得到了广泛应用。
二、炉排炉排是生物质能直燃发电站锅炉中的核心部件之一,炉排的性能直接影响着生物质能直燃发电站锅炉的整体运行效率。
1. 固定炉排固定炉排是一种较为常见的生物质能直燃发电站锅炉炉排形式。
这种炉排由一组金属条或砖石构成,燃料在炉膛中静止不动地燃烧。
其优点是结构简单、成本低廉,但固定炉排容易造成燃料的不完全燃烧和积灰现象,增加了清灰的频率和难度,并且对燃料的种类也有一定的限制。
2. 移动炉排移动炉排是一种逐渐替代固定炉排的新型炉排形式。
这种炉排通过机械装置使得炉排能够在炉膛内来回移动,以及翻搅燃料,使得燃料的燃烧更加均衡和充分。
移动炉排的燃烧效率更高,减少了炉膛积灰的现象,同时对于燃料种类的适应性也更广。
130t振动炉排生物质锅炉设计说明
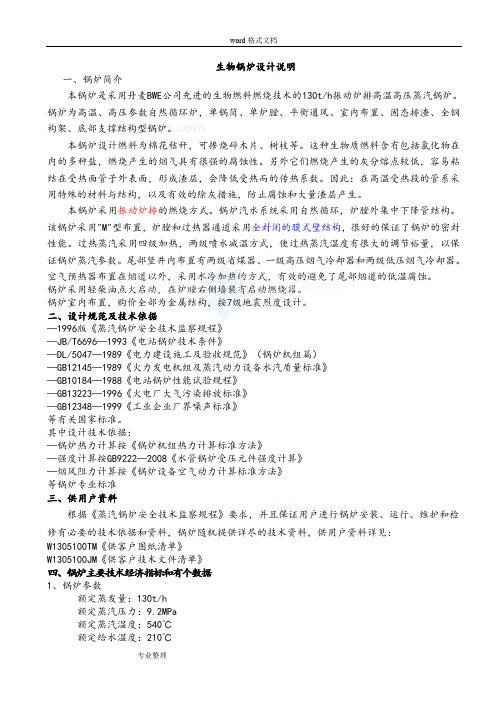
生物锅炉设计说明一、锅炉简介本锅炉是采用丹麦BWE公司先进的生物燃料燃烧技术的130t/h振动炉排高温高压蒸汽锅炉。
锅炉为高温、高压参数自然循环炉,单锅筒、单炉膛、平衡通风、室内布置、固态排渣、全钢构架、底部支撑结构型锅炉。
本锅炉设计燃料为棉花秸秆,可掺烧碎木片、树枝等。
这种生物质燃料含有包括氯化物在内的多种盐,燃烧产生的烟气具有很强的腐蚀性。
另外它们燃烧产生的灰分熔点较低,容易粘结在受热面管子外表面,形成渣层,会降低受热而的传热系数。
因此:在高温受热段的管系采用特殊的材料与结构,以及有效的除灰措施,防止腐蚀和大量渣层产生。
本锅炉采用振动炉排的燃烧方式。
锅炉汽水系统采用自然循环,炉膛外集中下降管结构。
该锅炉采用"M"型布置,炉膛和过热器通道采用全封闭的膜式壁结构,很好的保证了锅炉的密封性能。
过热蒸汽采用四级加热,两级喷水减温方式,使过热蒸汽温度有很大的调节裕量,以保证锅炉蒸汽参数。
尾部竖井内布置有两级省煤器、一级高压烟气冷却器和两级低压烟气冷却器。
空气预热器布置在烟道以外,采用水冷加热的方式,有效的避免了尾部烟道的低温腐蚀。
锅炉采用轻柴油点火启动,在炉膛右侧墙装有启动燃烧器。
锅炉室内布置,购价全部为金属结构,按7级地震烈度设计。
二、设计规范及技术依据—1996版《蒸汽锅炉安全技术监察规程》—JB/T6696—1993《电站锅炉技术条件》—DL/5047—1989《电力建设施工及验收规范》(锅炉机组篇)—GB12145—1989《火力发电机组及蒸汽动力设备水汽质量标准》—GB10184—1988《电站锅炉性能试验规程》—GB13223—1996《火电厂大气污染排放标准》—GB12348—1999《工业企业厂界噪声标准》等有关国家标准。
其中设计技术依据:—锅炉热力计算按《锅炉机组热力计算标准方法》—强度计算按GB9222—2008《水管锅炉受压元件强度计算》—烟风阻力计算按《锅炉设备空气动力计算标准方法》等锅炉专业标准三、供用户资料根据《蒸汽锅炉安全技术监察规程》要求,并且保证用户进行锅炉安装、运行、维护和检修有必要的技术依据和资料,锅炉随机提供详尽的技术资料,供用户资料详见:W1305100TM《供客户图纸清单》W1305100JM《供客户技术文件清单》四、锅炉主要技术经济指标和有个数据1、锅炉参数额定蒸发量:130t/h额定蒸汽压力:9.2MPa额定蒸汽温度:540℃额定给水温度:210℃3、技术经济指标冷风温度:35 ℃一次风预热温度190 ℃一、二次风预热温度190℃.二次风占总风量之比 1:1排烟温度 124℃锅炉热效率 92%燃料消耗量 22266.02Kg/h燃料粒度要求<100mm 100%<50mm 90%>5mm 5%排污率 2%设计数据锅炉外形尺寸宽度(锅炉架中心线) 24687mm深度(锅炉钢架中心线) 32388 nm锅筒中心线标度 23150 mm锅炉本体最高点标高 26074mm5、水质要求锅炉的给水、炉水、蒸汽品质均应符合GB12145 -1 9M0《火力发电机组及蒸汽动力设备水汽质量标准》;且符合用户的特殊要求。
锅炉炉排经常坏 原因和解决办法

锅炉炉排经常坏原因和解决办法
一、炉排故障的原因
1.运行时间过长
炉排在长时间的使用后,易受热膨胩和位移影响,从而损坏。
因此定期检修和更换炉排是非常必要的。
2. 灰渣积累
在燃煤锅炉燃烧煤炭的过程中,会产生大量的灰渣,灰渣在锅炉内积累过多,会增加炉排的负担,从而导致炉排出现故障。
3.炉排腐蚀
炉排在蒸汽锅炉中一般采用铸铁和复合材料制作,长时间在高温高压下工作,易发生氧化、热腐蚀、水腐蚀和钝化失效等问题,造成炉排材料的损坏和脱落。
二、炉排故障的解决方法
1. 正确使用设备
为了提高炉排的寿命,用户应该遵守生产厂家给出的使用规范,做好设备的保养和维护。
2. 定期检修和更换炉排
为避免机械故障,应该在炉排寿命到期前定期检修和更换设备,以保证其正常运行。
3. 做好灰渣清理工作
及时清理锅炉内部的灰渣,减轻炉排负担,延长设备的使用寿命。
4. 选用的炉排材料
用户在选用炉排时要选择的材料,确保设备可以在高温高压下坚固可靠地运行。
5. 炉排防腐蚀处理
炉排腐蚀是造成炉排损坏的重要原因之一,用户可以采用一些方法如涂料、贴膜等进行防腐处理,使材料不易腐蚀,延长设备使用寿命。
总之,针对锅炉炉排经常出现故障的问题,我们应该正确使用设备,定期检修和更换炉排,做好灰渣清理工作,选用的炉排材料,进行炉排防腐蚀处理等,以延长设备的使用寿命,保障正常生产。
锅炉燃烧方式
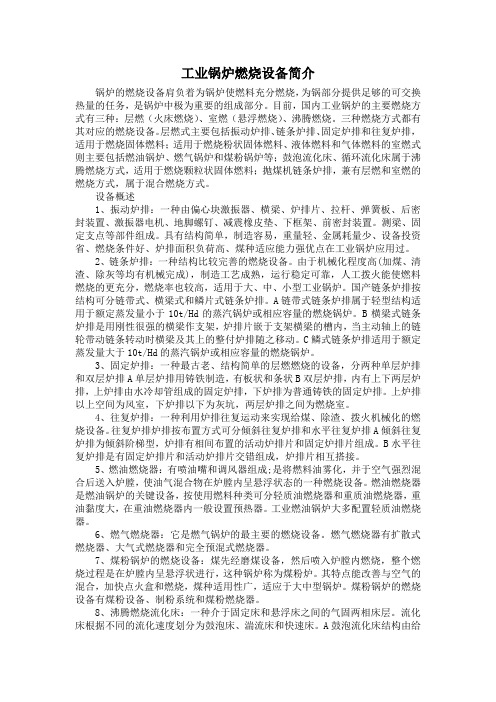
工业锅炉燃烧设备简介锅炉的燃烧设备肩负着为锅炉使燃料充分燃烧,为锅部分提供足够的可交换热量的任务,是锅炉中极为重要的组成部分。
目前,国内工业锅炉的主要燃烧方式有三种:层燃(火床燃烧)、室燃(悬浮燃烧)、沸腾燃烧。
三种燃烧方式都有其对应的燃烧设备。
层燃式主要包括振动炉排、链条炉排、固定炉排和往复炉排,适用于燃烧固体燃料;适用于燃烧粉状固体燃料、液体燃料和气体燃料的室燃式则主要包括燃油锅炉、燃气锅炉和煤粉锅炉等;鼓泡流化床、循环流化床属于沸腾燃烧方式,适用于燃烧颗粒状固体燃料;抛煤机链条炉排,兼有层燃和室燃的燃烧方式,属于混合燃烧方式。
设备概述1、振动炉排:一种由偏心块激振器、横梁、炉排片、拉杆、弹簧板、后密封装置、激振器电机、地脚螺钉、减震橡皮垫、下框架、前密封装置。
测梁、固定支点等部件组成。
具有结构简单,制造容易,重量轻、金属耗量少、设备投资省、燃烧条件好、炉排面积负荷高、煤种适应能力强优点在工业锅炉应用过。
2、链条炉排:一种结构比较完善的燃烧设备。
由于机械化程度高(加煤、清渣、除灰等均有机械完成),制造工艺成熟,运行稳定可靠,人工拨火能使燃料燃烧的更充分,燃烧率也较高,适用于大、中、小型工业锅炉。
国产链条炉排按结构可分链带式、横梁式和鳞片式链条炉排。
A链带式链条炉排属于轻型结构适用于额定蒸发量小于10t/Hd的蒸汽锅炉或相应容量的燃烧锅炉。
B横梁式链条炉排是用刚性很强的横梁作支架,炉排片嵌于支架横梁的槽内,当主动轴上的链轮带动链条转动时横梁及其上的整付炉排随之移动。
C鳞式链条炉排适用于额定蒸发量大于10t/Hd的蒸汽锅炉或相应容量的燃烧锅炉。
3、固定炉排:一种最古老、结构简单的层燃燃烧的设备,分两种单层炉排和双层炉排A单层炉排用铸铁制造,有板状和条状B双层炉排,内有上下两层炉排,上炉排由水冷却管组成的固定炉排,下炉排为普通铸铁的固定炉排。
上炉排以上空间为风室,下炉排以下为灰坑,两层炉排之间为燃烧室。
按目前常用的供热燃煤锅炉燃烧方式考虑
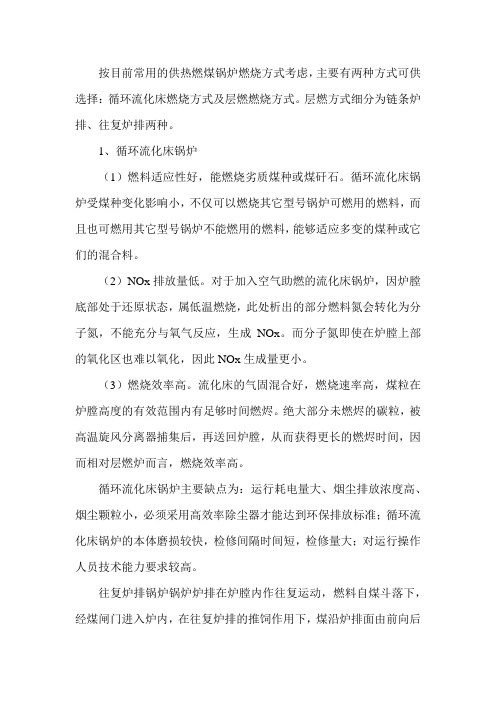
按目前常用的供热燃煤锅炉燃烧方式考虑,主要有两种方式可供选择:循环流化床燃烧方式及层燃燃烧方式。
层燃方式细分为链条炉排、往复炉排两种。
1、循环流化床锅炉(1)燃料适应性好,能燃烧劣质煤种或煤矸石。
循环流化床锅炉受煤种变化影响小,不仅可以燃烧其它型号锅炉可燃用的燃料,而且也可燃用其它型号锅炉不能燃用的燃料,能够适应多变的煤种或它们的混合料。
(2)NOx排放量低。
对于加入空气助燃的流化床锅炉,因炉膛底部处于还原状态,属低温燃烧,此处析出的部分燃料氮会转化为分子氮,不能充分与氧气反应,生成NOx。
而分子氮即使在炉膛上部的氧化区也难以氧化,因此NOx生成量更小。
(3)燃烧效率高。
流化床的气固混合好,燃烧速率高,煤粒在炉膛高度的有效范围内有足够时间燃烬。
绝大部分未燃烬的碳粒,被高温旋风分离器捕集后,再送回炉膛,从而获得更长的燃烬时间,因而相对层燃炉而言,燃烧效率高。
循环流化床锅炉主要缺点为:运行耗电量大、烟尘排放浓度高、烟尘颗粒小,必须采用高效率除尘器才能达到环保排放标准;循环流化床锅炉的本体磨损较快,检修间隔时间短,检修量大;对运行操作人员技术能力要求较高。
往复炉排锅炉锅炉炉排在炉膛内作往复运动,燃料自煤斗落下,经煤闸门进入炉内,在往复炉排的推饲作用下,煤沿炉排面由前向后缓慢移动,依次经历热力准备、焦炭燃烧和燃烬过程,所以燃烧过程与链条炉相似。
由于炉排的往复运动,可使部分新燃料推饲到已经着火的炽热火床上,一部分已经着火的炭粒回送到未燃煤层的底部,同时,燃料层被耙松,增加了透气性,焦炭块和煤粒外表的灰壳因挤压而破碎脱落,这些都有利于燃烧的强化和燃尽。
往复炉排炉对煤种的适应性较好,尤其对粘结性较强、含灰量多并难以着火的劣质煤,更能发挥其长处;消烟效果较佳,当操作及结构设计合理时,排烟含尘浓度低;锅炉运行操作简单,对运行人员技术水平要求较低。
往复炉排炉缺点是:炉排中段的炉排片容易烧坏;不宜燃用挥发分低、灰分少及发热值高的烟煤或贫煤;炉排两侧的漏风和漏煤较大,运行时,容易造成火床燃烧的不稳定;锅炉机械损失高,影响锅炉整体运行效率。
炉排

炉排编辑锅炉或工业炉中堆置固体燃料并使之有效燃烧的部件。
整个炉排主要包括框架和炉排片两个部分。
炉排片通常用铸铁制造,组装后片与片之间保持必要的通风缝隙,并且往往还在炉排下边设置可以调节风量的分隔的通风室,以便空气通过缝隙进入燃料层燃烧烧尽后的灰渣用人工或机械方法排出。
炉排有固定式、移动式、往复式、振动式和下饲式等类型。
目录1翻译2类型固定式移动式往复式振动式下饲式往复式倾斜往复式1翻译炉排grate2类型固定式炉排片一般为条状或板状,靠四周的框架固定安装在炉膛或燃烧室底部。
在这种炉排上只能定期由人工加煤和出渣,所以操作劳动强度大,燃烧经济效果也差,只适于小容量的炉子如蒸发量在0.5吨/时以下的工业锅炉。
炉排移动式有链带式和链条式两种。
链带式炉排的炉排面即链带本身;而链条式炉排的炉排片固定在链条上部的支架或支座上。
链带式炉排和链条式炉排均由链轮带动链条,使炉排片缓慢行进。
煤从炉排前端的煤斗均匀下落在炉排上。
煤层的厚度用一煤闸门上下起落加以调节。
随着炉排向后移动,煤由着火、燃烧直至烧尽。
也有不用煤斗给煤而用抛煤机把煤抛在炉排后部而炉排向前移动的。
炉排的速度依煤种和锅炉负荷的不同由齿轮变速器加以调节。
链条炉排运行可靠,燃烧稳定,燃料适应性广,广泛使用于工业锅炉中。
炉排往复式由一组固定的炉排片和一组往复运动的活动炉排片组成,分阶梯式和水平式两种。
活动炉排片的往复运动将煤层逐步推向后部燃烧,因而这种炉排对煤种的适应性较广。
炉排炉连片(6张)振动式炉排面与水平面之间有一个小的倾角,炉排片借电动机和偏心轮的作用产生定期振动。
振动时燃料层不断向炉的后部移动,使燃尽后的灰渣落入炉排端部的灰坑内。
这种炉排的特点是结构简单。
下饲式一个槽形结构炉排,槽底装有螺旋杆,通至炉外煤斗。
煤从煤斗下部通过螺旋杆送入煤槽,自下而上,进入燃烧高温区,当灰渣超过堆积角后,靠重力向两侧排出。
这种炉排结构简单,但对煤的粒度和湿度有一定要求,一般只适用于蒸发量在1吨/时以下的小型工业锅炉。
耐热耐磨炉排材质的组织和性能研究(综述)
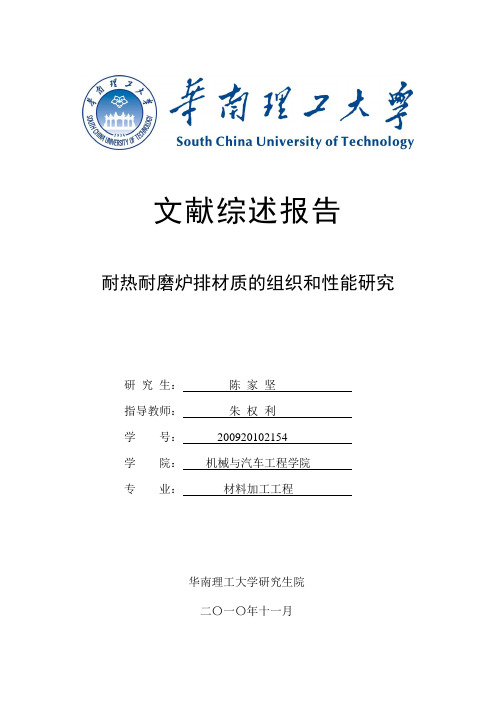
文献综述报告耐热耐磨炉排材质的组织和性能研究研究生:陈家坚指导教师:朱权利学号:200920102154学院:机械与汽车工程学院专业:材料加工工程华南理工大学研究生院二〇一〇年十一月耐热耐磨炉排材质的组织和性能研究摘要:研究了我国大型城市生活垃圾倾斜逆推式炉排炉中炉排片的工况条件,提出了相应工况下对炉排片材质耐热耐磨的要求。
对国内外耐热合金及高温耐磨合金材料的发展现状作了简述,并综合分析了国内外炉排材质的研究和应用状况,提出了我国大型城市生活垃圾焚烧往复炉排材质的现存问题,进而指出其发展趋势。
最后,提出了大型城市生活垃圾焚烧炉往复炉排材质的成分设计及其优化思想,为炉排材质的成分设计和组织性能研究提供一定的理论指导。
关键词:炉排,耐热,耐磨,组织,性能1 前言当前,城市生活垃圾处理已成为我国各个城市面临的严峻问题。
随着国民经济的高速发展以及人民生活水平的提高,生活垃圾日渐增多,如果处理不当将造成生态环境的严重破坏。
采用焚烧法来处理固态垃圾是实现其无害化、减量化、资源化的有效手段,在国内外受到了日益广泛的重视[1]。
目前,大型生活垃圾焚烧设备通常有流化床、回转窑、热分解炉和机械炉排焚烧炉等。
机械炉排焚烧炉的技术完善可靠,容量大,对垃圾的适应性强,绝大部分固体垃圾不需要任何预处理可直接进炉燃烧,尤其适用于大规模垃圾的集中处理,可进行垃圾焚烧发电(或供热),其应用占全世界垃圾焚烧市场总量的80%以上[2]。
针对我国目前垃圾处理的现状以及我国城市生活垃圾高水分、低热值的特点,机械往复炉排焚烧炉技术是最适宜我国城市垃圾焚烧的技术。
由于垃圾焚烧技术较复杂、技术含量高,我国在这方面的技术力量相对来说还比较薄弱,其中大型城市生活垃圾往复炉排炉焚烧厂的建设主要还是依靠引进国外先进的焚烧炉,建设投资相对较高。
炉排是往复炉排中堆置垃圾并使之充分燃烧的重要部件,生产高性能的炉排是大规模焚烧炉的关键技术之一。
然而,炉排的进口价格昂贵,运行成本很高,如果长期依赖国外进口,势必影响企业的效益,导致垃圾发电的推广应用受到阻碍。
工业锅炉链条炉排分类结构及工作过程

工业锅炉链条炉排分类结构及工作过程链条炉排是工业锅炉中历史悠久、结构可靠、运行稳定的一种机械化燃煤设备,获得了广泛的应用。
一、链条炉排的结构链条炉排的外形好像皮带输送机,其结构如图3—7 所示。
其运行过程是煤从煤斗内依靠自重落到炉排前端,随炉排自前向后缓慢移动,经煤闸板进入炉膛。
煤闸板的高度可以自由调节,以控制煤层的厚度。
空气从炉排下面分区送风室引入,与煤层运动方向相交。
煤在炉膛内受到辐射加热,依次完成预热、干燥、着火、燃烧,直到燃尽。
灰渣则随炉排移动到后部,经过挡渣板( 俗称老鹰铁) 落入后部水冷灰渣斗,由除渣机排出。
链条炉排的结构形式一般可分链带式、横梁式和鳞片式三种。
1 .链带式炉排链带式炉排属于轻型炉排,适用于蒸发量10t /h 以下的锅炉,其炉排片连接结构如图3_8 所示。
炉排片分为主动炉排片和从动炉排片两种,用圆钢拉杆串联在一起,形成一条宽幅的链带,围绕在前链轮和后滚筒上。
主动炉排片担负传递整个炉排运动的拉力,因此其厚度比从动炉排片厚,由可锻铸铁制成。
一台蒸发量 4 t /h 的锅炉,由主动炉排片组成的主动链条共有三条( 两侧和中间) 直接与前轴( 主动轴)上的三个链轮相啮合。
从动炉排片,由于不承受拉力,可由强度低的普通灰口铸铁制成。
链带式炉排的优点是:比其他链条炉排金属耗量低,结构简单,制造、安装和运行都比较方便。
缺点是:炉排片用圆钢串联,必须保证加工和装配质量,否则容易折断,而且不便于检修和更换;长时间运行后,由于炉排片互相磨损严重,使炉排间隙增大,漏煤损失增多。
2 .横梁式炉排横梁式炉排适用于蒸发量20 ~40 t /h 甚至更大的锅炉。
|其结构与链带式炉排的主要区别在于采用。
了许多刚性较大的横梁。
炉排片装在横梁的相应槽内,横梁固定在传动链条上。
传动链条一般是两条( 当炉排很宽时,可装置多条) 。
横梁式炉排的优点是:结构刚性大,炉排片受热不受力,而横梁和链条受力不受热,比较安全耐用;炉排面积可以较大,阻力小而风量分布均匀;运行中漏煤、漏风量少。
常用锅炉数据

工业锅炉常用资料本章内容仅适用于评价锅炉结构的合理性、发现设计上的明显错误等;而新设计锅炉时,应对所采用的每项数据进行仔细推敲、比较,并进行严格、详细的计算。
一、锅炉炉排面积锅炉炉排面积可查表26-1。
表26-1注:本表数据适用于锅炉效率为70%时。
二、锅炉炉膛容积锅炉炉膛容积可查表26-2。
表26-2注:本表数据适用于锅炉效率为70%(燃煤)、80%(燃油)时。
三、对流受热面中的建议烟速对流受热面中的烟速过低,因传热减弱,需增大受热面积,另外,烟速过低还使积灰加剧,进一步影响传热。
对流受热面中的烟速过高,使阻力增加,需多消耗风机电能,另外,烟速过高还会发生急剧磨损,影响锅炉寿命。
因而强制通风锅炉对流受热面额定负荷下的烟速建议按表26-3选取。
表26-3自然通风锅炉为减小阻力,对流受热面一般仅为蒸发管束,而且烟速约为3-4米/秒。
为防止积灰使传热恶化,要求定期吹灰。
四、对流受热面中烟气流通截面积1、仅有蒸发管束,每小时产生1吨蒸汽时烟气流通截面积按表26-4选取。
烟气流通截面积,米2/吨/时(对流受热面)表26-4注:锅炉效率为70%。
2、有省煤器及蒸发管束,每小时产生1吨蒸汽时烟气流通截面积按表26-5选取。
烟气流通截面积,米2/吨/时(对流受热面)表26-5 注:锅炉效率为70%。
3、热水锅炉,每小时产生1百万千卡热量时烟气流通截面积按表26-6选取。
烟气流通截面积,米2/百万千卡表26-6 注:锅炉效率为70%。
五、锅炉受热面积1、蒸汽锅炉每小时产生1吨蒸汽所需受热面积可按表26-7选取。
受热面积,米2/吨/时表26-72、热水锅炉每小时产生1百万千卡热量所需受热面积可按表26-8选取。
受热面积,米2/百万千卡/时表26-83、辐射受热面积按下式计算:辐射受热面积=辐射系数×布置辐射受热面的炉墙面积。
辐射系数可按表26-9选取。
表26-94、对流受热面积为与烟气接触的管子外表面积之和。
往复炉排工作原理

往复炉排工作原理
往复炉排是一种常用于锅炉中的燃烧设备,其工作原理如下:
1. 燃料供给:往复炉排通常用于燃烧固体燃料,燃料通过供给系统加入炉排的燃料仓中。
2. 往复运动:往复炉排由一组连杆、曲柄机构和推杆组成。
曲柄机构根据设定的节律通过连杆使炉排在炉膛内往复运动。
3. 燃烧过程:当炉排往复下移时,固体燃料从燃料仓中被推送到燃烧区域。
在燃烧区域中,燃料与空气进行充分混合并燃烧,产生高温气体。
4. 燃烧产物排放:燃烧后的燃烧产物以及未燃烧的固体燃料残渣通过炉排往复上移时排出炉膛。
5. 热能回收:燃烧产生的高温气体可用于锅炉中的热能回收系统,例如传导给锅炉水壁进行水蒸气生成。
这些步骤循环重复,不断地进行燃料供给、往复运动、燃烧和热能回收,以保持锅炉的稳定工作。
锅炉炉排材料
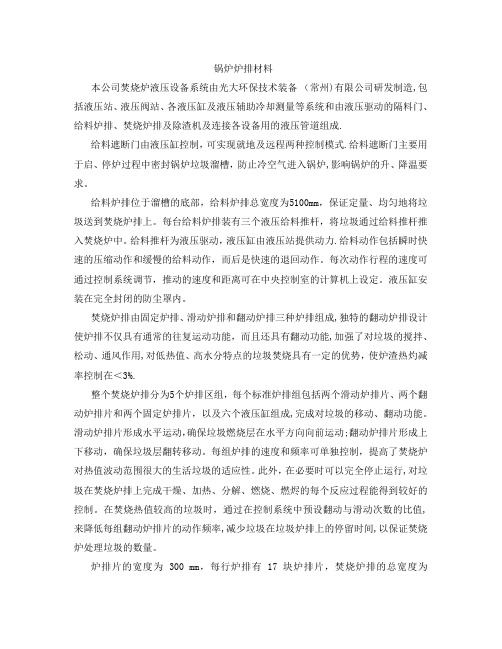
锅炉炉排材料本公司焚烧炉液压设备系统由光大环保技术装备(常州)有限公司研发制造,包括液压站、液压阀站、各液压缸及液压辅助冷却测量等系统和由液压驱动的隔料门、给料炉排、焚烧炉排及除渣机及连接各设备用的液压管道组成.给料遮断门由液压缸控制,可实现就地及远程两种控制模式.给料遮断门主要用于启、停炉过程中密封锅炉垃圾溜槽,防止冷空气进入锅炉,影响锅炉的升、降温要求。
给料炉排位于溜槽的底部,给料炉排总宽度为5100mm,保证定量、均匀地将垃圾送到焚烧炉排上。
每台给料炉排装有三个液压给料推杆,将垃圾通过给料推杆推入焚烧炉中。
给料推杆为液压驱动,液压缸由液压站提供动力.给料动作包括瞬时快速的压缩动作和缓慢的给料动作,而后是快速的退回动作。
每次动作行程的速度可通过控制系统调节,推动的速度和距离可在中央控制室的计算机上设定。
液压缸安装在完全封闭的防尘罩内。
焚烧炉排由固定炉排、滑动炉排和翻动炉排三种炉排组成,独特的翻动炉排设计使炉排不仅具有通常的往复运动功能,而且还具有翻动功能,加强了对垃圾的搅拌、松动、通风作用,对低热值、高水分特点的垃圾焚烧具有一定的优势,使炉渣热灼减率控制在<3%.整个焚烧炉排分为5个炉排区组,每个标准炉排组包括两个滑动炉排片、两个翻动炉排片和两个固定炉排片,以及六个液压缸组成,完成对垃圾的移动、翻动功能。
滑动炉排片形成水平运动,确保垃圾燃烧层在水平方向向前运动;翻动炉排片形成上下移动,确保垃圾层翻转移动。
每组炉排的速度和频率可单独控制,提高了焚烧炉对热值波动范围很大的生活垃圾的适应性。
此外,在必要时可以完全停止运行,对垃圾在焚烧炉排上完成干燥、加热、分解、燃烧、燃烬的每个反应过程能得到较好的控制。
在焚烧热值较高的垃圾时,通过在控制系统中预设翻动与滑动次数的比值,来降低每组翻动炉排片的动作频率,减少垃圾在垃圾炉排上的停留时间,以保证焚烧炉处理垃圾的数量。
炉排片的宽度为 300 mm,每行炉排有 17 块炉排片,焚烧炉排的总宽度为5100mm。
- 1、下载文档前请自行甄别文档内容的完整性,平台不提供额外的编辑、内容补充、找答案等附加服务。
- 2、"仅部分预览"的文档,不可在线预览部分如存在完整性等问题,可反馈申请退款(可完整预览的文档不适用该条件!)。
- 3、如文档侵犯您的权益,请联系客服反馈,我们会尽快为您处理(人工客服工作时间:9:00-18:30)。
锅炉炉排材料本公司焚烧炉液压设备系统由光大环保技术装备 (常州)有限公司研发制造,包括液压站、液压阀站、各液压缸及液压辅助冷却测量等系统和由液压驱动的隔料门、给料炉排、焚烧炉排及除渣机及连接各设备用的液压管道组成。
给料遮断门由液压缸控制,可实现就地及远程两种控制模式。
给料遮断门主要用于启、停炉过程中密封锅炉垃圾溜槽,防止冷空气进入锅炉,影响锅炉的升、降温要求。
给料炉排位于溜槽的底部,给料炉排总宽度为5100mm,保证定量、均匀地将垃圾送到焚烧炉排上。
每台给料炉排装有三个液压给料推杆,将垃圾通过给料推杆推入焚烧炉中。
给料推杆为液压驱动,液压缸由液压站提供动力。
给料动作包括瞬时快速的压缩动作和缓慢的给料动作,而后是快速的退回动作。
每次动作行程的速度可通过控制系统调节,推动的速度和距离可在中央控制室的计算机上设定。
液压缸安装在完全封闭的防尘罩内。
焚烧炉排由固定炉排、滑动炉排和翻动炉排三种炉排组成,独特的翻动炉排设计使炉排不仅具有通常的往复运动功能,而且还具有翻动功能,加强了对垃圾的搅拌、松动、通风作用,对低热值、高水分特点的垃圾焚烧具有一定的优势,使炉渣热灼减率控制在<3%。
整个焚烧炉排分为5个炉排区组,每个标准炉排组包括两个滑动炉排片、两个翻动炉排片和两个固定炉排片,以及六个液压缸组成,完成对垃圾的移动、翻动功能。
滑动炉排片形成水平运动,确保垃圾燃烧层在水平方向向前运动;翻动炉排片形成上下移动,确保垃圾层翻转移动。
每组炉排的速度和频率可单独控制,提高了焚烧炉对热值波动范围很大的生活垃圾的适应性。
此外,在必要时可以完全停止运行,对垃圾在焚烧炉排上完成干燥、加热、分解、燃烧、燃烬的每个反应过程能得到较好的控制。
在焚烧热值较高的垃圾时,通过在控制系统中预设翻动与滑动次数的比值,来降低每组翻动炉排片的动作频率,减少垃圾在垃圾炉排上的停留时间,以保证焚烧炉处理垃圾的数量。
炉排片的宽度为 300 mm,每行炉排有 17 块炉排片,焚烧炉排的总宽度为5100mm。
焚烧炉炉排的总长度为 m,前4个单元为燃烧段,最后1个单元是燃烬区,为了保证垃圾的完全充分焚烧,使焚烧炉的热灼减率控制在<3%,以达到比较严格的技术要求,所以最后1段适当加长。
炉排底部分室进风优化了燃烧空气供应,延长了炉排使用寿命。
炉排下部的灰斗有既能收集炉底灰,又是各个炉排组的一次风的进风口。
一次风沿炉排组下进入焚烧炉,向下吹至垃圾料层,这既有效地减少了垃圾表面结焦,又能比较好地冷却了炉排片,减少了炉排片的更换率。
此外,炉排选用优质材料,以及各个运动部件的精确的配合,炉排片具有很高的耐用性。
液压系统的运行调整:控制系统可自动设置相应的各段滑动和翻动炉排的频率、炉排运动速度、自动修改送风量、调配垃圾量与送风量的适当比例。
下列表中是几种标准的参数设定:不同热值下的炉排速度:同状态滑动与翻动炉排的动作频率(仅供参考):注:表中S表示滑动炉排动作频率,T表示翻动炉排动作频率。
根据垃圾发热值从低位到高位,滑动炉排和翻动炉排的周期比分别为1S/5T、1S/4T、1S/3T、1S/3T、1S/1T、2S/1T、3S/1T。
对炉中的垃圾进行拔火、搅拌,可以使垃圾与空气充分混合,改善燃烧,可以由操作员依据垃圾的发热值来进行设定调节。
几种特定的设置拔料:当垃圾厚度大、垃圾热值低,炉膛燃烧困难时炉排选择为0s/5T,滑动炉排立即回撤,所以翻动炉排仅作翻动动作。
倒空炉膛:若要进行停炉等操作将炉排上的垃圾排空,则需将炉排设置为1S/0T。
液压系统事故处理不出油、输油量不足、压力上不去:故障原因:电动机转向不对。
吸油管或过滤器堵塞。
轴向间隙或径向间隙过大。
连接处泄漏,油中混入空气。
油液粘度太大或油液温升太高。
处理方法:检查电动机转向。
疏通管道,清洗过滤器,换新油。
检查更换有关零件。
紧固各连接处螺钉,避免泄漏。
正确选用油液,控制温升。
噪音严重、压力波动厉害:故障原因:吸油管及过滤器堵塞或过滤器容量小。
吸油管密封处漏气或油液中有气泡。
泵与联轴节不同心。
油箱油位低。
油温低或粘度高。
油泵轴承损坏。
处理方法:清洗过滤器使吸油管通畅,正确选用过滤器。
在连接部位或密封处加油,如噪音减少,可拧紧接头处或更换密封圈,回油管口应在油面以下与吸油管有一定距离。
调整同心。
把油加热到适当温度。
检查(用手触感)泵轴温升。
泵轴颈油封漏油:故障原因:漏油管道液阻过大,使泵体内压力升高到超过油封许用的耐压值。
处理方法:检查柱塞泵泵体上的泄油是否用单独油管直接接通油箱。
若发现把几台柱塞泵的泄油管并联在一根同直径的总管后再接通油箱,或者把柱塞泵的泄油管接到总回油管上,则应予改正,最好在泵泄漏油口接一个压力表,以检查泵体内的压力,其值小于。
液压缸爬行:故障原因:空气侵入。
液压缸端盖密封圈压得太紧或过松。
活塞杆与活塞不同心。
活塞杆全长或局部弯曲。
液压缸的安装位置偏移。
液压缸内孔直线性不良。
缸内腐蚀,拉毛。
双活塞杆两端螺帽拧的太紧,使其同心度不良。
处理方法:增设排气装置,如无排气装置,可开动液压系统以最大行程使工作部件快速运动,强迫排除空气。
调整密封圈,使它不紧不松,保证活塞杆能来回用手平稳的拉动而无泄漏(大多允许微量渗油)。
校正二者同心。
校正活塞杆。
检查液压缸与导轨的平行性并校正。
镗磨修复,重配活塞。
轻微者修去锈蚀和毛刺,严重者必须镗磨。
螺帽不宜拧得太紧,一般用手旋紧即可,以保持活塞杆处于自然状态。
液压缸冲击:故障原因:靠间隙密封的活塞和液压缸间隙过大,节流阀失去节流作用。
端头缓冲的单向阀失灵,缓冲不起作用。
处理方法:按规定配活塞与液压缸的间隙,减少泄漏现象。
修正研配单向阀与阀座。
推力不足或工作速度逐渐下降甚至停止:故障原因:液压缸和活塞配合间隙太大或O型密封圈损坏,造成高低压腔互通。
由于工作时经常用工作行程的某一段,造成液压缸孔直线性不良(局部有腰彭形),致使液压缸两端高低压油互通。
缸端油封压得太紧或活塞杆弯曲,使摩擦力或阻力增加。
泄漏过多。
油温太高,粘度减少,靠间隙密封或密封在质量差的油缸行速度慢。
若液压缸两端高低压油腔互通,运行速度逐渐减慢至停止。
处理方法:单配活塞和液压缸的间隙或更换O型密封圈。
镗磨修复液压缸孔径,单配活塞。
放松油封,以不漏油为限,校直活塞杆。
寻找泄漏部分,紧固各结合面。
分析发热原理,设法散热降温。
如密封间隙过大则单配活塞或增装密封环。
溢流阀压力波动:故障原因:弹簧弯曲或太软。
锥阀与阀座接触不良。
钢球与阀座接触不良。
滑阀变形或拉毛。
油质不清洁,阻尼孔堵塞。
处理方法:更换弹簧。
如锥阀是新的即卸下调整螺帽,将导杆推几下,使其接触良好,或更换锥阀。
检查钢球圆度,更换钢球,研磨阀座。
更换或修研滑阀。
疏通阻尼孔,更换清洁油液。
溢流阀调整无效故障原因弹簧断裂或漏装。
阻尼孔堵塞。
滑阀卡住。
进出油口装反。
锥阀漏装。
处理方法:检查、更换或补装弹簧。
疏通阻尼孔。
拆出、检查、修整。
检查油源方向。
检查、补装。
溢流阀泄漏严重:故障原因:锥阀或钢球与阀座的接触不良。
滑阀与阀体配合间隙过大。
管接头没拧紧。
密封破坏。
处理方法:锥阀或钢球研磨更换新的锥阀或钢球。
检查阀芯与阀体间隙。
拧紧阀芯与阀体间隙。
检查更换密封。
故障原因:螺帽松动。
弹簧变形,不复原。
滑阀配合过紧。
主滑阀动作不良。
主滑阀磨损。
出油路中有空气。
流量超过允许值。
和其他阀产生共振。
处理方法:紧固螺帽。
检查并更换弹簧。
修研滑阀,使其灵活。
检查滑阀与壳体的同心度。
换锥阀。
排出空气。
更换与流量对应的阀。
略为改变阀的额定压力(如额定压力值的差在以内时,则容易发生共振。
故障原因:油液中混入空气。
阻尼有时堵塞。
滑阀与阀体内孔圆度超过规定,使阀卡住。
弹簧变形或在滑阀中卡住,使滑阀移动困难或弹簧变形。
钢球不圆,钢球与阀座配合不好或锥阀安装不正确。
处理方法:排除油中空气。
清理阻尼。
修研阀孔及滑阀。
更换弹簧。
更换钢球或折开锥阀调整。
故障原因:外泄漏。
锥阀与阀座接触不良。
处理方法:更换密封件,紧固螺钉,并保证力矩均匀。
修理或更换。
故障原因:泄油口不通;泄油管与回油管道相连,并有回油压力。
主阀芯在全开位置时卡死。
处理方法:泄油管必须与回油管道分开,单独回入油箱。
修理、更换零件,检查油质。
故障原因:节流阀和孔的间隙过大,有泄漏以及系统内部泄漏。
节流孔阻塞或阀芯卡住。
处理方法:检查泄漏部分零件损坏情况,予以修复、更新,注意结合处的油封情况。
拆开清洗,更换新油液,使阀芯运动灵活。
故障原因:油中杂质粘附在节流口边上,通流截面积减小,使速度减慢。
节流阀的性能较差,低速运动时由于振动使调节位置变化。
节流阀内部,外部有泄漏。
在简式的节流阀中,因系统负荷有变化使速度突变。
油温升高,油液的粘度降低,使其速度逐步升高。
阻尼装置堵塞,系统中有空气,出现压力变化及跳动。
处理方法:拆卸清洗有关零件,更换新油,并经常保持油液清洁。
增加节流联锁装置。
检查零件的精度和配合间隙,修配或更换超差的零件,连接处要严加封闭。
检查系统压力和减压装置等部件的作用以及溢流阀的控制是否正常。
液压系统稳定后调整节流阀或增加油散热装置冷却水量。
清洗零件,在系统中增设排气阀油液要保持洁净。
故障原因:滑阀卡死。
阀体变形。
具有中间位置的对中弹簧折断。
操纵压力不够。
电磁铁线圈烧坏或电磁铁推力不足。
电气线路出故障。
液控换向阀控制油路无油或被堵塞。
处理方法:拆开清洗脏物,去毛刺。
调节阀体安装螺钉使压紧力均匀或修研阀孔。
更换弹簧。
操纵压力必须大于。
检查、修理、更换。
消除故障。
检查原因并消除。
故障原因:滑阀卡住或摩擦力过大。
电磁铁不能压到底。
电磁铁铁芯接触面不平或接触不良。
处理方法修研或调配滑阀。
校正电磁铁高度。
消除污物,修正电磁铁铁芯。
故障原因:控制压力过低。
控制油管道接头漏油严重。
单向阀卡死。
处理方法:提高控制压力使之达到要求值。
紧固接头,消除漏油。
清洗。
故障原因:单向阀在全开位置上卡死。
单向阀锥面与阀座面接触不均匀。
处理方法:修配清洗。
检修或更换。
故障原因:回油管路的阀门动作不良。
阀规格过小,能量损失太大。
选用泵时,泵的流量过大。
冷却水供中断。
冷却水管路中有沉淀。
油箱的散热面积不足。
由于磨损造成功率损失。
工作油粘度过低或过高。
油箱中油位太低。
管道的内径和需要的流量不相适应。
处理方法:检查电气回路、电磁阀、回油管路的阀门动作是否正常。
根据系统的工作压力和通过该阀的最大流量选取阀门。
根据系统的工作压力、流量合理选泵。
消除冷却水管路中的沉淀。
改装冷却系统或加大油箱容量及散热面积。
更换管路,减轻磨损。
选择合适粘度的油。
加油至合适的工作位置。
装置适宜尺寸的管道和阀门,降低功率。